Analysis of Manufacturing Expenses for surface treatment cost
Surface treatment is an essential manufacturing process that not only enhances the aesthetics of a product but also adds a layer of protection against corrosion, wear and tear, and other chemical reactions. The cost of surface treatment can vary depending on several factors such as the type of surface treatment required, the size and shape of the product, and the material used. However, some common expenses associated with surface treatment are outlined below.
1. Labor costs: Surface treatment is a labor-intensive process that involves skilled workers who are responsible for prepping the surface, applying the treatment, and ensuring quality control. The cost of labor can vary depending on the complexity of the process and the location of the manufacturing facility.
2. Material costs: The cost of the surface treatment material itself can vary depending on the type of coating used. For instance, a simple powder-coating process may cost less than an anodizing process that requires a more specialized material.
3. Equipment and facility costs: The cost of surface treatment equipment and facilities can also be a significant expense. Some processes may require specialized equipment such as a sandblasting machine or a plating tank, which can significantly increase capital costs.
4. Regulatory compliance costs: Surface treatment processes must comply with environmental regulations, which can add to the cost. For example, the disposal of hazardous waste generated during the surface treatment process can be costly.
In conclusion, surface treatment is an essential manufacturing process that involves several costs such as labor, materials, equipment and facility, and regulatory compliance. The cost of surface treatment can vary depending on the type of coating used, the size and shape of the product, and the material used. By understanding these expenses, manufacturers can better manage their resources and optimize their manufacturing processes to reduce costs.
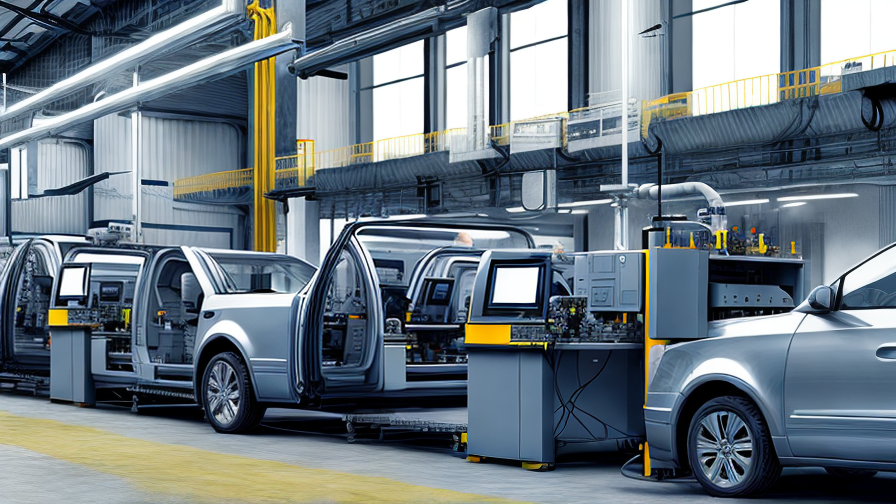
Understanding the Components that Contribute to the Price of surface treatment cost
Surface treatment cost can vary based on several components that contribute to the overall price. These components include material cost, labor cost, equipment cost, overhead cost, and quality assurance cost.
Material cost, which includes the cost of the coating material, is a vital component of surface treatment cost. The type, quality, and quantity of the coating material used are factors that influence the overall cost of surface treatment.
Labor cost is also a significant component that contributes to surface treatment cost. The labor cost includes the wages paid to the personnel responsible for performing surface treatment procedures. The cost is generally determined by the workers’ proficiency, skill level, and experience.
Equipment cost includes the expenses incurred in the purchase, maintenance, and repair of the equipment used for surface treatment. This includes the cost of the machinery, tools, and other materials needed for the surface treatment process.
Overhead cost is another factor that contributes to surface treatment cost. This type of cost includes the expense associated with running the business, which may include rent, utilities, taxes, insurance, and other administrative costs.
Quality assurance costs must also be taken into consideration when assessing surface treatment cost. This includes the cost of conducting quality tests throughout the surface treatment process, to ensure the surface meets the expected standards and customer requirements.
In conclusion, surface treatment cost comprises several factors such as material cost, labor cost, equipment cost, overhead cost, and quality assurance cost. Each component must be considered when calculating the total price of surface treatment, ensuring that the process remains cost-effective and offers an excellent value for money.
Comparing the Wholesale and Retail Prices of surface treatment cost in China
In China, surface treatment cost can vary greatly depending on whether it is being sold wholesale or retail. Wholesale prices are typically lower than retail prices because they are sold in larger quantities to businesses that then sell the product to customers. Retail prices are higher because they are sold directly to consumers.
The wholesale price of surface treatment in China is typically determined by the amount of product being purchased, as well as the quality and type of surface treatment. Production costs and economies of scale also play a role in determining wholesale prices. Wholesale prices are often negotiated between suppliers and buyers, with the latter seeking the best deal possible based on their individual needs and circumstances.
On the other hand, retail prices typically reflect the final cost of the product to the end consumer. Retail prices are influenced by a number of factors, including production costs, marketing expenses, and retail overheads. Retail prices are often set by the seller based on their perceived value of the product, as well as the competition in the market.
Overall, the difference between wholesale and retail price for surface treatment in China can be significant. While wholesale prices are generally lower due to bulk purchasing and negotiation, retail prices can be significantly more expensive due to additional costs associated with marketing and sales. As a result, businesses and consumers often seek to balance quality, price, and convenience when making purchasing decisions.

Understanding Shipping and Logistics for surface treatment cost from China
Shipping and logistics are an essential aspect of any business that deals with the import and export of goods. When it comes to surface treatment cost from China, businesses must consider the logistics involved in transporting the products to their final destination.
The cost of surface treatment from China typically includes various processes such as polishing, coating, and electroplating. These processes are critical in enhancing the durability, functionality, and aesthetic appeal of the products. However, the transportation of these products requires careful planning and coordination.
In China, businesses can choose from various shipping options such as sea freight, air freight, and rail freight. Sea freight is the most popular option for businesses that require larger quantities of products transported over a longer distance. Air freight is the fastest and most efficient option for shipping smaller quantities of products over a shorter distance. Rail freight may be used for intercontinental transportation, border-crossing transportation or to reach landlocked countries.
The cost of shipping and logistics for surface treatment from China varies depending on the mode of transport, the distance traveled, the weight and size of the products, and the desired delivery time. It requires careful planning and communication with the shipping provider to ensure that the products are delivered on time and in good condition while also keeping costs under control.
Overall, businesses must understand the different shipping and logistics options available in order to make informed decisions when it comes to surface treatment cost from China. With careful planning and coordination, businesses can effectively manage their shipping and logistics requirements to ensure timely and cost-effective delivery of products.
Potential Tariffs or Import Taxes on surface treatment cost Purchased from China
Due to the ongoing trade tensions between the US and China, there is a possibility of tariffs or import taxes being imposed on surface treatment costs purchased from China. Surface treatment is vast and includes a range of services like anodizing, electroplating, passivation, and coating. These treatments are commonly used in manufacturing and construction industries, and many businesses in the US rely on Chinese suppliers for these services.
If tariffs or import taxes are imposed on these surface treatment costs, the prices of these services are likely to increase. This would hit small and medium-sized businesses in the US hard, as they would struggle to compete with larger corporations that have internal surface treatment facilities. Suppliers in China may also struggle to retain their customers in the US, as the tariff costs would be passed on to the buyers.
Moreover, given the complexity and variety of surface treatment services, it will be difficult for US businesses to find alternative suppliers in other countries. The search for new suppliers or in-house facilities would lead to spending more time, as well as a lot of resources and money.
In conclusion, if tariffs or import taxes are imposed on surface treatment costs purchased from China, it is likely to impact the manufacturing and construction industries in the US significantly. The imposition of tariffs could result in decreased demand for these services, increased costs for businesses, and loss of customers for Chinese suppliers.

Impact of Market Demand and Competitive Environment on surface treatment cost
Market demand and competitive environment have a significant impact on the surface treatment cost. The surface treatment process involves various chemical and mechanical processes used to enhance the surface properties of materials, such as corrosion resistance, wear resistance, and adhesion properties.
The demand for surface treatment services is directly proportional to the demand for the end products and applications that require surface treatment. For example, the automotive and aerospace industries are significant consumers of surface treatment services due to the high corrosion and wear resistance requirements of their products. Therefore, the demand for surface treatment services from these industries is expected to be higher than other industries such as the construction industry.
The competitive environment also affects the surface treatment cost as the presence of many competitors in the market leads to intense price competition. Companies that offer surface treatment services need to ensure that their prices are competitive enough, while maintaining the quality of their services. This competitive pressure may result in the implementation of cost-cutting measures by companies such as sourcing raw materials at lower prices, implementing process improvements to reduce wastage, and investing in technologies that offer cost-effective methods.
Moreover, the cost of surface treatment services is also influenced by the availability of raw materials and the costs associated with manufacturing and handling these materials. Companies that require expensive or rare raw materials to provide high-quality surface treatment services may face higher costs than those that use commonly available materials.
In conclusion, market demand and competitive environment significantly impact the surface treatment cost. Surface treatment service providers can reduce costs by using cost-effective materials, adopting process improvements, and realizing economies of scale. At the same time, companies need to ensure that their prices remain competitive enough to attract and retain customers in the market.
FAQ about surface treatment cost with multiple answers
Q: What factors influence the cost of surface treatment?
A: The cost of surface treatment depends on various factors:
• Type of treatment: Different types of surface treatments like powder coating, anodizing, plating, and painting have varying costs.
• Material: The cost of the material being treated will affect the overall cost of surface treatment.
• Surface condition: The surface condition may require pre-treatment procedures such as sandblasting, chemical treatment, or metal finishing, which will affect the price.
• Quantity: The number of items being treated influences the overall cost. Large-scale projects typically receive discounts, while small-scale ones may result in higher prices.
• Labor: The cost of professional labor may also affect the total cost of surface treatment.
Q: How much does powder coating cost?
A: The cost of powder coating varies depending on the size and complexity of the job. Typically, the cost of powder coating ranges from $40 to $150 for a small to medium-sized object (like a bike frame). Large-scale projects like car parts or industrial equipment may cost between $500-$1,500.
Q: Is anodizing more expensive than powder coating?
A: The cost of anodizing is typically higher than powder coating, especially when dealing with small projects. Anodizing involves coating the surface using an electrochemical process. The higher cost is due to the complexity of the process, as well as the higher durability of the finished product.
Q: Does plating cost more than anodizing?
A: Plating can be more expensive than anodizing. Plating involves using a metallic coating on the object, which adds to the cost of surface treatment. Additionally, plating requires more elaborate preparation, making it more time-consuming than anodizing.
Q: Is painting cheaper than powder coating?
A: Paint is typically cheaper than powder coating, and the difference can range from $10-$40 per item. However, powder coating provides better protection against the elements, is more durable, and lasts longer than paint.