Introduce about machining plastic guide,Qulity,Cost,Supplier,Certification,Market,Tips,FAQ
Machining plastic guides involve the process of shaping plastic components used as guides in various industries such as automotive, aerospace, and machinery. The quality of the final product is of utmost importance to ensure proper functioning and longevity. Precision machining techniques are employed to achieve the desired dimensions, tolerances, and surface finishes.
Cost considerations play a crucial role in the selection of plastic guide machining services. Factors such as material costs, tooling, labor, and machining time influence the overall cost. It is essential to obtain quotes from different suppliers to ensure competitive pricing while maintaining the desired level of quality.
Choosing a reliable and experienced supplier is vital for machining plastic guides. Consider factors such as their expertise in plastic machining, available technology and equipment, manufacturing capabilities, and adherence to industry standards and specifications. Supplier certifications like ISO 9001 indicate a commitment to quality and reliability.
Market demand for plastic guides is driven by various industries requiring precision components for their machinery and equipment. The automotive sector, in particular, utilizes plastic guides extensively in applications such as seat rails, door mechanisms, and engine components. The aerospace industry also employs plastic guides in aircraft interiors, control systems, and landing gear mechanisms.
Tips for machining plastic guides involve selecting the right plastic material based on its intended application and desired properties. It is essential to choose materials with excellent dimensional stability, low friction coefficient, and resistance to wear, heat, and chemicals. Proper tool selection, machining speed, and cutting parameters also contribute to achieving high-quality results and minimizing costs.
Frequently Asked Questions (FAQ) about machining plastic guides may include queries about suitable plastic materials for particular applications, available machining techniques, production capabilities, and lead times. Customers may also inquire about secondary processes such as assembly, finishing, or customizations.
In conclusion, machining plastic guides requires precision and attention to detail to ensure high-quality components. Consider factors such as quality, cost, supplier certification, and market demand, while also following tips and addressing common questions to achieve successful outcomes in plastic guide production.
Types of machining plastic
Machining plastic materials involves the process of shaping or sizing a plastic workpiece into a desired form or shape. There are several types of machining techniques used for plastics, each offering unique advantages and suitable for specific applications.
1. Turning: Turning, also known as lathing, is a subtractive machining process where a workpiece rotates while a cutting tool removes material to create a cylindrical shape. This process is ideal for producing round plastic components like cylinders, tubes, or rods.
2. Milling: Milling is a versatile machining technique that involves the use of rotary cutters to remove material from a plastic workpiece. It is utilized to create complex shapes, slots, or contours on the surface of plastic materials. CNC milling machines are commonly employed to achieve precision and accuracy.
3. Drilling: Drilling involves the use of a rotating cutting tool with two cutting edges to create cylindrical holes in plastic workpieces. It is useful for creating holes of various sizes and depths in plastics. The process can be performed manually or through the use of CNC drilling machines for higher precision.
4. Grinding: Grinding is used to produce smooth surfaces and precise dimensions on plastic workpieces. Abrasive particles are used to remove material, resulting in a fine finish. It is often employed to achieve tight tolerances and refine surfaces after other machining processes.
5. Laser Machining: Laser machining employs a focused laser beam to cut or engrave plastic materials. It offers high precision and can produce intricate designs on a wide range of plastics. Laser machining is commonly used in industries such as electronics, signage, and medical devices.
6. Waterjet Cutting: Waterjet cutting utilizes a high-pressure stream of water mixed with abrasive particles to cut through plastics. This process is particularly useful for creating intricate shapes or cutting thick plastic materials, as it does not generate heat and thus avoids material distortions or melting.
In conclusion, machining plastic can be accomplished using various techniques, including turning, milling, drilling, grinding, laser machining, and waterjet cutting. Each technique offers different advantages and is suitable for specific applications, allowing for the precise shaping and sizing of plastic materials.
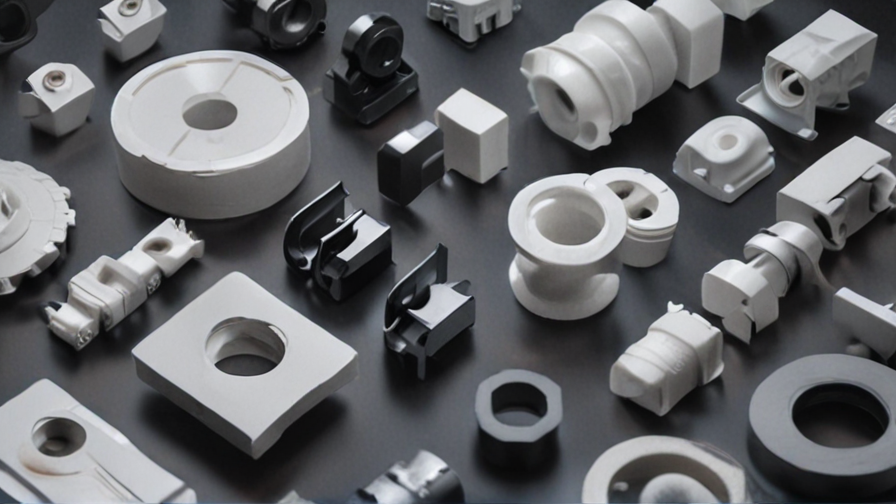
Pros and Cons of Using machining plastic
Pros of Using Machining Plastic
1. Versatility: Machining plastic offers a wide range of materials to choose from, each with its unique properties. This versatility allows for the production of intricate and complex parts, meeting the specific requirements of different industries.
2. Cost-effective: Machining plastic can be more cost-effective compared to other manufacturing methods, such as injection molding or casting. It eliminates the need for expensive molds or tooling, enabling the production of small quantities at a lower cost.
3. Lightweight: Plastic materials are generally much lighter than metals, making them ideal for applications where weight reduction is crucial. This can be beneficial in industries like aerospace, automotive, and consumer electronics, where lightweight components improve fuel efficiency, increase payload capacity, or enhance the portability of devices.
4. Resistance to corrosion: Many types of plastic have excellent resistance to corrosion and chemicals. This property makes them suitable for applications in harsh environments, such as marine, chemical processing, and oil and gas industries, as they can withstand exposure to corrosive substances without degradation.
5. Excellent electrical insulating properties: Most plastics are excellent electrical insulators, making them valuable for applications in the electrical and electronics industries. They reduce the risk of short circuits, provide insulation against electric shock, and help maintain the integrity of electronic components.
Cons of Using Machining Plastic
1. Limited heat resistance: While some plastic materials can withstand high temperatures, many others tend to have lower heat resistance compared to metals. This can restrict their use in applications requiring exposure to extreme temperatures or those involving intense friction or mechanical stress.
2. Lower strength and stiffness: In general, plastics exhibit lower strength and stiffness compared to metals. This can limit their use in applications that require high-load bearing or structural integrity. However, this limitation can often be alleviated by using reinforced plastics or composites.
3. Higher dimensional variability: Plastic materials can be prone to dimensional variation due to factors such as shrinkage, warping, and thermal expansion. This can pose challenges in achieving tight tolerances and consistency in large-scale production, necessitating careful design and quality control measures.
4. Environmental concerns: Some types of plastics can contribute to environmental pollution and waste generation, as they are not biodegradable. Proper disposal and recycling practices are essential to mitigate these concerns and promote sustainability in the use of machining plastic.
5. Machinability challenges: Certain plastics can be difficult to machine due to their low thermal conductivity and tendency to melt or chip during cutting processes. Special machining techniques, such as cooling, lubrication, or the use of specific tool geometries, may be required to overcome these challenges and ensure high-quality finished parts.
Overall, machining plastic offers numerous advantages in terms of versatility, cost-effectiveness, lightweight, corrosion resistance, and electrical insulation. However, it also presents challenges related to heat resistance, strength, dimensional variability, environmental impact, and machinability, which need to be carefully considered during the selection and design process.
machining plastic Reference Specifications (varies for different product)
When it comes to machining plastic, there are several reference specifications that vary depending on the specific product being manufactured. These specifications are crucial for ensuring the quality and precision of the plastic machining process. Here are some common reference specifications that are typically followed:
1. Material Selection: The choice of plastic material depends on various factors such as the desired mechanical properties, chemical resistance, temperature range, and electrical properties. Common plastic materials used for machining include ABS, PVC, acrylics, polyethylene, and polycarbonate.
2. Tolerances: Tolerances refer to the acceptable deviation from the specified dimensions. In plastic machining, tighter tolerances are usually achievable compared to metal machining. However, the exact tolerances can vary based on the material, part geometry, and machining process. Generally, the tolerances are specified in terms of a plus/minus value.
3. Surface Finish: The surface finish requirement depends on the intended application of the plastic part. Common surface finishes for machined plastic parts include smooth, matte, glossy, or textured finishes. The specific surface finish is important for achieving the desired appearance, functionality, and ease of cleaning.
4. Machining Processes: Various machining processes can be used for plastic, including CNC milling, turning, drilling, and sawing. The selection of the machining process depends on factors such as the part complexity, material properties, and production volume.
5. Tooling: Proper selection of cutting tools is vital to ensure the accuracy and efficiency of plastic machining. The choice of tools depends on factors like the material being machined, part geometry, surface finish requirements, and feed rates.
6. Environmental Considerations: Machining plastic can produce fumes and fine dust particles, which may need proper ventilation and filtration systems to ensure the health and safety of workers. Additionally, the recycling potential and sustainability of the plastic material should be taken into account to reduce environmental impact.
In summary, machining plastic requires adherence to reference specifications that vary depending on the specific product being manufactured. Material selection, tolerance requirements, surface finishes, machining processes, tooling, and environmental considerations are critical factors in achieving quality and precision in plastic machining processes.
Applications of machining plastic
Machining plastic offers numerous applications across various industries due to its versatility, durability, and cost-effectiveness. Some key applications include:
1. Manufacturing of Consumer Products: Plastic machining is widely used in the production of consumer products such as electronic devices, toys, household appliances, and kitchenware. It allows for precise shaping and finishing of plastic components, ensuring high-quality and functional end products.
2. Automotive Industry: Plastic machining plays a crucial role in automotive manufacturing, enabling the production of lightweight and durable components. These components include interior and exterior trim, engine parts, dashboard panels, and electrical connectors. Machining plastic allows for enhanced design flexibility, improved fuel efficiency, reduced emissions, and increased vehicle safety.
3. Medical Devices: The medical industry extensively utilizes plastic machining for the production of various medical devices and equipment. This includes surgical instruments, implants, prosthetics, laboratory equipment, and diagnostic devices. Machining plastic ensures the necessary biocompatibility, sterilizability, and dimensional accuracy required in medical applications.
4. Aerospace and Defense: Machining plastic finds applications in the aerospace and defense sectors for the production of lightweight components, instrument panels, cabin interiors, and missile guidance systems. Plastic materials with high strength-to-weight ratios, such as polycarbonates and acrylics, are machined to meet the stringent demands of the industry.
5. Electronics and Electrical: The electronics industry heavily relies on plastic machining for the production of circuit boards, connectors, enclosures, and housings. Machined plastic components provide electrical insulation, thermal management, and protection against electromagnetic interference (EMI), contributing to the efficient and reliable operation of electronic devices.
6. Packaging Industry: Plastic machining is widely employed in the packaging industry to produce customized plastic containers, caps, and closures. Machined plastic packaging offers design versatility, barrier properties, and cost-effectiveness, ensuring product safety, shelf life, and brand appeal.
7. Agricultural Equipment: Machined plastic components are utilized in agricultural machinery and equipment due to their resistance to chemicals, moisture, and UV exposure. Plastic machining enables the production of durable and lightweight parts for irrigation systems, seeders, sprayers, and animal husbandry equipment.
In conclusion, machining plastic finds extensive applications in diverse industries, ranging from consumer products, automotive, medical, aerospace, electronics, packaging, and agriculture sectors. The ability to shape, finish, and customize plastic materials allows for improved product performance, reduced weight, cost savings, and enhanced design capabilities across various applications.
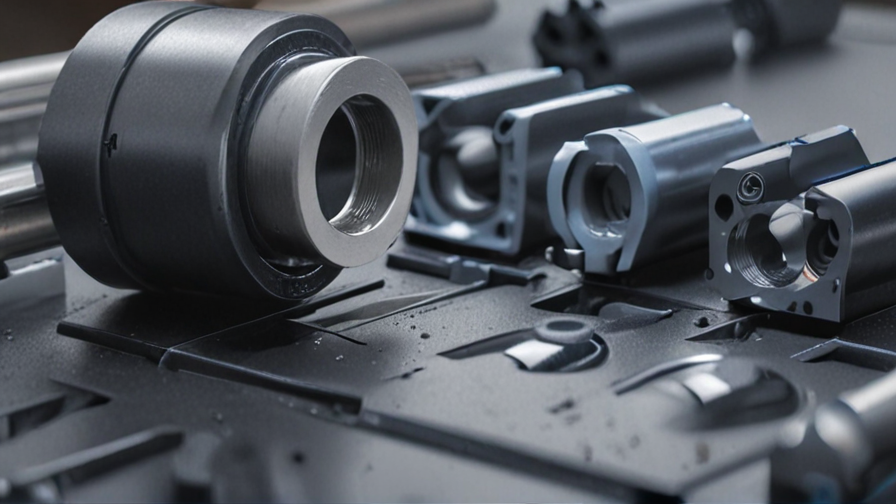
The Work Process and how to use machining plastic
The work process of machining plastic involves several steps including selecting the right material, creating a design or blueprint, setting up the machining equipment, and executing the machining operation. Machining plastic requires careful planning and attention to detail to ensure the desired results.
The first step in the work process is selecting the appropriate plastic material. There are various types of plastics available, each with different properties and characteristics. Factors such as durability, flexibility, heat resistance, and chemical resistance need to be considered when choosing the material.
Once the material is selected, a design or blueprint is created. This can be done using computer-aided design (CAD) software, which allows for precise measurements and detailed specifications. The design includes all the necessary dimensions and features required for the final product.
Next, the machining equipment is set up. This typically includes a CNC (computer numerical control) machine, which uses programmed instructions to control the movement of the machining tools. The machine is equipped with various tools such as drills, mills, and routers, which are selected based on the specific requirements of the design.
The machining operation begins by loading the plastic material onto the machine’s work table or chuck, securing it in place. The machine is then programmed with the instructions from the design to perform the necessary machining operations, such as cutting, milling, drilling, or shaping. During the process, coolant or lubrication may be used to reduce heat and improve tool performance.
Throughout the machining process, regular inspections and measurements are performed to ensure accuracy and quality. Any necessary adjustments are made to the machine or the program to maintain precision.
Finally, after the machining is completed, the plastic product is carefully removed from the machine and inspected for any defects or imperfections. Finishing processes such as sanding, polishing, or painting may be carried out to achieve the desired final appearance.
In conclusion, machining plastic involves the selection of the right material, creating a design, setting up the machining equipment, executing the machining operation, and inspecting the final product. Attention to detail and precision are crucial to ensure high-quality results.
Quality Testing Methods for machining plastic and how to control the quality
When it comes to machining plastic, it is crucial to ensure its quality through various testing methods. Here are some commonly employed techniques to control quality in plastic machining processes.
1. Visual Inspection: A basic yet essential method, visual inspection involves examining the machined parts for any visible defects such as cracks, scratches, uneven surfaces, or flash. This method helps identify obvious quality issues early in the process.
2. Dimensional Measurement: Dimensional accuracy is paramount in machining plastic components. Using precision measurement tools like calipers, micrometers, or coordinate measuring machines (CMMs), professionals can assess the dimensions of machined parts to ensure they meet the required specifications.
3. Surface Roughness Measurement: The surface finish of plastic parts significantly impacts their performance. Surface roughness measurement techniques like profilometers or surface roughness testers analyze the degree of smoothness or roughness on machined surfaces, enabling the evaluation of adherence to desired finish standards.
4. Mechanical Testing: Mechanical properties of plastic parts should be evaluated to guarantee their integrity and performance. Tensile strength, flexural strength, impact resistance, or hardness tests are commonly conducted to determine material strength and durability.
5. Chemical Resistance Testing: Plastic components may encounter various chemicals or solvents in real-world applications. Chemical resistance tests assist in assessing a plastic material’s susceptibility to degradation or corrosion when exposed to specific substances, ensuring the selected plastic is compatible with the intended environment.
6. Functionality Testing: Functionality tests simulate real-world operating conditions to evaluate the performance of machined plastic parts under stress, load, or environmental variations. Examples include endurance testing, vibration testing, or temperature cycling tests.
To control quality effectively, regular monitoring and proper documentation are essential. Implementing quality management systems, such as ISO 9001, helps in defining standardized processes, setting quality requirements, and ensuring ongoing quality control throughout the production of plastic machined parts. Communication between design engineers, machinists, and quality inspectors also plays a vital role in maintaining quality standards.
In conclusion, employing visual inspection, dimensional measurement, surface roughness testing, mechanical and chemical resistance tests, and functionality testing, along with implementing quality management systems, ensures the production of high-quality plastic machined parts.
machining plastic Sample Policy and Post-Purchase Considerations for machining plastic from China
Sample Policy:
When ordering plastic parts from China, it is recommended to request samples before proceeding with a full production run. The sample policy will ensure that the desired specifications, dimensions, and quality are met before making a bulk purchase. Typically, manufacturers offer a certain number of free samples while others may charge a nominal fee. It is important to clarify the sample policy with the supplier beforehand to avoid any confusion or unexpected expenses.
Post-Purchase Considerations:
Once the plastic parts are purchased from China, there are a few post-purchase considerations that can help ensure a smooth and successful transaction:
1. Quality Inspection: Before accepting the bulk order, conduct a thorough quality inspection of the plastic parts. Check for any defects, such as inconsistencies in dimensions, improper finishes, or color variations. Identify any issues and communicate them with the supplier immediately.
2. Communication with Supplier: Maintain open communication with the supplier throughout the production and shipping process. Address any questions or concerns promptly to avoid misunderstandings and delays.
3. Shipping and Packaging: Verify that the plastic parts are securely packaged to prevent damage during transit. Confirm that the packing meets your requirements for protection, labeling, and documentation for customs clearance.
4. Customs and Duties: Understand the customs regulations and duties applicable to importing plastic parts into your country. Ensure that all necessary paperwork, including invoices and certificates of origin, are provided by the supplier to facilitate a smooth customs process.
5. Dispute Resolution: In case of any disputes or issues, refer to the terms and conditions agreed upon in the purchase contract. Mediation, negotiation, or arbitration may be necessary to resolve conflicts.
6. Feedback and Reviews: Provide feedback to the supplier about your experience with the plastic parts and the overall transaction. Sharing your satisfaction or concerns helps both the supplier and potential buyers.
By following these guidelines, obtaining samples, and paying attention to post-purchase considerations, machining plastic parts from China can be a successful and cost-effective process.
Sourcing machining plastic from China: Opportunities, Risks, and Key Players
China has emerged as a prominent player in the global manufacturing industry, and sourcing machining plastic from China offers numerous opportunities. One key advantage is the country’s vast manufacturing infrastructure, which allows for large-scale production at competitive prices. Chinese manufacturers also possess extensive expertise in machining plastic, offering a wide range of capabilities, including CNC machining, injection molding, and 3D printing.
One significant opportunity of sourcing machining plastic from China is cost savings. Chinese manufacturers can produce plastic components at significantly lower prices compared to other regions. This cost advantage is primarily due to lower labor costs and economies of scale. Moreover, the presence of a large number of suppliers in China fosters fierce competition, driving prices down even further.
Another opportunity is the availability of a wide variety of materials and technologies for machining plastic. Chinese suppliers can offer a diverse range of plastic materials, such as ABS, PVC, polypropylene, and polycarbonate, among others. This allows buyers to find the most suitable material for their specific application needs. Additionally, Chinese manufacturers employ advanced technologies, such as CNC machining centers and injection molding machines, ensuring high precision and quality of plastic components.
However, there are certain risks associated with sourcing machining plastic from China. One major concern is the potential for product quality issues. Chinese manufacturers have been criticized for producing substandard products in the past. It is crucial for buyers to thoroughly vet potential suppliers, conduct thorough quality control inspections, and ensure compliance with international standards.
Intellectual property (IP) protection is another risk to consider. China’s record on protecting foreign companies’ IP has been a matter of concern. Unauthorized replication, counterfeiting, and infringement of patented technologies may pose challenges for companies sourcing machining plastic from China. It is advisable to work with trusted suppliers, establish clear agreements on IP protection, and explore legal avenues to safeguard one’s intellectual property.
Key players in the machining plastic industry in China include companies like Bright Plastic, ACO Mold, Shenzhen Dadesin Rapid Prototype Co., Ltd., and Junhua Prototypes. These companies have established a strong presence and enjoy a reputation for reliability, quality, and cost-effectiveness. Engaging with established players can mitigate risks and ensure a smoother sourcing process.
In conclusion, sourcing machining plastic from China holds significant opportunities, particularly in terms of cost savings and access to a wide range of materials and technologies. However, careful consideration of risks, such as product quality and IP protection, is necessary. Collaborating with reputable players in the industry can help mitigate these risks and unlock the potential benefits of sourcing from China.
How to find and select reliable machining plastic manufacturers in China,use google search manufacturers and suppliers
Finding reliable machining plastic manufacturers in China can be a daunting task, but using Google search for manufacturers and suppliers can be a helpful starting point. Here are a few steps to guide you in your search:
1. Start by typing relevant keywords into the Google search bar, such as “reliable machining plastic manufacturers in China” or “China plastic machining suppliers.” This will yield a list of potential manufacturers and suppliers.
2. Conduct a thorough review of the websites and online presence of the shortlisted companies. Look for clear and detailed information about their manufacturing capabilities, experience, certifications, and quality control processes. A reliable manufacturer will have a professional website, clearly stating their expertise and providing necessary contact information.
3. Check if the manufacturer has a physical address and visit their factory if possible. A legitimate company will have a physical presence and will be transparent about their location. This will help in verifying their operations and assessing their manufacturing capabilities.
4. Look for customer reviews and testimonials. Search for the manufacturer’s name on review websites and forums to gain insight into their reputation. Positive reviews from previous clients indicate reliability and satisfaction.
5. Assess the manufacturer’s production facilities and equipment. Look for pictures or videos on their website that showcase their machinery, infrastructure, and production lines. A well-equipped factory with modern machinery is an indication of their commitment to quality and efficiency.
6. Inquire about their quality control measures. A reliable manufacturer will have well-defined processes to ensure that products meet the required standards and specifications. Look for certifications such as ISO 9001, which demonstrates their commitment to quality management systems.
7. Contact the shortlisted manufacturers and suppliers directly. Engage in communication to discuss your specific requirements, technical details, and pricing. Ask for samples if necessary, as this allows you to evaluate the product’s quality firsthand.
8. Consider the manufacturer’s response time and communication. A reliable manufacturer should be prompt, responsive, and professional in their communication. This is an important factor in ensuring the smooth execution of your project.
By following these steps and performing due diligence, you can narrow down your search for reliable machining plastic manufacturers in China. It is crucial to thoroughly evaluate manufacturers to ensure that you select a partner that meets your quality standards, delivery timelines, and budgetary constraints.
How to check machining plastic manufacturers website reliable,use google chrome SEOquake check if ranking in top 10M
One way to check the reliability of a machining plastic manufacturer’s website is by using Google Chrome and the SEOquake tool. Here’s a step-by-step guide:
1. Install Google Chrome: If you don’t have Google Chrome already, download and install it on your computer. It is a widely-used web browser.
2. Install SEOquake: SEOquake is a browser extension that provides various SEO-related information about websites. Go to the Chrome Web Store and search for “SEOquake” to find and install the extension.
3. Go to the manufacturer’s website: Open Google Chrome and visit the website of the machining plastic manufacturer you want to evaluate.
4. Activate SEOquake: Once on the website, activate SEOquake by clicking on its icon in your browser toolbar. It usually appears as a magnifying glass or a ‘SQ’ logo.
5. Check the website ranking: The SEOquake tool will display a bar at the top of your browser window, showing essential information about the website you’re currently visiting. Look for the “Alexa Rank” or “Global Rank” section, and verify if the website ranks within the top 10 million. A higher ranking generally indicates a more reliable and established website.
6. Evaluate other factors: While the ranking is one aspect of a website’s reliability, it’s also essential to consider other factors like the website’s design, usability, content, customer reviews, and industry reputation. A reliable manufacturer’s website should have a professional design, clear product information, contact details, testimonials, and ideally certifications or affiliations related to the plastic machining industry.
Remember, checking the manufacturer’s website ranking alone is not enough to determine reliability. It should be considered alongside other elements that demonstrate professionalism, credibility, and transparency.
Top 10 machining plastic manufacturers in China with each 160 words introduce products,then use markdown create table compare
1. Shenzhen Yuda Crafts Co., Ltd. specializes in manufacturing high-quality machining plastic products. They offer a wide range of products such as plastic display stands, acrylic frames, and custom-made plastic components. With advanced CNC machining tools, they ensure precise and efficient production, providing customers with durable and intricate plastic products.
2. Dongguan City Prospertop International Co., Ltd. is a prominent manufacturer of machining plastic products in China. Their product line includes plastic injection molding, CNC machining, and vacuum forming. They offer OEM and ODM services for various industries, delivering top-quality products like plastic enclosures, automotive parts, and household appliances.
3. Topper Metal Parts Manufacturing Co., Ltd. specializes in producing precision machining plastic components. Their products range from automotive plastic parts and medical equipment components to engineering machinery accessories. With years of experience and advanced equipment, they ensure excellent quality, precise dimensions, and efficient production.
4. Dongguan Shenghua Plastic Mould Factory is a reputable manufacturer of machining plastic parts. They offer an extensive selection of plastic products, including electronic enclosures, industrial machinery parts, and consumer goods. Their efficient production processes, strict quality control, and competitive prices make them a top choice for both domestic and international clients.
5. Shine Precision Industry Co., Ltd. is a leading machining plastic manufacturer in China. They specialize in CNC machining and injection molding, producing high-quality plastic products such as automotive components, electronic devices, and medical equipment. With their advanced technology and skilled workforce, they ensure precise dimensions, excellent surface finish, and cost-effective solutions.
6. Suzhou Metal-Work Co., Ltd. is a reliable manufacturer of machining plastic parts. They utilize advanced CNC machining and injection molding techniques to produce a wide range of custom plastic components. Their products cater to various industries, including automotive, electronics, and household appliances, ensuring superior quality and timely delivery.
7. Ningbo Redsun Rapid Prototype Co., Ltd. is a leading machining plastic manufacturer in China, specializing in CNC machining and 3D printing. They offer a diverse range of plastic products like prototypes, model toys, and functional parts. With their cutting-edge technology and skilled workforce, they swiftly deliver high-quality plastic products that meet customer specifications.
8. Wuxi Glory Plastics Co., Ltd. is renowned for manufacturing machining plastic products. They focus on precision machining and injection molding, providing customers with top-quality plastic parts for automotive, electronic, and medical applications. With an emphasis on customer satisfaction, they ensure reliable production, timely delivery, and competitive pricing.
9. Hangzhou Evershining Machinery Co., Ltd. is a well-established machining plastic manufacturer in China. They specialize in CNC machining and plastic injection molding, offering a wide range of plastic components for various industries. Their extensive product line includes automotive parts, household appliances, and electrical components, all produced with high precision and durability.
10. Shenzhen Runpeng Precision Hardware Co., Ltd. is a trusted manufacturer of machining plastic products. They provide CNC machining, plastic injection molding, and vacuum casting services, offering a wide range of plastic components for different industries. Their products include electronic enclosures, consumer goods, and automotive parts, all manufactured with superior quality and competitive prices.
|Manufacturer|Products|Specialization|Industries Served|
|-|-|-|-|
|Shenzhen Yuda Crafts Co., Ltd.|Plastic display stands, acrylic frames, custom-made plastic components|High-quality machining plastic products|Retail, advertising, industrial|
|Dongguan City Prospertop International Co., Ltd.|Plastic injection molding, CNC machining, vacuum forming|OEM and ODM services|Automotive, household appliances, electronics|
|Topper Metal Parts Manufacturing Co., Ltd.|Precision machining plastic components|Automotive parts, medical equipment components, engineering machinery accessories|Automotive, medical, engineering|
|Dongguan Shenghua Plastic Mould Factory|Electronic enclosures, industrial machinery parts, consumer goods|Efficient production processes, strict quality control|Electronics, manufacturing, consumer goods|
|Shine Precision Industry Co., Ltd.|Automotive components, electronic devices, medical equipment|CNC machining, injection molding|Automotive, electronics, medical|
|Suzhou Metal-Work Co., Ltd.|Custom plastic components|CNC machining, injection molding|Automotive, electronics, household appliances|
|Ningbo Redsun Rapid Prototype Co., Ltd.|Prototypes, model toys, functional parts|CNC machining, 3D printing|Automotive, toys, manufacturing|
|Wuxi Glory Plastics Co., Ltd.|Plastic parts for automotive, electronic, and medical applications|Precision machining, injection molding|Automotive, electronics, medical|
|Hangzhou Evershining Machinery Co., Ltd.|CNC machining, plastic injection molding|Automotive parts, household appliances, electrical components|Automotive, household appliances, electronics|
|Shenzhen Runpeng Precision Hardware Co., Ltd.|Electronic enclosures, consumer goods, automotive parts|CNC machining, injection molding, vacuum casting|Electronics, consumer goods, automotive|
Background Research for machining plastic manufacturers Companies in China, use qcc.com archive.org importyeti.com
When it comes to machining plastic manufacturers in China, there are several resources available to conduct background research. Three notable platforms are qcc.com, archive.org, and importyeti.com. These platforms can be valuable tools in gathering information on companies operating in this industry in China.
Qcc.com is a Chinese business information service that allows users to access comprehensive company profiles, including registration details, financial reports, and contact information. By searching for specific keywords related to machining plastic manufacturers, users can gather information on companies’ legal status, registration details, and other relevant information.
Archive.org is a digital library that provides access to archived web pages, allowing users to view historical snapshots of websites. This can be helpful in evaluating the evolution of a company’s website, including previous products, services, and any changes made over time. Users can search for specific company websites related to machining plastic manufacturers to track their historical development.
Importyeti.com is an import-export trade database that provides information on companies’ import and export activities. This platform can offer insights into the import and export transactions of machining plastic manufacturers, including details on the type of plastic materials being imported or exported, countries of origin or destination, and trade volumes. Users can search for specific companies or products to gather useful information on the industry’s import-export dynamics.
By utilizing the above-mentioned platforms, researchers can gain insights into the background of machining plastic manufacturers in China. Qcc.com can provide detailed information on companies’ legal status and registration details, while Archive.org offers historical snapshots of company websites to track their development. Importyeti.com can provide valuable information on import and export activities, revealing industry dynamics and potential business opportunities.
In conclusion, with the help of qcc.com, archive.org, and importyeti.com, researchers can effectively gather background information on machining plastic manufacturers in China, contributing to a comprehensive understanding of the industry.
Leveraging Trade Shows and Expos for machining plastic Sourcing in China
Trade shows and expos present a golden opportunity to source machining plastic in China. By effectively leveraging these events, businesses can connect with reliable suppliers, explore the latest technologies, and gather market intelligence, all within a relatively short time frame.
To begin with, attending trade shows and expos enables businesses to establish direct contact with potential suppliers in China. These events bring together numerous manufacturers, suppliers, and industry professionals under one roof. By engaging in face-to-face interactions, businesses can build trust, evaluate suppliers in person, and negotiate favorable terms. Furthermore, developing personal relationships with suppliers helps foster long-term partnerships, leading to more efficient and reliable plastic sourcing.
Another advantage of trade shows and expos is the opportunity to explore the latest machining plastic technologies. Exhibitors often showcase cutting-edge machinery, equipment, and materials, giving businesses a firsthand experience of their capabilities. This allows buyers to assess the quality, precision, and efficiency of the machines, enabling them to make informed decisions and select the most suitable suppliers.
Furthermore, trade shows and expos provide valuable market intelligence for machining plastic sourcing in China. These events attract a wide range of industry participants, including competitors, experts, and industry associations. Attending seminars, workshops, or industry conferences held alongside the exhibitions exposes businesses to trending topics, market trends, and best practices. Such knowledge can help optimize sourcing strategies, improve competitiveness, and stay ahead of industry developments.
To make the most out of trade shows and expos, businesses should prepare adequately. They should thoroughly research and identify the trade shows and expos that are most relevant to their machining plastic sourcing needs. Understanding the exhibitor profiles, event schedules, and seminar topics in advance allows businesses to plan their visit and prioritize their objectives.
In conclusion, leveraging trade shows and expos for machining plastic sourcing in China offers significant advantages. It allows businesses to establish direct contact with suppliers, assess cutting-edge technologies, and gather market intelligence. By strategically utilizing these events, businesses can enhance their sourcing capabilities and ensure successful partnerships with Chinese suppliers.
The Role of Agents and Sourcing Companies in Facilitating machining plastic Purchases from China
Agents and sourcing companies play a crucial role in facilitating machining plastic purchases from China. These entities act as intermediaries between buyers and manufacturers, streamlining the procurement process and ensuring smooth transactions.
One of the primary functions of agents is to bridge the language and cultural gap between buyers and Chinese manufacturers. They have the necessary linguistic skills and cultural understanding to effectively communicate with suppliers, ensuring that requirements and specifications are clearly understood. By acting as translators, agents prevent miscommunication and eliminate potential misunderstandings that could lead to faulty or unsatisfactory products.
Furthermore, agents have extensive knowledge and expertise in the Chinese market. They are well-versed in local regulations, industry standards, and supplier capabilities. With this knowledge, agents can assist in identifying suitable manufacturers that specialize in machining plastic. They can conduct thorough market research to select reliable and reputable suppliers, thus mitigating the risk of dealing with fraudulent or low-quality manufacturers.
Agents also have networks and connections with a wide range of suppliers. They can leverage these relationships to negotiate favorable terms on behalf of the buyer, such as pricing, delivery schedules, and quality control measures. This enables buyers to obtain competitive prices and secure reliable sources of plastic machining services.
Sourcing companies, on the other hand, offer comprehensive sourcing solutions to buyers. They undertake the entire procurement process, from supplier selection to quality control. Sourcing companies have established relationships with multiple manufacturers, enabling them to quickly identify the most suitable supplier for a specific project. They also have a thorough understanding of each supplier’s capabilities, allowing them to match the buyer’s requirements with the appropriate manufacturer.
Moreover, sourcing companies provide quality control and inspection services to ensure that the purchased plastic machined parts meet the buyer’s specifications. They conduct regular factory audits, product inspections, and quality tests, assuring buyers that the products will be of high quality and meet their expectations.
In summary, agents and sourcing companies are essential in facilitating machining plastic purchases from China. Their expertise, market knowledge, and supplier networks enable seamless communication, supplier selection, and quality control, ultimately ensuring successful procurement for buyers.
Price Cost Research for machining plastic manufacturers Companies in China, use temu.com and 1688.com
When it comes to machining plastic manufacturers in China, two prominent online platforms to consider are temu.com and 1688.com. These websites provide a wide range of options, allowing buyers to research and compare prices from different suppliers. Conducting price cost research on these platforms is an efficient way to find the best deals within your budget.
Temu.com, often regarded as China’s leading industrial e-commerce platform, connects buyers with numerous plastic machining manufacturers. The platform offers a user-friendly interface with multiple search filters to help buyers refine their search and find the most suitable suppliers. It provides detailed product descriptions, photos, and ratings, allowing buyers to assess the quality and capabilities of different manufacturers. Temu.com also enables buyers to directly communicate with suppliers to negotiate prices, discuss specifications, and address any concerns.
1688.com is another popular e-commerce platform in China, known for its extensive range of suppliers and competitive pricing. Launched by Alibaba Group, this platform primarily serves businesses within China. However, it also provides an option for international buyers to connect with manufacturers and obtain price quotations. In terms of pricing, 1688.com often offers more cost-effective options, although navigating the website may be slightly more challenging since it is primarily in Chinese language. However, online translation tools can assist with overcoming this language barrier.
When using these platforms for price cost research, it is important to consider certain factors. Firstly, carefully review the specifications and capabilities of the manufacturers to ensure they can meet your requirements. Secondly, take note of minimum order quantities, as some suppliers may have specific requirements that impact pricing. Lastly, don’t forget to account for shipping costs, additional fees, and potential import duties when calculating the final cost.
In conclusion, temu.com and 1688.com are reliable platforms for conducting price cost research for machining plastic manufacturers in China. By utilizing the features offered by these websites, buyers can compare prices, assess supplier capabilities, and negotiate directly. Keeping in mind the mentioned factors, utilizing these platforms efficiently can help you find the best deals while ensuring the high quality of the plastic machined products.
Shipping Cost for machining plastic import from China
The shipping cost for importing plastic machined parts from China depends on various factors such as the weight and dimensions of the package, the shipping method chosen, and the distance between the origin and destination.
When it comes to shipping options, there are two main methods: air freight and sea freight. Air freight is generally faster but more expensive than sea freight. The weight and dimensions of the package will determine whether it can be shipped by air or sea.
For air freight, the cost is calculated based on the dimensional weight or actual weight, whichever is higher. Dimensional weight factors in the size of the package and is calculated by multiplying the dimensions (length x width x height) and dividing by a dimensional weight factor. It is essential to know the exact weight and dimensions of the package to get an accurate quote from a freight forwarder or shipping company.
Sea freight, on the other hand, is usually charged based on the volume of the cargo in cubic meters (CBM). The shipping cost varies depending on the shipping line and the chosen incoterm (terms of delivery). Incoterms such as EXW (Ex Works) or FOB (Free On Board) determine which party, the buyer or the seller, is responsible for the costs and risks during transportation.
To estimate the shipping cost, it is advisable to get quotes from multiple freight forwarders or shipping companies. They will require information about the weight, dimensions, and pickup/delivery locations. Additionally, they might ask for the Incoterms and any specific requirements for the packaging or handling of the goods.
While it is challenging to provide an exact shipping cost without knowing the specifics of the shipment, one can expect the cost to range from a few hundred dollars for small packages shipped via air freight to several thousand dollars for larger shipments sent via sea freight. It is recommended to work closely with a reputable freight forwarder or shipping company to get the best shipping cost and service for importing machined plastic parts from China.
Compare China and Other machining plastic Markets: Products Quality and Price,Visible and Hidden Costs
China has emerged as a dominant player in the machining plastic market globally. The country offers a wide range of plastic products, including components, prototypes, and finished goods. When comparing China to other machining plastic markets, several factors can be considered, including product quality, price, visible and hidden costs.
In terms of product quality, China has made significant strides in recent years. Many Chinese manufacturers have invested in advanced machinery and technologies to produce high-quality plastic products. However, the quality can vary across different suppliers and manufacturers. Other machining plastic markets, particularly those in developed countries, have a long-established reputation for superior product quality. These markets often adhere to strict quality standards and have better quality control measures in place.
In terms of price, China is well-known for its competitive pricing in the machining plastic market. The country’s large manufacturing base and extensive supply chain give it a cost advantage over other markets. Chinese manufacturers can leverage economies of scale to offer products at lower prices. However, lower prices might sometimes be indicative of lower quality, so it is crucial to exercise caution and conduct thorough due diligence when engaging with Chinese suppliers.
When evaluating visible and hidden costs, China may have certain advantages and disadvantages compared to other machining plastic markets. Visible costs such as labor, materials, and transportation are often lower in China due to its low-cost labor force and abundant manufacturing resources. However, hidden costs such as intellectual property risks, quality control issues, and lead time delays can potentially arise when sourcing from China. Other machining plastic markets may have higher visible costs but might offer more predictable supply chains, better protection of intellectual property rights, and reduced risks.
In conclusion, China has made substantial progress in the machining plastic market, offering competitive prices for a wide range of products. The country’s product quality has improved, although it can still vary among different manufacturers. While China has advantages in terms of visible costs, it also carries hidden costs that should be carefully evaluated. Other machining plastic markets may offer superior product quality, albeit at higher visible costs. Choosing between China and other markets ultimately depends on the specific requirements of the buyer and their risk tolerance levels.
Understanding Pricing and Payment Terms for machining plastic: A Comparative Guide to Get the Best Deal
When it comes to pricing and payment terms for machining plastic, it is essential to gather a comparative guide to ensure you get the best deal. Here are a few key points to consider within a limited word count:
1. Request Multiple Quotes: Obtain quotes from various machining plastic suppliers to compare pricing. Consider factors like the complexity of the design, material cost, machining time, and any additional services required.
2. Quantity Discounts: Inquire about quantity discounts. Often, machining plastic suppliers provide lower prices when larger quantities are ordered. Negotiate pricing based on your anticipated order volume.
3. Payment Terms: Understand the payment terms offered by different suppliers. Some may require full payment upfront, while others offer flexible options like partial payment on order placement and the remaining balance upon completion or delivery.
4. Material Cost Breakdown: Ask for a detailed breakdown of the material cost in the quote. This will help you identify if the supplier is charging reasonable prices for the plastic material required for your project.
5. Additional Costs: Inquire about any potential additional costs, such as tooling charges, setup fees, or delivery charges. These costs can significantly impact the overall pricing and should be compared across suppliers.
6. Quality Assurance: Ensure the supplier maintains high-quality standards. Cheaper prices may sometimes lead to compromised quality, resulting in subpar products. Evaluate the supplier’s reputation and inquire about their quality control processes.
7. Lead Time: Discuss the lead time required for machining plastic parts. Sometimes, suppliers charge premium prices for faster production. Compare the lead times and assess whether the cost difference justifies the urgency.
8. Warranty and Returns Policy: Understand the supplier’s warranty and returns policy in case of any manufacturing defects or product non-compliance. This will help you assess the value you are receiving for your money.
9. Payment Methods: Inquire about the payment methods accepted by the supplier. Some may only accept bank transfers, while others offer additional options like credit card payments or financing. Consider the convenience and potential transaction fees associated with each payment method.
10. Reputation and References: Research the reputation of potential suppliers, and if possible, request references. Feedback from previous clients can provide valuable insights into the supplier’s reliability, pricing, and overall service quality.
By considering these factors and comparing them across different suppliers, you can identify the best deal for machining plastic that aligns with your budget, quality requirements, and project timeline.
Chinese Regulations and Industry Standards Certifications for machining plastic,Import Regulations and Customs for machining plastic from China
China has established several regulations and industry standards certifications for machining plastic. These ensure the quality and safety of plastic products and promote the growth of the industry. Some important regulations and certifications include:
1. China Compulsory Certification (CCC): This certification is mandatory for certain products, including electrical and electronic appliances, automotive parts, and toys. It ensures that the products meet specific safety and quality standards.
2. ISO 9001: This internationally recognized certification focuses on quality management systems. It ensures that the manufacturer follows a robust quality management process, leading to consistent and reliable products.
3. ISO 14001: This certification focuses on environmental management systems. It ensures that the manufacturer follows eco-friendly practices, minimizing the negative impact on the environment.
4. GB Standards: China has established a series of national standards, known as GB standards, for various industries. These standards outline the technical specifications, performance requirements, and testing methods for specific products. For machining plastic, the relevant GB standards are GB/T 1449 for general-purpose plates and GB/T 1303 for plastic sheets.
Importing machined plastic products from China requires compliance with certain import regulations and customs procedures. These include:
1. Import Duties: Importing plastic products from China may be subject to import duties, which are determined based on the product’s classification and value. Importers should consult the local customs authorities to determine the applicable duties.
2. Documentation: Importers need to provide proper documentation, including a commercial invoice, packing list, bill of lading, and any certifications or test reports required for the specific product. These documents are necessary for customs clearance.
3. Customs Declaration: Importers must file a customs declaration with the relevant customs authorities, declaring the details of the imported plastic products, including their quantity, value, and classification.
4. Compliance with Regulations: Imported plastic products must comply with the local regulations, standards, and certifications, ensuring the safety and quality of the products. Non-compliant products may be subject to rejection or additional inspections.
It is important for importers to work with experienced customs brokers or freight forwarders who can provide guidance on complying with import regulations and customs procedures while machining plastic products from China.
Sustainability and Environmental Considerations in machining plastic Manufacturing
Sustainability and environmental considerations are increasingly important in the manufacturing industry, particularly in the machining of plastic materials. The production and use of plastic have significant environmental impact due to its high energy consumption, the depletion of non-renewable resources, and the generation of waste and pollution. Therefore, implementing sustainable practices in plastic machining is crucial to minimize these negative effects.
One approach to sustainability in plastic machining is to prioritize the use of recycled or biodegradable plastic materials. By using recycled plastics, manufacturers can reduce their consumption of virgin materials and decrease the amount of waste going to landfills. Biodegradable plastics, on the other hand, can break down naturally over time, further reducing the environmental impact.
In addition to material selection, energy efficiency measures should be implemented to minimize energy consumption during plastic machining processes. This can be achieved by optimizing machinery and equipment, improving insulation, and using energy-efficient technologies. Renewable energy sources such as solar or wind power can also be utilized to power machining operations, further reducing the carbon footprint.
Furthermore, waste reduction and proper disposal practices are integral to sustainable plastic manufacturing. Implementing waste management systems that include recycling, reusing, and proper disposal of plastic waste can significantly reduce the environmental impact of plastic machining. Manufacturers should also explore opportunities for creating closed-loop systems where waste plastic generated during machining processes is collected and recycled back into the production process.
Additionally, manufacturers can explore alternative manufacturing methods such as additive manufacturing or 3D printing, which have the potential to reduce material waste and energy consumption compared to traditional machining processes. Although these methods may not be suitable for all applications, they offer significant sustainability benefits when applicable.
To conclude, sustainability and environmental considerations in plastic machining require a multi-faceted approach. Material selection, energy efficiency, waste management, and exploring alternative manufacturing methods are key aspects to be addressed. By implementing these sustainable practices, manufacturers can contribute to a more environmentally friendly and socially responsible plastic manufacturing industry.
List The Evolution history of “machining plastic”
The history of machining plastic dates back to the early 20th century when manufacturers started using it as an alternative to metal in various industries. Initially, machining plastic involved manual processes such as sawing, drilling, and filing. However, with advancements in technology, new methods were developed to improve the efficiency and accuracy of plastic machining.
In the 1940s, the introduction of computer numerical control (CNC) revolutionized the machining industry, allowing for more precise and automated plastic machining. CNC machines could read instructions from a computer program and execute them, resulting in faster and more accurate production of plastic parts.
During the 1950s and 1960s, the development of new plastic materials such as polycarbonate and polypropylene expanded the possibilities for plastic machining. These materials offered increased strength and durability, making them suitable for a wide range of applications.
In the 1970s, the introduction of computer-aided design (CAD) and computer-aided manufacturing (CAM) further advanced plastic machining. CAD software allowed engineers to create 3D models of plastic parts, which could then be translated into instructions for CNC machines using CAM software. This integration of design and manufacturing significantly improved the efficiency and precision of plastic machining.
The 1990s saw the emergence of rapid prototyping technologies, such as 3D printing, which revolutionized the manufacturing industry, including plastic machining. 3D printing enabled the creation of complex plastic parts directly from digital designs, eliminating the need for traditional machining processes in certain cases.
Today, plastic machining continues to evolve with the development of new technologies and materials. High-speed machining techniques, such as milling and turning, are widely used to achieve even greater precision and efficiency. Additionally, advancements in plastics engineering have led to the manufacturing of specialized plastics with enhanced properties, such as high heat resistance or electrical insulation, further expanding the possibilities for plastic machining.
In conclusion, the evolution of plastic machining has been driven by technological advancements, from manual processes to CNC machining, CAD/CAM integration, rapid prototyping, and high-speed machining. This continuous innovation has significantly improved the efficiency, accuracy, and versatility of plastic machining, making it an essential process in various industries.
The Evolution and Market Trends in machining plastic Industry
The plastic machining industry has gone through significant evolution and witnessed various market trends over the years. Initially, plastic machining involved simple processes such as cutting and shaping materials using conventional tools. However, advancements in technology and the growing demand for complex plastic components have led to the adoption of more sophisticated machining techniques.
One major trend in the plastic machining industry is the shift towards computer numerical control (CNC) machining. CNC machines allow for precise and accurate plastic machining by using computer software to control the cutting tools. This technology has improved efficiency and reduced human error, resulting in faster production times and higher quality products. Additionally, CNC machines can handle complex shapes and designs, providing greater versatility to meet diverse customer demands.
Another market trend is the increasing demand for customized plastic components. With advancements in CAD/CAM software, plastic machining companies can now easily create prototypes and produce customized parts according to specific customer requirements. This trend has been fueled by the need for unique products in industries such as automotive, aerospace, and medical devices. Companies offering customized plastic machining services have gained a competitive advantage by catering to this growing market segment.
Furthermore, there has been a growing emphasis on sustainability within the plastic machining industry. With increasing environmental concerns, manufacturers are exploring eco-friendly alternatives to traditional plastics. Biodegradable and bio-based plastics have gained popularity, and the machining industry is adapting to accommodate these materials. This trend aligns with the broader shift towards sustainable production practices and the circular economy.
Additionally, the expansion of additive manufacturing, such as 3D printing, has had an impact on the plastic machining industry. While additive manufacturing enables the production of complex plastic parts with minimal material waste, certain applications still require the precision and strength that only machining can provide. The synergy between additive manufacturing and plastic machining has resulted in hybrid manufacturing processes, combining the advantages of both methods.
In conclusion, the plastic machining industry has undergone significant changes and continues to evolve. The adoption of CNC machining, customization of plastic components, focus on sustainability, and synergy with additive manufacturing are some of the major trends shaping the industry. Companies that adapt to these trends and invest in advanced technologies will be well-positioned to thrive in this competitive market.
Custom Private Labeling and Branding Opportunities with Chinese machining plastic Manufacturers
There are numerous opportunities for custom private labeling and branding with Chinese machining plastic manufacturers. China is one of the largest manufacturing hubs in the world and offers a wide range of capabilities in plastic machining.
By partnering with Chinese manufacturers, businesses can take advantage of their expertise in producing high-quality plastic products. These manufacturers have state-of-the-art facilities and advanced technology that can handle complex machining processes, ensuring precision and accuracy in every product.
The private labeling and branding opportunities in China are especially appealing due to their low labor costs and competitive pricing. Businesses can save on production costs, allowing for higher profit margins or reduced prices for customers. This affordability factor, coupled with the ability to customize products, allows businesses to cater to specific market demands and differentiate themselves from competitors.
Chinese manufacturers also offer flexible production quantities, making it feasible for businesses of all sizes to capitalize on these opportunities. Whether it’s a small order or large scale production, manufacturers can accommodate the needs of each business.
Furthermore, Chinese manufacturers understand the importance of branding and aesthetics. They can provide customized packaging options and help businesses create a unique brand identity. Custom private labeling ensures that products represent the business’s brand image and resonate with their target audience.
However, when considering partnering with Chinese manufacturers, businesses should undertake due diligence to ensure reliable and trustworthy suppliers. Conducting thorough research, reading reviews, and visiting manufacturing facilities can help businesses find reputable manufacturers and build strong business relationships.
In conclusion, the custom private labeling and branding opportunities with Chinese machining plastic manufacturers are vast and promising. Businesses can benefit from their expertise, competitive pricing, flexibility, and customization options. With careful selection of manufacturing partners, businesses can establish their brand presence and expand their market reach efficiently.
Tips for Procurement and Considerations when Purchasing machining plastic
When it comes to procurement and purchasing machining plastic, there are several considerations to keep in mind. Here are some important tips to help you make the right decisions:
1. Identify Your Requirements: Determine the specific properties and characteristics you require in the plastic material. Consider factors such as strength, heat resistance, chemical resistance, dimensional stability, and electrical conductivity.
2. Material Selection: Choose the most suitable plastic material for your project based on its properties. Common options include acetal, nylon, polycarbonate, PVC, and acrylic. Each material has its own strengths and weaknesses, so choose carefully.
3. Quality Assurance: Ensure that the supplier provides a certificate of conformance or a material data sheet with each delivery. This will help you verify the material’s quality, consistency, and compliance with your requirements.
4. Price and Lead Time: Compare prices from different suppliers to ensure you are getting the best value for your money. Also, consider the supplier’s lead time and their ability to meet your production schedule.
5. Minimum Order Quantity: Ask the supplier about their minimum order quantity (MOQ). This is important, especially if you have specific quantity requirements for your project. Some suppliers may have high MOQs, which can affect your purchasing decision.
6. Material Machinability: Consider the machinability of the plastic material you plan to purchase. Some plastics may be more difficult to machine than others, which can affect your production process and costs.
7. Technical Support: Choose a supplier who can provide technical support and guidance throughout the procurement process. They should be able to answer any questions you have and offer recommendations based on your specific project requirements.
8. Sustainability: Consider the environmental impact of the plastic material you are purchasing. Look for suppliers who offer sustainable or recycled plastic options that align with your organization’s environmental goals.
9. Delivery and Packaging: Discuss delivery options and packaging requirements with the supplier. Ensure that the material will be delivered securely and packaged appropriately to avoid any damage during transit.
10. Supplier Reputation: Research the supplier to ensure they have a good reputation in the industry. Look for reviews or testimonials from other customers to gain insight into their reliability, customer service, and product quality.
By considering these tips and taking into account your specific project requirements, you can make informed decisions when purchasing machining plastic.
FAQs on Sourcing and Manufacturing machining plastic in China
1. Can I trust the quality of machining plastic products from China?
China has a diverse range of manufacturers, and while some may deliver high-quality products, others may not meet international standards. It is crucial to conduct thorough research and due diligence before choosing the right supplier. Requesting samples, checking certifications, and reading customer reviews can help ensure the trustworthiness and quality of the manufacturer.
2. How can I find reliable suppliers for machining plastic in China?
Several methods can be employed to find reliable suppliers in China. Online resources such as Alibaba, Made in China, and Global Sources can help you research and connect with potential suppliers. Visiting trade shows, such as the Canton Fair, is another effective way to meet manufacturers face-to-face and assess their capabilities. Engaging with sourcing agents or hiring third-party inspection services can also provide an added layer of assurance.
3. What are the typical lead times for machining plastic parts in China?
Lead times for machining plastic parts can vary depending on the complexity of the project, quantity, and the manufacturer’s production capacity. On average, lead times range from 4-8 weeks. However, it is essential to communicate your desired delivery date with the supplier to ensure it aligns with their production schedule.
4. What are the costs associated with sourcing and manufacturing machining plastic in China?
China offers competitive pricing for machining plastic products due to its well-developed supply chain and lower labor costs. However, it is important to consider additional costs such as shipping, import duties, and potential quality control inspections. Engaging in price negotiations, comparing multiple suppliers, and considering all associated costs will help determine the best overall value.
5. How can I minimize potential risks when sourcing and manufacturing in China?
To minimize risks, working with an experienced sourcing agent or consultant who understands the Chinese market can be highly beneficial. Properly documenting and clearly communicating your requirements and specifications will help avoid misconceptions or misunderstandings. Conducting factory inspections, implementing quality control measures, and drafting clear contractual agreements with penalty clauses for non-compliance can further mitigate risks.
6. Are there any regulations or certifications that should be considered when sourcing machining plastic from China?
Yes, certain regulations and certifications should be considered, depending on the industry and application of the plastic products. Examples include ISO 9001 for quality management systems, ISO 14001 for environmental management, and RoHS compliance for products that do not contain hazardous substances. It is advisable to communicate your specific requirements with the supplier and confirm their ability to adhere to relevant regulations and obtain necessary certifications.
Overall, sourcing and manufacturing machining plastic in China can offer cost-effective solutions, but careful research, due diligence, and effective communication with potential suppliers are crucial to ensure quality and mitigate risks.
Why contact sourcifychina.com get free quota from reliable machining plastic suppliers?
Sourcifychina.com provides free quota from reliable machining plastic suppliers for several reasons. Firstly, offering a free quota helps in attracting potential customers and building trust. When potential buyers can receive a quotation without any upfront fees or commitments, they are more likely to engage with the platform and consider using its services.
Secondly, by connecting customers with reliable machining plastic suppliers, Sourcifychina.com aims to simplify the sourcing process. Sourcing plastic parts can be a complex task, especially for businesses unfamiliar with the Chinese market. By partnering with reliable suppliers, Sourcifychina.com ensures that customers receive high-quality products and a hassle-free experience.
Additionally, providing a free quota allows Sourcifychina.com to understand the customer’s requirements better. By gathering details like design specifications, quantities, and delivery timelines through the quotation process, the platform can assist customers more effectively. This information helps in matching customers with suitable suppliers, ensuring a tailored and efficient sourcing experience.
Furthermore, offering a free quota allows Sourcifychina.com to showcase its expertise and knowledge in the field of machining plastic sourcing. By providing accurate and competitive quotations, the platform demonstrates its ability to navigate the complexities of the Chinese market and negotiate fair prices on behalf of its customers.
In conclusion, Sourcifychina.com provides a free quota from reliable machining plastic suppliers to attract and gain the trust of potential customers, simplify the sourcing process, understand customer requirements, showcase expertise, and ensure a tailored and efficient sourcing experience.