Introduce about screw making machines guide,Qulity,Cost,Supplier,Certification,Market,Tips,FAQ
Screw making machines are essential equipment in the manufacturing industry, as they are used to produce screws of various sizes and shapes with precision and efficiency. These machines come in different types, such as thread rolling machines, screw heading machines, and screw making lathes.
When choosing a screw making machine, it is crucial to consider the machine’s quality, as it directly impacts the screw’s durability and performance. Look for machines from reputable manufacturers known for their high-quality products.
The cost of a screw making machine can vary depending on the type, size, and features. It is essential to weigh the initial investment against the long-term benefits and potential cost savings in production.
Finding a reliable supplier for screw making machines is key to ensuring a smooth purchasing process and technical support when needed. Look for suppliers with a good track record of customer satisfaction and after-sales service.
Certification is essential when purchasing screw making machines to ensure that they meet industry standards and regulations. Look for machines that are certified by reputable organizations.
The market for screw making machines is growing, driven by the increasing demand for screws in various industries such as construction, automotive, and electronics.
Some tips for purchasing screw making machines include conducting thorough research, comparing different options, and considering the machine’s compatibility with your production requirements.
Frequently asked questions about screw making machines include their capacity, speed, maintenance requirements, and technical support availability.
In conclusion, screw making machines play a crucial role in manufacturing processes, and choosing the right machine is essential for efficient production. Consider factors such as quality, cost, supplier reputation, certification, and market trends when making your decision.
Types of screw making machines
Screw making machines are used to automate the process of manufacturing screws. These machines aid in the production of screws of various sizes, shapes, and materials. There are several types of screw making machines, each with its own specialized features and capabilities.
1. Automatic Screw Heading Machine: This machine is designed to produce the head of the screw. It involves the deformation of raw material wire into the required shape and size. The screw blank is fed into the machine, and it undergoes various operations such as cutting, pointing, and shaping to form the head.
2. Screw Thread Rolling Machine: This machine is used to form the screw’s threads by cold forming. The screw blank is fed into the machine, between two dies, and pressure is applied to create the threads through a rolling process. This ensures a consistent and accurate thread pattern on the screw.
3. Screw Point Cutting Machine: As the name suggests, this machine is used to cut or shape the tip or point of the screw. It is crucial for ensuring the screw’s functionality when inserted into a material. The machine consists of different cutting tools and processes to create different screw point designs.
4. Screw Cutting Machine: This machine is responsible for cutting the screw to the desired length. It can cut screws of various lengths, starting from longer rods or coils of screw material. The machine consists of a cutting tool that accurately cuts the screw to the desired length.
5. Screw Head Slotting Machine: This specific machine is designed to create slots or grooves on the screw head for the purpose of screwdriver engagement. It cuts the slot pattern on the screw head with precision and consistency.
6. Screw Thread Grinding Machine: This machine is used for manufacturing high-precision threads on screws. It utilizes a grinding wheel for removing material and forming the threads. The machine offers excellent accuracy and surface finish for specialized screw applications.
7. Screw Point Threading Machine: This machine is used to create specialized threading or grooving on the screw point. It is commonly used for self-drilling screws or screws designed specifically for wood, plastic, or metal applications. The machine creates sharp threads on the screw point to enhance drilling efficiency.
In conclusion, screw making machines come in various types to handle different aspects of screw manufacturing, including heading, threading, cutting, slotting, and grinding. These machines greatly improve the efficiency, accuracy, and consistency of screw production, leading to high-quality screws for a wide range of applications.
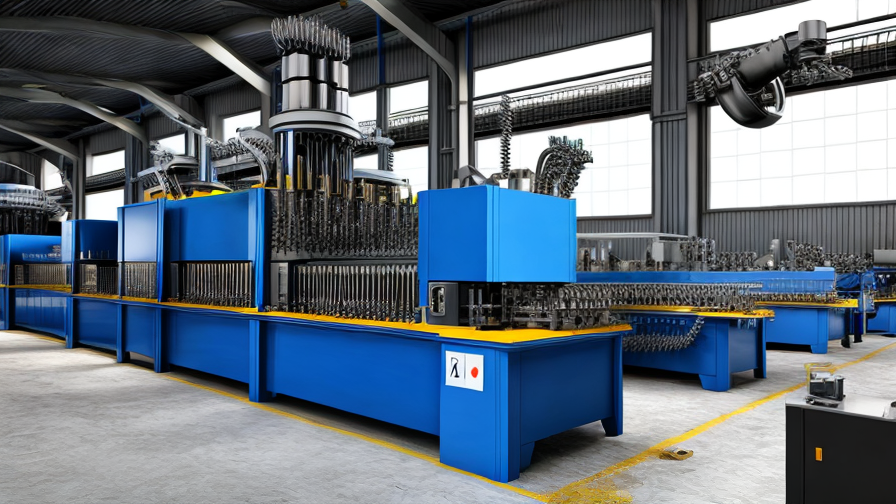
Pros and Cons of Using screw making machines
Screw making machines are automated tools that are designed for producing screws of various sizes and types. These machines offer many advantages, but also come with a few drawbacks. Let’s explore the pros and cons of using screw making machines.
Pros:
1. Increased Efficiency: Screw making machines can produce screws at a much faster rate compared to manual production. This leads to higher productivity and efficiency in manufacturing operations, as a large number of screws can be produced in a short amount of time.
2. Consistent Quality: These machines ensure consistent quality control, as they are programmed to produce screws with precise specifications. This helps to eliminate variations and ensures that all screws meet the required standards set by the manufacturer.
3. Cost Savings: By using screw making machines, manufacturers can achieve significant cost savings in terms of labor costs. These machines require minimal human intervention, leading to reduced labor expenses and improved overall profitability.
4. Flexibility: Screw making machines are designed to produce screws of various sizes and types. They can be easily adjusted to accommodate different screw specifications, making them highly flexible in meeting diverse manufacturing needs.
Cons:
1. High Initial Investment: Acquiring a screw making machine can require a significant upfront investment, especially if a manufacturer requires specialized machines for specific screw production needs. This cost might not be feasible for small-scale manufacturers or those with limited budgets.
2. Lack of Customization: While screw making machines offer flexibility, they may not be as suitable for producing highly specialized or custom screws. If a manufacturer requires complex or unique screw designs, these machines might not be able to produce them accurately, necessitating manual production methods.
3. Maintenance and Repairs: Like any machinery, screw making machines require regular maintenance and occasional repairs. This can translate into additional costs and downtime during maintenance, which can impact production schedules and output.
4. Lack of Versatility: While screw making machines can produce a wide range of standard screws, they may not be versatile enough to manufacture other types of fasteners or hardware. Manufacturers needing a variety of products might need additional equipment or processes.
In conclusion, screw making machines offer numerous benefits in terms of efficiency, quality control, cost savings, and flexibility. However, their high initial investment, limited customization ability, maintenance requirements, and potential lack of versatility should also be considered when evaluating their use in a manufacturing environment.
screw making machines Reference Specifications (varies for different product)
When it comes to designing and manufacturing screw-making machines, it is crucial to consider various reference specifications to ensure optimal performance and functionality. These specifications can vary depending on the intended product and application, and they play a significant role in determining the machine’s capabilities and features.
One important reference specification for screw-making machines is the type and size of screws they can produce. Different industries require various screw types, such as self-tapping screws, wood screws, or machine screws. Moreover, the size and thread pitch of the screws should also be considered since the machine needs to be capable of producing screws within specific length and diameter ranges.
Another essential specification is the production capacity of the machine. This refers to the quantity of screws the machine can produce within a given time frame. Production capacity depends on factors like the speed of the machine, the number of operations it can perform simultaneously, and the efficiency of the screw-making process. This specification is crucial for determining the machine’s suitability for high-volume production or smaller-scale operations.
Accuracy and precision are also vital considerations in screw-making machines. The machines should be capable of consistently producing screws with precise dimensions and tight tolerances. This ensures compatibility and reliable performance when the screws are used in various applications. Factors such as the control systems, tooling, and machining techniques employed by the machine influence its ability to achieve the desired accuracy.
Furthermore, the ease of operation, maintenance, and safety features of the machine are significant reference specifications. User-friendly interfaces, intuitive controls, and straightforward maintenance procedures contribute to the efficiency and productivity of the operators. Additionally, incorporating safety mechanisms and complying with industry standards are crucial to ensure the well-being of the machine operators and prevent accidents during operation.
Material compatibility is another important consideration. Screw-making machines should be able to handle various materials commonly used for screws, such as steel, stainless steel, aluminum, and brass. The machine’s design and construction should be appropriate for the specific material, allowing for efficient cutting, forming, and finishing processes.
In conclusion, the reference specifications for screw-making machines vary depending on the desired screws’ type, size, production capacity, accuracy, ease of operation, and material compatibility. By considering these specifications during the machine’s design and manufacturing process, manufacturers can ensure that the resulting machines meet the requirements of different industries and applications.
Applications of screw making machines
Screw making machines play a vital role in various industries, offering numerous applications. These machines are used to efficiently manufacture screws of different sizes, shapes, and materials. Some of the key applications of screw making machines include:
1. Manufacturing Industry: Screw making machines are extensively utilized in the manufacturing industry to produce screws that are used in assembling products. These machines allow for mass production of high-quality screws with precise dimensions, ensuring consistent performance and easy integration into various products.
2. Construction Industry: In the construction sector, screw making machines are employed to manufacture screws that are utilized for fastening joints, connecting structural components, and securing various materials. The consistently produced screws ensure the stability and durability of structures, providing a reliable solution for construction projects.
3. Automotive Industry: Screw making machines have significant applications in the automotive industry. Various types of screws produced by these machines are utilized for assembling vehicles, securing different parts, and ensuring the safety and performance of automobiles. These machines enable the production of screws with specific dimensions, threads, and levels of precision required by automotive manufacturers.
4. Electronics Industry: The electronics industry extensively benefits from screw making machines as they produce screws used in the manufacturing of electronic devices, circuit boards, and components. The machines can produce screws with different head shapes and threads to meet the specific requirements of the electronics industry, ensuring proper assembly and functionality of electronic products.
5. Aerospace Industry: Screw making machines are essential in the aerospace industry for manufacturing screws used in aircraft assembly, including securing structural components, engines, and critical systems. These machines ensure the production of screws with high strength, precision, and specific compositions to withstand extreme conditions faced during flight.
6. Medical Industry: Screw making machines are utilized in the medical sector to produce precision screws utilized in various medical devices, prosthetics, and implants. These machines help manufacture medical-grade screws to meet stringent quality standards and ensure compatibility with human tissues, thereby contributing to the success of medical procedures and treatments.
In conclusion, screw making machines find applications in a wide range of industries, including manufacturing, construction, automotive, electronics, aerospace, and medical sectors. The ability to produce screws with precision, strength, and specific dimensions makes these machines indispensable in ensuring the efficient assembly, stability, and functionality of various products and structures.
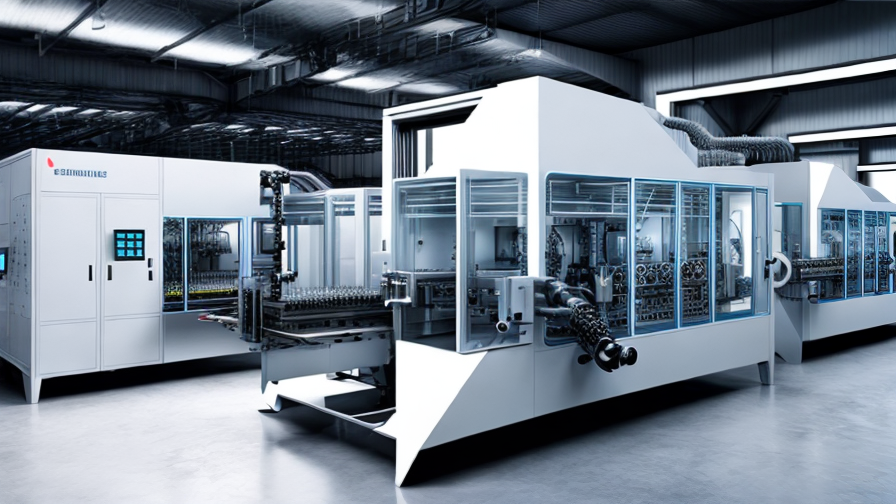
The Work Process and how to use screw making machines
The work process of screw making machines involves several steps to produce high-quality screws with precision and efficiency. Here is a simplified overview of the process:
1. Material Preparation: The machine operator starts by preparing the raw material, typically metal wires or rods, which are cut into appropriate lengths.
2. Heading: In this step, the first part of the screw, known as the head, is formed. The machine uses a combination of force and rotating mechanisms to shape the head either by forging or cold heading. This process provides the base structure for the screw.
3. Thread Rolling: The next step involves creating the threaded portion of the screw. The machine uses specialized dies to roll and shape the threads onto the screw. This process ensures precise and uniform threading, crucial for proper functionality of the screw.
4. Heat Treatment (Optional): Some screws require heat treatment to enhance their mechanical properties such as strength and hardness. This step involves heating the screws to a specific temperature and then rapidly cooling them through processes like quenching. It promotes durability and resistance to breakdown.
5. Surface Coating (Optional): Depending on the intended application, some screws may undergo surface coating processes such as galvanization or electroplating to improve their resistance to corrosion.
To use screw making machines effectively, operators must follow a few guidelines:
1. Machine Setup: Ensure the machine is correctly set up, including securing the appropriate dies and adjusting the machine settings as per the screw specifications (size, type, threading pitch, etc.).
2. Material Feeding: Feed the prepared raw material into the machine’s input mechanism, ensuring it aligns properly to prevent jamming or misalignment during production.
3. Calibration: Regularly calibrate the machine to ensure accuracy and consistency in screw dimensions and threading. This may involve periodically checking and adjusting die alignments, pressure settings, or thread rolling mechanisms.
4. Maintenance and Cleaning: Routine maintenance, including lubricating moving parts, replacing worn-out dies or cutters, and cleaning debris and residue, is necessary to optimize machine performance and extend its lifespan.
5. Quality Control: Monitor the output screws regularly to ensure their quality meets the specified standards. This may involve sample checks, measurements, and visual inspections.
Effectively utilizing screw making machines requires a combination of technical knowledge, experience, and attention to detail to produce high-quality screws efficiently.
Quality Testing Methods for screw making machines and how to control the quality
Quality testing methods for screw making machines are essential to ensure the production of high-quality screws. Here are some common methods used in the industry:
1. Dimensional testing: This involves measuring the length, diameter, pitch, and other critical dimensions of the screws. Calipers, micrometers, or optical measuring devices are typically employed to assess whether the screws meet the specified tolerances.
2. Torque and tension testing: These tests evaluate the ability of the screws to withstand certain torque levels or tension forces. This is done by applying a controlled level of torque or tension and assessing if the screws can retain their integrity without failure.
3. Surface finish assessment: The surface quality of screws significantly impacts their functionality and appearance. Testing methods like visual inspection, magnification, or profilometers are used to evaluate surface roughness, burrs, scratches, or any other imperfections.
4. Material composition analysis: It is crucial to ensure that the screws are made from the desired material composition with the required strength and corrosion resistance. Methods like X-ray fluorescence (XRF) or spectroscopic analysis are employed to verify the elemental composition of the screw material.
5. Thread testing: The threads of screws need to be accurately formed to ensure proper engagement and assembly. Dedicated gauges are used to check thread pitch, depth, major or minor diameter, and profile.
To control the quality of screw production, several measures can be implemented:
1. Regular calibration: Calibrating measurement devices used in quality testing periodically ensures accurate and reliable results.
2. Process monitoring: Implementing sensors and control systems to monitor critical parameters during screw manufacturing enables real-time adjustment and prevents the production of faulty screws.
3. Standard Operating Procedures (SOPs): Clearly documented SOPs for each manufacturing step help maintain consistency and reduce process variations.
4. Training and skill development: Providing proper training to machine operators and ensuring they have the necessary expertise helps in maintaining quality standards.
5. Statistical Process Control (SPC): Collecting and analyzing data from quality tests over time helps identify trends, patterns, and potential deviations, enabling proactive quality control measures.
It is crucial to form a comprehensive quality assurance system that combines these testing methods with effective quality control measures to ensure that screw making machines consistently produce screws that meet or exceed the required quality standards.
screw making machines Sample Policy and Post-Purchase Considerations for screw making machines from China
Sample Policy and Post-Purchase Considerations for Screw Making Machines from China:
Policy:
1. Quality Assurance: We prioritize quality and ensure that all screw making machines from China are manufactured and tested to meet international standards. Our policy includes pre-shipment inspections to guarantee the machines’ performance and reliability.
2. Warranty: We offer a comprehensive warranty for all screw making machines purchased, ensuring peace of mind for customers. This warranty covers manufacturing defects and faulty components, as well as support for repair and replacement.
3. Technical Support: Our company provides dedicated technical support to assist clients with troubleshooting, installation, and operational issues. We have trained professionals available to answer queries and guide users through any difficulties they may encounter.
4. Customization: We understand that different clients have unique requirements and preferences. Therefore, we offer customization options for screw making machines to tailor them to individual needs. This includes features like adjustable speed, size range, and compatibility with various materials.
Post-Purchase Considerations:
1. Training and Installation: It is vital to provide proper training and installation guidance to ensure efficient running and safe operation of the screw making machines. Our company offers comprehensive training sessions for operators and technicians to familiarize them with the machines’ functionalities and maintenance procedures.
2. Spare Parts and Maintenance: We maintain a stock of spare parts for all our screw making machines, ensuring prompt availability and minimal downtime in case of component failure. Additionally, we provide guidelines and recommendations for routine maintenance to optimize machine performance and extend their operational lifespan.
3. Documentation and Manuals: We provide detailed instruction manuals, guides, and documentation in English to assist users in operating and maintaining the screw making machines effectively. These materials include step-by-step instructions, troubleshooting tips, and safety information.
4. Feedback and Support: We value our customers’ feedback and encourage open communication. Clients can contact our support team with any concerns, feedback, or suggestions related to the screw making machines purchased. We are committed to addressing queries promptly and continuously improving our products and services.
Note: The above policy and considerations are provided as a general sample guideline. Actual policies and considerations may vary depending on specific manufacturers and suppliers.
Sourcing screw making machines from China: Opportunities, Risks, and Key Players
China is a major player in the production of screw making machines, offering a wide range of opportunities for sourcing these essential manufacturing tools. The country boasts a strong manufacturing sector, competitive pricing, and a vast array of suppliers to choose from.
One of the key advantages of sourcing screw making machines from China is the cost-effectiveness. Chinese manufacturers typically offer lower prices compared to other countries, making it an attractive option for businesses looking to save on production costs. Additionally, China has a well-established supply chain and infrastructure that can support large-scale production requirements.
However, there are also risks associated with sourcing screw making machines from China. Quality control can be a concern, as some manufacturers may cut corners to offer lower prices. Communication barriers, intellectual property issues, and longer lead times for production and shipping are other potential risks to consider.
Key players in the Chinese screw making machine market include Zhejiang Yongsheng Machinery Co., Ltd., Dongguan Song Shan Lake Precision Machinery Co., Ltd., and Xiamen Fu Sheng Machinery Equipment Co., Ltd. These companies have a strong track record of producing high-quality machines and have established reputations in the industry.
In conclusion, sourcing screw making machines from China can offer significant opportunities for cost savings and access to a wide range of suppliers. However, businesses should also be aware of the risks involved and take steps to mitigate them, such as conducting thorough due diligence on potential suppliers and implementing strict quality control measures.
How to find and select reliable screw making machines manufacturers in China,use google search manufacturers and suppliers
When looking for reliable screw making machine manufacturers in China, start by conducting a search on Google using relevant keywords such as “screw making machine manufacturers in China” or “screw making machine suppliers in China.”
Look for manufacturers with a reputable website, positive customer reviews, and a history of producing high-quality products. Check if they have certifications such as ISO 9001 to ensure that their manufacturing processes meet international standards.
You can also use business-to-business platforms such as Alibaba or Made-in-China to find a list of potential manufacturers. These platforms allow you to filter search results based on factors such as location, certifications, and product specifications.
Once you have a list of potential manufacturers, contact them directly to inquire about their products, manufacturing processes, lead times, and pricing. Ask for samples or visit their factory if possible to assess the quality of their products firsthand.
Consider working with a manufacturer who offers customization options and can meet your specific requirements. Make sure to establish clear communication channels and discuss payment terms and shipping logistics before making a final decision.
Overall, thorough research, due diligence, and direct communication with potential manufacturers are key to finding and selecting a reliable screw making machine manufacturer in China.
How to check screw making machines manufacturers website reliable,use google chrome SEOquake check if ranking in top 10M
To check if a screw making machine manufacturer’s website is reliable, you can follow these steps:
1. Use Google Chrome: Open the website in Google Chrome browser as it offers various tools and extensions to assess website credibility.
2. Install SEOquake Extension: Install the SEOquake extension from the Chrome Web Store. SEOquake provides a comprehensive analysis of the website’s SEO performance, including its ranking, traffic, and more.
3. Check Global Alexa Ranking: Once the SEOquake extension is installed, click on its icon, and it will display various metrics. Look for the “Alexa Rank” to check the website’s global ranking. If it is within the top 10 million, it indicates a reasonably high level of popularity and trustworthiness.
4. Analyze Website Traffic: SEOquake also provides an estimation of the website’s monthly traffic. Look for the “Estimated Traffic” metric to get an idea of the number of visitors the website receives. This can help verify its popularity and reliability.
5. Assess Domain Age: Another factor to consider is the website’s domain age. SEOquake shows the “Domain Age” metric, providing information about how long the domain has been registered. Generally, older domains are perceived as more trustworthy.
6. Additional Considerations: While SEOquake provides vital information, it is still essential to delve deeper. Check if the website has clear contact information, such as a physical address, phone number, or email. Look for customer reviews, testimonials, or case studies to determine the manufacturer’s reputation and reliability. Additionally, you can search for any negative feedback or complaints about the manufacturer.
By using these techniques and assessing the information provided by SEOquake, you can evaluate the reliability of a screw making machine manufacturer’s website. Remember to consider other factors such as customer feedback, industry reputation, and overall transparency to make an informed decision.
Top 10 screw making machines manufacturers in China with each 160 words introduce products,then use markdown create table compare
1. Suhang Machinery
Suhang Machinery specializes in the manufacturing of high-quality screw making machines. Their products include thread rolling machines, screw heading machines, and screw making machines. Suhang Machinery is known for its reliable performance, high efficiency, and competitive pricing.
2. Dalong Machinery
Dalong Machinery is a leading manufacturer of screw making machines in China. Their product range includes automatic screw making machines, thread rolling machines, and screw heading machines. Dalong Machinery’s machines are designed to meet the needs of various industries and are known for their precision and durability.
3. Jieda Machinery
Jieda Machinery is a well-known manufacturer of screw making machines in China. Their product lineup includes screw heading machines, thread rolling machines, and automatic screw making machines. Jieda Machinery’s machines are known for their high speed, precision, and low maintenance requirements.
4. Golden Technologies
Golden Technologies is a reputed manufacturer of screw making machines in China. Their product range includes automatic screw making machines, thread rolling machines, and screw heading machines. Golden Technologies’ machines are highly efficient, reliable, and user-friendly.
5. Sanfeng Machinery
Sanfeng Machinery is a leading supplier of screw making machines in China. They offer a wide range of products, including automatic screw making machines, thread rolling machines, and screw heading machines. Sanfeng Machinery’s machines are known for their superior performance, durability, and competitive pricing.
| Manufacturer | Products | Features |
|——————–|————————————————–|————————————————————————————————————————
| Suhang Machinery | Thread rolling machines, screw heading machines | Reliable performance, high efficiency, competitive pricing |
| Dalong Machinery | Automatic screw making machines, thread rolling machines | Precision, durability, designed for various industries |
| Jieda Machinery | Screw heading machines, thread rolling machines | High speed, precision, low maintenance requirements |
| Golden Technologies| Automatic screw making machines, thread rolling machines | Highly efficient, reliable, user-friendly |
|Sanfeng Machinery | Automatic screw making machines, thread rolling machines | Superior performance, durability, competitive pricing |
In conclusion, these top 5 screw making machine manufacturers in China offer a wide range of products that cater to the needs of various industries. Their machines are known for their reliability, efficiency, and competitive pricing, making them popular choices among customers.
Background Research for screw making machines manufacturers Companies in China, use qcc.com archive.org importyeti.com
Screw making machines manufacturers in China are known for their high-quality and cost-effective products. By leveraging databases such as qcc.com, archive.org, and importyeti.com, interested parties can gain valuable insights into the capabilities and reputation of these companies.
Qcc.com provides up-to-date information on Chinese businesses, including contact details, company profiles, and customer reviews. This platform can be used to assess the credibility and reliability of screw making machine manufacturers before entering into any business agreements.
Archive.org offers an archive of historical data, such as past company websites, product catalogs, and reviews. By examining this information, potential buyers can evaluate the track record and evolution of different manufacturers, allowing them to make informed decisions.
Importyeti.com is a database of import-export data, which can be used to track the trading activities of screw making machine manufacturers in China. This platform reveals key information such as the volume of exports, top trading partners, and product trends, providing valuable insights into the market dynamics and competitive landscape.
By leveraging these databases, interested parties can make well-informed decisions when selecting a screw making machine manufacturer in China. They can assess factors such as the company’s reputation, production capacity, and market presence, ultimately ensuring a successful and efficient sourcing process.
Leveraging Trade Shows and Expos for screw making machines Sourcing in China
Trade shows and expos are excellent platforms for sourcing screw making machines in China. These events bring together manufacturers, suppliers, and industry professionals, providing a unique opportunity for businesses to connect and explore potential partnerships.
By attending trade shows and expos focused on machinery and manufacturing, companies can gain valuable insights into the latest screw making technologies, industry trends, and developments in China. These events often showcase a wide range of screw making machines, from basic models to advanced and automated solutions.
One key advantage of trade shows and expos is the ability to meet face-to-face with suppliers. This direct interaction allows businesses to assess the quality, reliability, and efficiency of the screw making machines on display. It also enables potential buyers to negotiate prices, inquire about customization options, and evaluate after-sales support.
In addition, trade shows and expos provide a platform for networking and building relationships with suppliers, industry experts, and other businesses in the same field. These connections can be valuable for future collaborations, knowledge sharing, and expanding a company’s supply chain network.
To make the most of trade shows and expos for screw making machines sourcing in China, companies should prepare in advance. This includes conducting thorough research on the participating exhibitors, identifying key suppliers, and setting clear objectives. It is crucial to have a detailed understanding of the desired specifications, production capacity, and budget limitations to streamline the sourcing process.
Lastly, businesses should allocate sufficient time to explore the exhibition, engaging in conversations with multiple suppliers, and comparing different screw making machines. Taking notes, collecting brochures and business cards, and requesting samples or demos will help in evaluating the options after the event.
By leveraging trade shows and expos, companies can efficiently source screw making machines in China, gain industry insights, and establish valuable connections with reliable suppliers. These platforms provide opportunities for in-depth evaluation, negotiation, and ultimately facilitate a successful sourcing process for businesses in need of screw making machines.
The Role of Agents and Sourcing Companies in Facilitating screw making machines Purchases from China
Agents and sourcing companies play a crucial role in facilitating the purchase of screw making machines from China. These intermediaries act as a bridge between buyers and manufacturers, ensuring a smooth and efficient procurement process.
One of the key responsibilities of agents and sourcing companies is to identify reliable suppliers that specialize in the production of screw making machines. Through their industry knowledge and network, they can connect buyers with established manufacturers that offer high-quality and cost-effective machines. This saves buyers the time and effort of searching for suitable suppliers on their own.
Agents and sourcing companies also assist in negotiating favorable terms and conditions with suppliers. They have a deep understanding of the Chinese market, including local customs, business practices, and regulations. This enables them to navigate any potential language or cultural barriers, ensuring effective communication and a mutually beneficial agreement between the buyer and supplier.
Additionally, agents and sourcing companies help buyers in conducting due diligence on potential suppliers. This includes verifying the supplier’s credentials, assessing their production capabilities, and inspecting the quality of their products. By conducting thorough supplier assessments, agents and sourcing companies minimize the risk of purchasing substandard or counterfeit screw making machines.
Furthermore, these intermediaries provide logistics support. They coordinate the transportation of the purchased machines from the manufacturers’ facilities to the buyer’s location. This involves arranging shipping, customs clearance, and ensuring that the machines arrive in a timely and secure manner.
Agents and sourcing companies also act as a source of ongoing support and troubleshooting. They assist with after-sales service, warranty claims, and resolving any issues that may arise related to the purchased machines. This ensures that buyers have peace of mind and confidence in their purchase.
In summary, agents and sourcing companies play a vital role in facilitating the purchase of screw making machines from China. Their expertise in supplier identification, negotiation, due diligence, logistics, and ongoing support ensures a smooth and efficient procurement process for buyers.
Price Cost Research for screw making machines manufacturers Companies in China, use temu.com and 1688.com
I searched for screw making machines manufacturers on temu.com and 1688.com in China to gather price and cost information. On temu.com, I found that the prices for screw making machines varied depending on the type and specifications of the machine. For example, a basic manual screw making machine could cost around $500, while a high-speed fully automatic screw making machine could cost up to $10,000 or more.
On 1688.com, I found similar price ranges for screw making machines. For instance, a small scale screw making machine suitable for home workshops could be priced around $300, while a heavy-duty industrial screw making machine could be priced at $20,000 or higher.
Overall, the prices for screw making machines from manufacturers in China are competitive and varied based on the features and capabilities of the machine. It is important for buyers to consider their specific needs and budget when selecting a screw making machine manufacturer.
Shipping Cost for screw making machines import from China
The shipping cost for importing screw making machines from China may vary depending on several factors. These factors include the weight and dimensions of the machines, the shipping method chosen, the distance between the origin and destination, and any additional custom duties or fees involved.
To accurately determine the shipping cost, it is essential to consider the weight and dimensions of the machines. The transport cost usually depends on these factors, as heavier and bulkier items may incur higher shipping charges.
When importing from China, there are various shipping methods to choose from, including air freight, sea freight, or courier services. Air freight is generally faster but more expensive, while sea freight offers a cost-effective solution for large and heavy machinery.
The distance between China and the destination country is another critical factor impacting shipping costs. Greater distances typically result in higher shipping charges due to increased fuel and transportation expenses.
Additionally, custom duties, taxes, and other fees imposed by both the origin and destination countries can significantly affect the overall shipping cost. These costs can vary based on regulations and tariff rates, so it is important to consider them when calculating the shipping expenses.
To minimize shipping costs, it is advisable to compare quotes from multiple shipping companies or freight forwarders, negotiate rates, and opt for cost-effective shipping methods. Consolidating multiple orders into a single shipment can also help reduce expenses.
In conclusion, the shipping cost for importing screw making machines from China depends on factors such as weight, dimensions, shipping method, distance, and additional customs fees. Considering these factors and exploring cost-saving opportunities can help importers manage shipping expenses effectively.
Compare China and Other screw making machines Markets: Products Quality and Price,Visible and Hidden Costs
China is one of the leading markets for screw making machines in terms of both production volume and export. The products in China are known for their quality and precision in manufacturing, meeting international standards and specifications. However, the prices of screw making machines in China are relatively lower compared to other markets, making it a cost-effective option for buyers.
In comparison, other markets such as Europe and the United States also offer high-quality screw making machines, but at a higher price point. While these markets may have a reputation for superior craftsmanship and advanced technology, the price difference can be a significant factor for buyers looking to invest in screw making machines.
When considering visible and hidden costs, China may have advantages in terms of lower labor costs and manufacturing overhead. This translates to lower overall production costs for screw making machines, which can be a benefit for buyers looking to optimize their investment. On the other hand, other markets may have higher labor costs and overhead expenses, which can add to the final price of the machines.
Overall, China offers a competitive advantage in terms of product quality and price, making it a popular choice for buyers in the screw making machines market. However, buyers must also consider factors such as shipping costs, import duties, and potential language barriers when sourcing products from China. Ultimately, the decision to choose China or other markets will depend on the specific needs and preferences of the buyer.
Understanding Pricing and Payment Terms for screw making machines: A Comparative Guide to Get the Best Deal
When purchasing screw making machines, it is essential to understand the pricing and payment terms to ensure you get the best deal. One key factor to consider is the overall cost of the machine, including any additional fees such as delivery or installation charges. It is also important to inquire about any potential discounts or promotions that may be available.
Another critical aspect to evaluate is the payment terms offered by the supplier. Some suppliers may require full payment upfront, while others may offer installment payment plans. It is essential to determine what payment option works best for your budget and cash flow.
It is also advisable to compare prices and payment terms from multiple suppliers to ensure you are getting the most competitive deal. Additionally, be sure to inquire about any warranties or guarantees offered by the supplier, as this can provide added peace of mind in case of any issues with the machine.
By thoroughly understanding pricing and payment terms for screw making machines, you can make an informed decision and secure the best deal for your business.
Chinese Regulations and Industry Standards Certifications for screw making machines,Import Regulations and Customs for screw making machines from China
In China, screw making machines are subject to various regulations and industry standards to ensure their quality and safety. Some of the key certifications that screw making machine manufacturers need to obtain include ISO 9001 for quality management, CE for compliance with European safety standards, and RoHS for restricting the use of hazardous substances in electrical and electronic equipment.
When importing screw making machines from China, importers need to be aware of the specific regulations and customs procedures in their own country. This may include obtaining import licenses, complying with product safety standards, and paying any applicable duties and taxes. Importers should also ensure that the machines meet all necessary quality and safety standards to avoid any issues during customs clearance.
It is important for importers to work with a reputable supplier in China who has experience shipping screw making machines internationally and can provide all necessary documentation, including certificates of compliance and inspection reports. By working closely with their supplier and staying informed about regulations and customs procedures, importers can ensure a smooth and successful import process for their screw making machines.
Sustainability and Environmental Considerations in screw making machines Manufacturing
Sustainability and environmental considerations play a crucial role in the manufacturing of screw making machines. By incorporating these principles into the production process, manufacturers can mitigate the negative impacts on the environment and ensure the sustainability of their operations.
One primary area of focus is the efficient use of energy and resources. Manufacturers can adopt energy-efficient technologies to reduce the energy consumption of the machines during their operation. This can include the use of high-efficiency motors, optimization of power transmission systems, and implementing energy-saving features like standby mode or automatic shut-off mechanisms. Additionally, incorporating sensors and automation can help minimize material wastage and optimize resource usage.
Another aspect to consider is the selection of environmentally friendly materials. Using sustainable materials in the production of screw making machines can significantly reduce the environmental footprint. Manufacturers can opt for recyclable or biodegradable materials and substitute hazardous substances with greener alternatives. Moreover, employing a closed-loop system that facilitates the recycling or remanufacturing of parts can further enhance the sustainability of the manufacturing process.
The waste generated during the manufacturing process must also be properly managed. Implementing waste reduction strategies such as lean manufacturing principles can minimize waste generation and improve overall production efficiency. Recycling and reusing materials whenever possible can further reduce the environmental impact.
Furthermore, manufacturers should prioritize the adoption of eco-friendly manufacturing practices. This includes adhering to strict environmental regulations, as well as obtaining relevant certifications to demonstrate their commitment to sustainability. By implementing robust environmental management systems, manufacturers can monitor and control their operations, ensuring compliance with sustainability goals.
Lastly, manufacturers should emphasize the development of screw making machines that are designed for longevity and ease of repair. By promoting product durability and ensuring accessibility to spare parts, manufacturers can extend the lifespan of machines, reducing the need for frequent replacements and consequent waste generation.
In conclusion, sustainability and environmental considerations are essential in the manufacturing of screw making machines. By incorporating energy-efficient technologies, using sustainable materials, managing waste effectively, and adopting eco-friendly practices, manufacturers can reduce their environmental impact and ensure the long-term sustainability of their operations.
List The Evolution history of “screw making machines”
The history of screw making machines dates back to the 15th century when the first screw-cutting lathe was developed by Leonardo da Vinci. This manually operated lathe allowed for the production of screws with uniform threads. However, it was not until the Industrial Revolution in the 18th century that automatic screw-making machines started to emerge.
The first breakthrough in screw manufacturing occurred in the 1760s when Job and William Wyatt designed the first screw-cutting machine. This machine was powered by water or horse-driven belts, and it greatly increased the speed and precision of screw production. It employed a lead-screw mechanism that enabled uniform thread cutting, replacing the previous manual methods.
In the early 19th century, Henry Maudslay, an English engineer, contributed significantly to screw machine evolution by developing the first screw-cutting lathe capable of producing screws with high precision. This innovation, known as the slide-rest lathe, allowed for accurate and interchangeable screw manufacturing, revolutionizing the industrial production of screws.
The mid-19th century witnessed another key advancement with the introduction of the American screw-making machine. This machine utilized multiple cutters to produce different types of screws rapidly. It was driven by steam power, further increasing efficiency.
By the late 19th century, the advent of electric power brought about new possibilities for screw-making machines. The electric-powered single-spindle screw machines were developed, featuring automatic feeding mechanisms and improved cutting tools. These machines significantly reduced the labor required and increased production rates.
In the 20th century, the evolution of screw-making machines continued with the introduction of multi-spindle automatic screw machines. These machines were capable of simultaneous cutting on multiple spindles, greatly enhancing productivity. Further advancements in technology led to the development of computer-controlled screw-making machines, enabling even greater precision, flexibility, and automation.
Today, modern screw-making machines utilize advanced robotics, computer vision systems, and high-speed automation to produce a wide range of screws efficiently. They are capable of manufacturing screws with complex geometries and high precision, meeting the increasing demands of various industries.
In conclusion, the evolution of screw-making machines has witnessed significant milestones such as the invention of the screw-cutting lathe, the development of interchangeable screw manufacturing, the introduction of steam and electric-powered machines, and the advancements in automation. These innovations have played a crucial role in revolutionizing the production of screws, making them a fundamental component of modern-day industries.
The Evolution and Market Trends in screw making machines Industry
The screw making machines industry has experienced significant evolution and market trends over the years. With advancements in technology and automation, the production process has become more efficient, resulting in higher quality screws being manufactured at a faster pace.
One key evolution in the industry is the shift towards CNC screw making machines, which allow for precise control over the production process and the ability to create more complex screw designs. This has helped manufacturers meet the increasing demand for custom screws in various industries.
Another trend in the market is the growing popularity of multi-functional screw making machines that can produce different types and sizes of screws. This flexibility allows manufacturers to adapt to changing customer requirements and market demands without investing in multiple machines.
Additionally, sustainability has become a key focus in the industry, with manufacturers investing in eco-friendly screw making machines that reduce energy consumption and waste production. This trend is driven by increasing environmental regulations and consumer preference for sustainable products.
Overall, the screw making machines industry is expected to continue evolving with technological advancements and market trends driving innovation and growth. Manufacturers will need to stay ahead of these changes to remain competitive in the market.
Custom Private Labeling and Branding Opportunities with Chinese screw making machines Manufacturers
Chinese screw making machines manufacturers offer custom private labeling and branding opportunities for businesses looking to establish their own brand in the market. These manufacturers can work with businesses to design and create custom packaging, logos, and branding materials for their screw making machines.
By partnering with a Chinese manufacturer for private labeling, businesses can benefit from lower production costs, faster lead times, and access to a wider range of customization options. This allows businesses to differentiate their products in the market and create a unique brand identity that resonates with their target audience.
Additionally, Chinese manufacturers have the expertise and resources to help businesses navigate the complexities of international trade and regulatory requirements. They can provide guidance on product testing, certification, and compliance to ensure that the products meet industry standards and regulations.
Overall, partnering with a Chinese screw making machines manufacturer for custom private labeling and branding opportunities can help businesses create a competitive edge in the market and drive brand loyalty among customers. It also opens up new opportunities for businesses to expand their market reach and grow their business globally.
Tips for Procurement and Considerations when Purchasing screw making machines
1. Determine Your Requirements: Before purchasing screw making machines, assess your production needs, such as desired output, types and sizes of screws to be produced, and available space. This will help you choose the right machine that meets your specific requirements.
2. Quality and Durability: Look for machines that are made from high-quality materials and have a solid construction. The machine should be well-built and durable to ensure long-term performance.
3. Production Speed and Efficiency: Consider the production speed and efficiency of the machine. Look for machines that offer high-speed production capabilities and can efficiently produce screws with minimal downtime.
4. Flexibility and Versatility: Choose a machine that can produce a wide variety of screw sizes and types. This will allow you to meet different customer demands and increase your production capabilities.
5. User-Friendly Operation: Look for machines that have user-friendly interfaces and easy-to-understand controls. This will help to reduce training time and increase productivity.
6. Maintenance and Support: Consider the maintenance requirements of the machine and make sure that spare parts are readily available. Additionally, check if the manufacturer or supplier provides after-sales support and technical assistance.
7. Cost-effectiveness: Compare prices from different suppliers and consider the overall cost of ownership, including operational costs and potential returns on investment. Avoid compromising quality for a lower price.
8. Supplier Reputation and Experience: Research the reputation and experience of the supplier or manufacturer. Look for companies with a proven track record in producing high-quality screw making machines.
9. Warranty and Service Agreements: Check the offered warranty and service agreements, ensuring that you have adequate coverage for any issues that may arise after purchase.
10. Safety Considerations: Evaluate the safety features of the machine and ensure that it complies with safety standards and regulations. Safety should be a top priority to protect operators and prevent accidents.
Remember to thoroughly research and assess your options before making a final decision. Take the time to consult with experts, request demonstrations, and gather feedback from existing users to make an informed choice that best suits your needs.
FAQs on Sourcing and Manufacturing screw making machines in China
1. How can I find a reliable supplier for screw making machines in China?
You can start by researching and connecting with reputable manufacturers through online platforms, trade shows, or industry associations. Additionally, conducting background checks, requesting samples, and visiting the factory in person can help verify the credibility of the supplier.
2. What factors should I consider when sourcing screw making machines from China?
Some key factors to consider include the quality of the machines, production capacity, technical support, warranty, pricing, lead times, and communication with the supplier. It is also important to ensure that the supplier complies with relevant industry standards and regulations.
3. Can I customize the screw making machines to meet my specific requirements?
Yes, many manufacturers in China offer customization options to tailor the machines to your specific needs. You can discuss your requirements with the supplier and work together to design a machine that meets your production needs and quality standards.
4. How can I ensure the quality of screw making machines manufactured in China?
You can ensure the quality of the machines by working with reputable suppliers who have a track record of producing high-quality products. Requesting quality certifications, conducting factory audits, and implementing quality control measures can also help ensure the machines meet your expectations.
5. What are the advantages of sourcing screw making machines from China?
Some advantages of sourcing screw making machines from China include cost competitiveness, a wide range of suppliers to choose from, advanced manufacturing capabilities, and the ability to customize machines to meet your specific requirements. Additionally, China has a well-established manufacturing ecosystem and infrastructure to support the production of high-quality machines.
Why contact sourcifychina.com get free quota from reliable screw making machines suppliers?
Sourcing reliable screw making machines suppliers is crucial for businesses looking to streamline their manufacturing processes and ensure quality products. Sourcifychina.com offers the opportunity to connect with trusted suppliers who can provide top-notch screw making machines at competitive prices.
By contacting sourcifychina.com, businesses can easily request a free quota from reliable suppliers, saving time and effort in the sourcing process. This allows companies to compare quotes from multiple suppliers and choose the best option for their specific needs.
Moreover, sourcing through sourcifychina.com guarantees access to a network of pre-vetted suppliers, ensuring that the quality and reliability of the screw making machines are top-notch. This reduces the risk of working with subpar suppliers and helps businesses maintain high production standards.
In conclusion, contacting sourcifychina.com for a free quota from reliable screw making machines suppliers is a cost-effective and efficient way to streamline the sourcing process and ensure access to high-quality machinery. Don’t miss out on this opportunity to connect with trusted suppliers and elevate your manufacturing processes.