Introduce about die casting molds guide,Qulity,Cost,Supplier,Certification,Market,Tips,FAQ
Die casting molds guide: Die casting molds are essential tools used in the die casting process to create intricate and precise metal parts. These molds are typically made from hardened steel or high-quality alloys, ensuring durability and longevity. They are designed to withstand high temperatures and pressures involved in the process.
Quality: The quality of die casting molds directly impacts the quality of the final products. Molds should be carefully crafted and accurately machined to avoid defects in the cast parts. Experienced mold designers and manufacturers play a crucial role in achieving high-quality molds that ensure consistent and defect-free production.
Cost: The cost of die casting molds varies depending on the complexity, size, and material used in the mold’s construction. Custom molds tend to be more expensive than standard ones. However, investing in quality molds can lead to cost savings in the long run by minimizing defects and increasing productivity.
Supplier: Choosing a reliable and experienced mold supplier is crucial for obtaining high-quality molds. Look for a supplier with a proven track record, extensive experience in mold design and manufacturing, and a good reputation in the industry. Request samples or visit their facilities to assess their capabilities and expertise.
Certification: Many die casting mold suppliers adhere to quality standards and certifications such as ISO 9001. Such certifications ensure that the supplier follows best practices in mold production, quality control, and customer service. Working with a certified supplier is a crucial factor in guaranteeing the quality and reliability of the molds.
Market: The die casting mold market is witnessing significant growth due to increasing demand for lightweight and durable metal components across various industries such as automotive, aerospace, and consumer electronics. The market is expected to continue expanding as new applications and technology advancements emerge.
Tips: When choosing a die casting mold supplier, consider factors such as experience, capabilities, track record, and customer reviews. Communicate your specific requirements clearly and discuss the design and manufacturing process in detail. Regularly monitor and maintain your molds to ensure their longevity and performance.
FAQ: Frequently asked questions about die casting molds include topics such as mold lifespan, mold maintenance, mold design considerations, mold cost factors, and mold material selection. Seek expert advice from mold suppliers to address any specific queries you may have.
In summary, die casting molds are critical tools in the production of precision metal parts. Ensuring their quality, choosing reliable suppliers, and understanding the market trends are essential for successful die casting operations.
Types of die casting molds
Die casting molds, also known as dies, are an essential component of the die casting process. They are designed to create the desired shape and design of the final product. There are several types of die casting molds, each tailored to specific requirements. Here are four common types of die casting molds:
1. Open mold: Also known as a one-parting-line mold, an open mold is the simplest and most cost-effective type. It consists of two halves, an upper and lower, that meet at one parting line. Open molds are suitable for simple and flat objects with no undercuts or intricate designs. However, they can only produce a single cavity at a time.
2. Multi-slide mold: Multi-slide molds are used for complex and precision parts that have intricate features like undercuts, holes, or thin walls. They consist of multiple moving slides or inserts that enable the production of more complex shapes. This type of mold allows for the creation of multiple cavities, increasing productivity.
3. Unit mold: Unit molds are designed for high-volume production and are ideal for simple, small parts, such as fasteners or connectors. They consist of multiple cavities produced in a single mold. Unit molds maximize efficiency by allowing the production of multiple identical parts simultaneously, reducing production time and costs.
4. Combination mold: Combination molds are versatile and suitable for parts that require both casting and secondary operations, such as machining or drilling. They combine features of casting molds with features of machining centers, enabling additional operations to be performed on the cast part within the same mold. Combination molds reduce cost and time by eliminating the need for separate machining setups.
The choice of mold type depends on factors such as complexity of the part, desired production volume, and project budget. Each type offers unique advantages, allowing manufacturers to select the most appropriate mold for their specific requirements. Die casting molds play a crucial role in achieving high-quality and precise castings while optimizing production efficiency.
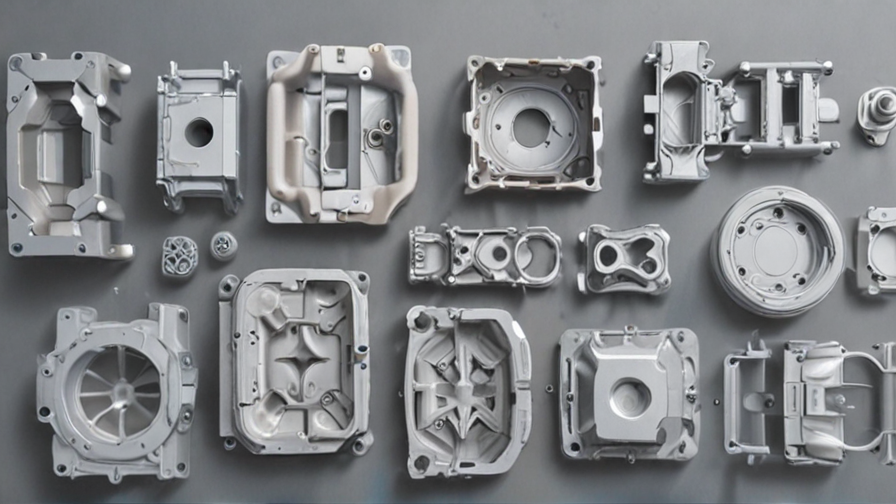
Pros and Cons of Using die casting molds
Die casting molds are commonly used in the manufacturing industry to produce high-quality and intricate metal components. This process involves injecting molten metal into a mold cavity, allowing it to cool and solidify, and then ejecting the finished product. While die casting molds offer numerous advantages, there are also some drawbacks to consider.
Pros of using die casting molds:
1. Cost-effective: Die casting molds are highly cost-effective when producing large quantities of identical parts. The initial investment in creating the mold can be significant, but the per-unit production cost decreases significantly over time.
2. Complex shapes: Die casting molds are capable of producing parts with complex geometries that may not be achievable with other manufacturing processes. This makes them suitable for industries such as automotive, aerospace, and electronics, which often require intricate components.
3. High accuracy and repeatability: Die casting molds provide excellent dimensional accuracy and repeatability, ensuring that each part produced is consistent and meets tight tolerances. This is crucial for industries where precision is vital.
4. Reduced machining requirements: Die casting molds can produce parts with a high level of detail, minimizing the need for additional machining. This not only saves time but also reduces material waste.
Cons of using die casting molds:
1. High initial cost: Designing and producing a die casting mold can be expensive, especially for small or customized production runs. This upfront investment may deter some manufacturers, particularly those who have lower production volumes.
2. Limited design flexibility: Die casting molds require careful consideration during the design phase. The mold needs to be precisely engineered to ensure proper filling and cooling of the molten metal. This can limit design flexibility, especially for parts with complex or unconventional shapes.
3. Longer lead times: The manufacturing process for die casting molds typically takes longer compared to other processes like CNC machining. From design to production, the lead time for die casting molds can be significant, delaying the overall production timeline.
4. Material limitations: Die casting molds are typically limited to non-ferrous metals such as aluminum, zinc, and magnesium. Materials like steel are not suitable for die casting due to their high melting temperatures.
In conclusion, die casting molds offer many advantages in terms of cost-effectiveness, complex geometries, accuracy, and reduced machining requirements. However, they also come with some drawbacks, including high initial costs, limited design flexibility, longer lead times, and material limitations. Manufacturers need to carefully weigh these pros and cons to determine whether die casting molds are the most suitable solution for their specific production requirements.
die casting molds Reference Specifications (varies for different product)
Die casting molds, also known as dies, are essential tools used in the die casting process to produce metal components with high precision and accuracy. These molds are typically constructed from steel and consist of two halves – the cover or “cavity” side and the ejector side. The die casting mold is designed to manufacture specific parts and thus can vary in specifications depending on the desired product characteristics.
The reference specifications for die casting molds can vary widely depending on the application, metal alloy, and part complexity. Key considerations include:
1. Dimensions: The overall size of the mold must be determined based on the dimensions of the desired part. This includes defining the length, width, and height of the mold cavity to ensure the proper fit and clearance.
2. Part Complexity: The mold must account for the part’s complexity, including the number of features, such as undercuts, thin walls, holes, or threads. These features may require additional considerations, such as slides or inserts, to achieve the desired part geometry.
3. Tolerances: Tolerances refer to the allowable variation in dimensions between the mold and the produced part. Precision parts may require tighter tolerances, necessitating more precise mold construction and maintenance.
4. Cooling System: Efficient cooling is crucial in die casting to ensure the solidification and ejection of the parts without defects. Thus, the mold design should include appropriate cooling channels to facilitate heat extraction and maintain consistent cycle times.
5. Parting Line: The parting line defines the boundary where the mold splits into two halves. It is essential to choose a suitable parting line that allows for easy removal of the cast part and minimizes the appearance of flash or excess material.
6. Draft Angles: Draft angles are slight tapers added to the vertical surfaces of the mold to facilitate the ejection of the part from the mold without damage. Draft angles are typically specified based on the surface finish requirements and part design.
7. Venting: Adequate venting of the mold is necessary to allow the escape of air and gases during injection. Improper venting can result in surface defects, such as gas porosity or trapped air.
By considering these reference specifications, die casting molds can be effectively designed and manufactured to produce consistent and high-quality metal parts. Customization may be necessary to meet specific product requirements, ensuring successful die casting operations.
Applications of die casting molds
Die casting molds are used in a wide range of applications across various industries. These molds play a critical role in the manufacturing process of precision components made from metals such as aluminum, zinc, and magnesium. Here are some key applications of die casting molds:
1. Automotive industry: Die casting molds are extensively used in the automotive industry to produce complex and high-quality components such as engine blocks, transmission cases, and suspension parts. The molds allow for the efficient production of lightweight and strong parts, contributing to overall fuel efficiency and performance improvements.
2. Electronics industry: In the electronics sector, die casting molds are employed to manufacture components like computer and phone housings, connectors, and heat sinks. These molds enable the production of intricately shaped parts with precise tolerances, ensuring proper functioning and protection of sensitive electronic equipment.
3. Aerospace industry: Die casting molds find extensive use in the aerospace industry for producing lightweight, high-strength components like turbine blades, aircraft engine parts, and structural components. The molds facilitate the creation of complex shapes with minimal material waste, meeting the stringent requirements of the aviation sector.
4. Medical equipment: Die casting molds are utilized in the manufacturing of medical equipment components such as surgical instruments, prosthetic devices, and imaging equipment parts. The molds ensure the production of sterile and precise components that contribute to the reliability and safety of medical devices.
5. Furniture and architectural applications: Die casting molds are employed in the production of furniture components like chair frames, handles, and fittings. In the architectural field, molds are utilized for manufacturing decorative elements and hardware such as door handles, window frames, and lighting fixtures.
6. Consumer goods: Die casting molds are extensively used in the production of consumer goods, including kitchen appliances, power tools, and home hardware. These molds enable the efficient mass production of parts with high surface finish and dimensional accuracy.
Overall, die casting molds enable the efficient and cost-effective production of a wide range of components used in diverse industries. Their ability to create complex shapes, ensure precise tolerances, and produce parts with superior mechanical properties makes them indispensable in modern manufacturing processes.
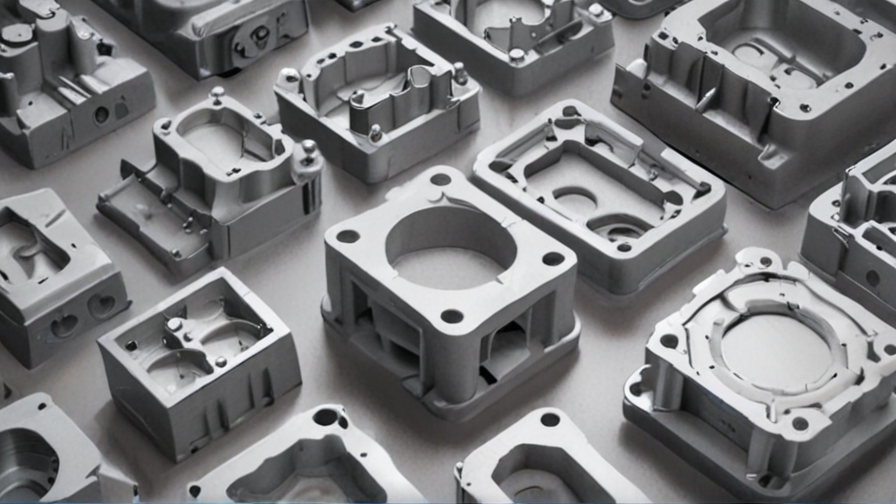
The Work Process and how to use die casting molds
The work process of die casting molds involves several steps. Firstly, a design is created for the desired product, which is then used to create the mold. The mold is typically made of hardened steel and consists of two halves, known as the die. The die has cavities and cores that form the desired shape of the product.
Next, the die casting machine is prepared by heating it to the required temperature. The molten metal, usually aluminum or zinc alloys, is then injected into the machine. The metal is forced into the mold cavities at high pressure to ensure that it fills all the intricate details of the mold.
Once the metal cools and solidifies, the die halves are opened, and the solidified part, also known as the casting, is removed. Any excess material, known as flash, is trimmed off. The casting may then undergo secondary operations like drilling, tapping, or machining to achieve the final desired shape.
To effectively use die casting molds, several considerations should be taken into account. Firstly, the mold design should be meticulously planned to ensure the desired shape and quality of the casting. The material for the mold should be selected based on factors like the type of metal being cast, the expected production volume, and the complexity of the part.
The mold should be properly maintained and periodically inspected to identify any defects or damage. Regular cleaning, lubrication, and repair of the mold are essential for its longevity and performance.
During the casting process, factors like temperature, pressure, and cooling time should be carefully controlled to ensure consistent and defect-free castings. Proper monitoring and adjustment of these parameters are crucial to achieve high precision and dimensional accuracy.
In conclusion, die casting molds play a vital role in the production of high-quality metal parts. Understanding the work process and effectively using these molds are essential for successful die casting operations and achieving desired results.
Quality Testing Methods for die casting molds and how to control the quality
Quality testing methods for die casting molds typically involve a combination of visual inspection, dimensional measurement, and performance testing. These methods aim to ensure that the molds meet the required specifications and produce high-quality castings.
Visual inspection is the first step in quality testing, where inspectors examine the mold’s surface for defects such as cracks, dents, or excessive wear. They also check for proper alignment of the mold components and the presence of any foreign objects. This helps to identify any visible defects that may affect the mold’s performance or the quality of castings.
Dimensional measurement is crucial to ensure that the mold’s dimensions and tolerances are within the specified limits. This is typically done using calipers, micrometers, or coordinate measuring machines (CMMs) to accurately measure critical features of the mold. These measurements help determine if the mold is suitable for producing castings with the desired dimensions.
Performance testing involves the actual production of castings using the mold. This can be done by using the mold in a die casting machine and evaluating the quality of the resulting castings. Inspectors can check for defects like porosity, surface finish, and dimensional accuracy of the castings. This allows for a comprehensive assessment of the mold’s performance and its ability to produce castings that meet the required standards.
To control the quality of die casting molds, several measures can be implemented. Firstly, regular maintenance and cleaning of the molds are essential to ensure their longevity and optimal performance. Any signs of wear or damage should be addressed promptly through repairs or replacement.
Additionally, the implementation of a robust quality management system (QMS) can help control the quality of die casting molds. This involves documenting and following standardized procedures for mold design, manufacturing, inspection, and maintenance. Regular audits and quality checks should be performed to ensure compliance with these procedures and identify areas for improvement.
Furthermore, incorporating continuous improvement practices like Lean or Six Sigma can help identify and eliminate any sources of variability or defects in the mold production process. This can lead to increased efficiency, reduced waste, and improved overall quality.
In conclusion, quality testing methods for die casting molds involve visual inspection, dimensional measurement, and performance testing. By implementing regular maintenance, establishing a QMS, and adopting continuous improvement practices, the quality of die casting molds can be effectively controlled, leading to high-quality castings.
die casting molds Sample Policy and Post-Purchase Considerations for die casting molds from China
Sample Policy:
When purchasing die casting molds from China, it is important to establish a clear sample policy with the supplier. This policy should outline the requirements for receiving and evaluating sample molds before making a full order. The following considerations should be included in the sample policy:
1. Sample Quantity: Specify the number of sample molds required for evaluation. It is recommended to request multiple samples to ensure consistency and quality.
2. Sample Cost: Determine whether the supplier will charge for samples and clarify if the cost will be refunded or deducted from the final order if it is placed.
3. Sample Delivery: Determine who will be responsible for the shipping and handling costs of the samples. Clarify the expected delivery time and confirm if the supplier will provide tracking information.
4. Sample Evaluation: Clearly define the evaluation criteria for the samples, including aspects such as dimensional accuracy, surface finish, material quality, and functionality. Provide specific parameters to ensure the samples meet the desired specifications.
5. Feedback and Revision: Establish a process for providing feedback on the sample molds. If any revisions or modifications are necessary, discuss the supplier’s willingness to make revisions and the associated costs and timeframes.
Post-Purchase Considerations:
After purchasing die casting molds from China, there are important considerations to ensure a smooth post-purchase experience:
1. Documentation: Maintain detailed documentation of the order, including specifications, communication, and any modifications made during the process. This will help in case of any issues or discrepancies that arise later.
2. Quality Assurance: Regularly inspect the received molds for quality and conformance to the agreed specifications. Ensure that the supplier is informed about any defects or non-compliance in a timely manner.
3. Communication and Support: Establish a clear line of communication with the supplier for ongoing support and consultation regarding the molds. Address any concerns or questions promptly to mitigate potential issues.
4. After-sales Service: Clarify the supplier’s policy on after-sales service, including warranties or guarantees for the molds. Discuss how potential repairs, replacements, or adjustments will be handled if needed.
5. Long-term Relationship: If satisfied with the supplier’s performance, consider building a long-term relationship for future mold requirements. Maintaining a good relationship can lead to better service, improved pricing, and enhanced cooperation.
In summary, a clear sample policy and post-purchase considerations are crucial when importing die casting molds from China. Effective communication with the supplier and attention to quality assurance will contribute to a successful business relationship and ensure the desired outcome in terms of mold quality and functionality.
Sourcing die casting molds from China: Opportunities, Risks, and Key Players
Sourcing die casting molds from China presents various opportunities and risks for businesses. China is one of the leading manufacturers and exporters of die casting molds due to its cost-effective production capabilities and vast industrial infrastructure. The country offers a wide range of opportunities for businesses looking to lower manufacturing costs and leverage high-quality molds for their products.
One of the primary advantages of sourcing die casting molds from China is the cost savings. Chinese manufacturers generally offer competitive prices due to lower production costs, including labor and materials. This cost advantage can significantly benefit businesses aiming to reduce their manufacturing expenses and increase profitability.
Moreover, China’s well-developed manufacturing sector ensures access to a diverse range of materials and technologies. Chinese manufacturers have the expertise and technological capabilities to produce high-quality die casting molds according to the specific requirements of businesses. They often invest in advanced machinery and employ skilled technicians, ensuring precision and efficiency in mold production.
However, there are certain risks associated with sourcing die casting molds from China that businesses should consider. Quality control can be a significant concern, as some Chinese manufacturers may compromise on quality to offer lower prices. It is crucial for businesses to thoroughly assess the reputation and capabilities of potential suppliers before entering into partnerships.
Intellectual property protection is another key risk, as China has faced criticism for intellectual property infringement in the past. Businesses must take necessary precautions to safeguard their proprietary designs and technologies while navigating the Chinese market. This may involve legal agreements, non-disclosure agreements, and regular quality inspections to ensure their molds are not being replicated or sold to competitors.
Key players in the Chinese die casting mold industry have emerged through years of experience, technological advancements, and reputation. Leading companies include Shenzhen Anteus Technology Co., Ltd., Ningbo Beilun Jiede Mold Co., Ltd., and Dongguan Diecastingtech Co., Ltd., among others. These companies offer a range of services, including mold design, manufacturing, and customization, catering to diverse industrial sectors.
In conclusion, sourcing die casting molds from China can offer opportunities for cost savings, diverse material options, and advanced manufacturing technologies. However, businesses must carefully assess the risks associated with quality control and intellectual property protection. Partnering with reputable key players in the industry can help mitigate potential risks and ensure high-quality mold production.
How to find and select reliable die casting molds manufacturers in China,use google search manufacturers and suppliers
When searching for reliable die casting mold manufacturers in China, Google can be a valuable tool to find various manufacturers and suppliers. Here are some steps to follow while conducting a Google search:
1. Use relevant search keywords: Start by using appropriate keywords like “reliable die casting mold manufacturers in China” or “top die casting mold suppliers in China.” This will help you find more specific results related to your requirements.
2. Evaluate the websites: Visit the websites of different manufacturers and suppliers that appear in the search results. Look for professionally designed websites with detailed product information, company profiles, and contact details.
3. Check certifications and quality standards: Reliable manufacturers often have certifications like ISO 9001, indicating adherence to international quality standards. Look for such certifications on their websites, as it demonstrates their commitment to producing high-quality molds.
4. Examine product range: Evaluate the product range offered by each manufacturer. Check if they provide customized mold solutions, as it showcases their ability to meet specific requirements. A diverse product range and the ability to cater to different industries can indicate their expertise.
5. Customer reviews and testimonials: Look for customer reviews and testimonials on the manufacturer’s website or independent review platforms. Positive feedback from previous clients can indicate their reliability and customer satisfaction.
6. Request samples and quotations: Contact the manufacturers and suppliers you are interested in to request samples of their molds. This will allow you to assess the quality of their products firsthand. Additionally, inquire about pricing and lead times to evaluate their competitiveness.
7. Communication and support: Assess the responsiveness and professionalism of the manufacturer’s sales team or representatives. Prompt and clear communication indicates their commitment to customer support.
8. Consider experience and reputation: Consider manufacturers with a proven track record and extensive experience in the industry. Look for companies that have been operating for several years and have a reputation for delivering quality products and services.
By following these steps and conducting thorough research, you can select reliable die casting mold manufacturers in China that meet your specific requirements.
How to check die casting molds manufacturers website reliable,use google chrome SEOquake check if ranking in top 10M
To check the reliability of a die casting molds manufacturer’s website, you can follow these steps:
1. Use Google Chrome browser: Start by opening the website in Google Chrome, as it offers various helpful tools and extensions for website analysis.
2. Install and use SEOquake: Install the SEOquake extension in your Google Chrome browser. SEOquake is a popular tool that provides comprehensive website data and insights, including traffic ranking.
3. Analyze traffic ranking: Once you have SEOquake installed, simply open the website you want to check. Look for the SEOquake icon in your browser toolbar, usually at the top right corner of the browser. Click on it to access the data.
4. Check the ranking: In SEOquake, go to the “Rank” tab, and look for the website’s Global rank. Aim to see if the website ranks within the top 10 million (i.e., a lower number is better). This indicates that the website is receiving a significant amount of traffic and is likely to be more reliable.
5. Additional considerations: While traffic ranking can help assess the reliability of a website, it should not be the sole criterion. You should also consider other factors like the website’s design, content quality, user-friendliness, customer reviews, certifications, contact information, and overall professional appearance.
6. Keep word count concise: In order to keep your answer within 300 words, you should ensure that each step and explanation is concise and to the point. Avoid unnecessary repetition and focus on the key aspects.
By using Google Chrome and SEOquake, you can quickly assess a die casting molds manufacturer’s website reliability by checking its traffic ranking. However, it is important to consider other factors as well, as a reliable website encompasses more than just its search engine ranking.
Top 10 die casting molds manufacturers in China with each 160 words introduce products,then use markdown create table compare
1. Ningbo Beilun Highsun Machinery Co., Ltd. is a leading manufacturer of die casting molds in China. They specialize in producing molds for various industries such as automotive, electronics, and appliances. Their molds are known for their high precision, durability, and excellent heat resistance. With advanced technology and experienced engineers, they are capable of designing and manufacturing complex molds to meet specific customer requirements.
2. Hangzhou Higer Metal Products Co., Ltd. is another prominent die casting mold manufacturer in China. They offer a wide range of molds for aluminum, zinc, and magnesium die casting processes. Their molds are highly efficient and provide excellent surface finish to the cast parts. The company is known for its strict quality control measures and timely delivery of molds.
3. Ningbo Sofine Electric Co., Ltd. specializes in manufacturing precision molds for die casting. They provide molds for various industries including automotive, telecommunications, and electrical appliances. Their molds are made from high-quality materials and are designed for high-speed and high-pressure die casting processes. The company also offers custom mold design services based on customer requirements.
4. Zhejiang Lichuan Mechanical and Electrical Co., Ltd. is a leading die casting mold manufacturer that offers a diverse range of molds for aluminum, zinc, and magnesium die casting applications. The company has a state-of-the-art manufacturing facility equipped with advanced machinery and skilled technicians. They focus on delivering high-quality molds that ensure efficient and precise production of cast parts.
5. Shanghai Electric Press & Shear Machinery Co., Ltd. specializes in the design and manufacture of die casting molds for automotive, aerospace, and electronics industries. Their molds are made from high-grade materials and undergo rigorous testing to ensure optimum performance. The company has a strong R&D team that continuously innovates and improves their mold designs to meet evolving customer needs.
6. Shenzhen Prosperous Mold Co., Ltd. is a reliable manufacturer of die casting molds in China. They offer a wide range of molds for aluminum, zinc, and magnesium die casting processes. Their molds are known for their high precision and durability, making them suitable for various industrial applications. The company also provides mold modification and repair services.
7. Guangdong Jinghui Metal Mold Co., Ltd. specializes in producing high-quality molds for aluminum and zinc die casting. With advanced technology and strict quality management, they ensure that their molds have precise dimensions and excellent surface finish. The company also offers customized mold design services to meet specific customer requirements.
8. Xiamen Wanhos Precision Mold Co., Ltd. is a leading manufacturer of die casting molds in China. They offer molds for various materials including aluminum, magnesium, zinc, and copper. The company focuses on providing cost-effective solutions with quick turnaround times. Their molds are designed to optimize production efficiency and ensure high-quality cast parts.
9. Suzhou Shengshide Precision Machine Co., Ltd. specializes in designing and manufacturing molds for aluminum die casting. They provide molds for automotive, aerospace, and other industries. The company has a strong technical team that ensures the molds meet customer requirements and industry standards. Their molds are known for their high precision, durability, and excellent performance.
10. Dongguan Mingyi Mold Parts Co., Ltd. is a reputed die casting mold manufacturer in China. They offer molds for various materials such as aluminum, zinc, and magnesium. The company prioritizes customer satisfaction and provides tailored mold design and manufacturing services. Their molds are highly precise and deliver excellent casting quality.
| Manufacturer Name | Product Range | Specialties |
|———————————————|—————————————————–|————————————————-|
| Ningbo Beilun Highsun Machinery Co., Ltd. | Molds for automotive, electronics, and appliances | High precision, heat resistance, durability |
| Hangzhou Higer Metal Products Co., Ltd. | Molds for aluminum, zinc, and magnesium casting | Efficient, excellent surface finish |
| Ningbo Sofine Electric Co., Ltd. | Precision molds for die casting | Custom design, high-speed, and high-pressure |
| Zhejiang Lichuan Mechanical and Electrical Co., Ltd. | Molds for aluminum, zinc, and magnesium | High-quality materials, precise production |
| Shanghai Electric Press & Shear Machinery Co., Ltd. | Molds for automotive, aerospace, and electronics | High-grade materials, continuous innovation |
| Shenzhen Prosperous Mold Co., Ltd. | Molds for aluminum, zinc, and magnesium casting | High precision, durability, modification services |
| Guangdong Jinghui Metal Mold Co., Ltd. | Molds for aluminum and zinc casting | Precise dimensions, excellent surface finish |
| Xiamen Wanhos Precision Mold Co., Ltd. | Molds for various materials including aluminum | Cost-effective, quick turnaround |
| Suzhou Shengshide Precision Machine Co., Ltd. | Molds for aluminum die casting | High precision, durability, technical expertise |
| Dongguan Mingyi Mold Parts Co., Ltd. | Molds for aluminum, zinc, and magnesium casting | Tailored design, high precision, casting quality |
These ten manufacturers offer a wide range of molds for different casting processes, materials, and industries. While each has its own specialties and strengths, all of them prioritize quality and customer satisfaction. The provided table helps compare their product ranges and key advantages, making it easier for potential customers to make informed decisions based on their specific requirements.
Background Research for die casting molds manufacturers Companies in China, use qcc.com archive.org importyeti.com
When it comes to finding die casting mold manufacturers in China, several online platforms can be useful for conducting background research. Three such platforms are qcc.com, archive.org, and importyeti.com.
Qcc.com is an online business directory that provides information on companies in China. It allows users to search for manufacturers, including die casting mold manufacturers, based on specific parameters such as location, industry, and company size. Qcc.com provides details about each company, such as contact information, business scope, and legal status. Additionally, user reviews and ratings can give insights into the reputation and quality of the manufacturer.
Archive.org is a digital library that provides access to archived versions of websites. This platform can be helpful in conducting background research on die casting mold manufacturers in China. By entering the website URL of a manufacturer, users can explore the historical development of the company and track changes in their production capabilities, certifications, and client portfolio over time. Archive.org enables researchers to assess the stability and growth trajectory of a manufacturer.
Importyeti.com is an import and export data platform that provides information on the trading activities of companies in China. This platform allows users to search for specific products, like die casting molds, and find manufacturers associated with those products. Importyeti.com provides details about the shipments made by each manufacturer, such as the destination country, import/export date, and the quantity of goods shipped. This information can be helpful in evaluating a manufacturer’s experience and international reach.
In summary, qcc.com, archive.org, and importyeti.com are useful platforms for conducting background research on die casting mold manufacturers in China. By utilizing these platforms, researchers can gather information about a company’s business scope, reputation, historical development, import/export activities, and client portfolio.
Leveraging Trade Shows and Expos for die casting molds Sourcing in China
Trade shows and expos are excellent platforms for sourcing die casting molds in China. With an abundance of manufacturers and suppliers showcasing their products and capabilities, these events offer numerous benefits for buyers looking to find reliable and experienced partners.
Firstly, trade shows and expos provide a unique opportunity to physically inspect and evaluate different die casting molds. Buyers can examine the quality of the molds, assess the materials and production processes used, and interact face-to-face with manufacturers. This enables them to make informed decisions based on their specific requirements.
In addition, trade shows and expos allow buyers to gain valuable insights into the latest trends, technologies, and innovations in the die casting industry. Attendees can attend seminars, presentations, and workshops where experts discuss advancements in mold design, material selection, and manufacturing techniques. This knowledge can help buyers identify potential suppliers who are staying up-to-date with industry best practices.
Furthermore, trade shows and expos provide a platform for buyers to network and establish relationships with suppliers. Face-to-face interactions foster trust and allow for open discussions about pricing, customization options, and future collaboration. Building a strong network of reliable suppliers is crucial for long-term success in die casting mold sourcing.
To maximize the benefits of trade shows and expos, it is important to have a well-defined sourcing strategy. Before attending, buyers should research and identify the key exhibitors who specialize in die casting molds. This enables focused interactions and eliminates wasting time on irrelevant suppliers.
Overall, trade shows and expos are an efficient and effective way to source die casting molds in China. By leveraging these platforms, buyers can physically assess the quality of molds, stay updated with industry trends, and build relationships with trusted suppliers. The opportunities presented by these events make them a vital component of any die casting mold sourcing strategy.
The Role of Agents and Sourcing Companies in Facilitating die casting molds Purchases from China
Agents and sourcing companies play a crucial role in facilitating die casting molds purchases from China. Their expertise and networks help alleviate the challenges and risks associated with sourcing products from a foreign country. These entities act as intermediaries between the buyer and the Chinese manufacturers, ensuring a smooth and reliable purchasing process.
One of the primary advantages of utilizing agents and sourcing companies is their extensive knowledge of the Chinese market. They possess a deep understanding of the local manufacturing industry, including the capabilities and specializations of different suppliers. This knowledge allows them to identify suitable manufacturers that can meet the specific requirements of the buyer.
Agents and sourcing companies also help to bridge the language and cultural gap between buyers and manufacturers. Communication is crucial in any business transaction, and these intermediaries can effectively communicate the buyer’s requirements to the Chinese manufacturers. They serve as interpreters, translating technical specifications and ensuring that the buyer’s needs are fully understood by the manufacturers.
Additionally, agents and sourcing companies can provide invaluable assistance during the product development stage. They can offer recommendations on design improvements, material selection, and cost-saving measures. This expertise helps buyers optimize their product and ensure the highest quality standards.
Another significant role of agents and sourcing companies is risk management. They conduct thorough research and due diligence on potential suppliers, evaluating their credibility, production capabilities, and quality control systems. This evaluation mitigates the risk of dealing with unreliable or untrustworthy manufacturers. Agents and sourcing companies can also conduct on-site visits to assess the supplier’s facilities, production processes, and quality assurance protocols.
Furthermore, these intermediaries manage the logistics and shipping process, ensuring the timely delivery of products. They negotiate pricing, terms, and conditions on behalf of the buyer to ensure a fair and competitive deal. They also provide post-purchase support, including handling any issues or disputes that may arise.
In summary, agents and sourcing companies are crucial in facilitating die casting molds purchases from China. Leveraging their expertise, knowledge of the local market, and network of manufacturers, they streamline the purchasing process, minimize risks, ensure quality, and ensure timely delivery.
Price Cost Research for die casting molds manufacturers Companies in China, use temu.com and 1688.com
When it comes to die casting molds manufacturers in China, two websites stand out for price cost research: temu.com and 1688.com. These platforms provide valuable information on various aspects such as product quality, manufacturing capabilities, and competitive pricing, allowing businesses to make informed decisions.
Temu.com is a popular marketplace for sourcing products from China. It offers a user-friendly interface where companies can search for die casting molds manufacturers. The website provides detailed profiles of suppliers, including their business information, manufacturing capabilities, and product range. One can also find customer reviews and ratings, helping in the evaluation process. Moreover, temu.com allows users to directly contact suppliers and negotiate prices, ensuring a seamless buying experience.
1688.com, on the other hand, is a local Chinese website owned by Alibaba Group, known for its extensive database of Chinese manufacturers. It is primarily targeted towards domestic buyers, making it an excellent platform for price research. By utilizing translation tools, non-Chinese speakers can navigate the website with relative ease. Companies can search for die casting mold manufacturers, compare prices, and identify the ones that meet their criteria. Moreover, 1688.com provides insights into the Chinese market, enabling businesses to understand the prevailing price trends.
By combining the information obtained from temu.com and 1688.com, companies can conduct thorough price cost research for die casting mold manufacturers in China. These platforms provide a vast pool of options, allowing businesses to consider factors such as product quality, manufacturing capabilities, and pricing before making a decision. With the convenience of direct communication and negotiation, companies can ensure a competitive deal. It is important to note that while conducting price research, businesses should also evaluate other aspects like supplier’s reputation, delivery time, and after-sales service to make an informed choice.
In conclusion, temu.com and 1688.com are two reliable platforms for conducting price cost research for die casting molds manufacturers in China. By using these resources, businesses can gather essential information, compare prices, and ultimately select a supplier that best fits their requirements.
Shipping Cost for die casting molds import from China
When importing die casting molds from China, the shipping cost can vary depending on several factors. These factors include the size and weight of the molds, the shipping method chosen, the distance to the destination, and any additional services required.
For smaller and lightweight molds, air freight is usually the preferred shipping method. This is a faster option but can be more expensive compared to other methods. The cost of air freight can range from a few hundred to a few thousand dollars, depending on the size and weight of the molds.
If the molds are large and heavy, sea freight is a more cost-effective option. The cost of sea freight is determined by the volume, weight, and distance to the destination port. On average, sea freight costs can range from $2,000 to $8,000 for a container load of molds. However, this cost can increase if additional services such as port handling, customs clearance, and delivery to the final destination are required.
It is important to note that these costs are estimates and can vary depending on the specific circumstances and negotiation with shipping companies. Additionally, other costs such as import duties, taxes, and customs clearance fees may apply and should be accounted for when calculating the total shipping cost.
To ensure cost-effectiveness, it is recommended to compare quotes from different shipping providers, consider consolidating multiple molds into one shipment if possible, and plan ahead to avoid rush shipping which can significantly increase costs.
Compare China and Other die casting molds Markets: Products Quality and Price,Visible and Hidden Costs
China is a major player in the die casting molds market, but it is important to compare it with other markets in terms of product quality, price, visible and hidden costs.
When it comes to product quality, China has made significant improvements over the years. There are many high-quality die casting molds manufacturers in China who produce precision molds that meet international standards. However, there are also some manufacturers who compromise on quality in order to offer lower prices. On the other hand, countries like Germany, Japan, and the United States are known for their superior product quality and precision in die casting molds. These countries have strict quality control measures in place and prioritize the use of high-quality materials, resulting in durable and reliable molds.
Price is a significant factor in the die casting molds market. China is often considered a cost-effective option due to its lower labor and manufacturing costs. Chinese manufacturers can offer competitive prices, especially for mass-produced molds. However, it is essential to consider hidden costs such as shipping, customs duties, and import taxes, which can significantly increase the overall cost of purchasing molds from China. Other markets like Germany and Japan may have higher initial prices, but they often provide more value for money considering their superior quality and after-sales service.
Visible and hidden costs play a crucial role in choosing a die casting molds market. Beyond the initial purchase price, other visible costs include transportation, packaging, and insurance. Chinese manufacturers can easily ship their molds worldwide, giving them an advantage in terms of convenience and accessibility. However, hidden costs such as intellectual property risks, language barriers, and cultural differences should also be considered. Other markets may impose higher visible costs due to higher shipping expenses, but they often provide a more secure environment, protecting intellectual property rights and offering better communication channels.
In conclusion, while China has made remarkable progress in the die casting molds market, it is essential to consider various factors when comparing it with other markets. Product quality, price, visible and hidden costs should all be carefully evaluated before making a decision.
Understanding Pricing and Payment Terms for die casting molds: A Comparative Guide to Get the Best Deal
When it comes to pricing and payment terms for die casting molds, it is crucial to have a clear understanding to ensure that you get the best deal. The cost of a die casting mold is influenced by various factors, including complexity, size, material, and the number of cavities.
The pricing structure for die casting molds typically includes both the initial cost, known as the tooling cost, and the unit price for each part produced using the mold. The tooling cost covers the design, engineering, and manufacturing of the mold itself. This cost can vary significantly depending on the complexity of the mold and the number of cavities required.
The unit price per part is the cost associated with producing each individual component using the mold. This price is determined by factors such as material cost, labor cost, cycle time, and machine utilization. It is essential to clarify whether the unit price includes additional costs, such as finishing, machining, or any other post-processing steps required.
Payment terms for die casting molds can also vary between suppliers. Common payment arrangements include a percentage of the total cost upfront, with the remaining balance due upon completion, or structured payments at various stages of the mold production process. It is essential to discuss payment terms with the supplier and come to a mutually agreed-upon arrangement.
To ensure you get the best deal, it is advisable to obtain quotes from multiple suppliers. This allows you to compare prices, quality, and delivery lead times. However, be cautious of excessively low prices, as they may indicate compromised quality or hidden costs later on.
When reviewing quotes, it is crucial to thoroughly analyze the specifications and ensure they align with your requirements. Look for any potential additional costs or exclusions mentioned in the quote. It is also beneficial to ask for samples or references from the supplier to assess the quality of their previous work.
Negotiating the pricing and payment terms is another vital aspect of getting the best deal. If you have a long-term business relationship or plan to provide regular work to the supplier, you may have more leverage in negotiating favorable terms. Additionally, discussing any value-added services, such as design assistance or ongoing technical support, may enable you to obtain a better overall package.
In conclusion, understanding the pricing and payment terms for die casting molds is crucial to ensure the best deal. Carefully analyze the quotes, clarify any potential additional costs, and negotiate favorable terms based on your specific requirements. By doing so, you can find a reliable supplier that delivers high-quality molds at a competitive price point.
Chinese Regulations and Industry Standards Certifications for die casting molds,Import Regulations and Customs for die casting molds from China
China has a well-established set of regulations and industry standards certifications for die casting molds that ensure quality and safety. The key certifications are as follows:
1. China Compulsory Certification (CCC): Die casting molds that are produced or sold in China need to comply with CCC standards. This certification ensures the molds meet the necessary safety requirements.
2. ISO Standards Certification: ISO 9001:2015 is the standard most commonly required for die casting mold manufacturers. This certification ensures that the manufacturer follows quality management systems and meets international standards.
3. Quality Control Certifications: Manufacturers often hold additional quality control certifications such as ISO/TS 16949:2009, which guarantees the adherence to specific automotive industry requirements.
4. Environmental Management Certifications: ISO 14001:2015 ensures that manufacturers have implemented effective environmental management systems, reducing the environmental impact of their operations.
Regarding import regulations and customs for die casting molds from China, importers need to be aware of the following:
1. Import Duties: Each country has its own import duty rates for die casting molds. Importers should consult the customs regulations of their respective countries or seek assistance from customs brokers to determine the applicable duties.
2. Documentation: Importers will need to provide proper documentation, including a commercial invoice, bill of lading, packing list, and any applicable certifications or permits. These documents are necessary for customs clearance and to meet regulatory requirements.
3. Customs Valuation: Die casting molds’ value must be accurately declared for customs purposes. The declared value should reflect the transaction price and include any additional costs such as packaging, insurance, and transportation.
4. Customs Inspection: Customs authorities may conduct inspections to ensure compliance with import regulations and verify the accuracy of documentation. Importers should be prepared to assist with any requested inspections.
In summary, importers of die casting molds from China should be aware of the relevant certifications and regulations, such as CCC and ISO standards. They should also familiarize themselves with import duties, required documentation, customs valuation, and possible inspections. Seeking assistance from customs brokers or experts can help ensure a smooth import process.
Sustainability and Environmental Considerations in die casting molds Manufacturing
Sustainability and environmental considerations play a crucial role in the manufacturing of die casting molds. Die casting is a widely used manufacturing process that involves the production of complex-shaped metal parts by injecting molten metal into a mold cavity. However, this process can have significant environmental impacts if not managed properly.
One important aspect of sustainability is the efficient use of resources in mold manufacturing. It is essential to optimize the design and production of molds to minimize material waste and energy consumption. Advanced computer-aided design (CAD) and manufacturing (CAM) technologies can be employed to create molds with intricate designs, reducing the amount of material needed. Additionally, using simulation tools can help analyze and optimize the mold filling process, further minimizing material waste.
The selection of materials for mold manufacturing is another critical consideration. Traditional mold materials such as steel have a high environmental impact due to their extraction and manufacturing processes. However, alternative materials like aluminum, which have a lower carbon footprint, can be used to create lightweight and durable molds. Moreover, the recycling of mold materials is crucial for sustainability. Aluminum molds, for example, can be easily melted down and reused, reducing the need for new material extraction.
Further, energy efficiency is crucial in the manufacturing process. Implementing energy-saving technologies, such as high-efficiency machinery and energy recovery systems, can significantly reduce energy consumption. Additionally, optimizing the production process, reducing idle times, and adopting lean manufacturing practices can further minimize energy waste.
Mitigating the environmental impact of mold manufacturing also involves proper waste management. The implementation of effective waste management strategies, such as recycling and proper disposal of waste materials, is important to minimize the impact on the environment.
In conclusion, sustainability and environmental considerations are vital in die casting mold manufacturing. Optimizing material usage, using environmentally friendly materials, focusing on energy efficiency, and implementing effective waste management strategies are all essential steps in reducing the environmental impact of the manufacturing process. By integrating these considerations, die casting mold manufacturers can contribute to a more sustainable and environmentally conscious industry.
List The Evolution history of “die casting molds”
The evolution of die casting molds can be traced back to ancient times, where metals like bronze and iron were cast using primitive methods. However, it was not until the 19th century that die casting as we know it today began to take shape.
In the early 1800s, hot chamber die casting was developed by midwestern inventor Joseph Hall. This method allowed for the production of intricate shapes with high accuracy and helped to popularize die casting in various industries. The molds used during this time were typically made of iron or steel.
By the early 20th century, advancements in technology led to the development of different types of die casting molds. The first injection molding machines were introduced in the 1920s, which allowed for the production of smaller and more detailed parts. These molds were often made of cast aluminum, as it offered better heat dissipation and shorter cycle times compared to iron or steel molds.
Over the following decades, die casting molds continued to evolve. The introduction of computer numerical control (CNC) machines in the 1970s allowed for greater precision and automation in mold making. This, along with improvements in design software and materials, enabled the production of more complex and efficient molds.
In recent years, advancements in additive manufacturing, commonly known as 3D printing, have significantly impacted the evolution of die casting molds. 3D printing enables the creation of molds with intricate geometries that were previously unachievable using traditional machining techniques. Additionally, it offers faster prototype development and reduces production costs.
Furthermore, with the increasing demand for sustainability and environmental consciousness, efforts have been made to develop molds that reduce material waste and energy consumption. Mold designs now strive to maximize the lifespan of the mold and minimize the scrap generated during the casting process.
In conclusion, die casting molds have come a long way since their primitive beginnings. From simple iron molds to complex aluminum and 3D-printed molds, the evolution has been driven by advances in technology, materials, precision, and sustainability. These advancements continue to redefine the capabilities and possibilities of die casting in various industries.
The Evolution and Market Trends in die casting molds Industry
The die casting molds industry has witnessed significant evolution and market trends in recent years. Die casting is a manufacturing process in which molten metal is injected under high pressure into a mold cavity to form complex shapes with high precision. The molds play a crucial role in this process as they determine the final shape and quality of the cast parts.
One major evolution in die casting molds is the shift towards the use of advanced materials. Traditional molds were typically made of steel, but now there is a growing preference for materials like ceramic, graphite, and composites. These materials offer improved thermal conductivity, higher strength-to-weight ratio, and better wear resistance, thus enhancing mold performance and durability.
Another important trend is the adoption of additive manufacturing or 3D printing in mold production. This technology allows for the rapid and cost-effective creation of complex mold designs. It also enables customization and faster prototyping, which is particularly beneficial for industries with high product variability or short product lifecycles.
Moreover, there has been a growing emphasis on process optimization and automation in die casting mold production. Manufacturers are using advanced software and simulation tools to design and analyze molds, ensuring optimal mold geometry and gating systems for improved casting quality and efficiency. Automation is also being employed in mold manufacturing and maintenance processes, reducing production time and costs while improving consistency and precision.
In terms of market trends, the die casting molds industry has been witnessing significant growth due to the increasing demand for lightweight and complex-shaped components in industries such as automotive, aerospace, and electronics. The need for energy-efficient vehicles, miniaturized electronics, and lightweight aircraft has driven the demand for high-quality die cast parts, thus propelling the demand for molds.
Additionally, the trend towards sustainable manufacturing practices has influenced the die casting molds industry. Manufacturers are adopting eco-friendly mold materials and implementing recycling programs to minimize waste and reduce environmental impact.
In conclusion, the die casting molds industry has evolved through advancements in materials, processes, and technologies. The market trends indicate a growing demand for high-quality, lightweight, and complex-shaped die cast components, which has fueled the need for advanced and sustainable die casting molds.
Custom Private Labeling and Branding Opportunities with Chinese die casting molds Manufacturers
Chinese die casting molds manufacturers offer a variety of custom private labeling and branding opportunities. With their extensive expertise and advanced technology, these manufacturers can help businesses create unique and professional die casting molds branded with their own logos and designs.
One of the primary benefits of working with Chinese manufacturers is their cost-effectiveness. With lower production costs compared to other countries, businesses can achieve substantial savings without compromising on quality. Chinese manufacturers can produce high-quality die casting molds that meet international standards while maintaining competitive pricing.
Moreover, these manufacturers offer flexibility in terms of customization. Businesses can collaborate closely with Chinese manufacturers to design and create customized molds that align with their brand image. From choosing the materials and finishes to incorporating intricate details, manufacturers can cater to specific branding requirements.
Chinese manufacturers also provide efficient turnaround times. Their expertise in die casting mold production and excellent logistical capabilities ensure prompt and timely delivery, meeting customers’ deadlines and satisfying their needs for quick production cycles.
Additionally, Chinese manufacturers often adopt strict quality control measures to ensure the durability and reliability of the molds. Keeping up with international standards and certifications, they focus on producing molds that are resistant to wear, corrosion, and deformation, ensuring a longer lifespan and reducing the need for frequent replacements.
To summarize, partnering with Chinese die casting molds manufacturers offers businesses the opportunity to customize and brand their molds efficiently, cost-effectively, and with high quality. The expertise, flexibility, and efficiency of these manufacturers make them a preferred choice for businesses seeking to enhance their branding through custom die casting molds.
Tips for Procurement and Considerations when Purchasing die casting molds
When procuring die casting molds, there are several important considerations to keep in mind to ensure the best possible outcome. Here are some tips and factors to consider when purchasing die casting molds:
1. Choose a reputable supplier: It is crucial to select a trustworthy and experienced supplier who has a proven track record in producing high-quality die casting molds. Conduct thorough research, read customer reviews, and request samples to assess their capabilities.
2. Define your requirements: Clearly communicate your specific needs and requirements to the supplier. This includes the type of material, dimensions, tolerances, surface finish, and any other essential features the mold must possess.
3. Consider mold design: The design of the die casting mold plays a crucial role in determining the final quality of the product. Ensure the supplier has skilled engineers who can optimize the mold design, considering factors such as part ejection, gating system, cooling, and venting.
4. Material selection: Selecting the right material for the mold is vital to ensure its longevity and performance. Common materials for die casting molds include steel, aluminum, and H13 tool steel. Consider factors such as mold life, part complexity, and budget when choosing the material.
5. Quality control: Request information about the supplier’s quality control processes to ensure that they meet your standards. Ask about their inspection procedures, certifications, and testing methods to ensure the molds are thoroughly checked before delivery.
6. Cost considerations: While cost should not be the sole determinant, it is still an essential factor. Compare the pricing between different suppliers, but make sure not to compromise on quality. Cheaper molds may have a shorter lifespan or lower quality, leading to increased costs in the long run.
7. Lead time: Discuss the lead time required for the mold production, considering your specific time frames and production needs. Balance the time required for mold production with your overall project timeline.
8. After-sales support: Inquire about the supplier’s after-sales support and warranty policies. Efficient customer service and assistance in case of repairs or modifications to the mold are essential.
In conclusion, when purchasing die casting molds, it is crucial to choose a reputable supplier, clearly define requirements, consider mold design and material selection, prioritize quality control, consider cost, evaluate lead time, and inquire about after-sales support. These considerations will help ensure the procurement of reliable and high-quality die casting molds for your specific needs.
FAQs on Sourcing and Manufacturing die casting molds in China
1. Why should I consider sourcing and manufacturing die casting molds in China?
Sourcing and manufacturing die casting molds in China offers several advantages such as cost-effectiveness, access to a skilled labor force, and a well-established manufacturing infrastructure. Chinese manufacturers often offer competitive pricing due to lower labor and production costs, making it an attractive option for businesses. Additionally, China has a large pool of experienced engineers and technicians who specialize in die casting mold production, ensuring high-quality manufacturing. The country’s well-developed transportation and logistics networks also facilitate efficient delivery of molds to global destinations.
2. How can I find reliable die casting mold manufacturers in China?
To find reliable manufacturers, it is recommended to conduct thorough research and due diligence. Online sourcing platforms like Alibaba, Global Sources, or Made-in-China can provide a wide range of suppliers. It is essential to scrutinize their certifications, reviews, and previous customer feedback to assess their reliability and expertise. Requesting samples, conducting factory visits, and engaging in detailed communication with potential suppliers can also help evaluate their capability and quality standards.
3. What should I consider when selecting a Chinese die casting mold supplier?
Several factors should be considered when selecting a supplier. It is crucial to assess their experience in die casting mold manufacturing, their technical capabilities, and their ability to meet quality standards. Evaluating their facility, equipment, and production capacity can provide insights into their manufacturing capabilities. Additionally, verifying their compliance with ISO or other relevant certifications ensures adherence to industry standards. Clear communication channels, prompt responses, and willingness to provide regular updates are also indicators of a reliable supplier.
4. How can I ensure the quality of die casting molds manufactured in China?
Ensuring quality requires adopting specific measures during the sourcing and manufacturing process. Clearly defining quality requirements, such as dimensional accuracy and material specifications, is crucial. Insisting on regular inspections at various production stages can help identify and address any issues before completion. Collaborating closely with the supplier, providing detailed specifications, and approving samples before mass production are highly recommended. Conducting third-party quality control inspections or working with independent quality control agencies can further ensure the reliability and conformity of the final product.
5. How long does it take to manufacture die casting molds in China?
The manufacturing time for die casting molds in China varies depending on the complexity of the design, size, and production capacity of the supplier. On average, it takes anywhere from four to twelve weeks, with some manufacturers offering expedited services for an additional cost. Timely communication and coordination with the supplier can help streamline the manufacturing process and ensure delivery within the desired timeline.
Why contact sourcifychina.com get free quota from reliable die casting molds suppliers?
Sourcifychina.com is likely to offer free quota for contacting reliable die casting molds suppliers for several reasons. Firstly, by providing a free quota, Sourcifychina.com aims to attract potential customers and generate interest in their services. Offering a cost-saving initiative helps to draw attention from individuals and businesses seeking die casting molds suppliers in China.
Secondly, by obtaining a free quota, customers can assess the capabilities and pricing of various die casting molds suppliers without incurring any expenses initially. This allows customers to compare different options and make an informed decision based on their specific requirements and budgets.
Moreover, Sourcifychina.com likely has partnerships or agreements with these die casting molds suppliers. By offering a free quota, Sourcifychina.com can promote these suppliers and encourage potential customers to engage with them. This benefits both Sourcifychina.com and the suppliers as they can gain exposure and potentially secure new business opportunities.
Furthermore, offering a free quota may assist in building trust and credibility with potential customers. By removing the financial barrier associated with contacting suppliers, Sourcifychina.com demonstrates a level of transparency and willingness to support customers in their sourcing needs. This can help establish a positive reputation for the platform and encourage more individuals and businesses to utilize their services.
In conclusion, Sourcifychina.com likely offers a free quota to incentivize potential customers to contact reliable die casting molds suppliers. This approach helps attract customers, allows for cost-effective decision-making, promotes the suppliers, and builds trust with customers.