Introduce about injection mould design guide,Qulity,Cost,Supplier,Certification,Market,Tips,FAQ
Injection mould design is a crucial aspect of the manufacturing process. A well-designed mould ensures quality products, cost-efficient production, and a reliable supplier. This guide will provide essential information about injection mould design, certification requirements, market trends, and some useful tips.
The primary objective of injection mould design is to produce high-quality moulds that result in flawless products. It involves careful consideration of factors like material selection, part design, gate location, cooling system, and ejection mechanism. By focusing on these elements, designers can minimize defects and enhance the overall product quality.
Cost plays a vital role in injection mould design. A cost-effective design will not only reduce manufacturing expenses but also boost profitability. Optimizing the number and complexity of mould cavities, using the right materials, and maximizing production efficiency are essential steps to achieve cost-effectiveness.
Choosing a reliable supplier is crucial for successful injection mould production. It is essential to select a supplier with experience, expertise, and a proven track record. Evaluating past projects, client testimonials, and facility capabilities will help ensure the best supplier for your needs.
Certification is a crucial aspect of injection mould design, especially in industries with strict regulations. Certified moulds comply with specific quality and safety standards, ensuring that products meet industry and customer requirements. ISO certifications, such as ISO 9001, are commonly sought after to guarantee reliability and consistency in manufacturing processes.
The injection mould market continues to grow due to the increasing demand for plastic products across various industries. Automotive, packaging, electronics, and consumer goods sectors are among the major contributors to this market’s growth. Staying updated with market trends and innovations is vital for designers and manufacturers to remain competitive.
Here are some tips to enhance injection mould design: consider manufacturability during the design phase, communicate effectively with suppliers and stakeholders, incorporate standard components to minimize costs, and continuously improve the design by learning from previous projects.
Frequently Asked Questions (FAQs):
1. What is injection mould design?
2. How does injection mould design affect product quality?
3. How can I reduce manufacturing costs through mould design?
4. What certifications are important for injection mould design?
5. Which industries drive the growth of the injection mould market?
In conclusion, injection mould design is a critical aspect of the manufacturing process. By ensuring quality, cost-effectiveness, reliable suppliers, and necessary certifications, businesses can thrive in the competitive market. Keeping up with market trends and adopting helpful design tips will further enhance the success of injection moulding projects.
Types of injection mould design
Injection mould design is the process of creating the blueprint for manufacturing a plastic product using injection moulding technology. There are several types of injection mould designs, each with its own advantages and applications.
1. Two-plate mould: This is the simplest and most common type of injection mould design. It consists of two plates – the cavity plate and the core plate – that come together to form the mould cavity. The plastic material is injected into the cavity through a sprue and runner system. Two-plate moulds are used for products with simple geometries and are generally cost-effective and easy to manufacture.
2. Three-plate mould: Three-plate moulds are used for more complex products that require additional features like side-actions or undercuts. They consist of three plates: the cavity plate, the core plate, and the runner plate. The runner plate contains channels for the plastic material to flow into the cavity and can move independently to release the product without causing any damage.
3. Hot runner mould: In hot runner moulds, the plastic material is injected directly into the cavity through a heated manifold system, eliminating the need for a runner system. This results in reduced material wastage, shorter cycle times, and improved product quality. Hot runner moulds are commonly used for high-volume production and complex parts that require precise control of the material flow.
4. Insert moulding: This type of mould design allows for the encapsulation of pre-formed inserts or components within the injected plastic. It is commonly used when additional strength or functionality is required, such as with electrical connectors or threaded inserts. The insert is placed in the mould cavity, and the plastic material flows around it during the injection process.
5. Overmoulding: Overmoulding involves encapsulating a pre-formed component with a second material during the injection moulding process. It is commonly used to add a soft-touch grip or to combine different materials with different properties in a single product. Overmoulding requires precise alignment of the two mould halves to ensure the component is correctly encapsulated.
In conclusion, injection mould design encompasses various types, each tailored to meet the specific requirements of the product being manufactured. Whether it is a simple two-plate mould or a complex hot runner mould, choosing the appropriate design is essential to achieve optimal product quality, cost efficiency, and manufacturing ease.
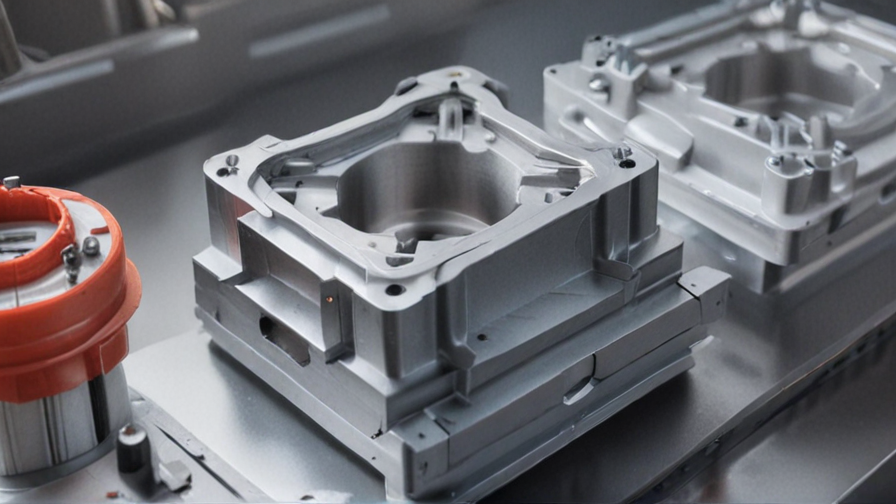
Pros and Cons of Using injection mould design
Injection mould design is a popular method used in manufacturing to produce large quantities of identical parts with precise dimensions. It involves injecting molten material into a mould cavity and allowing it to cool, solidify, and take the shape of the mould. While injection mould design offers several advantages, it also entails certain drawbacks. Here are some pros and cons of using injection mould design:
Pros:
1. Cost-effective production: Injection moulding is a cost-effective solution for high-volume production. The process allows for quick production cycles, reduced labour costs, and minimal scrap material.
2. Design flexibility: Injection moulding permits complex and intricate designs to be mass-produced with high precision. It offers design flexibility, allowing for the incorporation of various geometries, undercuts, and threads.
3. High productivity: Injection moulding enables machines to produce parts continuously with minimal human intervention. This results in high production rates and increased productivity.
4. Wide material selection: Injection moulding supports a vast range of materials, including thermoplastics, thermosetting plastics, elastomers, and metals, allowing manufacturers to choose the most suitable material for their application.
5. Excellent surface finish: Injection moulding provides parts with a smooth and polished surface finish, reducing the need for additional post-processing operations.
Cons:
1. High initial tooling cost: The cost of designing and manufacturing injection moulding tools can be significant, especially for intricate and complex designs. This high upfront investment may make the process less viable for small-scale production runs.
2. Long lead times: Developing custom injection moulding tools can take weeks or even months. This long lead time may cause delays in production and flexibility for design changes.
3. Limited part size and geometry: Injection moulding has limitations when it comes to producing large-sized or extremely complex parts. The geometry of the part should allow for easy ejection from the mould and uniform filling of the material.
4. Material limitations: While there is a wide selection of materials available for injection moulding, some materials may not be suitable due to their poor flow characteristics, high melting points, or high material costs.
5. Not environmentally friendly: Injection moulding produces a lot of plastic waste, and the disposal of excess material and defective parts can contribute to environmental pollution. However, efforts are being made to recycle and reuse plastic waste generated from injection moulding processes.
In summary, injection mould design offers numerous advantages, such as cost-effectiveness, design flexibility, high productivity, material selection, and excellent surface finish. However, it is important to consider the high initial tooling cost, long lead times, limited part size and geometry, material limitations, and environmental concerns when opting for this manufacturing method.
injection mould design Reference Specifications (varies for different product)
Reference Specifications for Injection Mold Design:
1. Material Selection:
The choice of material for the injection mold depends on the specific product requirements such as strength, durability, and resistance to temperature and chemicals. Commonly used materials include steel alloys, aluminum alloys, and high-density polyethylene (HDPE).
2. Mold Construction:
The mold design should consider factors like the number of cavities required, gate placement, and ejection system. Parting lines, draft angles, and surface finishes should be incorporated to ensure easy release of the molded product without any defects.
3. Cooling System:
Efficient cooling is crucial for maintaining part quality and reducing cycle time. The mold design should include cooling channels strategically placed to ensure uniform cooling throughout the mold. The use of conformal cooling, where the channels closely follow the contours of the part, can improve cooling efficiency.
4. Venting:
To prevent trapped air or gases during injection molding, proper venting design is essential. The mold should include venting channels or porous venting inserts to allow the escape of air, minimizing the risk of air pockets or blemishes on the molded product.
5. Gate Design:
The gate is the entrance point for the molten material into the mold cavity. The gate design should be optimized to minimize pressure drop and shear stress, ensuring smooth flow and preventing defects like flow marks and weld lines. Common gate designs include sprue, edge, and pin gates.
6. Mold Maintenance:
Considerations for mold maintenance should be incorporated into the design. This includes features like easy disassembly, access to critical components, and replaceable inserts. Proper maintenance will extend the mold’s lifespan and ensure consistent product quality.
7. Mold Flow Analysis:
Performing mold flow analysis using simulation software can help optimize the mold design by predicting potential issues like fill imbalances, air traps, and cooling inefficiencies. This analysis allows for adjustments to be made before manufacturing the mold, reducing time and costs.
8. Mold Testing and Validation:
After manufacturing, the mold should undergo rigorous testing to ensure its functionality, accuracy, and reliability. This includes conducting trial runs, inspecting samples for defects, and making any necessary adjustments before full-scale production.
By following these reference specifications, the injection mold design can be optimized for each specific product, leading to efficient manufacturing processes and high-quality end products.
Applications of injection mould design
Injection mold design is a critical aspect of the manufacturing process for various industries, as it allows for the mass production of high-quality, complex plastic parts. The following are some key applications of injection mold design:
1. Automotive Industry: Injection molded parts are widely used in the automotive sector for the production of various components, including interior and exterior trims, dashboard elements, door handles, bumpers, and engine parts. The ability to produce these parts in large volumes, with high precision and repeatability, makes injection molding a preferred method in the automotive industry.
2. Consumer Electronics: Injection mold design finds extensive use in the production of consumer electronics, such as mobile phones, tablets, laptops, and audio devices. It enables the manufacture of custom-designed enclosures and housing, ensuring a perfect fit for the electronic components while maintaining aesthetic appeal.
3. Medical Devices: Injection molding is crucial in the medical field for the fabrication of disposable and reusable medical devices. These include syringes, blood collection tubes, IV connectors, surgical tools, and diagnostic equipment. Injection molding ensures the production of medical devices that meet the industry’s stringent quality and regulatory standards.
4. Packaging Industry: Injection mold design is heavily utilized in the packaging industry for producing containers, bottles, caps, and closures. It allows for the manufacturing of lightweight, durable, and visually appealing packaging solutions for various consumer products, ranging from food and beverages to personal care items.
5. Industrial Equipment: Injection molding is employed to create components and parts used in the industrial sector. These can range from small gears, brackets, and knobs to large machine enclosures. The design flexibility and cost-effectiveness of injection molding make it an ideal choice for producing such industrial equipment.
6. Household Products: Many household items, including kitchenware, storage containers, toys, and furniture components, are manufactured using injection mold design. It enables the production of aesthetically pleasing and durable products that cater to the needs of everyday life.
In conclusion, injection mold design offers diverse applications in numerous industries, enabling the mass production of high-quality plastic parts with complex geometries. This method benefits industries ranging from automotive and consumer electronics to medical devices, packaging, industrial equipment, and household products. The versatility and efficiency of injection molding make it an indispensable manufacturing technique for a wide range of products.
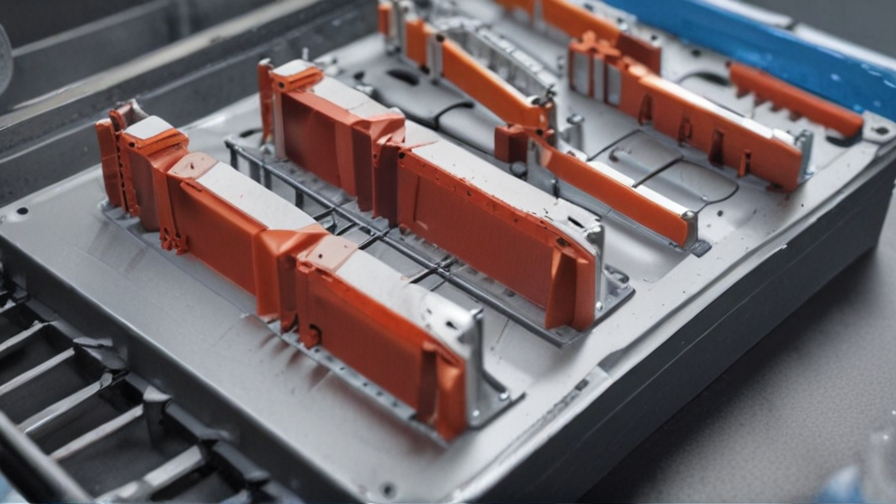
The Work Process and how to use injection mould design
The work process of injection mould design involves several steps that need to be followed in order to ensure an efficient and effective design. Here is a brief overview of the process:
1. Product Design: The first step is to have a clear understanding of the product requirements and design specifications. This includes considering factors such as product functionality, material selection, and part geometry.
2. Mold Design: Once the product design is finalized, the next step is to develop a mold design. This involves determining the number of cavities required, selecting the appropriate mold base, and designing the runner system and cooling channels.
3. Material Selection: The choice of material for the mold is crucial, as it should be able to withstand high temperatures and pressures without warping or deforming. Common materials used for injection molds include steel and aluminum alloys.
4. Mold Manufacturing: After the mold design is complete, it needs to be manufactured. This involves machining the mold components, such as the cavity and core, and assembling them into a complete mold.
5. Injection Molding Process: Once the mold is ready, it can be used for the actual injection molding process. This involves injecting molten plastic material into the mold cavity under high pressure. The material then solidifies and takes the shape of the mold.
6. Post-processing: After the injected part is cooled and solidified, it needs to be removed from the mold. This may require additional processes such as trimming and finishing to remove any excess material or improve the surface finish.
To ensure successful injection mould design, several factors need to be considered. These include part design optimization to minimize manufacturing issues, proper selection of mold materials and construction techniques, and effective cooling channel design to ensure uniform cooling and reduce cycle time.
Additionally, using CAD software can greatly aid in the design process, as it allows for accurate modeling and simulation of the mold design. This helps in identifying and rectifying any potential issues before the actual manufacturing process.
In conclusion, the work process of injection mould design involves product and mold design, material selection, mold manufacturing, injection molding, and post-processing. Following this process and considering various factors can help in achieving an efficient and successful injection mold design.
Quality Testing Methods for injection mould design and how to control the quality
Quality testing methods for injection mould design include the use of computer-aided design (CAD) software, prototyping, simulation, and mechanical testing. These methods help in identifying potential issues and ensuring that the mould design meets the required standards.
CAD software is extensively used in the initial stage of mould design. It allows designers to create a virtual model of the mould, enabling them to analyze various factors such as part geometry, draft angles, wall thickness, and gate locations. This helps in identifying potential manufacturing and mouldability issues before the mould is actually built.
Prototyping is another important quality testing method for injection mould design. It involves creating a physical model of the part using 3D printing or machining techniques. By evaluating the prototype, designers can ensure that the mould design is accurate and meets the desired specifications. Any design flaws or functional issues can be identified and corrected at this stage.
Simulation software is also employed for quality testing. It enables designers to simulate the injection moulding process virtually. By replicating the actual manufacturing conditions, they can analyze factors like fill time, pressure, temperature, and cooling rate. This helps in identifying potential defects like sink marks, warpage, or air traps in the final molded part. Design modifications can be made based on simulation results to optimize the mould design.
Mechanical testing is performed on the final molded parts to ensure their quality and functionality. This includes tests like dimensional accuracy measurement, tensile strength testing, impact resistance testing, and hardness testing. These tests validate the mould design and guarantee that the final product meets the required standards.
To control the quality of injection mould design, several measures can be taken. Regular design reviews should be conducted to ensure compliance with the desired specifications. Additionally, close collaboration between designers, engineers, and manufacturers throughout the design process is important to identify and address any potential issues. Proper communication and documentation of design changes are crucial to maintain control and ensure consistency. Clear quality standards and guidelines should be established and followed. Regular inspection and monitoring of the mould manufacturing process help in identifying any deviations and taking corrective actions. Continuous improvement initiatives based on feedback from manufacturing and end-users contribute to maintaining and improving the quality of injection mould design.
injection mould design Sample Policy and Post-Purchase Considerations for injection mould design from China
Sample Policy:
1. Quality Assurance: Ensure that the injection mold design meets all specified requirements and industry standards before proceeding with production. The supplier should provide detailed design drawings, 3D models, and mold flow analysis reports for approval.
2. Prototype Testing: Request the supplier to provide a prototype of the injection mold for initial testing and evaluation. This will help identify any design flaws or functional issues before mass production.
3. Modification and Iterations: If any modifications are required after prototype testing, clearly define the scope of changes and ensure that the supplier has the capability and willingness to accommodate these revisions.
4. Intellectual Property Protection: Address intellectual property concerns by signing a non-disclosure agreement (NDA) with the supplier. Additionally, include a clause in the contract that grants you exclusive rights to the injection mold design.
5. Pricing and Payment Terms: Clearly define the pricing structure, including tooling costs, design fees, and subsequent modification charges. Negotiate favorable payment terms such as a down payment, milestone payments, or installment payments based on specific project milestones.
Post-Purchase Considerations:
1. Quality Control: Conduct a thorough inspection of the injected molded parts produced using the acquired mold design. Ensure that the final product meets the desired specifications and international quality standards.
2. Continuous Improvement: Establish a feedback mechanism with the supplier to report any defects or areas for improvement observed during production. Encourage the supplier to implement corrective measures to enhance product quality and mold performance.
3. Spare Parts and Maintenance: Discuss spare part availability and maintenance requirements with the supplier. Ensure that proper documentation and instructions are provided to carry out routine maintenance and repairs as needed.
4. Warranty and Service Support: Establish a warranty period for the mold design, covering any defects or failures that may occur during normal usage. Discuss post-sales service support, including technical assistance, repairs, or replacements if necessary.
5. Partnership Development: Evaluate the supplier’s performance and consider exploring long-term partnerships with reliable and experienced injection mold design manufacturers. Building a strong relationship can lead to seamless communication, cost savings, and improved quality control.
By carefully considering these policies and post-purchase considerations when dealing with injection mold design manufacturers from China, you can reduce risks, ensure product quality, and establish a successful business relationship.
Sourcing injection mould design from China: Opportunities, Risks, and Key Players
Sourcing injection mold design from China presents a range of opportunities, along with associated risks, while engaging with key players in the industry.
Opportunities:
1. Cost Efficiency: China’s injection mold design industry offers competitive pricing compared to other global counterparts. This cost advantage can significantly reduce manufacturing expenses, making it an attractive option for businesses seeking cost efficiency.
2. Vast Experience and Expertise: China has a long-standing history in the field of injection mold design, resulting in a large pool of experienced and skilled professionals. These experts possess in-depth knowledge and have honed their skills over the years, ensuring high-quality designs.
3. Fast Turnaround Time: With efficient production processes and large-scale manufacturing capabilities, Chinese companies can provide quicker turnaround times for injection mold designs. This agility allows businesses to streamline their production cycles and bring products to market faster.
Risks:
1. Quality Control: Maintaining quality control standards can be challenging while sourcing injection mold design from China. Due diligence is required to ensure that the manufacturer adheres to international quality standards and has the necessary certifications and quality control processes in place.
2. Intellectual Property (IP) Protection: China has faced concerns regarding IP protection. There have been instances of design theft and the unauthorized use of proprietary technology. Businesses must establish clear contracts and agreements with Chinese manufacturers to protect their intellectual property rights.
3. Communication and Language Barriers: Effective communication is crucial for successful implementation of injection mold design projects. Language barriers and cultural differences may hinder clear communication, leading to misunderstandings and delays. Engaging with local representatives or translators can help overcome these challenges.
Key Players:
1. Foxconn Technology Group: As one of the largest electronics manufacturers in the world, Foxconn provides a range of services, including injection mold design. They have extensive experience in the industry and a solid track record.
2. Shenzhen Donghua Precision Mold Co., Ltd: This company specializes in precision mold design and manufacturing. With an emphasis on quality control and advanced technology, they have established themselves as a key player in the market.
3. Shanghai Sourcing International Trading Co., Ltd: This company focuses on sourcing and supplying injection mold designs from China. They serve as a bridge between international businesses and Chinese manufacturers, facilitating smooth transactions.
In conclusion, sourcing injection mold design from China offers opportunities for cost efficiency, access to experienced professionals, and faster turnaround times. However, businesses must be cautious of quality control and intellectual property risks while engaging with key players in the industry. Effective communication strategies can help overcome language barriers and ensure successful project implementation.
How to find and select reliable injection mould design manufacturers in China,use google search manufacturers and suppliers
Finding and selecting reliable injection mold design manufacturers in China can be a daunting task, but with the help of Google search and an effective evaluation process, you can narrow down your options. Here are some steps to follow:
1. Use relevant keywords: Start by searching for “reliable injection mold design manufacturers in China” or similar keywords on Google. This will provide you with a list of potential suppliers.
2. Evaluate the company’s website: Visit the websites of these manufacturers to gather information about their services, capabilities, certifications, and experience. Look for details regarding their injection mold design expertise, manufacturing facilities, quality control procedures, and customer reviews.
3. Check for certifications and standards: Determine if the manufacturers have relevant certifications such as ISO 9001:2015, ISO 13485 (for medical devices), or ISO/TS 16949 (for automotive industry). These certifications indicate that the manufacturer follows strict quality and manufacturing standards.
4. Assess their experience and specialization: Look for manufacturers that have extensive experience in injection mold design and production. They should have a portfolio of successful projects and expertise in producing molds for your specific industry or product.
5. Request samples or case studies: Ask the shortlisted manufacturers to provide examples of their previous work, such as sample products or case studies. This will allow you to evaluate the quality, precision, and complexity of their injection mold designs.
6. Communication and responsiveness: Contact the manufacturers and assess their responsiveness. Prompt and clear communication is crucial for successful collaboration. Inquire about their design process, mold modification capabilities, project management, and timelines.
7. Quality control and inspection: Understand the manufacturer’s quality control procedures, including their in-house inspection and testing capabilities. Reliable manufacturers ensure strict adherence to quality standards throughout the production process.
8. Obtain quotes and compare prices: Request detailed quotations from the remaining manufacturers. Evaluate the pricing structure, payment terms, tooling costs, and any additional charges. Be cautious of significantly lower prices, as they may indicate compromises in quality.
9. Get recommendations and validate reliability: Seek recommendations from industry experts or networks, and check if the manufacturers have positive reviews or testimonials from their previous clients. This can give you further insights into their reliability.
10. Request a visit or audit: If possible, plan a visit to the manufacturer’s facility or conduct an audit to assess their capabilities, work environment, and manufacturing processes.
By following these steps and conducting thorough research, you can find and select reliable injection mold design manufacturers in China that meet your requirements.
How to check injection mould design manufacturers website reliable,use google chrome SEOquake check if ranking in top 10M
To check if an injection mould design manufacturer’s website is reliable, you can follow these steps:
1. Use Google Chrome: Open the website using the Google Chrome browser. Chrome offers various tools and extensions that can help evaluate the reliability and credibility of a website.
2. Install SEOquake: Install the SEOquake extension on your Google Chrome browser. SEOquake is a powerful tool that provides important metrics and insights about a website’s search engine optimization (SEO). It can help you evaluate the website’s performance, visibility, and credibility.
3. Check the Google Search Ranking: Once SEOquake is installed, go to the manufacturer’s website and activate the extension by clicking on the SEOquake icon in your browser’s toolbar. From the dropdown menu, select “Parameters.” This will display various SEO metrics for the website.
4. Review Ranking Metrics: Pay attention to the website’s Alexa Rank, which indicates the site’s popularity and traffic. If the website has a ranking in the top 10 million, it generally suggests that it receives a decent amount of traffic and is recognized by search engines. This is a positive sign of reliability.
5. Evaluate Other Metrics: Explore other metrics provided by SEOquake, such as the number of indexed pages, backlink count, and social media presence. While these metrics do not directly determine reliability, they can provide additional insights into the website’s online presence and level of engagement.
6. Cross-Check Information: Verify the credibility and reputation of the manufacturer by looking for customer reviews, testimonials, and their presence on social media platforms. This information can help you gauge the reliability and professionalism of the company.
7. Consider Other Factors: While SEOquake can provide valuable insights, it is important to also consider other factors like the website’s design, user experience, and content quality. A reliable manufacturer website should have clear and detailed information about their services, product offerings, contact details, and policies.
By following these steps and using SEOquake, you can evaluate the reliability of an injection mould design manufacturer’s website in a quick and efficient manner. Remember to consider other factors beyond just the search ranking to form a comprehensive understanding of their credibility.
Top 10 injection mould design manufacturers in China with each 160 words introduce products,then use markdown create table compare
1. Mega Machinery Mold Co., Ltd:
Specializing in injection mold design and manufacturing, Mega Machinery Mold Co., Ltd has gained expertise in producing high-quality molds for various industries such as automotive, packaging, and consumer goods. Their product range includes precision molds, multi-cavity molds, and hot runner molds, all designed with precision and efficiency in mind. With a dedicated team of experienced designers and advanced equipment, Mega Machinery Mold ensures that their products meet the highest standards of quality.
2. Keyuan Industry Co., Ltd:
Keyuan Industry Co., Ltd is a renowned manufacturer of injection mold designs in China. They offer a wide range of products including precision injection molds, gas-assisted injection molds, and automotive molds. With advanced CAD/CAM software and CNC machining centers, Keyuan Industry is capable of delivering molds with high precision and efficiency. They also provide design optimization services to help customers improve product functionality and reduce manufacturing costs.
3. Aco Mold Co., Limited:
Aco Mold Co., Limited is a leading injection mold design manufacturer in China. With over 10 years of experience, they specialize in providing customized plastic injection molds for various industries such as electronics, medical, and automotive. Their product range includes multi-cavity molds, large-size molds, and hot runner molds, ensuring the best quality and cost-effectiveness for their clients. Aco Mold also offers design assistance and prototyping services to meet specific customer requirements.
4. Xiamen Qiqiangsheng Moulds Co., Ltd:
Xiamen Qiqiangsheng Moulds Co., Ltd is a well-known injection mold design manufacturer in China. They specialize in producing high-quality molds for industries like automotive, electronics, and household appliances. Their product range includes precision molds, multi-cavity molds, and hot runner molds, designed to meet the most demanding customer specifications. With a strong focus on quality and innovation, Xiamen Qiqiangsheng Moulds has gained a reputation for delivering superior mold design solutions.
5. Sino Mold Tooling Co., Ltd:
Sino Mold Tooling Co., Ltd is a leading injection mold design manufacturer based in China. They offer a wide range of mold design and manufacturing services for industries like automotive, medical, and consumer goods. With state-of-the-art facilities and experienced engineers, Sino Mold Tooling can deliver precision molds with high efficiency. Their product range includes multi-cavity molds, hot runner molds, and custom molds tailored to meet specific customer needs.
6. Shenzhen Tec-Shine Technology Co., Ltd:
Shenzhen Tec-Shine Technology Co., Ltd is a trusted manufacturer of injection mold designs in China. With an experienced team of designers and engineers, they specialize in producing precision molds for industries such as automotive, electronics, and aerospace. Their product range includes multi-cavity molds, unscrewing molds, and insert molds, designed to meet the highest quality standards. Shenzhen Tec-Shine Technology also offers value-added services like mold flow analysis and design optimization to ensure optimal performance.
7. Inno Molding Co., Ltd:
Inno Molding Co., Ltd is a reputable injection mold design manufacturer in China. They provide comprehensive mold design and manufacturing services for various industries including automotive, electronics, and medical. With advanced CAD/CAM software and CNC machining centers, Inno Molding can deliver precision molds with quick turnaround times. Their product range includes multi-cavity molds, two-shot molds, and hot runner molds, providing high quality and cost-effective solutions to their customers.
8. SINCERE TECH plastic mold company:
SINCERE TECH is a prominent injection mold design manufacturer based in China. They specialize in providing custom mold design and manufacturing services for industries such as automotive, electronics, and consumer goods. With advanced technology and a dedicated team of designers, SINCERE TECH can deliver high-quality molds that meet stringent customer requirements. Their product range includes multi-cavity molds, thin-wall molds, and stack molds, ensuring maximum efficiency and productivity.
9. HT Moulding Ltd:
HT Moulding Ltd is an established injection mold design manufacturer in China. They have extensive experience in producing molds for industries such as automotive, electrical appliances, and packaging. HT Moulding offers a wide range of mold design solutions, including multi-cavity molds, two-shot molds, and hot runner molds. With their commitment to innovation and quality, HT Moulding provides reliable and cost-effective mold design services to their global clientele.
10. Intertech Machinery Inc:
Intertech Machinery Inc is a leading injection mold design manufacturer in China, specializing in precision mold making and related services. They offer a diverse range of mold design solutions for industries like automotive, electronics, and medical. Intertech Machinery uses cutting-edge technology and advanced equipment to deliver high-quality molds with precise specifications. Their product range includes multi-cavity molds, insert molds, and unscrewing molds, providing comprehensive solutions for complex mold design requirements.
| Manufacturer | Product Range |
|————————–|————————————————-|
| Mega Machinery Mold Co. | Precision molds, multi-cavity molds, hot runner molds |
| Keyuan Industry Co. | Precision injection molds, gas-assisted molds, automotive molds |
| Aco Mold Co., Limited | Customized plastic injection molds |
| Xiamen Qiqiangsheng Moulds | Precision molds, multi-cavity molds, hot runner molds |
| Sino Mold Tooling Co. | Multi-cavity molds, hot runner molds, custom molds |
| Shenzhen Tec-Shine Technology Co. | Precision molds, unscrewing molds, insert molds |
| Inno Molding Co., Ltd | Multi-cavity molds, two-shot molds, hot runner molds |
| SINCERE TECH plastic mold company | Custom mold design and manufacturing |
| HT Moulding Ltd | Multi-cavity molds, two-shot molds, hot runner molds |
| Intertech Machinery Inc | Precision mold making, multi-cavity molds, insert molds |
In conclusion, these top 10 injection mold design manufacturers in China offer a wide range of products and services, catering to various industries. Each manufacturer has its unique specialties and expertise, delivering high-quality molds designed with precision and efficiency in mind. Customers can choose based on their specific requirements, such as mold type, industry focus, and customization options.
Background Research for injection mould design manufacturers Companies in China, use qcc.com archive.org importyeti.com
When it comes to injection mold design manufacturers in China, several resources can be utilized to gather background research. These resources include qcc.com, archive.org, and importyeti.com. Combined, they provide valuable information about the companies and their operations.
Qcc.com is a comprehensive business database that allows users to search for specific companies in China and obtain detailed information about their background, registration details, contact information, and more. This platform enables researchers to gather insights into the legal status, history, and ownership of potential injection mold design manufacturers.
Archive.org is a well-known digital archive that captures and stores copies of web pages over time. By searching for specific company websites or industry-related forums on Archive.org, researchers can access past versions of websites. This is useful for tracking a company’s evolution over time, including changes in product offerings, services, and overall reputation.
Importyeti.com is a global trade data platform that allows users to search and analyze import-export records. By inputting specific company names or keywords related to injection mold design manufacturing, researchers can obtain valuable insights, such as the types and quantities of products exported or imported, customer details, and shipping information. This data can provide an overview of a company’s international reach, customer base, and potential manufacturing capabilities.
In conclusion, qcc.com provides detailed company information, archive.org offers historical website data, and importyeti.com provides import-export records, offering comprehensive background research on injection mold design manufacturers in China. Utilizing these resources, researchers can gain insights into a company’s history, operations, and international reach, aiding in decision-making and finding reliable manufacturing partners.
Leveraging Trade Shows and Expos for injection mould design Sourcing in China
Trade shows and expos can be valuable platforms for sourcing injection mold design in China. These events bring together suppliers, manufacturers, and industry professionals, providing an opportunity to explore a wide range of options and make informed decisions. By leveraging trade shows and expos, businesses can benefit from the following:
1. Networking and connections: Trade shows and expos attract a diverse range of industry players, including injection mold designers and manufacturers. This allows businesses to establish valuable connections, meet potential suppliers, and gain insights into the latest industry trends and technologies.
2. Direct interaction with suppliers: Trade shows and expos offer an ideal setting for face-to-face discussions with suppliers. This allows businesses to communicate their requirements, negotiate terms, and assess the capabilities and quality of different injection mold design providers. Direct interaction also fosters trust and provides an opportunity to form long-lasting partnerships.
3. Comparison and benchmarking: Attending trade shows and expos provides businesses with an opportunity to compare different injection mold design providers. By viewing and assessing their portfolios and discussing their expertise and capabilities, businesses can make informed decisions regarding the most suitable supplier for their specific requirements. This also enables businesses to benchmark suppliers against each other in terms of quality, cost, lead time, and other important factors.
4. Knowledge gathering and industry insights: Trade shows and expos often feature seminars, workshops, and demonstrations focused on injection mold design. By attending these sessions, businesses can gain valuable knowledge, learn about the latest design trends, and stay up-to-date with industry advancements. This information can be useful in making design-related decisions and understanding the capabilities and limitations of different suppliers.
In conclusion, leveraging trade shows and expos for injection mold design sourcing in China provides businesses with networking opportunities, direct interaction with suppliers, the ability to compare and benchmark different providers, and access to industry knowledge and insights. These events serve as a comprehensive platform for businesses to find reputable injection mold designers who can meet their specific requirements.
The Role of Agents and Sourcing Companies in Facilitating injection mould design Purchases from China
Agents and sourcing companies play a crucial role in facilitating injection mold design purchases from China. These intermediaries act as a bridge between buyers and suppliers, assisting in the entire procurement process. Their primary responsibilities include sourcing reliable suppliers, negotiating prices, ensuring quality control, and managing logistics.
Sourcing companies possess extensive knowledge and experience in the Chinese market, allowing them to identify suitable suppliers based on the buyer’s specific requirements. They have established networks of manufacturers that specialize in injection mold design, increasing the chance of finding a reliable and cost-effective supplier.
One significant advantage of using agents or sourcing companies is their ability to negotiate prices on behalf of the buyer. Chinese suppliers may initially quote higher prices for their products, especially for international buyers, but agents can leverage their expertise to negotiate favorable deals. They understand the local market dynamics, enabling them to secure competitive prices while ensuring the buyer’s interests are protected.
Quality control is another critical aspect handled by agents and sourcing companies. They conduct thorough supplier assessments, including factory visits and product inspections, to ensure that the products meet the buyer’s specifications and quality standards. This step minimizes the risk of receiving subpar or defective injection molds. Agents also provide feedback and communicate customer requirements to the supplier, ensuring ongoing quality improvements.
Logistics management is another area where agents and sourcing companies excel. They handle the complex process of shipping, customs clearance, and delivery, ensuring that the products reach the buyer’s desired location in a timely and cost-efficient manner. Agents also assist in managing any issues that may arise during transportation, such as delays or damages.
In summary, agents and sourcing companies play a vital role in facilitating injection mold design purchases from China. They possess the necessary knowledge, experience, and networks to source reliable suppliers, negotiate prices, ensure quality control, and manage logistics. By utilizing their services, buyers can streamline the procurement process, mitigate risks, and ultimately secure high-quality injection molds at competitive prices.
Price Cost Research for injection mould design manufacturers Companies in China, use temu.com and 1688.com
In China, there are numerous injection mould design manufacturing companies that offer competitive prices. Two popular online platforms for sourcing such companies are temu.com and 1688.com.
temu.com is a business-to-business (B2B) platform that connects global buyers with Chinese manufacturers. It provides a wide range of injection mould design manufacturers and allows users to compare prices and quality. The platform offers a user-friendly interface that simplifies the process of finding suitable suppliers. temu.com also provides customer reviews and ratings, helping buyers make informed decisions.
On the other hand, 1688.com is a leading Chinese B2B platform that offers a vast selection of suppliers. It provides comprehensive product listings, including injection mould design manufacturers. The platform provides detailed product information, price ranges, and customer reviews. 1688.com also offers a secure transaction service to ensure a safe buying experience.
When searching for injection mould design manufacturers on temu.com and 1688.com, various factors should be considered. These include the type of mould designs offered, manufacturing capabilities, quality assurance processes, lead time, and, most importantly, cost.
To conduct price cost research on temu.com and 1688.com, start by narrowing down the search criteria based on requirements. Next, evaluate different suppliers based on their pricing structures, such as unit costs, bulk order discounts, and any additional charges. It is crucial to communicate directly with the suppliers to negotiate prices, clarify specifications, and assess their overall responsiveness.
While searching for the most cost-effective injection mould design manufacturers, it is advisable to request quotes from multiple suppliers and compare them. However, it’s essential not to compromise on product quality solely for the sake of a lower price.
In conclusion, temu.com and 1688.com are valuable platforms to conduct price cost research for injection mould design manufacturers in China. These platforms offer extensive supplier options, comprehensive product information, and user reviews to facilitate informed decision-making. By utilizing these platforms and considering various factors, it is possible to find reliable suppliers in China at competitive prices.
Shipping Cost for injection mould design import from China
The shipping cost for importing an injection mould design from China can vary depending on several factors. These factors include the weight and dimensions of the mould, the shipping method chosen, and the destination country.
For small and lightweight injection mould designs, air freight is usually the preferred shipping method. Air freight is fast and efficient, but it can be more expensive compared to other options. On average, air freight costs can range from $5 to $10 per kilogram.
Alternatively, for larger and heavier mould designs, sea freight is a more cost-effective option. However, it is a slower mode of transportation, and delivery times can take several weeks. The cost of sea freight is determined by the volume or size of the shipment, rather than the weight. On average, sea freight costs can range from $500 to $2000 per cubic meter.
In addition to the shipping cost, it is important to consider other charges that may be associated with the import process. These charges include customs duties, taxes, documentation fees, and any additional services required, such as insurance or customs brokerage. It is recommended to work with a freight forwarder or shipping agent who can provide guidance and manage these processes.
To minimize shipping costs, it is advisable to optimize the packaging of the mould design to reduce its dimensions and weight. Additionally, consolidating multiple orders into a single shipment can help to reduce shipping expenses. It is important to coordinate with the supplier and efficiently plan the shipping arrangements to ensure timely delivery at an affordable cost.
Overall, the shipping cost for importing an injection mould design from China will depend on various factors, and it is recommended to obtain quotes from different shipping providers or freight forwarders to compare prices and services.
Compare China and Other injection mould design Markets: Products Quality and Price,Visible and Hidden Costs
China is a dominant player in the injection mould design market, but it faces competition from other markets such as the United States, Germany, and Japan. When comparing these markets, several factors need to be considered, including product quality and price, visible and hidden costs.
In terms of product quality, China has made significant strides in recent years. Many Chinese manufacturers have invested in advanced technology and improved their production processes, resulting in higher quality products. However, markets like the United States, Germany, and Japan are still perceived as having superior product quality due to their long-standing reputation for precision engineering and advanced manufacturing techniques.
When it comes to price, China has a distinct advantage. The country’s low labor and operational costs allow manufacturers to offer competitive pricing compared to other markets. This cost advantage often attracts businesses looking for cost-effective solutions. On the other hand, markets like the United States, Germany, and Japan may have higher price points due to higher labor and operational costs.
Visible costs, such as the cost of materials and labor, are relatively straightforward to compare. However, hidden costs can significantly impact the overall affordability of injection mould design. These hidden costs include logistics, intellectual property protection, and potential delays due to bureaucratic processes. When compared to China, markets like the United States, Germany, and Japan have generally more streamlined logistics, stronger intellectual property protection frameworks, and lesser bureaucratic obstacles. These factors contribute to more predictable and manageable hidden costs in these markets.
In conclusion, while China dominates the injection mould design market, there are other markets such as the United States, Germany, and Japan that offer their advantages. China has made significant progress in improving product quality, but it still faces competition from markets known for their superior engineering and manufacturing capabilities. China’s cost advantage makes it an attractive option for businesses seeking cost-effective solutions. However, other markets may offer more predictable and manageable hidden costs, which can impact the overall affordability of injection mould design.
Understanding Pricing and Payment Terms for injection mould design: A Comparative Guide to Get the Best Deal
When it comes to injection mould design, understanding the pricing and payment terms is essential to ensure you get the best deal. This comparative guide highlights the key factors to consider while keeping the word limit under 300 words.
Pricing for injection mould design can be determined based on various factors such as complexity, size, material, and quantity of the mould. Mould complexity refers to the level of intricacy involved in the design, while size and material affect the overall cost of production. It is important to discuss these details with different service providers to get accurate quotes and compare them effectively.
Payment terms are another crucial aspect to consider. It is common to pay a percentage upfront as a deposit to secure the services of the mould design company. The remaining balance can be paid in installments or upon completion of the project. It is important to clearly establish the payment schedule and terms to avoid any confusion or delays during the process.
To get the best deal, it is recommended to obtain quotes from multiple injection mould design service providers. This allows for a comprehensive comparison of the pricing and payment terms offered by different companies. However, it is equally important to consider the reputation, experience, and quality of work provided by each service provider.
Additionally, negotiating and bargaining can play a role in securing a favorable deal. Some companies may be open to negotiating the price or payment terms based on the volume of work or a long-term partnership. It is worth exploring these options to ensure a mutually beneficial arrangement.
Finally, it is important to carefully review the terms and conditions outlined in the contract before finalizing any agreement. This includes clarifying the intellectual property rights, warranties, liability, and delivery timelines. Seek legal advice if necessary to ensure all terms are fair and protect your interests.
In conclusion, understanding the pricing and payment terms for injection mould design is crucial to secure the best deal. Comparing quotes, negotiating, and reviewing the contract terms are essential steps to achieve a cost-effective and satisfactory partnership with the chosen mould design service provider.
Chinese Regulations and Industry Standards Certifications for injection mould design,Import Regulations and Customs for injection mould design from China
Chinese Regulations and Industry Standards Certifications for injection mold design are essential to ensure safety, quality, and compliance with industry guidelines. One of the primary regulations is the “GB/T 14486-1993 Plastic injection mold terminology.” This standard establishes terminology, classifications, and basic requirements for injection molds.
Additionally, the Chinese Ministry of Industry and Information Technology (MIIT) has issued a series of specific industry standards related to injection mold design. These include the “JJF 2084-2017 Injection mold steel material hardness verification,” which specifies the hardness requirements and measurement methods for injection mold steel materials.
In terms of certifications, the most recognized one is the ISO 9001. Obtaining ISO 9001 certification indicates that the injection mold design company has implemented a quality management system and meets international quality standards.
When importing injection mold designs from China, it is crucial to adhere to import regulations and customs requirements. The first step is to verify the supplier’s credibility and manufacturing capabilities. It is recommended to conduct thorough research, request samples, and check if the supplier has appropriate licenses and certificates.
During the import process, the importer must provide the necessary documents such as commercial invoice, packing list, bill of lading or airway bill, and customs declaration form. These documents should accurately describe the injection mold design and its value for customs purposes.
Customs duties and taxes might be applicable upon importing injection molds from China. The specific rates depend on the country of import and the harmonized system code assigned to the product. Importers should consult their local customs authorities to determine the applicable duties and taxes beforehand.
In conclusion, adhering to Chinese regulations and industry standards certifications is vital for injection mold design to ensure quality and compliance. When importing from China, it is crucial to follow import regulations and customs procedures and consult with local customs authorities to determine the applicable duties and taxes.
Sustainability and Environmental Considerations in injection mould design Manufacturing
In recent years, there has been an increasing emphasis on sustainability and environmental considerations in injection mold design manufacturing. This shift is driven by the growing recognition of the detrimental effects of traditional manufacturing processes on the environment and the urgent need to adopt more sustainable practices.
One key aspect of sustainable injection mold design manufacturing is the reduction of material waste. By optimizing the shape and size of the mold, designers can minimize the amount of material required for each product, thus reducing waste generation. Moreover, the use of advanced software tools allows for the creation of more complex and efficient molds, resulting in improved material utilization and decreased environmental impact.
Another important consideration is the choice of materials. Designers are now opting for eco-friendly and recyclable materials, such as biodegradable polymers, to minimize the environmental footprint of their products. These materials can be easily decomposed, reducing landfill waste and pollution. Additionally, the use of recycled plastics in injection mold design manufacturing helps reduce the demand for virgin materials, conserving natural resources.
Furthermore, energy consumption is a significant environmental concern in manufacturing processes. Injection mold designers are implementing energy-saving strategies, such as incorporating efficient heating and cooling systems, to reduce energy consumption during the manufacturing process. This not only lowers greenhouse gas emissions but also decreases operating costs, making sustainable practices economically viable.
Finally, the lifespan and durability of injection molds are critical for sustainable manufacturing. By employing high-quality materials and design techniques, designers can create molds that have a longer lifespan and require less maintenance. This not only reduces the generation of waste from mold replacements but also minimizes the energy and resources required for mold production.
In conclusion, sustainability and environmental considerations have become integral aspects of injection mold design manufacturing. By focusing on waste reduction, material selection, energy efficiency, and durability, designers can contribute to a more sustainable and environmentally-friendly manufacturing industry. By adopting these practices, manufacturers can meet the increasing demand for eco-friendly products and contribute to a greener future.
List The Evolution history of “injection mould design”
The evolution of injection mold design has undergone significant changes over the years, leading to the creation of more sophisticated and efficient molding processes.
The earliest forms of injection molding can be traced back to the late 19th century when a manual plunger was used to inject hot plastic into a mold. At this stage, molding was primarily limited to simple shapes and designs due to the rudimentary nature of the process.
In the 1930s, the development of the reciprocating screw injected molding machine revolutionized the industry. This innovation enabled precise control over the injection process, facilitating the production of more complex and intricate designs. The advent of this technology marked a turning point in injection mold design, as it led to improved speed, accuracy, and flexibility in creating molds.
Throughout the 1960s and 1970s, advancements in computer technology paved the way for the introduction of computer-aided design (CAD) systems. CAD software allowed designers to create virtual models of injection molds, eliminating the need for physical prototypes. This innovation significantly reduced design errors, streamlining the production process, and minimizing costs.
In the 1980s, the development of computer-aided manufacturing (CAM) systems further propelled the evolution of injection mold design. CAM software integrated with CAD software enabled direct communication with manufacturing equipment, such as CNC machines. This integration allowed for seamless transitions from design to production, optimizing efficiency and accuracy.
The 1990s witnessed the introduction of more advanced materials, such as thermoplastics, and the development of technologies like over-molding and gas-assisted injection molding. These advancements expanded the possibilities for complex injection mold designs, enabling the production of multi-component and hollow parts with enhanced strength and functionality.
In recent years, the emergence of additive manufacturing, specifically 3D printing, has also influenced mold design. 3D printing allows for the rapid prototyping of molds, reducing time and cost associated with traditional mold-making processes. This technology has opened new avenues for customization and experimentation in injection mold design.
Overall, the evolution of injection mold design has seen continuous advancements driven by technological innovations. From manual plunger systems to advanced CAM and CAD software, each stage has played a significant role in expanding the capabilities and possibilities of injection molding.
The Evolution and Market Trends in injection mould design Industry
The injection mould design industry has evolved significantly over the years, driven by advancements in technology and changing market demands. Initially, injection moulding was a manual process where designers would create moulds by hand. However, with the advent of computer-aided design (CAD) software, the industry shifted towards computerized design and simulation.
One of the key trends in injection mould design is the use of 3D printing technology. 3D printing allows designers to rapidly create prototypes and test their designs before investing in expensive moulds. This technology has revolutionized the industry by reducing lead times and costs associated with traditional mould making processes.
Another trend is the increasing demand for complex and intricate designs. Consumers are looking for unique and customized products, and injection mould designers are challenged to create moulds that can produce these complex shapes. This trend has fueled the development of advanced mould design techniques, such as multi-cavity moulds and hot runner systems, which enable the production of complex parts with high precision.
Additionally, sustainability has become a major concern in the injection mould design industry. Manufacturers and consumers are increasingly focused on reducing waste and minimizing the environmental impact of their products. As a result, there is a growing demand for mould designs that minimize material usage, incorporate recycled materials, and optimize the production process to reduce energy consumption.
Furthermore, the industry is witnessing a shift towards automation and integration of robotics in the injection mould design process. Automation not only improves efficiency and productivity but also ensures consistent quality and reduces the reliance on manual labor.
In terms of market trends, the injection mould design industry is experiencing significant growth due to the increasing demand for plastic products in various industries, including automotive, packaging, electronics, and medical devices. The rise of e-commerce and online shopping has also contributed to the demand for injection moulded products such as packaging and consumer goods.
Overall, the injection mould design industry is evolving to meet the changing demands of the market. With advancements in technology, the industry is embracing 3D printing, complex designs, sustainability, automation, and robotics. In addition, the growing demand for plastic products from various industries is driving the growth of the market.
Custom Private Labeling and Branding Opportunities with Chinese injection mould design Manufacturers
China is well-known for its expertise in injection mould design and manufacturing, making it an ideal destination for businesses seeking custom private labeling and branding opportunities. Chinese manufacturers offer a vast range of options and capabilities that can be tailored to the specific needs of businesses from various industries.
One of the key advantages of partnering with Chinese injection mould design manufacturers is the cost-effectiveness they offer. Due to lower labor costs and a well-developed supply chain, Chinese manufacturers can provide competitive pricing without compromising on quality. This makes it an attractive option for businesses looking to customize their products with private labeling or branding, as it allows for cost-effective manufacturing while maintaining product integrity.
Furthermore, Chinese injection mould design manufacturers have extensive experience in producing various types of molds, offering businesses a wide range of customization options. These manufacturers are capable of handling intricate designs, complex geometries, and unique specifications, thereby allowing businesses to create products that align with their brand identity and market positioning.
Chinese manufacturers also provide flexible production quantities, accommodating both small and large-scale orders. This allows businesses to test the market with smaller quantities before scaling up production, minimizing risks and reducing upfront investments. Moreover, Chinese manufacturers have quick turnaround times, enabling businesses to bring their products to market swiftly and stay ahead of competitors.
Partnering with Chinese injection mould design manufacturers also offers businesses access to a well-established supply chain and infrastructure. These manufacturers have access to a vast network of suppliers and raw materials at competitive prices. This helps ensure a steady supply of high-quality materials, reducing the chances of delays or production issues.
In conclusion, Chinese injection mould design manufacturers present excellent opportunities for businesses seeking custom private labeling and branding solutions. With their cost-effectiveness, extensive customization options, flexibility in production quantities, quick turnaround times, and access to a well-established supply chain, Chinese manufacturers can help businesses bring their branded products to market efficiently and competitively.
Tips for Procurement and Considerations when Purchasing injection mould design
When it comes to purchasing injection mold designs, there are several key considerations and tips that procurement professionals should keep in mind.
1. Clear specifications: Provide a detailed and precise description of the required mold design. This includes dimensional accuracy, material specifications, expected production volume, and any special features or requirements.
2. Supplier qualification: Ensure that the supplier has experience and expertise in injection mold design. Check their portfolio of past projects and verify their reputation in the industry.
3. Cost optimization: Seek suppliers who can provide competitive pricing without compromising quality. Consider obtaining multiple quotes and negotiate for the best value for money.
4. Quality assurance: Request quality certifications and examine the supplier’s quality control processes. Make sure their molds undergo rigorous inspections and testing to meet industry standards.
5. Mold materials: Understand the different types of mold materials available (e.g., steel, aluminum) and their properties. Balance cost, durability, and maintenance requirements when selecting the most suitable material.
6. Lead time: Determine the supplier’s ability to deliver the mold design within the required timeframe. Timely production is crucial for meeting production schedules.
7. Intellectual property protection: Ensure that the supplier respects intellectual property rights. Sign non-disclosure agreements if necessary to safeguard confidential information related to the mold design.
8. Support and warranty: Inquire about after-sales services, technical support, and warranty options provided by the supplier. Having a reliable partner that can assist with any issues or repairs is vital.
9. Scalability: Consider the long-term requirements for the mold design. Will it be compatible with future product iterations or modifications? Discuss scalability options with the supplier.
10. Communication and collaboration: Foster open and transparent communication with the supplier throughout the procurement process. Regular updates and consultations will help maintain a smooth workflow.
By taking into account these considerations and following these tips, procurement professionals can ensure a successful and cost-effective purchase of injection mold designs.
FAQs on Sourcing and Manufacturing injection mould design in China
Q: What is injection mould design?
A: Injection mould design refers to the process of creating a design for a mould that will be used in the injection moulding process. This design includes the dimensions, shape, and features required for producing a specific product.
Q: Why should I consider sourcing injection mould design in China?
A: China is known for its manufacturing capabilities and cost-effectiveness. Many businesses choose to source injection moulds from China due to the lower production costs and access to a large pool of skilled labour. Additionally, China has a well-established infrastructure for mould manufacturing and a wide range of materials available.
Q: How can I find reliable manufacturers for injection mould design in China?
A: To find reliable manufacturers, it is important to conduct thorough research and due diligence. One approach is to search online directories and platforms that connect businesses with manufacturers. It is advisable to request samples, visit their facilities if possible, and verify their certifications and past client reviews to ensure their credibility.
Q: What are the key considerations when sourcing injection mould design in China?
A: Some key considerations include the manufacturer’s experience and expertise in injection mould design, their production capacity, quality control measures, and their ability to meet your specific requirements and timelines. It is also crucial to establish clear communication channels and understand the terms of pricing, payment, and intellectual property protection.
Q: How can I overcome language and cultural barriers when working with Chinese manufacturers?
A: Language and cultural barriers can be overcome by hiring an interpreter or translator, or by utilizing tools like online translation services. Building a strong relationship with the manufacturer through regular communication, clear instructions, and mutual understanding can also help mitigate potential issues stemming from cultural differences.
Q: What are the typical lead times for injection mould design and manufacturing in China?
A: Lead times can vary depending on the complexity of the design, the availability of materials, and the manufacturing capabilities of the chosen supplier. Generally, injection mould design can take a few weeks to a couple of months, while manufacturing of the moulds can take several weeks to a few months, depending on the size and intricacy of the mould.
In summary, injection mould design in China offers the advantages of cost-effectiveness, a vast manufacturing infrastructure, and a skilled labour pool. Finding reliable manufacturers requires thorough research, and key considerations include experience, quality control, and communication. Overcoming language and cultural barriers is possible through effective communication channels and understanding. Lead times vary depending on factors such as design complexity and material availability.
Why contact sourcifychina.com get free quota from reliable injection mould design suppliers?
Sourcifychina.com offers free quota from reliable injection mold design suppliers for several reasons. Firstly, by providing a free quota, Sourcifychina.com aims to attract potential customers and build trust. This is especially important in the highly competitive injection mold design industry where customers prefer working with reputable and trusted suppliers.
Secondly, by partnering with reliable injection mold design suppliers, Sourcifychina.com ensures that customers receive high-quality products and services. The suppliers go through a rigorous vetting process to ensure their capabilities, expertise, and track record meet Sourcifychina.com’s standards.
Additionally, offering a free quota allows customers to assess and compare different suppliers before making a decision. This enables them to make an informed choice based on their specific requirements, budget, and timeline.
Moreover, the free quota service helps customers save time and effort in sourcing and evaluating potential suppliers. Sourcifychina.com has a vast network of reliable suppliers, which eliminates the need for customers to personally reach out to multiple suppliers and request quotations. This streamlines the sourcing process and provides convenience to customers.
Furthermore, Sourcifychina.com understands the value of providing a positive customer experience. By offering a free quota, they enhance customer satisfaction, as it gives customers an opportunity to evaluate suppliers without any financial commitment. This is particularly beneficial for customers who are new to the injection mold design industry or are looking for alternative suppliers.
In conclusion, Sourcifychina.com provides a free quota from reliable injection mold design suppliers to attract customers, build trust, ensure quality, enable comparison, save time, and enhance the overall customer experience.