Introduce about machining factory guide,Qulity,Cost,Supplier,Certification,Market,Tips,FAQ
Welcome to the Machining Factory Guide, your comprehensive resource for all things related to machining factories. In this guide, we will cover various aspects including quality, cost, suppliers, certification, market trends, tips, frequently asked questions (FAQs), and more.
Quality is of utmost importance in machining factories. From precision machining to the selection of materials, ensuring high-quality standards is crucial. This guide will provide insights on how to assess the quality of a machining factory, the importance of quality control measures, and how to choose a factory that meets your specific quality requirements.
Cost is another critical factor when it comes to machining factories. We will explore cost considerations, such as the cost of materials, labor, and machinery. Our guide will also provide tips on how to optimize costs without compromising on quality, helping you make cost-effective decisions.
Choosing the right supplier is essential for the success of your machining projects. We will discuss how to find reliable suppliers, evaluate their capabilities, and establish long-term partnerships. Additionally, we will explore different sourcing options, such as domestic and international suppliers, to help you make an informed decision.
Certification plays a significant role in ensuring quality and compliance with industry standards. This guide will delve into various certifications relevant to machining factories, such as ISO 9001, AS9100, and more. Understanding the importance of certifications and their impact on the overall supplier selection process will be covered.
Keeping up with market trends and developments is crucial to stay competitive. We will provide insights into the current market scenario, emerging technologies, and industry best practices. By staying informed about the latest trends, you can make informed decisions and stay ahead in this dynamic industry.
Furthermore, our guide will offer valuable tips on project management, order tracking, and communication with machining factories. These tips will assist you in streamlining your production processes and maximizing efficiency.
Lastly, we have compiled a list of frequently asked questions (FAQs) to address common concerns regarding machining factories. From lead times and shipping options to capabilities and customization, this section will provide answers to the most common queries.
In conclusion, the Machining Factory Guide aims to be your go-to resource for all your machining factory needs. Whether you are a seasoned industry professional or just starting, this guide will equip you with the necessary knowledge to make informed decisions about quality, cost, suppliers, certifications, market trends, and more. Stay tuned for valuable insights, tips, and FAQs to enhance your machining factory experience.
Types of machining factory
There are several types of machining factories that specialize in different types of machining processes and products. Some of the common types of machining factories are:
1. Metal machining factory: These factories specialize in machining metal components such as steel, aluminum, brass, and copper. They use various machining processes like turning, milling, drilling, and grinding to shape and finish metal parts.
2. Plastic machining factory: These factories focus on machining plastic components using processes like CNC milling, routing, turning, and drilling. They work with various types of plastics such as acrylic, polyethylene, and polycarbonate to produce parts for industries like automotive, electronics, and consumer goods.
3. Wood machining factory: These factories specialize in precision cutting, shaping, and carving of wood materials. They use processes like CNC routing, milling, and carving techniques to create components for furniture, cabinetry, flooring, and wooden crafts.
4. Precision machining factory: These factories are known for their high-precision machining capabilities, producing tight-tolerance parts for industries like aerospace, medical devices, and electronics. They utilize advanced machining techniques like multi-axis CNC milling, grinding, EDM (Electrical Discharge Machining), and laser cutting.
5. Prototype machining factory: These factories cater to the needs of product developers and designers by offering rapid prototyping services. They use CNC machining or 3D printing technologies to quickly produce prototypes for design validation and testing purposes.
6. Production machining factory: These factories focus on large-scale production of machined components, meeting the demand of various industries. They use automated machining processes and advanced technologies to achieve high-volume production efficiently.
7. Job shop machining factory: These factories offer custom machining services, taking on diverse projects and producing parts in small quantities or one-off pieces. They employ a wide range of machining techniques and equipment to fulfill the unique requirements of each project.
Each type of machining factory requires specialized knowledge, skills, and equipment to deliver high-quality machined products. By understanding the different types of machining factories available, companies can find the right manufacturer to cater to their specific machining needs.
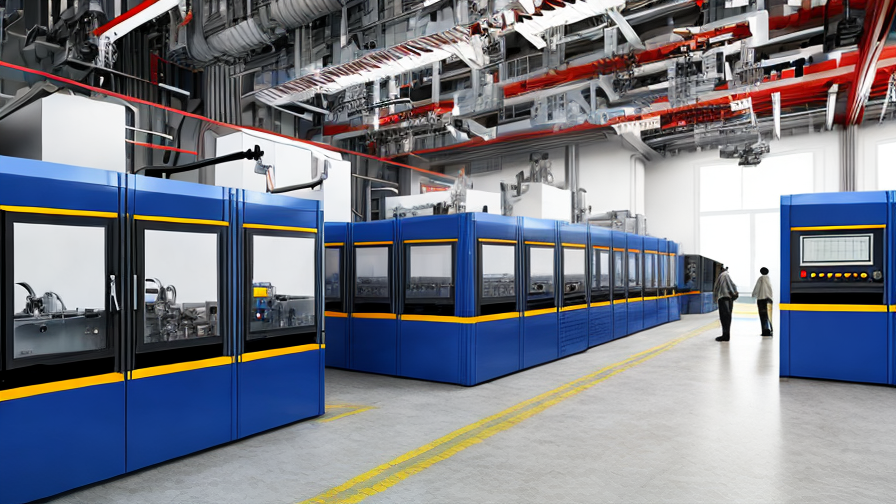
Pros and Cons of Using machining factory
There are several pros and cons to consider when using a machining factory for manufacturing purposes.
Pros:
1. Expertise and Skill: Machining factories provide access to highly skilled and experienced machinists who are well-trained in various machining techniques. They possess the knowledge and expertise required to produce high-quality and precise components.
2. Advanced Technology and Equipment: Machining factories typically invest in state-of-the-art machinery and equipment, which allows for efficient and accurate manufacturing processes. This leads to improved product quality and reduced production time.
3. Cost-effective: Outsourcing production to a machining factory can be cost-effective for businesses. Setting up an in-house machining facility can be expensive, involving significant capital investments in machinery, equipment, and skilled labor. By collaborating with a machining factory, businesses can save on these upfront costs.
4. Versatility: Machining factories often offer a wide range of machining processes such as milling, drilling, turning, and grinding. This versatility allows businesses to manufacture various types of components and adapt to changing market demands.
Cons:
1. Lack of Control: When collaborating with a machining factory, businesses may have limited control over the manufacturing process and timelines. This can be challenging, especially when deadlines are critical, or there is a need for modifications during the production phase.
2. Communication Challenges: Working with a machining factory may lead to communication issues due to the geographical distance or language barriers. Ensuring effective communication regarding specifications and design requirements is crucial to avoid misunderstandings and errors.
3. Quality Control: While machining factories strive to maintain high-quality standards, there is always a risk of variability in output quality. Businesses need to establish proper quality control measures, such as regular inspections and stringent quality assurance protocols, to minimize the risk of subpar components.
4. Intellectual Property Risks: Sharing proprietary designs and details with external machining factories may expose businesses to intellectual property risks. Careful consideration of legal agreements and non-disclosure agreements is essential to protect sensitive information.
In summary, partnering with a machining factory offers expertise, access to advanced technology, and cost savings. However, businesses need to carefully consider the potential lack of control, communication challenges, quality control risks, and intellectual property concerns when making the decision to outsource manufacturing processes.
machining factory Reference Specifications (varies for different product)
The reference specifications for a machining factory can vary depending on the specific product being manufactured. However, there are some common specifications that should be considered in order to ensure quality and efficiency in the production process.
Firstly, dimensional accuracy is a critical reference specification that needs to be maintained. This involves ensuring that the final product meets the specified dimensions and tolerances. It is essential for proper functioning and integration with other parts.
Surface finish is another important specification that should be addressed. The quality and appearance of the product’s surface can greatly impact its functionality and overall aesthetics. Different manufacturing processes and materials may require specific surface finish requirements to be met.
Material properties are also crucial to consider. The choice of material for the product should be in accordance with the required strength, hardness, heat resistance, or any other characteristic that is necessary for its application.
In terms of production rate, the machining factory should have a reference specification regarding the desired volume of products to be produced within a specific time frame. This specification helps in determining the necessary capacity and capability of the factory’s machines and workforce.
Efficiency and productivity are critical factors for any manufacturing facility. The reference specifications should include targets for cycle time, machine uptime, and overall production yield. These specifications guide the factory in achieving optimal operational performance.
Quality control measures must be specified to ensure that all products meet the required standards. This can include inspections, testing, and documentation procedures to assess and verify the product’s conformance.
Lastly, it is essential for the machining factory to have reference specifications regarding safety regulations and environmental standards. These specifications ensure that the production process is carried out in a safe and sustainable manner, protecting both the workers and the environment.
In summary, the reference specifications for a machining factory are specific to each product but generally include dimensional accuracy, surface finish, material properties, production rate, efficiency, productivity, quality control measures, safety regulations, and environmental standards.
Applications of machining factory
A machining factory is a manufacturing facility that specializes in using various machining tools and techniques to shape and fabricate metal and plastic parts. These factories have a wide range of applications across various industries, including automotive, aerospace, electronics, medical, and many others. Some common applications of a machining factory include:
1. Automotive Industry: Machining factories play a significant role in the automotive industry by producing various components such as engine blocks, cylinder heads, pistons, transmission parts, and brake components. These factories ensure the precision and accuracy required for reliable and efficient operation of vehicles.
2. Aerospace Industry: Precision machining is crucial in the aerospace industry to produce critical components such as turbine blades, aircraft engine parts, landing gear components, and control surfaces. High-quality machining processes ensure the structural integrity and safety of the aircraft.
3. Electronics Industry: A machining factory is essential in the electronics industry for producing components like heat sinks, connectors, brackets, and housings for electronic devices. These factories ensure the precise dimensions required for proper functionality and efficient thermal management.
4. Medical Industry: In the medical field, machining factories manufacture surgical instruments, implants, prosthetics, and medical device components. They ensure the highest standards of quality and precision to meet the strict safety and regulatory requirements of the industry.
5. Energy Industry: Machining factories are involved in the production of components for various energy-related applications. They manufacture parts for wind turbines, gas turbines, generators, and other energy-generation systems to ensure their optimal performance and durability.
6. Industrial Equipment: Machining factories produce components essential for industrial equipment such as pumps, valves, hydraulic cylinders, and gears. These factories ensure that the manufactured parts are reliable and can withstand harsh operating conditions.
7. Defense Industry: Machining factories play a crucial role in producing components for defense equipment, such as armored vehicles, weapons, aircraft, and naval vessels. These parts require high precision and durability to meet the demands of military operations.
Overall, machining factories are versatile and serve a wide range of industries by providing the necessary manufacturing capabilities to produce high-quality components. They ensure precision, accuracy, and adherence to specifications to meet the unique needs of each industry.
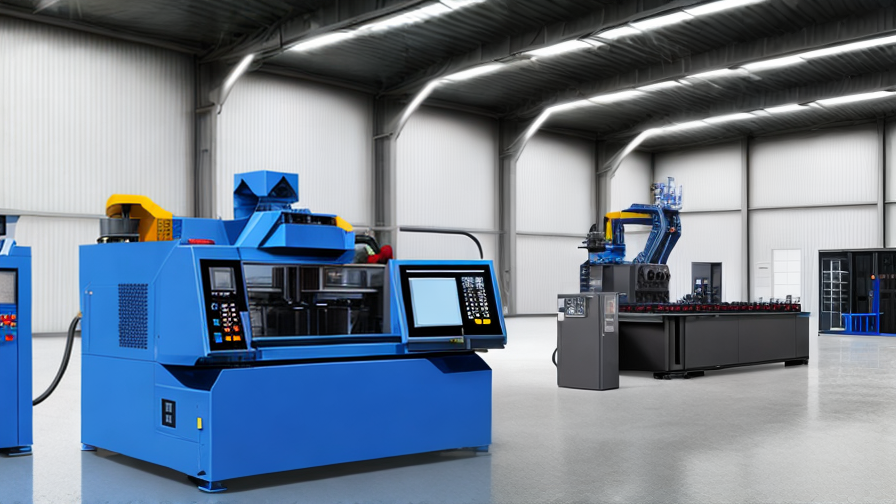
The Work Process and how to use machining factory
A machining factory is a production facility that specializes in the manufacturing of parts and components through various machining processes. The work process in a machining factory involves several steps to ensure efficient and accurate production.
First, the factory receives an order or a set of specifications from a client. These specifications outline the dimensions, material, and any additional requirements for the parts to be manufactured. The factory then evaluates the order to determine the feasibility and cost of production.
Once the order is accepted, the factory proceeds with the planning stage. This involves determining the best machining methods, tools, and equipment required for the job. The factory ensures that it has the necessary resources to complete the order, including skilled operators and suitable machines.
Next, the actual machining process begins. This typically involves operations such as milling, turning, drilling, grinding, and threading. Skilled operators use computer numerical control (CNC) machines to precisely shape and cut the material according to the specifications provided. The factory focuses on maintaining quality control throughout the production process to ensure the parts meet the required standards.
After the machining is complete, the parts undergo a series of inspections to ensure they meet the specified tolerances and quality requirements. This may involve using measuring instruments such as calipers, micrometers, and coordinate measuring machines (CMMs).
Once the parts pass the inspection phase, they undergo any necessary finishing processes, such as polishing or coating. These processes enhance the aesthetics and functionality of the parts.
Finally, the finished parts are carefully packaged and prepared for shipping to the client. The packaging is designed to protect the parts during transportation and delivery.
To effectively use a machining factory, clients should provide accurate and detailed specifications for their parts. It is important to communicate any specific requirements or expectations to ensure the parts are manufactured correctly.
Clients should also maintain open communication with the factory throughout the process. Regular updates and feedback can help address any issues or modifications needed.
In summary, a machining factory follows a structured work process from receiving the order to delivering the finished parts. By understanding this process and collaborating effectively with the factory, clients can ensure successful production outcomes.
Quality Testing Methods for machining factory and how to control the quality
Quality testing methods for a machining factory are crucial to ensure that the products meet the required standards. There are several approaches that can be employed to control the quality effectively.
Firstly, dimensional inspection is a primary method used to verify the accuracy and precision of machined parts. This involves measuring key dimensions using various instruments such as calipers, micrometers, and coordinate measuring machines. With these measurements, the parts can be compared against engineering drawings to ensure they meet the specified tolerances.
Secondly, surface inspection is essential to evaluate the finish, surface roughness, and overall appearance of the machined components. Visual and tactile inspections can be carried out to identify any defects like scratches, burrs, or uneven surfaces. Specialized instruments such as profilometers can also be used to measure the roughness of surfaces.
Further, functional testing is necessary to ensure that the machined parts perform as intended. This involves testing the parts under realistic conditions to evaluate their functionality and performance. For example, if the machined component is meant to withstand a certain load or pressure, it can be subjected to a strength test to validate its capability.
To control the quality effectively, implementing a comprehensive quality management system (QMS) is crucial. This includes developing standard operating procedures (SOPs), specifying quality requirements, and implementing robust inspection and testing protocols.
Additionally, it is vital to train and educate the workforce on quality control methods, ensuring they understand the importance of quality and how to implement it. Regular audits and inspections should be conducted to check compliance with QMS and identify areas for improvement.
Furthermore, maintaining proper documentation and traceability of the manufacturing process is essential. This allows for effective tracking of any quality issues, identifying their root causes, and implementing corrective actions.
Utilizing statistical process control (SPC) techniques can also be beneficial for quality control. SPC involves monitoring and analyzing production processes using statistical methods to identify any variations or trends that may impact quality. With SPC, proactive measures can be taken to prevent quality issues before they occur.
In conclusion, quality testing methods for a machining factory should include dimensional and surface inspections, functional testing, and the implementation of a comprehensive quality management system. By employing these methods and ensuring proper training and documentation, a machining factory can effectively control the quality of its products.
machining factory Sample Policy and Post-Purchase Considerations for machining factory from China
Sample Policy and Post-Purchase Considerations for Machining Factory from China
Sample Policy:
1. Quality Assurance: Our machining factory from China ensures strict quality control measures throughout the production process. We guarantee that all products meet international quality standards before being shipped.
2. Product Customization: We offer customization options to meet specific customer requirements. Our engineering team uses the latest technology and equipment to satisfy individual specifications.
3. Competitive Pricing: Our pricing strategy is competitive, offering value for money without compromising on quality. We strive to provide cost-effective solutions while maintaining high product standards.
4. On-Time Delivery: We understand the importance of timely delivery and ensure that orders are processed and shipped promptly. We work closely with reliable freight forwarding companies to facilitate efficient and secure transportation.
5. After-Sales Service: Our commitment does not end after the purchase. We provide comprehensive after-sales support, including technical assistance and product maintenance. We are available to address any concerns or queries promptly.
Post-Purchase Considerations:
1. Quality Inspection: Upon receiving the products from the machining factory, it is essential to conduct a thorough quality inspection to ensure they meet the expected specifications. Any discrepancies or defects should be reported to the supplier immediately.
2. Communication: Maintaining good communication with the machining factory is crucial. Openly discuss any issues, concerns, or inquiries with the supplier to ensure a smooth post-purchase experience.
3. Documentation and Warranty: Keep all relevant documentation, including invoices, shipping receipts, and warranties, in a secure place. These documents may be required for filing claims or seeking warranty support in the future.
4. Feedback and Reviews: Providing feedback or leaving reviews about the machining factory’s products and services can help other potential buyers make informed decisions. It also encourages the supplier to continually improve their offerings.
5. Long-term Relationship: Establishing a long-term relationship with the machining factory can lead to benefits such as preferential pricing, priority in production, and better customer service. Regularly evaluate the supplier’s performance and consider engaging in long-term contracts if satisfied.
By adhering to these policies and considerations, customers can ensure a positive experience with a machining factory from China, receiving high-quality products and excellent support throughout the purchase and beyond.
Sourcing machining factory from China: Opportunities, Risks, and Key Players
Sourcing machining factories from China can offer numerous opportunities for businesses. The Chinese machining industry is well-developed, offering a wide range of services, including CNC machining, precision machining, and prototyping, at competitive prices. Chinese factories are equipped with advanced machinery and technologies, ensuring high-quality products. Furthermore, the availability of skilled labor and a large number of machining factories provide businesses with ample options to choose from.
However, there are also risks associated with sourcing from China. The language and cultural barriers can pose communication challenges, leading to misunderstandings and delays in production. Intellectual property protection is another concern, as China has been known for unauthorized copying and counterfeiting. Therefore, businesses must ensure proper legal agreements and protect their intellectual property rights before engaging with Chinese machining factories.
Despite the risks, there are several key players in the Chinese machining industry that businesses can consider for sourcing. Some prominent manufacturers include Foxconn Technology Group, BYD Company Limited, and Huawei Technologies Co., Ltd. These companies have established themselves as reliable and innovative players in the industry, catering to both domestic and international markets.
To mitigate the risks and make the most of the opportunities, businesses should adopt certain strategies. Conducting thorough due diligence and background checks on potential manufacturing partners is crucial. Regular communication and maintaining a strong business relationship are essential to avoid misunderstandings and ensure smooth production processes. Additionally, implementing proper quality control measures and clearly defining product specifications can help maintain high-quality standards.
In conclusion, sourcing machining factories from China presents great opportunities for businesses, considering the industry’s capabilities and competitive prices. However, businesses must also be aware of the risks involved and take necessary precautions to protect their intellectual property and ensure smooth operations. By partnering with key players in the industry and implementing effective strategies, businesses can successfully source from Chinese machining factories.
How to find and select reliable machining factory manufacturers in China,use google search manufacturers and suppliers
When searching for reliable machining factory manufacturers in China, using Google search can be a helpful tool. Here are some steps to follow:
1. Begin by typing relevant keywords in the Google search bar, such as “reliable machining factory manufacturers in China” or “machining supplier in China.”
2. Go through the search results and browse the websites of potential manufacturers. Pay attention to their credibility, experience, and the range of services offered.
3. Look for testimonials or customer reviews on the manufacturer’s website or other platforms. This can provide insights into their reputation, customer satisfaction, and the quality of their products.
4. Check if the manufacturer has any certifications or accreditations, such as ISO 9001, which ensures adherence to quality management standards. This indicates a commitment to maintaining high-quality manufacturing processes.
5. Look for information about the company’s production capabilities, equipment, and technology. A reliable manufacturer should have modern machinery and advanced technology to ensure efficient and precise machining processes.
6. Contact the manufacturer directly through email or phone. Inquire about their production capacity, lead times, quality control measures, and any specific requirements you have. Prompt and knowledgeable responses can indicate their professionalism and willingness to cater to your needs.
7. Consider visiting trade shows or industry exhibitions in China, where you can meet manufacturers in person, check their product samples, and discuss your requirements face-to-face. This offers a better opportunity to assess their capabilities and build a direct relationship.
8. Obtain quotes from several potential manufacturers and compare them based on cost, quality, lead time, and other factors important to your project or business.
9. Consider requesting samples of their work, especially for critical or complex parts, to evaluate the manufacturer’s precision and quality firsthand.
10. Lastly, it is recommended to carry out due diligence by conducting a background check, such as verifying the manufacturer’s business license, registration, and any legal proceedings against them, if possible.
By following these steps, you can find and select a reliable machining factory manufacturer in China that best meets your requirements and expectations.
How to check machining factory manufacturers website reliable,use google chrome SEOquake check if ranking in top 10M
When evaluating the reliability of a machining factory manufacturer’s website, you can follow the steps below, making use of Google Chrome and the SEOquake extension:
1. Install SEOquake: Install the SEOquake extension on your Google Chrome browser. SEOquake provides valuable data and insights about a website’s ranking, traffic, and other important factors.
2. Google Search: Use the Google search engine to find the website of the machining factory manufacturer you want to check. Enter relevant keywords like the company name or type of products they offer.
3. Website Ranking: Once you have the search results, open the SEOquake tool by clicking on its icon in your browser’s extensions or in the menu bar. It will display information about the website that appears in the search results.
4. Check the Ranking: Look for the website’s Google PageRank or Alexa Rank. If the website is ranked within the top 10 million, it indicates a certain level of credibility and popularity. The higher the ranking, the more reliable the website is likely to be.
5. Analyze Other Metrics: SEOquake provides additional metrics such as the number of pages indexed by search engines (Google, Bing, etc.), social media metrics (Facebook likes, Twitter followers), and domain age. These metrics can give you a better understanding of the website’s authority and online presence.
6. User Experience: Navigate through the website and assess its user-friendliness, professional appearance, and the availability of essential information such as contact details, company background, product/service descriptions, and customer testimonials. A reliable manufacturer usually maintains a well-designed, informative, and user-friendly website.
7. Verification: If feasible, try to verify the website’s authenticity by cross-referencing information on trusted directories, forums, or industry-specific websites that often list reputable machining factories.
By following these steps, using SEOquake to check the ranking of the manufacturer’s website, and analyzing its credibility and overall user experience, you can make a more informed judgment about the website’s reliability. Remember, it’s crucial to exercise caution and conduct thorough research before making any business decisions with a machining factory.
Top 10 machining factory manufacturers in China with each 160 words introduce products,then use markdown create table compare
1. Haas Automation, Inc.
Haas Automation, Inc. is a renowned machining factory manufacturer in China known for its cutting-edge CNC machines. Their range of products includes vertical and horizontal machining centers, turning centers, and rotary tables. Haas machines are highly versatile, offering high-speed precision machining with excellent reliability and durability. From aerospace and automotive industries to medical and energy sectors, Haas machines cater to various applications efficiently.
2. DMG Mori
DMG Mori is a global leader in machine tools and machining systems. Their China-based factory manufactures an extensive range of products, including milling machines, lathes, machining centers, and multi-axis machines. DMG Mori machines are known for their advanced technology, delivering exceptional accuracy, productivity, and flexibility. With a focus on automation and digitization, their products excel in industries such as automotive, aircraft, and general engineering.
3. SMTCL
SMTCL is one of China’s largest machining factory manufacturers, specializing in CNC and conventional metalworking machines. Their diversified product line includes vertical and horizontal machining centers, drilling machines, lathes, and grinding machines. SMTCL focuses on delivering high-quality machines at competitive prices, making them popular among small and medium-sized enterprises worldwide. Their machines find applications in the automotive, aerospace, mold and die, and energy industries.
4. Goodway Machine Corp.
Goodway Machine Corp., based in China, offers a comprehensive range of CNC turning centers, machining centers, and Swiss-type lathes. With exceptional precision and reliability, Goodway machines serve industries like automotive, aerospace, medical, and electronics. They incorporate advanced technologies such as live tooling, Y-axis capabilities, and multi-tasking capabilities for efficient and complex machining operations.
| **Manufacturers** | **Products** | **Key Features** |
|——————–|—————|—————–|
| Haas Automation, Inc. | CNC machines, machining centers, rotary tables | Versatile, high-speed precision machining |
| DMG Mori | Milling machines, lathes, machining centers | Advanced technology, accuracy, productivity |
| SMTCL | CNC and conventional metalworking machines | Competitive pricing, diverse product line |
| Goodway Machine Corp. | CNC turning centers, machining centers, Swiss-type lathes | Precision, reliability, advanced machining capabilities |
5. Doosan Machine Tools
Doosan Machine Tools from China offers a wide range of machining solutions, including vertical and horizontal machining centers, turning centers, and multitasking machines. Known for their robustness and stability, Doosan machines deliver superior performance in industries such as automotive, mold and die, and aerospace. Their advanced features, such as automatic tool changers and high-speed spindles, enhance productivity and efficiency.
6. Yama Seiki
Yama Seiki is a prominent machining factory manufacturer in China, specializing in CNC turning centers, machining centers, and double column machining centers. Their machines offer excellent precision, high cutting power, and exceptional rigidity, making them suitable for industries like automotive, aerospace, and energy. Yama Seiki focuses on incorporating intelligent technologies to improve machining accuracy and productivity.
7. Mazak Corporation
Mazak Corporation’s China-based machining factory manufactures a wide range of advanced CNC machines, including turning centers, machining centers, and laser processing machines. Their innovative technologies, such as Smooth CNC controls and hybrid multi-tasking machines, enhance efficiency and versatility. Mazak machines find applications in industries like automotive, aerospace, and medical equipment manufacturing.
8. Makino
Makino’s China machining factory produces high-performance CNC machines like vertical and horizontal machining centers, wire EDM machines, and graphite machining centers. Known for their precision, speed, and reliability, Makino machines are widely used in industries such as mold and die, automotive, and medical equipment manufacturing. They are designed to maximize productivity and reduce machining time.
9. Okuma Corporation
Okuma Corporation, a renowned machining factory manufacturer in China, offers a diverse range of products, including CNC lathes, machining centers, and multitasking machines. Their machines feature advanced technologies like Intelligent Technology, Thermo-Friendly Concept, and Collision Avoidance System, ensuring high precision and productivity. Okuma machines cater to industries like automotive, aerospace, and industrial equipment manufacturing.
10. Starrag Group
Starrag Group’s China-based machining factory manufactures a comprehensive range of metal cutting and metal forming machinery. Their product portfolio includes milling machines, turning machines, jig boring machines, and laser machines. Starrag machines excel in terms of precision, productivity, and process reliability, making them ideal for industries like aerospace, energy, and transportation. They focus on developing innovative solutions for complex machining requirements.
In conclusion, China has a vast number of machining factory manufacturers that offer a wide range of products catering to diverse industries. Each manufacturer brings unique features and technologies to deliver precision, efficiency, and productivity in machining operations.
Background Research for machining factory manufacturers Companies in China, use qcc.com archive.org importyeti.com
When conducting background research on machining factory manufacturers in China, three valuable resources to explore are qcc.com, archive.org, and importyeti.com. These platforms provide comprehensive information on companies, historical data, and import/export records, allowing for a deeper understanding of the market and specific manufacturers.
Qcc.com is a Chinese business database that offers a vast array of company information, including registration details, financials, shareholders, and legal filings. It can provide insights into the company’s structure, size, and ownership, allowing for a more informed decision when selecting a manufacturer. Additionally, qcc.com often includes contact information and customer reviews, helping to assess the reputation and reliability of potential manufacturers.
Archive.org, on the other hand, is a digital library that allows users to access saved versions of webpages. This site can be useful in understanding the historical development of a company or tracking changes in their manufacturing processes, certifications, or partnerships over time. By reviewing past iterations of the company’s website or online presence, one can evaluate their growth trajectory and determine if their capabilities align with the desired requirements.
Importyeti.com is a platform focusing specifically on import and export data. It provides shipment records, customs data, and product details, aiding in understanding a manufacturer’s global trade activities. By analyzing the import/export records, one can assess a potential manufacturer’s capacity, volumes, and international clientele. This information can be useful for gauging their experience, expertise, and ability to meet specific quality and quantity demands.
By utilizing qcc.com, archive.org, and importyeti.com, researchers can obtain a comprehensive view of machining factory manufacturers in China. These resources allow for a detailed analysis of financials, ownership, history, capabilities, and trade activities, significantly aiding in the selection and evaluation of potential partners in the machining industry.
Leveraging Trade Shows and Expos for machining factory Sourcing in China
Trade shows and expos provide an excellent platform for businesses looking to source machining factories in China. These events bring together a wide range of reputable suppliers, creating an opportunity to connect with potential manufacturing partners efficiently and effectively. Leveraging trade shows and expos can offer several benefits:
1. Extensive Supplier Network: Trade shows and expos attract numerous suppliers specializing in machining services. This allows businesses to explore a wide range of options and find the most suitable factory for their specific requirements.
2. Face-to-Face Interaction: Unlike online sourcing platforms, trade shows and expos provide the opportunity for direct, face-to-face communication with suppliers. This enables businesses to establish a personal connection, ask questions, and assess a supplier’s capabilities and credibility.
3. Demo and Sample Evaluation: Exhibitors at trade shows often showcase their products, equipment, and services. Businesses can witness firsthand the quality of machining work, analyze the machinery used, and evaluate the overall manufacturing processes. This enables them to make informed decisions about potential suppliers.
4. Industry Insights and Trends: Trade shows and expos offer an excellent opportunity to stay updated on the latest industry trends, innovations, and technology advancements. By attending seminars, workshops, and networking events, businesses can gain valuable insights into improving their sourcing strategies and identifying potential partnerships in China.
To make the most of trade shows and expos for sourcing in China, businesses should come prepared. It is advisable to research and shortlist potential suppliers before attending the event. Setting clear objectives and establishing a plan for each meeting or visit maximizes efficiency.
In conclusion, trade shows and expos serve as a valuable platform for businesses seeking to source machining factories in China. By attending these events, companies can expand their supplier network, establish personal connections, evaluate samples and demos, and gain industry insights – all of which contribute to successful sourcing endeavors.
The Role of Agents and Sourcing Companies in Facilitating machining factory Purchases from China
Agents and sourcing companies play a crucial role in facilitating the purchase of machining factory equipment and products from China. With their extensive knowledge and experience in the Chinese market, they act as intermediaries between buyers and suppliers, offering a range of services to ensure smooth and successful transactions.
One of the main advantages of working with agents and sourcing companies is their local presence and understanding of the Chinese business culture. They have established connections and relationships with reputable machining factories in China, enabling them to identify reliable suppliers that meet the buyer’s specific requirements. These connections also provide access to a wider range of products and technologies, ensuring buyers can find the best-fit solutions for their needs.
Agents and sourcing companies also offer valuable assistance in negotiating prices and contract terms. They have a deep understanding of the local market and can leverage their industry expertise to obtain favorable pricing and conditions on behalf of the buyers. Additionally, they have a thorough understanding of the legal and regulatory frameworks in China, ensuring that contracts are in compliance with local laws and protecting the interests of the buyers.
Furthermore, agents and sourcing companies provide quality control services throughout the production process. They conduct factory audits and inspections to assess the capabilities and quality standards of the machining factories. This helps buyers ensure that their chosen supplier has the necessary infrastructure, equipment, and expertise to deliver high-quality products.
Another significant role played by agents and sourcing companies is logistics management. They are responsible for coordinating the shipping, customs clearance, and delivery of the purchased products. This alleviates the burden of logistics management from the buyers, allowing them to focus on their core business activities.
Overall, agents and sourcing companies play a vital role in facilitating machining factory purchases from China. Their local presence, industry expertise, and extensive network help buyers identify suitable suppliers, negotiate favorable terms, ensure product quality, and manage logistics. Working with these professionals can streamline the purchasing process and minimize risks, enabling buyers to access cost-effective solutions from Chinese machining factories.
Price Cost Research for machining factory manufacturers Companies in China, use temu.com and 1688.com
When it comes to finding machining factory manufacturers in China, two popular online platforms that can be utilized for price cost research are temu.com and 1688.com. These platforms offer a wide range of options for businesses looking to source their manufacturing needs from China.
Temu.com is an online marketplace that connects buyers and sellers in the mechanical industry. It enables businesses to search for specific manufacturers and obtain quotations for their machining requirements. The platform provides a direct channel for communication between buyers and manufacturers, facilitating easy discussion of pricing, terms, and technical details. Temu.com also allows users to compare prices from multiple manufacturers, ensuring that they get the best possible deal for their machining needs.
Another useful platform is 1688.com, which is part of the Alibaba Group. This website serves as a wholesale marketplace, offering a vast array of products and services directly from Chinese manufacturers. Many machining factory manufacturers can be found on 1688.com, allowing businesses to explore different options and compare prices. The platform is available in Chinese, but with the help of translation tools, non-Chinese speakers can navigate through the website and communicate with the manufacturers.
When conducting price cost research on these platforms, it is essential to keep a few key considerations in mind. Firstly, businesses should clearly define their requirements and specifications to ensure accurate quotations from the manufacturers. It is crucial to provide detailed information about the desired machining processes, materials, quantities, and any other specific requirements.
Additionally, it is advisable to reach out to multiple manufacturers to obtain competitive quotes and negotiate favorable terms. Comparing prices, quality, lead times, and other factors can help businesses make informed decisions and find the most suitable manufacturer for their needs.
In conclusion, temu.com and 1688.com are valuable online platforms for conducting price cost research when looking for machining factory manufacturers in China. With comprehensive product listings, competitive pricing, and direct communication channels, these platforms offer businesses an efficient way to source their machining requirements and secure the best possible deals.
Shipping Cost for machining factory import from China
When importing machinery from China, shipping costs can vary depending on various factors such as the size and weight of the equipment, shipping method, and destination.
There are generally two main shipping methods for importing machinery from China: air freight and sea freight. Air freight is typically faster but more expensive, while sea freight is slower but more cost-effective for larger shipments.
For smaller machines or urgent orders, air freight might be more suitable. The shipping cost is calculated based on the dimensions and weight of the package. It includes charges for customs clearance, documentation, airway fees, handling, and delivery to your destination. It is advisable to obtain quotes from different shipping companies to compare prices and services.
Sea freight is commonly used for larger machinery as it offers better economies of scale. Shipping costs for sea freight are based on the size of the cargo, measured in cubic meters (CBM) or shipping containers. Additional charges may apply, such as port fees, customs clearance, and destination handling fees.
The shipping cost can also be influenced by the Incoterm agreed upon with the supplier. The Incoterm determines who is responsible for shipping costs, insurance, and risk during transit. Commonly used Incoterms for importing machinery from China are FOB (Free on Board) or CIF (Cost, Insurance, and Freight). Under FOB, the buyer is responsible for shipping costs, while under CIF, the seller is responsible for shipping costs and insurance.
If the total shipping cost exceeds a certain threshold, additional charges such as import duties, taxes, and customs broker fees may apply. It is crucial to consider these expenses when budgeting for importing machinery.
To determine the exact shipping cost from China, it is recommended to consult with freight forwarders or shipping companies that specialize in international trade. They can provide comprehensive quotes based on your specific requirements and guide you through the import process, ensuring a smooth and cost-effective shipping experience.
Compare China and Other machining factory Markets: Products Quality and Price,Visible and Hidden Costs
China is known for its vast manufacturing capabilities, making it one of the world’s largest machining factory markets. However, there are other competing markets that also offer machining services. This comparison aims to assess the products’ quality and price, as well as the visible and hidden costs associated with each market.
In terms of product quality, China has gained a reputation for producing both high-quality and low-quality products. Chinese machining factories offer a wide range of options, allowing customers to find products that meet their specific requirements. However, quality control can be inconsistent in some cases, leading to variations in product quality. On the other hand, other machining factory markets, such as Germany, Japan, and the United States, have a strong reputation for producing high-quality products consistently. These markets often focus on precision and innovation, ensuring that their products meet strict quality standards.
When considering the price of products, China generally offers competitive pricing due to its large manufacturing scale and lower labor costs. This lower cost advantage has made China an attractive destination for businesses seeking cost-effective machining services. Other markets, especially Western countries like Germany and the United States, have higher labor costs, resulting in higher product prices. However, it is important to note that the price advantage in China can sometimes be offset by additional costs associated with product quality control, inspections, and logistics.
Visible costs, such as labor, raw materials, and transportation, vary in each market. China’s low labor costs have been a significant advantage, allowing for lower production costs. Other markets may have higher labor costs but compensate with advanced technology, skilled workforce, and better infrastructure. Regarding raw materials, China has a vast network of suppliers and resources, ensuring a steady supply chain. However, other markets may offer higher quality raw materials, but at a higher price.
Hidden costs can also significantly impact the total product cost. For instance, intellectual property rights infringement has been a concern in China, leading to potential legal and financial complications for businesses. Additionally, language barriers, cultural differences, and time zone differences can create communication challenges when working with Chinese manufacturing companies. In contrast, working with machining factories in other markets may mitigate these hidden costs due to greater legal protection, shared cultural and language understanding, and closer proximity.
In conclusion, China’s machining factory market offers competitive pricing and a wide range of products, but quality control can be a challenge. Other markets, such as Germany, Japan, and the United States, prioritize high-quality products. While China has the advantage of lower labor costs, other markets counterbalance this with advanced technology and better infrastructure. Visible costs, such as labor and raw materials, vary across markets, and hidden costs, such as legal issues and communication challenges, can impact the overall cost. Businesses should carefully consider their priorities and assess the advantages and disadvantages of each market when choosing a machining factory.
Understanding Pricing and Payment Terms for machining factory: A Comparative Guide to Get the Best Deal
When it comes to working with a machining factory, understanding pricing and payment terms is essential to getting the best deal. Here is a comparative guide to help you navigate through the process.
1. Pricing Structure: Machining factories may use different pricing structures, such as hourly rates, piece rates, or project-based pricing. It’s important to understand which pricing model applies to your project to avoid any surprises. Compare the pricing structures of multiple factories to find the most cost-effective option.
2. Material Costs: In machining, the cost of materials can significantly impact the overall price. Ask each factory about their sourcing methods and markup percentages for materials. Compare multiple suppliers to ensure you get the best deal on materials without compromising quality.
3. Volume Discounts: If your project requires a large volume of machined parts, inquire about potential volume discounts. Many factories offer reduced pricing for higher quantities. Obtain quotes from various factories to compare the discounts offered.
4. Tooling Costs: Depending on the complexity of your project, tooling costs may be involved. These costs cover the creation and maintenance of custom tools required for machining. Discuss tooling costs with each factory and compare estimates to minimize expenses.
5. Lead Time and Rush Orders: Urgent projects often incur rush order fees. Ask each factory about their lead times and associated charges for priority processing. Compare these fees to ensure a fair and reasonable cost if you have time constraints.
6. Payment Terms: Understanding payment terms is crucial to managing your budget. Inquire about payment methods, such as advance payments, progress payments, or full payment upon project completion. Consider the financial impact of different payment terms and choose the one that aligns with your cash flow.
7. Additional Fees: Machining factories may have additional fees for services like CAD/CAM programming, assembly, packaging, or shipping. Discuss these fees with various factories and compare them to find the most cost-effective solution for your project.
8. Quality Assurance: Machining factories may provide different levels of quality assurance, which can affect pricing. Compare the quality control measures of each factory to ensure you are getting the best value for your money without compromising on quality.
By comparing these factors across multiple machining factories, you can ensure that you get the best deal for your project. Invest time in requesting quotes, negotiating terms, and discussing requirements to make an informed decision that meets your budget and quality expectations.
Chinese Regulations and Industry Standards Certifications for machining factory,Import Regulations and Customs for machining factory from China
When it comes to regulations and industry standards certifications for a machining factory in China, there are several key aspects to consider. Firstly, the machining industry in China is regulated by the Chinese government through various regulatory bodies.
One important certification for machining factories in China is the ISO 9001 certification, which ensures that the factory follows a set of international standards for quality management systems. This certification is often highly regarded and required by many international customers.
Another critical certification is the China Compulsory Certification (CCC), which is a mandatory certification for certain products sold in China. While not specific to the machining industry, it is important for factories to ensure that their products adhere to this regulation if they plan to sell within the domestic market.
In addition to certifications, there are also import regulations and customs procedures for machining factories looking to import from China. It is crucial to be aware of these regulations to avoid any issues or delays in the import process.
Importers must ensure that their products meet all necessary safety and quality standards of their home countries. They may need to provide relevant documentation such as product specifications, compliance certificates, and test reports to customs authorities to demonstrate compliance.
Furthermore, importers must consider any applicable customs duties, taxes, and tariffs imposed by their home countries when importing from China. It is essential to familiarize oneself with these regulations to calculate the total import cost accurately.
In summary, ensuring compliance with industry standards certifications such as ISO 9001 and CCC is crucial for machining factories in China. Additionally, understanding import regulations and customs procedures will help facilitate the smooth import process and avoid any potential issues.
Sustainability and Environmental Considerations in machining factory Manufacturing
In recent years, sustainability and environmental considerations have become increasingly important in the manufacturing industry. Machining factories, in particular, need to address these concerns to minimize their impact on the environment and ensure long-term sustainability.
One key aspect of sustainability in machining factories is energy consumption. These facilities typically require a significant amount of energy to operate the machinery and provide lighting and heating. Implementing energy-efficient measures such as using energy-saving equipment, optimizing machine schedules, and installing LED lighting can significantly reduce energy consumption and decrease the carbon footprint of the factory.
Another important consideration is the management of waste and emissions. Machining processes generate various types of waste, including metal shavings, coolants, and chemicals. It is crucial for factories to have effective waste management systems in place, such as recycling and proper disposal methods, to minimize the impact on the environment. Additionally, the adoption of cleaner and more efficient cutting fluids and lubricants can reduce the release of harmful emissions during the machining process.
Water conservation is also a significant aspect of sustainability in machining factories. These facilities typically utilize water for cooling, cleaning, and lubrication purposes. Implementing water-saving measures like recycling water, using low-flow nozzles, and investing in water treatment technologies can help minimize water consumption and preserve this valuable resource.
Furthermore, machining factories should prioritize the use of environmentally friendly materials and processes. Choosing sustainable materials that are recyclable or biodegradable can reduce the overall environmental impact. Adopting advanced machining techniques, like high-speed machining and precision machining, can minimize material waste and improve overall production efficiency.
Lastly, integrating renewable energy sources, such as solar panels or wind turbines, into the factory’s infrastructure can help reduce the reliance on fossil fuels and further promote sustainability in machining operations.
In conclusion, sustainability and environmental considerations are crucial in machining factories. By focusing on energy consumption, waste and emissions management, water conservation, material and process selection, and renewable energy integration, these facilities can strive for long-term sustainability and minimize their impact on the environment.
List The Evolution history of “machining factory”
The evolution history of the machining factory can be traced back to ancient times when early civilizations began using rudimentary tools and techniques for shaping and manipulating materials. However, the concept of dedicated facilities solely focused on machining and production emerged during the Industrial Revolution in the 18th century.
In the early years of the Industrial Revolution, machining processes were primarily carried out by skilled craftsmen in small workshops. These workshops utilized manual tools such as drills, lathes, and milling machines to shape metals and other materials. The production output was limited, and innovation was slow due to the dependence on human labor.
As the demand for precision components and machined products increased, there was a need for larger and more efficient facilities. This led to the establishment of the first dedicated machining factories in the late 19th century. These factories saw the introduction of steam-powered machines, which significantly increased production capacity and improved the precision of machining processes.
With the advent of electricity in the early 20th century, machining factories underwent another transformation. Electric motors replaced steam-powered machines, leading to improved efficiency, faster production, and greater precision. The introduction of automated machinery, such as turret lathes and multiple-axis milling machines, further revolutionized the machining process, reducing human involvement and increasing productivity.
In the mid-20th century, the development of computer numerical control (CNC) technology brought about a significant shift in machining factories. CNC machines allowed for programmable automation, enabling precise and complex machining operations with minimal human intervention. This advancement led to mass production of standardized components and higher levels of quality control.
In recent years, machining factories have embraced advanced technologies like robotics, 3D printing, and Artificial Intelligence (AI). These technologies have further improved productivity, accuracy, and versatility in machining processes. Additionally, the integration of data-driven software solutions has enabled real-time monitoring, predictive maintenance, and optimization of production schedules in machining factories.
In conclusion, the evolution history of machining factories has witnessed a progression from manual workshops to large-scale, steam-powered facilities, and later to electrically-powered and automated factories. The advent of CNC technology and the subsequent incorporation of advanced technologies have propelled the industry forward, enabling increased efficiency, precision, and productivity.
The Evolution and Market Trends in machining factory Industry
The machining factory industry has witnessed significant evolution and market trends over the years. This industry refers to the manufacturing sector that specializes in the production of machine tools, parts, and components using various machining processes such as cutting, milling, turning, and drilling.
In terms of evolution, the machining factory industry has experienced substantial technological advancements. The introduction of computer numerical control (CNC) machines revolutionized the industry by automating various machining processes. CNC machines offer greater precision, accuracy, and speed compared to traditional manual machining techniques. Furthermore, the integration of advanced software and artificial intelligence has further enhanced the capabilities of these machines.
Another noteworthy evolution in this industry is the adoption of additive manufacturing, commonly known as 3D printing. This technology enables the production of complex parts and components using various materials such as metals, polymers, and ceramics. 3D printing provides greater design flexibility, reduced waste, and faster production times compared to traditional machining methods.
As for market trends, there has been a growing demand for customized and high-quality machining products. Industries such as aerospace, automotive, medical, and electronics require precise and customized parts that meet their specific requirements. Machining factories that can deliver such products quickly and efficiently have a competitive advantage in the market.
Additionally, there is a rising trend towards sustainable manufacturing practices in the machining factory industry. Manufacturers are increasingly focusing on reducing waste, energy consumption, and emissions in their operations. This includes implementing recycling programs, utilizing eco-friendly materials, and adopting energy-efficient technologies. Green manufacturing practices not only contribute to environmental sustainability but also help companies meet evolving regulatory standards and attract environmentally conscious customers.
Furthermore, the market trends in the machining factory industry are also influenced by globalization and outsourcing. Many companies choose to outsource their machining needs to countries with lower labor costs, such as China and India. This globalization trend has led to both opportunities and challenges for domestic machining factories. While it increases competition, it also presents opportunities for collaboration and growth through partnerships and joint ventures.
In conclusion, the machining factory industry has evolved significantly with advancements in technology, including CNC machines and 3D printing. Market trends include a rising demand for customized products, a focus on sustainable manufacturing practices, and the impact of globalization and outsourcing. Machining factories that adapt and embrace these trends are likely to maintain a competitive edge in this dynamic industry.
Custom Private Labeling and Branding Opportunities with Chinese machining factory Manufacturers
Chinese machining factory manufacturers offer custom private labeling and branding opportunities for businesses looking to establish their own unique identity in the market. With their advanced machining capabilities and expertise, they can produce high-quality products with personalized branding features.
Custom private labeling allows businesses to have their logo, name, and other branding elements printed or engraved on the products. This provides a distinctive identity, making the products easily recognizable among customers. Chinese machining factories are equipped with state-of-the-art machinery and skilled technicians who can ensure precise and accurate labeling on various materials such as metal, plastic, or wood.
Moreover, these manufacturers offer branding opportunities beyond just labeling. They can collaborate with businesses to design custom product shapes, colors, and finishes that align with their brand image and target market. This enables businesses to create unique and differentiated products, enhancing their brand positioning.
Chinese machining factories also offer custom packaging options, which play a crucial role in brand presentation. From custom-designed boxes to specialized inserts, businesses can tailor their packaging to reflect their brand identity and values. Attention to detail in packaging can greatly influence customers’ perception and enhance brand loyalty.
Partnering with Chinese machining factories for custom private labeling and branding opportunities comes with several advantages. These manufacturers often offer competitive pricing, allowing businesses to lower production costs and increase profit margins. Additionally, they have a vast production capacity, ensuring timely delivery even for large orders.
In conclusion, Chinese machining factory manufacturers provide businesses with custom private labeling and branding opportunities, allowing them to create a distinct and recognizable brand identity. With their advanced machining capabilities, custom packaging options, and competitive pricing, businesses can confidently establish their products in the market and build brand value.
Tips for Procurement and Considerations when Purchasing machining factory
When purchasing a machining factory, there are several essential considerations to ensure a successful procurement process. Here are some tips and considerations to keep in mind:
1. Identify your needs: Before starting the procurement process, clearly define your requirements and priorities. Consider factors such as the size and capacity of the machinery, the types of products you aim to manufacture, and any specific technical specifications you may require.
2. Research potential suppliers: Conduct thorough research to identify reputable suppliers with a track record of delivering quality machining equipment. Look for suppliers with extensive experience, positive customer reviews, and a strong reputation in the industry.
3. Check compliance and certifications: Ensure that the supplier and their machining factory comply with all relevant industry standards and certifications. This includes certifications for machine safety, quality management systems, and environmental management systems.
4. Evaluate the machinery’s condition: Inspect the machinery to determine its condition and any necessary repairs or upgrades. Consider factors like the age of the equipment, maintenance history, and whether spare parts are readily available in case of breakdowns.
5. Consider energy efficiency: Machining factories can consume a significant amount of energy. Therefore, evaluate the energy efficiency of the machinery being procured and consider its impact on long-term operational costs and sustainability goals.
6. Assess the supplier’s after-sales support: It is crucial to ensure that the supplier offers a comprehensive after-sales support package. Look for suppliers who provide training, maintenance services, and readily available technical support to ensure smooth operations.
7. Consider scalability: If you anticipate future growth or expansion, assess whether the machining factory can accommodate your future needs. Factors such as available floor space, capacity for additional machinery, and flexibility in production processes should be taken into account.
8. Financial considerations: Evaluate the total cost of ownership, including the machinery’s initial cost, installation charges, ongoing operational expenses, and potential financing options. Consider your budgetary constraints and explore opportunities for negotiation with the supplier.
9. Seek expert advice: If you lack expertise in machinery procurement, consider consulting professionals or industry experts who can provide guidance during the evaluation and selection process.
10. Conduct a site visit: Finally, before making a final decision, arrange a site visit to the machining factory. This will allow you to physically inspect the equipment, assess the working conditions, and engage with the supplier’s team firsthand.
By carefully considering these tips and considerations, you will be able to make an informed decision while purchasing a machining factory that aligns with your operational requirements and long-term business goals.
FAQs on Sourcing and Manufacturing machining factory in China
1. Why should I consider sourcing and manufacturing from a machining factory in China?
Sourcing and manufacturing from a machining factory in China can provide several advantages. China has a vast manufacturing industry with a well-established infrastructure, skilled workforce, and cost-effective production capabilities. The country also offers a wide range of materials and technologies for machining processes. Moreover, Chinese factories often have experience working with international clients, making them familiar with exporting and ensuring quality standards.
2. What types of machining services can I expect from a factory in China?
Machining factories in China typically offer a variety of services, including CNC machining, milling, turning, drilling, grinding, and more. They can work with materials such as metals (aluminum, stainless steel, brass, etc.), plastics, and some composites. Some factories may also provide additional services like surface finishing, heat treatment, or assembly.
3. How can I find a reliable machining factory in China?
Finding a reliable machining factory in China requires thorough research and due diligence. You can start by searching online directories, trade platforms, or industry exhibitions to identify potential factories. Verify their certifications, experience, and capabilities. Additionally, consider requesting samples, visiting the factory if possible, and contacting previous clients for feedback. Working with a trusted sourcing agent or a local manufacturing consultant can also streamline the process.
4. Are there any challenges or risks involved in sourcing and manufacturing from China?
While sourcing and manufacturing from China can be advantageous, some challenges and risks should be considered. Language and cultural differences may lead to miscommunication, so clear specifications and effective communication channels are crucial. Intellectual property protection can also be a concern, so it’s essential to establish legal agreements and protect your designs or patents accordingly. Quality control is another aspect to be cautious about, so regular inspections and quality checks are recommended.
5. How can I ensure quality control when sourcing from a China-based machining factory?
To ensure quality control, you can implement several measures. Prioritize working with factories that already have quality management systems, such as ISO certifications. Clearly define your quality requirements, specifications, and acceptance criteria in written agreements. Conduct regular inspections during production or before shipment. Utilize third-party quality inspection companies that can assess the products independently. Regularly communicate and maintain transparency with the factory to address any quality concerns promptly.
In conclusion, sourcing and manufacturing from a machining factory in China offers numerous benefits, but it is essential to conduct thorough research, due diligence, and establish clear communication and quality control measures to mitigate potential risks and ensure successful outcomes.
Why contact sourcifychina.com get free quota from reliable machining factory suppliers?
SourcifyChina.com offers free quotas from reliable machining factory suppliers for several reasons. Firstly, SourcifyChina.com aims to provide a convenient and efficient sourcing platform for businesses looking to procure machined products or parts from China. By offering free quotas, they can attract potential customers and build trust in their services.
Secondly, the free quota system helps businesses to understand the cost and feasibility of their machining projects without incurring any upfront expenses. This allows them to assess the affordability and viability of their production requirements before committing to a supplier.
Additionally, by offering free quotas from reliable machining factory suppliers, SourcifyChina.com demonstrates their commitment to quality assurance. It ensures that the suppliers they work with are reputable, capable of delivering precise machining services, and meet the necessary standards and specifications.
Furthermore, by providing a free quota, SourcifyChina.com encourages businesses to engage with their platform and build relationships with reliable suppliers. This helps streamline the sourcing process, as businesses can directly communicate with potential suppliers, discuss project details, and negotiate pricing terms.
Overall, the provision of free quotas benefits both businesses and SourcifyChina.com. Businesses can assess project requirements and connect with reliable suppliers, while SourcifyChina.com can attract potential customers, build trust, and establish themselves as a reliable sourcing platform for machining services.