Introduce about plastics machining guide,Qulity,Cost,Supplier,Certification,Market,Tips,FAQ
Plastics machining is the process of shaping or machining plastic materials into desired shapes or products. This machining guide provides essential information about various aspects related to plastics machining.
Quality is a crucial aspect in plastics machining. Depending on the application, different plastic materials may be chosen to meet specific quality requirements such as strength, durability, and chemical resistance. Understanding the properties of different plastics is essential to ensure the desired quality of the final product.
Cost is another important consideration in plastics machining. Different plastics have varying costs, and the choice of material can significantly impact the overall project cost. Factors such as the complexity of the design, tolerance requirements, and quantity needed also affect the cost of plastics machining.
Finding a reliable supplier is vital to ensure the availability of high-quality plastic materials and machining services. It is essential to work with a supplier that offers a wide range of plastic materials, has a strong track record in plastics machining, and provides excellent customer service.
Certification is an important aspect to consider when selecting a plastics machining supplier. ISO certifications such as ISO 9001 ensure that a supplier follows specific quality management standards, which can guarantee the quality and consistency of their products and services.
The market for plastics machining is vast and diverse. It is used in various industries, including automotive, aerospace, electronics, healthcare, and consumer goods. The demand for plastics machining continues to grow due to the increasing need for lightweight and durable materials.
Here are some tips for successful plastics machining: carefully select the appropriate plastic material, consider the design and functionality of the parts, optimize machining parameters, and ensure proper cooling and lubrication during the machining process.
Frequently Asked Questions (FAQ) about plastics machining may include inquiries about the suitable plastic materials for specific applications, machining tolerances, lead times, and cost factors.
In conclusion, plastics machining is a complex process that requires careful consideration of quality, cost, supplier reliability, certification, and market trends. By understanding the fundamentals of plastics machining and following the provided tips, businesses can achieve successful outcomes in their plastic machining projects.
Types of plastics machining
Plastics machining refers to the process of shaping and forming plastic materials into various products using different techniques. There are several types of plastics machining methods available, each with its own advantages and applications. Here are some of the commonly used plastics machining methods:
1. CNC Machining: Computer Numerical Control (CNC) machining is a precise and automated method of plastic machining. It involves the use of computer-controlled cutting tools to remove material from a plastic block or sheet. CNC machining offers high accuracy, repeatability, and complex geometries, making it suitable for manufacturing prototypes, custom parts, and intricate components.
2. Injection Molding: Injection molding is a widely used plastics machining method for mass production of plastic products. It involves injecting molten plastic material into a mold cavity under high pressure and then cool it to solidify. Injection molding allows for high production rates, consistency, and versatility in creating products of various shapes and sizes.
3. Extrusion: Plastic extrusion is a process of creating long continuous shapes by forcing molten plastic material through a die. The plastic material is melted and pushed through a specialized extruder, which shapes it into a specific profile or cross-section. Extrusion is commonly used for manufacturing plastic tubes, pipes, rods, and sheets with constant cross-sections.
4. Vacuum Forming: Vacuum forming is a technique used to create 3D shapes from thin sheets of plastic. The plastic sheet is heated and placed over a mold, and a vacuum is applied to force the plastic to take the shape of the mold. Vacuum forming is often used for making packaging trays, trays, and exterior parts of various products.
5. Thermoforming: Thermoforming is similar to vacuum forming but involves heating a sheet of plastic and pressing it onto a mold using pressure instead of vacuum. This method is commonly used for making disposable cups, food packaging, and automotive interior components.
6. Laser Cutting: Laser cutting is a precise method where a high-powered laser beam is used to cut plastic materials into desired shapes. It offers high accuracy, speed, and flexibility in cutting intricate designs on various plastic materials.
7. Waterjet Cutting: Waterjet cutting involves using a high-pressure jet of water mixed with abrasive materials to cut through plastic materials. It is known for its accuracy, versatility, and is particularly suitable for cutting thick plastic materials.
These are just a few examples of the types of plastics machining methods available. Each technique has its own advantages and limitations, and the choice of method depends on the desired product, material properties, and manufacturing requirements.
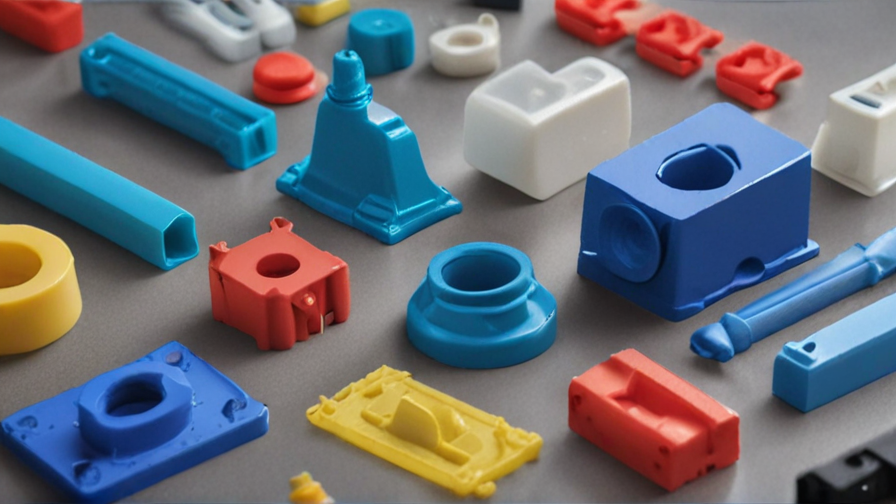
Pros and Cons of Using plastics machining
Plastics machining, also known as plastic fabrication or plastic machining, involves the process of creating precise and complex components or products from various types of plastics. As with any manufacturing process, there are both advantages and disadvantages to using plastics machining. Here are some of the pros and cons to consider:
Pros of using plastics machining:
1. Versatility: Plastics machining offers a wide range of possibilities in terms of design and shape. It allows for the production of intricate and complex parts that may be challenging or impossible to create with other manufacturing methods.
2. Cost-effectiveness: Plastics machining can be a cost-effective option, especially when producing small to medium-sized quantities of parts. It eliminates the need for expensive molds or tooling, and reduces the time required for setup and production.
3. Flexibility: Plastic machining enables the use of various types of plastics, such as acrylics, polycarbonates, and polypropylene. Each type of plastic has its own properties and characteristics, allowing manufacturers to choose the material that best suits their specific requirements.
4. Quick turnaround time: With plastics machining, parts can be produced relatively quickly, especially compared to other manufacturing methods like injection molding. This makes it suitable for rapid prototyping and fast production cycles.
Cons of using plastics machining:
1. Limited production scale: Plastics machining may not be as efficient or cost-effective for large-scale production runs. As the production process is manual, it may not be able to match the speed and cost efficiencies of automated processes like injection molding.
2. Material waste: Machining plastics can generate a significant amount of waste material. This is especially true for complex designs or parts with intricate features, where more material may need to be removed during the machining process.
3. Surface finish limitations: Plastics machining may not always achieve the same level of smoothness and finish as other manufacturing methods, such as injection molding. Depending on the complexity of the part and the machining technique used, the surface finish may have visible marks or roughness.
4. Tooling costs: While plastics machining eliminates the need for expensive molds or tooling, it still requires the use of cutting tools. These tools need to be maintained, replaced, or sharpened regularly, which can add to the overall cost of production.
In conclusion, plastics machining offers versatility, cost-effectiveness, and quick turnaround time, making it suitable for small to medium-sized production runs. However, it may not be ideal for large-scale production, can generate waste material, and may have limitations in terms of surface finish. Careful consideration of these pros and cons is necessary when deciding whether plastics machining is the most suitable manufacturing process for a particular application.
plastics machining Reference Specifications (varies for different product)
When it comes to plastics machining, it is essential to follow reference specifications that vary depending on the specific product being manufactured. These specifications outline the guidelines and requirements needed to produce high-quality plastic components.
One crucial aspect in plastics machining is material selection. Proper selection of the plastic material is critical as it directly impacts the machining process, the component’s performance, and its durability. Reference specifications provide information on the recommended materials, their physical properties, and their compatibility with the intended application.
In terms of machining processes, reference specifications provide guidelines on various techniques such as turning, milling, drilling, and grinding. They specify the tool types, speeds, feeds, and cutting depths required for different plastics. Moreover, they provide recommendations on the use of coolants and lubricants to optimize the machining process and prevent heat-related issues or workpiece damage.
Besides machining techniques, reference specifications also cover other manufacturing aspects such as dimensional tolerances, surface finishes, and part quality requirements. These specifications define the acceptable range of dimensional variations and surface roughness, ensuring the produced components meet the desired functional and aesthetic standards.
To assure consistent and reliable production, reference specifications may also include inspection and testing procedures. They outline the necessary equipment, measurement techniques, and acceptance criteria for verifying the component’s dimensions, material properties, and performance characteristics. This helps in ensuring that the manufactured components conform to the required standards and meet customer expectations.
Furthermore, reference specifications also address post-machining processes like annealing, polishing, welding, or assembly if they are applicable to the product. They provide instructions and guidelines for ensuring proper execution of these processes, resulting in the desired product functionality and durability.
In conclusion, plastics machining reference specifications serve as a comprehensive guide for manufacturing plastic components. They cover aspects such as material selection, machining techniques, dimensional tolerances, surface finishes, inspection procedures, and post-machining processes. Adhering to these specifications ensures the production of high-quality plastic components that meet the required standards and customer expectations.
Applications of plastics machining
Plastics machining, also known as plastic fabrication or plastic manufacturing, involves shaping and forming plastic materials into desired shapes and sizes. This process is widely used in various industries due to the unique properties and versatility of plastics. Here are some applications of plastics machining:
1. Packaging Industry: Plastics machining plays a crucial role in the packaging industry. It is used in the manufacturing of bottles, containers, trays, and other packaging materials. Plastic packaging offers advantages such as lightweight, durability, and flexibility, making it an ideal choice for various products.
2. Automotive Industry: Plastics are extensively used in the automotive industry for components such as dashboards, bumpers, door panels, and interior trims. Plastics provide design flexibility, weight reduction, and improved fuel efficiency in vehicles. Machining allows for the precise and efficient production of these components.
3. Aerospace Industry: Plastics machining is highly valued in the aerospace industry due to its ability to produce lightweight parts with high strength. It is used to manufacture various components like housings, brackets, and interior fittings. These lightweight components help reduce fuel consumption and increase aircraft efficiency.
4. Medical Industry: Plastics machining is crucial in the medical industry for the production of medical devices, equipment, and components. Plastics are preferred in medical applications due to their biocompatibility, sterilizability, and chemical resistance. Examples include surgical tools, prosthetics, implantable devices, and diagnostic equipment.
5. Electronics Industry: Plastics machining is widely used in the electronics industry for the production of enclosures, connectors, and other components. Plastics offer excellent electrical insulation properties, which are vital for electronic devices. The machining process allows for the precise creation of intricate shapes required in electronic applications.
6. Consumer Goods Industry: Plastics machining is prevalent in the manufacturing of consumer goods such as toys, kitchenware, and household appliances. Plastics provide versatility in design, color options, and durability, making them ideal for consumer products. Machining ensures that each product is accurately produced to meet the desired specifications.
7. Construction Industry: Plastics machining is employed in the construction industry for various applications, including windows, doors, pipes, and insulation materials. Plastic materials offer lightweight alternatives to traditional construction materials, reducing costs and simplifying installation. Machining allows for the precise shaping and customization of these components.
In conclusion, plastics machining is widely utilized across various industries due to its numerous advantages. It enables the production of lightweight, durable, and cost-effective components, making it an integral part of different manufacturing processes. The applications mentioned above are just a few examples of how plastics machining contributes to different sectors.
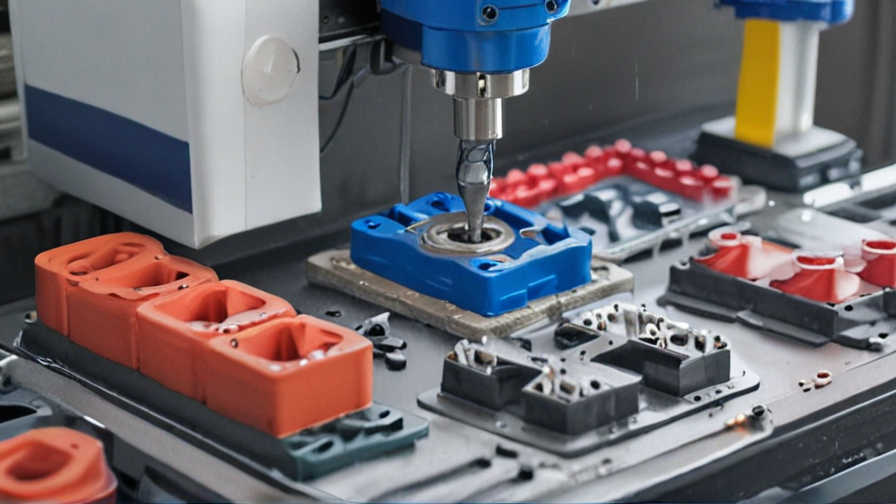
The Work Process and how to use plastics machining
Plastics machining refers to the process of shaping and modifying plastic materials using cutting tools and equipment. It is commonly used in various industries for creating precise and intricate plastic components.
The work process of plastics machining typically involves the following steps:
1. Design: The first step is to create a detailed design of the required plastic component. This includes specifying dimensions, tolerances, and material selection.
2. Material preparation: Once the design is finalized, the appropriate plastic material is selected and prepared for machining. This may involve cutting the plastic sheet, rod, or block to the desired size.
3. CNC programming: Computer Numerical Control (CNC) machines are commonly used for plastics machining. The design specifications are translated into machine instructions through programming. This includes determining the tool paths, cutting speeds, and feed rates.
4. Machining: The CNC machine is set up and the plastic material is securely clamped into place. The cutting tool, typically a drill bit or end mill, is then used to remove excess material and shape the component according to the design. This may involve drilling, milling, turning, or other machining operations.
5. Finishing operations: Once the basic shape is achieved, additional finishing operations may be performed. This includes deburring, smoothing, and polishing the plastic component to improve its surface finish and remove any rough edges.
6. Inspection and quality control: After machining and finishing, the plastic component is thoroughly inspected to ensure it meets the required specifications. This may involve measuring dimensions, checking tolerances, and conducting performance tests.
7. Assembly or further processing: After passing quality control, the plastic component may be assembled with other parts or undergo additional processing such as painting, coating, or surface treatment, depending on the specific application.
In summary, plastics machining involves designing, preparing materials, programming CNC machines, performing machining operations, conducting quality control, and potentially further processing or assembly. It is a precise and versatile manufacturing method widely used in industries such as automotive, aerospace, electronics, and healthcare to produce a wide range of plastic components.
Quality Testing Methods for plastics machining and how to control the quality
When it comes to ensuring the quality of plastics machining, there are various methods that can be employed. Here are a few essential quality testing methods and approaches that can effectively control the quality of plastic machining processes.
1. Dimensional Inspection: This method involves measuring the geometric dimensions of machined plastic parts using precise tools such as micrometers, calipers, and coordinate measuring machines (CMMs). This helps ensure that the dimensions of the finished parts meet the required specifications.
2. Visual Inspection: Visual inspection is an important method to detect any visible defects on the machined plastic parts, such as surface imperfections, scratches, or blemishes. This can be done by trained inspectors or through automated optical inspection (AOI) systems, which use cameras to capture and analyze images of the parts.
3. Mechanical Testing: Mechanical testing involves subjecting machined plastic parts to various mechanical stresses to assess their strength, resilience, and durability. Common mechanical tests include tensile strength testing, flexural testing, impact resistance testing, and hardness testing.
4. Chemical Resistance Testing: Plastics are often exposed to various chemicals in their intended applications. Chemical resistance testing evaluates the compatibility of the material with different substances, ensuring it can withstand exposure without degradation, such as swelling or loss of mechanical properties.
5. Manufacturing Process Monitoring: Quality control can be enhanced by continuously monitoring the manufacturing process parameters, such as cutting speed, feed rate, and coolant flow. Monitoring technologies, such as sensors and control systems, can detect abnormalities or deviations from the desired parameters, allowing for timely adjustments to minimize defects.
To control the quality in plastics machining, several measures can be implemented:
1. Implementing Standard Operating Procedures (SOPs): SOPs ensure that every step of the machining process is performed consistently, minimizing variations and maintaining quality standards.
2. Training and Skill Development: Providing regular training to machine operators and quality inspectors enables them to understand the quality requirements and perform their tasks effectively. This helps in reducing errors and improving the overall quality of machined plastic parts.
3. Statistical Process Control (SPC): SPC involves the collection and analysis of data from various quality testing methodologies. Statistical methods are applied to identify trends, outliers, or patterns, enabling early detection of any potential quality issues, thus allowing for proactive measures to be taken.
4. Continuous Improvement: Implementing quality improvement initiatives like Lean manufacturing or Six Sigma helps identify and eliminate wasteful practices, streamline processes, and enhance overall quality, ultimately leading to a better control of quality in plastics machining.
By utilizing these quality testing methods and employing effective quality control measures, manufacturers can ensure the consistent production of high-quality machined plastic parts.
plastics machining Sample Policy and Post-Purchase Considerations for plastics machining from China
Sample Policy: Plastics Machining from China
At [Company Name], we strive to provide our customers with high-quality plastics machining solutions at competitive prices. We understand that sourcing products from overseas can be a daunting task, which is why we have implemented a comprehensive sample policy to ensure customer satisfaction.
1. Free Sample Request: We are more than happy to provide free samples of our plastics machining products to potential customers upon request. These samples will allow you to assess the quality and suitability of our products for your specific needs.
2. Sample Shipping: Customers are responsible for the cost of shipping the requested samples. However, as a gesture of goodwill, we are willing to provide a partial shipping reimbursement for the samples once a first order is placed.
3. Sample Evaluation: Upon receipt of the samples, we encourage you to thoroughly evaluate the quality, precision, and performance of the products. Our dedicated team will be available to address any questions or concerns you may have during this evaluation process.
Post-Purchase Considerations: Plastics Machining from China
When purchasing plastics machining products from China, it is essential to consider the following post-purchase aspects to ensure smooth transactions and maximize value:
1. Communication and Lead Time: Communication is key to successful collaboration. Keep open lines of communication with our team to ensure clarity on specifications, production timelines, and shipping arrangements. Promptly respond to any inquiries or requests for information to avoid delays.
2. Quality Assurance: Our team employs stringent quality control measures to ensure that our plastics machining products meet your expectations. However, it is prudent to inspect the goods upon arrival. If any concerns arise, promptly communicate with us to resolve any issues or initiate product replacement or refund.
3. After-Sales Support: We take pride in our customer service and strive to provide ongoing support after the initial purchase. Should you require assistance with installation, usage, or maintenance of our plastics machining products, we are here to assist you.
4. Feedback and Reviews: Your feedback is invaluable to us. We encourage you to provide feedback on your experience with our products and services. Positive feedback is greatly appreciated and helps us improve our operations. Similarly, constructive feedback allows us to address any shortcomings and improve our service further.
At [Company Name], we are committed to providing exceptional plastics machining products from China to our customers. Our sample policy and post-purchase considerations aim to ensure your satisfaction throughout the buying process, and we welcome the opportunity to serve your plastics machining needs.
Sourcing plastics machining from China: Opportunities, Risks, and Key Players
China has emerged as a leader in plastics machining, offering numerous opportunities for businesses worldwide. The country’s advanced technology, vast production capacity, and cost-effective operations make it an attractive sourcing option. However, there are also risks involved that businesses must carefully consider.
One key opportunity of sourcing plastics machining from China is the vast number of manufacturers available. China has a large pool of skilled laborers and expertise in plastic machining. This ensures a wide range of options for businesses seeking specific requirements or large-scale production. Additionally, Chinese manufacturers often offer cost advantages compared to other countries, making it a financially viable option for businesses.
China’s advanced technology is another significant advantage. Many Chinese manufacturers employ state-of-the-art machinery, such as CNC machining centers, which ensures high-quality and precision in the finished products. These technologies enable businesses to obtain complex and detailed plastic components that meet international standards.
However, there are certain risks associated with sourcing from China. Quality control can be a concern due to variations in manufacturing standards and practices. It is crucial for businesses to carefully vet potential suppliers, conduct thorough inspections, and establish quality control measures to mitigate these risks.
Intellectual property theft is another risk that businesses must be cautious about. China has been criticized for its lack of intellectual property protection laws and enforcement. To protect sensitive designs and ideas, businesses should consider having proper legal agreements, confidentiality clauses, and trademarks in place while dealing with Chinese manufacturers.
While there are numerous key players in the plastics machining industry in China, some notable companies include Hutchinson China Meditech, Shandong Dongsheng Metallurgical Engineering Materials, and Jiangsu Wujiel Testing Equipment. These companies have earned a reputation for their quality products, advanced technology, and reliable services.
In conclusion, sourcing plastics machining from China offers significant opportunities for businesses due to its advanced technology, large manufacturing capacity, and cost advantages. However, businesses must also assess and manage the associated risks, such as quality control and intellectual property protection. By carefully selecting reputable suppliers and establishing proper safeguards, businesses can benefit from sourcing plastics machining from China while minimizing potential drawbacks.
How to find and select reliable plastics machining manufacturers in China,use google search manufacturers and suppliers
When searching for reliable plastics machining manufacturers in China, Google can be an effective tool to find manufacturers and suppliers. Here are a few steps to follow:
1. Understand your requirements: Before starting the search, have a clear understanding of your specific needs, including the type of plastic machining services you require, quantities, quality standards, and desired production lead time.
2. Conduct a Google search: Begin by conducting a general search using keywords such as “plastics machining manufacturers in China” or more specific terms like “CNC plastic machining suppliers.” Browse through the search results to identify potential manufacturers.
3. Evaluate manufacturer’s website: Visit the websites of the shortlisted manufacturers to gain insights into their capabilities, experience, certifications, quality control processes, and machinery. Look for details on their plastic machining expertise, production capacity, client portfolio, and any available case studies or testimonials.
4. Check certifications and quality standards: Reliable manufacturers in China often possess certifications such as ISO 9001, ISO 14001, or various specific industry certifications. Verify if the manufacturer meets your desired quality standards, as this ensures adherence to consistent quality.
5. Assess communication capabilities: Contact the manufacturers via email or phone to gauge their responsiveness and communication skills. Prompt and clear communication is essential for a successful collaboration.
6. Request samples or visit their facility: If possible, request samples, or consider visiting the manufacturer’s facility to assess their infrastructure, equipment, and production processes. This can help ensure that they have the necessary capabilities to meet your requirements.
7. Verify references: Ask for references or customer testimonials to gain insights into previous clients’ experiences. This can provide valuable information on the manufacturer’s reliability, product quality, and customer service.
8. Evaluate pricing: Request quotes from multiple manufacturers to compare pricing. However, keep in mind that while cost is important, it should not be the sole determining factor. Focus on finding a trustworthy manufacturer that delivers consistent quality.
9. Consider support services: In addition to manufacturing capabilities, evaluate if the manufacturer provides additional services such as design assistance, prototyping, packaging, and logistics support. Such comprehensive services can streamline the production process.
10. Assess intellectual property protection: If your product design or intellectual property is critical, ensure that the manufacturer understands and respects the importance of protecting your intellectual property rights.
By following these steps and conducting thorough research, you can find and select reliable plastics machining manufacturers in China using Google search.
How to check plastics machining manufacturers website reliable,use google chrome SEOquake check if ranking in top 10M
To check the reliability of a plastics machining manufacturer’s website, you can follow these steps:
1. Use Google Chrome: Open the website using Google Chrome as your web browser. It provides various tools and extensions that can help you assess the reliability of a website.
2. Install SEOquake: SEOquake is a helpful Chrome extension that provides an overview of a website’s SEO performance. Install SEOquake from the Chrome Web Store.
3. Check website ranking: Once you have installed SEOquake, open the manufacturer’s website and click on the SEOquake icon in your browser toolbar. A dashboard will appear displaying various metrics.
4. Verify global ranking: In the SEOquake dashboard, check the “Rank” section for the website’s global ranking. A reliable plastics machining manufacturer might have a ranking within the top 10 million websites worldwide. If the manufacturer’s website ranks within this range, it could signify a reasonable level of reliability.
5. Assess additional SEO metrics: SEOquake provides various SEO metrics that can assist you in evaluating a website’s reliability. For example, you can check the number of indexed pages, the website’s age, the Alexa rank, and the number of backlinks.
6. Consider website design and information: Besides relying solely on SEO metrics, it’s important to assess the website design and the information provided. A professional and well-designed website with comprehensive information about the manufacturer’s capabilities, certifications, previous projects, and contact details indicates reliability.
7. Explore customer reviews and testimonials: Look for customer reviews or testimonials on the manufacturer’s website. Genuine testimonials provide insights into the manufacturer’s expertise and customer satisfaction, enhancing their reliability.
Remember, using the SEOquake extension in Google Chrome and considering additional factors like website design and customer testimonials will give you a comprehensive view of a plastics machining manufacturer’s website reliability. Stay cautious and make an informed decision based on your findings.
Top 10 plastics machining manufacturers in China with each 160 words introduce products,then use markdown create table compare
1. Bright Plastics Machining Co., Ltd.
Bright Plastics Machining specializes in high-quality plastics machining products. With advanced facilities and experienced engineers, they offer custom machining services for a wide range of plastic materials, including ABS, PVC, PE, and more. They provide CNC milling, turning, drilling, and other machining processes to meet various industrial needs.
2. Foison Plastics Machinery Co., Ltd.
Foison Plastics Machinery is known for its precision plastic machining products. They have a wide product range, including plastic fittings, valves, and customized components. Their expertise lies in CNC machining, injection molding, and assembly process. The company emphasizes quality control and offers competitive pricing to their clients.
3. Gem Polymer Engineering Co., Ltd.
Gem Polymer Engineering specializes in manufacturing plastic machined components for different industries, including automotive, electronics, and medical sectors. They utilize advanced equipment and employ highly skilled technicians to provide precision machining services. Their product range includes plastic gears, rollers, and various custom components.
4. Huashiang Precision Machinery Co., Ltd.
Huashiang Precision Machinery is a leading manufacturer of precision plastics machining products. They provide a comprehensive range of services, such as CNC milling, turning, and drilling. Their products are widely used in industries like electronics, telecommunications, and automotive. The company emphasizes quality control and offers efficient solutions to meet customer requirements.
5. Huiyi Precision Machinery Manufacturing Co., Ltd.
Huiyi Precision Machinery Manufacturing specializes in the production of high-precision plastic machining products. Their services include CNC milling, turning, and drilling, with a focus on tight tolerances and complex geometries. They cater to industries like aerospace, medical, and electronics, and provide customized solutions based on clients’ specifications.
6. Japheth Plastic Machining Co., Ltd.
Japheth Plastic Machining is renowned for its expertise in CNC plastics machining. They offer a diverse range of products, including plastic housings, prototypes, and components. Their skilled team utilizes advanced CNC equipment to provide precise machining solutions. The company emphasizes quality assurance and on-time delivery.
7. JJT Plastic Machining Co., Ltd.
JJT Plastic Machining specializes in the production of high-quality plastic components. They offer CNC milling, turning, and drilling services for various plastics, including ABS, PE, and nylon. Their products cater to industries like automotive, electronics, and telecommunications. The company focuses on product innovation, cost-effectiveness, and excellent customer service.
8. Leadertech Precision Engineering Co., Ltd.
LeaderTech Precision Engineering is a leading manufacturer of plastic machining products in China. They provide complete CNC machining solutions for different plastic materials, including PEEK, POM, and polycarbonate. Their product range covers components for industries like medical devices, automotive, and consumer electronics. The company is committed to delivering superior quality products and fast turnaround times.
9. Shengwei Precision Machinery Co., Ltd.
Shengwei Precision Machinery specializes in custom plastic machining services. They boast advanced CNC equipment and a highly skilled team to cater to various industrial sectors. Their product portfolio includes plastic molds, fixtures, and components. The company focuses on meeting customer requirements with cost-effective solutions and high-quality products.
10. Wuxi Hualong Plastics Machinery Co., Ltd.
Wuxi Hualong Plastics Machinery is a leading manufacturer of plastic machining products. They offer CNC milling, turning, and drilling services for a wide range of plastic materials, including polypropylene, PVC, and acrylic. Their products cater to industries like automotive, telecommunications, and electronics. The company adheres to strict quality control processes to ensure customer satisfaction.
| Manufacturer Name | Product Range | Key Features |
|—————————–|——————————————————|————————————————————————————————-|
| Bright Plastics Machining | Custom plastics machining services | Advanced facilities, experienced engineers |
| Foison Plastics Machinery | Plastic fittings, valves, and customized components | Precision machining, competitive pricing |
| Gem Polymer Engineering | Plastic gears, rollers, and custom components | Extensive experience, various industries served |
| Huashiang Precision Machinery | Precision plastics machining products | Emphasis on quality control, efficient solutions |
| Huiyi Precision Machinery | High-precision plastic machining products | Tight tolerances, complex geometries |
| Japheth Plastic Machining | Plastic housings, prototypes, and components | Expertise in CNC plastics machining |
| JJT Plastic Machining | Plastic components for automotive, electronics, etc. | Emphasis on product innovation, cost-effectiveness |
| LeaderTech Precision Engineering | CNC machining solutions for various plastics | Extensive range of components for multiple industries |
| Shengwei Precision Machinery | Custom plastic machining services | Cost-effective solutions, meeting customer requirements |
| Wuxi Hualong Plastics Machinery | Plastic machining for automotive, electronics, etc. | Adherence to strict quality control processes |
Background Research for plastics machining manufacturers Companies in China, use qcc.com archive.org importyeti.com
When it comes to the plastics machining industry, China is known for its extensive manufacturing capabilities and vast supplier network. To conduct background research on plastics machining manufacturers in China, several online platforms can provide valuable information about the companies. Three such platforms are qcc.com, archive.org, and importyeti.com.
1. qcc.com: QCC (Quan Shang Chang) is a prominent Chinese business information website that offers comprehensive profiles of companies. It provides details about a company’s registration information, legal status, financial status, management team, and more. By using qcc.com, researchers can access up-to-date and reliable information about plastics machining manufacturers, ensuring they have accurate data to make informed decisions.
2. archive.org: Archive.org is a platform that allows users to access historical versions of websites. Researchers can make use of this platform to gain insights into a company’s past activities, evolution, and changes in its manufacturing processes or product offerings over time. By analyzing the archived versions of a manufacturer’s website, one can gain a comprehensive understanding of their expertise and capabilities in plastics machining.
3. importyeti.com: Import Yeti is a digital directory of suppliers and manufacturers from various industries, including plastics machining. This platform enables users to search for manufacturers based on specific criteria such as product type, location, and certifications. By using Import Yeti, researchers can find a list of plastics machining manufacturers in China along with their contact information. The platform can also provide additional details such as export history, customer information, and shipment data, allowing researchers to further evaluate a manufacturer’s reliability and track record.
By combining the data gathered from qcc.com, archive.org, and importyeti.com, researchers can gain comprehensive insights into plastics machining manufacturers in China. This information will enable them to identify suitable manufacturers, assess their capabilities and credibility, and make well-informed decisions when choosing a partner for their plastic machining needs.
Leveraging Trade Shows and Expos for plastics machining Sourcing in China
Trade shows and expos can be highly valuable for businesses looking to source plastics machining services in China. These events provide a unique opportunity to connect with a wide range of suppliers, manufacturers, and industry experts, ensuring that companies can find the right partners to meet their specific needs.
Attending trade shows and expos focused on plastics machining in China allows businesses to evaluate and compare multiple suppliers during a short period. Exhibitors often showcase their capabilities, machinery, and finished products, providing a comprehensive overview of their expertise. This allows companies to assess the quality of their work, their production capabilities, and their commitment to maintaining high standards. Additionally, trade shows often feature live demonstrations, giving professionals the chance to see the machining processes in action and better understand the suppliers’ technical expertise.
Furthermore, trade shows and expos provide an ideal environment for networking. Companies can engage in meaningful conversations with industry experts and other attendees to gain insights into the latest trends, innovations, and best practices related to plastics machining in China. These interactions can lead to the discovery of new suppliers, partnerships, or even potential customers.
To make the most of trade shows and expos in China for plastics machining sourcing, businesses should follow a strategic approach. Before attending the event, it is crucial to conduct thorough research on the exhibitors, identifying the ones most aligned with the company’s specific requirements. This ensures that time spent at the trade show is focused on interacting with relevant suppliers who have the potential to meet sourcing needs.
Once at the trade show, professionals should actively engage with exhibitors, asking detailed questions regarding their capabilities, quality control processes, lead times, and pricing. It is also essential to collect samples and business cards for follow-up communication. After the event, companies should carefully evaluate the information gathered and compare multiple suppliers before making a final decision. Ongoing communication with potential suppliers is crucial to negotiate terms, clarify expectations, and build a long-lasting business relationship.
In conclusion, trade shows and expos provide an ideal platform for sourcing plastics machining services in China. By attending these events, businesses can connect with a wide range of suppliers, evaluate their capabilities, and gather valuable market insights. With careful planning and strategic engagement, trade shows and expos can be highly effective for finding the right partners to meet sourcing needs in plastics machining.
The Role of Agents and Sourcing Companies in Facilitating plastics machining Purchases from China
Agents and sourcing companies play a crucial role in facilitating plastics machining purchases from China. These intermediaries act as a bridge between buyers and suppliers, helping to streamline the procurement process and ensure successful transactions.
One of the primary roles of agents and sourcing companies is to identify reliable and reputable suppliers. They have extensive networks and knowledge about the industry, allowing them to connect buyers with trusted manufacturers in China who specialize in plastics machining. This saves buyers valuable time and effort in searching for suitable suppliers on their own.
Agents and sourcing companies also handle negotiations on behalf of buyers. They are experienced in contract negotiations, pricing, and quality control, ensuring that buyers receive the best possible terms and conditions. Their expertise in dealing with Chinese suppliers enables them to navigate the cultural and business differences that may arise during the negotiation process.
Furthermore, these intermediaries provide logistical support. They assist in arranging shipping, managing customs clearance, and handling any necessary documentation related to the purchase. This helps to simplify and expedite the shipping process, ensuring that the products are delivered to the buyers in a timely manner.
Agents and sourcing companies also play a crucial role in quality control and inspection. They conduct factory audits and inspections to ensure that the selected suppliers meet industry standards and adhere to the specific requirements of the buyers. They can help buyers verify the quality of the products before shipment, reducing the risk of receiving substandard or defective goods.
In summary, agents and sourcing companies play a vital role in facilitating plastics machining purchases from China. They help buyers connect with reliable suppliers, negotiate favorable terms, handle logistics, and ensure quality control. Their expertise and knowledge of the Chinese market contribute to a smoother and more efficient procurement process for buyers seeking plastics machining services.
Price Cost Research for plastics machining manufacturers Companies in China, use temu.com and 1688.com
When it comes to plastic machining manufacturers in China, two popular online platforms for price and cost research are temu.com and 1688.com. These platforms offer a wide range of suppliers and products, making them ideal for sourcing plastic machining services at competitive prices. Here is a brief overview of these platforms and some key tips for conducting price and cost research efficiently.
Temu.com is a comprehensive online platform that connects buyers with Chinese suppliers, covering various industries including plastics machining. It provides detailed supplier information, product catalogs, and allows buyers to request quotes directly. Temu.com is known for its user-friendly interface and advanced search features, making it easier for buyers to find suitable suppliers based on their specific requirements. The platform also offers an extensive database of verified suppliers and user reviews, ensuring a reliable sourcing experience.
1688.com, on the other hand, is an online business-to-business platform owned by Alibaba Group, specifically designed for the domestic Chinese market. Although primarily in Chinese language, it can be accessed using translation tools or with the help of a Mandarin speaker. 1688.com offers a wide range of plastics machining manufacturers, providing buyers with a vast selection of suppliers to choose from. The platform not only allows buyers to compare prices but also provides information on minimum order quantities, production capacities, and other relevant details.
When conducting price and cost research on these platforms, it is essential to follow some key tips:
1. Define your requirements: Clearly outline your plastic machining needs, including material specifications, machining processes, and desired quantities. This will help you narrow down your search and find the most suitable suppliers.
2. Compare multiple suppliers: Obtain quotes from different suppliers and compare their prices, product quality, lead times, and services. Consider factors such as supplier reputation, manufacturing capabilities, and communication abilities to make an informed decision.
3. Request samples: Before placing bulk orders, it is advisable to request samples from potential suppliers to evaluate the quality of their workmanship and the suitability of their plastic machining capabilities.
4. Communicate effectively: Ensure clear communication with suppliers, discussing pricing details, order quantities, shipping terms, and any additional requirements. Maintaining good communication throughout the sourcing process is crucial for a successful partnership.
By utilizing temu.com and 1688.com, buyers can efficiently conduct price and cost research for plastic machining manufacturers in China. These platforms offer an extensive selection of suppliers, a variety of products, and valuable information to aid buyers in making informed decisions while sourcing plastic machining services.
Shipping Cost for plastics machining import from China
When importing plastics machining from China, one of the crucial factors to consider is the shipping cost. The shipping cost depends on various factors such as the volume or weight of the shipment, the shipping method, and the destination country.
For lightweight and small volume shipments, air freight is a popular and faster option. The cost is typically calculated based on the weight or volumetric weight, whichever is greater. Volumetric weight considers the size of the package, and it is calculated by multiplying the length, width, and height of the package and dividing by a volumetric factor.
If the shipment is large and heavy, sea freight is a cost-effective option. The cost is mainly determined based on the volume or weight of the goods and the shipping distance. It is advisable to opt for Full Container Load (FCL) if the volume is substantial, as this will provide better cost savings compared to Less than Container Load (LCL) shipments.
Additionally, it is essential to consider other costs associated with importing. These may include customs duties, taxes, import fees, and handling charges. These charges will vary based on the destination country’s regulations and the nature of the product being imported.
To mitigate shipping costs, it is recommended to compare quotes from different freight forwarders or shipping companies. Negotiating better shipping rates or consolidating multiple orders can also help reduce costs. Working with an experienced customs broker or freight forwarder can provide valuable insights and guidance to ensure a smoother shipping process and potentially lower costs.
Ultimately, the shipping cost for plastics machining imports from China will depend on the packaging dimensions, weight, shipping method, and destination. By carefully considering these factors and exploring cost-saving measures, it is possible to import plastics machining with cost efficiency in mind.
Compare China and Other plastics machining Markets: Products Quality and Price,Visible and Hidden Costs
China is a major player in the plastics machining market, but it faces competition from other countries in terms of product quality, price, and various visible and hidden costs.
In terms of product quality, China has made significant strides over the years and is now capable of producing high-quality plastic machined products. However, it still faces competition from countries like Germany and the United States, which are known for their precision and expertise in plastics machining. These countries often have stricter quality controls and regulations, resulting in products that may be perceived as superior in terms of quality.
When it comes to pricing, China has a comparative advantage due to its lower labor and manufacturing costs. This has allowed China to offer competitive prices in the global plastics machining market. However, other countries such as India and Thailand are emerging as cost-effective alternatives, offering competitive pricing similar to China. These countries benefit from lower labor costs and proximity to raw material sources, which can reduce transportation costs.
Visible costs in the plastics machining market include raw material costs, labor costs, and overhead expenses. China, with its large manufacturing base and access to low-cost labor, has been able to keep these visible costs relatively low. This has facilitated its competitiveness in the market. However, other countries may also have access to low-cost labor and raw materials, making them equally viable options with similar visible costs.
Hidden costs in the plastics machining market include factors such as intellectual property protection, logistics, and supply chain risks. China has faced criticism in the past for issues related to intellectual property rights infringement, which could result in hidden costs for businesses operating in the country. Additionally, the physical distance between China and its major export markets can lead to higher logistic costs and potential supply chain disruptions. Other countries may be perceived as having lower hidden costs due to stronger intellectual property protections and closer proximity to markets.
In conclusion, China is a major player in the plastics machining market, offering competitive pricing and quality products. However, it faces competition from other countries with superior product quality, similar pricing, and potentially lower hidden costs. The decision to choose a particular market for plastics machining would depend on the specific requirements and priorities of businesses and customers.
Understanding Pricing and Payment Terms for plastics machining: A Comparative Guide to Get the Best Deal
When it comes to plastics machining, understanding pricing and payment terms is essential to ensure you’re getting the best deal for your needs. With so many options available in the market, it can be challenging to navigate through the various pricing structures and payment terms. This comparative guide aims to shed light on these aspects, providing you with valuable insights for making informed decisions.
Pricing strategies in plastics machining typically vary based on factors such as the complexity of the project, material specifications, quantity required, and turnaround time. Understanding these factors will help you negotiate and compare prices effectively.
One common pricing approach is the “per part” pricing, where the cost is calculated based on the number of parts you require. This approach is beneficial for larger quantities and is often subject to quantity discounts. On the other hand, for smaller quantities, you may encounter “set-up” fees, which cover the costs of tooling and programming specific to your project. It’s crucial to consider these set-up fees when comparing pricing options.
Material cost is another significant component of pricing. Different types of plastics come with varying price tags, mainly depending on their characteristics and availability. Therefore, it’s important to discuss material options with your machining supplier to find a cost-effective solution that meets your requirements.
Payment terms are equally crucial in securing the best deal for plastics machining. Common payment terms include upfront payments, payment upon delivery, or a mix of both. Suppliers may also offer credit terms for long-term projects or regular customers. Negotiating favorable payment terms can help manage your cash flow effectively and ensure a smooth transaction process.
Additionally, it’s essential to inquire about any extra charges that might not be included in the initial pricing quote. These can include packaging, shipping, or handling fees, which can significantly impact the final cost.
To make an informed decision, it’s recommended to obtain quotes from multiple suppliers and compare not only the pricing but also the quality, lead time, and customer reviews. Take into account the supplier’s experience, certifications, and expertise in plastics machining.
In conclusion, understanding pricing and payment terms is crucial in obtaining the best deal for plastics machining. Consider factors like quantity, complexity, material costs, and determine a suitable payment structure. By comparing quotes from different suppliers, you can make an informed decision and ensure you’re getting the best value for your investment.
Chinese Regulations and Industry Standards Certifications for plastics machining,Import Regulations and Customs for plastics machining from China
When it comes to plastics machining, China has established regulations and industry standards certifications to ensure quality and safety. These standards are essential for manufacturers, exporters, and importers in the plastics machining industry.
The main regulatory body in China is the National Standardization Management Committee (NSMC), which is responsible for the development and implementation of industry standards. The NSMC has established several standards for plastics machining, covering different aspects such as materials, machining processes, safety requirements, and environmental protection.
One of the important industry standards for plastics machining is the GB/T 16886 series. This series includes standards for dimensional tolerances, surface roughness, and other technical specifications. These standards help ensure the accuracy and quality of plastic machined parts.
In addition to industry standards, manufacturers in China should comply with various certifications and quality management systems. One of the most widely recognized certifications is the ISO 9001:2015, which demonstrates a company’s commitment to quality management.
When importing plastics machining products from China, it is essential to be aware of the import regulations and customs procedures. In general, the import of plastics machining products is subject to customs duties and taxes. Importers need to provide necessary documents such as commercial invoices, packing lists, and bill of lading or airway bills.
Importers should also ensure compliance with the regulations of their own countries regarding plastics machining products. For example, some countries may have specific restrictions or requirements for certain types of plastics or additives used in the machining process.
To summarize, China has established regulations and industry standards certifications to ensure the quality and safety of plastics machining products. Manufacturers should comply with these standards and certifications to enhance the credibility of their products. Importers should be aware of the import regulations and customs procedures when importing plastics machining products from China.
Sustainability and Environmental Considerations in plastics machining Manufacturing
Sustainability and environmental considerations in plastics machining manufacturing are becoming increasingly important as the world recognizes the need for sustainable practices. Plastics machining refers to the process of shaping or finishing plastic parts through cutting, grinding, drilling, and other methods.
One of the main sustainability considerations in plastics machining is the choice of materials. Selecting environmentally friendly plastics, such as biodegradable or recyclable ones, can minimize the negative impact on the environment. These materials can be sourced from renewable resources and have a lower carbon footprint compared to traditional plastics derived from fossil fuels.
Energy efficiency is another crucial aspect to consider. Implementing energy-saving measures, such as using efficient machinery, improving production processes, and optimizing operational efficiency, can reduce the overall energy consumption during plastics machining. This not only reduces environmental impact but also saves costs in the long run.
Waste management is a critical component of sustainability in plastics machining manufacturing. Minimizing waste generation by accurately calculating material needs and embracing lean manufacturing principles can significantly reduce the amount of plastic waste produced. Additionally, recycling and reusing plastic waste generated during the machining process can help divert plastic from landfills and reduce the demand for new raw materials.
Water usage needs to be carefully managed to minimize environmental impact. Implementing water-efficient technologies and processes, such as recycling and treating water used in plastics machining, can help reduce water consumption. Moreover, using water-based coolant or lubricants rather than oil-based alternatives can limit the potential damage to aquatic ecosystems.
Transportation also plays a role in sustainability. Minimizing the distance travelled by raw materials and finished products can reduce the carbon emissions associated with transportation. Using local suppliers and implementing efficient logistics practices can help achieve this goal.
Overall, incorporating sustainability and environmental considerations into plastics machining manufacturing involves selecting eco-friendly materials, optimizing energy efficiency, managing waste effectively, reducing water usage, and implementing sustainable transportation practices. By adopting these practices, plastics machining manufacturers can contribute to a more sustainable future and reduce their ecological footprint.
List The Evolution history of “plastics machining”
The evolution of plastics machining has seen significant advancements and changes since the early 20th century. Plastics were first introduced as a replacement for natural materials such as wood and metal due to their lightweight and versatile properties. Here is a brief overview of the evolution history of plastics machining:
1. Early 1900s: In the early stages, machining plastics involved manual processes, such as sawing, turning, and drilling. Plastics like celluloid and Bakelite were commonly machined using traditional techniques used for working with metals.
2. 1940s-1950s: The development of synthetic polymers, such as polyethylene and polypropylene, marked a significant milestone in plastics machining. These new materials offered improved qualities, including increased strength, heat resistance, and chemical stability. Machining techniques began to evolve to accommodate these advancements.
3. 1960s-1970s: The introduction of computer-controlled machining, known as Computer Numerical Control (CNC), revolutionized the plastics machining industry. CNC machines allowed for more precise and automated operations, reducing human error and increasing efficiency. This period also witnessed the development of various cutting tools specifically designed for plastics.
4. 1980s-1990s: The emergence of advanced CAD/CAM software further revolutionized plastics machining. These tools provided engineers and machinists with the ability to design and simulate machining processes digitally before actual production, saving time and resources. Additionally, new machining methods, such as laser cutting and waterjet cutting, expanded the capabilities and applications of plastics machining.
5. 2000s-Present: Continual advancements in materials science have led to the development of high-performance engineering plastics, such as polycarbonate and polyether ether ketone (PEEK). These materials offer exceptional strength, durability, and resistance to extreme environments. Machining techniques have adapted to accommodate these specialized materials, requiring enhanced tooling and expertise.
Furthermore, the focus on sustainability and environmental concerns has led to the development of new machining techniques, such as recyclable and bio-based plastics, as well as more efficient and eco-friendly machining processes.
In summary, plastics machining has come a long way from manual processes to computer-controlled precision machining. Advancements in materials, machining methods, and technology have paved the way for an ever-expanding range of applications, making plastics machining an integral part of various industries, including automotive, aerospace, healthcare, and electronics.
The Evolution and Market Trends in plastics machining Industry
The plastics machining industry has undergone significant evolution and witnessed various market trends over the years. With advancements in technology and increasing demand for precision-engineered plastic components, the industry has adapted to new techniques and market dynamics.
One major evolution in plastics machining is the shift towards high-speed machining (HSM) methods. HSM allows for faster production rates, improved accuracy, and better surface finishes. This development has been driven by the need to meet growing customer demands for quick turnaround times and cost-effective manufacturing solutions.
Another important trend in the plastics machining industry is the use of advanced software and computer-controlled machines. This enables manufacturers to program complex designs and optimize production processes, resulting in higher efficiency and reduced waste. Additionally, these technologies have led to the adoption of automation and robotics, further enhancing productivity and reducing labor costs.
The market trends in the plastics machining industry are also influenced by changing consumer preferences and industry requirements. One significant trend is the increasing demand for lightweight materials in various sectors, such as automotive, aerospace, and consumer electronics. Plastics offer advantages such as weight reduction, design flexibility, and corrosion resistance, making them a preferred choice for component manufacturing.
Additionally, there is a growing emphasis on sustainability and environmental responsibility in the plastics machining industry. Manufacturers are adopting eco-friendly materials and processes, such as using recycled plastics and reducing energy consumption. This trend is driven by both regulatory requirements and consumer awareness, as more customers are seeking products from socially and environmentally conscious companies.
Furthermore, the industry is witnessing a shift towards collaboration and partnerships, as manufacturers strive to offer comprehensive solutions to their customers. This includes providing value-added services such as design assistance, prototyping, and assembly. By expanding their capabilities and expertise, plastics machining companies can cater to the evolving needs of their customers and enhance their market competitiveness.
In conclusion, the plastics machining industry has experienced significant evolution and market trends. Advancements in technology, such as high-speed machining and computer-controlled machines, have improved productivity and efficiency. The demand for lightweight materials and sustainable manufacturing practices has also shaped the market dynamics. Moreover, collaboration and partnerships have become essential for providing comprehensive solutions to customers’ requirements.
Custom Private Labeling and Branding Opportunities with Chinese plastics machining Manufacturers
Chinese plastics machining manufacturers offer a wide range of custom private labeling and branding opportunities for businesses looking to establish their own unique brand in the market. With their advanced technology and expertise in plastics machining, these manufacturers can fulfill the specific requirements of businesses and customize their products accordingly.
One of the key advantages of working with Chinese plastics machining manufacturers is their ability to offer private labeling services. They can help businesses in designing and manufacturing products with their own brand name and logo. This gives businesses the opportunity to establish themselves as a distinct brand in the market and enhance customer recognition and loyalty.
Additionally, these manufacturers also offer branding opportunities by providing various customization options. They can modify product design, shape, color, and functionality to meet the specific needs and preferences of businesses. With their state-of-the-art machinery and skillful technicians, they can produce high-quality plastic components and products that reflect the brand identity of businesses.
Moreover, Chinese plastics machining manufacturers offer flexibility in order quantities, allowing businesses to customize their products even for small-scale orders. This enables businesses to go to market quickly with their branded products without the need for large investments or high inventory levels.
Furthermore, these manufacturers have the capability to provide cost-effective solutions. China’s robust manufacturing infrastructure and economies of scale enable them to offer competitive pricing without compromising on product quality. Businesses can benefit from this advantage and increase their profit margins.
In conclusion, Chinese plastics machining manufacturers provide excellent opportunities for businesses to establish their own brand through custom private labeling and branding. With their expertise, flexibility, and cost-effective solutions, businesses can confidently create and market their unique products, strengthening their position in the market.
Tips for Procurement and Considerations when Purchasing plastics machining
When it comes to procurement and purchasing plastics machining, there are several factors and considerations that one should keep in mind. Here are some tips that can help streamline the process and ensure a successful transaction:
1. Identify your specific requirements: Before initiating the procurement process, it is crucial to clearly define your specific needs and requirements. Determine the type of plastic material, dimensions, tolerances, quantity, and any additional finishing or assembly requirements.
2. Quality assurance: It is important to partner with a reputable and reliable plastics machining supplier. Conduct thorough research and ensure that the supplier has a proven track record of delivering high-quality products. Ask for samples or visit their facility to assess their manufacturing capabilities.
3. Request for quotation: Contact multiple suppliers and request detailed quotations. Provide them with comprehensive project specifications and ask for quotations that cover all aspects, including material costs, machining processes, finishing, packaging, and shipping costs.
4. Price negotiation: Negotiate the price with the suppliers while keeping a balance between cost and quality. Consider factors such as the supplier’s expertise, reputation, and lead time when evaluating the proposed prices.
5. Capacity and lead time: Enquire about the supplier’s capacity and production capabilities to ensure that they can meet your desired quantity and lead time requirements. Discuss the expected turnaround time and make sure it aligns with your project timeline.
6. Supplier capabilities: Evaluate the supplier’s equipment, technology, and expertise in plastics machining. Ensure they have the necessary machinery and skilled personnel to handle your specific project requirements.
7. Material selection: If you are unsure about the ideal plastic material for your project, consult with the supplier. They can provide guidance on selecting the most suitable material based on your application, environment, durability, and cost requirements.
8. Certifications and compliance: Verify if the supplier adheres to relevant industry standards, such as ISO certifications. Compliance with regulations, such as RoHS (Restriction of Hazardous Substances) and REACH (Registration, Evaluation, Authorization, and Restriction of Chemicals), is also important, especially if your products will be exported or used in specific industries.
9. Communication and collaboration: Establish effective communication channels with the supplier to ensure transparency and timely updates throughout the procurement process. Promptly provide any necessary clarifications or modifications to avoid delays or misunderstanding.
10. Risk management: Assess potential risks and establish contingency plans to mitigate any issues that may arise during the procurement process. Consider factors such as supplier reliability, backup suppliers, and emergency response plans.
By following these procurement tips and considerations, you can streamline the plastics machining purchasing process, mitigate risks, and ensure that your requirements are met with quality products and timely delivery.
FAQs on Sourcing and Manufacturing plastics machining in China
Q: Why should I consider sourcing and manufacturing plastics machining in China?
A: There are several reasons to consider sourcing and manufacturing plastics machining in China. Firstly, China has a vast manufacturing industry which allows for a wide range of capabilities and options when it comes to plastics machining. This means that you can find suppliers and manufacturers that specialize in specific types of plastics, machinery, or processes. Additionally, China often offers competitive pricing due to lower labor and overhead costs compared to many other countries. The country also has a comprehensive supply chain, ensuring a consistent supply of materials for plastics machining. China has also invested heavily in technological advancements, making it possible to access state-of-the-art machinery and equipment for precision machining. Finally, many Chinese manufacturers have experience and expertise in plastics machining, making them reliable partners for producing high-quality products.
Q: How can I find reliable suppliers and manufacturers for plastics machining in China?
A: To find reliable suppliers and manufacturers for plastics machining in China, you can start by conducting thorough research. Use online directories, trade platforms, and forums to find a list of potential suppliers. It is recommended to verify the reputation and track record of these suppliers by checking their certifications, customer reviews, and industry experience. Next, communicate directly with the potential suppliers to assess their responsiveness, technical capabilities, and willingness to provide samples or references. This will help you gauge their reliability and determine if they can meet your specific requirements. It is also useful to visit their facilities in person, if possible, to evaluate their production capacity, quality control processes, and overall infrastructure. This will provide you with a firsthand understanding of their capabilities and allow you to build a stronger relationship with the chosen supplier.
Q: What are the potential challenges in sourcing and manufacturing plastics machining in China?
A: While sourcing and manufacturing plastics machining in China can have numerous benefits, some challenges may arise. Language and cultural barriers can pose communication difficulties, so it is important to establish clear communication channels and ensure mutual understanding. Another potential challenge is the distance, which can lead to longer lead times and shipping costs. Therefore, it is crucial to plan production timelines accordingly and choose reliable logistics partners. Intellectual property protection is another concern, so it is recommended to practice due diligence in selecting reputable suppliers and manufacturers with a strong commitment to intellectual property rights. Lastly, constantly shifting regulations and policies can affect import/export procedures, so staying updated on customs requirements and compliance is essential to avoid any disruptions in the supply chain.
Why contact sourcifychina.com get free quota from reliable plastics machining suppliers?
Sourcifychina.com, a platform connecting businesses with reliable plastics machining suppliers in China, offers a free quota for various reasons.
Firstly, by providing a free quota, Sourcifychina.com aims to attract potential clients who are interested in sourcing plastic machining services from China. Offering a free quota allows businesses to explore the platform’s capabilities and assess the suitability of their services without initially committing any financial resources. This serves as an incentive for businesses to consider Sourcifychina.com as a valuable sourcing solution.
Secondly, Sourcifychina.com understands the importance of building trust and credibility with their potential clients. By offering a free quota, they demonstrate confidence in their ability to deliver reliable suppliers. This encourages businesses to engage with the platform and explore the opportunities available to them without any risk.
Furthermore, Sourcifychina.com recognizes the competitive nature of the plastics machining industry and aims to differentiate itself by providing a value-added service. By offering a free quota, they provide businesses with an opportunity to save costs and potentially negotiate better terms with reliable suppliers. This helps businesses maximize their sourcing efforts and ultimately gain a competitive edge in their respective markets.
In conclusion, Sourcifychina.com offers a free quota from reliable plastics machining suppliers to attract potential clients, build trust, and provide added value. By doing so, they facilitate the sourcing process and enable businesses to make informed decisions while minimizing financial risks.