Types and Applications of drum core inductors
Drum core inductors are a type of electromagnetic component used to store electrical energy in a magnetic field. These inductors consist of a coil of wire wound around a magnetic core in the shape of a cylindrical drum. The magnetic core provides a high magnetic permeability that enhances its inductance while reducing core losses.
There are two main types of drum core inductors: toroidal and bobbin. Toroidal inductors have a circular core that forms a torus around the coil, while bobbin inductors have a cylindrical core with a hole in the center for the wire to pass through. Both types can be customized to meet the specific requirements of a particular application.
Drum core inductors have a wide range of applications, including power supplies, DC-DC converters, audio equipment, and telecommunications systems. In power supplies and converters, they are used to filter and smooth out the output voltage or current. In audio equipment, they are used to filter out unwanted noise or signals. In telecommunications systems, they are used to filter and remove unwanted signals from the data being transmitted.
Drum core inductors are also used in power factor correction circuits, where they help to improve power efficiency and reduce harmonic distortion. They can also be used in high-frequency electronic circuits, where they enable high performance and stability.
Overall, drum core inductors are essential components in many electronic devices and systems. Their high inductance and magnetic permeability make them efficient and effective at storing and delivering electrical energy, while their customizable designs allow them to adapt to the specific needs of different applications.
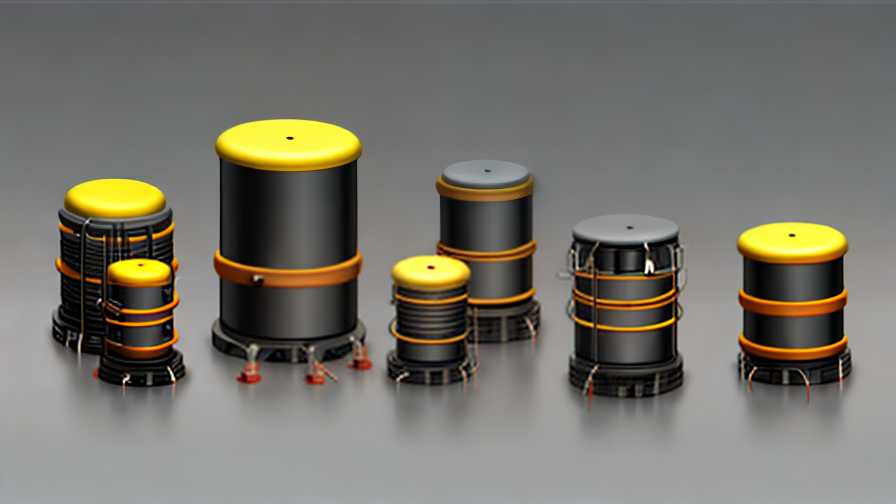
Benefits and Feature of Utilizing drum core inductors
Drum core inductors have become increasingly popular in power electronics due to their numerous benefits and features. The core is made of a cylindrical shape with a winding wrapped around it, providing a large surface area for the wire to be wound in multiple layers. Here are the benefits of utilizing drum core inductors:
Higher Saturation Currents: Drum core inductors have higher saturation currents in comparison to other types of inductors, which make them perfect for high power applications.
Low Magnetic Leakage: Drum core inductors possess low magnetic leakage, reducing the electromagnetic field and minimizing the chances of interference with other nearby electrical equipment.
Low AC Resistance: Drum core inductors have a low AC resistance and are highly-efficient, which is highly desirable for all electrical applications.
Customizable: Drum core inductors are customizable for specific application requirements, design constructions, and size limitations.
Broad Frequency Range: The wide frequency range of the drum core inductors make them a versatile choice for high power applications in power supplies, solar inverters, and electric vehicles.
Improved Thermal Management: Drum core inductors present a low profile design, which allows an optimal surface to volume ratio produces high-performance components, with reduced heat generation and effective thermal dissipation.
Compact Design: Their compact design and high construction flexibility make drum core inductors a valuable component in various applications.
Overall, the benefits of utilizing drum core inductors include their high efficiency and energy-saving features, low profile design, and customizable options. These attributes make them an excellent fit for high power applications in automotive, industrial, and renewable systems.
The Process of drum core inductors
Drum core inductors are passive electronic components used in a variety of applications, including power supplies, electric motors, and audio equipment. They are designed to store energy in the form of a magnetic field when a current flows through them. The magnetic field generates a voltage that opposes changes in the current, resulting in a smooth and stable output.
The process of manufacturing a drum core inductor typically involves several stages, starting with the selection of high-quality materials. The core itself is made of a soft magnetic material, such as iron powder or ferrite, which enables high flux density and low core loss. The wire used to wind the coils is typically made of copper or aluminum, with high conductivity and low resistivity.
The first stage in manufacturing a drum core inductor is to form the core. The core material is typically compressed into a cylindrical or toroidal shape using a special press. The core is then sintered at high temperatures to increase its strength and density. After sintering, the core is machined to ensure its shape and dimensions are accurate.
Next, the wire is wound onto the drum core to form the coils. The number of coils and the thickness of the wire will depend on the specific application and the desired inductance value. The wire is typically wound using automated machinery to ensure consistent and precise winding.
Once the wire is wound, the inductor undergoes several finishing processes, including insulation and encapsulation. The wire is typically coated with a layer of enamel or other insulating material to prevent shorts between the coils. The entire inductor is then encapsulated in a protective material, such as epoxy or plastic. The encapsulation provides additional insulation and helps to protect the inductor from mechanical stress and environmental factors such as temperature and humidity.
Finally, the inductor undergoes testing to ensure its performance meets the design specifications. This typically involves measuring the inductance value, resistance, and other electrical characteristics. The inductor is then packaged and shipped to the customer for use in their electronic system or device.
In summary, the process of manufacturing a drum core inductor involves selecting the appropriate materials, forming the core, winding the coils, insulating and encapsulating the inductor, and testing its performance. The result is a high-quality passive component that enables efficient and reliable operation of electronic systems and devices.

How to use drum core inductors
Drum core inductors are used in electronic circuits to store and release energy in the form of magnetic fields. They are commonly used in power supplies, filters, and RF circuits. The drum core inductor is a type of inductor that has a cylindrical shaped core, with windings of wire around it.
To use a drum core inductor, one needs to connect it to the circuit by soldering the ends of the wire to the appropriate circuit nodes. When current flows through the inductor, a magnetic field is created inside the core. This magnetic field stores energy and opposes changes in the current flowing through the inductor.
Drum core inductors are characterized by their inductance value, which is measured in henries (H). The inductance value of a drum core inductor is determined by the number of turns of wire around the core, the diameter of the core, and the material used to make the core.
To select the appropriate drum core inductor for a circuit, one needs to consider the required inductance value, the operating frequency, and the maximum current that will flow through the inductor. The inductor’s resistance and the frequency of the circuit will also impact the inductor’s performance.
In summary, drum core inductors are an essential component in electronic circuits used to store and release energy in the form of magnetic fields. They can be selected based on the required inductance value, the operating frequency, and the maximum current that will flow through the circuit. Properly utilized, they help ensure the stability and proper operation of electronic circuits.
drum core inductors Manufacturer,Supplier and Wholesale
Drum core inductors are highly efficient and reliable inductors used in various applications such as power supplies, audio equipment, and telecommunications. These inductors are made up of a cylindrical core with windings around it, which allow for high magnetic performance and low resistance.
As a leading drum core inductors manufacturer, supplier, and wholesale company, we specialize in producing high-quality inductors to meet the needs of a broad range of industries. Our inductors are available in different sizes and configurations, making it easy for customers to find the right solution for their project.
Our drum core inductors are designed to handle high currents, maintain stable inductance values, and minimize resistive losses. We use the latest technologies and manufacturing techniques to ensure that our inductors are reliable and durable. Our inductors are capable of withstanding extreme temperatures and harsh operating conditions, making them suitable for use in a wide range of environments.
We understand the importance of delivering products that meet the needs of our customers. That is why we offer customized drum core inductors, tailored to meet your specific requirements. Our team of experienced engineers can design inductors to match your unique specifications, ensuring that you get the solution you need for your project.
We are committed to providing our customers with the highest level of service and support. Whether you need technical assistance or have a general inquiry, our team is always ready to help. We offer fast and efficient shipping, ensuring that your order is delivered on time.
In conclusion, our drum core inductors are among the most reliable and efficient in the market, making them a preferred choice for various applications. We take pride in providing high-quality inductors that meet the needs of our customers while delivering exceptional customer service. Contact us today to learn more about our drum core inductors and how we can help you with your project.

drum core inductors Price
Drum core inductors are electronic components used to store electrical energy in a magnetic field. They are known for their high performance, stability, and durability, making them a popular choice in various industries, including telecommunications, power electronics, and automotive.
The price of drum core inductors varies depending on various factors. One significant factor is the type of material used for the core. Inductors made with high-performance materials such as ferrite and amorphous metals tend to be more expensive than those made with lower-cost materials such as iron powder. Additionally, the inductor’s size, value, and application complexity may affect its price.
Inductors are measured in values such as inductance, series resistance, and saturation current. The cost of an inductor increases with higher values of inductance, lower series resistance, and higher saturation current. Moreover, inductors used for digital circuits and high-frequency applications are typically more expensive due to their greater complexity and need for tighter tolerances.
The cost of a drum core inductor can range from a few cents to hundreds of dollars. For instance, a standard 1mH inductor with a 1A rating can cost around $0.30, while a high-performance inductor with a 20mH inductance rating and 10A current rating can cost around $170.
Moreover, the price of drum core inductors is also affected by the market conditions and global factors. For instance, the COVID-19 pandemic has caused disruptions in the supply chain, leading to shortages of raw materials and increased prices of electronic components, including inductors.
In conclusion, drum core inductors have a varying price range, mainly dependent on core material, size, value, application complexity, and market conditions. When choosing the right inductor for your project, it is essential to consider its price-value ratio, as well as performance, reliability, and compatibility with other components.
FAQ sourcing drum core inductors manufacturer from China with multiple answers
1. What types of drum core inductors are commonly manufactured in China?
China is home to various drum core inductors manufacturers that produce various types of drum core inductors to meet different customer demands. These include radial leaded, SMD drum core inductors, and axial leaded drum core inductors. Each type has different specifications tailored to specific applications.
2. What are the most common applications of drum core inductors?
Drum core inductors are used in a wide range of applications that require the storage and transfer of energy in electronic circuitry. They are commonly used in high-frequency applications such as switch-mode power supply (SMPS) circuits, DC-DC converters, radio frequency transmitters, and receivers.
3. How do I find a reliable drum core inductors manufacturer in China?
There are many reliable drum core inductors manufacturers in China. To find one, you can start by conducting a thorough online search and shortlist at least three potential suppliers. Request for their product catalog and certifications to check whether they meet the required industry standards. You can also check their customer reviews and ratings to assess their reputation and reliability.
4. What factors should I consider when selecting a drum core inductors manufacturer in China?
When selecting a drum core inductors manufacturer in China, there are several factors to consider. These include the manufacturer’s experience and reputation, the quality of their products, certifications and standards they follow, production capacity, lead time, and customer service and support.
5. How do I ensure the quality of drum core inductors from a Chinese manufacturer?
Quality assurance is a critical aspect when importing products from China. To ensure the quality of drum core inductors from a Chinese manufacturer, it’s crucial to check if they comply with relevant industry standards, such as ROHS, UL, and ISO. It’s also recommended to conduct a factory inspection and product test before placing an order. Additionally, consider working with a trusted third-party inspection company for quality control and assurance.