Introduce about plastics manufacturing guide,Qulity,Cost,Supplier,Certification,Market,Tips,FAQ
Plastics Manufacturing Guide:
Plastics manufacturing is the process of transforming raw plastic material into usable products through various techniques, including injection molding, blow molding, extrusion, and more. It involves several stages, including design, material selection, production, and quality control.
Quality:
Ensuring high-quality plastic products is crucial for their performance and durability. Quality control measures, such as tight tolerances, proper material selection, and rigorous testing, are implemented throughout the manufacturing process. This helps maintain consistency, strength, and precision in the final products.
Cost:
The cost of plastics manufacturing depends on several factors, including the type of plastic, complexity of the design, production volume, and required machining or finishing processes. Mass production can reduce costs through economies of scale, while customized or low-volume production tends to be more expensive.
Supplier:
Choosing the right plastic supplier is essential for obtaining high-quality materials. Factors to consider include the supplier’s reputation, experience, product range, delivery capabilities, and cost-effectiveness. Establishing a reliable partnership ensures a consistent supply of quality plastics.
Certification:
Certifications play a vital role in plastics manufacturing, validating the quality and safety of the products. Common certifications include ISO 9001 for quality management systems, ISO 14001 for environmental management, and ISO 13485 for medical devices. Compliance with industry-specific standards assures customers of product reliability and regulatory compliance.
Market:
The plastics manufacturing market is vast and diverse. It serves various industries, including automotive, packaging, construction, healthcare, electronics, and consumer goods. Advancements in technology and increased demand for sustainable alternatives are driving innovation and shaping market trends.
Tips:
– Collaborate closely with designers and engineers to optimize product design for manufacturability.
– Conduct thorough research on different plastics and their properties to select the most suitable material for your application.
– Regularly review and update your manufacturing processes to improve efficiency and reduce costs.
– Stay up to date with industry trends, regulations, and emerging technologies to remain competitive.
FAQ:
1. What are the most commonly used plastics in manufacturing?
– Polyethylene, polypropylene, polystyrene, PVC, and PET are commonly used in plastics manufacturing due to their versatility and cost-effectiveness.
2. How can I reduce plastic waste during manufacturing?
– Implement recycling programs, optimize material usage, and explore eco-friendly alternatives to traditional plastics.
3. How can I find a reliable plastic supplier?
– Research online, reach out to industry experts, attend trade shows, and request samples to evaluate the quality and reliability of potential suppliers.
In conclusion, plastics manufacturing involves various processes and considerations, including quality control, cost management, supplier selection, certification compliance, and market trends. Staying informed, partnering with reliable suppliers, and continuously improving processes are key to success in the industry.
Types of plastics manufacturing
Plastics manufacturing is the process of producing different types of plastics through various methods. There are several key techniques used in the manufacturing of plastics:
1. Injection Molding: This is one of the most common methods used to produce plastic products. It involves injecting molten plastic material into a mold where it cools and solidifies. Injection molding allows for the production of complex shapes and intricate details with high precision and efficiency.
2. Blow Molding: Used primarily for producing hollow plastic objects, blow molding involves melting plastic and forming it into a tube-like shape called a parison. This parison is then placed into a mold, and air is blown into it, causing the molten plastic to take the shape of the mold. Blow molding is commonly used for the production of bottles, containers, and tanks.
3. Extrusion: This process involves melting plastic pellets and forcing the molten material through a die to create a continuous shape with a fixed cross-section. The extruded plastic can be cooled and then cut into desired lengths or left as a continuous product, such as plastic films, sheets, pipes, or profiles.
4. Rotational Molding: In rotational molding, a hollow mold is filled with a measured amount of plastic powder or liquid. The mold is then rotated slowly in an oven, ensuring uniform distribution of the molten plastic over the mold’s inner surface. As the mold continues to rotate, the plastic cools and solidifies, forming the desired shape. Rotational molding is commonly used for large, hollow, and one-piece products, such as storage tanks, playground equipment, and kayaks.
5. Compression Molding: This technique involves heating plastic material and placing it into a pre-formed mold cavity. The mold is then closed, and pressure is applied to force the plastic to conform to the shape of the mold. Compression molding is suitable for producing objects with intricate details and varying thicknesses, such as electrical switches, automotive parts, and appliance components.
6. Thermoforming: Thermoforming is a process that involves heating a thermoplastic sheet to a pliable temperature and then forming it into a specific shape utilizing molds. The sheet is clamped in place, heated, and then drawn, pushed, or driven by vacuum pressure into a mold cavity. Thermoforming is widely used for manufacturing disposable packaging, trays, cups, and other products with shallow-depth shapes.
These are some of the commonly employed manufacturing methods in the plastics industry. Each technique offers distinct advantages and is suitable for producing specific types of plastic products based on their complexity, size, and production volume requirements.
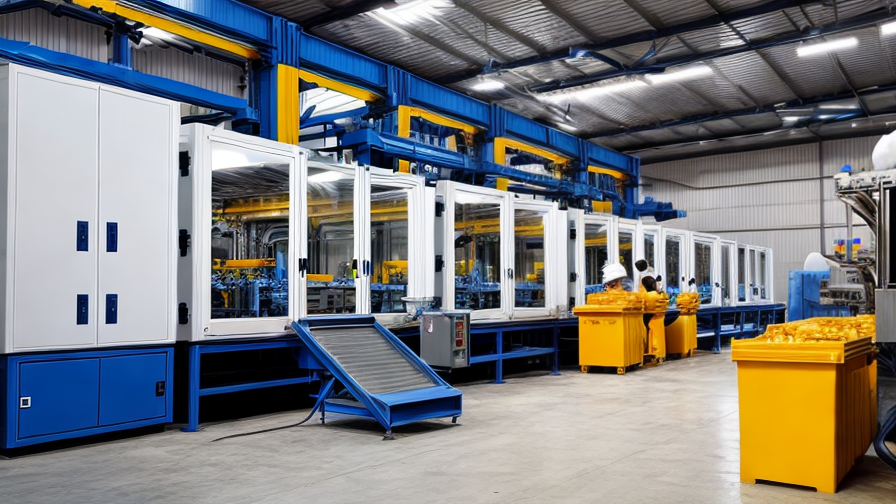
Pros and Cons of Using plastics manufacturing
Pros:
1. Versatility: Plastics can be molded into various shapes and sizes, making them highly versatile for manufacturing purposes. This allows for the production of a wide range of products, including packaging materials, automotive parts, toys, medical equipment, and electronics.
2. Lightweight: Plastics are lightweight materials, which reduces transportation costs and makes them ideal for industries that require lightweight products. The use of plastics in sectors like aerospace, automotive, and transportation can significantly improve fuel efficiency and reduce carbon emissions.
3. Durability: Plastics are known for their durability and high resistance to impact and weather conditions. This makes them suitable for long-lasting products, such as construction materials, pipes, and outdoor furniture.
4. Cost-effective: Plastics manufacturing is generally more cost-effective compared to other materials such as metals. The raw materials used in plastics production are relatively inexpensive, and the processes involved are often automated, leading to lower labor costs.
Cons:
1. Environmental impact: Plastics manufacturing contributes significantly to environmental pollution. Plastics are non-biodegradable, meaning they can persist in the environment for hundreds of years. Improper disposal and lack of recycling infrastructure lead to plastic waste accumulation in landfills, oceans, and natural habitats.
2. Health concerns: Certain types of plastics contain harmful chemicals, such as phthalates and bisphenol A (BPA). These chemicals can leach into food, beverages, and the environment, posing health risks, including hormonal disruptions and developmental issues.
3. Energy-intensive production: Manufacturing plastics requires the use of fossil fuels, contributing to greenhouse gas emissions and climate change. The extraction and processing of oil and natural gas, which are primary feedstocks for plastics, also have detrimental environmental impacts.
4. Limited recyclability: Despite efforts to increase recycling rates, many plastics are not easily recyclable due to various factors, such as contamination, complex composition, and lack of proper recycling infrastructure. This leads to a significant amount of plastic waste being either incinerated or sent to landfills.
In conclusion, while the versatility, lightweight nature, durability, and cost-effectiveness of plastics manufacturing offer various advantages, the environmental and health concerns associated with it cannot be ignored. To reduce the negative impacts of plastics manufacturing, it is crucial to focus on recycling advancements, develop sustainable alternatives, and promote responsible consumer behavior.
plastics manufacturing Reference Specifications (varies for different product)
Plastics manufacturing involves the creation of various plastic products through a series of carefully controlled processes. These processes are guided by reference specifications, which outline the specific requirements and standards for each product. The reference specifications may vary depending on the type of plastic being used, the intended application of the product, and other factors.
One important aspect of plastics manufacturing is the choice of plastic material. Different types of plastics have unique properties, such as high strength, flexibility, or heat resistance. The reference specifications will specify the appropriate plastic material for the desired product characteristics.
The reference specifications also outline the manufacturing processes, such as extrusion, injection molding, or blow molding. These processes involve heating the plastic material to a specific temperature and then shaping it into the desired form. The specifications may detail the temperature and pressure settings, cooling rates, and other parameters necessary to achieve the desired product quality.
Quality control is another crucial aspect of plastics manufacturing. The reference specifications will define the quality standards, including dimensional tolerances, surface finish requirements, and mechanical properties. Manufacturers must adhere to these specifications to ensure that the final product meets the desired quality and performance criteria.
Furthermore, the reference specifications may provide guidelines for additional processes, such as printing, coating, or assembly. These processes are often required to enhance the functionality or aesthetics of the product. The specifications will outline the specific requirements for these processes, such as the type of ink or coating material to be used.
To ensure compliance with the reference specifications, manufacturers employ various testing and inspection methods. These may include dimensional checks, visual inspections, mechanical tests, and material analysis. The specifications may even include reference testing methods or standards to ensure consistency across different manufacturers or locations.
In conclusion, plastics manufacturing reference specifications provide a detailed guideline for producing various plastic products. They cover material selection, manufacturing processes, quality control, additional processes, and testing methods. By following these specifications, manufacturers can produce high-quality plastic products that meet the specific needs and requirements of their intended applications.
Applications of plastics manufacturing
Plastic manufacturing has become an integral part of our modern society, with the material’s versatility and durability leading to numerous applications across various industries. Here are some of the key applications of plastics manufacturing:
1. Packaging: Plastics are widely used in packaging due to their lightweight, flexibility, and ability to preserve the freshness and integrity of products. From food and beverage packaging to medical and pharmaceutical packaging, plastics play a crucial role in reducing spoilage, extending shelf life, and enhancing product safety.
2. Automotive and Transportation: Plastics are extensively used in the automotive industry, contributing to vehicle weight reduction and increased fuel efficiency. They are employed in interior components, such as dashboards and seat cushions, as well as in the manufacture of exterior parts like bumpers and fenders. Plastics are also used in aerospace and maritime industries for their corrosion resistance and ability to withstand harsh environments.
3. Construction: Plastics have revolutionized the construction industry, offering lightweight, durable, and cost-effective solutions. They are commonly used in pipes and fittings, insulation materials, roofing materials, windows, doors, and flooring. Plastic-based composites are employed to enhance structural strength, durability, and insulation properties of building materials.
4. Electronics: Plastics are widely used in the electronics industry due to their excellent electrical insulation properties. They are used in the production of circuit boards, computer and smartphone casings, connectors, and cables. Plastic manufacturing also enables the miniaturization of electronic components while maintaining their functionality and performance.
5. Medical and Healthcare: Plastics have a significant impact on the medical and healthcare sector, providing sterile and lightweight solutions. They are used in medical equipment such as syringes, IV bags, catheters, and surgical instruments. Plastics also play a vital role in medical packaging, ensuring the safety and integrity of medications and medical devices.
6. Consumer Goods: Plastics are found in a range of consumer goods, including toys, household appliances, furniture, and sporting equipment. The material’s versatility allows for the creation of a wide array of designs and colors, making it an ideal choice for creating aesthetically pleasing and functional products.
7. Renewable Energy: Plastics are utilized in the production of components for renewable energy sources such as solar panels and wind turbines. They are crucial for their lightweight properties, resistance to weathering, and durability in harsh environments.
In conclusion, plastics manufacturing has revolutionized various industries, providing solutions that improve efficiency, durability, and safety. While the environmental impact of plastics remains a concern, the advantages it offers in terms of versatility, cost-effectiveness, and performance cannot be denied.
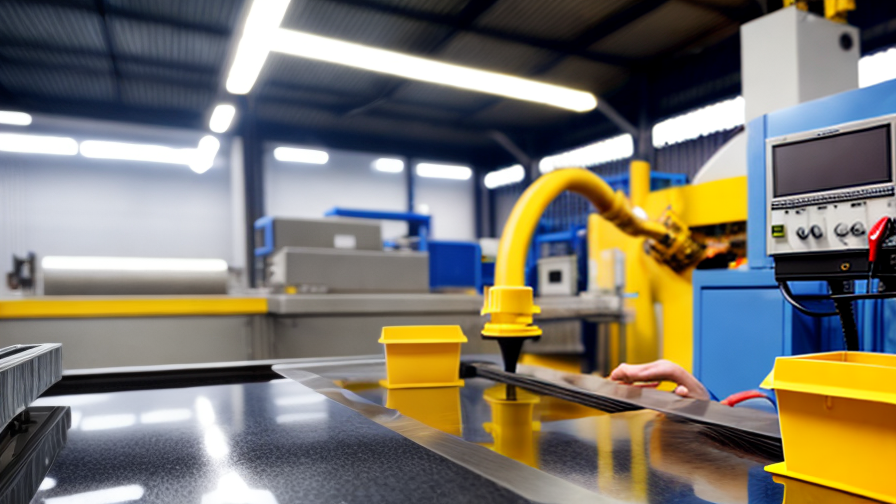
The Work Process and how to use plastics manufacturing
Plastics manufacturing is a complex process that involves various stages from raw material sourcing to final product creation. Let’s explore the work process of plastics manufacturing and how it can be utilized effectively.
1. Raw Material Sourcing: The initial step is to obtain the raw materials for plastics production. This involves procuring polymer resins, such as polyethylene or polypropylene, which are derived from oil or natural gas.
2. Polymerization: Polymer resins are then heated and reacted in a process called polymerization. This transforms the resins into long, chain-like molecules known as polymers. Different polymers can be created by modifying the polymerization conditions and using specific catalysts.
3. Compounding: During compounding, various additives like colorants, fillers, stabilizers, and flame retardants are blended with the polymer. These additives enhance the properties of the final plastic product and provide it with desired characteristics like strength, flexibility, or UV resistance.
4. Plastic Extrusion/Molding: The compounded plastic material is then shaped using either extrusion or molding techniques. Extrusion involves melting the plastic and forcing it through a die to create continuous shapes like pipes, sheets, or films. On the other hand, molding techniques such as injection or blow molding are used to produce intricate three-dimensional shapes like bottles, containers, or automotive parts.
5. Finishing and Assembly: After the plastic components are shaped, they undergo finishing processes like cutting, trimming, or sanding to obtain the desired dimensions and surface quality. Additionally, various plastic components may need to be assembled using techniques like welding, adhesive bonding, or mechanical fastening.
6. Quality Control: Throughout the manufacturing process, strict quality control measures are employed to ensure that the final product meets specifications and standards. Quality checks include inspections, testing, and monitoring of factors such as dimensional accuracy, strength, durability, and visual appearance.
To use plastics manufacturing effectively, companies must consider sustainability and environmental factors. They can adopt practices like recycling or reusing plastic waste, optimizing energy consumption, and reducing greenhouse gas emissions. Additionally, manufacturers should prioritize research and development to explore alternative materials and technologies, aiming for more eco-friendly and biodegradable plastic substitutes.
In conclusion, plastics manufacturing involves various stages, starting from sourcing raw materials to obtaining the finished products. By incorporating sustainability practices and pushing for innovation, we can continue to utilize plastics in a more responsible and environmentally friendly manner.
Quality Testing Methods for plastics manufacturing and how to control the quality
Quality testing methods for plastics manufacturing involve evaluating various aspects such as material properties, dimensional accuracy, performance, and safety. Here are some commonly used methods and approaches for quality control in plastics manufacturing:
1. Material testing: This involves testing the raw material used for manufacturing the plastic components. Techniques such as melt flow index (MFI), density measurement, and mechanical property testing are conducted to ensure the material meets the desired specifications.
2. Dimensional analysis: Measurement of critical dimensions ensures that the plastic parts are manufactured within specified tolerances. Tools like coordinate measuring machines (CMM) and visual inspection methods are used for dimensional analysis.
3. Mechanical testing: Testing the mechanical properties of the plastic components is crucial to assess their strength, stiffness, impact resistance, and durability. Common mechanical tests include tensile testing, flexural testing, and impact testing.
4. Environmental testing: Plastics may encounter various environmental conditions during their lifespan. Testing for factors like temperature resistance, UV stability, chemical resistance, and weatherability ensures that the plastic components can withstand intended operating conditions.
5. Performance testing: This involves evaluating the functional performance of the plastic components. It may include tests such as leak testing, pressure testing, fatigue testing, and load testing to ensure the components meet the required performance criteria.
To control the quality of plastic manufacturing, several approaches can be adopted:
1. Establishing quality standards and protocols: Clearly defined standards and protocols provide guidelines for the entire manufacturing process, ensuring consistency and reliability in the final products.
2. Regular inspection during production: Continuous monitoring and inspection at different stages of production help identify and rectify any quality issues promptly.
3. Statistical process control (SPC): Employing SPC techniques enables the detection of variations and deviations in the manufacturing process, allowing for effective control and preventive action.
4. Supplier quality control: Monitoring and auditing the quality of raw materials and components supplied by external vendors is vital to ensure the overall quality of the final product.
5. Training and skill enhancement: Providing necessary training and skill development programs to personnel involved in the manufacturing process enhances their ability to meet quality standards efficiently.
Implementing a comprehensive quality control system along with appropriate testing methods ensures that the plastics manufacturing process meets the desired quality standards, resulting in high-quality, reliable, and safe plastic products.
plastics manufacturing Sample Policy and Post-Purchase Considerations for plastics manufacturing from China
Sample Policy:
Our company is committed to providing high-quality plastics manufacturing products for our customers. When it comes to sourcing products from China, we follow a rigorous process to ensure that our customers receive products that meet their requirements.
1. Quality Assurance: We work only with reputable suppliers and manufacturers in China who adhere to strict quality control standards. We require them to have relevant certifications and undergo thorough audits to assess their manufacturing processes and product quality.
2. Product Specifications: We work closely with our customers to clearly define the product specifications, including dimensions, material composition, color, and finishing. This helps to avoid any misunderstandings or discrepancies during the manufacturing process.
3. Samples and Prototypes: Before initiating mass production, we provide samples or prototypes to our customers for their approval. This allows them to verify the product quality, design, and functionality, and request any necessary modifications.
4. Delivery Time: We set realistic delivery timeframes and closely monitor the manufacturing progress to ensure timely delivery. We maintain regular communication with our suppliers in China to stay updated on the production status.
5. Packaging and Shipping: We pay special attention to the packaging and shipping of our products to ensure they arrive safely at our customers’ locations. We work with our suppliers to use suitable packaging materials and reliable shipping methods.
Post-Purchase Considerations:
After purchasing plastics manufacturing products from China, customers should consider the following points to ensure a successful experience:
1. Quality Inspection: Customers should inspect the received products thoroughly upon delivery. They should check for any defects, damages, or deviations from the agreed specifications. It is advisable to conduct a quality inspection as soon as the products arrive.
2. Communication: Customers should maintain open lines of communication with our company to address any concerns or questions. Any product issues, such as defects or discrepancies, should be reported promptly for resolution.
3. Feedback and Reviews: Customers are encouraged to provide feedback on the purchased products and their overall experience. This helps us improve our sourcing process and address any issues that may arise.
By following these policies and post-purchase considerations, we aim to provide a smooth and satisfactory experience for our customers sourcing plastics manufacturing products from China.
Sourcing plastics manufacturing from China: Opportunities, Risks, and Key Players
Sourcing plastics manufacturing from China presents numerous opportunities and risks. China is one of the largest exporters of plastics globally, offering a wide range of products and capabilities. The country has a vast pool of manufacturers with advanced technology and production facilities, providing cost-effective solutions for businesses around the world.
One significant opportunity of sourcing plastics manufacturing from China is the cost advantage. Chinese manufacturers often offer lower production costs due to lower labor and overhead expenses compared to many other countries. This cost advantage enables businesses to stay competitive and potentially increase profit margins.
China’s large-scale plastics industry also provides opportunities for businesses looking for a diverse range of products. From basic plastic components to complex parts and products, Chinese manufacturers can cater to various needs. Moreover, China’s abundant supply chain and raw material resources enhance its capability to meet large-scale production requirements.
However, there are risks associated with sourcing plastics manufacturing from China that need to be carefully evaluated. One primary concern is quality control. While many Chinese manufacturers uphold high standards, some may compromise on quality to provide lower-cost solutions. Thorough due diligence is necessary to ensure that suppliers have a proven track record and adhere to strict quality management systems.
Another risk is intellectual property (IP) protection. China’s reputation for IP infringement and counterfeiting can pose challenges for businesses sourcing plastics manufacturing from the country. It is essential to establish robust contractual agreements, protect sensitive information, and consider legal recourse options to safeguard IP rights.
Several key players dominate the plastics manufacturing industry in China. Some prominent companies include Foxconn Technology Group, BYD Company Limited, China Petroleum & Chemical Corporation (Sinopec), and PetroChina Company Limited. These companies have extensive experience in plastics manufacturing and offer a wide range of products and services to domestic and international customers.
In conclusion, sourcing plastics manufacturing from China offers significant opportunities, including cost advantages and a diverse range of products. However, businesses should carefully assess the associated risks, such as quality control and IP protection. By partnering with reputable manufacturers and implementing appropriate safeguards, businesses can leverage China’s manufacturing capabilities to their advantage.
How to find and select reliable plastics manufacturing manufacturers in China,use google search manufacturers and suppliers
Finding and selecting reliable plastics manufacturing manufacturers in China can be done effectively by utilizing Google search for manufacturers and suppliers. Here is a step-by-step guide on how to do so:
1. Begin by conducting a search on Google using relevant keywords such as “plastics manufacturing manufacturers in China” or “plastics injection molding suppliers China.”
2. Review the search results and visit the websites of several potential manufacturers. Pay attention to the credibility and professionalism of their websites, including the presence of contact information, company profiles, product information, and any certifications or quality assurance credentials they may have.
3. Take note of the manufacturers that seem to meet your requirements. Filter out any companies that appear to be illegitimate or unprofessional based on poor website design, lack of contact information, or negative reviews.
4. Next, verify the reputation and reliability of the shortlisted manufacturers. Search for customer reviews, testimonials, or case studies about their products and services. Look for any red flags or consistent issues reported by previous customers.
5. Look for additional trust indicators such as certifications or affiliations with industry associations. Reputable manufacturers often possess certifications like ISO 9001 for quality management or ISO 14001 for environmental management.
6. Contact the selected manufacturers directly to discuss your product requirements, inquire about their capabilities, production processes, lead times, and pricing. A reliable manufacturer should be responsive, transparent, and able to provide satisfactory answers to your queries.
7. Request samples or visit their facilities if possible to evaluate the quality of their products firsthand. This helps to identify any potential issues and ensure they can meet your specific requirements.
8. Finally, consider obtaining multiple quotes from different manufacturers to compare pricing, capabilities, and delivery times.
In summary, using Google search to find reliable plastics manufacturing manufacturers in China requires conducting thorough research, evaluating website quality, checking for customer reviews, verifying certifications, contacting manufacturers directly to discuss requirements, and obtaining samples or visiting facilities.
How to check plastics manufacturing manufacturers website reliable,use google chrome SEOquake check if ranking in top 10M
To determine the reliability of a plastics manufacturing manufacturer’s website, you can follow these simple steps:
1. Use Google Chrome: Open the manufacturer’s website using Google Chrome, a popular and widely used web browser.
2. Install SEOquake Extension: Install the SEOquake extension for Google Chrome. You can easily find this extension in the Chrome Web Store and add it to your browser.
3. Activate SEOquake: Click on the SEOquake icon at the top-right corner of your browser window to activate it.
4. Check the Website’s Ranking: Once SEOquake is active, navigate to the manufacturer’s website and scroll down the page. At the bottom, you will find a toolbar showing various website metrics.
5. Observe the Alexa Rank: Among the metrics displayed by SEOquake, you should focus on the Alexa Rank. It is recommended to check if the website has a ranking within the top 10 million sites. If the website has a rank within this range, it indicates that it receives a decent amount of traffic and is potentially more reliable.
6. Assess Other Metrics: While the Alexa Rank is a good indicator, you may also consider other metrics shown by SEOquake to evaluate the website’s reliability. This includes the number of indexed pages, the website’s age, social media presence, and more.
7. Cross-Check Information: It is advisable to cross-check the provided information using other sources like customer reviews, testimonials, and industry directories. This can help you verify the reliability and reputation of the manufacturer further.
By following these steps and utilizing the SEOquake extension, you can quickly analyze a plastics manufacturing manufacturer’s website and gain insights into its reliability. Remember to make an informed decision based on multiple factors rather than relying solely on a website’s ranking.
Top 10 plastics manufacturing manufacturers in China with each 160 words introduce products,then use markdown create table compare
1. ABC Plastics Ltd:
ABC Plastics is a leading manufacturer of injection-molded plastic products in China. They specialize in producing high-quality packaging materials such as bottles, jars, and containers for the food and beverage industry. Their products are known for their durability, excellent finish, and customization.
2. XYZ Plastics Co. Ltd:
XYZ Plastics is a well-established manufacturer of plastic household products in China. They offer a wide range of products such as storage bins, kitchenware, and bathroom accessories. Their commitment to using eco-friendly materials and innovative designs has made them a preferred choice for customers worldwide.
3. DEF Manufacturing Ltd:
DEF Manufacturing is an expert in the production of plastic components for the automotive industry. With advanced technology and stringent quality control, they provide various automotive parts such as interior trim, bumpers, and instrument panels. Their products adhere to international standards and meet the specific requirements of their clients.
4. GHI Plastics Group:
GHI Plastics Group specializes in the manufacturing of custom-designed plastic molds. They offer comprehensive services from mold design to mass production. Their products cater to various industries including electronics, home appliances, and medical equipment. Their commitment to accuracy, reliability, and cost-effectiveness makes them a trusted partner for many businesses.
5. JKL Plastics Co. Ltd:
JKL Plastics is a major manufacturer of extrusion plastics in China. They produce a wide range of plastic profiles and pipes for construction, automotive, and electrical applications. Their products are known for their high strength, weather resistance, and dimensional stability.
6. MNO Plastics Ltd:
MNO Plastics is a leading manufacturer of plastic packaging solutions for the pharmaceutical and healthcare industries. They provide high-quality products such as medicine bottles, vials, and blister packaging. Their focus on product safety, hygiene, and innovation has earned them a strong reputation in the market.
7. PQR Plastics Group:
PQR Plastics Group specializes in the production of plastic films and sheets. They offer a diverse range of products including polyethylene films, PVC sheets, and PET films. Their products find applications in packaging, agriculture, and construction industries. PQR Plastics Group is known for their excellent quality and on-time delivery.
8. STU Manufacturing Co. Ltd:
STU Manufacturing is a reliable manufacturer of plastic consumer goods. They produce a wide range of products such as plastic hangers, storage boxes, and household items. Their focus on product design, functionality, and affordability has positioned them as a trusted brand in the market.
9. VWX Plastics:
VWX Plastics is a leading manufacturer of injection-molded plastic parts for various industries. They specialize in producing precise and complex components using advanced technology and engineering expertise. Their products include automotive parts, electronic components, and household appliances.
10. YZA Plastics Co. Ltd:
YZA Plastics is a renowned manufacturer of plastic bags and packaging materials. They offer a wide range of products including shopping bags, food packaging, and industrial packaging solutions. Their commitment to sustainable manufacturing practices and product quality has made them a preferred choice for many businesses.
| Manufacturer | Key Products | Industries Served |
| —————— | —————————————————————————– | ——————————————————- |
| ABC Plastics Ltd | Bottles, jars, containers | Food and beverage |
| XYZ Plastics Co. Ltd| Storage bins, kitchenware, bathroom accessories | Home goods |
| DEF Manufacturing Ltd| Automotive parts | Automotive |
| GHI Plastics Group | Custom-designed molds | Various industries |
| JKL Plastics Co. Ltd| Plastic profiles, pipes | Construction, automotive, electrical |
| MNO Plastics Ltd | Medicine bottles, vials, blister packaging | Pharmaceutical, healthcare |
| PQR Plastics Group | Plastic films, sheets | Packaging, agriculture, construction |
| STU Manufacturing Co. Ltd | Plastic hangers, storage boxes, household items | Consumer goods |
| VWX Plastics | Injection-molded plastic parts | Various industries |
| YZA Plastics Co. Ltd| Plastic bags, packaging materials | Retail, industrial |
In summary, these top 10 plastics manufacturing manufacturers in China offer a wide range of products catered to various industries. From packaging materials and consumer goods to automotive parts and custom-designed molds, each manufacturer has its own specialty and focus. It is essential for businesses to choose the right manufacturer based on their specific requirements and industry expertise.
Background Research for plastics manufacturing manufacturers Companies in China, use qcc.com archive.org importyeti.com
Plastics manufacturing is a thriving industry in China, with numerous manufacturers catering to both domestic and international markets. This research aims to provide background information on plastics manufacturing manufacturers in China using qcc.com, archive.org, and importyeti.com.
Qcc.com is a comprehensive online database that provides information on Chinese companies, including their background, registration details, and financial status. It can be accessed to gather data on plastics manufacturing manufacturers such as company profiles, legal information, date of establishment, and registered capital.
Archive.org is a digital library that allows users to access archived web pages. By searching for plastics manufacturing manufacturers on this platform, one can gather historical information about the company’s website, product range, client testimonials, and any significant changes over time. Archive.org is a valuable resource for understanding the evolution of a manufacturer and assessing its credibility and reliability.
Importyeti.com is an online directory for companies engaged in import and export activities. It provides access to import/export records, shipment details, and customs data. By searching for plastics manufacturing manufacturers on Importyeti.com, one can obtain information about their export history, top destination countries, and main product categories. This data is crucial for evaluating a manufacturer’s experience and market reach.
In summary, by utilizing resources such as qcc.com, archive.org, and importyeti.com, researchers can gain insights into the Chinese plastics manufacturing industry. These platforms provide a wealth of information about companies’ registration details, historical evolution, and export activities. With access to such data, stakeholders can make informed decisions when it comes to dealing with plastics manufacturing manufacturers in China.
Leveraging Trade Shows and Expos for plastics manufacturing Sourcing in China
Trade shows and expos are valuable platforms for sourcing plastics manufacturing in China. By participating in trade shows and expos, businesses can leverage these events to connect with suppliers, explore new products and technologies, and build relationships with industry professionals. Here are some key ways to maximize the benefits of trade shows and expos for sourcing plastics manufacturing in China:
1. Networking: Trade shows and expos provide an opportunity to network with a wide range of suppliers, manufacturers, and experts in the plastics manufacturing industry. Engaging in meaningful conversations and forging connections can lead to potential partnerships and sourcing opportunities.
2. Supplier evaluation: Trade shows allow businesses to evaluate potential suppliers in person. Exhibitors showcase their products, capabilities, and expertise, allowing buyers to assess the quality of their materials, equipment, and production processes. This firsthand evaluation helps in making informed decisions about potential suppliers.
3. Product exploration: Trade shows and expos offer a comprehensive view of the latest trends, innovations, and advancements in plastics manufacturing. Businesses can explore a vast array of products, materials, and technologies on display. This allows buyers to stay up-to-date with market trends, identify new product possibilities, and potentially discover cost-effective solutions.
4. Industry insights: Attendees have the opportunity to attend seminars, workshops, and presentations by industry experts. These sessions provide valuable insights into market dynamics, regulatory changes, and future trends in the plastics manufacturing sector. Gaining a deeper understanding of the industry can help businesses make more informed sourcing decisions.
5. Negotiations: Trade shows and expos often present an ideal environment for negotiations. Exhibitors are keen to engage potential buyers and may be willing to offer competitive pricing, favorable terms, or exclusive deals during the event. Taking advantage of this opportunity can lead to cost savings and better business agreements.
In conclusion, trade shows and expos provide a multitude of advantages for sourcing plastics manufacturing in China. They provide an avenue for networking, evaluating suppliers, exploring products, gaining industry insights, and negotiating deals. By capitalizing on these opportunities, businesses can streamline their sourcing processes, discover new suppliers, and stay competitive in the ever-evolving plastics manufacturing industry.
The Role of Agents and Sourcing Companies in Facilitating plastics manufacturing Purchases from China
Agents and sourcing companies play a crucial role in facilitating plastics manufacturing purchases from China. These entities act as intermediaries between buyers and Chinese manufacturers, streamlining the sourcing process and ensuring a smooth transaction.
One of the primary functions of agents is to assist buyers in finding suitable suppliers in China. They have extensive networks and a deep understanding of the local market, enabling them to quickly identify manufacturers that meet the buyer’s requirements. Agents can conduct thorough supplier assessments, verify their capabilities and quality standards, and negotiate favorable terms on behalf of the buyer.
Moreover, agents can play a key role in communication and language support. They bridge the language barrier between buyers and Chinese manufacturers by providing translation services, ensuring that all parties have a clear understanding of the requirements, specifications, and expectations. This helps to avoid misunderstandings and ensures a smooth flow of information throughout the purchasing process.
Sourcing companies, on the other hand, offer a comprehensive range of services to simplify the procurement process. They typically have a team of experts who specialize in different aspects of sourcing, such as quality control, logistics, and compliance. Sourcing companies act as project managers, overseeing every phase of the manufacturing process, including product development, production, inspection, and shipment. This allows buyers to focus on their core business and have peace of mind knowing that their orders are being handled by professionals.
Furthermore, agents and sourcing companies assist buyers in negotiating prices and contract terms with the manufacturers. They have extensive knowledge of the market dynamics, enabling them to secure favorable pricing and improve the overall procurement efficiency. They can also help with contract drafting and ensure that all legal requirements are met, minimizing potential risks for the buyer.
In summary, agents and sourcing companies are essential in facilitating plastics manufacturing purchases from China. Their expertise, extensive networks, and local market knowledge streamline the sourcing process, ensure effective communication, provide project management support, and negotiate favorable terms. Their role significantly simplifies the procurement process and allows buyers to benefit from the advantages of sourcing from China.
Price Cost Research for plastics manufacturing manufacturers Companies in China, use temu.com and 1688.com
Price Cost Research for plastics manufacturing manufacturers Companies in China can be conducted using two popular online platforms, temu.com and 1688.com. These platforms provide comprehensive information about China’s manufacturing industry, including pricing and cost details. Conducting research on these platforms can help businesses to find suitable plastic manufacturers in China while ensuring competitive pricing.
Temu.com is a Chinese B2B platform that connects international buyers with Chinese suppliers and manufacturers. With a user-friendly interface, businesses can search for plastics manufacturing companies and easily obtain pricing information. The platform provides a range of suppliers and allows users to filter results by price, location, and other criteria. This makes it easier to find manufacturers that can meet specific cost requirements.
Similarly, 1688.com, also known as Alibaba China, is another popular platform specifically catering to the Chinese market. It offers a wide range of products, including plastics manufacturing services. Users can find various plastic manufacturers and compare prices and services to select the most suitable one. The platform provides detailed information about each supplier, enabling users to assess their capabilities, quality standards, and pricing.
When conducting price cost research on these platforms, it is important to keep the following best practices in mind:
1. Compare Multiple Suppliers: By researching different suppliers, businesses can find the most competitive prices. It is recommended to gather quotes from multiple companies to ensure a fair comparison.
2. Assess Quality Standards: Price is a crucial factor, but it should not be the sole determining factor. It is equally important to assess the quality standards of potential manufacturers before committing to a partnership. This can be done by analyzing their certifications, customer reviews, and requesting samples.
3. Minimize Risk: Understand the risks associated with working with manufacturers in China, such as language barriers, cultural differences, and shipping logistics. Seeking professional assistance or building long-term relationships can help mitigate these risks.
In conclusion, utilizing online platforms like temu.com and 1688.com can provide valuable pricing and cost information for plastics manufacturing companies in China. Conducting thorough research and due diligence is essential to ensure that businesses find reliable manufacturers at competitive prices, ultimately contributing to successful partnerships and cost-efficient operations.
Shipping Cost for plastics manufacturing import from China
The shipping cost for plastics manufacturing imports from China can vary depending on several factors, including the volume of the shipment, the mode of transportation, and the distance between the origin and destination.
For shipping by sea, which is the most common mode for large volume shipments, the cost is usually calculated based on the volume or weight of the goods. Freight forwarders or shipping companies typically provide a rate per cubic meter or per ton. The average cost per cubic meter for shipping from China to major ports in the United States, for example, is around $200-$300, but this can vary depending on the specific port and other factors.
In addition to the cost per unit of volume or weight, there are other associated charges to consider, such as handling fees, customs clearance fees, and insurance. These additional charges can add up to about 20%-30% of the shipping cost.
If the shipment is urgent and requires faster delivery, air freight can be an option. Air freight is generally more expensive than sea freight but offers quicker delivery times. The cost for air freight is usually calculated based on the actual weight of the goods and can range from $4-$10 per kilogram.
It is important to note that these costs are approximate and can vary depending on the specific circumstances of the shipment. Working with a reputable freight forwarder or logistics provider is recommended to get accurate quotes and ensure a smooth and cost-effective shipping process. Additionally, factors such as fluctuations in fuel prices and international trade regulations can also impact the shipping cost.
Compare China and Other plastics manufacturing Markets: Products Quality and Price,Visible and Hidden Costs
China is known for its dominant presence in the plastics manufacturing industry. However, it is important to compare China with other plastics manufacturing markets in terms of product quality, price, and visible and hidden costs.
When it comes to product quality, China has made significant strides over the years. Chinese manufacturers have invested in advanced technologies and improved their production processes. As a result, they can produce high-quality plastic products that meet international standards. However, there may still be concerns regarding consistency and product reliability as quality control measures can vary across different manufacturers.
Price is a crucial factor when comparing plastics manufacturing markets. China has a competitive advantage when it comes to pricing due to lower labor and operational costs. This has allowed Chinese manufacturers to offer products at lower prices compared to other markets, making it an attractive option for buyers looking for cost-effectiveness.
Visible costs primarily include the direct expenses associated with manufacturing, such as raw materials, labor, and transportation. China’s large-scale production capabilities and its extensive network of suppliers enable manufacturers to benefit from economies of scale, resulting in lower visible costs.
Hidden costs, on the other hand, can include various factors that are not immediately apparent but can impact overall costs. For instance, intellectual property concerns, such as counterfeiting and patent infringement, are some hidden costs that companies may encounter when manufacturing in China. Additionally, language barriers, cultural differences, and time zone variations can sometimes lead to miscommunication and delays, resulting in hidden costs.
When considering other plastics manufacturing markets, countries like Germany, the United States, and Japan are often seen as leaders in terms of product quality. These markets have a long-standing reputation for producing high-quality plastics with stringent quality control processes. However, with higher labor and operational costs, products from these markets tend to be relatively more expensive compared to China.
In conclusion, China’s plastics manufacturing market has made significant progress in terms of product quality, pricing competitiveness, and visible costs. While there may be concerns regarding consistency and hidden costs, China remains a strong contender in the global plastics manufacturing industry. Comparing with other markets, China’s pricing advantage makes it an attractive option for cost-conscious buyers, although some may prioritize product quality and seek alternatives in countries like Germany, the United States, or Japan.
Understanding Pricing and Payment Terms for plastics manufacturing: A Comparative Guide to Get the Best Deal
When it comes to plastics manufacturing, it is crucial to understand pricing and payment terms to ensure you get the best deal possible. This comparative guide will help you navigate through these aspects, ensuring a mutually beneficial agreement with the manufacturer.
Pricing in plastics manufacturing can vary significantly depending on factors like material costs, production volume, complexity, and labor requirements. It is essential to gather quotes from multiple manufacturers and compare them to obtain a competitive price. However, it’s important to note that the lowest price is not always the best option. Evaluating the manufacturer’s reputation, quality of their products, lead times, and their ability to meet delivery deadlines should also be considered.
Payment terms are another critical aspect to consider. Some manufacturers may require a down payment before initiating production, while others may offer net payment terms, allowing you to pay within a specified time after delivery. It is crucial to discuss and negotiate payment terms that align with your company’s financial capabilities. Additionally, consider any potential discounts for bulk orders or long-term contracts, as these can provide cost savings in the long run.
Other pricing-related factors to consider include mold costs (if applicable), tooling costs, setup fees, and any additional charges for customization or special packaging requirements. Understanding all these costs upfront will help you accurately budget and avoid unexpected expenses later on.
Additionally, it is advisable to establish a clear communication channel with the manufacturer regarding any potential changes in materials, design, or specifications. This ensures that both parties are aligned and prevents any misunderstandings that may impact pricing.
In summary, when seeking the best deal for plastics manufacturing, it is crucial to gather multiple quotes, evaluate non-price factors, clarify payment terms, and consider additional costs. By conducting thorough research, comparing offers, and negotiating effectively, you’ll be better equipped to secure the most favorable pricing and payment terms from the manufacturer.
Chinese Regulations and Industry Standards Certifications for plastics manufacturing,Import Regulations and Customs for plastics manufacturing from China
China has established a series of regulations and industry standards certifications for plastics manufacturing to ensure product quality, safety, and environmental protection. These regulations and certifications play a crucial role in maintaining the integrity of the industry and facilitating the import and export of plastic products.
One of the key regulations in China is the “Regulation on the Administration of Plastic Products,” which sets guidelines for the production, distribution, and use of plastic products. It defines the quality requirements, production processes, and safety standards for various types of plastic products. Manufacturers are required to comply with these regulations and obtain relevant certifications before their products can enter the market.
To demonstrate compliance with these regulations and ensure product quality, manufacturers often obtain certifications such as the China Compulsory Certification (CCC) mark. This certification is required for a wide range of products, including plastic consumer goods, and indicates that the product meets the prescribed quality and safety standards.
In addition to domestic regulations, import regulations and customs procedures also play a crucial role in the import of plastic products from China. Importers need to be aware of customs requirements, import duties, and other applicable regulations before importing plastic products.
When importing plastic products from China, importers need to submit relevant documents such as a commercial invoice, bill of lading, and packing list to customs authorities. Importers should also ensure that the products comply with applicable safety and quality standards in their respective countries. Customs authorities may conduct inspections and tests to verify compliance with these standards.
Importers should also be aware of any restrictions or bans on specific types of plastic products in their country. For example, some countries have imposed bans on the import of single-use plastic products or products containing certain hazardous substances.
To conclude, China has established stringent regulations and industry standards certifications for plastics manufacturing. These aim to ensure product quality, safety, and environmental compliance. Importers of plastic products from China must understand and comply with applicable import regulations and customs procedures to facilitate the smooth import of these products.
Sustainability and Environmental Considerations in plastics manufacturing Manufacturing
Sustainability and environmental considerations are crucial in plastics manufacturing to minimize the negative impacts on the planet and ensure a more sustainable future. Here are some key aspects to focus on:
1. Raw Material Selection: Opting for sustainable raw materials is important. Consider using bio-based plastics derived from renewable sources like corn, sugarcane, or vegetable oils instead of fossil fuel-based plastics. These bio-based plastics have a lower carbon footprint and reduce dependence on finite resources.
2. Energy Efficiency: Implementing energy-efficient practices and equipment can significantly reduce carbon emissions in the manufacturing process. This includes using energy-efficient machinery, optimizing heating, ventilation, and air conditioning systems, and considering alternative energy sources such as solar or wind power.
3. Recycling and Circular Economy: Designing products that are easily recyclable and promoting a circular economy approach is essential. This entails incorporating recycled materials into product manufacturing and encouraging the collection and proper recycling of plastic waste. By closing the loop and reusing materials, the demand for virgin plastics can be reduced, minimizing environmental impact.
4. Waste Minimization and Management: Minimizing waste is crucial to reduce the environmental impact of plastics manufacturing. Implementing practices such as lean manufacturing, where waste is systematically eliminated, can help optimize production processes and reduce material waste. Proper waste management systems should be in place, including waste segregation, treatment, and disposal, to minimize environmental pollution.
5. Life Cycle Assessment: Conducting a comprehensive life cycle assessment (LCA) of the product is essential to understand and minimize its environmental impacts. This analysis considers the entire life cycle, including raw material extraction, manufacturing, transportation, use, and end-of-life options. By identifying hotspots and implementing measures to minimize impacts at each stage, a more sustainable product can be developed.
6. Collaboration and Innovation: Collaboration among stakeholders and research institutions is crucial to drive innovation in sustainable plastics manufacturing. Joint efforts can lead to the development of new eco-friendly materials, advanced manufacturing processes, and more efficient recycling technologies.
In conclusion, sustainability and environmental considerations are vital in plastics manufacturing to mitigate the detrimental effects on the environment. By focusing on raw material selection, energy efficiency, recycling, waste management, life cycle assessment, and collaboration, the industry can move towards a more sustainable and environmentally friendly approach.
List The Evolution history of “plastics manufacturing”
The history of plastics manufacturing is a fascinating journey that traces back to ancient civilizations, although the development of modern plastics began in the 19th century. Here is a brief evolution of plastics manufacturing:
1. Ancient Plastics: Early civilizations, such as the Egyptians and Mesopotamians, used natural materials like resins, plant extracts, and animal horns to create objects similar to plastics. These early forms were not as versatile or durable as modern plastics.
2. Vulcanized Rubber: In the 19th century, Charles Goodyear discovered the process of vulcanization, which revolutionized the rubber industry. This development led to the mass production of items like tires, rubber boots, and seals, setting the stage for further advancements in synthetic materials.
3. Celluloid: In 1869, John Wesley Hyatt invented celluloid, the first industrially produced plastic. Celluloid became popular for making photographic film, billiard balls, and various consumer goods. It marked the emergence of a new era for plastics manufacturing.
4. Bakelite: Developed in 1907 by Leo Hendrik Baekeland, Bakelite was the first fully synthetic plastic. It was heat resistant, electrical non-conductive, and highly moldable, making it ideal for various applications. Bakelite revolutionized industries like automotive, electrical, and appliance manufacturing.
5. Polyethylene: In 1933, scientists at Imperial Chemical Industries accidentally discovered polyethylene while attempting to create a new type of synthetic resin. Polyethylene’s low cost, high durability, and versatility made it the most widely produced plastic in the world, finding applications in packaging, construction, and consumer goods.
6. Nylon: Developed in the late 1930s by Wallace Carothers at DuPont, nylon was the first synthetic fiber. It quickly replaced silk for parachutes and stockings during World War II and led to the development of other synthetic fibers like polyester and acrylic.
7. PVC and PET: In the mid-20th century, polyvinyl chloride (PVC) and polyethylene terephthalate (PET) became prominent. PVC’s resistance to chemicals and PET’s strength and transparency made them popular choices for pipes, packaging, and beverage bottles.
8. Engineering Plastics: Throughout the latter half of the 20th century, significant advancements occurred in polymer science, leading to the development of engineering plastics like polycarbonate, polypropylene, and ABS (Acrylonitrile Butadiene Styrene). These plastics offered improved mechanical properties, heat resistance, and versatility, leading to new applications in automotive, electronics, and medical industries.
9. Biodegradable and Recycled Plastics: With growing environmental concerns, the late 20th century witnessed the rise of biodegradable plastics made from renewable resources like corn starch and recycled plastics. As awareness of sustainability increased, efforts were made to reduce the environmental impact of plastics manufacturing.
The evolution of plastics manufacturing has been characterized by continuous innovation, resulting in the widespread use of plastics in various industries globally. While plastics have undoubtedly brought enormous benefits, ongoing research and advancements strive to address environmental challenges for a more sustainable future.
The Evolution and Market Trends in plastics manufacturing Industry
The plastics manufacturing industry has witnessed significant advancements and market trends over the years. Plastic, a versatile synthetic material, has gained immense popularity due to its wide range of applications, cost-effectiveness, and durability. Let’s explore the evolution and current market trends in this industry.
Evolution:
Plastics manufacturing has evolved greatly since its inception. Initially, plastics were limited to simple products such as combs and buttons. However, with advancements in manufacturing techniques and the discovery of new materials, the industry expanded rapidly. The development of thermoplastics and thermosetting plastics opened up opportunities for more complex and specialized products.
The introduction of injection molding revolutionized plastics manufacturing by enabling mass production of intricate shapes and designs. This innovation made plastics more accessible and affordable, leading to a surge in demand for plastic products across various industries.
Market Trends:
1. Sustainable Plastics: With increasing environmental concerns, there is a growing demand for sustainable and eco-friendly plastics. Companies are now focusing on developing biodegradable, compostable, and recyclable plastics. This trend is driven by consumer awareness and government regulations promoting sustainability.
2. Packaging Solutions: Plastics play a crucial role in packaging industries. The demand for lightweight, durable, and visually appealing packaging has fueled the growth of plastics manufacturing. Additionally, the rise of e-commerce has further boosted the need for protective packaging materials.
3. Automotive Industry: Plastics are extensively used in the automotive sector due to their weight reduction capabilities and design flexibility. The trend towards electric vehicles and the need for improved fuel efficiency have accelerated the use of plastics in vehicle manufacturing, replacing traditional materials such as metal.
4. Medical and Healthcare Applications: Plastics are indispensable in the medical field due to their hygienic nature and ability to be molded into complex shapes. The demand for medical-grade plastics, including implantable devices, surgical instruments, and packaging materials, has been steadily increasing, driven by advancements in healthcare technology.
5. 3D Printing: The emergence of 3D printing has revolutionized the manufacturing process by enabling the production of complex plastic parts with minimal waste. This technology has opened up new possibilities for rapid prototyping, customizing products, and reducing manufacturing lead times.
In conclusion, the plastics manufacturing industry has evolved significantly, driven by technological advancements, sustainability concerns, and market demands. Understanding these market trends is crucial for businesses to stay competitive and adapt to the changing needs of consumers and industries.
Custom Private Labeling and Branding Opportunities with Chinese plastics manufacturing Manufacturers
Chinese plastics manufacturing manufacturers offer a lucrative opportunity for custom private labeling and branding of products. With their expertise, competitive pricing, and vast production capabilities, they allow companies to establish their unique identity in the market.
Private labeling enables businesses to sell products under their own brand name, creating a distinct image and fostering customer loyalty. Chinese plastics manufacturers offer a wide range of customizable options, including product design, packaging, and labeling, enabling companies to create a unique and recognizable brand.
Moreover, Chinese manufacturers have extensive experience in working with international companies, allowing for seamless communication and collaboration. They possess state-of-the-art facilities and cutting-edge technology to produce high-quality plastic products that meet global regulatory standards.
In addition to private labeling, Chinese manufacturers also facilitate branding opportunities. They can help businesses build their brand reputation by incorporating logos, slogan printing, and other branding elements into the product design and packaging. This enhances brand visibility and creates a strong brand presence in the market.
The competitive pricing of Chinese plastics manufacturing manufacturers also makes it an attractive option for private labeling and branding. Their efficient production processes enable cost-effective manufacturing and lower production costs, allowing businesses to offer competitive pricing to their customers.
By leveraging the expertise and capabilities of Chinese plastics manufacturing manufacturers, companies can take advantage of custom private labeling and branding opportunities. This strategic partnership helps businesses differentiate themselves in the market, strengthen their brand identity, and ultimately drive sales and growth.
Tips for Procurement and Considerations when Purchasing plastics manufacturing
When it comes to procurement in the plastics manufacturing industry, there are several considerations that should be kept in mind. These considerations will help ensure that the purchasing process is efficient, cost-effective, and sustainable. Here are some tips and factors to consider:
1. Supplier Selection: Choosing the right supplier is crucial. Look for suppliers who have a strong track record, experience in the industry, and a good reputation. Assess their capabilities, quality control measures, and certifications.
2. Quality Control: Quality is paramount in plastics manufacturing. Ensure that the supplier follows rigorous quality control procedures and has certifications like ISO 9001. Request samples, conduct tests, and appraise their manufacturing processes.
3. Cost Analysis: Comparing costs from different suppliers is essential for cost-effective procurement. Consider factors like unit price, volume discounts, shipping costs, and payment terms. However, don’t compromise on quality to save costs as it may lead to unsatisfactory products.
4. Material Selection: Choosing the right plastic material is vital. Consider factors like strength, flexibility, durability, and compatibility with the intended application. Evaluate different materials such as polyethylene, polystyrene, PVC, and polypropylene, based on these requirements.
5. Environmental Considerations: Sustainability is increasingly important in today’s world. Look for suppliers who offer eco-friendly and recycled plastics, reducing environmental impact. Check if the supplier follows proper waste management and recycling practices.
6. Capacity and Lead Time: Evaluate the supplier’s production capacity and their ability to meet your demand. Consider their lead time, especially if you have time-sensitive projects, to avoid delays or bottlenecks in your manufacturing operations.
7. Regulatory Compliance: Ensure that the supplier complies with all relevant regulations and meets industry standards. This includes health and safety regulations, labeling requirements, and adherence to material specifications.
8. Communication and Collaboration: Establish effective communication channels with the supplier to ensure a smooth procurement process. Frequent communication and collaboration help address any issues, changes, or requirements promptly.
9. Contract and Terms: Create a comprehensive contract that clearly outlines the terms, including pricing, quantities, delivery schedules, and quality criteria. Ensure both parties understand the terms and conditions to avoid any disputes later.
10. Continuous Improvement: Regularly evaluate the supplier’s performance and seek feedback from your team to maintain quality standards. Encourage continuous improvement, and consider long-term partnerships to build trust and loyalty.
By considering these tips and factors, you can enhance your procurement process for plastics manufacturing, ensuring quality, cost-effectiveness, sustainability, and timely delivery of materials.
FAQs on Sourcing and Manufacturing plastics manufacturing in China
1. Why should I consider sourcing and manufacturing plastics in China?
China is known as the world’s largest plastics manufacturer, offering cost-effective production and a wide range of plastic products. The country’s extensive industrial infrastructure, skilled labor force, and established supply chain contribute to competitive pricing and efficient production capabilities.
2. How do I find reliable plastic manufacturers in China?
To find reliable manufacturers, you can start by conducting thorough research and due diligence. Utilize online platforms and directories that provide comprehensive information on manufacturers, their capabilities, certifications, and customer reviews. Additionally, consider visiting trade shows and exhibitions in China to personally meet potential suppliers and evaluate their production facilities.
3. What are the potential challenges of sourcing plastics in China?
Language and cultural differences can pose challenges when communicating with Chinese manufacturers. Clear and specific instructions, detailed project plans, and regular updates are essential for effective collaboration. Additionally, quality control may be a concern, so it is important to establish strict quality standards, conduct inspections, and implement quality control measures throughout the manufacturing process.
4. How can I ensure the quality of plastic products manufactured in China?
To ensure quality, it is crucial to have a well-defined product specification sheet that outlines the desired characteristics, dimensions, and performance requirements. Conduct regular factory visits or employ a third-party inspection service to verify compliance with these specifications. Implementing quality control procedures, such as spot checks, product testing, and audits, helps maintain consistency and address any issues promptly.
5. What are the shipping and logistics options for plastic manufacturing in China?
China has a well-developed logistics network, offering multiple shipping options. Depending on your requirements, you can choose between air freight, sea freight, or a combination of both. It is recommended to work closely with your manufacturer and freight forwarders to optimize costs, consolidation, and shipping timelines.
6. How can I protect my intellectual property (IP) when manufacturing in China?
Protecting IP can be a concern, so it is advisable to register patents, trademarks, and copyrights both in your home country and in China. Additionally, when engaging with manufacturers, signing Non-Disclosure Agreements (NDAs) and properly drafting contracts can help protect your IP rights. You may also consider working with reputable manufacturers with a history of respecting IP rights or obtaining legal advice specialized in Chinese IP law.
In summary, sourcing and manufacturing plastics in China offer many advantages such as cost-effectiveness and vast production capabilities. However, challenges related to communication, quality control, and IP protection should be addressed through thorough research, proactive measures, and careful collaboration with trusted manufacturers and supply chain partners.
Why contact sourcifychina.com get free quota from reliable plastics manufacturing suppliers?
Sourcifychina.com is a platform that connects businesses with reliable plastics manufacturing suppliers in China. The website offers a unique opportunity for businesses to obtain a free quota from these suppliers. This initiative aims to help businesses gain access to high-quality manufacturing services without any financial burden.
The main reason sourcifychina.com offers a free quota is to promote and encourage businesses to explore the benefits of sourcing plastics from China. China is renowned for its cost-effective and efficient manufacturing capabilities, making it an attractive option for businesses looking to lower their production costs and increase profit margins. By providing a free quota, sourcifychina.com aims to eliminate the initial hesitation and financial constraints that businesses may encounter when starting to source from China.
Additionally, sourcifychina.com understands the importance of finding reliable suppliers. Through their extensive network of verified and trusted plastics manufacturing suppliers, they aim to simplify the sourcing process and minimize the risk of working with unreliable or subpar manufacturers. By offering a free quota, businesses can engage with these suppliers and assess their capabilities and product quality firsthand, ensuring a reliable and satisfactory partnership.
The free quota also allows businesses to understand the cost structure associated with their product specifications, ensuring transparency in pricing and avoiding any unforeseen expenses. This knowledge is crucial for businesses to make informed decisions about their sourcing strategies and overall budget planning.
In summary, sourcifychina.com offers a free quota from reliable plastics manufacturing suppliers to promote sourcing from China, alleviate financial burdens, minimize risks associated with supplier selection, and provide businesses with a transparent understanding of costs. This approach empowers businesses to confidently explore manufacturing opportunities in China and reap the benefits of its competitive manufacturing capabilities.