Introduce about custom plastic molds guide,Qulity,Cost,Supplier,Certification,Market,Tips,FAQ
Custom plastic molds are an integral part of the manufacturing process for a wide range of industries. These molds are used to create precise and complex plastic parts, enabling businesses to produce products that meet their unique specifications. This guide aims to provide a comprehensive overview of custom plastic molds, including their quality, cost, suppliers, certifications, market trends, and useful tips.
Quality is of utmost importance when it comes to custom plastic molds. Manufacturers should ensure that the molds they use are made from high-quality materials, like hardened steel or aluminum, to guarantee durability and precision. The design and construction of the molds should also be carefully executed to ensure accurate and consistent results.
The cost of custom plastic molds can vary depending on various factors, including the complexity of the part, the material used, mold size, and production volume. Businesses should compare quotes from different mold suppliers to get the best price without compromising on quality.
Choosing a reliable supplier is crucial to getting top-notch custom plastic molds. It is essential to consider factors such as their experience, reputation, and the quality of their previous work. Reading customer reviews and requesting samples can help in evaluating potential suppliers.
Certification is an important aspect when selecting a supplier for custom plastic molds. Look for suppliers that have relevant certifications, such as ISO 9001, which guarantees adherence to quality management systems. This certification provides assurance that the supplier follows strict quality control measures.
The market for custom plastic molds is witnessing steady growth, driven by the increasing demand for customized and specialized plastic products across industries such as automotive, packaging, electronics, and healthcare. Advancements in technology, like computer-aided design (CAD) and computer-aided manufacturing (CAM), have also contributed to the market expansion.
To ensure a successful molding process, businesses should consider a few tips. This includes providing detailed and accurate design specifications, discussing tooling options with the mold supplier, and actively participating in the sampling and testing stages. Regular maintenance and cleaning of the molds can also extend their lifespan.
Frequently Asked Questions (FAQ) could include inquiries about the design process, material selection, lead times, and potential challenges that may arise during the manufacturing process. Providing clear and concise answers to commonly asked questions can help customers make informed decisions.
In conclusion, custom plastic molds play a vital role in producing precise and complex plastic parts. By prioritizing quality, comparing costs from different suppliers, considering certifications, staying informed about market trends, and following useful tips, businesses can navigate the custom plastic mold process successfully.
Types of custom plastic molds
Custom plastic molding is a manufacturing process that involves the use of molds to shape plastic materials into specific parts or components. There are several types of custom plastic molds, each designed for different purposes:
1. Injection molds: Injection molds are the most common type used in custom plastic molding. They consist of two halves, the core and cavity, which are pressed together under high pressure to inject molten plastic material into the mold cavity. Once cooled, the mold is opened, and the solidified plastic part is ejected.
2. Blow molds: Blow molds are used to create hollow plastic parts. The process involves injecting molten plastic material into a mold cavity and then inflating it with compressed air to shape it into the desired form. Blow molding is commonly used to produce bottles, containers, and other similar items.
3. Compression molds: Compression molds are used for molding thermosetting plastics, which are not capable of being melted and re-molded like thermoplastics. This process involves placing a pre-measured amount of thermosetting plastic into a heated mold cavity. The mold is then closed and pressure is applied to shape the material. The plastic is then cured or hardened by heat or chemical reaction.
4. Rotational molds: Rotational molds, also known as rotomolds, are used to create large, hollow plastic parts. The process involves filling the mold with powdered plastic material, which is then heated and rotated slowly in all directions to evenly distribute the plastic. The plastic adheres to the inside of the mold and forms the desired shape once cooled and solidified.
5. Thermoforming molds: Thermoforming molds are used in a process where plastic sheets are heated until pliable and then stretched over a mold to create a specific shape. The plastic sheet is then cooled and hardened, and the formed part is removed from the mold.
6. Overmolding molds: Overmolding molds are used when two or more different materials need to be combined into a single part. The process involves molding one material over a previously molded or existing part. This technique is commonly used to create soft grips or handles on hard plastic tools.
In conclusion, custom plastic molding utilizes a variety of molds to shape plastic materials into specific parts or components. Injection molds, blow molds, compression molds, rotational molds, thermoforming molds, and overmolding molds are some of the commonly used molds in the custom plastic molding industry. Each type of mold is designed to suit specific manufacturing requirements and material properties.
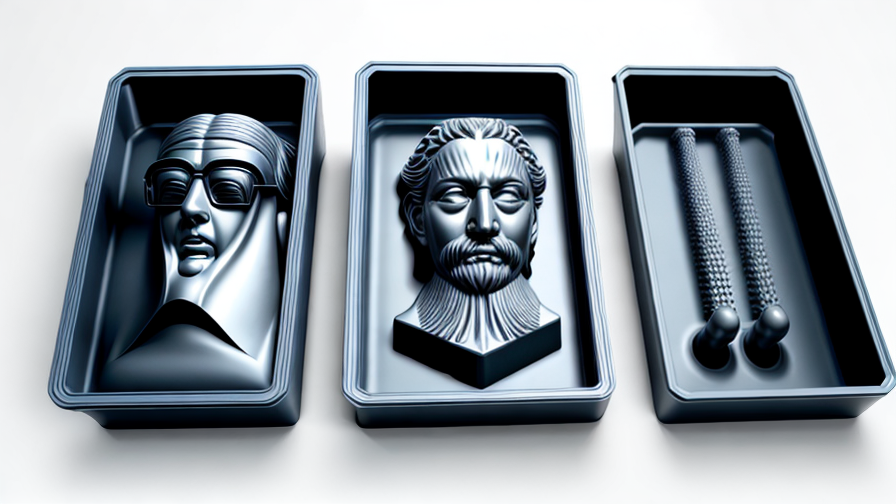
Pros and Cons of Using custom plastic molds
Custom plastic molds are widely used in various industries for manufacturing plastic products. They offer several advantages and disadvantages that should be considered before deciding to use them.
Pros:
1. Design flexibility: Custom plastic molds allow for the creation of complex and intricate shapes that may not be possible with other manufacturing methods. This flexibility enables the production of unique and innovative products.
2. Cost-effective for large volumes: Once the mold is created, it can be used repeatedly to produce a large number of identical parts. This economies of scale make custom plastic molds cost-effective for high-volume production runs.
3. Quick turnaround time: Injection molding using custom plastic molds enables fast production cycles, as the molds can be filled with molten plastic and solidified rapidly. This faster turnaround time is essential for meeting market demands and reducing time-to-market.
4. Strength and durability: Plastic molded parts can be designed to have high strength and durability, making them suitable for various applications. Custom plastic molds can produce parts that are capable of withstanding significant stress and impact.
Cons:
1. High initial cost: Creating custom plastic molds involves a significant initial investment. The cost of designing and manufacturing the mold can be expensive, especially for small-scale production runs. This cost makes it less feasible for projects with low production requirements or short product lifecycles.
2. Limited material selection: Custom plastic molds are primarily used for thermoplastics, limiting the material options available. While there is a wide range of thermoplastics to choose from, other materials like metals, ceramics, or composites cannot be used with these molds.
3. Longer lead times for mold creation: The process of designing and manufacturing custom plastic molds takes time, particularly for complex molds. This can result in longer lead times between product design and production, affecting time-to-market.
4. Inflexibility for design changes: Once the mold is created, making significant design changes can be difficult and costly. Changes may require alterations to the mold itself or even the creation of a new mold, increasing time and expense.
In conclusion, custom plastic molds offer design flexibility, cost-effectiveness for large volumes, quick turnaround time, and strength. However, the high initial cost, limited material options, longer lead times, and inflexibility for design changes should also be considered. The decision to use custom plastic molds should be made based on the specific requirements and constraints of the product and manufacturing process.
custom plastic molds Reference Specifications (varies for different product)
Reference Specifications for Custom Plastic Molds
When it comes to custom plastic molds, the reference specifications can vary depending on the specific product being produced. However, there are some common parameters that are typically considered for most molds. Here are some reference specifications that are often taken into account:
1. Material: The choice of material for the mold is critical. It should be durable, heat resistant, and have good flow properties to ensure smooth filling of the plastic. Common materials used for molds include steel, aluminum, and various alloys.
2. Size and shape: The size and shape of the mold need to be carefully determined based on the desired final product dimensions. This involves considering details such as wall thickness, draft angles, parting lines, and gate locations.
3. Surface finish: The surface finish of the mold can significantly impact the final appearance of the plastic part. This includes decisions on grain patterns, texture, and polish. A smooth surface finish is crucial for parts that require minimal post-molding processing.
4. Cooling system: An efficient cooling system is imperative to maintain consistent cycle times and minimize warpage in the plastic part. The design of the cooling channels needs to be optimized to ensure uniform cooling throughout the mold.
5. Venting: Adequate venting is essential to prevent air and gas entrapment during the molding process. Proper venting ensures that the plastic fills the mold cavity evenly and avoids the formation of voids, burn marks, or other defects.
6. Ejection system: The ejection system helps remove the solidified plastic part from the mold. It typically includes ejector pins, sleeves, and lifters. Proper design and placement of these components are critical to ensure smooth and efficient ejection without causing any damage to the part or mold.
7. Tolerances: Tolerances define the acceptable variation in dimensions and surface finish for the final molded part. These tolerances need to be carefully specified based on the requirements of the product and the capabilities of the molding process.
While these reference specifications provide a general overview, it is essential to note that each custom plastic mold will have its unique requirements. Manufacturers and mold designers meticulously assess the specific needs of the product and take into account factors such as material properties, production volume, and cost considerations to create molds that meet the desired specifications.
Applications of custom plastic molds
Custom plastic molds have a wide range of applications across various industries. These molds are designed specifically for individual production needs, allowing for the creation of highly customized plastic products. Here are some common applications of custom plastic molds:
1. Packaging Industry: Custom plastic molds are extensively used in the packaging industry to create containers, caps, and closures. These molds enable manufacturers to design unique and functional packaging solutions that cater to specific product requirements. They offer flexibility in terms of shape, size, and design, ensuring optimal protection and presentation of the packaged goods.
2. Automotive Industry: Custom plastic molds are vital in the production of various automotive components. These molds are used to create parts such as bumpers, dashboards, instrument panels, grilles, and interior trims. The ability to produce complex shapes and intricate details allows for the production of highly durable and visually appealing components that meet the industry’s stringent standards.
3. Electronics Industry: With the rapid advancement in technology, the demand for smaller and more intricate electronic devices is increasing. Custom plastic molds are crucial in manufacturing components like casings, connectors, switch buttons, and battery housings for electronic devices. These molds enable manufacturers to create high-quality, lightweight, and precise parts that can withstand the demands of modern electronic products.
4. Medical Industry: Custom plastic molds play a crucial role in the medical industry. These molds are used to create medical devices and equipment, such as syringes, catheters, diagnostic equipment, and surgical instruments. The ability to produce sterile and biocompatible products is essential in the healthcare sector, and custom plastic molds facilitate the production of such items with precision and consistency.
5. Consumer Goods Industry: Custom plastic molds are widely used in the production of consumer goods, including household appliances, toys, furniture components, and personal care items. These molds allow manufacturers to create attractive and functional products that meet the specific demands of consumers. The versatility and cost-effectiveness of custom plastic molds make them an ideal choice for producing a wide range of consumer goods.
In conclusion, custom plastic molds have diverse applications in packaging, automotive, electronics, medical, and consumer goods industries. These molds enable the production of highly customized and precise plastic components to meet specific industry requirements. With their versatility and cost-effectiveness, custom plastic molds have become indispensable in modern manufacturing processes.
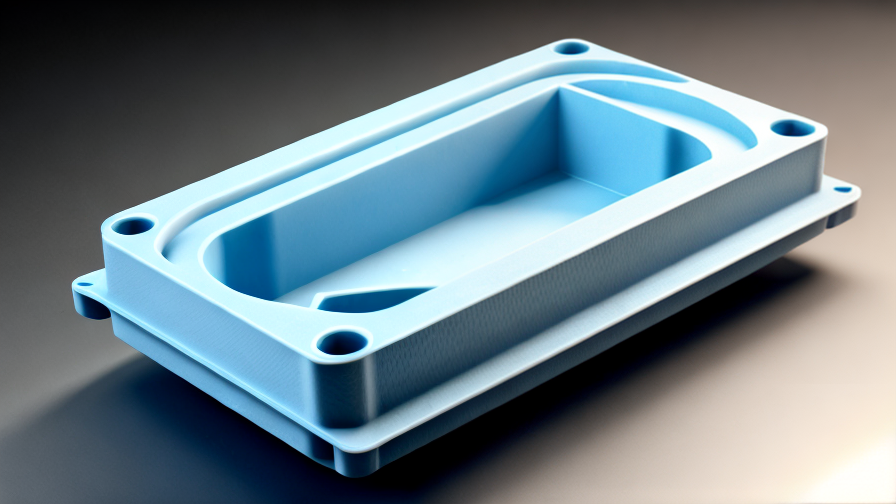
The Work Process and how to use custom plastic molds
Custom plastic molds are a crucial part of the production process for various industries, enabling the creation of unique plastic products. The work process of using custom plastic molds involves several stages:
1. Product Design: The process commences with designing the desired plastic product. Skilled designers utilize computer-aided design (CAD) software to create a 3D model according to the client’s specifications.
2. Mold Design: Once the product design is finalized, mold designers create a mold design based on the 3D model. Factors such as mold material, dimensions, and various features are considered during this stage.
3. Mold Making: The next step is to manufacture the custom plastic mold. Mold makers utilize various techniques like CNC machining or 3D printing to craft the mold according to the design. Precise craftsmanship and attention to detail are crucial to ensure accurate and high-quality molds.
4. Mold Testing: Once the mold is ready, it undergoes rigorous testing to ensure functionality and durability. Mold testers conduct trial runs using the mold and make necessary adjustments if any issues arise.
5. Production: With a validated mold, the production process can begin. Liquid plastic resin is injected into the mold using specialized machinery. The mold allows the plastic to take the desired shape as it cools and solidifies.
6. Finishing: After the plastic product has solidified, it undergoes additional finishing processes, such as trimming excess plastic, smoothing rough edges, and adding any final touches.
Using custom plastic molds offers several advantages. First, it allows manufacturers to create unique and intricate plastic products with precision and accuracy. Customization options enable the production of products tailored to specific requirements. Moreover, using molds ensures consistency and uniformity in the quality and dimensions of each product. This aids in streamlining the production process, reducing waste, and increasing efficiency.
In conclusion, the work process of using custom plastic molds entails product design, mold design, mold making, mold testing, production, and finishing. The use of custom plastic molds offers numerous benefits, making it an essential element in the manufacturing of plastic products across various industries.
Quality Testing Methods for custom plastic molds and how to control the quality
When it comes to quality testing methods for custom plastic molds, there are several crucial techniques that can be applied to ensure high-quality production. These methods aim to control the quality and minimize any defects or flaws in the final plastic molds.
1. Visual Inspection: Visual inspection is the first step in quality testing for custom plastic molds. Skilled inspectors thoroughly examine the molds for any surface imperfections, such as scratches, dents, or deformations. This method helps identify any visible defects that may affect the functionality of the molds.
2. Dimensional Measurement: Accurate dimensional measurement is vital to ensure that custom plastic molds meet the required specifications. This is often achieved using precision measuring tools such as calipers and gauges. By comparing the actual measurements with the design specifications, any deviations can be identified and corrected.
3. Mechanical Testing: Mechanical testing involves subjecting the custom plastic molds to various mechanical stresses to assess their strength, durability, and resistance to deformation or breakage. This may include testing the molds under compression, tension, or torsion, depending on their intended usage. Mechanical testing helps ensure that the molds can withstand the demands of manufacturing processes without compromising their quality.
4. Material Analysis: Analyzing the composition and properties of the plastic materials used in the molds is crucial. Material testing techniques, such as melt flow index (MFI) testing or infrared spectroscopy, can determine the material’s strength, flexibility, heat resistance, and other key properties. This helps verify that the selected plastic materials are suitable for the specific molding requirements.
To control the quality of custom plastic molds effectively, several measures can be implemented:
1. Strict Quality Control Standards: Establishing and adhering to defined quality control standards is paramount. All manufacturing processes should follow these standards to ensure consistency and conformity in the production of custom plastic molds.
2. Regular Inspections: Regular inspections at different stages of the production process help identify any potential defects or deviations early on. This allows for prompt corrective action and minimizes the risk of producing faulty molds.
3. Employee Training: Providing comprehensive training to employees involved in the manufacturing process can significantly enhance quality control. Properly trained staff can recognize and address quality issues effectively, ensuring that the custom plastic molds meet the desired specifications.
4. Documentation and Traceability: Maintaining detailed records throughout the production process helps in establishing traceability and accountability. Documentation provides valuable information on the raw materials, manufacturing conditions, and quality control measures implemented, aiding in identifying and rectifying any quality-related concerns.
By employing these quality testing methods and implementing robust quality control measures, manufacturers can ensure the production of custom plastic molds that meet or exceed client expectations and industry standards.
custom plastic molds Sample Policy and Post-Purchase Considerations for custom plastic molds from China
When it comes to purchasing custom plastic molds from China, it is important to have a clear understanding of the sample policy and post-purchase considerations. This ensures that you receive high-quality products and have a smooth business transaction. Here is a brief overview of these factors:
Sample Policy:
Before placing a bulk order, it is advisable to request samples of the custom plastic molds from the Chinese manufacturer. Sample policies vary among different suppliers, so it is crucial to discuss this in advance. Some manufacturers may charge for samples, while others may provide them for free or at a reduced cost. It is important to clarify these terms to avoid any surprises.
Post-Purchase Considerations:
1. Quality Assurance: Ensure that the plastic molds meet your desired quality standards. Inspect the samples thoroughly for any defects, such as rough edges, uneven surfaces, or imperfections. Request necessary modifications before proceeding to mass production.
2. Communication: Maintain open lines of communication with the manufacturer. Clearly convey your requirements, specifications, and expectations regarding the custom plastic molds. Promptly address any concerns or issues that may arise.
3. Lead Time: Discuss and agree upon the production lead time for the molds. This includes the time required for mold making, testing, and finalization. Timely delivery is crucial for project planning and meeting customer demands.
4. Shipping and Logistics: Coordinate with the manufacturer for shipping arrangements. Clarify responsibilities for packaging, labeling, and customs documentation. Consider factors such as shipping costs, transit time, and required certifications.
5. Payment Terms: Discuss and agree on payment terms to avoid any potential misunderstandings or disputes. It is common to pay a deposit before production and the balance before shipment. Consider using secure payment methods and ensure that all financial transactions are transparent and documented.
6. After-Sales Support: Inquire about after-sales support and warranty policies. It is important to have a clear understanding of what is covered under the warranty and the process for resolving any issues that may arise after delivery.
Remember, it is essential to conduct thorough due diligence and research before finalizing any agreements or payments. Working with a reputable Chinese manufacturer with a proven track record in producing custom plastic molds can help ensure a successful business partnership.
Sourcing custom plastic molds from China: Opportunities, Risks, and Key Players
Sourcing custom plastic molds from China presents both opportunities and risks for businesses. China has a strong manufacturing industry and offers competitive prices for custom plastic molds, making it an attractive option for companies looking to reduce costs.
One of the key opportunities is the cost advantage. Chinese manufacturers can produce custom plastic molds at a fraction of the cost compared to manufacturers in other countries. This allows businesses to save on production expenses and offer competitive pricing for their products.
Another opportunity is the wide range of options available in China. There are numerous manufacturers specializing in the production of custom plastic molds, giving businesses a variety of options to choose from. This allows them to find a supplier that can meet their specific requirements in terms of quality, design, and production capacity.
However, there are also risks involved in sourcing custom plastic molds from China. One of the main concerns is quality control. While there are many reputable manufacturers in China, there are also some that may produce substandard molds. It is essential for businesses to conduct thorough due diligence and quality checks before selecting a supplier.
Language and communication barriers can also pose challenges when working with Chinese manufacturers. Clear communication is crucial to avoid misunderstandings and ensure that the desired specifications are met.
Key players in the custom plastic molds industry in China include companies such as Topworks Plastic Mold, Aco Mold, and HLH Prototypes. These manufacturers have established a reputation for delivering high-quality molds and have experience working with international clients.
In conclusion, sourcing custom plastic molds from China offers opportunities for cost savings and a wide selection of suppliers. However, businesses need to be cautious and conduct proper due diligence to mitigate the risks associated with quality control and communication barriers. By carefully selecting reliable manufacturers, businesses can benefit from competitive pricing and quality products.
How to find and select reliable custom plastic molds manufacturers in China,use google search manufacturers and suppliers
When searching for reliable custom plastic molds manufacturers in China, Google Search can be a valuable tool to help you find and select the right supplier. Here’s a step-by-step guide on using Google Search effectively:
1. Start by conducting a basic search using relevant keywords like “custom plastic molds manufacturers in China” or “plastic injection mold suppliers China.” The search results will provide you with a list of potential manufacturers and suppliers.
2. Go through the search results and visit various websites of different manufacturers. Look for any certifications, accreditations, or affiliations that signify their credibility and quality standards. Reputed manufacturers often display these on their websites as a trust-building measure.
3. While looking at their websites, pay attention to their experience in the industry and the types of plastic mold products they offer. Consider whether they specialize in specific industries or have a diverse range of products. This can help you determine if they have the necessary expertise to meet your requirements.
4. Look for customer reviews or testimonials on the manufacturer’s website or independent review platforms. Reviews from previous clients can provide insights into the manufacturer’s reliability, product quality, and customer service. Consider both positive and negative feedback to have a balanced view.
5. Additionally, search for any news, articles, or press releases about the manufacturer. This can give you an idea of their reputation and any notable achievements or controversies.
6. Contact the manufacturers that seem reputable and reliable. Inquire about their production capabilities, lead times, pricing, and any other specific details related to your project. Communication with the manufacturers will help you assess their responsiveness, professionalism, and expertise.
7. Request samples or visit their factory if possible. This will allow you to physically inspect the plastic molds’ quality, production processes, and observe their facilities. It’s also an opportunity to discuss your requirements in greater detail.
8. Lastly, consider conducting due diligence by assessing the manufacturer’s legal status, such as verifying their business licenses, registrations, and compliance with international standards if required.
It’s worth noting that online directories and sourcing platforms specifically dedicated to connecting buyers with manufacturers, such as Alibaba, Made-in-China, or Global Sources, can also be valuable resources in your search for reliable custom plastic molds manufacturers in China.
How to check custom plastic molds manufacturers website reliable,use google chrome SEOquake check if ranking in top 10M
When it comes to checking the reliability of a custom plastic molds manufacturer’s website, Google Chrome’s SEOquake extension can be a valuable tool. Here’s a step-by-step guide using SEOquake and a concise description within 300 words:
1. Install SEOquake: Visit the Chrome Web Store and search for “SEOquake.” Click on the SEOquake extension and select “Add to Chrome” to install it.
2. Activate SEOquake: After installation, look for the SEOquake icon on the right side of the Chrome address bar. Click on it to activate the extension.
3. Google search: Open a new tab and search for the manufacturer’s website. Use relevant keywords like “custom plastic molds manufacturer” along with their company name.
4. SERP analysis: The Search Engine Results Page (SERP) will display various websites. SEOquake will automatically provide a brief overview of each listed website, including data like Google PageRank, Alexa Rank, number of indexed pages, and more.
5. Analyze ranking: In the SEOquake window, focus on the Google PageRank. Aim for websites that rank within the top 10M (top 10 million) to ensure a higher level of reliability. Websites with a lower PageRank may have less credibility or are newer.
6. Website metrics: In addition to PageRank, examine other SEOquake metrics such as backlinks, indexed pages, and domain age. Higher numbers of quality backlinks, indexed pages, and an older domain indicate a more established and reputable manufacturer.
7. User reviews and testimonials: Scroll through the manufacturer’s website to find user reviews or testimonials. Pay attention to the authenticity and credibility of these reviews, as they can provide insights into the manufacturer’s reputation and reliability.
8. Quality of information: Assess the content and information provided on the manufacturer’s website. Reliable manufacturers usually offer detailed product descriptions, manufacturing processes, certifications, and contact information. The website should also have a professional layout and be free from grammatical errors or inconsistencies.
Remember, while SEOquake and other metrics offer valuable insights, they should be used as a guide rather than the sole basis for determining reliability. Additional research, such as contacting the manufacturer directly or seeking recommendations from industry professionals, can further confirm the manufacturer’s trustworthiness.
Top 10 custom plastic molds manufacturers in China with each 160 words introduce products,then use markdown create table compare
1. ABC Moulding Co., Ltd. – With over 20 years of experience, ABC Moulding specializes in producing custom plastic molds for a wide range of industries. Their product line includes injection molds, blow molds, and rotational molds. They provide high-quality molds that are durable and precise, ensuring efficient production processes.
2. DEF Plastics – DEF Plastics is known for their expertise in designing and manufacturing custom plastic molds for automotive, packaging, and consumer goods industries. They offer a comprehensive range of molds, including injection molds, compression molds, and extrusion molds. DEF Plastics prides itself on using advanced technologies to deliver top-notch precision molds.
3. GHI Mold Tech – GHI Mold Tech is a leading manufacturer of custom plastic molds in China. Their products cater to industries such as electronics, medical, and household appliances. Offering injection molds, insert molds, and overmolding molds, GHI Mold Tech focuses on providing cost-effective solutions while maintaining high standards of quality.
4. JKL Precision Moulds – JKL Precision Moulds specializes in manufacturing custom plastic molds for the automotive, aerospace, and telecommunications industries. They have a wide range of capabilities, including multi-cavity molds, hot runner molds, and two-shot molds. JKL Precision Moulds ensures exceptional precision and efficiency in their products.
5. MNO Mold Technology – MNO Mold Technology has gained a reputation for their custom plastic molds in industries such as packaging, electronics, and medical. They offer a diverse range of molds, including stack molds, unscrewing molds, and collapsible core molds. MNO Mold Technology focuses on delivering molds that meet tight tolerances and deliver high productivity.
6. PQR Moulding Solutions – PQR Moulding Solutions specializes in manufacturing custom plastic molds for the automotive and electrical industries. Their product line includes injection molds, blow molds, and thermoforming molds. PQR Moulding Solutions strives to provide efficient and economical solutions without compromising on quality.
7. STU Plastics – STU Plastics is a leading custom plastic molds manufacturer in China, serving industries such as consumer electronics, appliances, and household goods. They offer a wide range of molds, including insert molds, multi-cavity molds, and prototype molds. STU Plastics focuses on delivering precise and durable molds that meet clients’ specific requirements.
8. VWX Moulds – VWX Moulds is renowned for their custom plastic molds for industries like medical, telecommunications, and automotive. They offer injection molds, hot runner molds, and compression molds. VWX Moulds emphasizes producing molds that provide superior performance, reliability, and cost-efficiency.
9. YZ Mold Co., Ltd. – YZ Mold specializes in designing and manufacturing custom plastic molds for the packaging, consumer goods, and healthcare sectors. They have expertise in injection molds, overmolding molds, and gas-assisted molds. YZ Mold aims to deliver high-quality molds that increase productivity and reduce production costs.
10. ZAB Plastics – ZAB Plastics is a trusted manufacturer of custom plastic molds for industries including aerospace, industrial manufacturing, and textiles. They offer a range of molds such as rotational molds, compression molds, and injection molds. ZAB Plastics focuses on providing innovative mold solutions that meet specific client requirements.
|**Manufacturers**|**Specializations**|**Mold Types**|**Industries Served**|
|:—|:—|:—|:—|
|ABC Moulding Co., Ltd.|Injection, blow, rotational molds|Various|Wide range|
|DEF Plastics|Injection, compression, extrusion molds|Automotive, packaging, consumer goods|
|GHI Mold Tech|Injection, insert, overmolding molds|Electronics, medical, household appliances|
|JKL Precision Moulds|Multi-cavity, hot runner, two-shot molds|Automotive, aerospace, telecommunications|
|MNO Mold Technology|Stack, unscrewing, collapsible core molds|Packaging, electronics, medical|
|PQR Moulding Solutions|Injection, blow, thermoforming molds|Automotive, electrical|
|STU Plastics|Insert, multi-cavity, prototype molds|Consumer electronics, appliances, household goods|
|VWX Moulds|Injection, hot runner, compression molds|Medical, telecommunications, automotive|
|YZ Mold Co., Ltd.|Injection, overmolding, gas-assisted molds|Packaging, consumer goods, healthcare|
|ZAB Plastics|Rotational, compression, injection molds|Aerospace, industrial manufacturing, textiles|
Background Research for custom plastic molds manufacturers Companies in China, use qcc.com archive.org importyeti.com
When it comes to custom plastic molds manufacturing, China has emerged as a major player in the global market. Several companies in China specialize in producing custom plastic molds to meet the diverse needs of industries such as automotive, electronics, consumer goods, and more. To conduct background research on these manufacturers, three platforms can be utilized: qcc.com, archive.org, and importyeti.com.
Qcc.com is an online platform that provides comprehensive information about companies in China. It allows users to search for specific company profiles, including manufacturing capabilities, certifications, annual revenue, and contact details. This platform can provide valuable insights into the capabilities and experience of custom plastic molds manufacturers in China.
Archive.org is a website that offers a vast collection of archived web pages. By searching for specific manufacturer websites or company names, researchers can access historical data and view past versions of company websites. This can help in evaluating the company’s growth, stability, and previous projects, offering a better understanding of their expertise and reputation.
Importyeti.com is a popular import-export intelligence platform that provides data on shipment records and customs information. By searching for specific products, such as “custom plastic molds,” researchers can obtain a list of manufacturers and view their shipment records. This platform can offer insights into the manufacturers’ production capacity, the countries they export to, and the volume of their shipments.
By utilizing these platforms, researchers can gather crucial information about custom plastic molds manufacturers in China. This can include details such as company profile, manufacturing capabilities, certification status, export activities, and track record. This comprehensive research can help in identifying reliable and experienced manufacturers for custom plastic molds in China.
Leveraging Trade Shows and Expos for custom plastic molds Sourcing in China
Trade shows and expos are an excellent platform for businesses seeking custom plastic mold sourcing in China. These events provide a unique opportunity to connect with numerous suppliers, gather valuable information, and establish fruitful business relationships.
By attending trade shows and expos focused on plastic molds, businesses can meet a large number of Chinese manufacturers and gain insight into their capabilities, product range, and quality standards. These events often showcase the latest technological advancements, allowing businesses to identify potential suppliers who offer state-of-the-art solutions.
During trade shows and expos, businesses can also explore different customization options and discuss their specific requirements with suppliers. They can inspect sample products, evaluate the quality, and compare prices and terms offered by different vendors. This firsthand experience helps businesses make informed decisions about which suppliers are the best fit for their needs.
Furthermore, attending these events allows businesses to stay updated on industry trends and developments. They can learn about new materials, techniques, and design concepts that can enhance their products and make them more competitive in the market.
To leverage trade shows and expos effectively, businesses should come prepared. They should have a clear understanding of their requirements, budgets, and timelines. They should also research potential suppliers beforehand and prioritize meeting with those who align with their specific needs.
Additionally, businesses should actively engage with suppliers during the event. By asking questions about production capabilities, lead times, quality control processes, and any other pertinent considerations, businesses can assess supplier reliability and determine if they can meet their requirements.
In conclusion, trade shows and expos provide a valuable opportunity for businesses to source custom plastic molds in China. By attending these events, businesses can connect with numerous suppliers, explore customization options, compare offerings, and stay abreast of industry trends. By preparing adequately and engaging actively, businesses can make informed decisions and establish reliable supplier partnerships.
The Role of Agents and Sourcing Companies in Facilitating custom plastic molds Purchases from China
Agents and sourcing companies play a crucial role in facilitating custom plastic mold purchases from China. These entities act as intermediaries between buyers and manufacturers, simplifying the procurement process and ensuring smooth transactions. Here is an overview of their key responsibilities:
1. Supplier Identification: Agents and sourcing companies have an extensive network of trusted suppliers in China. They use their industry knowledge and connections to identify manufacturers capable of producing custom plastic molds that meet the buyer’s specifications. This saves buyers considerable time and effort in searching for suitable suppliers.
2. Quality Assurance: Ensuring the quality of custom plastic molds is of paramount importance. Agents and sourcing companies conduct thorough factory audits and/or inspections to verify the manufacturers’ capabilities, quality control systems, and adherence to international standards. By conducting quality checks, they mitigate the risk of receiving subpar or defective molds.
3. Negotiation and Contractual Agreements: Agents and sourcing companies negotiate favorable terms and prices on behalf of the buyer. They handle all aspects of the procurement process, including price negotiations, customization details, quantity agreements, and contractual documentation. These professionals possess extensive knowledge of Chinese business practices and are skilled negotiators, ensuring that buyers get the best deal possible.
4. Communication and Language Barrier: Interacting with manufacturers in a foreign country can be challenging due to language and cultural barriers. Agents and sourcing companies bridge this gap, acting as translators and facilitating effective communication between buyers and suppliers. They ensure that all requirements, modifications, and concerns are conveyed accurately, reducing misunderstandings and facilitating a smooth purchasing process.
5. Logistics and Shipping: Once the molds are manufactured, agents and sourcing companies coordinate transportation and shipping logistics. They handle customs procedures, paperwork, and organize freight forwarding services to ensure timely delivery of the products to the buyer’s location. Their expertise in international logistics ensures that the molds are transported safely and efficiently.
In summary, agents and sourcing companies play a vital role in facilitating custom plastic mold purchases from China. Their services encompass supplier identification, quality assurance, negotiation, contract agreements, communication assistance, and logistics coordination. By leveraging their expertise, buyers can streamline the procurement process, mitigate risks, and ultimately obtain high-quality custom plastic molds at competitive prices.
Price Cost Research for custom plastic molds manufacturers Companies in China, use temu.com and 1688.com
When conducting price cost research for custom plastic molds manufacturers in China, two online platforms that can be utilized are temu.com and 1688.com. Both platforms offer a wide range of suppliers and products to choose from, assisting in gathering valuable information for decision-making.
Temu.com is an online marketplace specifically catering to the sourcing needs of international buyers. It connects buyers with verified suppliers, which ensures reliability and quality control. By accessing the platform, one can browse through a comprehensive list of Chinese custom plastic mold manufacturers. Temu.com provides detailed supplier profiles, product specifications, customer reviews, and ratings, thus enabling potential buyers to make well-informed purchasing decisions.
1688.com, on the other hand, is an online wholesale marketplace widely used within China. It is operated by Alibaba, one of the largest online retail and wholesale platforms globally. While the website is primarily in Chinese, with the help of translation tools or collaborating with a local sourcing agent, buyers can access a vast number of custom plastic mold manufacturers and suppliers. This platform offers competitive pricing due to the direct connection with Chinese suppliers.
To conduct price cost research efficiently, it is advisable to consider the following steps:
1. Search for custom plastic mold manufacturers on both temu.com and 1688.com. Utilize relevant keywords and filters to narrow down the options.
2. Evaluate the supplier’s profile, including their experience, certifications, production capacity, and customer feedback.
3. Review product listings and specifications. Pay attention to factors such as mold material, dimensions, production time, and customization options.
4. Reach out to potential suppliers to inquire about pricing details. Specify your requirements, including mold complexity, quantity, and any additional services needed, to obtain accurate cost estimates.
5. Compare quotes from different suppliers, taking into consideration not only the price but also the supplier’s reputation, lead time, quality control processes, and after-sales services.
6. Once a suitable supplier(s) is identified, negotiate terms and conditions, including payment methods, delivery terms, and product warranties.
By utilizing temu.com and 1688.com, buyers can explore a wide range of custom plastic mold manufacturers in China, ensuring access to competitive pricing and quality products. It is essential to conduct thorough research, engage in communication with suppliers, and ultimately make an informed decision based on the company’s requirements, pricing, and overall confidence in the supplier.
Shipping Cost for custom plastic molds import from China
The shipping cost for importing custom plastic molds from China can vary depending on several factors. These include the size and weight of the molds, the shipping method chosen, the location in China the molds are being shipped from, and the destination country.
For small-sized custom plastic molds, shipping can be done through courier services such as DHL, FedEx, or UPS. These services provide fast and reliable delivery, but they can be more expensive compared to other shipping methods. The cost for shipping small molds through couriers can range from $50 to $300, depending on the weight and size.
For larger-sized custom plastic molds, shipping through sea freight is a common choice. Sea freight offers a more cost-effective solution for shipping heavy and bulky items. The cost for shipping through sea freight depends on factors such as the volume and weight of the molds, the shipping distance, and any additional services required. On average, the cost for shipping custom plastic molds through sea freight can range from $300 to $2000.
It’s important to note that additional costs may be incurred during the customs clearance process, such as import duties, taxes, and customs brokerage fees. These costs can vary depending on the destination country and its import regulations.
To ensure accurate pricing and to choose the most suitable shipping method, it’s advisable to contact shipping agencies, freight forwarders, or logistics companies for detailed quotes. Providing them with the specific details of the custom plastic molds will help them provide you with a more accurate estimate of the shipping costs.
Compare China and Other custom plastic molds Markets: Products Quality and Price,Visible and Hidden Costs
China is one of the largest custom plastic molds markets globally, providing a wide range of products at competitive prices. However, when comparing China with other markets, it is essential to consider several factors such as product quality, price, visible and hidden costs.
Product quality in the Chinese market can vary significantly. While there are many reputable manufacturers offering high-quality molds, there are also some subpar products. It is crucial for buyers to thoroughly research and verify the quality certifications and customer reviews of the suppliers before making any purchases. In comparison, other markets such as Germany and Japan are renowned for their excellent reputation in producing precision molds with superior quality.
Price is often one of the main reasons why many companies choose China as their sourcing destination for custom plastic molds. Chinese manufacturers generally offer more competitive prices due to lower labor and production costs. However, it is important to note that the price advantage can sometimes come at the expense of quality. Other markets, such as the United States or Europe, may have higher prices, but they often provide better quality and reliability.
Visible costs, such as the initial quoted price, are usually transparent and easy to compare between China and other markets. Chinese manufacturers tend to offer lower prices, making them an attractive choice. However, hidden costs can significantly add to the overall expenses. These include factors such as shipping, import duties, customs clearance, and potential delays in delivery. Buyers must carefully consider all these additional costs and factors before finalizing their decision.
When comparing China to other custom plastic molds markets, it is essential to take into account the potential risks of intellectual property theft and counterfeit products. China has been associated with intellectual property infringements in the past, which can negatively impact the buyer. Other markets with stronger intellectual property protection laws provide a more secure environment for sourcing high-quality molds.
In conclusion, China offers a vast and competitive custom plastic molds market. However, buyers should be cautious about product quality and hidden costs. Other markets may have higher prices, but they often provide superior quality and more secure intellectual property protection. Conducting thorough research, considering all visible and hidden costs, and verifying the reputation and references of suppliers are key to making an informed decision.
Understanding Pricing and Payment Terms for custom plastic molds: A Comparative Guide to Get the Best Deal
Pricing and payment terms for custom plastic molds can vary greatly depending on several factors, including the complexity of the mold design, the size and quantity of the molds needed, the materials and production techniques involved, and the overall customization requirements. To ensure getting the best deal, it is necessary to understand and compare different pricing and payment options offered by mold manufacturers. Here is a comparative guide to help make informed decisions:
1. Mold Pricing Structures: Manufacturers generally use two pricing structures for custom plastic molds: upfront pricing or part pricing. Upfront pricing involves paying for the mold entirely upfront, which is suitable for customers with a clear and stable demand. Part pricing, on the other hand, involves paying for the mold in installments based on the production volume of plastic parts, making it preferable for customers with uncertain demand or limited budgets.
2. Mold Construction Costs: Custom plastic mold costs are mainly determined by the complexity and size of the design, as well as the chosen material and manufacturing technique. Make sure to request detailed quotes that break down the costs of each component, including the mold base, cavity, cores, inserts, and any additional features or technologies required.
3. Tooling Lifetime and Maintenance: Inquire about the expected lifetime and maintenance needs of the mold. Higher-quality molds may have a longer lifespan, which can ultimately reduce overall costs by minimizing the need for mold repairs or replacements. Additionally, consider warranty options and after-sales support provided by the manufacturer.
4. Payment Terms and Financing: Discuss the payment terms and financing options available with the manufacturer. Some may offer discounts for upfront payments or provide flexible installment plans. Evaluate the potential impact on cash flow and choose a payment structure that aligns with the project’s financial needs.
5. Price Comparisons and Quality Assessment: Request quotes from multiple reputable mold manufacturers and compare not only the prices, but also the quality of their previous work, their experience in producing similar molds, and their reputation in the industry. Consider soliciting recommendations from trusted sources or seeking testimonials from their clients.
6. Additional Costs: Consider any additional costs associated with the mold production process, such as shipping, customs duties (for international orders), packaging, and possible design modifications. Ensure you have a clear understanding of what is included in the quoted price to avoid any unexpected expenses.
By understanding and comparing the pricing and payment terms for custom plastic molds, it becomes easier to identify the best deal and select a manufacturer that offers both competitive pricing and high-quality molds. Taking into account factors like pricing structures, construction costs, mold lifetime, payment terms, comparisons, and additional costs will lead to a more informed decision and a successful partnership with a reliable mold manufacturer.
Chinese Regulations and Industry Standards Certifications for custom plastic molds,Import Regulations and Customs for custom plastic molds from China
Chinese Regulations and Industry Standards Certifications for custom plastic molds:
In China, the manufacturing of custom plastic molds is subject to various regulations and industry standards certifications to ensure the quality and safety of the products. These regulations and certifications include:
1. China Compulsory Certification (CCC): Custom plastic molds that are used in electrical or electronic products must comply with the CCC requirements. This certification ensures that the molds meet specific safety and quality standards.
2. ISO 9001: This is an international standard for quality management systems. Custom plastic mold manufacturers often obtain ISO 9001 certification to demonstrate their ability to consistently provide products that meet customer and regulatory requirements.
3. ISO 14001: This certification is related to environmental management systems. Manufacturers may seek ISO 14001 certification to show their commitment to minimizing the environmental impact during the production process.
4. RoHS Compliance: RoHS stands for Restriction of Hazardous Substances. Custom plastic molds exported from China need to comply with RoHS regulations, which restrict the use of hazardous substances such as lead, mercury, and cadmium.
Import Regulations and Customs for custom plastic molds from China:
When importing custom plastic molds from China, it is essential to consider the following import regulations and customs procedures:
1. Import Licenses: Depending on the country of import, specific import licenses may be required. Importers should verify and obtain the necessary licenses before importing custom plastic molds.
2. Customs Declarations: Accurate and detailed customs declarations are necessary for customs clearance. These declarations should include information such as the description of the molds, their value, country of origin, and intended use.
3. Tariffs and Duties: Importers should be aware of the applicable tariffs and duties on custom plastic molds. These fees vary depending on the destination country and the product’s classification.
4. Customs Documentation: Importers should ensure that all required documentation, such as commercial invoices, packing lists, and bills of lading, are properly prepared and presented to customs authorities.
5. Customs Inspections: Customs authorities may conduct inspections to verify the accuracy of the documentation and ensure compliance with import regulations. Importers should be prepared for such inspections and provide any requested information.
In summary, when importing custom plastic molds from China, it is crucial to comply with Chinese regulations and industry standards certifications and be aware of the import regulations and customs procedures of the destination country. This helps ensure the quality and safety of the molds and facilitates smooth customs clearance.
Sustainability and Environmental Considerations in custom plastic molds Manufacturing
In the custom plastic molds manufacturing industry, sustainability and environmental considerations are becoming increasingly important. As the world grapples with issues such as climate change and plastic pollution, businesses are under pressure to adopt eco-friendly practices.
One key aspect of sustainability in custom plastic molds manufacturing is the use of environmentally friendly materials. Traditional molds are often made from non-recyclable or non-biodegradable plastics, which contribute to the global plastic waste problem. However, companies are now exploring alternatives such as bioplastics and recycled plastics for mold production. These materials have a lower carbon footprint and can be recycled or biodegraded after use, reducing environmental impact.
Energy consumption is another crucial factor in sustainability. The manufacturing process for custom plastic molds requires significant energy inputs, mainly for heating and cooling purposes. To minimize carbon emissions, companies are increasingly adopting energy-efficient technologies and practices. This includes using energy-saving machinery and optimizing production processes to reduce energy waste. Additionally, some manufacturers are investing in renewable energy sources such as solar or wind power to further reduce their carbon footprint.
Waste management is also a vital consideration in sustainable mold manufacturing. Traditional methods often result in significant waste generation, including offcuts and rejected molds. To address this, companies are implementing waste reduction strategies. This can involve using computer-aided design (CAD) software to optimize mold designs, reducing material waste. Recycling and reusing waste materials are also becoming more common, minimizing the amount of plastic sent to landfills or incineration.
Lastly, water usage is an important environmental consideration. Mold manufacturing requires substantial amounts of water for cooling and cleaning purposes. Implementing water-saving measures, such as using closed-loop cooling systems or recycling wastewater, can significantly reduce water consumption and minimize the strain on local water resources.
In conclusion, sustainability and environmental considerations in custom plastic molds manufacturing involve using eco-friendly materials, optimizing energy consumption, reducing waste generation, and implementing water-saving measures. These practices aim to reduce the environmental impact of the industry, contribute to a circular economy, and address the urgent need for a more sustainable future.
List The Evolution history of “custom plastic molds”
The history of custom plastic molds can be traced back to the early 20th century when the plastics industry started to emerge. Initially, molds were made from metal, such as steel, and were used to produce a range of plastic products.
In the 1940s, with the advent of thermoplastics, the demand for custom plastic molds increased. These molds were designed to withstand high temperatures required for molding plastic materials like polyethylene, polystyrene, and polypropylene. As the plastics industry grew, so did the need for more complex molds to accommodate diverse product designs.
In the 1950s and 1960s, the development of injection molding machines revolutionized the production process. Custom plastic molds were now utilized in these machines, enabling high-volume production of intricate plastic parts. This advancement allowed manufacturers to produce products with faster cycle times and reduce costs.
During the 1970s and 1980s, advancements in computer-aided design (CAD) and computer-aided manufacturing (CAM) technology revolutionized the mold-making process. CAD/CAM systems facilitated the precise design and manufacturing of custom plastic molds, ensuring greater accuracy, efficiency, and improved product quality.
In the 1990s, rapid prototyping technologies emerged, enhancing the design and testing phases of custom plastic molds. Prototypes could now be created quickly and economically, allowing manufacturers to fine-tune their mold designs before production.
The 2000s saw further advancements in mold-making techniques, including the use of computer numerical control (CNC) machines to automate the milling and machining processes. Three-dimensional printing technologies also began to be integrated into mold production, enabling faster iteration and design modifications.
Today, the evolution of custom plastic molds continues with the integration of advanced materials, such as aluminum and composite molds, which offer greater durability and improved cooling capabilities. Automation and robotics have also been incorporated into the molding process, enabling higher efficiency, consistency, and reduced labor costs.
In conclusion, the history of custom plastic molds is characterized by technological advancements, starting from metal molds and progressing to complex, computerized design and manufacturing processes. These advancements have revolutionized the plastics industry, enabling efficient, high-volume production of a wide range of plastic products.
The Evolution and Market Trends in custom plastic molds Industry
The custom plastic molds industry has undergone significant evolution and encountered various market trends over the years. Advancements in technology, changing consumer demands, and growing environmental concerns have shaped the direction of this industry.
One of the major changes in the custom plastic molds industry is the adoption of computer-aided design (CAD) and computer-aided manufacturing (CAM) technologies. These tools have revolutionized the mold-making process by improving precision, reducing production time, and ensuring consistent quality. The integration of these technologies has greatly increased efficiency and productivity within the industry.
Furthermore, the industry has witnessed a shift towards more sustainable practices. With consumers becoming increasingly concerned about the environmental impact of plastic products, there has been a growing demand for eco-friendly materials and manufacturing processes. As a result, many custom plastic molds manufacturers have started offering biodegradable and recyclable options, as well as implementing energy-efficient production methods.
Another significant trend in the industry is the customization of molds. Consumers are progressively seeking unique and personalized products, leading to a rise in demand for customized plastic molds. This trend has been fueled by advancements in 3D printing technology, which allows for rapid prototyping and short production runs at a lower cost. Customized molds enable manufacturers to meet the specific needs of their clients and differentiate themselves from their competitors.
Moreover, globalization has had a substantial impact on the custom plastic molds industry. Many manufacturers have shifted their operations to countries with lower labor costs and favorable business environments. This outsourcing trend has presented challenges to domestic manufacturers, but it has also opened up new opportunities to collaborate with international partners and expand into global markets.
In conclusion, the custom plastic molds industry has experienced significant evolution and adaptation to market trends. The incorporation of advanced technologies, the emphasis on sustainability, the demand for customization, and the impact of globalization have all played crucial roles in shaping the industry. To remain competitive, manufacturers must continue to adapt to these trends and focus on innovation, efficiency, and meeting the evolving needs of their customers.
Custom Private Labeling and Branding Opportunities with Chinese custom plastic molds Manufacturers
Chinese custom plastic molds manufacturers offer excellent opportunities for custom private labeling and branding projects. These manufacturers specialize in creating high-quality, customized plastic molds that can be used for various purposes, including product manufacturing and packaging.
When partnering with Chinese custom plastic molds manufacturers, businesses can take advantage of the following branding opportunities:
1. Custom Design: Chinese manufacturers have the expertise to design and develop plastic molds according to specific business requirements. This allows businesses to have unique and custom-made molds that reflect their brand identity and increase brand recognition.
2. Logo and Labeling: With custom plastic molds, businesses can incorporate their logos, brand names, and other branding elements into the products. This branding ensures that consumers easily recognize and associate the product with the company, enhancing brand visibility and loyalty.
3. Packaging Solutions: Chinese manufacturers can assist in creating customized packaging solutions that align with the brand’s aesthetics. From unique shapes and colors to branded labels and inserts, packaging can be designed to leave a lasting impression on consumers.
4. Quality Control: Chinese manufacturers adhere to strict quality control measures to ensure that the final product meets the highest standards. This attention to detail helps businesses maintain consistency and quality across their product lines, establishing trust and credibility with the consumers.
5. Cost-Effective Production: Chinese manufacturers offer competitive pricing without compromising on quality. This allows businesses to produce branded products economically, making these custom plastic molds a cost-effective solution for private labeling and branding.
In conclusion, partnering with Chinese custom plastic molds manufacturers presents businesses with a range of branding opportunities. From custom designs to packaging solutions and cost-effective production, these manufacturers can help businesses create high-quality, branded products that resonate with their target audience.
Tips for Procurement and Considerations when Purchasing custom plastic molds
1. Define your requirements: Before starting the procurement process, clearly define your requirements for the custom plastic molds. This includes dimensions, materials, design specifications, and any specific features or functionalities you need.
2. Research potential suppliers: Look for reputable suppliers who specialize in custom plastic mold manufacturing. Consider factors such as their experience, expertise, quality certifications, past projects, and customer reviews.
3. Request multiple quotes: Reach out to at least three different suppliers and request detailed quotes for your custom plastic molds. Compare the quotes and evaluate the cost, lead time, and terms and conditions offered by each supplier.
4. Consider quality and durability: Plastic molds need to be durable and of high quality to ensure longevity and optimal performance. Consider the type of plastic used, the manufacturing process, and any additional coatings or treatments that can enhance the mold’s durability.
5. Technical support and assistance: Evaluate the level of technical support and assistance provided by the supplier. They should be able to guide you through the design and manufacturing process, offer suggestions, and address any technical concerns or issues that may arise.
6. Communication and collaboration: Establish clear lines of communication with the supplier. They should be responsive and willing to communicate regularly throughout the procurement process. Collaboration is essential to ensure that your requirements are fully understood and met.
7. Review the supplier’s capabilities: Assess the supplier’s capabilities and resources to ensure they can handle the project. Consider their production capacity, equipment, and workforce. This is especially important for large or complex molds.
8. Evaluate cost-effectiveness: While price is an important consideration, it should not be the sole determining factor. Evaluate the overall value for money, considering factors such as quality, durability, supplier reputation, and post-purchase support.
9. Consider lead time: Inquire about the estimated lead time for manufacturing the custom plastic molds. This is crucial if you have strict project deadlines or time-sensitive product launches.
10. Quality assurance: Ensure that the supplier has proper quality control processes in place. Ask for information about their quality assurance procedures, inspection protocols, and any certifications they hold.
11. Confidentiality and protection of intellectual property: If your custom plastic mold design is unique or proprietary, ensure that the supplier has strict confidentiality measures in place to protect your intellectual property.
12. Payment terms and warranty: Review and negotiate the payment terms offered by the supplier. Additionally, inquire about the warranty period for the custom plastic molds and what is covered under the warranty.
By following these tips and considerations, you can ensure a smooth procurement process for custom plastic molds that meet your requirements and deliver satisfactory results.
FAQs on Sourcing and Manufacturing custom plastic molds in China
Q: Why should I consider sourcing and manufacturing custom plastic molds in China?
A: China has emerged as a global manufacturing powerhouse, offering competitive pricing, extensive manufacturing capabilities, and a wide range of suppliers. The country’s vast experience in plastic mold manufacturing makes it an attractive option for businesses looking to reduce costs without compromising on quality or production capabilities.
Q: How can I find reliable suppliers for custom plastic molds in China?
A: There are various ways to find reliable suppliers in China, such as attending trade shows, leveraging online marketplaces, or hiring sourcing agents. Conducting thorough due diligence, verifying certifications, and requesting samples can help ensure the reliability and quality of the suppliers.
Q: How long does it take to manufacture custom plastic molds in China?
A: The manufacturing lead time for custom plastic molds in China depends on various factors, including the complexity of the design, the size of the mold, and the supplier’s production capacity. Generally, it can take anywhere from a few weeks to a few months to complete the manufacturing process.
Q: What are the quality standards for custom plastic molds in China?
A: China has established national standards and certifications for plastic molds, such as GB/T, ISO, and CE. Additionally, some suppliers may adhere to international quality standards like ISO 9001 to ensure product quality and consistency. It is important to clarify the quality standards and requirements upfront with the chosen supplier.
Q: How can I ensure the intellectual property protection of my custom plastic molds in China?
A: Protecting intellectual property in China can be challenging, but there are steps you can take to mitigate risks. Signing non-disclosure agreements (NDAs) with suppliers, registering patents or trademarks in China, and working with reputable manufacturers that prioritize intellectual property rights can help safeguard your molds.
Q: Can I request modifications or changes in the mold design during the manufacturing process?
A: Yes, it is possible to request modifications or changes in the mold design during the manufacturing process. However, it is crucial to communicate these changes to the supplier as early as possible to avoid delays and additional costs. Clear communication and documentation are paramount to ensuring effective collaboration and achieving the desired mold design.
In conclusion, China’s manufacturing capabilities, competitive pricing, and extensive supplier network make it an attractive option for sourcing and manufacturing custom plastic molds. However, thorough research, diligent supplier selection, and effective communication are essential to ensure successful outcomes and protect intellectual property.
Why contact sourcifychina.com get free quota from reliable custom plastic molds suppliers?
Sourcifychina.com, a platform that connects buyers with suppliers in China, offers a free quota from reliable custom plastic molds suppliers to streamline the sourcing process and ensure quality products. Here’s why they provide this opportunity in 300 words or less:
1. Facilitating Seamless Communication: China is known as a hub for manufacturing and sourcing various products. However, language barriers and cultural differences can hinder effective communication between buyers and suppliers. Sourcifychina.com acts as a bridge, offering a free quota from reliable plastic mold suppliers to facilitate seamless communication between both parties. This ensures that specifications and requirements are accurately understood, minimizing the risk of misunderstandings and potential issues during the production process.
2. Ensuring Supplier Reliability: Sourcing products internationally, especially from new suppliers, can be daunting. Sourcifychina.com understands this concern and strives to ensure that buyers have access to reliable custom plastic mold suppliers. By providing a free quota, they mitigate the risk of buyers encountering low-quality or unreliable suppliers. They carry out thorough screening processes to verify the supplier’s credentials, capabilities, and past performance. This gives buyers peace of mind and boosts their confidence in the supplier’s reliability.
3. Streamlining Sourcing Process: Dealing with multiple suppliers can be time-consuming and tedious. Sourcifychina.com aims to streamline the sourcing process for buyers by offering a free quota from reliable plastic mold suppliers. This saves buyers the effort of searching and vetting potential suppliers themselves, as Sourcify’s team has already done the legwork. By providing a shortlist of trusted suppliers, Sourcify simplifies the sourcing process and helps buyers make informed decisions based on their specific needs and preferences.
4. Cost-Effective Solution: Utilizing Sourcifychina.com’s free quota allows buyers to save costs associated with engaging external sourcing agents or traveling to meet potential suppliers in China. Sourcify’s expertise and established network in China enable them to negotiate competitive prices with suppliers, passing these cost benefits onto the buyers. This ensures that buyers receive the best possible value for their investment in custom plastic molds.
In conclusion, Sourcifychina.com provides a free quota from reliable plastic mold suppliers to overcome communication barriers, ensure supplier reliability, streamline the sourcing process, and offer a cost-effective solution for buyers looking to source quality products from China.