Introduce about metal sheet bending guide,Qulity,Cost,Supplier,Certification,Market,Tips,FAQ
Metal sheet bending is a widely used technique in the manufacturing industry for various applications. This guide will provide an overview of the process, key considerations, and tips to ensure quality results while minimizing costs.
Quality is a crucial aspect of metal sheet bending. It is essential to ensure precise and accurate bending angles to meet specific design requirements. High-quality equipment, such as hydraulic or mechanical presses, should be used to achieve consistent and reliable results. Additionally, employing skilled operators with experience in metal sheet bending can significantly contribute to the overall quality of the bent sheet.
Cost considerations play a vital role in metal sheet bending. Factors such as material type, thickness, and complexity of the bend determine the overall cost. Selecting the most suitable bending method, such as air bending, bottoming, or coining, can help minimize costs. Efficient material utilization and optimized tooling design are also crucial to reduce waste and keep costs under control.
Choosing a reliable supplier is essential to ensure a steady supply of high-quality metal sheets. Suppliers with a proven track record in the industry and a wide range of material options are preferable. It is advisable to evaluate their production capabilities, quality control processes, and delivery timelines to make an informed decision.
Certification, such as ISO 9001, is an important consideration when selecting a metal sheet bending supplier. Certification indicates that the supplier adheres to international standards for quality management, ensuring consistent and reliable products.
The market for metal sheet bending is vast and diverse, spanning industries like automotive, aerospace, construction, and more. Understanding specific market requirements and tailoring the bending process accordingly can help businesses cater to unique demands effectively.
To ensure successful metal sheet bending, here are some valuable tips:
1. Accurate measurement and marking are crucial before bending.
2. Proper tool selection, including punches and dies, should match material thickness and bend radius.
3. Applying lubricants can improve the bending process and enhance the surface finish.
4. Regular maintenance of bending equipment is essential to ensure consistent performance and prevent unnecessary downtime.
Frequently Asked Questions (FAQ):
1. What are the common materials used for metal sheet bending?
Stainless steel, aluminum, carbon steel, and galvanized steel are frequently used materials.
2. What is the maximum thickness that can be bent using metal sheet bending techniques?
The maximum thickness depends on the bending method and equipment used. Hydraulic presses can typically handle thicker materials compared to manual presses.
In summary, metal sheet bending is a critical process in numerous industries. By considering factors such as quality, cost, supplier selection, certification, and market requirements, businesses can excel in this field. Adhering to the mentioned tips and addressing common FAQs allows for successful metal sheet bending operations.
Types of metal sheet bending
Metal sheet bending is a process used to reshape a metal sheet into the desired shape or form. There are several types of metal sheet bending methods, each suitable for different applications and shapes. Some common types include:
1. V-bending: V-bending involves clamping the metal sheet between a punch and a die to create a V-shaped bend. This method is commonly used for creating sharp corners in sheet metal components.
2. U-bending: U-bending, also known as bottom bending, is utilized to create a U-shaped bend in the metal sheet. It involves clamping the metal sheet between a punch and a die, forming a smooth curve.
3. Edge bending: In edge bending, the metal sheet is bent along the edge, resulting in a straight bend. This method is often used to create flanges or lips on sheet metal components.
4. Coining: Coining is a precise method used to create small, tight-radius bends in metal sheets. It involves pressing the metal sheet into a specially designed die to create the desired shape.
5. Air bending: Air bending is a versatile method that uses a punch to push the metal sheet into a V-shaped die, creating a bend. This method allows for flexibility in choosing the desired bend angle.
6. Rotary bending: Rotary bending involves using a roller or a die that rotates while pressing against the metal sheet. This method is suitable for creating large, rounded bends and can be performed using manual or automated equipment.
7. Roll bending: Roll bending utilizes rollers to gradually bend the metal sheet into a curved shape. This method is commonly employed for creating cylindrical or conical shapes.
8. Elastic bending: Elastic bending involves bending the metal sheet beyond its elastic limit, causing it to permanently retain the desired shape. This method is suitable for creating complex curved shapes.
It is important to choose the appropriate bending method based on factors such as desired shape, material thickness, desired bend angle, and production volume. Each method has its advantages and limitations, and the selection depends on the specific requirements of the project.
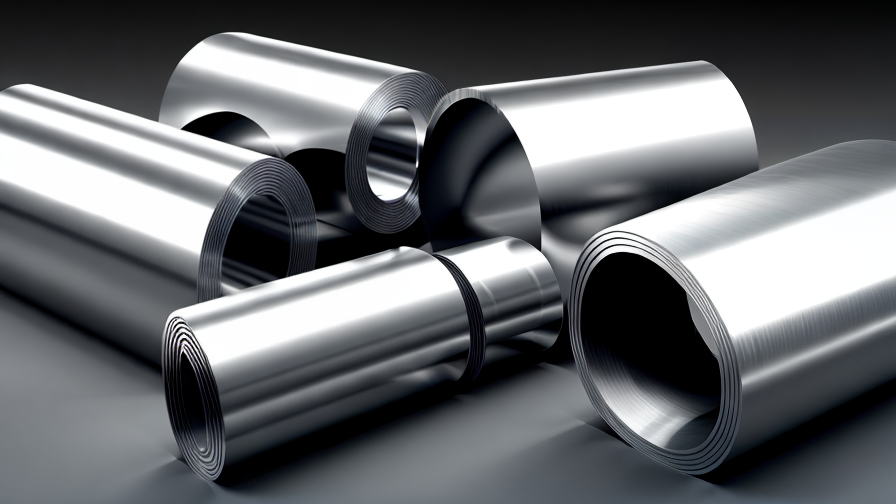
Pros and Cons of Using metal sheet bending
Metal sheet bending is a commonly used technique in various industries such as automotive, aerospace, construction, and manufacturing. It involves shaping metal sheets into different forms through the application of force. Here are some pros and cons of using metal sheet bending:
Pros:
1. Versatility: Metal sheet bending allows for a wide range of shapes and designs to be achieved, offering manufacturers considerable flexibility in product development.
2. Strength and durability: The bending process increases the overall strength and rigidity of the metal sheet, making it suitable for applications that require load-bearing capacity and longevity.
3. Cost-effective: Compared to other metal forming techniques like casting or forging, sheet bending tends to be a more affordable option, making it suitable for mass production.
4. Material suitability: Metal sheet bending can be applied to a variety of materials, including aluminum, steel, stainless steel, and copper, providing manufacturers with material options based on their specific needs.
5. Time efficiency: With modern machinery and automation, the bending process can be completed quickly, reducing production time and increasing overall efficiency.
Cons:
1. Complexity: Metal sheet bending requires skilled technicians who possess knowledge of various bending techniques and the ability to interpret technical drawings accurately. This complexity can increase production costs.
2. Material limitations: While sheet bending is applicable to a variety of materials, certain metals may be prone to cracking or tearing during the bending process. This limitation necessitates careful material selection and potential additional steps like annealing.
3. Tooling costs: The setup and maintenance of bending machinery, including the production of unique bending dies, can be expensive, particularly for small-scale production runs.
4. Precision challenges: Achieving tight tolerances and consistent bending angles may pose challenges, especially when dealing with thin or fragile materials. These challenges can impact the overall quality of the final product.
5. Design limitations: The bending process may impose constraints on product design, particularly for intricate shapes or designs that require multiple bends. Complex designs may require secondary operations or alternative forming techniques.
Overall, metal sheet bending offers numerous advantages such as versatility in shape, strength, cost-effectiveness, and material suitability. However, it also presents challenges in terms of complexity, material limitations, tooling costs, precision, and design restrictions. By considering these pros and cons, manufacturers can make informed decisions regarding the suitability of metal sheet bending for their specific applications.
metal sheet bending Reference Specifications (varies for different product)
Metal sheet bending is a common manufacturing process used to create various products and components in industries such as automotive, aerospace, construction, and more. It involves deforming a piece of metal sheet to form specific angles or shapes by applying force.
To ensure accurate and consistent results, manufacturers often refer to reference specifications that outline the requirements for the bending process. These specifications may vary depending on the specific product being manufactured. Some key reference specifications include:
1. Bend Angle Tolerance: This specification establishes the acceptable range of deviation from the desired bend angle. It ensures that the bent component meets the necessary dimensional requirements.
2. Bend Radius: This specification determines the minimum radius that can be achieved without causing material deformation, cracking, or wrinkling. It depends on the material type, thickness, and the specific bending process used.
3. Springback: Springback refers to the elastic recovery of the metal sheet after bending. Reference specifications provide guidelines to compensate for this springback effect so that the final bent component matches the intended dimensions.
4. Material Allowances: These specifications define the amount of material required for bending, including excess material needed to compensate for elongation or thinning during the process. They ensure that the final bent component meets the required dimensional and structural integrity standards.
Moreover, reference specifications address other important factors such as the type of tooling required, bending sequence, measurement techniques, and tolerances for surface finish.
Manufacturers aim to use these specifications to achieve consistent and repeatable bending results. Advanced bending techniques, such as CNC (Computer Numerical Control) bending, use computer-generated programs that follow these reference specifications precisely, ensuring high accuracy and minimizing human error.
Overall, reference specifications play a vital role in metal sheet bending operations, providing manufacturers with a standardized framework to achieve desired product outcomes. By adhering to these specifications, manufacturers can produce high-quality bent components that meet dimensional, structural, and aesthetic requirements.
Applications of metal sheet bending
Metal sheet bending is a versatile process that finds wide applications in various industries and manufacturing processes. Here are some key areas where metal sheet bending is commonly utilized:
1. Automotive Industry: Metal sheet bending is extensively employed in the automotive sector for manufacturing the body panels of cars and other vehicles. It allows for the creation of complex shapes and curves required to meet the aerodynamic and structural requirements of modern vehicles.
2. Aerospace Industry: Metal sheet bending is crucial in the aerospace industry for fabricating aircraft components such as wing sections, fuselages, and engine enclosures. The process enables the production of lightweight yet durable parts to withstand the rigorous conditions experienced during flight.
3. Construction Sector: In the construction industry, metal sheet bending is used to create architectural elements like window frames, roofing, and facade systems. It provides the ability to achieve different geometrical shapes, enabling the creation of aesthetically appealing and functional structures.
4. Industrial Machinery: Metal sheet bending plays a vital role in the manufacturing of industrial machinery across various sectors. It allows for the production of customized equipment components, such as brackets, enclosures, and chassis, ensuring proper fit, strength, and functionality.
5. Furniture Manufacturing: Metal sheet bending is widely employed in the furniture industry to create intricate designs, stylish curves, and smooth finishes for items like chairs, tables, and cabinets. It enables manufacturers to produce aesthetically pleasing and durable furniture pieces.
6. Electronics and Electrical Sector: Metal sheet bending is used to fabricate enclosures, casings, and brackets for electronic devices and electrical equipment. This process ensures proper protection for sensitive components, efficient heat dissipation, and easy integration of various parts.
7. Household Appliances: Home appliances like refrigerators, ovens, and washing machines often require metal sheet bending for creating outer panels, inner components, or structural elements. This process enhances both the appearance and functionality of these appliances.
8. Medical Equipment: Metal sheet bending finds its application in the medical sector for manufacturing equipment such as hospital beds, surgical tables, and diagnostic devices. The process enables the creation of ergonomic designs, ensuring comfort and functionality for patients and medical staff.
9. Energy Sector: Metal sheet bending is utilized in the energy industry for manufacturing components of renewable energy systems, such as wind turbines and solar panels. It enables the creation of intricate shapes that maximize energy capture and improve overall efficiency.
10. Jewelry and Artwork: Metal sheet bending is also employed in the creation of intricate jewelry designs and artistic sculptures. It allows artists and jewelers to bring their visions to life by forming and shaping the metal sheets into unique and appealing forms.
Overall, metal sheet bending is a fundamental manufacturing process that finds extensive applications across various industries, ranging from automotive and aerospace to construction, furniture, electronics, healthcare, and more. Its versatility and ability to create complex shapes and designs make it indispensable for many manufacturing sectors.
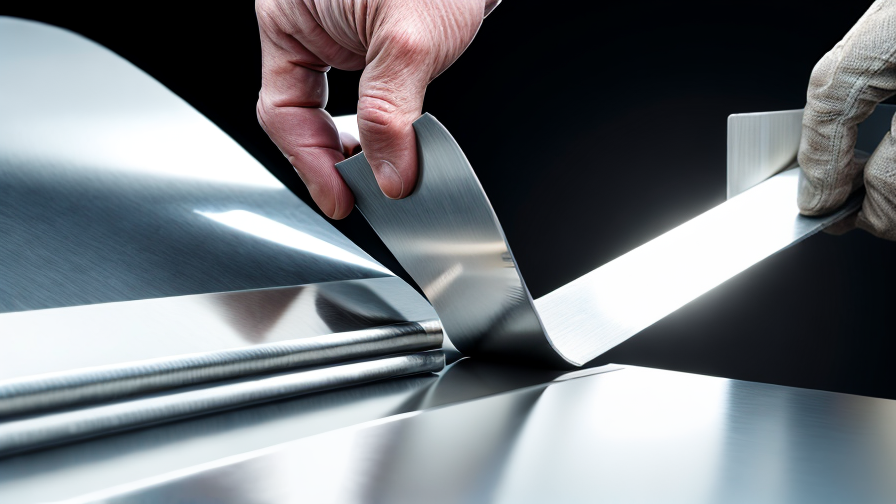
The Work Process and how to use metal sheet bending
Metal sheet bending is a common process used in various industries to shape metal sheets into different forms, such as boxes, cylinders, or angular shapes. It involves the use of specialized tools and equipment to apply force on a metal sheet, causing it to bend and form the desired shape.
The work process of metal sheet bending typically involves several steps. First, the metal sheet is measured and marked with specific dimensions and bend lines. This ensures accuracy and precision in the final product. Next, the metal sheet is secured to a bending machine, which can vary from manual hand-operated tools to advanced automated systems.
The bending machine consists of a clamp or hold-down device to secure the metal sheet in place. It also has a bending tool, such as a punch or die, that exerts pressure on the sheet to induce the required bend. The operator adjusts the position of the bending tool according to the marked bend lines, ensuring the correct angle and radius of the bend.
Once everything is set up, the bending process begins. The operator activates the machine, and the bending tool comes into contact with the metal sheet, gradually applying pressure to create the bend. The amount of force applied depends on the type and thickness of the metal sheet.
During the bending process, the operator closely monitors the progress to ensure the metal sheet is bending smoothly and evenly. Adjustments may be made if necessary, to achieve the desired shape. Once the bending is complete, the metal sheet is released from the machine, and any additional finishing touches or modifications can be made if required.
To effectively use metal sheet bending, it is essential to consider several factors. These include selecting the appropriate bending machine and tooling based on the thickness and type of metal sheet. Proper measurement and marking of the sheet are crucial in achieving accurate bends. Skill and experience are also necessary to ensure optimal results and avoid common issues like spring-back or material distortion.
Metal sheet bending offers immense flexibility in creating various shapes and is widely used in industries such as automotive, aerospace, construction, and manufacturing. Mastering this process can greatly enhance productivity and efficiency in metal fabrication projects.
Quality Testing Methods for metal sheet bending and how to control the quality
Quality testing methods for metal sheet bending involve assessing the mechanical and dimensional properties of the bent sheet. These methods ensure that the bent sheet meets the specified quality standards and functionality requirements. Here are some common testing methods:
1. Visual Inspection: This is the initial step performed to detect any visible defects such as cracks, dents, or uneven bends. It helps identify cosmetic issues that may affect the overall quality.
2. Dimensional Measurements: Measurements are taken using precision tools such as calipers, micrometers, or coordinate measuring machines (CMM). Key dimensions like bend angle, bend radius, and flatness are checked against design specifications to ensure accuracy.
3. Tensile Testing: Tensile tests are conducted to measure the mechanical strength and ductility of the sheet material before and after bending. This helps determine if any defects or weaknesses have occurred during the bending process.
4. Hardness Testing: Hardness is an important parameter as it indicates the material’s resistance to deformation. Various hardness testing methods, like Rockwell or Vickers hardness tests, are performed to assess the material’s hardness before and after bending, ensuring it remains within acceptable limits.
5. Surface Finish Evaluation: The surface finish of the bent sheet is evaluated by visually inspecting for scratches, imperfections, or rough patches. Instruments like profilometers or surface roughness testers can quantify the surface roughness and ensure it meets the required specifications.
To control the quality of metal sheet bending, several steps can be implemented:
1. Pre-production planning: This includes thorough design review, material selection, and establishing detailed bending process parameters to ensure the intended quality.
2. Regular maintenance and calibration of bending machinery and precision measurement tools to ensure accurate and consistent results.
3. Proper operator training to understand the importance of quality control, adhere to standard procedures, and monitor critical parameters during the bending process.
4. Establishing inspection checkpoints at different stages of bending to detect and correct any quality issues promptly.
5. Continuous process monitoring and improvement through statistical process control (SPC) techniques to identify and rectify any variations or defects in the bending process.
By implementing these quality testing methods and control measures, manufacturers can ensure the production of high-quality bent metal sheets that meet or exceed customer expectations and industry standards.
metal sheet bending Sample Policy and Post-Purchase Considerations for metal sheet bending from China
When purchasing metal sheet bending services from China, it is essential to have a clear policy in place to ensure quality control and satisfactory outcomes. Here is a sample policy and some post-purchase considerations to help guide your procurement process:
1. Specification and Quality Control:
Clearly communicate your specific requirements in terms of dimensions, material quality, thickness, tolerances, and surface finish. Request detailed information about the production process, including the machinery and technology involved. Insist on material certifications and quality control measures, such as inspections and testing, to ensure compliance with international standards.
2. Communication and Documentation:
Maintain effective communication with the supplier throughout the process. Ensure that all agreements, specifications, and changes are documented in writing to avoid misunderstandings. Regularly update each other on progress, potential delays or issues, and seek timely resolutions.
3. Sample and Prototype Approval:
Request a sample or prototype for evaluation and approval before mass production. Thoroughly examine the sample for dimensional accuracy, structural integrity, and finish quality. Test the bending durability and assess the conformity to your requirements. Only proceed with bulk production if the sample meets your expectations.
4. Production Timeline and Capacity:
Discuss the expected production timeline and ensure the supplier has the capacity to meet your demand. Request a detailed production schedule and monitor progress closely. If lead times are crucial, consider negotiating penalties for delays or incentivizing timely delivery.
5. Packaging and Shipment:
Clearly communicate your packaging requirements to prevent damage to the metal sheets during transportation. Discuss shipping terms, insurance, and responsibilities to ensure smooth delivery. Arrange inspections before shipment to verify order accuracy and quality.
6. After-sale Service:
Establish the supplier’s commitment to after-sale service, including addressing any potential defects, rework, or replacements. Seek clear warranties or guarantees for a specific period after the purchase to protect your interests.
Post-purchase considerations:
1. Quality Assessment:
Upon receiving the metal sheet bending, thoroughly inspect the products for dimensional accuracy, surface finish, and any defects. Compare them to the approved sample or prototype.
2. Feedback and Assessment:
Evaluate the supplier’s performance based on communication, adherence to specifications, delivery timeline, and overall satisfaction. Provide constructive feedback if necessary, highlighting both positive and negative aspects of their service.
3. Long-term Partnership:
If satisfied with the supplier’s performance, explore opportunities for a long-term partnership. Negotiate better terms, pricing, and engage in continuous improvement discussions to strengthen your relationship.
By implementing a comprehensive policy and considering these post-purchase aspects, you can enhance the efficiency and quality of your metal sheet bending procurement process from China.
Sourcing metal sheet bending from China: Opportunities, Risks, and Key Players
Sourcing metal sheet bending services from China presents several opportunities, risks, and key players in the market.
Opportunities:
1. Cost-effectiveness: China is known for its competitive pricing due to low labor and manufacturing costs, making metal sheet bending services more affordable compared to other countries.
2. Wide range of capabilities: Chinese manufacturers offer a diverse range of metal bending capabilities, including CNC bending, press braking, rolling, and custom tooling, allowing for flexibility in meeting various project requirements.
3. Quality and reliability: Many Chinese suppliers have experience working with international clients and adhere to strict quality control measures to ensure the production of high-quality metal sheet bent products.
Risks:
1. Language and communication barriers: Communication challenges can arise due to language differences, potentially leading to misunderstandings or misinterpretations of product specifications and requirements.
2. Intellectual property concerns: China’s reputation for intellectual property theft and counterfeiting remains a concern. Protecting proprietary designs and ensuring confidentiality can be essential when sourcing metal bending services.
3. Product quality variability: While there are reputable manufacturers in China, there can also be variations in quality standards and consistency across different suppliers. Careful vetting and due diligence are necessary to select reliable partners.
Key Players:
1. BYJC Tools: BYJC Tools is a leading Chinese manufacturer specializing in metal sheet bending machinery and tooling. They offer a wide range of bending solutions, including hydraulic press brakes and CNC bending machines.
2. Dongguan Tianshui Metal Products Co., Ltd.: Tianshui Metal Products is a prominent sheet metal fabricator in China, providing comprehensive sheet bending services using CNC, hydraulic, and manual bending techniques.
3. Ningbo Yinzhou Hybers Imp.& Exp. Co., Ltd.: Hybers is a trusted supplier in the metal fabrication industry, offering an array of metal sheet bending capabilities, including press braking and folding, with a focus on precision and quality.
In conclusion, sourcing metal sheet bending from China offers opportunities for cost savings, a wide range of capabilities, and reliable production. However, risks regarding communication, intellectual property, and product quality variability exist. Key players like BYJC Tools, Tianshui Metal Products, and Hybers should be considered when seeking metal bending services in China.
How to find and select reliable metal sheet bending manufacturers in China,use google search manufacturers and suppliers
1. Start by conducting a Google search for “metal sheet bending manufacturers in China.” This will provide you with a list of potential manufacturers and suppliers to choose from.
2. Narrow down your search by using specific keywords related to your requirements. For example, if you need stainless steel sheet bending, add the keyword “stainless steel” to your search query.
3. Review the websites and online profiles of these manufacturers for information about their capabilities, experience, certifications, and quality management systems. Look for manufacturers with a solid track record and extensive experience in metal sheet bending.
4. Check if the manufacturers have any specific industry certifications or qualifications such as ISO 9001:2015, ISO 14001:2015, or ISO/TS 16949:2016. These certifications indicate that the manufacturer follows standardized processes and maintains quality standards.
5. Read customer reviews and testimonials to get an idea of the manufacturer’s reliability and customer satisfaction. Websites like Alibaba, Made-in-China, and Global Sources often include ratings and feedback from previous clients.
6. Contact the manufacturers that seem most promising and request additional information such as product catalogs, samples, and price quotes. Assess their responsiveness and professionalism in handling your inquiries.
7. Consider visiting trade shows and exhibitions related to metal fabrication in China such as the Canton Fair or Metal + Metallurgy China. These events allow you to meet potential manufacturers in person, assess their facilities, and discuss your requirements.
8. Verify the manufacturer’s legal status and business credentials. Check if they have the necessary licenses and registrations to operate in China.
9. Request references from the manufacturer and contact their existing clients to inquire about their experience working with them. This can provide valuable insights into their reliability, product quality, and timely delivery.
10. Finally, consider the manufacturer’s pricing, lead times, payment terms, and logistics capabilities. Ensure that they can meet your specific requirements and deliver the desired results.
By adopting these steps and carefully evaluating each manufacturer, you can find reliable metal sheet bending manufacturers in China who meet your quality, cost, and delivery expectations.
How to check metal sheet bending manufacturers website reliable,use google chrome SEOquake check if ranking in top 10M
To check the reliability of a metal sheet bending manufacturer’s website, you can use Google Chrome’s SEOquake extension and follow these steps:
1. Install SEOquake: Open Google Chrome and go to the Chrome Web Store. Search for “SEOquake” and click on the search result that matches the SEOquake logo. Click “Add to Chrome” to install the extension.
2. Enable SEOquake: Once SEOquake is installed, you’ll see its icon in the upper right corner of your browser. Click on the icon to enable it for your current webpage.
3. Check Website Ranking: With SEOquake enabled, visit the website of the metal sheet bending manufacturer you want to assess. SEOquake will display a toolbar at the top of the page with various metrics.
4. Look for Alexa Rank: One of the metrics provided by SEOquake is the Alexa Rank, which indicates the popularity and traffic rank of the website. If the metal sheet bending manufacturer’s website ranks within the top 10 million, it can often be considered reliable.
5. Analyze Other Metrics: SEOquake also provides other metrics like the number of indexed pages, domain age, and social media presence. Consider these factors to have a comprehensive understanding of the website’s reliability.
6. Additional Checks: While SEOquake can provide an initial assessment, it’s advisable to conduct further research. Look for customer reviews, testimonials, certifications, and contact information on the manufacturer’s website. A reliable manufacturer will usually provide transparent and detailed information about their services, products, and credentials.
Remember to use SEOquake in conjunction with other evaluation methods to form a well-rounded judgment about the reliability of a metal sheet bending manufacturer’s website.
Top 10 metal sheet bending manufacturers in China
China is known for its robust manufacturing industry, and metal sheet bending is no exception. Here are the top 10 metal sheet bending manufacturers in China:
1. Jiangsu Yawei Machine Tool Co., Ltd.: Yawei Machine Tool is a leading manufacturer of sheet metal bending machines, offering a wide range of products to cater to various industries.
2. Nanjing Klaus CNC Machinery Co., Ltd.: Klaus CNC Machinery specializes in the production of CNC metal bending machines, providing customized solutions for different requirements.
3. Shenzhen LMS Machinery Co., Ltd.: LMS Machinery offers a broad range of sheet metal bending machines, including hydraulic press brakes, CNC press brakes, and more, serving both domestic and international markets.
4. Zhejiang Rongwin Machinery Co., Ltd.: Rongwin Machinery is a professional manufacturer of metal bending machines, providing solutions for various applications, such as HVAC, automotive, and aerospace.
5. Anhui Zhongrui Machine Tool Co., Ltd.: Zhongrui Machine Tool is known for its high-performance CNC press brakes and hydraulic press brakes, serving clients in industries like construction, energy, and transportation.
6. Maanshan Prima CNC Machinery Co., Ltd.: Prima CNC Machinery specializes in sheet metal bending machines, offering advanced technology and reliable performance for diverse manufacturing needs.
7. Nantong Reliantt Co., Ltd.: Reliantt Co. focuses on the production of hydraulic press brakes and CNC press brakes, meeting the bending requirements of industries like aviation, shipbuilding, and machinery.
8. Hako CNC Machine (Anhui) Manufactory Co., Ltd.: Hako CNC Machine is a leading provider of CNC hydraulic press brakes, sheet metal bending machines, and related equipment, serving the global market.
9. Suzhou Baoma Numerical Control Equipment Co., Ltd.: Baoma Numerical Control Equipment produces high-quality CNC hydraulic press brakes and other sheet metal bending machines, meeting the demands of various industries.
10. Jinan GT International Trading Co., Ltd.: GT International Trading offers high-end sheet metal bending machines, including CNC press brakes and hydraulic press brakes, with a focus on export-oriented markets.
These top 10 metal sheet bending manufacturers in China offer a wide range of products, from standard machines to customized solutions, enabling them to cater to diverse industry requirements. With continuous advances in technology and a strong commitment to quality, these manufacturers have established themselves as trusted partners for metal sheet bending needs globally.
Background Research for metal sheet bending manufacturers Companies in China, use qcc.com archive.org importyeti.com
When it comes to metal sheet bending manufacturers in China, there are several resources available to conduct research. Websites like qcc.com, archive.org, and importyeti.com can provide valuable information on these companies.
Qcc.com is a comprehensive business directory in China that provides details on various industries and companies. Users can search for metal sheet bending manufacturers by location, company name, or industry classification. The website often includes information like company profiles, key executives, contact details, and business scope. It is an excellent resource to gain insights into the background and capabilities of metal sheet bending manufacturers in China.
Archive.org is a digital archive that stores historical web pages. Although it might not provide real-time information, it can be useful to access older versions of manufacturer websites or gather information on their past activities. It can offer insight into a metal sheet bending manufacturer’s history, product range, certifications, and potentially their growth or changes over time.
Importyeti.com is a platform that tracks import and export data for companies worldwide. By searching for specific keywords like “metal sheet bending manufacturers” or related terms, it is possible to identify Chinese manufacturers and gain insights into their export activities, customers, shipment volumes, and destinations. This resource can be helpful in understanding the market reach and competitiveness of different metal sheet bending manufacturers.
In summary, conducting background research on metal sheet bending manufacturers in China can be facilitated by using resources like qcc.com, archive.org, and importyeti.com. These platforms allow users to gather information on company profiles, historical data, and export activities. By leveraging these resources effectively, researchers can gain a comprehensive understanding of metal sheet bending manufacturers in China in a concise manner.
Leveraging Trade Shows and Expos for metal sheet bending Sourcing in China
Trade shows and expos serve as valuable platforms for sourcing metal sheet bending services in China. These events bring together a wide range of manufacturers, suppliers, and industry experts, providing an opportunity to establish connections, explore new technologies, and evaluate potential suppliers.
One major advantage of attending trade shows is the ability to directly interact with multiple suppliers in one location. This facilitates efficient comparison of various offerings, including quality, pricing, and production capabilities. By interacting face-to-face, buyers can gain a better understanding of a supplier’s expertise, reliability, and willingness to collaborate.
In addition, trade shows offer the chance to see machines, equipment, and production processes in action. This allows buyers to assess the latest technologies and innovations in the metal sheet bending industry. Identifying advanced machinery can help ensure the selection of a supplier capable of meeting specific requirements, such as precision, efficiency, and speed.
Furthermore, trade shows provide a platform for networking and knowledge exchange among industry professionals. Engaging in conversations with other attendees can lead to valuable insights and recommendations for sourcing quality metal sheet bending services in China. Sharing experiences and challenges faced in the industry can help buyers make informed decisions and avoid potential pitfalls.
To make the most of trade shows and expos, thorough preparation is essential. Buyers should research and identify relevant events in China, ensuring that they align with their specific sourcing needs. It is advisable to set clear objectives and prioritize the exhibitors to visit based on pre-gathered information. Connecting with suppliers before the event can allow for scheduled meetings, ensuring focused discussions during the show.
In conclusion, trade shows and expos provide an efficient and effective way to source metal sheet bending services in China. They offer the opportunity to directly interact with suppliers, assess production capabilities, and explore new technologies. Additionally, networking and knowledge exchange contribute to informed decision-making. With careful planning and preparation, attending trade shows can help secure reliable and quality suppliers in the metal sheet bending industry.
The Role of Agents and Sourcing Companies in Facilitating metal sheet bending Purchases from China
Agents and sourcing companies play a crucial role in facilitating metal sheet bending purchases from China. These entities act as intermediaries between buyers and suppliers, streamlining the procurement process and ensuring smooth transactions.
One of the main benefits of using an agent or sourcing company is their local presence and deep understanding of the Chinese market. They have established relationships with numerous metal sheet bending suppliers, allowing them to quickly identify reputable and reliable manufacturers. This saves buyers significant time and effort in researching and vetting potential suppliers themselves.
Agents and sourcing companies also have expertise in negotiating prices and contract terms. Their knowledge of local business practices and cultural nuances enables them to secure favorable deals for buyers. They can help navigate language barriers, overcome communication challenges, and ensure that all specific requirements are effectively conveyed to the suppliers.
Quality control is another critical aspect facilitated by agents and sourcing companies. They inspect products throughout the production process and conduct final quality checks before shipment. This ensures that the metal sheet bending products meet the buyer’s specifications and industry standards.
Furthermore, these intermediaries provide logistical support, managing the transportation and shipping arrangements. They coordinate with freight forwarders to optimize shipping routes and select the most cost-effective transport options. This end-to-end service guarantees efficient and timely delivery of metal sheet bending products, reducing logistical risks for buyers.
Agents and sourcing companies also assist with customs clearance and handle documentation procedures. They have a comprehensive understanding of import regulations and requirements, ensuring compliance with legal and administrative obligations. This expertise ensures a smoother importation process for buyers and minimizes potential issues or delays at customs.
In summary, agents and sourcing companies play a vital role in facilitating metal sheet bending purchases from China. Their local knowledge, procurement expertise, quality control measures, shipping coordination, and customs support all contribute to a seamless buying experience for customers. By leveraging these intermediaries, buyers can confidently navigate the Chinese market and secure high-quality metal sheet bending products at competitive prices.
Price Cost Research for metal sheet bending manufacturers Companies in China, use temu.com and 1688.com
When it comes to metal sheet bending manufacturers in China, there are numerous options available that offer competitive prices. Two prominent B2B platforms that can be utilized for price and cost research are temu.com and 1688.com.
Temu.com is a comprehensive website that connects buyers with manufacturers in China. It provides a user-friendly interface where buyers can specify their requirements, such as the type of metal sheets, dimensions, and quantity needed. The platform then generates a list of relevant manufacturers along with their prices, allowing buyers to compare and choose the most suitable option. Temu.com also provides information about each manufacturer’s production capacity, certifications, and customer reviews, enabling buyers to make an informed decision.
1688.com is another popular platform that primarily caters to the Chinese market. It is an effective tool for conducting price research as it features a vast array of suppliers specializing in metal sheet bending. Buyers can search for manufacturers by filtering their requirements and obtain price quotes accordingly. The platform also offers options to negotiate prices, ensuring buyers can secure the best deal.
When using both platforms, it is important to consider certain factors to obtain accurate cost estimates. Factors such as material quality, sheet thickness, the complexity of bends, and production volume can impact the final price. Therefore, it is advisable to provide detailed specifications to the manufacturers while requesting a quote.
Both temu.com and 1688.com offer a wide range of manufacturers, ensuring buyers have plenty of choices. It is recommended to reach out to multiple manufacturers and compare the prices, production capacities, and quality standards before making a final decision. Additionally, buyers can also communicate with the manufacturers directly through these platforms to clarify their requirements and negotiate prices further.
In conclusion, temu.com and 1688.com are valuable resources for conducting price and cost research for metal sheet bending manufacturers in China. By utilizing these platforms, buyers can access a plethora of options, compare prices, and ultimately select a manufacturer that meets their specific requirements.
Shipping Cost for metal sheet bending import from China
The shipping costs for metal sheet bending imports from China can vary depending on various factors. These factors include the size and weight of the shipment, the shipping method chosen, the distance between the origin and destination, and any additional services required.
For smaller shipments, air freight is often a preferred option. The cost of air freight is generally higher due to the speed and convenience it offers. However, it is important to note that air freight is more suitable for urgent or time-sensitive shipments.
Another option is sea freight, which is typically more cost-effective for larger shipments. The cost of sea freight depends on the volume and weight of the cargo, as well as the shipping route and any applicable surcharges. A slower transit time should be expected compared to air freight.
To estimate the shipping cost, it is essential to provide specific information such as the dimensions and weight of the metal sheets, the desired transport method, and the origin and destination locations. Additionally, any customs duties, taxes, or fees should also be considered.
To keep shipping costs as low as possible, it is advisable to optimize the packaging to reduce the volume and weight of the shipment. Consolidating multiple shipments into one can also help achieve cost savings. Working with a reliable freight forwarder or shipping agent experienced in importing metal sheets can be beneficial in obtaining accurate cost estimates and ensuring a smooth shipping process.
In conclusion, accurately estimating shipping costs for metal sheet bending imports from China requires considering various factors such as shipment size, weight, shipping method, and additional services required. This information is crucial in determining the most cost-effective and efficient shipping solution.
Compare China and Other metal sheet bending Markets: Products Quality and Price,Visible and Hidden Costs
China is widely recognized as the world’s largest metal sheet bending market, accounting for a significant share of the global market. When comparing China’s metal sheet bending market with other markets, it is important to consider aspects such as product quality, price, and visible and hidden costs.
In terms of product quality, China has made considerable progress in recent years. With advancements in technology and manufacturing processes, Chinese metal sheet bending companies have been able to offer products with good quality standards. The use of advanced machinery and skilled labor contributes to the overall quality of metal sheet bending in China.
Price is an essential factor when comparing markets. China’s metal sheet bending industry is known for offering competitive prices. The availability of raw materials at lower costs and economies of scale enables Chinese manufacturers to provide cost-effective solutions. This has made China a preferred destination for outsourcing metal sheet bending requirements.
Visible costs, such as raw material expenses, labor costs, and transportation expenses, play a significant role in the overall pricing of metal sheet bending products. China benefits from its vast domestic market and a well-established supply chain, enabling it to offer competitive pricing.
However, hidden costs need to be taken into account as well. These include factors like intellectual property issues, quality consistency, and compliance with international standards. While China has made strides in improving these areas, concerns over intellectual property rights and counterfeit products still exist. Buyers need to consider these hidden costs when deciding to source from China or other markets.
In conclusion, China’s metal sheet bending market offers good product quality and competitive prices. The country’s manufacturing capabilities and economies of scale contribute to its position as a leading market. While concerns about hidden costs persist, China remains a popular destination for metal sheet bending needs due to its overall cost-effectiveness. Other markets may offer different advantages and considerations, but China’s dominance in the industry makes it a significant player in the global market.
Understanding Pricing and Payment Terms for metal sheet bending: A Comparative Guide to Get the Best Deal
When it comes to metal sheet bending services, understanding pricing and payment terms is essential in order to secure the best deal. This comparative guide aims to provide some insights into this process and help customers make informed decisions.
Pricing for metal sheet bending services can be determined by various factors, including the complexity of the bending required, the type and thickness of the metal sheet, and the quantity of sheets needed. Each sheet bending provider may have their own pricing structure, so it is important to compare quotes from multiple suppliers to get an idea of the average market price.
To begin, customers should request detailed quotes from different suppliers. These quotes should include information on the cost per bending operation, labor charges, material costs, and any additional fees for specific equipment or tools required. By comparing these quotes, customers can identify the most competitive pricing.
One crucial aspect to look out for is any hidden costs that could potentially inflate the final bill. Some suppliers may not include transportation fees, packaging charges, or setup costs in their initial quotes. Therefore, it is important to clarify and confirm these aspects to avoid any surprises later on.
Payment terms can also vary among different suppliers. Typically, customers will be required to pay a percentage upfront to initiate the order, with the remaining balance due upon completion. However, this can vary depending on the size and nature of the project. Customers should evaluate these payment terms to ensure they align with their budget and cash flow requirements.
In some cases, suppliers may offer discounts or incentives for larger orders or long-term partnerships. It is worth discussing such possibilities with the suppliers to see if any cost savings can be obtained. Additionally, payment options such as credit, installment plans, or financing arrangements may be available, and customers should inquire about these options.
Lastly, it is important to consider the reputation and reliability of the supplier. Working with a reputable and experienced sheet bending provider can minimize the risk of quality issues and delays that could lead to unforeseen costs.
In conclusion, understanding pricing and payment terms for metal sheet bending services is crucial to ensure obtaining the best deal. By comparing quotes, looking out for hidden costs, evaluating payment terms, considering potential discounts, and partnering with a reputable supplier, customers can make informed decisions that not only meet their budget but also guarantee high-quality products.
Chinese Regulations and Industry Standards Certifications for metal sheet bending,Import Regulations and Customs for metal sheet bending from China
In China, there are several regulations and industry standards certifications that apply to metal sheet bending processes. These regulations aim to ensure the quality and safety of the products, protect the environment, and comply with international standards. Some of the important regulations and certifications include:
1. National Standards (GB): The metal sheet bending industry in China is regulated by various national standards, such as GB/T 1804-2000 for tolerances, GB/T 5231-2012 for aluminum alloy sheets, and GB/T 6892-2006 for aluminum alloy extrusions. These standards specify the requirements for product dimensions, mechanical properties, and quality control.
2. ISO 9001: This is an international standard for quality management systems. Many metal sheet bending manufacturers in China have obtained ISO 9001 certifications, which demonstrate their commitment to quality control and continuous improvement.
3. Environmental Protection Requirements: China has strict regulations for environmental protection. Metal sheet bending companies are required to comply with laws regarding pollution prevention, waste management, and emissions control. They must implement measures to reduce environmental impact and obtain necessary permits for operation.
4. Import Regulations and Customs: When importing metal sheet bending products from China, it is important to comply with customs regulations and import requirements of the destination country. This may include providing necessary documentation, such as invoices, packing lists, and certificates of origin. Importers should also be aware of any specific import duties, taxes, or restrictions imposed by their country.
It is recommended to work with reputable suppliers in China who have experience in exporting metal sheet bending products and are familiar with the relevant regulations and certifications. Proper due diligence and communication with the supplier will help ensure compliance with import regulations and customs requirements.
Sustainability and Environmental Considerations in metal sheet bending Manufacturing
Metal sheet bending is a widely used manufacturing process that involves shaping metal sheets into desired forms. While this technique offers numerous benefits, it is crucial to consider sustainability and environmental factors associated with it.
One primary concern in metal sheet bending is the excessive energy consumption often required during the process. The use of large hydraulic or mechanical presses can lead to a significant carbon footprint. To address this issue, manufacturers can adopt energy-efficient machinery that minimizes energy usage without compromising the quality of the final product. Additionally, implementing power-saving measures, such as automatic shutdown systems during idle periods, can further reduce energy consumption.
Another environmental consideration is the waste generated during metal sheet bending. Scrap material, such as leftover metal pieces or trimmings, can contribute to landfill pollution if not properly managed. Implementing recycling programs within the manufacturing facility can help mitigate this issue. For instance, manufacturers can collect and recycle scrap materials, reducing the demand for virgin metal resources.
To enhance sustainability, manufacturers can also evaluate the choice of materials used in metal sheet bending. Opting for eco-friendly materials, such as recycled or sustainably sourced metals, can significantly reduce the environmental impact. These materials often require less energy during production and minimize the extraction of finite resources.
Furthermore, the implementation of advanced technologies like computer numerical control (CNC) systems can optimize the manufacturing process, reducing material waste and enhancing efficiency. CNC systems enable precise bending operations, minimizing errors and ensuring accurate product dimensions. This accuracy reduces the need for rework or scrapping of defective components, resulting in lower waste generation.
Lastly, incorporating sustainable design principles into the product development phase can further improve the overall sustainability of metal sheet bending manufacturing. Emphasizing lightweight designs, for example, reduces material consumption, transportation costs, and energy demands.
In conclusion, sustainable practices and environmental considerations are vital in metal sheet bending manufacturing. By adopting energy-efficient machinery, implementing recycling strategies, selecting eco-friendly materials, utilizing advanced technologies, and incorporating sustainable design principles, manufacturers can minimize the environmental impact of metal sheet bending while maintaining high-quality products.
List The Evolution history of “metal sheet bending”
Metal sheet bending is a technique that involves shaping metal sheets into desired forms by bending or folding. The history of metal sheet bending can be traced back to ancient civilizations, where early metalworkers developed rudimentary methods to manipulate metal sheets.
1. Ancient Egypt and Mesopotamia: In ancient Egypt and Mesopotamia, metalworkers used basic tools like hammers and anvils to bend metal sheets. They primarily worked with softer metals like gold, silver, and copper.
2. Ancient Greece and Rome: The techniques of metal sheet bending became more refined during the ancient Greek and Roman civilizations. Metalworkers used various techniques, including hammering, folding, and creasing, to achieve complex forms. They also developed specialized tools like bending bars and presses to enhance the bending process.
3. Middle Ages: During the Middle Ages, metal sheet bending techniques continued to evolve. Blacksmiths experimented with different techniques and tools, including vices, stakes, and hammers with various shapes. Bending was commonly used in the production of armor, weapons, and decorative metalwork.
4. Industrial Revolution: With the advent of the Industrial Revolution in the 18th century, metal sheet bending underwent significant advancements. The introduction of steam-powered machinery enabled mass production and improved precision in bending. Machines like the bending brake and press brake were developed, making it easier to achieve accurate bends.
5. Modern Era: In the 20th century, metal sheet bending techniques further advanced with the introduction of hydraulic and pneumatic-powered machines. These machines allowed for greater control and flexibility in bending various metals, including steel and aluminum. Computer Numerical Control (CNC) technology revolutionized the industry, enabling precise automated bending processes.
Today, metal sheet bending has become an integral part of numerous industries, including automotive, aerospace, construction, and manufacturing. Advanced techniques, such as air bending, bottom bending, and roll bending, have been developed to meet the diverse requirements of different applications.
In summary, metal sheet bending has come a long way from its early origins in ancient civilizations to the modern era of advanced machinery and technology. The continuous evolution of techniques and tools has enabled metalworkers to create intricate, complex, and precise bends in various metal sheets, opening up endless possibilities for design and fabrication.
The Evolution and Market Trends in metal sheet bending Industry
The metal sheet bending industry has witnessed significant evolution and market trends over the years. With advancements in technology and growing demand for precision and efficiency, manufacturers have adopted new techniques and processes to stay competitive in the market.
One of the major trends in the metal sheet bending industry is the shift towards automation. Manufacturers are increasingly investing in automated bending machines that can perform complex bending operations with minimal human intervention. This not only improves the precision of the bending process but also enhances productivity by reducing cycle time and eliminating errors.
Another important trend is the adoption of computer-aided design (CAD) software and computer numerical control (CNC) machines. CAD software enables engineers to create accurate 3D models of sheet metal components, which can be directly used for bending operations. CNC machines, on the other hand, can interpret these CAD models and automatically bend the sheets accordingly. This integration of CAD and CNC technology has revolutionized the metal sheet bending process, making it highly efficient and streamlined.
Marketwise, there has been a growing demand for lightweight and durable materials in various industries such as automotive, aerospace, and construction. This has led to the increased use of aluminum and composite materials in sheet metal bending applications. Aluminum offers excellent strength-to-weight ratio and corrosion resistance, making it ideal for many applications. Composite materials, on the other hand, provide exceptional strength and rigidity while being lightweight. This trend towards lightweight materials has influenced the design and manufacturing processes in the metal sheet bending industry.
Furthermore, the industry has witnessed a shift towards customization and shorter product life cycles. Customers are demanding unique and tailored sheet metal components, requiring manufacturers to adapt their bending processes to accommodate these specific requirements. This has led to the development of flexible and versatile bending machines that can handle a wide range of designs and specifications.
In conclusion, the metal sheet bending industry has evolved significantly over the years, driven by advancements in technology and changing market demands. Automation, CAD/CNC integration, the use of lightweight materials, and customization have emerged as key trends shaping the industry. Manufacturers who embrace these trends and invest in the latest technologies will be better positioned to meet the evolving needs of their customers and remain competitive in the market.
Custom Private Labeling and Branding Opportunities with Chinese metal sheet bending Manufacturers
Chinese metal sheet bending manufacturers offer great opportunities for custom private labeling and branding. With their expertise and advanced technology, these manufacturers can provide high-quality metal bending services that can be tailored to meet specific branding and labeling requirements.
By partnering with Chinese metal sheet bending manufacturers, businesses can have their own custom designs and logos imprinted on the metal sheets. This allows for the creation of unique and personalized products that stand out in the market. Whether it’s for industrial or commercial applications, private labeling and branding can help businesses differentiate themselves from competitors and build a strong brand identity.
Additionally, Chinese manufacturers offer flexibility in terms of materials, finishes, and dimensions. They have a wide range of metal materials available, including aluminum, stainless steel, and galvanized steel, which can be selected based on the specific branding needs. They can also provide different finishing options, such as powder coating, anodizing, or painting, to enhance the appearance and durability of the products.
Moreover, partnering with Chinese manufacturers enables businesses to benefit from cost-effective production. China is known for its competitive pricing in the manufacturing industry, making it an attractive option for private labeling and branding. With efficient production processes and access to a variety of resources, these manufacturers can offer competitive pricing without sacrificing quality.
In conclusion, Chinese metal sheet bending manufacturers offer excellent opportunities for businesses looking to establish their own private labels and branding. Their expertise, advanced technology, flexibility, and cost-effectiveness make them ideal partners in creating unique and personalized metal products. By leveraging these opportunities, businesses can enhance their visibility, build brand loyalty, and gain a competitive edge in the market.
Tips for Procurement and Considerations when Purchasing metal sheet bending
When it comes to procurement of metal sheet bending, there are several considerations to keep in mind to ensure a successful purchase. Here are some key tips and factors that should be considered:
1. Determine the bending requirements: Start by identifying your specific bending needs, including the thickness, size, and type of metal sheets you require. This will help you select the right bending machine or service provider.
2. Identify reputable suppliers: Research and identify reputable suppliers or manufacturers who specialize in metal sheet bending. Look for companies with a proven track record, positive customer reviews, and a wide range of bending capabilities.
3. Quality and durability: Insist on high-quality metal sheets that meet industry standards. The durability and strength of the metal sheets are crucial factors to consider, especially if the end product will be subjected to heavy usage or extreme conditions.
4. Price comparison: Request quotes from multiple suppliers to compare prices. While cost should not be the sole deciding factor, it is essential to ensure you are getting value for your money. Take into account factors like quality, warranty, and after-sales service when comparing prices.
5. Delivery and lead times: Discuss delivery schedules and lead times with potential suppliers. Ensure that the supplier has the capacity to meet your production deadlines and can deliver the metal sheets within the required timeframe.
6. Technical support: Inquire about the availability of technical support, especially if you are purchasing a bending machine. It is crucial to have access to reliable technical assistance, either online or through phone support, to address any issues or queries that may arise during the operation of the bending equipment.
7. Customization options: If you require customized bending, discuss your specific requirements with the supplier. Ensure that they can accommodate your needs and have the necessary expertise and equipment for custom bending.
8. After-sales service and warranty: Check the supplier’s after-sales service and warranty policies. A reputable supplier should have a good warranty program and offer prompt and efficient support in case of any defects or issues with the metal sheet bending.
By following these procurement tips and considering the essential factors, you can make an informed decision when purchasing metal sheet bending.
FAQs on Sourcing and Manufacturing metal sheet bending in China
Q: What is metal sheet bending?
A: Metal sheet bending is a manufacturing process that involves reshaping a metal sheet by applying force to it, typically using a press brake or a similar machine. This process allows the metal sheet to be bent into various shapes and angles.
Q: Why should I source metal sheet bending in China?
A: China is known for its expertise in manufacturing and has a robust metalworking industry. Sourcing metal sheet bending in China offers numerous advantages, such as cost-effectiveness due to lower labor and production costs, a wide range of available materials and finishes, access to advanced machinery and technology, and the ability to handle large production volumes.
Q: How can I find reliable suppliers for metal sheet bending in China?
A: To find reliable suppliers, you can utilize online platforms specialized in connecting buyers with manufacturers, such as Alibaba or Global Sources. It is essential to carefully review and compare potential suppliers, considering factors like their experience, reputation, certifications, manufacturing capabilities, and customer reviews. You should also request samples and visit factories if possible to assess the quality and reliability firsthand.
Q: What types of metal can be used for sheet bending in China?
A: Metal sheet bending in China can be performed on a variety of metals, including aluminum, stainless steel, carbon steel, galvanized steel, and brass. The choice depends on your specific application requirements, such as strength, corrosion resistance, and appearance.
Q: Can Chinese manufacturers handle custom metal sheet bending projects?
A: Yes, Chinese manufacturers are capable of handling custom metal sheet bending projects. They often have extensive experience with working on diverse customer specifications and can accommodate different bending angles, sizes, and finishes.
Q: How long does it take to manufacture metal sheet bending products in China?
A: The manufacturing time for metal sheet bending products in China depends on various factors, including the complexity of the design, the order size, the availability of raw materials, and the workload of the manufacturer. Generally, lead times can range from a few days for simpler projects to several weeks for more complex or larger-volume orders.
In conclusion, sourcing and manufacturing metal sheet bending in China offer cost-effectiveness, access to a wide range of materials, and advanced manufacturing capabilities. However, thorough supplier evaluation and communication are crucial to ensure product quality and meet specific project requirements.
Why contact sourcifychina.com get free quota from reliable metal sheet bending suppliers?
Sourcifychina.com offers a free quota to contact reliable metal sheet bending suppliers for several reasons. By providing a free quota, Sourcifychina.com aims to facilitate and streamline the sourcing process for businesses looking to procure metal sheet bending services.
Firstly, the free quota allows businesses to easily obtain price and production information from multiple suppliers. This saves time and effort by consolidating the initial communication and negotiation phase into a single platform. Instead of individually reaching out to each supplier, businesses can submit their requirements on Sourcifychina.com and receive multiple quotations. This simplifies the sourcing process and provides businesses with a comprehensive overview of available options.
Furthermore, by offering a free quota, Sourcifychina.com encourages businesses to explore the capabilities and offerings of a wide range of metal sheet bending suppliers. It enables businesses to compare different suppliers in terms of pricing, manufacturing capabilities, lead times, and quality standards. This helps businesses make informed decisions and select the most suitable supplier based on their specific requirements and preferences.
Moreover, the free quota allows businesses to establish direct communication with reliable metal sheet bending suppliers without any financial commitment. This eliminates any barriers to initial contact, ensuring that businesses can easily connect with potential suppliers and discuss their project details. This direct communication helps build trust and rapport between the buyer and supplier, facilitating a smooth and efficient collaboration.
Overall, the provision of a free quota by Sourcifychina.com benefits businesses by simplifying the sourcing process, offering multiple options, fostering direct communication, and ultimately enabling them to find reliable metal sheet bending suppliers that meet their needs.