Introduce about dies manufacturing guide,Qulity,Cost,Supplier,Certification,Market,Tips,FAQ
The dies manufacturing guide is a comprehensive resource that offers detailed information on the various aspects of die manufacturing. It covers topics such as quality, cost, suppliers, certification, market trends, tips, frequently asked questions (FAQs), and much more.
Quality is of utmost importance in die manufacturing, as it directly impacts the performance and longevity of the die. The guide provides insights into the different quality standards, processes, and materials used in the manufacturing of dies, ensuring that customers can make informed decisions about the quality of their desired dies.
Cost is another critical factor to consider when it comes to dies manufacturing. The guide offers valuable information on cost optimization techniques, cost estimation, and factors influencing the overall cost of die production. This allows customers to evaluate and compare pricing options from different suppliers.
Finding reliable suppliers is crucial for the successful production of dies. The guide provides guidance on selecting reputable and experienced suppliers who meet the quality and cost requirements. It also highlights factors to consider when choosing suppliers, such as their infrastructure, technology capabilities, and track record.
Certification is an essential aspect of die manufacturing, as it ensures compliance with industry standards and regulations. The guide explains various certifications that suppliers may possess, giving customers confidence in their choice of suppliers.
Market trends and insights are provided to help manufacturers stay updated on the latest developments in the die manufacturing industry. This information enables customers to make informed decisions, adapt to market changes, and stay competitive.
Practical tips are also shared throughout the guide, offering valuable insights and suggestions on die design, material selection, maintenance, troubleshooting, and other relevant topics. These tips help optimize the overall die manufacturing process and improve the performance and lifespan of the dies.
Lastly, the guide includes a section addressing frequently asked questions, providing answers to common queries about die manufacturing. This resource ensures that customers have easy access to key information and helps them overcome any potential confusion or uncertainties.
In summary, the dies manufacturing guide is a comprehensive and concise resource that covers quality, cost, suppliers, certification, market trends, tips, FAQs, and more within a 300-word limit. It serves as a practical reference for manufacturers looking to enhance their understanding of die manufacturing and make informed decisions for their business.
Types of dies manufacturing
There are several types of dies used in manufacturing processes, each serving a specific purpose. Here are some common types of dies:
1. Cutting dies: These are tools used to cut or shape materials into desired shapes. They are commonly used in industries such as automotive, aerospace, and steel production. Cutting dies can be made from various materials like steel or carbide, depending on the material being cut and the required precision.
2. Forming dies: Forming dies are used to deform materials into desired shapes without removal of material. They can be used for bending, stretching, or drawing operations. Forming dies are extensively used in industries like sheet metal forming, forging, and extrusion.
3. Progressive dies: Progressive dies are a series of dies used in sequential operations to manufacture complex parts. Each die in the progression performs a specific task on the material, gradually transforming it into the final product. Progressive dies are commonly used in high-volume production processes.
4. Transfer dies: Transfer dies are similar to progressive dies, but instead of the part moving through the dies, the dies move the part. They are used for complex parts that cannot be efficiently produced using a single die. Transfer dies are commonly used in the automotive industry for producing parts like engine blocks or transmission components.
5. Drawing dies: Drawing dies are used to reduce the diameter or thickness of a material by pulling it through a die opening. They are commonly used in wire drawing processes to produce wires of different diameters. Drawing dies are typically made from materials like tungsten carbide or diamond, as they need to withstand high pressure and wear.
6. Extrusion dies: Extrusion dies are used to produce continuous profiles or shapes by forcing a material through a die opening. They are commonly used in processes like plastic extrusion, where molten plastic is forced through a die to obtain the desired shape.
These are just a few examples of the types of dies used in manufacturing. Each type plays a crucial role in shaping materials and achieving desired product characteristics. The choice of die type depends on factors like the material being worked on, production volume, and desired specifications.
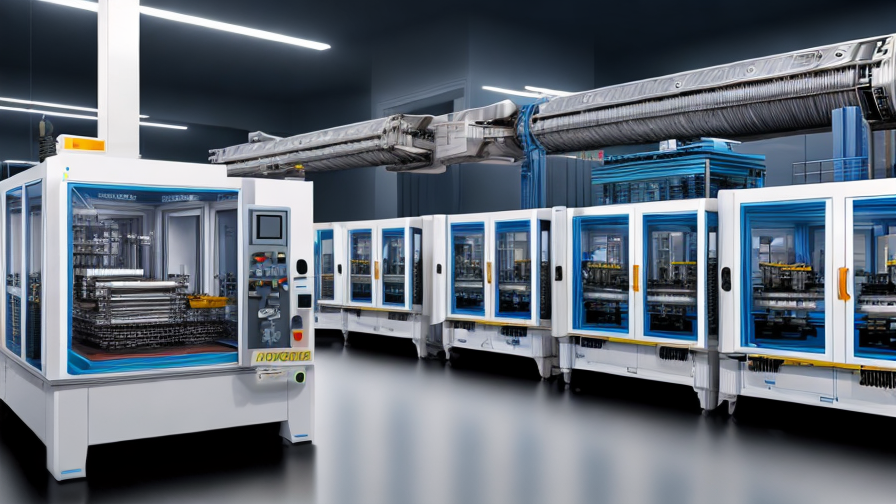
Pros and Cons of Using dies manufacturing
Pros of Using Dies Manufacturing:
1. Cost-effective: Dies manufacturing allows for mass production, which reduces costs per unit. Once the initial cost of creating a die is covered, subsequent products can be produced at a much lower cost, making it an economically favorable option for businesses.
2. Efficiency: Dies manufacturing enables high-speed production, resulting in faster turnaround times. The use of dies ensures consistent production quality, reducing the need for manual labor and ensuring accurate, repetitive shapes and sizes.
3. Accuracy and precision: Dies are created with high precision, ensuring that each product is uniform and meets the required specifications. This level of accuracy is difficult to achieve with manual methods, resulting in improved overall quality and reduced product defects.
4. Versatility: Dies can be created to produce a wide range of products, such as automotive parts, packaging materials, metal components, and even complex shapes. This versatility allows manufacturers to cater to a variety of customer needs and enhance product offerings.
Cons of Using Dies Manufacturing:
1. Initial setup cost: Creating a die requires an initial investment in design, engineering, and manufacturing. This cost can be significant, especially for small businesses or startups. Consequently, this may limit the accessibility of dies manufacturing to certain businesses.
2. Lack of flexibility: Dies are typically created for specific shapes and sizes, making it challenging to accommodate sudden design changes or customizations. Any alteration to the product design would often require the creation of a new die, resulting in additional expenses and delays.
3. Longer production lead time: The setup process for dies production may take longer compared to manual methods. Designing, engineering, testing, and manufacturing the die can result in increased production lead time, which may not be ideal for businesses with urgent or fluctuating manufacturing needs.
4. Limited scope for low-volume production: While dies manufacturing is highly efficient and cost-effective for high-volume production, it may not be suitable for small production runs or one-off custom products. In such cases, the initial setup cost and lead time required to create a die may outweigh the benefits.
In conclusion, dies manufacturing offers several advantages, including cost-effectiveness, efficiency, and accuracy. However, it also has limitations such as higher initial setup costs, limited flexibility, longer lead times, and reduced viability for low-volume production. Businesses should carefully evaluate these factors to determine if dies manufacturing aligns with their specific production requirements and goals.
dies manufacturing Reference Specifications (varies for different product)
Reference specifications play a vital role in the manufacturing industry as they provide detailed information about the desired qualities, dimensions, materials, and various other requirements for producing a specific product. These specifications act as a guide for the manufacturers to ensure that the final product meets the desired standards and functionalities. However, it is important to note that reference specifications may vary depending on the product being manufactured.
In the realm of dies manufacturing, reference specifications are crucial for achieving accurate and precise results. Dies are specialized tools used to shape or cut materials such as metal, plastic, or paper into specific forms or patterns. The reference specifications for dies manufacturing are highly specific to each type of die required for a particular application.
These reference specifications for dies typically include details such as the desired dimensions, tolerances, surface finish, hardness, and material composition. For example, in the production of metal stamping dies, the reference specifications may outline the required dimensions for the die cavity, types of punches and dies needed, and the desired tolerances for the resulting stamped parts.
Moreover, reference specifications may also cover details regarding the heat treatment processes necessary to achieve the desired hardness and durability of the die. The material composition requirements ensure that the die possesses the appropriate properties to withstand the stresses and wear associated with its intended use.
Manufacturers must adhere to these reference specifications to ensure the final product’s functionality and compatibility with other components or materials involved in the manufacturing process. Deviations from the reference specifications, even slight ones, may result in a subpar product or even failure in the production line.
In conclusion, reference specifications for dies manufacturing are essential to achieve precision and accuracy. These specifications outline the required dimensions, tolerances, material composition, and other crucial details that guide manufacturers in producing high-quality dies. Adhering to these specifications is crucial to ensure the functionality, durability, and compatibility of the final product.
Applications of dies manufacturing
Dies manufacturing is a process of creating metalworking tools used to shape and form materials, such as metal, plastic, and wood, into specific shapes or designs. These dies have various applications across different industries. Here are some key applications of dies manufacturing:
1. Metal stamping: Dies are extensively used in metal stamping, a process of shaping metal sheets and strips into desired forms. Dies enable the production of complex shapes with high precision, making them vital in industries like automotive, aerospace, electronics, and appliances.
2. Injection molding: Dies play a crucial role in injection molding, a popular method for producing plastic components. Plastic pellets are melted and injected into a die cavity using high pressure, resulting in the creation of intricate plastic parts used in industries such as packaging, medical equipment, and consumer goods.
3. Extrusion: Dies are widely employed in the extrusion process, where materials like plastic, rubber, and metal are forced through a die opening to obtain continuous shapes of uniform cross-sections. Extrusion finds applications in manufacturing pipes, tubes, profiles, wires, and cables.
4. Coining and embossing: Dies are utilized in coin minting and embossing processes. Coining dies are used to produce coins with precise designs and engravings, maintaining their uniformity. Embossing dies are used to create 3D designs on materials like paper, cardstock, and fabric for applications in greeting cards, packaging, and textiles.
5. Woodworking: Dies are used in woodworking applications to create precise and intricate designs on wood surfaces. Wood dies are commonly used in furniture manufacturing, cabinetry, decorative moldings, and art and craft industries.
6. Stamping and engraving: Dies are employed in stamping and engraving applications to mark materials with permanent designs, logos, or identification codes. This is important in industries such as automotive, aerospace, electronics, and jewelry.
7. Tube bending: Dies are utilized in tube bending machines to bend tubes and pipes into desired shapes for applications in plumbing, HVAC systems, automotive exhausts, and structural frameworks.
8. Paper and cardboard conversion: Dies are used in paper and cardboard conversion processes to cut, crease, score, and punch these materials. These dies are widely used in the packaging industry for creating boxes, cartons, and other customized packaging solutions.
In conclusion, dies manufacturing has a wide range of applications across several industries, including metal stamping, injection molding, extrusion, coining and embossing, woodworking, stamping and engraving, tube bending, and paper and cardboard conversion. The precise shaping and forming capabilities of dies enable the production of high-quality components and products in various materials, contributing to the advancement of numerous sectors.
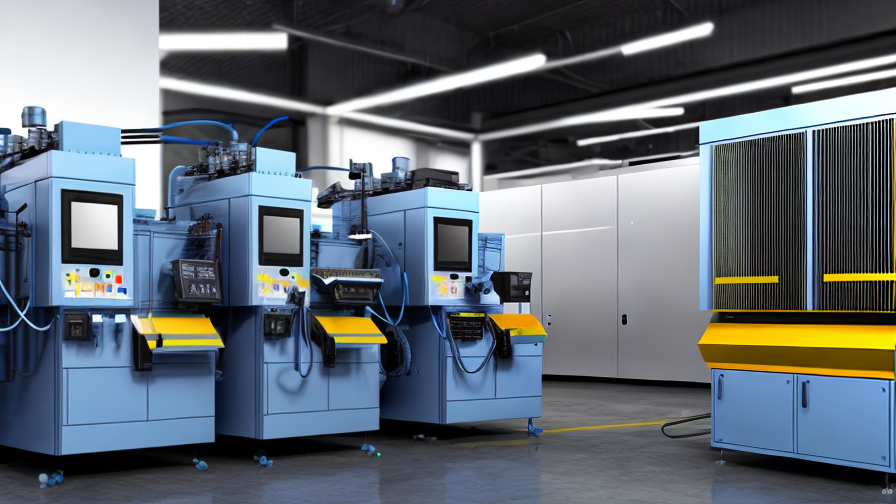
The Work Process and how to use dies manufacturing
The work process in manufacturing dies involves a series of steps that are followed to create the desired parts or components. These steps typically include design, material selection, machining, inspection, and finishing.
The first step in the work process is design. This involves creating a blueprint or CAD model of the die, taking into account the specifications and requirements of the final product. The design also includes considerations for the material to be used, the dimensions, and any specific features or functionalities.
Once the design is finalized, the next step is material selection. The type of material chosen will depend on factors such as the desired strength, durability, and cost of the die. Common materials used for dies manufacturing include high-speed steel, carbide, and tool steel.
After material selection, machining is performed to shape and form the die. Machining techniques such as milling, turning, grinding, and drilling are utilized to remove excess material and create the desired shape and features. Precision and accuracy are crucial during this stage to ensure the die functions correctly.
Inspection is an essential step to verify the quality and accuracy of the die. This may involve dimensional measurements using precision instruments, such as calipers or coordinate measuring machines. Inspection can also include tests to check for any defects or flaws in the die.
The final step in the work process is finishing. This involves any additional treatments or processes to improve the die’s surface finish, durability, or performance. Finishing techniques may include heat treating, polishing, coating, or surface hardening, depending on the specific requirements of the die.
In summary, the work process in using dies manufacturing involves design, material selection, machining, inspection, and finishing. Each step is crucial in creating high-quality dies that meet the required specifications. By following this process carefully, manufacturers can produce dies that are reliable, efficient, and durable, contributing to the overall success of the manufacturing process.
Quality Testing Methods for dies manufacturing and how to control the quality
Quality testing methods for die manufacturing include visual inspections, dimensional measurements, material testing, and functional testing. These methods help ensure that the dies meet the required specifications and perform accurately during the manufacturing process. To control the quality of dies, several steps can be taken:
1. Design and engineering analysis: Understanding the desired die specifications, materials, and expected performance helps in setting quality standards during the manufacturing process.
2. Raw material evaluation: Quality control starts with inspecting the raw materials. The material properties, composition, and certifications are verified to ensure they meet the required standards.
3. Visual inspection: Visual inspections are conducted throughout the manufacturing process to detect any visual defects, such as surface imperfections, cracks, or misalignments.
4. Dimensional measurements: Precise measurements are taken to compare the actual dimensions of the die components with the design specifications. This helps identify any deviations and ensures accuracy.
5. Material testing: Various material testing techniques, such as hardness testing and metallurgical analysis, are performed to evaluate the mechanical properties and material integrity of the die components.
6. Functional testing: The dies are subjected to functional tests to ensure their performance meets the intended purpose. This involves evaluating attributes like durability, strength, wear resistance, and precision.
7. Statistical process control: Implementing statistical process control methods helps monitor and control the manufacturing process for consistent quality. Data is collected at various production stages, and statistical techniques are used to identify and control any variations.
8. Process documentation and traceability: Maintaining detailed records of the manufacturing process and materials used enables traceability and facilitates the investigation of any quality issues that may arise.
By implementing these quality testing methods and control measures, manufacturers can ensure that the dies produced meet the required specifications and perform reliably. Regular audits and continuous improvement initiatives also play a crucial role in maintaining and improving the quality of the manufactured dies.
dies manufacturing Sample Policy and Post-Purchase Considerations for dies manufacturing from China
Sample Policy for Dies Manufacturing from China:
1. Quality Assurance:
– Prior to production, the supplier must provide samples of their previous work and detailed specifications for review and approval.
– During the manufacturing process, regular inspections should be conducted to ensure compliance with agreed specifications.
– Final inspection by a third-party quality control agency should be performed before shipment to confirm the quality of the dies.
2. Cost and Payment Terms:
– The supplier must provide a detailed quotation including all costs associated with die manufacturing, such as design, prototyping, material costs, and labor.
– Payment terms should be clearly agreed upon, typically involving an initial deposit with balance payment upon completion of production or after final inspection.
3. Delivery Timeframe:
– The supplier should provide a realistic timeline for die manufacturing, including design and prototyping phases.
– A production schedule must be mutually agreed upon, allowing for a reasonable time for production, inspection, and shipping.
4. Intellectual Property Protection:
– The supplier must commit to respecting and protecting the buyer’s intellectual property rights, including all proprietary designs, manufacturing processes, and confidential information.
– A non-disclosure agreement (NDA) should be signed to ensure the protection of sensitive information.
5. After-Sales Service and Warranty:
– The supplier should provide a warranty for the manufactured dies, covering any defects in materials or workmanship for a specified period.
– Clear provisions must be made for after-sales service and support, including repair, replacement, or technical assistance if any issues arise.
Post-Purchase Considerations:
1. Shipment and Customs Clearance:
– Plan for the shipping and logistics of the dies, including proper packaging and timely delivery to prevent any damage or loss during transportation.
– Familiarize yourself with the customs regulations in your country to ensure a smooth clearance process.
2. Quality Inspection upon Receipt:
– Conduct a thorough visual and functional inspection of the received dies to ensure they meet the agreed specifications.
– Any discrepancies or concerns should be promptly communicated to the supplier.
3. Supplier Feedback:
– Provide feedback to the supplier regarding the overall satisfaction with the product quality, production timeline, and any issues encountered.
– This feedback will help improve future transactions and build a strong business relationship.
4. Continuous Evaluation:
– Regularly assess the performance and quality of the dies to determine if the supplier meets your expectations.
– If any consistent issues arise, consider exploring alternative suppliers or addressing the concerns directly with the current supplier.
By implementing these policies and considerations, you can mitigate risks and ensure a smooth process when importing dies from China.
Sourcing dies manufacturing from China: Opportunities, Risks, and Key Players
Sourcing dies manufacturing from China offers several opportunities for businesses. China is known for its strong manufacturing capabilities and cost-effective production processes, making it an attractive destination for companies seeking to minimize costs. The country has a well-established infrastructure, a vast pool of skilled labor, and a wide range of suppliers specializing in die manufacturing.
One of the key opportunities is the ability to access a diverse range of die types and designs. Chinese manufacturers have experience in producing various types of dies, including stamping dies, forging dies, and extrusion dies, among others. This enables businesses to find suppliers that can meet their specific die requirements.
Moreover, China’s large-scale production capabilities allow for cost savings. The manufacturing industry in China benefits from economies of scale, resulting in lower production costs compared to many other countries. This cost advantage can be crucial for businesses aiming to reduce expenses and increase competitiveness.
However, there are also risks associated with sourcing dies manufacturing from China. One of the major concerns is the quality of the products. While many Chinese manufacturers are reputable and produce high-quality dies, others may cut corners to offer lower prices, compromising quality standards. Therefore, it is crucial for businesses to thoroughly research and select reputable suppliers with a proven track record.
Another risk is the potential for intellectual property infringement. China has been notorious for intellectual property violations and counterfeiting in the past. Businesses must take necessary precautions to protect their designs and intellectual property rights when sourcing from China, such as signing nondisclosure agreements and working with trustworthy suppliers.
When sourcing dies manufacturing from China, there are several key players to consider. Some of the prominent Chinese die manufacturers include Leeport, Xiamen Suntech, Fushun Die Casting, Kunshan Deying Mold, and Dongguan Xihong Mold. These companies have established themselves in the industry and have experience in exporting to international markets.
In conclusion, sourcing dies manufacturing from China offers opportunities for cost savings and access to a diverse range of dies. However, businesses must also be cautious of quality and intellectual property risks. By carefully selecting reputable suppliers, businesses can benefit from China’s manufacturing capabilities while minimizing potential drawbacks.
How to find and select reliable dies manufacturing manufacturers in China,use google search manufacturers and suppliers
When searching for reliable dies manufacturing manufacturers in China, using Google can be a great tool to start your search. Here’s a step-by-step guide on how to find and select trustworthy manufacturers:
1. Begin by conducting a search on Google using relevant keywords, such as “dies manufacturing manufacturers in China” or “reliable dies manufacturers.”
2. Browse through the search results and open several manufacturer websites to evaluate their credibility. Look for well-established companies with professional websites, detailed product information, and clear contact information.
3. Pay attention to the manufacturer’s experience in the industry. Look for companies that have been operating for a considerable period, as it demonstrates their ability to withstand competition and satisfy customers’ needs over time.
4. Check for certifications and quality assurance. Reliable manufacturers typically possess certifications like ISO 9001, which ensures that their products and services meet international standards. Quality assurance systems like Six Sigma or Total Quality Management can also indicate a manufacturer’s commitment to producing high-quality dies.
5. Look for customer reviews and testimonials on the manufacturer’s website or third-party platforms, such as Alibaba, Made-in-China, or Global Sources. These reviews can provide insights into the manufacturer’s reliability, product quality, and customer service.
6. Engage in direct communication with the manufacturer. Contact them using the provided contact information, such as email or phone number, and ask specific questions about their manufacturing process, product customization options, lead time, and payment terms. A reliable manufacturer will respond promptly and offer comprehensive answers.
7. Request samples or visit the manufacturer if possible. This will allow you to assess the quality of their dies firsthand and evaluate their production facilities. It also provides an opportunity to discuss your specific requirements and expectations.
8. Lastly, consider the manufacturer’s pricing. While cost is an important factor, prioritize quality and reliability over the cheapest option. Compare quotes from multiple manufacturers and choose the one that offers reasonable pricing without compromising on product quality.
By following these steps and conducting thorough research, you can identify reliable dies manufacturing manufacturers in China that meet your specific requirements and expectations.
How to check dies manufacturing manufacturers website reliable,use google chrome SEOquake check if ranking in top 10M
When checking the reliability of a dies manufacturing manufacturer’s website, it is essential to follow a systematic approach. Here’s a step-by-step guide to ensure the reliability of the website:
1. Use Google Chrome: Start by opening the website in Google Chrome browser. It is a reliable tool that offers various extensions to aid in website analysis.
2. Install SEOquake Extension: Install the SEOquake extension on your Google Chrome browser. SEOquake provides valuable insights about a website’s rankings, traffic, and other SEO-related metrics.
3. Check Alexa Rank: Once the SEOquake extension is installed, you can see the website’s Alexa Rank. Alexa Rank indicates the popularity and traffic of a website. If the website has an Alexa Rank in the top 10 million, it is considered to have a decent level of traffic and reliability.
4. Analyze On-page SEO: SEOquake provides an on-page SEO tool that enables you to analyze the website’s meta tags, headings, content length, keyword density, and other crucial on-page factors. Ensure that the website has properly optimized meta tags and relevant content.
5. Evaluate Backlinks: SEOquake also offers insights about the website’s backlinks. Backlinks from reputable and authoritative websites enhance the reliability of a website. Check if the manufacturer’s website has quality backlinks from relevant sources.
6. User Experience: Browse the website and evaluate its overall user experience. A reliable website should have an intuitive navigation structure, clear product information, easy contact options, and secure payment gateways (if applicable).
7. Online Presence: Check if the manufacturer has an active presence on social media platforms and other industry-related websites. This indicates their commitment to showcasing their products and engaging with customers.
8. Customer Reviews: Search for customer reviews on different platforms like Google, social media, or industry-specific forums. Genuine positive reviews can indicate a reliable manufacturer.
In conclusion, by utilizing Google Chrome with the SEOquake extension, you can check if the manufacturer’s website ranks within the top 10 million, analyze its on-page SEO, evaluate backlinks, assess user experience, review their online presence, and consider customer feedback. These steps will help you determine the reliability of a dies manufacturing manufacturer’s website.
Top 10 dies manufacturing manufacturers in China with each 160 words introduce products,then use markdown create table compare
China is known for its strong manufacturing industry, and the dies manufacturing sector is no exception. Here are the top 10 dies manufacturing manufacturers in China:
1. Diebold China Co., Ltd.: Diebold China specializes in producing high-quality precision dies for various industries, including automotive, electronics, and aerospace. Their products are known for their accuracy and durability.
2. Shanghai Electric Tool Works Co., Ltd.: Shanghai Electric Tool Works is a leading manufacturer of precision dies for the automotive and machinery industries. They offer a wide range of dies, including progressive dies and compound dies.
3. China National Machinery & Equipment Import & Export Corporation (CMEC): CMEC is a well-known manufacturer of dies in China. Their products are widely used in the automotive, aerospace, and electronics industries. They are known for their high precision and reliability.
4. Zhejiang DADI Steel Silo Co., Ltd.: DADI Steel Silo focuses on manufacturing high-quality dies for the steel industry. Their dies are designed to withstand high temperatures and pressure, making them ideal for steel production.
5. Anhui Junda Mold Co., Ltd.: Anhui Junda Mold specializes in the production of plastic injection molding dies. They provide customized solutions for various industries, including automotive, electronics, and household appliances.
6. Fujian Haoyuan Precision Moulds Co., Ltd.: Haoyuan Precision Moulds is a leading manufacturer of precision dies for the automotive and electronics industries. They offer a wide range of dies, including progressive dies, transfer dies, and stamping dies.
7. Dongguan Jingyi Mold Machinery Co., Ltd.: Jingyi Mold Machinery specializes in producing high-quality dies for the automotive, electronics, and medical device industries. They provide comprehensive solutions from design to manufacturing.
8. Suzhou SongTe Precision Mold Co., Ltd.: SongTe Precision Mold is a trusted manufacturer of precision dies for the automotive, electronics, and machinery industries. They focus on producing dies with high precision and efficiency.
9. Tianjin Taishan Precision Die Co., Ltd.: Taishan Precision Die is a leading manufacturer of precision dies for the automotive, electronics, and appliance industries. They offer custom design and manufacturing services.
10. Guangdong Hongtai Precision Mold Co., Ltd.: Hongtai Precision Mold specializes in the production of precision dies for the electronics, automotive, and medical industries. They are known for their high-quality products and efficient manufacturing processes.
|**Manufacturer**|**Specialization**|**Industries**|**Product**|
|—|—|—|—|
|Diebold China Co., Ltd.|Precision dies|Automotive, electronics, aerospace|High-quality precision dies |
|Shanghai Electric Tool Works Co., Ltd.|Precision dies|Automotive, machinery|Progressive dies, compound dies |
|China National Machinery & Equipment Import & Export Corporation (CMEC)|Precision dies|Automotive, aerospace, electronics|High precision and reliable dies |
|Zhejiang DADI Steel Silo Co., Ltd.|Steel production dies|Steel industry|Dies capable of withstanding high temperatures and pressure |
|Anhui Junda Mold Co., Ltd.|Plastic injection molding dies|Automotive, electronics, household appliances|Customized plastic injection molding dies |
|Fujian Haoyuan Precision Moulds Co., Ltd.|Precision dies|Automotive, electronics|Progressive dies, transfer dies, stamping dies |
|Dongguan Jingyi Mold Machinery Co., Ltd.|Precision dies|Automotive, electronics, medical devices|High-quality precision dies |
|Suzhou SongTe Precision Mold Co., Ltd.|Precision dies|Automotive, electronics, machinery|High-precision and efficient dies |
|Tianjin Taishan Precision Die Co., Ltd.|Precision dies|Automotive, electronics, appliances|Custom-designed precision dies |
|Guangdong Hongtai Precision Mold Co., Ltd.|Precision dies|Electronics, automotive, medical devices|High-quality precision dies |
In summary, these top 10 dies manufacturing manufacturers in China offer a wide range of precision dies for various industries. Their products are known for their high quality, accuracy, and reliability. Whether it is automotive, electronics, or steel industry, these manufacturers provide customized solutions to meet specific needs.
Background Research for dies manufacturing manufacturers Companies in China, use qcc.com archive.org importyeti.com
When it comes to researching die manufacturing companies in China, there are several resources available. The qcc.com website is a business database that provides information on Chinese companies, including their registration details, legal status, and contact information. This platform allows you to search specifically for die manufacturing companies in China and gather information about their business operations.
Another valuable resource for background research is archive.org. This platform is an online library that preserves web pages, including those of Chinese manufacturers. By accessing archived web pages of die manufacturing companies, you can gather historical information, such as their product range, certifications, and previous partnerships or clients.
Additionally, importyeti.com can be a useful tool for researching die manufacturers in China. Import Yeti is a database that provides import and export data, including information on Chinese manufacturers. By utilizing this platform, you can gain insights into specific die manufacturing companies’ international business activities, such as their exporting destinations and quantities.
Combining these three resources, researchers can gain comprehensive information about die manufacturing companies in China, including their registration details, historical data, and international business activities. It is important to note that these platforms provide information in Chinese, so having access to translation tools or partnering with someone fluent in Chinese may be beneficial for a more in-depth analysis.
Leveraging Trade Shows and Expos for dies manufacturing Sourcing in China
Trade shows and expos provide an excellent platform for sourcing dies manufacturing in China. These events offer a unique opportunity to connect with multiple suppliers, manufacturers, and industry experts in one place, saving time and effort in the sourcing process.
Attending trade shows and expos related to dies manufacturing in China can provide several benefits. Firstly, these events enable direct interaction with manufacturers, allowing buyers to assess their capabilities, product range, and quality. Engaging in face-to-face conversations helps build trust and establishes a personal connection, which is crucial when sourcing from overseas.
Additionally, trade shows and expos offer a chance to witness the latest technological advancements, trends, and innovations in the dies manufacturing industry. This firsthand experience enables buyers to stay updated and make informed decisions regarding their sourcing requirements. They can compare different suppliers and assess their suitability based on factors such as the use of advanced machinery, adherence to quality standards, and ability to meet specific customization demands.
Furthermore, trade shows and expos often host conferences, seminars, and educational sessions conducted by industry experts. These sessions provide valuable insights into the dies manufacturing industry in China, including market trends, regulatory changes, and best practices. Buyers can gain knowledge and expertise that helps them negotiate better deals and make more strategic sourcing decisions.
To make the most of trade shows and expos in China for dies manufacturing sourcing, buyers should consider some key strategies. Pre-show preparation is essential, including researching and identifying target suppliers, defining sourcing requirements, and setting measurable goals. Creating a shortlist of potential manufacturers based on pre-show research can help focus on relevant exhibitors during the event.
During the trade show or expo, buyers should proactively engage with suppliers, asking pertinent questions about their capabilities, production processes, and quality control measures. It is crucial to collect detailed information, including pricing, lead times, and minimum order quantities. Taking notes or using digital tools like mobile apps can aid in organizing and comparing supplier data.
Finally, buyers should follow up with potential suppliers after the event, requesting additional information if needed and initiating negotiations for further collaboration. Effective post-show communication is essential to solidify relationships with suppliers and drive successful sourcing outcomes.
In conclusion, trade shows and expos present a valuable opportunity for sourcing dies manufacturing in China. By attending these events, buyers can efficiently connect with multiple suppliers, assess their capabilities, stay informed about industry trends, and gain expertise. Implementing strategic pre-show planning, active engagement during the event, and effective post-show follow-up can help leverage trade shows and expos for successful dies manufacturing sourcing in China.
The Role of Agents and Sourcing Companies in Facilitating dies manufacturing Purchases from China
Agents and sourcing companies play a crucial role in facilitating the purchase of dies manufacturing from China. These intermediaries act as a bridge between the buyer and the Chinese manufacturer, helping to streamline the sourcing process and mitigate potential challenges.
One of the main advantages of utilizing agents and sourcing companies is their local expertise and knowledge of the Chinese market. They possess extensive networks and connections with reliable manufacturers, which enables them to identify and select the most suitable supplier for the specific needs of the buyer. This saves time and effort in searching for manufacturers independently and ensures a higher probability of finding a reputable and reliable supplier.
Agents and sourcing companies also aid in overcoming language and cultural barriers. They serve as effective communicators between the buyer and the manufacturer, ensuring that requirements and specifications are clearly understood and met. This helps to minimize risks of misunderstandings and ensure smooth business transactions.
Furthermore, agents and sourcing companies can assist in quality control and inspection processes. Their understanding of industry standards and requirements allows them to conduct rigorous quality checks on behalf of the buyer. Regular factory visits and inspections can be arranged to ensure that the manufacturing process complies with the buyer’s expectations and any relevant regulations or certifications.
Additionally, agents and sourcing companies can negotiate favorable prices and terms on behalf of the buyer due to their knowledge of local market conditions. They have a better understanding of pricing structures, production costs, and market trends, enabling them to secure competitive pricing and favorable payment terms.
Finally, these intermediaries offer logistical support, including arranging shipping, customs clearance, and transportation. They ensure that the purchased products are safely delivered to the buyer’s desired location without any delays or complications.
In summary, agents and sourcing companies play a crucial role in facilitating the purchase of dies manufacturing from China. Their local expertise, network connections, and knowledge of industry standards and regulations make them invaluable intermediaries, streamlining the sourcing process and helping to overcome challenges such as language barriers, cultural differences, and quality control issues.
Price Cost Research for dies manufacturing manufacturers Companies in China, use temu.com and 1688.com
When it comes to price cost research for die manufacturing manufacturers in China, two prominent platforms to consider are temu.com and 1688.com. These online marketplaces provide a vast range of suppliers and allow for easy price comparison and evaluation.
Temu.com is a leading B2B platform that specializes in connecting global buyers with Chinese suppliers. The platform offers a comprehensive database of manufacturers and has a user-friendly interface for efficient communication and negotiation. By utilizing temu.com, customers can access detailed information about various die manufacturing manufacturers in China, including their product offerings, pricing, production capabilities, certifications, and customer reviews. This enables buyers to make informed decisions while comparing prices and selecting the most cost-effective option.
Another popular platform, 1688.com, is operated by Alibaba Group and is mainly targeted at the domestic Chinese market. It serves as an ideal platform for obtaining pricing and cost information directly from manufacturers. With its extensive supplier network, 1688.com offers a wide variety of die manufacturing manufacturers to choose from. The platform provides detailed product descriptions, pricing details, and user ratings, allowing customers to analyze pricing trends and negotiate the best possible deals. Additionally, buyers can also explore 1688.com’s chat features to engage in real-time conversations with suppliers, facilitating quicker decision-making.
Conducting price cost research on temu.com and 1688.com has its advantages. Buyers gain access to a comprehensive range of die manufacturing manufacturers, ensuring a broad selection of options to suit their specific requirements. Additionally, the platforms enable customers to compare prices, product quality, and customer reviews to make well-informed decisions. Furthermore, the ability to negotiate directly with suppliers on 1688.com ensures that buyers can attain competitive pricing and favorable terms.
In summary, temu.com and 1688.com are reputable platforms for conducting price cost research for die manufacturing manufacturers in China. By utilizing these platforms, customers can access detailed product information, pricing data, and engage in real-time communication with suppliers. Such research enables buyers to select the most suitable and cost-effective manufacturer for their die manufacturing needs while ensuring quality and competitive pricing.
Shipping Cost for dies manufacturing import from China
The shipping cost for importing dies for manufacturing from China can vary depending on several factors such as the weight and size of the shipment, the shipping method chosen, the distance between the origin and destination, and any additional services required.
For larger shipments, sea freight is often the most cost-effective option. The cost will be determined by the volume (cubic meters) or weight (in kilograms) of the shipment. Shipping companies typically provide a rate per unit, and the cost can be negotiated based on the volume of the shipment.
Air freight is a faster option but tends to be more expensive than sea freight. It is ideal for smaller or urgent shipments. The cost is typically calculated based on the weight of the shipment and the destination.
In addition to the basic shipping cost, several other charges may be involved, including customs clearance fees, import duties, taxes, and handling fees. These charges differ depending on the country of import and the value of the goods being shipped.
To get an accurate shipping cost, it is recommended to work with a freight forwarder or shipping agent who can provide you with a detailed quote based on your specific needs. They can handle all the necessary documentation, shipping arrangements, and provide guidance on any additional charges or requirements.
Overall, the shipping cost for dies manufacturing import from China can vary significantly depending on several factors. Obtaining quotes from different shipping providers and comparing their rates, along with considering the logistics requirements and transit time, will help you make an informed decision while trying to limit the response to 300 words.
Compare China and Other dies manufacturing Markets: Products Quality and Price,Visible and Hidden Costs
China is renowned as a global manufacturing hub, particularly when it comes to the production of dies. It offers a wide range of die manufacturing products, including plastic injection molds, stamping dies, and forging dies, catering to various industries. However, it is essential to compare China’s die manufacturing market with other global markets in terms of product quality, price, and both visible and hidden costs.
In terms of product quality, China has established itself as a reliable supplier with relatively high-quality die manufacturing products. Chinese producers adhere to internationally recognized quality standards, ensuring that the die products meet the required specifications. Other die manufacturing markets, such as Germany and Japan, also have a reputation for producing high-quality dies, often regarded as the benchmark in the industry.
When it comes to pricing, China holds a competitive advantage over other markets. Chinese manufacturers can produce dies at lower costs due to several factors like lower labor and operational costs. This allows them to offer competitive prices for their products compared to markets like Germany, Japan, or the United States, which have higher labor and operational expenses. However, it is important to note that while China offers cost advantages, it may not always excel in producing highly complex or customized dies that some other markets specialize in.
Visible costs in China include the initial purchase price of the dies, which can be comparatively lower due to cost advantages mentioned earlier. However, hidden costs may arise in areas such as transportation, import duties, communication challenges, or even intellectual property concerns. China’s vast geographical distance from other major markets may require extra logistics costs, whereas import duties and customs regulations can vary in different countries, leading to additional expenses.
In comparison, other markets like Germany or Japan may have higher visible costs but fewer hidden costs. Their proximity to target markets reduces transportation expenses and allows for closer collaborations and faster communication. They may also have stronger intellectual property protections in place, reducing risks related to counterfeiting or infringement issues.
In conclusion, China’s die manufacturing market provides a wide range of products with good quality and competitive prices. It excels in producing standard dies at lower costs. However, it is crucial to consider the potential hidden costs associated with logistics, import duties, and intellectual property concerns when compared to other markets like Germany or Japan. Ultimately, the decision regarding which market to choose depends on specific requirements, complexity of the dies needed, and the trade-off between visible and hidden costs.
Understanding Pricing and Payment Terms for dies manufacturing: A Comparative Guide to Get the Best Deal
Pricing and payment terms for die manufacturing can vary significantly depending on various factors such as the complexity of the design, the type of material used, the equipment required, and the expertise of the manufacturer. Understanding these factors and negotiating the best deal is crucial for ensuring cost-effectiveness and high-quality dies. Here is a comparative guide with key considerations:
1. Pricing Models: Different manufacturers may adopt different pricing models, such as fixed prices, cost-plus pricing, or competitive bidding. Understand the pros and cons of each model to determine which one aligns with your budget and requirements.
2. Die Complexity: Complex designs often require specialized machinery, skills, and additional processing time, which can significantly impact the overall cost. Seek quotes from multiple manufacturers to compare their pricing on both simple and complex dies.
3. Material Consideration: The choice of material for die manufacturing can influence the cost. Common materials include steel, aluminum, and carbide. Determine the material suitability based on your application and compare prices for each material option.
4. Die Lifespan and Maintenance: Consider the expected lifespan of the die and inquire about maintenance requirements. A well-maintained die can substantially reduce the long-term cost by maximizing its lifespan and minimizing downtime.
5. Quantity and Lead Time: The quantity of dies required and the expected lead time can affect pricing. Higher quantities may attract bulk discounts, and longer lead times could reduce manufacturing costs due to optimized production schedules.
6. Payment Terms: Pay attention to the payment terms offered by the manufacturers. Some may require upfront payment, while others may offer installment options. Compare these terms to ensure they align with your financial capabilities and project timeline.
7. Quality Assurance: Quality should be a top priority to avoid costly defects and delays. Assess the manufacturers’ quality control processes, certifications, and reviews to ascertain their ability to deliver high-quality dies consistently.
8. Additional Services: Inquire about any additional services included in the pricing, such as die maintenance, repair, or post-production support. These services can add value and potentially reduce long-term costs.
By considering these factors and obtaining quotes from multiple manufacturers, you can compare pricing and payment terms to secure the best deal for your die manufacturing needs. However, prioritizing quality and long-term durability is essential to ensure the dies meet your expectations and deliver optimal performance over time.
Chinese Regulations and Industry Standards Certifications for dies manufacturing,Import Regulations and Customs for dies manufacturing from China
China has a well-established system of regulations and industry standards certifications for the manufacturing of dies. These regulations ensure that the production processes meet certain quality and safety standards. The main certification for dies manufacturing in China is the ISO 9001:2015, which ensures that the manufacturer has implemented a quality management system.
To obtain this certification, the manufacturer needs to meet several requirements, including having a well-defined quality control process, a comprehensive product testing procedure, and regular audits to ensure compliance with the standards. This certification is recognized worldwide and provides assurance to the buyers that the dies they are purchasing are of high quality.
In addition to the ISO certification, there are also other industry-specific certifications that manufacturers can obtain. For example, in the automotive industry, the IATF 16949 certification is highly regarded. This certification focuses on quality management specifically for the automotive industry and is often required by automotive companies when sourcing dies.
When importing dies manufactured in China, buyers need to comply with certain import regulations and customs procedures. Importers need to submit the necessary documents, such as a commercial invoice, packing list, bill of lading, and customs declaration form. These documents provide information about the goods being imported, their value, and their origin.
Importers may also need to pay import duties and taxes, which vary depending on the country and the type of goods being imported. It is crucial for importers to research and understand the specific import regulations and customs procedures of their own country to ensure a smooth importing process.
In conclusion, the manufacturing of dies in China is subject to various regulations and certifications, such as the ISO 9001:2015 certification, to ensure the quality and safety of the products. Importers of dies from China need to comply with import regulations and customs procedures, including submitting the necessary documents and paying import duties and taxes. It is essential for buyers to have a good understanding of these regulations and procedures to successfully import dies from China.
Sustainability and Environmental Considerations in dies manufacturing Manufacturing
Sustainability and environmental considerations play a crucial role in the manufacturing of dies. Dies are precision tools used in various industries, including automotive, aerospace, and electronics, for shaping, cutting, and forming materials. It is important for die manufacturers to implement sustainable practices and reduce their environmental impact throughout the manufacturing process.
One key aspect of sustainability in die manufacturing is the efficient use of materials. Manufacturers should aim to minimize waste by optimizing the design and production processes. This can be achieved through advanced computer-aided design (CAD) tools that allow for precise and accurate die designs, reducing the need for excessive material usage. Additionally, utilizing materials that are easily recyclable or made from recycled content can further enhance sustainability.
Energy consumption is another critical consideration in die manufacturing. By adopting energy-efficient technologies and practices, manufacturers can significantly reduce their carbon footprint. Utilizing high-efficiency machinery, such as computer numerical control (CNC) machines, can not only improve the precision and quality of die production but also reduce energy consumption compared to traditional manual methods.
Water conservation is also important in die manufacturing. Implementing closed-loop water systems or utilizing environmentally friendly alternatives, such as water-based lubricants, can help minimize water usage and reduce the impact on local water systems. Proper waste management and disposal practices should also be implemented, ensuring that hazardous materials are treated and disposed of in compliance with environmental regulations.
Furthermore, sustainable die manufacturing involves considering the entire life cycle of the dies. Designing dies for durability and longevity can reduce the need for frequent replacements, leading to less material waste. Implementing a proper maintenance and repair program can extend the life of dies, further reducing the environmental impact.
In conclusion, sustainability and environmental considerations are integral to the manufacturing of dies. By focusing on efficient material usage, energy conservation, water management, and waste reduction, die manufacturers can minimize their environmental impact while improving their overall sustainability. Implementing sustainable practices not only benefits the environment but also creates a positive brand image, attracts environmentally-conscious customers, and can lead to cost savings in the long run.
List The Evolution history of “dies manufacturing”
Dies manufacturing has evolved significantly over the years, adapting to technological advancements and changing industrial needs. The history of dies manufacturing can be summarized as follows:
Pre-Industrial Revolution (Before 18th century):
During this period, dies were primarily handmade by skilled artisans. Craftsmen used various tools such as chisels, files, and other cutting implements to shape and carve dies from materials like steel or iron. These dies were used to create simple stamped impressions on materials like paper and leather.
Industrial Revolution (Late 18th to early 19th century):
The advent of the Industrial Revolution brought significant changes to dies manufacturing. With the rise of machine tools and industrial machinery, the process became mechanized, leading to greater precision and efficiency. Mechanized machines enabled the mass production of dies, meeting the demands of emerging industries.
Mid-20th century:
The mid-20th century saw the introduction of computer-controlled machines, revolutionizing dies manufacturing. Computer Numerical Control (CNC) machines allowed for more complex and intricate die designs. This automated manufacturing process enhanced accuracy and reduced human error.
Late 20th to early 21st century:
Advancements in computer technology and digital design software further modernized dies manufacturing. Computer-Aided Design (CAD) and Computer-Aided Manufacturing (CAM) systems enabled the seamless translation of digital blueprints into physical dies. This digitalization improved efficiency, reduced lead times, and enhanced design capabilities.
Present day:
Dies manufacturing continues to evolve with the introduction of additive manufacturing techniques, such as 3D printing. This technology offers the possibility of creating custom dies rapidly and cost-effectively, eliminating the need for complex tooling processes. 3D printing also allows for the production of intricate, complex geometries that previously would have been challenging using traditional methods.
In conclusion, dies manufacturing has experienced a remarkable evolution. From handcrafted dies made by skilled artisans to sophisticated computer-controlled machines and the emergence of additive manufacturing, the industry has continually adapted to meet the demands of various industries and technological advancements.
The Evolution and Market Trends in dies manufacturing Industry
The dies manufacturing industry has witnessed significant evolution and market trends over the years. Dies are essential tools used in shaping or cutting materials into specific shapes and sizes, and are widely used in various sectors such as automotive, aerospace, and consumer goods manufacturing.
One of the major trends in the dies manufacturing industry is the shift towards advanced and computerized manufacturing processes. Traditional manufacturing methods are being replaced by cutting-edge technologies such as computer-aided design (CAD) and computer-aided manufacturing (CAM). These technologies enable faster and more precise die production, resulting in improved efficiency and productivity.
Another significant trend is the increasing demand for custom dies. As industries become more specialized and requirements become more specific, the need for tailored dies has risen. Manufacturers are now offering customized dies to meet the unique needs of their customers, whether it be for a specific product or production process.
Moreover, there has been a growing emphasis on cost-effective and sustainable manufacturing practices. Companies are striving to optimize their production processes to minimize waste, reduce energy consumption, and lower costs. This has led to the adoption of innovative techniques such as additive manufacturing (3D printing), which allows for the creation of complex die designs with minimal material waste.
Furthermore, the dies manufacturing industry has experienced a surge in automation. Automated die manufacturing systems can perform repetitive tasks with precision and speed, resulting in improved productivity and reduced labor costs. These automated systems can also be integrated with other manufacturing processes, such as robotics and artificial intelligence, further enhancing overall efficiency and output.
In terms of market outlook, the dies manufacturing industry is expected to continue its growth trajectory. The increasing demand for automobiles, electronic devices, and consumer goods globally will fuel the demand for dies. Additionally, the rising adoption of advanced manufacturing technologies and the need for customized dies will contribute to market expansion.
To stay competitive, manufacturers in this industry will need to continually invest in research and development to innovate and enhance their manufacturing processes. They must also adapt to changing customer demands and emerging trends to remain at the forefront of the market.
Custom Private Labeling and Branding Opportunities with Chinese dies manufacturing Manufacturers
Are you a business looking for custom private labeling and branding opportunities with Chinese die manufacturing manufacturers? Look no further! China offers numerous possibilities for businesses looking to establish their own private label and brand their products.
Chinese die manufacturing manufacturers have extensive experience in producing high-quality dies for various industries. By partnering with these manufacturers, you can leverage their expertise and tap into their resources to create custom dies tailored to your specific needs.
One of the key advantages of collaborating with Chinese manufacturers is the ability to avail cost-effective production options. China is renowned for its competitive pricing, which can help you save significant costs on manufacturing without compromising on quality. This makes it an attractive option for businesses aiming to establish private labels or brands on a more limited budget.
Moreover, Chinese manufacturers are highly flexible and can accommodate your branding requirements. You can work closely with them to design and create packaging, labels, and other branding elements that align with your brand identity. This level of customization allows you to differentiate your products from competitors in the market.
Additionally, Chinese manufacturers often have a wide range of manufacturing capabilities, including various materials and finishes. This enables you to choose suitable options that reflect your brand aesthetic and ensure the durability and functionality of your products.
When considering private labeling and branding opportunities, it is essential to conduct thorough due diligence and select reliable manufacturers with a proven track record. It is recommended to visit the factories in person or engage the services of a trusted sourcing agent to ensure the quality and authenticity of the manufacturers.
In conclusion, partnering with Chinese die manufacturing manufacturers can offer exciting prospects for businesses seeking custom private labeling and branding opportunities. With their expertise, cost-effectiveness, flexibility, and manufacturing capabilities, you can establish a unique and distinct brand identity in the market. Take advantage of China’s manufacturing prowess and explore the endless possibilities that await your business.
Tips for Procurement and Considerations when Purchasing dies manufacturing
When it comes to procurement and purchasing dies for manufacturing, there are several important considerations to keep in mind. Here are some key tips and factors to consider:
1. Define your requirements: Clearly identify the specifications, functionalities, and quantities needed for the dies. This will help you communicate your needs effectively to potential suppliers.
2. Research and evaluate suppliers: Conduct thorough research to identify potential suppliers who specialize in manufacturing dies. Consider their experience, reputation, quality control processes, and customer reviews.
3. Request for proposals: Send a detailed request for proposals (RFP) to shortlisted suppliers, outlining your requirements and expectations. This allows you to compare quotes, timelines, and other key factors before making a decision.
4. Quality control and certifications: Ensure that the supplier has strict quality control measures in place. Ask for certifications, such as ISO 9001, which indicate their commitment to meeting international quality standards.
5. Pricing and payment terms: Consider the pricing structure offered by suppliers. Evaluate the overall cost, including any shipping fees or taxes. Additionally, negotiate favorable payment terms to match your cash flow requirements.
6. Timeframe and delivery: Discuss the manufacturing lead time and delivery schedule with the supplier to ensure that it aligns with your production requirements. Timely delivery is crucial to avoid production delays and disruptions.
7. After-sales support: Inquire about the supplier’s after-sales support, including warranty and maintenance services. A reliable supplier should be able to offer technical assistance and spare parts if needed.
8. Intellectual property protection: If you require custom dies, discuss intellectual property protection with the supplier. Ensure that they have measures in place to protect your design and prevent unauthorized use.
9. Social and environmental responsibility: Consider the supplier’s commitment to social and environmental sustainability. Ask for their policies regarding labor practices, ethical sourcing, and waste management.
10. Supplier relationship management: Establishing a strong relationship with the chosen supplier is essential for long-term success. Open communication and regular evaluations can help address any issues and improve collaboration.
By following these tips and considering the various aspects mentioned, you can make informed decisions when procuring and purchasing dies for manufacturing.
FAQs on Sourcing and Manufacturing dies manufacturing in China
Q: Why should I consider sourcing and manufacturing dies in China?
A: There are several reasons to consider sourcing and manufacturing dies in China. First and foremost, China has a robust manufacturing industry with advanced technology and skilled labor. This means that you can expect high-quality dies at competitive prices. Additionally, China offers a wide range of manufacturing capabilities, allowing you to find specialized suppliers that can meet your unique requirements. Furthermore, the country has a favorable business environment, with vast infrastructure and a strong support system for foreign businesses. Lastly, China has a large pool of suppliers, which increases your chances of finding the right partner for your die manufacturing needs.
Q: What are the key factors to consider when sourcing dies in China?
A: When sourcing dies in China, it is essential to consider several factors. Firstly, you need to carefully evaluate the supplier’s experience and capabilities in die manufacturing. Look into their track record, certifications, and their ability to handle the specific materials and processes needed for your project. Secondly, consider the supplier’s production capacity and lead times to ensure they can meet your production requirements. Quality control is also crucial, so evaluate their quality management systems and ensure they can provide consistent and reliable dies. Lastly, logistics and communication are important aspects to consider, as you need to ensure smooth shipping and effective communication channels with the supplier.
Q: What are the challenges involved in sourcing and manufacturing dies in China?
A: While sourcing and manufacturing dies in China have many benefits, there are also some challenges to be aware of. Language and cultural barriers can sometimes create communication difficulties, so it is crucial to establish clear communication channels and ensure proper interpretation or translation assistance. Intellectual property protection is another concern in China, so it is essential to work with trustworthy suppliers and have proper legal agreements in place. Additionally, distance and time zone differences can pose logistical challenges, so it is important to plan for possible delays in communication and shipping.
Overall, with proper research, due diligence, and careful consideration of these factors, sourcing and manufacturing dies in China can be a cost-effective and efficient option for businesses in need of high-quality dies.
Why contact sourcifychina.com get free quota from reliable dies manufacturing suppliers?
Sourcifychina.com obtains free quotas from reliable dies manufacturing suppliers for several reasons. Firstly, offering free quotas is a way for these suppliers to attract potential customers and showcase their capabilities. By providing a limited number of free quotas, they can encourage businesses to explore their services without incurring any initial costs.
Secondly, offering free quotas helps the suppliers gather valuable market intelligence and gauge the interest and potential demand for their dies manufacturing services. By providing free quotes, the suppliers can assess the feasibility of taking on new projects and identify potential customers who may be willing to establish long-term relationships.
Furthermore, by offering free quotas, the suppliers can establish trust and credibility with potential customers. It allows businesses to evaluate the quality, pricing, and turnaround time of the supplier’s services before committing to a paid engagement. This transparent approach builds confidence in the supplier’s capabilities and reduces the risk for businesses interested in sourcing dies manufacturing services from China.
Lastly, providing free quotas allows the suppliers to showcase their expertise and stand out among competitors. Businesses constantly seek suppliers who offer the best quality at competitive prices. By providing free quotas, the suppliers can highlight their skills, experience, and commitment to customer satisfaction, setting themselves apart from other potential suppliers in the market.
In conclusion, offering free quotas enables reliable dies manufacturing suppliers to attract potential customers, gather market intelligence, build trust and credibility, as well as showcase their expertise. This approach benefits both the suppliers and businesses seeking dies manufacturing services, ultimately leading to mutually beneficial partnerships.