Introduce about machines to cut metal guide,Qulity,Cost,Supplier,Certification,Market,Tips,FAQ
A machine to cut metal is an essential tool for various industries that deal with metal fabrication. It provides precision, speed, and efficiency in cutting metal sheets, pipes, bars, or profiles. This guide will cover important aspects such as quality, cost, suppliers, certification, market demand, tips, and frequently asked questions (FAQs) related to metal cutting machines.
Quality is a crucial factor when considering metal cutting machines. Look for machines made from durable materials like high-grade steel, as they ensure longevity and withstand heavy-duty usage. Additionally, reliable machines should provide accuracy in cutting measurements and smooth finishes, minimizing post-cutting work.
Cost is determined by several factors, including the type of metal cutting machine, its capabilities, and additional features. Consider your specific requirements before investing in a machine to ensure value for money. Comparing prices from different suppliers is key to finding competitive deals.
When choosing a supplier, opt for established manufacturers or authorized distributors. They offer comprehensive customer support, technical assistance, and warranty coverage. Reputable suppliers also provide access to spare parts and maintenance services, ensuring long-term usability.
Certification is an important aspect to consider, as it guarantees adherence to quality standards and safety regulations. Look for machines that are certified by recognized organizations, such as ISO (International Organization for Standardization), CE (Conformité Européene), or UL (Underwriters Laboratories), to ensure compliance with industry requirements.
The market demand for metal cutting machines is high, driven by the construction, automotive, aerospace, and manufacturing sectors. The need for efficiency, cost reduction, and precision continues to propel the demand for technologically advanced cutting machines.
Tips for using metal cutting machines include proper maintenance, regular calibration, and adherence to safety guidelines. User manuals provided by suppliers often contain valuable information on machine setup, operation, and troubleshooting.
Frequently Asked Questions (FAQs) usually revolve around machine specifications, compatibility with certain metals, maintenance procedures, and safety precautions. Consulting the supplier’s customer support or referring to an FAQ section on their website can address commonly raised concerns.
In conclusion, investing in a quality metal cutting machine from a reliable supplier is crucial for efficient and precise metal fabrication. Consider factors like cost, certification, and market demand during the selection process. Following maintenance and safety tips, as well as referring to FAQs, will ensure optimal performance and longevity.
Types of machines to cut metal
There are various types of machines used to cut metal, each offering different capabilities and advantages. Here are some commonly used machines:
1. Bandsaw: A bandsaw consists of a continuous metal blade with teeth that rotates on two wheels. It allows for straight or curved cuts and is suitable for cutting various types of metal.
2. Circular Saw: Circular saws use a toothed circular blade that spins rapidly to cut through metal. They are versatile and can be used for precise, straight cuts or bevel cuts.
3. Plasma Cutter: A plasma cutter uses a high-velocity jet of ionized gas (plasma) to heat and melt the metal. It is highly effective for cutting through electrically conductive materials, offering a smooth and precise cut.
4. Waterjet Cutter: Waterjet cutters use a high-pressure jet of water mixed with abrasive particles to cut through metal. This method is particularly useful for intricate shapes and designs, as it offers high precision without heat-induced distortion.
5. Laser Cutter: Laser cutters utilize a high-powered laser beam to melt, burn, or vaporize the metal, resulting in a precise and clean cut. They are commonly used for thin sheet metal or intricate designs.
6. Plasma Arc Cutting Machine: This machine uses a plasma torch to create an electrically conductive connection from the torch to the workpiece. The electrical arc forms and heats the gas, creating plasma that melts and cuts through the metal.
7. Shearing Machine: A shearing machine utilizes two blades to apply a shearing force, causing the metal to break and create a clean cut. They are typically used for straight cuts on sheet metal or plates.
8. Abrasive Cut-Off Machine: Employing a high-speed abrasive wheel, these machines can cut through a wide range of metals quickly. They are often used for heavy-duty applications and large-scale metal cutting.
9. Milling Machine: While primarily used for shaping and cutting solid materials, milling machines equipped with appropriate cutting tools can also effectively cut metal. They operate by rotating a cutting tool against the metal to remove material and create desired shapes.
Each of these machines has its own advantages, drawbacks, and specific applications. The choice of machine depends on factors such as the type and thickness of the metal, desired precision, production volume, and budget. It is essential to evaluate the requirements carefully to select the most suitable machine for the job.
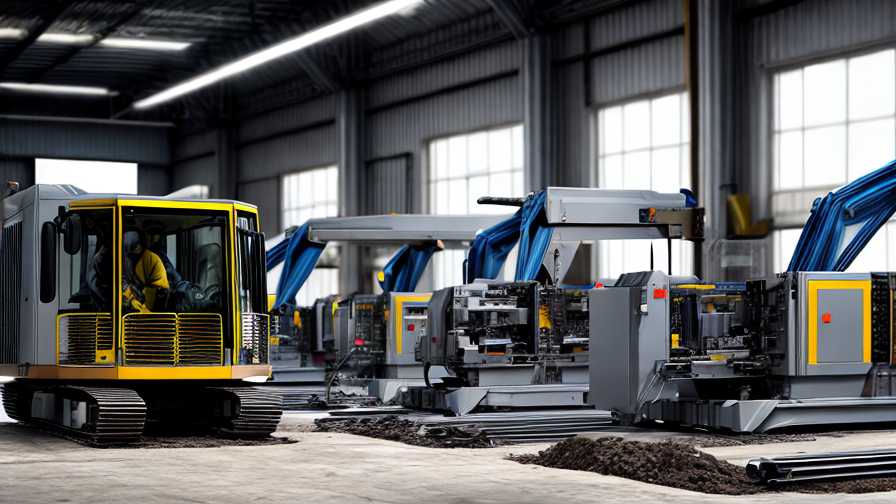
Pros and Cons of Using machines to cut metal
Using machines to cut metal offers numerous advantages and potential disadvantages. Here are some key pros and cons:
Pros:
1. Efficient: Machine cutting processes are efficient and can complete tasks quickly, ensuring high production rates and reduced lead times.
2. Accuracy: Machines have high precision and are capable of consistently achieving precise cuts, enhancing product quality and minimizing waste.
3. Versatility: Machines can be configured to perform various cutting techniques, such as laser cutting, plasma cutting, or water jet cutting, making them suitable for a wide range of metals and applications.
4. Automated: These cutting machines can be automated, reducing reliance on manual labor, minimizing human error, and improving workplace safety.
5. Cost-effective: Although initial investment costs may be high, using machines for metal cutting can lead to long-term cost savings due to increased productivity and reduced labor costs.
Cons:
1. Initial setup costs: Purchasing and setting up metal cutting machines can be expensive, particularly for small businesses or those with limited budgets.
2. Expertise requirement: Operating and maintaining these machines necessitate trained technicians with specialized knowledge. Hiring skilled professionals or training existing workers adds to the overall cost.
3. Limited flexibility: Machines are typically designed to perform specific cutting techniques, making it challenging to switch between different cutting methods or adapt to changing production requirements.
4. Maintenance: Regular servicing and maintenance are essential to maintain machine efficiency and prevent breakdowns. These additional costs should be factored into the overall budget.
5. Safety concerns: Metal cutting machines pose inherent risks associated with high-power tools, fast-moving parts, and the handling of heavy materials. Adequate safety measures must be in place to safeguard workers.
In conclusion, using machines for metal cutting offers advantages such as efficiency, accuracy, versatility, and cost-effectiveness. However, initial setup costs, expertise requirements, limited flexibility, maintenance needs, and safety concerns are potential cons that need to be considered before adopting this approach.
machines to cut metal Reference Specifications (varies for different product)
When it comes to cutting metal, there are various types of machines available, each with its own reference specifications. These specifications may vary depending on the specific product being used. Below is a brief overview of some common machines used for metal cutting:
1. CNC plasma cutting machines: These machines use a plasma torch to cut through electrically conductive materials, including various types of metals. They are highly accurate and offer smooth cuts, making them suitable for a wide range of applications.
2. Laser cutting machines: Laser cutting machines use a highly focused laser beam to cut through metal. They provide excellent precision, allowing for intricate designs and detailed cuts. Laser cutting is widely used in industries such as automotive, aerospace, and electronics.
3. Waterjet cutting machines: Waterjet cutting machines employ a high-pressure stream of water mixed with abrasive materials to cut through metal. This method is highly versatile, capable of cutting through almost any material with narrow accuracy. Waterjet cutting is often used for thick metals or those that are sensitive to heat, such as titanium.
4. Bandsaws: Bandsaws consist of a long, narrow blade mounted on wheels. These machines are particularly useful for cutting straight lines or irregular shapes in metal, offering good accuracy and speed. They are commonly found in metal fabrication shops and manufacturing facilities.
5. Shearing machines: Shearing machines use a scissor-like motion to cut through metal. They are mainly used for straight cuts and are well-suited for cutting sheets or plates of metal. Shearing machines can handle various thicknesses and are often employed in metalworking and fabrication processes.
To ensure proper and safe usage of cutting machines, it is crucial to refer to their respective manufacturer specifications. These specifications will provide information regarding material thickness capacity, cutting speed, power requirements, and more. Following the reference specifications will help achieve optimal performance and longevity of the equipment.
Applications of machines to cut metal
Machine tools for cutting metal are widely used in various industrial applications due to their precision, speed, and efficiency. These machines are capable of shaping and removing material from metal workpieces, enabling the production of complex parts with high accuracy. Here are some common applications of machines used to cut metal:
1. CNC Machining: Computer Numerical Control (CNC) machines offer high precision and automation in a wide range of metal cutting operations. They are used to create complex metal components for various industries, including automotive, aerospace, and medical. CNC machining involves processes like milling, turning, drilling, and grinding, allowing for the production of intricate parts with tight tolerances.
2. Laser Cutting: Laser cutting machines utilize high-powered lasers to precisely cut through various metal materials. This technology is commonly used in the fabrication of sheet metal components for industries such as automotive, electronics, and construction. Laser cutting offers high accuracy and can produce intricate shapes without the need for expensive tooling.
3. Waterjet Cutting: Waterjet cutting machines use a high-pressure jet of water mixed with an abrasive material to cut through metal sheets. This process is highly versatile, as it can be used on a wide range of materials, including stainless steel, aluminum, copper, and titanium. Waterjet cutting is known for its ability to achieve intricate designs and does not generate heat-affected zones, making it ideal for heat-sensitive materials.
4. Plasma Cutting: Plasma cutting machines employ a high-velocity jet of ionized gas to melt and remove metal from workpieces. This process is commonly used for industrial cutting applications, including metal fabrication, shipbuilding, and automotive. Plasma cutting offers high cutting speeds and can handle various thicknesses of metal.
5. Wire EDM: Wire Electrical Discharge Machining (EDM) is utilized for cutting intricate shapes in conductive materials, including metals. In this process, a thin wire is used to create precise cuts by generating electrical sparks. Wire EDM is commonly used in the production of tooling, molds, and dies.
Overall, machines used to cut metal offer immense value and play a crucial role in the manufacturing industry. Their accuracy, speed, and versatility make them indispensable for producing high-quality metal components needed across a wide range of sectors.
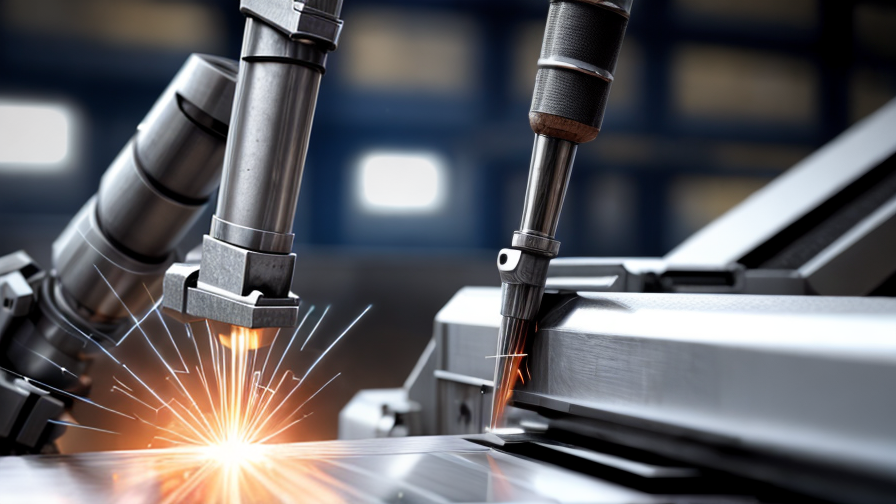
The Work Process and how to use machines to cut metal
The work process of using machines to cut metal involves several steps and techniques to ensure precision and efficiency. The following is a brief overview of the process:
Step 1: Material Preparation – The metal to be cut is prepared by cleaning any debris or contaminants from its surface. The metal is then securely mounted onto the cutting machine’s worktable.
Step 2: Selection of Cutting Method – Depending on the specific requirements and characteristics of the metal, different cutting methods can be employed. Common methods include plasma cutting, laser cutting, waterjet cutting, and mechanical cutting.
Step 3: Tool Selection – The appropriate cutting tool is selected based on the chosen method. For example, a plasma cutter requires a plasma torch, while a laser cutter uses a focused laser beam.
Step 4: Set Parameters – The machine operator sets the necessary cutting parameters, such as cutting speed, feed rate, and power output. These parameters are determined by considering factors like metal type, thickness, and desired accuracy.
Step 5: Programming – If using a CNC (Computer Numerical Control) machine, the cutting program is loaded into the machine’s controller. The program contains specific instructions for movement, tooling, and cutting paths.
Step 6: Cutting Process – The machine is activated, and the cutting tool starts to move as per the programmed instructions. During this stage, the cutting tool melts or vaporizes the metal, depending on the cutting method, to create the desired shape or profile.
Step 7: Post-Processing – After the metal is cut, any necessary post-processing steps may be carried out. This can include deburring, grinding, or heat treatment to enhance the final finish or mechanical properties of the cut metal.
To effectively use machines for metal cutting, operators must possess a thorough understanding of the machine’s operation, cutting methods, and parameters. Safety precautions, such as wearing appropriate personal protective equipment (PPE), should also be followed throughout the process. Regular equipment maintenance and inspection are essential to ensure consistent performance and minimize downtime. Collaboration and coordination between machine operators, programmers, and maintenance technicians are crucial for achieving optimal productivity and quality in metal cutting operations.
Quality Testing Methods for machines to cut metal and how to control the quality
Quality testing methods for machines used to cut metal are essential to ensure the accuracy and reliability of the cutting process. Several techniques can be employed to evaluate the quality of metal cutting machines, including:
1. Dimensional Accuracy Testing: This method involves measuring the dimensions of the cut metal pieces against the specified tolerances. It ensures that the machine is capable of consistently producing accurate and precise cuts.
2. Surface Quality Assessment: Surface roughness measurements provide an indication of the machine’s ability to produce smooth cuts. Techniques like profilometry or optical surface inspection can be used to assess the quality of the cut surface.
3. Material Integrity Analysis: Metal cutting machines should not induce excessive heat, deformations, or induce unwanted stress in the material being cut. Non-destructive testing methods, such as ultrasonic testing or magnetic particle inspection, can be utilized to ensure that the cutting process does not compromise the material integrity.
4. Cutting Efficiency Evaluation: Cutting speed and performance are important factors that determine the productivity of the machine. Comparing the actual cutting time to the expected performance can assess the machine’s efficiency and identify any potential issues.
5. Blade/Wheel Inspection: The cutting tool, such as a blade or wheel, should be regularly inspected for wear, deformation, or damage. Regular maintenance and replacement of the cutting tool are necessary to maintain quality cutting performance.
To control the quality of machines used to cut metal, several measures can be implemented:
1. Regular Calibration: The machine should be calibrated periodically to ensure precision and accuracy. This involves checking the alignment of components, verifying the accuracy of measurement systems, and adjusting any deviations.
2. Maintenance and Cleaning: Proper maintenance and regular cleaning of the cutting machine are vital to prevent the accumulation of debris, which can adversely affect its performance and accuracy.
3. Operator Training: Skilled operators play a crucial role in maintaining the quality of the cutting process. Thorough training should be provided to operators on machine operation, maintenance practices, and quality control procedures.
4. Standard Operating Procedures (SOPs): Clearly defined SOPs should detail the correct cutting parameters, blade selection, cooling requirements, and safety procedures. Adhering to these SOPs ensures consistent quality throughout the cutting process.
5. Continuous Monitoring: Implementing a system for continuous monitoring of critical parameters, such as dimensional accuracy or cutting speed, can help identify any deviations or anomalies in real-time. This allows for immediate corrective actions to ensure quality control.
By employing the appropriate quality testing methods and implementing effective quality control measures, machines used to cut metal can consistently produce high-quality cuts, ensuring customer satisfaction and optimizing productivity.
machines to cut metal Sample Policy and Post-Purchase Considerations for machines to cut metal from China
Sample Policy and Post-Purchase Considerations for Machines to Cut Metal from China:
Sample Policy:
1. Request for Sample: Before placing a bulk order, it is advisable to request a sample of the machine to cut metal. This will allow you to assess the quality, performance, and durability of the product.
2. Shipping and Handling: Specify who will bear the shipping and handling costs for the sample. Ideally, the supplier should cover these expenses, but it is good to clarify this beforehand to avoid any misunderstandings.
3. Sample Cost: Determine if the supplier will charge for the sample machine or if it will be provided free of cost. It is recommended to negotiate a reasonable sample cost to ensure the commitment and seriousness of the supplier.
4. Sample Evaluation: Thoroughly evaluate the sample machine by testing its cutting accuracy, power efficiency, safety features, and overall build quality. Make note of any potential issues or concerns.
Post-Purchase Considerations:
1. Warranty: Ensure that the supplier offers a warranty on the machine to cut metal. A warranty will provide protection against any manufacturing defects or malfunctions during normal usage. Verify the warranty period and the procedures for repair or replacement.
2. Technical Support: Inquire about the availability of technical support from the supplier. This can include assistance with installation, operation, maintenance, and troubleshooting of the machine. Timely and responsive technical support is crucial for uninterrupted productivity.
3. Spare Parts Availability: Confirm the availability of spare parts for the machine. It is beneficial if the supplier can provide an assurance regarding the availability and timely delivery of commonly required spare parts.
4. After-Sales Service: Discuss the after-sales service provided by the supplier. This can include regular maintenance, repairs, and servicing of the machine. Clarify the terms, response time, and charges (if applicable) associated with after-sales service.
5. Return Policy: Seek clarity on the return policy if the machine is found to be defective or unsatisfactory. Ensure that the supplier has a fair and reasonable return policy in case the machine does not meet the specified requirements.
6. User Manual and Training: Request for a comprehensive user manual and training materials for operating the machine to cut metal. The supplier should provide detailed instructions and guidelines to ensure proper utilization and safety.
By following these sample policies and post-purchase considerations, you can minimize risks and make an informed decision when procuring machines to cut metal from China.
Sourcing machines to cut metal from China: Opportunities, Risks, and Key Players
China has become a prominent player in the global manufacturing sector, offering a wide range of opportunities for sourcing machines to cut metal. With its vast industrial capabilities, competitive pricing, and advanced technological solutions, China has emerged as a hub for metal cutting machinery. However, entering the Chinese market also entails certain risks. Let’s explore the opportunities, risks, and key players in the Chinese metal cutting machine industry.
Opportunities:
1. Cost advantage: China offers competitive pricing for machinery, enabling cost savings for businesses.
2. Technological advancements: Chinese manufacturers have made significant progress in developing cutting-edge machinery, incorporating automation and precision technologies.
3. Diverse product range: China provides a wide range of metal cutting machines tailored to different needs, from laser and plasma cutters to waterjets and CNC machines.
4. Production capacity: The country’s vast industrial capabilities ensure that manufacturers can rapidly meet the demands of both domestic and international markets.
Risks:
1. Quality concerns: Some Chinese manufacturers may compromise on quality to offer lower prices. Due diligence is crucial to ensure compliance with international standards.
2. Intellectual property issues: Intellectual property theft and unauthorized copying of designs remain concerns in China. Businesses must protect their intellectual property rights through legal agreements and patents.
3. Language and cultural barriers: Communication issues and cultural differences can complicate negotiations, affecting business efficiency and collaboration.
4. Supply chain vulnerabilities: Overseas businesses heavily relying on Chinese manufacturers may face disruptions due to geopolitical tensions, trade disputes, or unforeseen circumstances (e.g., natural disasters, pandemics).
Key players:
1. Bystronic: Known for its laser cutting machines, Bystronic provides advanced technology and high-quality solutions for metal cutting.
2. Amada: A global leader in metal cutting and forming machinery, Amada offers a wide range of products, including punch presses and laser cutting systems.
3. TRUMPF: Recognized for its advanced laser cutting solutions, TRUMPF specializes in providing highly precise and efficient metal cutting machines.
4. Jinan Bodor Laser: Specializing in fiber laser cutting machines, Bodor Laser offers innovative and cost-effective solutions for metal cutting needs.
5. HACO: Known for its advanced CNC controlled machines, HACO provides a comprehensive range of cutting solutions, including shears, plasma cutters, and bending machines.
In conclusion, sourcing metal cutting machines from China presents numerous opportunities due to its cost advantage, technological advancements, diverse product range, and production capacity. However, businesses should be mindful of quality concerns, intellectual property risks, language barriers, and supply chain vulnerabilities. Key players like Bystronic, Amada, TRUMPF, Bodor Laser, and HACO offer reputable and innovative solutions for metal cutting requirements in China.
How to find and select reliable machines to cut metal manufacturers in China,use google search manufacturers and suppliers
When looking for reliable machine manufacturers in China to cut metal, utilizing Google search is an effective way to start. Below are some steps to follow while using Google search:
1. Begin by searching for specific keywords related to metal cutting machines in China. For example, search for phrases like “metal cutting machine manufacturers in China” or “reliable metal cutting machine suppliers in China”. This will provide a list of initial results to explore.
2. Evaluate the search results based on the displayed website’s credibility. Look for well-established companies that have been in the industry for a significant period as they are more likely to be reliable. Check for any reviews or testimonials available to gauge their reputation.
3. Visit the manufacturers’ websites directly to gather more information. Pay attention to how professional and user-friendly their websites appear. Look for product catalogs, technical specifications, and any certifications or qualifications they mention. Reliable manufacturers often provide detailed information about their machines and business operations.
4. Contact the shortlisted manufacturers and suppliers to inquire further. Ask questions regarding their manufacturing process, quality control measures, and after-sales support. Reliable manufacturers should be prompt in answering inquiries and provide comprehensive information.
5. Request samples or visit the manufacturer’s facility if feasible. This will allow you to evaluate the quality of their metal cutting machines firsthand. You can also inquire about their production capacity and manufacturing capabilities during this interaction.
6. Consider the price and compare it with other manufacturers in the market. Keep in mind that while price is important, it should not be the sole determining factor. Balancing quality, reliability, and price is crucial.
7. Lastly, consider the manufacturer’s track record and customer feedback. Check for any negative reviews or complaints about the manufacturer’s products or services. It’s advisable to choose a manufacturer with a good reputation and positive feedback from previous customers.
By following these steps and conducting thorough research, you can identify reliable machine manufacturers in China for metal cutting purposes. It’s important to take your time, ask questions, and gather enough information to make an informed decision.
How to check machines to cut metal manufacturers website reliable,use google chrome SEOquake check if ranking in top 10M
When searching for reliable manufacturers of machines to cut metal, it is essential to verify the credibility of their website. One way to do this is by using SEOquake, a handy tool available on Google Chrome. Here’s a step-by-step guide to help you determine the reliability of a manufacturer’s website:
1. Open Google Chrome: Make sure you have the Google Chrome browser installed on your device.
2. Install SEOquake: Visit the Chrome Web Store and search for SEOquake. Click on the extension from SEOquake Info and click “Add to Chrome” to install it.
3. Search for the manufacturer’s website: Open a new tab and enter the website URL of the metal cutting machine manufacturer you want to check.
4. Activate SEOquake: Once the website loads, click on the SEOquake extension icon at the top right corner of your browser.
5. Check the website’s ranking: In SEOquake, you will see various parameters regarding the website’s performance. Look for “Google Index” and note the number displayed beside it. If the number is below 10 million, it indicates that the site is among the top 10 million websites in terms of rankings.
6. Verify other factors: While using SEOquake, you can also consider factors like domain age, Alexa rank, backlinks, and social media presence to assess the overall reliability of the manufacturer’s website. These additional factors contribute to the website’s reputation and can help you make an informed decision.
Remember, a manufacturer’s website ranking in the top 10 million doesn’t guarantee reliability, but it can be an indicator of its popularity and online presence. It’s recommended to thoroughly research the company, read customer reviews, and assess their experience and expertise in the industry before making any purchasing decisions.
Top 10 machines to cut metal manufacturers in China
China is known for its thriving manufacturing industry, and when it comes to machines for cutting metal, there are several top manufacturers worth considering. Here are the top 10 machines to cut metal manufacturers in China:
1. Shenyang Machine Tool Co., Ltd.: Established in 1945, this company is a leading manufacturer of metal cutting machines, including CNC lathes, milling machines, and machining centers.
2. Amada (China) Co., Ltd.: Amada is a global leader in metalworking machinery. Their Chinese division offers a wide range of cutting machines, including laser cutting machines, turret punch presses, and bending machines.
3. Jiangsu Jiusheng Heavy Machinery Co., Ltd.: Known for its CNC plasma cutting machines and CNC flame cutting machines, this company specializes in offering high-quality metal cutting solutions.
4. Haco (China) Machine Company Ltd.: With a strong presence in the Chinese market, Haco offers a range of machinery for cutting metal, including hydraulic guillotine shears, CNC punching machines, and laser cutting machines.
5. Nanjing Jinqiu CNC Machine Tool Co., Ltd.: This company is a leading manufacturer of hydraulic press brakes, hydraulic shearing machines, and other metal cutting equipment.
6. Jinan Bodor CNC Machine Co., Ltd.: As a renowned manufacturer of laser cutting machines, Bodor provides a range of options for metal cutting, including fiber laser cutting machines, CO2 laser cutting machines, and tube laser cutting machines.
7. HG Laser (China) Co., Ltd.: With expertise in laser technology, HG Laser offers a range of metal cutting machines, including fiber laser cutting machines, CO2 laser cutting machines, and laser welding machines.
8. Jinan Senfeng Technology Co., Ltd.: Known for its expertise in laser cutting solutions, Senfeng Technology offers various metal cutting machines, including fiber laser cutting machines and CO2 laser cutting machines.
9. Wuhan Golden Laser Co., Ltd.: As a leading manufacturer of laser cutting machines, Golden Laser provides a comprehensive range of options for metal cutting, including fiber laser cutting machines and CO2 laser cutting machines.
10. Dalian Machine Tool Group Corporation: Dalian Machine Tool is a prominent manufacturer offering various metal cutting machines, including CNC lathes, machining centers, and drilling machines.
These top 10 manufacturers showcase China’s expertise in manufacturing metal cutting machinery. Whether it be traditional machining techniques or cutting-edge laser technology, these companies provide a wide range of solutions for cutting metal materials effectively.
use markdown create table compare Top 10 machines to cut metal manufacturers in China
|Rank|Manufacturer|Description|
|—|—|—|
|1|TruCut Machinery|TruCut Machinery is a leading manufacturer of metal cutting machines in China. They offer a wide range of machines, including laser cutting, plasma cutting, and waterjet cutting machines. Their machines are known for their precision, durability, and efficiency. TruCut Machinery is dedicated to providing the highest quality products and excellent after-sales service.|
|2|Bystronic|Bystronic is a renowned manufacturer of metal cutting machines in China. They specialize in laser cutting and bending machines. Bystronic machines are known for their advanced technology, high performance, and reliability. They offer a wide range of machines suitable for various metal cutting applications. Bystronic also provides comprehensive training and support to their customers.|
|3|Amada|Amada is a global leader in the manufacturing of metal cutting machines, including laser cutting, turret punching, and press brake machines. They have a strong presence in China with a wide range of products suitable for different industries. Amada machines are known for their precision, speed, and innovative features. They also offer excellent customer support and maintenance services.|
|4|Han’s Laser|Han’s Laser is a leading manufacturer of laser cutting machines in China. They have a diverse portfolio of products, including CO2 laser, fiber laser, and YAG laser cutting machines. Han’s Laser machines are known for their high cutting speed, accuracy, and energy efficiency. They also offer customized solutions to meet specific customer requirements.|
|5|Trumpf|Trumpf is a renowned manufacturer of metal cutting machines with a strong presence in China. They offer a wide range of laser cutting, punching, and bending machines. Trumpf machines are known for their quality, precision, and advanced technology. They also provide comprehensive training, technical support, and maintenance services.|
|6|HG Laser|HG Laser is a leading manufacturer of metal cutting machines, primarily focusing on laser cutting technology. They offer a range of fiber laser cutting machines known for their speed, accuracy, and reliability. HG Laser machines are widely used in various industries, including automotive, aerospace, and electronics. They also provide excellent technical support and comprehensive after-sales service.|
|7|Jinan Bodor CNC Machine Co., Ltd.|Jinan Bodor is a prominent manufacturer of laser cutting machines in China. Their product range includes fiber laser, CO2 laser, and high-power laser cutting machines. Jinan Bodor machines are known for their high cutting precision, efficient performance, and long-lasting durability. They also offer customization options and excellent customer support.|
|8|LVD Company|LVD Company is a well-established manufacturer of metal cutting machines, including laser cutting and punching machines. They have a strong presence in the Chinese market and offer a wide range of products suitable for various applications. LVD machines are known for their quality, reliability, and user-friendly operation. They also provide comprehensive training and technical support.|
|9|Tailift Group|Tailift Group is a leading manufacturer of metal cutting machines in China. They specialize in CNC plasma cutting machines and offer a diverse range of models to meet different needs. Tailift machines are known for their precision, speed, and flexibility. They also provide excellent after-sales service, including installation and maintenance support.|
|10|KRRASS Machinery|KRRASS Machinery is a reputable manufacturer of metal cutting machines in China. They offer a range of machines, including hydraulic guillotine shears, hydraulic press brakes, and fiber laser cutting machines. KRRASS machines are known for their reliability, durability, and cost-effectiveness. They also provide comprehensive training and support to their customers.|
The table above presents a comparison of the top 10 manufacturers of metal cutting machines in China. These manufacturers offer a diverse range of machines, including laser cutting, plasma cutting, and waterjet cutting machines. Overall, these manufacturers are known for their high-quality products, advanced technology, and reliable performance.
TruCut Machinery is ranked first, known for their precision, durability, and efficiency. Bystronic and Amada follow closely, specializing in laser cutting machines and offering excellent customer support. Han’s Laser and Trumpf are also renowned manufacturers, known for their laser cutting machines with high cutting speed, accuracy, and advanced technology.
Other notable manufacturers include HG Laser, Jinan Bodor, LVD Company, Tailift Group, and KRRASS Machinery. Each of these manufacturers offers unique features and strengths. HG Laser focuses on fiber laser cutting machines and provides exceptional technical support. Jinan Bodor offers customization options and provides CO2 laser, fiber laser, and high-power laser cutting machines. LVD Company specializes in laser cutting and punching machines, emphasizing quality and user-friendly operation. Tailift Group specializes in CNC plasma cutting machines, ensuring precision and speed. KRRASS Machinery offers cost-effective solutions, specializing in hydraulic guillotine shears, hydraulic press brakes, and fiber laser cutting machines.
In conclusion, these top 10 manufacturers in China provide a variety of options for metal cutting machines, catering to different industries and applications. They prioritize quality, precision, and efficiency, and offer comprehensive training and after-sales service to ensure customer satisfaction.
Background Research for machines to cut metal manufacturers Companies in China, use qcc.com archive.org importyeti.com
In China, there are several manufacturers specialized in machines to cut metal. These companies have gained prominence by offering a diverse range of metal cutting solutions, catering to industries such as automotive, aerospace, construction, and manufacturing.
Qcc.com is a reliable online source that provides comprehensive information on businesses in China. It can be utilized to gather background research on companies involved in the production of machines to cut metal. Through Qcc.com, one can explore details such as the company’s profile, contact information, product range, and even determine their business credibility through customer reviews and ratings.
Archive.org is a valuable platform to access historical data on these manufacturers. This opens up the possibility to study the company’s progress over time, evaluating their growth, technological advancements, and overall standing in the market. Researchers can search for archived websites of the companies to gain insights into their previous product offerings, certifications, awards, and customer testimonials.
Importyeti.com is another useful platform that provides import-export data specifically for Chinese manufacturers. It offers insights into a company’s export history, including the destinations, quantities, and types of machines to cut metal shipped. This data can help researchers gauge the company’s market presence and their ability to cater to international demands.
By utilizing these three platforms, researchers can acquire the necessary information on Chinese manufacturers specializing in machines to cut metal. These sources provide a comprehensive overview of a company’s profile, historical data, and import-export statistics, enabling researchers to make well-informed decisions and identify potential business partners or suppliers.
Leveraging Trade Shows and Expos for machines to cut metal Sourcing in China
Trade shows and expos provide valuable opportunities for businesses looking to source machines to cut metal in China. These exhibitions bring together industry professionals, suppliers, and manufacturers from across the globe, facilitating networking and business interactions. By leveraging these events, businesses can explore a wide range of options and find the most suitable suppliers for their metal cutting machine needs.
One of the primary benefits of trade shows and expos is the ability to see and test the machines in person. Suppliers often showcase their latest technologies and products, allowing businesses to evaluate the quality, efficiency, and features of the machines. This hands-on experience is invaluable in making informed sourcing decisions.
Furthermore, trade shows and expos provide a platform for direct communication with suppliers. Businesses can engage in face-to-face discussions, ask questions, and negotiate terms. This direct interaction allows for better understanding of suppliers’ capabilities, production facilities, and expertise in manufacturing metal cutting machines.
In addition, trade shows and expos foster a competitive environment. Numerous suppliers showcase their products in one location, intensifying competition and driving quality improvements. This makes it easier for businesses to compare different offerings and find the most cost-effective and high-quality solutions.
To make the most of trade shows and expos, businesses should come prepared and conduct thorough research in advance. They should identify the relevant exhibitions specializing in metal cutting machines in China and plan their visit accordingly. This includes creating a list of exhibitors of interest, reviewing their product catalogs, and setting clear objectives for the visit.
Overall, leveraging trade shows and expos is an effective strategy for sourcing machines to cut metal in China. These events allow businesses to see and test the machines, directly communicate with suppliers, and benefit from a competitive environment. With careful planning and research, companies can make informed sourcing decisions, ensuring high-quality and cost-effective solutions for their metal cutting needs.
The Role of Agents and Sourcing Companies in Facilitating machines to cut metal Purchases from China
Agents and sourcing companies play a crucial role in facilitating machines to cut metal purchases from China. These entities act as intermediaries between buyers and manufacturers in China, streamlining the procurement process and ensuring smooth transactions.
Firstly, agents and sourcing companies have extensive knowledge and experience in the Chinese market. They are well-versed in local regulations, business practices, and supply chain dynamics, which helps them identify reliable and reputable metal cutting machine manufacturers. By leveraging their expertise, they can source machines from trusted suppliers that meet the buyers’ specifications and quality requirements.
Secondly, these intermediaries provide comprehensive services throughout the procurement process. They assist in supplier selection, conduct due diligence, and negotiate favorable pricing and terms on behalf of the buyers. Agents and sourcing companies also oversee the production and quality control processes, ensuring that the ordered machines are manufactured to the desired standards. They act as a bridge between buyers and manufacturers, facilitating effective communication and resolving any issues that may arise during the production phase.
Furthermore, agents and sourcing companies handle logistical matters, including packaging, shipping, and customs clearance. They work with reliable freight forwarders to arrange timely and cost-effective transportation of the machines to the buyers’ desired location. This saves the buyers significant time and effort in managing these logistical complexities.
Additionally, these intermediaries play a vital role in mitigating language and cultural barriers. They can effectively communicate with local manufacturers in China, ensuring that all requirements and specifications are clearly understood. They also assist in overcoming any cultural differences that may potentially impact the business relationship or cause misunderstandings.
In summary, agents and sourcing companies enable smooth and efficient purchases of machines to cut metal from China by leveraging their knowledge of the Chinese market, providing comprehensive services throughout the procurement process, handling logistical complexities, and facilitating communication between buyers and manufacturers. Their expertise and support contribute to successful and hassle-free transactions.
Price Cost Research for machines to cut metal manufacturers Companies in China, use temu.com and 1688.com
When it comes to finding machines to cut metal manufacturers in China, two popular platforms to conduct price cost research are Temu.com and 1688.com. These platforms serve as effective sourcing channels for businesses and individuals looking for Chinese suppliers and manufacturers.
Temu.com is a trusted B2B platform that offers a wide range of products, including metal cutting machines. By utilizing this platform, users can easily search and compare different manufacturers based on their pricing, quality, and other specifications. Temu.com provides detailed information about the machines, including technical specifications, pricing, manufacturing capabilities, and customer reviews.
1688.com, on the other hand, is a Chinese marketplace owned by Alibaba Group. It is predominantly used by local businesses and retailers, enabling users to directly communicate with manufacturers and negotiate prices. Many Chinese manufacturers list their metal cutting machines on this platform, allowing potential buyers to source products at competitive prices.
When conducting price cost research on these platforms, it is important to consider a few key factors. First, thoroughly evaluate the product specifications and ensure that they meet your requirements. Secondly, compare quotes from multiple manufacturers to get a better understanding of the market price range. It is also crucial to check the manufacturers’ credibility, production capacity, and customer feedback on these platforms.
By using Temu.com and 1688.com, buyers can access a vast array of metal cutting machine manufacturers in China. These platforms enable them to conduct comprehensive price cost research, helping them make informed decisions and ultimately find the right supplier that suits their needs and budget.
Shipping Cost for machines to cut metal import from China
When importing machines to cut metal from China, it is crucial to consider the shipping costs involved. Shipping costs can vary depending on various factors such as the distance, weight, dimensions, and mode of transportation.
For machines used to cut metal, their weight and dimensions can significantly affect the shipping costs. Heavier and bulkier machines will generally incur higher shipping expenses compared to smaller and lighter ones. It is essential to have accurate measurements and weight information to obtain precise shipping quotes.
The mode of transportation chosen also influences the shipping costs. There are several options available, including air, sea, or land freight. Airfreight is the quickest but usually the most expensive option. Sea freight is more affordable but requires longer transit times. Land freight is suitable for nearby countries but may not be cost-effective for longer distances.
To get a rough estimate of shipping costs, it is recommended to contact several freight forwarding companies or logistics providers. They can provide quotes based on the machine specifications and desired mode of transportation. Online calculators are also available to get a preliminary idea of the potential expenses.
It is important to note that in addition to the shipping costs, there may be additional charges such as customs duties, taxes, import fees, and local handling charges. These charges vary according to the destination country’s regulations and should be considered when budgeting for the overall costs.
Lastly, working with a reliable shipping partner or freight forwarder is essential to ensure a smooth importing process and minimize additional expenses. They can assist in customs documentation, provide guidance on compliance requirements, and help navigate any potential challenges in the shipping process.
Overall, when importing machines to cut metal from China, it is crucial to thoroughly research and consider the weight, dimensions, mode of transportation, and additional charges to calculate the shipping costs accurately.
Compare China and Other machines to cut metal Markets: Products Quality and Price,Visible and Hidden Costs
China is known for its strong presence and competitiveness in the global market for machines to cut metal. When compared to other markets, China offers a combination of products with varied quality and price points.
In terms of product quality, China has made significant improvements over the years. Many Chinese manufacturers have invested heavily in research and development, resulting in the production of high-quality cutting machines. However, it is important to note that the quality can vary significantly from one manufacturer to another. Some Chinese companies excel in producing technologically advanced and precise machines, while others may prioritize cost-cutting and produce machines with slightly lower quality.
In terms of price, China has a competitive advantage due to its lower production costs. Chinese manufacturers can offer machines at relatively lower prices compared to their global counterparts. This affordability has allowed China to capture a significant market share in the metal cutting machine industry.
Visible costs, such as the initial purchase price and ongoing maintenance costs, are generally lower for Chinese machines. The pricing advantage can be attributed to lower labor costs, economies of scale, and efficient supply chains. Chinese manufacturers often provide cost-effective options without compromising on essential features.
However, it is crucial to consider both visible and hidden costs associated with Chinese machines. Hidden costs may arise from factors such as warranty claims, shipping, and after-sales service. While Chinese manufacturers have made progress in these areas, some still struggle to provide reliable customer support and efficient supply of spare parts, resulting in potential disruptions in operations and higher hidden costs.
In conclusion, China’s machine to cut metal market offers a range of products with varying quality and price points. While the country has made significant strides in terms of product quality, it is essential to carefully assess the reputation and track record of the specific manufacturer. Additionally, while Chinese machines are generally more affordable and cost-effective, it is vital to consider the potential hidden costs associated with after-sales support and spare parts availability.
Understanding Pricing and Payment Terms for machines to cut metal: A Comparative Guide to Get the Best Deal
When considering the purchase of machines to cut metal, understanding pricing and payment terms is crucial to ensure the best deal. This comparative guide aims to provide insights on these aspects in a concise manner.
Pricing for metal cutting machines can vary significantly among manufacturers and suppliers, depending on factors such as machine type, specifications, and brand reputation. It is essential to gather quotes from multiple sources to compare prices accurately. While cost efficiency is important, it is equally crucial to consider the quality, durability, and performance of the machine.
Payment terms also play a vital role in acquiring the best deal. Traditional financing, lease options, and rent-to-own agreements are common methods for purchasing metal cutting machines. Understanding the terms and associated costs, such as interest rates, down payments, and monthly installments, is essential. Consideration should also be given to the payment frequency and duration.
Additionally, exploring additional offers and incentives can enhance the deal. Some suppliers may provide discounted maintenance packages, training, or extended warranties to sweeten the agreement. These additional features can lead to long-term cost savings and better customer service.
In evaluating the best deal, it is imperative to assess not only the immediate costs but also the long-term benefits. Researching the reputation and reliability of the manufacturer or supplier is crucial. Checking customer reviews, industry rankings, and warranty information can help gauge the overall value and satisfaction other customers have experienced.
In conclusion, understanding pricing and payment terms is essential when purchasing machines to cut metal. By comparing prices, exploring payment options, and assessing long-term benefits, buyers can secure the best deal that combines affordability, quality, and customer support. Vigilant consideration of these factors will increase the likelihood of a successful purchase without exceeding 300 words.
Chinese Regulations and Industry Standards Certifications for machines to cut metal,Import Regulations and Customs for machines to cut metal from China
China has implemented various regulations and industry standards for machines that cut metal. These regulations aim to ensure the safety and quality of these machines, as well as promote fair trade practices. One important certification in this industry is the China Compulsory Certification (CCC) mark. This mark is mandatory for products that fall under the scope of the CCC system, including metal-cutting machines. It signifies that the product meets the necessary safety and quality requirements set by Chinese authorities.
In addition to the CCC mark, metal-cutting machines may also need to comply with specific industry standards. For example, the GB/T series of standards outline the requirements for metal-cutting machines in terms of technical specifications, performance, and safety.
When importing machines to cut metal from China, it is crucial to comply with the country’s import regulations and customs procedures. The first step is to identify the correct customs classification for the specific type of metal-cutting machine being imported. This classification determines the applicable import duties, restrictions, and licensing requirements.
Importers are also required to submit certain documents to customs. These documents typically include the commercial invoice, bill of lading or airway bill, packing list, import license (if applicable), and the CCC certificate (if required). It is important to ensure that all documents are accurately completed to avoid any delays or issues with customs clearance.
Furthermore, it is advisable to work with a reputable freight forwarder or customs broker who is knowledgeable about the import regulations and customs procedures for importing metal-cutting machines from China. They can provide guidance on the necessary steps to comply with the regulations and ensure smooth importation.
In conclusion, complying with Chinese regulations and industry standards certifications, such as the CCC mark, is essential when dealing with machines to cut metal. Importers should also familiarize themselves with the country’s import regulations and customs procedures to ensure a successful and compliant importation process.
Sustainability and Environmental Considerations in machines to cut metal Manufacturing
In the manufacturing industry, sustainability and environmental considerations are becoming increasingly important, including in machines used to cut metal. Such machines play a crucial role in metal fabrication processes, but they also have the potential to consume significant energy and produce harmful emissions. To address these concerns, manufacturers are now focusing on incorporating sustainable design principles and implementing environmentally friendly practices.
One key aspect of sustainability in metal cutting machinery is energy efficiency. By utilizing advanced technologies such as energy-efficient motors and optimizing power transmission systems, manufacturers can significantly reduce power consumption. Intelligent control systems can also be implemented to ensure machines operate at peak efficiency while minimizing idle time. Additionally, the use of regenerative braking systems can recover and reuse energy that would otherwise be wasted during deceleration, further enhancing overall energy efficiency.
In terms of emissions, measures can be taken to reduce the environmental impact of metal cutting machinery. Implementation of advanced filtration systems can effectively capture and filter out harmful particles, ensuring that emissions released into the atmosphere are minimized. Furthermore, the use of eco-friendly cutting fluids or dry cutting techniques can help reduce or eliminate the need for hazardous chemicals, thus minimizing the potential for water and soil contamination.
To promote sustainability, manufacturers are also incorporating recyclability and longevity into the design of metal cutting machines. This ensures that the materials used in machine construction can be recycled at the end of their life cycle, reducing waste and minimizing the extraction of new raw materials. Additionally, building machines with modular components allows for repair and upgrades, extending their lifespan and reducing overall resource consumption.
In conclusion, sustainability and environmental considerations are crucial aspects of modern metal cutting machinery. By prioritizing energy efficiency, emissions reduction, recyclability, and longevity, manufacturers can contribute to a more sustainable and environmentally friendly manufacturing industry. These efforts not only help preserve the planet but also support long-term cost savings and improve the overall reputation of the companies involved.
List The Evolution history of “machines to cut metal”
The evolution of machines to cut metal can be traced back to the ancient civilizations, where simple tools like chisels and saws were used. These manual tools required significant human effort and were limited in their accuracy and efficiency.
In the 18th century, the Industrial Revolution brought about significant advancements in metal cutting technology. The development of the steam engine enabled the creation of power-driven machines, such as the early lathe and milling machine. These machines revolutionized metal cutting by automating the process and improving precision.
The 19th century witnessed further advancements in metal cutting machines. The invention of the hacksaw in the 1830s allowed for more efficient cutting of metal, followed by the introduction of the bandsaw in the 1860s. These sawing machines greatly facilitated mass production and were widely adopted in industries.
The late 19th and early 20th centuries introduced several transformative machines. The introduction of the power hacksaw in the late 1800s revolutionized metal cutting, as it employed mechanical power to drive the cutting process more efficiently. Another significant innovation was the advent of the oxy-fuel cutting method around the same time, which utilized a mixture of oxygen and fuel gases to generate a high-temperature flame for metal cutting.
The mid-20th century witnessed the emergence of more sophisticated metal cutting machines. The development of the plasma cutting technique in the 1950s allowed for the efficient cutting of electrically conductive metals using ionized gas. Soon after, the laser cutting technology was invented, enabling precise and efficient metal cutting through the use of high-powered lasers.
In recent years, computer numerical control (CNC) technology has revolutionized metal cutting. CNC machines utilize computer programs to control the cutting process intricately. This advancement has led to increased automation, improved accuracy, and higher production rates.
Today, modern machines to cut metal employ various cutting techniques, including traditional sawing, abrasive cutting methods, waterjet cutting, and advanced laser and plasma cutting. Continuous technological advancements continue to enhance the efficiency and precision of metal cutting, allowing for a wide range of applications in industries such as automotive, aerospace, and manufacturing.
The Evolution and Market Trends in machines to cut metal Industry
The machine industry has witnessed significant evolution and market trends in metal cutting technology over the years. These trends have transformed the way metal components are manufactured and contributed to increased efficiency and precision in the industry.
One key development in metal cutting machines is the shift towards computer numerical control (CNC) technology. CNC machines have revolutionized metal cutting by enabling automation and reducing reliance on manual labor. These machines rely on programmed instructions to precisely cut metal components, resulting in higher accuracy and repeatability.
Another notable trend is the adoption of high-speed cutting (HSC) technology. HSC machines use advanced cutting tools and techniques to achieve faster cutting speeds without compromising accuracy. This trend has significantly reduced production time, leading to increased productivity and cost savings for manufacturers.
Integration of advanced technologies such as robotics and artificial intelligence (AI) has also impacted the metal cutting industry. Robotic arms are increasingly being used to handle and maneuver metal parts during cutting processes, enhancing efficiency and flexibility. AI algorithms are used to optimize cutting parameters, resulting in improved quality and reduced material waste.
In terms of market trends, there is a growing demand for multi-axis machines. These machines offer increased flexibility and enable complex cutting operations, making them ideal for industries such as aerospace and automotive. Additionally, there is a rising focus on sustainability and energy efficiency. Manufacturers are investing in eco-friendly machines that consume less energy, reduce emissions, and optimize material utilization.
Furthermore, the market is seeing a shift towards the use of composite materials, which require specialized cutting techniques. The metal cutting industry is adapting by developing machines capable of efficiently cutting these materials while maintaining their integrity.
In conclusion, the metal cutting industry has witnessed significant evolution and market trends driven by technological advancements. CNC technology, HSC, integration of robotics and AI, and the demand for multi-axis machines are reshaping the industry. Additionally, sustainability, energy efficiency, and the growth of composite materials are influencing the development of new cutting machines. These trends are expected to continue shaping the industry as manufacturers strive for increased productivity, precision, and cost-effectiveness.
Custom Private Labeling and Branding Opportunities with Chinese machines to cut metal Manufacturers
If you are looking for custom private labeling and branding opportunities with Chinese manufacturers specializing in machines to cut metal, you can find a range of options to suit your needs. Chinese manufacturers offer high-quality machines at competitive prices, making them an attractive choice for businesses looking to enhance their product offerings.
By partnering with Chinese manufacturers, you have the opportunity to customize and brand the machines according to your specifications. Private labeling allows you to establish your own brand identity while benefiting from the expertise and efficiency of Chinese manufacturers. This enables you to promote your products under your brand name while maintaining consistent quality and performance.
Chinese manufacturers offer a vast array of metal-cutting machines, including laser cutters, plasma cutters, waterjet cutters, and more. These machines are known for their precision, durability, and cutting-edge technology, which makes them suitable for various industries such as automotive, aerospace, construction, and manufacturing.
To proceed with private labeling and branding, Chinese manufacturers typically offer flexible options to customize the machines according to your requirements. You can incorporate your logo, colors, and other branding elements to create a unique product that aligns with your brand identity. Additionally, manufacturers can assist with packaging design and labeling to provide a cohesive and professional appearance.
By collaborating with Chinese manufacturers, you can take advantage of their extensive experience, advanced production capabilities, and cost-effective solutions. The competitive pricing allows you to remain competitive in the market, offering high-quality metal-cutting machines to your customers while maximizing profitability.
In conclusion, exploring private labeling and branding opportunities with Chinese manufacturers specializing in machines to cut metal can be a strategic move for your business. With their customizable options, you can develop a unique product under your brand name, leveraging the expertise and efficiency of Chinese manufacturers while enjoying competitive pricing.
Tips for Procurement and Considerations when Purchasing machines to cut metal
1. Determine your specific cutting needs: Before purchasing a metal cutting machine, it is crucial to understand the specific requirements of your business. Identify the types of metals you will be cutting, the thicknesses involved, and the volume of cutting required. This will help you choose a machine that can handle your workload efficiently.
2. Research different cutting technologies: There are various cutting technologies available, such as laser cutting, plasma cutting, and waterjet cutting. Each technology has its pros and cons, so it is important to research and evaluate which one suits your needs best. Consider factors like precision, speed, maintenance requirements, and operating costs.
3. Quality and durability: Look for machines from reputable manufacturers known for their quality and durability. Cutting metal can be a demanding process, so invest in a machine that can withstand heavy usage and provide consistent performance over time. Check for warranties and after-sales support to ensure peace of mind.
4. Efficiency and productivity: Consider the speed and accuracy of the machine. Look for features like automatic loading and unloading, fast cutting speeds, and minimal setup time. High precision and repeatability are also essential, as they minimize waste and improve overall productivity.
5. Safety features: Safety should be a top priority when considering metal cutting machines. Look for features like emergency stop buttons, protective enclosures, and safety interlocks to minimize the risk of accidents. Ensure that the machine complies with applicable safety standards and regulations.
6. Operating costs: Consider the overall operating costs of the machine, including energy consumption, maintenance, and consumables. Opt for energy-efficient models to reduce long-term costs. Additionally, evaluate the availability and cost of consumables such as cutting blades or gas for plasma cutting.
7. Ease of use and maintenance: Choose a machine that is user-friendly and easy to operate. Look for features like intuitive controls, clear interface, and easy maintenance procedures. Training and support from the manufacturer should also be considered to ensure proper utilization of the machine.
8. Scalability and future-proofing: Consider your future requirements and growth plans when selecting a metal cutting machine. Invest in a machine that can be upgraded or expanded to accommodate changing needs, such as increased capacity or additional cutting capabilities. This will help avoid the need for frequent machine replacements.
By considering these factors, you can make an informed decision when purchasing a metal cutting machine, ensuring that it meets your specific needs, operates efficiently, and provides a good return on investment.
FAQs on Sourcing and Manufacturing machines to cut metal in China
1. Why should I consider sourcing and manufacturing machines to cut metal in China?
Sourcing and manufacturing machines to cut metal in China offers several advantages. The country has a vast manufacturing landscape with a well-established industrial sector. China is known for its cost-effective production, which allows businesses to obtain high-quality machines at competitive prices. Additionally, China has advanced technological capabilities and a wide range of suppliers, providing options for customization and meeting specific cutting needs.
2. What types of metal cutting machines can I find in China?
China offers a wide range of metal cutting machines to suit various applications. This includes laser cutting machines, plasma cutting machines, waterjet cutting machines, and CNC milling machines, among others. These machines come in different sizes, power capacities, and cutting precision to cater to diverse industrial requirements.
3. How can I find reliable suppliers in China?
When sourcing machines to cut metal in China, it is essential to conduct thorough research to find reliable suppliers. Online platforms like Alibaba, Made-in-China, and Global Sources provide a valuable starting point to identify potential suppliers. It is crucial to evaluate their product quality, manufacturing capabilities, certifications, and customer reviews to ensure reliability. Direct communication with suppliers is also recommended to gauge their responsiveness and understanding of your specific requirements.
4. How can I ensure the quality of machines sourced from China?
To ensure the quality of machines sourced from China, it is advisable to request samples or visit the supplier’s facility for quality assessment. Additionally, requesting product certifications and ensuring compliance with international quality standards, such as ISO 9001, can help ensure the machines meet the required specifications. Conducting independent product testing or partnering with a third-party inspection agency can provide an unbiased evaluation of the machine’s quality.
5. What is the general lead time for manufacturing machines in China?
The lead time for manufacturing machines in China varies based on factors such as the complexity of the machine, customization requirements, and the supplier’s production capacity. Generally, it can range from a few weeks to a few months. It is essential to discuss the lead time with the supplier upfront and establish clear communication regarding production timelines and any potential delays.
In summary, sourcing and manufacturing machines to cut metal in China offers cost-effective options, a wide variety of machines, and advanced technological capabilities. To ensure success, thorough research and due diligence are necessary to find reliable suppliers, assess quality, and establish clear communication throughout the manufacturing process.
Why contact sourcifychina.com get free quota from reliable machines to cut metal suppliers?
Sourcifychina.com offers a free quota from reliable machines to cut metal suppliers for a few reasons. First, by providing a free quota, Sourcify China aims to attract potential customers to try out their services without any financial commitment. This allows suppliers to test the capabilities and quality of the machines before making a purchasing decision.
Another reason for offering a free quota is to showcase the reliability of the machines. By allowing suppliers to use the machines for free, Sourcify China demonstrates the efficiency and effectiveness of their equipment, ultimately building trust and confidence in their services.
Moreover, the free quota allows suppliers to experience the cost-saving benefits of using reliable machines. Metal cutting can be an expensive process, and by providing a free quota, Sourcify China enables suppliers to assess how these machines can help reduce production costs and improve overall efficiency.
Furthermore, offering a free quota also serves as a marketing strategy for Sourcify China. By providing value upfront, they are likely to generate positive word-of-mouth and attract more potential customers. It serves as a way to showcase their expertise in sourcing reliable machines and positioning themselves as a trustworthy and knowledgeable supplier in the industry.
In conclusion, Sourcifychina.com offers a free quota from reliable machines to cut metal suppliers to attract potential customers, demonstrate the reliability and cost-saving benefits of their equipment, and enhance their marketing efforts. This approach allows suppliers to test the machines and make informed decisions based on their experience, ultimately benefiting both the suppliers and Sourcify China.