Introduce about knit line injection molding guide,Qulity,Cost,Supplier,Certification,Market,Tips,FAQ
Knit line injection molding is a unique manufacturing process that involves knitting together plastic material to create a strong and durable final product. This guide provides valuable information about the key aspects of knit line injection molding, including quality, cost, suppliers, certification, market trends, useful tips, and frequently asked questions.
Quality is a crucial consideration in knit line injection molding. By using advanced knitting techniques, manufacturers are able to produce products with improved strength, flexibility, and resistance to wear and tear. This process ensures that the knit lines are seamless and free from any defects, resulting in high-quality end products.
Cost is another important factor to consider. Knit line injection molding technology offers cost-effective solutions due to its ability to produce complex designs and intricate patterns. It helps reduce production time and materials, leading to lower manufacturing costs compared to other traditional molding methods.
Finding reliable suppliers for knit line injection molding is essential. It is recommended to choose suppliers with extensive experience in this field and a proven track record of delivering high-quality products. Thoroughly evaluating potential suppliers’ capabilities, machinery, and previous projects will help ensure a successful partnership.
Certification is crucial to confirm the quality and safety standards of knit line injection molded products. Suppliers and manufacturers should obtain appropriate certifications, such as ISO 9001, to ensure compliance with international quality management standards.
The market for knit line injection molded products is expanding rapidly. These products find applications in various industries, including automotive, aerospace, electronics, and consumer goods. With ever-increasing demand for lightweight and durable products, knit line injection molding is gaining popularity.
To optimize your knit line injection molding process, here are some useful tips:
1. Optimize knitting parameters to achieve the desired strength and aesthetics of the product.
2. Regularly inspect molds and machinery to prevent any potential defects or malfunctions.
3. Collaborate closely with suppliers or manufacturers to ensure a smooth production process.
Frequently Asked Questions (FAQ):
1. What materials can be used in knit line injection molding?
Knit line injection molding supports a wide range of materials, including thermoplastics like ABS, nylon, and polycarbonate.
2. How does knit line injection molding differ from traditional molding methods?
Knit line injection molding utilizes a knitting mechanism to create seamless patterns, whereas traditional molding methods involve filling a mold cavity with molten material.
In conclusion, knit line injection molding is a revolutionary manufacturing process that provides high-quality, cost-effective, and durable products. Evaluating suppliers, obtaining certifications, and staying informed about market trends are crucial elements for success in this field. By following these guidelines and taking advantage of valuable tips, one can optimize their knit line injection molding process and achieve desired outcomes.
Types of knit line injection molding
Knit line injection molding, also known as melt front knit lines or weld lines, occurs when two or more flow fronts of molten plastic meet and solidify during the injection molding process. This phenomenon is common in complex-shaped products or when the flow of molten plastic encounters obstacles or converges at certain points. Knit lines can significantly affect the structural integrity, mechanical properties, and aesthetics of the molded parts. To mitigate these effects, various types of knit line injection molding techniques have been developed.
1. Sequential Valve Gate: This technique involves injecting plastic into different sections of the mold sequentially, allowing each flow front to solidify before the next one is introduced. By controlling the timing and sequence of injections, the knit line can be strategically positioned in non-critical areas or hidden locations, minimizing its impact on the final product’s performance.
2. Hot Runner System: In this method, a network of heated channels delivers molten plastic from the injection unit to various locations in the mold. By controlling the flow rates and temperature profiles of the plastic in the channels, the melt fronts can be synchronized, reducing the formation of knit lines. Hot runner systems offer greater flexibility in mold design and help achieve uniform flow fronts.
3. Mold Design Optimization: By adjusting the mold design, it is possible to minimize knit line formation. This can be achieved through techniques such as the addition of ribs or flow leaders to guide the plastic flow and maintain a more consistent melt front. Additionally, reducing the complexity of the part’s geometry and avoiding obstacles or sharp corners can help minimize knit line formation.
4. Material Selection: The choice of plastic material can also play a significant role in reducing knit line formation. Certain materials, such as filled plastics or those with high melt viscosity, are more prone to forming knit lines. Selecting materials with good flow properties and lower melt viscosity can help reduce knit line visibility.
5. Processing Parameters: Optimal processing parameters, such as injection speed, temperature, and pressure, can influence the formation of knit lines. By carefully optimizing these parameters, it is possible to reduce knit line visibility and improve overall part quality.
In conclusion, knit line injection molding techniques involve a combination of mold design optimization, material selection, and process parameters optimization to minimize the formation of knit lines. Implementing these strategies can help produce high-quality molded parts with enhanced mechanical properties and aesthetics.
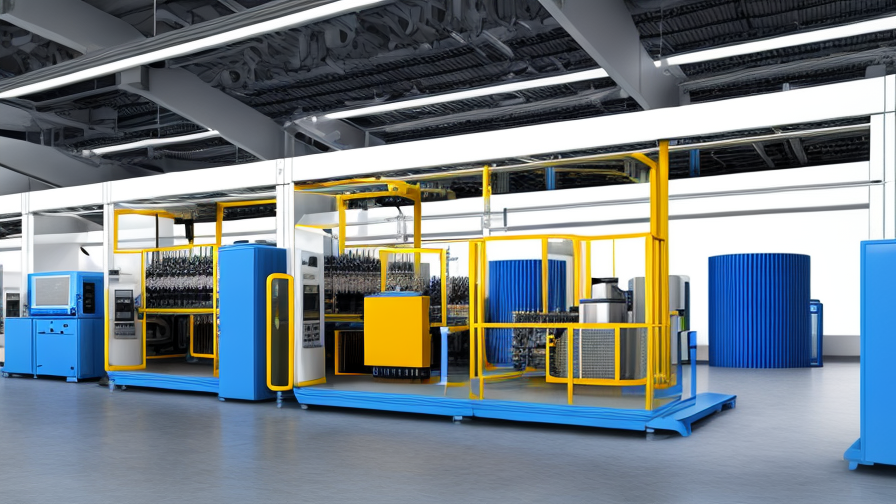
Pros and Cons of Using knit line injection molding
Knit line injection molding, also known as weld line injection molding, is a technique used in the manufacturing process of plastic parts. It involves joining two or more molten plastic flows to form a solid part. Like any manufacturing process, it has both advantages and disadvantages. Below are the pros and cons of using knit line injection molding:
Pros:
1. Increased production efficiency: Knit line injection molding allows for the simultaneous injection of multiple materials or colors, saving time and reducing production costs.
2. Versatile design possibilities: This technique enables the creation of complex molded parts by combining various materials or colors in specific areas, providing greater design flexibility.
3. Enhanced product quality: By minimizing or eliminating visible weld lines, knit line injection molding can improve the visual appearance and strength of the final product.
4. Cost-effective: Compared to other techniques that require multiple molds, knit line injection molding can be more cost-effective since it uses a single mold.
5. Reduced waste: With this technique, the injection points can be strategically placed, minimizing leftover materials and reducing waste.
Cons:
1. Weaker bond lines: The joining of molten plastic flows in knit line injection molding may result in weaker bond lines compared to a solid part. This can affect the overall strength and durability of the final product.
2. Limited material options: Certain materials may not be suitable for knit line injection molding due to compatibility issues. Some materials may not melt or bond together effectively, limiting the range of materials that can be used.
3. Increased complexity: Implementing knit line injection molding requires additional steps, such as carefully controlling the temperature, flow rate, and pressure to ensure proper bonding. This complexity can increase the risk of production errors or defects.
4. Reduced surface quality: In some cases, knit line injection molding may result in visible lines on the surface of the molded part. While they can often be minimized, they may still be present and impact the aesthetics of the product.
In conclusion, knit line injection molding offers advantages such as increased efficiency, versatile design possibilities, improved product quality, cost savings, and waste reduction. However, it also has disadvantages, including weaker bond lines, limited material options, increased complexity, and potentially reduced surface quality. Choosing this technique should be based on careful consideration of the specific requirements and constraints of the manufacturing process.
knit line injection molding Reference Specifications (varies for different product)
Knit line injection molding is a manufacturing process commonly used in the production of plastic products. It involves the use of a specialized injection molding machine that injects molten plastic resin into a mold cavity, which then cools and solidifies to form the desired product.
The knit line refers to the area where two or more flows of molten resin meet during the injection process. It is a seam-like line that can occur when the molten plastic cools and solidifies. The presence of knit lines can have implications on the strength, appearance, and functionality of the final product.
To ensure optimal results, various reference specifications need to be considered, which may vary depending on the specific product being manufactured. These specifications generally account for factors such as the type and grade of plastic resin used, mold design, processing conditions, and product requirements.
The choice of plastic resin is crucial in determining the performance of the finished product. Factors such as strength, flexibility, temperature resistance, and appearance are typically taken into account when selecting the appropriate resin. Additionally, the grade of the resin, which may be determined by its molecular weight, melt flow index, or other parameters, can impact the flow characteristics during injection molding.
Mold design is another critical aspect in knit line injection molding. The mold design should be carefully engineered to minimize the occurrence of knit lines. This can be achieved through techniques such as gate placement, mold venting, and proper cooling channel design. The mold should also be designed to accommodate any specific product requirements, such as surface textures, inserts, or overmolding.
Processing conditions, including injection speed, temperature, and pressure, play a crucial role in controlling knit line formation. Optimal processing parameters need to be determined to achieve the desired balance between filling the mold quickly and minimizing knit line occurrence.
Product requirements can vary widely and may include factors such as part appearance, mechanical strength, dimensional accuracy, and functional requirements. Each product may have specific specifications that need to be met during the injection molding process to ensure the product’s quality and performance.
In conclusion, knit line injection molding requires careful consideration of various reference specifications. These specifications encompass the choice of plastic resin, mold design, processing conditions, and product requirements. By following these specifications, manufacturers can achieve high-quality, functional, and aesthetically pleasing plastic products through the knit line injection molding process.
Applications of knit line injection molding
Knit line injection molding, also known as weld line injection molding, is a technique used in plastic injection molding processes. It involves the joining or knitting together of two or more flow fronts as they meet and solidify during the injection molding process. This technique is particularly useful when creating complex and intricate plastic parts. Here are some applications where knit line injection molding is commonly used:
1. Automotive industry: Knit line injection molding finds extensive use in the automotive industry for manufacturing various parts, such as exterior body panels, interior components, and engine parts. These parts often require complex geometries and multiple functionalities. Knit line injection molding allows for the creation of such parts by joining two or more flow fronts. It helps in achieving structural integrity and maintaining the desired aesthetics of the final part.
2. Electronic devices: Knit line injection molding is widely used in the production of electronic devices such as smartphones, tablets, and laptops. These devices often require precise and intricate designs with multiple functional components. Knit line injection molding enables the creation of such parts by combining different flow fronts. The technique helps in ensuring the structural integrity of the parts and eliminating the risk of weak points or failure.
3. Medical devices: The medical device industry extensively uses knit line injection molding in the manufacturing of various instruments, implants, and surgical devices. The technique allows for the creation of complex parts with intricate designs and specific requirements. Knit line injection molding helps in achieving precise dimensions, maintaining the desired surface finish, and ensuring the necessary functionality of the medical devices.
4. Consumer goods: Knit line injection molding is also applied in the production of consumer goods such as household appliances, toys, and packaging materials. These applications often demand intricate designs, multiple functionalities, and cost-effective production. Knit line injection molding allows for the creation of parts with complex geometries and functional requirements, ensuring the overall performance and durability of the consumer products.
Overall, knit line injection molding is a versatile technique that finds applications in various industries. It enables the production of intricate parts with complex designs, multiple functionalities, and structural integrity. The technique plays a crucial role in achieving cost-effective and efficient manufacturing processes for a wide range of products.
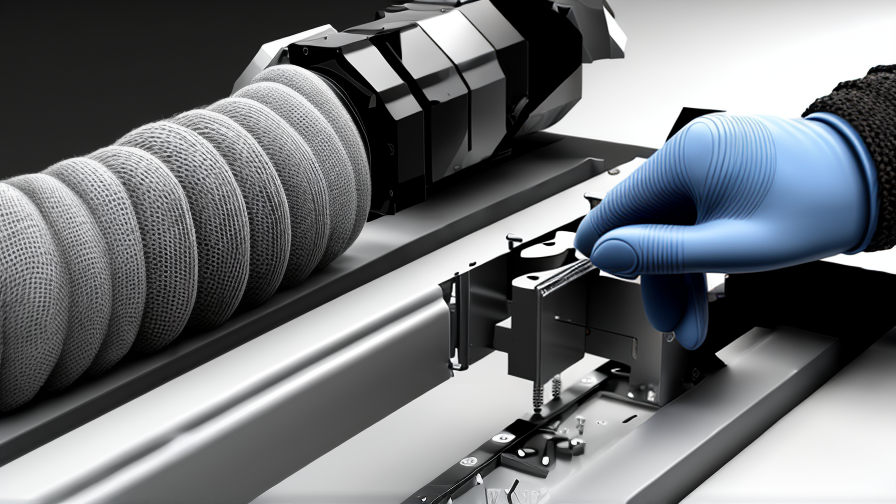
The Work Process and how to use knit line injection molding
Knit line injection molding is a manufacturing process used to create plastic parts with multiple flow paths or sections that meet and fuse together at a single point. These flow paths are created when the molten plastic is injected into a mold with different cavities, creating a junction or “knit line.”
The work process of knit line injection molding involves several steps. First, the mold is designed and fabricated, taking into consideration the location and design of the knit line. The mold typically consists of multiple cavities or sections that will be filled with molten plastic. The mold is then mounted onto an injection molding machine.
Next, the plastic material is selected based on its properties and suitability for the desired part. The material is melted and injected into the mold using the injection molding machine. The molten plastic flows through the different cavities, creating the desired part with multiple flow paths.
At the point where the flow paths meet, the plastic material cools and solidifies, forming the knit line. The knit line is the area where the separate flow paths fuse together. It is essential to ensure that the knit line has adequate strength and integrity for the intended application.
After the plastic has fully cooled and solidified, the mold is opened, and the finished parts are ejected. The parts may require additional finishing processes, such as trimming excess material or adding texture.
Knit line injection molding offers several advantages. It allows for the production of complex parts with multiple flow paths, reducing the need for assembly and increasing efficiency. The fusion of flow paths at the knit line also enhances the part’s strength and structural integrity.
In conclusion, knit line injection molding is a versatile manufacturing process used to create plastic parts with multiple flow paths. It involves designing a mold with different cavities, injecting molten plastic, and creating a knit line where the flow paths fuse together. This process allows for the production of complex parts with increased strength and efficiency.
Quality Testing Methods for knit line injection molding and how to control the quality
Knit line injection molding is a manufacturing process used to produce plastic parts with visible knit lines due to the flow of molten plastic meeting at a specific point. These knit lines can affect the strength, appearance, and overall quality of the final product. Therefore, it is essential to implement quality testing methods and control measures to ensure the desired outcome.
The following quality testing methods can be used for knit line injection molding:
1. Visual Inspection: A visual assessment is necessary to identify any visible knit lines, their locations, and their impact on the part’s aesthetics. This can be done by trained inspectors who check the parts against the specified design requirements.
2. Tensile Testing: Tensile strength testing helps evaluate a part’s ability to resist forces that could lead to knit line failure. Tensile testers apply pressure to the part until it reaches its breaking point, determining the material’s ultimate strength.
3. Dimensional Measurement: Precise dimensional measurements assist in ensuring that the knit lines do not deviate from the part’s intended specifications. This can be done using instruments such as calipers, coordinate measuring machines (CMM), or optical measurement systems.
4. X-Ray Inspection: X-ray inspection can detect any internal defects caused by knit lines, such as voids, air pockets, or incomplete bonding. X-ray imaging enables a comprehensive evaluation of the part’s internal structure, ensuring integrity.
To control the quality of knit line injection molding, the following measures are recommended:
1. Process Optimization: Fine-tuning the injection molding process parameters, including temperature, pressure, flow rate, and cooling time, allows for proper material flow and minimizes the occurrence of knit lines.
2. Material Selection: Choosing appropriate materials, additives, and fillers can help improve the melt flow properties, reducing the chances of knit line formation during the process.
3. Mold Design: Optimizing the mold design can minimize knit lines by ensuring proper gate placement, eliminating abrupt changes in part thickness, and providing adequate venting to allow proper gas escape during injection.
4. Regular Maintenance: Timely mold maintenance and cleaning, along with equipment calibration, help prevent defects and ensure consistent production.
5. Statistical Process Control (SPC): Monitoring and analyzing data collected during the manufacturing process can help identify any trends, anticipate issues, and maintain consistent quality output.
By implementing these quality testing methods and control measures, manufacturers can ensure that knit line injection molded parts meet the desired standards of strength, appearance, and functionality.
knit line injection molding Sample Policy and Post-Purchase Considerations for knit line injection molding from China
Sample Policy:
When it comes to knit line injection molding from China, it is essential to establish a clear sample policy with the manufacturer before proceeding with production. This policy should include the following considerations:
1. Provision of samples: Before placing a bulk order, request the manufacturer to provide samples of their knit line injection molded products. This will allow you to assess the quality, design, and functionality of the products before committing to a larger order.
2. Quality assurance: Specify in the sample policy that the provided samples should be representative of the final product’s quality. The samples should accurately reflect the manufacturing process, materials used, and desired specifications. This ensures that the final products meet your expectations.
3. Cost and time of sampling: Discuss with the manufacturer any costs associated with providing samples and the expected time frame for sample delivery. It is important to identify any potential expenses or delays beforehand to avoid misunderstandings and meet project deadlines.
4. Revisions and modifications: Clearly define the policy regarding revisions and modifications to samples. Specify how many rounds of revisions are allowed, who is responsible for any additional costs incurred, and the acceptable timeframe for making these revisions.
Post-Purchase Considerations:
After a successful purchase of knit line injection molded products from China, it is essential to consider the following aspects to ensure a smooth transition from purchase to usage:
1. Quality control: Regularly inspect the products upon arrival to check for any defects, damages, or deviations from the provided samples. If any issues are identified, communicate with the manufacturer immediately to address them and ensure proper resolution.
2. Communication with the manufacturer: Maintain an open line of communication with the manufacturer to address any concerns or questions that may arise during the usage of the products. Promptly inform them about any performance issues or necessary modifications.
3. Feedback and reviews: Provide constructive feedback to the manufacturer about your experience with their knit line injection molded products. This will allow them to improve their processes, products, and services, while also building a long-term relationship.
4. Warranty and support: Clarify the warranty period and customer support available from the manufacturer. In case of any defects or product failures within the defined warranty period, establish the required steps for submitting claims and obtaining replacements or repairs.
By setting clear sample policies and considering these post-purchase aspects, you can minimize potential issues, improve product quality, and maintain a reliable partnership with the China-based manufacturer of knit line injection molded products.
Sourcing knit line injection molding from China: Opportunities, Risks, and Key Players
Sourcing knit line injection molding from China offers numerous opportunities for businesses. The country has become a global manufacturing powerhouse, offering cost-effective production solutions. The Chinese market provides a vast pool of skilled labor and advanced infrastructure necessary for producing high-quality products. Outsourcing to China can significantly reduce manufacturing costs, resulting in increased profitability for companies.
However, there are also risks associated with sourcing from China. One major concern is intellectual property theft. China has a reputation for lax enforcement of patent and copyright laws, which can expose businesses to the risk of their designs being copied or counterfeited. It is crucial to work with reputable suppliers and take appropriate legal measures to protect intellectual property rights.
Another challenge when sourcing from China is the potential language and cultural barriers. Effective communication can be a hurdle, requiring businesses to invest in translation services or hire bilingual staff to ensure smooth collaboration with manufacturers.
Despite the risks, key players in the knit line injection molding industry in China offer compelling solutions. Tianjin Knitline Injection Molding Co., Ltd is one of the prominent manufacturers specializing in this field. They provide a wide range of knit line injection molding services, combining cutting-edge technology and skilled craftsmanship. Other key players include Shanghai JSOL Precision Mould Co., Ltd and Suzhou Xinwei Injection Molding Machinery Co., Ltd.
In conclusion, sourcing knit line injection molding from China presents opportunities for cost-saving and accessing a skilled workforce. However, businesses need to be cautious about the potential risks, such as intellectual property theft and communication barriers. Collaborating with reputable key players in the industry can mitigate these risks and ensure successful outsourcing endeavors.
How to find and select reliable knit line injection molding manufacturers in China,use google search manufacturers and suppliers
Finding reliable knit line injection molding manufacturers in China can be a daunting task, considering the vast number of options available. However, by following a few steps, you can successfully identify and select reliable manufacturers. One of the primary methods is to use Google search wisely to find manufacturers and suppliers. Here is a step-by-step guide to help you through the process.
1. Start by conducting a comprehensive search using relevant keywords, such as “knit line injection molding manufacturers in China.” This will yield a list of potential manufacturers.
2. Analyze their websites to gather essential information about their manufacturing capabilities, certifications, experience, clients they have worked with, and the types of products they specialize in. Look for any testimonials or case studies provided on their websites.
3. Make a list of potential manufacturers that meet your requirements and seem reliable based on the information gathered from their websites.
4. Use online directories and platforms specializing in connecting manufacturers and suppliers, such as Alibaba or Made-in-China. These platforms provide detailed company profiles, product lists, reviews, and ratings from previous clients, which can help in assessing the manufacturers’ reliability.
5. Pay attention to the manufacturer’s experience and specialization. Look for manufacturers who have been in the industry for a significant period as it indicates their stability and expertise.
6. Check if the manufacturer has the necessary certifications and quality control processes in place, such as ISO 9001. This ensures that they adhere to international quality standards and can deliver the desired quality of knit line injection moldings.
7. Contact the shortlisted manufacturers and request quotations, samples, or product catalogs. Evaluate their responsiveness, willingness to provide information, and ability to communicate in English effectively. Prompt and professional communication signifies their reliability and commitment to customer satisfaction.
8. Consider visiting their manufacturing facilities or arranging video conferences to gain deeper insights into their capabilities, infrastructure, and the overall manufacturing process.
9. Seek references from other clients or industry professionals who have worked with the manufacturers you are considering. Their feedback and experiences can help you make an informed decision.
10. Lastly, compare the quotations, sample quality, overall communication, and past performance of different manufacturers before making a final selection.
By diligently following these steps and utilizing Google search along with other online resources, you can identify reliable knit line injection molding manufacturers in China that align with your requirements.
How to check knit line injection molding manufacturers website reliable,use google chrome SEOquake check if ranking in top 10M
To determine the reliability of a knit line injection molding manufacturer’s website, you can follow these steps:
1. Use Google Chrome: Open the manufacturer’s website using Google Chrome as your browser. Chrome offers various built-in tools and extensions that can aid in evaluating a website’s trustworthiness.
2. Install SEOquake Extension: Install the SEOquake extension for Google Chrome if you do not already have it. SEOquake provides valuable information about a website’s ranking, traffic, and overall SEO performance.
3. Check Alexa Ranking: Once SEOquake is installed, click on its icon at the top-right corner of your browser. It will display a range of metrics related to the website you’re visiting. Look for the Alexa Rank, which offers an approximation of the website’s popularity compared to others. A lower rank usually indicates higher website traffic and credibility.
4. Analyze Traffic Data: SEOquake also provides estimated traffic figures. Examine the number of unique visitors per month or daily page views to get a sense of the website’s popularity and reach. A higher number suggests a more reputable website.
5. Verify Backlinks: Another SEOquake feature is the Backlinks tab, which displays the number of websites that link back to the manufacturer’s site. A substantial number of high-quality backlinks signifies the website’s reliability and authority within the industry. A lack of backlinks or low-quality ones might raise doubts about the website’s trustworthiness.
6. Evaluate Overall Design and Information: Besides using SEOquake, carefully assess the website’s overall design, content quality, and relevance. A professional-looking layout, comprehensive information about the manufacturing process, product details, and contact information are positive indicators of reliability.
7. Read Reviews and Testimonials: Look for reviews and testimonials on other reputable platforms or directories about the manufacturer. Genuine positive feedback from previous customers can further confirm the reliability of their services.
Remember to take all these factors into account collectively rather than relying solely on one indicator. By utilizing SEOquake, examining website traffic, design, backlinks, and customer feedback, you can gain a comprehensive overview of the knit line injection molding manufacturer’s website’s reliability.
Top 10 knit line injection molding manufacturers in China with each 160 words introduce products,then use markdown create table compare
1. Jabil Circuit, Inc.: With over 50 years of experience in electronics manufacturing, Jabil is a leading global manufacturer of knit line injection molding products. They offer a wide range of services including design, prototyping, and production of complex molded components. Their advanced technologies ensure precision and high-quality products, meeting customer specifications.
2. Flex Ltd.: Flex is a renowned knit line injection molding manufacturer in China. They specialize in creating innovative solutions for industries such as automotive, healthcare, and consumer electronics. Their expertise lies in designing and manufacturing complex, high-volume components with excellent quality and efficiency.
3. Foxconn Technology Group: Foxconn is a prominent player in the knit line injection molding industry. Their diversified product portfolio includes telecommunication equipment, computer peripherals, and consumer electronics. They are known for their state-of-the-art manufacturing facilities and commitment to delivering top-quality products.
4. Sanmina Corporation: Sanmina is a trusted manufacturer of knit line injection molding products, focusing on the medical, aerospace, and defense sectors. Their advanced capabilities include precision molding, cleanroom manufacturing, and value-added services. They leverage their extensive experience to meet the stringent requirements of these industries.
5. Celestica Inc.: Celestica is a leading provider of knit line injection molding solutions, offering a comprehensive range of services. They excel in manufacturing complex, high-precision components for industries like aerospace, healthcare, and industrial equipment. With a global presence, they ensure efficient delivery and superior quality products.
6. Benchmark Electronics, Inc.: Benchmark Electronics specializes in knit line injection molding for industries such as aerospace, defense, and medical. They provide end-to-end services, from design and prototyping to full-scale production. Their advanced manufacturing capabilities and strict quality control ensure optimal performance and reliability.
7. Plexus Corp.: Plexus is known for its exceptional knit line injection molding services, catering to industries like healthcare, industrial, and defense. Their expertise lies in designing and manufacturing complex, high-reliability products. They offer value-added services such as supply chain management, testing, and validation.
8. Wistron Corporation: Wistron is a leading knit line injection molding manufacturer, offering comprehensive solutions for electronics, communication, and consumer products. They leverage their advanced manufacturing capabilities to deliver high-quality, cost-effective products. Their global presence ensures efficient supply chain management and timely delivery.
9. SIIX Corporation: SIIX specializes in knit line injection molding, providing end-to-end solutions for industries like automotive, industrial, and consumer electronics. Their expertise lies in complex, high-volume production with stringent quality standards. They offer value-added services such as supply chain management and product testing.
10. Venture Corporation Limited: Venture Corporation is a well-established knit line injection molding manufacturer, serving industries like medical, automotive, and industrial equipment. They offer a wide range of services from design and prototyping to full-scale production. With their strong technical capabilities, they ensure reliable and high-quality products.
Comparison Table:
| Manufacturer | Core Industries | Specializations |
|—————————-|——————————-|————————-|
| Jabil Circuit, Inc. | Electronics | Design, prototyping |
| Flex Ltd. | Automotive, healthcare | Complex high-volume |
| Foxconn Technology Group | Telecommunications | State-of-the-art |
| Sanmina Corporation | Medical, aerospace, defense | Cleanroom manufacturing |
| Celestica Inc. | Aerospace, healthcare | Precision components |
| Benchmark Electronics, Inc. | Aerospace, defense, medical | End-to-end services |
| Plexus Corp. | Healthcare, industrial, defense | High-reliability |
| Wistron Corporation | Electronics, communication | Cost-effective |
| SIIX Corporation | Automotive, industrial | Complex high-volume |
| Venture Corporation Limited | Medical, automotive, industrial | Reliable, high-quality |
These top 10 knit line injection molding manufacturers in China offer a diverse range of services and cater to various industries. Each manufacturer has its unique specialization, ensuring high-quality products and efficient manufacturing processes.
Background Research for knit line injection molding manufacturers Companies in China, use qcc.com archive.org importyeti.com
When conducting background research on knit line injection molding manufacturers in China, several resources can be utilized, such as qcc.com, archive.org, and importyeti.com. These platforms provide valuable information about companies’ backgrounds, histories, and capabilities.
Qcc.com is a popular Chinese website that offers business information about various companies in China. It provides details such as company registration data, ownership structure, management information, financial status, and more. By accessing qcc.com, one can retrieve important background information about knit line injection molding manufacturers, including their legal status, registered capital, and contact details.
Archive.org is a digital library that allows users to access and view snapshots of previous versions of websites. It can be used to track changes in a company’s website over time, providing insights into its history, products, and services. By searching for the websites of specific knit line injection molding manufacturers, valuable information can be gathered from archived versions of their sites on archive.org.
Importyeti.com is an online directory that provides information about companies involved in international trade, including importers, exporters, and manufacturers. One can search for knit line injection molding manufacturers on this platform to obtain details such as company profiles, product descriptions, contact information, and even shipping records, which can help in assessing their credibility and reliability.
Considering the limited word count of 300, it is crucial to focus on the most important aspects when conducting background research on knit line injection molding manufacturers in China. These resources provide a comprehensive overview of companies, enabling users to gather relevant information swiftly and efficiently.
Leveraging Trade Shows and Expos for knit line injection molding Sourcing in China
Trade shows and expos are excellent platforms for sourcing knit line injection molding services in China. These events bring together suppliers, manufacturers, and industry professionals under one roof, providing businesses with the opportunity to explore and establish connections with potential partners.
Attending trade shows and expos dedicated to injection molding and textile manufacturing allows companies to gain firsthand experience of the latest technologies, advancements, and trends in the industry. By interacting with exhibitors and manufacturers, businesses can learn about the capabilities, quality standards, and production processes of various knit line injection molding suppliers in China.
These events also offer the chance to compare different suppliers, evaluate their products and services, and make informed decisions about potential partnerships. Directly engaging with suppliers allows businesses to examine the quality of their products, discuss customization options, negotiate pricing, and understand their ability to meet specific requirements.
Furthermore, trade shows and expos provide a networking platform where businesses can connect with industry experts, gain insights through seminars and educational programs, and exchange knowledge with other professionals. These interactions can significantly contribute to building relationships, sharing best practices, and learning about successful strategies and experiences in sourcing knit line injection molding services in China.
To make the most out of trade shows and expos, it is essential to plan ahead and set clear objectives. Researching and identifying relevant events, understanding the exhibiting companies and their specialties, and preparing a list of targeted suppliers will maximize the effectiveness of attending these events. Additionally, having a clear understanding of one’s own requirements and expectations will enable businesses to effectively communicate and evaluate potential suppliers.
In conclusion, trade shows and expos offer a comprehensive platform for sourcing knit line injection molding services in China. By attending these events, businesses can explore a wide range of suppliers, evaluate their products and services, network with industry professionals, and gain valuable insights, ultimately facilitating successful sourcing ventures.
The Role of Agents and Sourcing Companies in Facilitating knit line injection molding Purchases from China
Agents and sourcing companies play a crucial role in facilitating knit line injection molding purchases from China. With their expertise and knowledge of the Chinese market, these intermediaries act as a bridge between buyers and manufacturers, ensuring a smooth and efficient sourcing process.
One of the main advantages of using agents and sourcing companies is their ability to locate and evaluate suitable manufacturers. They have an extensive network of reliable suppliers, making it easier for the buyer to find the best-fit manufacturer for their knit line injection molding needs. This saves buyers significant time and effort in searching for manufacturers themselves.
Additionally, these intermediaries are well-versed in the local business culture and regulations. They can navigate the complexities of language barriers, negotiate prices, and establish mutually beneficial agreements with Chinese manufacturers. They also possess in-depth knowledge of product quality standards and can conduct thorough quality control inspections during the manufacturing process. This helps to minimize the risk of receiving subpar or defective products.
Agents and sourcing companies also handle logistics and shipping arrangements. They have the necessary connections and expertise to handle transportation, customs clearance, and documentation, ensuring that the ordered products reach the buyer’s destination in a timely and organized manner. This saves the buyer from the hassle of dealing with complex shipping procedures.
Furthermore, these intermediaries provide valuable support throughout the entire purchase process. They assist with sample approval, production monitoring, and even act as a mediator in case of any conflicts or disputes with the manufacturer. This fosters a transparent and reliable working relationship between the buyer and the manufacturer.
In conclusion, agents and sourcing companies serve as valuable facilitators in the procurement of knit line injection molding products from China. Their extensive networks, knowledge of the local market, and expertise in logistics and quality control contribute to a smooth and successful sourcing experience for buyers.
Price Cost Research for knit line injection molding manufacturers Companies in China, use temu.com and 1688.com
When conducting price cost research for knit line injection molding manufacturers in China, two popular online platforms to consider are temu.com and 1688.com. These platforms provide a wide range of options and access to manufacturers that specialize in injection molding.
Temu.com is an online marketplace that connects buyers and suppliers. It offers a comprehensive search feature, allowing users to filter through a variety of criteria such as location, product category, and certifications. By using temu.com to search for knit line injection molding manufacturers, users can compare prices and evaluate the quality and capabilities of different suppliers.
1688.com, on the other hand, is a business-to-business platform owned by Alibaba Group. It is particularly popular in China and provides access to a large network of manufacturers and suppliers. Users can search for knit line injection molding manufacturers on 1688.com, and the platform provides detailed information about each supplier, including their product range, manufacturing capabilities, and pricing.
When using these platforms for price cost research, it’s important to follow some best practices. Firstly, clearly define your requirements and specifications for the knit line injection molding project. This will help you accurately assess the pricing provided by manufacturers.
Secondly, reach out to multiple manufacturers to collect quotes and compare them. By doing so, you can gain a better understanding of the market average and negotiate more effectively.
Lastly, keep in mind that factors such as order quantity, design complexity, and material specifications can significantly impact the final pricing. Therefore, it is advisable to provide detailed information to the manufacturers to obtain the most accurate price estimates.
In conclusion, temu.com and 1688.com are valuable resources for conducting price cost research for knit line injection molding manufacturers in China. By leveraging the features and capabilities of these platforms, you can effectively compare prices, evaluate suppliers, and find the best manufacturing partner for your specific needs.
Shipping Cost for knit line injection molding import from China
When importing knit line injection molding products from China, it is essential to consider the shipping costs involved. Several factors influence the overall shipping expenses, including the size and weight of the shipment, the chosen shipping method, and any additional services required.
Typically, knit line injection molding products are bulky and heavy, thus affecting the shipping costs. The size and weight of the shipment determine the shipping rates charged by carriers. It is advisable to optimize the packaging to reduce any unnecessary weight and dimensions, as this can help mitigate transportation expenses.
The shipping method chosen also affects the costs. Air freight is generally faster but more expensive compared to ocean freight. For knit line injection molding products, considering the weight and size, shipping by sea may be more cost-effective. It is crucial to plan the lead time accordingly when opting for ocean freight, as it generally takes longer than air freight.
To ensure a smooth import process, it is recommended to engage with a reliable freight forwarder who can negotiate competitive rates. Freight forwarders can also assist in arranging customs clearance and handling any necessary documentation. They have established relationships with carriers, ensuring better pricing options.
Additional services such as insurance, customs duties, and taxes should also be considered when calculating the overall shipping costs. Insurance coverage is advisable to protect the shipment against any damages or losses that may occur during transit. Import duties and taxes vary by country and are typically based on the import value of the products.
To summarize, the shipping cost for importing knit line injection molding products from China depends on factors such as size, weight, shipping method, and additional services required. By optimizing packaging, choosing the right freight forwarder, and considering sea freight as a cost-effective option, importers can aim to keep shipping expenses within a reasonable range.
Compare China and Other knit line injection molding Markets: Products Quality and Price,Visible and Hidden Costs
China has emerged as a dominant player in the knit line injection molding market, competing with other markets around the world. When comparing China with other markets, several factors come into play, including product quality, price, and visible and hidden costs.
Product Quality:
China has made significant strides in improving product quality in recent years. However, when compared to other markets such as Germany, Japan, and the United States, there can still be variations in quality standards. These countries have a long-standing reputation for producing high-quality products, often adhering to strict quality control measures. Customers who prioritize premium quality may still prefer products from these markets over China.
Price:
China has typically been known for its competitive pricing, offering lower manufacturing costs compared to other markets. This cost advantage has made China an attractive destination for businesses looking to lower production expenses. However, in recent years, other markets have also become more competitive, offering cost-effective manufacturing solutions. For example, countries like Vietnam, India, and Mexico are emerging as viable alternatives to China due to their lower labor costs and improving infrastructure.
Visible and Hidden Costs:
While China may offer lower manufacturing costs, it is essential to consider both visible and hidden costs. Transportation costs, import duties, and tariffs can significantly impact the final cost of the product. Additionally, intellectual property concerns, product recalls, and quality control issues may lead to hidden costs in production. Other markets that prioritize customer satisfaction often invest heavily in quality control measures, reducing the chances of such hidden costs.
In conclusion, China has become a major player in the knit line injection molding market, offering competitive pricing and improving product quality. However, compared to other markets like Germany, Japan, and the United States, China may still have some catching up to do in terms of quality standards. Additionally, businesses need to carefully consider visible and hidden costs associated with manufacturing in China, such as transportation costs, import duties, and product recalls. As other markets, including Vietnam, India, and Mexico, become more competitive in terms of pricing and quality, businesses can explore a broader range of options beyond China for their manufacturing needs.
Understanding Pricing and Payment Terms for knit line injection molding: A Comparative Guide to Get the Best Deal
Pricing and payment terms play a crucial role in securing the best deal for your knit line injection molding project. As such, it is essential to understand these aspects to ensure a successful and cost-effective collaboration with your manufacturing partner. This comparative guide will provide you with key insights into negotiating pricing and payment terms to obtain the most favorable arrangement.
When discussing pricing, it is important to consider various factors that can influence the overall cost. These factors may include the complexity of the design, the size and quantity of the order, material selection, production timeline, and additional services such as packaging and shipping. It is advisable to request quotes from different suppliers to compare costs and analyze the breakdown of pricing components. This way, you can identify any discrepancies or hidden charges, enabling you to make an informed decision.
Payment terms are equally vital, as they dictate the financial agreement between you and the manufacturer. Different suppliers may offer diverse payment options, including full upfront payment, milestone-based payments, or a percentage upfront with the remainder upon completion. Evaluate these options in accordance with your cash flow capabilities and the level of trust you have established with the supplier. You may also negotiate the payment terms to better suit your needs and mitigate any potential risks, such as late deliveries or defective products.
Furthermore, consider the overall financial stability and reputation of the supplier. A financially secure and reputable manufacturer is more likely to provide reliable pricing and payment terms, ensuring a smooth production process. It is advisable to review customer feedback, certifications, and conduct due diligence to assess their track record.
Additionally, don’t overlook the importance of establishing clear communication channels and a strong working relationship with your supplier. Effective communication can lead to better negotiation outcomes and resolve any potential pricing or payment conflicts more easily.
To summarize, understanding pricing and payment terms for your knit line injection molding project is crucial to obtain the best deal. Research, compare quotes, analyze pricing components, and negotiate payment terms to align with your financial capacity and mitigate risks. Moreover, prioritize working with reputable suppliers to ensure transparency and reliability throughout the manufacturing process.
Chinese Regulations and Industry Standards Certifications for knit line injection molding,Import Regulations and Customs for knit line injection molding from China
China has specific regulations and industry standards certifications for knit line injection molding. These regulations aim to ensure product quality, safety, and conformity with industry standards. Manufacturers in China must obtain the necessary certifications to export their knit line injection molding products.
One of the key certifications required in China is the ISO 9001:2015 certification. This certification demonstrates that the manufacturer has a quality management system in place and follows international standards for design, development, production, and delivery of knit line injection molding products.
In addition to ISO 9001:2015, manufacturers may also obtain other certifications such as ISO 14001 for environmental management systems and ISO 45001 for occupational health and safety management systems. These certifications demonstrate the manufacturer’s commitment to sustainable and safe production practices.
When importing knit line injection molding products from China, there are certain import regulations and customs procedures that need to be followed. Importers should ensure compliance with their country’s import regulations, including product safety standards and labeling requirements. It is essential to verify that the Chinese manufacturer has obtained the necessary certifications and that their products meet the regulatory requirements in the importing country.
Customs documentation, such as commercial invoices, packing lists, and bills of lading or airway bills, must be accurately completed to facilitate smooth customs clearance. Importers should work closely with their freight forwarders or customs brokers to ensure all necessary documents are prepared and submitted correctly.
It is important to note that these regulations and customs procedures can be subject to change, so importers should stay updated and informed about any new requirements or updates from both Chinese regulatory authorities and the importing country’s customs authorities.
In conclusion, to import knit line injection molding products from China, importers must ensure that the Chinese manufacturer has the necessary certifications, comply with import regulations and customs procedures, and work closely with their freight forwarders or customs brokers to ensure a smooth import process.
Sustainability and Environmental Considerations in knit line injection molding Manufacturing
In today’s world, sustainability and environmental considerations have become increasingly important in various industries, including manufacturing. The knit line injection molding process is no exception, as it involves the production of plastic parts and components.
One of the key sustainability aspects in knit line injection molding manufacturing is the choice of materials. Using eco-friendly and recycled materials can significantly reduce the carbon footprint of the manufacturing process. Manufacturers can opt for materials that have a lower environmental impact, such as biodegradable plastics or those made from renewable resources.
Another crucial consideration is energy consumption. Energy-efficient machinery and processes can help minimize the environmental impact associated with knit line injection molding. Implementing energy-saving measures, such as using automated systems and optimizing production schedules, can reduce energy usage during the manufacturing process.
Waste management is another critical aspect of sustainability. Reducing, reusing, and recycling waste generated during knit line injection molding can help minimize environmental pollution. Implementing proper waste disposal systems and encouraging responsible waste management practices can contribute to a more sustainable manufacturing process.
Furthermore, water usage should be carefully monitored and minimized in knit line injection molding manufacturing. Implementing water-saving techniques, such as reusing water and installing efficient cooling systems, can help reduce water consumption and minimize the impact on local water resources.
To enhance sustainability, manufacturers can also focus on optimizing transportation and logistics. Reducing the distance traveled by raw materials and finished products can significantly decrease carbon emissions. Implementing supply chain strategies that prioritize local sourcing and efficient transportation can contribute to a more environmentally friendly manufacturing process.
In conclusion, sustainability and environmental considerations should be at the forefront of knit line injection molding manufacturing. By focusing on material selection, energy efficiency, waste management, water usage, and transportation optimization, manufacturers can reduce their environmental impact and contribute to a more sustainable future.
List The Evolution history of “knit line injection molding”
Knit line injection molding, also known as weld line injection molding, is a specialized technique used in plastic injection molding to improve product quality and strength. It is a process that minimizes the visible lines or seams that appear on the surface of injection molded products.
The evolution of knit line injection molding can be traced back to the early days of traditional injection molding in the mid-20th century. Initially, injection molding processes resulted in visible seams or weld lines due to the flow of molten plastic around the mold inserts. These lines weakened the structural integrity of the products and affected their aesthetics.
In the 1970s, manufacturers started experimenting with various methods to reduce or eliminate these seams. They began incorporating technologies like hot runner systems, which allowed for more precise control of the plastic flow, minimizing the formation of knit lines. This improvement significantly enhanced product quality, especially for high-demand industries like automotive and electronics.
Further advancements in mold design and material engineering led to the development of more sophisticated techniques in the 1990s. Mold flow analysis and computer-aided engineering (CAE) simulations became critical tools for optimizing mold designs and identifying potential knit line issues before production. Manufacturers could now predict and eliminate knit lines, ensuring better product performance.
In recent years, process improvements and innovations in injection molding machinery have further enhanced knit line injection molding. Advanced equipment allows for better control of melt flow and cavity pressure, reducing the occurrence of knit lines. The use of specialized additives and blending techniques also optimizes material performance, resulting in stronger and more visually appealing products.
Today, knit line injection molding has become a standard process used in various industries, including automotive, electronics, consumer goods, and medical devices. Its evolution has been driven by the need for higher quality, more durable products with improved aesthetics. As technology continues to advance, the focus will be on further refining the process, reducing cycle times, and increasing production efficiency while maintaining product integrity.
The Evolution and Market Trends in knit line injection molding Industry
The knit line injection molding industry has seen significant evolution and market trends in recent years. Knit line injection molding is a manufacturing process used to create complex plastic parts by injecting molten plastic into a mold cavity.
One of the key evolution in this industry is the development of advanced machinery and technology. Manufacturers are continuously investing in research and development to improve the precision and efficiency of the injection molding process. This has led to the introduction of sophisticated equipment, such as computer numerical control (CNC) machines, which can produce intricate designs with high accuracy and repeatability.
Another important evolution is the focus on sustainability and environmental impact. As the world becomes more conscious of the need for eco-friendly manufacturing practices, knit line injection molding companies are adapting their processes to reduce waste and energy consumption. This includes implementing recycling and waste reduction programs, using biodegradable or recycled materials, and optimizing production techniques to minimize resource usage.
In terms of market trends, there is a growing demand for lightweight and durable plastic components in various industries, including automotive, electronics, and consumer goods. This trend is driving the adoption of knit line injection molding, as it allows for the production of complex and lightweight parts that offer improved performance and cost-effectiveness.
Another market trend is the increasing use of automation and robotics in the injection molding process. Automation helps to streamline production, reduce labor costs, and improve overall efficiency. With the integration of robotics, manufacturers can achieve higher production volumes and faster cycle times, enabling them to meet the growing demand for plastic parts.
Furthermore, customization and personalization have become key drivers in the market. Consumers are increasingly seeking products that cater to their unique preferences and needs. Knit line injection molding allows for the production of highly customized plastic parts, enabling manufacturers to meet this demand and gain a competitive edge.
In conclusion, the knit line injection molding industry has evolved significantly in response to technological advancements, sustainability concerns, and changing market demands. With a focus on precision, sustainability, and customization, this industry is poised for continued growth and innovation in the coming years.
Custom Private Labeling and Branding Opportunities with Chinese knit line injection molding Manufacturers
Chinese knit line injection molding manufacturers offer a range of custom private labeling and branding opportunities for businesses looking to establish their own product lines. With decades of experience in the industry, these manufacturers have developed expertise in creating high-quality products that meet international standards.
With the ability to provide custom private labeling, businesses can have their logo, brand name, and other unique identifiers printed or embossed on the products. This allows for easy brand recognition and a professional look, helping businesses establish a distinctive identity in the market.
Moreover, Chinese manufacturers offer extensive branding opportunities to businesses. They can help design and create custom packaging for the products, including boxes, labels, and inserts. This allows businesses to present their products in a visually appealing and cohesive manner, further enhancing their brand image.
Chinese knit line injection molding manufacturers also offer flexibility in product customization. They can work with businesses to develop unique product specifications, colors, materials, and finishes. This ensures that businesses can create products that align with their brand’s values and customer preferences, ultimately enhancing brand loyalty.
Furthermore, partnering with Chinese manufacturers for private labeling and branding offers cost advantages. Chinese manufacturers often offer competitive pricing due to their access to raw materials, advanced manufacturing processes, and economies of scale. This allows businesses to have high-quality custom-branded products at affordable prices, maximizing profitability.
Overall, Chinese knit line injection molding manufacturers provide excellent opportunities for businesses seeking custom private labeling and branding. With their expertise, flexibility, cost advantages, and ability to deliver high-quality products, these manufacturers are ideal partners to help businesses establish their own product lines and create a strong brand presence in the market.
Tips for Procurement and Considerations when Purchasing knit line injection molding
When conducting the procurement of knit line injection molding, there are several tips and considerations to keep in mind:
1. Define your requirements: Clearly establish your needs and specifications for the knit line injection molding. Consider factors such as the desired quantity, materials to be used, color requirements, surface finish, performance standards, and any specific certifications needed.
2. Supplier selection: Research and identify reputable suppliers who specialize in knit line injection molding. Look for companies with a proven track record, good reputation, and extensive experience in the field. Obtain references and reviews from previous clients.
3. Quality assurance: Quality is crucial when purchasing knit line injection molding. Ensure that the supplier has robust quality control measures in place and adheres to industry standards. Ask for samples and prototypes to assess the quality of their products. Evaluate the durability, strength, and dimensional accuracy of the molded parts.
4. Price and affordability: Obtain detailed quotes from multiple suppliers to compare prices. However, it is essential to consider both the upfront cost and the long-term value. Cheaper options may compromise quality and durability, resulting in increased maintenance and replacement costs in the future. Strike a balance between price and quality.
5. Production capacity and lead time: Evaluate the supplier’s production capacity to ensure they can meet your required quantity within the desired timeframe. Discuss lead times, production schedules, and turnaround times to avoid delays in your own production process.
6. Communication and collaboration: Maintain open and transparent communication with the supplier throughout the procurement process. Clearly convey your requirements, expectations, and any potential challenges. Seek their expertise and suggestions to optimize the design and manufacturing of the knit line injection molded parts.
7. Contractual terms and conditions: Establish a comprehensive contract that outlines the specifications, delivery terms, payment terms, intellectual property rights, quality assurance measures, and any applicable warranties or guarantees.
8. Certifications and compliance: Ensure that the supplier complies with all necessary regulations and standards. Depending on the industry and application, certifications such as ISO 9001, ISO 14001, or specific industry standards may be required. Confirm the supplier’s ability to meet these requirements.
9. After-sales support: Inquire about the supplier’s after-sales support, including warranty, maintenance, and repair services. Establish a channel for ongoing communication and support to address any issues that may arise.
By considering these tips and taking the necessary precautions, you can make an informed procurement decision when purchasing knit line injection molding.
FAQs on Sourcing and Manufacturing knit line injection molding in China
1. What is knit line injection molding?
Knit line injection molding is a manufacturing process that combines the elements of both injection molding and knitting. It involves injecting molten plastic into a mold to create a knitted-like texture or pattern on the surface of the final product.
2. Why source and manufacture knit line injection molding in China?
China is known for its expertise in manufacturing and is often the go-to country for various production processes. Sourcing and manufacturing knit line injection molding in China can offer numerous advantages, including cost-effectiveness, skilled labor force, and a wide range of production capabilities. Chinese manufacturers also have access to advanced machinery and technologies that enable efficient and high-quality production.
3. How can I find reliable suppliers in China for knit line injection molding?
To find reliable suppliers in China, you can start by conducting extensive research online and utilizing platforms like Alibaba or Made-in-China. It’s crucial to thoroughly evaluate suppliers by checking their years of experience, product portfolio, customer reviews, and certifications. Moreover, requesting samples and conducting factory visits can help verify their capabilities and credibility.
4. What are the key considerations for quality control during production?
Quality control is vital during the production of knit line injection molding. Key considerations include:
– Ensuring the suppliers have appropriate quality management systems and certifications, such as ISO 9001.
– Implementing a comprehensive quality control plan that covers materials inspection, in-process checks, and final product testing.
– Conducting regular factory audits and inspections to monitor the manufacturing process and ensure adherence to quality standards.
– Establishing clear communication channels with the supplier to address any issues promptly.
5. How can production and shipping timelines be managed effectively?
Managing production and shipping timelines can be facilitated through careful planning and clear communication with the supplier. Key strategies include:
– Developing a detailed production schedule and setting clear deadlines.
– Regularly monitoring the production progress and addressing any delays promptly.
– Utilizing project management tools or software to track and manage the production process.
– Discussing shipping options and selecting reliable logistics partners to ensure on-time delivery.
In conclusion, sourcing and manufacturing knit line injection molding in China provide access to cost-effective production, skilled labor, and advanced technologies. Finding reliable suppliers, implementing robust quality control measures, and effective timeline management are crucial steps to ensure successful production.
Why contact sourcifychina.com get free quota from reliable knit line injection molding suppliers?
Sourcifychina.com offers free quota from reliable knit line injection molding suppliers for several reasons. Firstly, Sourcifychina.com aims to provide a seamless experience for businesses looking to source products from China. By connecting businesses with reliable suppliers, they ensure that customers receive high-quality products manufactured through efficient knit line injection molding processes.
In addition, providing a free quota allows businesses to get an initial understanding of the costs and feasibility of their desired products. This acts as a starting point and helps businesses in budgeting and decision-making. The free quota is especially beneficial for small and medium-sized enterprises (SMEs) who may not have significant financial resources to invest in their sourcing process upfront.
Moreover, Sourcifychina.com understands that transparency and trust are paramount in the sourcing business. By offering a free quota, they demonstrate their commitment to building trustworthy relationships with their clients. This allows businesses to gauge the reliability and professionalism of the suppliers before committing to any production contracts.
By limiting the word count, it is essential to highlight that Sourcifychina.com’s sourcing platform aims to simplify the sourcing process, enhance transparency, reduce risk, and save time for businesses. The free quota from reliable knit line injection molding suppliers ensures that businesses can make informed decisions without any financial burden or commitment. It showcases Sourcifychina.com’s dedication to providing top-notch services and facilitating successful sourcing experiences for businesses.