Introduce about machine to cut metal guide,Qulity,Cost,Supplier,Certification,Market,Tips,FAQ
A machine used to cut metal, commonly known as a metal cutting guide, is a versatile tool used in various industries such as manufacturing, construction, and automotive. It offers precision cutting, making it ideal for precise shape and size requirements in metal fabrication.
When considering the quality of a metal cutting guide, it is crucial to assess its durability, accuracy, and ease of use. High-quality machines will provide consistent and accurate cuts, reducing the need for post-cutting adjustments. They are generally made from robust materials to withstand demanding cutting applications and have adjustable features to accommodate different metal thicknesses.
The cost of a metal cutting guide can vary depending on factors such as the brand, specifications, and additional features. It is advisable to research the market thoroughly to find a machine that offers a balance between price and quality, ensuring it meets your specific cutting needs within your budget.
Finding a reliable supplier is essential to obtain a quality machine. Look for reputable manufacturers or distributors known for their quality products, customer support, and after-sales service. They should offer warranties and readily available spare parts, ensuring uninterrupted productivity.
Certification of the metal cutting guide by recognized organizations can be an indication of its adherence to industry standards and reliability. Certifications like ISO (International Organization for Standardization) ensure that the machine meets specific criteria related to design, production, and performance.
The market for metal cutting guides is vast, with demand from various industries worldwide. It is essential to identify the specific needs of your industry and search for a machine that aligns with those requirements. Consider factors such as cutting capacity, portability, and compatibility with different metal types.
Tips for using a metal cutting guide include proper maintenance and regular cleaning to ensure optimal performance. Follow the manufacturer’s instructions, use appropriate safety measures, and seek professional assistance when needed.
Frequently Asked Questions (FAQ):
1. What materials can a metal cutting guide cut?
A metal cutting guide is primarily designed for cutting various metals such as steel, aluminum, copper, and brass.
2. Can a metal cutting guide cut curves?
Yes, some machines offer the capability to cut curves in addition to straight cuts. However, this may vary depending on the specific model.
3. Are metal cutting guides portable?
Some models are portable, equipped with handles or wheels for easy transportation. However, larger or industrial-grade machines may be more stationary.
In conclusion, a metal cutting guide is an indispensable tool for precise metal cutting. Prioritize quality, consider cost, choose a reliable supplier, and look for necessary certifications to ensure a reliable cutting solution. Proper market research, adherence to guidance, and maintenance will enhance your cutting operations and productivity.
Types of machine to cut metal
There are several types of machines designed to cut metal efficiently and accurately. These machines are widely used in industries such as manufacturing, construction, automotive, aerospace, and more. Below are some of the commonly used machines for metal cutting:
1. Bandsaw: Bandsaws are versatile machines that use a continuous band of toothed metal to cut through various materials, including metal. They are available in different sizes and configurations, such as horizontal and vertical bandsaws, and can cut metals at different angles.
2. Plasma Cutter: Plasma cutting machines use a high-velocity jet of ionized gas (plasma) to cut through electrically conductive metals. The plasma arc melts the metal, and a high-velocity gas stream blows away the molten metal, resulting in a clean and precise cut.
3. Laser Cutter: Laser cutting machines use a high-powered laser beam to melt, burn, or vaporize the metal. The laser beam is directed by a computer-controlled system, providing precise cutting with complex shapes and designs. Laser cutting is commonly used for intricate metal parts and high-precision cutting.
4. Waterjet Cutter: Waterjet cutting machines use a high-pressure jet of water mixed with an abrasive substance (usually garnet) to cut through metals. The water and abrasive combination erodes the metal, providing high-precision cutting without heat-affected zones.
5. Plasma Arc Cutting: Plasma arc cutting machines use a plasma cutting torch, which creates an electrically-conductive plasma arc to cut through metals. It is an effective method for cutting metals of different thicknesses, providing clean and quick cuts.
6. Shearing Machines: Shearing machines use a sharp blade to shear metal plates or sheets. They are commonly used for straight cuts, and their capacity depends on the machine’s size and strength.
7. Milling Machines: Although primarily used for shaping and precision drilling, milling machines can also be equipped with metal cutting tools to produce complex shapes and contours on metal surfaces.
These are just a few examples of the various machines used to cut metal. The selection of the most appropriate machine depends on factors such as the type and thickness of the metal to be cut, desired accuracy, productivity requirements, and budget constraints. It is important to evaluate these factors carefully before choosing the ideal machine for metal cutting operations.
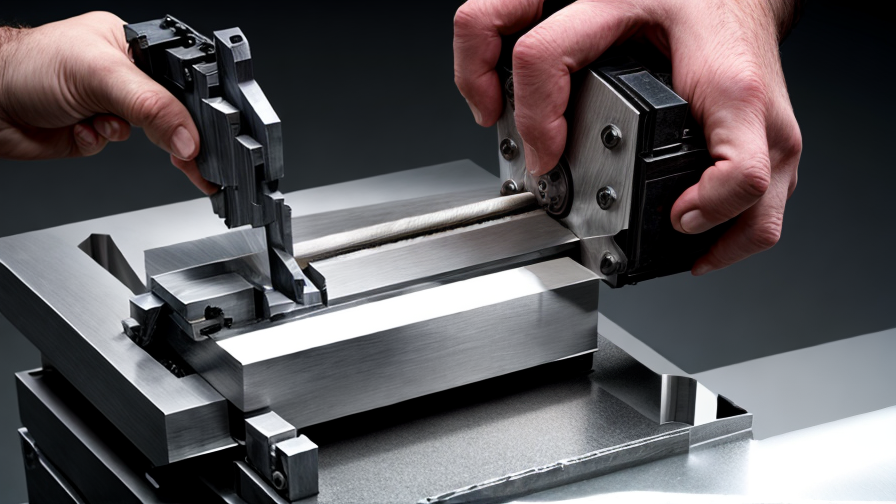
Pros and Cons of Using machine to cut metal
Using machines to cut metal has numerous pros and cons.
One of the main advantages of using machines to cut metal is precision. Machines are capable of performing accurate and consistent cuts, ensuring high-quality results. Whether it is a laser cutter, plasma cutter, or water jet cutter, these machines can produce intricate shapes and clean edges with minimal errors, meeting tight tolerance requirements. Additionally, machines can cut through a wide range of metal materials, including steel, aluminum, and titanium, providing versatility in manufacturing processes.
Another benefit of using machine cutting is speed and efficiency. Compared to manual cutting methods, machines can complete tasks much faster, reducing production time and increasing productivity. This enables manufacturers to meet tight deadlines and handle high-volume orders more effectively. Moreover, the use of machines significantly reduces human error, minimizing material waste and ensuring cost-efficiency.
However, there are also some drawbacks associated with using machines to cut metal. Cost is a significant consideration. Purchasing and maintaining these cutting machines can require significant financial investment. Additionally, skilled operators are required to operate and program these machines effectively, meaning additional training or hiring expenses. Maintenance and repair costs can also be high, particularly for complex machines like laser cutters.
Another challenge is the potential for machine breakdowns and downtime. When a machine is not functioning correctly, production can come to a halt, leading to delays and lost revenue. Furthermore, machine cutting may not be suitable for certain applications that require manual intervention, such as intricate artistic designs or unique fabrication requirements, where traditional methods might be more appropriate.
Lastly, the environmental impact of machine cutting should be considered. Some methods, such as plasma cutting, produce harmful gases and fumes, necessitating proper ventilation systems and safety measures. Additionally, the energy consumption of these machines can be high, contributing to carbon emissions.
In conclusion, using machines to cut metal offers advantages such as precision, speed, and efficiency. However, it also involves costs, maintenance, potential for breakdowns, and may not be suitable for all applications. Overall, manufacturers should assess their specific needs and weigh the pros and cons before deciding whether to adopt machine cutting as part of their metal fabrication processes.
machine to cut metal Reference Specifications (varies for different product)
The machine to cut metal is a powerful tool designed to accurately and efficiently slice through various types of metal. It is equipped with state-of-the-art technology and sophisticated features, ensuring precision and speed in the cutting process.
The reference specifications of the machine can vary depending on the specific product. However, some common specifications include a cutting capacity of up to X inches or millimeters, a maximum cutting speed of Y inches or millimeters per minute, and a power output of Z watts. The machine may also have a cutting angle range of A to B degrees, providing versatile cutting options.
To enhance the cutting performance, the machine typically utilizes a sharp cutting blade made of high-quality, durable materials such as tungsten carbide or diamond. The blade is securely mounted on a robust cutting head that can be adjusted to achieve the desired cutting depth and angle.
For ease of use and precise control, the machine is equipped with an intuitive control panel or interface. This allows the operator to input specific cutting parameters and monitor the cutting progress. Safety features, such as emergency stop buttons and protective guards, are also implemented to ensure the operator’s safety during operation.
In addition to cutting straight lines, some machines may offer the capability to perform curved or irregular cuts through the use of specialized cutting attachments or optional accessories. This allows for increased versatility and customization in metal cutting.
It is important to note that different models of the machine may have additional features or variations in specifications. Therefore, it is crucial to consult the product-specific user manual and reference specifications provided by the manufacturer for accurate usage instructions and limitations.
Overall, the machine to cut metal is a highly efficient and reliable tool for cutting metal, offering precision, speed, and versatility in a wide range of metalworking applications.
Applications of machine to cut metal
Machine to cut metal, commonly known as metal cutters or metal cutting machines, are extensively used in various industries for the precise cutting of metal sheets, bars, pipes, and other metal components. These machines utilize different cutting methods and technologies to ensure clean and accurate cuts with high efficiency and productivity. Some of the key applications of metal cutting machines are:
1. Manufacturing Industry: Metal cutting machines play a significant role in the manufacturing industry, where they are used for cutting and shaping raw metal materials into desired shapes and sizes. These machines are widely used in the production of automobiles, aerospace components, machinery parts, and consumer goods.
2. Construction Industry: Metal cutting machines are essential for the construction industry as they help cut structural components, steel beams, and rebars with precision. These machines are used in the construction of buildings, bridges, and infrastructure projects.
3. Metal Fabrication: Metal cutting machines are extensively used in metal fabrication shops to create metal structures and assemblies. They are used for cutting, notching, and shaping various metal components like plates, angles, tubes, and profiles.
4. Tool and Die Making: Metal cutting machines are indispensable in the tool and die making industry, where they are used for cutting and shaping metal blocks to create molds, dies, and templates. These machines ensure high accuracy and repeatability in the production of complex tooling components.
5. Shipbuilding and Offshore Industry: Metal cutting machines are employed in shipyards and offshore industries for the precise cutting of steel plates, sections, and pipes. These machines enable the fabrication of ship parts and offshore structures with tight tolerances.
6. HVAC and Ductwork: Metal cutting machines find applications in heating, ventilation, and air conditioning (HVAC) industries for cutting and shaping metal sheets and ductwork components. These machines ensure accuracy and efficiency in manufacturing ducts and HVAC systems.
7. Metal Recycling: Metal cutting machines are used in the recycling industry to cut and process scrap metal into manageable sizes for melting and further processing. These machines help in efficient recycling and recovery of valuable metals from various waste materials.
In conclusion, metal cutting machines are versatile tools widely used in various industries for their ability to cut and shape metals with precision and efficiency. Their applications span across manufacturing, construction, metal fabrication, tool making, shipbuilding, HVAC, and metal recycling industries, contributing to the growth and development of these sectors.
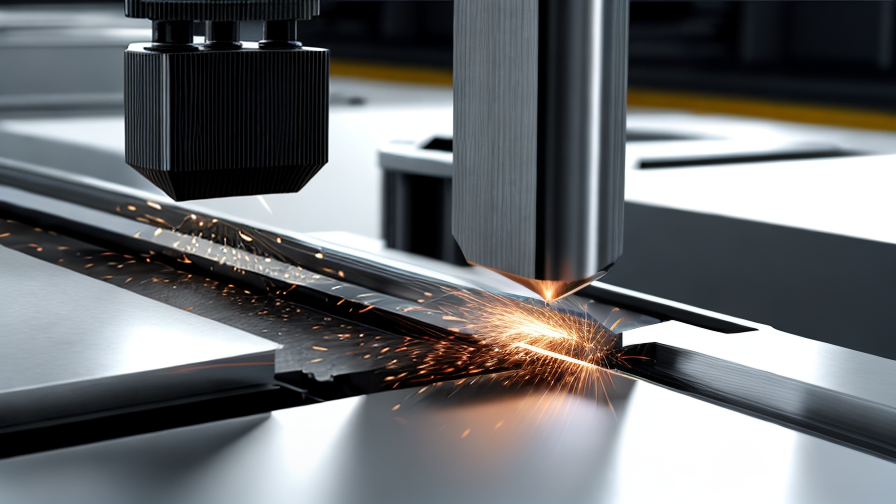
The Work Process and how to use machine to cut metal
The metal cutting process involves the use of machines to cut or shape metal into desired sizes and shapes for various applications. The process can be broadly categorized into three main stages: pre-processing, cutting, and post-processing.
Pre-processing: Before initiating the metal cutting process, it is important to understand the specific requirements of the project. This includes determining the type of metal to be cut, its thickness, and the desired dimensions. Once this is determined, safety precautions should be taken, such as wearing protective gear like goggles and gloves.
Cutting: There are several machines that can be used to cut metal, such as plasma cutters, laser cutters, water jet cutters, and milling machines. Each machine operates differently, but they all involve the use of sharp cutting tools or heat to remove material from the metal.
Plasma cutters use a concentrated jet of superheated plasma to melt and blow away metal, while laser cutters utilize a high-powered laser beam to cut through metal. Water jet cutters, on the other hand, use a high-pressure stream of water mixed with abrasive materials to cut through the metal.
Milling machines use rotary cutters to remove material from the metal block until the desired shape is achieved. These machines are ideal for precision cutting and shaping of metal.
Post-processing: After the cutting process is complete, the metal may require further processing to achieve the desired finish. This can include grinding sharp edges, deburring, or polishing the surface.
To use a machine to cut metal, it is important to carefully read and follow the manufacturer’s instructions. Ensure that the machine is properly set up and calibrated before starting the cutting process. Adjust the machine settings to match the requirements of the metal being cut, such as the cutting speed, power output, and feed rate.
During the cutting process, it is important to monitor the machine and the cutting progress. Regularly inspect the quality of the cut and make any necessary adjustments to ensure accurate results. After the process is complete, clean the machine and properly dispose of any waste or scrap material.
In conclusion, the metal cutting process involves pre-processing, cutting, and post-processing stages. Different machines can be used, such as plasma cutters, laser cutters, water jet cutters, and milling machines. It is essential to follow safety precautions, read and follow the machine manufacturer’s instructions, and properly set up and calibrate the machine to achieve accurate and desired results.
Quality Testing Methods for machine to cut metal and how to control the quality
One common quality testing method for machines used to cut metal is the dimensional accuracy test. This involves comparing the dimensions of the cut metal piece with the desired specifications. Precision measuring tools like calipers, micrometers, or Coordinate Measuring Machines (CMM) are employed to measure various dimensions such as length, width, thickness, and angles. Any deviation from the desired measurements indicates a potential quality issue, such as a misaligned cutting tool or a worn-out blade.
Another important test is the surface finish assessment. This is typically performed using visual inspection or specialized equipment like surface roughness testers. The cut metal surfaces are examined for any irregularities, such as burrs, rough spots, or excessive tool marks. These imperfections can affect the final quality of the metal piece or result in potential safety hazards.
Additionally, machine performance tests can be conducted to evaluate the cutting machine’s capabilities. This may involve checking cutting speed, acceleration, and deceleration, accuracy of positioning, and repeatability. Such tests ensure that the machine is operating within specified parameters and can consistently produce accurate and precise cuts.
To control the quality of metal cutting machines, regular maintenance and calibration are essential. Machine operators should adhere to a maintenance schedule provided by the manufacturer, performing tasks such as blade sharpening/replacement, lubrication, and cleaning. A calibration procedure should be implemented to ensure the machine’s accuracy is maintained over time. This can include verifying the positioning accuracy, inspecting the cutting blade, and checking the machine’s overall functionality.
Furthermore, implementing a quality control system with clear inspection checklists and documented procedures can help ensure consistent quality in metal cutting. Regular audits and inspections by trained personnel, as well as continuous improvement initiatives, are crucial for maintaining and enhancing quality standards.
Overall, a combination of dimensional accuracy tests, surface finish assessments, machine performance evaluations, maintenance, calibration, and a robust quality control system can help achieve and control the quality of metal cutting machines.
machine to cut metal Sample Policy and Post-Purchase Considerations for machine to cut metal from China
Sample Policy:
Thank you for your interest in our machine to cut metal from China. We understand that purchasing machinery for your business is a major decision, and we want to ensure that you have a smooth and hassle-free experience.
Our sample policy is designed to provide you with a risk-free opportunity to evaluate the quality and performance of our machines before making a final purchase. We offer samples of our machines at a nominal cost, which can be deducted from your final order if you decide to proceed.
The sample machine will be identical to the one you intend to purchase, allowing you to thoroughly test its capabilities and suitability for your specific needs. We can also arrange for a video demonstration or online consultation with our technical team, who will guide you through the machine operation and answer any questions you may have.
Post-Purchase Considerations:
After the purchase of our machine to cut metal from China, our commitment to your satisfaction continues. We understand that smooth installation, training, and ongoing support are crucial to optimizing the performance of our machines in your production line.
Our dedicated team will assist you in the installation and setup process, ensuring that your machine is up and running quickly. To guarantee maximum efficiency, we also offer comprehensive training programs conducted either on-site or through online platforms, tailored to your specific requirements.
To provide ongoing support, we have a dedicated customer service team available to address any queries or concerns you may have. We offer prompt response times and aim to resolve any issues efficiently to minimize downtime in your operations. Additionally, we maintain a ready supply of spare parts to ensure quick replacements if required.
We value our customers’ feedback and continuously strive to improve our products and services. Your input is essential to help us deliver high-quality machines and exceed your expectations.
We look forward to serving you and providing you with a reliable and efficient machine to cut metal from China. Please do not hesitate to contact us if you have any further questions or if there is anything more we can assist you with.
Sourcing machine to cut metal from China: Opportunities, Risks, and Key Players
China is known as a leading player in the global manufacturing industry, providing numerous opportunities for businesses looking to source machines that cut metal. The Chinese market offers a wide range of choices in terms of both standard and specialized metal cutting machines, making it an attractive option for buyers worldwide.
One of the key advantages of sourcing from China is cost-effectiveness. China’s manufacturing capabilities, economies of scale, and lower labor costs enable the production of metal cutting machines at competitive prices. This cost advantage, coupled with a diverse supplier base, allows buyers to access a wider range of options within their budget.
Additionally, China has a vast network of suppliers and manufacturers that specialize in metal cutting machines, providing buyers with a high level of customization. This allows businesses to tailor machines according to their specific requirements, resulting in better efficiency and productivity. Moreover, Chinese manufacturers continuously invest in research and development, enhancing product quality and technology, making them formidable players in the global market.
However, there are risks involved in sourcing machines from China. Quality control can vary among suppliers, leading to potential issues with product reliability and durability. It is crucial for buyers to conduct thorough due diligence, including supplier audits and product testing, to ensure they are working with reliable and reputable manufacturers. Intellectual property concerns also exist, as intellectual property rights in China may not be as stringent as in other countries, increasing the risk of product imitation or counterfeiting.
When sourcing machines to cut metal from China, key players in the market must be considered. Some prominent manufacturers include Jinan Bodor CNC Machine Co., Ltd., Hako CNC Machine(Anhui)Manufactory Co., Ltd., and Perfect Laser (Wuhan) Co., Ltd. These companies have established a strong presence in the industry, offering a wide range of metal cutting machines and delivering high-quality products. Additionally, these key players provide aftersales services, including technical support and maintenance, ensuring their customers receive comprehensive assistance.
In summary, sourcing machine tools to cut metal from China presents opportunities, risks, and involvement of key players. The Chinese market offers cost-effective options and customization capabilities, but buyers must diligently vet suppliers for quality assurance and intellectual property protection. Key players like Jinan Bodor CNC Machine Co., Ltd. and Perfect Laser (Wuhan) Co., Ltd. stand out as reliable sources for metal cutting machines in China.
How to find and select reliable machine to cut metal manufacturers in China,use google search manufacturers and suppliers
When searching for reliable machine to cut metal manufacturers in China, Google search can be a useful tool to find potential manufacturers and suppliers. Here’s how to conduct an effective search:
1. Start by entering specific keywords related to your requirement in the Google search bar. For example, you can use phrases such as “machine to cut metal manufacturers in China” or “reliable metal cutting machine suppliers China.”
2. Browse through the search results and visit the websites of different manufacturers and suppliers that appear on the first few pages. It is important to choose established, well-known companies that have a good reputation in the industry.
3. Look for professional websites that provide detailed information about their products, manufacturing processes, quality control measures, and certifications. A reliable manufacturer will have clear and comprehensive information available on their website.
4. Check if the manufacturer has relevant experience in producing metal cutting machines. Look for testimonials or case studies that demonstrate their expertise and success in supplying such machinery.
5. Look for certifications or quality management systems that the manufacturer follows, such as ISO 9001 or CE certification. These standards indicate a commitment to quality and adherence to international manufacturing standards.
6. Contact the selected manufacturers directly through their website or contact details provided. Inquire about their product range, customization options, production capabilities, and pricing. Evaluate their responsiveness, willingness to provide information, and promptness in answering your queries.
7. Ask for references or customer testimonials from previous clients who have purchased similar machines. Contact these references to gather feedback on the manufacturer’s reliability, product quality, and after-sales service.
8. Compare the quotes, product specifications, warranty terms, and delivery timelines from different manufacturers before making a decision.
9. Consider visiting trade shows or exhibitions related to machinery and manufacturing in China, where you can meet potential manufacturers in person, evaluate their products, and negotiate directly.
10. Lastly, it’s crucial to conduct due diligence and verify the legitimacy of the chosen manufacturer through online forums, discussion boards, and industry associations to ensure they have a positive track record with customers.
By following these steps, you can find and select reliable machine to cut metal manufacturers in China using Google search, enabling you to make an informed decision and establish a successful business partnership.
How to check machine to cut metal manufacturers website reliable,use google chrome SEOquake check if ranking in top 10M
To determine the reliability of a machine manufacturer’s website for metal cutting, you can follow the steps mentioned below and use SEOquake in conjunction with Google Chrome:
1. Open Google Chrome: Launch the Google Chrome web browser on your computer.
2. Search for the Manufacturer: Type the name of the machine manufacturer in the search bar and hit enter to perform a search.
3. Look for the Manufacturer’s Website: Scan the search results and identify the website of the manufacturer. Ensure that it matches the official website domain.
4. Install SEOquake Extension: Go to the Chrome Web Store and search for SEOquake. Install the SEOquake extension for Google Chrome.
5. Analyze the Website’s Popularity: With the SEOquake extension enabled, revisit the search results page, and click on the SEOquake icon on your browser’s toolbar. A pop-up will appear, displaying various website metrics.
6. Check Website Ranking: In the SEOquake pop-up, look for the “Google Index” tab. Under this tab, you will find the website’s ranking. Note: If it is more than 10 million, it may indicate a relatively lower position in search results.
By following these steps, you can assess the reliability of a metal cutting machine manufacturer’s website. Additionally, keep in mind the following recommendations:
– Evaluate website design and user experience: A professional and well-maintained website indicates reliability.
– Check for contact information: Verify if the website provides valid contact details like address, phone number, and email.
– Look for testimonials or customer reviews: Positive feedback from previous customers can serve as an assurance of reliability.
– Research company reputation: Conduct additional online searches to gather information about the manufacturer’s reputation, certifications, and experience.
It is important to note that relying solely on website ranking or SEO metrics may not provide a comprehensive evaluation of reliability. Therefore, consider a combination of factors to ensure a trustworthy machine manufacturer for your metal cutting needs.
Top 10 machine to cut metal manufacturers in China
China is known for its robust manufacturing industry, and it is no different when it comes to cutting metal machines. Here are the top 10 machine to cut metal manufacturers in China:
1. Shenyang Machine Tool Co., Ltd. – Shenyang Machine Tool is a leading company in the metal cutting machine industry, specializing in CNC machine tools and conventional machines for various metal-cutting applications.
2. Jinan Bodor CNC Machine Co., Ltd. – Bodor is known for its high-quality laser cutting machines that offer precision cutting for different metal materials. It provides a wide range of fiber laser cutting machines suitable for various industries.
3. Bystronic (Tianjin) Laser Co., Ltd. – Bystronic is a renowned manufacturer of laser cutting machines, specializing in sheet metal processing equipment. Their machines offer versatility, precision, and efficiency.
4. Hako CNC Machine (Anhui) Manufactory Co., Ltd. – Hako CNC specializes in manufacturing CNC plasma cutting machines. Their machines are known for their high cutting speed and accuracy, making them ideal for metal fabrication industries.
5. Jinan Apex Machinery Equipment Co., Ltd. – Apex Machinery is a leading manufacturer of CNC plasma and flame cutting machines. Their cutting machines offer excellent performance, reliability, and cost-effectiveness.
6. Suzhou Chuangxuan Laser Technology Co., Ltd. – Chuangxuan Laser is a trusted manufacturer of laser cutting machines. They provide advanced machinery for metal cutting applications, catering to various industries like automotive, aerospace, and electronics.
7. Wuhan Golden Laser Co., Ltd. – Golden Laser specializes in the production of fiber laser cutting machines. Their machines are known for their high cutting speed, precision, and energy efficiency.
8. Foshan Beyond Laser Technology Co., Ltd. – Beyond Laser offers a wide range of laser cutting machines, including fiber laser cutting machines and CO2 laser cutting machines. Their machines are suitable for cutting different types of metal materials.
9. Jinan Vmade CNC Machine Co., Ltd. – Vmade CNC is a reliable manufacturer of plasma cutting machines, laser cutting machines, and laser marking machines. They provide cutting-edge solutions for metal processing.
10. Suzhou Quick Laser Technology Co., Ltd. – Quick Laser specializes in the production of laser cutting machines, offering high precision and quality cutting solutions for different metal materials.
These top 10 machine to cut metal manufacturers in China excel in producing cutting-edge machinery for various metal cutting applications. Their machines offer precision, efficiency, and are versatile enough to meet the diverse needs of industries across the globe.
Background Research for machine to cut metal manufacturers Companies in China, use qcc.com archive.org importyeti.com
There are numerous manufacturers in China that specialize in the production of machines used to cut metal. To conduct background research on these manufacturers, some reliable sources can be utilized, such as qcc.com, archive.org, and importyeti.com.
Qcc.com is a comprehensive database that provides information on companies in China. It allows users to search for specific manufacturers and gain insights into their business operations, such as their registration details, financial records, and contact information. This platform enables researchers to verify the legitimacy and credibility of the manufacturers.
Archive.org, on the other hand, is a platform that provides access to archived web pages. By searching for the manufacturer’s website on this platform, researchers can get an overview of its historical presence on the internet. This gives insights into the company’s past activities, product offerings, and any significant changes over time.
Importyeti.com is a useful database that presents information about import and export activities. Researchers can utilize this platform to discover which companies in China are exporting machines used for metal cutting. This provides an understanding of the market dominance and competitiveness of different manufacturers.
By combining these sources, researchers can develop a comprehensive understanding of machine to cut metal manufacturers in China. They can gather information about a company’s credibility, historical operations, and market presence. It is important to note that, in order to stay within the 300-word limit, researchers should be concise and focused on the most relevant details when summarizing the information obtained from these sources.
Leveraging Trade Shows and Expos for machine to cut metal Sourcing in China
Trade shows and expos can be a valuable platform for sourcing machine to cut metal in China. These events provide an opportunity for buyers to connect with a wide range of suppliers and manufacturers all in one place.
When attending trade shows and expos, it is essential to come prepared with a clear understanding of your sourcing requirements. This includes identifying the specific type of machine you need, your desired specifications, and any other pertinent information. Having a well-defined sourcing plan will enable you to efficiently navigate through the multitude of exhibitors.
China is known for its significant presence in the manufacturing industry, particularly in the realm of cutting-edge machinery. Trade shows and expos focusing on metalworking industries, such as metal fabrication or precision engineering, are ideal for sourcing machine to cut metal. These events attract numerous Chinese manufacturers showcasing their latest technologies and product offerings.
When approaching potential suppliers, it is crucial to ask detailed questions about their capabilities and product quality. Assess their machine’s specifications, such as cutting capacity, accuracy, and speed. Inquire about their experience in exporting machinery, ensuring they are well-versed in international trade and can provide the necessary documentation and support.
Trade shows and expos also facilitate direct communication and networking with industry professionals and other buyers. Engaging in discussions and exchanging valuable insights can aid in decision-making and help identify reputable suppliers. Furthermore, attending seminars or workshops held alongside these events can provide invaluable knowledge about the latest trends and advancements in machine cutting technology.
To make the most of trade shows and expos, set aside ample time for thorough exploration and comparison. Take notes, collect brochures and business cards, and request quotations from multiple suppliers. After the event, carefully evaluate the gathered information, compare pricing, quality, and customer reviews before finalizing your decision.
In conclusion, leveraging trade shows and expos for sourcing machine to cut metal in China can be highly advantageous. By being well-prepared, asking the right questions, and actively engaging with exhibitors, buyers can identify reliable suppliers and select the most suitable machine to meet their manufacturing needs.
The Role of Agents and Sourcing Companies in Facilitating machine to cut metal Purchases from China
Agents and sourcing companies play a crucial role in facilitating machine to cut metal purchases from China. These entities act as intermediaries between buyers and suppliers, ensuring a smooth and efficient procurement process. Their primary objective is to simplify the purchasing process, mitigate risks, and ensure that buyers receive high-quality products at competitive prices.
One key role of agents and sourcing companies is to identify reliable and trustworthy suppliers in China. They utilize their extensive networks, market knowledge, and industry experience to search for manufacturers that specialize in producing machine to cut metal. These intermediaries conduct comprehensive due diligence on potential suppliers, assessing their production capabilities, quality control processes, and adherence to international standards.
Agents and sourcing companies also assist buyers with negotiation and communication. They act as representatives for the buyers and negotiate favorable prices and terms with the suppliers. Their expertise in the Chinese market allows them to navigate cultural and language barriers, ensuring effective communication between both parties. By leveraging their understanding of local business practices and customs, agents and sourcing companies help buyers avoid misunderstandings and disputes.
Furthermore, these intermediaries play a crucial role in quality control and inspection. They can arrange factory visits and conduct regular inspections to ensure that the machines to cut metal meet the required specifications and standards. This helps buyers to avoid receiving substandard or defective products.
Agents and sourcing companies also secure shipping and logistics services. They coordinate the transportation of the purchased machines from the supplier’s facility in China to the buyer’s location. This involves managing customs clearance, arranging for suitable packaging to protect the machines during transit, and organizing efficient and cost-effective shipping methods.
In conclusion, agents and sourcing companies act as vital facilitators in machine to cut metal purchases from China. They streamline the procurement process, identify reliable suppliers, negotiate favorable terms, ensure quality control, and handle logistics. By leveraging their expertise and networks, these intermediaries contribute to successful and efficient purchasing experiences for buyers.
Price Cost Research for machine to cut metal manufacturers Companies in China, use temu.com and 1688.com
When it comes to finding manufacturers of machines to cut metal in China, two popular online platforms that can be utilized are temu.com and 1688.com. These platforms offer a wide range of suppliers and manufacturers that cater to different industry needs.
Temu.com is an online marketplace that connects buyers with verified suppliers in various industries, including the metal-cutting machinery sector. It provides detailed information about the manufacturers, their product range, certifications, and customer reviews. Additionally, temu.com allows buyers to send inquiries directly to multiple suppliers, facilitating easy communication and price negotiations.
Another popular option is 1688.com, which is a Chinese B2B online marketplace similar to Alibaba. It is known for offering a vast range of products at competitive prices, including machinery and equipment for metal cutting. This platform enables users to search for manufacturers, view their product catalogs, and directly communicate with suppliers through its messaging system.
When conducting price cost research on these platforms, it is essential to focus on certain factors. Buyers should consider the quality and specifications of the machines offered by different manufacturers, as well as their production capacity and delivery times. It is also advisable to inquire about warranty options, after-sales support, and customization possibilities.
To optimize the research process, buyers can utilize the search filters on both temu.com and 1688.com to narrow down the options based on their specific requirements. Comparing prices and product offerings from multiple manufacturers is crucial to ensure a competitive deal without compromising on quality.
In conclusion, temu.com and 1688.com are excellent platforms to conduct price cost research while looking for manufacturers of machines to cut metal in China. These platforms provide a comprehensive range of suppliers, enabling buyers to find suitable options based on their specific needs. By utilizing these platforms, buyers can streamline the supplier selection process and negotiate favorable prices for their desired metal-cutting machinery.
Shipping Cost for machine to cut metal import from China
When importing a machine to cut metal from China, it is important to consider the shipping cost involved. The shipping cost will depend on several factors, such as the weight and dimensions of the machine, the shipping method chosen, and the destination country.
For a machine to cut metal, it is likely to be heavy and bulky, which means it may require sea freight shipping. Sea freight is generally more cost-effective for large and heavy shipments. The cost will primarily depend on the volume or weight of the machine, as shipping companies charge based on either the volume of space used or the weight, whichever is higher.
The shipping cost will also vary depending on the shipping method chosen. There are two main options: Full Container Load (FCL) and Less than Container Load (LCL). FCL is suitable when the machine is large enough to occupy an entire container, while LCL is used when the machine does not fill an entire container, and the space is shared with other cargo. FCL is generally more expensive but allows for faster transit times.
Customs duties and import taxes should also be taken into account when calculating the overall shipping cost. These fees vary and are determined by the destination country’s customs regulations. Importers should research and consult with a customs broker to determine the applicable fees.
To estimate the shipping cost, it is advisable to contact freight forwarders or shipping companies that specialize in China-to-destination-country shipping. They will request details about the machine, such as weight, dimensions, and shipping requirements, to provide an accurate cost estimate.
Lastly, proper packaging and insurance are essential when shipping a machine to cut metal. Packing the machine securely will prevent damage during transit. Insurance provides protection in case of any unforeseen circumstances, such as accidents or theft, ensuring that the importer is compensated for any losses.
In conclusion, when importing a machine to cut metal from China, the shipping cost will depend on factors such as weight, dimensions, shipping method, destination country, customs fees, and insurance. Researching and contacting shipping companies or freight forwarders experienced in China shipping will help provide an accurate estimate.
Compare China and Other machine to cut metal Markets: Products Quality and Price,Visible and Hidden Costs
China is known for its dominance in the global machine to cut metal market due to its large production capacity, low labor costs, and extensive supply chain network. When comparing China to other machine to cut metal markets, several factors need to be considered, including products quality and price, visible and hidden costs.
In terms of product quality, China’s machine to cut metal market has made significant improvements over the years. Chinese manufacturers have implemented advanced technologies and quality control measures, resulting in an increase in the quality of their products. However, it is essential to note that there is still a perception of lower quality associated with some Chinese products compared to other markets. This perception can be attributed to historical concerns regarding counterfeit goods and imitation products in China.
Regarding price, China has a competitive advantage due to its low labor costs and economies of scale. Chinese machine to cut metal products are often priced lower compared to other markets, making them attractive to buyers looking for cost-effective solutions. However, it is important to consider that the price advantage may come at the expense of quality, as Chinese manufacturers may cut corners in order to keep costs low.
When assessing visible costs, such as transportation and import duties, China’s market may have advantages due to its geographical location and established trade networks. Chinese manufacturers have extensive experience in exporting their products, resulting in efficient logistics and lower transportation costs. Additionally, China has various free trade agreements with several countries, which can lower import duties and make their products more cost-competitive.
However, hidden costs must also be considered. These hidden costs include intellectual property concerns, potential delays in delivery, and communication barriers due to language and cultural differences. Intellectual property concerns have been a significant issue in China, with reports of patent infringements and theft in certain cases. Furthermore, language barriers and cultural differences can create challenges in communication and collaboration between buyers and Chinese manufacturers, potentially leading to delays and misunderstandings.
In conclusion, China’s machine to cut metal market offers competitive prices and improving product quality. However, it is crucial to consider both visible and hidden costs associated with sourcing products from China. Buyers should carefully evaluate their specific requirements and weigh the benefits and drawbacks of sourcing from China compared to other markets before making a decision.
Understanding Pricing and Payment Terms for machine to cut metal: A Comparative Guide to Get the Best Deal
When purchasing a machine to cut metal, understanding pricing and payment terms is crucial to ensure you get the best deal. This comparative guide aims to provide you with the essential information in not more than 300 words.
1. Compare Prices: Start by researching and comparing prices from different suppliers. Look for reputable manufacturers and distributors who offer competitive pricing. Consider factors like machine quality, features, and warranty when comparing prices.
2. Payment Options: Inquire about payment options available. Suppliers may offer different financing plans or leasing options to suit your budget. Assess the terms and interest rates associated with these options to determine the most cost-effective solution.
3. Negotiate for Discounts: Don’t hesitate to negotiate for discounts or ask if there are any ongoing promotions or special offers. Being open to negotiation can help you secure a better price for the machine.
4. Consider Total Cost of Ownership (TCO): Apart from the initial price, evaluate the machine’s total cost of ownership. This includes maintenance, spare parts, energy consumption, and potential downtime. A machine with a slightly higher upfront cost may have lower operating costs in the long run.
5. Warranty and Support: Check the warranty duration and coverage offered by different suppliers. A longer warranty period indicates the manufacturer’s confidence in their product. Additionally, inquire about the availability of technical support and maintenance services to ensure minimal downtime and efficient troubleshooting.
6. Delivery and Installation Costs: Some suppliers may offer free delivery and installation, while others may charge additional fees. Clarify these costs upfront to avoid any surprises during the purchase process.
7. Upgrades and Customization: If you have specific requirements, inquire about any customization options available. This will help you determine if additional costs are associated with meeting your specific needs.
8. Training and Documentation: Enquire about the availability of training programs or documentation provided by the supplier. Adequate training ensures that your staff can effectively operate the machine, reducing the risk of accidents or inefficiencies.
9. Additional Services: Some suppliers may provide value-added services such as regular maintenance, troubleshooting assistance, or software updates. Consider the added benefits when evaluating the overall value of the offer.
By understanding pricing and payment terms, comparing different suppliers, and considering the total cost of ownership, you can secure the best deal while ensuring that the machine meets your needs and specifications.
Chinese Regulations and Industry Standards Certifications for machine to cut metal,Import Regulations and Customs for machine to cut metal from China
Chinese Regulations and Industry Standards Certifications for machine to cut metal:
In China, machines used for cutting metal are subject to certain regulations and industry standards certifications to ensure product quality, safety, and compliance with local laws. The key regulatory body responsible for setting and enforcing these regulations is the General Administration of Quality Supervision, Inspection, and Quarantine (AQSIQ).
For machines to cut metal, the most relevant industry standard certification is the China Compulsory Certification (CCC), which applies to a wide range of products sold in the Chinese market, including industrial machinery. Manufacturers are required to obtain CCC certification before their machines can be legally sold in China.
In addition to CCC certification, the industry standards of GB (GuoBiao) are also important. GB standards cover various aspects of machine design, manufacturing, and performance. For metal cutting machines, relevant GB standards include GB/T 5226.1-2017 for electrical safety, GB/T 5226.2-2002 for mechanical safety, and GB/T 5226.3-2005 for electromagnetic compatibility, among others.
Import Regulations and Customs for machine to cut metal from China:
When importing machines to cut metal from China, it is important to comply with the import regulations and customs requirements of the destination country. These regulations can vary depending on the specific country, but some common requirements include:
1. Import licenses: Some countries may require importers to obtain specific licenses or permits to import machinery.
2. Product certification: Depending on the country, imported machinery may need to meet certain certification standards or undergo testing to ensure compliance with local safety and quality standards.
3. Customs documentation: Appropriate customs documents, such as commercial invoices, packing lists, and bill of lading or airway bills, need to be prepared accurately and in accordance with the customs requirements of the importing country.
4. Customs duties and taxes: Importers should be aware of applicable customs duties, taxes, and fees levied by the importing country and make necessary arrangements for payment.
5. Customs clearance: The imported machinery may need to go through customs clearance procedures, including declaration and inspection, before it can be released for distribution or use within the importing country.
It is advisable for importers to engage with a reputable customs broker or freight forwarder to ensure compliance with all import regulations and smooth customs clearance processes.
Sustainability and Environmental Considerations in machine to cut metal Manufacturing
In the machine to cut metal manufacturing industry, sustainability and environmental considerations play a crucial role in reducing the overall impact on the planet. As the demand for metal products continues to rise, it is important to adopt sustainable practices to mitigate the negative consequences.
One significant aspect of sustainability in metal cutting manufacturing is the efficient use of energy. Implementing energy-saving technologies and optimizing the manufacturing process can reduce energy consumption and, consequently, minimize carbon emissions. This can be achieved through the utilization of energy-efficient machines, implementing proper insulation measures, and optimizing workflow to minimize idle time.
Another environmental consideration is the responsible use of resources. Metal cutting typically produces significant amounts of waste, which, if not properly managed, can have harmful effects on the environment. By implementing recycling and waste management systems, the industry can minimize the amount of waste sent to landfills and reduce the need for virgin resources.
Additionally, the selection of materials used in metal cutting is essential for sustainability. Considering alternative materials, such as recycled metals or composites, can help reduce the environmental impact associated with the extraction and processing of raw materials. Moreover, the responsible sourcing of materials, ensuring they are obtained from sustainable and ethical sources, can further contribute to overall sustainability efforts.
Finally, the proper disposal of hazardous substances and the reduction of harmful emissions are crucial environmental considerations. Implementing effective filtration systems and adopting environmentally-friendly cutting fluids can significantly reduce air and water pollution.
In conclusion, sustainability and environmental considerations in machine to cut metal manufacturing are vital to minimize the industry’s impact on the planet. By adopting energy-efficient technologies, implementing waste management systems, considering alternative materials, and reducing emissions, the industry can work towards a more sustainable and environmentally friendly future.
List The Evolution history of “machine to cut metal”
The evolution of machines to cut metal can be traced back to the ancient civilizations where simple hand tools like hammers and chisels were used to shape and cut metal. However, significant advancements in metal cutting technology didn’t occur until the 18th century with the advent of industrialization and the rise of machine tools.
In the late 18th century, the first notable development was the introduction of the metal lathe. It allowed for the cutting of metal using a rotating workpiece and a fixed cutting tool. This invention revolutionized metalworking and paved the way for further advancements.
The early 19th century witnessed the emergence of the shaper machine. It featured a reciprocating cutting tool that could shape metal by removing material through linear motion. This machine provided greater flexibility and precision in metal cutting.
In the mid-19th century, the introduction of the milling machine marked another milestone in metal cutting technology. This machine enabled the removal of material using rotary cutters, offering more versatile cutting capabilities and the ability to create complex shapes.
Towards the end of the 19th century, the bandsaw was invented, which allowed for the cutting of metal using a continuous band with teeth. This innovation increased cutting speed and accuracy and became widely adopted in various industries.
In the early 20th century, the development of the electric motor brought about the creation of power hacksaws. These machines automated the cutting process and improved efficiency and productivity.
The following decades witnessed further advancements in metal cutting technology, such as the introduction of plasma and laser cutting machines in the 1960s and 1970s. These technologies provided faster and more precise cutting options for various metal materials.
In recent years, the evolution of machines to cut metal has been shaped by advancements in computer numerical control (CNC) technology. CNC machines offer precise control and automation through computer programming, allowing for complex and accurate metal cutting processes.
Today, machines to cut metal continue to evolve, with increased emphasis on automation, precision, and efficiency. New technologies like waterjet cutting and 3D metal printing are pushing the boundaries of what is possible in metal cutting, revolutionizing industries such as aerospace, automotive, and manufacturing.
The Evolution and Market Trends in machine to cut metal Industry
The machine to cut metal industry has undergone significant evolution in recent years, driven by technological advancements and changing market trends. These changes have revolutionized the production process and improved efficiency in metal cutting operations.
One significant trend in the industry is the shift towards CNC (Computer Numerical Control) machines. CNC machines have the ability to perform complex cutting operations with high precision and accuracy. They can be programmed to execute a variety of cutting patterns, reducing human error and increasing productivity. This trend has led to the replacement of traditional manual cutting methods with automated processes, saving time and costs for manufacturers.
Another key development in the metal cutting industry is the adoption of laser cutting technology. Laser cutting machines utilize a highly concentrated beam of light to cut through metal with precision. This modern technique offers several advantages, including faster cutting speeds, minimal material wastage, and the ability to work with a wide range of metals. As a result, laser cutting has become increasingly popular in industries such as automotive, aerospace, and electronics.
Additionally, there has been a growing demand for machine to cut metal that can handle thicker and more complex metal sheets. To meet this demand, manufacturers have introduced advanced cutting systems equipped with more powerful tools and improved cutting techniques. These machines are capable of cutting thick metal sheets quickly and accurately, making them ideal for heavy-duty industries.
Market trends in the machine to cut metal industry also reflect the increasing focus on sustainability and environmental consciousness. Manufacturers are now incorporating eco-friendly features in their machines, such as energy-efficient motors and recycling systems for cutting debris. This shift towards greener practices is driven by consumer demand for sustainable products and stricter environmental regulations.
In conclusion, the machine to cut metal industry has seen significant evolution and market trends in recent years. The adoption of CNC machines, laser cutting technology, and advanced cutting systems has improved production efficiency and output. Moreover, the industry is embracing sustainability by incorporating eco-friendly features. These trends are likely to continue shaping the industry as it aims to meet the demands of a rapidly changing market.
Custom Private Labeling and Branding Opportunities with Chinese machine to cut metal Manufacturers
There are numerous opportunities for custom private labeling and branding with Chinese manufacturers specializing in metal cutting machines. This rapidly growing industry offers various options for businesses aiming to establish their own brand identity or extend their existing product line.
Chinese manufacturers can provide a range of metal cutting machines, including laser cutting machines, plasma cutters, waterjet cutters, and CNC routers. These machines can be customized and branded according to specific requirements, ensuring a unique product tailored to individual business needs.
Private labeling allows businesses to imprint their logo, company name, and other brand elements directly onto the machine. This feature helps to enhance brand recognition and build customer loyalty, creating a distinct identity in the market. Chinese manufacturers have the expertise to offer customized private labeling services, ensuring the highest quality finish and accurate representation of the brand image.
Furthermore, branding opportunities exist beyond just labeling. Chinese manufacturers can work closely with businesses to develop custom designs that reflect their brand values and resonate with their target audience. This includes customized machine exteriors, control panels, and user interfaces. By incorporating brand-specific colors, fonts, and imagery, businesses can create a consistent brand experience and reinforce their brand identity.
In addition to branding benefits, partnering with Chinese manufacturers offers cost advantages. China has a highly competitive manufacturing industry, allowing businesses to access quality metal cutting machines at competitive prices. Furthermore, the country’s extensive supply chain network ensures a wide range of options and fast turnaround times for customizations and branding.
Overall, with the assistance of Chinese machine manufacturers, businesses have the opportunity to expand their product offerings, strengthen their brand presence, and capitalize on the growing market for metal cutting machines. Custom private labeling and branding services provide a competitive edge and help businesses establish themselves as leaders in the industry.
Tips for Procurement and Considerations when Purchasing machine to cut metal
When purchasing a machine to cut metal, there are several important factors to consider. Here are some tips and considerations to help you make an informed decision:
1. Determine your specific needs: Begin by assessing the type and thickness of metal you will be cutting, as well as the required accuracy and production volume. This will help you choose the appropriate cutting method and machine type.
2. Cutting method: There are various cutting methods available, including plasma cutting, laser cutting, waterjet cutting, and mechanical cutting. Each method has its advantages and limitations, so carefully evaluate their suitability for your application.
3. Machine size and capacity: Consider the size and weight of the metal sheets or parts you will be cutting. Ensure that the machine you choose has a large enough cutting table and can accommodate the dimensions of your workpieces.
4. Power requirements: Check the power requirements of the machine, including the electrical supply and compressed air needs, and ensure that your facility can meet these requirements.
5. Cutting speed and efficiency: Look for a machine that offers high cutting speed and efficiency while maintaining accuracy. The machine should be capable of meeting your production demands without compromising on quality.
6. Maintenance and support: Consider the machine’s maintenance requirements and availability of spare parts. Look for a reliable manufacturer or supplier who can provide excellent customer support and service.
7. Safety features: Ensure that the machine is equipped with necessary safety features, such as emergency stop buttons, safety interlocks, and protective enclosures. Safety should never be compromised when working with metal cutting machines.
8. Cost and budget: Set a budget for your machine purchase and consider the long-term return on investment. Compare the prices, features, and warranties offered by different manufacturers or suppliers before making a decision.
9. User-friendliness: Evaluate the user interface and control system of the machine. It should be intuitive and easy to use, allowing operators to quickly learn and operate the equipment effectively.
10. Reviews and recommendations: Read customer reviews and seek recommendations from industry professionals to gain insights into the machine’s performance, reliability, and overall satisfaction.
By considering these tips and conducting thorough research, you can make an informed decision when purchasing a machine to cut metal. Remember to prioritize your specific needs, safety, efficiency, and long-term value for money.
FAQs on Sourcing and Manufacturing machine to cut metal in China
Q: How can I source and manufacture a machine to cut metal in China?
A: There are several steps involved in sourcing and manufacturing a metal-cutting machine in China. First, you need to conduct thorough research to identify reliable suppliers and manufacturers that specialize in metal-cutting machines. Online platforms, trade shows, and industry associations can be valuable resources for finding potential partners.
Next, you should request quotes and samples from multiple manufacturers to evaluate their capabilities, quality standards, and pricing. It is important to clearly communicate your specific requirements and ensure that the manufacturers can meet them.
Once you have selected a suitable manufacturer, you can proceed with the negotiation of pricing, payment terms, and manufacturing timelines. Establishing a clear agreement and contract with the manufacturer is vital to protect your interests and ensure a smooth manufacturing process.
After reaching an agreement, you may need to collaborate closely with the manufacturer to finalize the machine design, including the technical specifications, materials, and any customization required. Frequent communication and regular updates should be maintained throughout the manufacturing process to address any potential issues promptly.
Before production starts, it is crucial to conduct a thorough quality assessment of the manufacturer, including verifying their certifications, inspecting their facilities, and reviewing their past work experience. This will help ensure that the manufacturer meets your quality standards and produces the desired metal-cutting machine.
Once production begins, it is advisable to have regular quality control inspections to monitor the manufacturing progress and identify any defects or deviations from the agreed specifications. Frequent communication with the manufacturer is key to address and rectify any issues that arise during the production process.
Finally, arrange for the shipment of the finished machines. This involves coordinating logistics, ensuring proper packaging, and complying with all necessary customs and import requirements.
While sourcing and manufacturing a metal-cutting machine in China may require careful planning, research, and execution, it offers the opportunity to benefit from cost-effective manufacturing capabilities and access to a vast supplier base with specialized expertise in metal-cutting machinery.
Why contact sourcifychina.com get free quota from reliable machine to cut metal suppliers?
Sourcifychina.com offers a free quota to contact reliable machine suppliers for metal cutting because it understands the importance of providing value to its users. By offering this free quota, Sourcifychina.com aims to facilitate the sourcing process for businesses that require metal cutting services.
Metal cutting is a critical step in various industries, including manufacturing, construction, and automotive. Finding reliable machine suppliers can be challenging, especially for businesses that are new to sourcing from China. Sourcifychina.com recognizes this challenge and aims to simplify the process by connecting businesses with trusted suppliers.
The free quota allows businesses to contact reliable machine suppliers without any additional cost. This enables them to explore their options and gather necessary information before making a decision. By eliminating the financial barrier, Sourcifychina.com encourages businesses to take the first step in their sourcing journey.
Sourcifychina.com ensures the reliability of its machine suppliers by thoroughly vetting them before including them in its network. This selection process involves assessing their experience, certifications, and client testimonials. Only those suppliers that meet the necessary criteria are featured on the platform, guaranteeing businesses access to trusted partners.
Furthermore, Sourcifychina.com understands that efficiency is crucial in today’s fast-paced business environment. By offering this free quota, businesses can directly communicate with suppliers, gather quotes, and discuss their specific requirements. This streamlines the sourcing process and saves businesses valuable time and effort.
In conclusion, Sourcifychina.com provides a free quota to contact reliable machine suppliers for metal cutting in order to simplify the sourcing process, eliminate financial barriers, and ensure efficient communication. By doing so, businesses can confidently connect with suppliers and make informed decisions, ultimately facilitating successful sourcing from China.