Introduce about factory sheet metal guide,Qulity,Cost,Supplier,Certification,Market,Tips,FAQ
Factory sheet metal guide is a comprehensive resource that provides essential information about the manufacturing of sheet metal products. It serves as a go-to reference for manufacturers, designers, engineers, and anyone involved in the sheet metal industry. This guide covers various aspects including quality, cost, suppliers, certification, market, tips, and frequently asked questions (FAQs) to help users make informed decisions.
Quality is a crucial aspect of sheet metal fabrication, and this guide emphasizes the importance of ensuring high-quality standards throughout the manufacturing process. It includes information about material selection, fabrication techniques, and quality control measures to meet customer requirements and industry standards.
Cost is another significant consideration, and the guide provides insights into factors that influence sheet metal fabrication costs such as material costs, labor costs, tooling expenses, and design complexity. It provides cost-saving tips and strategies to optimize manufacturing processes and minimize expenses.
Finding reliable suppliers is essential for successful sheet metal fabrication. The guide offers guidance on selecting reputable suppliers, assessing their capabilities, and establishing strong partnerships to ensure consistent quality, timely delivery, and competitive pricing.
Certification is a testament to a manufacturer’s adherence to industry standards and quality control procedures. This guide highlights various certifications that sheet metal manufacturers can obtain, such as ISO and AS9100, and explains their significance in building trust and credibility with customers.
Market analysis and trends are covered in the guide to help businesses understand the current sheet metal industry landscape. It provides insights into market dynamics, emerging technologies, and customer preferences, enabling manufacturers to stay competitive and identify potential growth opportunities.
The guide also includes useful tips and best practices for sheet metal fabrication, covering areas such as design considerations, material selection, finishing techniques, and assembly methods. These tips aim to improve manufacturing efficiency, product quality, and overall customer satisfaction.
A comprehensive FAQ section addresses common queries and provides answers to frequently encountered challenges in the sheet metal fabrication process.
In summary, the factory sheet metal guide is an invaluable resource that offers a holistic view of sheet metal manufacturing. By providing information on quality, cost, suppliers, certification, market trends, tips, and FAQs, it equips users with the knowledge needed to make informed decisions and excel in the sheet metal industry.
Types of factory sheet metal
There are various types of factory sheet metal used in different industries for various applications. Some common types of sheet metal used in factories include:
1. Steel: Steel sheet metal is commonly used in factories due to its durability, strength, and versatility. It is used in the construction of structural components, automotive parts, machinery, appliances, and more.
2. Aluminum: Aluminum sheet metal is known for its lightweight nature, corrosion resistance, and excellent thermal and electrical conductivity. It is often used in the aerospace industry, automotive manufacturing, and electrical equipment production.
3. Stainless Steel: Stainless steel sheet metal is highly resistant to corrosion and staining, making it suitable for industries such as food processing, medical equipment manufacturing, chemical processing, and architectural applications.
4. Copper: Copper sheet metal is valued for its high electrical and thermal conductivity. It is commonly used in electrical wiring, electronic components, roofing materials, and plumbing systems.
5. Brass: Brass sheet metal is an alloy of copper and zinc, known for its corrosion resistance, low-friction properties, and decorative appeal. It is used in the production of musical instruments, decorative hardware, plumbing fittings, and electrical connectors.
6. Galvanized Steel: Galvanized steel sheet metal is coated with a layer of zinc to protect it from corrosion. It is commonly used in outdoor applications such as roofing, fencing, gutters, and agricultural equipment.
7. Titanium: Titanium sheet metal is lightweight, strong, and highly corrosion-resistant. It finds applications in the aerospace industry, medical implants, chemical processing equipment, and sporting goods.
8. Nickel: Nickel sheet metal is used in industries such as aerospace, chemical processing, and electronics manufacturing due to its resistance to corrosion, high-temperature stability, and magnetic properties.
These are just a few examples of the many types of sheet metal used in factory settings. Each type has its unique properties and applications, making them suitable for a wide range of industries and manufacturing processes.
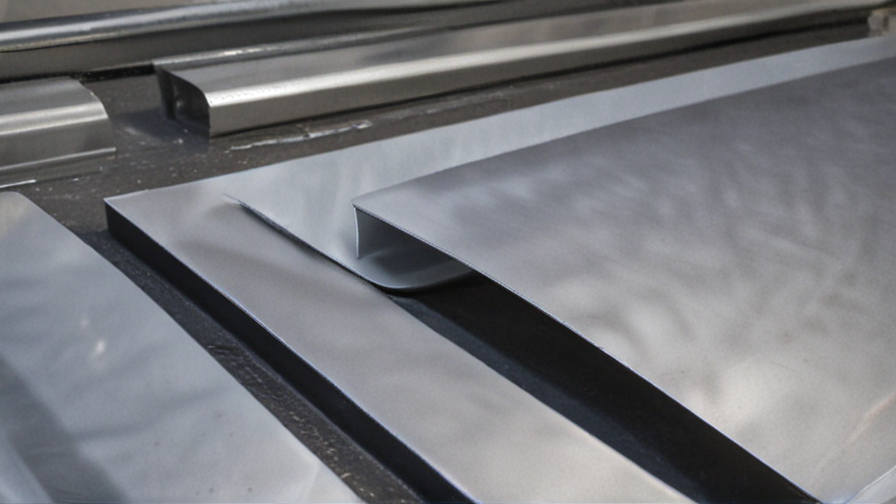
Pros and Cons of Using factory sheet metal
Using factory sheet metal has its own set of pros and cons. Here are some key points to consider:
Pros:
1. Quality control: Factory sheet metal is produced using advanced manufacturing techniques and equipment, ensuring a high level of quality control. This can result in consistent and standardized products that meet specific requirements.
2. Cost-effective: Since factory sheet metal is mass-produced, it is often more cost-effective compared to custom-made sheet metal. The economies of scale result in lower production costs, making factory sheet metal an attractive option for large-scale projects.
3. Availability: Factory sheet metal is readily available in various sizes and thicknesses. This allows for easy sourcing and quick availability, reducing lead times for projects.
4. Efficiency: Factory sheet metal is generally designed for efficient production, resulting in shorter manufacturing times. This can be advantageous when time is a critical factor.
5. Compliance with regulations: Factory sheet metal is manufactured in compliance with industry standards and guidelines, ensuring that it meets the required safety and performance regulations.
Cons:
1. Limited customization: Factory sheet metal is produced in large quantities with standardized designs. This may limit the level of customization options available for specific projects.
2. Size limitations: Factory sheet metal typically comes in standard sizes and thicknesses, which may not be suitable for all applications. Custom sizing may be required, which can add to the cost and lead time.
3. Design limitations: Factory sheet metal may have design limitations due to the manufacturing process. Complex or intricate designs may not be feasible, and this can impact the aesthetic appeal or functionality of the final product.
4. Reduced control: When using factory sheet metal, there is limited control over the production process. This means that any defects or quality issues may not be identified until after the product has been delivered.
5. Sustainability concerns: Factory sheet metal production can have a significant environmental impact due to the use of energy, raw materials, and waste generation. Sustainable alternatives may need to be considered for environmentally conscious projects.
In conclusion, using factory sheet metal offers advantages such as quality control, cost-effectiveness, and availability. However, it also has limitations in customization, design, and control over the production process. These pros and cons should be carefully assessed in relation to the specific requirements of a project to make an informed decision.
factory sheet metal Reference Specifications (varies for different product)
The factory sheet metal reference specifications vary based on the specific product being manufactured. These specifications outline the requirements for the sheet metal used in the manufacturing process and ensure consistent quality and performance.
In terms of material, the reference specifications indicate the type of sheet metal to be used, such as aluminum, stainless steel, or galvanized steel. The specifications provide details on the acceptable thickness range, which can vary depending on the product and its intended use. Additionally, the reference specifications may specify any specific metallurgical requirements, such as desired tensile strength or hardness levels.
The reference specifications also provide guidance on the manufacturing processes that should be followed. This includes information on cutting, bending, and forming techniques, as well as welding or joining methods. The specifications may outline any necessary tolerances for dimensions, surface finishes, or tightness of bends.
Surface treatment requirements are also included in the reference specifications. This may involve specifying coatings or finishes to protect the sheet metal from corrosion or to enhance its appearance. Additionally, the specifications may indicate any testing or inspection procedures that should be conducted to ensure the quality of the finished product.
While the specific content of the reference specifications will vary depending on the product, they serve as a crucial guide for the factory’s sheet metal manufacturing process. Adhering to these specifications helps ensure that the sheet metal meets the necessary performance and quality standards.
In conclusion, the factory sheet metal reference specifications vary for different products and provide essential details regarding the material, manufacturing processes, surface treatment, and quality requirements for the sheet metal used in the manufacturing process. By following these specifications, the factory can produce sheet metal components that meet the desired performance and quality criteria.
Applications of factory sheet metal
Factory sheet metal, also known as sheet metal fabrication, refers to the process of shaping metal sheets into different components or structures using specialized tools and techniques. This versatile material finds various applications across numerous industries, including:
1. Automotive Industry: Factory sheet metal is extensively used in the automotive sector for manufacturing car bodies, hoods, fenders, and structural components. Its high strength-to-weight ratio makes it ideal for ensuring vehicle safety while reducing weight.
2. Aerospace Industry: Due to its lightweight nature, factory sheet metal is widely used in the aerospace industry for building aircraft fuselages, wings, and structural components. It helps maintain the overall strength of the aircraft while optimizing fuel efficiency.
3. Construction: Factory sheet metal plays a crucial role in the construction industry, particularly for commercial buildings. It is used to create HVAC (heating, ventilation, and air conditioning) systems, roofing materials, wall panels, and building frameworks.
4. Electronics: The electronics industry utilizes factory sheet metal for manufacturing enclosures, chassis, and cabinets to house various electronic components and devices, such as computers, smartphones, and servers. Sheet metal fabrication provides excellent electrical shielding and protection.
5. Medical Equipment: Factory sheet metal is commonly used in the production of medical equipment and devices. It is employed for fabricating surgical instruments, beds, diagnostic tools, and cabinets. The hygienic and easy-to-clean properties of sheet metal are essential for maintaining a sterile environment in healthcare settings.
6. Industrial Machinery: Sheet metal fabrication is extensively used in the production of industrial machinery like conveyor systems, assembly line equipment, and machine guards. The durability and precision achieved through this process ensure optimum performance and worker safety.
7. Energy Sector: Factory sheet metal finds application in the renewable energy sector for the manufacturing of wind turbine components, solar panel frames, and power distribution systems. Its strength and corrosion resistance make it ideal for withstanding harsh environmental conditions.
8. Food and Beverage Industry: Sheet metal is used in the food and beverage industry to manufacture processing equipment, storage tanks, and machinery components. Its clean, non-reactive surface and ease of maintenance comply with strict hygiene standards.
9. Furniture and Interior Design: Factory sheet metal is employed in the production of furniture and decorative elements, such as chairs, tables, shelves, and decorative panels. Its versatility allows for creative and unique designs.
In summary, factory sheet metal has a wide range of applications across industries including automotive, aerospace, construction, electronics, medical, machinery, energy, food and beverage, and furniture. Its strength, durability, lightweight nature, and ability to be shaped into complex structures make it a preferred material for various manufacturing processes.
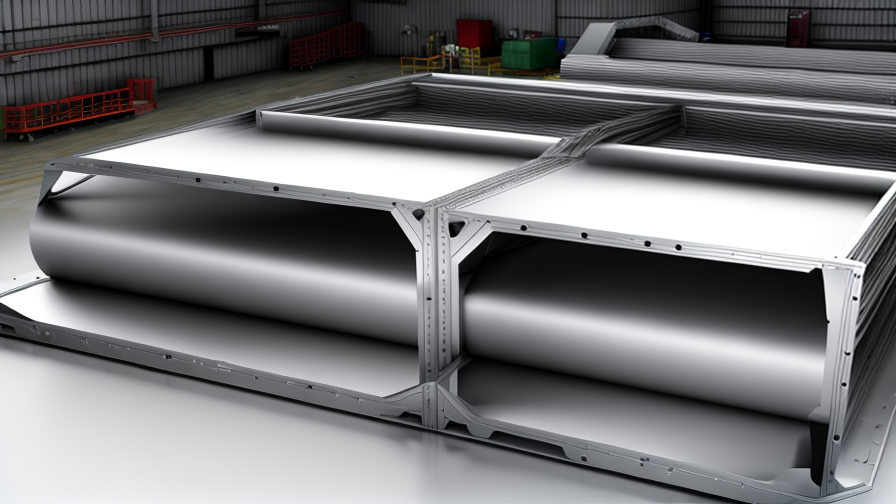
The Work Process and how to use factory sheet metal
The work process of utilizing factory sheet metal involves several steps that ensure efficient and high-quality production. Firstly, the design of the sheet metal component is finalized using computer-aided design (CAD) software. The specifications such as dimensions, tolerances, and material requirements are determined.
Once the design is ready, the next step involves the preparation of the factory sheet metal. This includes procuring the required raw materials, which are typically metal sheets made of aluminum, steel, or stainless steel. These sheets are then inspected for any defects or imperfections before being cut to the desired size using tools like shears or laser cutters.
After cutting, the sheet metal undergoes various forming processes. These processes can include bending, folding, or deep drawing to create the desired shape as per the design specifications. Specialized machinery like hydraulic presses or stamping machines are used in this step to achieve precise and accurate results.
Once the forming is complete, additional operations like welding, riveting, or fastening may be carried out to assemble multiple sheet metal components or attach other parts to the sheet metal. These processes ensure structural integrity and functionality of the final product.
After all the required operations are executed, the finished sheet metal components are inspected for quality and dimensional accuracy. Any necessary adjustments or corrections are made if deviations are found. Once approved, the components are surface treated, such as through painting, powder coating, or plating, to enhance their appearance and protect against corrosion.
Finally, the completed sheet metal components are carefully packaged and prepared for shipment to the customer or the next stage of the production process.
To effectively utilize factory sheet metal, it is essential to have a comprehensive understanding of the design requirements and manufacturing capabilities. Collaborating with engineers or sheet metal fabrication experts can help optimize designs and select suitable materials and manufacturing techniques.
Moreover, utilizing advanced software tools for modeling and simulating sheet metal forming processes can help streamline production and reduce any potential errors or inefficiencies.
Regular maintenance of machinery and equipment, along with ensuring the availability of skilled labor, is also crucial for efficient and safe sheet metal fabrication operations.
In conclusion, the work process of utilizing factory sheet metal involves design finalization, material preparation, cutting, forming, assembly, inspection, surface treatment, and packaging. By following this process and employing appropriate techniques, sheet metal can be used effectively to produce high-quality components for various industries.
Quality Testing Methods for factory sheet metal and how to control the quality
When it comes to factory sheet metal, ensuring high-quality production is essential for meeting customer expectations and maintaining an impeccable reputation. Quality testing methods play a crucial role in achieving this, allowing manufacturers to identify any defects or deviations from desired specifications. Here are some commonly used quality testing methods for factory sheet metal along with tips on how to control the quality.
1. Visual Inspection: Visual inspection involves a thorough examination of the finished sheet metal product to identify any visible defects, such as scratches, dents, or uneven surfaces. This method requires trained inspectors who can spot even minor imperfections.
2. Dimensional Inspection: This testing method involves measuring critical dimensions of the sheet metal using tools like calipers and micrometers. By comparing the measurements against the specified tolerances, manufacturers can ensure that the product is within acceptable limits.
3. Surface Finish Testing: Surface finish testing assesses the quality of the sheet metal’s outer surface. Methods like profilometers or visual assessment can be employed to check for smoothness, roughness, or any kind of irregularity that may affect the part’s functionality or aesthetics.
4. Mechanical Testing: Mechanical properties, such as tensile strength, hardness, or ductility, are vital for sheet metal performance. Testing techniques like tensile testing, hardness testing, or impact testing can determine if the material meets the specified mechanical requirements.
5. Coating and Plating Inspection: If the sheet metal requires coatings or plating for protection or aesthetic reasons, inspection methods like adhesion testing or thickness measurement can gauge the quality and uniformity of the applied layer.
To effectively control quality in factory sheet metal production, manufacturers should adhere to the following practices:
1. Establish Clear Quality Standards: Define precise quality standards, specifications, and tolerances for the sheet metal products, ensuring that all stakeholders understand and follow them.
2. Proper Training: Train employees involved in quality control to understand the different testing methods and criteria to spot, assess, and categorize defects accurately.
3. Regular Calibration: Calibrate all testing instruments regularly to maintain accurate measurements and minimize errors.
4. Implement Quality Control Plans: Develop comprehensive quality control plans that specify the test points, inspection frequency, and acceptance criteria at different stages of production.
5. Feedback Loop: Establish a feedback loop between production, quality control, and design teams. Any quality issues discovered should lead to corrective actions in the production process or redesign if necessary.
By implementing these testing methods and quality control measures, manufacturers can ensure that the sheet metal products leaving their factories meet the required standards, resulting in satisfied customers and enhanced business reputation.
factory sheet metal Sample Policy and Post-Purchase Considerations for factory sheet metal from China
Sample Policy:
1. Before finalizing any orders for factory sheet metal from China, it is advisable to request samples from prospective suppliers. This will help in assessing the quality of the products and ensuring they meet the required specifications.
2. The buyer should clearly communicate the sample requirements to the supplier, including the material, dimensions, finishes, and any other specific details. It is important to have a written agreement outlining these requirements.
3. The buyer should also request samples of different products or variations that they intend to purchase. This will help in evaluating consistency in quality across the supplier’s range of factory sheet metal products.
4. Once the samples are received, the buyer should carefully inspect them for defects, such as scratches, dents, or irregularities in finish. It is recommended to involve a qualified professional to assess the samples if needed.
5. The buyer should also compare the samples with the agreed specifications. Any discrepancies should be immediately communicated to the supplier for rectification.
6. If the samples meet the buyer’s requirements, the buyer can proceed with placing an order. If not, the buyer can negotiate with the supplier for improvements or search for alternative suppliers.
Post-Purchase Considerations:
1. After the purchase of factory sheet metal from China, it is advisable to conduct thorough quality inspections upon receipt of the products. This can be done by either the buyer’s quality control team or by hiring an independent third-party inspection service.
2. Any quality issues or defects should be documented with supporting evidence, such as photographs or videos. This will be useful for negotiations with the supplier for compensation or replacements.
3. It is important to maintain open lines of communication with the supplier throughout the post-purchase phase. Any concerns or issues should be promptly discussed to find suitable solutions.
4. In case of major quality issues, the buyer may need to consider initiating a dispute resolution process, such as mediation or arbitration, as per the agreed terms and conditions with the supplier.
5. Regular evaluation of the supplier’s performance is crucial to ensure ongoing quality and consistency of factory sheet metal. This can involve feedback sessions, periodic quality inspections, or even considering alternative suppliers if necessary.
Ultimately, a thorough sample policy and post-purchase considerations help in mitigating risks and ensuring a satisfactory purchasing experience for factory sheet metal from China.
Sourcing factory sheet metal from China: Opportunities, Risks, and Key Players
China has emerged as a leading global manufacturing hub, offering a wide range of opportunities for sourcing factory sheet metal. The low labor costs and vast production capacity make China an attractive option for businesses seeking cost-effective solutions. However, there are certain risks associated with sourcing from China, and it is crucial to identify key players in the market to mitigate potential challenges.
Opportunities:
Sourcing factory sheet metal from China provides numerous opportunities for businesses. The country boasts an extensive supply chain network and a large pool of skilled workers with expertise in metal fabrication. The availability of raw materials at competitive prices enables cost-effective production. Additionally, China’s manufacturing infrastructure is well-developed, offering advanced technology and machinery, which ensures high-quality output. Furthermore, Chinese manufacturers focus on mass production, allowing for large-scale orders to be fulfilled efficiently and quickly.
Risks:
While China offers substantial opportunities, there are also risks associated with sourcing factory sheet metal from the country. Quality control can be a concern, as some manufacturers may cut corners to reduce costs, leading to substandard products. Intellectual property protection is another significant risk, as counterfeiting and infringement issues have plagued the Chinese market. Distance and language barriers may also lead to communication challenges, potentially impacting project timelines and specifications.
Key Players:
Identifying reliable and reputable key players is essential in mitigating the risks associated with sourcing from China. Some prominent Chinese manufacturers in the sheet metal industry include Foxconn, Huawei Technologies, BYD, and Zhejiang Jiahua Industrial Belt. These companies have a proven track record in delivering high-quality products and are known for their professionalism and adherence to international standards. However, it is essential to conduct thorough research, verify certifications, and request samples before finalizing any partnerships.
In conclusion, sourcing factory sheet metal from China presents lucrative opportunities due to its cost-effectiveness, extensive supply chain, and advanced manufacturing infrastructure. However, businesses must navigate the risks associated with quality control, intellectual property protection, and communication challenges. By identifying reliable key players, companies can mitigate potential challenges and establish successful partnerships in China’s competitive sheet metal market.
How to find and select reliable factory sheet metal manufacturers in China,use google search manufacturers and suppliers
Finding and selecting reliable factory sheet metal manufacturers in China can be a challenging task, but with the right approach, it is possible to find trustworthy and high-quality suppliers. One effective way to start is by using Google search to identify potential manufacturers and suppliers. Here are a few steps to follow:
1. Start by searching for relevant keywords: Use specific keywords related to “sheet metal manufacturers” and “China” to initiate the search. For example, search terms like “sheet metal factory China” or “sheet metal suppliers in China.”
2. Narrow down your search: Go through the search results and browse different websites of manufacturers and suppliers. Check their product range, company profile, certifications, and customer reviews (if available).
3. Verify legitimacy and credibility: Look for visible contact information, such as a physical address, phone number, and email. Also, check if the company has a professional and well-designed website with detailed information about their manufacturing capabilities and experience.
4. Assess experience and specialization: It is important to focus on manufacturers who have experience in producing sheet metal products similar to your requirements. Look for details about their production processes, machinery, and the types of industries they cater to.
5. Check certifications and quality standards: Reliable manufacturers should have appropriate certifications and comply with international quality standards. Look for certifications such as ISO 9001, ISO 14001, or specific industry-related certifications.
6. Reach out for quotations and communicate: Shortlist a few potential manufacturers and contact them to request detailed quotations. A professional manufacturer will respond promptly and provide all the necessary information about pricing, lead times, and customization options.
7. Request samples or visit their facility: If possible, ask for samples of their sheet metal products or, if feasible, plan a visit to their factory to evaluate their production capabilities firsthand.
8. Verify customer references: Ask for references or testimonials from their current or previous clients to gain insights into their reliability and quality of service.
9. Consider other factors: Factors like pricing, communication proficiency, flexibility in manufacturing, and proximity to transportation hubs should also be taken into account before making a final decision.
In conclusion, the process of finding reliable factory sheet metal manufacturers in China starts with using Google search to locate potential suppliers, followed by thorough evaluation of their credibility, experience, certifications, and customer reviews. Communication and verification steps should be undertaken to ensure a successful and reliable partnership.
How to check factory sheet metal manufacturers website reliable,use google chrome SEOquake check if ranking in top 10M
To check the reliability of a factory sheet metal manufacturer’s website, you can follow these steps using Google Chrome and an SEO tool like SEOquake:
1. Open Google Chrome: Launch the Google Chrome web browser on your computer.
2. Install SEOquake extension: Go to the Chrome Web Store and search for the “SEOquake” extension. Click on the “Add to Chrome” button to install it.
3. Visit the manufacturer’s website: Enter the URL of the factory sheet metal manufacturer’s website in the Chrome address bar and press “Enter” to visit the site.
4. Launch SEOquake: Once the website loads, click on the SEOquake icon in your browser’s toolbar to activate the extension. A panel with various SEO metrics will appear on the right side of the screen.
5. Check website rank: In the SEOquake panel, locate the “Google Index” section. Look for the number next to “Google Rank.” If it is within the top 10 million, it indicates that the website holds a reasonably good rank.
6. Analyze other SEO metrics: SEOquake provides various metrics like Alexa Rank, number of backlinks, social media shares, etc. You can assess these to get an idea of the website’s credibility and popularity.
7. Evaluate website design and content: Browse through the manufacturer’s website to analyze its overall design and content. Look for professional presentation, detailed information about products and services, certifications, client testimonials, and contact details. A reliable manufacturer often invests in a well-designed website with comprehensive information.
8. Verify contact information: Ensure that the website provides accurate contact information such as phone numbers, email addresses, and physical addresses. Authentic contact details increase reliability.
9. Seek reviews or references: Look for online reviews or customer references about the manufacturer’s products or services. This can give you insights into their reputation and reliability.
By following these steps and analyzing the website’s SEO metrics, design, content, contact information, and customer feedback, you can make an informed assessment of a factory sheet metal manufacturer’s website reliability. Remember to consider multiple sources before making a final decision.
Top 10 factory sheet metal manufacturers in China with each 160 words introduce products,then use markdown create table compare
Here are the top 10 factory sheet metal manufacturers in China, along with a brief introduction of their products in 160 words each:
1. Foxron Precision Metal Parts Co., Ltd: Known for its precision sheet metal fabrication, Foxron offers a wide range of products such as enclosures, brackets, panels, and frames. Their focus on advanced machinery ensures high-quality and accurate manufacturing.
2. Suzhou Xinglian Precision Sheet Metal Co., Ltd: Specializing in customized sheet metal fabrication, Xinglian provides various products, including cabinets, enclosures, and brackets, with precise dimensions and excellent surface treatment.
3. Qianjin Sheet Metal Co., Ltd: Qianjin is experienced in producing sheet metal cabinets, boxes, and enclosures, which are widely used in industries like telecommunications, electronics, and automotive. Their strong R&D capability enables them to meet specific customer requirements.
4. Shenzhen Runze Hardware Technology Co., Ltd: With expertise in stainless steel and aluminum fabrication, Runze offers a diverse range of sheet metal products, including housings, frames, and brackets. Their strict quality control ensures good finishing and precision.
5. Yuda Sheet Metal Co., Ltd: Yuda specializes in sheet metal processing, mainly providing cabinets, enclosures, and brackets for industries like electronics, telecommunications, and medical equipment. Their skilled workforce ensures high-quality output.
6. Ningbo Beilun Montary Sheet Metal Technology Co., Ltd: Montary focuses on precision sheet metal products, including cabinets, racks, and enclosures, designed for electrical equipment, communication devices, and machinery. Their production is supported by advanced machinery and professional engineers.
7. Hangzhou Hengli Metal Processing Co., Ltd: Hengli offers sheet metal products such as chassis, enclosures, and cabinets for various industries. They emphasize efficient production processes and strict quality standards to provide customers with superior products.
8. Guangdong Dongji Intelligent Device Co., Ltd: Dongji specializes in sheet metal processing and manufacturing, covering a wide range of products like cabinets, brackets, and enclosures. Their advanced equipment and skilled technicians ensure high precision and quality.
9. Nanjing Prima CNC Machinery Co., Ltd: Prima focuses on producing sheet metal products such as cabinets, enclosures, and panels. With advanced machinery and strict quality control, they offer precision fabrication solutions for different industries.
10. Jiangmen CNCT Hardware Electric Appliances Co., Ltd: CNCT specializes in sheet metal fabrication, providing products like cabinets, enclosures, and brackets. Their customized manufacturing capabilities and advanced production equipment ensure high accuracy and quality.
## Markdown Table Comparison
| Manufacturer | Products | Specialization | Industries Served |
|:————–:|:——————:|:—————————-:|:———————:|
| Foxron | Enclosures, brackets, panels, frames | Precision sheet metal fabrication | Various |
| Suzhou Xinglian | Cabinets, enclosures, brackets | Customized sheet metal fabrication | Various |
| Qianjin | Cabinets, boxes, enclosures | Sheet metal fabrication for specific requirements | Telecommunications, electronics, automotive |
| Shenzhen Runze | Housings, frames, brackets | Stainless steel and aluminum fabrication | Various |
| Yuda | Cabinets, enclosures, brackets | Sheet metal processing | Electronics, telecommunications, medical equipment |
| Ningbo Beilun Montary | Cabinets, racks, enclosures | Precision sheet metal products | Electrical equipment, communication devices, machinery |
| Hangzhou Hengli | Chassis, enclosures, cabinets | Various sheet metal products | Various |
| Guangdong Dongji | Cabinets, brackets, enclosures | Sheet metal processing and manufacturing | Various |
| Nanjing Prima | Cabinets, enclosures, panels | Precision sheet metal fabrication | Various |
| Jiangmen CNCT | Cabinets, enclosures, brackets | Customized sheet metal fabrication | Various |
In this table, the manufacturers are listed along with their product range, specialization, and the industries they serve. This provides a concise comparison, assisting potential buyers in making informed decisions.
Background Research for factory sheet metal manufacturers Companies in China, use qcc.com archive.org importyeti.com
When researching factory sheet metal manufacturers in China, there are several platforms that can provide valuable information. Three popular resources include qcc.com, archive.org, and importyeti.com.
Qcc.com is an online platform that offers comprehensive company information and business credit reports in China. It provides details such as the company’s registered address, legal representative, business scope, and financial data. Users can access basic company profiles for free or purchase more in-depth reports for a fee. Qcc.com is a reliable source for verifying the authenticity of Chinese manufacturers.
Archive.org, also known as the Wayback Machine, is a digital archive of the internet. It allows users to access and view previously saved versions of websites. This can be helpful when investigating the history and credibility of a factory sheet metal manufacturer in China. By browsing through past versions of a company’s website, one can gain insights into its growth, reputation, and any changes that have occurred over time.
Importyeti.com is an online platform that provides comprehensive data on imports and exports. It allows users to search for specific products, importers, and exporters. Importyeti.com provides information about the suppliers, including their contact details, shipment history, and buyer reviews. This platform can help identify Chinese factory sheet metal manufacturers and provide insights into their export capabilities and reputation.
When utilizing these resources, it is essential to cross-reference information gathered from different platforms to ensure accuracy. Additionally, consider reaching out to potential manufacturers directly to inquire about their capabilities, certifications, and quality control processes. Building a list of reputable manufacturers in China requires thorough research and verification.
In summary, qcc.com, archive.org, and importyeti.com are valuable online platforms for background research on factory sheet metal manufacturers in China. These resources provide information about a company’s profile, history, and credibility, allowing buyers to make informed decisions when selecting suppliers.
Leveraging Trade Shows and Expos for factory sheet metal Sourcing in China
Trade shows and expos offer an invaluable platform for sourcing factory sheet metal in China. These events bring together manufacturers, suppliers, and industry professionals, allowing businesses to connect directly with potential partners and explore the latest trends and developments in the sheet metal industry.
By attending trade shows and expos in China, companies can gain a better understanding of the market landscape and identify reliable and experienced suppliers. These events showcase a wide range of sheet metal products, technologies, and materials, providing businesses with the opportunity to compare and assess various options before making a sourcing decision.
Additionally, trade shows and expos serve as a platform for networking and establishing valuable business relationships. By engaging with industry experts and participants, companies can gather insights on market trends, product innovations, and industry best practices. This information can inform decision-making processes and help optimize the sourcing strategy for factory sheet metal in China.
Furthermore, trade shows and expos often feature seminars, workshops, and conferences where experts share their knowledge and experiences. Attending these sessions can enhance understanding of the sheet metal industry in China while providing opportunities to learn about new manufacturing techniques, quality standards, and compliance regulations.
To leverage trade shows and expos effectively, businesses should thoroughly research the events and plan their agenda in advance. This includes identifying the most relevant exhibitions, understanding the exhibitors’ profiles, and scheduling meetings with potential suppliers. Proactive communication with suppliers before the event can facilitate a focused discussion, allowing businesses to clarify their requirements and evaluate the supplier’s capabilities.
In conclusion, trade shows and expos offer a comprehensive platform for sourcing factory sheet metal in China. By attending these events, businesses can connect with potential suppliers, gain market insights, and stay updated on industry trends. Leveraging these opportunities effectively can help companies find reliable and suitable partners for their sheet metal sourcing needs.
The Role of Agents and Sourcing Companies in Facilitating factory sheet metal Purchases from China
Agents and sourcing companies play a vital role in facilitating factory sheet metal purchases from China. With their expertise and knowledge of the local market, they act as intermediaries between buyers and manufacturers, ensuring smooth and efficient transactions.
One of the main responsibilities of agents and sourcing companies is to identify suitable suppliers for factory sheet metal purchases. They have a vast network of manufacturers and can provide options that meet specific requirements. By conducting comprehensive supplier research and due diligence, they ensure that the chosen manufacturers are reliable, experienced, and have a good track record.
Agents and sourcing companies also assist with price negotiation and contract agreement. With their understanding of the Chinese market and industry standards, they can negotiate the best possible prices on behalf of the buyers. They help establish terms and conditions that protect the interests of both parties and ensure a fair and transparent transaction.
Furthermore, agents and sourcing companies facilitate communication between buyers and manufacturers. They bridge the language and cultural barriers, ensuring effective communication and understanding of requirements. This helps in avoiding misunderstandings and ensures that the desired specifications and quality standards are clearly communicated to the manufacturers.
During the production process, agents and sourcing companies act as quality controllers. They conduct factory inspections and monitor production progress to ensure that the sheet metal products meet the specified standards. This reduces the risk of receiving faulty or substandard products and provides buyers with peace of mind.
Finally, agents and sourcing companies help with logistics and shipping arrangements. They coordinate the transportation of goods from the factory in China to the buyer’s location or any other designated destination. Their knowledge of shipping regulations and documentation requirements ensures a smooth and timely delivery.
Overall, agents and sourcing companies play a pivotal role in facilitating factory sheet metal purchases from China. They streamline the entire process, from supplier identification to final delivery, while mitigating risks and ensuring buyer satisfaction. Their expertise and local market knowledge are invaluable in navigating the complexities of international trade and establishing successful business partnerships.
Price Cost Research for factory sheet metal manufacturers Companies in China, use temu.com and 1688.com
When it comes to finding factory sheet metal manufacturers in China, two popular websites that can be utilized for price and cost research are temu.com and 1688.com. These platforms provide extensive options and information to help in the search for suitable suppliers.
Temu.com is a comprehensive sourcing platform that connects buyers with suppliers in China. It offers a wide range of products, including sheet metal manufacturing services. By using this platform, buyers can easily find and compare multiple suppliers based on their capabilities, certifications, and customer reviews. One can also directly contact the suppliers to negotiate prices and discuss specific product requirements.
Similarly, 1688.com is an online sourcing platform owned by Alibaba Group. It is primarily targeted at domestic users in China but can still be utilized by international buyers. The website provides access to a large number of manufacturers and suppliers dealing with various products including sheet metal manufacturing. It allows users to send inquiries, negotiate prices, and even order samples directly. Additionally, 1688.com provides detailed information about suppliers, such as their factory size, production capacity, certifications, and product range, which can be helpful in making informed decisions.
Conducting price and cost research on these platforms is relatively straightforward. Users can start by searching for sheet metal manufacturers in their desired location within China. Filters can be applied to narrow down the search results based on factors like product specifications, certifications, and minimum order quantity. It is advisable to shortlist multiple suppliers and collect quotes from them to compare prices and services.
While temu.com and 1688.com provide valuable information and a platform for conducting research, it is crucial to exercise due diligence when finalizing a deal. Buyers should aim to establish a clear understanding of the supplier’s capabilities, quality control measures, lead times, and payment terms. Additionally, verifying the supplier’s reputation through customer reviews and conducting sample testing before placing a large order can help ensure a successful partnership and minimize risks.
In summary, temu.com and 1688.com are useful platforms for conducting price and cost research when looking for factory sheet metal manufacturers in China. They provide a wide range of suppliers to choose from, along with detailed information and direct communication options. Using these platforms, buyers can efficiently compare prices and services, ultimately finding a suitable and reliable supplier for their sheet metal manufacturing needs.
Shipping Cost for factory sheet metal import from China
The shipping cost for importing factory sheet metal from China can vary depending on various factors such as the size and weight of the shipment, the shipping method chosen, the distance between the origin and destination, and any additional services required. However, we can provide a general overview of the shipping costs involved.
The most commonly used shipping methods for importing goods from China are sea freight and air freight. Sea freight is more cost-effective for large and heavy shipments, while air freight is faster but more expensive.
For sea freight, the shipping cost is usually calculated based on the volume or weight of the shipment, whichever is higher. As factory sheet metal can be heavy and take up a significant amount of space, the weight-based calculation is often used. A typical rate for shipping sheet metal by sea might range from $700 to $2500 per 20-foot container, depending on the distance and specific requirements.
Air freight is generally more expensive than sea freight but offers faster delivery times. The cost for shipping by air is typically calculated based on the weight of the shipment, with rates varying between $2 and $5 per kilogram. However, there may also be additional charges such as fuel surcharges, customs fees, and handling fees.
It is important to consider that the shipping cost is just one aspect of the total cost involved in importing goods from China. Other costs to keep in mind include customs duties, taxes, insurance, and any additional handling or transportation required within the destination country.
To get an accurate estimate of the shipping cost for importing factory sheet metal from China, it is advisable to contact a freight forwarder or shipping agent who can provide a detailed quote based on your specific requirements.
Compare China and Other factory sheet metal Markets: Products Quality and Price,Visible and Hidden Costs
China, one of the key players in the global manufacturing industry, offers a wide range of products in the sheet metal market. When comparing China with other factory sheet metal markets, several factors must be considered, including product quality and price, as well as visible and hidden costs.
In terms of product quality, Chinese manufacturers have made significant improvements over the years. They have adopted advanced technologies and improved production processes, ensuring that their sheet metal products meet international quality standards. However, it is important to note that there can still be variations in quality among different manufacturers in China. On the other hand, some other factory sheet metal markets, such as Germany and Japan, are known for their precision engineering and high-quality products. These markets have built a reputation for producing durable and reliable sheet metal components.
In terms of pricing, China has a competitive advantage due to its lower labor and production costs. As a result, Chinese manufacturers can offer sheet metal products at more affordable prices compared to other factory markets. This cost advantage has made China an attractive destination for companies looking to reduce production costs. However, it is important to consider additional factors such as transportation costs, import duties, and taxes, which can vary depending on the location of the buyer. In contrast, some other factory markets like the United States and Western European countries tend to have higher production costs, resulting in higher price tags for their sheet metal products.
Visible costs, such as material and labor costs, are relatively easy to assess and compare between different factory markets. However, hidden costs can significantly impact the overall cost of sourcing sheet metal products. For example, logistical costs, such as shipping and customs clearance fees, can vary greatly depending on the distance between the factory and the buyer’s location. Additionally, intellectual property protection and product compliance costs should also be considered when comparing different factory markets. China, for instance, has faced criticism in the past for intellectual property infringement, which can be a hidden cost for companies seeking to protect their designs and patents.
In summary, China offers a wide range of sheet metal products with improved quality and competitive pricing. However, other factory markets such as Germany and Japan are known for their superior product quality and precision engineering. When comparing factory markets, it is crucial to consider both visible and hidden costs. While China may have lower labor and production costs, transportation expenses and intellectual property protection can significantly impact the total cost. Ultimately, the choice of factory market depends on the specific requirements and priorities of the buyer.
Understanding Pricing and Payment Terms for factory sheet metal: A Comparative Guide to Get the Best Deal
When it comes to purchasing factory sheet metal, understanding pricing and payment terms is crucial to ensure you get the best deal. This comparative guide aims to help you navigate through the complexities of pricing and payment terms in the sheet metal industry.
Pricing for factory sheet metal can vary greatly depending on several factors. These factors include the type and grade of metal, specifications, dimensions, quantities, and processing requirements. Different suppliers may also have varying pricing structures, making it important to obtain quotes from multiple sources.
To ensure fair pricing, it is advisable to compare quotes on a standardized basis. This can be done by specifying the same metal grade, dimensions, and processing requirements, allowing for an apples-to-apples comparison. It is also recommended to request a breakdown of costs, including material, labor, and any additional fees, to identify any hidden charges.
Payment terms are another crucial aspect to consider. Common payment terms in the industry include upfront payment, partial payment, and payment upon delivery. Suppliers may offer discounts for upfront payments or longer payment terms. However, it is important to balance the payment terms with the financial capabilities of your organization.
Negotiating payment terms can be a viable option, especially for large orders. This can involve discussing installment plans, milestone payments, or credit options. Suppliers may be open to such negotiations if the order size and potential for future business are significant.
Additionally, taking into account the reputation and financial stability of the supplier is essential. A financially stable supplier is more likely to offer competitive pricing and favorable payment terms. Checking for any customer reviews or references can provide insights into the supplier’s reliability and performance.
Finally, it is crucial to review the terms and conditions of any agreement before finalizing the deal. Pay attention to clauses related to quality, delivery timelines, return policies, and warranty provisions. Ensuring clear communication and understanding of the terms can help avoid any future disputes or inconveniences.
In summary, understanding pricing and payment terms for factory sheet metal requires careful consideration of various factors. Obtaining multiple quotes, standardizing specifications, and negotiating payment terms can help secure the best deal. Evaluating the supplier’s reputation and reviewing the agreement’s terms and conditions are equally important steps in ensuring a successful transaction.
Chinese Regulations and Industry Standards Certifications for factory sheet metal,Import Regulations and Customs for factory sheet metal from China
In China, factory sheet metal production is regulated by several regulations and industry standards certifications aimed at ensuring the quality, safety, and compliance of the products. Some of these regulations and standards include:
1. China Compulsory Certification (CCC): CCC certification is a mandatory requirement for various products in China, including sheet metal products. It ensures that the products meet the minimum safety and quality standards set by the government.
2. National Standards: China has established national standards for various sheet metal products, such as GB/T 3880 for aluminum sheet and GB/T 2518 for steel sheet. These standards specify the requirements for product dimensions, mechanical properties, and surface quality.
3. ISO 9001: This international standard provides guidelines for implementing a quality management system. Many sheet metal factories in China obtain ISO 9001 certification as it demonstrates their commitment to quality control and customer satisfaction.
4. Environmental Regulations: China has implemented strict environmental regulations for manufacturing industries, including sheet metal production. Factories must comply with laws regarding waste management, emissions control, and pollution prevention.
5. Import Regulations and Customs: When importing factory sheet metal from China, it is essential to comply with the import regulations and customs requirements of the destination country. These may include documentation, labeling, packaging, and compliance with safety and import standards.
To ensure compliance and mitigate potential risks when importing factory sheet metal from China, it is advisable to work with a reputable supplier who holds the necessary certifications and can provide relevant documentation. Additionally, conducting thorough product inspections and quality control checks can help identify any potential issues before shipment. It is also recommended to consult with a customs broker or import expert to navigate the import requirements of the destination country.
Sustainability and Environmental Considerations in factory sheet metal Manufacturing
In factory sheet metal manufacturing, sustainability and environmental considerations play a crucial role in ensuring responsible and eco-friendly practices. These considerations focus on minimizing the negative impacts on the environment, conserving resources, and promoting sustainable development.
One key aspect of sustainability is the efficient use of raw materials. Factories can implement practices such as recycling and waste reduction to minimize material wastage. By implementing recycling programs and optimizing material usage, manufacturers can reduce the demand for virgin resources, conserve energy, and decrease waste generation.
Another important aspect is energy conservation. Factories can adopt energy-efficient technologies, such as using high-efficiency equipment and implementing energy management systems. Additionally, renewable energy sources like solar or wind power can be integrated into the manufacturing process to reduce reliance on fossil fuels and decrease greenhouse gas emissions.
Water conservation is another critical consideration. Factories can implement measures like water recycling and rainwater harvesting to reduce water consumption. Additionally, proper wastewater management systems can be implemented to ensure that water discharged from the facility meets environmental standards.
To address environmental concerns, factories should also prioritize the reduction of harmful emissions. This can be achieved by implementing effective exhaust systems, investing in air filtration technologies, and adopting cleaner production processes. Moreover, minimizing air pollution not only contributes to environmental sustainability but also creates a healthier and safer working environment for employees.
Furthermore, sustainable transportation practices should be followed to reduce the carbon footprint associated with logistics. Factories can consider using electric or hybrid vehicles for transportation, optimizing shipping routes to minimize distance, and investing in advanced logistics management systems to improve efficiency.
Lastly, sustainability requires a culture of continuous improvement and innovation. Regular assessments, audits, and certifications can help identify areas for improvement and ensure compliance with environmental standards. Additionally, collaboration with suppliers and customers can facilitate the adoption of sustainable practices throughout the supply chain.
In conclusion, sustainability and environmental considerations have become inherent aspects of factory sheet metal manufacturing. By implementing practices that prioritize resource efficiency, energy and water conservation, emissions reduction, and sustainable transportation, manufacturers can contribute to a greener future while benefiting from improved operational efficiency and maintaining a competitive edge.
List The Evolution history of “factory sheet metal”
Factory sheet metal has evolved significantly over time, transforming from a manual and labor-intensive process to one that is highly automated and efficient. The following is a brief history of the evolution of factory sheet metal:
1. Early Handcrafted Techniques (Pre-Industrial Revolution): Before the Industrial Revolution, sheet metal was usually handcrafted by skilled artisans. They would shape and form metal sheets using hammers, anvils, and other manual tools.
2. Industrial Revolution: The use of steam-powered machines during the Industrial Revolution brought significant advancements to sheet metal manufacturing. Punching and cutting machines powered by steam were introduced to increase productivity and precision.
3. Introduction of the Assembly Line (Early 20th Century): With the advent of the assembly line, factory sheet metal production became more streamlined. Specialized machines were developed to perform specific tasks, such as shearing, bending, and shaping metal. This allowed for faster and more consistent production.
4. Computer Numerical Control (CNC) Machines (1960s onwards): The introduction of computer numerical control (CNC) machines revolutionized sheet metal manufacturing. CNC machines use computer programming to control the movement of tools, allowing for precise and automated metal cutting, bending, and shaping. This technology greatly improved production speed, accuracy, and repeatability.
5. Laser Cutting and 3D Printing (Late 20th Century): In the late 20th century, laser cutting technology emerged, enabling highly accurate and efficient cutting of sheet metal. Additionally, advancements in 3D printing have opened up new possibilities in sheet metal production, allowing for complex and intricate designs to be manufactured with ease.
6. Robotic Automation (Present): Presently, factory sheet metal production has witnessed further automation with the integration of robotics. Robots are now used for tasks such as material handling, welding, and assembly, increasing productivity and reducing human error.
Overall, the evolution of factory sheet metal has been characterized by the introduction of new technologies, from steam-powered machines to CNC, lasers, 3D printing, and robotics. These advancements have greatly improved efficiency, precision, and versatility in sheet metal manufacturing, catering to the ever-changing demands of various industries.
The Evolution and Market Trends in factory sheet metal Industry
The factory sheet metal industry has experienced significant evolution and market trends over the years. Advancements in technology and increasing demand for efficient and customized metal products have shaped the industry’s trajectory.
One major evolution in the factory sheet metal industry is the adoption of automation and computer numerical control (CNC) machines. These technologies have revolutionized the production process by improving precision, reducing human error, and increasing production speed. CNC machines also allow for complex and intricate designs to be manipulated easily, enabling manufacturers to create highly customized products. This evolution has resulted in increased productivity and reduced manufacturing costs.
Another noteworthy trend in the factory sheet metal industry is the growing importance of sustainability and environmental consciousness. With global concerns about climate change and resource depletion, manufacturers are increasingly adopting eco-friendly practices. This involves implementing energy-efficient machines and processes, recycling and reusing materials, and reducing waste during production. Not only does this trend align with societal values, but it also provides a competitive advantage in the market, as more customers prefer sustainable products.
Additionally, the market trends in the factory sheet metal industry are heavily influenced by the rise of e-commerce and globalization. Online platforms have made it easier for manufacturers to reach a global customer base, expanding their market opportunities. This has also increased competition, as companies from different countries can now offer their products to customers worldwide. As a result, manufacturers are focusing on improving their product quality, reducing lead times, and offering competitive pricing to attract and retain customers.
Furthermore, the factory sheet metal industry has seen a shift towards the production of lightweight and durable metals. As industries such as automotive and aerospace demand lighter materials to improve fuel efficiency and overall performance, manufacturers have responded by developing advanced alloys and composites. This trend has also led to the innovation of new manufacturing techniques such as additive manufacturing, commonly known as 3D printing.
In conclusion, the evolution of factory sheet metal industry is driven by advancements in technology, such as automation and CNC machines, as well as the market trends of sustainability, globalization, and lightweight materials. Manufacturers must adapt to these changes to remain competitive and meet the evolving demands of customers in an increasingly globalized market.
Custom Private Labeling and Branding Opportunities with Chinese factory sheet metal Manufacturers
Chinese factory sheet metal manufacturers offer a range of custom private labeling and branding opportunities for businesses around the world. With a strong manufacturing infrastructure and expertise in sheet metal production, Chinese factories can help businesses create their own unique branded products.
Private labeling allows businesses to place their own brand name or logo on the products manufactured by Chinese factories. This enables companies to establish a distinct brand identity and build customer loyalty. Chinese factories work closely with businesses to understand their branding requirements and ensure that the products are produced according to their specifications.
In addition to private labeling, Chinese factories also offer custom branding opportunities. Businesses can collaborate with the factories to design and develop products that align with their brand image. This could include custom shapes, colors, finishes, and packaging options. Leveraging the expertise of Chinese manufacturers, businesses can create products that stand out in the market and resonate with their target audience.
Moreover, Chinese factories provide cost-effective solutions for private labeling and branding. The country’s manufacturing capabilities, economies of scale, and competitive pricing make it an attractive option for companies looking to establish their own branded products. With strict quality control standards and efficient manufacturing processes, businesses can be assured of high-quality products at affordable prices.
To seize these opportunities, it is important for businesses to find reliable and experienced Chinese factory sheet metal manufacturers. Thoroughly researching and vetting potential suppliers, checking their track record and certifications, and visiting their facilities can help businesses identify trustworthy partners who can deliver their private labeling and branding requirements.
In conclusion, partnering with Chinese factory sheet metal manufacturers enables businesses to tap into custom private labeling and branding opportunities. By leveraging the country’s manufacturing capabilities, companies can create their own branded products, build brand loyalty, and benefit from cost-effective solutions.
Tips for Procurement and Considerations when Purchasing factory sheet metal
When purchasing factory sheet metal for a procurement project, there are several tips and considerations that should be taken into account to ensure optimal results. These include:
1. Quality Assessment: Before making a purchase, thoroughly evaluate the quality of the sheet metal to ensure it meets the required standards. Consider factors such as material composition, thickness, durability, and finish.
2. Supplier Evaluation: Research and choose a reputable supplier who has a proven track record of delivering high-quality products on time. Consider factors such as their experience, certifications, customer reviews, and compliance with industry standards.
3. Cost Analysis: Compare prices from different suppliers to ensure that you are getting the best value for your money. However, remember that the cheapest option may not always be the best in terms of quality and long-term performance.
4. Material Compatibility: Ensure that the chosen sheet metal is compatible with the intended application and the manufacturing process in your factory. This includes considering factors such as weldability, formability, and corrosion resistance.
5. Customization Options: If your project requires specific dimensions or features, verify whether the supplier can provide customization services. This can help ensure the sheet metal fits your exact requirements and avoids unnecessary rework.
6. Lead Time: Consider the lead time required by the supplier to deliver the sheet metal. If you have time constraints, choose a supplier who can meet your delivery timeline without compromising on quality.
7. Packaging and Shipping: Inquire about the supplier’s packaging methods to ensure the sheet metal arrives in good condition. Additionally, consider the supplier’s shipping options, including costs and reliability.
8. Sustainability: If environmental sustainability is a priority, look for suppliers who offer sheet metal made from recycled materials or have eco-friendly production processes.
9. After-Sales Support: Evaluate the supplier’s after-sales support, including warranty coverage and customer service. This ensures that any issues or defects can be addressed promptly.
10. Compliance and Documentation: Ensure that the supplier provides all necessary documentation, such as material certifications, test reports, and compliance with industry regulations or standards.
By following these tips and considerations, you can make an informed decision when purchasing factory sheet metal, ultimately ensuring that you receive high-quality products that meet your project requirements.
FAQs on Sourcing and Manufacturing factory sheet metal in China
1. Why should I consider sourcing and manufacturing sheet metal in China?
Sourcing and manufacturing sheet metal in China offers several advantages, including cost savings due to lower labor and production costs compared to many Western countries. China has a well-established manufacturing infrastructure and a wide range of skilled workers, ensuring access to high-quality sheet metal fabrication services. Additionally, the country’s large-scale production capabilities enable quick turnaround times for large orders.
2. How do I find reliable sheet metal manufacturers in China?
It is crucial to conduct thorough research and due diligence to find reliable sheet metal manufacturers in China. Online platforms such as Alibaba and Global Sources can provide a starting point to identify potential suppliers. Verify the manufacturer’s credibility by reviewing their company profile, customer reviews, and certifications. Request samples and assess their quality standards through factory visits or third-party inspection services. Communication is key, so ensure effective communication channels are established with the manufacturer to avoid misunderstandings.
3. Are there any risks associated with sourcing sheet metal from China?
While sourcing sheet metal from China presents numerous advantages, there are potential risks to consider. These include language barriers, cultural differences, intellectual property infringements, and product quality inconsistencies. To mitigate these risks, it is essential to have clear and detailed specifications, sign a comprehensive manufacturing agreement, and protect intellectual property through patents or NDAs. Conducting strict quality control inspections and regular communication with the supplier can also help minimize any potential issues.
4. How can I ensure product quality when manufacturing in China?
To ensure product quality when manufacturing sheet metal in China, it is crucial to implement a robust quality control process. Start by establishing clear product specifications, quality standards, and inspection criteria. Conduct regular factory visits to assess the manufacturer’s production capabilities and quality control procedures. Additionally, consider hiring third-party inspection agencies to inspect the product during various manufacturing stages. Maintaining strong communication channels with the supplier and addressing any quality issues promptly will help maintain product consistency.
5. What are the typical lead times when sourcing sheet metal from China?
Lead times for sheet metal manufacturing in China can vary based on the complexity of the product, order quantity, and the manufacturer’s production capacity. It is important to discuss lead times with your supplier during the negotiation phase to set realistic expectations. Typically, lead times range from a few weeks to several months, including production, packaging, and transportation.
Remember, while sourcing and manufacturing sheet metal in China can offer cost savings and access to a wide range of capabilities, it is crucial to conduct thorough research, maintain effective communication, and implement stringent quality control measures to ensure a successful business relationship.
Why contact sourcifychina.com get free quota from reliable factory sheet metal suppliers?
Sourcifychina.com offers a free quota from reliable factory sheet metal suppliers for several reasons. Firstly, by obtaining a free quota, companies and individuals can gauge the costs and feasibility of their sheet metal projects without committing any financial resources upfront. This allows clients to make informed decisions based on accurate pricing and production capabilities.
Secondly, Sourcifychina.com partners with reliable factory sheet metal suppliers to ensure that clients receive high-quality products and services. These suppliers have been vetted and selected based on their expertise, track record, and ability to meet international quality standards. By providing a free quota, Sourcifychina.com instills confidence in clients regarding the quality and reliability of the chosen suppliers.
Additionally, offering a free quota helps foster trust and transparency between Sourcifychina.com and its clients. The company aims to build long-term relationships by demonstrating its commitment to providing genuine, trustworthy information and services. By offering a free quota, Sourcifychina.com establishes itself as a reputable sourcing platform that prioritizes customer satisfaction.
Furthermore, the free quota serves as an incentive to choose Sourcifychina.com as a sourcing partner. It eliminates the financial barrier to entry and encourages clients to explore the platform’s capabilities and expertise in sheet metal sourcing. By experiencing the benefits of a free quota, clients are more likely to continue using Sourcifychina.com for future sourcing needs.
In summary, Sourcifychina.com offers a free quota from reliable factory sheet metal suppliers to help clients assess costs, ensure product quality, foster trust, and encourage long-term partnerships. This approach aligns with their objective of providing a seamless and reliable sourcing experience for businesses and individuals.