Introduce about lathe machining parts guide,Qulity,Cost,Supplier,Certification,Market,Tips,FAQ
Lathe machining parts play a crucial role in various industries, serving as key components in the production process. This guide aims to provide an overview of these parts, including quality, cost, suppliers, certifications, market, tips, frequently asked questions (FAQs), and more.
Quality is a vital aspect when it comes to lathe machining parts. These parts need to be durable, precise, and reliable to ensure optimal performance. Manufacturers use high-quality materials, such as stainless steel, aluminum, brass, and various alloys, to produce parts that meet specific requirements.
The cost of lathe machining parts can vary depending on factors like complexity, material, size, and quantity. It is essential to consider different suppliers to compare prices and services offered. Some suppliers may provide bulk discounts or custom manufacturing options, which can help reduce costs.
When choosing a supplier for lathe machining parts, it is crucial to evaluate their reputation, reliability, and expertise. Look for suppliers with extensive experience in the industry, a track record of delivering high-quality products, and positive customer feedback.
Certification is an essential consideration for lathe machining parts. Suppliers who hold certifications, such as ISO 9001, demonstrate their commitment to quality management systems. Certification ensures that the parts meet certain industry standards and undergo rigorous testing and inspection procedures.
The market for lathe machining parts is extensive, serving industries like automotive, aerospace, electronics, medical, and more. As technology advances, the demand for innovative and precise machining parts continues to grow. Suppliers must stay up to date with industry trends and invest in the latest machinery and techniques to remain competitive.
Here are a few additional tips when dealing with lathe machining parts:
1. Clearly communicate your requirements to the supplier to ensure they understand your needs accurately.
2. Regularly maintain and inspect the parts to ensure optimal performance and longevity.
3. Work closely with the supplier to address any concerns or issues that may arise during the manufacturing process.
Frequently asked questions (FAQs) about lathe machining parts may include queries about turnaround time, minimum order quantities, customization options, material selection, and quality control measures. It is advisable to reach out to suppliers directly to get comprehensive answers to specific questions.
In conclusion, lathe machining parts are essential components in various industries, providing durability, precision, and reliability. Choosing a reputable supplier, considering quality, cost, certifications, and market demands, is crucial for obtaining high-quality parts. Regular maintenance and clear communication with suppliers contribute to achieving optimal performance and satisfaction with these machining parts.
Types of lathe machining parts
There are several types of lathe machining parts that are commonly used in various industries. These parts serve different purposes and are crucial in the overall functioning of the lathe machine. Some of the prominent lathe machining parts are:
1. Chuck: A chuck is used to hold the workpiece firmly in place, allowing it to rotate while being machined. It is available in different types such as three-jaw, four-jaw, and six-jaw chucks, each offering unique advantages based on the specific application.
2. Tailstock: The tailstock is an important part of a lathe machine that provides support to the workpiece during machining. It is adjustable and can be moved forward or backward as required. The tailstock often contains a live center to prevent the workpiece from bending under stress.
3. Carriage: The carriage is responsible for the movement of the cutting tool and the workpiece. It consists of several parts like saddle, apron, cross-slide, and compound rest. The saddle moves along the bed, while the cross-slide allows lateral movement of the cutting tool.
4. Toolpost: The toolpost holds the cutting tool at the desired height and angle. It is essential for accurate machining and can be adjusted as per the requirements of the job. Quick change toolposts are also available that allow for easy and rapid tool changes.
5. Lead Screw: The lead screw is responsible for the longitudinal movement of the carriage. It is driven by gears and transmits power from the spindle to the carriage. The thread on the lead screw determines the rate of movement and accuracy of the lathe machine.
6. Headstock: The headstock houses the main spindle, which is responsible for rotating the workpiece. It provides the necessary power and speed for machining operations. The headstock also contains mechanisms for changing spindle speed and direction.
7. Steady Rest: A steady rest is used to support long and slender workpieces that tend to vibrate during machining. It prevents the workpiece from deflecting and ensures accurate machining along the entire length.
8. Follow Rest: A follow rest is similar to a steady rest but supports the workpiece on the opposite side of the cutting tool. It is used when machining requires extra support to prevent deflection and maintain consistent accuracy.
9. Chuck Key: A chuck key is used to tighten or loosen the chuck. It is a hand tool that consists of a handle and a gear to engage the chuck’s teeth.
In conclusion, these are some of the essential lathe machining parts that play vital roles in ensuring accurate and efficient machining operations. Each part serves a specific function and contributes to the overall performance and versatility of the lathe machine.
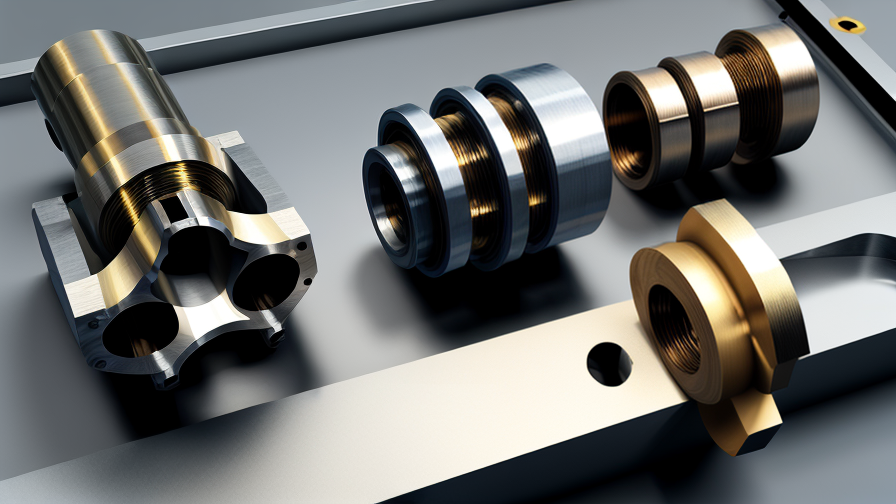
Pros and Cons of Using lathe machining parts
Lathe machining parts offer several advantages and disadvantages when it comes to manufacturing processes and product performance. Here are some of the pros and cons of using lathe machining parts:
Pros:
1. Versatility: Lathe machining parts are highly versatile and can be used to create a wide range of complex shapes and designs. This makes them ideal for creating custom components with intricate details.
2. High precision: Lathe machining is known for its high precision and accuracy. It allows for tight tolerances, ensuring consistent and precise dimensions for each part produced. This is crucial for industries that demand strict quality control.
3. Cost-effective: Compared to other machining methods, lathe machining can be more cost-effective, especially for small to medium-sized production runs. Its efficiency and minimal material wastage contribute to cost savings over time.
4. Wide range of materials: Lathe machining parts can be manufactured from a variety of materials, including metals, plastics, and even composites. This flexibility allows for tailored solutions for specific applications depending on mechanical, thermal, and chemical properties required.
5. Time-saving: Lathe machining parts offer fast turnaround times and short lead times for production runs. The simplicity of the process and the ability to work with multiple materials contribute to quick manufacturing cycles.
Cons:
1. Limited size and shape options: Lathe machining parts have limitations when it comes to the size and shape of components that can be produced. Complex geometries may require additional secondary operations or different machining methods.
2. Material waste: While lathe machining is generally efficient, some waste is inevitable due to the subtraction of material. This can result in increased material costs, especially when working with expensive or hard-to-source materials.
3. Limited surface finishes: Lathe machining parts may have limitations when it comes to surface finishes and textures. Achieving certain surface qualities may require secondary operations or additional finishing techniques, increasing production time and costs.
4. Size limitations: Lathe machining is typically suitable for smaller to medium-sized parts. Larger components may require more specialized equipment, leading to increased production costs and time.
5. Specialized expertise required: Operating a lathe machine and producing high-quality parts requires specialized training and expertise. Finding skilled technicians or outsourcing the machining process can add additional costs and dependencies.
In conclusion, lathe machining parts offer versatility, precision, and cost-effective solutions for many manufacturing applications. However, they may have limitations in terms of component size, shape options, surface finishes, and require specialized knowledge to operate effectively.
lathe machining parts Reference Specifications (varies for different product)
Lathe machining is a process used to shape and create various parts for different products. It involves the use of a lathe machine, which rotates a workpiece while a cutting tool is moved across it to remove material and shape it into the desired form.
When machining parts on a lathe, there are certain reference specifications that need to be followed to ensure the accuracy and quality of the finished product. These specifications can vary depending on the specific part being machined and the requirements of the product it will be used in.
Some common reference specifications for lathe machining parts include:
1. Dimensions: The dimensions of the part, such as its length, diameter, and any specific measurements required for fitment or assembly, need to be precisely followed to ensure proper functionality.
2. Tolerances: Tolerances define the allowable variation in dimensions from the specified size. It is crucial to maintain tight tolerances to ensure parts fit and function correctly.
3. Surface finish: The surface finish required for the part needs to be specified. This could range from rough to smooth, depending on the intended application.
4. Material: The material used for the part needs to be specified to ensure the correct cutting tools and machining techniques are used. Different materials have different properties that can influence the machining process.
5. Machining operations: The specific machining operations, such as turning, facing, drilling, or threading, need to be specified to ensure the correct sequence and methods are used to produce the desired shape.
6. Additional features: Any additional features or specifications, such as slots, holes, or grooves, need to be clearly defined to ensure they are accurately machined.
By following these reference specifications, manufacturers can ensure that the machined parts meet the required standards and function as intended. It is important to note that these specifications may vary significantly depending on the specific product and its application. Therefore, close collaboration between the design engineers and machining experts is crucial to achieving the desired results.
In conclusion, lathe machining parts require adherence to reference specifications that vary depending on the specific product. Dimensions, tolerances, surface finish, material, machining operations, and additional features need to be clearly defined to ensure the successful production of high-quality, accurate parts.
Applications of lathe machining parts
Lathe machining parts find extensive applications across various industries:
1. Automotive Industry: Lathe machining is commonly used to produce engine components such as pistons, connecting rods, and crankshafts. Additionally, brake rotors, wheel hubs, and other automotive parts can be accurately machined using a lathe.
2. Aerospace Industry: Lathe machining is crucial for producing precision aircraft components like turbine blades, compressor parts, and landing gear components. The high level of accuracy and intricate detailing offered by lathes make them indispensable in aerospace manufacturing.
3. Electronics Industry: Lathes are utilized in the production of electronic components such as connectors, pins, and sockets. These components require precise tolerances and smooth finishes, which can be achieved through lathe machining.
4. Medical Industry: Lathe machining plays a significant role in the production of various medical instruments and devices. For instance, surgical implants like knee or hip replacement components are manufactured using a lathe for precise shaping and accurate dimensions.
5. Tool Manufacturing: Lathe machining is extensively employed in tool manufacturing to produce a wide range of tools, including drills, taps, dies, and cutting tools. Lathes enable the creation of customized tool geometries and profiles as per specific requirements.
6. Defense Industry: The defense sector utilizes lathe machining for manufacturing various components of military equipment, including artillery shells, gun barrels, missile parts, and armored vehicle components. Precision and strength are critical in such applications, and lathes provide the required accuracy.
7. Furniture Industry: Lathe machining is used in the production of wooden components for furniture, such as table legs, chair spindles, and decorative elements. Lathes enable the creation of intricate designs and smooth surfaces on wooden pieces.
8. Energy Industry: Lathes are essential for manufacturing components used in energy generation, including turbine shafts, rotor blades, and generator parts. The accuracy and efficiency offered by lathe machining contribute to the reliability and performance of energy systems.
9. Construction Industry: Lathe machining is involved in producing building components like balusters, stair railings, columns, and decorative architectural features. Lathes enable the creation of aesthetically appealing and durable building elements.
In conclusion, lathe machining parts find versatile applications across numerous industries, including automotive, aerospace, electronics, medical, tool manufacturing, defense, furniture, energy, and construction. The ability to achieve accurate dimensions, intricate detailing, and smooth surfaces makes lathes indispensable in modern manufacturing processes.
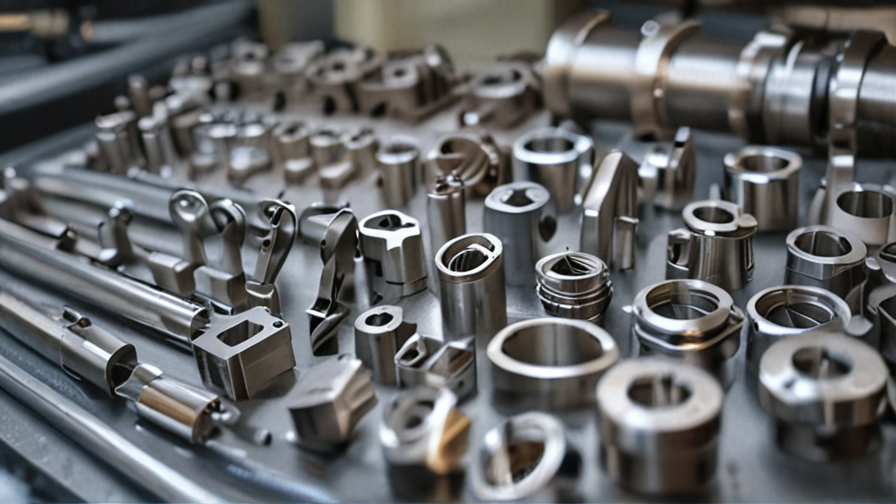
The Work Process and how to use lathe machining parts
Lathe machining is a process used to shape and create precision parts. It involves the use of a lathe machine, which rotates a workpiece against a cutting tool to remove material and achieve the desired shape. Understanding the work process and how to effectively use lathe machining parts is crucial for successful production.
The first step in the work process is to select the appropriate lathe machine for the desired task. Lathe machines come in different sizes and configurations, so choosing the right one for the job is essential. Once the machine is set up and the workpiece is secured on the spindle, the cutting tool is positioned to make the necessary cuts.
To begin machining, the lathe machine is activated, and the workpiece starts rotating. The cutting tool, controlled by the machine operator, is then brought into contact with the rotating workpiece. The tool is carefully guided along the workpiece surface to remove material and shape it according to the desired specifications. Different tools, such as turning tools, boring tools, and threading tools, can be used depending on the required machining operation.
During the machining process, it is important to maintain proper cutting speeds and feeds to ensure efficient material removal and avoid tool wear. The operator must monitor the machining operation, making adjustments as needed to achieve the desired results. Additionally, proper lubrication and cooling should be employed to prevent overheating of the workpiece and prolong the life of the cutting tools.
After completing the machining operation, the finished part is carefully examined for accuracy and quality. Any necessary post-machining processes, such as deburring or polishing, may be performed to achieve the desired surface finish.
To effectively use lathe machining parts, operators must have a strong understanding of the machine’s capabilities and limitations. They should be knowledgeable about cutting tool selection, machining techniques, and proper maintenance of the equipment. Training and experience are key in ensuring safe and successful lathe machining operations.
In conclusion, lathe machining is a versatile and widely used process for creating precision parts. By understanding the work process and effectively using lathe machining parts, operators can produce high-quality components efficiently and accurately.
Quality Testing Methods for lathe machining parts and how to control the quality
When it comes to quality testing methods for lathe machining parts, there are several approaches to ensure that the produced parts meet the required standards. Here, we will discuss some common methods and strategies to control the quality during lathe machining.
Firstly, one of the most widely used methods is dimensional measurement. This involves using precision instruments such as calipers, micrometers, and gauges to measure the dimensions of the machined parts accurately. These measurements are then checked against the specified tolerances to ensure that the parts are within the acceptable range.
Another important quality testing method is visual inspection. This involves visually examining the machined parts for any signs of defects, such as surface finish imperfections, cracks, or burrs. Proper lighting and magnifying tools can be used to enhance the inspection process and identify even minor flaws that might affect the functionality or aesthetics of the parts.
Functional testing is also crucial to ensure the quality of lathe machining parts. This involves conducting tests to evaluate and validate the functional performance of the parts. For example, if the machined part is meant to rotate, a functionality test can be performed to verify smoothness, alignment, and accuracy of the rotation. Similarly, if the part is meant to connect with other components, assembly tests can be conducted to ensure proper fit and functionality.
In addition to these testing methods, process control is equally important to maintain the quality of lathe machining parts. This involves continuously monitoring and adjusting the machining parameters like cutting speed, feed rate, and tool wear to keep the process in control. Implementing statistical process control techniques and regular machine maintenance can also contribute to consistent and controlled production.
To summarize, quality testing methods for lathe machining parts include dimensional measurement, visual inspection, and functional testing. Process control through monitoring and adjustment of machining parameters is vital to maintain quality. By combining these methods and implementing rigorous quality control protocols, manufacturers can produce high-quality lathe machining parts that meet or exceed customer expectations.
lathe machining parts Sample Policy and Post-Purchase Considerations for lathe machining parts from China
Sample Policy:
When purchasing lathe machining parts from China, it is important to establish a clear and comprehensive sample policy to ensure the quality and suitability of the products. The following sample policy can be implemented:
1. Request for initial product samples: Before placing a bulk order, request samples of the lathe machining parts from the supplier. This will allow you to assess the quality, dimensions, and performance of the parts.
2. Inspection and testing of samples: Conduct a thorough inspection and testing of the samples to ensure that they meet your specific requirements and standards. Verify the accuracy of dimensions, the functionality of moving parts, and the overall durability.
3. Request for multiple samples: To minimize the risk of receiving inconsistent or faulty parts, request samples from different batches or production runs. This will help determine if the supplier maintains consistency in quality across different manufacturing cycles.
4. Detailed specifications: Provide the supplier with detailed specifications for the desired lathe machining parts, including materials, dimensions, finish, and any specific tolerance requirements. Clear communication is essential to avoid any misunderstandings or discrepancies in the final products.
5. Documentation of sample approval: Once the samples have been thoroughly inspected and tested, document the approval or disapproval of the samples. This will serve as a reference point during the production process and will help hold the supplier accountable for delivering consistent quality.
Post-Purchase Considerations:
After purchasing lathe machining parts from China, the following considerations should be taken into account:
1. Regular quality control inspections: Conduct regular quality control inspections throughout the production process to ensure that the supplier maintains the agreed-upon standards. This will help identify any deviations or issues early on and allow for timely corrective actions.
2. Communication and feedback: Maintain open and effective communication with the supplier to address any concerns or queries promptly. Provide feedback on the quality of the received parts and collaborate with the supplier to improve any deficiencies.
3. Performance evaluation: Evaluate the performance of the lathe machining parts in real-world applications. Assess the durability, accuracy, and reliability of the parts and determine if they meet your expectations and requirements.
4. Supplier relationship: Establish a good working relationship with the supplier based on mutual trust and transparency. Maintain regular communication, visit their manufacturing facilities if possible, and invest in building a long-term partnership for continuous improvement.
5. Retaining samples: Retain some samples from each batch or order as a reference for future quality comparisons. This will enable you to track any changes or discrepancies in the quality and quickly identify any issues.
In conclusion, implementing a comprehensive sample policy and post-purchase considerations when sourcing lathe machining parts from China is essential to ensure quality, reliability, and customer satisfaction.
Sourcing lathe machining parts from China: Opportunities, Risks, and Key Players
Sourcing lathe machining parts from China can present various opportunities for businesses. China is known for its vast manufacturing capabilities and competitive pricing, making it an attractive option for companies looking to acquire lathe machining parts at a lower cost. The country also has a large pool of skilled labor, enabling manufacturers to produce high-quality parts efficiently.
One of the significant advantages of sourcing from China is the availability of a wide range of lathe machining parts. Chinese manufacturers offer a comprehensive selection of standard and customized parts, allowing businesses to find the perfect match for their specific requirements. Additionally, many Chinese suppliers are experienced in working with international clients, making communication and transaction processes relatively smooth.
However, there are risks to consider when sourcing from China. Quality control can be a concern, as there may be variations in the quality of parts, especially when dealing with different suppliers. Conducting rigorous due diligence, such as requesting samples, certifications, and visiting manufacturing facilities, is essential to mitigate these risks. Intellectual property protection is another consideration, as counterfeit products and unauthorized replicas can pose a threat to businesses. Ensuring proper contracts and agreements with suppliers that address intellectual property rights is crucial in protecting one’s interests.
Several key players dominate the lathe machining parts market in China. Some notable companies include Shenyang Machine Tool Co., Ltd., Dalian Machine Tool Group Corporation, and Qingdao Chuangming Commerce and Trade Co., Ltd. These companies have established themselves as reliable suppliers of lathe machining parts, adhering to strict quality standards.
In conclusion, sourcing lathe machining parts from China presents opportunities in terms of cost-effectiveness, a wide range of available parts, and skilled manufacturing labor. However, risks related to quality control and intellectual property protection need to be carefully managed. By engaging with reputable suppliers and implementing proper due diligence measures, businesses can leverage the advantages of sourcing from China while minimizing potential risks.
How to find and select reliable lathe machining parts manufacturers in China,use google search manufacturers and suppliers
Finding and selecting reliable lathe machining parts manufacturers in China can be a daunting task. However, by using Google search and following a few simple steps, you can narrow down your options and find trustworthy suppliers. Here’s a guide to help you in your search, using not more than 300 words.
1. Begin by conducting a Google search using relevant keywords such as “lathe machining parts manufacturers in China.” This will provide you with a list of potential suppliers.
2. Visit the websites of the manufacturers that appear in your search results. Look for clear and comprehensive product information, including specifications, certifications, and any quality control measures they follow.
3. Check if the manufacturer provides detailed contact information, such as a physical address, phone number, and email address. A reliable manufacturer will have transparent communication channels.
4. Look for customer reviews or testimonials on the manufacturer’s website or search for them separately. This will help you gauge the manufacturer’s reputation and customer satisfaction level.
5. Verify the manufacturer’s experience and expertise in lathe machining parts. Look for information about their manufacturing facilities, machinery, and ability to meet your specific requirements.
6. Check if the manufacturer has the necessary certifications and quality management systems in place. Some common certifications include ISO 9001, ISO 14001, and ISO 45001.
7. Contact the manufacturer directly and ask for additional information or clarification. A reputable manufacturer will be responsive and willing to answer your questions promptly.
8. Request samples or a product catalog to evaluate the quality of their lathe machining parts. This will allow you to assess their precision, durability, and overall performance.
9. Inquire about the manufacturer’s production capacity and lead times. Ensure they can accommodate your production requirements within the desired timeframe.
10. Obtain multiple price quotes from different manufacturers and compare them. However, beware of significantly low prices, as they may indicate compromised quality.
11. If possible, visit the manufacturer’s facilities in person to assess their manufacturing processes, quality control measures, and to build a personal relationship.
12. Consider working with a sourcing or inspection agent who has on-the-ground experience in China. They can help you verify the manufacturer’s credibility and conduct quality inspections.
By following these steps, you can find and select reliable lathe machining parts manufacturers in China, ensuring the quality of your products and a smooth business relationship.
How to check lathe machining parts manufacturers website reliable,use google chrome SEOquake check if ranking in top 10M
When evaluating the reliability of a lathe machining parts manufacturer’s website, you can follow a few steps to ensure credibility.
1. Use Google Chrome: Firstly, ensure that you are using Google Chrome as your web browser as it offers useful extensions to help assess the website’s reliability.
2. Install SEOquake: Add the SEOquake extension to your Chrome browser. This tool will provide essential information about the website’s search engine rankings, including its placement within the top 10 million websites.
3. Check Search Engine Ranking: Once SEOquake is installed, perform a Google search using relevant keywords related to the lathe machining parts manufacturer. You should find the manufacturer’s website among the top search results. If it falls within the top 10 million placements, it indicates that the website receives a significant amount of traffic and is more likely to be reliable.
4. Assess Website Quality: Review the website’s design, user interface, and overall aesthetic appeal. A professionally designed website with an easy-to-navigate layout suggests that the manufacturer is investing in their online presence and reflects a more reliable business.
5. Verify Contact Information: Look for clear and accurate contact information, such as a physical address, phone number, and email address. Reliable manufacturers will provide transparent ways to reach them, indicating a commitment to open communication.
6. Validate Certifications and Quality Standards: Check for industry certifications, quality standards, or any other relevant accreditations prominently displayed on the website. These affiliations demonstrate the manufacturer’s commitment to meeting specified criteria and can enhance their credibility.
7. Examine Testimonials and Reviews: Look for customer testimonials or reviews on the website. Genuine reviews provide insights about the manufacturer’s products and services. Additionally, search for external reviews on other platforms to gain a more comprehensive understanding of their reputation.
By following these steps and using Google Chrome with the SEOquake extension, you can quickly evaluate a lathe machining parts manufacturer’s website reliability and make an informed decision about their credibility. Remember to also exercise discretion and consider additional factors, such as industry experience and customer feedback, before finalizing your decision.
Top 10 lathe machining parts manufacturers in China with each 160 words introduce products,then use markdown create table compare
1. Shanghai SIEG Machinery Co., Ltd. specializes in the production of precision lathe machining parts. Their product range includes turning tools, chucks, and cutting inserts. These parts are made from high-quality materials and are known for their durability and precision.
2. Shenzhen Ruizi Light and Electricity Technology Co., Ltd. is a leading manufacturer of lathe machining parts in China. Their products include precision mechanical components, such as shafts, gears, and pulleys. These parts are widely used in industries like automotive, aerospace, and electronics.
3. Ningbo Hewcho Industrial Limited offers a wide range of lathe machining parts, including bronze bushings, flange shafts, and aluminum alloy fittings. Their products are known for their excellent quality and reliability.
4. Jiangyin Shuanghui Machinery Co., Ltd. specializes in the production of lathe machining parts, such as precision shafts, bevel gears, and precision machining components. Their products are widely used in industries like automotive, medical, and aerospace.
5. Changzhou Mingquan Machinery Co., Ltd. is a leading manufacturer of lathe machining parts, including precision shafts, flanges, and CNC turning parts. Their products are known for their high precision and excellent performance.
6. Shenzhen Xindongyuan Precision Metal Co., Ltd. produces high-quality lathe machining parts, including CNC-turned parts, brass fittings, and stainless steel shafts. Their products are widely used in industries like electronics, telecommunication, and automotive.
7. Hangzhou ODM Precision Machinery Co., Ltd. offers a wide range of lathe machining parts, including aluminum alloy profiles, stainless steel tubes, and plastic connectors. Their products are characterized by their precision and reliability.
8. Shenzhen Guochanghong Precision Hardware Co., Ltd. specializes in the production of lathe machining parts, such as shafts, flanges, and brackets. Their products are known for their high quality and excellent performance.
9. Ningbo Xianglong Metal Products Co., Ltd. produces a variety of lathe machining parts, including stainless steel connecting pipes, copper fittings, and aluminum alloy components. Their products are widely used in industries like HVAC, automotive, and electronics.
10. Wuxi Baide Precision Machinery Co., Ltd. is a leading manufacturer of lathe machining parts, offering a wide range of products like precision shafts, gears, and bushings. Their products are known for their high precision, durability, and excellent performance.
| Manufacturer | Products | Industries Served |
|———————————–|—————————————————-|——————————————–|
| Shanghai SIEG Machinery Co., Ltd. | Turning tools, chucks, cutting inserts | Various industries including manufacturing, automotive |
| Shenzhen Ruizi Light and Electricity Technology Co., Ltd. | Precision mechanical components, shafts, gears | Automotive, aerospace, electronics |
| Ningbo Hewcho Industrial Limited | Bronze bushings, flange shafts, aluminum fittings | Various industries including automotive, aerospace |
| Jiangyin Shuanghui Machinery Co., Ltd. | Precision shafts, bevel gears, machining components | Automotive, medical, aerospace |
| Changzhou Mingquan Machinery Co., Ltd. | Precision shafts, flanges, CNC turning parts | Various industries including automotive |
| Shenzhen Xindongyuan Precision Metal Co., Ltd. | CNC-turned parts, brass fittings, stainless steel shafts | Electronics, telecommunication, automotive |
| Hangzhou ODM Precision Machinery Co., Ltd. | Aluminum alloy profiles, stainless steel tubes, plastic connectors | Various industries including electronics |
| Shenzhen Guochanghong Precision Hardware Co., Ltd. | Shafts, flanges, brackets | Various industries |
| Ningbo Xianglong Metal Products Co., Ltd. | Stainless steel connecting pipes, copper fittings, aluminum alloy components | HVAC, automotive, electronics |
| Wuxi Baide Precision Machinery Co., Ltd. | Precision shafts, gears, bushings | Various industries |
The table above compares the top 10 lathe machining parts manufacturers in China based on the products they offer and the industries they serve. These manufacturers produce a wide range of precision parts including shafts, gears, chucks, turning tools, and various other components. Industries served by these manufacturers include automotive, aerospace, electronics, HVAC, and more.
It is worth noting that the quality and precision of these lathe machining parts are highly regarded in the industry. With their exceptional reliability and performance, these manufacturers have gained a strong reputation both domestically and internationally. By utilizing advanced manufacturing techniques and high-quality materials, they continue to meet the stringent requirements of various industries.
The competitive edge of these manufacturers lies in their expertise, well-equipped facilities, strict quality control processes, and constant innovation. They remain committed to providing customers with reliable and high-performing lathe machining parts that contribute to the success of various industries worldwide.
Background Research for lathe machining parts manufacturers Companies in China, use qcc.com archive.org importyeti.com
When it comes to finding lathe machining parts manufacturers in China, there are several reliable platforms that can provide valuable information and facilitate the search process. Qcc.com, archive.org, and importyeti.com are some of the platforms that can help in this area.
Qcc.com is a renowned Chinese business information database that provides comprehensive details about various companies in China. The platform offers information on company profiles, contact details, and product lists. Users can search for lathe machining parts manufacturers in China and obtain information regarding their capabilities, certifications, and other relevant details.
Archive.org, on the other hand, is a digital library that provides access to web pages saved from the past. By utilizing this platform, one can access old versions of manufacturer’s websites or web pages that might not be active anymore. This can be helpful in obtaining historical data and understanding the development and growth of different manufacturers over time.
Importyeti.com is a popular directory specifically created for importers and exporters. It provides valuable data about various companies engaged in international trade, including lathe machining parts manufacturers. The platform offers information on import and export records, helping users identify potential manufacturers and assess their trading history.
By utilizing these platforms, one can gather essential information about lathe machining parts manufacturers in China. It is important to conduct thorough research regarding the capabilities, certifications, production capacity, and reputation of potential manufacturers. Additionally, one should also consider factors such as production lead time, quality control processes, and post-sales support before finalizing any manufacturer.
Leveraging Trade Shows and Expos for lathe machining parts Sourcing in China
Trade shows and expos are invaluable platforms for sourcing lathe machining parts in China. These events provide businesses with the opportunity to connect directly with manufacturers, suppliers, and industry professionals, making them an ideal avenue for engaging in face-to-face interactions and building fruitful business relationships.
Attending trade shows and expos allows companies to gain firsthand insights into the latest trends in lathe machining parts, discover new products, explore different manufacturing techniques, and assess the capabilities of various suppliers. Exhibitors at these events often showcase a wide range of parts, machinery, and technology, offering a comprehensive view of the industry and the available options.
Furthermore, trade shows and expos facilitate networking, allowing businesses to engage in discussions and negotiations with potential suppliers. This direct interaction enables companies to evaluate suppliers’ expertise, quality control processes, production capacities, and pricing structures. By engaging in face-to-face meetings, businesses can establish trust, enhance communication, and potentially negotiate more favorable terms.
Trade shows and expos in China, such as the China International Machine Tool Show (CIMT), the Canton Fair, and the Shanghai International Machine Tool Fair, are particularly important for sourcing lathe machining parts. These events gather a vast number of manufacturers and suppliers from all over the country, showcasing their products and capabilities on a large scale. The concentration of suppliers in one place allows for efficient comparison and evaluation of different options, saving both time and resources.
To make the most of these events, companies should invest time in preparing a clear sourcing strategy, identifying their specific requirements, and conducting thorough research on potential suppliers. Pre-scheduling meetings with selected suppliers can further optimize the sourcing process and ensure productive discussions.
In conclusion, trade shows and expos offer a unique opportunity to source lathe machining parts in China efficiently. Leveraging these events allows companies to engage directly with suppliers, discover new products, and gather valuable industry insights, ultimately aiding in effective sourcing and building successful business relationships.
The Role of Agents and Sourcing Companies in Facilitating lathe machining parts Purchases from China
Agents and sourcing companies play a crucial role in facilitating lathe machining parts purchases from China. These professionals act as intermediaries between buyers and suppliers, ensuring a smooth and efficient procurement process. Here, we discuss the key responsibilities and benefits of utilizing agents and sourcing companies for such purchases.
Firstly, agents and sourcing companies have extensive knowledge and experience in the Chinese market. They possess in-depth understanding of the local manufacturing landscape, including the various suppliers, their capabilities, and the quality of their products. This expertise enables them to identify reputable suppliers who can deliver high-quality lathe machining parts at competitive prices.
Moreover, agents and sourcing companies act as representatives of the buyers in China. They communicate with suppliers on behalf of the buyers, negotiating prices, lead times, and technical specifications. This relieves the buyers from the burden of dealing with language barriers, cultural differences, and time zone disparities. It also ensures effective communication and reduces the risk of misinterpretation or misunderstandings.
Furthermore, agents and sourcing companies conduct thorough supplier assessments to ensure compliance with international standards and regulations. They verify the supplier’s certifications, quality management systems, and production capabilities. This helps buyers to mitigate risks and make informed decisions based on reliable information. Additionally, agents and sourcing companies often conduct on-site visits and inspections to validate the supplier’s facilities and manufacturing processes.
In addition to these responsibilities, agents and sourcing companies offer logistical support, including arranging shipping, customs clearance, and delivery. They handle the complexities of international shipping, ensuring that the lathe machining parts reach the buyers in a timely manner and in good condition. This streamlines the entire procurement process and saves buyers the effort and time associated with logistics management.
In summary, agents and sourcing companies are indispensable in facilitating lathe machining parts purchases from China. Their expertise, local market knowledge, negotiation skills, supplier assessments, and logistical support greatly simplify the procurement process. By utilizing agents and sourcing companies, buyers can access a wide range of suppliers, benefit from competitive prices, and ensure the quality and timely delivery of their purchases.
Price Cost Research for lathe machining parts manufacturers Companies in China, use temu.com and 1688.com
When it comes to researching the price cost of lathe machining parts manufacturers in China, two popular online platforms that can be utilized are temu.com and 1688.com.
temu.com is a comprehensive sourcing platform that connects global buyers with suppliers in China. It provides users with a wide range of product options and gives them the ability to request quotations directly from manufacturers. By searching for lathe machining parts manufacturers on temu.com, buyers can get an idea of the price ranges offered by different suppliers for their required parts. Additionally, they can communicate with the manufacturers to negotiate prices and discuss specific requirements.
1688.com, on the other hand, is a Chinese business-to-business (B2B) e-commerce platform operated by Alibaba Group. It is mainly directed towards domestic buyers and sellers within China. However, by using translation tools or collaborating with a local agent, international buyers can also utilize this platform to research the price cost of lathe machining parts manufacturers. Similar to temu.com, users can search for manufacturers, compare prices, and communicate directly with suppliers on 1688.com.
To conduct an effective price cost research on these platforms, a few tips can be followed:
1. Be specific: Provide detailed specifications and requirements for the lathe machining parts you are looking for. This will help suppliers understand your needs accurately, and it will be easier to compare prices.
2. Request quotations: Utilize the request for quotation (RFQ) feature provided by both platforms. This allows you to reach out to multiple suppliers simultaneously and request quotations directly.
3. Compare prices and services: Carefully analyze the quotations received from different manufacturers. Consider factors such as price, quality, lead time, shipping options, and after-sales services.
4. Communicate effectively: Initiate communication with potential suppliers to discuss any further details or negotiate prices when necessary. Clear communication will help ensure that you obtain accurate pricing information.
By utilizing temu.com and 1688.com, buyers can efficiently conduct price cost research for lathe machining parts manufacturers in China. These platforms provide a wide range of options along with direct communication opportunities to establish reliable business relationships with manufacturers.
Shipping Cost for lathe machining parts import from China
When importing lathe machining parts from China, the shipping cost can vary depending on several factors. The two main factors that influence the shipping cost are the weight and volume of the parts being shipped and the shipping method chosen.
For lighter and smaller parts, air freight is a popular shipping method. Air freight is faster but can be more expensive compared to sea freight. The cost is calculated based on the dimensions and weight of the package. Shipping charges are typically higher for packages that exceed certain weight thresholds.
Sea freight is a more economical option for larger and heavier parts. The shipping cost is determined by the volume of the cargo, which is measured in cubic meters. Sea freight also takes longer for delivery compared to air freight.
In addition to the weight and volume, other factors such as the destination country, port charges, customs duties, and any additional services required can affect the shipping cost. It is essential to consider these factors when calculating the overall shipping cost.
To ensure cost-effectiveness, it is recommended to negotiate shipping rates with freight forwarders or shipping agents. These professionals have the expertise and contacts to provide competitive shipping quotes based on the specific requirements of lathe machining parts.
Furthermore, consolidating multiple shipments into a single container or utilizing less-than-container load (LCL) shipments can help optimize costs, especially for smaller orders.
In conclusion, when importing lathe machining parts from China, the shipping cost will depend on factors such as weight, volume, shipping method, destination, customs duties, and additional services. Negotiating shipping rates and considering consolidation options can help minimize costs and make the import process more cost-effective.
Compare China and Other lathe machining parts Markets: Products Quality and Price,Visible and Hidden Costs
China and other lathe machining parts markets differ in terms of product quality, price, visible and hidden costs.
When it comes to product quality, China has made significant progress in recent years. The country has invested heavily in improving manufacturing processes and technology, resulting in higher quality products. However, the quality can still vary depending on the manufacturer and price range. On the other hand, other lathe machining parts markets may have a reputation for higher quality products due to stringent regulations and quality control measures.
Price is another key factor in comparing China and other markets. China is known for its competitive pricing, offering lower costs for lathe machining parts. This is due to several factors such as lower labor and manufacturing costs. Other markets may have higher prices due to higher operating costs or stricter labor regulations.
Visible costs refer to the obvious expenses associated with purchasing lathe machining parts. In China, this includes the cost of the products themselves, transportation fees, and import duties or taxes. Other markets may have similar visible costs, but they can vary depending on the country and its specific trade regulations.
Hidden costs are the less obvious expenses that can arise from purchasing from a particular market. In China, hidden costs may include longer lead times, potential language barriers, and the need to navigate complex supply chains. Other markets may also have hidden costs such as limited product availability or higher shipping costs due to distance.
In summary, China and other lathe machining parts markets differ in terms of product quality, price, visible and hidden costs. While China has made strides in improving product quality, other markets may have a reputation for higher quality products. China offers lower prices due to lower manufacturing costs, while other markets may have higher prices due to various factors. Visible costs such as transportation fees and import duties exist in both markets, but hidden costs such as longer lead times and language barriers may be more prevalent in China. It is important for buyers to carefully consider these factors when comparing China with other lathe machining parts markets.
Understanding Pricing and Payment Terms for lathe machining parts: A Comparative Guide to Get the Best Deal
When it comes to obtaining machined parts for a lathe, understanding pricing and payment terms is crucial to ensure the best deal. This comparative guide seeks to shed light on these factors and enable buyers to make informed decisions.
Pricing for lathe machining parts can vary significantly depending on several factors. First and foremost, the complexity and design of the part play a significant role. More intricate designs often require additional machining operations and may result in higher costs. Similarly, the material used for the part is decisive in determining pricing, as certain materials are more expensive or require specialized machining techniques.
In addition to these factors, the quantity of parts ordered also affects the pricing. Manufacturers often offer volume discounts, where the per-unit cost decreases as the order size increases. Thus, it is advisable to consider the desired quantity when negotiating prices.
Apart from pricing, payment terms also play a crucial role in obtaining the best deal. Manufacturers commonly offer different options such as upfront payment, partial payment, or payment upon delivery. Understanding these terms is essential to align with the buyer’s financial capabilities and preferences.
Another aspect to consider is whether the manufacturer requires a minimum order quantity (MOQ). Some manufacturers may have a MOQ to cover their expenses and ensure profitability. It is advisable to inquire about this requirement as it can impact pricing, especially for smaller orders.
When comparing different suppliers, it is important to gather quotes from multiple sources to ensure a fair comparison. Additionally, obtaining samples from potential manufacturers can help assess their quality and compatibility with specific needs.
Furthermore, buyers should carefully review the offered warranties and return policies. A reputable manufacturer should provide assurances against defects or damages and have a clear return and refund process.
Engaging in effective communication with suppliers is key throughout the negotiation process. This includes discussing any possible customization requirements, lead times, and shipping arrangements. Clear and concise communication helps prevent misunderstandings and ensures a smooth transaction.
In conclusion, understanding pricing and payment terms is essential for securing the best deal when acquiring lathe machining parts. Considering factors such as part complexity, material, order quantity, payment options, MOQ, warranties, and effective communication can aid in making an informed decision. By taking a comparative approach and carefully evaluating these factors, buyers can achieve the most favorable outcome in terms of cost, quality, and delivery.
Chinese Regulations and Industry Standards Certifications for lathe machining parts,Import Regulations and Customs for lathe machining parts from China
Chinese Regulations and Industry Standards Certifications for lathe machining parts play a vital role in ensuring the quality and safety of these imported products. China has implemented a series of regulations and industry standards to regulate the production, operation, and import/export of lathe machining parts.
Firstly, one of the most important regulations is the “China Compulsory Certification” (CCC) system. This certification is mandatory for many products, including lathe machining parts, and ensures that they meet specific safety and quality requirements. Manufacturers and exporters of these parts must obtain CCC certification before they can be sold on the Chinese market or exported.
Additionally, there are various industry standards that specify the technical requirements and performance standards for lathe machining parts. These standards help guarantee the reliability and consistency of these products. Some commonly followed industry standards in China include GB (GuoBiao) standards and ISO (International Organization for Standardization) standards.
Regarding import regulations and customs for lathe machining parts from China, importing countries need to abide by their own customs policies and regulations. Generally, the imported lathe machining parts must meet certain criteria to be accepted into the importing country. These criteria may include proper documentation, compliance with safety and quality standards, and adherence to import duties and taxes.
Importers should be familiar with the customs requirements of their respective countries and ensure that the imported lathe machining parts comply with all relevant regulations. The import process may involve paperwork such as commercial invoices, packing lists, and certificates of origin. It is crucial to properly classify the imported products according to the Harmonized System (HS) code, which helps determine the applicable import duties and taxes.
In conclusion, Chinese regulations and industry standards certifications, such as the CCC system and various industry standards, ensure the quality and safety of lathe machining parts. Importers should be aware of their own country’s import regulations and customs requirements to successfully import these products from China.
Sustainability and Environmental Considerations in lathe machining parts Manufacturing
Sustainability and environmental considerations in lathe machining parts manufacturing are critical to minimize the negative impact on the planet and ensure a sustainable future. Several aspects should be taken into account to achieve sustainable practices:
1. Energy Efficiency: Implementing energy-efficient measures in lathe machining operations can significantly reduce the carbon footprint. This includes using energy-efficient motors, optimizing machine utilization, and employing smart energy management systems to minimize energy consumption.
2. Waste Reduction: Lathe machining can generate substantial waste materials such as metal shavings, coolant, and oils. Implementing recycling and waste reduction strategies like proper collection and recycling of metal shavings, treating and reusing coolant, and adopting responsible disposal methods for hazardous materials can help minimize waste and its impact on the environment.
3. Water Conservation: Water is used in cooling and lubrication processes during lathe machining. Employing water-saving technologies, such as closed-loop cooling systems, can help conserve water resources. Efficient use and recycling of water through filtration systems can reduce water consumption and minimize environmental impact.
4. Material Efficiency: Optimize material usage by employing efficient cutting techniques, reducing scrap, and promoting the use of sustainable materials. Choosing materials with lower environmental impacts and longer life cycles can contribute to a more sustainable manufacturing process.
5. Emission Reduction: Lathe machining can generate greenhouse gas emissions through energy consumption. Implementing emission reduction strategies such as improving equipment efficiency, utilizing renewable energy sources, and offsetting carbon emissions can help mitigate the environmental impact.
6. Supply Chain Management: Partnering with suppliers who prioritize sustainability and ecological responsibility can ensure that the raw materials used in lathe machining parts manufacturing are sourced ethically and sustainably.
7. Lifecycle Analysis: Conducting a lifecycle analysis of lathe machining parts can help identify areas where improvements can be made to minimize environmental impact. This analysis can consider the extraction of raw materials, production processes, product use, and end-of-life disposal or recycling.
In conclusion, sustainable practices in lathe machining parts manufacturing are crucial for preserving the environment. Emphasizing energy efficiency, waste reduction, water conservation, material efficiency, emission reduction, responsible supply chain management, and lifecycle analysis can lead to significant sustainability improvements in the manufacturing process.
List The Evolution history of “lathe machining parts”
Lathe machining parts have come a long way since their inception, evolving over centuries to meet the growing needs of industries and craftsmen. The evolution history of lathe machining parts can be summarized in the following key stages:
1. Ancient Lathes: The earliest known lathes date back to ancient Egypt, where simple handheld devices were used for woodworking. These lathes featured a rotating workpiece, which was manipulated by hand tools to shape it according to the craftsman’s requirements.
2. Medieval Period: During the medieval period, lathes advanced significantly, acquiring the treadle-powered mechanism. This innovation allowed craftsmen to use their feet to control the rotation of the workpiece, enabling them to have both hands free for shaping and cutting.
3. Industrial Revolution: The advent of the Industrial Revolution in the late 18th century brought about a significant leap forward in lathe machining parts. The introduction of steam power and the development of more advanced mechanisms, such as the slide rest, enabled the production of more precise and complex parts.
4. Electric Lathes: In the late 19th century, with the widespread use of electricity, lathe machining parts transitioned from steam-powered to electric-powered machines. Electric motors allowed for greater control over speeds, resulting in improved accuracy and efficiency.
5. CNC (Computer Numerical Control) Lathes: The introduction of computer technology revolutionized lathe machining parts in the late 20th century. CNC lathes made it possible to program complex shapes and automate the production process. This advancement led to increased precision, repeatability, and reduced production time.
6. Modern Innovations: Over the past few decades, lathe machining parts have continued to evolve. Advancements in materials, tooling, and cutting techniques have further improved performance and efficiency. Some contemporary lathe machines also incorporate features like automatic tool changers and live tooling, allowing for multitasking operations.
In conclusion, the evolution of lathe machining parts has been driven by advancements in technology and the need to meet the demands of various industries. From the simple handheld devices of ancient times to the advanced CNC lathes of today, lathe machining parts have transformed significantly, enabling the production of increasingly sophisticated and precise components.
The Evolution and Market Trends in lathe machining parts Industry
The lathe machining parts industry has witnessed significant evolution and market trends over the years. Initially, lathes were manually operated machines that required skilled workers to produce parts. However, with technological advancements, the industry has embraced automation, leading to increased efficiency and productivity.
One key evolution in the lathe machining parts industry is the adoption of Computer Numerical Control (CNC) technology. CNC lathes allow for precise and complex machining operations, reducing human errors and increasing accuracy. This technology has revolutionized the industry by enabling the production of intricate and high-quality parts with minimal human intervention.
Another notable evolution is the incorporation of advanced materials in lathe machining. Traditional lathes were primarily used to machine metals such as steel and aluminum. However, with the rise of industries like aerospace and defense, there is a growing demand for machining parts from advanced materials like composites, ceramics, and titanium alloys. Manufacturers have adapted to this trend by upgrading their machinery and using cutting tools specifically designed for these materials.
The market trends in the lathe machining parts industry are shaped by various factors. One significant trend is the increasing demand for customization. Customers now expect personalized parts that meet their specific requirements. This has led to the development of flexible manufacturing systems that can quickly adapt to unique specifications, enabling manufacturers to offer customized solutions.
Furthermore, there is a growing focus on sustainability and environmental friendliness. Manufacturers are implementing energy-efficient practices and utilizing recyclable materials to minimize their environmental impact. This trend is driven by both customer demands for eco-friendly solutions and regulatory requirements.
Additionally, the industry is witnessing a shift towards digitization and connectivity. Manufacturers are integrating their machines with Internet of Things (IoT) technologies, allowing real-time monitoring and data analysis. This enables predictive maintenance, optimizing machine performance, and reducing downtime.
In conclusion, the lathe machining parts industry has evolved significantly with the advent of CNC technology, the use of advanced materials, and the incorporation of customization and sustainability. The market trends reflect the increasing demand for personalized solutions and environmentally friendly practices. Embracing digitization and connectivity is crucial for staying competitive in this rapidly changing industry.
Custom Private Labeling and Branding Opportunities with Chinese lathe machining parts Manufacturers
Chinese lathe machining parts manufacturers offer excellent opportunities for custom private labeling and branding. With their advanced technology, efficient production methods, and cost-effective pricing, Chinese manufacturers can help businesses create high-quality products that are tailored to their brand’s specifications.
By collaborating with Chinese lathe machining parts manufacturers, businesses can benefit from their expertise in precision engineering and extensive production capabilities. These manufacturers possess a wide range of tools and equipment to handle various lathe machining requirements, such as turning, drilling, milling, and threading. This enables them to produce customized parts according to a brand’s specific design and functional requirements.
Additionally, Chinese manufacturers understand the importance of private labeling and branding. They offer services to incorporate a brand’s logo, packaging design, and other branding elements onto the products. With their experience in handling diverse manufacturing projects, they can ensure the branding requirements are met while maintaining the high quality of the manufactured parts.
Moreover, Chinese manufacturers often have extensive experience in global trade and international shipping. This makes it convenient for businesses to receive their customized products in a timely manner, regardless of their location.
However, while Chinese manufacturers offer significant advantages, businesses should undertake proper due diligence when selecting a partner. It is crucial to thoroughly research and assess potential manufacturers based on their credibility, past client references, quality certifications, and their ability to meet delivery timelines.
In conclusion, Chinese lathe machining parts manufacturers provide custom private labeling and branding opportunities. Their technological expertise, production capabilities, and understanding of branding requirements make them an ideal partner for businesses looking to create high-quality, customized products. By collaborating with these manufacturers, businesses can leverage their strengths in precision engineering and efficient production methods, while ensuring their brand identity is preserved.
Tips for Procurement and Considerations when Purchasing lathe machining parts
When it comes to procuring lathe machining parts, there are several tips and considerations that can help ensure a successful purchase. Here are some key points to keep in mind:
1. Identify your requirements: Clearly define the specifications, quality standards, and quantity needed for the lathe machining parts. This will help you in finding the right supplier who can meet your specific needs.
2. Research suppliers: Look for reputable suppliers with a proven track record in the industry. Consider factors such as experience, customer reviews, certifications, and past performance. Request references and evaluate their capabilities and reliability.
3. Quality assurance: Verify if the supplier follows strict quality control measures. Ask for quality certificates, inspection reports, and any other relevant certifications. Ensure that the parts meet industry standards and have undergone necessary testing and documentation.
4. Cost and pricing: Obtain detailed quotations from multiple suppliers to compare prices. Remember that the lowest price may not always guarantee the best quality. Analyze the pricing structure, payment terms, and any additional charges, such as shipping or taxes, to arrive at the most cost-effective option.
5. Manufacturing capabilities: Evaluate the supplier’s manufacturing capabilities, such as the type of lathe machines they use, their production capacity, and ability to handle custom orders. This is crucial for ensuring that the supplier can meet your demand and deliver within the required timeframe.
6. Communication and responsiveness: Choose a supplier that exhibits excellent communication skills and responsiveness. Timely and transparent communication is vital for effective collaboration and resolving any potential issues or concerns during the procurement process.
7. Warranty and after-sales support: Check for warranties provided by the supplier and inquire about their after-sales support. A reliable supplier should offer assistance in case of any defects, repairs, or replacements required after purchase.
8. Long-term relationship: Consider forming a long-term partnership with a trusted supplier. This can lead to more favorable pricing, improved delivery schedules, and better cooperation on future projects.
9. Read customer reviews and testimonials: Look for online reviews or testimonials from other customers who have purchased lathe machining parts from the supplier. This can provide valuable insights into the supplier’s reputation, customer service, and overall satisfaction level.
Remember that each procurement process may have unique requirements, and it is crucial to tailor the considerations to your specific needs. By diligently researching, evaluating, and selecting the right supplier, you can ensure a successful purchase of lathe machining parts.
FAQs on Sourcing and Manufacturing lathe machining parts in China
Q: Why should I consider sourcing and manufacturing lathe machining parts in China?
A: China has emerged as a global manufacturing hub, offering competitive prices, a vast supplier base, and advanced manufacturing capabilities. Chinese manufacturers specialize in producing high-quality lathe machining parts at lower costs than many other countries.
Q: How do I find reliable suppliers in China for lathe machining parts?
A: You can start by researching online directories, such as Alibaba and Global Sources, which list a wide range of suppliers. It’s advisable to carefully review their profiles, customer reviews, and ratings. Additionally, attending trade shows like the Canton Fair allows you to meet potential suppliers and assess their capabilities firsthand.
Q: What is the typical lead time for manufacturing lathe machining parts in China?
A: The lead time depends on various factors such as the complexity of the part, order quantity, and the supplier’s capacity. Generally, it ranges from a few weeks to a couple of months. Establishing clear communication and specifying your requirements upfront can help ensure timely delivery.
Q: Can I request customized lathe machining parts from suppliers in China?
A: Yes, most Chinese suppliers are willing to accommodate customization requests. It is essential to provide detailed technical drawings, specifications, and quality standards to ensure the desired outcome. Effective communication with your chosen supplier is key to achieving the desired customization.
Q: How can I ensure the quality of lathe machining parts from China?
A: Conducting thorough supplier screenings, including factory audits and verifying certifications, is crucial. Requesting product samples or prototypes, performing inspections during production, and implementing a robust quality control process are essential steps. Engaging a third-party inspection agency can further strengthen quality assurance.
Q: What are the payment terms usually offered by Chinese suppliers?
A: Common payment methods are telegraphic transfer (T/T) or letter of credit (L/C). Suppliers typically require a deposit (around 30%) upon order confirmation, with the remaining amount to be paid before shipment. Negotiating payment terms that align with your business needs is possible, but it is advisable to maintain a balance between trust and caution.
Q: How about intellectual property protection when manufacturing lathe machining parts in China?
A: Intellectual property protection in China has significantly improved in recent years; however, it is still advisable to take precautionary measures. Signing non-disclosure agreements (NDAs), registering trademarks or patents, and working with reputable suppliers with a history of respecting IP rights can help safeguard your intellectual property.
In conclusion, sourcing and manufacturing lathe machining parts in China provide cost-efficient solutions with a vast supplier base. By following due diligence, maintaining effective communication, and implementing quality control measures, businesses can successfully navigate the process and benefit from the advantages offered.
Why contact sourcifychina.com get free quota from reliable lathe machining parts suppliers?
SourcifyChina.com is a platform that provides sourcing and manufacturing services in China for businesses around the world. They offer a wide range of services to help businesses find reliable suppliers and manufacturers for their specific needs.
One of the services they offer is sourcing reliable lathe machining parts suppliers. Lathe machining is a crucial process in manufacturing, and finding reliable suppliers for these parts is essential for businesses requiring high-quality components.
To attract businesses in need of lathe machining parts, SourcifyChina.com offers a free quota for sourcing these suppliers. This allows businesses to submit their requirements and receive a quotation for their desired parts without any upfront fees.
The purpose of this free quota is to provide businesses with a no-risk opportunity to explore SourcifyChina.com’s services and find reliable suppliers for their lathe machining needs. It allows businesses to assess the competitiveness, quality, and pricing of the suppliers recommended by SourcifyChina.com.
By offering a free quota, SourcifyChina.com aims to demonstrate their dedication to customer satisfaction and build trust with potential clients. It also allows businesses to compare different suppliers and make informed decisions based on the quotations and information provided.
Overall, the free quota offered by SourcifyChina.com for sourcing reliable lathe machining parts suppliers is a strategic marketing approach to attract businesses, showcase their sourcing capabilities, and build long-term relationships with clients in need of such components.