Introduce about plastic cnc machining guide,Qulity,Cost,Supplier,Certification,Market,Tips,FAQ
Plastic CNC machining has become a crucial process in manufacturing various plastic components due to its precision, reliability, and cost-effectiveness. This guide aims to provide an overview of plastic CNC machining, covering aspects such as quality, cost, suppliers, certification, market trends, helpful tips, and frequently asked questions.
When it comes to quality, plastic CNC machining offers exceptional accuracy and repeatability. CNC machines can achieve tight tolerances, ensuring the finished plastic parts meet the required specifications. The process also provides excellent surface finishes, enhancing the appearance and functionality of the components.
In terms of cost, plastic CNC machining is relatively economical compared to other manufacturing methods. By automating the manufacturing process, CNC machines can produce parts in large quantities, reducing labor costs. Additionally, the machines are versatile and can work with various plastics, further optimizing production efficiency.
Choosing the right supplier for plastic CNC machining is crucial. Look for established manufacturers with a reputation for delivering quality products and services. It is vital to review their capabilities, machinery, experience, and customer reviews to ensure they meet your specific requirements.
Certifications play a significant role in ensuring the supplier’s competence and adherence to industry standards. ISO 9001 certification is commonly sought after as it demonstrates a manufacturer’s commitment to providing quality products and services.
The market for plastic CNC machining is continually expanding, driven by the demand for plastic parts in numerous industries. These components find applications in automotive, electronics, medical, aerospace, and consumer goods sectors, among others. As technology advances, the market is expected to grow further, offering new opportunities for manufacturers and suppliers.
To maximize the benefits of plastic CNC machining, consider a few essential tips. Optimize your designs for CNC machining, providing clear and precise instructions. Communicate effectively with the supplier, discussing specifications, tolerances, and any other requirements. Regularly monitor the manufacturing process to ensure quality and avoid any issues that may arise.
In the frequently asked questions section, address common queries about plastic CNC machining, such as the suitability of specific plastic materials, common production issues, and the compatibility with various design file formats.
In conclusion, plastic CNC machining is a reliable and cost-effective method for manufacturing plastic components. Its high quality, versatility, and growing market make it an attractive choice for many industries. By following the tips and answering frequently asked questions, manufacturers can optimize their plastic CNC machining process and achieve successful outcomes.
Types of plastic cnc machining
CNC machining, also known as computer numerical control machining, is a manufacturing process that utilizes computerized controls and machine tools to remove material from a workpiece. This process is widely used in the production of plastic parts due to its high precision and efficiency. There are several types of plastic CNC machining processes that can be used to create a wide range of plastic components.
One of the most common types of plastic CNC machining is milling. This process involves rotating multi-point cutting tools to remove material from the workpiece. This is typically used for creating complex shapes and features on plastic parts. Another type of plastic CNC machining is turning, which involves rotating the workpiece while a cutting tool is traversed along the surface to remove material. This process is often used for creating cylindrical or conical shapes on plastic parts.
Plastic CNC machining also includes processes such as drilling, tapping, and threading, which are used to create holes and threads in plastic components. Additionally, CNC routing is a machining process that involves cutting and shaping plastic sheets or blocks using a rotating cutting tool.
It is important to note that different types of plastic materials have unique properties and characteristics, which can affect the CNC machining process. For example, thermoplastics such as ABS, polycarbonate, and acrylic are commonly machined using CNC processes due to their ability to be easily melted and reformed. On the other hand, thermoset plastics such as epoxy and phenolic are more rigid and may require specialized CNC machining techniques.
In conclusion, CNC machining offers a variety of processes to efficiently machine plastic components with high precision and accuracy. Whether it is milling, turning, drilling, or routing, these processes provide flexibility and versatility in creating a wide range of plastic parts for various applications. Understanding the properties of different plastic materials is essential in choosing the right CNC machining process for optimal results.
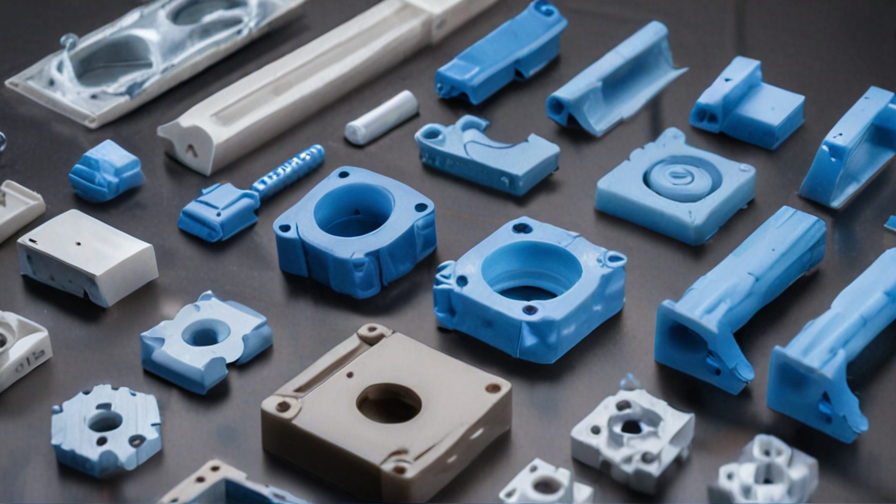
Pros and Cons of Using plastic cnc machining
Pros of Using Plastic CNC Machining:
1. Versatility: Plastic CNC machining offers a wide range of possibilities for manufacturing various parts, components, and prototypes. It enables the creation of complex and intricate designs that may be difficult or impossible to achieve through other manufacturing methods.
2. Cost-effective: Compared to other methods such as injection molding, plastic CNC machining can be a more cost-effective option, especially for low volume production or rapid prototyping. It eliminates the need for expensive molds, tooling, and setup costs, making it a more economical choice for small-scale projects.
3. Quick turnaround time: CNC machines can produce plastic parts quickly, making it ideal for projects that require rapid production. With computer-controlled automation, CNC machining eliminates the need for manual labor and reduces the overall production time.
4. High precision: CNC machines offer exceptional precision and accuracy, making it possible to achieve intricate designs and tight tolerances consistently. This level of precision is particularly important in industries such as aerospace, medical, and automotive, where quality and reliability are critical.
Cons of Using Plastic CNC Machining:
1. Limited material selection: While plastic CNC machining offers versatility, the range of materials available for machining is limited compared to other manufacturing methods. Some materials may not be compatible with CNC machining processes, reducing the choice of materials for specific applications.
2. Higher cost for large-scale production: While plastic CNC machining can be cost-effective for small-scale projects, it may not be the most economical choice for large-scale production. Injection molding, for example, can be more cost-effective and efficient for high-volume production runs.
3. Surface finish limitations: CNC machining may not provide the same level of surface finish quality as other methods like injection molding. Depending on the chosen material and part design, additional post-processing may be required to achieve the desired surface finish, increasing production time and cost.
4. Structural limitations: Certain types of plastics may have limitations in terms of strength and load-bearing capabilities. For applications requiring high tensile strength or structural integrity, other manufacturing methods like injection molding or 3D printing may be better suited.
In summary, plastic CNC machining offers versatility, cost-effectiveness for low-volume production, and high precision. However, it has limitations in material selection, cost for large-scale production, surface finish quality, and structural capabilities. Choosing the right manufacturing method ultimately depends on specific project requirements and trade-offs between cost, quality, and timeline.
plastic cnc machining Reference Specifications (varies for different product)
Plastic CNC machining is a versatile manufacturing technique used to produce high-quality plastic components. The process involves using computer numerical control (CNC) machines to remove material from a plastic workpiece, forming the desired shape.
When it comes to plastic CNC machining, there are certain reference specifications that vary depending on the specific product being manufactured. These specifications dictate the material requirements, tolerances, surface finish, and other crucial parameters to ensure the quality and functionality of the final product.
One of the primary considerations is the choice of plastic material. Different plastics have varying properties, such as strength, rigidity, heat resistance, chemical resistance, and electrical conductivity. Common plastics used in CNC machining include ABS, acrylic, polycarbonate, nylon, and PEEK. The choice of material depends on the end-use application and its specific requirements.
Tolerances are another crucial aspect of plastic CNC machining. Tolerances define the allowable deviation from the intended dimensions. In precision applications, tighter tolerances are required. The general rule of thumb is that the smaller the part, the tighter the tolerances. CNC machines can achieve high accuracy, often within a few thousandths of an inch, ensuring precise dimensions and tight fits.
Surface finish is another critical specification. CNC machining can provide smooth finishes, typically up to around 16 microinches. However, additional post-processing techniques like polishing or sanding may be required to achieve an even smoother surface, depending on the application.
Other specifications include part geometry, such as the complexity of designs, the number and size of features, threads, and undercuts. These factors can affect the machining time, tooling requirements, and overall cost of production.
In conclusion, plastic CNC machining reference specifications vary depending on the specific product being manufactured. Material selection, tolerances, surface finish, and part geometry are all crucial aspects that need to be carefully considered. By adhering to these specifications, manufacturers can ensure that the final plastic components meet the required quality and performance standards.
Applications of plastic cnc machining
Plastic CNC machining is a versatile process that involves the use of computer numerical control (CNC) machines to shape and assemble plastic materials. This manufacturing technique offers several advantages and finds applications in various industries.
One of the primary applications of plastic CNC machining is in the automotive industry. Manufacturers utilize CNC machining to create precision components such as dashboards, interior panels, and exterior trim. The ability of CNC machines to produce complex shapes with high accuracy and repeatability makes them well-suited for achieving the intricate designs required in automotive applications.
Medical devices and equipment also benefit from plastic CNC machining. The process enables the creation of custom-made components, such as surgical instruments and prosthetic limbs. CNC machines can produce intricate parts with tight tolerances, ensuring the quality and precision required in the medical field.
Plastic CNC machining is widely used in the electronics industry as well. The production of housings for electronic devices, such as smartphones, laptops, and gaming consoles, is facilitated by CNC machines. The ability to achieve intricate designs with plastic CNC machining makes it an ideal choice for producing visually appealing and functional electronic enclosures.
Moreover, the packaging industry relies on plastic CNC machining for the manufacturing of molds and custom packaging solutions. CNC machines can create precise molds that allow for efficient and cost-effective production of plastic packaging containers, trays, and other products. The high level of customization and repeatability offered by CNC machining benefits companies seeking unique packaging designs.
Lastly, the aerospace industry utilizes plastic CNC machining for various applications such as manufacturing lightweight components, interior fittings, and cabin panels. CNC machines can accurately shape plastic materials with low weight and high strength, contributing to the overall efficiency and safety of aircraft.
In conclusion, plastic CNC machining finds applications in a range of industries due to its ability to produce complex shapes, maintain high accuracy, and provide customized solutions. From automotive and medical to electronics and packaging industries, CNC machines enable the production of precise plastic components and molds, meeting the demanding requirements of these sectors. The versatility and efficiency of plastic CNC machining make it a vital process in modern manufacturing.
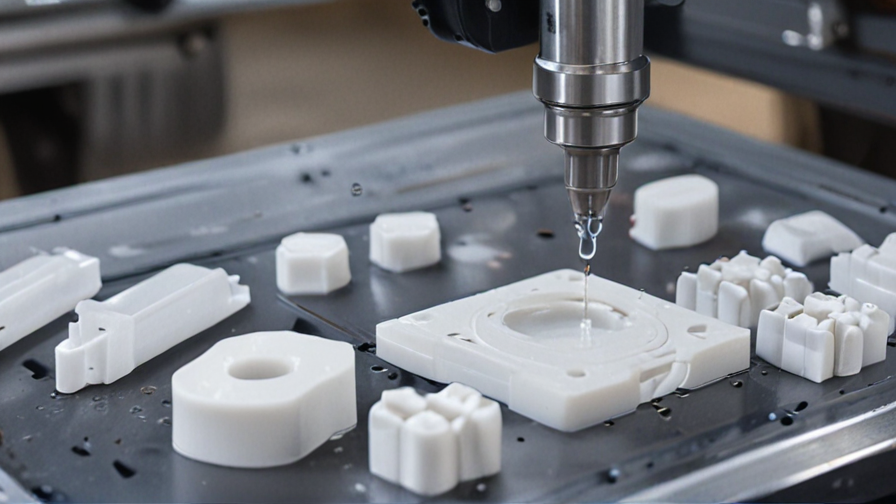
The Work Process and how to use plastic cnc machining
Plastic CNC machining is a manufacturing process that involves the use of computer numerical control (CNC) machines to create plastic parts and products. The process begins with the design of the part using computer-aided design (CAD) software. Once the design is complete, the CAD file is converted into a format that the CNC machine can read.
The next step is to select the appropriate type of plastic material for the part. Different plastics have different properties, such as strength, flexibility, and heat resistance, so it’s important to choose the right material for the specific application.
Once the material is selected, it is loaded into the CNC machine, and the machine is programmed to carve out the part according to the CAD design. The CNC machine uses a variety of cutting tools, such as end mills and drills, to remove material from the plastic block and shape it into the desired form. The process is highly precise and can produce complex shapes and intricate geometries with accuracy.
After the part is machined, it may undergo additional finishing processes, such as polishing or sanding, to achieve the desired surface finish. The final part is then inspected for quality and accuracy before being used in the final product.
Plastic CNC machining is widely used in industries such as automotive, aerospace, electronics, and consumer goods, where high precision and tight tolerances are required. It offers a cost-effective and efficient way to produce plastic parts in small to medium volumes.
In conclusion, plastic CNC machining is a versatile and accurate manufacturing process that can be used to create a wide range of plastic parts and products. By following the steps outlined above and utilizing the capabilities of CNC machines, manufacturers can efficiently produce high-quality plastic components for various applications.
Quality Testing Methods for plastic cnc machining and how to control the quality
Plastic CNC machining is a widely used manufacturing process to produce high-precision plastic components. To ensure the quality of these components, various testing methods and quality control measures can be implemented. Some of the commonly used methods include:
1. Dimensional and geometric accuracy testing: This involves measuring the dimensions of the machined plastic parts using precision tools such as calipers, micrometers, or CMM (Coordinate Measuring Machines). Geometric accuracy can be verified by checking the concentricity, parallelism, perpendicularity, or other required tolerances.
2. Surface finish analysis: Surface roughness and quality of machined plastic parts are critical for many applications. Instruments like profilometers or optical microscopes are used to assess the surface finish and ensure it meets the required specifications.
3. Visual inspection: Operators visually inspect the machined plastic parts for any visible defects such as surface cracks, burrs, or damage. This can be done manually or with the assistance of automated vision inspection systems.
4. Mechanical property testing: Tensile and flexural testing machines can be employed to evaluate the mechanical properties of the plastic components. This includes checking factors such as tensile strength, yield strength, modulus, elongation, or impact resistance.
Quality control in plastic CNC machining can be achieved through several strategies, including:
1. Documented specifications: Clearly defining the required dimensions, tolerances, material properties, and surface finish in technical drawings or manufacturing instructions helps establish the quality standards.
2. Standard operating procedures (SOPs): Implementing SOPs ensures consistent manufacturing processes and allows for easy identification of deviations that might affect the quality.
3. In-process inspections: Regular checks during the machining process help detect any quality issues early on and minimize the production of non-conforming parts.
4. Calibration and maintenance: Regular maintenance and calibration of CNC machines and measuring tools are crucial to ensure accuracy and reliability.
5. Statistical process control (SPC): Monitoring and analyzing production data using SPC techniques can identify trends or variations in the quality, facilitating timely corrective actions.
By combining these quality testing methods and control measures, manufacturers can produce plastic CNC machined parts with high precision, surface quality, and mechanical properties, ensuring customer satisfaction and compliance with industry standards.
plastic cnc machining Sample Policy and Post-Purchase Considerations for plastic cnc machining from China
Sample Policy:
1. Requesting for samples: Before placing a bulk order for plastic CNC machining from China, it is advisable to request a sample of the desired product. This allows you to assess the quality, accuracy, and suitability of the machining process.
2. Sample cost and shipping: In most cases, the buyer is responsible for covering the cost of the sample and the shipping charges. Ensure that you are aware of the total costs involved before proceeding with the sample request.
3. Quality assurance: Request information on the quality control measures implemented by the Chinese supplier. Confirm their ability to meet predetermined quality standards and ask for any relevant certifications or test reports.
4. Communication: Establish clear communication channels with the supplier to ensure effective and timely responses. Language barriers can often be a hurdle, so ensure that effective communication is established to avoid any misunderstanding.
Post-Purchase Considerations:
1. Quality assessment: Upon receiving the bulk order, thoroughly inspect the plastic CNC machined parts to ensure they meet the required specifications. Any deviations should be promptly addressed with the supplier.
2. Feedback and dispute resolution: Provide detailed feedback to the supplier regarding the quality, accuracy, and overall satisfaction of the received products. In case of any disputes, try to resolve them through negotiation or mediation, keeping in mind cultural differences and business practices.
3. Long-term partnership: If satisfied with the products and services provided by the Chinese supplier, consider establishing a long-term partnership. This helps build trust, enhances communication, and allows for better negotiation on future orders.
4. Continuous improvement: Provide constructive feedback to the supplier so they can improve their manufacturing processes and meet your future needs more effectively.
It is essential to establish a mutually beneficial relationship with your Chinese supplier to ensure that you receive high-quality plastic CNC machining products in a timely and cost-effective manner.
Sourcing plastic cnc machining from China: Opportunities, Risks, and Key Players
Sourcing plastic CNC machining from China provides various opportunities for businesses worldwide. China is known for its cost-effective manufacturing capabilities, making it an attractive option for companies seeking to reduce production costs. The country has a vast network of suppliers, offering a wide range of plastic materials and CNC machining services at competitive prices.
One significant opportunity of sourcing plastic CNC machining from China is the potential for large-scale production. China’s manufacturing infrastructure enables businesses to handle high-volume orders efficiently. This advantage is especially beneficial for companies with high-demand products or those aiming to enter new markets. Moreover, Chinese suppliers often have the capacity to provide custom solutions, meeting specific requirements and designs.
However, there are inherent risks associated with sourcing from China. Quality control can be challenging, particularly when dealing with numerous suppliers. There is a possibility of receiving substandard plastic parts, which may affect the final product’s functionality and overall customer satisfaction. Maintaining regular communication and establishing a strong quality control process is crucial to mitigate such risks.
A significant risk in the Chinese market is intellectual property (IP) protection. While China has made strides in improving IP rights, cases of counterfeiting and product piracy still exist. It is essential for businesses to take appropriate measures to safeguard their designs and patents, such as signing non-disclosure agreements with suppliers and working with reputable manufacturers who prioritize IP protection.
When sourcing plastic CNC machining from China, several key players dominate the market. Some notable companies include Bomei Precision Hardware Co. Ltd, Bysintek, JIGNXIN Precision Machinery Ltd, and VMT Industry Co. Ltd. These key players have extensive experience in plastic CNC machining and can offer a range of services to suit different customer needs. Performing thorough research, reading customer reviews, and conducting background checks are essential to identify reliable and reputable suppliers.
In conclusion, sourcing plastic CNC machining from China presents opportunities for cost-effective large-scale production and custom solutions. However, businesses must diligently manage risks related to quality control and intellectual property protection. Identifying and partnering with reputable key players in the Chinese market is crucial for a successful sourcing experience.
How to find and select reliable plastic cnc machining manufacturers in China,use google search manufacturers and suppliers
When searching for reliable plastic CNC machining manufacturers in China, Google can be a valuable tool. Here are some steps to help you find and select reputable manufacturers and suppliers using Google search:
1. Start by entering relevant keywords into the Google search bar. For example, search for “plastic CNC machining manufacturers in China” or “reliable plastic CNC machining suppliers.”
2. Review the search results carefully. The top results are often paid advertisements, so focus on the organic search results below.
3. Visit the websites of the manufacturers or suppliers that appear in the search results. Assess the overall design and professionalism of their websites, as well as the range of services they offer.
4. Look for information on their experience and certifications. Check if they mention any partnerships or clients they have worked with in the past. This can give you an idea of their reputation in the industry.
5. Check for product samples or a portfolio section on their website. This will help you evaluate the quality of their CNC machining work and the types of plastic materials they can handle.
6. Look for contact information, such as phone numbers and email addresses, on their website. Reach out to them with any specific questions you may have, such as their manufacturing process, lead time, or pricing.
7. Consider reading online reviews and testimonials about the manufacturers or suppliers. Look for feedback from their previous customers to gauge their reliability and customer satisfaction levels.
8. Take note of the manufacturer’s location. Proximity can play a role in shipping costs and communication ease.
9. Request quotes from multiple manufacturers or suppliers to compare pricing and turnaround time. Ensure that you provide them with detailed information about the project requirements.
10. Before finalizing your decision, consider requesting samples to evaluate the quality of their work and ensure it meets your specifications.
Remember to take your time when researching and selecting a reliable plastic CNC machining manufacturer in China. It’s important to assess their capabilities, reliability, and customer feedback to make an informed decision.
How to check plastic cnc machining manufacturers website reliable,use google chrome SEOquake check if ranking in top 10M
When searching for a reliable plastic CNC machining manufacturer’s website, you can use Google Chrome and the SEOquake tool to check if the website is ranking in the top 10M.
To do this, first, install the SEOquake extension on your Google Chrome browser. Once installed, go to the manufacturer’s website and click on the SEOquake icon. This will give you a detailed analysis of the website’s SEO metrics, including its Google ranking. If the website is ranking within the top 10M, it is a good indication that it is a reliable and reputable source.
Additionally, when evaluating the website, look for clear and detailed information about the company, its experience in plastic CNC machining, the range of services offered, and any certifications or industry affiliations.
It’s also important to check for customer testimonials, case studies, or examples of past projects to gauge the manufacturer’s quality and reliability. A reliable manufacturer will typically have a professional-looking website with clear contact information and a quick response time to any inquiries.
By using the SEOquake tool and evaluating the website’s content, you can determine the reliability of a plastic CNC machining manufacturer’s website and make an informed decision when choosing a supplier for your plastic machining needs.
Top 10 plastic cnc machining manufacturers in China with each 160 words introduce products,then use markdown create table compare
1. First with a focus on precision plastic CNC machining, Company A offers a range of plastic materials such as ABS, PC, POM, PMMA, and more. Their products include plastic parts for automotive, electronics, medical, and consumer goods industries.
2. Company B specializes in custom plastic CNC machining for a wide variety of industries, offering products such as plastic enclosures, panels, and components. They work with materials like PVC, Teflon, and Nylon to create high-quality plastic parts.
3. With a strong emphasis on quality and customer satisfaction, Company C provides plastic CNC machining services for prototypes, low-volume production, and mass production. Their products include custom-made plastic parts for aerospace, defense, and industrial applications.
4. Company D is known for its expertise in CNC machining of engineering plastics, offering products such as insulators, gears, and bushings. They work with materials like PEEK, Polyethylene, and PTFE to provide durable and reliable plastic components.
5. Specializing in high-precision plastic CNC machining, Company E offers a wide range of plastic materials, including Delrin, Ultem, and PET. Their products cater to industries such as telecommunications, robotics, and automotive.
6. Company F focuses on providing custom plastic CNC machining solutions for medical devices, electronic housings, and consumer products. They offer a variety of plastic materials such as HDPE, Polypropylene, and Acrylic for their products.
7. Company G specializes in producing precision plastic parts for the automotive industry, including components for engines, interiors, and exterior trims. They work with materials like ABS, Nylon, and Polycarbonate to meet industry standards and requirements.
8. With a strong commitment to precision and quality, Company H offers plastic CNC machining for a wide variety of industries, including aerospace, electronics, and industrial equipment. Their products range from custom-made plastic parts to large-scale production runs.
9. Company I provides plastic CNC machining services for industries such as telecommunications, consumer goods, and medical devices. Their products are made from a variety of plastic materials such as PVC, Polyethylene, and Polycarbonate to ensure high-quality and durability.
10. Last but not least, Company J specializes in custom plastic CNC machining for the electronics and telecommunications industries, offering products such as plastic enclosures, panels, and components. They work with materials like PVC, Teflon, and Nylon to create high-quality plastic parts.
| Company | Specialization | Materials | Industries |
| ——— | —————- | ———— | ———– |
| A | Precision plastic CNC machining | ABS, PC, POM, PMMA | Automotive, electronics, medical, consumer goods |
| B | Custom plastic CNC machining | PVC, Teflon, Nylon | Various industries |
| C | Quality plastic CNC machining | Various materials | Aerospace, defense, industrial |
| D | CNC machining of engineering plastics | PEEK, Polyethylene, PTFE | Various industries |
| E | High-precision plastic CNC machining | Delrin, Ultem, PET | Telecommunications, robotics, automotive |
| F | Custom plastic CNC machining solutions | HDPE, Polypropylene, Acrylic | Medical devices, electronics, consumer products |
| G | Precision plastic parts for automotive | ABS, Nylon, Polycarbonate | Automotive industry |
| H | Plastic CNC machining for various industries | Various materials | Aerospace, electronics, industrial equipment |
| I | Plastic CNC machining for multiple industries | PVC, Polyethylene, Polycarbonate | Telecommunications, consumer goods, medical devices |
| J | Custom plastic CNC machining | PVC, Teflon, Nylon | Electronics, telecommunications |
Background Research for plastic cnc machining manufacturers Companies in China, use qcc.com archive.org importyeti.com
When it comes to plastic CNC machining manufacturers in China, several resources can be utilized for conducting background research. Three reliable platforms for this purpose include qcc.com, archive.org, and importyeti.com.
Qcc.com is a comprehensive business database that provides information on various companies in China. This platform offers a wide range of data, such as company registration details, financial information, production capacity, and contact information. By searching for plastic CNC machining manufacturers on qcc.com, researchers can gather important background information about these companies.
Archive.org is a website that allows users to access archived versions of different web pages. It can be helpful for examining a company’s website history, tracking changes, and understanding the evolution of its services, products, or business strategies over time. Researchers can utilize this platform to review the websites of various plastic CNC machining manufacturers and gain valuable insights into their past operations.
Another valuable resource is importyeti.com, which supplies information about import and export data. By searching for specific plastic CNC machining manufacturers, researchers can access data on their overseas shipments, including details about the type and quantity of products exported, the countries they were exported to, and the names of the importing companies. This information can help gauge a manufacturer’s market reach and reputation.
In conclusion, for background research on plastic CNC machining manufacturers in China, platforms like qcc.com, archive.org, and importyeti.com are useful in obtaining essential company details, reviewing historical changes, and accessing import-export data. These resources can collectively provide researchers with a comprehensive understanding of the companies in question.
Leveraging Trade Shows and Expos for plastic cnc machining Sourcing in China
Trade shows and expos are excellent platforms for sourcing plastic CNC machining services in China. These events gather a wide range of suppliers, manufacturers, and industry professionals in one place, allowing buyers to connect with potential suppliers, gather information, and make informed decisions on partnerships.
Participating in trade shows and expos related to plastic CNC machining offers numerous advantages. Firstly, these events provide an opportunity to meet suppliers face-to-face, fostering personalized communication and building trust. This direct interaction enables buyers to assess the potential suppliers’ capabilities, understand their processes, and evaluate their products’ quality firsthand.
Moreover, trade shows and expos enable buyers to compare various suppliers and their offerings in a short span of time. With multiple exhibitors showcasing their products and services, interested buyers can quickly identify the ones that align best with their requirements and evaluate their competitiveness. This allows for efficient supplier screening and shortlisting.
Expos also provide a platform to stay updated on the latest trends, technologies, and innovations in the plastic CNC machining industry. Seminars, workshops, and product demonstrations offer valuable insights into emerging techniques, materials, and equipment. This knowledge empowers buyers to have meaningful discussions with potential suppliers, facilitating better decision-making and ensuring the selection of the most suitable and advanced partners.
To maximize the effectiveness of sourcing at trade shows and expos, it is essential to prepare thoroughly. Buyers should research the participating exhibitors in advance, identify key suppliers of interest, and craft a list of relevant questions. This preparation ensures that valuable time is not wasted and that essential information is gathered during the event.
In conclusion, trade shows and expos serve as invaluable platforms for sourcing plastic CNC machining services in China. These events facilitate direct communication, allow for quick comparisons, and provide insight into industry trends. By utilizing these opportunities and adequately preparing, businesses can find reliable suppliers for their plastic CNC machining needs.
The Role of Agents and Sourcing Companies in Facilitating plastic cnc machining Purchases from China
Agents and sourcing companies play a critical role in facilitating plastic CNC machining purchases from China by streamlining the procurement process and ensuring quality and reliability.
Agents in China act as intermediaries between the buyer and the supplier, helping to bridge the communication and cultural gap. They have close relationships with a network of manufacturers and can provide valuable insights into the capabilities and reputation of each supplier. They also assist in negotiations, ensuring that the buyer gets the best possible price and terms for their purchase. Agents can also provide quality control and inspection services to ensure that the products meet the buyer’s specifications and standards.
Sourcing companies, on the other hand, have a broader scope of services and often work with multiple manufacturers to offer a range of options to the buyer. They can help in identifying the most suitable suppliers for the specific plastic CNC machining requirements, based on factors such as capacity, expertise, and price. Sourcing companies also typically have their own quality control processes in place and can provide more comprehensive support in product development, logistics, and supply chain management.
Overall, both agents and sourcing companies play crucial roles in facilitating plastic CNC machining purchases from China by providing expertise, network, and support throughout the procurement process. Their involvement helps to ensure that the buyer can access a wider pool of suppliers, negotiate better terms, and have confidence in the quality and reliability of the products they are purchasing.
Price Cost Research for plastic cnc machining manufacturers Companies in China, use temu.com and 1688.com
When conducting price cost research for plastic CNC machining manufacturers in China, two popular websites to use are temu.com and 1688.com. These platforms provide an extensive list of suppliers and manufacturers in China, making it easy to compare prices and quality.
Using these platforms, you can search for plastic CNC machining manufacturers and request quotes for your specific requirements. It is important to provide detailed specifications, such as the type of plastic material, quantity, tolerance, finish, and any other special requirements.
Once you receive quotes from multiple manufacturers, you can compare the prices and also consider the quality and reputation of the manufacturer. It’s important to note that the cheapest option may not always be the best in terms of quality and reliability.
When comparing prices, it’s also important to consider other factors such as shipping costs, lead times, and payment terms. Some manufacturers may offer lower prices but have higher shipping costs, while others may have longer lead times.
Additionally, it’s a good idea to communicate directly with the manufacturers to negotiate prices and discuss any custom requirements. Building a good relationship with the manufacturer can also lead to better pricing and flexibility for future orders.
Overall, using platforms like temu.com and 1688.com can help you gather information on the pricing and cost of plastic CNC machining manufacturers in China, allowing you to make informed decisions for your manufacturing needs.
Shipping Cost for plastic cnc machining import from China
The shipping cost for plastic CNC machining import from China can vary depending on several factors such as the size and weight of the shipment, the shipping method, and the destination country. Generally, there are three main shipping methods for importing goods from China: air freight, sea freight, and express courier services.
Air freight is the fastest shipping method but also the most expensive. The cost of air freight is calculated based on the weight and dimensions of the shipment, and the distance it needs to travel. On average, the cost of air freight from China to most destinations can range from $5 to $10 per kilogram.
Sea freight is a more cost-effective shipping method for larger shipments. The cost of sea freight is calculated based on the volume of the shipment and the distance it needs to travel. On average, the cost of sea freight from China to most destinations can range from $300 to $800 per cubic meter.
Express courier services such as DHL, UPS, and FedEx are often used for smaller and urgent shipments. The cost of express courier services is usually higher than sea freight but lower than air freight. The cost is calculated based on the weight and dimensions of the shipment, and the delivery time frame. On average, the cost of express courier services from China to most destinations can range from $20 to $50 per kilogram.
It is important to note that in addition to the shipping cost, there may be other charges such as customs duties, import taxes, and handling fees that need to be considered when importing goods from China. It is recommended to work with a reliable freight forwarder or shipping agent to get an accurate quote and to ensure a smooth importing process.
Compare China and Other plastic cnc machining Markets: Products Quality and Price,Visible and Hidden Costs
China is a leading plastic CNC machining market, offering a wide range of products at competitive prices. However, the quality of products from China can vary widely, with some manufacturers producing lower quality items compared to other markets. In contrast, other plastic CNC machining markets, such as Europe and North America, are known for their high-quality products. These markets have strict regulations and standards in place, ensuring that products meet certain quality criteria.
In terms of price, China has a competitive edge due to its lower labor and production costs. This allows Chinese manufacturers to offer products at a lower price point compared to other markets. However, it is important to consider the visible and hidden costs associated with purchasing products from China. This includes shipping, import duties, and potential quality control issues. On the other hand, products from other markets may have a higher upfront cost but may come with fewer hidden costs, as they are often produced under stricter regulations and quality standards.
When comparing the visible and hidden costs, it is crucial to consider the potential risks and benefits of purchasing from different markets. While China may offer lower prices, the quality and potential additional costs should be carefully assessed. Other markets may offer higher quality products with fewer hidden costs, despite a higher upfront price.
Overall, China’s plastic CNC machining market offers a wide range of products at competitive prices, but with varying quality and potential hidden costs. In contrast, other markets are known for their high-quality products with potentially fewer hidden costs, despite a higher upfront price. It is essential for buyers to carefully evaluate their options and consider the trade-offs between product quality, price, and visible and hidden costs when choosing a plastic CNC machining market.
Understanding Pricing and Payment Terms for plastic cnc machining: A Comparative Guide to Get the Best Deal
When it comes to plastic CNC machining, understanding pricing and payment terms is crucial in order to secure the best deal possible. Here is a comparative guide to help you navigate through this process and ensure you get the best value for your money.
Firstly, it is important to consider the pricing structure of plastic CNC machining. Typically, pricing is determined based on several factors, including the complexity of the part, material requirements, quantity, and machining time. Some manufacturers may have a minimum order quantity, so be sure to check if it aligns with your project needs. It is advisable to obtain quotes from multiple suppliers to compare prices and services.
In terms of payment terms, there are a few common options to consider. One is the upfront payment model, where you pay the total cost of the project before manufacturing begins. Another option is a partial payment structure, where you pay a percentage upfront and the remaining balance upon completion. Some manufacturers might offer flexible payment terms, such as installment payments, which can be beneficial for budgeting purposes.
To ensure you are getting the best deal, consider the added value that different suppliers may offer. Some may provide additional services like design assistance, material sourcing, or post-machining finishing options. These value-added services can help streamline your project and potentially save costs in the long run.
It is also crucial to verify the quality and reliability of the manufacturer. Look for certifications like ISO 9001, which indicates adherence to quality management standards. Reviews and testimonials from previous clients can provide insights into the supplier’s performance and customer satisfaction.
When comparing quotes, be cautious of extremely low pricing as it may indicate compromising on quality or using subpar materials. It is recommended to choose a supplier that offers a fair balance between quality and pricing.
Lastly, consider the manufacturing lead time. While faster turnaround times might be desirable, ensure that it aligns with your project timeline and does not compromise the quality of the end product.
In conclusion, understanding the pricing structure, payment terms, added value, and reliability of different plastic CNC machining suppliers is vital to securing the best deal. By comparing quotes, considering value-added services, and selecting a reputable manufacturer, you can ensure a successful and cost-effective plastic CNC machining project.
Chinese Regulations and Industry Standards Certifications for plastic cnc machining,Import Regulations and Customs for plastic cnc machining from China
Chinese Regulations and Industry Standards Certifications for plastic CNC machining:
In China, plastic CNC machining is subject to a variety of regulations and industry standards certifications to ensure the quality, safety, and environmental compliance of the products. These regulations and certifications include:
1. ISO 9001: This certification ensures that the plastic CNC machining process adheres to international standards for quality management systems.
2. ISO 14001: This certification ensures that the plastic CNC machining process follows international standards for environmental management systems.
3. ROHS: This regulation restricts the use of certain hazardous substances in electrical and electronic equipment, including plastic CNC machined components.
4. REACH: This regulation controls the use of chemicals in products to protect human health and the environment. It is applicable to various plastic materials used in CNC machining.
5. UL Listing: UL certification ensures compliance with safety standards in various industries requiring plastic CNC machined products.
Import Regulations and Customs for plastic CNC machining from China:
When importing plastic CNC machining products from China, it is important to understand the import regulations and customs procedures to ensure a smooth and compliant process. Some key considerations include:
1. Customs Duties: Importers should be aware of the applicable customs duties and tariffs associated with plastic CNC machining products. These charges may vary depending on the specific product category and its country of origin.
2. Product Certification: Importers should ensure that the plastic CNC machined products comply with the necessary certifications and standards required by their own country. This may include verifying conformity with safety, health, and quality standards.
3. Packaging and Labeling: The packaging and labeling of plastic CNC machined products should meet the import country’s requirements, including proper labeling of materials, country of origin, and handling instructions.
4. Import Documentation: Importers should ensure that they have all the necessary documentation, such as invoice, packing list, bill of lading, and certificates of origin, to facilitate customs clearance.
5. Intellectual Property Rights: Importers need to ensure that the plastic CNC machining products they are importing do not violate any intellectual property rights or patents held by others.
By understanding these regulations and customs procedures, importers can ensure a smooth and compliant import process for plastic CNC machining products from China.
Sustainability and Environmental Considerations in plastic cnc machining Manufacturing
Sustainability and environmental considerations play a crucial role in plastic CNC machining manufacturing processes. While CNC machining offers various benefits such as precision, repeatability, and versatility, it also has the potential to generate negative environmental impacts. Therefore, manufacturers must adopt sustainable practices to mitigate these impacts and ensure responsible production.
One major environmental concern in plastic CNC machining is the generation of plastic waste. CNC machines produce plastic chips and scrap materials during the machining process. These waste materials need to be properly managed to prevent them from ending up in landfills or polluting natural ecosystems. Manufacturers can implement recycling programs to collect and reuse these plastic waste materials, reducing the demand for virgin plastic and minimizing the overall environmental footprint.
Another important consideration is the selection of materials. Plastic CNC machining often utilizes a wide range of plastics, each with different environmental characteristics. Manufacturers should consider using environmentally friendly materials, such as biodegradable or recycled plastics, which have a lower impact on ecosystems and can contribute to a circular economy. Additionally, optimizing material usage by minimizing waste through careful design and machining strategies is important.
Energy consumption is another area where sustainability practices can be implemented. CNC machines require significant amounts of energy to operate, which contributes to greenhouse gas emissions and relies on non-renewable resources. Manufacturers can reduce their carbon footprint by using energy-efficient machines, exploring renewable energy sources, and implementing energy management systems to minimize energy waste.
Furthermore, water usage and chemical management are important considerations in sustainable plastic CNC machining. Manufacturers should aim to reduce water consumption and properly treat and manage any water or chemical waste generated during the machining process. Implementing technologies like closed-loop cooling systems and using eco-friendly coolant fluids can help minimize the environmental impact of water and chemical usage.
In conclusion, sustainability and environmental considerations are essential in plastic CNC machining manufacturing. By adopting recycling programs, selecting environmentally friendly materials, optimizing energy usage, and managing water and chemical waste responsibly, manufacturers can effectively minimize their environmental footprint and contribute to a more sustainable and responsible manufacturing industry.
List The Evolution history of “plastic cnc machining”
Plastic CNC machining has gone through significant evolution since its inception. In the early years of CNC machining, plastic parts were typically made using manual milling and turning processes. This involved a lot of manual labor and was time-consuming.
In the 1980s, computer numerical control (CNC) technology began to revolutionize the manufacturing industry. This allowed for more precise and efficient production of plastic parts. CNC machines could now be programmed to perform complex machining operations on plastic materials with high accuracy.
As the demand for high-quality plastic parts grew, CNC machining continued to evolve. The introduction of advanced CAD/CAM software further improved the precision and capabilities of CNC machines. This allowed for the design and production of highly intricate and complex plastic components.
In recent years, the development of multi-axis CNC machines has further expanded the capabilities of plastic CNC machining. These machines can perform simultaneous machining operations on multiple axes, allowing for even more complex geometries to be achieved in plastic parts.
Additionally, advancements in cutting tools, workholding, and material handling technologies have further enhanced the efficiency and accuracy of plastic CNC machining processes. This has led to the production of high-quality plastic parts with tight tolerances and excellent surface finishes.
Today, plastic CNC machining has become a widely used manufacturing process in various industries, including automotive, aerospace, medical, and consumer goods. The continuous evolution of CNC technology and the integration of automation and robotics have further improved the speed and efficiency of plastic CNC machining, making it an essential process in modern manufacturing.
The Evolution and Market Trends in plastic cnc machining Industry
The plastic CNC machining industry has seen significant evolution over the years, driven by advancements in technology, changing market trends, and increasing demand for high-quality plastic components. CNC machining, which involves computer-controlled processes for cutting and shaping plastic materials, has become a preferred method for producing precise and complex plastic parts.
One of the key evolutions in the plastic CNC machining industry is the adoption of advanced CNC machines and software. This has led to improved efficiency, accuracy, and productivity in plastic machining operations. Additionally, the industry has witnessed the development of new materials and cutting techniques, allowing for a wider range of plastic materials to be machined with high precision.
Market trends in the plastic CNC machining industry have also shifted in response to changing consumer demands and technological advancements. There is a growing demand for custom-designed plastic components in various industries such as aerospace, automotive, medical, and consumer goods. This has led to an increased focus on providing bespoke CNC machining services to meet specific customer requirements.
Furthermore, sustainability and environmental impact have become important considerations in the plastic CNC machining industry. As a result, there is a growing trend towards using recyclable and eco-friendly plastic materials, as well as implementing sustainable manufacturing practices.
Looking ahead, the plastic CNC machining industry is expected to continue evolving with the integration of advanced technologies such as 3D printing and automation. This will further enhance the capabilities of CNC machining for producing highly complex and customized plastic components. Additionally, the industry is likely to see continued growth in the demand for high-precision plastic parts across a wide range of applications.
In conclusion, the plastic CNC machining industry has evolved significantly, driven by technological advancements, changing market trends, and increasing demand for high-quality plastic components. As the industry continues to innovate and adapt to emerging trends, it is poised for continued growth and development in the coming years.
Custom Private Labeling and Branding Opportunities with Chinese plastic cnc machining Manufacturers
If you are looking to create custom private labeling and branding opportunities with Chinese plastic CNC machining manufacturers, you are in luck. Many Chinese manufacturers offer the option to customize products with your own branding and labeling, providing a unique and personalized product for your business.
When working with Chinese plastic CNC machining manufacturers, you can collaborate with their design and engineering teams to create custom products that meet your specific branding and labeling requirements. This can include incorporating your logo, company name, and specific product details into the design and manufacturing process.
Additionally, working with Chinese manufacturers can be a cost-effective solution for creating custom branded products. With competitive pricing and high-quality manufacturing capabilities, you can create custom products without the high costs typically associated with custom manufacturing.
Furthermore, by partnering with Chinese plastic CNC machining manufacturers, you can benefit from their expertise in the industry. They can provide valuable insights and guidance on the best materials, manufacturing processes, and design options to ensure that your custom branded products are of the highest quality.
In conclusion, working with Chinese plastic CNC machining manufacturers provides you with the opportunity to create custom private labeling and branding opportunities for your business. By collaborating with their design and engineering teams, you can create unique products that are tailored to your specific branding requirements, at a competitive price and with high-quality manufacturing capabilities.
Tips for Procurement and Considerations when Purchasing plastic cnc machining
When procuring plastic CNC machining, there are several tips and considerations to keep in mind:
1. Material selection: Identify the specific type of plastic material that suits your requirements. Consider factors such as durability, strength, heat resistance, chemical compatibility, and aesthetics.
2. Quality assurance: Ensure that the supplier has the necessary certifications and quality control measures in place. Request samples or prototypes to assess the quality of the finished products.
3. Customization options: Discuss with the supplier their ability to customize the plastic CNC machining to meet your unique specifications. This includes features such as size, shape, surface finish, and additional machining processes like drilling or threading.
4. Production capabilities: Investigate the supplier’s production capacity and lead times. Make sure they have the necessary equipment, expertise, and resources to handle your volume requirements and deliver within the desired timeframe.
5. Price competitiveness: Obtain quotes from multiple suppliers to compare prices. However, keep in mind that the cheapest option may not always provide the best quality. Consider value for money rather than solely focusing on the lowest price.
6. Technical support: Determine whether the supplier offers technical support or assistance during the design and engineering stage. This can be valuable in optimizing your design for manufacturability and cost-efficiency.
7. Environmental considerations: Inquire about the supplier’s sustainability practices, such as recycling or minimizing waste generation. Selecting a supplier that aligns with your organization’s environmental values can contribute to a more sustainable procurement strategy.
8. Communication and responsiveness: Establish clear communication channels and ensure that the supplier is responsive to your inquiries and concerns. Prompt and effective communication is crucial in ensuring a smooth procurement process.
9. Long-term partnership: Consider the possibility of establishing a long-term partnership with the supplier. Building a mutually beneficial relationship can lead to better pricing, improved quality, and a more reliable supply chain.
10. Intellectual property protection: If you have proprietary designs or confidential information, discuss the supplier’s commitment to intellectual property protection. Ensure they have appropriate measures in place to protect your design and prevent unauthorized use.
In summary, when purchasing plastic CNC machining, it is important to carefully consider factors such as material selection, quality assurance, customization options, production capabilities, price competitiveness, technical support, environmental considerations, communication, long-term partnership potential, and intellectual property protection. By taking these considerations into account, you can find a supplier that meets your specific requirements and ensures a successful procurement process.
FAQs on Sourcing and Manufacturing plastic cnc machining in China
Q1: What is plastic CNC machining?
Plastic CNC machining is a manufacturing process that utilizes computer numerical control (CNC) machines to shape plastic materials into desired parts or components. It involves the use of milling machines, lathes, or routers that are programmed to cut and shape plastic materials according to specific designs.
Q2: Why should I consider sourcing and manufacturing plastic CNC machining in China?
China has emerged as a global manufacturing hub, offering cost-effective and high-quality plastic CNC machining services. Chinese manufacturers have advanced CNC technology, skilled labor, and a vast supply chain network, enabling them to provide competitive pricing and quick turnaround times for plastic machining projects. Moreover, China’s plastic industry has access to a wide range of raw materials, ensuring flexibility in material options for CNC machining processes.
Q3: How can I find reliable plastic CNC machining suppliers in China?
To find reliable suppliers, it is advisable to conduct thorough research and due diligence. Utilize online platforms or directories that specialize in connecting buyers with verified Chinese suppliers. It is also necessary to review supplier profiles, check certifications, read customer reviews, and request samples or prototypes to assess the quality of their work.
Q4: What considerations should I keep in mind when sourcing plastic CNC machining services from China?
Communication can be a critical factor, so it is essential to verify the supplier’s proficiency in English or agree on a translator if needed. Additionally, ascertain whether the chosen supplier can meet your specific requirements in terms of material selection, precision, tolerance levels, and surface finishes. Delivery time, packaging, and shipping arrangements must also be discussed and agreed upon beforehand.
Q5: How can I ensure the quality of plastic CNC machined parts manufactured in China?
It is vital to establish a clear quality control plan with your supplier, including regular inspections and quality assurance measures throughout the manufacturing process. Requesting samples or prototypes before full production can help identify any potential quality issues early. Open communication, regular updates, and setting mutual expectations can contribute to maintaining the desired quality standards.
Q6: How can I manage logistics and shipping for plastic CNC machined parts from China?
Collaborate with your chosen supplier to define shipping arrangements, including transportation modes (air, sea, or land), packaging, and insurance. Engaging a professional freight forwarder or logistics company specializing in international shipping from China can streamline the process and provide assistance in customs clearance and documentation.
In summary, sourcing and manufacturing plastic CNC machining in China offers several advantages, such as cost-effectiveness, a wide range of material options, and access to advanced technology. However, thorough research, quality control measures, and effective communication are crucial to ensure a successful partnership with Chinese suppliers.
Why contact sourcifychina.com get free quota from reliable plastic cnc machining suppliers?
Sourcifychina.com offers free quotas from reliable plastic CNC machining suppliers for a variety of reasons. These reasons include:
1. Building trust and establishing relationships: By providing free quotas, Sourcifychina.com aims to create a sense of trust and build rapport with potential customers. This helps establish a strong foundation for long-term partnerships with reliable suppliers.
2. Demonstrating credibility: Offering free quotas shows that Sourcifychina.com has vetted and verified the plastic CNC machining suppliers they work with. This demonstrates their credibility as a sourcing platform and ensures that customers are connected with reliable and trustworthy suppliers.
3. Encouraging customer engagement: Providing a free quota incentivizes potential customers to engage with Sourcifychina.com and its suppliers. This engagement allows both parties to understand each other’s requirements, capabilities, and expectations before committing to a full order or partnership.
4. Showcasing supplier capabilities: Free quotas give suppliers a chance to showcase their expertise and capabilities in plastic CNC machining. By delivering a sample or a quote, suppliers can demonstrate the quality of their work, their production capacity, and their ability to meet specific requirements.
5. Streamlining the sourcing process: Offering a free quota helps streamline the sourcing process for customers. It allows them to assess different suppliers without any upfront costs, saving time and effort in the initial stage of supplier selection.
Overall, providing a free quota from reliable plastic CNC machining suppliers benefits both Sourcifychina.com and potential customers. It builds trust, establishes credibility, encourages customer engagement, showcases supplier capabilities, and streamlines the sourcing process, ultimately leading to successful partnerships and satisfied customers.