Introduce about how does cnc machining work guide,Qulity,Cost,Supplier,Certification,Market,Tips,FAQ
CNC machining, which stands for Computer Numerical Control, is a manufacturing process that utilizes computerized controls and machine tools to produce precise and complex parts from a variety of materials. In this guide, we will explore how CNC machining works, its benefits, and provide insight into finding a reliable supplier.
CNC machining operates through a series of pre-programmed instructions that control the movement of machine tools. These instructions are coded in a language called G-code and tell the machine how to position, move, and cut the material. The process starts with creating a 3D model of the part using CAD software, which is then transformed into a CNC program. The program is then transferred to the CNC machine, which follows the instructions to shape the material into the desired shape.
One of the key advantages of CNC machining is its ability to produce high-quality parts with tight tolerances. The computer-controlled precision ensures consistent results and eliminates human errors. CNC machining can work with a wide range of materials, including metals, plastics, and composites, allowing for versatility in manufacturing.
When considering the cost of CNC machining, several factors come into play, such as material cost, machine setup time, and complexity of the part. While CNC machining may have higher upfront costs compared to other manufacturing methods, its efficiency, accuracy, and reduced labor requirements often make it cost-effective in the long run.
Finding a reliable CNC machining supplier is crucial to ensure quality results. It is important to evaluate the supplier’s experience, capabilities, and certifications. ISO 9001 certification is a recognized standard for quality management systems in machining. Additionally, a supplier with a well-maintained and regularly updated CNC machine fleet is more likely to deliver consistent and high-quality parts.
In terms of market demand, CNC machining is widely utilized across various industries, including automotive, aerospace, medical, and electronics. The ability to produce complex parts with precision and speed has contributed to its growing popularity.
Finally, here are a few tips and frequently asked questions related to CNC machining:
1. Optimize part designs for CNC machining to reduce costs and improve manufacturability.
2. Consider using standard materials and tooling options to minimize expenses.
3. Collaborate closely with the supplier to ensure clear communication and understanding of requirements.
FAQ:
– How long does CNC machining take?
The time required depends on factors such as part complexity, material, and supplier capabilities. Typically, CNC machining can produce parts within a few days to a couple of weeks.
– What are the advantages of CNC machining over traditional machining?
CNC machining offers greater precision, repeatability, and higher production speeds compared to traditional machining methods.
In conclusion, CNC machining is a precise and efficient manufacturing process that offers numerous benefits. By understanding the process, evaluating suppliers, and optimizing designs, businesses can harness the potential of CNC machining to produce high-quality parts at competitive costs.
Types of how does cnc machining work
CNC machining, or Computer Numerical Control machining, is a manufacturing process that utilizes computerized controls and machine tools to remove material from a workpiece to create a desired shape or design. There are several different types of CNC machining processes, each with its own unique characteristics and applications. Some of these include:
1. Milling: In milling, a rotating cutting tool removes material from the workpiece to produce a desired shape. The cutting tool typically moves along multiple axes, allowing for precise cutting and complex designs.
2. Turning: Turning involves rotating the workpiece while a cutting tool shapes it to the desired form. This process is commonly used to create cylindrical shapes, such as shafts or discs.
3. Drilling: Drilling utilizes a rotating cutting tool with two edges to create holes in the workpiece. The drill bit moves in a linear motion, and multiple holes can be drilled accurately in a short time.
4. Grinding: Grinding is a precision machining process that utilizes a rotating abrasive wheel to remove tiny amounts of material from the workpiece. It is commonly used to produce smooth and accurate finishes on surfaces.
5. Laser Cutting: Laser cutting uses a high-powered laser beam to cut through the workpiece. It is a precise and efficient method commonly used for intricate designs, contours, and thin materials.
6. Electrical Discharge Machining (EDM): EDM uses electrical discharges to shape the workpiece. A tool, typically made of copper or graphite, acts as an electrode that discharges sparks onto the workpiece, eroding the material to create the desired shape.
CNC machining involves feeding specific instructions into a computer program, which controls the machine and guides its movements. These instructions, often in the form of a digital model or computer-aided design (CAD) file, provide dimensional and geometrical information for the desired part. The machine tools operate with precision and repeatability, allowing for efficient and accurate production. This computer-controlled automation enhances productivity and reduces human error, resulting in high-quality, reliable machined parts and components.
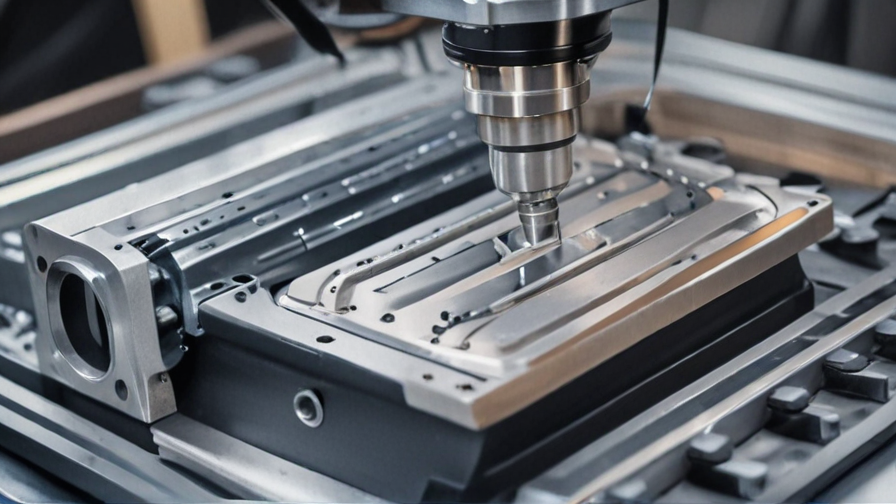
Pros and Cons of Using how does cnc machining work
CNC machining, or Computer Numerical Control machining, is a process that utilizes computerized controls and programming to operate machine tools for manufacturing various precision parts and components. It offers several advantages and disadvantages, demonstrated below:
Pros of Using CNC Machining:
1. Precision: CNC machining provides exceptional accuracy and precision, as it follows pre-programmed designs which are highly accurate. This ensures consistency and reduces errors, resulting in higher quality parts.
2. Efficiency: CNC machines can operate continuously, with minimal downtime for tool changes or adjustments. This allows for increased productivity and faster turnaround times.
3. Versatility: CNC machines can produce a wide range of parts with varying sizes and complexities. The versatility of the technology allows for flexibility in manufacturing and the ability to handle different materials.
4. Automation: CNC machines are fully automated, reducing the need for extensive manual labor and increasing the level of safety since operators can monitor operations remotely.
5. Reproducibility: Once a design is programmed and tested, CNC machines can replicate it repeatedly, ensuring consistent product quality and reducing the chances of human error.
Cons of Using CNC Machining:
1. High Initial Costs: CNC machines can be expensive to acquire and set up. The cost of purchasing the equipment and the necessary software, along with the training required, can be significant for smaller businesses.
2. Complex Programming: Programming CNC machines can be a challenging task, requiring skilled operators with technical knowledge and expertise. The intricate programming process may also result in increased development time.
3. Limited Flexibility: While CNC machines offer versatility, they may have limitations when it comes to intricate designs or shapes that require precise human intervention. Certain complex geometries may be difficult or impossible to achieve using CNC machining alone.
4. Maintenance and Repair: CNC machines require regular maintenance to ensure optimal performance. Additionally, if a machine malfunctions or breaks down, repairs can be expensive and time-consuming, leading to operational interruptions.
5. Lack of Human Interaction: The fully automated nature of CNC machining means that there is limited human interaction and creativity involved in the manufacturing process. This can reduce the personal touch and adaptability that human operators can bring to certain manufacturing tasks.
Overall, while CNC machining offers numerous advantages in terms of precision, efficiency, versatility, automation, and reproducibility, it is important to consider the potential drawbacks such as high initial costs, complex programming requirements, limited flexibility in design, maintenance and repair needs, and reduced human interaction.
how does cnc machining work Reference Specifications (varies for different product)
CNC machining, or Computer Numerical Control machining, is a manufacturing process used to produce precise parts and components. It utilizes computer-controlled machines to remove material from a workpiece, following a pre-determined path or set of instructions.
The process starts with a design or blueprint of the desired part. This design is then converted into a specialized computer program called a CNC program. The program contains instructions for the machine, such as the tooling path, cutting speeds, and depths. It also includes the specific dimensions and tolerances required for the part.
Once the CNC program is ready, it is loaded into the CNC machine. The machine consists of various components, including a worktable, cutting tools, and a cutting head that holds the tool. The workpiece, typically made of metal or plastic, is securely clamped onto the worktable.
The machine operator initiates the machining process by running the CNC program. The program controls the movement of the cutting tool in multiple axes (usually 3 to 5 axes) to perform precise cuts on the workpiece. The machine removes material by either cutting, drilling, milling, or turning, depending on the required shape and features.
During the machining process, the machine operator may monitor the operation to ensure everything is running smoothly. They can also make adjustments to the program or machine settings if necessary.
After the machining is complete, the finished part is carefully inspected for accuracy and quality. Any necessary post-processing steps, such as polishing, deburring, or assembly, may be performed before the part is considered complete.
CNC machining offers several advantages over traditional manual machining. It allows for higher precision, faster production times, and repeatability. It also reduces the chances of human error and can accommodate complex geometries.
In conclusion, CNC machining is a highly automated process that uses computer-controlled machines to produce precise parts. It follows a programmed path and removes material from a workpiece to create the desired shape and features. The process offers several advantages in terms of accuracy, speed, and versatility.
Applications of how does cnc machining work
CNC machining, which stands for computer numerical control machining, is a manufacturing process that utilizes computer software to control and automate the movements of tools and machines. This technology has revolutionized various industries by providing precise, efficient, and consistent manufacturing capabilities. Here are some key applications of CNC machining:
1. Automotive Industry: CNC machining is extensively used in the automotive sector for manufacturing components with high precision and intricate designs. It can produce engine parts, transmission components, brake system parts, and other critical automotive components.
2. Aerospace Industry: CNC machining plays a vital role in the aerospace industry by providing the ability to produce complex parts with stringent tolerances. It is used for manufacturing aircraft components like turbine blades, engine mounts, landing gear, and cockpit controls.
3. Medical Industry: CNC machining has transformed the medical sector by enabling the production of precise and customized medical devices and implants. It is used to manufacture implants, prosthetics, surgical tools, and dental components that require accuracy and biocompatibility.
4. Electronics Industry: CNC machining is widely used in electronic manufacturing for creating intricate components used in devices such as smartphones, computers, and tablets. It enables the production of microchips, circuit boards, connectors, and housings with exceptional accuracy.
5. Prototyping and Rapid Manufacturing: CNC machining is a preferred choice for prototyping due to its flexibility and fast turnaround time. It allows designers to quickly develop prototypes and refine their designs before moving to mass production. Rapid manufacturing using CNC machining provides a cost-effective solution for small-batch production of customized parts.
6. Defense Industry: CNC machining is extensively used in the defense sector for manufacturing various components, including firearms, missiles, military vehicles, and protective gear. It ensures the production of high-quality components that meet the stringent requirements of defense applications.
7. Furniture and Design Industry: CNC machining is employed in the furniture and design industry for precise cutting, shaping, and carving of wood, as well as other materials. It enables the creation of intricately designed furniture, decorative pieces, signage, and architectural elements.
8. Energy Industry: CNC machining is used in the energy sector for manufacturing parts required in power generation, transmission, and distribution. It is used to produce turbine blades, shafts, valves, and other critical components in power plants.
In conclusion, CNC machining has diverse applications across various industries including automotive, aerospace, medical, electronics, defense, furniture and design, energy, and more. Its ability to provide precision, speed, and versatility has made it an integral part of modern manufacturing processes.
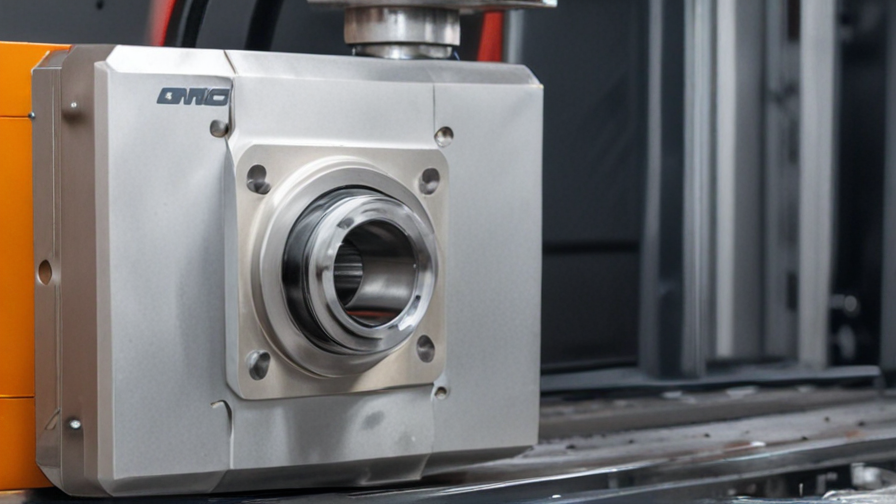
The Work Process and how to use how does cnc machining work
CNC machining, or Computer Numerical Control machining, is a manufacturing process that uses computerized technology to control the movement and operation of machine tools. It is widely used in various industries for precision and efficient production of parts and components.
The work process of CNC machining involves several steps. First, a design file or blueprint is created using Computer-Aided Design (CAD) software. The design file provides instructions on the dimensions, geometry, and features of the desired part.
Next, the design file is loaded into the CNC machine’s computer system. The operator sets up the machine by installing the required cutting tools and securing the workpiece onto the machine bed or vice.
Once the setup is complete, the machine is started, and the CNC program is executed. The computer system directs the movement of the machine’s axes, controlling the cutting tools to remove material from the workpiece according to the design specifications. The cutting tools may include drills, mills, lathes, or grinders, depending on the desired outcome.
During the machining process, the machine constantly monitors and adjusts the cutting parameters, such as speed, feed rate, and depth of cut, to ensure accurate and precise results. This real-time control is achieved through sensors and feedback mechanisms that provide information on the cutting tool’s position and the workpiece’s dimensions.
Once the machining operation is completed, the finished part is inspected for quality control. It may undergo additional processes like deburring, polishing, or surface treatment to meet the desired specifications. The CNC machine can also perform these secondary operations if programmed to do so.
Overall, CNC machining offers numerous advantages such as high precision, efficiency, and the ability to produce complex parts with minimal human intervention. It is widely used in industries like automotive, aerospace, healthcare, and electronics to create a wide range of components and products.
In conclusion, CNC machining is a computer-controlled manufacturing process that follows a step-by-step approach from design to finishing. It utilizes cutting-edge technology and tools to produce accurate and high-quality parts efficiently. With continuous advancements in CNC technology, the capabilities and applications of this process are expanding, revolutionizing the manufacturing industry.
Quality Testing Methods for how does cnc machining work and how to control the quality
CNC machining is a manufacturing process that utilizes computer-controlled machines to produce high-quality and precise parts or products. To ensure the quality of CNC machining work, several testing methods can be implemented. Some commonly used methods include:
1. Dimensional and geometric measurements: This involves measuring key dimensions and geometry of the machined parts using precision measurement tools such as calipers, micrometers, and coordinate measuring machines (CMMs). It helps ensure that the parts meet the required specifications.
2. Visual inspection: Visual inspection involves examining the machined parts for any surface defects, tool marks, burrs, or other visible flaws that may impact the quality or functionality. It is typically performed by trained inspectors or quality control personnel.
3. Material testing: Material testing methods such as hardness testing, tensile testing, or chemical composition analysis can be employed to verify the mechanical properties and material integrity of the machined parts. This helps ensure that the materials used are of the desired quality and strength.
4. Functional testing: Functional testing involves subjecting the machined parts to simulated or actual working conditions to evaluate their performance. This can include testing the parts for functionality, durability, load capacity, or any specific requirements defined by the customer or industry standards.
5. Statistical process control (SPC): SPC is a method used to monitor and control the quality of CNC machining by collecting and analyzing data throughout the manufacturing process. It helps identify any variations or trends that may affect the quality and allows for timely corrective actions.
To control the quality in CNC machining, a few key strategies can be employed. Firstly, employing highly skilled and trained operators who have a good understanding of the machining process and quality requirements is important. Regular training programs can also help enhance the knowledge and skills of the operators.
Additionally, implementing robust quality management systems such as ISO 9001 can help establish clear quality control procedures and ensure adherence to industry standards. Regular audits and inspections can be carried out to monitor and evaluate the effectiveness of these systems.
Furthermore, having proper documentation and record-keeping systems in place can help track and trace the quality-related information, including inspection reports, material certificates, and process parameters. This facilitates traceability and enables quick identification of any quality issues or deviations.
Ultimately, a comprehensive quality control plan that incorporates these testing methods and strategies can help ensure that CNC machining work meets the desired standards and requirements, leading to high-quality products and customer satisfaction.
how does cnc machining work Sample Policy and Post-Purchase Considerations for how does cnc machining work from China
CNC (Computer Numerical Control) machining is a manufacturing process that utilizes pre-programmed computer software to control the movement and operation of machines, such as mills, lathes, routers, and grinders.
The process begins with the creation of a digital model or CAD (Computer-Aided Design) drawing of the part to be manufactured. This model contains detailed specifications and dimensions. The CAD drawing is then converted into a CNC program using CAM (Computer-Aided Manufacturing) software.
The CNC program is then loaded into the CNC machine, which is equipped with various cutting tools. The machine operator sets up the workpiece and positions it correctly within the machine. The CNC machine operates autonomously, following the program’s instructions.
The machine works by moving the cutting tool along different axes (X, Y, and Z), based on the programmed instructions. The cutting tool removes material from the workpiece, creating the desired shape and dimensions. The speed and direction of the tool’s movement, as well as the feed rate, are all controlled by the CNC program.
CNC machining offers several advantages over traditional manual machining. It allows for highly accurate and repeatable parts production, as the computer-controlled machines can maintain precise dimensions throughout the manufacturing process. Additionally, CNC machining enables complex designs and shapes to be easily achieved, as the machines can move in multiple directions.
When sourcing CNC machining services from China, it is essential to consider the following post-purchase factors:
1. Quality Assurance: Ensure that the supplier has a proven track record of producing high-quality CNC machined parts. Request samples or reviews from their previous customers to evaluate the quality of their work.
2. Communication and Transparency: Establish clear communication with the supplier to discuss design requirements, specifications, and any modifications needed. A reliable supplier should be responsive, provide regular updates, and answer any queries promptly.
3. Shipping and Logistics: Consider the supplier’s shipping capabilities and lead times. Get clarification on packaging, handling, and customs duties to avoid any unexpected costs or delays.
4. Warranty and After-sales Service: Inquire about the supplier’s warranty policies and after-sales support. A reputable supplier should offer a warranty for their products and be willing to address any issues or concerns that may arise post-purchase.
By understanding the workings of CNC machining and considering these post-purchase factors, one can confidently source CNC machining services from China and ensure a smooth and successful manufacturing process.
Sourcing how does cnc machining work from China: Opportunities, Risks, and Key Players
CNC machining, also known as computer numerical control machining, is a manufacturing process that utilizes pre-programmed computer software to control the movement of machinery and tools. It is a popular method for producing high-quality and precise metal or plastic parts. In recent years, China has emerged as a major player in the global CNC machining market due to its low costs, advanced technological capabilities, and efficient production processes.
One of the key opportunities of sourcing CNC machining from China is the cost advantage. China offers competitive pricing for CNC machining services compared to many other countries. This cost advantage arises from lower labor and operational costs, as well as strong supply chain networks. Sourcing from China can result in significant cost savings for businesses looking to produce custom parts or components.
Moreover, Chinese CNC machining companies have made significant advancements in terms of technology and machinery. They have heavily invested in modern equipment, ensuring high precision and efficient production processes. Chinese companies also offer a wide range of capabilities, such as milling, turning, drilling, and grinding, allowing for versatile production options. This enables businesses to access a comprehensive range of CNC machining services from a single source.
However, there are risks associated with sourcing CNC machining from China as well. One primary concern is the potential for intellectual property theft or infringement. Companies must take precautions to protect their designs, patents, and proprietary information when engaging with Chinese manufacturers. Transparency and legal protection measures, such as Non-Disclosure Agreements, should be established to mitigate these risks.
Another risk is the language and cultural barrier. Effective communication is vital for successful collaboration in CNC machining projects. Language differences and cultural nuances may lead to misunderstandings or incorrect execution of specifications. Selecting a reliable manufacturing partner with experience in international transactions and a proficient English-speaking team can help mitigate these risks.
When sourcing CNC machining services from China, it is essential to choose reliable and reputable key players in the industry. Some prominent Chinese CNC machining companies include Foxron Precision Metal Parts, SG Prototype, Shenzhen Ebelno Technology Co., Ltd., and Huayang Rapid Manufacturing Co., Ltd. These companies have established a strong track record and have earned recognition for their precision, quality, and customer service.
In conclusion, sourcing CNC machining services from China presents significant opportunities due to competitive pricing and advanced technological capabilities. However, businesses must be aware of the potential risks, such as intellectual property theft and communication challenges. Engaging with reputable key players in the Chinese CNC machining industry can help mitigate these risks and ensure successful outcomes for manufacturing projects.
How to find and select reliable how does cnc machining work manufacturers in China,use google search manufacturers and suppliers
Finding and selecting reliable CNC machining manufacturers in China can be a daunting task, but with the help of Google search and a few key strategies, it can be made easier. Here are some steps to follow:
1. Start with a Google search: Use specific keywords such as “CNC machining manufacturers in China” or “reliable CNC machining suppliers” to find a list of potential manufacturers. Make sure to include relevant specifications or requirements in your search.
2. Refine your search: Go through the search results and shortlist the manufacturers that seem to meet your requirements. Look for websites that convey professionalism and provide detailed information about their services, capabilities, certifications, and experience. Make note of contact information and relevant details for each manufacturer.
3. Check company credibility: Research each shortlisted manufacturer to verify their credibility. Look for customer reviews and ratings on platforms like Alibaba, Thomasnet, or other industry-specific directories. These reviews can provide insights into their reputation and customer satisfaction levels.
4. Evaluate capabilities and quality standards: Assess each manufacturer’s CNC machining capabilities, including the range of materials they can work with, the size of parts they can handle, and the type of CNC machines they use. Ensure they have the necessary quality certifications, such as ISO 9001, to meet your standards.
5. Communication and responsiveness: Reach out to the shortlisted manufacturers via email or phone. Evaluate their responsiveness and willingness to provide detailed information about their services, pricing, and lead times. Good communication is essential for successful collaboration.
6. Request samples and ask for references: Ask the manufacturers to provide samples of their previous work or refer you to existing customers. This will help you assess the quality of their products and services firsthand.
7. Pricing and terms: Obtain detailed quotes from the manufacturers that passed your evaluation. Compare prices, production lead times, and payment terms to ensure they align with your budget and project requirements.
8. Visit the manufacturing facility (if possible): If feasible, consider visiting the manufacturing facility in person to assess their infrastructure, equipment, and overall capabilities. This will give you additional confidence in the manufacturer’s reliability.
9. Start with a small order: Initially, place a small order to test the manufacturer’s capabilities and to verify their commitment to meeting your quality and delivery requirements.
By following these steps, it is possible to find and select reliable CNC machining manufacturers in China. Remember to focus on reputation, capabilities, communication, and quality standards during the evaluation process.
How to check how does cnc machining work manufacturers website reliable,use google chrome SEOquake check if ranking in top 10M
To verify the reliability of a CNC machining manufacturer’s website, you can follow these steps using Google Chrome and SEOquake:
1. Install the SEOquake extension: Open Google Chrome browser, go to the Chrome Web Store, search for ‘SEOquake’, and click ‘Add to Chrome’ to install the extension.
2. Visit the manufacturer’s website: Go to the website of the CNC machining manufacturer that you want to evaluate.
3. Check the website’s Alexa Rank: Once you are on the manufacturer’s website, click on the SEOquake icon in your browser’s toolbar. It will display a drop-down menu with various statistics. Look for the ‘Alexa Rank’ of the website. Alexa Rank indicates how popular a website is based on its traffic. A lower number implies higher popularity and reliability. If the ranking is within the top 10 million or better, it suggests a decent level of visibility and credibility.
4. Verify other SEO statistics: Take a look at other SEO-related metrics provided by SEOquake. You can view the number of external links, the website’s age, number of indexed pages, and social media presence. While these metrics alone may not determine reliability, they can provide additional insights.
5. Assess website content and design: Evaluate the quality and professionalism of the website’s content. Check if the information provided is accurate, up-to-date, and presents the necessary details about the company, services, and process. A reliable website should have a well-organized layout, intuitive navigation, and clear contact information.
By following these steps, you can get a quick overview of a CNC machining manufacturer’s website reliability using SEOquake and Google Chrome. Remember, it is essential to consider these indicators alongside other factors, such as customer reviews and industry reputation, to make an informed assessment.
Top 10 how does cnc machining work manufacturers in China with each 160 words introduce products,then use markdown create table compare
There are numerous CNC machining manufacturers in China that offer high-quality products. Here, we will introduce the top 10 manufacturers and give a brief description of their products, followed by a table comparing their key features.
1. Ningbo Redfir Hi-Tech Board Industry Co., Ltd. specializes in producing precision CNC machined parts, including aluminum and stainless steel components for industries such as automotive, aerospace, and electronics.
2. Dongguan Kaizhida Precision Machinery Co., Ltd. provides precision CNC machining services for parts like connectors, housings, and brackets. They focus on small to medium-sized production runs.
3. Suzhou Parts Home Limited offers CNC milling and turning services with a wide range of materials, including aluminum, brass, and plastics. They have extensive experience in manufacturing medical, automotive, and industrial components.
4. Shenzhen Xinwo Precision Machining Co., Ltd. specializes in CNC machining for military, aerospace, and medical industries. Their products include connectors, valves, and control devices.
5. Xiamen Xinchuanghui Industry & Trade Co., Ltd. offers CNC machining services for various industries, including electronics, automotive, and telecommunications. They provide customized solutions for complex parts production.
6. Shenzhen Qinwei Industrial Co., Ltd. focuses on CNC precision machining, offering services for industries such as automotive, electronics, and telecommunications. Their products cover components like chassis, heat sinks, and brackets.
7. Suzhou Hengtong Import and Export Co., Ltd. provides CNC machining services for aerospace, automotive, and electronics industries. They manufacture high-precision parts using various materials like aluminum, stainless steel, and brass.
8. Ningbo Target Machinery Co., Ltd. specializes in CNC machining of aluminum and steel components, offering solutions for industries such as automotive, telecommunications, and home appliances.
9. Dongguan Fuhong Precision Hardware Co., Ltd. offers a wide range of CNC machining services, including milling, turning, and grinding. Their products are used in industries like automotive, medical, and electronics.
10. Shenzhen Yixin Precision Metal and Plastic Ltd. focuses on CNC machining for industries such as automotive, medical, and robotics. They provide services for complex parts with high precision requirements.
| Manufacturer | Specialty | Materials | Industries |
| — | — | — | — |
| Ningbo Redfir Hi-Tech Board Industry Co., Ltd. | Precision CNC machining | Aluminum, stainless steel | Automotive, aerospace, electronics |
| Dongguan Kaizhida Precision Machinery Co., Ltd. | CNC machining services | Connectors, housings, brackets | Various |
| Suzhou Parts Home Limited | CNC milling, turning | Aluminum, brass, plastics | Medical, automotive, industrial |
| Shenzhen Xinwo Precision Machining Co., Ltd. | CNC machining for military, aerospace, medical | Connectors, valves, control devices | Various |
| Xiamen Xinchuanghui Industry & Trade Co., Ltd. | Customized CNC machining | Various | Electronics, automotive, telecommunications |
| Shenzhen Qinwei Industrial Co., Ltd. | CNC precision machining | Various | Automotive, electronics, telecommunications |
| Suzhou Hengtong Import and Export Co., Ltd. | CNC machining | Aluminum, stainless steel, brass | Aerospace, automotive, electronics |
| Ningbo Target Machinery Co., Ltd. | CNC machining | Aluminum, steel | Automotive, telecommunications, home appliances |
| Dongguan Fuhong Precision Hardware Co., Ltd. | CNC machining | Various | Automotive, medical, electronics |
| Shenzhen Yixin Precision Metal and Plastic Ltd. | CNC machining | Various | Automotive, medical, robotics |
This table provides a comparative overview of the top 10 CNC machining manufacturers in China. Each manufacturer specializes in various materials and serves different industries. Customers can choose the suitable company based on their specific requirements and industry needs.
Background Research for how does cnc machining work manufacturers Companies in China, use qcc.com archive.org importyeti.com
CNC machining, also known as Computer Numerical Control machining, is a manufacturing process that utilizes pre-programmed computer software to control the movement and operation of machinery in order to create precise and complex parts. Many companies in China specialize in CNC machining due to its efficiency, accuracy, and cost-effectiveness.
Qcc.com, a Chinese business information website, provides a database of companies in China along with their registered information, corporate profiles, and business activities. This platform can be used to search for CNC machining manufacturers in China, gaining access to their contact details and further research about their capabilities.
Archive.org, a digital library, allows users to access archived web pages and browse through historical records of various websites. It can be utilized to explore the historical information and past developments of CNC machining companies in China, providing insights into their growth, expertise, and experience over time.
Importyeti.com is an import/export data platform that offers detailed shipment records, trade data, and supplier information. It can be utilized to identify CNC machining manufacturers in China, their business details, and their import/export trends. This data can shed light on their global market presence, customer base, and potential business opportunities.
By utilizing these resources, researchers can gather crucial information about CNC machining manufacturers in China. This includes their background, capabilities, size, production capacity, certifications, quality control processes, and customer reviews. Additionally, researchers can gain insights into the types of materials they work with, machining capabilities, CNC machine tools used, and value-added services provided.
Conducting thorough background research using platforms like qcc.com, archive.org, and importyeti.com can help buyers, entrepreneurs, and engineers make informed decisions when selecting CNC machining manufacturers in China. This information will enable them to choose the most suitable partner based on their specific requirements, quality standards, production volume, and budget.
Leveraging Trade Shows and Expos for how does cnc machining work Sourcing in China
Trade shows and expos are excellent platforms for sourcing CNC machining services in China. These events bring together industry professionals, suppliers, and manufacturers, providing a unique opportunity to learn about the latest trends, technologies, and products in the CNC machining industry.
By attending these events, business owners and procurement managers can connect directly with Chinese CNC machining suppliers. This face-to-face interaction allows for a better understanding of their manufacturing capabilities, quality standards, and production processes.
During trade shows and expos, suppliers showcase their CNC machines, display samples of their work, and provide detailed information about their services. This enables buyers to assess the supplier’s capabilities and determine if they meet their specific requirements. Moreover, attendees can evaluate potential suppliers based on their manufacturing expertise, equipment, certifications, and product quality.
Furthermore, trade shows and expos often feature industry experts who share insights and knowledge on CNC machining techniques and best practices. These educational sessions can help buyers understand the intricacies of CNC machining, allowing them to make informed decisions when selecting a supplier.
Trade shows and expos also allow buyers to network with other professionals in the industry and gather recommendations or referrals for reliable CNC machining suppliers in China. Building relationships with industry stakeholders can provide valuable insights and connections, further streamlining the sourcing process.
In conclusion, leveraging trade shows and expos for sourcing CNC machining services in China offers a range of benefits. It enables buyers to evaluate suppliers’ capabilities, assess product quality, gain industry insights, and network with industry professionals. By utilizing these platforms, businesses can find reputable CNC machining suppliers in China to meet their manufacturing needs.
The Role of Agents and Sourcing Companies in Facilitating how does cnc machining work Purchases from China
Agents and sourcing companies play a crucial role in facilitating CNC machining purchases from China. These intermediaries act as a bridge between buyers and manufacturers, ensuring a smooth and efficient procurement process.
Agents and sourcing companies have extensive knowledge of the Chinese market and its manufacturing capabilities. They have established relationships with reliable and trustworthy CNC machining manufacturers in China. This enables them to source high-quality products at competitive prices.
When a buyer requires CNC machining services, they can contact an agent or sourcing company with their specifications and requirements. The intermediary will then locate suitable manufacturers in China that can meet these needs. They will negotiate prices and terms on behalf of the buyer, ensuring that they obtain the best possible deal.
Agents and sourcing companies also play a vital role in quality control. They have local representatives or quality inspectors in China who can visit the manufacturing facilities and assess the production process. This helps to verify the manufacturer’s capabilities and ensure that they adhere to the buyer’s quality standards. If there are any issues or concerns, the intermediary can address them directly with the manufacturer, minimizing potential risks for the buyer.
Furthermore, agents and sourcing companies often handle logistics and shipping arrangements. They coordinate the transportation of the CNC machined parts from the manufacturer’s facility in China to the buyer’s location. This includes managing customs clearance, documentation, and arranging the most cost-effective and reliable shipping methods.
By utilizing the services of agents and sourcing companies, buyers can overcome language and cultural barriers, as well as navigate the complexities of international trade. These intermediaries simplify the procurement process, streamline communication, mitigate risks, and ultimately facilitate successful CNC machining purchases from China.
Price Cost Research for how does cnc machining work manufacturers Companies in China, use temu.com and 1688.com
When it comes to understanding the pricing and cost aspects of CNC machining work manufacturers in China, two popular platforms to explore are temu.com and 1688.com. These platforms provide comprehensive information regarding the services offered by various companies, allowing businesses to make informed decisions.
Temu.com is an online sourcing platform that connects buyers with suppliers, allowing users to search for specific products or services. By searching for “CNC machining work manufacturers” on temu.com, businesses can find a list of companies in China that specialize in this field. Each company profile typically includes details such as their location, manufacturing capabilities, certifications, and customer reviews. This information can help businesses determine the quality and reliability of the manufacturers, factors which may influence the pricing.
Another valuable platform for price and cost research is 1688.com, a Chinese wholesale website owned by Alibaba Group. While the site is primarily in Chinese, it provides a wide range of products and services at competitive prices. By searching for “CNC machining work” on 1688.com, buyers can access a vast array of suppliers and compare prices for different manufacturing processes. The website also allows users to directly communicate with manufacturers, diving deeper into production details and negotiating quotes.
By leveraging these platforms, businesses can access a wealth of information about CNC machining work manufacturers in China and gather insights into potential pricing and costing. However, it’s important to note that the pricing of CNC machining work can vary significantly based on several factors, including the complexity of the part, the material used, the quantity required, and the supplier’s capabilities. Therefore, businesses should thoroughly communicate their requirements and expectations to suppliers to obtain accurate pricing information.
Shipping Cost for how does cnc machining work import from China
When importing CNC machining services from China, one of the key considerations is the shipping cost. The shipping cost is determined by several factors, including the weight and volume of the shipment, the shipping method chosen, and the distance between China and the destination country.
There are different shipping methods available, each with its own cost implications. One common method is sea freight, which is generally the most cost-effective option for large and heavy shipments. Sea freight costs are calculated based on the cubic meter (CBM) or weight of the cargo. Depending on the volume and weight, sea freight can take anywhere from a few weeks to several months for delivery.
Alternatively, air freight is a faster shipping option, albeit more expensive. It is suitable for urgent orders or smaller shipments since it offers faster delivery times. Air freight costs are calculated based on the weight or volume weight of the cargo, whichever is higher. Transit time by air is generally between a few days to a week.
Apart from the shipping method, other factors can contribute to the total shipping cost. These include packaging materials, insurance, customs duties or taxes, and any additional services required, such as customs clearance or inland transportation from the port to the final destination.
To estimate the shipping costs accurately, it is essential to provide detailed information about the shipment, including the dimensions, weight, and shipping requirements. It is also advisable to consult a freight forwarder or logistics company experienced in importing from China. They can provide guidance on the most suitable shipping method and help negotiate the best rates.
In conclusion, when importing CNC machining services from China, the shipping cost will depend on factors such as the weight and volume of the shipment, the chosen shipping method, and additional services or fees. Careful planning, accurate information, and collaboration with a reliable logistics partner will ensure a smooth and cost-effective import process.
Compare China and Other how does cnc machining work Markets: Products Quality and Price,Visible and Hidden Costs
China is known as the world’s largest manufacturing powerhouse, offering a wide range of products across various industries, including the CNC machining market. Comparing China to other markets in terms of product quality and price, as well as visible and hidden costs, provides insight into the advantages and disadvantages of sourcing from each market.
Product Quality and Price:
China has established a reputation for offering competitive prices in the CNC machining market. Due to its large manufacturing capacity and lower labor costs, products from China tend to have a price advantage over other markets, particularly in mass production. However, product quality can vary significantly, with some Chinese manufacturers offering high-quality components while others produce subpar products. This disparity makes it crucial for buyers to carefully research and evaluate potential suppliers’ track record, certifications, and customer reviews to ensure satisfactory quality.
Visible and Hidden Costs:
Visible costs in China include the cost of the product itself, shipping fees, and import duties. China’s dense manufacturing network and well-developed logistics infrastructure facilitate cost-effective transportation options. However, hidden costs such as intellectual property (IP) risks, quality control expenses, and potential supply chain disruptions should also be considered. Intellectual property theft is a concern in China, and companies need to invest in measures to protect their designs and proprietary information. Furthermore, additional expenses might arise from the need to have quality control inspectors on-site or frequent visits to ensure consistent product quality.
Comparisons:
When comparing China to other markets, the value proposition primarily lies in its competitive pricing. However, countries with developed manufacturing industries, such as Japan or Germany, often offer higher product quality at a higher price point. These markets might be more suitable for specialized or precision components, where quality and reliability are paramount.
It is important to note that other markets may also have hidden costs. For example, countries with higher labor costs might have increased manufacturing costs that are passed on to the buyer. Additionally, shipping costs and import duties could differ depending on the location of the buyer.
In conclusion, China’s CNC machining market offers competitive prices due to its manufacturing capability and lower labor costs. However, product quality can vary, necessitating thorough supplier vetting. Visible costs such as product price and shipping fees are relatively competitive, but hidden costs, such as IP risks and quality control, should not be disregarded. Comparing China to other markets reveals that factors such as product quality, specialization, and regional costs play a significant role in determining the best sourcing option for CNC machining products.
Understanding Pricing and Payment Terms for how does cnc machining work: A Comparative Guide to Get the Best Deal
CNC machining is a widely used manufacturing process that involves the use of computer-controlled machines to shape and cut various materials, such as metal, plastic, wood, and foam. It offers precise and efficient production capabilities, making it ideal for creating complex parts and components. When engaging in a CNC machining project, understanding pricing and payment terms is crucial to ensure you get the best deal. This comparative guide aims to provide essential insights into these aspects.
Pricing for CNC machining typically depends on several factors. Firstly, the complexity and size of the part significantly affect the cost. Intricate designs or larger parts may require more machining time and resources, leading to higher prices. Secondly, the material used also plays a role in pricing. Different materials have varying costs and may require specialized tools or techniques, impacting the overall expense. Additionally, batch size and quantity can influence pricing. Larger orders generally have lower per-unit costs, while small volume orders may incur setup fees.
To get the best deal possible, obtaining quotes from multiple CNC machining service providers is essential. By comparing prices and services offered, you can identify the most competitive options. However, it is crucial to consider other factors beyond pricing alone, such as the quality of service, lead times, and the provider’s reputation.
Payment terms vary between CNC machining service providers. Some may require a full payment upfront, especially for small orders or when dealing with new clients. However, reputable companies often offer flexible payment terms, such as a percentage upfront with the remainder upon completion. It is advisable to clarify payment terms before proceeding with any project to ensure alignment and avoid any unexpected financial complications.
In conclusion, understanding pricing and payment terms is crucial when engaging in CNC machining projects. Factors such as part complexity, material, and batch size all impact pricing, and obtaining multiple quotes from different providers is recommended. Payment terms can vary, so it is important to clarify them upfront to ensure a smooth transaction. By considering these aspects, you can make informed decisions and secure the best deal for your CNC machining needs.
Chinese Regulations and Industry Standards Certifications for how does cnc machining work,Import Regulations and Customs for how does cnc machining work from China
China has a comprehensive set of regulations and industry standards certifications to ensure the quality and safety of CNC machining processes. The most relevant certification for how CNC machining works is the ISO 9001 certification. This international standard focuses on quality management systems, requiring companies to establish and adhere to stringent quality control procedures throughout their manufacturing processes. CNC machining companies in China often obtain this certification to demonstrate their commitment to delivering high-quality products.
Additionally, the China Compulsory Certification (CCC) is essential for CNC machines imported from China. The CCC mark indicates that the product complies with national safety and quality standards. It is necessary to ensure that CNC machining equipment meets the country’s regulations regarding safety, electromagnetic compatibility, and environmental protection.
When importing CNC machining equipment from China, it is essential to comply with the country’s import regulations and customs procedures. First, importers need to understand the specific import requirements of their own country. This may involve obtaining import licenses, ensuring compliance with import restrictions or quotas, and paying applicable import duties and taxes.
It is necessary to ensure that the CNC machines adhere to local safety standards, as some countries may have additional safety requirements. Importers should also provide accurate labeling and packaging information in accordance with local regulations.
When importing CNC machining equipment from China, it is crucial to work with freight forwarders and customs brokers experienced in handling imports from China. These professionals can assist with the necessary paperwork, customs clearance, and ensure compliance with import regulations.
In summary, Chinese regulations and industry standards certifications ensure the quality and safety of CNC machining processes. The ISO 9001 certification demonstrates adherence to stringent quality control procedures, while the CCC mark indicates compliance with national safety and quality standards. Importing CNC machining equipment from China requires compliance with import regulations, knowledge of import requirements, and working with experienced freight forwarders and customs brokers.
Sustainability and Environmental Considerations in how does cnc machining work Manufacturing
CNC (Computer Numerical Control) machining is a modern manufacturing process that utilizes computer software to control machine tools and produce precise and complex parts. While CNC machining offers many benefits in terms of efficiency and accuracy, it is also important to consider its sustainability and environmental impact.
One major consideration in CNC machining is the choice of materials. Certain materials, such as aluminum and steel, require a significant amount of energy and emit greenhouse gases during their production. Opting for more sustainable alternatives, such as recycled or bio-based materials, can help reduce the environmental footprint of CNC machining. Additionally, proper material selection and optimization can minimize waste generation, saving both resources and costs.
Energy consumption is another aspect to consider. CNC machining equipment typically requires a substantial amount of electricity to operate. Implementing energy-efficient machines and optimizing the manufacturing process can help reduce energy consumption. Manufacturers can also explore the use of renewable energy sources, such as solar or wind power, to power their CNC machines, further reducing their carbon footprint.
Furthermore, waste management is critical in CNC machining. Precision machining often results in the generation of waste materials, such as metal shavings and chips. Proper collection, sorting, and recycling of these waste materials can help minimize the environmental impact. Implementation of closed-loop systems that recycle and reuse materials within the production process can also contribute to sustainability.
Water usage is also a consideration, primarily in CNC machining processes that involve cooling or lubricating fluids. Implementing water conservation strategies, such as recycling and reusing water, can minimize the demand for freshwater resources and the discharge of wastewater.
In conclusion, sustainability and environmental considerations should play a vital role in CNC machining manufacturing. Opting for sustainable materials, reducing energy consumption through efficient machines and renewable energy sources, implementing proper waste management, and conserving water resources are all important steps to minimize the environmental impact of CNC machining and ensure a sustainable manufacturing process.
List The Evolution history of “how does cnc machining work”
CNC (Computer Numerical Control) machining is a process that has gone through several stages of evolution over the years. This technology has revolutionized the manufacturing industry by increasing precision, efficiency, and automation. The following is a brief overview of the evolution history of CNC machining.
1. Early Numerical Control (NC) Machines: In the late 1940s and early 1950s, the first attempts at computer-controlled machines were made. These early NC machines utilized punched paper tapes or punched cards to store instructions for machining operations.
2. Introduction of Computers: With the advent of computers in the 1960s, further advancements were made, allowing for more complex machining operations. Computers enabled the storage of machining instructions in digital format, which increased reliability and flexibility.
3. CNC Machining Emerges: In the 1970s, CNC machining as we know it today started to take shape. The integration of computers with machine tools led to the development of more capable CNC machines. These machines were capable of executing complex instructions, storing and retrieving programs, and performing repetitive tasks with a high degree of accuracy.
4. CAD/CAM Integration: In the 1980s, computer-aided design (CAD) and computer-aided manufacturing (CAM) technologies were integrated with CNC machines. This integration allowed for the generation of machining programs directly from digital designs, increasing efficiency and reducing errors.
5. Multi-Axis Machining: As the demand for more complex parts increased, CNC machines evolved to incorporate multiple axes of movement. This enabled the machining of intricate shapes and contours that were previously difficult or impossible to achieve.
6. High-Speed Machining: In the 2000s, the focus shifted towards achieving higher machining speeds while maintaining accuracy. CNC machines were equipped with advanced tooling, spindles, and control systems to allow for faster material removal rates.
7. Automation and Robotics: The latest trend in CNC machining is the integration of automation and robotics. This allows for unmanned operation, increased productivity, and reduced labor costs. Robots can load and unload workpieces, change tools, and perform quality control inspections.
In summary, the evolution of CNC machining has progressed from early numerical control machines to highly advanced and automated systems today. The combination of computer technology, CAD/CAM integration, multi-axis capability, high-speed machining, and automation has significantly improved the efficiency and precision of manufacturing processes.
The Evolution and Market Trends in how does cnc machining work Industry
CNC machining, or computer numerical control machining, refers to a manufacturing process where pre-programmed computer software directs the movement of tools and machinery. This precise technology has greatly evolved since its inception, leading to significant market trends.
In the early days, CNC machining involved the use of punched tapes to control machine movements. This method was slow and limited in its capabilities. However, advancements in computer technology allowed for the development of more sophisticated control systems that improved precision and speed. Additionally, the use of graphical software interfaces made it easier for operators to program and control CNC machines.
One major evolution in CNC machining is the introduction of multi-axis machines. Initially, CNC machines were limited to three axes of movement, which restricted the complexity of the shapes that could be produced. However, with the advent of multi-axis machines, manufacturers could achieve more intricate geometries and produce parts with higher tolerance levels. This has opened up new possibilities for industries such as aerospace, automotive, and medical, where intricate and complex components are required.
Another significant trend in the CNC machining industry is the integration of automation and robotics. Automation allows for continuous operation, reduces human error, and enhances productivity. For instance, robotic arms can load and unload workpieces, minimizing downtime and improving efficiency. This integration of automation and CNC machining has led to lights-out manufacturing, where manufacturing processes can run 24/7 without human intervention.
The market trends in the CNC machining industry reflect the demand for precision, efficiency, and cost-effectiveness. As industries require more complex and intricate parts, the need for advanced CNC machining capabilities, such as multi-axis machines, continues to grow. Additionally, the integration of automation and robotics allows for increased productivity and reduced labor costs.
Furthermore, advancements in CNC machining technology have made it more accessible to small and medium-sized enterprises (SMEs). Lower equipment costs and easier programming interfaces have allowed SMEs to adopt CNC machining as a viable manufacturing solution, further driving market growth.
In conclusion, the evolution of CNC machining has led to significant market trends, including the development of multi-axis machines and the integration of automation and robotics. These advancements address the increasing demand for precision, efficiency, and cost-effectiveness in various industries. Moreover, CNC machining is becoming more accessible to SMEs, driving market growth and expansion.
Custom Private Labeling and Branding Opportunities with Chinese how does cnc machining work Manufacturers
CNC machining is a manufacturing process that utilizes computer numerical control (CNC) technology to produce custom-made parts and products. It involves the use of computer-aided design (CAD) software to create a digital model of the desired object, which is then translated into instructions that control the movement of precision machining tools.
Chinese manufacturers offer custom private labeling and branding opportunities by leveraging their expertise in CNC machining. With their advanced facilities and skilled workforce, they can produce high-quality products to meet specific requirements and enable businesses to establish their own brand identity.
The process involves various steps. Firstly, the CAD model or design is created, specifying the dimensions, shape, and features of the desired product. This digital design is then converted into a format that CNC machines can understand. The CNC machine is programmed with these instructions, including the tool paths, cutting speeds, feed rates, and any other parameters necessary for machining.
The machinist or operator then loads the chosen material into the CNC machine, such as metal, plastic, or wood, depending on the requirements. The CNC machine precisely guides the cutting tools, such as drills, lathes, or mills, based on the programmed instructions. This ensures that the material is accurately cut, shaped, or engraved to match the desired design, maintaining tight tolerances and high precision.
Chinese manufacturers have extensive experience in CNC machining and can efficiently manufacture products in bulk quantities while maintaining consistency and quality. They are capable of working with a wide range of materials, including metals like aluminum, stainless steel, and titanium, as well as plastics and composites. This versatility allows for the production of diverse products, from automotive parts and aerospace components to electronic enclosures and consumer goods.
By collaborating with Chinese manufacturers, businesses can take advantage of their cost-effective production capabilities and access a vast range of machinery and equipment. Additionally, Chinese manufacturers offer private labeling and branding opportunities by allowing businesses to customize the products with their logos, packaging, and other branding elements.
In conclusion, Chinese manufacturers specialize in CNC machining and provide custom private labeling and branding opportunities. With their expertise, advanced facilities, and cost-effective production capabilities, they can produce high-quality products that meet specific requirements. This enables businesses to establish their own brand identity and access a wide range of customized products.
Tips for Procurement and Considerations when Purchasing how does cnc machining work
Procurement is the process of acquiring goods or services from an external source, and when it comes to purchasing CNC (Computer Numerical Control) machining services, there are several important considerations. CNC machining is a manufacturing process that utilizes pre-programmed computer software to control the movement of machinery and tools. Here are some tips for procurement and key considerations when purchasing CNC machining services:
1. Identify your specific needs: Before purchasing CNC machining services, determine your specific requirements such as the type of material, the size and complexity of the parts, and the desired turnaround time. This will help you find a supplier that can cater to your unique needs.
2. Quality and expertise: Look for a supplier with a proven track record of delivering high-quality CNC machined parts. Consider their experience, reputation, and industry certifications. Evaluate their capabilities in terms of precision, accuracy, and their ability to work with different materials.
3. Cost-effectiveness: Compare prices from different suppliers, but be cautious of extremely low-cost options as they may compromise on quality. Focus on finding a balance between price and quality. Suppliers that offer competitive pricing and value-added services can provide better cost-effectiveness.
4. Capacity and lead time: Evaluate the supplier’s production capacity and their ability to meet your required lead time. CNC machining services with a faster turnaround time and flexibility in handling changing demands can be advantageous for your procurement needs.
5. Communication and collaboration: Effective communication with the supplier is crucial for successful procurement. Ensure that they are responsive and proactive in addressing your queries and concerns. A supplier that values collaboration can help in optimizing designs and ensuring smooth project execution.
6. Quality control and inspection process: Inquire about the supplier’s quality control measures and inspection processes. A reputable supplier should have comprehensive quality assurance protocols in place to ensure the dimensional accuracy, surface finish, and overall quality of the CNC machined parts.
7. Intellectual property protection: If your products or designs are proprietary or have intellectual property considerations, discuss confidentiality and non-disclosure agreements with the supplier to safeguard your information.
In conclusion, when purchasing CNC machining services, consider your specific needs, evaluate suppliers based on their quality, cost-effectiveness, capacity, and lead time, prioritize effective communication and collaboration, understand their quality control processes, and ensure the protection of your intellectual property. These considerations will aid in making an informed procurement decision and ensure successful outcomes from CNC machining operations.
FAQs on Sourcing and Manufacturing how does cnc machining work in China
CNC machining, also known as Computer Numerical Control machining, is a manufacturing process that utilizes pre-programmed computer software to control the movement of machinery and tools. In China, CNC machining has gained immense popularity due to its efficiency, precision, and cost-effectiveness.
The process begins with a CAD (Computer-Aided Design) model, which is fed into the CNC machine’s computer. The machine then interprets the design and generates a path that the cutting tools will follow. This path is based on the specific instructions provided in the CAD model.
The CNC machine consists of various components, such as a spindle, cutting tools, and a workpiece. The spindle rotates the cutting tools, which methodically carve away material from the workpiece to create the desired shape or design. The machine’s computer precisely controls the movement of the tools, ensuring high accuracy.
China has become a preferred destination for CNC machining due to its large number of skilled technicians, advanced manufacturing facilities, and competitive pricing. Numerous Chinese manufacturers offer CNC machining services with capabilities to handle different materials, such as metals, plastics, and composites.
The Chinese CNC machining industry maintains strict quality control measures to ensure the precision and reliability of the manufactured components. Many facilities also utilize advanced inspection equipment, such as coordinate measuring machines (CMMs), to verify the accuracy of the finished products.
When sourcing CNC machining services in China, it is crucial to consider factors like the supplier’s experience, the range of offered services, and their ability to meet specific customer requirements. Communication is key to ensure that the design specifications are understood, and any necessary modifications or adjustments can be made before production.
To summarize, CNC machining in China involves the use of computer-controlled machinery to precisely manufacture components based on CAD designs. This process offers numerous benefits including high accuracy, cost-effectiveness, and efficient production. By selecting a reputable manufacturer in China, businesses can take advantage of skilled labor and advanced manufacturing capabilities to obtain quality CNC machined products.
Why contact sourcifychina.com get free quota from reliable how does cnc machining work suppliers?
Sourceifychina.com offers a free quota from reliable CNC machining suppliers because of the strong relationships it has established with these suppliers. The platform acts as a trusted intermediary between manufacturers in China and international businesses looking to source products.
To understand how CNC machining works, it is important to know that CNC stands for Computer Numerical Control. This manufacturing process involves the use of computer-controlled machines to produce precise and intricate parts or products from raw materials. The process starts with a design created using computer-aided design (CAD) software.
Once the design is ready, it is converted into a set of instructions that the CNC machine can understand. These instructions, known as G-code, define the specific movements and operations required to create the desired part. The G-code is then fed into the CNC machine’s control unit.
The machine consists of various tools and cutting implements that are controlled by motors and actuators. These tools are moved across the raw material, such as metal or plastic, based on the instructions in the G-code. The cutting implements remove material, shape the part, and create the desired features.
Throughout the machining process, sensors and feedback mechanisms ensure that the machine operates accurately, maintaining tight tolerances and producing high-quality parts. The CNC machine can perform a variety of operations, including milling, turning, drilling, and grinding, depending on the specific requirements of the design.
By partnering with reliable CNC machining suppliers, sourcifychina.com can offer its users a free quota of sourcing projects. This allows businesses to submit their product requirements and receive quotations for the manufacturing process from trusted suppliers. The platform’s strong relationships with these suppliers ensure that the quotations provided are competitive and reliable.
In conclusion, sourcifychina.com obtains a free quota from reliable CNC machining suppliers due to its established relationships. CNC machining involves using computer-controlled machines to produce precise parts, and sourcifychina.com acts as an intermediary between manufacturers and businesses looking to source products. By partnering with trusted suppliers, the platform offers users a free quota for sourcing projects, ensuring competitive and reliable quotations.