Introduce about custom plastic injection molding guide,Qulity,Cost,Supplier,Certification,Market,Tips,FAQ
Custom plastic injection molding is a versatile manufacturing process that uses thermoplastic materials to create a wide range of plastic products. This guide aims to provide an overview of the key aspects associated with custom plastic injection molding.
Quality is of utmost importance in plastic injection molding. To ensure high-quality products, it is crucial to work with an experienced and reputable manufacturer. Look for suppliers with a proven track record in delivering consistent and reliable results. The use of high-quality molds and rigorous quality control measures also contribute to the overall quality of the final product.
Cost considerations play a vital role in custom plastic injection molding. Factors such as material selection, mold design, production volume, and complexity affect the manufacturing cost. It is advisable to conduct a cost analysis before initiating a project to optimize expenses and maximize value.
Finding the right supplier is crucial for a successful plastic injection molding project. Consider factors such as expertise, experience, manufacturing capabilities, and customer reviews before choosing a supplier. A reliable supplier will provide valuable guidance throughout the process and ensure timely delivery of the finished products.
Certifications play a vital role in ensuring the credibility and reliability of suppliers. Look for suppliers with certifications such as ISO 9001, which demonstrates their commitment to quality management standards. Additionally, certifications like ISO 13485 are essential for medical device manufacturing.
The market for custom plastic injection molding is vast and diverse. It caters to various industries, including automotive, aerospace, electronics, medical, and consumer goods. Understanding the market dynamics and specific requirements of the industry is essential for successful product development and market penetration.
Tips for a successful plastic injection molding project include thoroughly defining project requirements, collaborating closely with the supplier, conducting prototyping and testing, and focusing on design for manufacturability. Communication and feedback loops with the supplier are critical to achieve desired outcomes.
Frequently asked questions (FAQ) about plastic injection molding cover topics such as material selection, design considerations, tooling, production timelines, and costs. These FAQs provide valuable insights for both newcomers and experienced professionals in the injection molding field.
In conclusion, custom plastic injection molding offers a flexible and efficient manufacturing solution for a wide range of plastic products. By prioritizing quality, optimizing costs, selecting the right supplier, obtaining certifications, understanding the market, following tips for success, and referring to FAQs, one can ensure a successful plastic injection molding project.
Types of custom plastic injection molding
Custom plastic injection molding is a process in which plastic materials are melted and injected into a mold to create various products and components. This versatile manufacturing technique offers numerous advantages such as high production output, precision, design flexibility, and cost-effectiveness. Here are some of the most common types of custom plastic injection molding:
1. Prototyping: Prototyping is the initial stage of custom plastic injection molding. It allows manufacturers to create a sample or prototype of the desired product before mass production. This helps in evaluating the design, functionality, and appearance of the product, allowing for any necessary modifications.
2. High-Volume Production Molding: This type of injection molding is used for large-scale production of plastic components. It involves the use of highly efficient machines capable of producing a high volume of parts with precision and consistency. The process is suitable for industries such as automotive, consumer electronics, and appliance manufacturing.
3. Low-Volume Production Molding: Low-volume production molding is ideal for manufacturing small quantities of plastic parts. This method is typically used for customized or niche products that may not require mass production. It offers cost-effective solutions with shorter lead times, making it suitable for small businesses and startups.
4. Insert Molding: In insert molding, plastic materials are injected around pre-inserted metal or plastic components. This process combines multiple materials into a single part, resulting in enhanced functionality and reduced assembly costs. It is commonly used in the production of electrical connectors, threaded fasteners, and surgical instruments.
5. Overmolding: Overmolding involves molding one material over another to create a composite product. It provides improved aesthetics, better grip, and enhanced comfort. Overmolding is commonly used in the production of toothbrush handles, medical devices, and hand tools.
6. Two-Shot Molding: Two-shot molding, also known as dual-shot or multi-shot molding, involves injecting two or more different materials into a single mold in a sequential or simultaneous manner. This method allows for the production of complex parts with multiple colors, materials, or textures. Two-shot molding is commonly used in automotive interiors, consumer products, and electronics.
These are just a few examples of the various types of custom plastic injection molding available. Manufacturers can choose the most suitable method based on their specific requirements, desired product characteristics, and production volume. Custom plastic injection molding is a widely adopted manufacturing process that enables the production of a broad range of plastic components for different industries.
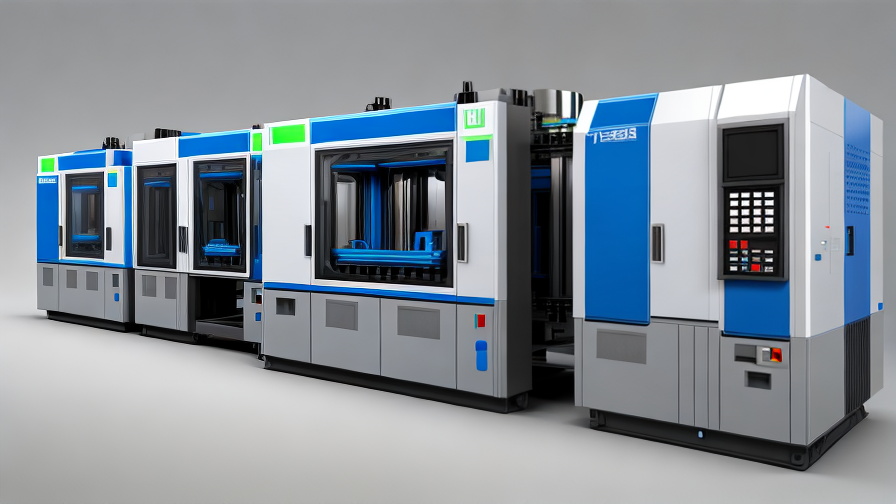
Pros and Cons of Using custom plastic injection molding
Custom plastic injection molding refers to the process of manufacturing plastic products by injecting molten plastic into a mold. This method offers several advantages and disadvantages, which are outlined below.
Pros:
1. Design flexibility: Custom plastic injection molding allows for intricate and complex designs that are difficult or impossible to achieve with other manufacturing processes. This flexibility gives manufacturers the freedom to create unique and customized plastic products.
2. Cost-effective for large production runs: Once the initial mold is created, producing large quantities of plastic parts becomes cost-effective. The high production output and fast cycle times of plastic injection molding make it an efficient option for large-scale manufacturing.
3. High accuracy and repeatability: The precision and accuracy of custom plastic injection molding results in high-quality finished products. The process enables consistent and repeatable production, ensuring that each part meets the desired specifications.
4. Wide range of materials: Plastic injection molding supports a variety of thermoplastic materials, enabling manufacturers to choose the most suitable material for their specific application. This includes different types of plastics with varying properties, such as strength, flexibility, and heat resistance.
Cons:
1. High initial costs: Developing a custom mold can be expensive, particularly for complex designs or when specialized materials are required. The initial investment for tooling and equipment may be cost-prohibitive for small-scale production or one-off projects.
2. Longer lead times: The production of custom molds can take several weeks or even months, which can delay the overall manufacturing process. This can be a drawback when quick turnaround times are required.
3. Limited design modifications: Once the mold is created, making design changes can be a costly and time-consuming process. This limits the ability to modify or improve on the design during the production stage.
4. Parting line and ejector marks: Custom plastic injection molding often leaves behind visible parting lines and ejector marks on the finished product. While these marks are usually cosmetic and do not affect functionality, they may be undesirable for certain applications.
In summary, custom plastic injection molding offers design flexibility, cost-effectiveness for large production runs, and high accuracy. However, the high initial costs, longer lead times, limited design modifications, and cosmetic marks on finished products may present drawbacks.
custom plastic injection molding Reference Specifications (varies for different product)
Custom plastic injection molding is a highly versatile and cost-effective manufacturing process used to create a wide range of plastic products. It involves injecting molten plastic into a mold cavity, where it cools and solidifies to form the desired shape.
The reference specifications for custom plastic injection molding can vary depending on the specific product being produced. Some of the key factors that influence these specifications include the type of plastic material used, the design complexity of the product, the required dimensional accuracy, and the desired surface finish.
The type of plastic material plays a vital role in determining the quality and performance of the final product. Commonly used plastic materials in injection molding include polyethylene (PE), polypropylene (PP), polyvinyl chloride (PVC), polystyrene (PS), and acrylonitrile butadiene styrene (ABS). Each of these materials has different physical and mechanical properties, such as tensile strength, stiffness, impact resistance, and temperature resistance, which can influence the product’s suitability for specific applications.
The design complexity of the product affects the mold design and manufacturing process. Complex designs with intricate features, thin walls, or undercuts may require additional mold components, such as slides, lifters, or inserts, to ensure proper ejection and shape replication. Moreover, the complexity of the design also affects the cycle time, i.e., the time required for each molding cycle, and thus impacts the overall production efficiency and cost.
Dimensional accuracy is critical in many applications to ensure proper fitment, assembly, and functionality. Injection molds are designed with tight tolerances to achieve the desired dimensional precision. Factors such as material shrinkage, thermal expansion, and mold wear need to be considered during the design and production process to maintain accuracy.
Surface finish requirements vary depending on the product’s aesthetics, functional needs, and post-molding processes. Injection molds can provide various surface finishes, including smooth, textured, matte, or glossy finishes, based on the type of mold steel, surface treatment, and texture applied to the mold cavity.
In conclusion, custom plastic injection molding offers immense flexibility and customization options to meet the specific requirements of different products. These requirements can vary significantly, including the choice of plastic material, design complexity, dimensional accuracy, and surface finish. Manufacturers must carefully consider these specifications during the product development and mold design process to manufacture high-quality plastic products efficiently and cost-effectively.
Applications of custom plastic injection molding
Custom plastic injection molding is a versatile manufacturing process that allows for the production of a wide range of plastic products. It involves injecting molten plastic material into a mold cavity, where it cools and solidifies to form a desired shape. This manufacturing method offers several applications across various industries.
One of the most common applications of custom plastic injection molding is in the production of consumer goods. This includes items such as plastic containers, utensils, and household appliances. The ability to create complex shapes and intricate designs makes injection molding ideal for manufacturing these everyday products. It also allows for the use of different types of plastics, providing the necessary flexibility to meet specific requirements, such as durability or heat resistance.
Medical devices and equipment also benefit from custom plastic injection molding. It enables the production of products like syringes, catheters, and surgical instruments. The process ensures precise and consistent dimensions, critical for medical applications where accuracy and reliability are paramount. Moreover, injection molding allows for the integration of multiple components into a single unit, reducing the risk of leakage or failure.
Automotive manufacturers extensively utilize custom plastic injection molding for the production of various interior and exterior parts. These can include dashboard components, trim pieces, bumpers, and even engine parts. Injection molding provides a cost-effective solution for mass-producing these components while maintaining high strength, durability, and dimensional accuracy. Additionally, the lightweight nature of plastic contributes to overall fuel efficiency.
Electronics and telecommunications industries also rely on custom plastic injection molding for the production of enclosures, connectors, and other components. The ability to create custom shapes, including intricate designs for PCB (Printed Circuit Board) housings, allows for optimal space utilization and ensures protection from environmental factors.
Lastly, custom plastic injection molding finds applications in the construction industry. It enables the production of precision components like connectors and fittings for plumbing systems. Additionally, custom plastic injection molding can be used for manufacturing building materials, such as insulation panels or piping systems, due to its cost-effectiveness and versatility.
In conclusion, custom plastic injection molding serves a diverse range of industries, facilitating the production of a wide variety of products. Its ability to create complex shapes, maintain dimensional accuracy, and use different types of plastics makes it an essential manufacturing method for consumer goods, medical devices, automotive parts, electronics, and construction materials.
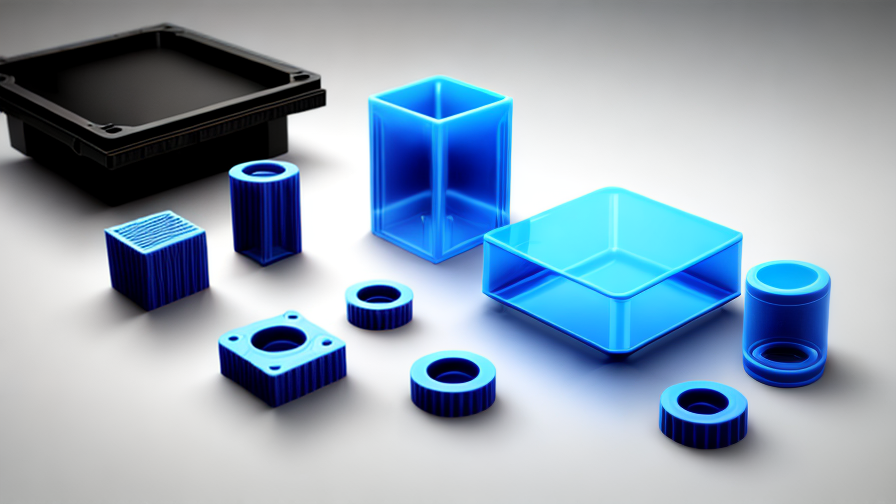
The Work Process and how to use custom plastic injection molding
Custom plastic injection molding is a manufacturing process that involves the creation of plastic parts through injecting molten plastic material into a mold. This process allows for the production of highly complex and precise plastic components, making it a popular choice in various industries such as automotive, medical, and consumer goods.
The work process of custom plastic injection molding generally follows a few key steps. Firstly, a mold is created based on the desired design of the plastic part. The mold consists of two or more halves that fit together and form a cavity, which determines the shape of the final product.
Next, the chosen plastic material is melted down and injected into the mold under high pressure. This plastic resin is typically heated to a molten state in a hopper and then forced into the mold through a nozzle and runner system. The pressure ensures that the material completely fills the mold cavity and takes its shape.
Once the plastic has cooled and solidified within the mold, the mold is opened, and the newly formed part is ejected. This process is usually automated and performed by machines called injection molding machines. The cycle time, or the time it takes to complete one entire molding cycle, varies depending on factors such as the size and complexity of the part, as well as the type of plastic material being used.
After the parts are ejected, they may undergo additional processes such as trimming, polishing, or assembly to achieve the desired final product. These post-molding operations can be done manually or using automated systems.
Using custom plastic injection molding offers several advantages. It allows for the production of intricate designs with high precision and repeatability. The process also enables the use of a wide range of plastic materials, each possessing different properties and characteristics. This flexibility in material selection allows for customization based on the specific requirements of the application.
In conclusion, custom plastic injection molding is an efficient and versatile process that enables the production of complex and accurate plastic parts. By following a well-defined work process, manufacturers can leverage this technology to create custom-made components for a variety of industries.
Quality Testing Methods for custom plastic injection molding and how to control the quality
Quality testing methods for custom plastic injection molding include the following:
1. Visual Inspection: This involves examining the finished product for any visible defects, such as surface blemishes, scratches, or uneven texture. Inspectors may use magnifying lenses or specialized tools to identify the defects more effectively.
2. Dimensional Inspection: This method ensures that the final product meets the specified measurements and tolerances. Inspection tools, like calipers or coordinate measuring machines (CMM), are used to verify dimensions and compare them against the design specifications.
3. Mechanical Testing: This involves subjecting the plastic part to various mechanical stresses to evaluate its strength, durability, and resistance to deformation. Common mechanical tests include tensile strength, impact resistance, flexural strength, and compression testing.
4. Functional Testing: This method tests the ability of the plastic part to perform its intended function within the product assembly. It may involve testing for leakages, flow rate, valve functionality, or other specific performance criteria.
5. Environmental Testing: This type of testing evaluates the plastic part’s performance under extreme environmental conditions such as temperature, humidity, UV exposure, or chemical resistance. It ensures that the material doesn’t deteriorate or fail when subjected to demanding environmental factors.
To control the quality of custom plastic injection molding, several measures can be implemented:
1. Implementing Standard Operating Procedures (SOPs): Clearly defined procedures and work instructions should be in place to guide operators in the manufacturing process. These SOPs ensure consistency and uniformity of the end products.
2. Training and Skill Development: Proper training should be provided to operators and quality control personnel to ensure a thorough understanding of the quality standards and testing procedures. Skilled operators can identify and address potential quality issues proactively.
3. Regular Maintenance of Equipment: Timely maintenance and calibration of machinery and equipment used in plastic injection molding help prevent deviations in dimensions and ensure accurate production. Regular maintenance routines should be established and followed.
4. Statistical Process Control (SPC): Monitoring critical process parameters using SPC techniques helps in identifying and eliminating variations that may affect product quality. This involves collecting and analyzing real-time data to make informed decisions about process control.
5. Raw Material Quality Control: Ensuring the quality of the raw materials used in plastic injection molding is crucial. Conducting inspections and verifying the material quality before it enters the production process can prevent potential defects and inconsistencies.
By employing these quality testing methods and implementing stringent quality control measures, manufacturers can effectively monitor and maintain the quality of custom plastic injection molding. This helps ensure that the final products meet or exceed the desired standards, leading to increased customer satisfaction and reduced rework or rejection rates.
custom plastic injection molding Sample Policy and Post-Purchase Considerations for custom plastic injection molding from China
Sample Policy:
When considering custom plastic injection molding from China, it is important to inquire about the sample policy of the manufacturer. Many manufacturers offer the option to provide samples of the plastic injection molded products before bulk production. This allows the customer to review the quality, design, and functionality of the product to ensure it meets their requirements. It is advisable to clarify whether the samples will be charged or provided free of cost. Additionally, the customer should inquire about the time frame for sample production and delivery, as this can vary depending on the manufacturer’s capabilities and workload.
Post-Purchase Considerations:
After purchasing custom plastic injection molded products from China, there are a few essential considerations to keep in mind. Firstly, it is crucial to thoroughly inspect the products upon delivery to ensure they meet the agreed-upon specifications. If any discrepancies or quality issues are identified, it is important to communicate these concerns to the manufacturer immediately. Secondly, it is advisable to maintain open and consistent communication with the manufacturer throughout the production and delivery process. This can help address any concerns or questions, as well as provide updates on the progress of the order. Lastly, it is recommended to establish a long-term relationship with the manufacturer for potential future orders. By maintaining a positive relationship, it becomes easier to resolve any issues and ensure a smooth and efficient production process.
Sourcing custom plastic injection molding from China: Opportunities, Risks, and Key Players
China has become a significant player in the global plastic injection molding market, offering opportunities for companies seeking cost-effective manufacturing solutions. However, it is essential for businesses to carefully consider the associated risks and identify key players in this industry.
Opportunities:
1. Cost-effective manufacturing: China offers competitive pricing due to lower labor and production costs compared to other countries.
2. Wide range of services: Chinese manufacturers offer a diverse range of plastic injection molding services, including design, prototyping, tooling, and production capabilities.
3. High production capacity: China has numerous manufacturing facilities equipped with advanced technology, ensuring large-scale production capabilities and quick lead times.
4. Quality standards: Many Chinese manufacturers adhere to international quality standards, such as ISO 9001, ensuring the consistency and reliability of their products.
5. Local supply chain: Establishing partnerships with Chinese manufacturers allows companies to tap into an extensive local supply chain, reducing logistics costs and lead times.
Risks:
1. Quality control issues: Although many Chinese manufacturers maintain high standards, there have been instances of substandard products due to lax quality control practices. Rigorous vetting of potential suppliers and regular quality checks are necessary to mitigate this risk.
2. Intellectual property (IP) protection: China has faced scrutiny regarding IP protection. Companies must have robust legal agreements in place and take appropriate steps to safeguard their designs and proprietary information.
3. Communication and language barriers: Effective communication can be challenging due to language differences and time zone disparities. This can lead to delays, misunderstandings, and product discrepancies if not managed properly.
4. Supply chain disruptions: External factors such as natural disasters, political instability, or trade disputes may disrupt the supply chain, impacting production schedules and delivery times.
Key players:
1. Foxconn: A global electronics manufacturing company offering plastic injection molding services.
2. Flex Ltd.: A leading contract manufacturer for various industries, including plastic injection molding.
3. Jabil: An American company with a strong presence in China, providing comprehensive plastic injection molding solutions.
4. Luxshare Precision Industry Co., Ltd.: Known for its precision plastic injection molding and assembly services.
5. Higoal: Specializes in custom plastic injection molding and provides solutions for automotive, electronics, and medical sectors.
In conclusion, sourcing custom plastic injection molding from China offers attractive opportunities due to competitive pricing, a wide range of services, and high production capacity. However, businesses must be aware of the risks associated with quality control, IP protection, and supply chain disruptions. Additionally, identifying trustworthy key players in the Chinese market is crucial for successful partnerships and quality manufacturing.
How to find and select reliable custom plastic injection molding manufacturers in China,use google search manufacturers and suppliers
Finding and selecting reliable custom plastic injection molding manufacturers in China can be a daunting task. However, with the right approach, utilizing Google search for manufacturers and suppliers can help streamline the process. Here’s a step-by-step guide in not more than 300 words:
1. Define your requirements: Clearly define your project requirements, including design specifications, quantity needed, budget, and desired timeline. This will help you filter potential manufacturers later on.
2. Google search: Start by searching for “custom plastic injection molding manufacturers in China” on Google. This will provide you with a list of potential suppliers.
3. Company background check: Visit the websites of the manufacturers and assess their credibility. Look for important information such as years of experience, certifications, company culture, equipment capabilities, and customer reviews.
4. Verify certifications: Ensure that the manufacturer holds necessary certifications such as ISO 9001 or ISO 13485, which demonstrate their commitment to quality management systems.
5. Evaluate manufacturing capabilities: Determine if their facilities and equipment meet your project’s requirements. Look for aspects like injection molding machines, mold-making capabilities, plastic materials offered, and secondary operations they specialize in.
6. Communication: Contact the manufacturers directly through email or phone and assess their responsiveness. Prompt and clear communication is crucial throughout the manufacturing process.
7. Request for quotes: Share your project requirements and request quotations from multiple manufacturers. Analyze the pricing structure, payment terms, lead times, and any additional services offered.
8. Product samples: Requesting samples of previously manufactured products allows you to evaluate the manufacturer’s quality standards and capabilities firsthand.
9. Check references: Ask manufacturers for references and follow up with their past or existing clients. This will provide insights into their reliability, product quality, and customer service.
10. Consider logistics: Evaluate the manufacturer’s proximity to shipping ports, as well as their experience in exporting goods. This can impact shipping costs, timelines, and potential logistic issues.
11. Quality assurance: Inquire about their quality control processes, including inspections, testing protocols, and certifications. High-quality manufacturers often have robust quality assurance systems in place.
12. Intellectual property protection: Discuss intellectual property protection measures with the manufacturer, such as non-disclosure agreements (NDAs) and confidentiality agreements.
By following these steps and conducting due diligence, you can find and select reliable custom plastic injection molding manufacturers in China who can meet your specific requirements effectively and efficiently.
How to check custom plastic injection molding manufacturers website reliable,use google chrome SEOquake check if ranking in top 10M
To determine the reliability of a custom plastic injection molding manufacturer’s website, you can follow these steps:
1. Use Google Chrome: Open the manufacturer’s website using Google Chrome as your browser. Chrome provides several useful tools and extensions to assess website reliability and performance.
2. Install SEOquake Extension: Install the SEOquake extension from the Chrome Web Store. SEOquake is a powerful SEO tool that provides valuable insights about a website’s ranking, traffic, and authority.
3. Check Website Ranking: Once the SEOquake extension is installed, activate it by clicking on the icon on your browser’s toolbar. A toolbar will appear displaying various metrics. Look for the box that contains the website’s Alexa Rank. If the manufacturer’s website has a ranking within the top 10 million websites globally, it is considered relatively well-established.
4. Assess Alexa Rank: While the exact significance of specific Alexa ranks may vary, a relatively good Alexa Rank indicates that the website has decent traffic, recognition, and reliability. However, do note that small businesses or niche manufacturers may have higher ranks, so consider the industry context.
5. Evaluate Overall Website Quality: Browse through the manufacturer’s website and carefully assess its overall design, user interface, and content. A reliable website usually exhibits a professional appearance, clear navigation, and well-structured information. Look for detailed product descriptions, industry certifications, customer testimonials, and clear contact information.
6. Research Manufacturer’s Reputation: Conduct additional research to verify the manufacturer’s reputation. Look for reviews and testimonials from previous clients, search for their presence on industry directories or associations, and check if they have any certifications or quality management systems in place. This information will help you assess their reliability and expertise in the field.
Remember to exercise caution even if a website ranks well or appears professional, as these factors alone do not guarantee reliability. Conducting thorough research and due diligence is crucial when selecting a custom plastic injection molding manufacturer.
Top 10 custom plastic injection molding manufacturers in China with each 160 words introduce products,then use markdown create table compare
1. HQ Mould – HQ Mould is a leading plastic injection molding manufacturer in China with extensive experience in producing high-quality plastic products. Their wide range of products includes automotive parts, electronic components, household items, medical equipment, and more. With state-of-the-art facilities and advanced technology, they have the capability to meet customized requirements and deliver products with precision and efficiency.
2. Star Rapid – Star Rapid specializes in rapid prototyping and low-volume production of plastic injection molded parts. They offer a wide selection of materials and finishes to cater to various industries such as automotive, electronics, consumer products, and medical devices. With their advanced equipment and strict quality control, they ensure that the products meet industry standards and customer expectations.
3. Sino Mould – Sino Mould is a renowned manufacturer of custom plastic injection molds and molded parts. They have a wide range of products, including industrial containers, household items, automotive parts, and more. With their experienced team and advanced manufacturing processes, they can produce high-quality products with quick turnaround times.
4. JasonMould Industrial Company Limited – JasonMould specializes in manufacturing precision plastic injection molds and molded parts. Their products are widely used in electronics, automotive, medical, and other industries. With their advanced equipment and strict quality control system, they ensure the products meet the highest standards of quality and durability.
5. Molding USA Inc. – Molding USA Inc. is a one-stop solution for all plastic injection molding needs. They provide custom manufacturing services for a wide range of industries, including aerospace, automotive, electronics, and consumer goods. Their team of experts is dedicated to delivering high-quality products within the specified time frame.
6. LK Mould – LK Mould is a leading manufacturer of plastic injection molds and molded parts. They have a diverse range of products, including automotive components, consumer goods, and electronic parts. With their advanced machinery and skilled workforce, they ensure precise and efficient production.
7. Sun On Plastic Moulding Limited – Sun On Plastic Moulding Limited specializes in the production of custom plastic molds and plastic injection molded parts. Their products cater to industries such as medical, automotive, electronic, and consumer goods. With their commitment to quality and customer satisfaction, they have built a strong reputation in the industry.
8. CN-Moulding – CN-Moulding is a trusted manufacturer of plastic injection molded parts. They offer a wide range of products, including electronic components, medical devices, automotive parts, and more. With their state-of-the-art facilities and skilled workforce, they are capable of meeting various customization requirements.
9. Dragon Manufacturing Limited – Dragon Manufacturing Limited is a leading manufacturer of custom injection molded plastic parts. They specialize in producing high-quality components for various industries, including electronics, automotive, medical, and consumer goods. With their modern manufacturing facilities and rigorous quality control, they ensure consistent and reliable products.
10. Ming-Li Precision Industries – Ming-Li Precision Industries has been a pioneer in plastic injection molding in China. They provide comprehensive manufacturing services, including mold design, mold making, and plastic injection molding. Their products are widely used in industries such as electronics, automotive, and medical equipment. With their advanced technologies and years of experience, they deliver superior quality plastic components to meet customer specifications.
**Comparison Table**
| Manufacturer | Specializations | Industries Served | Customization Capabilities | Quality Control |
| —————————- | ———————————– | —————————————— | ————————- | —————————— |
| HQ Mould | Automotive parts, electronic components, household items, medical equipment | Various industries | Yes | Advanced technology, precision and efficiency |
| Star Rapid | Rapid prototyping, low-volume production | Automotive, electronics, consumer products, medical devices | Yes | Advanced equipment, strict quality control |
| Sino Mould | Industrial containers, household items, automotive parts, etc. | Wide range of industries | Yes | Experienced team, advanced manufacturing processes |
| JasonMould Industrial Co. Ltd | Precision plastic injection molds and molded parts | Electronics, automotive, medical, and other industries | Yes | Advanced equipment, strict quality control system |
| Molding USA Inc. | Custom manufacturing services | Aerospace, automotive, electronics, consumer goods | Yes | High-quality products, quick turnaround times |
| LK Mould | Molded parts for automotive, consumer goods, electronics | Various industries | Yes | Advanced machinery, skilled workforce |
| Sun On Plastic Moulding Ltd | Custom plastic molds and plastic injection molded parts | Medical, automotive, electronic, consumer goods | Yes | Commitment to quality, customer satisfaction |
| CN-Moulding | Plastic injection molded parts, electronic components, medical devices | Various industries | Yes | State-of-the-art facilities, flexible customization |
| Dragon Manufacturing Ltd | Custom injection molded plastic parts | Electronics, automotive, medical, consumer goods | Yes | Modern manufacturing facilities, rigorous quality control system |
| Ming-Li Precision Industries | Plastic injection molding, mold making, mold design | Electronics, automotive, medical equipment | Yes | Advanced technologies, superior quality components |
In this table, the manufacturers’ specializations, industries served, customization capabilities, and quality control practices have been compared to provide an overview of their offerings.
Background Research for custom plastic injection molding manufacturers Companies in China, use qcc.com archive.org importyeti.com
When it comes to custom plastic injection molding manufacturers in China, there are a few platforms that can provide valuable background research. Qcc.com, archive.org, and importyeti.com are reliable sources for obtaining information about companies operating in this industry.
Qcc.com is an online Chinese company database that offers a wide range of information about businesses, including their registered information, credit reports, business scopes, and key personnel. It provides insights into a company’s size, location, legal status, and financial performance. This platform can be utilized to identify potential manufacturers and acquire contact information for further inquiries.
Archive.org is a digital library that captures web pages over time. It allows users to access stored website data, which can be useful for tracking a company’s historical presence and evaluating changes in their operations, services, or product offerings. By reviewing previous iterations of a manufacturer’s website, one can gain insights into their experience, stability, and evolving capabilities.
Importyeti.com, on the other hand, specializes in providing import and export data to help locate potential suppliers in China. By searching for custom plastic injection molding manufacturers on this platform, users can retrieve information about a company’s export history, including the types of products they have shipped and the countries they have exported to. This data can give a better understanding of a manufacturer’s expertise and international experience.
In conclusion, conducting background research on custom plastic injection molding manufacturers in China can be effectively performed using platforms like qcc.com, archive.org, and importyeti.com. These sources provide detailed information about a company’s registration data, financial performance, historical presence, and export history. Utilizing these platforms allows potential buyers to make informed decisions when selecting a reliable manufacturer in China.
Leveraging Trade Shows and Expos for custom plastic injection molding Sourcing in China
Trade shows and expos provide excellent opportunities for businesses looking to source custom plastic injection molding from China. These events allow companies to connect with suppliers, learn about new technologies, and gain valuable market insights. Leveraging trade shows and expos effectively can help streamline the sourcing process and ensure high-quality products.
Firstly, trade shows and expos in China provide a platform for meeting potential suppliers face-to-face. This direct interaction allows businesses to gauge the capabilities, expertise, and reliability of different injection molding manufacturers. It also enables discussions on specific product requirements, customization options, and pricing.
Trade shows and expos also offer access to a wide range of injection molding suppliers that specialize in various industries or materials. This variety allows businesses to find the most suitable partner for their specific project needs. Attendees can compare different suppliers, assess their quality standards, and even request sample parts to evaluate their manufacturing capabilities.
Furthermore, these events often showcase the latest injection molding technologies and innovations. Companies can explore new manufacturing techniques, materials, and equipment, which may enhance the quality, efficiency, and cost-effectiveness of their products. This exposure to cutting-edge solutions can drive innovation and competitiveness.
In addition to supplier sourcing and technology exploration, trade shows and expos provide valuable market insights. Attendees can gather information about industry trends, competitor strategies, and regional market demands. This knowledge can help businesses make informed decisions when selecting suppliers and designing products.
To maximize the benefits of trade shows and expos, businesses should prepare in advance. This includes conducting thorough research on participating suppliers, setting clear objectives, and creating a list of questions to ask potential partners. It is also crucial to allocate adequate time for networking and follow-up meetings to solidify relationships with selected suppliers.
In conclusion, trade shows and expos in China offer fruitful avenues for sourcing custom plastic injection molding products. These events enable direct supplier interactions, access to various suppliers, exposure to new technologies, and valuable market insights. By leveraging trade shows effectively, businesses can streamline their sourcing process and find reliable and suitable injection molding partners.
The Role of Agents and Sourcing Companies in Facilitating custom plastic injection molding Purchases from China
Agents and sourcing companies play a critical role in facilitating custom plastic injection molding purchases from China. These entities act as intermediaries between buyers and manufacturers, assisting in the sourcing, negotiation, quality control, and logistics aspects of the procurement process.
Firstly, agents and sourcing companies provide access to a wide network of reliable plastic injection molding manufacturers in China. They leverage their industry expertise, local knowledge, and established relationships to identify and connect buyers with suitable suppliers based on their specific requirements. This saves buyers significant time and effort that would otherwise be spent researching and vetting potential manufacturers.
Secondly, these intermediaries aid in negotiation and pricing. Due to their experience in dealing with Chinese manufacturers, agents can effectively negotiate the best price and favorable terms on behalf of the buyer. They possess an in-depth understanding of Chinese business practices, culture, and local regulations, which enables them to navigate potential challenges such as language barriers, cultural differences, and intellectual property protection.
In addition, agents and sourcing companies play a crucial role in ensuring product quality. They conduct thorough due diligence on manufacturers, assessing their capabilities, certifications, and production facilities. During the production process, agents perform regular quality control inspections to ensure that the products meet the buyer’s specifications and standards. This reduces the risk of receiving subpar or non-compliant products, which can lead to costly rework or rejection of the entire shipment.
Furthermore, agents and sourcing companies handle logistics and shipping arrangements. They coordinate the transportation of the goods from the manufacturer’s facility in China to the buyer’s desired destination. This involves managing customs clearance, documentation, and arranging the most cost-effective and efficient shipping methods, ensuring timely delivery.
Overall, agents and sourcing companies serve as invaluable partners in facilitating custom plastic injection molding purchases from China. They streamline the procurement process, mitigate risks, and provide comprehensive support at each stage. By leveraging their expertise, buyers can confidently navigate the complexities of international sourcing and achieve successful outcomes in their plastic injection molding endeavors.
Price Cost Research for custom plastic injection molding manufacturers Companies in China, use temu.com and 1688.com
When researching custom plastic injection molding manufacturers in China, two prominent websites to consider are temu.com and 1688.com. These platforms provide extensive information about various manufacturers, allowing potential buyers to explore their offerings, compare prices, and select the most suitable partner for their needs.
Temu.com is an online industrial platform that connects buyers and suppliers worldwide. It offers a wide range of services, including product sourcing, factory visits, quality control, and logistics support. By utilizing temu.com, individuals can easily find and evaluate custom plastic injection molding manufacturers in China.
1688.com, on the other hand, is a leading business-to-business platform owned by Alibaba Group. While primarily popular within China, it provides a vast database of suppliers covering various industries, including plastic injection molding. Users can directly communicate with manufacturers, negotiate prices, and track product delivery.
When conducting price and cost research on these platforms, it is important to utilize the available search filters and parameters to narrow down the options based on specific requirements. Manufacturers’ profiles often display information about their production capabilities, certifications, previous customers, and past projects. This data can assist in evaluating their credibility and suitability.
Furthermore, it is advisable to directly contact shortlisted manufacturers to discuss specific project requirements, including the desired mold design, production volumes, materials, and any additional customization needs. By providing clear specifications, buyers can receive accurate quotations and compare prices among different manufacturers.
To ensure transparency, it is crucial to inquire about additional costs beyond the quoted price, such as tooling fees, packaging costs, transportation fees, and any potential taxes or import duties. Buyers should also discuss payment terms, production lead times, and the manufacturer’s quality control processes.
In conclusion, conducting price and cost research for custom plastic injection molding manufacturers in China can be efficiently done through temu.com and 1688.com. By utilizing these platforms and following the recommended steps, buyers can find reliable partners offering competitive prices for their specific needs.
Shipping Cost for custom plastic injection molding import from China
The shipping cost for custom plastic injection molding imports from China varies depending on several factors such as the size and weight of the shipment, the shipping method chosen, the destination, and any additional services required.
For small to medium-sized shipments, air freight is commonly used. Air freight costs are determined by the size and weight of the shipment, with charges calculated per kilogram or per cubic meter. On average, air freight costs from China to most major destinations range from $3 to $8 per kilogram. However, costs can be significantly higher for urgent or time-sensitive shipments.
For larger shipments, sea freight is a more cost-effective option. Sea freight costs are calculated based on container sizes, which can either be full container load (FCL) or less than container load (LCL). FCL shipments are more economical for larger quantities, while LCL shipments are used when the shipment does not fill an entire container. On average, sea freight costs from China to most major ports range from $500 to $2000 for FCL shipments and $50 to $250 per cubic meter for LCL shipments.
In addition to the basic shipping costs, additional charges such as customs duties, taxes, and import handling fees may apply depending on the destination country’s regulations. It is recommended to consult with a freight forwarder or shipping agent to obtain a detailed quote based on specific shipment requirements.
Overall, when importing custom plastic injection molding from China, it is crucial to consider not only the shipping cost but also the quality, lead time, and reliability of the supplier to ensure a successful and cost-effective import process.
Compare China and Other custom plastic injection molding Markets: Products Quality and Price,Visible and Hidden Costs
China is a prominent player in the custom plastic injection molding market, but it faces competition from other markets as well. One of the key factors to compare between China and other markets is the quality and price of the products.
China has gained a reputation for providing cost-effective solutions in plastic injection molding. The country has invested heavily in its manufacturing capabilities and has developed a vast network of suppliers and manufacturers. This has enabled China to offer competitive prices for custom plastic injection molding products.
However, quality can vary significantly among Chinese manufacturers. While there are reputable providers in China that adhere to international quality standards, there are also lower-quality manufacturers offering cheaper products. This poses a challenge for buyers who need to carefully select a reliable supplier to ensure consistent product quality.
In comparison, other markets such as the United States, Germany, and Japan are known for their high-quality products. These markets have a long-standing reputation for producing durable and reliable custom plastic injection molded products. However, the price of products from these markets is often higher than those from China due to factors such as higher labor and manufacturing costs.
When examining costs, it is crucial to consider both visible and hidden costs associated with custom plastic injection molding. Visible costs include the upfront costs of manufacturing, such as the price of raw materials, labor costs, and tooling expenses. China often offers lower visible costs due to its lower labor and manufacturing costs.
However, hidden costs can arise from factors like communication challenges, intellectual property protection issues, logistics, and lead times. China’s geographical distance from many Western markets can result in longer lead times and increased freight costs. Additionally, concerns about protecting intellectual property rights when working with Chinese manufacturers can be a potential hidden cost.
In conclusion, China’s custom plastic injection molding market offers competitive prices, but product quality can be variable. Other markets like the United States, Germany, and Japan are known for higher quality products but at a higher price point. It is important to carefully consider both visible and hidden costs when comparing these markets, to ensure the best balance between quality and price for custom plastic injection molded products.
Understanding Pricing and Payment Terms for custom plastic injection molding: A Comparative Guide to Get the Best Deal
When it comes to custom plastic injection molding, understanding pricing and payment terms is crucial to ensure you get the best deal. This comparative guide aims to provide a comprehensive overview in less than 300 words.
Pricing for custom plastic injection molding is determined by several factors. These include the complexity of the part design, the material used, the quantity required, and the desired quality. Suppliers often provide quotes based on the specific project requirements provided by the customer. It is essential to communicate all details accurately to avoid any misunderstandings.
Payment terms can vary between suppliers. Commonly, a deposit is required upfront to cover material costs and tooling expenses. The remaining balance is typically paid upon completion or in agreed-upon installments. It is advisable to clarify the payment schedule before starting the project to avoid any surprises.
To get the best deal, obtaining multiple quotes from different suppliers is essential. This allows for a price comparison and ensures you are receiving a competitive offer. It is important to consider not only the price but also the supplier’s experience, quality control measures, and turnaround time.
When comparing prices, be cautious of overly low quotes as they may indicate substandard quality or hidden costs. A reputable supplier should be transparent about their pricing structure and provide detailed breakdowns of the costs involved.
Negotiating with suppliers can also help secure a better deal. Requesting a volume discount for larger quantities or longer-term contracts is a common practice. However, keep in mind that negotiating too aggressively may affect the relationship with the supplier and compromise the quality of the product.
The terms of payment can also be negotiated to align with your financial capabilities. Some suppliers may offer flexible payment options, such as negotiating longer payment terms or providing discounts for prompt payments. Open and clear communication regarding your requirements and limitations is crucial to reach a mutually beneficial agreement.
In conclusion, understanding pricing and payment terms is essential when engaging in custom plastic injection molding. Obtaining multiple quotes, evaluating the supplier’s reputation, and negotiating can help ensure the best deal. Transparent communication is critical to avoid misunderstandings and establish a successful business relationship.
Chinese Regulations and Industry Standards Certifications for custom plastic injection molding,Import Regulations and Customs for custom plastic injection molding from China
China has established a set of regulations and industry standards for custom plastic injection molding to ensure product quality and safety. These certifications play a crucial role in determining the quality and reliability of plastic injection molds produced in China.
The primary certification for plastic injection molding in China is the ISO 9001:2015. This certification ensures that the manufacturer has implemented a quality management system and has the necessary procedures in place to consistently produce high-quality injection molds.
In addition to ISO 9001, various industry-specific certifications may also be required based on the specific application of the injection molds. For instance, if the molds are intended for use in the automotive industry, manufacturers may need to comply with the IATF 16949 standard, which focuses on quality management specifically for the automotive sector.
Importing custom plastic injection molding from China requires compliance with import regulations and customs procedures. The importer must ensure that the product complies with all applicable safety and quality standards of their country. They may need to provide relevant certificates and documentation to prove compliance.
Moreover, it is essential to verify the reputation and reliability of the Chinese manufacturer before making any import transactions. Conducting due diligence, including checking the manufacturer’s experience, client reviews, and certifications, can help identify trustworthy suppliers.
Correct documentation, including invoices, packing lists, and a bill of lading, should be prepared accurately to ensure smooth customs clearance. Import duties and taxes may also apply, and the importer should be aware of the specific regulations and rates for plastic injection molding in their own country.
In conclusion, Chinese regulations and industry standards certifications such as ISO 9001:2015, and potentially industry-specific certifications, are vital for ensuring the quality of custom plastic injection molding. Importers must also comply with import regulations and customs procedures, including providing necessary documentation and fulfilling customs duties and taxes.
Sustainability and Environmental Considerations in custom plastic injection molding Manufacturing
Custom plastic injection molding manufacturing is a widely used technique in producing plastic products. However, it is important to consider sustainability and environmental factors in this process to minimize the negative impact on the planet.
One key aspect to address is the choice of raw materials. Opting for biodegradable or recyclable plastics can significantly reduce the environmental footprint of custom plastic injection molding. Biodegradable plastics can decompose naturally, reducing plastic waste in landfills. Recyclable plastics, on the other hand, can be reused, reducing the need for virgin materials and saving energy in the manufacturing process.
Another important consideration is energy consumption. Implementing energy-efficient manufacturing methods and utilizing renewable energy sources can significantly decrease the carbon footprint of custom plastic injection molding. This can be achieved by optimizing equipment and processes, using energy-efficient machinery, and adopting renewable energy sources such as solar or wind power.
Reducing waste generation is another sustainable practice. Implementing lean manufacturing principles, such as reducing material waste and reusing or recycling scrap materials, can help minimize waste in the production process. Additionally, implementing closed-loop systems for water and material reclamation can further reduce waste generation.
Toxicity and emissions should also be accounted for. Using eco-friendly additives and colorants that do not contain harmful substances or volatile organic compounds (VOCs) ensures the safety of both the environment and workers. Proper management of emissions and waste disposal, in compliance with environmental regulations, is crucial to prevent pollution.
Considering the entire product lifecycle is essential for sustainability. Designing products that are easily disassembled and recycled at the end of their life promotes circular economy principles. By incorporating recycled content into new products, the demand for virgin materials can be reduced, conserving natural resources.
Overall, adopting sustainable practices in custom plastic injection molding manufacturing is crucial to mitigate the environmental impact of this process. By choosing biodegradable/recyclable materials, reducing energy consumption, minimizing waste generation, considering toxicity and emissions, and incorporating circular economy principles, manufacturers can contribute to a greener and more sustainable future.
List The Evolution history of “custom plastic injection molding”
Custom plastic injection molding has come a long way since its inception in the late 19th century. This manufacturing process has witnessed significant technological advancements and played a crucial role in the development of various industries worldwide.
The concept of injection molding dates back to the 1860s when John Wesley Hyatt and his brother Isaiah Patented the first plastic injection molding machine. Initially, they used a mixture of cellulose nitrate and camphor to create a material called celluloid, which marked the birth of plastic injection molding. This new material was soon embraced by various industries due to its versatility and cost-effectiveness compared to traditional materials like metal and wood.
In the early 20th century, thermoplastics such as polyvinyl chloride (PVC) and polyethylene (PE) were introduced, which further expanded the possibilities of custom plastic injection molding. The process became more efficient with the development of hydraulic and electric injection molding machines.
The 1940s witnessed a significant milestone in the evolution of injection molding with the creation of the screw injection molding machine by James Watson Hendry. This invention revolutionized the industry by automating the previously time-consuming process of melting and injecting the plastic material into molds.
The 1950s marked a turning point in the widespread adoption of injection molding as various industries recognized its immense potential. Advances in mold design, cooling systems, and plastic materials broadened its applications. The shift towards using plastics for consumer goods, automotive parts, and packaging materials fueled the demand for custom plastic injection molding.
In the following decades, computer numerical control (CNC) technology began to be implemented in injection molding, allowing for more precise and complex designs. The 1980s brought the advent of computer-aided design (CAD) and computer-aided manufacturing (CAM) systems, which further enhanced the efficiency and precision of the process.
In recent years, the focus has shifted towards sustainability and environmentally friendly practices within the injection molding industry. The introduction of biodegradable and recyclable plastics has contributed to reducing the environmental impact of custom plastic injection molding.
Today, custom plastic injection molding is a mature and highly advanced manufacturing process. The use of advanced materials, automated machinery, and cutting-edge technologies like 3D printing has opened new doors for innovation. The process has become more efficient, cost-effective, and environmentally conscious, making it a preferred choice in industries ranging from automotive and electronics to healthcare and consumer goods.
The Evolution and Market Trends in custom plastic injection molding Industry
Custom plastic injection molding is a manufacturing process that involves injecting molten plastic into a mold to create specific products. Over the years, this industry has witnessed significant evolution and has adapted to various market trends.
One major evolution in the custom plastic injection molding industry is the advancement in technology. Automation and robotics have revolutionized the manufacturing process, leading to increased efficiency and precision. Computer-aided design (CAD) software, along with computer numerical control (CNC) machining, has made it easier to design and produce molds with complex and intricate designs. This technology has enabled manufacturers to produce high-quality products at a faster rate, reducing lead times and costs.
Another evolution is the growing emphasis on sustainability. With increasing environmental concerns, custom plastic injection molding companies are adopting more sustainable practices. They are using biodegradable and recycled plastics instead of traditional petroleum-based materials, reducing waste and carbon footprint. Additionally, manufacturers are implementing energy-efficient technologies and recycling processes to minimize environmental impact.
Market trends have also shaped the custom plastic injection molding industry. One notable trend is the rising demand for lightweight and durable plastic components in various sectors, such as automotive, healthcare, and electronics. The shift towards lightweight materials for fuel efficiency and improved performance has increased the demand for custom plastic injection molded products.
The customization trend is another significant factor driving the industry. With consumers seeking personalized products, manufacturers are offering customized solutions to meet specific requirements. Custom plastic injection molding allows for the production of unique shapes, sizes, and designs, catering to individual needs and preferences.
Furthermore, global sourcing has become a prevalent trend in the industry. Many companies are opting to outsource their plastic injection molding requirements to regions with lower labor costs, such as Asia. This trend has led to the establishment of numerous manufacturing facilities in emerging economies, further fueling the growth of the industry.
In conclusion, the custom plastic injection molding industry has evolved through technological advancements, sustainable practices, and market trends. The adoption of automation and robotics, the focus on sustainability, the demand for lightweight products, the customization trend, and global sourcing have significantly influenced this industry’s growth and development. As the industry continues to evolve, manufacturers must stay updated with emerging technologies and market demands to remain competitive.
Custom Private Labeling and Branding Opportunities with Chinese custom plastic injection molding Manufacturers
Chinese custom plastic injection molding manufacturers offer numerous opportunities for custom private labeling and branding. With their expertise in plastic injection molding technology, these manufacturers can produce a wide range of plastic products, allowing businesses to create tailor-made products that reflect their brand identity.
One of the key advantages of working with Chinese manufacturers is their ability to offer custom private labeling. This allows businesses to include their own logos, brand names, and other customized details on the products. By doing so, it helps to promote brand awareness and visibility in the market. Custom private labeling also provides an opportunity to differentiate products from competitors, as customers can easily associate the branded products with a specific brand and its values.
Furthermore, Chinese manufacturers offer branding opportunities through custom packaging solutions. They can design and manufacture unique packaging that embodies the brand’s image and message. Whether it’s an eye-catching box or a custom-shaped container, these packaging options enhance the overall product presentation, reinforcing brand recognition and increasing perceived value.
In addition to custom private labeling and branding, Chinese plastic injection molding manufacturers often provide assistance with product development and design. They have experienced engineers who can work closely with businesses to refine product designs and ensure they meet specific functional and aesthetic requirements. This collaboration helps to create products that align perfectly with the brand’s vision, ensuring a seamless integration into the market.
Overall, partnering with Chinese custom plastic injection molding manufacturers offers businesses the advantage of providing customized products under their own brand. With custom private labeling, unique packaging, and support for product development, these manufacturers enable businesses to build a strong brand presence in the market and gain a competitive edge.
Tips for Procurement and Considerations when Purchasing custom plastic injection molding
When purchasing custom plastic injection molding, it is crucial to consider certain factors to ensure that the procurement process runs smoothly and meets your requirements. Here are some tips and considerations:
1. Identify your requirements: Clearly define your specific needs, including the type and size of the plastic parts, desired volume, quality standards, and any specific features or materials.
2. Supplier selection: Thoroughly research and assess potential suppliers. Look for reputable manufacturers with a track record of delivering high-quality custom plastic injection molding solutions. Consider their experience, expertise, capabilities, equipment, and certifications.
3. Quality assurance: Ensure that the supplier follows strict quality control processes and holds relevant certifications like ISO 9001. Request information about their quality control measures, inspection protocols, and testing procedures.
4. Material selection: Discuss the material requirements with the supplier. Different materials have varying properties, such as strength, durability, temperature resistance, and chemical compatibility. Choose a material that best fits your application and specifications.
5. Design support: Find suppliers that offer design support services. They can provide valuable insights and suggestions for optimizing the design, reducing costs, improving manufacturability, and enhancing the overall performance of your molded plastic parts.
6. Tooling and molds: Inquire about the supplier’s tooling capabilities and experience. Tooling is a critical aspect of plastic injection molding. Make sure the supplier uses advanced tooling techniques and equipment for producing high-quality molds that meet your specifications.
7. Cost considerations: Obtain detailed quotes from different suppliers and compare their pricing structures. However, be cautious of overly cheap options as they may compromise quality. Consider factors like tooling costs, production volume, material costs, and any additional services required.
8. Communication and collaboration: Establish effective communication with the supplier throughout the procurement process. Clear communication ensures that both parties are aligned on expectations, timelines, revisions, and any potential challenges.
9. Intellectual property protection: If your plastic parts have unique designs or features, ensure that the supplier signs a non-disclosure agreement (NDA) to protect your intellectual property rights.
10. After-sales support: Inquire about the supplier’s after-sales support services, such as warranty policies, defect resolution, and replacement parts availability.
By considering these tips and factors, you can ensure a successful procurement process for custom plastic injection molding, leading to high-quality products that meet your specific requirements.
FAQs on Sourcing and Manufacturing custom plastic injection molding in China
1. Why should I consider sourcing and manufacturing custom plastic injection molding in China?
Sourcing and manufacturing custom plastic injection molding in China can offer numerous advantages such as cost-effectiveness due to lower labor and production costs, access to a wide range of manufacturing capabilities and advanced technologies, a large pool of skilled labor, and the ability to handle high production volumes. China has established itself as a global manufacturing hub, offering competitive pricing, quicker turnaround times, and a strong supply chain network.
2. How can I find a reliable manufacturer for my custom plastic injection molding needs in China?
Finding a reliable manufacturer in China requires careful research and due diligence. Consider using reputable sourcing platforms, engaging with experienced third-party sourcing agents, attending trade shows and exhibitions, and requesting samples for evaluation. Verify their credentials, certifications, and manufacturing capabilities. Conducting on-site visits and audits can also provide insight into their facilities, quality control systems, and production processes.
3. What considerations should I keep in mind during the sourcing process?
When sourcing custom plastic injection molding in China, keep several factors in mind. Ensure that the manufacturer has experience in producing similar products and the necessary certifications and quality control systems. Discuss your design specifications, material requirements, manufacturing timeline, and budget extensively to avoid misunderstandings. Consider the logistics, shipping costs, and import regulations associated with bringing the products to your destination country.
4. What quality control measures are in place during the manufacturing process?
Reputable manufacturers in China often implement comprehensive quality control measures. These may include regular inspections during production, adherence to ISO and other quality management system standards, using high-quality raw materials, conducting rigorous testing and inspection of finished products, and ensuring compliance with customer specifications through documentation and verification processes.
5. What are the typical lead times for custom plastic injection molding in China?
Lead times for custom plastic injection molding in China can vary depending on the complexity of the product, the manufacturer’s production capacity, and the quantities required. On average, lead times can range from a few weeks to several months. It is important to discuss and agree upon realistic lead times with the manufacturer to avoid delays in production and delivery.
6. How can I ensure intellectual property protection when sourcing from China?
Intellectual property protection is a crucial consideration when sourcing from China. It is recommended to work with manufacturers who have a solid reputation for respecting intellectual property rights or have experience working with clients from your country. Sign Non-Disclosure Agreements (NDAs) and enforceable contracts to protect your designs, patent applications, and proprietary information. Consulting with legal experts in intellectual property law can provide additional guidance and protection.
In conclusion, sourcing and manufacturing custom plastic injection molding in China can be an advantageous option, offering cost-effectiveness, advanced manufacturing capabilities, and a robust supply chain. However, thorough research, due diligence, and proper management of the sourcing process are crucial to ensure finding reliable manufacturers and protect intellectual property rights.
Why contact sourcifychina.com get free quota from reliable custom plastic injection molding suppliers?
Sourcifychina.com offers free quota from reliable custom plastic injection molding suppliers to provide businesses with an easy and efficient way to connect with trustworthy manufacturers in China for their injection molding needs. By offering this free quota service, Sourcifychina.com aims to provide several benefits to businesses:
1. Cost-saving advantage: Finding suitable manufacturers for custom plastic injection molding can be a tedious and time-consuming process. Sourcifychina.com helps businesses save time and money by connecting them directly with reliable suppliers, eliminating the need for extensive research and negotiations.
2. Reliable supplier network: Sourcifychina.com has established a network of reliable custom plastic injection molding suppliers in China. These manufacturers are pre-vetted to ensure high-quality production and excellent manufacturing capabilities. By accessing this network, businesses can be confident in the reliability and professionalism of the suppliers they choose.
3. Streamlined communication: Sourcifychina.com acts as a bridge between businesses and suppliers, facilitating efficient communication throughout the sourcing and manufacturing process. Through their platform, businesses can easily communicate their requirements and specifications, ensuring that their needs are accurately understood by the suppliers.
4. Transparency and accountability: Sourcifychina.com maintains transparency in the sourcing process. They provide businesses with detailed quotes and information about the suppliers, allowing them to make informed decisions. In addition, Sourcifychina.com monitors supplier performance, ensuring that suppliers adhere to quality standards and meet delivery deadlines.
5. Sourcing expertise: Sourcifychina.com has a team of sourcing experts who understand the complexities of the Chinese manufacturing market. They possess extensive knowledge and experience in the injection molding industry, enabling them to effectively match businesses with the most suitable suppliers based on their specific requirements.
In conclusion, Sourcifychina.com offers businesses an opportunity to connect with reliable custom plastic injection molding suppliers in China through their free quota service. This service aims to save businesses time, money, and effort while ensuring transparency, accountability, and high-quality manufacturing.