Introduce about multi jet fusion guide,Qulity,Cost,Supplier,Certification,Market,Tips,FAQ
Multi Jet Fusion (MJF) is an advanced additive manufacturing process that uses inkjet printhead technology to create intricate and highly detailed 3D printed objects. This guide provides valuable information about the different aspects of MJF, including quality, cost, suppliers, certification, market trends, tips, frequently asked questions, and more.
The quality of MJF is exceptional, offering high resolution, smooth surfaces, and fine details. The technology allows for the production of complex geometries and robust parts, making it suitable for a wide range of applications, from prototyping to end-use production.
In terms of cost, MJF offers a competitive advantage due to its high productivity and efficiency. The printing process is fast and allows for batch production, resulting in reduced overall production costs. Additionally, MJF materials are cost-effective, offering a great value for money.
Suppliers offering MJF services are numerous and can be easily found online. However, it is recommended to choose a reputable supplier with experience in using MJF technology to ensure optimal results.
Certification plays a vital role in ensuring the quality and reliability of MJF parts. Some suppliers may have certifications such as ISO 9001 or ISO 13485, which guarantee adherence to industry standards and quality control processes.
The market for MJF technology is rapidly expanding across various industries, including automotive, aerospace, healthcare, and consumer goods. The versatility and efficiency of MJF make it an attractive choice for many manufacturers looking to improve their production processes.
Tips for maximizing the benefits of MJF include optimizing part designs for additive manufacturing, choosing suitable material options, and leveraging post-processing techniques to achieve desired surface finishes or functional properties.
Frequently asked questions about MJF may revolve around its compatibility with different materials, part size limitations, turnaround times, pricing structures, and post-processing capabilities. Consulting with experienced suppliers can provide comprehensive answers and tailored guidance.
In conclusion, MJF is an advanced additive manufacturing process that offers exceptional quality, cost-effectiveness, and versatility. With a growing market presence, numerous suppliers, and a wide range of applications, MJF is a technology that continues to push the boundaries of 3D printing.
Types of multi jet fusion
Multi Jet Fusion (MJF) is a revolutionary 3D printing technology that utilizes inkjet arrays to deposit a binding agent and a fusing agent onto a bed of powder, layer by layer, to create objects. This process allows for the simultaneous printing of several parts, reducing production time and costs significantly. There are two main types of MJF: HP Multi Jet Fusion and Desktop Metal Studio System.
1. HP Multi Jet Fusion: Developed by Hewlett-Packard (HP), this is the pioneering version of MJF. It employs a combination of thermal and chemical processes to produce strong, functional parts. The process begins with a thin layer of polymer powder being spread evenly over the build platform. The print head then deposits a fusing agent across the entire layer, while thermal energy is applied to specific areas to melt the powder. A detailing agent is also deposited to enhance the object’s quality. The process continues by adding successive layers until the final part is complete. HP’s MJF technology offers great accuracy, fine resolution, and high production speed.
2. Desktop Metal Studio System: This is a compact and more affordable MJF alternative developed by Desktop Metal. It offers a 3D printing solution for small to mid-sized enterprises. The Desktop Metal Studio System combines a printer, debinder, and sintering furnace into a unified solution. The process starts with a cartridge of metal powder loaded into the printer. Similar to HP’s MJF, a binding agent is jetted onto the powder layer by layer, creating green parts. Once the printing is complete, the green parts are placed in a debinding unit, where the binding agent is removed. Finally, the debound parts are sintered in a furnace, resulting in fully dense metal parts. The Desktop Metal Studio System enables the production of complex parts with excellent surface finish.
Both HP Multi Jet Fusion and Desktop Metal Studio System provide unique advantages in the field of additive manufacturing. They allow for the creation of intricate geometric designs, offer high material strength, and provide a cost-effective solution for prototype development and small-batch production. These MJF technologies are being further developed and refined, opening up exciting possibilities for industries such as automotive, aerospace, and medical.
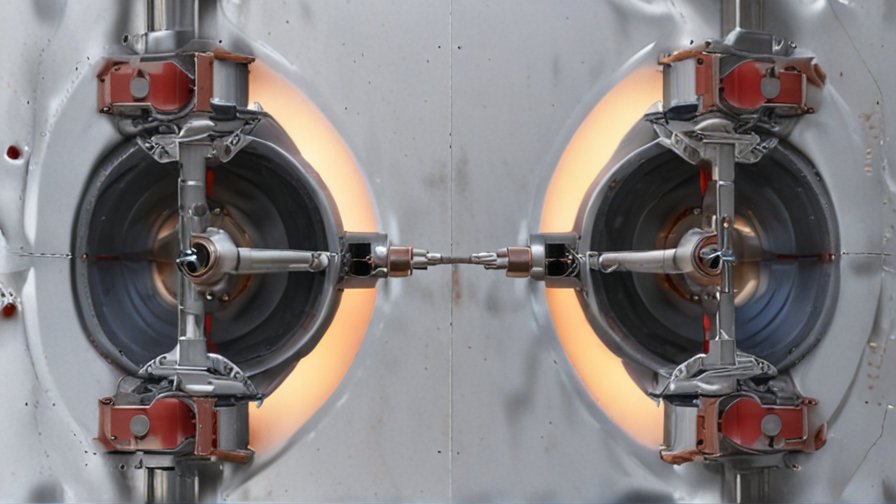
Pros and Cons of Using multi jet fusion
Multi Jet Fusion (MJF) is an additive manufacturing technology that offers several benefits but also has its limitations. Here are some of the pros and cons of using MJF:
Pros:
1. Speed: MJF is known for its high printing speeds compared to other 3D printing technologies. It uses multiple print heads simultaneously, allowing for rapid production of parts. This makes it ideal for time-sensitive projects or industries where quick turnaround times are essential.
2. Accuracy and Resolution: MJF can achieve high accuracy and resolution, producing parts with fine details and intricacies. This makes it great for applications that require precise dimensions and intricate geometries.
3. Material Versatility: MJF can work with a wide range of materials, including thermoplastics and elastomers. It allows for the production of parts with various mechanical properties, such as flexibility, durability, and transparency. This versatility expands the potential applications of MJF to different industries.
4. Cost-effective: MJF has a lower cost per part compared to traditional manufacturing processes, especially for small production runs. It eliminates the need for expensive tooling and allows for the production of complex designs without additional costs. Additionally, it minimizes material waste since only the required amount is used for each part.
Cons:
1. Limited Build Size: One limitation of MJF is the restricted build size. The size of the parts that can be produced is limited by the available build volume. This can be problematic for producing large-scale components or assemblies.
2. Surface Finish: While MJF can achieve high accuracy, the surface finish of the printed parts may not be as smooth as desired. Additional post-processing steps may be required to achieve the desired surface quality, adding to the overall production time and cost.
3. Material Limitations: While MJF offers material versatility, it may not be suitable for all applications. Certain specialized materials or composites may not be compatible with MJF technology. This could limit certain industries or applications that require specific material properties.
4. Complex Post-processing: MJF requires post-processing steps, such as removing the excess powder and applying finishing treatments if desired. The post-processing can be time-consuming and labor-intensive, affecting the overall manufacturing efficiency.
In summary, Multi Jet Fusion technology offers high-speed production, accuracy, versatility, and cost-effectiveness. However, it has limitations concerning build size, surface finish, material compatibility, and complex post-processing requirements. Evaluating these pros and cons is crucial in determining whether MJF is the right choice for a specific application or project.
multi jet fusion Reference Specifications (varies for different product)
Multi Jet Fusion (MJF) is a 3D printing technology developed by HP that allows for the production of high-quality, functional parts at a rapid speed. Its reference specifications can vary for different products, depending on the specific requirements and design considerations.
MJF printers typically have a build volume of around 380 x 284 x 380 mm, allowing for the creation of parts in various sizes. The printers utilize a multi-agent printing process, where a fusing agent and a detailing agent are selectively applied to a powdered material bed layer by layer.
Fusing agent is jetted onto the powder bed to selectively fuse and solidify it, while the detailing agent is applied to define fine features and improve part quality. A heating element then passes over the powder bed to further enhance the fusion process. The process is repeated layer by layer until the complete part is built.
The MJF technology offers excellent dimensional accuracy with tolerances as low as ±0.2 mm. It can handle a wide range of materials, including engineering-grade plastics like Nylon 12 and Nylon 12 Glass Beads, for producing parts with good mechanical properties. These materials also exhibit enhanced thermal conductivity, making them suitable for applications that involve heat transfer.
The MJF process enables the production of parts with isotropic properties, meaning the mechanical characteristics are consistent in all directions, resulting in strong and durable end products. Moreover, the technology offers high printing speeds, making it suitable for rapid prototyping and low to mid-volume manufacturing.
Post-processing for MJF parts typically involves removing excess powder using air pressure and brushing, followed by bead blasting or sanding for surface refinement. The parts can be further finished with painting, dyeing, or coating processes for aesthetic purposes or to meet specific requirements.
Overall, Multi Jet Fusion technology provides a versatile and efficient solution for producing functional parts with high precision, mechanical strength, and excellent surface finishes. Its use can be tailored to meet the unique specifications of various products, making it a preferred choice across industries for additive manufacturing applications.
Applications of multi jet fusion
Multi Jet Fusion (MJF) is an advanced 3D printing technology that offers numerous applications across various industries. By using fusing agents and a heating element, MJF can transform powdered materials into highly precise and durable parts. Here are a few key applications of MJF:
1. Prototyping: MJF is ideal for rapid prototyping due to its speed and accuracy. With the ability to print complex geometries and intricate design features, it allows engineers and designers to create physical prototypes quickly, facilitating better product development and iterations.
2. Manufacturing: MJF has found applications in low-volume production runs where customization and complexity are prioritized. It enables the production of end-use parts with high precision and consistency while reducing manufacturing time and costs compared to traditional manufacturing methods.
3. Automotive Industry: MJF is widely adopted in the automotive industry for manufacturing interior components and small parts, such as brackets, connectors, and customized jigs. It facilitates rapid tooling production, allowing car manufacturers to streamline their product development and customization processes.
4. Aerospace Industry: MJF is particularly valuable in the aerospace sector due to its ability to create lightweight, high-strength parts with complex geometries. It is used for producing parts like brackets, ducting, engine components, and even prototypes of entire aircraft. MJF enables the production of intricate structures that were previously impossible or costly to manufacture.
5. Medical Field: MJF is revolutionizing healthcare by providing customized medical devices and prosthetics. It enables the creation of patient-specific implants, surgical guides, orthopedic supports, and dental components. MJF’s capability to produce anatomically accurate and biocompatible parts significantly improves patient outcomes and reduces costs associated with traditional manufacturing techniques.
6. Consumer Products: MJF finds its applications in the consumer product industry for manufacturing various plastic components like handles, closures, and casings. Its ability to produce items with intricate details and textures enables the creation of aesthetically appealing products.
7. Architecture and Design: MJF is increasingly used in architecture and design for creating intricate models, molds, and custom architectural elements. Its high-resolution capabilities and the ability to produce accurate prototypes allow architects and designers to validate their designs before expensive production processes.
The versatile applications of Multi Jet Fusion make it a powerful and cost-effective manufacturing technology that is transforming industries by enabling faster production, customization, and prototyping capabilities.
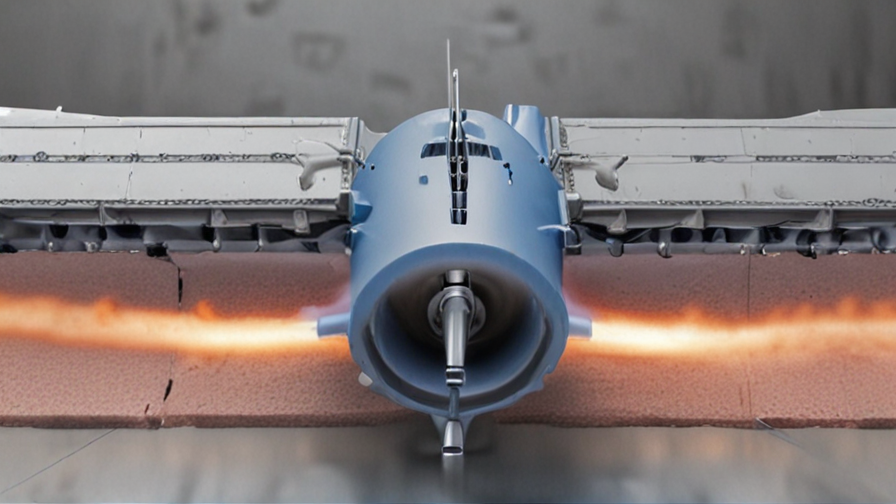
The Work Process and how to use multi jet fusion
The work process of using Multi Jet Fusion (MJF) involves several steps to achieve high-quality 3D printed objects. Here is a brief overview of the process:
1. Design: Start by creating a 3D model using computer-aided design (CAD) software. Design considerations should include wall thickness, support structures, and material compatibility.
2. Preparation: Clean the build chamber and apply a thin layer of the powdered material used in MJF. The powder bed should be even and smooth.
3. Printing: The MJF machine selectively deposits chemical agents onto the powdered material using an inkjet array. One agent promotes fusion while the other serves as a detailing agent to improve resolution. This process continues layer by layer until the object is complete.
4. Cooling and Solidification: After printing, the entire build chamber is heated to just below the melting point of the powdered material. This enables fusion where the chemical agents were deposited. The object then cools, solidifies, and becomes ready for post-processing.
5. Support Removal: Once the object is cooled, it is removed from the build chamber. Excess powder and support structures are carefully removed, potentially using pressurized air or mechanical vibration.
6. Cleaning: The printed object may still retain excess powder. It is essential to clean it thoroughly, typically by immersing it in a cleaning agent or using pressurized air to remove any remaining loose powder particles.
7. Post-processing: Depending on the desired finish and application, additional steps may be needed. These can include sanding, painting, or dyeing to enhance the appearance and functionality of the object.
Using the MJF technology offers advantages such as high productivity, accuracy, and the ability to print complex geometries. It is suitable for creating functional prototypes, small-batch production runs, and customized end-use parts across various industries.
In conclusion, the work process for using Multi Jet Fusion involves designing the 3D model, preparing the powder bed, printing layer by layer with the aid of chemical agents, cooling and solidifying the printed object, removing supports, cleaning, and potentially applying additional post-processing steps.
Quality Testing Methods for multi jet fusion and how to control the quality
Multi Jet Fusion (MJF) is a 3D printing technology that enables the production of high-quality parts with excellent dimensional accuracy and high geometric complexity. To ensure the quality of MJF parts, several testing methods are commonly used.
1. Visual Inspection: Visual inspection is the most straightforward method to identify any visual defects or inconsistencies in the printed parts. It involves examining the surface finish, layer adhesion, and overall appearance of the parts.
2. Dimensional Accuracy: Measurement techniques such as coordinate measuring machines (CMMs) or laser scanners are employed to verify if the parts meet the specified dimensions and tolerances. This ensures that the final product matches the intended design.
3. Density and Porosity Analysis: Density and porosity tests are conducted to assess the interior structure of MJF parts. Various non-destructive testing methods, such as X-ray computed tomography (CT) or ultrasound, are utilized to detect and analyze any voids, defects, or inconsistencies within the printed parts.
4. Mechanical Testing: Mechanical properties, including tensile strength, flexural strength, and impact resistance, are crucial for evaluating the performance and durability of MJF parts. Universal testing machines are commonly used to conduct these tests, ensuring compliance with the desired mechanical requirements.
5. Surface Roughness Analysis: Surface roughness can impact the functionality and aesthetics of a part. Profilometers or other surface roughness measurement instruments assess the quality of MJF parts’ outer surfaces by quantifying roughness parameters such as Ra, Rz, or Rt.
Controlling the quality of MJF parts involves a combination of process optimization and monitoring. Key parameters that need to be controlled include printing parameters (e.g., layer thickness, temperature, print speed), powder quality, and post-processing techniques (e.g., bead blasting, infiltration). Regular calibration of printing systems and routine maintenance are imperative to ensure consistent quality over time.
Additionally, employing statistical process control (SPC) techniques can aid in identifying any deviations or trends in quality parameters. By analyzing the collected process data, manufacturers can make real-time adjustments and prevent potential quality issues.
To summarize, effective quality control for MJF parts requires a comprehensive approach incorporating visual inspection, dimensional analysis, density and porosity testing, mechanical testing, and surface roughness analysis. Simultaneously, continuous process monitoring and optimization are crucial to maintaining consistent quality throughout production.
multi jet fusion Sample Policy and Post-Purchase Considerations for multi jet fusion from China
Sample Policy:
Thank you for choosing multi jet fusion from China. We are committed to delivering high-quality products and excellent service to our valued customers. To ensure a smooth purchasing experience, please find below our sample policy:
1. Sample Request:
– Customers are welcome to request samples of our multi jet fusion products.
– Samples can be obtained by contacting our sales team or visiting our website.
– We may charge a nominal fee for sample products, which will be refunded upon placing a subsequent order.
2. Sample Evaluation:
– We encourage customers to thoroughly evaluate the samples before making a purchase decision.
– Customers should check the product quality, performance, and compatibility with their specific requirements.
– Our team is available to address any queries or concerns related to the sample products.
3. Sample Order:
– After evaluating the samples, customers can place an order with our sales team directly.
– The ordering process will include specifying the desired quantity, customization options, and delivery address.
– Our team will provide detailed pricing and payment terms for the order.
Post-Purchase Considerations:
Once you have purchased our multi jet fusion products from China, please consider the following points to ensure a satisfactory experience:
1. Product Installation and Training:
– Upon receiving the products, follow the provided installation instructions carefully.
– If required, our team can offer remote or on-site assistance for installation and training.
2. Product Warranty and Support:
– Our multi jet fusion products come with a [X]-year warranty against manufacturing defects.
– For any warranty claims or technical support, please contact our customer service team for prompt assistance.
– Please ensure to provide the necessary documents, such as the purchase invoice and warranty card.
3. Feedback and Reviews:
– We greatly value your feedback and encourage you to share your experience using our multi jet fusion products.
– Your reviews and suggestions help us improve our products and services, benefiting both existing and future customers.
Thank you for choosing multi jet fusion from China. We strive to provide exceptional products, reliable support, and complete customer satisfaction. Feel free to contact us with any further inquiries or assistance needed.
Sourcing multi jet fusion from China: Opportunities, Risks, and Key Players
Sourcing multi jet fusion (MJF) technology from China can offer both opportunities and risks for companies looking to adopt or expand the use of this additive manufacturing technology. MJF is a 3D printing process that enables the production of complex and functional parts with high accuracy and speed.
One of the main opportunities of sourcing MJF from China is the country’s well-established manufacturing capabilities and expertise. China has a strong manufacturing industry and is well-positioned to produce MJF machines, parts, and materials at a competitive cost. This can be attractive for companies looking to reduce production costs and access a larger supply of MJF technology.
Furthermore, China’s extensive supply chain can provide a wide range of options for sourcing MJF-related components and materials. This can help reduce lead times and provide greater flexibility in sourcing options. Additionally, partnering with Chinese manufacturers can offer access to a vast network of skilled engineers and technicians who can provide technical support and assistance in implementing MJF technology.
However, there are also risks associated with sourcing MJF from China. One of the key risks is the protection of intellectual property (IP). China has been criticized in the past for inadequate IP protection, which may give rise to potential issues such as counterfeiting or unauthorized replication of MJF technology. Companies should carefully consider strategies to protect their IP when engaging with Chinese manufacturing partners.
Another risk is the potential for quality issues or inconsistencies in the manufactured products. Companies should conduct thorough due diligence on the capabilities and reputation of the selected Chinese manufacturers to ensure that they meet the required quality standards. Regular quality checks and compliance monitoring should also be implemented to minimize potential risks.
Key players in the Chinese MJF market include established 3D printing companies such as Shining 3D and Farsoon Technologies. These companies have extensive experience in the additive manufacturing industry and offer a range of MJF machines and services. Partnering with reputable and established players in the Chinese market can mitigate risks and ensure the availability of technical support and customer service.
In conclusion, sourcing MJF from China can provide opportunities for cost reduction, increased supply chain flexibility, and access to technical expertise. However, companies should carefully consider and manage the risks associated with IP protection and product quality. Partnering with reputable players in the Chinese market can mitigate these risks and ensure successful adoption of MJF technology.
How to find and select reliable multi jet fusion manufacturers in China,use google search manufacturers and suppliers
When searching for reliable multi jet fusion manufacturers in China, using Google can be a valuable tool. Here are a few steps to help you find and select suitable manufacturers and suppliers.
1. Start by conducting a Google search using relevant keywords such as “multi jet fusion manufacturers China” or “professional 3D printing service providers China.” This will provide you with a list of potential options.
2. Go through the search results and visit the websites of manufacturers and suppliers that appear to offer multi jet fusion services. Look for key information such as their years of experience, certifications, customer reviews, and quality control processes.
3. Check if the manufacturers have specific experience with multi jet fusion technology and whether they have successfully completed similar projects in the past. Look for any case studies or examples on their website that showcase their expertise in this field.
4. Evaluate the manufacturing facilities and equipment. The manufacturers should have advanced 3D printers suitable for multi jet fusion. Look for information about their production capacity, speed, and turnaround times to ensure they can handle your project requirements.
5. Contact the shortlisted manufacturers and suppliers to discuss your specific needs. Inquire about their pricing, available materials, finishing options, and any additional services they can provide, such as design assistance or post-processing.
6. Request samples or prototypes to evaluate the quality of their work. This will allow you to assess the accuracy, surface finish, and overall performance of the multi jet fusion parts.
7. Ask for references or customer testimonials to validate the manufacturers’ reputation and reliability. Reach out to their previous clients to gauge their satisfaction with the services provided.
8. Consider the overall cost, including production, shipping, and any additional fees or taxes. Balance this with the quality and reliability offered by each manufacturer.
9. Finally, make a decision based on all the collected information, comparing the expertise, capabilities, and pricing of the different manufacturers. Choose the one that best aligns with your project requirements, quality expectations, and budget.
Remember to conduct thorough due diligence and take the time to research and evaluate the manufacturers before making a final selection.
How to check multi jet fusion manufacturers website reliable,use google chrome SEOquake check if ranking in top 10M
To check the reliability of a multi jet fusion manufacturer’s website, you can follow these steps:
1. Use Google Chrome: Open the website you want to check in the Google Chrome web browser. This browser provides various helpful extensions that can assist in evaluating a website’s reliability.
2. Install SEOquake: Go to the Chrome Web Store and search for the SEOquake extension. Install it on your browser.
3. Enable SEOquake: Once installed, you should see the SEOquake icon appear in your Chrome toolbar. Click on it, and a menu will appear.
4. Check Website Data: In the SEOquake menu, click on the “Diagnosis” tab. Here, you will find various metrics and data related to the website’s reliability and performance.
5. Check Ranking: Look for the “Google Index” section on the SEOquake diagnosis page. It will provide the website’s ranking among the top 10 million websites on the internet. If the website is ranked within the top 10 million, it indicates a relatively high level of traffic and popularity.
6. Consider Additional Factors: While the ranking is an important indicator of a website’s reliability, it is also essential to evaluate other factors such as website design, customer reviews, product information, and security measures.
7. Verify Information: Ensure that the manufacturer’s website provides accurate and up-to-date information about their multi jet fusion technology, services, and products. Check for contact details or customer support options to further validate their legitimacy.
Remember not to solely rely on SEOquake rankings as they indicate popularity but not necessarily reliability. It is crucial to assess various factors to determine the overall trustworthiness and credibility of the multi jet fusion manufacturer’s website.
Top 10 multi jet fusion manufacturers in China with each 160 words introduce products,then use markdown create table compare
1. HP Inc.: One of the leading multi jet fusion manufacturers in China, HP Inc. offers a range of industrial-grade 3D printing solutions. Their multi jet fusion printers utilize advanced technology to deliver high-speed and high-resolution printing. These printers are capable of creating complex prototypes and functional parts with great precision, making them ideal for various industrial applications.
2. Shining 3D: Shining 3D is renowned for its expertise in 3D scanning and printing technologies. They offer multi jet fusion printers that are designed for rapid prototyping and small-batch production. Their printers boast high accuracy and excellent surface quality, enabling the creation of intricate designs with ease.
3. UnionTech: UnionTech is a leading provider of industrial-grade multi jet fusion printers in China. Their printers offer fast and accurate printing capabilities, making them suitable for applications in industries like automotive, aerospace, and consumer goods. UnionTech’s printers also support a wide range of materials, allowing for versatile printing options.
4. Zhuhai CTC Electronic: Zhuhai CTC Electronic specializes in the development and manufacturing of multi jet fusion 3D printers. Their printers provide high efficiency and stability, enabling the production of high-quality parts at a rapid pace. They also offer customization options and comprehensive technical support to cater to specific client requirements.
| Manufacturer | Specialization | Printing Speed | Accuracy |
|———————-|———————————————–|—————–|——————|
| HP Inc. | Industrial-grade 3D printing solutions | High | High |
| Shining 3D | 3D scanning and printing technologies | High | Excellent |
| UnionTech | Industrial-grade multi jet fusion printers | Fast | High |
| Zhuhai CTC Electronic| Development and manufacturing of 3D printers | High | High |
5. Creality 3D: Creality 3D is a well-known manufacturer of multi jet fusion printers. Their printers are widely recognized for their affordability and user-friendly interface. Creality’s printers come with a large build volume and are capable of delivering high-resolution prints, making them suitable for both professional and personal use.
6. Anycubic: Anycubic offers a range of multi jet fusion printers that prioritize ease of use and affordability. Their printers feature a sturdy construction and offer excellent printing quality. Anycubic also provides a wide range of compatible materials for versatile printing options.
7. Flashforge: Flashforge is known for its high-performance multi jet fusion printers. Their printers offer fast printing speed and high accuracy, enabling the creation of intricate models and functional parts. Flashforge also provides efficient customer support and a user-friendly printing software interface.
8. Zhejiang Qidi Technology: Zhejiang Qidi Technology specializes in the manufacturing of multi jet fusion printers for educational and industrial purposes. Their printers prioritize ease of use and safety, making them suitable for educational institutions. Qidi Technology’s printers also offer reliable performance and precise printing capabilities.
| Manufacturer | Specialization | Printing Speed | Accuracy |
|———————-|———————————————–|—————–|——————|
| Creality 3D | Affordable and user-friendly 3D printers | Fast | High |
| Anycubic | Affordable multi jet fusion printers | Fast | High |
| Flashforge | High-performance 3D printers | Fast | High |
| Zhejiang Qidi Tech | Multi jet fusion printers for educational use | Fast | High |
9. JG Maker: JG Maker is a prominent manufacturer of multi jet fusion printers known for their reliable performance and high printing quality. Their printers offer various connectivity options and support multiple file types, making them suitable for a diverse range of applications.
10. Wanhao: Wanhao specializes in the production of multi jet fusion printers that provide excellent print quality and durability. Their printers offer precision printing with smooth finishes, making them suitable for industrial and professional use.
Overall, the multi jet fusion printer market in China offers a wide range of options from various manufacturers. The table above provides a comparison of some leading manufacturers based on their specialization, printing speed, and accuracy, giving users a better understanding of the available choices in the market.
Background Research for multi jet fusion manufacturers Companies in China, use qcc.com archive.org importyeti.com
China is known for its thriving manufacturing industry and has become a global leader in various sectors. When it comes to multi jet fusion (MJF) technology manufacturers, several companies in China have emerged as key players in this field. Three notable companies are Beijing Zhongke Jietong Technology Co. Ltd., Shenyang Machine Tool Co. Ltd., and Sichuan Qinchuan Machinery Development Co. Ltd.
Beijing Zhongke Jietong Technology Co. Ltd. is a company focused on the research, development, and production of industrial 3D printing equipment, including MJF technology. They offer a range of products, from small-scale models to large-scale industrial-grade systems. With a strong emphasis on innovation and quality, Zhongke Jietong has become a trusted MJF manufacturer in China.
Shenyang Machine Tool Co. Ltd. is another prominent player in the Chinese manufacturing industry. While they are primarily known for their machine tools, the company also offers MJF products. With their advanced production facilities and expertise in precision manufacturing, Shenyang Machine Tool produces high-quality MJF machines, catering to various industrial needs.
Sichuan Qinchuan Machinery Development Co. Ltd. is a leading manufacturer of industrial machinery and equipment, including MJF technology. The company has a dedicated research and development team and holds multiple patents in the field of additive manufacturing. Their MJF machines are designed for high-speed, high-precision production and have gained popularity among both domestic and international clients.
These three manufacturers exemplify China’s growing prowess in the MJF technology sector. As the country continues to invest in research and development, it is likely that more companies will emerge as strong contenders in this field. By leveraging their expertise in precision manufacturing, technological innovation, and robust production capabilities, Chinese MJF manufacturers are poised to contribute significantly to the global 3D printing market.
Leveraging Trade Shows and Expos for multi jet fusion Sourcing in China
Trade shows and expos provide excellent opportunities for sourcing multi jet fusion products in China. These events bring together a wide range of manufacturers, suppliers, and industry experts, allowing businesses to connect and explore new sourcing options.
Attending trade shows and expos focused on 3D printing and additive manufacturing in China can provide valuable insights into the latest developments in multi jet fusion technology. These events often showcase the most innovative products, materials, and equipment in the industry, giving businesses a chance to see the potential of multi jet fusion in person.
Interacting with exhibitors at these events allows businesses to establish direct communication with suppliers in China. This face-to-face interaction is essential for building relationships and gaining a deeper understanding of the capabilities and offerings of different suppliers. It also offers the opportunity to discuss specific requirements, negotiate pricing, and explore customization options.
Trade shows and expos also offer a platform for businesses to compare different suppliers and their products. With numerous exhibitors under one roof, it becomes easier to evaluate and assess different options, ensuring that the chosen supplier can meet the desired quality, quantity, and cost requirements.
In addition to sourcing opportunities, trade shows and expos provide a wealth of knowledge through seminars, workshops, and demonstrations. These educational sessions offer insights into the latest trends, best practices, and advancements in multi jet fusion technology, enabling businesses to stay ahead of the competition and make informed sourcing decisions.
To leverage trade shows and expos effectively, businesses must plan ahead and allocate sufficient time to visit relevant events. They should research and identify the most suitable trade shows and expos for multi jet fusion sourcing in China based on their specific needs and priorities. Proper preparation, including setting objectives, identifying key suppliers to meet, and preparing a list of questions, is crucial to maximize the benefits of these events.
In conclusion, trade shows and expos provide a unique and valuable platform for sourcing multi jet fusion products in China. By attending these events and actively engaging with exhibitors, businesses can evaluate suppliers, establish connections, gain insights, and ultimately find the best sourcing solutions for their multi jet fusion needs.
The Role of Agents and Sourcing Companies in Facilitating multi jet fusion Purchases from China
Agents and sourcing companies play a crucial role in facilitating multi jet fusion purchases from China. With their expertise and knowledge of the Chinese market, they act as intermediaries between the buyers and manufacturers, helping to streamline the purchasing process and ensure the smooth execution of the transaction.
Firstly, agents and sourcing companies assist in finding reliable and reputable manufacturers in China that specialize in multi jet fusion technology. They have a deep understanding of the local market and can identify manufacturers that meet the buyer’s specific requirements in terms of quality, cost, and production capabilities.
Once potential manufacturers are identified, agents and sourcing companies act as a bridge between the buyer and the manufacturer. They facilitate communication, provide translation services, and assist in negotiating favorable terms and conditions for the purchase. This is particularly important as language and cultural barriers can often pose challenges in international business dealings.
Moreover, agents and sourcing companies also play a crucial role in ensuring quality control. They conduct thorough background checks on manufacturers to verify their credentials and assess their production facilities. They may also arrange visits to the manufacturer’s facilities for the buyer to inspect the production process and ensure compliance with the required standards.
Additionally, agents and sourcing companies play a vital role in logistics and shipping. They handle the necessary documentation, customs clearance, and shipping arrangements, ensuring that the purchased goods are delivered safely and on time to the buyer’s location. This expertise in logistics saves the buyer from the complexities and hassles of international shipping.
In summary, agents and sourcing companies are essential facilitators in the multi jet fusion purchasing process from China. Their knowledge of the local market, ability to bridge communication gaps, and expertise in logistics and quality control contribute to a seamless and successful purchasing experience for buyers.
Price Cost Research for multi jet fusion manufacturers Companies in China, use temu.com and 1688.com
Multi Jet Fusion (MJF) is a popular 3D printing technology that is widely used in various industries. In China, there are several manufacturers specializing in the production of MJF machines. To gather price and cost data for these manufacturers, two popular online platforms can be utilized: temu.com and 1688.com.
Temu.com is a comprehensive online marketplace in China that offers a wide range of industrial machinery, including MJF machines. By utilizing the search function on temu.com and filtering the results to specifically include MJF manufacturers, one can find a list of companies that provide these machines. These listings often provide information on pricing, specifications, and contact details to directly reach out to the manufacturer for more detailed cost information.
1688.com, on the other hand, is a Chinese wholesale e-commerce platform owned by Alibaba. It is known for providing direct access to manufacturers and suppliers in China. By searching for MJF machines on 1688.com, one can find numerous suppliers offering various models at different price points. Contacting these suppliers through the platform or their provided contact information can yield further details, negotiate prices, and seek bulk order discounts.
When researching prices and costs on both temu.com and 1688.com, it is advisable to compare multiple manufacturers for the best pricing options. Additionally, analyzing the specifications and features offered by different manufacturers is essential to ensure the selected MJF machine meets the specific requirements.
It is important to note that while these online platforms can be helpful in obtaining initial price estimates, negotiation and other factors such as shipping costs, after-sales service, and warranty terms should be considered to determine the final cost of purchasing from a specific multi-jet fusion manufacturer in China.
In conclusion, temu.com and 1688.com are valuable resources for conducting price cost research on multi-jet fusion manufacturers in China. These platforms provide access to a range of MJF machines and allow direct communication with suppliers to gather detailed cost information.
Shipping Cost for multi jet fusion import from China
The shipping cost for importing multi jet fusion printers from China can vary depending on several factors. The primary factors that affect the shipping cost include the weight and dimensions of the package, the shipping method chosen, the distance between the origin and destination, as well as any additional services required.
When importing multi jet fusion printers, it is crucial to consider the weight and dimensions of the package. These printers can be heavy and bulky, which may increase the shipping cost. Freight companies typically charge based on the weight or volumetric weight, whichever is higher. Therefore, it is advisable to compare different shipping options to find the most cost-effective solution.
The shipping method chosen also impacts the cost. Air freight is generally faster but more expensive compared to sea freight. Air freight is suitable for urgent deliveries, while sea freight is more economical for larger shipments. However, it is important to consider the transit time when choosing the shipping method as it may affect the overall lead time of the import process.
The distance between China and the destination country also influences the shipping cost. Longer distances will generally result in higher shipping costs. Additionally, import duties, taxes, and customs clearance fees should be taken into account when calculating the overall import costs.
Lastly, any additional services required, such as insurance, packaging, or delivery to a specific location, will also add to the shipping cost. These services should be evaluated based on their necessity and cost-effectiveness.
In conclusion, the shipping cost for importing multi jet fusion printers from China varies depending on the weight and dimensions of the package, shipping method chosen, distance, and additional services required. It is crucial to thoroughly compare different shipping options and consider all relevant factors to ensure a cost-effective and timely import process.
Compare China and Other multi jet fusion Markets: Products Quality and Price,Visible and Hidden Costs
China has emerged as a major player in the multi jet fusion (MJF) market, competing with other global players such as the United States and Germany. When comparing China with other MJF markets, several factors can be considered, including product quality and price, visible and hidden costs.
In terms of product quality, China has made significant strides in recent years. Chinese manufacturers have invested heavily in research and development, resulting in improved product quality and capabilities. Many Chinese MJF machines now rival their global counterparts in terms of precision, resolution, and surface finish. However, it is worth noting that there may still be variations in quality among different Chinese manufacturers, and some international brands are still perceived to have an edge in this area due to their long-standing reputation and expertise.
Price is another significant factor in the MJF market. China has a reputation for offering competitive pricing across various industries, including 3D printing. Chinese manufacturers often have cost advantages due to lower labor and production costs, which can translate into affordable MJF machines. This competitive pricing has enabled China to gain traction in both domestic and international markets, appealing to budget-conscious customers.
When considering visible costs such as the initial purchase price, China’s offerings, including the machines themselves and associated accessories, tend to be relatively affordable compared to some international counterparts. However, it is important to consider hidden costs such as maintenance, training, and support. In some cases, international brands may have a more established network of trained technicians and better customer support, which can influence the overall cost of ownership. Additionally, while Chinese companies have made progress in this area, some customers may still have concerns about the reliability and durability of Chinese MJF machines over the long run.
In summary, China has become a formidable player in the MJF market, offering competitive pricing and improved product quality. Chinese manufacturers have narrowed the gap with international brands, but variations in quality and customer support still exist. Customers evaluating their options should consider both visible and hidden costs to make an informed decision.
Understanding Pricing and Payment Terms for multi jet fusion: A Comparative Guide to Get the Best Deal
When considering the purchase or use of a multi jet fusion (MJF) machine, it is essential to understand the pricing and payment terms to secure the best possible deal. This comparative guide aims to provide insights into the factors affecting pricing and payment options for MJF technology, all within a concise 300 words.
Pricing for MJF machines can vary significantly depending on several factors. These include the machine’s configuration, build volume, speed, and additional features. It is crucial to compare prices from different manufacturers or suppliers to ensure the best deal. Some companies may offer package deals that include maintenance, training, and software updates, while others may charge separately for these services.
Payment terms for MJF machines can also differ across suppliers. Generally, payment options include upfront payment, lease agreements, or financing arrangements. Upfront payment means purchasing the machine outright, which may result in higher initial costs but lower overall expenses. Leasing allows for regular payments over a fixed period, providing flexibility and potential tax benefits. Financing options enable businesses to spread out payments over time, minimizing the immediate financial impact.
When analyzing pricing and payment terms, it is crucial to consider the total cost of ownership (TCO) rather than solely focusing on the machine price. TCO factors in operational costs, material expenses, maintenance, and potential downtime. By evaluating TCO, businesses can better assess the long-term financial implications of owning an MJF machine.
Negotiating with suppliers can also help achieve the best deal. Seek transparency regarding additional costs, such as warranty extensions, spare parts, or consumables. Understanding the supplier’s pricing structure, volume-based discounts, or loyalty incentives may provide leverage during negotiations.
Additionally, considering the supplier’s reputation, customer service, and the availability of technical support is vital. Investing in a reliable supplier with hands-on support can ensure smooth operations and minimize potential financial losses due to machine downtime.
To conclude, understanding pricing and payment terms is crucial when acquiring MJF technology. Compare prices, evaluate payment options, consider TCO, and negotiate with suppliers to secure the best deal. Additionally, prioritize suppliers offering quality support and services to protect your investment and ensure long-term success.
Chinese Regulations and Industry Standards Certifications for multi jet fusion,Import Regulations and Customs for multi jet fusion from China
Chinese Regulations and Industry Standards Certifications for multi jet fusion:
In China, the multi jet fusion (MJF) technology is regulated by various industry standards and certifications to ensure quality and safety. One of the key standards is the GB/T standard, which covers the general requirements for additive manufacturing processes, materials, and equipment. This standard sets guidelines for the manufacturing process, parameter optimization, and material specifications to guarantee the reliability and consistency of MJF products.
Additionally, there are specific certifications required for MJF equipment and materials. The China Compulsory Certification (CCC) mark is mandatory for certain categories of products, including machinery and electrical devices, to enter the Chinese market. Therefore, MJF equipment must comply with the CCC certification requirements to meet safety and quality standards.
Moreover, the ISO 9001 certification is essential for manufacturers of MJF equipment and materials, as it demonstrates their adherence to quality management systems. This certification ensures that the production processes, quality control, and customer satisfaction are all effectively managed.
Import Regulations and Customs for multi jet fusion from China:
When importing MJF equipment or materials from China, it is crucial to comply with the import regulations and customs procedures to avoid any delays or complications. Firstly, a detailed description of the MJF product and its specifications must be provided for customs declaration.
Customs duties and taxes depend on the classification of the product under the Harmonized System (HS) codes. The importer needs to determine the correct HS code for the MJF equipment or materials to calculate the applicable duties and taxes accurately.
Furthermore, it is necessary to obtain an Import License, which can be obtained from the appropriate government department. This license assures that the MJF products meet the necessary safety and quality standards and are allowed to enter China.
Proper documentation, including commercial invoices, bill of lading, packing lists, and certificates of compliance, is required for customs clearance. The goods may also undergo inspections by the relevant authorities to ensure conformity to regulations.
In conclusion, adherence to Chinese regulations and industry standards certifications is paramount when dealing with multi jet fusion technology. When importing MJF equipment or materials from China, compliance with import regulations and customs procedures is crucial to ensure successful clearance and entry into the market.
Sustainability and Environmental Considerations in multi jet fusion Manufacturing
Multi jet fusion (MJF) manufacturing is an additive manufacturing process that allows for the creation of complex and highly detailed parts using a variety of materials. While MJF offers numerous advantages in terms of speed, precision, and design flexibility, it is essential to consider the sustainability and environmental implications of this manufacturing technique.
One of the key sustainability benefits of MJF is the reduction in material waste. Compared to traditional subtractive manufacturing processes, MJF minimizes material waste by only using the required amount of material to build each part. This is achieved by spreading a thin layer of powdered material and selectively fusing it where needed, resulting in significantly less material waste compared to conventional manufacturing methods.
Moreover, MJF enables the reuse and recycling of unused powdered material, further enhancing its sustainability profile. Any leftover material from the build process can be collected, sieved, and reused for future manufacturing runs, eliminating unnecessary waste and optimizing resource utilization.
In terms of energy consumption, MJF is relatively energy-efficient compared to other manufacturing techniques. The use of infrared lamps to selectively fuse the powdered material requires less energy compared to high-temperature heating required in other additive manufacturing processes. Additionally, the ability to build multiple parts simultaneously in the MJF chamber allows for higher production rates, minimizing energy consumption per part.
From an environmental perspective, the materials used in MJF should be carefully considered. Selecting sustainable and eco-friendly materials, such as biodegradable or recyclable powders, can further enhance the environmental advantages of this manufacturing technique.
It is worth noting that the sustainability and environmental considerations of MJF can be optimized by integrating circular economy principles into the manufacturing process. This includes designing products for disassembly and reusability, utilizing recycled materials, and implementing closed-loop material management systems.
In conclusion, while multi jet fusion manufacturing offers numerous advantages, it is crucial to address sustainability and environmental considerations. By minimizing material waste, reusing and recycling materials, optimizing energy consumption, and selecting eco-friendly materials, MJF can contribute to a more sustainable and environmentally friendly manufacturing industry.
List The Evolution history of “multi jet fusion”
Multi Jet Fusion (MJF) is a 3D printing technology developed by Hewlett-Packard (HP) that utilizes a combination of inkjet printing and powder-based additive manufacturing. The evolution of MJF can be traced through four key phases, from its initial development in 2016 to its growing impact on the additive manufacturing industry today.
1. Development Phase:
In 2016, HP introduced Multi Jet Fusion technology, aiming to revolutionize the 3D printing industry. It combined thermal inkjet arrays with an agent deposition system and an infrared heating source, enabling precise and rapid 3D printing. The technology laid the foundation for high-resolution, high-speed, and cost-effective production of functional parts.
2. Expansion Phase:
As MJF gained traction, HP expanded its capabilities. In 2017, they introduced the 3D Jet Fusion 4210, a commercial production system that offered higher productivity and reduced costs per part. This advancement made MJF more accessible to businesses looking for cost-effective and scalable manufacturing solutions.
3. Material and Color Expansion:
In 2018, HP unveiled the 3D Jet Fusion 300/500 series, expanding the possibilities of MJF to full-color 3D printing. By incorporating color voxel control technology, this advancement allowed the production of vibrant, detailed, and multi-colored parts, opening doors to new applications in product design and customization.
4. Open Material Platform:
To further enhance the versatility of MJF, HP introduced the open materials platform in 2019. This allowed third-party materials manufacturers to develop and certify compatible materials for MJF technology. By embracing an open approach, HP encouraged collaboration and innovation within the 3D printing ecosystem, expanding the range of materials available for MJF and providing users with more options for functional prototyping and production applications.
Today, Multi Jet Fusion technology continues to evolve, with ongoing research and development focused on increasing print speeds, improving material properties, enabling larger build volumes, and enhancing post-processing techniques. The evolution of MJF highlights HP’s commitment to advancing additive manufacturing, making it more accessible, efficient, and capable of producing high-quality parts for various industries, including automotive, aerospace, and healthcare.
The Evolution and Market Trends in multi jet fusion Industry
Multi jet fusion (MJF) is a 3D printing technology that has significantly evolved and gained traction in various industries over the years. Developed by HP, MJF utilizes inkjet arrays to selectively apply fusing and detailing agents onto powdered materials, resulting in highly precise and functional 3D printed objects. This innovative technology addresses many limitations of traditional manufacturing processes, leading to its increasing adoption and market growth.
The evolution of multi jet fusion has been driven by constant improvements in printer capabilities, material availability, and software advancements. Initially, MJF was primarily used for rapid prototyping, enabling faster production and iteration of product designs. However, with advancements in printer speed and refinement, MJF has transitioned into a viable solution for low-volume production. The ability to print multiple parts simultaneously, without compromising on quality or speed, has made MJF an attractive option for small-scale manufacturing.
One of the prominent market trends in the multi jet fusion industry is the expansion of material options. Initially limited to a few plastic materials, MJF now supports a wide range of materials, including nylon, elastomers, and metals. This diversification of materials has broadened the applicability of MJF across industries, catering to various product requirements. Furthermore, advancements in material development and testing have improved the mechanical properties and overall performance of MJF printed parts, making them suitable for end-use applications.
Another significant market trend is the integration of MJF with digital manufacturing ecosystems. Software advancements have enabled seamless integration of MJF printers with design and production workflows, allowing for greater automation and efficiency. This integration simplifies the process of converting digital designs into physical objects, facilitating mass customization and on-demand manufacturing. Such capabilities are highly valued by industries seeking to optimize supply chains and reduce inventory costs.
Overall, the multi jet fusion industry has experienced substantial growth and innovation, primarily driven by advancements in printer capabilities, material options, and software integration. This technology has proven to be a versatile and efficient solution, enabling faster prototyping and production cycles, while offering a wide range of material choices. As industries continue to embrace additive manufacturing, multi jet fusion is anticipated to play a pivotal role in shaping the future of manufacturing processes.
Custom Private Labeling and Branding Opportunities with Chinese multi jet fusion Manufacturers
Chinese multi jet fusion manufacturers offer custom private labeling and branding opportunities for businesses looking to create their own unique products. With multi jet fusion technology, these manufacturers can produce high-quality and precise 3D printed items, ranging from small accessories to large industrial parts.
The process begins by collaborating with the manufacturer to design and develop the desired product. This can involve sharing specifications, sketches, or digital files. The manufacturer’s experienced team can provide insights and suggestions to optimize the design and ensure it meets the desired requirements.
Once the design is finalized, the manufacturer will produce a sample for the client’s approval. This step allows for any necessary adjustments or improvements to be made before proceeding with mass production. The manufacturing facility is equipped with state-of-the-art printers and advanced materials to ensure the highest quality and accuracy of the printed products.
When it comes to private labeling and branding, Chinese multi jet fusion manufacturers offer various options. Clients can choose to have their logo, company name, or any other branding elements incorporated into the product design itself. This can be achieved through embossing, engraving, or adding custom textures. Additionally, manufacturers can apply custom labels or tags on the packaging to reinforce brand identity.
By taking advantage of these opportunities, businesses can differentiate themselves in the market and strengthen their brand recognition. Custom private labeling and branding allow for exclusivity and create a unique selling point for the products. Furthermore, manufacturing in China provides cost-efficiency without compromising quality, making it an attractive option for businesses of all sizes.
In conclusion, Chinese multi jet fusion manufacturers offer extensive opportunities for custom private labeling and branding. Through collaboration, high-quality printing, and a range of customization options, businesses can create their own unique products that align with their brand identity. With its competitive advantages, manufacturing in China is a viable solution for companies looking to meet their branding goals while maintaining cost-effectiveness.
Tips for Procurement and Considerations when Purchasing multi jet fusion
When considering the purchase of a multi jet fusion (MJF) system for your procurement needs, there are several important factors to take into consideration. Here are some tips and considerations to keep in mind:
1. Research and evaluate the available options: There are multiple suppliers offering MJF systems, so it is crucial to research and compare different options. Look for reliable suppliers with a good track record and positive customer feedback.
2. Analyze your requirements: Determine your specific needs and requirements for the MJF system. Consider factors such as production volume, material compatibility, part size, and turnaround time. This will help you identify the most suitable system for your needs.
3. Understand the cost implications: MJF systems come with upfront costs, including the purchase price and installation fees. Additionally, consider the ongoing costs of materials, maintenance, and potential upgrades. Evaluate the potential return on investment (ROI) based on your procurement needs and projected savings.
4. Consider the versatility and scalability: Ensure that the MJF system you choose is versatile enough to accommodate your current and future procurement requirements. It should be able to handle multiple materials and offer scalability options to accommodate increased production volumes.
5. Assess the quality and reliability: Look for MJF systems that offer high-quality output and reliable performance. Check for the system’s build resolution, dimensional accuracy, and consistency across multiple runs. It is also essential to consider the supplier’s customer support and warranty options.
6. Evaluate post-processing requirements: Understand the post-processing requirements for the MJF system. Some systems may require additional steps such as powder removal, cleaning, and curing. Consider these factors and their impact on your procurement operations.
7. Training and support: Ensure that the supplier provides comprehensive training for your staff to operate the MJF system effectively. Additionally, inquire about the availability of technical support and service options.
8. Environmental considerations: Consider the environmental impact of the MJF system, such as energy consumption and waste generation. Opt for systems that have energy-efficient features and sustainable material usage.
9. Seek references and testimonials: Request references from the supplier to connect with existing customers who can provide feedback on the system’s performance and the supplier’s reliability.
10. Plan for integration: Evaluate how the MJF system will integrate into your existing procurement and supply chain processes. Consider any necessary modifications or adaptations required to streamline the entire workflow.
By carefully considering these tips and factors, you can make an informed decision when purchasing a multi jet fusion system for your procurement needs.
FAQs on Sourcing and Manufacturing multi jet fusion in China
Q1: What is multi jet fusion (MJF) technology?
A: Multi jet fusion is an additive manufacturing technique that uses inkjet arrays to selectively deposit fusing and detailing agents onto a powder bed. The powdered material is then fused together using an infrared energy source, resulting in the creation of complex and durable three-dimensional objects.
Q2: Why source and manufacture MJF products in China?
A: China is known for its robust manufacturing capabilities and cost-effective production processes. Sourcing and manufacturing MJF products in China can provide access to a large pool of skilled labor, advanced machinery, and an extensive supply chain. Additionally, China’s strong infrastructure and experience in technology manufacturing make it an attractive option for producing high-quality MJF products at competitive prices.
Q3: How can I find reliable suppliers of MJF in China?
A: To find reliable MJF suppliers in China, you can leverage various sourcing platforms and online directories such as Alibaba, Made-in-China, or Global Sources. These platforms enable you to connect directly with potential suppliers, review their product catalogs, and read customer reviews and ratings for better decision-making. It is advisable to conduct thorough due diligence by requesting samples, visiting production facilities, and assessing the supplier’s qualifications before finalizing any agreements.
Q4: Are there any challenges in sourcing and manufacturing MJF in China?
A: While China offers numerous advantages, there are some challenges to consider. Language and cultural barriers may arise during communication and negotiation with suppliers. Intellectual property protection is another concern, so it’s crucial to work with reputable suppliers and consider legal measures like non-disclosure agreements. Quality control and managing production schedules can also be challenging, necessitating regular inspections and clear contractual agreements.
Q5: How can I ensure quality control during the manufacturing process of MJF products in China?
A: To ensure quality control, it is essential to establish clear specifications, requirements, and quality standards with your chosen supplier. Regular inspections during manufacturing, random product testing, and thorough pre-shipment inspections can help identify and correct any production issues. It is recommended to work with third-party quality assurance agencies that specialize in manufacturing audits and inspections to ensure compliance with international quality standards.
In conclusion, sourcing and manufacturing multi jet fusion products in China can offer cost-effective production and access to advanced manufacturing capabilities. However, it is crucial to conduct thorough due diligence, establish clear communication channels, and implement robust quality control measures to ensure successful operations.
Why contact sourcifychina.com get free quota from reliable multi jet fusion suppliers?
Sourcifychina.com is likely to get a free quota from reliable multi jet fusion suppliers due to several reasons. Firstly, offering a free quota allows the suppliers to attract potential customers and showcase their capabilities. By providing a limited amount of free service, the suppliers can demonstrate the quality and efficiency of their multi jet fusion process, hoping to convert recipients into long-term paying customers.
Moreover, offering a free quota can help the suppliers gain an edge over their competitors. In the highly competitive manufacturing industry, it is essential for suppliers to stand out and differentiate themselves. By providing a free quota, the suppliers can create a positive impression, build relationships with potential clients, and potentially gain a competitive advantage.
Additionally, providing a free quota may be a strategic marketing tactic for the suppliers. By offering a limited amount of free service, the suppliers can collect valuable data and feedback from the recipients. This information can be used to improve their processes, identify any potential issues, and refine their services.
Furthermore, providing a free quota can be seen as a gesture of goodwill and trust-building. It allows the suppliers to demonstrate their commitment to customer satisfaction and their willingness to invest in potential clients. By offering a free quota, the suppliers may be aiming to establish a positive reputation and foster long-term partnerships.
In conclusion, offering a free quota by reliable multi jet fusion suppliers to sourcifychina.com is a strategic move to attract potential customers, gain a competitive advantage, gather valuable feedback, and build trust and goodwill. It serves as a means for the suppliers to showcase their capabilities and establish long-term relationships with potential clients.