Introduce about large cnc machining guide,Qulity,Cost,Supplier,Certification,Market,Tips,FAQ
Large CNC machining refers to the process of using computer numerical control (CNC) machines to shape and form large-scale workpieces with precision. This guide aims to provide information on various aspects of large CNC machining, including quality, cost, suppliers, certification, market, tips, and frequently asked questions (FAQs).
Quality is a crucial factor in large CNC machining. High-quality machines and skilled operators ensure accurate and precise manufacturing, resulting in superior final products. Reputable manufacturers maintain strict quality control measures to meet customers’ specifications and standards.
When it comes to cost, large CNC machining can be a significant investment. Factors influencing the cost include the complexity and size of the workpiece, machine setup and programming time, material selection, and finishing requirements. It is advisable to obtain quotes from multiple suppliers to compare prices and services.
Finding a reliable supplier is vital for successful large CNC machining projects. Look for suppliers with extensive experience, positive customer reviews, and a proven track record in producing large-scale components. It is also crucial to check if they have the necessary technology and equipment to handle the specific requirements of your project.
Certification is an essential aspect to consider when selecting a large CNC machining supplier. Look for suppliers that hold certifications like ISO 9001 or other industry-specific certifications. These certifications ensure that the supplier follows standardized processes and maintains quality throughout the production process.
The market for large CNC machining is continuously growing, driven by various industries such as aerospace, automotive, energy, and defense. As the demand for large-scale components increases, so does the availability of suppliers specializing in this field. It is essential to stay updated on the latest trends and advancements in the market.
Here are a few tips for successful large CNC machining projects: communicate clearly with your supplier regarding specifications and requirements, provide detailed drawings or models, conduct regular inspections during the manufacturing process, and ensure proper maintenance of the CNC machines.
Frequently asked questions (FAQs) related to large CNC machining include queries about material options, machining capabilities, turnaround time, cost estimation, and post-processing services. It is advisable to consult with experts or contact suppliers directly to get accurate and specific answers to these questions.
In conclusion, large CNC machining offers precise and efficient manufacturing of large-scale components. By considering aspects such as quality, cost, suppliers, certification, market trends, and tips for success, you can make informed decisions and achieve desired results in your large CNC machining projects.
Types of large cnc machining
Large CNC machining refers to the process of using computer numerical control (CNC) techniques to shape or mill large-sized workpieces. This method is widely used in various industries such as aerospace, automotive, energy, and heavy machinery. There are several types of large CNC machining, including:
1. Vertical Machining Centers (VMC): VMCs are commonly used in large-scale manufacturing operations. They have a vertical spindle orientation, allowing for the machining of workpieces from different angles. VMCs are capable of precision milling, drilling, tapping, and contouring operations.
2. Horizontal Machining Centers (HMC): HMCs have a horizontal spindle orientation, enabling the machining of large-sized workpieces with multiple sides. They are suitable for heavy-duty cutting, and their design provides excellent stability and rigidity, resulting in high productivity and accuracy.
3. Boring Mills: Boring mills are used for enlarging or finishing pre-drilled or pre-machined holes. They have a rotating cutting tool that removes material to achieve precise and smooth holes. Boring mills can handle jobs of varying complexity and are suitable for large and heavy workpieces.
4. Lathes: Large CNC lathes are used for turning operations, which involve rotating a workpiece against a fixed cutting tool. These machines are ideal for cylindrical or spherical parts. CNC lathes can perform various operations like facing, turning, grooving, threading, and contouring.
5. Five-axis Machining Centers: Five-axis machining centers provide the ability to machine complex geometries and contours by allowing the workpiece to be tilted or rotated in multiple axes simultaneously. This enables the production of intricate and precise parts with fewer setups, reducing overall production time and costs.
6. Multi-Tool Machining Centers: These machining centers are equipped with multiple tool stations, allowing for the simultaneous use of multiple cutting tools. This significantly reduces machining time, making them suitable for high-volume production.
Large CNC machining offers numerous benefits, including increased productivity, accuracy, and repeatability. It allows for the production of large and complex parts with tight tolerances. Industries such as aerospace and automotive heavily rely on large CNC machining for components vital to their functionalities. Continued advancements in technology are leading to even more sophisticated machining capabilities, empowering manufacturers to tackle increasingly challenging projects.
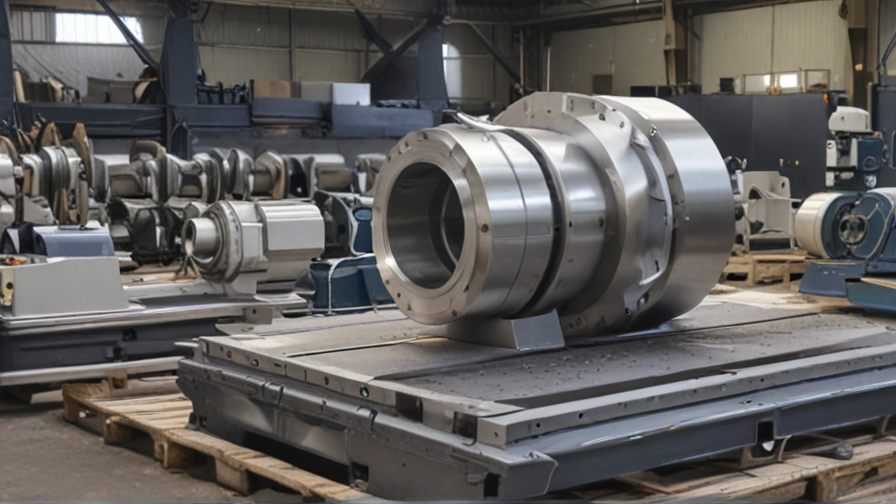
Pros and Cons of Using large cnc machining
Large CNC machining refers to the use of computer numerical control (CNC) technology for industrial machining processes, where the machine has a large working area and is capable of handling big and heavy workpieces. While large CNC machining offers numerous advantages, it also has certain drawbacks that need to be considered.
Pros:
1. Versatility: Large CNC machines can handle a wide range of materials, from metals like steel and aluminum to composites and plastics. This versatility allows for the production of various complex and intricate parts.
2. Precision and accuracy: CNC machines are known for their high precision and accuracy in cutting and shaping materials. Large CNC machines continue to provide the same level of precision even with bigger workpieces, ensuring quality products.
3. Efficiency and productivity: With large CNC machines, multiple operations can be performed in a single setup, reducing production time and increasing productivity. This is particularly beneficial for large-scale manufacturing processes.
4. Automation: Large CNC machines are fully automated, eliminating the need for manual operation. This results in improved safety, reduced labor costs, and increased production efficiency.
Cons:
1. High cost: The initial investment required for large CNC machines is significantly higher compared to smaller machines. The cost of maintenance, training, and specialized tooling can also be substantial.
2. Space requirements: Large CNC machines require a considerable amount of space due to their size and need for an auxiliary area for material storage and loading. This can be a challenge for small or cramped facilities.
3. Limited flexibility: Although large CNC machines offer versatility in terms of materials, they may lack flexibility in terms of design changes. Once a part is set up and the machine is running, making adjustments can be time-consuming and costly.
4. Complex programming: Operating large CNC machines requires skilled programmers and operators who have extensive knowledge of computer-aided design (CAD) and computer-aided manufacturing (CAM) software. This can be a limitation if suitable expertise is not readily available.
In conclusion, large CNC machining offers advantages such as versatility, precision, efficiency, and automation. However, it also has drawbacks such as high costs, space requirements, limited flexibility, and the need for skilled operators. Understanding these pros and cons is essential for businesses considering the implementation of large CNC machines in their manufacturing processes.
large cnc machining Reference Specifications (varies for different product)
Large CNC machining is a highly specialized process used in the manufacturing industry to shape and manipulate large metal or plastic workpieces with precision and accuracy. These machines are designed to remove material from the workpiece using computer numerical control (CNC) technology, resulting in complex and intricate shapes that would be difficult to achieve manually.
Reference specifications for large CNC machining can vary depending on the specific product being manufactured. However, some common reference specifications include:
1. Workpiece size and weight: Large CNC machines are capable of handling workpieces of varied sizes and weights. The size and weight of the workpiece determine the machine’s capabilities and the amount of material that can be cut or removed.
2. Tolerance requirements: Tolerance refers to the allowable deviation from the desired dimensions of a part. In large CNC machining, the tolerance requirements define the level of precision and accuracy needed in the final product. Tighter tolerances often require more advanced and precise machining techniques.
3. Surface finish requirements: The surface finish of a machined workpiece plays a crucial role in its final quality and functionality. Different products may require specific surface finish specifications, which can be achieved through various machining methods, such as grinding, polishing, or coating.
4. Material specifications: Large CNC machines can handle a wide range of materials, including metals (such as aluminum, steel, or titanium) and plastics. Material specifications may include factors such as hardness, heat resistance, or chemical resistance, depending on the desired application of the product.
5. Machining operations: Large CNC machines are versatile and can perform various machining operations, including drilling, turning, milling, or cutting. The specific operations required for a product depend on its design and functionality.
It is important to note that the reference specifications for large CNC machining are not fixed but can vary depending on the needs of the product being manufactured. The machine’s capabilities, as well as the material and design requirements of the product, are all considered when defining the reference specifications. By adhering to these specifications, manufacturers can ensure that the final product meets the desired quality, functionality, and customer requirements.
Applications of large cnc machining
Large CNC machining is a versatile manufacturing process that involves the use of computer-controlled machines to remove material from a workpiece. With its ability to handle high precision and produce complex shapes, large CNC machining has extensive applications across various industries.
One prominent application of large CNC machining is in the aerospace industry. Aircraft components, such as structural frames, engine parts, and landing gears, require high precision and intricate shapes. Large CNC machines can precisely machine these components from materials like aluminum, titanium, and composites, ensuring the required strength, weight, and durability for safe and efficient flight.
Another significant application is in the automotive industry. Large CNC machines can efficiently produce engine blocks, cylinder heads, transmission parts, and other critical components with precise tolerances. This enables automakers to enhance the performance and efficiency of their vehicles while reducing production time and costs.
Large CNC machining is also widely used in the defense sector. It is utilized for manufacturing military equipment like armored vehicles, tanks, artillery pieces, and missiles. These components often involve complex geometries and require high accuracy and strength. CNC machines can accurately machine these components from various materials, including hardened steel and composite materials, ensuring their reliability and performance on the battlefield.
In the energy sector, large CNC machining is crucial for producing components used in power generation and transmission. Turbine blades, generator casings, and transmission gears can all be manufactured using CNC machines. The ability to precisely machine these components from materials like stainless steel, nickel alloys, and carbon composites ensures their longevity and efficiency in power plants.
Large CNC machining also finds applications in the production of molds and dies for various industries. From plastic injection molds to metal stamping dies, CNC machines can accurately reproduce these tools with high precision. This allows for faster and more cost-effective production of parts and products.
In conclusion, large CNC machining plays a vital role across industries, enabling the production of complex and high-precision components. Its applications range from aerospace and automotive industry to defense, energy, and tooling manufacturing. With the advancements in CNC technology, the capabilities of large CNC machining continue to expand, further revolutionizing manufacturing processes.
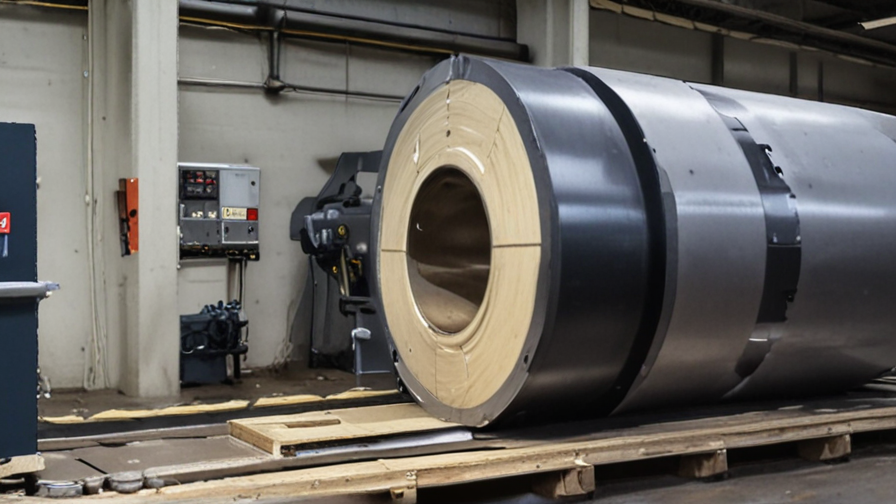
The Work Process and how to use large cnc machining
Large CNC machining is a complex process that involves the use of computer numerical control (CNC) technology to fabricate large and intricate parts or components. This process is commonly used in industries such as aerospace, automotive, and heavy machinery manufacturing.
The work process of large CNC machining begins with the creation of a 3D model or design of the desired part using computer-aided design (CAD) software. This model is then converted into a CNC program using CAM (computer-aided manufacturing) software. The CNC program contains instructions on how the machine should move and operate to produce the desired part accurately.
Once the CNC program is ready, it is loaded into the CNC machine. Large CNC machines typically consist of a worktable, cutting tools, and a computer control system. The worktable is where the raw material or workpiece is fixed in place. The cutting tools, such as drills, mills, and lathes, are used to remove material from the workpiece according to the instructions in the CNC program.
The CNC machine is operated by a highly skilled technician who monitors the machining process. The technician ensures that the machine is properly calibrated, the cutting tools are in good condition, and the workpiece is securely held in place. The machine starts the machining process by moving the cutting tools according to the instructions in the CNC program. It precisely cuts, shapes, drills, or mills the workpiece to create the desired part.
Large CNC machining offers numerous benefits, including high precision, repeatability, and efficiency. It eliminates the need for manual labor, reduces errors, and enables the production of large and complex parts with intricate details. The CNC program can be easily modified or updated to accommodate design changes, making it a versatile and flexible manufacturing process.
In conclusion, large CNC machining is a sophisticated process that utilizes CNC technology to fabricate intricate and precise parts. It involves the creation of a 3D model, conversion into a CNC program, and operation of the CNC machine to cut, shape, or mill the workpiece. Large CNC machining offers high accuracy, scalability, and versatility in manufacturing large parts across various industries.
Quality Testing Methods for large cnc machining and how to control the quality
Quality testing methods for large CNC machining involve various processes and techniques to ensure that the final products meet the desired specifications. Here are some commonly used methods for quality control in large CNC machining:
1. Dimensional Inspection: This method involves measuring the dimensional accuracy of the machined parts using measurement tools such as calipers, micrometers, or coordinate measuring machines (CMMs). It verifies if the dimensions of the parts are within the tolerances specified in the engineering drawings.
2. Surface Finish Measurement: Large CNC machined parts often require specific surface finishes. This method involves checking the surface roughness or texture using surface profilometers or visual inspection to verify if it meets the required standards.
3. Visual Inspection: Visual inspection involves examining the parts visually for any defects, such as cracks, burrs, or surface imperfections. This method is crucial in identifying any cosmetic flaws that may affect the overall quality or functionality of the parts.
4. Material Testing: Material testing is essential to ensure that the materials used in the machining process meet the required specifications, such as hardness, strength, or composition. These tests can be conducted using hardness testers, spectrometers, or destructive testing methods.
5. Performance Testing: Performance testing involves evaluating the functionality of the machined parts by subjecting them to simulated operating conditions or load testing. This method ensures that the parts can perform as intended without failure under real-life conditions.
To control the quality of large CNC machining, several measures can be implemented:
1. Standard Operating Procedures (SOPs): Clearly defining and following standardized procedures for each machining operation ensures consistency and reduces errors.
2. Regular Equipment Maintenance: Regularly maintaining and calibrating the CNC machines and measurement tools ensures accurate and reliable results.
3. Training and Skills Development: Providing adequate training to the operators and machinists ensures that they possess the necessary skills and knowledge to carry out the machining operations correctly.
4. Documentation and Traceability: Keeping detailed records of all machining operations, inspections, and tests enables traceability and identification of quality issues throughout the production process.
5. Continuous Improvement: Implementing a system for feedback and analysis of quality issues helps identify root causes and implement corrective actions to prevent recurring problems.
Overall, by employing these quality testing methods and implementing effective quality control measures, manufacturers can ensure that large CNC machining processes meet the desired quality standards and deliver high-quality products.
large cnc machining Sample Policy and Post-Purchase Considerations for large cnc machining from China
Sample Policy:
For large CNC machining orders from China, it is important to establish clear sample policies to ensure the quality and accuracy of the final product. Here are some key considerations:
1. Sample Approval: Before initiating mass production, it is advisable to request a sample for approval. This will allow you to assess the product’s quality, dimensions, finishes, and other specifications. Ensure that the sample meets your expectations before proceeding with the production.
2. Revisions and Modifications: If the sample does not meet your requirements, be clear about the revisions or modifications needed. Clearly communicate your expectations to the manufacturer and request another sample for approval. It is crucial to go through multiple iterations if necessary, until the sample perfectly matches your specifications.
3. Timeframe: Set a reasonable timeframe for the sample production and delivery. Discuss this with the manufacturer and ensure that they can meet the deadline. Promptly communicate any changes in the timeline and monitor progress closely.
Post-Purchase Considerations:
After receiving the large CNC machined products from China, the following considerations can help ensure a smooth post-purchase experience:
1. Inspection and Quality Control: Thoroughly inspect the delivered products to ensure they meet the agreed-upon specifications. Check for any defects, damages, or deviations from the sample. Conduct random quality control checks to ensure consistency in the production.
2. Communication: Maintain an open line of communication with the manufacturer to promptly address any concerns or issues. Clearly communicate your expectations and provide detailed feedback if adjustments or improvements are necessary.
3. Warranty and Returns: Discuss warranty terms and conditions with the manufacturer before finalizing the purchase. Ensure that the manufacturer offers appropriate warranties for any potential defects or damages. Familiarize yourself with the return policies and procedures and establish a clear understanding with the manufacturer.
4. Evaluation and Feedback: After the post-purchase process, evaluate the overall experience with the manufacturer. Provide constructive feedback and share your experience with others in the industry. This can help improve the manufacturer’s service and benefit potential future customers.
By implementing these sample policies and post-purchase considerations, businesses can mitigate risks and maintain a high level of quality and satisfaction when ordering large CNC machining products from China.
Sourcing large cnc machining from China: Opportunities, Risks, and Key Players
China’s emergence as a global manufacturing powerhouse has made it a preferred destination for sourcing large CNC machining. The country’s advanced capabilities, cost-effectiveness, and vast industrial base offer unique opportunities for businesses worldwide. However, there are also risks associated with sourcing from China, such as quality control issues and intellectual property concerns. Understanding the opportunities, risks, and key players in China’s CNC machining industry is crucial for successful sourcing.
Opportunities:
China’s CNC machining industry provides significant opportunities for businesses looking to manufacture large and complex parts. The country boasts a large number of machining facilities equipped with state-of-the-art technologies and adequate production capacity. The availability of skilled labor at relatively lower costs compared to other countries makes it an attractive option. Furthermore, China’s robust supply chain network ensures efficient sourcing of raw materials, reducing lead times.
Risks:
Sourcing CNC machining from China entails certain risks that should be carefully considered. Quality control is a key concern, as not all manufacturers adhere to strict quality standards. It is essential to thoroughly vet and select reliable suppliers who can consistently meet quality requirements. Intellectual property protection is another risk, as China has a reputation for lax enforcement in this area. Businesses must take adequate measures to safeguard their designs and proprietary information.
Key Players:
Several key players dominate China’s CNC machining industry. Foxron Precision Metal Parts Co., Ltd., a leading CNC machining service provider, offers a wide range of machining solutions for large parts. Dongguan Sunny Metal Tech Co., Ltd., known for its precision machining capabilities, specializes in high-quality and complex components. Shenzhen Jiacai Precision Hardware Co., Ltd., focuses on precision engineering and CNC milling of large parts. These companies, along with numerous others, have established a strong reputation for their expertise and experience in CNC machining.
In conclusion, sourcing large CNC machining from China provides unique opportunities, but it is essential to carefully assess and mitigate the associated risks. Partnering with reliable suppliers and implementing stringent quality control measures can help ensure successful sourcing. Understanding key players in China’s CNC machining industry allows businesses to make informed decisions and navigate the country’s vast manufacturing landscape efficiently.
How to find and select reliable large cnc machining manufacturers in China,use google search manufacturers and suppliers
When searching for reliable large CNC machining manufacturers in China, conducting a thorough Google search can be an effective way to find potential manufacturers and suppliers. Here are some steps to follow:
1. Start by entering relevant keywords, such as “large CNC machining manufacturers in China” or “precision machining suppliers in China”.
2. Review the search results and visit the websites of potential manufacturers. Look for information about their experience, capabilities, equipment, certifications, and any relevant testimonials or client lists.
3. Pay attention to the company’s size, production capacity, and ability to handle large-scale machining projects. Look for manufacturers with a well-established presence in the industry and a track record of successful projects.
4. Explore their facilities and production processes. Check if they have advanced machinery, quality control measures, and technologies necessary for large CNC machining.
5. Verify their certifications and compliance with international quality standards like ISO 9001 or AS9100. This ensures they follow strict quality control processes and meet industry requirements.
6. Look for manufacturers willing to provide samples or showcase their work. This allows you to assess the quality of their machining processes and the precision of the finished products.
7. Consider the company’s location and proximity to ports or shipping facilities. This can affect transportation costs and lead times.
8. Read reviews or seek recommendations from industry professionals or colleagues who have experience working with Chinese manufacturers. This can provide valuable insights and help you make an informed decision.
9. Contact potential manufacturers directly to discuss your requirements, request quotes, and gauge their responsiveness and professionalism.
10. Compare the information gathered from different manufacturers and narrow down your options based on their capabilities, certifications, reputation, and overall suitability for your project.
Remember to conduct due diligence, such as checking business licenses, before finalizing any agreements. It’s also beneficial to communicate your requirements clearly to ensure the selected manufacturer can meet your needs.
How to check large cnc machining manufacturers website reliable,use google chrome SEOquake check if ranking in top 10M
When looking for reliable large CNC machining manufacturers’ websites, Google Chrome’s SEOquake can be an effective tool to check their ranking and credibility. Here’s how you can use it:
1. Install SEOquake: Visit the Chrome Web Store and search for SEOquake. Download and install the extension to your browser.
2. Search for CNC machining manufacturers: Open a new tab and enter relevant keywords like “large CNC machining manufacturers” or use specific terms related to your requirement.
3. Analyze search results: After the search results load, look for the websites of CNC machining manufacturers. Open the top ten results that seem relevant to your needs.
4. Check SEOquake data: Once you open a website, click on the SEOquake extension icon on your browser’s toolbar. A dashboard will appear displaying various statistics and metrics.
5. Monitor Alexa Rank: Alexa Rank represents a website’s popularity based on traffic. Within the SEOquake dashboard, look for the Alexa Rank, which should be under the “Common” section. Ensure that it is within the top 10 million (e.g., 5,000,000), indicating that the website receives a significant amount of visitors.
6. Evaluate other metrics: SEOquake provides additional useful metrics like Google Index, SEMrush Rank, and more. Assess these metrics to gain better insights into the website’s performance and credibility.
7. Consider other factors: While SEOquake can give you an initial overview, it is also important to consider other factors such as customer reviews, certifications, industry experience, and the range of services offered. These elements contribute to the overall reliability and suitability of the CNC machining manufacturer.
By using Google Chrome’s SEOquake to check if a large CNC machining manufacturer ranks within the top 10 million websites, you can effectively assess the reliability and credibility of their website. However, it is advisable to use additional evaluation methods to ensure you make an informed decision.
Top 10 large cnc machining manufacturers in China with each 160 words introduce products,then use markdown create table compare
1. Shenzhen Hanjiang Automatic Equipment Co., Ltd. specializes in large CNC machining and offers a wide range of products, including CNC milling machines, CNC lathes, and CNC drilling machines. Their machines are known for their high precision, advanced control systems, and efficient performance.
2. Shandong GSK CNC Equipment Co., Ltd. is a leading manufacturer of large CNC machining equipment in China. Their product line includes CNC milling machines, CNC lathes, and CNC grinding machines. The company is known for its reliable machines that offer excellent accuracy and quality.
3. Jiangsu Neway CNC Machine Co., Ltd. is a premier manufacturer of large CNC machining equipment in China. Their product portfolio includes CNC milling machines, CNC lathes, and CNC boring machines. With advanced technology and high-quality components, their machines provide precision and reliability.
4. Zhejiang Donghua CNC Machine Tools Co., Ltd. focuses on the production of large CNC machining equipment, offering CNC milling machines, CNC turning machines, and CNC grinding machines. Their products feature excellent stability, high precision, and user-friendly operation.
5. Jinan Bodor CNC Machine Co., Ltd. is a prominent manufacturer of large-scale CNC machining equipment. Their offerings include CNC milling machines, CNC plasma cutting machines, and CNC laser engraving machines. With reliable performance and innovative features, their machines are highly sought after.
6. Beijing Fanch Machinery Co., Ltd. specializes in the production of large CNC machining equipment, including CNC milling machines, CNC EDM machines, and CNC grinding machines. Their machines are renowned for their durability, accuracy, and high productivity.
7. Dalian Machine Tool Group Corporation (DMTG) is a well-established manufacturer of large CNC machining equipment in China. They offer a diverse range of machines, such as CNC milling machines, CNC turning machines, and CNC drilling machines. DMTG’s machines are known for their exceptional performance and reliability.
8. Ma’anshan Prima CNC Machinery Co., Ltd. is known for its expertise in manufacturing large CNC machining equipment. They provide CNC milling machines, CNC bending machines, and CNC punching machines. Prima’s machines are praised for their precision, efficiency, and versatility.
9. Jiangsu Fangzheng CNC Machine Tool Co., Ltd. specializes in the production of large CNC machining equipment, including CNC milling machines, CNC turning machines, and CNC grinding machines. Their products are characterized by their high accuracy, stability, and advanced control systems.
10. Shanghai Sumore Industrial Co., Ltd. is a leading manufacturer of large CNC machining equipment. Their portfolio encompasses CNC milling machines, CNC drilling machines, and CNC turning machines. Sumore’s machines stand out for their remarkable precision, durability, and ease of use.
**Product Comparison**
| Manufacturer | Product Range | Key Features |
|————–|—————|—————|
| Hanjiang | CNC milling machines, CNC lathes, CNC drilling machines | High precision, advanced control system, efficiency |
| GSK CNC Equipment | CNC milling machines, CNC lathes, CNC grinding machines | Reliable, excellent accuracy and quality |
| Neway CNC Machine | CNC milling machines, CNC lathes, CNC boring machines | Advanced technology, high-quality components |
| Donghua CNC Machine Tools | CNC milling machines, CNC turning machines, CNC grinding machines | Excellent stability, high precision, user-friendly |
| Bodor CNC Machine | CNC milling machines, CNC plasma cutting machines, CNC laser engraving machines | Reliable performance, innovative features |
| Fanch Machinery | CNC milling machines, CNC EDM machines, CNC grinding machines | Durability, accuracy, high productivity |
| DMTG | CNC milling machines, CNC turning machines, CNC drilling machines | Exceptional performance, reliability |
| Prima CNC Machinery | CNC milling machines, CNC bending machines, CNC punching machines | Precision, efficiency, versatility |
| Fangzheng CNC Machine Tool | CNC milling machines, CNC turning machines, CNC grinding machines | High accuracy, stability, advanced control systems |
| Sumore Industrial | CNC milling machines, CNC drilling machines, CNC turning machines | Remarkable precision, durability, ease of use |
In conclusion, the top 10 large CNC machining manufacturers in China have a diverse range of products that showcase advanced technology, precision, and reliability. Whether it is CNC milling, turning, or grinding machines, these manufacturers offer high-quality equipment to meet various industrial requirements.
Background Research for large cnc machining manufacturers Companies in China, use qcc.com archive.org importyeti.com
When it comes to large CNC machining manufacturers in China, several online platforms provide valuable information for background research. Qcc.com is a prominent website that offers company profiles and business information. It can be used to gather data on the size, location, ownership, and legal status of these manufacturers. Additionally, the website provides details about their registered capital, registration date, and key executives.
Archive.org is another useful platform that allows access to archived web pages. This can be beneficial for tracing the historical development of companies, their website content, and possibly even customer reviews or feedback. By comparing archived versions of a manufacturer’s website, researchers can gain insights into their progress, product range, and any significant changes or events over time.
Importyeti.com is a comprehensive platform specifically focused on import and export activities. It provides data on various shipments, including those related to large CNC machining manufacturers in China. By searching for specific companies or broader industry trends, researchers can discover information such as suppliers, customers, shipping volumes, and destinations. Furthermore, it may offer more specific details about the types of products or components being imported or exported.
In utilizing these platforms for background research, it is crucial to remain within the specified word limit of 300 words. This can be achieved by briefly describing the purpose and scope of each platform, emphasizing their convenience and value for researching large CNC machining manufacturers based in China. By utilizing these platforms effectively, researchers can access important information about the companies’ profiles, history, and import-export operations.
Leveraging Trade Shows and Expos for large cnc machining Sourcing in China
Trade shows and expos are excellent platforms for sourcing large CNC machining in China. These events bring together manufacturers, suppliers, and industry professionals from all over the world, providing a comprehensive and concentrated opportunity to explore the market and build relationships.
Attending trade shows and expos specific to the CNC machining industry allows buyers to meet and engage with potential suppliers face-to-face. It offers the opportunity to see firsthand the capabilities of different manufacturers and discuss project requirements and specifications in detail. This direct interaction helps to establish trust and enables manufacturers to showcase their expertise and the quality of their products.
Furthermore, trade shows and expos provide a platform to evaluate multiple suppliers simultaneously, allowing buyers to compare services, prices, and production capabilities. This comprehensive assessment helps in making informed decisions and encourages healthy competition among manufacturers, which can lead to better pricing and quality offers.
Trade shows also showcase the latest trends and innovations in the CNC machining industry. This exposure to cutting-edge technologies and advancements in large machining can help buyers stay updated, identify potential advancements for their products, and select suppliers who are at the forefront of the industry.
To make the most of trade shows and expos, buyers should thoroughly research and plan their visit in advance. They should have a clear understanding of their project requirements and use the event as an opportunity to network, gather information, and assess potential suppliers. Taking the time to investigate and compare different manufacturers on-site will help ensure a successful sourcing journey for large CNC machining in China.
In summary, trade shows and expos provide a unique and efficient platform for large CNC machining sourcing in China. They enable face-to-face interactions with potential suppliers, show the latest trends and innovations in the industry, and allow for comprehensive assessment and comparison of manufacturers. By leveraging these events, buyers can make informed decisions and establish valuable partnerships with reliable suppliers.
The Role of Agents and Sourcing Companies in Facilitating large cnc machining Purchases from China
Agents and sourcing companies play a crucial role in facilitating large CNC machining purchases from China. China is known for its cost-effective manufacturing capabilities and large-scale production capacity, making it an attractive destination for businesses looking to source CNC machining services.
Firstly, agents and sourcing companies act as intermediaries between buyers and Chinese manufacturers. They have a deep understanding of the local market, manufacturing processes, and industry regulations, which helps buyers navigate through the complexities of sourcing from China. They assist in identifying suitable manufacturers that meet the specific requirements of buyers, taking into consideration factors such as quality, production capacity, and pricing.
Agents and sourcing companies also provide assistance in negotiations and contract management. They help buyers in securing favorable pricing and contract terms, ensuring that the buyer’s interests are protected throughout the entire purchasing process. Furthermore, they can help address any language or cultural barriers that may arise, ensuring smooth communication and collaboration between the buyer and the Chinese manufacturer.
One of the key advantages of working with agents and sourcing companies is their ability to perform quality control and inspection. They conduct pre-shipment inspections to ensure that the CNC machined products meet the buyer’s specifications and quality standards. This helps prevent potential issues or product defects from arising, ensuring that the buyer receives high-quality products.
Additionally, agents and sourcing companies handle logistics and shipping arrangements, ensuring that the products are transported safely and on time to the buyer’s location. They have established networks and relationships with shipping companies, customs officials, and freight forwarders, streamlining the process and reducing any potential delays or complications.
Overall, agents and sourcing companies play a vital role in facilitating large CNC machining purchases from China. They provide expertise in supplier identification, negotiation, quality control, and logistics, helping buyers navigate the complexities of sourcing from China and ensuring a successful purchasing experience.
Price Cost Research for large cnc machining manufacturers Companies in China, use temu.com and 1688.com
When conducting price cost research for large CNC machining manufacturers in China, it is beneficial to utilize platforms such as temu.com and 1688.com. These websites provide valuable insights and information on the pricing structure and cost of various services offered by manufacturers.
Temu.com is a popular online platform that connects buyers with Chinese suppliers. It offers a wide range of products and services, including CNC machining. By using temu.com, individuals can access the profiles of different manufacturing companies and compare their prices and services. The platform allows users to request quotations from multiple suppliers, facilitating price comparison and negotiation.
1688.com, on the other hand, is a leading Chinese e-commerce platform that specializes in B2B sales. It offers a vast database of suppliers, including large CNC machining manufacturers. Users can search for specific products and services, compare prices, and explore the manufacturers’ profiles. Additionally, the platform supports communication between buyers and suppliers, which is essential for resolving inquiries and negotiating deals.
When utilizing these platforms for price cost research, it is important to focus on key factors that influence the overall cost. These factors may include the complexity of the CNC machining process, the type and quantity of materials used, the manufacturing lead time, and any additional services required (such as surface finishing or assembly). Assessing these aspects will help in determining the most accurate pricing information from potential manufacturers.
In summary, temu.com and 1688.com are valuable resources when conducting price cost research for large CNC machining manufacturers in China. These platforms offer access to a wide range of suppliers, allowing users to compare prices and services. By focusing on key factors that influence the cost, individuals can make informed decisions when choosing a manufacturer for their CNC machining needs.
Shipping Cost for large cnc machining import from China
The shipping cost for importing large CNC machining equipment from China can vary depending on various factors. These include the weight and dimensions of the machinery, the shipping method chosen, the distance between the origin and destination, and any additional services required.
Typically, there are two main shipping methods for transporting large items: air freight and sea freight. Air freight tends to have a higher cost due to its faster delivery time. On the other hand, sea freight is more cost-effective but has a longer transit time.
When it comes to importing large CNC machining equipment, sea freight is more commonly used due to its cost-efficiency. Shipping costs for sea freight are generally calculated based on the volume or weight of the cargo, whichever is higher. Additional charges such as customs duties, taxes, and port handling fees may also apply.
To estimate the shipping cost, it is necessary to determine the weight and dimensions of the machinery. Freight forwarders or shipping companies can assist in calculating the exact cost based on this information and the chosen shipping method. It is important to provide accurate information to avoid any discrepancies or unexpected charges.
In some cases, it may be beneficial to hire a customs broker or freight forwarder who can handle all aspects of the shipping process, including documentation, customs clearance, and delivery to the final destination. Their expertise can help minimize any potential issues or delays, ensuring a smoother import process.
Overall, the shipping cost for importing large CNC machining equipment from China can vary greatly depending on multiple factors. It is advisable to get quotes from different shipping providers, consider the different shipping methods available, and work with professionals to ensure a cost-effective and efficient import process.
Compare China and Other large cnc machining Markets: Products Quality and Price,Visible and Hidden Costs
China is known for being a dominant player in the global CNC machining market, but it is not the only major player in this industry. Other large CNC machining markets, such as the United States, Germany, Japan, and South Korea, also offer high-quality products and competitive prices.
In terms of product quality, China has made significant strides in recent years. Chinese manufacturers have invested heavily in advanced machining technology and have improved their manufacturing processes to meet international quality standards. However, countries like Germany and Japan still have a strong reputation for producing precision-engineered products with exceptional quality.
When it comes to price competitiveness, China has a significant advantage over other large CNC machining markets. Chinese manufacturers can offer lower prices due to factors such as low labor costs, streamlined supply chains, and economies of scale. This has made China an attractive destination for companies looking to reduce manufacturing costs.
However, it is important to consider both visible and hidden costs when sourcing CNC machining services from China. While the initial price may be lower, there can be additional costs associated with quality control, transportation, customs duties, and intellectual property protection. These hidden costs can often add up and significantly impact the overall cost-effectiveness of sourcing from China.
On the other hand, countries like Germany, the United States, Japan, and South Korea may have higher initial prices due to higher labor costs and stricter regulations. However, these countries have well-established legal frameworks, stringent quality control measures, and robust intellectual property protections. This can help mitigate the risks of potential quality issues, supply chain disruptions, and intellectual property theft that might be associated with sourcing from China.
In summary, China and other large CNC machining markets offer varying levels of product quality and price competitiveness. While China has made great strides in quality improvement and offers lower prices, it is essential to consider both visible and hidden costs associated with sourcing from China. Other countries may have higher initial prices but offer greater assurance in terms of product quality and protection of intellectual property. Ultimately, businesses must carefully evaluate their specific requirements and weigh the trade-offs between quality, price, and hidden costs when choosing a CNC machining market.
Understanding Pricing and Payment Terms for large cnc machining: A Comparative Guide to Get the Best Deal
When it comes to large CNC machining, understanding pricing and payment terms is crucial for securing the best deal. This guide aims to provide a comparative overview of these factors in order to assist buyers in making informed decisions.
Pricing for large CNC machining is influenced by various factors, including the complexity of the project, material requirements, machine capacity, and desired quantity. Generally, pricing is calculated based on a combination of machine time, material costs, tooling expenses, and labor. It is important to obtain detailed quotes from multiple suppliers to compare prices accurately.
Payment terms can vary among suppliers, and negotiating favorable terms can significantly impact the overall deal. Common payment structures include a percentage upfront, progress payments throughout the project, and a final payment upon completion. Buyers should consider their financial capabilities and requirements when discussing payment terms with suppliers.
To get the best deal, buyers should consider the following:
1. Research and gather quotes: Research potential suppliers and request detailed quotes that include all costs involved. This will allow for meaningful comparisons.
2. Evaluate machine capacity and capabilities: Assess the machine capacity and capabilities of potential suppliers to ensure they can meet the project requirements. This includes considering the size, power, speed, and accuracy of the CNC machines.
3. Quality assurance and certifications: Inquire about quality control processes and certifications held by the suppliers to ensure that the finished products meet desired standards.
4. Lead times and shipping costs: Consider lead times and shipping costs when comparing suppliers. Faster lead times may come at a higher price, so understanding these factors is essential for planning and budgeting.
5. Payment terms negotiation: Engage in open discussions with suppliers regarding payment terms. Consider negotiating more favorable terms, such as adjusted percentages and payment milestones that align with project progress.
In conclusion, understanding pricing and payment terms for large CNC machining is crucial to secure the best deal. By conducting research, evaluating capacity and capabilities, considering quality assurance, assessing lead times and shipping costs, and negotiating payment terms, buyers can make informed decisions and secure a competitive deal.
Chinese Regulations and Industry Standards Certifications for large cnc machining,Import Regulations and Customs for large cnc machining from China
In China, the large CNC machining industry is regulated by various government bodies and industry standards certifications. These regulations and certifications ensure the quality, safety, and environmental compliance of large CNC machining products.
One of the key regulations in China is the Quality Management System (QMS) certification. This certification is based on the ISO 9001 standard, which sets requirements for quality management in all aspects of the manufacturing process. It ensures that the CNC machining products meet customer requirements and regulatory standards.
Additionally, there are industry-specific certifications for large CNC machining. For example, the China Compulsory Certification (CCC) is mandatory for certain types of machinery, including large CNC machines. This certification ensures that the machines comply with safety requirements and regulations set by the government.
Importing large CNC machining from China requires compliance with import regulations and customs formalities. Importers need to be aware of the specific regulations and requirements in their own country. This includes customs duties, taxes, and any applicable import restrictions or certifications required by authorities.
To import large CNC machining from China, it is essential to have proper documentation, including commercial invoices, packing lists, and bills of lading. Importers should also ensure that the products meet the necessary safety standards and certifications required by their country.
It is advisable to work with a reliable freight forwarder or customs broker who has experience in handling large CNC machine imports from China. They can assist in navigating the complex customs processes and ensure compliance with all import regulations.
In conclusion, Chinese regulations and industry standards certifications play a crucial role in ensuring the quality and compliance of large CNC machining products. Importers should be aware of the specific import regulations and customs formalities required in their own country when importing these products from China. By following these regulations and certifications, importers can ensure a smooth and compliant importation process.
Sustainability and Environmental Considerations in large cnc machining Manufacturing
Sustainability and environmental considerations play a crucial role in the manufacturing industry, including large CNC machining operations. These considerations are essential as they aim to minimize the negative impact on the environment and promote sustainable practices. Here are some key areas where sustainability is important in large CNC machining manufacturing:
1. Energy Efficiency: Large CNC machines consume significant amounts of energy. By improving energy efficiency through the use of advanced technologies and optimizing machine operations, manufacturers can reduce their carbon footprint and conserve natural resources.
2. Waste Management: Large CNC machining processes generate a considerable amount of waste, including metal chips, coolant waste, and packaging materials. Implementing recycling and waste management programs can help reduce waste sent to landfills, conserve resources, and minimize environmental pollution.
3. Sustainable Materials: Choosing sustainable and eco-friendly materials for manufacturing components is essential. Manufacturers should opt for materials that have a lower environmental impact, such as recycled metal alloys or biodegradable plastics.
4. Water Conservation: Water is used in large CNC machining for cooling purposes. Implementing water-saving measures, such as recycling and reusing coolant, can minimize water consumption and reduce the strain on freshwater resources.
5. Emissions Reduction: CNC machines can generate harmful emissions, including volatile organic compounds (VOCs) and particulate matter. Employing emission control technologies and methodologies can help mitigate air pollution and promote cleaner air quality.
6. Supply Chain Management: Ensuring sustainability throughout the supply chain is crucial. Manufacturers should partner with suppliers who align with sustainable practices, such as using environmentally friendly transportation methods or adhering to responsible sourcing principles.
7. Employee Training: Educating and training employees on sustainability practices can be instrumental in achieving environmental goals. This can include energy conservation awareness, waste reduction, and proper handling of hazardous materials.
By integrating sustainability and environmental considerations into large CNC machining manufacturing processes, companies can not only reduce their environmental impact but also enhance their reputation as responsible and eco-conscious organizations. This approach contributes to long-term sustainability and helps preserve the planet for future generations.
List The Evolution history of “large cnc machining”
The evolution of large CNC machining can be traced back to the early 1950s when numerical control (NC) technology was first developed. Initially, these machines were manually operated and required skilled operators to input the desired coordinates for each machining operation. This limited their use to only a few industries and applications.
In the 1960s, the introduction of computer technology revolutionized the CNC machining industry. With the development of computer numerical control (CNC), machines were capable of automatically executing complex machining operations based on pre-programmed instructions. This led to increased precision, efficiency, and versatility in large machining processes.
Throughout the 1970s and 1980s, CNC machining continued to evolve with advancements in computer software and hardware. Control systems became more sophisticated, enabling machines to handle larger workpieces and perform multiple operations simultaneously. This increased the capabilities and productivity of large CNC machines, making them essential tools in various industries such as aerospace, automotive, and manufacturing.
In the 1990s, machine builders began incorporating advanced technologies like dual-spindle configurations, multi-axis capabilities, and high-speed machining into large CNC machines. These advancements allowed for increased accuracy, reduced cycle times, and improved overall performance.
The early 2000s witnessed the integration of CAD/CAM software and simulation tools into CNC machining systems. These innovations facilitated the design, programming, and optimization of large-scale machining processes, leading to enhanced productivity and reduced errors.
In recent years, the use of advanced materials and complex geometries in various industries has driven further advancements in large CNC machining. Cutting-edge technologies like robotics, additive manufacturing, and real-time monitoring systems are being integrated into CNC machines to enhance automation, agility, and flexibility.
Looking ahead, the future of large CNC machining is expected to involve the integration of artificial intelligence (AI) and machine learning algorithms. This will enable self-optimization, predictive maintenance, and adaptive machining strategies, further pushing the boundaries of what is possible with these powerful machines.
In conclusion, from the manual operation of early NC machines to the highly automated and technologically advanced CNC systems of today, the evolution of large CNC machining has been characterized by continuous advancements in software, hardware, and automation technologies. These advancements have revolutionized industries, enabling the production of complex and precise parts on a large scale.
The Evolution and Market Trends in large cnc machining Industry
The large CNC machining industry has undergone significant evolution over the years, with advancements in technology leading to improved efficiency, accuracy, and capabilities. CNC (Computer Numerical Control) machining is a process that utilizes computer-aided design (CAD) and computer-aided manufacturing (CAM) to control the movements of machine tools and create complex parts with high precision.
One of the key trends that have emerged in the large CNC machining industry is the adoption of advanced machining techniques such as multi-axis machining. This allows for the simultaneous movement of multiple axes, enabling the creation of more complex geometries and reducing the need for multiple setups. As a result, manufacturers can produce intricate and custom-designed components more efficiently and at a lower cost.
Another significant trend in the market is the integration of automation and robotics in CNC machining processes. Automated systems can handle repetitive tasks, enhance productivity, and minimize errors, resulting in increased throughput and reduced lead times. Additionally, the integration of robotics enables lights-out manufacturing, where machines can run continuously without human intervention, further optimizing efficiency and reducing labor costs.
The industry has also witnessed the development of more advanced and specialized CNC machining centers. These machines are equipped with higher horsepower, faster spindle speeds, and greater tool capacity, allowing for increased material removal rates and improved overall performance. Moreover, the introduction of hybrid CNC machines that combine multiple machining operations in a single unit has led to space savings and enhanced workflow.
Furthermore, there has been a growing emphasis on sustainability in the large CNC machining industry. Manufacturers are increasingly adopting eco-friendly practices, such as using environmentally-friendly machining fluids, optimizing energy consumption, and reducing waste through recycling and reclamation processes. This trend aligns with the global movement towards sustainability and helps companies lower their carbon footprint.
Overall, the large CNC machining industry has evolved significantly, driven by advancements in technology and changing market demands. The adoption of advanced machining techniques, integration of automation and robotics, development of specialized machining centers, and the focus on sustainability are all key trends in the industry. These trends have enabled manufacturers to produce complex parts more efficiently, reduce lead times, and enhance overall productivity, positioning the industry for continued growth in the future.
Custom Private Labeling and Branding Opportunities with Chinese large cnc machining Manufacturers
Chinese large CNC machining manufacturers offer custom private labeling and branding opportunities to businesses looking to establish their own unique identity in the market. These manufacturers have extensive experience in producing high-quality CNC machined parts and components, catering to a wide range of industries such as automotive, aerospace, electronics, and more.
With custom private labeling, businesses can imprint their own logo, design, and other relevant information on the products manufactured by these Chinese suppliers. This helps in creating brand recognition and building a loyal customer base. Whether it’s small-scale or high-volume production, these manufacturers can meet the customized labeling requirements of businesses.
Moreover, Chinese large CNC machining manufacturers also offer branding opportunities by providing options for custom packaging. Businesses can choose to have their products packaged in unique and attractive boxes, pouches, or containers, along with the customized labels. This enhances the overall presentation and market appeal of the products.
Collaborating with Chinese large CNC machining manufacturers for private labeling and branding also comes with benefits such as cost-effectiveness and quick turnaround times. These manufacturers often offer competitive pricing for customized products, enabling businesses to have a favorable profit margin. Additionally, their efficient production processes and speedy delivery ensure timely fulfillment of orders.
In conclusion, Chinese large CNC machining manufacturers present businesses with lucrative opportunities for custom private labeling and branding. By partnering with these manufacturers, businesses can establish their own unique identity in the market and present high-quality products with customized labeling and packaging. With cost-effective pricing and quick turnaround times, these manufacturers prove to be reliable partners in helping businesses create a distinct brand image.
Tips for Procurement and Considerations when Purchasing large cnc machining
When purchasing large CNC machining equipment, there are several important considerations to keep in mind to ensure a successful procurement process. Here are some tips and factors to consider:
1. Determine your requirements: Clearly define your needs and specifications for the CNC machine. Consider factors such as size, capacity, and functionality to make sure it aligns with your business objectives.
2. Research suppliers: Conduct thorough research to identify reputable suppliers with a proven track record in delivering high-quality CNC machines. Get recommendations from industry peers, read online reviews, and visit trade shows to find reliable suppliers.
3. Quality assurance: Check if the supplier follows stringent quality control measures during the manufacturing process. Ensure that the CNC machine complies with industry standards and certifications, as well as safety regulations to avoid any operational or safety issues.
4. Technical support and training: Inquire about the availability of technical support and training programs provided by the supplier. Proper training and ongoing technical assistance are essential for a successful integration and operation of the large CNC machine.
5. Long-term viability: Consider the long-term viability of the supplier and their ability to provide spare parts, maintenance, and repairs. Choose a supplier with a strong presence in the industry and a good reputation for after-sales support.
6. Cost-benefit analysis: While cost is an important factor, it should not be the sole criteria for decision-making. Consider the overall value for money, including the quality, durability, and maintenance costs of the machine. Calculate the return on investment (ROI) to justify the purchase.
7. Testimonials and references: Request testimonials and references from the supplier to gauge their previous clients’ satisfaction with the purchased equipment. This can provide valuable insights into the supplier’s credibility and customer service.
8. Negotiate warranty terms: Negotiate warranty terms and conditions that cover any potential defects, damage, or malfunctioning of the CNC machine. Ensure that you have a clear understanding of what is covered under warranty and how any issues will be addressed.
9. Scalability and expansion: Consider the scalability of the machine to accommodate potential growth and expansion of your business. Discuss with the supplier if the CNC machine can be easily upgraded or customized in the future to meet changing demands.
10. Assess energy efficiency: Evaluate the energy efficiency of the large CNC machine to understand its impact on your operational costs. Opting for energy-efficient equipment can result in long-term savings and sustainability.
By considering these tips and factors during the procurement process, you can ensure the purchase of a large CNC machining equipment that meets your business requirements, supports growth, and provides value for your investment.
FAQs on Sourcing and Manufacturing large cnc machining in China
Q1: What is large CNC machining?
Large CNC machining refers to the process of using computer numerical control (CNC) technology to manufacture large-scale or oversized components or products. It involves using automated machines to control the movement of tools and machines to shape, cut, or carve out parts from raw materials such as metal or plastic.
Q2: Why source large CNC machining from China?
China is known for its vast manufacturing capabilities and cost-effective production. The country has a large number of skilled technicians, advanced machinery, and abundant raw materials, making it an ideal destination for sourcing large CNC machining. Chinese manufacturers also offer competitive prices, allowing businesses to save costs without compromising on quality.
Q3: What are the challenges in sourcing large CNC machining from China?
One of the major challenges is the language barrier. Communication with Chinese suppliers may require an interpreter if they do not speak English fluently. Additionally, there can be cultural differences and time zone challenges when coordinating production and delivery. Quality control is another concern, as not all Chinese suppliers maintain high standards. It is vital to thoroughly vet and verify the credibility and capabilities of manufacturers before finalizing any agreements.
Q4: How can I ensure quality control when sourcing large CNC machining from China?
To ensure quality control, it is essential to conduct thorough due diligence on potential manufacturers. This includes reviewing their certifications, assessing their production facilities, and requesting samples or prototypes for evaluation. Regular inspections during production, strict adherence to specifications, and implementing a comprehensive quality control plan can help maintain consistent product quality. It is also advisable to work with a reputable sourcing agent or third-party quality inspection company to provide oversight and ensure compliance with international standards.
Q5: How long does it take to manufacture large CNC machined parts in China?
The manufacturing lead time for large CNC machined parts in China can vary depending on factors such as the complexity of the component, quantity, and the specific manufacturing processes involved. Typically, it can range from a few weeks to a few months. Clear communication and proper planning with the manufacturer are crucial to establish realistic timelines and ensure timely delivery.
In conclusion, sourcing large CNC machining from China offers cost-effective advantages, but it comes with challenges such as language barriers, cultural differences, and quality control concerns. Conducting thorough due diligence, clearly communicating expectations, and implementing quality control measures are essential for successful sourcing and manufacturing in China.
Why contact sourcifychina.com get free quota from reliable large cnc machining suppliers?
Sourcifychina.com is able to obtain a free quota from reliable large CNC machining suppliers for a few reasons. Firstly, Sourcifychina.com is a reputable platform that connects buyers with suppliers in China. It has established long-term partnerships with various reliable manufacturing companies, including large CNC machining suppliers.
These suppliers offer a free quota to Sourcifychina.com as a way to attract potential buyers and showcase their services and capabilities. By providing a designated quantity of products or services for free, suppliers can demonstrate the quality of their CNC machining capabilities, gain exposure to a wider customer base, and potentially secure long-term business opportunities.
Furthermore, the free quota offer serves as a marketing strategy for suppliers to differentiate themselves from competitors and gain a competitive edge in the market. By partnering with Sourcifychina.com and offering a free quota, suppliers can leverage the platform’s user base and reach a broader audience of potential buyers who are actively seeking CNC machining services.
For Sourcifychina.com, this free quota arrangement allows them to offer an added benefit to their customers. By accessing a free quota from reliable large CNC machining suppliers, buyers can test the quality and efficiency of the suppliers’ work without any financial commitment. It provides an opportunity for buyers to assess the compatibility of the supplier’s capabilities with their specific requirements before proceeding with larger orders.
In conclusion, Sourcifychina.com receives a free quota from reliable large CNC machining suppliers as it benefits both parties involved. Suppliers can showcase their capabilities to a wider audience, while buyers can evaluate the suitability and quality of the services without upfront costs.