Introduce about cutting machine for metal guide,Qulity,Cost,Supplier,Certification,Market,Tips,FAQ
A cutting machine for metal is a powerful tool used in various industries for precise and efficient cutting of different types of metals. This guide aims to provide an overview of the key aspects related to such machines, including their quality, cost, suppliers, certifications, market trends, and some tips and FAQs.
Quality: The quality of a cutting machine for metal depends on various factors such as the manufacturer’s expertise, materials used, precision of cutting, and durability. Look for machines with solid construction, advanced technology, and positive customer reviews to ensure high-quality performance.
Cost: The cost of cutting machines for metal can vary significantly depending on their size, capacity, and features. There are budget-friendly options available for small-scale operations, as well as high-end, industrial-grade machines that come at a higher price point. Consider your specific requirements and budget constraints before making a purchase.
Supplier: Numerous suppliers offer cutting machines for metal. It is essential to research and select a reputable supplier known for delivering reliable products, excellent customer service, and timely support. Look for suppliers with a strong track record in the industry.
Certification: Ensure that the cutting machine you choose complies with relevant certifications and safety standards. Look for certifications such as ISO (International Organization for Standardization) and CE (Conformité Européene) to ensure that the machine meets industry standards and safety regulations.
Market: The market for cutting machines for metal is rapidly growing due to the increasing demand in industries such as automotive, aerospace, construction, and manufacturing. Keep an eye on market trends and innovations to stay updated with the latest advancements and opportunities.
Tips: Before purchasing a cutting machine for metal, carefully assess your cutting needs, including the type and thickness of metals you will be working with. Consider factors such as cutting speed, accuracy, maintenance requirements, and after-sales support. Additionally, familiarize yourself with the machine’s features, controls, and safety precautions to ensure optimal performance and user safety.
FAQs:
– What are the common types of cutting machines for metal?
– What is the maximum thickness of metal that a cutting machine can handle?
– How often should the machine be serviced?
– Can the machine handle different shapes and sizes of metal?
– What safety precautions should I follow when operating the machine?
In conclusion, a cutting machine for metal is a versatile and indispensable tool used in various industries. By considering factors such as quality, cost, suppliers, certifications, market trends, and following the given tips and FAQs, you can make an informed decision while purchasing and operating such machines effectively.
Types of cutting machine for metal
There are several types of cutting machines used for metalworking. The choice of machine depends on the type and thickness of the metal being cut, as well as the desired cutting method and overall production requirements. Here are some common types of cutting machines for metal:
1. Bandsaws: Bandsaws use a continuous band of toothed metal to cut through metal. They can be horizontal or vertical, with the horizontal type being more common. Bandsaws offer high cutting speeds and precision, making them suitable for cutting various types of metal.
2. Plasma Cutters: Plasma cutters use ionized gas to cut through electrically conductive metals. The high-velocity gas jet melts the metal and blows away the molten material, resulting in a clean cut. Plasma cutters provide fast cutting speeds and can handle thicker metal plates.
3. Laser Cutters: Laser cutters use a high-powered laser beam to melt, burn, or vaporize the metal. The concentrated laser energy delivers precise and clean cuts, and it can be used to cut intricate patterns. Laser cutting is commonly used for thin and medium-thickness metal sheets.
4. Waterjet Cutters: Waterjet cutting machines use a high-pressure jet of water mixed with an abrasive substance to cut through metal. The highly pressurized water stream erodes the metal, resulting in a smooth and precise cut. Waterjet cutting can effectively handle thick metal sheets and reflective materials.
5. Shearing Machines: Shearing machines use blades to cut through metal sheets. The blades close against a fixed lower blade, shearing the metal in between. Shearing machines are used for straight cuts in thin and medium-thickness metal sheets.
6. Punching Machines: Punching machines use specialized tools to punch holes or shapes into metal sheets. They are commonly used in mass production applications and can create consistent and precise cuts.
7. CNC Machining Centers: CNC (Computer Numerical Control) machining centers use computer-controlled tools to cut, drill, and shape metal parts. They offer high precision and can perform various cutting operations, making them versatile for different metalworking tasks.
These are just some of the types of cutting machines used in metalworking. Each machine has its own advantages and limitations, so it’s important to choose the appropriate machine based on the specific metal cutting requirements.
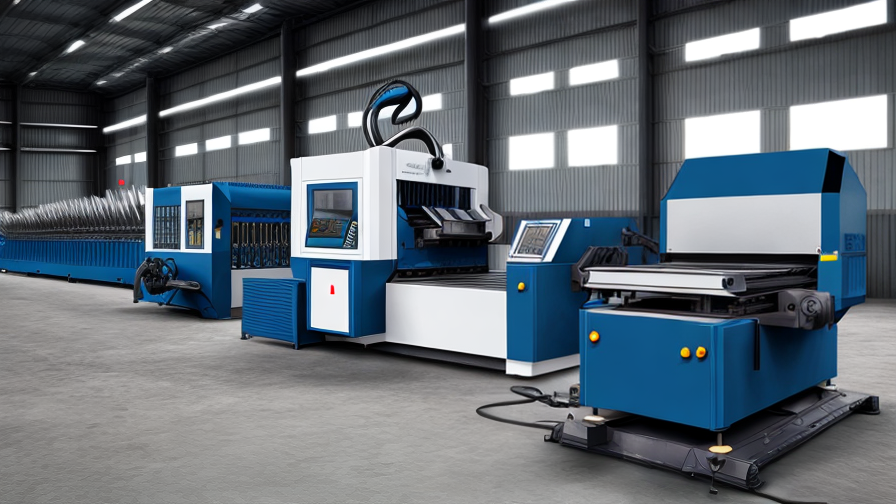
Pros and Cons of Using cutting machine for metal
Using a cutting machine for metal can offer several advantages, as well as some potential drawbacks. Here are the pros and cons of using a cutting machine for metal:
Pros:
1. Precision and accuracy: Cutting machines utilize advanced technology and computerized controls, enabling them to make precise and accurate cuts. This is particularly important when working with complex metal shapes or intricate designs.
2. Increased productivity: Cutting machines can significantly increase productivity, as they are capable of making multiple cuts in a short period. This is particularly beneficial for large-scale projects or industries that require high production rates.
3. Time and cost-saving: By automating the cutting process, a cutting machine can reduce labor costs and overall production time. It eliminates the need for manual handling of materials and reduces human error, leading to cost savings in the long run.
4. Versatility: Cutting machines can often be programmed to cut various types of metals, ranging from stainless steel to aluminum and copper. This versatility makes them suitable for a wide range of applications across different industries.
Cons:
1. Initial investment: Purchasing a cutting machine can be a significant upfront investment. These machines often come with a high price tag, especially if advanced features or additional accessories are required. This can be a deterrent for small businesses or individuals on a tight budget.
2. Training and maintenance: Operating a cutting machine for metal requires specialized training to ensure safe and efficient use. In addition, regular maintenance is crucial to keep the machine in optimal condition. Both training and maintenance can add to the overall operating costs.
3. Limited mobility: Cutting machines are typically large and bulky, which can limit their mobility. They are often stationary and require a dedicated workspace, making them less suitable for on-site or mobile cutting needs.
4. Noise and environmental impact: Cutting machines can produce high levels of noise during operation, which can be a concern for the well-being of operators and surrounding workers. Additionally, some cutting processes generate fumes or debris, which may require additional safety measures or ventilation systems.
In conclusion, utilizing a cutting machine for metal can offer numerous benefits, including enhanced precision, increased productivity, and time and cost savings. However, it also presents certain drawbacks, such as the initial investment, training requirements, limited mobility, and potential environmental impacts. Careful consideration of these pros and cons is necessary to determine whether using a cutting machine for metal is the right choice for a specific application or business.
cutting machine for metal Reference Specifications (varies for different product)
Metal cutting machines are versatile tools used in various industries to precisely cut different types of metals. These machines are designed to offer high efficiency and accuracy, ensuring clean and smooth cuts. The reference specifications of metal cutting machines can vary depending on the specific product, but here are some common features found in these machines:
1. Power and Speed: Metal cutting machines are equipped with powerful motors and high-speed cutting tools. The power output ranges from small machines requiring a few kilowatts to larger industrial models requiring several hundred kilowatts. High cutting speeds ensure faster processing times.
2. Cutting Capacity: The cutting capacity of metal cutting machines varies based on the product. Some machines can cut through thick metal sheets, while others specialize in precision cutting of thin materials. The cutting capacity is typically specified in terms of the maximum thickness of the metal that can be cut.
3. Cutting Method: There are various cutting methods used in metal cutting machines. These include sawing, laser cutting, plasma cutting, water jet cutting, and abrasive cutting. The choice of cutting method depends on the materials being cut, their thickness, and the desired precision.
4. Control System: Metal cutting machines are integrated with advanced control systems for precise cutting. These control systems may include computer numerical control (CNC) technology, which allows for automated and programmable cutting operations. CNC machines can follow complex cutting paths with high accuracy.
5. Safety Features: Safety is a crucial aspect of metal cutting machines. They are equipped with safety features like emergency stop buttons, safety interlocks, shields, and sensors to prevent accidents and injuries during operation.
6. Maintenance and Durability: Metal cutting machines are built to be durable and withstand harsh working conditions. Regular maintenance is required to keep the machines in optimal condition and ensure their longevity.
7. Additional Features: Some metal cutting machines may offer additional features such as automatic material feeding, integrated cooling systems, and integrated workpiece clamping mechanisms. These features enhance productivity and ease of operation.
It’s important to consult the specific product’s specifications while considering a metal cutting machine as they can significantly vary based on the manufacturer and intended application.
Applications of cutting machine for metal
Cutting machines for metal are widely used in various industries for a range of applications. These machines use advanced technology to cut through metal sheets, bars, pipes, and other metallic materials with precision and efficiency. Here are a few common applications of cutting machines for metal:
1. Fabrication: Metal cutting machines are extensively used in fabrication processes to cut metals into desired shapes and sizes. They are utilized in industries like construction, automotive, aerospace, and more, where metal structures or components need to be manufactured.
2. Metalworking: Metalworking industries such as forging, welding, and machining also employ cutting machines to shape metal materials. These machines are used to cut out intricate patterns, chamfer edges, or create precision cuts for welding joints.
3. Industrial manufacturing: Cutting machines for metal are crucial in industrial manufacturing processes, where precise and efficient cutting is essential. They enable bulk production of metal components, machine parts, and various products made from metals.
4. Automotive industry: The automotive sector heavily relies on metal cutting machines for the production of car body parts, engine components, and other metal structures. These machines enable precise and consistent cutting, contributing to the overall quality and safety of vehicles.
5. Shipbuilding: Cutting machines for metal play a significant role in shipbuilding, where large metal sheets and plates need to be cut. These machines ensure accurate and smooth cuts for assembling different sections of the ship, including decks, bulkheads, and hulls.
6. HVAC industry: Heating, ventilation, and air conditioning (HVAC) systems often require metal components that need to be cut to specific dimensions. Cutting machines aid in the manufacturing of ductwork, pipes, and other metal parts used in HVAC systems.
7. Construction industry: Metal cutting machines are widely used in the construction industry to prepare and shape structural steel components for buildings, bridges, and other infrastructure projects. They enable the fabrication of beams, columns, trusses, and other metal elements required in construction.
8. Metal recycling: Metal cutting machines are also utilized in the recycling industry to process scrap metal into reusable materials. These machines help in cutting, shredding, and separating different types of metals, making the recycling process more efficient and cost-effective.
In conclusion, cutting machines for metal have numerous applications across various industries. They are indispensable for fabrication, metalworking, industrial manufacturing, automotive and shipbuilding industries, as well as in HVAC, construction, and metal recycling sectors. With their ability to deliver precise and efficient cutting, they contribute to the advancement and productivity of these industries.
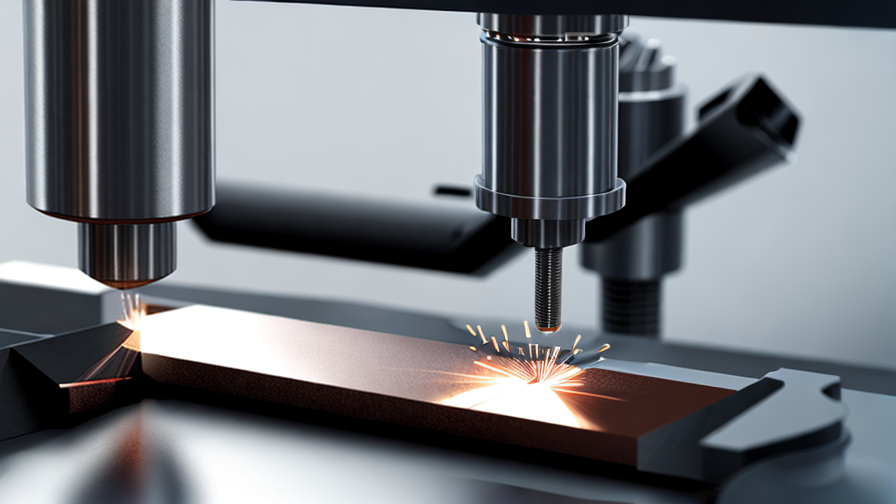
The Work Process and how to use cutting machine for metal
The work process of using a cutting machine for metal involves several steps. Firstly, it is important to ensure that the machine is set up correctly and all safety protocols are followed. This includes checking that the machine is properly secured and that the cutting blade is in good condition.
Once the machine is ready, the metal piece to be cut is placed on the cutting table or held securely in a vise. The operator then selects the appropriate cutting blade for the task at hand. Different blades may be required depending on the thickness and type of metal being cut.
Next, the operator adjusts the settings on the cutting machine, such as the cutting speed and feed rate, to achieve the desired cutting outcome. It is important to set these parameters accurately to ensure a precise and clean cut. The operator must also ensure that the metal piece is positioned correctly to align with the cutting blade.
Once everything is set, the cutting process begins. The operator carefully guides the metal piece through the cutting blade, ensuring a smooth and even movement. It is crucial to maintain a steady pace and apply consistent pressure to achieve a clean and accurate cut. The operator should always be mindful of safety and wear appropriate protective gear such as gloves, goggles, and ear protection.
After the cut is complete, the machine is turned off and the metal piece is inspected for any rough edges or burrs. These can be smoothed out using a file or other finishing tools if necessary. Finally, the cut metal piece is ready for further processing or to be used as desired.
In summary, using a cutting machine for metal involves setting up the machine correctly, selecting the appropriate cutting blade, adjusting the machine settings, guiding the metal piece through the cutting blade, inspecting for smoothness, and finishing the cut as necessary. It is important to follow safety guidelines and operate the machine with caution to achieve accurate and high-quality cuts.
Quality Testing Methods for cutting machine for metal and how to control the quality
Quality testing methods for a cutting machine for metal play a crucial role in ensuring that the machine functions efficiently, accurately, and safely. Several testing approaches are commonly employed to assess the quality of such machines.
Firstly, performance testing is vital to determine if the cutting machine meets the desired specifications and requirements. This involves conducting tests to evaluate factors such as the cutting speed, accuracy, and precision. Machine operators should measure and assess how well the cutting machine performs in terms of speed, as well as its ability to achieve precise cuts, without any deviation or error.
Secondly, material testing is necessary to ensure that the cutting machine can handle various types of metals effectively. Different metals have different properties, such as hardness, thickness, and toughness. The cutting machine should be tested using a variety of metal materials to assess its capability to cut through them efficiently and without any issues.
Furthermore, safety testing is paramount to control the quality of the cutting machine. This involves evaluating whether the machine has adequate safety features such as emergency stop buttons, safety guards, and automatic shut-off mechanisms. It is crucial to ensure that the cutting machine operates in a safe manner to prevent accidents and injuries.
To control the quality of the cutting machine, regular maintenance and inspections are essential. This includes conducting routine checks of the machine’s parts, verifying that they are in good condition and are functioning correctly. Additionally, calibration and alignment tests should be performed periodically to ensure the machine’s accuracy and precision are maintained.
Quality control in the manufacturing process is also crucial to ensure that the cutting machine meets the required standards. This involves implementing a robust quality management system, which includes techniques such as statistical process control (SPC) and lean manufacturing principles. SPC involves monitoring and controlling the manufacturing process to ensure that it remains within specified limits, reducing variations and defects. Lean manufacturing principles focus on eliminating waste and continuously improving processes to enhance quality and efficiency.
In conclusion, quality testing methods for cutting machines for metal involve performance testing, material testing, and safety testing. Regular maintenance, inspections, calibration, and alignment are necessary to control quality. Implementing a comprehensive quality management system and utilizing techniques like SPC and lean manufacturing principles also contribute to ensuring high-quality cutting machines.
cutting machine for metal Sample Policy and Post-Purchase Considerations for cutting machine for metal from China
Sample Policy:
1. Sample availability: Before making a bulk order, it is essential to request samples of the cutting machine for metal from the Chinese supplier. The supplier should be capable of providing samples for evaluation and testing purposes.
2. Sample cost: Some suppliers may provide samples free of charge, while others may charge a nominal fee or require the customer to bear shipping costs. It is advisable to clarify the sample cost with the supplier beforehand to avoid any misunderstandings.
3. Sample delivery: The supplier should specify the estimated delivery time for the samples. It is crucial to assess whether the supplier delivers the samples promptly and without any damages.
4. Sample quality: The sample received should accurately represent the quality of the cutting machine for metal that will be delivered in bulk. It is essential to thoroughly evaluate the sample for its functionality, durability, and overall performance.
Post-Purchase Considerations:
1. Quality assurance: Once the order has been placed, it is crucial to establish a quality assurance mechanism with the supplier. This includes a discussion about warranty, after-sales service, and potential repair or replacement options in case of any defects or malfunctions.
2. Packaging and shipping: It is important to discuss packaging requirements with the supplier to ensure that the cutting machine for metal is adequately protected during transit. Shipping details, including the estimated delivery time, should also be confirmed.
3. Customs clearance and documentation: The supplier should assist in providing all necessary documents, such as commercial invoices, packing lists, and certificates of origin, to facilitate customs clearance. The supplier’s cooperation in this regard is crucial to avoid any unnecessary delays or complications.
4. Payment terms and methods: The agreed-upon payment terms, such as the amount and mode of payment, should be clearly communicated and complied with. It is advisable to use secure payment methods that offer protection to both parties.
In conclusion, when sourcing a cutting machine for metal from China, it is important to follow a sample policy that ensures thorough evaluation before proceeding with a bulk order. Additionally, post-purchase considerations such as quality assurance, packaging, shipping, customs clearance, and payment terms should all be carefully considered to ensure a smooth and successful transaction.
Sourcing cutting machine for metal from China: Opportunities, Risks, and Key Players
Sourcing a cutting machine for metal from China can present both opportunities and risks for businesses. China is known as a global manufacturing hub, offering a wide range of industrial equipment at competitive prices. The country has a robust infrastructure and a highly skilled workforce, making it a convenient source for various machinery, including metal cutting machines.
One of the key opportunities of sourcing a cutting machine for metal from China is cost savings. Chinese manufacturers often offer lower prices than their counterparts in other countries. This can be attributed to lower labor costs and economies of scale. By sourcing from China, businesses can potentially reduce their production costs and increase their profitability.
Moreover, China offers a vast selection of cutting machine options, providing businesses with ample choices to find the specific machine that meets their requirements. Whether it’s a laser cutting machine, plasma cutting machine, or waterjet cutting machine, Chinese manufacturers cater to various cutting technologies and can offer customization options.
However, there are also risks associated with sourcing from China. Quality control can be a concern, especially when dealing with numerous manufacturers. It is crucial to thoroughly research and vet potential suppliers to ensure they meet quality standards. Conducting factory visits, requesting product samples, and checking their certifications are all important steps in mitigating risks.
Another risk is intellectual property infringement. China has been criticized in the past for intellectual property violations. To safeguard their intellectual property, businesses should consider implementing legal protections, such as patents or trademarks, and work with reputable manufacturers that uphold intellectual property rights.
When it comes to key players in the metal cutting machine market in China, some well-known manufacturers include and are not limited to Amada Group, Bystronic Group, TRUMPF Group, and Rofin-Sinar Technologies. However, there are also numerous smaller manufacturers that provide equally competitive products.
In conclusion, sourcing a cutting machine for metal from China offers opportunities for cost savings, a wide selection of options, and customization. However, businesses should be aware of the associated risks, such as quality control and intellectual property infringement. Conducting thorough research, vetting suppliers, and implementing legal protections are essential steps in successful sourcing from China.
How to find and select reliable cutting machine for metal manufacturers in China,use google search manufacturers and suppliers
When searching for reliable cutting machine manufacturers in China, using Google search can be an effective method. Here are some steps to follow:
1. Begin by typing relevant keywords into the search bar, such as “metal cutting machine manufacturers in China” or “reliable cutting machine suppliers in China.” Adding specific details about the type of cutting machine you require can narrow down the search results.
2. Evaluate the search results and focus on the first few pages. Typically, reliable manufacturers tend to appear higher in the search results due to their strong online presence.
3. Visit the websites of a few manufacturers that catch your attention. Browse through their product catalog and look for detailed information about the cutting machines they offer. Take note of their experience, certifications, and customer testimonials.
4. Look for manufacturers who have been in the industry for a considerable period. Longevity often indicates their ability to provide reliable products and services. Ensure they have experience specifically in producing metal cutting machines.
5. Check if the manufacturer has relevant certifications and quality control measures in place, such as ISO certifications or CE compliance. These certifications ensure that the manufacturer adheres to international quality standards.
6. While on their website, search for information about their production process, technologies used, and quality management systems. Pay attention to details that assure precision, durability, and efficiency of their cutting machines.
7. It is beneficial to contact a few manufacturers directly to inquire about their products, manufacturing capabilities, and pricing. Communication with the manufacturer can help you assess their responsiveness and professionalism.
8. Seek recommendations from industry professionals or fellow buyers who have experience with purchasing cutting machines from China. They can provide insights into their experiences with different manufacturers.
By conducting thorough research and due diligence, you can find reliable cutting machine manufacturers in China who can provide high-quality products at competitive prices.
How to check cutting machine for metal manufacturers website reliable,use google chrome SEOquake check if ranking in top 10M
When looking for a reliable cutting machine manufacturer website for metal, there are a few steps you can take. One of the first things you can do is use Google Chrome and install the SEOquake extension. This tool allows you to check the website’s ranking in the top 10 million websites on the internet.
To begin, open Google Chrome and search for the cutting machine manufacturer you are interested in. Once you have found their website, click on the SEOquake extension icon located in the top-right corner of your browser. This will open a pop-up window providing you with various SEO-related data.
In the SEOquake pop-up, you will find the website’s Alexa Rank. Alexa Rank provides an estimate of the website’s popularity based on its traffic volume. If the manufacturer’s website has an Alexa Rank within the top 10 million, it indicates a relatively high level of traffic and could be considered reliable.
Additionally, you can scroll down in the SEOquake pop-up to find other valuable information about the website. This includes the number of indexed pages on Google, the number of backlinks it has, and its social media presence. A well-established and reliable manufacturer should have a considerable number of indexed pages and backlinks.
It is important to note that while using SEOquake to check website rankings and other data can provide some insights into a manufacturer’s reliability, it should not be the sole factor in determining their credibility. Considering customer reviews, certifications, quality of products, and customer support are equally important when assessing a manufacturer’s reliability.
In summary, to check the reliability of a cutting machine manufacturer’s website for metal, you can use Google Chrome’s SEOquake extension to determine its ranking within the top 10 million websites. This, coupled with other factors, can help you make an informed decision.
Top 10 cutting machine for metal manufacturers in China
1. Jinan Bodor CNC Machine Co., Ltd. – specializing in high-quality laser cutting machines for metal with exceptional precision and speed, Bodor offers a wide range of models suitable for various metal cutting applications.
2. Jiangsu Dalian CNC Machine Tool Co., Ltd. – renowned for their advanced CNC plasma cutting machines, Dalian CNC has a strong R&D team focused on producing reliable and efficient metal cutting solutions.
3. Hako CNC Machine (Anhui) Manufactory Co., Ltd. – recognized for their expertise in manufacturing CNC water jet cutting machines, Hako offers cutting-edge technology that delivers precise and smooth metal cutting results.
4. Shandong BCAMCNC Machinery Group Co., Ltd. – known for their high-performance fiber laser cutting machines, BCAMCNC offers reliable and durable solutions with improved cutting speeds and precision.
5. Wuhan Hans Goldensky Laser System Co., Ltd. – a leading provider of laser metal cutting machines, Hans Goldensky specializes in CO2, fiber, and YAG lasers, catering to a wide range of metal cutting needs.
6. Jinan Upbull Machinery Equipment Co., Ltd. – recognized for their innovative and efficient plasma cutting machines, Upbull Machinery offers cost-effective solutions with high cutting speeds and exceptional accuracy.
7. Suzhou Suntop Laser Technology Co., Ltd. – a well-established manufacturer of fiber laser cutting machines, Suntop Laser provides reliable solutions for precision metal cutting, incorporating advanced technology and user-friendly interfaces.
8. Hangzhou Yile Shangyun Robot Technology Co., Ltd. – specializing in CNC flame and plasma cutting machines, Yile Shangyun offers robust and durable solutions for efficient metal cutting, meeting diverse customer requirements.
9. Beijing Vmade CNC Machine Co., Ltd. – focusing on fiber and CO2 laser cutting machines, Vmade CNC emphasizes product performance, precision, and stability, delivering high-quality metal cutting solutions.
10. Anhui Leshi Intelligent Technology Co., Ltd. – known for their high-power laser cutting machines, Leshi provides a wide range of models suitable for various metal cutting applications, along with excellent after-sales service and technical support.
Note: This information is based on available data and may not be an exhaustive list. Further research is advised to gather comprehensive information about specific manufacturers.
Background Research for cutting machine for metal manufacturers Companies in China, use qcc.com archive.org importyeti.com
In China, the metal manufacturing industry has become a significant player in the global market. The country is known for its advanced technologies, cost-effective production, and a wide range of metal products. To meet the demands of this growing industry, many metal manufacturers in China rely on cutting machines, which play a vital role in achieving precise and efficient metal cutting operations.
Qcc.com provides comprehensive information about Chinese companies, including detailed profiles, product portfolios, and contact details. By searching specifically for metal manufacturers, one can easily find companies offering cutting machine solutions. This platform facilitates direct communication with manufacturers, enabling potential buyers to request quotes, compare products, and explore various options simultaneously.
Another useful platform is importyeti.com, which offers access to detailed import and export data. It allows researchers to find specific product categories, such as cutting machines for metal, and provides insights into which Chinese companies are exporting these machines globally. Import Yeti also provides information about the destination countries, which helps gauge the demand for cutting machines in different markets.
For a historical perspective or access to websites that might be no longer available, archive.org is a valuable resource. It allows users to browse archived web pages and retrieve information from past versions of websites. This feature is particularly useful for conducting research on Chinese metal manufacturers who may have changed their websites or removed valuable content.
Considering the limited word count, researchers can effectively utilize these platforms to gather essential information about metal cutting machine manufacturers in China. From qcc.com, users can find relevant company details, while importyeti.com offers import-export insights. For historical information or accessing websites that might not be available through regular means, archive.org can come in handy.
Leveraging Trade Shows and Expos for cutting machine for metal Sourcing in China
Leveraging trade shows and expos in China is an effective way to source cutting machines for metal. These events bring together a wide range of manufacturers, suppliers, and industry professionals, providing an opportunity to explore various options and make informed sourcing decisions.
By attending trade shows and expos focused on metalworking machinery, buyers can gain valuable insights into the latest technologies, innovations, and trends in the industry. These events often showcase a wide array of cutting machine options, allowing buyers to compare features, prices, and quality of different products.
Trade shows and expos also offer a platform for face-to-face interactions with manufacturers and suppliers. This facilitates the establishment of personal relationships and fosters open communication, which can be crucial in negotiating deals, discussing product specifications, and addressing any concerns or questions the buyer may have.
In addition to evaluating and comparing cutting machine options, trade shows and expos provide an opportunity to assess the credibility and reputation of potential suppliers. Buyers can gather information about the manufacturer’s background, production capabilities, certifications, and customer references, helping them make an informed decision when selecting a supplier.
Furthermore, attending these events allows buyers to stay up-to-date with the latest industry developments and advancements. Industry experts often conduct presentations, seminars, or demonstrations, providing valuable knowledge and insights about the use, maintenance, and optimization of cutting machines for metal.
To fully leverage trade shows and expos, buyers should come prepared with a clear understanding of their sourcing requirements, budget constraints, and desired product specifications. It is essential to conduct thorough research beforehand to identify the most relevant events and exhibitors.
In conclusion, trade shows and expos in China offer an excellent opportunity for buyers to source cutting machines for metal. These events provide a comprehensive platform to evaluate products, establish relationships with suppliers, and stay updated with the latest industry developments. By effectively utilizing these events, buyers can make informed sourcing decisions and find the most suitable cutting machine for their metalworking needs.
The Role of Agents and Sourcing Companies in Facilitating cutting machine for metal Purchases from China
Agents and sourcing companies play a vital role in facilitating cutting machine for metal purchases from China. These intermediaries bridge the gap between buyers and manufacturers, ensuring a smooth and efficient procurement process. Their expertise and local knowledge help buyers navigate the complexities of international trade, providing valuable support at every stage.
First and foremost, agents and sourcing companies help buyers identify reputable and reliable manufacturers in China. They have an extensive network of suppliers and can thoroughly assess the capabilities, quality standards, and production capacity of various manufacturers. This saves buyers significant time and effort in researching and vetting potential suppliers.
Furthermore, these intermediaries assist buyers in negotiating favorable prices and terms with manufacturers. They possess in-depth knowledge of product pricing, market trends, and local regulations. Leveraging this expertise, they can drive down costs and secure the best possible deals. Additionally, agents and sourcing companies can help buyers overcome language and cultural barriers, ensuring effective communication and understanding between both parties.
Agents and sourcing companies also play a crucial role in quality control and inspection. They can conduct pre-production inspections to assess the manufacturer’s capabilities and ensure they meet the buyer’s requirements. During production, regular inspections can be carried out to monitor quality standards and identify any issues early on. This ensures that the final products meet the buyer’s specifications and expectations.
Logistics and shipping arrangements are another area where agents and sourcing companies provide valuable assistance. They can handle the complex paperwork, documentation, and customs processes involved in international shipping. This includes arranging transportation, coordinating with freight forwarders, and ensuring compliance with import regulations. This streamlines the logistics process and helps buyers receive their cutting machines in a timely and hassle-free manner.
In conclusion, agents and sourcing companies play an indispensable role in facilitating cutting machine for metal purchases from China. Their expertise in identifying reliable manufacturers, negotiating favorable prices, ensuring quality control, and managing logistics greatly simplifies the procurement process for buyers. By leveraging their services, buyers can confidently navigate the complexities of international trade and make successful purchases from China.
Price Cost Research for cutting machine for metal manufacturers Companies in China, use temu.com and 1688.com
When it comes to purchasing cutting machines for metal manufacturers in China, two popular online platforms are temu.com and 1688.com. These platforms offer a wide range of options at competitive prices.
Temu.com is an e-commerce platform specifically tailored for industrial equipment and machinery. It provides a convenient and reliable avenue for metal manufacturers to explore and purchase cutting machines. The platform offers a user-friendly interface and search filters that allow users to find the most suitable cutting machines based on their specific requirements. Additionally, temu.com offers a variety of convenient features such as secure payment options and reliable after-sales support.
1688.com, on the other hand, is a popular Chinese wholesale platform owned by Alibaba. The platform focuses on connecting wholesale buyers with suppliers directly. It offers a vast array of cutting machines for metal manufacturers at factory-direct prices, making it an attractive option for businesses looking to cut costs. However, users should keep in mind that communication with suppliers on 1688.com may require proficiency in Mandarin or the use of translation tools.
When conducting price and cost research on these platforms, it is recommended to thoroughly compare the specifications, pricing, and user reviews of the cutting machines available. By taking these factors into consideration, metal manufacturers can make informed decisions regarding their purchasing options on temu.com and 1688.com.
In conclusion, temu.com and 1688.com are go-to online platforms for metal manufacturers in China seeking cutting machines. Both platforms offer various options at competitive prices. Conducting thorough research and comparing specifications and pricing on these platforms enables businesses to find the most suitable cutting machines while staying within their budget.
Shipping Cost for cutting machine for metal import from China
The shipping cost for importing a cutting machine for metal from China will vary depending on various factors such as the weight and dimensions of the machine, the shipping method, and the destination country.
For smaller cutting machines, air freight can be a suitable option. This method is faster but may be more expensive compared to sea freight. The cost can range from $500 to $2000, depending on the size and weight of the machine.
Alternatively, for larger and heavier machines, sea freight is a cost-effective option. The cost is calculated based on the volume of the machine, usually in cubic meters. On average, the sea freight cost can be around $1000 to $5000, which includes transportation from China to the destination port.
However, additional charges need to be considered. These charges may include customs duties, taxes, import fees, and handling charges. The exact amount will depend on the import regulations of the destination country. It is advisable to check with the customs authorities or a freight forwarder for accurate details.
Insurance is another important aspect to consider. It helps protect the machine against damages or loss during transportation. The insurance cost is typically around 0.5% to 2% of the machine’s value.
In conclusion, the shipping cost for importing a cutting machine for metal from China will depend on factors such as size, weight, shipping method, destination country, customs fees, and insurance. A thorough understanding of these factors and careful planning can help in controlling the shipping cost and ensuring a smooth import process.
Compare China and Other cutting machine for metal Markets: Products Quality and Price,Visible and Hidden Costs
China has emerged as a key player in the global market for cutting machines for metal due to its competitive products quality and price. Chinese cutting machines for metal are known for their durability, precision, and advanced technology. They offer a wide range of options, including laser cutting machines, plasma cutting machines, and waterjet cutting machines, catering to the diverse needs of industries.
In terms of product quality, Chinese cutting machines for metal have significantly improved over the years. They meet international standards and are built with high-quality components and materials, ensuring reliable performance and longevity. With a focus on research and development, Chinese manufacturers continuously strive to enhance the quality and functionality of their cutting machines.
Chinese cutting machines for metal also offer competitive pricing compared to their counterparts in the market. The cost-effectiveness is a result of lower labor and production costs in China. Additionally, Chinese manufacturers benefit from economies of scale due to the high demand for their products both domestically and internationally. As a result, buyers can acquire cutting machines for metal from China at a relatively lower price without compromising on quality.
However, it is important to consider both visible and hidden costs when dealing with Chinese cutting machines for metal. Visible costs may include shipping, import duties, and customs tariffs, which can vary depending on the buyer’s location. Buyers should thoroughly research and factor in these costs when comparing prices.
Hidden costs, on the other hand, can arise in terms of after-sales services, maintenance, and spare parts availability. While Chinese manufacturers have made significant improvements in these areas, some buyers may still encounter challenges in terms of language barriers, response time, and availability of spare parts. It is crucial for buyers to establish effective communication channels and conduct due diligence regarding the manufacturer’s service network and reliability.
In conclusion, China’s cutting machines for metal market offers competitive products quality and pricing. However, buyers need to carefully consider visible and hidden costs associated with purchasing from China. By thoroughly researching and communicating with manufacturers, buyers can ensure they acquire high-quality cutting machines for metal with minimal additional costs.
Understanding Pricing and Payment Terms for cutting machine for metal: A Comparative Guide to Get the Best Deal
When it comes to purchasing a cutting machine for metal, understanding pricing and payment terms is crucial to getting the best deal. This comparative guide aims to provide valuable insights on how to navigate these aspects efficiently and make an informed decision.
Firstly, pricing can vary significantly depending on various factors such as machine type, brand, specifications, and features. It is essential to conduct thorough market research to identify the average price range for the desired cutting machine. This research can be done by exploring online marketplaces, contacting multiple suppliers, or consulting industry experts.
Furthermore, when comparing prices, it is vital to consider the overall value offered by the supplier. This includes examining the warranty period, after-sales service, and the reputation of the company. Opting for a slightly higher-priced machine from a reputable supplier often proves to be a better long-term investment, as it ensures product durability and reliability.
Payment terms also play a crucial role in the purchasing process. While some suppliers may offer a one-time payment option, others may provide installment plans or leasing options. It is important to assess the financial feasibility of each payment term and choose the option that best fits one’s budget and business requirements. Additionally, exploring financing options or seeking equipment loans from financial institutions can also help in managing the upfront costs effectively.
Negotiation is another aspect that should not be overlooked. Many suppliers are open to negotiating the pricing and payment terms to attract potential buyers. It is beneficial to have all the necessary research and information at hand to leverage during negotiations. Furthermore, bulk orders or establishing a long-term partnership with a supplier can also lead to more favorable pricing and payment terms.
In conclusion, understanding the pricing and payment terms for a cutting machine for metal is crucial to securing the best deal. Thorough market research, assessing the overall value offered by suppliers, considering various payment options, and engaging in negotiations are effective strategies to ensure a successful purchasing experience. By following these guidelines, individuals and businesses can make an informed decision that suits their needs while maximizing their return on investment.
Chinese Regulations and Industry Standards Certifications for cutting machine for metal,Import Regulations and Customs for cutting machine for metal from China
China has established several specific regulations and industry standards certifications for cutting machines for metals. These regulations ensure the product’s quality and safety, and also help to streamline trade and export processes. The main regulatory bodies responsible for overseeing these certifications are the State Administration for Market Regulation (SAMR) and the Certification and Accreditation Administration of the People’s Republic of China (CNCA).
The main industry standards certification for cutting machines for metal in China is the China Compulsory Certification (CCC) mark. This certification is mandatory for products sold in China and ensures that they meet safety, health, and environmental protection requirements. The CCC mark ensures that the cutting machines comply with the applicable standards and regulations set by the China National Institute of Standardization (CNIS). Manufacturers must obtain this certification before selling their products in the Chinese market.
In addition to industry standards certifications, it is important to understand the import regulations and customs procedures for cutting machines for metal from China. Importers must be aware of the relevant documentation required, including the commercial invoice, packing list, bill of lading, and certificate of origin. These documents must be prepared accurately and submitted to the customs authorities for clearance.
Furthermore, importers should be aware of any specific import regulations in their home country. Certain countries may have additional standards or certifications that the cutting machines must meet before being allowed entry. It is important to research and comply with these regulations to avoid delays or rejections at the customs checkpoints.
Understanding the Chinese regulations and certifications for cutting machines for metal is crucial for both manufacturers and importers. Compliance with these regulations and obtaining the necessary certifications will not only ensure the product’s quality and safety but also facilitate smoother trade between China and other countries.
Sustainability and Environmental Considerations in cutting machine for metal Manufacturing
Sustainability and environmental considerations in the manufacturing of cutting machines for metal are crucial for reducing the industry’s ecological footprint. There are several areas where sustainability can be incorporated during the manufacturing process.
Firstly, reducing energy consumption is vital. Implementing energy-efficient systems and components in the cutting machines can significantly decrease their environmental impact. This can be achieved through the use of energy-efficient motors, optimized operating systems, and automated shut-off mechanisms to minimize idle energy consumption. Additionally, incorporating renewable energy sources, such as solar or wind power, into the manufacturing facilities can further reduce the overall energy consumption and carbon emissions.
Secondly, material selection plays a crucial role in sustainability efforts. Using recycled or reclaimed materials in the construction of cutting machines can minimize the need for extracting new resources and reduce waste generation. Furthermore, incorporating materials that have a lower carbon footprint and can be easily recycled at the end of the machine’s life cycle promotes a circular economy.
Thirdly, waste reduction and resource optimization are essential considerations. Implementing lean manufacturing principles can help minimize material waste and improve overall efficiency. Designing cutting machines with modular components can also facilitate the repair and replacement of specific parts, extending the machine’s lifespan and reducing the need for complete replacements.
Moreover, implementing effective waste management practices is essential. This includes proper disposal of hazardous materials and recycling of non-hazardous waste generated during the manufacturing process. Additionally, establishing partnerships with recycling centers or organizations that specialize in the recycling of metal and electronic components can ensure responsible waste management.
Lastly, considering the end-of-life phase is crucial. Designing cutting machines with disassembly in mind can facilitate the recycling and proper disposal of components. Implementing take-back programs that allow customers to return outdated or malfunctioning machines for recycling can further promote sustainability.
In conclusion, incorporating sustainability and environmental considerations in the manufacturing of cutting machines for metal is essential for reducing their ecological impact. By focusing on energy efficiency, material selection, waste reduction, and end-of-life management, manufacturers can contribute to a more sustainable and environmentally conscious industry.
List The Evolution history of “cutting machine for metal”
Cutting machines for metal have evolved significantly over time, from simple hand tools to advanced automated devices. Here is a brief overview of their evolution history:
1. Early Hand Tools (Antiquity-18th Century): The earliest cutting machines for metal were basic handheld tools such as chisels, axes, and saws. These tools required physical force to cut through metal, limiting their precision and efficiency.
2. Industrial Revolution (18th-19th Century): The Industrial Revolution brought significant advancements in metal cutting. Early machines like the fly press and the power hacksaw were invented, enabling greater cutting efficiency and accuracy. These machines were powered by steam engines or mechanized systems.
3. Introduction of Water Jet Cutting (1960s): In the 1960s, the first water jet cutting machine was invented. Water jet cutting utilized a high-pressure jet of water mixed with an abrasive material to cut through metal. This method provided a non-thermal cutting process, allowing for intricate and precise cuts.
4. Development of Laser Cutting (1960s-1970s): Laser cutting technology emerged in the late 1960s and became increasingly popular in the 1970s. Laser cutting machines used a high-powered laser beam to melt or vaporize metal, resulting in precise cuts with minimal heat distortion. As technology advanced, lasers became more powerful and accurate.
5. Computer Numerical Control (CNC) Machines (1970s-Present): The advent of CNC technology revolutionized metal cutting. CNC machines are controlled by computer programs, allowing for automated and precise cutting processes. These machines use a variety of cutting methods, including laser cutting, plasma cutting, and water jet cutting. CNC machines can cut complex shapes and patterns with high speed and accuracy.
6. Advanced Automation (Present): Modern cutting machines for metal feature advanced automation and robotics capabilities. They can be integrated into production lines and controlled remotely, optimizing efficiency and reducing manual labor. Additionally, machine vision systems are employed to provide real-time monitoring and adjustment for improved accuracy.
In conclusion, the evolution of cutting machines for metal has been marked by advancements in power sources, cutting methods, precision, and automation. From primitive hand tools to sophisticated CNC and automated systems, metal cutting has dramatically improved, enabling more intricate and efficient processes in various industries.
The Evolution and Market Trends in cutting machine for metal Industry
The cutting machine for metal industry has come a long way in terms of technology and efficiency. Over the years, there have been several advancements that have greatly improved the capabilities of these machines, making them an essential tool in various industries.
One of the key evolutionary trends in cutting machines for metal is the shift towards Computer Numerical Control (CNC) technology. This technology has revolutionized the industry by providing precise and automated cutting capabilities. CNC machines are able to follow complex cutting patterns and produce highly accurate cuts, resulting in improved productivity and reduced waste. Additionally, CNC machines can be easily programmed and controlled, making them versatile and adaptable to different cutting requirements.
Another trend in the market is the integration of laser technology in cutting machines. Laser cutting machines offer several advantages over traditional cutting methods. They provide high precision cuts, minimal distortion, and reduced material waste. Laser cutting is also a faster process compared to other methods, allowing for increased productivity. As a result, laser cutting machines have gained popularity in industries such as automotive, aerospace, and electronics.
There is also a growing demand for cutting machines that are environmentally friendly. With increasing concerns about sustainability and reducing carbon footprint, manufacturers are focusing on developing machines that are energy-efficient and use environmentally friendly cutting techniques. For example, waterjet cutting machines use a high-pressure water stream mixed with abrasive particles to cut metal. This method is non-toxic, produces no harmful emissions, and generates minimal waste.
Another notable trend is the integration of automation and robotics in cutting machines. Robot-assisted cutting machines offer increased precision, speed, and safety. These machines can perform complex cutting tasks with minimal human intervention, resulting in improved productivity and reduced labor costs. Automation also allows for continuous operation, enabling manufacturers to meet high production demands.
In conclusion, the cutting machine for metal industry has evolved significantly with the aid of CNC technology, laser cutting, environmentally friendly methods, and automation. These advancements have led to increased precision, productivity, and efficiency in metal cutting processes. As market demands continue to change, manufacturers will likely continue to innovate and improve cutting machines to meet the evolving needs of various industries.
Custom Private Labeling and Branding Opportunities with Chinese cutting machine for metal Manufacturers
If you are looking for custom private labeling and branding opportunities with Chinese cutting machine for metal manufacturers, you have come to the right place. Chinese manufacturers have made a name for themselves in the field of cutting machines for metal due to their high-quality products, competitive pricing, and efficient production capabilities.
One of the key advantages of working with Chinese manufacturers is the ability to customize and private label their products. This means that you can have your own brand name, logo, and design on the cutting machines, effectively creating a unique product that aligns with your brand identity. This can be a powerful marketing tool to differentiate yourself from the competition and build brand recognition in the market.
Chinese manufacturers offer a wide range of custom private labeling and branding options. You can choose from different sizes, models, and specifications of cutting machines that best fit your requirements. Manufacturers can also help you with the design and development of customized features and functionalities according to your specific needs.
Furthermore, Chinese manufacturers have the expertise and resources to provide comprehensive branding solutions. They can assist you with the packaging design, user manuals, and other promotional materials that go along with the cutting machines. This ensures that your brand image is consistent across all touchpoints and enhances the overall customer experience.
In terms of production capabilities, Chinese manufacturers are known for their efficiency and timely delivery. They have state-of-the-art manufacturing facilities, advanced technology, and experienced workforce, enabling them to meet large volume orders within strict deadlines. This makes them an ideal partner for businesses looking to scale up their operations quickly.
In conclusion, partnering with Chinese cutting machine for metal manufacturers for custom private labeling and branding opportunities can be a cost-effective and efficient way to bring your products to market. You can leverage their expertise, production capabilities, and competitive pricing to create a unique and branded product that meets your customer’s needs.
Tips for Procurement and Considerations when Purchasing cutting machine for metal
When purchasing a cutting machine for metal, there are several important considerations that should be taken into account. Here are some tips for procurement and things to consider:
1. Type of Cutting Machine: There are various types of cutting machines available, such as laser cutting machines, plasma cutting machines, and waterjet cutting machines. Consider the specific requirements of your metal cutting needs and choose the appropriate type of machine.
2. Cutting Capacity: Determine the maximum thickness and size of metal that the cutting machine can handle. Make sure it aligns with your intended usage.
3. Accuracy and Precision: Look for a cutting machine that offers high accuracy and precision in cutting. This ensures clean and precise cuts, reducing the need for additional finishing work.
4. Speed and Efficiency: Consider the speed at which the cutting machine can operate. Higher cutting speeds can lead to increased productivity and reduced production time.
5. Maintenance and Service: Check the reputation of the manufacturer in terms of providing maintenance and service support. Ensure that spare parts are easily available and that technical assistance can be obtained if needed.
6. Safety Features: Safety should be a top priority when purchasing a cutting machine. Look for features such as emergency stop buttons, safety interlocks, and operator protection systems to ensure a safe working environment.
7. Cost and Return on Investment: Consider the initial cost of the machine, as well as ongoing operational costs such as energy consumption and consumables. Evaluate the potential return on investment based on factors like increased productivity and reduced production time.
8. Training and Support: Ensure that the manufacturer provides proper training for operating the cutting machine. Training and after-sales support can contribute to the optimal operation and longevity of the machine.
9. User-Friendly Interface: Look for a cutting machine with an intuitive and user-friendly interface. This facilitates ease of operation and reduces the learning curve for the operators.
10. Reviews and References: Before making a final decision, read reviews and seek references from other users who have purchased similar cutting machines. Their experiences can provide valuable insights into the performance and reliability of different models.
By taking these considerations into account, you can make an informed decision when purchasing a cutting machine for metal.
FAQs on Sourcing and Manufacturing cutting machine for metal in China
Q: Why should I source and manufacture cutting machines for metal in China?
A: China is one of the largest manufacturers and exporters of cutting machines for metal in the world. By sourcing and manufacturing in China, you can benefit from its extensive industrial expertise, cost-effective labor, and advanced production capabilities. Additionally, China has a well-established supply chain and a vast network of metal cutting machine suppliers, making it easier to find a suitable partner.
Q: How can I find reliable suppliers in China for cutting machines?
A: To find reliable suppliers, you can leverage online platforms such as Alibaba, Global Sources, or Made-in-China. These platforms allow you to browse through numerous suppliers, compare prices, and read customer reviews. It is recommended to shortlist multiple suppliers, communicate with them, and request samples or past client references for quality assurance.
Q: What should I consider when selecting a manufacturer in China?
A: When selecting a manufacturer, consider factors such as their experience and specialization in cutting machines for metal. Ensure they have the required certifications and quality control measures in place to meet your standards. Additionally, evaluate their production capacity, lead times, pricing, and after-sales support.
Q: How can I verify the quality of metal cutting machines from China?
A: Before finalizing a supplier, it is crucial to inspect the quality of their cutting machines. You can either visit their manufacturing facility in China or hire a third-party inspection agency to ensure compliance with your specifications. Conducting sample tests, checking the machines’ durability, and reviewing the supplier’s quality control processes can help verify the product quality.
Q: What are the potential challenges or risks of sourcing and manufacturing cutting machines in China?
A: Some potential challenges include language barriers, cultural differences, and intellectual property protection. Language barriers can cause misunderstandings, while cultural differences might impact business negotiations. Protecting your intellectual property rights can also be a concern, so it is advisable to protect your designs and establish legal agreements with suppliers.
Q: Is there a minimum order quantity requirement when sourcing cutting machines from China?
A: Minimum order quantity (MOQ) requirements vary among different suppliers. Some may have a minimum quantity requirement due to production capacity or cost considerations, while others may be more flexible. It is important to discuss MOQs with potential suppliers to ensure it aligns with your business needs.
Q: How can I ensure a smooth manufacturing process in China?
A: To ensure a smooth manufacturing process, clear communication with your supplier is essential. Clearly define your requirements, provide detailed specifications, and maintain regular communication throughout the production cycle. Conduct onsite inspections, clarify any doubts promptly, and establish a strong working relationship with your supplier.
In conclusion, sourcing and manufacturing cutting machines for metal in China offer numerous advantages such as cost-effectiveness, expertise, and a wide range of suppliers. However, it is important to conduct due diligence, verify product quality, and address any potential challenges to ensure a successful partnership.
Why contact sourcifychina.com get free quota from reliable cutting machine for metal suppliers?
Sourcifychina.com, being a platform that connects buyers with suppliers in China, gets free quotas from reliable cutting machine for metal suppliers for a variety of reasons. Firstly, by offering free quotas, suppliers can attract potential customers and increase their chances of securing business partnerships. The free quota acts as a promotional strategy to showcase the supplier’s capabilities and the quality of their cutting machines.
Moreover, providing free quotas allows suppliers to build trust and establish credibility with potential buyers. This demonstrates the supplier’s confidence in their products and services and encourages buyers to consider them as reliable and trustworthy partners.
For Sourcifychina.com, obtaining these free quotas benefits their platform and their customers in several ways. Firstly, it allows them to offer a wider range of options to their users, ensuring that buyers have access to a diverse pool of cutting machine suppliers. This ultimately increases the chances of finding a suitable supplier that meets their specific requirements.
Additionally, the provision of free quotas promotes healthy competition among suppliers. By showcasing their capabilities through free quotas, suppliers strive to offer the best possible products and services, ultimately benefiting the buyers who can choose from a range of high-quality options.
Sourcifychina.com can leverage these free quotas as a value-added benefit for their users. By presenting potential buyers with the opportunity to receive free quotas from reliable cutting machine suppliers, they differentiate themselves as a platform that not only facilitates connections but also adds tangible value to the sourcing process.
In conclusion, sourcifychina.com obtains free quotas from reliable cutting machine for metal suppliers as a means to attract potential customers, build trust and credibility, offer a wider range of options, encourage healthy competition, and differentiate themselves as a valuable platform in the sourcing industry.