Introduce about panel manufacturing guide,Qulity,Cost,Supplier,Certification,Market,Tips,FAQ
The Panel Manufacturing Guide is a comprehensive resource that provides information and guidelines for the production of high-quality panels. It covers various aspects such as quality control, cost management, supplier selection, certifications, market analysis, helpful tips, frequently asked questions (FAQs), and much more.
Quality is of utmost importance in panel manufacturing. The guide emphasizes the adoption of rigorous quality control procedures to ensure the panels meet or exceed industry standards. It outlines the various quality checks and tests that should be conducted at different stages of the manufacturing process.
Cost management is another crucial aspect covered in the guide. It provides strategies and techniques to optimize costs without compromising the quality of the panels. This includes efficient material sourcing, production planning, and minimizing waste.
Selecting reliable suppliers is paramount in ensuring the success of panel manufacturing. The guide offers valuable insights into evaluating potential suppliers based on their reputation, experience, and ability to meet quality and delivery requirements.
Certifications play a significant role in gaining credibility and expanding market opportunities. The guide provides an overview of relevant certifications, such as ISO standards, and guidance on the certification process.
Market analysis featured in the guide enables manufacturers to understand industry dynamics, identify potential growth opportunities, and adapt their strategies accordingly.
Additionally, the guide offers practical tips and best practices to enhance panel manufacturing efficiency, improve product quality, and maximize profitability. It addresses common challenges and provides solutions to ensure smooth operations throughout the manufacturing process.
Frequently asked questions (FAQs) section in the guide addresses common queries of manufacturers, providing clear and concise answers to assist them in making informed decisions.
In summary, the Panel Manufacturing Guide is an invaluable resource that equips manufacturers with essential knowledge and guidance to produce high-quality panels, manage costs, choose reliable suppliers, obtain certifications, navigate the market, and implement effective manufacturing practices.
Types of panel manufacturing
Panel manufacturing involves the production of various types of panels that serve different purposes in industries such as construction, automotive, electronics, and furniture. There are several types of panel manufacturing processes:
1. Wood-based Panel Manufacturing: Wood-based panels are manufactured from wood fibers or particles bonded together with adhesive under high temperature and pressure. Common examples include plywood, particleboard, and medium-density fiberboard (MDF). These panels are lightweight, durable, and widely used in construction, furniture, and cabinetry.
2. Metal Panel Manufacturing: Metal panels are produced by shaping and reshaping metal sheets through processes such as rolling, pressing, stamping, and welding. They are commonly used in construction for roofing, cladding, and wall systems. Metal panels offer high strength, durability, and fire resistance.
3. Plastic Panel Manufacturing: Plastic panels are manufactured using extrusion, injection molding, or vacuum forming processes. They are used in various industries, including automotive, electronics, signage, and packaging. Plastic panels are lightweight, versatile, and can be molded into complex shapes.
4. Glass Panel Manufacturing: Glass panels are produced through processes such as float glass manufacturing, lamination, and tempering. They are widely used in the construction industry for windows, doors, facades, and partitions. Glass panels provide transparency, aesthetic appeal, and insulation properties.
5. Composite Panel Manufacturing: Composite panels are manufactured by combining two or more materials to create a panel with enhanced properties. Examples include aluminum composite panels (ACP) consisting of aluminum sheets bonded to a polyethylene core. Composite panels offer a combination of strength, lightweight, and design flexibility.
6. Solar Panel Manufacturing: Solar panels are fabricated using photovoltaic (PV) cells that convert sunlight into electricity. PV cells are typically made of semiconductor materials such as silicon and are assembled into panels with protective glass and encapsulation. Solar panels are used for renewable energy generation in residential, commercial, and industrial applications.
Panel manufacturers utilize advanced technologies and machinery to produce panels with specific dimensions, shapes, and properties. These manufacturing processes ensure consistent quality, efficiency, and cost-effectiveness in the production of panels for various applications.
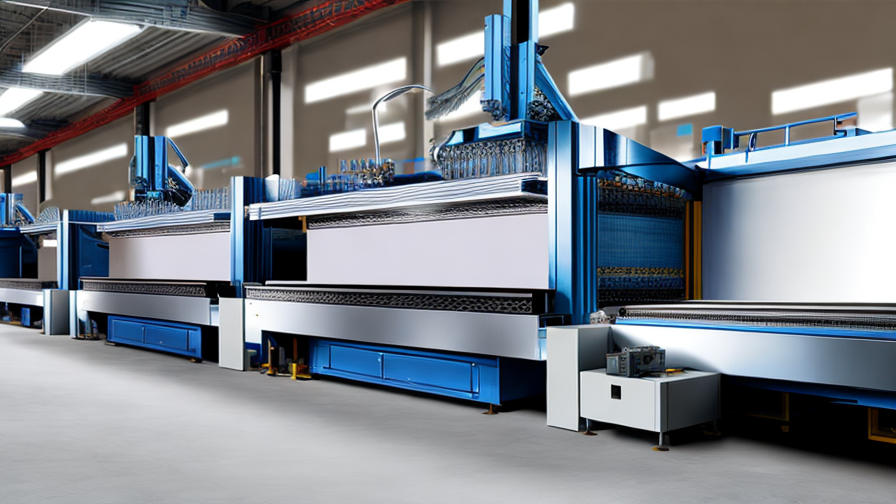
Pros and Cons of Using panel manufacturing
Panel manufacturing refers to the process of creating large flat structures, often made of wood or composite materials. These panels are commonly used in the construction industry for various applications, such as roofing, flooring, and wall systems. Like any other manufacturing method, panel manufacturing has its own set of pros and cons.
Pros of Panel Manufacturing:
1. Efficiency: One of the biggest advantages of panel manufacturing is its efficiency. Panels can be mass-produced in a controlled factory environment using automated machinery. This allows for a streamlined and efficient production process, reducing construction time and labor costs.
2. Quality control: Panel manufacturing enables strict quality control measures. Since the process is carried out in a controlled environment, manufacturers can closely monitor and regulate the production, ensuring consistent quality and reducing the likelihood of defects or errors during construction.
3. Sustainability: Many panel manufacturing processes prioritize sustainability. By using recycled materials and optimizing the use of resources, panel manufacturing can contribute to reducing waste and minimizing environmental impact.
4. Versatility: Panels can be customized to fit specific requirements, allowing for a wide range of applications. They can be designed as structural or non-structural elements, with various finishes and insulation options, providing flexibility to architects and builders.
Cons of Panel Manufacturing:
1. Transportation costs: Panel manufacturing usually entails transporting the finished panels to the construction site. This can result in high transportation costs, especially for large and bulky panels. Additionally, long transportation distances may increase the carbon footprint of the project.
2. Limited design flexibility: While panels offer versatility, they may have limitations in terms of design flexibility. Complex architectural designs that require intricate detailing and unique shapes may not be easily achieved with panel manufacturing methods.
3. Initial investment: Setting up a panel manufacturing facility requires a significant initial investment in machinery, infrastructure, and skilled labor. This can be a barrier for small-scale or individual construction projects, as the cost may outweigh the benefits.
4. Maintenance and repair: In the case of damage or wear, panels may require specialized repair techniques or replacement. This can be more challenging than repairing traditional construction methods since panel systems are often prefabricated and interconnected.
In conclusion, panel manufacturing offers efficiency, quality control, sustainability, and versatility benefits. However, transportation costs, limited design flexibility, initial investment, and potential maintenance challenges should be considered as drawbacks. Each project should evaluate these pros and cons to determine if panel manufacturing aligns with their specific needs and priorities.
panel manufacturing Reference Specifications (varies for different product)
Panel manufacturing reference specifications can vary depending on the specific product being produced. However, there are some common specifications that are considered in the manufacturing process.
Firstly, the dimensions of the panel are a critical factor to consider. This includes the length, width, and thickness of the panel. The dimensions are usually determined based on the intended use of the panel and the structural requirements. These dimensions must be within certain tolerances to ensure the quality and functionality of the panel.
The material used in panel manufacturing is another important specification. Different materials can be used depending on the desired properties of the panel. Common materials include metals, such as steel or aluminum, as well as various types of wood or composite materials. The choice of material depends on factors like strength, durability, weather resistance, and cost.
Surface finish is another specification that must be considered. This refers to the type of coating or treatment applied to the panel’s surface. The surface finish can enhance the panel’s appearance and protect it from corrosion, UV radiation, or other external factors. Common surface finishes include powder coating, paint, or laminate.
The panel manufacturing process also involves determining the design and layout of any patterns or textures on the panel’s surface. This is important for aesthetic purposes or for specific functional requirements.
Various mechanical and physical properties are considered during panel manufacturing. These include factors such as tensile strength, bending strength, thermal insulation, fire resistance, and sound absorption. These properties are essential for ensuring that the panel meets the required standards and performs adequately for its intended application.
Additional specifications may include electrical conductivity, weight, acoustic performance, flammability rating, and environmental sustainability. These specifications vary depending on the specific product and its intended use.
In conclusion, panel manufacturing reference specifications cover a wide range of factors. These include dimensions, material selection, surface finish, design features, mechanical and physical properties, as well as other specific requirements for the intended application. By adhering to these specifications, manufacturers can produce panels that meet the necessary standards and provide reliable performance.
Applications of panel manufacturing
Panel manufacturing is a versatile industry that produces a wide range of panels used in various applications across different sectors. The following are some of the key applications of panel manufacturing:
1. Construction: Panels are extensively used in the construction industry for building interiors and exteriors. Plywood panels, for example, are commonly used for flooring, roofing, wall sheathing, and formwork. They offer strength, durability, and ease of installation.
2. Furniture and cabinetry: Panels play a crucial role in the manufacturing of furniture and cabinetry. Medium-density fiberboard (MDF) and particleboard panels are often used as a substrate for veneer, laminate, or paint finishes. These panels provide a smooth and uniform surface, allowing for intricate designs and customizations.
3. Automotive industry: Panels are integral to the production of automobiles. They are used in the interior trim, doors, body panels, dashboards, and more. Automotive panels need to be lightweight, durable, and have excellent aesthetic qualities. Different types of composites and composites reinforced with natural fibers are often used due to their high strength-to-weight ratio.
4. Electronics and electrical equipment: Panels are used in the manufacturing of electronic devices and electrical equipment such as control panels, switchboards, and circuit boards. These panels are made from materials that provide electrical insulation, fire resistance, and mechanical support. The manufacturing process focuses on precision and reliability.
5. Renewable energy: Manufactured panels are an important component of renewable energy systems. Solar panels, for instance, comprise photovoltaic cells that convert sunlight into electricity. These panels are typically made using silicon, glass, or other semiconductor materials. Wind turbine blades, another example, are manufactured using composite panels designed to withstand high winds and stresses.
6. Cold storage and refrigeration: Insulated panels are widely used in cold storage facilities, refrigerators, and freezers. They provide a thermal barrier to maintain the desired temperature and prevent heat transfer. These panels are made with materials that offer excellent insulation properties, such as rigid polyurethane foam or other insulating materials.
7. Aerospace industry: Panels are crucial for aircraft and spacecraft manufacturing. They are used for structural purposes, such as wings, fuselage, and interior components. Aerospace panels are made from lightweight materials like aluminum alloys, carbon fiber-reinforced composites, or titanium, which offer high strength and withstand extreme conditions.
In conclusion, panel manufacturing is a critical industry that finds applications in construction, furniture, automotive, electronics, renewable energy, cold storage, and aerospace sectors. With ongoing advancements in materials and manufacturing processes, panel manufacturers continue to contribute to various industries by providing innovative solutions for diverse applications.
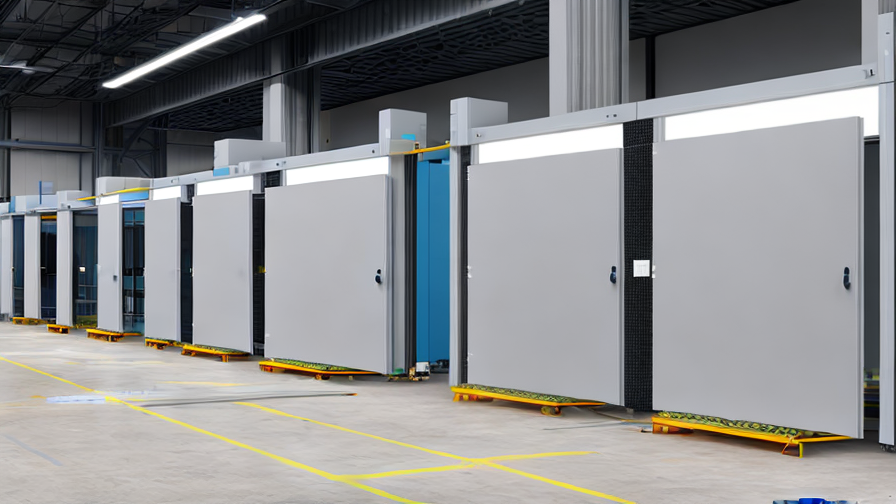
The Work Process and how to use panel manufacturing
Panel manufacturing refers to the process of producing panels made of different materials such as wood, metal, or plastic, which are commonly used in various industries and applications. The work process involves a series of steps, which include design, material selection, cutting, shaping, assembly, and finishing.
The first step in panel manufacturing is the design phase. This involves determining the specific dimensions, shape, and features required for the panel. The design is typically created using computer-aided design (CAD) software, which allows for precise measurements and specifications.
Once the design is finalized, the next step is material selection. The choice of material depends on factors such as the panel’s intended use, desired strength, durability, and cost. Wood, metal, and plastic are the most commonly used materials in panel manufacturing. Each material has its own set of advantages and disadvantages, and it is important to select the one that best meets the requirements of the panel.
After material selection, the manufacturing process begins with cutting the selected material to the required dimensions. This can be achieved using various cutting techniques, such as sawing, laser cutting, or waterjet cutting. Precision is crucial during this stage to ensure accurate panel dimensions.
The cut panels are then shaped and formed according to the design specifications. This may involve processes such as bending, molding, or pressing. These shaping techniques help achieve the desired curvature or contour of the panel.
Once the panel components are ready, they are assembled together using various techniques. This involves joining the different parts of the panel securely, either through adhesive bonding, screwing, welding, or other fastening methods. The assembly process ensures the structural integrity and stability of the panel.
Finally, the assembled panel undergoes finishing processes to enhance its appearance and functionality. This typically involves sanding, painting, varnishing, or applying protective coatings to improve the panel’s aesthetic appeal and protect it from external factors such as moisture or UV radiation.
In conclusion, panel manufacturing involves a series of steps, including design, material selection, cutting, shaping, assembly, and finishing. By following these processes, manufacturers can produce high-quality panels that meet specific requirements for various industries and applications.
Quality Testing Methods for panel manufacturing and how to control the quality
Quality testing methods for panel manufacturing include various techniques and procedures aimed at ensuring that the panels meet the required standards and specifications. These methods generally involve both visual inspections and functional tests to assess the quality of manufactured panels.
Visual inspections are conducted to identify any visible defects or imperfections in the panels. This may involve checking for surface defects such as scratches, dents, or discoloration. Additionally, visual inspections can also include verifying the accuracy of panel dimensions, alignment, and overall appearance.
Functional tests are performed to evaluate the performance and functionality of the panels. These tests can include assessing the electrical conductivity, insulation resistance, and dielectric strength of the panels. Other functional tests may involve checking the load-bearing capacity, structural integrity, and resistance to environmental factors such as temperature, humidity, or vibration.
To control the quality of panel manufacturing, various measures can be implemented. Firstly, implementing comprehensive quality control processes throughout the manufacturing process is vital. This includes establishing quality checkpoints at each stage, ensuring that only defect-free materials are used, and monitoring the manufacturing parameters closely.
Furthermore, regular training programs can be conducted to educate the manufacturing staff on quality standards and proper manufacturing techniques. This will help in minimizing human error and ensuring consistency in the production process.
Collaborating with reliable suppliers for raw materials is another imperative aspect of quality control. This ensures that the materials used in panel manufacturing meet the required standards and are of high quality.
Incorporating automated testing equipment and technologies can also significantly improve quality control. These technologies can provide more accurate and reliable measurements, reducing human error and improving the overall testing efficiency.
Moreover, implementing a comprehensive quality management system that complies with international standards (e.g., ISO 9001) can help in establishing effective quality control practices. This involves documenting processes, conducting regular audits, and continuously improving the manufacturing processes based on feedback and data analysis.
By combining visual inspections, functional tests, strict quality control measures, staff training, reliable suppliers, automated testing, and an effective quality management system, manufacturers can ensure the production of high-quality panels that meet the required standards and customer expectations.
panel manufacturing Sample Policy and Post-Purchase Considerations for panel manufacturing from China
Sample Policy for Panel Manufacturing from China:
1. Quality Assurance:
– Before placing an order, request a sample to assess the quality of the panels.
– Insist on inspecting the production facility to ensure it meets your quality standards.
– Include clauses in the contract specifying the acceptable quality levels and penalties for non-compliance.
2. Competitive Pricing:
– Compare prices from multiple manufacturers to ensure you are getting the best deal.
– Negotiate bulk discounts for large orders or long-term partnerships.
– Be cautious of excessively low prices, as they may indicate compromised quality.
3. Timely Delivery:
– Set clear timelines with the manufacturer and incorporate them into the contract.
– Ask for regular updates on the production progress and shipping status.
– Add penalties for delayed delivery to encourage timely fulfillment.
4. Intellectual Property Protection:
– Ensure the manufacturer is committed to protecting your intellectual property rights.
– Sign a Non-Disclosure Agreement (NDA) to safeguard your proprietary information.
– Verify the manufacturer’s reputation and credibility in terms of IP protection.
Post-Purchase Considerations:
1. Product Inspection:
– Upon receiving the shipment, conduct a thorough inspection to check for any damages or defects.
– Report any issues immediately to the manufacturer, providing photographic evidence if necessary.
– Follow the agreed-upon procedures for returns or replacements.
2. Customer Support:
– Establish clear lines of communication with the manufacturer for ongoing support.
– Promptly address any queries or concerns regarding the panels’ performance or maintenance.
– Maintain a long-term relationship for future cooperation and assistance.
3. Feedback and Reviews:
– Share your experience with the manufacturer on reputable online platforms or industry forums.
– Provide constructive feedback to help them improve their services and products.
– Read and consider other customers’ reviews to make informed decisions in the future.
4. Continuous Improvement:
– Regularly assess the quality and performance of the panels against your expectations.
– Identify areas for improvement and communicate them with the manufacturer.
– Work collaboratively to enhance the product specifications or manufacturing processes.
By implementing these policies and considerations, you can mitigate risks and ensure a successful panel manufacturing experience from China.
Sourcing panel manufacturing from China: Opportunities, Risks, and Key Players
Sourcing panel manufacturing from China offers various opportunities for businesses, but it also comes with certain risks. This article aims to provide an overview of the opportunities and risks associated with sourcing panel manufacturing from China, along with key players in the industry.
Opportunities:
1. Cost-effectiveness: China is known for its low labor and production costs, making it an attractive option for businesses seeking cost-effective panel manufacturing solutions.
2. Wide range of suppliers: China has a vast number of panel manufacturers, offering a wide range of options in terms of technologies, materials, and product quality.
3. Technological advancements: Chinese panel manufacturers have made significant strides in technology, making them competitive in terms of product innovation and development.
4. Supply chain integration: China has a well-established and efficient supply chain that facilitates the sourcing of raw materials and other components required for panel manufacturing.
Risks:
1. Quality control: Maintaining consistent product quality can be a challenge in China, as some manufacturers may prioritize cost-cutting over quality. Thorough due diligence and regular quality checks are necessary to mitigate this risk.
2. Intellectual property protection: Intellectual property rights infringement is a concern, as there have been cases of counterfeiting and unauthorized production in China. Protecting intellectual property through legal agreements and patents is crucial.
3. Communication and language barriers: Language differences and communication gaps can lead to misunderstandings and delays in production. Effective communication channels and clear specifications are vital to overcome this challenge.
4. Supply chain disruptions: The long distance between China and other global markets may lead to supply chain disruptions due to factors like natural disasters, political unrest, or logistical issues.
Key Players:
1. BOE Technology Group Co., Ltd.: A leading panel manufacturer in China, BOE specializes in the production of LCD panels, OLED panels, and display modules.
2. Tianma Microelectronics Co., Ltd.: Tianma is known for its advanced display technologies, providing LCD panels, LTPS-TFT panels, and AMOLED panels.
3. Innolux Corporation: Innolux is a prominent manufacturer of TFT-LCD panels, offering a wide range of sizes and resolutions for various applications.
4. China Star Optoelectronics Technology (CSOT): CSOT focuses on producing innovative display products, including LCD and AMOLED panels.
In conclusion, while sourcing panel manufacturing from China presents opportunities such as cost-effectiveness, technological advancements, and a wide range of suppliers, it also carries risks like quality control, intellectual property protection, communication barriers, and supply chain disruptions. Understanding these factors and collaborating with reliable key players can help businesses navigate and leverage the benefits of sourcing from China’s panel manufacturing industry.
How to find and select reliable panel manufacturing manufacturers in China,use google search manufacturers and suppliers
When looking to find and select reliable panel manufacturing manufacturers in China, using Google search can be an effective method. Here are some steps to follow:
1. Begin by conducting a basic search using keywords related to panel manufacturing in China, such as “panel manufacturers China” or “panel suppliers China.”
2. Review the search results and visit the websites of potential manufacturers. Look for reputable companies with well-designed websites that provide detailed information about their products, manufacturing processes, and certifications.
3. Pay attention to the manufacturer’s experience in the industry. Look for companies that have been in operation for a substantial period and have a proven track record of delivering quality products.
4. Check if the manufacturer has the necessary certifications and compliance with international quality standards. Examples of relevant certifications include ISO 9001 for quality management, ISO 14001 for environmental management, and ISO 45001 for occupational health and safety.
5. Look for testimonials or customer reviews on the manufacturer’s website or other trustworthy platforms. Feedback from previous clients can provide insights into the manufacturer’s reliability, product quality, and customer service.
6. It is recommended to contact potential manufacturers directly. Send them inquiries through their website or contact details provided. This will allow you to assess their responsiveness, communication capabilities, and willingness to provide information and address your concerns.
7. Consider requesting samples from shortlisted manufacturers. Evaluating the quality of their products firsthand will help you gauge whether they meet your requirements.
8. Assess the manufacturer’s production capacity and capability to meet your specific needs. Check if they have the necessary equipment and facilities to handle your order volume efficiently.
9. Once you have gathered all the necessary information, compare the shortlisted manufacturers based on their reputation, product quality, pricing, lead times, and any other criteria important to your business.
10. Finally, select the manufacturer that best suits your requirements, has a good reputation, and provides reliable and efficient communication throughout the process.
Remember to conduct thorough due diligence, verify the credentials and capabilities of the panel manufacturing manufacturers, and consider engaging the services of a third-party quality inspection company when finalizing your selection.
How to check panel manufacturing manufacturers website reliable,use google chrome SEOquake check if ranking in top 10M
To ensure the reliability of a panel manufacturing manufacturer’s website, you can follow a few steps:
1. Use Google Chrome: Google Chrome is a widely used and reliable web browser that offers various extensions and tools for analyzing websites.
2. Install SEOquake: SEOquake is a popular extension for Google Chrome that provides useful data about a website’s search engine ranking, traffic, and other relevant metrics.
3. Check the website’s ranking: Once you have installed SEOquake, open the manufacturer’s website and activate the extension. It will display a toolbar with various metrics. Look for the “About” section within the SEOquake toolbar and click on “Google Index.” This will show you the approximate ranking of the website in Google’s top 10 million sites.
4. Assess the ranking: If the website ranks within the top 10 million, it indicates a decent level of popularity and online presence. However, keep in mind that the ranking alone doesn’t guarantee reliability. Also, consider the niche or industry the manufacturer operates in — a lower ranking in a specialized industry might still imply a reputable website.
5. Analyze other factors: While the SEOquake ranking provides a preliminary indication, it’s essential to consider other factors to determine reliability. Look for customer reviews, testimonials, certifications, or professional affiliations displayed on the website. Check for the manufacturer’s physical address, contact information, and presence on social media platforms.
In conclusion, by using Google Chrome and the SEOquake extension to check a panel manufacturing manufacturer’s website’s ranking, you can get valuable insights into its online presence. However, it is also crucial to consider other factors like customer reviews, certifications, and professional affiliations to assess reliability comprehensively.
Top 10 panel manufacturing manufacturers in China with each 160 words introduce products,then use markdown create table compare
1. Trina Solar: Trina Solar is a leading panel manufacturer in China, specializing in the production of high-quality solar panels. Their products are known for their efficiency and durability. Trina Solar offers a wide range of panels including monocrystalline, polycrystalline, and bifacial panels, suitable for residential, commercial, and utility-scale applications.
2. Jinko Solar: Jinko Solar is another major player in the Chinese panel manufacturing industry. They are known for their technologically advanced solar panels, offering high conversion rates and excellent performance even in low-light conditions. Jinko Solar’s range of products includes monocrystalline, polycrystalline, and bifacial panels, catering to various customer needs.
3. Canadian Solar: Canadian Solar is a renowned panel manufacturer with a significant presence in the Chinese market. They produce both monocrystalline and polycrystalline panels, known for their durability and efficiency. Canadian Solar offers a wide range of panels suitable for residential, commercial, and utility-scale installations.
4. Longi Solar: Longi Solar is known for manufacturing high-efficiency monocrystalline panels. Their panels utilize PERC (Passivated Emitter Rear Cell) technology, ensuring optimal energy conversion. Longi Solar’s products are widely used in residential and commercial solar installations.
5. JA Solar: JA Solar is a prominent manufacturer of both monocrystalline and polycrystalline solar panels in China. Their panels are known for their affordability and reliability. JA Solar offers a diverse portfolio of panels suitable for various applications, including residential, commercial, and utility-scale projects.
6. Hanwha Q Cells: Hanwha Q Cells is a globally recognized panel manufacturer with a strong presence in China. They produce high-quality monocrystalline and polycrystalline panels, known for their efficiency and longevity. Hanwha Q Cells offers a comprehensive range of panels for residential, commercial, and utility-scale installations.
7. TrinaPro: TrinaPro is a subsidiary of Trina Solar, specializing in the production of advanced solar panel systems. They offer integrated solutions that combine high-efficiency panels, inverters, and trackers to maximize energy output and system performance.
8. GCL System Integration: GCL System Integration is a leading solar panel manufacturer offering a wide range of monocrystalline and polycrystalline panels. Their products are known for their excellent performance in all weather conditions.
9. Risen Energy: Risen Energy is a prominent solar panel manufacturer known for its high-quality monocrystalline and polycrystalline panels. Their products are widely used in residential, commercial, and utility-scale solar projects.
10. Talesun Solar: Talesun Solar is a well-established panel manufacturer, providing high-performance monocrystalline and polycrystalline panels. Their products are engineered for optimum performance and reliability.
|**Manufacturer**|**Panel Types**|**Specializations**|
|—|—|—|
|Trina Solar|Monocrystalline, Polycrystalline, Bifacial|Efficiency and durability|
|Jinko Solar|Monocrystalline, Polycrystalline, Bifacial|High conversion rates, advanced technology|
|Canadian Solar|Monocrystalline, Polycrystalline|Durability, efficiency|
|Longi Solar|Monocrystalline|High efficiency, PERC technology|
|JA Solar|Monocrystalline, Polycrystalline|Affordability, reliability|
|Hanwha Q Cells|Monocrystalline, Polycrystalline|Efficiency, longevity|
|TrinaPro|Integrated systems|High-efficiency panels, enhanced performance|
|GCL System Integration|Monocrystalline, Polycrystalline|Excellent performance in all weather conditions|
|Risen Energy|Monocrystalline, Polycrystalline|High-quality, residential, commercial, and utility-scale projects|
|Talesun Solar|Monocrystalline, Polycrystalline|Optimum performance and reliability|
This table provides an overview of the top 10 panel manufacturers in China, their panel types, and their specializations in brief.
Background Research for panel manufacturing manufacturers Companies in China, use qcc.com archive.org importyeti.com
When it comes to panel manufacturing manufacturers in China, there are several reputable sources where background research can be conducted. Here, we will focus on three platforms that provide useful information about Chinese companies in this industry: qcc.com, archive.org, and importyeti.com.
Qcc.com is a comprehensive business information database that provides detailed company profiles and records in China. By using the website’s search function, researchers can find information on panel manufacturing manufacturers in China, including their legal status, registration details, business scope, and financial data.
Archive.org is a digital library that allows users to access archived versions of websites. It can be utilized to study the historical development of panel manufacturing manufacturers in China by looking at their websites, product catalogs, and any relevant news or announcements. Additionally, users can analyze the changes in capabilities, market presence, partnerships, and achievements of these companies over time.
Importyeti.com is a platform that provides import and export data for Chinese companies. Researchers can review shipment details, including the volume and value of panel products exported by manufacturers in China, as well as their trading partners. This information can help in understanding the market reach and international activity of these companies, leveraging their track records to assess their reliability and reputation.
It is essential to keep the background research concise, so let’s summarize the main points within the 300-word limit:
Qcc.com offers comprehensive company profiles and records, providing information on legal status, registration details, business scope, and financial data for panel manufacturing manufacturers in China.
Archive.org allows researchers to access historical versions of websites and study the development, changes, and achievements of these companies over time.
Importyeti.com provides import and export data, including shipment details and trading partners, to understand the market reach and international activity of panel manufacturing manufacturers in China.
By utilizing these platforms, researchers can gather valuable insights into the background and performance of panel manufacturing manufacturers in China, helping them make informed business decisions.
Leveraging Trade Shows and Expos for panel manufacturing Sourcing in China
Trade shows and expos can be valuable platforms for sourcing panel manufacturing in China. These events provide an opportunity for businesses to connect with potential suppliers, explore the latest products and developments in the industry, and establish meaningful business relationships.
One of the key advantages of attending trade shows and expos is the ability to meet face-to-face with multiple suppliers in one location. This saves time and effort that would otherwise be spent on individually sourcing and vetting potential manufacturers. By meeting with different suppliers, businesses can compare their capabilities, quality standards, and prices, enabling them to make informed decisions.
Trade shows and expos also serve as a showcase for the latest trends and innovations in panel manufacturing. This allows businesses to gather valuable market intelligence and stay up to date with technological advancements. It provides an opportunity to discover new products or techniques that can potentially improve their own manufacturing processes or offer a competitive advantage.
In addition, trade shows and expos often feature industry experts and thought leaders who participate in panel discussions and seminars. These sessions offer insights and expertise on a wide range of topics related to panel manufacturing, such as design, material selection, and production techniques. By attending these discussions, businesses can gain a deeper understanding of the industry, learn best practices, and network with professionals in the field.
To maximize the benefits of attending trade shows and expos, businesses should come prepared. It is important to research and identify the specific events that are relevant to panel manufacturing in China. This ensures that the event aligns with the business’s sourcing objectives and target market.
Furthermore, businesses should establish clear goals for attending the trade show or expo, such as finding new suppliers, exploring new technologies, or networking with industry professionals. This will help focus efforts during the event and ensure that the desired outcomes are achieved.
Overall, leveraging trade shows and expos for panel manufacturing sourcing in China can provide businesses with a competitive edge. It allows for efficient and effective supplier discovery, keeps businesses updated with industry trends, and offers opportunities for knowledge sharing and networking.
The Role of Agents and Sourcing Companies in Facilitating panel manufacturing Purchases from China
Agents and sourcing companies play an essential role in facilitating panel manufacturing purchases from China. These intermediaries act as a bridge between international buyers and Chinese manufacturers, assisting in various stages of the procurement process.
Firstly, agents and sourcing companies in China possess a deep understanding of the local manufacturing landscape, including panel production. They have a network of reliable and trusted manufacturers that produce high-quality panels at competitive prices. This knowledge enables them to identify suitable suppliers based on the specific requirements of the buyer, such as panel type, size, material, and technology.
Moreover, these intermediaries provide valuable support in communication and negotiation. They bridge the language and cultural gap between international buyers and Chinese manufacturers, facilitating effective communication and ensuring accurate understanding of buyer’s needs. Agents and sourcing companies also assist in negotiating favorable terms, including prices, payment terms, and delivery schedules, leveraging their experience and knowledge of the local market to secure the best deals for their clients.
Furthermore, agents and sourcing companies in China oversee the production process to ensure compliance with quality standards and delivery deadlines. They conduct factory audits, inspect production facilities, and monitor the entire manufacturing process to maintain quality control. These intermediaries act as an on-site representative for the buyer, addressing any issues that may arise during production and ensuring that the final product meets the buyer’s expectations.
Additionally, agents and sourcing companies assist in logistics and shipping. They handle documentation, customs clearance, and arrange transportation, ensuring smooth and efficient delivery of the panels to the buyer’s location. Their expertise in logistics and knowledge of international trade regulations help streamline the import process and minimize any potential delays or issues.
In conclusion, agents and sourcing companies in China play a crucial role in facilitating panel manufacturing purchases from the country. By leveraging their local knowledge, communication skills, negotiation expertise, and quality control measures, they simplify the procurement process for international buyers, ensuring efficient sourcing, manufacturing, and delivery of high-quality panels from China.
Price Cost Research for panel manufacturing manufacturers Companies in China, use temu.com and 1688.com
Temu.com and 1688.com are popular e-commerce platforms in China that are commonly used for price cost research and purchasing goods from manufacturers. These platforms are particularly useful for researching panel manufacturing manufacturers and comparing their prices and product offerings.
Panel manufacturing is a significant industry in China, and these platforms offer a wide range of options for buyers to choose from. By using these platforms, buyers can access a comprehensive list of manufacturers, view their product catalogs, and compare prices. Additionally, buyers can communicate directly with the manufacturers, allowing for efficient and effective negotiation or customization of products.
Temu.com is an online marketplace that offers a range of products, including panel manufacturing equipment and panels. It provides a user-friendly interface that enables buyers to search for manufacturers by industry, product category, or specific keywords. The platform also provides detailed product descriptions, specifications, and photos, making it easier for buyers to understand what they are purchasing.
1688.com, on the other hand, is a popular wholesale marketplace in China. It connects buyers with manufacturers, making it easier to find competitive prices for panel manufacturing. It offers a wide variety of panels, materials, and machinery from different manufacturers, allowing buyers to explore options and select the one that meets their requirements.
When conducting price cost research on these platforms, buyers should consider several factors. These include product quality, minimum order quantities, delivery time, payment terms, and manufacturers’ reputation. Buyers can review product ratings, customer reviews, and feedback on both platforms to ascertain the reliability and credibility of the manufacturers.
To ensure the best outcomes, buyers should compare prices from multiple manufacturers, communicate with them regarding their specific requirements, and request samples if necessary. It is also advisable to verify the manufacturers’ certifications, production capabilities, and conduct due diligence before finalizing any deals.
In conclusion, temu.com and 1688.com are valuable resources for price cost research for panel manufacturing manufacturers in China. These platforms offer an extensive range of products, competitive prices, and the ability to communicate directly with manufacturers. Buyers should conduct thorough research, compare prices, and consider various factors before making their final purchasing decisions.
Shipping Cost for panel manufacturing import from China
The shipping cost for panel manufacturing imports from China can vary depending on a few key factors. These factors include the size of the panels, the weight, the destination country, and the chosen shipping method.
Typically, panel manufacturing imports are transported via ocean freight. The cost of ocean freight is calculated based on the cubic meter (CBM) or weight (tonnage) of the goods. For lightweight and small-sized panels, the cost is usually determined by CBM, while for heavier and larger panels, the cost may be calculated by weight.
To give an estimate, the average cost of shipping a 20-foot container from China to major ports in the United States or Europe can range from $900 to $2,500. This cost includes the ocean freight, documentation fees, customs clearance charges, local delivery charges, and any additional surcharges or taxes.
It is important to note that there might be additional charges involved during the shipping process, such as handling fees at the port of origin and destination, customs duties and taxes, and any other charges imposed by the shipping line or freight forwarder.
To minimize shipping costs, importers can consider consolidating their panels with other goods in a container through a process known as LCL (Less than Container Load) shipping. This can help distribute the overall cost among multiple shipments and reduce the per-unit shipping costs.
Furthermore, importers can also negotiate with shipping carriers or freight forwarders for more competitive rates based on the volume or frequency of their shipments. It is advisable to work closely with reliable and experienced freight forwarders who can provide guidance and assistance in navigating the shipping process and ensuring the best possible rates.
In conclusion, the shipping cost for panel manufacturing imports from China depends on various factors such as panel size, weight, shipping method, and destination. Importers can take advantage of cost-saving measures such as consolidating shipments and negotiating with carriers to minimize their shipping expenses.
Compare China and Other panel manufacturing Markets: Products Quality and Price,Visible and Hidden Costs
China is one of the biggest players in the panel manufacturing market, and as such, it is worthwhile to compare its product quality and price with other manufacturing markets. Additionally, examining visible and hidden costs will provide a comprehensive understanding of the market landscape.
In terms of product quality, China has made significant strides in recent years. Chinese manufacturers have invested heavily in technology and advanced machinery, enabling them to produce high-quality panels. However, it is important to note that quality can vary among manufacturers, and due diligence is required to identify reliable suppliers.
Price is an area where China shines, as its manufacturing costs are generally lower compared to other markets. This cost advantage can be attributed to several factors, including economies of scale, access to raw materials, and a large pool of skilled labor. As a result, Chinese manufacturers can offer competitive prices, attracting buyers from around the world.
When discussing visible costs, it is essential to consider factors such as product price, shipping costs, and any additional expenses associated with manufacturing. China’s manufacturing prices are often lower compared to other markets, allowing buyers to enjoy cost savings on the visible front.
However, hidden costs must also be taken into account. These costs include intellectual property risks, supply chain disruptions, and quality control issues. Intellectual property risks are often associated with Chinese manufacturers, as concerns over counterfeiting and piracy remain. Supply chain disruptions, such as delays in shipping or customs clearance, can also impact costs and lead to unforeseen expenses. Additionally, maintaining quality control can be challenging due to logistical complexities when dealing with manufacturers in another country.
In summary, China offers a combination of competitive prices and improving product quality. Buyers looking for cost savings often turn to Chinese manufacturers due to their lower manufacturing costs. However, hidden costs such as intellectual property risks and supply chain disruptions should not be overlooked. It is important to weigh both visible and hidden costs before making a decision on panel manufacturing sources.
Understanding Pricing and Payment Terms for panel manufacturing: A Comparative Guide to Get the Best Deal
Pricing and payment terms for panel manufacturing play a crucial role in determining the overall cost of a project and the financial feasibility of a partnership. To ensure that you get the best deal, it is essential to have a thorough understanding of the various factors that influence pricing and negotiation strategies for favorable payment terms. This comparative guide aims to shed light on these aspects to help you navigate the panel manufacturing market efficiently.
The first step in assessing pricing is to consider the type of panel being manufactured. Different panel types, such as solar panels, electronic display panels, or construction panels, have varying cost structures due to differences in materials, manufacturing processes, and market demand. It is crucial to evaluate the specific requirements and quality standards of your project to understand the potential impact on pricing.
Once you have identified the panel type, it is imperative to gather quotes from multiple manufacturers. This allows you to compare pricing and negotiate the best deal. When requesting quotes, provide comprehensive specifications to ensure accurate and comparable pricing. Additionally, consider the manufacturer’s reputation, experience, and production capacity, as these factors can influence their pricing structure.
Payment terms negotiation is equally important to secure a favorable deal. Most manufacturers require a deposit or down payment, typically ranging from 30% to 50% of the total order value, before commencing production. Negotiating a lower upfront payment can help manage your cash flow effectively. However, be cautious not to compromise the manufacturer’s trust or jeopardize the production timeline.
Another vital aspect of payment terms negotiation is determining milestone payments. Based on the size and complexity of your project, establishing payment milestones tied to specific production stages can mitigate risks and ensure accountability. This approach allows you to release funds only as each milestone is achieved, providing you with more control over the manufacturing process.
Furthermore, analyzing the manufacturer’s payment terms is essential. Some manufacturers may offer discounts for upfront payment or cash transactions, while others may provide flexible payment options, such as installment plans. Evaluating these possibilities and understanding any associated charges or interest rates can significantly impact the ultimate cost of your project.
In conclusion, understanding pricing factors and negotiation strategies is essential when engaging in panel manufacturing. By thoroughly researching and comparing quotes, negotiating payment terms, and considering associated discounts, you can secure the best deal. Remember to balance cost considerations with the manufacturer’s reputation and production capabilities to ensure a successful partnership.
Chinese Regulations and Industry Standards Certifications for panel manufacturing,Import Regulations and Customs for panel manufacturing from China
Chinese Regulations and Industry Standards Certifications for panel manufacturing cover a wide range of aspects, ensuring product quality, safety, and environmental compliance. The key certifications and regulations include:
1. China Compulsory Certification (CCC): This certification is mandatory for many products, including electrical and electronic equipment, to ensure their safety, quality, and compliance with Chinese standards.
2. National Energy Efficiency Label: This label is required for electrical products to prove their energy efficiency and compliance with energy-saving requirements.
3. RoHS (Restriction of Hazardous Substances): This regulation restricts the use of certain hazardous substances in electrical and electronic equipment, thereby ensuring their environmental safety. Compliance with RoHS is required for exporting products to China.
4. GB Standards: These are national standards applicable to various industries, including the panel manufacturing industry. Adhering to these standards is crucial for ensuring product quality, performance, and safety.
5. ISO Certifications: Several ISO certifications, such as ISO 9001 (Quality Management System) and ISO 14001 (Environmental Management System), are widely recognized and sought after by manufacturers. Obtaining these certifications demonstrates compliance with international quality and environmental standards.
In terms of import regulations and customs for panel manufacturing from China, importers need to consider the following:
1. Import Tariffs: Check the import tariff rates, as they vary based on the type of panel being imported. Certain product categories might be subjected to higher tariffs.
2. Import Licenses: Some panel products may require import licenses or specific permits from relevant Chinese authorities. It is important to ensure compliance with these requirements before importing.
3. Customs Documentation: Proper documentation, including commercial invoices, packing lists, and bill of lading/airway bill, must be prepared accurately to facilitate customs clearance.
4. Customs Duties and Taxes: Importers should be aware of applicable customs duties, value-added tax (VAT), and other taxes, which are calculated based on the declared value of the goods.
5. Customs Inspection: Imported panel products may undergo customs inspections to verify compliance with relevant regulations and standards.
It is crucial for panel manufacturers and importers to conduct thorough research, consult with experts, and ensure compliance with both Chinese regulations and the import regulations of their destination country.
Sustainability and Environmental Considerations in panel manufacturing Manufacturing
Sustainability and environmental considerations play a crucial role in the manufacturing of panels. The manufacturing process for panels involves the use of various materials and energy sources that can have significant environmental impacts. Therefore, it is essential for panel manufacturers to adopt sustainable practices to minimize their ecological footprint.
One of the primary environmental considerations in panel manufacturing is the selection of materials. Manufacturers should aim to use sustainable and renewable materials whenever possible. For instance, utilizing wood from responsibly managed forests or using recycled materials can help reduce the pressure on natural resources. Additionally, reducing the amount of hazardous substances present in panels, such as formaldehyde or volatile organic compounds (VOCs), is vital to ensure the panels are environmentally friendly.
Furthermore, energy consumption during the manufacturing process is a significant sustainability concern. Manufacturers should strive to minimize energy usage and seek renewable energy options to power their operations. Switching to energy-efficient equipment, implementing energy-saving technologies, and optimizing production processes can help reduce energy consumption and associated greenhouse gas emissions.
Waste management is another critical aspect of sustainability in panel manufacturing. Manufacturers should implement strategies to minimize waste generation and properly manage any waste produced. This can involve recycling materials, implementing waste reduction initiatives, and treating or disposing of waste in an environmentally responsible manner.
Reducing water consumption is also an important environmental consideration. Panel manufacturing requires water for various processes such as cleaning, cooling, or mixing raw materials. Employing water-efficient technologies and implementing water recycling systems can help minimize water usage and decrease the impact on local water resources.
Transportation is yet another factor to consider. Panel manufacturers should strive to minimize their carbon footprint by optimizing shipping routes, utilizing eco-friendly transportation options, and reducing packaging waste. Adopting sustainable logistics practices can significantly contribute to sustainability goals.
In conclusion, sustainability and environmental considerations are crucial in panel manufacturing. By selecting sustainable materials, reducing energy consumption, managing waste, minimizing water usage, and employing eco-friendly transportation practices, panel manufacturers can contribute to environmental preservation and create more sustainable products. Incorporating these considerations into manufacturing processes is not only essential for the environment but also for meeting the rising demand for sustainable products in the market.
List The Evolution history of “panel manufacturing”
The evolution history of panel manufacturing can be traced back to ancient times when humans discovered methods to create panels from natural resources like wood and stone. These panels were primarily used for construction purposes, providing structural support and aesthetic appeal to buildings.
In the 19th century, with the industrial revolution, the manufacturing process of panels underwent a significant change. The introduction of machinery and improved techniques allowed for mass production of panels, increasing their availability and reducing costs. Wood panels became popular in furniture manufacturing, while stone panels were utilized for architectural purposes.
The 20th century marked a significant shift in panel manufacturing with the advent of new materials and technologies. In the early 1900s, the invention of plywood revolutionized the industry. Plywood panels, made by layering thin sheets of wood, offered increased strength and flexibility, making them ideal for construction and furniture production.
In the mid-1900s, advancements in chemistry led to the development of composite panels. These panels were made by combining different materials like fibers, resins, and plastics to create lightweight, durable, and weather-resistant panels. Aluminum composite panels gained popularity in architectural design due to their versatility and sleek appearance.
The late 20th century witnessed the rise of solar panel manufacturing. Solar panels, made from photovoltaic cells, were developed to harness solar energy and convert it into electricity. This innovation brought renewable energy solutions into the mainstream and revolutionized the global energy landscape.
In recent years, panel manufacturing has seen further advancements with the introduction of sustainable materials and advanced manufacturing techniques. Materials like bamboo, recycled plastic, and composite materials derived from agricultural waste are being utilized to create eco-friendly panels. Furthermore, digital manufacturing technologies such as 3D printing are enabling the production of customized and intricate panel designs.
In conclusion, the evolution of panel manufacturing can be seen as a journey from using natural resources for construction to embracing new materials, technologies, and sustainability. From wood and stone panels to plywood, composites, and solar panels, the industry has constantly evolved to meet the changing needs of various sectors, including construction, furniture, and renewable energy.
The Evolution and Market Trends in panel manufacturing Industry
The panel manufacturing industry has experienced significant evolution and market trends in recent years. This industry primarily focuses on producing various types of panels, including solar panels, electronic display panels, and building panels.
One key evolution in panel manufacturing is the increasing adoption of renewable energy sources, particularly solar panels. With the growing concerns over climate change and the need for sustainable energy solutions, solar panel manufacturing has seen a tremendous boost. Technological advancements and government incentives have driven the demand for solar panels, making this segment a crucial part of the panel manufacturing industry.
Another significant trend in panel manufacturing is the shift towards technologically advanced electronic display panels. With the rising demand for high-resolution screens, advanced panel manufacturing techniques have evolved to produce large-sized, ultra-high-definition displays. This trend is particularly prominent in the consumer electronics industry, where smartphones, tablets, and televisions require superior display quality.
The building panels segment has also undergone notable developments. Energy-efficient building regulations and the need for sustainable construction practices have led to the emergence of new materials and manufacturing techniques for building panels. These panels now focus on insulation, soundproofing, fire resistance, and eco-friendly attributes, enabling the construction industry to meet evolving sustainability requirements.
Market trends in panel manufacturing include increasing globalization and consolidation. As panel manufacturers expand their operations to new regions and establish global supply chains, production costs can be reduced, leading to competitive pricing. Additionally, market consolidation has driven the industry towards larger manufacturers who have the resources to invest in research and development, technological innovation, and economies of scale.
Lastly, customers’ preferences for panels that are lightweight, durable, and customizable have become more influential in the industry. Manufacturers are increasingly investing in lightweight materials like carbon fiber and high-strength aluminum alloys to meet these demands. Customization options, such as flexible panels or curved screens, are also gaining popularity, catering to specific customer needs and design preferences.
In conclusion, the panel manufacturing industry has evolved significantly to adapt to market trends and changing demands. The rise of solar panels, advanced electronic display panels, environmentally friendly building panels, as well as globalization, consolidation, and customer preferences, have shaped the industry’s trajectory. As technology continues to progress and sustainability becomes increasingly important, panel manufacturing is likely to experience continuous evolution and innovation.
Custom Private Labeling and Branding Opportunities with Chinese panel manufacturing Manufacturers
China is a global leader in panel manufacturing, offering vast opportunities for custom private labeling and branding. Working with Chinese manufacturers allows businesses to leverage their expertise, cost-efficient production processes, and access to a wide range of materials and technologies.
Private labeling allows businesses to create their own unique brand identity by customizing products manufactured by Chinese panel makers. This includes adding logos, designs, and other brand elements to the manufactured panels. Chinese manufacturers have experience in handling private labeling requests, ensuring that the branding process is seamless and meets the business’s requirements.
Furthermore, Chinese manufacturers provide a broad spectrum of branding opportunities. They often offer customization options in terms of panel sizes, shapes, colors, and finishes. This flexibility enables businesses to create bespoke panels that align with their brand image and specific product requirements.
Chinese panel manufacturers also provide branding services such as packaging and labeling. They can assist in designing and producing customized packaging materials that include the business’s logo and other branding elements. This attention to detail contributes to a cohesive brand experience and enhances the product’s overall appeal.
Moreover, Chinese manufacturers have established networks of suppliers and can source high-quality materials for panel production. This ensures that the final product meets the desired standards and reinforces the business’s commitment to quality.
Additionally, partnering with Chinese panel manufacturers provides businesses with cost advantages. China’s manufacturing capabilities, economies of scale, and efficient production processes allow for competitive pricing. This affordability allows businesses to allocate resources towards marketing and other aspects of brand development.
In conclusion, the Chinese panel manufacturing industry offers immense potential for custom private labeling and branding opportunities. By collaborating with Chinese manufacturers, businesses can create unique products that align with their brand identity while benefiting from their expertise, cost-efficiency, and diverse range of materials and technologies.
Tips for Procurement and Considerations when Purchasing panel manufacturing
When it comes to procuring panel manufacturing materials, it is crucial to consider several factors to ensure you make the right purchasing decisions. Here are some tips and considerations you should keep in mind:
1. Quality: Prioritize high-quality panel materials that meet recognized industry standards. Look for manufacturers that have a reputation for producing reliable and long-lasting products.
2. Durability: Consider the intended usage of the panels and choose materials that can withstand environmental conditions, such as weathering, temperature variations, or chemical exposure. Panels intended for outdoor use should be corrosion-resistant and UV-stabilized.
3. Cost: While price should not be the sole determining factor, it is important to evaluate the cost of the materials. Compare prices from different suppliers to ensure you are getting the best value for your money while maintaining quality.
4. Supplier reputation: Conduct research on the supplier’s background and reputation. Check for customer reviews and testimonials to ensure they have a history of providing reliable products and excellent customer service.
5. Customization options: If you require specific dimensions, colors, or finishes for your panel manufacturing, ensure that the supplier can accommodate your customization needs. Confirm the lead times and any additional costs associated with customization.
6. Support and warranty: Inquire about the supplier’s after-sales support and warranty policies. Understanding what is covered under warranty and what support you can expect will be essential for any potential issues that may arise.
7. Compliance: Ensure that the supplier and the panel materials comply with relevant industry standards and regulations. This could include certifications related to fire resistance, electrical conductivity, or sustainability credentials.
8. Delivery logistics: Discuss shipping and delivery with the supplier, ensuring they can deliver to your location within your required timeframe. Verify packaging methods to guarantee that the panels will arrive undamaged.
9. Sustainability: Consider the environmental impact of the panel manufacturing materials. Opt for suppliers that actively promote sustainability through their product offerings and manufacturing processes.
10. Past projects and references: Request references or examples of similar projects where the supplier has provided panel manufacturing materials. This will allow you to evaluate their experience and expertise in the industry.
By taking these tips and considerations into account, you can make an informed decision when procuring panel manufacturing materials that meet your specific requirements in terms of quality, durability, cost-effectiveness, and environmental sustainability.
FAQs on Sourcing and Manufacturing panel manufacturing in China
1. Why should I consider sourcing and manufacturing panel manufacturing in China?
China is known for its high-quality manufacturing capabilities and cost-effective production. The country has a well-developed supply chain infrastructure, abundant raw materials, and a large pool of skilled labor. Additionally, Chinese manufacturers have extensive experience in producing panels for various industries, offering a wide range of options in terms of size, material, and finishes. Sourcing from China can help businesses reduce costs and access a wide array of panel manufacturing capabilities.
2. How can I find reliable panel manufacturers in China?
Finding reliable panel manufacturers in China requires thorough research and due diligence. Utilize online sourcing platforms and directories to identify potential manufacturers. Read client reviews, ensure the manufacturer is compliant with industry standards and certifications, and request samples or references before finalizing any agreements. It is also recommended to visit the manufacturer’s facilities and conduct factory audits to verify their capabilities, quality control processes, and production capacity.
3. What are the typical lead times for panel manufacturing in China?
Lead times for panel manufacturing in China can vary depending on the complexity, quantity, and customization requirements of the panels. Generally, lead times range from a few weeks to a couple of months. It is crucial to communicate your desired timeline to manufacturers and plan accordingly. Effective communication and clear expectations can help minimize delays and ensure timely delivery.
4. Can I customize panels manufactured in China?
Yes, Chinese manufacturers offer a high level of flexibility in customizing panels to meet specific requirements. They can work with different materials like wood, metal, plastic, and composite materials. Manufacturers can also accommodate individualized sizes, finishes, colors, branding, and packaging options. Working closely with the manufacturer and providing detailed specifications will help achieve the desired customization.
5. What quality control measures are in place for panel manufacturing in China?
Most reputable manufacturers in China have well-established quality control procedures. They often adhere to internationally recognized quality standards such as ISO 9001. Manufacturers may conduct regular inspections throughout the production process, including material testing, dimensional checks, and final product inspection. Communication with the manufacturer about quality expectations and requirements is essential to ensure satisfactory results.
6. What are the payment terms when working with a Chinese panel manufacturer?
Payment terms can vary depending on the manufacturer and the agreement reached between the parties. It is common for Chinese manufacturers to require an initial deposit, often around 30% of the total order value, before production begins. The remaining balance is typically paid upon completion of production and before shipping. Negotiating favorable payment terms and using secure payment methods is recommended to mitigate any financial risks.
7. How can I arrange shipping and manage logistics for panel manufacturing in China?
Chinese panel manufacturers often have experience in exporting their products globally and can assist with arranging shipping and managing logistics. They can provide guidance on the most suitable shipping methods, carriers, and freight forwarding services based on your specific requirements. Close coordination with the manufacturer and clear communication regarding delivery expectations ensure a smooth shipping process.
In summary, sourcing and manufacturing panel manufacturing in China can offer cost-effective solutions, customization options, and reliable quality. Conducting thorough research, engaging in transparent communication, and implementing effective quality control measures will contribute to successful outcomes when partnering with Chinese panel manufacturers.
Why contact sourcifychina.com get free quota from reliable panel manufacturing suppliers?
SourcifyChina.com is able to provide free quotas from reliable panel manufacturing suppliers due to several reasons. Firstly, SourcifyChina.com has built strong and long-standing relationships with a wide network of panel manufacturing suppliers in China. These relationships have been developed over time through trust, good communication, and successful collaboration on past projects. As a result, panel manufacturing suppliers are willing to offer free quotas as a gesture of goodwill and to maintain the ongoing partnership with SourcifyChina.com.
Secondly, SourcifyChina.com has established itself as a reputable and reliable sourcing agent in the industry. By consistently delivering high-quality products and efficient services, they have gained the trust and confidence of panel manufacturing suppliers. Suppliers are more inclined to offer free quotas to SourcifyChina.com as a way to attract their business and ensure a continued supply of orders in the future.
Furthermore, SourcifyChina.com has a proven track record of bringing in substantial order volumes for panel manufacturing suppliers. This means that suppliers are willing to offer free quotas as a strategic investment to secure large contracts from SourcifyChina.com. By providing a free quota, suppliers can showcase their capabilities, product quality, and competitive pricing to potentially win long-term contracts.
Additionally, SourcifyChina.com operates at scale and has a large customer base. By leveraging their network, they are able to negotiate favorable terms and conditions with panel manufacturing suppliers. This negotiation power allows them to secure free quotas or discounted rates, which they pass on to their clients, further solidifying their position as a trusted sourcing partner.
In conclusion, SourcifyChina.com is able to obtain free quotas from reliable panel manufacturing suppliers due to their established relationships, reputation, track record, and negotiation power. These factors contribute to a win-win situation for all parties involved, where SourcifyChina.com can provide its clients with the best pricing and suppliers can secure ongoing business opportunities.