Introduce about custom injection moulding guide,Qulity,Cost,Supplier,Certification,Market,Tips,FAQ
Custom injection moulding is a versatile manufacturing process that involves injecting molten material into a designed mould to create a custom-shaped product. This guide aims to provide valuable information on various aspects of custom injection moulding in a concise manner.
Quality is paramount when it comes to custom injection moulding. To ensure high-quality production, it is crucial to work with an experienced and reputable manufacturer that follows strict quality control measures. The manufacturer should have the necessary expertise, equipment, and inspection processes in place to deliver consistent and defect-free products.
Cost is an important consideration in custom injection moulding. The complexity and size of the product, the type of material used, and the production volume can significantly impact the overall cost. Opting for a manufacturer that offers competitive pricing without compromising on quality is advisable. Getting multiple quotes from different suppliers can help in assessing the most cost-effective option.
Choosing the right supplier is crucial for successful custom injection moulding. Look for a supplier with a strong track record, good customer reviews, and the ability to meet your specific requirements. It is essential to evaluate their manufacturing capabilities, technical expertise, and responsiveness to ensure a smooth and reliable production process.
Certification plays a significant role in custom injection moulding. Verify that the manufacturer holds relevant certifications such as ISO 9001 that ensure adherence to international quality standards. Certifications like ISO 13485 may be necessary for medical applications, while automotive applications might require certifications like ISO/TS 16949.
The market for custom injection moulding is vast and diverse, catering to various industries such as automotive, medical, consumer goods, and electronics. Understanding the specific market requirements and trends can help in developing products that meet consumer demands and stay ahead of the competition.
Tips for successful custom injection moulding include careful material selection, proper design considerations, regular communication with the supplier, and thorough testing to identify and rectify any manufacturing issues.
Frequently Asked Questions (FAQ) about custom injection moulding may revolve around topics such as production lead times, material options, tooling costs, design limitations, and post-production finishing processes. Providing comprehensive answers to these FAQs can offer valuable insights to those new to or exploring custom injection moulding.
In summary, custom injection moulding is a versatile manufacturing process that requires attention to quality, cost, supplier selection, certification, market understanding, and adherence to tips for success. Gathering essential information and clarifying frequently asked questions can ensure a smooth and efficient custom injection moulding experience.
Types of custom injection moulding
Custom injection moulding is a versatile manufacturing process that allows for the production of a wide range of plastic parts and components. There are several types of custom injection moulding techniques, each suited to different applications and requirements. Here are some of the commonly used types:
1. Thermoplastic injection moulding: This is the most common type of custom injection moulding. It involves melting a thermoplastic material, injecting it into a mould cavity, and then cooling and solidifying it to form the desired shape. Thermoplastics offer advantages such as high strength, durability, and flexibility.
2. Thermoset injection moulding: This process is similar to thermoplastic injection moulding but uses thermosetting materials that undergo a chemical reaction during curing, becoming rigid and non-meltable. The resulting parts offer excellent dimensional stability, high heat resistance, and superior electrical insulation properties.
3. Overmoulding: Overmoulding is a process that involves moulding one material over another to create a combined part with multiple layers or colors. It is often used to provide additional features, aesthetics, or functional elements to a base part.
4. Insert moulding: Insert moulding involves placing metal or plastic inserts into the mould cavity before injection moulding. The molten material then encapsulates the insert, creating a strong bond between the two. This technique is commonly used to add threaded inserts, electrical components, or reinforcement to plastic parts.
5. Multi-shot injection moulding: Multi-shot moulding enables the production of complex parts with different materials or colors in a single moulding cycle. It involves injecting different materials sequentially into the same mould to create multi-color parts, overmoulded parts, or parts with different properties in specific regions.
6. Gas-assisted injection moulding: Gas-assisted injection moulding utilizes a high-pressure gas to help form hollow sections or provide channels within a part, thereby reducing material usage and obtaining lighter, stronger parts with enhanced aesthetics.
7. Micro-injection moulding: Micro-injection moulding is used to produce extremely small and precise plastic parts, typically with features in the micrometre range. This technique is essential in industries such as medical devices, electronics, and automotive, where miniaturization is crucial.
In conclusion, custom injection moulding encompasses various techniques to meet specific industry needs. Whether it is thermoplastic or thermoset, overmoulding or multi-shot moulding, each method offers unique advantages and applications, enabling the production of high-quality plastic parts tailored to specific requirements.
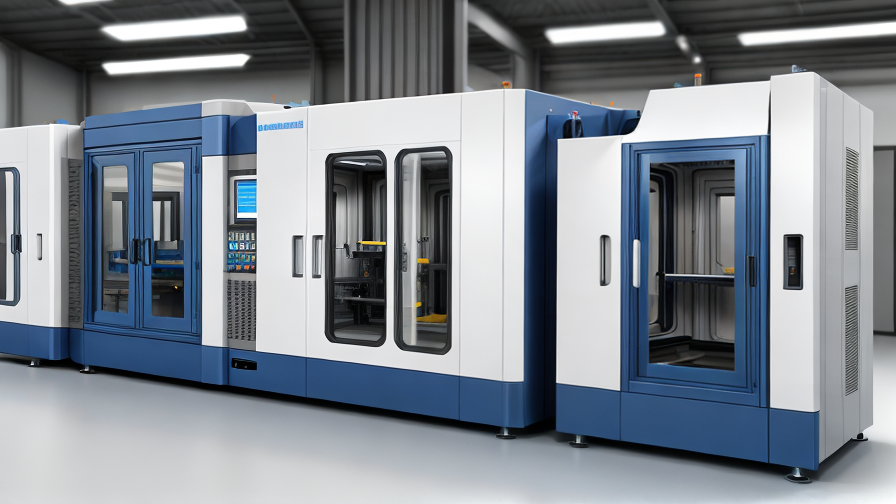
Pros and Cons of Using custom injection moulding
Custom injection molding is a widely used manufacturing process that involves injecting molten plastic into a mold cavity to create a desired shape. It offers various advantages and disadvantages, as outlined below.
Pros of Using Custom Injection Molding:
1. Cost-effective: Custom injection molding can be cost-effective for large production runs due to its ability to produce consistent and high-quality products at a lower cost per part. The use of automated machinery and efficient production processes help reduce labor costs.
2. High production efficiency: Injection molding allows for high production efficiency as it can produce a large number of identical parts within a short timeframe. This makes it highly suitable for mass production applications.
3. Wide range of material options: Injection molding allows for the use of a wide range of thermoplastic and thermosetting materials, providing flexibility in material selection according to the desired properties, strength, and durability of the final product.
4. Complex shapes and intricate details: With injection molding, complex shapes and intricate details can be achieved, including undercuts, threads, and thin walls. This makes it suitable for producing intricate and customized parts that may not be easily achievable with other manufacturing methods.
5. Minimal material wastage: The injection molding process typically generates minimal material wastage as the excess material can be recycled and reused for future production runs. This helps minimize costs and supports eco-friendly practices.
Cons of Using Custom Injection Molding:
1. High upfront cost: Setting up a custom injection molding process requires significant upfront investment in tooling and molds. This can be a barrier for small-scale or low-volume production runs.
2. Limited design changes: Once the molds and tooling are created, it becomes difficult and costly to make design changes. This lack of flexibility can be a downside for products that may require frequent design modifications.
3. Long lead time: The initial production setup, including mold creation, can be time-consuming, resulting in relatively long lead times. This may not be suitable for projects requiring quick turnaround times.
4. Design limitations: The design of injection molded parts may have certain limitations due to factors such as part thickness, draft angles, and undercuts. These limitations need to be considered during the product design phase.
5. Material limitations: While injection molding offers a wide range of material options, certain materials, such as metals and rubber, cannot be used in the process. This can limit the choice of materials for certain applications.
In conclusion, custom injection molding offers cost-effectiveness, high production efficiency, versatility in material selection, and the ability to produce complex shapes. However, it has limitations in terms of upfront investment, limited design changes, long lead times, design and material limitations. Consideration of these pros and cons is crucial when determining whether to use custom injection molding for a specific manufacturing project.
custom injection moulding Reference Specifications (varies for different product)
Custom injection molding is a versatile manufacturing process used to produce plastic parts with intricate details and complex shapes. However, the specifications for each product may differ based on specific requirements. Here are some reference specifications commonly associated with custom injection molding:
1. Material Selection: The choice of material depends on the desired properties of the final product. Common materials used in injection molding include thermoplastics like ABS, polycarbonate, polypropylene, and nylon. The selection of material affects factors such as strength, flexibility, and heat resistance.
2. Part Design: The design of the part plays a crucial role in the success of injection molding. It includes factors like wall thickness, gate location, undercuts, and draft angles. The design should facilitate proper flow of molten plastic into the mold cavity, ensuring uniform filling and minimizing defects like warping or sink marks.
3. Mold Design: The mold is a precision tool used to shape the molten plastic into the desired part. It consists of two halves, the cavity, and the core. The mold design should consider factors such as part ejection, cooling, and venting. The mold should be durable and capable of withstanding repeated cycles of injection molding.
4. Injection Parameters: The injection process parameters control various aspects of the molding process, such as injection speed, temperature, and pressure. These parameters need to be fine-tuned for each material and part design to achieve optimum results. Improper settings can lead to issues like short shots, flash, or excess part shrinkage.
5. Quality Control: Quality control measures ensure that each molded part meets the required specifications. This involves inspecting the parts for defects such as voids, warping, or dimensional inaccuracies. Advanced techniques like statistical process control (SPC) may be employed to monitor and control process variables for consistent part quality.
6. Production Volume: The required production volume affects various aspects of the injection molding process, including mold design, tooling, and automation. Low-volume production may utilize rapid tooling techniques, while high-volume production may require more durable and long-lasting molds.
In summary, custom injection molding specifications vary depending on the product being manufactured. Material selection, part and mold design, injection parameters, quality control, and production volume all play significant roles in achieving desired results. By considering these specifications, manufacturers can produce high-quality plastic parts with precision and efficiency.
Applications of custom injection moulding
Custom injection moulding is a versatile manufacturing process that has a wide range of applications across various industries. Here are a few examples of how custom injection moulding is used:
1. Automotive Industry: Injection moulding is extensively used in the automotive industry for producing various components such as interior trim, dashboard parts, door panels, handles, and knobs. The process allows for the production of high-quality and durable parts that meet the strict requirements of the automotive industry.
2. Medical Device Manufacturing: Custom injection moulding is crucial in the manufacturing of medical devices and equipment. It is used to produce components like syringes, IV connectors, catheters, and other disposable medical supplies. The process ensures precision and consistency, helping to maintain the high standards of the medical industry.
3. Consumer Products: Injection moulding plays a vital role in the production of consumer products such as household items, electronics, toys, and packaging. It allows for the mass production of complex and detailed designs, providing cost-effective solutions for manufacturers.
4. Aerospace Industry: The aerospace industry relies on custom injection moulding for producing lightweight and high-performance components. These components include interior lighting fixtures, brackets, connectors, and various parts for aircraft engines and systems. The process helps to meet the stringent requirements of the aerospace industry, including weight reduction and high strength-to-weight ratios.
5. Electronics Industry: Injection moulding is widely used in the electronics industry to manufacture casings, enclosures, connectors, and other components. The process ensures the production of precise and intricate designs, providing functionality and protection for electronic devices.
6. Packaging Industry: Injection moulding is utilized for manufacturing plastic bottles, caps, closures, and containers used in the food and beverage, pharmaceutical, and cosmetic industries. It offers flexibility in design, allows for customization, and ensures product safety and durability.
In conclusion, custom injection moulding plays a significant role in various industries, ranging from automotive and medical device manufacturing to consumer products, aerospace, electronics, and packaging. Its versatility, precision, and efficiency make it a preferred choice for producing high-quality components and products.
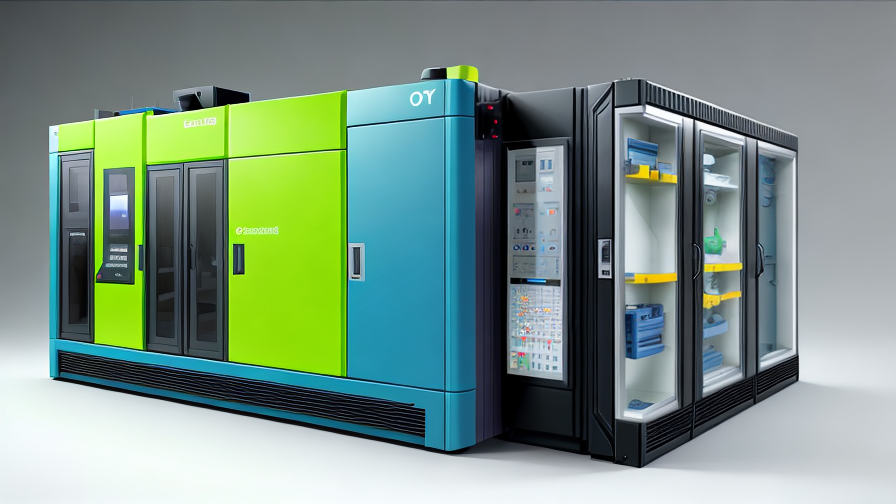
The Work Process and how to use custom injection moulding
The work process of custom injection moulding involves several steps to create plastic parts with precision and accuracy. Here is an overview of the process:
1. Design and Engineering: The process begins with the design and engineering of the desired plastic part. This includes creating CAD models and considering factors such as material selection, part geometry, and production feasibility.
2. Mold Design and Manufacturing: Once the design is finalized, a mold is designed and manufactured. The mold is typically made from steel and consists of two halves – the cavity and core – that form the shape of the part.
3. Material Selection: The appropriate thermoplastic material is selected based on the properties required for the part, such as strength, flexibility, heat resistance, etc. Factors like cost and availability also come into play.
4. Injection Moulding: The selected material is heated to a molten state and then injected into the mold under high pressure. The molten material fills the cavity, taking the shape of the part.
5. Cooling and Ejection: The molten material is allowed to cool and solidify inside the mold. Once the part has cooled down sufficiently, it is ejected from the mold using ejector pins or plates.
6. Post-Moulding Operations: The ejected part may undergo additional operations like trimming, deburring, or surface finishing to achieve the desired final product.
Custom injection moulding offers several advantages, including:
– Design Flexibility: With custom injection moulding, complex part designs can be easily produced. This process allows for intricate details, sharp corners, and thin walls that are difficult to achieve with other manufacturing methods.
– Cost Efficiency: Injection moulding is a highly efficient and repeatable process, making it cost-effective for large production runs. It also results in minimal material wastage.
– Faster Production: Injection moulding offers fast production cycles, allowing for quick turnaround times from design to finished part. This makes it ideal for industries that require rapid prototyping and production.
In conclusion, custom injection moulding involves designing and engineering the desired part, creating a mold, selecting the appropriate material, injecting the molten material into the mold, cooling, ejecting, and performing post-moulding operations. This process offers design flexibility, cost efficiency, and faster production, making it a popular choice for manufacturing plastic parts.
Quality Testing Methods for custom injection moulding and how to control the quality
Quality testing methods for custom injection moulding involve a series of checks and inspections to ensure that the manufactured products meet specified requirements. These methods serve to control the quality throughout the manufacturing process, from material selection to final product inspection.
One commonly used quality testing method is visual inspection. This involves inspecting the product’s appearance for any defects, such as surface imperfections, cracks, or deformities. Through visual inspection, manufacturers can identify and address any issues that may affect the product’s quality.
Another crucial method is dimensional inspection. This process verifies if the manufactured product meets the dimensional specifications outlined in the design. It typically involves using precision measurement tools, such as digital calipers or coordinate measuring machines, to assess critical dimensions and tolerances. By ensuring that the product meets the required dimensions, manufacturers can guarantee its functionality and compatibility with other components or parts.
To assess the product’s mechanical properties, various testing methods can be employed. These include hardness testing, which measures the material’s resistance to indentation or deformation, as well as tensile and flexural testing, which assess the product’s strength and elasticity. These tests verify if the product can withstand expected loads or forces during its intended usage.
Moreover, functional testing evaluates the product’s performance under real-world conditions. This could involve simulating the product’s intended use or subjecting it to accelerated aging or endurance tests. Functional testing can help identify issues related to product design, material selection, or manufacturing process. It ensures that the product functions as intended and meets customer expectations.
To control the quality of custom injection moulding, manufacturers should adopt a comprehensive quality management system. This system includes regular process audits, continuous employee training, and adherence to industry standards and best practices. It also encompasses traceability measures, where each product can be tracked back to its specific manufacturing process and raw material. In addition, manufacturers should establish clear quality control checkpoints throughout the production line to minimize defects and deviations.
By implementing these quality testing methods and control measures, manufacturers can ensure that their custom injection moulding processes produce high-quality products that meet customer requirements and expectations.
custom injection moulding Sample Policy and Post-Purchase Considerations for custom injection moulding from China
Sample Policy:
When engaging in custom injection moulding with a Chinese supplier, it is essential to establish a clear sample policy to ensure quality control and meet the desired specifications. The following considerations can be taken into account:
1. Sample Preparation: Provide the supplier with precise technical drawings, including dimensions, materials, and finishing requirements. Communicate your expectations clearly to avoid misunderstandings and ensure accurate sample preparation.
2. Sample Cost: Clarify whether the sample cost will be borne by the buyer or if it will be included in the overall production cost. If a considerable number of iterations are foreseen, negotiating a lower sample cost or sampling fees per iteration may be beneficial.
3. Sample Approval: Set clear criteria for sample approval to avoid confusion and unnecessary iterations. Determine factors such as product appearance, dimensions, functionality, and performance. Both parties should agree on the acceptable level of quality before proceeding to mass production.
4. Sample Revisions: Discuss the number of sample iterations included in the initial cost and clarify the cost implications for additional revisions. Clearly define the responsibilities and deadlines for each round of revisions, ensuring efficient and timely communication.
Post-Purchase Considerations:
After moving forward with a custom injection moulding order from China, several post-purchase considerations are essential to ensure a successful project:
1. Production Monitoring: Establish a system to monitor the production process. Regular communication with the supplier will help address any issues or changes required during the manufacturing process.
2. Quality Control: Implement a stringent quality control process that includes regular inspections during production. Random checks, sample testing, and third-party inspections can help identify and rectify any potential defects or deviations from the specifications.
3. Delivery Schedule: Establish clear delivery schedules and associated penalties for delays. Consistent follow-up on progress and timely communication can help ensure on-time delivery of the products.
4. Communication: Maintain open and regular communication with the supplier regarding any concerns, modifications, or updates. Promptly address any issues that may arise during the production phase.
5. Documentation: Keep a detailed record of all communications, agreements, and modifications made throughout the project. Proper documentation will serve as a reference and potential evidence in case of any disputes or quality-related concerns.
By establishing a sample policy and considering post-purchase aspects diligently, businesses can enhance their experience in custom injection moulding from China, ensuring high-quality products that meet their requirements.
Sourcing custom injection moulding from China: Opportunities, Risks, and Key Players
Custom injection molding is a widely used manufacturing process for producing complex plastic parts. China has emerged as a global leader in this industry due to its competitive pricing, vast manufacturing capabilities, and extensive experience in plastic production. Sourcing custom injection molding from China presents numerous opportunities, but also comes with inherent risks that need to be carefully managed. Additionally, there are some key players in the Chinese market worth considering.
Opportunities:
1. Cost advantages: China offers significant cost advantages compared to other countries, mainly due to lower labor costs and economies of scale.
2. Manufacturing expertise: Chinese manufacturers have accumulated vast experience in injection molding, enabling them to deliver high-quality products efficiently.
3. Vast supplier network: China has a vast network of suppliers for raw materials, molds, and auxiliary components, ensuring a seamless supply chain for injection molding projects.
4. Rapid production turnaround: China’s manufacturing capabilities allow for faster production turnaround times, enabling businesses to meet demanding deadlines.
Risks:
1. Intellectual property concerns: China’s reputation for intellectual property protection can be a concern, as some companies have faced issues with their designs being reverse-engineered or copied.
2. Quality control: It is crucial to ensure that the manufacturing partner has a comprehensive quality control system in place to maintain consistency in product quality.
3. Communication and language barriers: Language barriers and cultural differences can impact effective communication, leading to misunderstandings and delays in project execution.
4. Supply chain disruptions: China’s export-focused economy is susceptible to disruptions such as trade disputes, political instability, and natural disasters, which may impact the timely delivery of products.
Key Players:
1. Sositar Mould: Sositar is a reputable custom injection molding manufacturer, known for its expertise in producing high-quality plastic parts for various industries.
2. Xiamen Qiqiangsheng Moulds: Qiqiangsheng specializes in developing molds for custom injection molding and offers comprehensive services, from design to production.
3. Taizhou Huangyan Solidco Mould Co., Ltd.: Solidco Mould is a leading manufacturer of plastic injection molds, offering a wide range of customization options to meet diverse customer requirements.
4. Foshan Mogel Hardware and Plastic Co., Ltd.: Mogel Hardware and Plastic is a reliable supplier of custom injection molded products, ensuring high-quality production and exceptional customer service.
In conclusion, sourcing custom injection molding from China provides significant opportunities for businesses seeking cost-effective manufacturing solutions. However, it is essential to carefully assess and manage the risks associated with intellectual property, quality control, communication, and supply chain disruptions. By partnering with reputable companies like Sositar Mould, Qiqiangsheng Moulds, Solidco Mould, and Mogel Hardware and Plastic, businesses can leverage China’s manufacturing expertise to their advantage.
How to find and select reliable custom injection moulding manufacturers in China,use google search manufacturers and suppliers
When it comes to finding and selecting reliable custom injection moulding manufacturers in China, Google search can be a valuable tool. Here are some steps to help you in the process:
1. Begin by conducting a Google search using relevant keywords such as “custom injection moulding manufacturers in China” or “plastic injection moulding suppliers in China.” This will provide you with a list of potential manufacturers and suppliers.
2. Visit the websites of the listed companies to gather basic information about their capabilities, certifications, experience, and the types of products they specialize in. Look for manufacturers with a professional-looking website and comprehensive information.
3. Check if the companies have relevant certifications such as ISO 9001 or ISO 13485, which demonstrate their commitment to quality and international standards compliance.
4. Look for customer reviews or testimonials on their website or external review platforms to gain insights into their reputation and reliability. Positive reviews and ratings indicate a higher likelihood of reliability.
5. Contact the shortlisted manufacturers to ask for more details about their manufacturing processes, quality control measures, lead times, and payment terms. A responsive and transparent communication style is a good sign of reliability.
6. Request samples or prototypes to evaluate the quality of their work. This will give you a firsthand experience of their manufacturing capabilities and help you assess if they can meet your specific requirements.
7. Consider visiting the manufacturer’s facility in person if feasible. This allows you to personally observe their production processes, equipment, and overall quality control measures.
8. Ask for references from their existing clients who have had similar projects. Speaking to these references directly will give you an unbiased opinion about the manufacturer’s performance and reliability.
9. Compare the pricing, lead times, and quality among the shortlisted manufacturers. Avoid selecting a manufacturer solely based on the lowest price as it may compromise the quality and reliability.
10. Finally, make an informed decision based on the collected information, evaluations, and your specific requirements.
By following these steps, you can effectively use Google search and other resources to find and select reliable custom injection moulding manufacturers in China.
How to check custom injection moulding manufacturers website reliable,use google chrome SEOquake check if ranking in top 10M
To determine if a custom injection molding manufacturer’s website is reliable, you can follow these steps:
1. Use Google Chrome: Start by opening the manufacturer’s website in Google Chrome, as this browser provides various tools and extensions that can help assess reliability.
2. Install SEOquake Extension: SEOquake is a reliable extension for Chrome that provides valuable website statistics and insights. You can easily install it from the Chrome Web Store (it’s free).
3. Check Alexa Rank: Once SEOquake is installed, you’ll notice a new toolbar at the top of your browser. Click on the SEOquake icon, and it will display a variety of website metrics. Look for the Alexa Rank, which indicates the website’s popularity and traffic. If the manufacturer’s website has a ranking within the top 10 million, it generally signifies that it attracts a decent amount of visitors.
4. Examine Page Authority: SEOquake also provides a metric called “Page Authority” or “PA.” This statistic assesses the overall strength and credibility of a webpage. A higher PA suggests that the website has quality content, gets reliable backlinks, and is trustworthy.
5. Analyze Keyword Density: SEOquake allows you to analyze the keyword density of the custom injection molding manufacturer’s website. If the website excessively uses certain keywords or shows signs of keyword stuffing, it may indicate poor content quality or an attempt to manipulate search rankings, which could be a red flag.
6. Evaluate On-page Optimization: SEOquake presents an on-page optimization score, which reflects how well the website is optimized for search engines. A high score indicates that the website follows best practices and is likely to provide reliable information.
7. Verify Backlinks: SEOquake provides a quick overview of a website’s backlink profile. While this won’t directly determine reliability, it gives an idea of the website’s link building efforts or potential partnerships with reputable sources.
In conclusion, using Google Chrome and SEOquake to check if a custom injection molding manufacturer’s website is reliable can provide valuable insights into its overall credibility.
Top 10 custom injection moulding manufacturers in China with each 160 words introduce products,then use markdown create table compare
1. Richfields Corporation Limited: With over 20 years of experience, Richfields is a leading custom injection moulding manufacturer in China. They offer a wide range of plastic parts and components for various industries such as automotive, electronics, and medical devices. Their products include precision moulded parts, injection moulded enclosures, and plastic injection moulds. Richfields is known for their advanced manufacturing capabilities, strict quality control, and competitive pricing.
2. ACO Mold: ACO Mold specializes in producing high-quality moulds and plastic injection moulded products. They have a diverse product range, including automotive parts, consumer electronics, and industrial components. ACO Mold prides themselves on their advanced technology, efficient production processes, and excellent customer service.
3. Feman Tooling (China) Limited: Feman Tooling is a prominent custom injection moulding manufacturer based in China. They provide a wide range of injection moulding solutions, including plastic gears, electronic components, and medical devices. Feman Tooling is renowned for their expertise in mould designing, precise mould making, and reliable production.
4. HQMOULD: HQMOULD specializes in producing high-precision injection moulds and plastic components. They offer customized solutions for industries like automotive, electronics, and packaging. HQMOULD is known for their commitment to quality, advanced manufacturing techniques, and fast delivery.
5. Sositar Mould: Sositar Mould is a leading injection moulding manufacturer in China. They offer comprehensive mould design, manufacturing, and injection moulding services. Their product range includes automotive parts, home appliances, and industrial components. Sositar Mould focuses on customer satisfaction, consistent quality, and efficient production.
6. SunOn Industrial Group Limited: SunOn Industrial Group is a trusted injection moulding manufacturer with a wide range of plastic products for industries like automotive, electronics, and healthcare. Their offerings include precision moulded parts, injection moulded enclosures, and custom plastic components. SunOn Industrial Group emphasizes innovation, quality control, and cost-effective solutions.
7. Taizhou Huangyan Jmt Mould Co., Ltd: JMT Mould is a renowned manufacturer specializing in mould designing, manufacturing, and injection moulding. They provide custom solutions for industries like automotive, household appliances, and consumer electronics. JMT Mould is known for their advanced machinery, skilled workforce, and competitive pricing.
8. LK-Mould: LK-Mould specializes in plastic injection moulding and provides comprehensive services from design to production. They produce a wide range of plastic products, including automotive parts, medical devices, and consumer electronics. LK-Mould emphasizes precision engineering, reliability, and on-time delivery.
9. Shine Brother Mould & Plastic Products Co., Ltd: Shine Brother Mould offers custom injection moulding services for various industries, including automotive, electronics, and packaging. They are known for their expertise in precision mould making and manufacturing of high-quality plastic parts. Shine Brother Mould focuses on customer satisfaction, technical excellence, and cost-effective solutions.
10. Xiamen Karo Industry & Trade Co., Ltd: Xiamen Karo Industry & Trade is a leading custom injection moulding manufacturer in China. They offer a wide range of plastic products, including automotive parts, electronic components, and industrial supplies. Xiamen Karo Industry & Trade is renowned for their advanced moulding techniques, strict quality control, and excellent customer service.
| Manufacturer | Specializations | Advantages |
|————————————-|———————————|——————————————|
| Richfields Corporation Limited | Precision moulded parts | Advanced manufacturing, competitive pricing |
| ACO Mold | Automotive parts | High-quality moulds, efficient production processes |
| Feman Tooling (China) Limited | Electronic components | Expertise in mould designing, precise mould making |
| HQMOULD | Industrial components | High-precision moulds, advanced manufacturing techniques |
| Sositar Mould | Home appliances | Comprehensive mould design, efficient production |
| SunOn Industrial Group Limited | Injection moulded enclosures | Innovation, quality control, cost-effective solutions |
| Taizhou Huangyan Jmt Mould Co., Ltd | Household appliances | Advanced machinery, skilled workforce, competitive pricing |
| LK-Mould | Medical devices | Precision engineering, reliability, on-time delivery |
| Shine Brother Mould | Packaging | Expertise in precision mould making, customer satisfaction |
| Xiamen Karo Industry & Trade Co., Ltd | Electronic components, industrial supplies | Advanced moulding techniques, excellent customer service |
The table above compares the top 10 custom injection moulding manufacturers in China based on their specializations and advantages. These manufacturers offer a wide range of products for industries like automotive, electronics, and packaging. They differentiate themselves through their advanced manufacturing capabilities, competitive pricing, and commitment to quality and customer satisfaction.
Background Research for custom injection moulding manufacturers Companies in China, use qcc.com archive.org importyeti.com
When looking for custom injection molding manufacturers in China, several websites can provide valuable information. Three such platforms include qcc.com, archive.org, and importyeti.com. These websites offer insights into the background and capabilities of different manufacturers, helping businesses make informed decisions.
Qcc.com is an online business information portal that provides comprehensive company data in China. It allows users to search for specific manufacturers and obtain details such as company profiles, registration information, and historical records. By utilizing this platform, businesses can verify the authenticity and credibility of potential custom injection molding manufacturers in China.
Archive.org, commonly known as the Wayback Machine, is a digital archive of the World Wide Web. It allows users to access and explore historical versions of websites. This can be particularly useful in evaluating the track record and online presence of custom injection molding manufacturers in China. By reviewing archived versions of manufacturer websites, businesses can gain insights into their past performance, product range, and industry experience.
Importyeti.com is an import and export data platform that provides information on shipments made by companies worldwide. It allows users to search for specific manufacturers and gain access to essential import/export data, including shipment details, shipping partners, and product descriptions. By utilizing this platform, businesses can assess the export activities and market reach of potential custom injection molding manufacturers in China.
Overall, these websites can be valuable tools for conducting background research on custom injection molding manufacturers in China. By utilizing qcc.com, archive.org, and importyeti.com, businesses can gather crucial information about a manufacturer’s credibility, past performance, online presence, and market reach, helping them make informed decisions when choosing a partner for their injection molding needs.
Leveraging Trade Shows and Expos for custom injection moulding Sourcing in China
Trade shows and expos are excellent platforms for sourcing custom injection moulding services in China. These events provide an opportunity for businesses to connect with manufacturers, evaluate their capabilities, and establish valuable relationships.
China, being a major manufacturing hub, hosts numerous trade shows and expos related to injection moulding throughout the year. These events attract a wide range of suppliers, showcasing their equipment, technologies, and solutions. By attending these shows, businesses can access a pool of potential suppliers without the need for extensive travel or language barriers.
Trade shows and expos provide a comprehensive overview of the injection moulding industry in China. They offer a chance to witness the latest advancements in technology, industry trends, and innovative solutions. This information is valuable in assessing manufacturers’ capabilities and determining their suitability for specific custom injection moulding needs.
Moreover, these events provide an opportunity for face-to-face interactions with potential suppliers. Networking with industry professionals and manufacturers allows businesses to establish personal connections and gain insights into their reliability, quality control practices, and overall manufacturing process. This is crucial for building trust and confidence in the chosen supplier.
Trade shows and expos also facilitate the comparison of different suppliers under one roof. Businesses can evaluate multiple manufacturers’ offerings, processes, and pricing structures in a short period. This allows for efficient decision-making and the selection of the most suitable supplier for their custom injection moulding requirements.
To make the most of trade shows and expos, businesses should prepare in advance. This includes researching participating exhibitors, their specialties, and offerings. Setting specific objectives and questions to ask potential suppliers will help streamline the sourcing process. It is also essential to collect and organize relevant information from each supplier met at the event to facilitate later evaluation and comparison.
In conclusion, leveraging trade shows and expos for custom injection moulding sourcing in China provides businesses with a unique opportunity to connect with numerous suppliers, evaluate their capabilities, and establish valuable relationships. These events offer a comprehensive overview of the industry, facilitate face-to-face interactions, and allow for efficient supplier comparison. By taking advantage of these platforms, businesses can successfully source custom injection moulding services from China.
The Role of Agents and Sourcing Companies in Facilitating custom injection moulding Purchases from China
Agents and sourcing companies play a vital role in facilitating custom injection molding purchases from China. China has become the global manufacturing hub for custom injection molding due to its cost-effective production capabilities and vast industrial infrastructure. However, navigating the Chinese market and finding reliable suppliers can be challenging for foreign companies. This is where agents and sourcing companies come in.
Agents are individuals or firms who act as intermediaries between the buyer and the supplier. They have extensive knowledge of the Chinese market, including the local regulations, customs, and business practices. Agents help foreign buyers find reputable suppliers, negotiate prices, facilitate communication, and oversee the production process. They act as a bridge between the buyer and the supplier, ensuring smooth transactions and minimizing risks.
Sourcing companies, on the other hand, specialize in connecting buyers with Chinese manufacturers. They have a wide network of suppliers and can identify the most suitable ones for a specific project. Sourcing companies provide comprehensive sourcing services, including supplier qualification, sample development, quality control, and logistics management. They can also assist in verifying supplier credentials, conducting factory audits, and ensuring compliance with international standards.
By leveraging the expertise of agents and sourcing companies, foreign buyers can minimize the risks typically associated with sourcing from China. These professionals have a deep understanding of the Chinese market dynamics and can help buyers identify reliable suppliers with proven track records. They also help buyers negotiate competitive prices, navigate cultural and language barriers, and manage logistics, ensuring timely delivery of products.
Moreover, agents and sourcing companies play a crucial role in quality control. They can conduct inspections, monitor production processes, and enforce quality standards to ensure the desired quality of the injection-molded products is achieved. This helps buyers reduce the risks of receiving defective or subpar products.
In conclusion, agents and sourcing companies are instrumental in facilitating custom injection molding purchases from China. Their knowledge, expertise, and extensive networks enable foreign buyers to navigate the complexities of the Chinese market, find reliable suppliers, ensure quality control, and secure cost-effective production. Their role in the sourcing process is crucial for foreign companies seeking custom injection molding services in China.
Price Cost Research for custom injection moulding manufacturers Companies in China, use temu.com and 1688.com
When looking for custom injection moulding manufacturers in China, two reliable platforms to consider are temu.com and 1688.com. These platforms provide comprehensive information about manufacturers, allowing you to conduct price cost research effectively.
Temu.com is a trusted online platform that connects businesses with manufacturers in China. With a user-friendly interface, it offers a wide range of manufacturers specializing in injection moulding. You can browse through their extensive directory, filter by location, production capacity, and certification to find the most suitable manufacturers for your custom moulding needs. The platform also provides valuable information such as the number of employees, annual revenue, and years of operation, helping you assess the manufacturer’s credibility.
Another popular platform for sourcing manufacturers in China is 1688.com. This website is similar to Alibaba and is primarily used by domestic Chinese sellers. However, it is accessible to international buyers who can benefit from its vast network of injection moulding manufacturers. By using the search bar and applying filters, you can specify your requirements and narrow down the list of potential manufacturers. 1688.com also offers direct communication with suppliers, enabling you to ask for quotations and negotiate prices.
When conducting price cost research on both platforms, it is essential to compare different manufacturers and request quotations from multiple suppliers. Factors such as product complexity, material requirements, production volume, and quality standards can influence the overall cost. By clearly communicating your specifications and expectations, you can obtain accurate pricing information and make informed decisions. Additionally, remember to factor in shipping costs, lead time, and the manufacturer’s payment terms to have a comprehensive understanding of the total cost.
In summary, temu.com and 1688.com are reliable platforms for conducting price cost research when searching for custom injection moulding manufacturers in China. Make use of the comprehensive information provided on these platforms and compare multiple manufacturers to ensure you find the best supplier for your specific needs.
Shipping Cost for custom injection moulding import from China
When importing custom injection moulding from China, the shipping cost can vary depending on several factors. These include the size and weight of the products, the mode of transportation, and the distance between the manufacturing site in China and the destination country.
Typically, there are two main modes of transportation for shipping from China: air freight and sea freight. Air freight is generally faster but more expensive, while sea freight takes longer but offers a more cost-effective solution for larger shipments.
For small orders, air freight is often the preferred choice. The shipping cost is calculated based on the volumetric weight of the package, which is determined by the length, width, and height of the shipment. Additionally, air freight charges may include fees for customs clearance and handling.
Alternatively, for larger orders, sea freight is recommended to reduce shipping costs. Similar to air freight, the charges are determined by the volume or weight of the cargo. Additional expenses may include customs duties, taxes, and port handling fees. It is advisable to consult with a freight forwarder or logistics company to get accurate quotes and assistance with the shipping process.
To estimate the shipping cost, it is essential to have detailed information about the products, such as the dimensions, weight, and quantity. This will help calculate the volume or weight, which will then be used to obtain accurate shipping rates.
Importing custom injection moulding from China can be a cost-effective solution for businesses. However, it is important to consider not only the shipping cost but also other factors like production quality, lead time, and potential customs and import regulations. Working with a reliable supplier and experienced logistics partner is crucial to ensure a smooth and cost-efficient import process.
Compare China and Other custom injection moulding Markets: Products Quality and Price,Visible and Hidden Costs
China is widely recognized as one of the largest and most competitive custom injection molding markets in the world. When comparing China with other custom injection molding markets, several factors need to be considered, including product quality and price, as well as visible and hidden costs.
In terms of product quality, China has made significant improvements over the years and now offers comparable quality to other global markets. Chinese manufacturers have adopted advanced technologies and quality control measures to ensure precise and consistent molding results. However, it is important to note that quality can vary among different Chinese manufacturers, so careful evaluation and monitoring of the manufacturing process is crucial to maintain consistent quality.
Regarding price, China’s lower labor and production costs provide a competitive advantage over other markets. The abundance of skilled labor and materials, coupled with efficient production processes, allow Chinese manufacturers to offer more cost-effective solutions. This has attracted many multinational companies to outsource their injection molding projects to China.
Visible costs, such as production and transportation expenses, in China are generally lower compared to other markets. Chinese manufacturers often have large-scale facilities and well-established logistics networks, enabling them to produce and deliver products more efficiently. This results in savings for customers in terms of transportation costs and economies of scale.
However, hidden costs can also arise when dealing with the Chinese market. For example, communication challenges and language barriers can lead to misunderstandings and delays. Intellectual property protection can also be a concern, as some Chinese manufacturers may not uphold stringent measures to safeguard designs and technologies. Extensive due diligence and legal protection are necessary to mitigate these risks.
In summary, China’s custom injection molding market offers competitive product quality and pricing. While quality has improved significantly, variability among manufacturers necessitates careful monitoring. The lower labor and production costs in China provide a cost advantage, with visible cost savings in areas such as production and transportation. However, customers should consider potential hidden costs such as communication challenges and intellectual property protection. By doing so, they can effectively compare China with other custom injection molding markets and make informed decisions for their specific needs.
Understanding Pricing and Payment Terms for custom injection moulding: A Comparative Guide to Get the Best Deal
Pricing and payment terms are crucial factors to consider when engaging in custom injection moulding projects. Understanding these aspects thoroughly ensures that you get the best deal while avoiding any potential issues or misunderstandings. This comparative guide aims to provide a concise overview of essential points to consider, limited to 300 words.
When it comes to pricing, the cost of custom injection moulding is typically determined by various factors such as the complexity of the part, the material used, the required volume, and the manufacturing process. It’s important to obtain detailed quotes from multiple suppliers to compare prices effectively.
To assess the pricing structure, consider the production cost breakdown provided by the suppliers. This breakdown should reflect the costs associated with tooling, material, labor, overheads, and profit margin. Evaluating these cost components will help you determine if a supplier offers a fair and competitive price.
Additionally, understanding the payment terms is crucial for budgeting and financial planning. Custom injection moulding suppliers often require an initial payment to cover tooling costs or a down payment before production begins. Some suppliers may require milestone payments, where funds are released at specific stages of the project. Be sure to clarify payment terms to prevent any surprises or delays.
Exploring payment methods is also essential. Common options include wire transfers, credit cards, and letters of credit. It’s crucial to determine the most convenient and secure payment method for your business. Additionally, inquire about any potential discounts for larger orders or long-term partnerships.
Maintain clear communication with your supplier regarding payment due dates and invoicing procedures. Establishing a solid understanding of the payment schedule prevents misunderstandings and ensures a smooth transaction process.
Lastly, don’t solely focus on the price but consider the overall value provided. Evaluate factors such as the supplier’s experience, quality control processes, lead times, and customer service. Considering these aspects in conjunction with pricing will help you make an informed decision and secure the best deal for your custom injection moulding needs.
In conclusion, when navigating the world of custom injection moulding pricing and payment terms, obtaining detailed quotes, assessing the production cost breakdowns, clarifying payment terms, exploring payment methods, maintaining clear communication, and evaluating value are all crucial steps towards securing the most favorable deal.
Chinese Regulations and Industry Standards Certifications for custom injection moulding,Import Regulations and Customs for custom injection moulding from China
Custom injection moulding is a popular manufacturing process in the Chinese market, and it is essential for businesses to understand the Chinese regulations, industry standards certifications, import regulations, and customs procedures associated with it.
Chinese Regulations and Industry Standards Certifications for custom injection moulding:
In China, the custom injection moulding industry is regulated by several government bodies, such as the National Development and Reform Commission (NDRC), the Ministry of Commerce (MOFCOM), and the General Administration of Quality Supervision, Inspection, and Quarantine (AQSIQ). These organizations ensure compliance with the relevant regulations, safety standards, and environmental protection requirements.
Certifications play a vital role in the custom injection moulding industry in China. The most commonly required certifications include the ISO 9001:2015 quality management system certification, ISO 14001:2015 environmental management system certification, and ISO 13485:2016 medical device quality management system certification. These certifications ensure that the manufacturing process adheres to strict quality standards, environmental regulations, and safety measures.
Import Regulations and Customs procedures for custom injection moulding from China:
When importing custom injection moulding products from China, businesses need to adhere to the import regulations and customs procedures. The first step is to identify the Harmonized System (HS) code for the specific product. This code determines the applicable customs duties and import taxes.
Companies are required to provide necessary documentation, including a commercial invoice, packing list, bill of lading or airway bill, and import declaration form. Additionally, certain products may require special permits or licenses.
Customs procedures are carried out by the General Administration of Customs (GAC) in China. Imported goods are subject to customs inspections to ensure compliance with regulations and are cleared through customs based on the provided documentation.
In conclusion, understanding Chinese regulations and industry standards certifications for custom injection moulding, as well as import regulations and customs procedures, is crucial for businesses planning to import such products from China. Compliance with these regulations and certifications ensures quality manufacturing processes and smooth customs clearance, facilitating a successful importation process.
Sustainability and Environmental Considerations in custom injection moulding Manufacturing
Custom injection molding manufacturing plays a crucial role in the production of various consumer goods, automotive components, and medical devices. However, it is essential to consider sustainability and environmental factors in this manufacturing process. Here, we will discuss some key considerations in custom injection molding that can contribute to sustainability.
Firstly, the choice of raw materials can significantly impact sustainability. Opting for materials with a lower carbon footprint, such as biodegradable or recycled plastics, can reduce environmental impact. Additionally, selecting materials that are lighter in weight can decrease energy consumption during production and transportation.
Energy efficiency is another critical aspect of sustainable custom injection molding. Implementing energy-efficient machinery, optimizing the production process, and utilizing automation technologies can reduce energy consumption and greenhouse gas emissions. By adopting greener energy sources like solar or wind power, manufacturers can further minimize their carbon footprint.
Reducing waste generation is essential for both sustainability and cost-effectiveness. Implementing lean manufacturing techniques like just-in-time production and process optimization can minimize material waste. Furthermore, proper waste management practices such as recycling and reusing materials can mitigate environmental impact and conserve resources.
Water conservation is yet another important consideration. By implementing water-saving measures such as closed-loop cooling systems and efficient water management strategies, manufacturers can minimize water usage and ensure responsible water stewardship.
In addition to these considerations, manufacturers should prioritize safe and eco-friendly manufacturing practices. This includes using non-toxic and environmentally friendly additives, reducing emissions of volatile organic compounds (VOCs), and complying with relevant environmental regulations and certifications.
Lastly, collaboration and communication throughout the supply chain are key to achieving sustainability goals. Working closely with suppliers and customers to promote sustainable practices, sharing best practices, and encouraging responsible product life cycle management can further enhance environmental sustainability in custom injection molding manufacturing.
In conclusion, sustainability and environmental considerations in custom injection molding manufacturing are vital for minimizing environmental impact, conserving resources, and meeting the growing demand for eco-friendly products. By focusing on raw material choices, energy efficiency, waste reduction, water conservation, safe manufacturing practices, and supply chain collaboration, manufacturers can enhance sustainability in this critical manufacturing process.
List The Evolution history of “custom injection moulding”
Custom injection molding is a manufacturing process that involves creating custom-designed plastic parts by injecting molten material into a mold cavity. It has evolved over the years in response to advancements in materials, technology, and industry demands.
The history of custom injection molding can be traced back to the late 19th century when Alexander Parkes developed the first plastic material called celluloid. However, it wasn’t until the 1940s when James Watson Hendry improved and patented the first injection molding machine. This invention revolutionized the industry by enabling mass production of plastic parts.
In the early years, custom injection molding was limited to simple shapes and small-scale production. However, with the advent of new materials such as polypropylene and polystyrene in the 1950s and 1960s, the possibilities for more complex and precise molding designs expanded. This led to the introduction of multi-cavity molds and the ability to produce larger quantities of parts at a faster rate.
Throughout the 1970s and 1980s, computer-aided design (CAD) and computer-aided manufacturing (CAM) technologies were incorporated into the process. This allowed for more precise designs and improved productivity. Another pivotal development during this period was the use of robotics and automation to streamline the injection molding process, reducing labor costs and increasing efficiency.
In the 1990s, the custom injection molding industry greatly benefited from advancements in material science. High-performance polymers like polycarbonate and polyethylene offered enhanced strength, heat resistance, and durability. Additionally, the introduction of gas-assisted injection molding further expanded the design possibilities by allowing for hollow parts and reducing material usage.
In recent years, sustainability and environmental concerns have influenced the evolution of custom injection molding. The industry has been exploring bio-based and biodegradable materials, as well as recycling and reducing waste. Additionally, advancements in additive manufacturing technologies, such as 3D printing, have opened up new possibilities for rapid prototyping and smaller-scale production.
Today, custom injection molding continues to evolve, driven by emerging technologies like artificial intelligence, Internet of Things (IoT), and machine learning. The ability to create highly complex and intricate designs, coupled with efficient and cost-effective production methods, has made custom injection molding an integral part of many industries, including automotive, healthcare, consumer products, and electronics.
The Evolution and Market Trends in custom injection moulding Industry
The custom injection moulding industry has witnessed significant evolution and market trends over the years, fueled by technological advancements and changing consumer demands. This industry involves the production of customized plastic parts through the injection moulding process, which provides manufacturers with a cost-effective and efficient solution for mass production.
One of the key trends in the custom injection moulding industry is the increasing demand for complex and intricate designs. Traditional manufacturing methods often struggle to produce such designs, but injection moulding allows for precise replication of intricate details, reducing manual labor and ensuring consistent quality. This trend has been driven by various sectors such as automotive, healthcare, and consumer electronics, which require sophisticated and aesthetic parts.
Another notable trend is the growing importance of sustainability in the industry. The rising awareness about environmental concerns has prompted manufacturers to seek more sustainable alternatives in their operations. This has led to the development of bio-based and recycled plastic materials that can be utilized in injection moulding processes. Additionally, energy-efficient machines and processes have gained prominence, reducing waste and minimizing carbon footprint.
Furthermore, the custom injection moulding industry has experienced a shift towards automation and digitalization. The integration of robotics and automation in production lines enhances efficiency, consistency, and reduces human error. Moreover, advancements in digital technologies have enabled manufacturers to create virtual models of the mould designs, facilitating faster design iterations and reducing time-to-market.
In terms of market trends, there has been a surge in outsourcing custom injection moulding services to low-cost regions, such as Asia and Eastern Europe. This shift is driven by the cost advantages offered by these regions, including cheaper labor and production costs. However, manufacturers are also focusing on building strong partnerships and collaborations with local suppliers to ensure quality and timely delivery.
Overall, the custom injection moulding industry is witnessing continuous evolution and adaptation to meet the changing demands of various industries. The trends towards intricate designs, sustainability, automation, and outsourcing are likely to shape the future of this industry. Manufacturers who embrace these trends and invest in advanced technologies will be well-positioned to thrive in the evolving marketplace.
Custom Private Labeling and Branding Opportunities with Chinese custom injection moulding Manufacturers
Chinese custom injection molding manufacturers offer lucrative opportunities for custom private labeling and branding. With their expertise and advanced technologies, these manufacturers can help businesses create distinctive products and establish a unique brand identity.
Custom private labeling allows businesses to customize their products with their own branding elements such as logos, colors, and packaging. Chinese manufacturers understand the significance of branding in today’s competitive market, and they are equipped with the necessary capabilities to meet these demands.
By partnering with Chinese custom injection molding manufacturers, businesses can benefit from their vast range of molding techniques, including injection molding, blow molding, and compression molding. These manufacturers have extensive experience in creating complex and intricate designs, ensuring the production of high-quality customized products.
Furthermore, Chinese manufacturers offer competitive pricing and shorter lead times, making them an attractive option for businesses looking to cut costs and launch products quickly. They have efficient production processes and economies of scale, enabling them to offer cost-effective options without compromising on quality.
Chinese manufacturers also provide comprehensive services, including product design and development, prototype production, and quality control. They have skilled engineers and designers who collaborate with businesses to turn their ideas into reality. This collaboration ensures that the final product meets all specifications and requirements.
In addition, Chinese custom injection molding manufacturers are experienced in working with a wide variety of materials, ranging from plastics to metals. This versatility allows businesses to select the most suitable material for their product, considering factors such as durability, aesthetics, and functionality.
Overall, partnering with Chinese custom injection molding manufacturers presents businesses with a range of opportunities for custom private labeling and branding. By leveraging their manufacturing capabilities, businesses can create unique products that resonate with their target audience and establish a strong brand presence in the market.
Tips for Procurement and Considerations when Purchasing custom injection moulding
When considering custom injection molding for procurement, it is essential to keep a few key tips and considerations in mind. These can help ensure a successful and cost-effective purchase:
1. Define your requirements: Clearly outline your needs and specifications for the desired custom injection molding project. This includes factors such as the desired material, part dimensions, quantity of parts required, and any specific design features. Defining these requirements in detail will help procurement professionals communicate effectively with suppliers.
2. Evaluate supplier capabilities: Look for suppliers with experience in custom injection molding and a proven track record of delivering quality products. Consider their capabilities, such as available machinery, production capacity, and any additional services they can provide, such as tooling or design assistance.
3. Quality control measures: Ensure the supplier has robust quality control processes in place. Ask for certifications and check if they adhere to industry standards, such as ISO 9001. Request samples or prototypes to evaluate the supplier’s ability to meet your quality requirements.
4. Cost-efficiency: Seek competitive pricing and consider the overall value offered by different suppliers. Compare quotes from multiple suppliers and ask for a breakdown of costs to understand what factors contribute to pricing differences. Be cautious of unusually low prices, as they may indicate compromised quality or hidden charges.
5. Communication and project management: Effective communication and project management are crucial for successful procurement. Clearly communicate your expectations, timelines, and any specific milestones. Ensure the supplier has a dedicated project manager who can address any concerns or provide regular updates on the progress of the project.
6. Intellectual property protection: If your custom injection molding project involves proprietary designs or intellectual property, it’s vital to have proper agreements and safeguards in place. Ensure the supplier respects your confidentiality and has protocols to protect sensitive information.
7. Environmental considerations: Consider the environmental impact of the custom injection molding process. Inquire about the supplier’s sustainability practices, such as recycling or waste management initiatives.
8. Long-term partnerships: Building strong relationships with reliable suppliers is beneficial for future procurements. Consider the supplier’s willingness to collaborate, provide ongoing support, and their ability to meet your changing needs over time.
By following these tips and considering the essential factors while procuring custom injection molding, you can make informed decisions and ensure a successful and satisfactory outcome.
FAQs on Sourcing and Manufacturing custom injection moulding in China
Q: What is custom injection moulding?
A: Custom injection moulding is a manufacturing process in which molten plastic is injected into a mould cavity. The plastic then cools and solidifies, resulting in the desired shape or part.
Q: Why choose China for custom injection moulding?
A: China is a popular choice for custom injection moulding due to its lower labour and manufacturing costs compared to Western countries. China has a well-established manufacturing industry with a vast network of suppliers and skilled workforce.
Q: How to source custom injection moulding manufacturers in China?
A: There are several ways to source manufacturers in China, including online platforms like Alibaba and Global Sources, trade shows and exhibitions, referrals from industry contacts, and engaging with sourcing agents or consultants.
Q: What should I consider when selecting a manufacturer in China?
A: When selecting a manufacturer, consider factors such as their experience and expertise, production capabilities, quality control measures, certifications, ability to communicate effectively in English, and their reputation in the industry.
Q: How to ensure the quality of custom injection moulding from China?
A: To ensure quality, conduct thorough research on potential manufacturers, request samples and visit their facilities if possible. Implement quality control measures such as inspections during the manufacturing process and pre-shipment inspections. It is also recommended to have a written agreement specifying quality standards, production timeline, and other important details.
Q: What are the potential challenges when manufacturing in China?
A: Potential challenges include language and cultural barriers, intellectual property protection, supply chain issues, and the distance involved in managing production remotely. It is important to address these challenges through effective communication, legal protections, and proactive supply chain management.
Q: What are the advantages of manufacturing in China?
A: Advantages of manufacturing in China include lower production costs, vast supplier network, access to skilled labor, scalable production capabilities, and a competitive market. Chinese manufacturers often offer a wide range of services and can accommodate custom requirements.
Q: Can I import custom injection moulded parts from China?
A: Yes, it is possible to import custom injection moulded parts from China. It is important to comply with import regulations, including customs duties and any necessary certifications or documentation required by your country.
In summary, custom injection moulding is a manufacturing process where molten plastic is injected into a mould cavity. China is a popular choice for sourcing custom injection moulding due to its lower costs and well-established industry. To ensure quality, thorough research and quality control measures are necessary. Challenges may arise, but advantages include lower costs and a wide range of manufacturing capabilities. Importing custom injection moulded parts from China is possible with compliance to import regulations.
Why contact sourcifychina.com get free quota from reliable custom injection moulding suppliers?
Sourcifychina.com offers free quotas from reliable custom injection molding suppliers for several reasons. Firstly, they aim to facilitate the sourcing process for businesses by providing them with access to a wide network of trusted suppliers. By offering free quotas, Sourcifychina.com allows businesses to obtain initial cost estimates without any financial commitment.
Secondly, the platform strives to ensure the quality and reliability of the injection molding suppliers it works with. By conducting a rigorous screening process, Sourcifychina.com selects only trusted and experienced suppliers to be part of its network. The free quota enables businesses to assess the expertise and capabilities of these suppliers before making any commitments.
Furthermore, providing free quotas promotes transparency within the sourcing process. Businesses can compare multiple quotes from different suppliers, allowing them to make informed decisions based on cost, quality, and delivery time. This transparency helps establish trust between the buyers and suppliers and ensures that businesses can make the most cost-effective choices.
Offering free quotes also aligns with Sourcifychina.com’s mission to support small and medium-sized businesses. By eliminating the financial barrier of obtaining quotes, Sourcifychina.com enables businesses of all sizes to access the benefits of custom injection molding without the need for a significant upfront investment.
In summary, Sourcifychina.com provides free quotas from reliable custom injection molding suppliers to simplify the sourcing process, ensure supplier quality, promote transparency, and support businesses of all sizes. By removing financial barriers, the platform facilitates the connection between buyers and suppliers, enabling businesses to make informed decisions and obtain cost-effective solutions.