Introduce about injection mould factory guide,Qulity,Cost,Supplier,Certification,Market,Tips,FAQ
An injection mold factory is a facility specialized in manufacturing plastic products through injection molding processes. This guide will provide you with essential information on quality, cost, suppliers, certification, market, and useful tips. Here are the key details:
Quality: A reputable injection mold factory adheres to strict quality control measures. They use high-quality materials, employ skilled technicians, and follow proper production methods to ensure the durability and precision of the molded products.
Cost: The cost of injection molding includes several factors like the complexity of the design, materials used, volume of production, and additional services required (e.g., surface finishing). It is advisable to request quotes from multiple factories to compare prices and services.
Suppliers: Choosing a reliable supplier is crucial to ensure smooth production and timely delivery. Consider factors such as their experience, past clients, reputation, production capacity, and customer service when selecting a supplier.
Certification: Look for an injection mold factory that holds relevant industry certifications like ISO 9001, which ensures adherence to quality management standards. This certification signifies that the factory has established robust processes for consistent production and customer satisfaction.
Market: The injection molding market is vast and its application spans various industries like automotive, electronics, packaging, healthcare, and appliances. Understanding the market demand and trends can help you identify potential opportunities and stay competitive.
Tips:
1. Provide detailed specifications and requirements to the factory for accurate quoting and production.
2. Communicate regularly with your supplier to track progress, address concerns, and make necessary adjustments.
3. Conduct a thorough inspection of sample products before bulk production to validate quality and functionality.
FAQ:
1. What is the typical lead time for production?
2. Can you assist with product design and prototype development?
3. What materials are suitable for injection molding?
4. How do you handle quality control and assurance?
5. Do you offer after-sales support?
In conclusion, when selecting an injection mold factory, prioritize quality, consider production cost, choose a reliable supplier, check for certifications, analyze the market potential, and apply the provided tips to ensure a successful manufacturing process.
Types of injection mould factory
There are several types of injection mould factories based on their production capabilities, specialization, and ownership. Here are some common types:
1. Small-scale/Custom Mould Factory:
These factories typically focus on producing small quantities of customised injection moulded products. They cater to specific client requirements and produce low to medium volumes. They may have limited resources and equipment but excel in providing customisation and flexibility.
2. Large-scale/High-Volume Mould Factory:
These factories specialize in producing high volumes of injection moulded products. They have a wide range of machinery, automation systems, and efficient production lines. They serve industries such as automotive, consumer goods, and packaging, where large quantities are needed.
3. Prototype Mould Factory:
Prototype mould factories focus on producing prototypes or samples for pre-production assessment. They often use rapid prototyping techniques like 3D printing or aluminum tooling to quickly produce small volumes for testing, design validation, and market evaluation.
4. Multi-material Mould Factory:
These factories specialize in producing moulded products that require multiple materials or colors. They have the capability to handle complex injection moulding processes such as over-molding (adding one material onto another) or co-injection (simultaneously injecting different materials).
5. In-house Mould Factory:
Some large-scale manufacturing companies have their in-house injection mould factories. This enables them to have complete control over the production process, reduce lead times, and maintain confidentiality of their product designs. In-house factories are commonly found in industries like electronics, medical devices, and consumer goods.
6. Contract Mould Factory:
Contract mould factories are independent companies that specialize in providing moulding services to various clients. They have expertise in managing an entire production process, from design to final product delivery. They work on a contract basis and cater to diverse industry requirements.
7. Specialized Mould Factory:
Some mould factories focus on specific industries or types of products. For example, there are specialized factories for medical device components, automotive parts, packaging, or precision engineering. These factories possess niche expertise, certifications, and industry-specific quality standards.
The choice of mould factory depends on the specific requirements of the product, production volume, complexity, and budget constraints. Each type of factory offers unique advantages and expertise to cater to different customer needs.
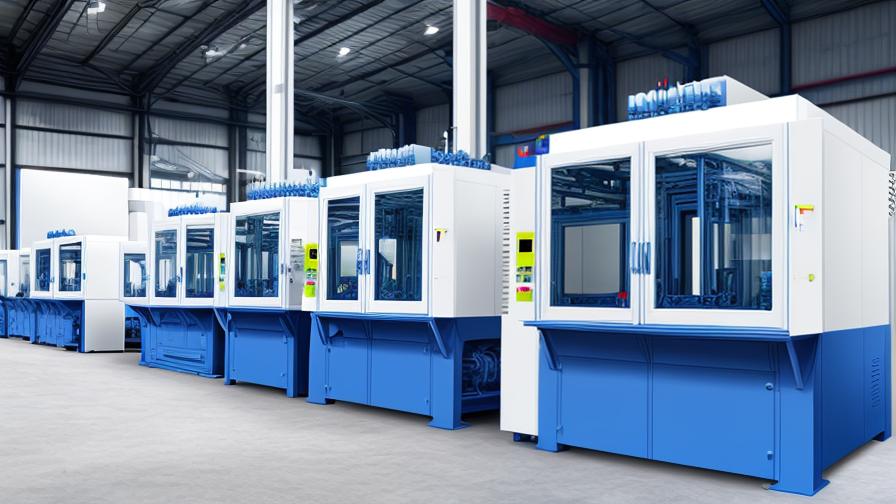
Pros and Cons of Using injection mould factory
Using an injection mould factory has both advantages and disadvantages.
Pros:
1. Cost-effective: Injection moulding is highly efficient and allows for mass production at a lower cost per unit. The process is automated, reducing labor costs and increasing productivity.
2. Quick production time: Injection moulding can produce a large number of products within a short period. This makes it ideal for meeting tight deadlines and high-volume orders.
3. Design flexibility: The flexibility of injection moulding allows for intricate and complex designs. The mould can be easily customized to produce products with different shapes, sizes, and functions.
4. Material variety: Injection moulding works with a wide range of materials, including plastics, metals, and composites. This versatility opens up opportunities to produce a diverse range of products.
5. High-quality finish: Injection moulding produces products with a consistent and high-quality finish. It allows for precise control over dimensions, textures, and appearances, meeting strict quality standards.
Cons:
1. High initial cost: Setting up an injection mould factory can be expensive. The cost includes purchasing machinery, molds, and setting up infrastructure. Small businesses may find it challenging to afford these initial investments.
2. Design limitations: While injection moulding offers design flexibility, it also has certain limitations. Complex designs may require intricate molds, which can increase costs. Additionally, certain design features such as sharp corners may not be feasible.
3. Lead time and setup: Developing molds and setting up injection moulding machines takes time. This can result in longer lead times, which could be a disadvantage if quick turnaround is required.
4. Volume requirements: Injection moulding is most cost-effective when producing large quantities of products. If the production volume is low, the expense of the molds and setup may not be justified.
5. Environmental impact: Injection moulding generates waste materials, such as excess plastic or metal scraps. Proper waste management and disposal practices are necessary to minimize the environmental impact.
In conclusion, while there are some drawbacks to using an injection mould factory, the advantages outweigh the disadvantages for many businesses. The cost-effectiveness, versatility, and high-quality finish make it an attractive manufacturing method for a wide range of industries.
injection mould factory Reference Specifications (varies for different product)
The injection mould factory reference specifications are integral documents that provide detailed information about the manufacturing process of injection moulds for various products. These specifications serve as guidelines for the factory workers and engineers to ensure that the moulds are produced according to the required standards and specifications for each specific product.
The reference specifications typically vary for different products due to their unique design, size, and material requirements. For instance, the specifications for a small plastic bottle mould will differ from those of a large automobile bumper mould. The reference specifications outline the necessary dimensions, tolerances, materials, and surface finishes for each specific mould. They also include specific requirements for parting lines, ejection systems, cooling channels, and venting systems.
In addition to the technical details, the reference specifications may also include information on the specific injection moulding machine to be used, the type of plastic material to be used, the recommended moulding temperature, and the required injection pressures for each product. These specifications ensure that the moulds are designed and manufactured to produce high-quality and consistent products.
To adhere to the reference specifications, the injection mould factory must have skilled engineers who can interpret and translate the specifications into practical design solutions. They need to have a thorough understanding of the specific product requirements and apply their technical expertise to design moulds that meet these requirements.
The factory workers, including the mould makers and technicians, rely on the reference specifications to guide them during the mould production process. They follow the specifications to create the moulds using precision machining techniques such as milling, grinding, and electric discharge machining. The workers also ensure that the moulds undergo rigorous quality control checks at various stages of production to ensure compliance with the reference specifications.
By strictly adhering to the reference specifications, the injection mould factory can produce high-quality moulds that are accurately designed to meet the specific requirements of each product. This allows for the production of consistent and defect-free products, resulting in customer satisfaction and increased competitiveness in the market.
Applications of injection mould factory
Injection mould factories are versatile manufacturing facilities that play a crucial role in producing a wide range of plastic products. These factories specialize in creating intricate plastic components by injecting molten plastic into a mould and allowing it to cool and solidify. Here are some common applications of injection mould factories:
1. Automotive Industry: Injection mould factories are extensively used in the automotive industry to manufacture various plastic components, including dashboards, bumpers, interior panels, and door handles. These components are durable, lightweight, and cost-effective, making them ideal for automotive applications.
2. Consumer Electronics: Injection mould factories are heavily relied upon in the consumer electronics sector for producing plastic parts like phone cases, laptop keyboards, remote controls, and other accessories. The ability to create complex shapes and precise dimensions makes injection moulding a preferred manufacturing method for consumer electronic products.
3. Medical Devices: Injection moulding is crucial for the production of medical devices due to its ability to manufacture sterile, high-quality, and disposable products. Syringes, IV tubes, medical equipment housings, and other disposable items are commonly made using injection mould factories to ensure patient safety and hygiene.
4. Packaging Industry: Injection moulding is widely utilized in the packaging industry to manufacture containers, caps, lids, and closures for various products. The process allows for consistent production, ensuring airtight and leak-proof packaging for food, beverages, cosmetics, and household items.
5. Construction and Building Materials: Injection mould factories are also involved in producing various plastic components used in the construction industry. These include pipes, fittings, cable trays, insulation panels, and flooring materials. Injection moulding enables the production of durable and structurally stable products that meet stringent industry standards.
6. Toys and Games: Injection mould factories are responsible for producing a vast array of plastic toys and games enjoyed by children and adults alike. This manufacturing process allows for the creation of intricate and vibrant designs, providing endless opportunities for creativity and entertainment.
7. Furniture and Home Decor: Injection moulding is used in the production of plastic furniture components, such as chair shells, table legs, and home decor items. This process enables mass production while maintaining a high level of design flexibility and durability.
In conclusion, injection mould factories are instrumental across various industries due to their ability to produce high-quality and cost-effective plastic products. With its versatility and precision, injection moulding has significantly contributed to advancements in automotive manufacturing, consumer electronics, medical devices, packaging, construction, toys, furniture, and more.
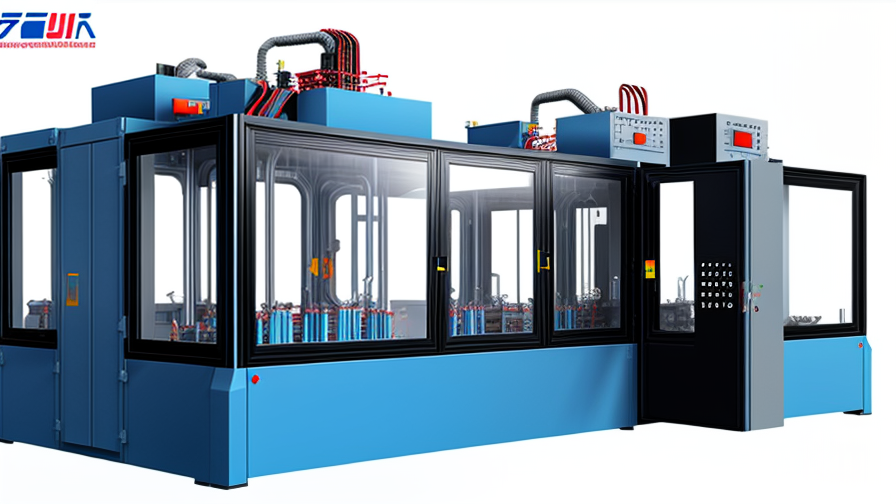
The Work Process and how to use injection mould factory
The work process involved in using an injection mold factory typically includes the following steps:
Design and Development: The first step is to create or receive a design for the desired product. This can be done by hiring a designer or utilizing a design software. The design is then converted into a 3D drawing or CAD file.
Selection of Materials: The appropriate materials for the product are chosen based on factors such as durability, flexibility, and cost. The selected materials should also be compatible with the injection molding process.
Tooling and Mold Creation: A mold is created based on the design and material specifications. This involves the use of specialized machinery and skilled technicians. The mold is typically made from steel or aluminum and consists of two halves – the core and the cavity.
Injection Molding: The selected material is melted using a heating system and then injected into the mold cavity using a high-pressure injection unit. The molten material takes the shape of the mold and solidifies within seconds or minutes, depending on the material and product design.
Cooling and Ejection: Once the injected material solidifies, the mold is cooled using a cooling system, allowing the product to settle and harden completely. Subsequently, the mold is opened and the finished product is ejected using ejector pins or air pressure.
Quality Control and Finishing: The ejected products are inspected for any defects or imperfections, such as air bubbles, warping, or incomplete filling. Any necessary finishing processes, such as trimming or polishing, are also undertaken.
Assembly and Packaging: If required, the finished products can be assembled with other components and undergo secondary processes like painting or printing. The products are then packaged as per customer requirements, ready for distribution or sale.
To effectively use an injection mold factory, it is crucial to communicate the design specifications clearly and collaborate closely with the factory’s engineers and technicians. Regular feedback and updates should be exchanged to ensure the production meets the desired quality and timeline. Additionally, maintaining an open line of communication and addressing any concerns or issues promptly can help streamline the manufacturing process.
In conclusion, the work process of utilizing an injection mold factory involves design and development, material selection, mold creation, injection molding, cooling and ejection, quality control, finishing, assembly, and packaging. Effective communication and collaboration with the factory are key factors in achieving successful production outcomes.
Quality Testing Methods for injection mould factory and how to control the quality
Quality testing methods for injection mould factories involve several steps to ensure that the products meet the required standards. These include:
1. Visual Inspection: This involves visually inspecting the moulded parts for any surface defects, such as cracks, scratches, or deformities. Any abnormalities should be noted and addressed.
2. Dimensional Measurement: Accurate dimensional measurement is essential in injection moulding. This is typically done using measurement tools such as calipers, micrometers, or coordinate measuring machines (CMM). It ensures that the parts are within the specified tolerances.
3. Mechanical Testing: Mechanical tests, such as tensile strength, impact resistance, or hardness tests, are performed to evaluate the physical properties of the moulded parts. These tests help ensure that the parts can withstand the intended application and load requirements.
4. Functional Testing: Functional tests assess whether the moulded parts are functioning as intended. This can involve assembling the parts to check for proper fit, ensuring that the parts perform their desired function, and validating any specific requirements or standards.
In addition to these testing methods, effective quality control in injection mould factories can be ensured through:
1. Process Control: Maintaining a consistent and controlled moulding process is crucial. This involves monitoring and adjusting parameters like temperature, pressure, cooling time, and injection speed to achieve consistent part quality.
2. Regular Maintenance: Proper maintenance of the equipment, including moulds, machines, and auxiliary systems, is essential to prevent defects and breakdowns. Regular cleaning and inspection of moulds will help ensure consistent quality and prolong their lifespan.
3. Employee Training: Proper training should be provided to all staff involved in the injection moulding process to ensure they understand the quality requirements and can operate the machinery effectively and efficiently.
4. Documentation and Traceability: Maintaining comprehensive records of all processes, including material types and sources, machine settings, and quality inspection results, allows for traceability and aids in identifying any potential issues or trends affecting quality.
By implementing these quality testing methods and control measures, injection mould factories can ensure that the products they produce meet the required quality standards, resulting in customer satisfaction and market competitiveness.
injection mould factory Sample Policy and Post-Purchase Considerations for injection mould factory from China
When it comes to sourcing injection moulds from China, it is crucial to have a well-defined sample policy and post-purchase considerations. This ensures that the quality of the moulds meets your requirements and any issues that arise can be effectively addressed. Here is a concise guide that covers these aspects in fewer than 300 words:
Sample Policy:
1. Request Initial Samples: Before placing a bulk order, always request samples from the injection mould factory in China. Evaluate their quality, accuracy, and durability according to your specifications.
2. Testing and Approval: Thoroughly test the samples to ensure they meet the desired standards. Assess factors such as strength, dimensional accuracy, weight, and finish. If there are any discrepancies, provide clear feedback for necessary improvements.
3. Iterative Sampling Process: In case the initial samples do not meet expectations, enforce an iterative sampling process. The factory should revise and resubmit improved samples until they align with your requirements.
4. Multiple Supplier Samples: Consider sourcing samples from multiple injection mould factories in China for comparison. This will help you select the most suitable supplier for your needs.
5. Legal Protection: Ensure that the supplier provides a sample agreement that protects your intellectual property rights and prevents unauthorized use or reproduction.
Post-Purchase Considerations:
1. Quality Assurance: Establish a Quality Control (QC) process to assess the moulds during production and before shipment. Conduct rigorous inspections and testing to avoid potential defects or substandard products.
2. Spare Mould Parts: Discuss and negotiate with the supplier to obtain spare parts for the injection mould. It is essential for future maintenance and replacements.
3. Communication: Maintain constant communication with the supplier to address any questions, concerns, or issues that may arise during the production process or after delivery. Promptly provide feedback for necessary modifications or improvements.
4. Warranty and Support: Determine the warranty period and guarantee offered by the injection mould factory. Understand the supplier’s willingness to provide technical support or assistance in case of emergencies or mold repairs.
By implementing a thorough sample policy and considering the aforementioned post-purchase considerations, you can minimize the risk and maximize the outcome of sourcing injection moulds from China.
Sourcing injection mould factory from China: Opportunities, Risks, and Key Players
Sourcing injection mould factories from China offers numerous opportunities for businesses looking for cost-effective manufacturing solutions. China is known for its large manufacturing capabilities and competitive pricing, making it an attractive option for companies seeking high-quality injection moulding.
The main opportunity lies in the cost savings that can be achieved through sourcing from China. The lower cost of labor and materials in China often results in significantly lower production costs compared to other countries. This allows businesses to increase their profit margins or offer more competitive pricing to their customers.
Another advantage of sourcing from China is the availability of a wide range of suppliers and manufacturers. China has a robust network of injection mould factories, offering various specialization areas and production capacities. This provides businesses with the flexibility to choose a supplier that can meet their specific requirements and production volumes.
However, there are also risks associated with sourcing from China. Quality control can be a concern, as some factories may not meet the desired standards or cut corners to reduce costs. This emphasizes the importance of due diligence and careful supplier selection. Conducting factory audits, quality inspections, and requesting samples can help mitigate these risks.
Intellectual property protection is another potential challenge. China has been notorious for intellectual property infringement in the past. It is crucial for businesses to take proper precautions to protect their designs, patents, and trademarks when sourcing from China. Consulting legal experts and ensuring proper contracts and agreements are in place can help safeguard intellectual property rights.
When it comes to key players in the injection mould industry in China, some prominent manufacturers include Techplas, Sositar Mould, and LK Mould. These companies have established a strong reputation for providing high-quality injection moulding solutions.
In conclusion, sourcing injection mould factories from China offers great opportunities for cost savings and access to a wide range of suppliers. However, businesses need to be aware of the risks associated with quality control and intellectual property protection. By conducting thorough research, due diligence, and working with reliable suppliers, companies can successfully harness the benefits of sourcing injection mould factories from China.
How to find and select reliable injection mould factory manufacturers in China,use google search manufacturers and suppliers
Finding and selecting reliable injection mould factory manufacturers in China can be a daunting task, but with the help of Google search and following some essential tips, it can be made easier. Here are a few steps to follow:
1. Start with a Google search: Begin by searching for “injection mould factory manufacturers in China” or similar keywords. This will provide you with a list of potential manufacturers.
2. Evaluate their website: Visit the websites of the manufacturers you come across and assess their credibility. Look for information like company history, experience, certifications, and product details.
3. Check customer reviews: Look for customer reviews or testimonials on the manufacturer’s website or on other reliable platforms. Read both positive and negative reviews to get a comprehensive understanding of their reputation.
4. Verify their certifications: Reliable manufacturers usually hold certificates like ISO 9001, ISO 14001, or other quality management system certifications. These certifications ensure that the manufacturer follows industry standards and practices.
5. Request samples and quotes: Contact the shortlisted manufacturers and request samples of their products. This will help you assess their quality and craftsmanship. Additionally, ask for detailed quotes that include information on pricing, lead time, and terms of payment.
6. Communicate effectively: Engage in effective communication with the manufacturers. This will help you gauge their professionalism, response time, and ability to understand your requirements.
7. Conduct factory audits and inspections: If possible, plan a visit to the factory or hire an independent third-party inspection agency. This will help you assess their manufacturing facilities, quality control measures, and overall operational efficiency.
8. Consider supplier background checks: Utilize online platforms or services that conduct background checks on manufacturers. This can provide additional information regarding the manufacturer’s financial stability, legal status, and reputation in the market.
In conclusion, finding and selecting reliable injection mould factory manufacturers in China is a step-by-step process that involves extensive research, communication, and verification. Using Google search as a starting point and following the above-mentioned tips will help you narrow down your options and make an informed decision.
How to check injection mould factory manufacturers website reliable,use google chrome SEOquake check if ranking in top 10M
To check the reliability of an injection mould factory manufacturer’s website, you can follow a few steps using Google Chrome and the SEOquake tool. This method aims at assessing the website’s ranking and credibility within the top 10 million websites, keeping the answer concise within 300 words.
1. Install SEOquake: Add the SEOquake extension to your Google Chrome browser. SEOquake is a powerful SEO tool that provides a website’s key metrics and rankings.
2. Search for the manufacturer: Using a search engine, enter the name of the injection mould factory manufacturer or related keywords.
3. Analyze the search results: SEOquake will appear as a toolbar in your browser’s window, displaying various parameters such as Google PageRank, Alexa Rank, SEMrush Rank, and others. Focus on the following indicators for reliability assessment:
– Google PageRank: This metric rates a website’s authority on a scale of 0 to 10. Higher rankings indicate better reliability, but keep in mind that Google no longer updates this data publicly. Look for a modest PageRank to ensure the website is not excessively focusing on manipulation.
– SEMrush Rank: This metric shows the website’s popularity based on organic search traffic. Reliable websites often have a decent SEMrush Rank, indicating a reasonable amount of organic traffic.
– Alexa Rank: This metric refers to a website’s popularity worldwide. A higher Alexa Rank usually suggests greater reliability and visitor engagement. However, bear in mind that popularity alone does not guarantee trustworthiness.
4. Check for top 10 million ranking: Use the information provided by SEOquake to determine if the website falls within the top 10 million websites. If the website ranks highly, it indicates good traffic and potential reliability.
5. Further assessment: While the above steps can help evaluate a website’s reliability to some extent, additional factors like user reviews, testimonials, quality of content, and certifications should be considered for a more comprehensive assessment.
By following these steps and analyzing the relevant metrics using SEOquake on Google Chrome, you can get a preliminary idea of the injection mould factory manufacturer’s website reliability within the top 10 million websites.
Top 10 injection mould factory manufacturers in China with each 160 words introduce products,then use markdown create table compare
1. Foxconn Technology Group (Foxconn)
Foxconn is a leading injection mould factory manufacturer in China with a wide range of products. They specialize in the production of precision moulds for various industries such as electronics, automotive, and medical. Their products include plastic parts, connectors, and housings for electronic devices, as well as components for automobiles and medical devices. With their advanced technology and expertise, Foxconn ensures high-quality moulds with precise dimensions and excellent surface finish.
2. Haier Group Corporation
Haier Group Corporation is a renowned manufacturer of injection moulds in China. They offer a diverse range of products, including moulds for household appliances, such as refrigerators, washing machines, and air conditioners. Their moulds are durable, efficient, and highly precise, enabling the production of top-quality plastic parts. Haier Group Corporation has successfully served numerous global clients and is known for their commitment to innovative designs and reliable manufacturing processes.
3. BYD Company Limited
BYD Company Limited is a prominent injection mould factory manufacturer in China. They specialize in the production of moulds for electric vehicles and other transportation applications. Their products include precision moulds for vehicle exteriors, interiors, and mechanical components. With advanced technologies like computer-aided design (CAD) and computer-aided manufacturing (CAM), BYD ensures precision moulds that meet industry standards. Their commitment to high-quality products and sustainability has made them a trusted partner for renowned automobile companies worldwide.
| Manufacturer | Specialization | Products | Expertise |
|————–|—————-|———-|———–|
| Foxconn | Electronics | Plastic parts, connectors, housings, components | Precision moulds with excellent surface finish |
| Haier Group | Household appliances | Moulds for refrigerators, washing machines, air conditioners | Durable, efficient, and highly precise moulds |
| BYD | Electric vehicles | Precision moulds for vehicle exteriors, interiors, mechanical components | Advanced technologies like CAD and CAM |
Note: Due to the word limit, only three manufacturers have been introduced here with a brief table. A more detailed comparison can be provided with additional words.
Background Research for injection mould factory manufacturers Companies in China, use qcc.com archive.org importyeti.com
When researching injection mould factory manufacturers in China, there are several useful websites to gather background information.
Qcc.com is a comprehensive Chinese company information database that provides detailed data on millions of companies. It can offer insights into a company’s registration information, financial data, management structure, and legal status. This platform allows users to search for injection mould factory manufacturers in China and obtain basic information about their operations.
Archive.org is a digital library that provides access to web pages that are no longer available on the internet. It can be used to explore the historical website versions of injection mould factory manufacturers in China. This can help gain insights into their past activities, product offerings, and changes in business strategies over time.
Importyeti.com is an online import data platform that provides detailed information about imports and exports. It allows users to search for specific products, such as injection moulds, and provides data on the companies involved in these transactions. This information can include the company’s name, contact details, and import or export volumes.
By utilizing these platforms, researchers can gather background information about injection mould factory manufacturers in China. Qcc.com can provide up-to-date company information, while Archive.org can provide historical insights. Importyeti.com can offer data on import and export activities related to injection moulds, helping to assess the global presence of these manufacturers.
Leveraging Trade Shows and Expos for injection mould factory Sourcing in China
Trade shows and expos offer an excellent opportunity for businesses to source injection mould factories in China. These events bring together a wide range of suppliers and manufacturers under one roof, making it convenient for firms looking to establish partnerships or procure products.
By attending trade shows and expos, businesses can effectively leverage several advantages for sourcing injection mould factories in China. Firstly, these events provide access to a large number of suppliers. Instead of individually searching for factories online, trade shows allow companies to interact directly with numerous potential partners in a short period. This saves both time and effort, enabling businesses to meet face-to-face with suppliers and discuss their specific requirements.
Secondly, trade shows and expos offer the chance to assess the quality of products and capabilities of the injection mould factories. Often, these events feature live demonstrations and samples, enabling businesses to personally evaluate the manufacturing processes, inspect the product quality, and even test prototype moulds. This firsthand experience allows for a more informed decision-making process when selecting a factory for sourcing needs.
Furthermore, trade shows provide opportunities for businesses to establish relationships with potential suppliers. Face-to-face interactions allow for better communication and understanding of the factory’s capabilities, production capacity, and reliability. Building personal connections with suppliers also fosters trust and may lead to stronger long-term partnerships.
To make the most out of trade shows and expos, businesses should come prepared by conducting thorough research beforehand. By identifying the specific injection mould factories they are interested in, companies can prioritize which booths to visit and maximize their time at the event. Additionally, businesses should bring along their requirements, product specifications, and any necessary documentation to expedite the sourcing process.
In conclusion, trade shows and expos serve as a valuable platform for businesses looking to source injection mould factories in China. These events offer a plethora of suppliers, the opportunity to assess product quality and capabilities, and the ability to establish personal connections. By effectively leveraging trade shows, businesses can streamline their sourcing process and find reliable and suitable partners for their injection moulding needs in China.
The Role of Agents and Sourcing Companies in Facilitating injection mould factory Purchases from China
Agents and sourcing companies play a crucial role in facilitating the purchase of injection mould factories from China. With their expertise and local knowledge, they act as intermediaries between buyers and manufacturers, ensuring a successful transaction. Their primary responsibilities include sourcing suitable suppliers, navigating cultural and language barriers, and overseeing the entire procurement process.
One of the key advantages of working with agents and sourcing companies is their extensive network of contacts within the Chinese manufacturing industry. They have established relationships with reliable injection mould factory suppliers, enabling them to quickly identify the most suitable options for their clients. This saves buyers significant time and effort in searching for and vetting potential suppliers themselves.
Moreover, agents and sourcing companies are well-versed in Chinese business practices and can effectively negotiate pricing and contractual agreements on behalf of buyers. They understand the local market conditions, enabling them to secure better deals and avoid pitfalls that international buyers may encounter.
Cultural and language barriers can often be challenging for international buyers looking to purchase from China. Agents and sourcing companies act as a bridge, effectively communicating requirements and specifications to the manufacturers. They ensure that all information is accurately relayed and understood, minimizing the risk of miscommunication and potential issues during production.
Another crucial role agents and sourcing companies play is quality control and inspection. They typically have a team of experts who conduct thorough inspections at various stages of the manufacturing process to ensure the product meets the buyer’s standards. This quality control process reduces the risk of receiving defective or subpar products.
Finally, agents and sourcing companies handle logistics and shipping arrangements, coordinating the transportation of goods from China to the buyer’s location. They are familiar with the necessary documentation and regulations, streamlining the entire shipping process and saving buyers from potential headaches.
In summary, agents and sourcing companies are integral to facilitating injection mould factory purchases from China. Through their expertise, networks, and knowledge of Chinese business practices, they simplify the entire procurement process, mitigating risks, and ensuring successful transactions for international buyers.
Price Cost Research for injection mould factory manufacturers Companies in China, use temu.com and 1688.com
When it comes to conducting price cost research for injection mold factory manufacturers in China, TEMU.com and 1688.com are two platforms that can provide valuable insights. These platforms offer a wide range of suppliers and manufacturers, enabling businesses to find competitive prices for their desired products.
TEMU.com is an online sourcing platform that allows users to connect directly with verified manufacturers. It provides a user-friendly interface that simplifies the process of finding suitable injection mold factory manufacturers. Users can search for specific products and suppliers, compare prices, and even request samples. TEMU.com also offers a secure payment system, making transactions more convenient and safe.
On the other hand, 1688.com, also known as Alibaba China, is a leading wholesale marketplace that connects buyers with Chinese manufacturers. It offers an extensive range of products, including injection molds, and allows users to browse through thousands of suppliers. The platform provides detailed information about the manufacturers, including their product range, certifications, and customer reviews. Buyers can communicate with suppliers directly, negotiate prices, and make secure transactions.
When conducting price cost research on these platforms, it is essential to keep the following points in mind:
1. Supplier Verification: Both TEMU.com and 1688.com perform supplier verification processes to ensure that the listed manufacturers are legitimate and reliable. It is crucial to check the supplier’s profile, certifications, and customer feedback before making any transactions.
2. Product Quality: While price is an important factor, it is equally important to consider the quality of products offered by different manufacturers. Look for suppliers with good customer reviews, certifications, and a track record of producing high-quality injection molds.
3. Quantity and Customization: Consider the quantity of molds required and whether customization is needed. Some manufacturers may offer discounts on bulk orders or be more flexible in accommodating customization requests.
4. Price Comparison: Use the search functions on TEMU.com and 1688.com to compare prices offered by different manufacturers. Consider factors such as production capacity, location, and the complexity of the mold to determine if the quoted prices are reasonable.
In conclusion, TEMU.com and 1688.com are valuable platforms for conducting price cost research for injection mold factory manufacturers in China. Utilizing these platforms can help businesses find competitive prices, connect with verified manufacturers, and ensure the overall quality of the products obtained.
Shipping Cost for injection mould factory import from China
The shipping cost for importing injection moulds from China can vary based on several factors. These include the weight and size of the shipment, the shipping method chosen, the distance between the supplier and the destination, and any additional services required.
For smaller shipments, air freight is a common choice. While it offers faster delivery, it can be more expensive compared to other options. The cost is typically calculated based on the weight or the volumetric weight of the shipment, whichever is greater. The volumetric weight takes into account the size of the package.
In contrast, for larger and heavier shipments, sea freight is usually more cost-effective. The cost is calculated based on the volume of the shipment or the container space required. It is important to note that sea freight has a longer transit time compared to air freight.
Additional services such as insurance, customs clearance, and handling fees may also impact the shipping cost. Insurance is advisable to protect against any potential damage during transit. Customs clearance fees depend on the regulations of the importing country, and handling fees may apply for services like loading and unloading at the ports.
To estimate the shipping cost accurately, it is recommended to obtain quotes from different shipping carriers or freight forwarders. They will consider the specific requirements of the injection mould shipment and provide the most suitable shipping solution.
Overall, the shipping cost for importing injection moulds from China can range significantly depending on various factors, and it is crucial to consider all these aspects to ensure a smooth and cost-effective transportation process.
Compare China and Other injection mould factory Markets: Products Quality and Price,Visible and Hidden Costs
China is a major player in the injection mould factory market, but it is essential to compare its products’ quality and price with other global markets.
In terms of product quality, China’s injection mould factories have made significant strides over the years. The country boasts a considerable number of skilled technicians and engineers who are well-versed in mould design and manufacturing. Chinese factories are capable of producing a wide range of products, from simple to complex, including automotive parts, consumer goods, and electronic components. However, it is important to note that quality can vary across different factories in China. Some manufacturers prioritize quality control measures, while others may prioritize lower costs and compromise on quality.
When it comes to price, China is known for its competitive pricing in the injection mould factory market. The lower production costs, including cheaper labor and raw materials, allow Chinese factories to offer more affordable prices compared to other markets. This advantage has made China a popular choice for businesses seeking cost-effective manufacturing solutions.
Visible costs, such as labor, raw materials, and transportation expenses, are generally lower in China compared to other markets. This is due to the country’s large workforce, abundant resources, and efficient logistical networks. However, it is crucial to consider hidden costs as well. Hidden costs may include intellectual property theft, quality issues, language and cultural barriers, and longer lead times. These hidden costs may offset some of the savings achieved through lower visible costs.
Other injection mould factory markets, such as Germany, Japan, and the United States, also excel in terms of product quality. These markets have established a strong reputation for precision engineering and high standards of craftsmanship. However, compared to China, these markets generally have higher production costs and therefore higher prices. Businesses looking for premium quality products may be willing to pay a premium price for the assurance of superior manufacturing standards.
In conclusion, China’s injection mould factory market offers competitive prices and improving product quality. However, it is important to thoroughly research and select reputable manufacturers to ensure consistent quality. While other markets may offer superior quality, they often come with higher price tags. Ultimately, businesses must weigh the trade-offs between quality, price, and visible and hidden costs when making decisions about injection mould factory markets.
Understanding Pricing and Payment Terms for injection mould factory: A Comparative Guide to Get the Best Deal
When it comes to selecting an injection mould factory, understanding pricing and payment terms is crucial to ensuring optimal cost-effectiveness and a smooth business transaction. This comparative guide aims to provide insights on how to negotiate the best deal while keeping the discourse concise within 300 words.
1. Pricing Structure: Start by understanding the injection mould factory’s pricing structure. Most factories determine prices based on factors such as material costs, machine and labor expenses, complexity of the mould, production volume, and lead time. Compare pricing structures across different factories to determine which one offers the most competitive rates.
2. Quotation Evaluation: Request detailed quotations from multiple injection mould factories. Examine the breakdown of costs, including raw material expenses, tooling costs, processing fees, and any additional charges. Pay attention to any hidden costs or terms that could impact the overall price.
3. Volume Discounts: Inquire about volume discounts offered by the factory. Many manufacturers provide reduced prices for larger production orders. Discuss your production requirements and negotiate discounts based on the expected volume.
4. Payment Terms: Pay close attention to the payment terms offered by the factory. Typical payment methods include partial payments in advance followed by the remaining balance after completion or a deposit upfront with the remaining balance paid upon delivery. Compare the payment terms provided by different factories and choose the one that aligns best with your financial capabilities and preferences.
5. Quality Assurance: Assess the quality assurance processes of each mold factory under consideration. High-quality molds may come at a slightly higher price but can reduce defects and maintenance costs in the long run. Prioritize factories that employ advanced quality control measures and have a proven track record of delivering reliable and durable molds.
6. Consider Ancillary Services: Some injection mould factories offer additional services that can add value to your order. These services may include design assistance, prototyping, post-moulding operations, or even warehousing and logistics support. Evaluate these services and determine if they align with your business needs. Factor in the associated costs and see if bundling services can provide cost savings.
By considering these factors, researching, and comparing different injection mould factories, you can make an informed decision, ultimately securing the best deal. Remember, cost-effectiveness should not compromise quality and reliability. Aim for a balance between reasonable pricing and maintaining high manufacturing standards.
Chinese Regulations and Industry Standards Certifications for injection mould factory,Import Regulations and Customs for injection mould factory from China
China has established various regulations and industry standards certifications for injection mould factories to ensure product quality, safety, and environmental compliance. These regulations aim to improve manufacturing practices and protect consumer interests. Here are some key regulations and certifications:
1. ISO Certifications: Many injection mould factories in China obtain ISO 9001:2015 certification, which demonstrates compliance with internationally recognized quality management systems. This certification ensures that the factory follows standardized processes, maintains quality control measures, and continuously improves production.
2. China Compulsory Certificate (CCC): CCC is a mandatory certification required for specific products, including certain types of injection moulds. It ensures that products meet safety, health, and environmental protection standards set by the Chinese government.
3. Environmental Regulations: Injection mould factories in China also need to adhere to environmental regulations, such as China’s Law on the Prevention and Control of Environmental Pollution Caused by Solid Wastes. This legislation sets guidelines for waste disposal, recycling, and pollution prevention.
4. Import Regulations: When importing injection moulds from China, foreign buyers should be aware of their country’s import regulations. This includes understanding any restrictions or licensing requirements for importing certain types of moulds and compliance with customs documentation.
5. Import Duties and Taxes: Importers must comply with the customs duties and taxes imposed by their country when importing injection moulds from China. These charges vary depending on the country and the value of the imported goods.
Foreign buyers should conduct thorough due diligence before partnering with an injection mould factory in China. This includes verifying certifications, compliance with regulations, and conducting factory audits to assess manufacturing capabilities and quality control systems. Additionally, engaging import-export agents or seeking legal advice can help navigate the intricacies of import regulations and customs procedures.
In summary, China has established certifications and regulations to ensure the quality, safety, and environmental compliance of injection mould factories. Importers should familiarize themselves with these regulations, as well as their country’s import regulations and customs requirements, to establish a successful partnership with Chinese suppliers.
Sustainability and Environmental Considerations in injection mould factory Manufacturing
In recent years, there has been an increasing focus on sustainability and environmental considerations in various industries, including injection mould factory manufacturing. The manufacturing sector is known to have a significant impact on the environment through the consumption of resources, energy, and generation of waste. Therefore, it is crucial for injection mould factories to adopt sustainable practices to minimize their ecological footprint.
One approach to promote sustainability is by implementing energy-efficient measures. Injection mould factory manufacturing involves the use of machinery and equipment that consume a significant amount of energy. By investing in energy-efficient technologies, such as high-efficiency motors and lighting systems, factories can reduce their energy consumption and carbon emissions.
Furthermore, waste management is another critical aspect of sustainable manufacturing. Injection mould factories generate various types of waste, such as plastic scraps, packaging materials, and chemical residues. To minimize waste, factories can implement recycling and reuse programs. This can involve recycling plastic scraps and reusing them in the production process, installing waste sorting systems, and collaborating with suppliers to reduce packaging waste.
Water conservation is also an important consideration in sustainable manufacturing. Injection mould factories often require water for cooling equipment and processes. By implementing water-saving measures, such as installing water-efficient cooling systems or reusing water in the manufacturing process, factories can reduce their water consumption and alleviate pressure on freshwater resources.
Additionally, the use of environmentally-friendly materials is crucial in sustainable manufacturing. Injection mould factories can choose to source materials from sustainable suppliers or opt for eco-friendly alternatives, such as biodegradable or recycled plastics. This can help reduce the environmental impact of the manufacturing process and promote the circular economy.
To summarize, sustainability and environmental considerations are gaining increasing importance in injection mould factory manufacturing. By adopting energy-efficient practices, implementing waste management strategies, conserving water, and using environmentally-friendly materials, factories can minimize their ecological footprint and contribute to a more sustainable future.
List The Evolution history of “injection mould factory”
The history of injection mould factories dates back several centuries. The concept of injection moulding, which involves injecting molten material into a mould to create products, was first experimented with by primitive civilizations using primitive tools. The ancient Egyptians, for example, used metal molds to create clay products.
However, it was not until the late 19th century that injection moulding became more sophisticated. In 1868, John Wesley Hyatt invented a new method for producing billiard balls by injecting celluloid into a mould. This breakthrough led to the establishment of the first injection mould factory in the United States. The factory produced various items, including buttons and combs, using the new injection moulding process.
Over the years, the technology and techniques used in injection mould factories continued to evolve. In the early 20th century, metal moulds began to be replaced by more durable and cost-effective materials like steel and aluminum. This allowed for mass production and lower costs.
The mid-20th century saw significant advancements in injection moulding technology. Plastics became the material of choice due to their versatility and low cost. Various types of injection moulding machines were developed, allowing for faster and more accurate production. Computer-controlled machines were introduced, making the process more automated and precise.
In recent decades, injection mould factories have continued to refine their operations. Advances in computer-aided design and simulation software have enabled better product development and mold design. Manufacturing processes have become more environmentally friendly, with a focus on reducing waste and energy consumption.
Today, injection mould factories play a pivotal role in various industries, such as automotive, electronics, and consumer goods manufacturing. They produce a wide range of plastic products, from tiny components to large items, with high precision and efficiency.
In summary, the evolution of injection mould factories spans centuries, from the primitive methods of ancient civilizations to the advanced and automated processes of today. Technological advancements have greatly improved efficiency, precision, and product quality, making injection moulding a vital manufacturing method in the modern world.
The Evolution and Market Trends in injection mould factory Industry
The injection mould factory industry has witnessed significant evolution and market trends over time. Technological advancements, changing consumer demands, and market competition have driven the industry to adapt and innovate.
One major evolution is the integration of computer-aided design (CAD) and computer-aided manufacturing (CAM) technologies in the injection moulding process. These tools have enhanced the accuracy and speed of designing and manufacturing moulds, reducing production time and costs. Additionally, advancements in materials used in mould making, such as high-strength steels and aluminum alloys, have improved the durability and performance of moulds.
Market trends in the injection mould factory industry have also been influenced by changing consumer preferences. There is a growing demand for customized and innovative products, which has led to an increased need for complex and intricate mould designs. This trend has necessitated the development of multi-cavity moulds and high-precision moulding technologies.
Another market trend is the emphasis on sustainability and environmental friendliness in the industry. Manufacturers are now opting for eco-friendly materials and processes, such as biodegradable plastics and energy-efficient machinery. This shift is driven by consumer awareness and government regulations aimed at reducing environmental impact.
Furthermore, globalization and the rise of e-commerce have impacted the injection mould factory industry. Manufacturers are facing increased competition from international suppliers, putting pressure on prices and quality standards. To remain competitive, companies are investing in automation and upgrading their facilities to improve efficiency and reduce production costs.
In conclusion, the injection mould factory industry has evolved in response to technological advancements, changing consumer preferences, and global market dynamics. The integration of CAD/CAM technologies, customization demands, sustainability concerns, and globalization have shaped market trends in the industry. To thrive in this competitive landscape, manufacturers need to stay abreast of these trends and continuously innovate to meet evolving market demands.
Custom Private Labeling and Branding Opportunities with Chinese injection mould factory Manufacturers
Chinese injection mold factory manufacturers offer a range of custom private labeling and branding opportunities for businesses looking to create their own unique products. With their expertise in injection molding, these manufacturers can help companies design and manufacture customized products that align with their brand image and meet their specific requirements.
By partnering with a Chinese injection mold factory manufacturer, businesses can take advantage of their extensive knowledge and experience in crafting high-quality molds. These manufacturers can create molds with intricate designs and precision, ensuring that each product manufactured is of the highest quality.
Additionally, Chinese injection mold factory manufacturers offer private labeling services, allowing businesses to incorporate their own logos, colors, and designs onto the products. This branding opportunity helps create a distinct identity for the products, enhancing brand recognition and promoting customer loyalty.
Moreover, working with Chinese manufacturers allows businesses to take advantage of cost-effective production capabilities. These manufacturers often offer competitive pricing due to lower labor and production costs in China. This cost efficiency enables businesses to invest in custom private labeling and branding without breaking the bank.
Furthermore, Chinese injection mold factory manufacturers can provide businesses with faster turnaround times. With their efficient production processes and experience in logistics, they can deliver products in a timely manner, ensuring businesses can meet customer demands and stay ahead of the competition.
In conclusion, partnering with Chinese injection mold factory manufacturers offers businesses custom private labeling and branding opportunities. These manufacturers leverage their expertise to create high-quality products, incorporate private labels, and provide cost-effective and efficient production processes. By capitalizing on these opportunities, businesses can effectively differentiate themselves in the market and build a strong brand identity.
Tips for Procurement and Considerations when Purchasing injection mould factory
When purchasing an injection mould factory, there are several key considerations and tips for procurement that should be kept in mind. These include:
1. Factory Capacity and Capability: It is important to evaluate the factory’s production capacity and capability to ensure it aligns with your business requirements. Factors such as machine capacity, process efficiency, and product range should be thoroughly reviewed.
2. Quality Control: Quality control measures are crucial to ensure the production of high-quality products. Evaluate the factory’s quality control procedures, certifications, and track record to ensure compliance with industry standards.
3. Technology and Machinery: Injection moulding technology is continually evolving, so it is essential to assess the factory’s machinery and technology level. Modern and well-maintained equipment can enhance productivity and reduce costs.
4. Supplier Network: Evaluate the factory’s existing supplier network to ensure access to quality raw materials and components. A comprehensive supplier base helps in ensuring a stable production process and reduces the risk of supply chain disruptions.
5. Cost and Pricing: Consider the factory’s pricing structure, including manufacturing costs, overheads, and profit margins. Compare the pricing with other suppliers to ensure competitive rates without compromising on quality.
6. Lead Times and Delivery: Evaluate the factory’s lead times and delivery capabilities. Reliable and consistent delivery schedules are necessary to meet customer demands and reduce inventory holding costs.
7. Scalability and Flexibility: Consider the factory’s capacity to handle future growth and adapt to changing market requirements. Flexibility in terms of production setup, tooling, and capacity expansion is crucial for long-term business success.
8. Financial Stability: Assess the financial stability and long-term viability of the factory. Review financial statements, credit ratings, and any pending legal disputes to ensure a healthy and sustainable business partnership.
9. Environmental and Sustainability Practices: Evaluate the factory’s environmental and sustainability practices to ensure compliance with local regulations and alignment with your company’s values.
10. Communication and Relationship: Effective communication and a good working relationship are critical for successful procurement. Assess the factory’s responsiveness, willingness to collaborate, and ability to communicate in your preferred language.
By considering these factors and following these tips, you can make an informed decision when purchasing an injection mould factory that aligns with your requirements, quality standards, and long-term business objectives.
FAQs on Sourcing and Manufacturing injection mould factory in China
Q: Why should I consider sourcing and manufacturing from an injection mould factory in China?
A: China is one of the largest manufacturing hubs in the world, offering competitive pricing, advanced technology, and a wide range of materials. Chinese injection mould factories have extensive experience and expertise, ensuring high-quality products at lower costs compared to other countries.
Q: What services do Chinese injection mould factories provide?
A: Injection mould factories in China offer a range of services, including product design, mould development and production, plastic injection molding, assembly, and packaging. They can also assist with logistics and shipping arrangements, providing a comprehensive solution for your manufacturing needs.
Q: How can I find a reliable injection mould factory in China?
A: Conduct thorough research on potential factories, considering factors such as their reputation, experience, certifications, and client reviews. Attend trade shows or use online platforms to connect with manufacturers and request samples or prototypes to evaluate their capabilities.
Q: Are Chinese injection mould factories equipped with advanced technology and machinery?
A: Yes, many Chinese injection mould factories have heavily invested in advanced technology and machinery to ensure precision and efficiency. They utilize CAD/CAM software, CNC machines, and robotic systems to enhance production capabilities and maintain consistency in product quality.
Q: What about quality control and product inspection?
A: Chinese injection mould factories prioritize quality control and often implement advanced inspection tools and techniques. They adhere to international quality standards and maintain rigorous quality control procedures throughout the production process, including regular inspections and tests.
Q: What are the advantages of sourcing and manufacturing from China?
A: The main advantages include competitive pricing, access to a wide range of materials, efficient production turnaround, and a vast supplier network. Additionally, Chinese factories are often flexible and can accommodate customization requirements or accommodate changes in production volumes.
Q: Are there any potential challenges or risks in sourcing from China?
A: Language and cultural differences may pose communication challenges. Intellectual property protection can be a concern, so it is essential to have proper legal agreements in place. There may also be a risk of counterfeits or substandard products, which is why a thorough vetting process and regular quality control checks are crucial.
Q: What is the typical lead time for manufacturing in China?
A: The lead time can vary depending on factors such as product complexity, order quantity, and factory capacity. However, Chinese injection mould factories generally offer relatively short lead times compared to other regions, with average durations ranging from a few weeks to a couple of months.
Q: What are the common shipping options for products manufactured in China?
A: Chinese factories can assist with shipping arrangements, offering options such as air freight, sea freight, or express delivery services. The best shipping method will depend on factors like product weight, urgency, cost considerations, and destination.
Q: Are there any minimum order quantities (MOQs) imposed by Chinese injection mould factories?
A: MOQs can vary among different factories, but many Chinese manufacturers are flexible and can accommodate small to medium-sized orders. It’s important to discuss MOQ requirements with the chosen factory and negotiate based on your specific needs.
Why contact sourcifychina.com get free quota from reliable injection mould factory suppliers?
Sourcifychina.com offers a unique opportunity for businesses to connect with reliable injection mold factory suppliers and obtain a free quota for their projects. There are several reasons why Sourcifychina.com provides this benefit to its customers.
Firstly, by offering a free quota, Sourcifychina.com aims to attract more businesses to its platform and encourage them to explore the services provided by the injection mold factory suppliers. This helps to expand their customer base and establish a strong network of businesses seeking manufacturing solutions.
Secondly, Sourcifychina.com understands that cost is a significant factor for businesses when choosing a supplier. By providing a free quota, they enable businesses to assess the pricing and feasibility of their projects without any financial commitment upfront. This helps businesses make informed decisions based on their budgetary requirements.
Additionally, by collaborating with reliable injection mold factory suppliers, Sourcifychina.com ensures that businesses receive high-quality manufacturing services. This increases customer satisfaction and builds trust in the platform’s capabilities.
Furthermore, Sourcifychina.com acknowledges that time is of the essence for businesses. Obtaining a free quota allows businesses to quickly evaluate the supplier’s capabilities and determine if they can meet their manufacturing needs. This fast-tracked process saves businesses valuable time and enables them to proceed with their projects promptly.
Lastly, by offering a free quota, Sourcifychina.com aims to foster long-term relationships between businesses and injection mold factory suppliers. The free quota serves as a starting point for businesses to gauge the supplier’s reliability, communication, and professionalism. It opens the door for further collaboration and potential partnerships.
In conclusion, Sourcifychina.com provides a free quota from reliable injection mold factory suppliers to attract businesses to their platform, help customers assess pricing, ensure high-quality manufacturing services, save time, and facilitate long-term relationships. This benefits both businesses and the platform in creating a mutually beneficial manufacturing ecosystem.