Introduce about types of welding machines guide,Qulity,Cost,Supplier,Certification,Market,Tips,FAQ
Types of welding machines guide:
Welding machines come in various types, each catering to different welding needs. The four most common types are MIG (Metal Inert Gas), TIG (Tungsten Inert Gas), Stick (Shielded Metal Arc), and Flux-Cored welding machines. MIG machines are versatile and suitable for beginners, while TIG machines offer precise and clean welds. Stick machines are ideal for heavy-duty applications, and Flux-Cored machines are excellent for outdoor welding.
Quality and Cost:
The quality of welding machines can vary depending on the brand and specifications. Higher-quality machines often offer advanced features and better durability, but they come at a higher price. It is essential to consider your welding needs and budget when choosing a machine.
Supplier and Certification:
There are numerous suppliers of welding machines, both online and in physical stores. It is crucial to choose a reputable supplier that offers reliable machines and after-sales support. Additionally, certifications such as ISO 9001 ensures that the supplier maintains quality standards.
Market and Tips:
The welding machine market is highly competitive. It is advisable to research different brands and compare prices before making a purchase. Reading customer reviews and seeking recommendations from experienced welders can also provide valuable insights. Furthermore, it is essential to ensure the machine’s compatibility with your power source and welding materials.
FAQ:
Some frequently asked questions about welding machines include:
1. How do I choose the right welding machine for my needs?
2. What type of power source is required for a welding machine?
3. Can I weld different materials with the same machine?
4. Are welding machines suitable for beginners?
5. What safety precautions should I take when using a welding machine?
In conclusion, selecting the right welding machine involves understanding the different types available, considering the quality and cost, choosing a reliable supplier, and seeking relevant certifications. Research, market analysis, and gathering expert advice can assist in making an informed decision. Additionally, ensuring safety measures and following guidelines are essential for efficient and safe welding.
Types of types of welding machines
There are several types of welding machines available, each designed for specific welding processes and applications. Some common types of welding machines include:
1. Arc Welders: This type of welding machine uses a direct current (DC) or alternating current (AC) power supply to generate an electric arc between an electrode and the workpiece. Arc welders can be further classified into different subtypes depending on the type of electrode used, such as Shielded Metal Arc Welding (SMAW) machines, Flux-Cored Arc Welding (FCAW) machines, and Gas Metal Arc Welding (GMAW/MIG) machines.
2. Resistance Welders: These machines utilize electric currents and pressure to join metals. Spot welding machines are commonly used in automotive and manufacturing industries to fuse thin metal sheets together through the application of heat generated by electrical resistance.
3. TIG Welders: Tungsten Inert Gas (TIG) welders are used for precise and high-quality welding. They employ a non-consumable tungsten electrode to produce the weld, while protecting the area with an inert gas such as argon or helium. TIG welders are ideal for thin materials or when welding metals like stainless steel or aluminum.
4. MIG Welders: Metal Inert Gas (MIG) welders are versatile and widely used in various industries. They utilize a consumable wire electrode and a shielding gas, typically a mixture of argon and carbon dioxide, to create the weld. MIG welding machines are known for their ease of use and high welding speed, making them suitable for both professional and hobbyist welders.
5. Plasma Welders: Plasma welding machines are capable of producing high-quality and precise welds. They use a focused plasma arc generated by passing gas through a small nozzle, along with an electrical arc, to join metals. Plasma welding is commonly used in aerospace and automotive industries.
6. Laser Welders: Laser welding machines produce high-energy laser beams to melt and fuse metals together. They offer exceptional precision and control, making them ideal for delicate applications in electronics, medical devices, and jewelry manufacturing.
These are just a few examples of welding machines available in the market. Each type has its unique advantages, limitations, and suitable applications. Welders can select the appropriate machine based on the material to be welded, the desired welding process, and the necessary precision and speed for the specific job.
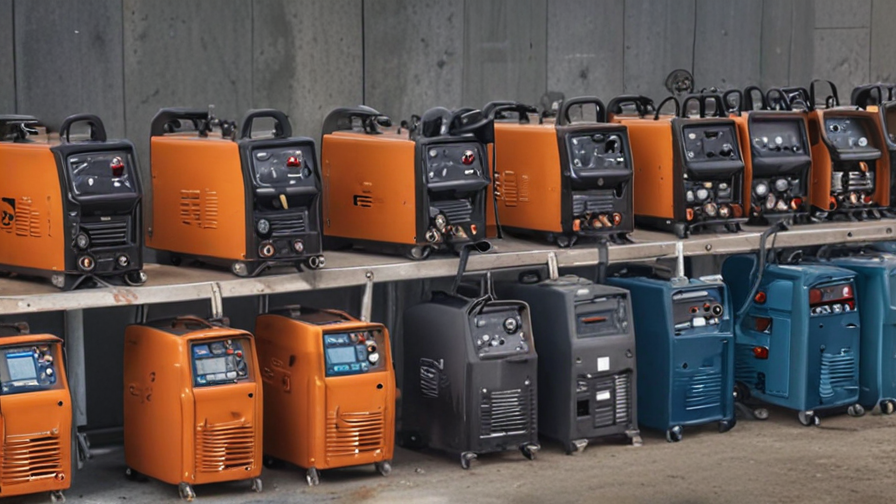
Pros and Cons of Using types of welding machines
Welding machines play a crucial role in joining different metals together. There are several types of welding machines available, each with its own pros and cons. Here is a brief analysis of three popular types:
1. Shielded Metal Arc Welding (SMAW):
Pros: SMAW machines are versatile and can be used to weld various types of metals and alloys. They are portable and do not require an external shielding gas, making them suitable for outdoor or remote job sites. SMAW is relatively easy to learn, making it a popular choice for beginners. Additionally, the equipment is affordable and widely available.
Cons: SMAW produces a lot of smoke and fumes, requiring proper ventilation and personal protective equipment. The process is relatively slow and can result in lower productivity compared to other welding methods. It also produces more spatter, resulting in increased cleanup time. SMAW may not be suitable for welding thin materials due to the risk of warping or burn-through.
2. Gas Metal Arc Welding (GMAW/MIG):
Pros: GMAW provides high welding speeds and can be used on a wide range of materials and thicknesses. It offers good control and produces clean welds with minimal spatter, reducing post-weld cleanup. GMAW is semi-automated or fully automated, making it suitable for high-volume production environments. The process is relatively easy to learn and can be used in various positions.
Cons: GMAW requires a shielding gas, which adds to the cost and makes the equipment less portable. It may not be suitable for outdoor use or in areas with wind circulation. GMAW machines can be more expensive compared to SMAW machines, and they require regular maintenance. Additionally, the process produces a bright arc, making it difficult to see the weld pool clearly.
3. Tungsten Inert Gas Welding (GTAW/TIG):
Pros: TIG offers excellent control and precision, making it suitable for intricate and critical welds. It produces high-quality, clean welds with low distortion and minimal spatter. TIG can be used on various metals, including thin materials and nonferrous alloys, such as aluminum. The process allows for welding in all positions, and the equipment offers features like foot pedal controls for precise heat management.
Cons: TIG welding is relatively slow and requires a high level of skill and experience to master. It is not suitable for high-volume production due to its slower welding speed. TIG machines are more expensive compared to other types of welding machines, and they require a clean and contaminant-free work environment. The process also requires the use of both hands for proper electrode manipulation, limiting the welder’s mobility.
Overall, the choice of welding machine depends on the specific application’s requirements, budget, skill level of the operator, and the desired quality of the welds.
types of welding machines Reference Specifications (varies for different product)
There are various types of welding machines, each designed to perform specific welding tasks. Here are some commonly used welding machines along with their reference specifications:
1. Arc Welding Machines: These machines use an electric current to create an arc between the welding electrode and the base material. The most common types of arc welding machines include:
– Shielded Metal Arc Welding (SMAW) Machines: Suitable for welding thick materials and can operate on both AC and DC currents. Reference specifications may include voltage range, current range, duty cycle, and electrode diameter compatibility.
– Gas Metal Arc Welding (GMAW) Machines: Ideal for welding thin to medium thickness materials. Reference specifications may include wire feed speed, voltage range, current range, and shielding gas compatibility.
2. Gas Tungsten Arc Welding (GTAW) Machines: Also known as Tungsten Inert Gas (TIG) welding machines, they use a non-consumable tungsten electrode to create an arc for welding. Reference specifications may include AC/DC power capability, current range, gas flow rate, and maximum electrode diameter.
3. Resistance Spot Welding Machines: These machines create welds by pressing two or more metal parts together and passing an electric current through them. Reference specifications may include welding current range, electrode force, electrode material, and welding time.
4. Laser Welding Machines: They use a high-powered laser beam to melt and join materials. Reference specifications may include laser power, welding speed, beam diameter, and focal length.
5. Plasma Arc Welding Machines: These machines use a concentrated plasma beam to create a high-temperature arc for welding. Reference specifications may include power supply capacity, gas flow rates, electrode diameter, and torch design.
6. Submerged Arc Welding Machines: They use a continuous wire electrode and a granular flux to create a weld. Reference specifications may include current type (AC/DC), current range, electrode diameter, and welding speed.
7. Electron Beam Welding Machines: They use a beam of high-velocity electrons to join materials. Reference specifications may include beam power, beam current, chamber size, and vacuum level.
Please note that the reference specifications mentioned may vary depending on the specific product and manufacturer. It is essential to consult the manufacturer’s documentation for accurate and up-to-date specifications.
Applications of types of welding machines
There are various types of welding machines available today, each with its own specific applications and advantages. Here are a few examples:
1. MIG Welding Machine: MIG (Metal Inert Gas) welding machines are popular for their versatility and ease of use. They are commonly used in automotive, manufacturing, and construction industries. MIG welding is particularly suitable for welding thin metal sheets and light to medium thickness materials.
2. TIG Welding Machine: TIG (Tungsten Inert Gas) welding machines are known for producing high-quality, precise welds. They are commonly used in aerospace, automotive, and artistic applications. TIG welding is ideal for welding aluminum, stainless steel, and other non-ferrous metals.
3. Stick Welding Machine: Stick welding machines, also known as Shielded Metal Arc Welding (SMAW) machines, are widely used for maintenance and repair work in construction, pipelines, and farming industries. They are durable and work well in outdoor environments or on dirty, rusty materials.
4. Plasma Arc Welding Machine: Plasma arc welding machines are used in specialized applications where high precision and control are required, such as aerospace, nuclear, and chemical industries. They are capable of producing high-quality welds on a variety of materials, including stainless steel, aluminum, and titanium.
5. Resistance Welding Machine: Resistance welding machines are widely used in the automotive and electronics industries. They are fast, efficient, and ideal for joining two or more metal parts together. Spot welding and projection welding are common forms of resistance welding.
6. Laser Welding Machine: Laser welding machines use a focused laser beam to create a highly concentrated heat source for welding. They are used in industries such as electronics, medical devices, and jewelry making. Laser welding offers high precision, excellent control, and minimal distortion.
In conclusion, each type of welding machine has its own unique applications and advantages. MIG, TIG, Stick, Plasma Arc, Resistance, and Laser welding machines are just a few examples of the various options available to cater to different welding needs across multiple industries.
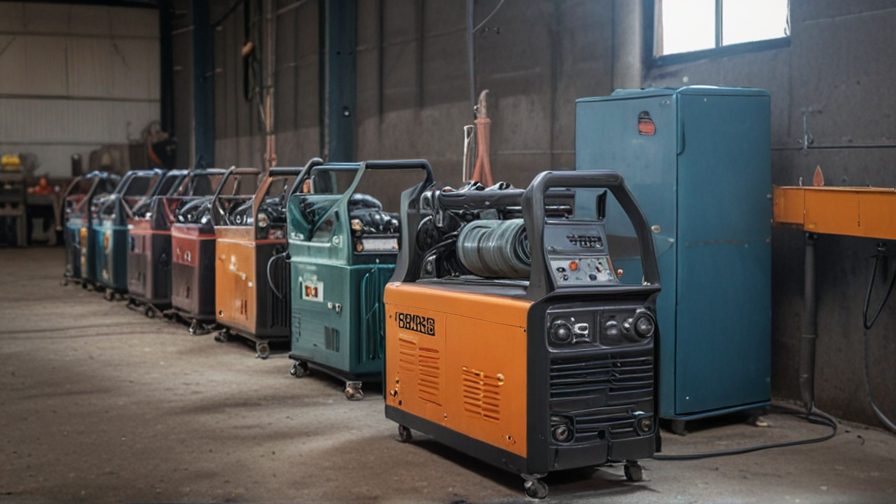
The Work Process and how to use types of welding machines
The work process of welding involves joining two or more pieces of metal together by melting and fusing them with the help of heat and pressure. Different types of welding machines are used for this purpose, each suited for specific applications. Here we will discuss three common types of welding machines and how to use them.
1. MIG Welding Machine:
MIG (Metal Inert Gas) welding machines are widely used for their versatility and ease of use. To use a MIG welding machine, start by preparing the workpiece by cleaning the surface and ensuring it is free from any contaminants. Next, select the appropriate wire and gas for the specific metal being welded. Insert the wire into the machine and secure it properly. Set the appropriate voltage and wire feed speed based on the material thickness. Finally, wear appropriate safety gear and start feeding the wire while directing the electrode towards the joint to create a strong, reliable weld.
2. TIG Welding Machine:
TIG (Tungsten Inert Gas) welding machines are preferred for their precise control and excellent weld quality. Using a TIG welding machine begins with properly cleaning and preparing the workpiece. Select the appropriate tungsten electrode size and grind it to a sharp point. Set the machine to DC or AC current based on the metal being welded. Adjust the gas flow rate and shielding gas depending on the specific application. Strike an arc by touching the tungsten electrode to the workpiece and start feeding the filler material to create a clean, strong weld.
3. Stick Welding Machine:
Stick welding machines, also known as shielded metal arc welding (SMAW) machines, are robust and versatile, making them suitable for various applications. To use a stick welding machine, start by cleaning and preparing the workpiece. Choose the appropriate electrode based on the metal being welded and set the machine’s amperage accordingly. Strike an arc by scratching the electrode on the workpiece’s surface and start making the required weld beads by moving the electrode along the joint. Control the rate of electrode consumption and manipulate the weld puddle for desired results.
In conclusion, understanding the work process and how to use different types of welding machines is essential for successful welding operations. MIG, TIG, and Stick welding machines offer unique advantages and require specific techniques and settings to achieve optimal results. Practice, safety precautions, and knowledge of the characteristics of various metals are crucial for obtaining strong, durable welds.
Quality Testing Methods for types of welding machines and how to control the quality
When it comes to quality testing methods for different types of welding machines, several approaches can be employed to ensure the final product’s excellence. The primary goal is to verify that the machines adhere to performance standards and produce high-quality welds consistently.
One common quality testing method is destructive testing, in which samples from the welded joint are subjected to extreme conditions to determine their strength and integrity. Tensile testing involves pulling the welded sample to measure its maximum load capacity before failure. Bend testing evaluates the sample’s ductility by bending it to certain angles without cracking. Finally, impact testing measures the ability of the welded joint to withstand dynamic loading by striking the sample with a pendulum.
Non-destructive testing (NDT) techniques are also widely used to assess the quality of welding machines. Radiographic testing employs X-rays or gamma rays to inspect welds for internal defects such as cracks and porosity. Ultrasonic testing uses high-frequency sound waves to detect discontinuities in the welded material, providing data on the flaw’s size and location. Magnetic particle testing utilizes magnetic fields to detect surface and near-surface defects like cracks and fractures. Liquid penetrant testing involves applying dyes or fluorescent liquids to the weld surface to reveal any surface-breaking defects, highlighting flaws that may not be visible to the naked eye.
To control the quality of welding machines, various measures can be implemented. Firstly, a comprehensive quality management system (QMS) should be established to define procedures, work instructions, and inspection criteria throughout the manufacturing process. Regular audits and assessments are conducted to ensure compliance with the QMS.
Training and qualification programs for machine operators and welders are crucial to ensure they possess the necessary skills and knowledge. This can include certifications such as the American Welding Society (AWS) certifications.
Furthermore, implementing statistical process control (SPC) techniques allows manufacturers to monitor and control welding processes. This involves collecting real-time data during production, analyzing it, and taking corrective actions if any deviations are detected.
Regular maintenance and calibration of welding machines are essential to sustain their performance and accuracy. Strict adherence to manufacturer guidelines for maintenance schedules and procedures is crucial to ensure the longevity and optimal functioning of the equipment.
In conclusion, achieving high-quality welding machines requires a combination of destructive and non-destructive testing methods. Effective quality control can be achieved through the implementation of a comprehensive QMS, operator training and qualification programs, statistical process control, and regular maintenance and calibration. These measures ensure the production of reliable and durable welding machines that consistently deliver excellent welds.
types of welding machines Sample Policy and Post-Purchase Considerations for types of welding machines from China
When purchasing welding machines from China, it is important to establish a clear sample policy to ensure quality and suitability. The following sample policy and post-purchase considerations can help facilitate a smooth process:
Sample Policy:
1. Request samples: Before making a bulk purchase, request samples of the welding machines from multiple suppliers. This will enable you to evaluate their quality, performance, and features.
2. Specifications: Provide the suppliers with detailed specifications of the welding machines you require, including voltage, power, welding current range, duty cycle, and any other specific requirements.
3. Sample testing: Conduct thorough testing of the samples to ensure they meet your quality standards and are capable of achieving your desired welding results.
4. Certification and standards: Verify that the welding machines comply with relevant international standards such as CE, RoHS, or ISO certifications.
5. Warranty: Inquire about warranties offered by the suppliers. A warranty can provide assurance regarding the product quality and protect against potential defects.
Post-Purchase Considerations:
1. Quality control: Implement a thorough quality control procedure upon receiving the bulk order. Inspect the welding machines for any defects or damages, and test them to ensure they function properly.
2. Documentation: Maintain proper documentation of the purchase, including invoices, packing lists, and shipping documents. This will be useful for future reference or in case of any disputes.
3. Custom duties and import regulations: Familiarize yourself with custom duties and import regulations in your country to avoid any unexpected costs or delays in the shipment.
4. Communication: Establish open channels of communication with the supplier to address any concerns or issues that may arise. Promptly notify them about any defects or damages to seek resolution.
5. Supplier relationship: Building a strong relationship with the supplier can be beneficial for future business. Promptly provide feedback on the purchased welding machines and maintain regular communication for further collaboration.
By implementing a robust sample policy and carefully considering post-purchase factors, you can enhance the overall purchasing experience while ensuring the quality and suitability of welding machines imported from China.
Sourcing types of welding machines from China: Opportunities, Risks, and Key Players
Sourcing welding machines from China can provide significant opportunities for businesses in terms of cost-effectiveness and a wide range of options. However, it also carries certain risks that need to be considered. This article will discuss the opportunities, risks, and key players in the Chinese market for welding machines in a concise manner, within 300 words.
Opportunities:
1. Cost-effectiveness: Chinese manufacturers offer competitive prices, making it an attractive option for businesses looking to save costs on welding machines.
2. Wide range of options: China has numerous manufacturers that produce various types of welding machines, offering businesses a wide range of choices to suit their specific requirements.
3. Technological advancements: Chinese welding machine manufacturers have made significant advancements in terms of technology, providing access to innovative and efficient welding machines.
Risks:
1. Quality control issues: Some Chinese manufacturers may compromise on quality to maintain lower prices, making it crucial for businesses to thoroughly vet suppliers to ensure their products meet required standards.
2. Intellectual property concerns: China has faced concerns related to intellectual property rights infringement in the past, which can pose risks for businesses looking to source welding machines from the country.
3. Language and communication barriers: Language differences and communication challenges can sometimes hinder effective communication with Chinese suppliers, resulting in misunderstandings or delays in product delivery.
Key Players:
1. Lincoln Electric Holdings Inc.: This US-based company has a presence in China and is known for manufacturing various types of welding machines, including arc welding machines and robotic welding systems.
2. ABB Group: A leading global industrial automation company, ABB also operates in China and offers a range of welding machine solutions, focusing on automation and robotics.
3. ESAB Welding & Cutting Products: Known for its cutting-edge welding and cutting equipment, ESAB has a strong presence in China, providing a variety of welding machines for industrial applications.
In conclusion, sourcing welding machines from China presents significant opportunities in terms of cost-effectiveness, a wide range of options, and technological advancements. However, businesses need to be mindful of risks related to quality control, intellectual property, and communication barriers. Key players in the Chinese market for welding machines include Lincoln Electric Holdings Inc., ABB Group, and ESAB Welding & Cutting Products.
How to find and select reliable types of welding machines manufacturers in China,use google search manufacturers and suppliers
When looking to find and select reliable types of welding machine manufacturers in China, one effective way is to use Google search. By utilizing relevant keywords such as “welding machine manufacturers in China” or “reliable welding machine suppliers,” one can easily find a list of potential manufacturers.
To narrow down the options and choose reliable manufacturers, certain criteria can be considered. Firstly, it is important to look for well-established companies with a strong reputation in the industry. This can be determined by checking their website, looking for reviews and testimonials, and verifying their experience and expertise.
Secondly, it is advisable to choose manufacturers that have the necessary certifications and compliance with international standards, such as ISO 9001 or CE certification. This ensures that the welding machines they produce meet the required quality standards.
Furthermore, consider the manufacturers’ production capacity and capabilities. A reliable manufacturer should have a well-equipped factory and the ability to produce welding machines in large quantities without compromising on quality.
Additionally, it is crucial to assess a manufacturer’s customer service and communication. Look for companies that are responsive, prompt, and willing to provide necessary technical support or answer any queries.
To ensure smooth transactions and minimize any potential risks, it is advisable to consider visiting the manufacturer’s premises in person or contacting them directly. Engaging in discussions about product specifications, pricing, warranty, and delivery options can provide better insights and clear any doubts.
It is also advisable to explore multiple manufacturers to compare their offerings, features, and prices. Obtaining quotations from different manufacturers and analyzing their terms and conditions can help make an informed decision.
In summary, finding reliable welding machine manufacturers in China through Google search involves analyzing factors such as reputation, certifications, production capacity, customer service, and direct communication. By taking these factors into account, one can make an informed decision when selecting a manufacturer.
How to check types of welding machines manufacturers website reliable,use google chrome SEOquake check if ranking in top 10M
One way to determine the reliability of a welding machine manufacturer’s website is to use Google Chrome’s SEOquake tool to check its ranking in the top 10 million websites. SEOquake is a browser extension that provides useful metrics and data about a website’s SEO performance. By checking the website’s ranking, you can get an idea of its authority and popularity in the online domain.
To use SEOquake, you need to have Google Chrome installed on your computer. Once installed, open the website of the welding machine manufacturer that you want to evaluate. Then, click on the SEOquake extension icon located in the browser’s toolbar. A pop-up window will appear, displaying various metrics and data related to the website’s SEO performance.
One key metric to pay attention to is the website’s Alexa Rank, which is a measure of its popularity and traffic compared to other websites globally. If the welding machine manufacturer’s website ranks relatively high among the top 10 million websites, it indicates that it is likely more reliable and trustworthy.
It’s important to note that while SEOquake can provide valuable insights into a website’s SEO performance, it should not be the sole factor in determining the reliability of a manufacturer’s website. You should also consider other factors such as user reviews, customer testimonials, industry reputation, and the presence of trust signals like SSL certificates or verified partnerships.
In conclusion, using Google Chrome’s SEOquake tool to check a welding machine manufacturer’s website ranking in the top 10 million can help assess its reliability and authority. However, it should be considered alongside other factors to make a well-informed decision.
Top 10 types of welding machines manufacturers in China with each 160 words introduce products,then use markdown create table compare
There are numerous welding machine manufacturers in China, offering a wide range of products to cater to various industrial needs. Here are the top 10 manufacturers and a brief introduction to their welding machine products:
1. Lincoln Electric: Lincoln Electric produces a range of welding machines, including stick, MIG, TIG, and multi-process welders. They are known for their advanced technology and reliable performance.
2. Miller Electric: Miller Electric offers a comprehensive line of welding machines, including arc and resistance welders, as well as plasma cutters. Their machines are renowned for their precision and versatility.
3. ESAB: ESAB manufactures a wide range of welding machines, such as MIG, TIG, and submerged arc welders. They are known for their innovative designs and high-quality performance.
4. Fronius International: Fronius International produces advanced welding machines, including MIG/MAG, TIG, and robotic welders. Their machines offer excellent energy efficiency and precision welding capabilities.
5. Huaheng Automation: Huaheng Automation specializes in the production of robotic welding machines and equipment. They offer flexible and automated solutions for various welding applications.
6. Kjellberg Finsterwalde: Kjellberg Finsterwalde manufactures plasma cutting and welding machines, along with welding consumables. Their products are renowned for their durability and cutting-edge technology.
7. Riland: Riland produces a range of welding machines, including arc, MIG/MAG, and TIG welders. Their machines are known for their affordability and reliable performance.
8. Jasic Technology: Jasic Technology offers a wide range of welding machines, such as inverter-based arc, MIG/MAG, and TIG welders. They focus on providing high-quality machines at competitive prices.
9. Longevity Welding: Longevity Welding manufactures a variety of welding machines, including stick, MIG, TIG, and plasma cutters. Their machines are designed for durability and offer excellent value for money.
10. Hugong Group: Hugong Group specializes in the production of welding machines, including manual arc, MIG/MAG, and TIG welders. Their machines are known for their reliability and ease of use.
| Manufacturer | Products Offered |
|———————-|————————————————————-|
| Lincoln Electric | Stick, MIG, TIG, and multi-process welders |
| Miller Electric | Arc and resistance welders, plasma cutters |
| ESAB | MIG, TIG, and submerged arc welders |
| Fronius International| MIG/MAG, TIG, and robotic welders |
| Huaheng Automation | Robotic welding machines and equipment |
| Kjellberg Finsterwalde| Plasma cutting and welding machines, welding consumables |
| Riland | Arc, MIG/MAG, and TIG welders |
| Jasic Technology | Inverter-based arc, MIG/MAG, and TIG welders |
| Longevity Welding | Stick, MIG, TIG, and plasma cutters |
| Hugong Group | Manual arc, MIG/MAG, and TIG welders |
In conclusion, China is home to many reliable and innovative welding machine manufacturers, offering a wide range of products to meet various industrial needs. Each manufacturer mentioned above specializes in different types of welding machines, ensuring there is a suitable option available for every welding requirement.
Background Research for types of welding machines manufacturers Companies in China, use qcc.com archive.org importyeti.com
When it comes to welding machines, China has emerged as one of the leading manufacturers and exporters in the world. The country is home to a wide range of welding machine manufacturers, offering various types of machines to cater to different welding needs.
One reliable source for information on Chinese welding machine manufacturers is qcc.com. This online platform provides detailed company profiles, including their product range, production capacity, certifications, and customer reviews. It also allows users to compare different manufacturers based on their capabilities and customer feedback, making it easier to select the most suitable company.
Another useful resource is archive.org, which offers access to archived web pages of Chinese welding machine manufacturers. This platform allows users to explore the company websites as they existed in the past, providing valuable insights into their history, product development, and market presence. It can be helpful in assessing the growth and evolution of a manufacturer over time.
Furthermore, importyeti.com is a powerful tool for tracking import and export data. By using this platform, one can obtain information on the shipment activities of Chinese welding machine manufacturers, including their overseas clients, quantity and value of exports, and ports of entry or exit. This data can give an understanding of a manufacturer’s international reach and market preferences.
In summary, qcc.com, archive.org, and importyeti.com are valuable resources for conducting background research on different types of welding machine manufacturers in China. These platforms provide insights into a manufacturer’s capabilities, history, market presence, customer feedback, and global reach. By utilizing these tools, one can make informed decisions when selecting a welding machine manufacturer in China.
Leveraging Trade Shows and Expos for types of welding machines Sourcing in China
Trade shows and expos can be incredibly valuable resources for sourcing types of welding machines in China. These events provide a platform for manufacturers, suppliers, and industry professionals to showcase their products and connect with potential buyers.
One of the key advantages of trade shows and expos is the opportunity to see a wide range of welding machines from different manufacturers all in one place. This allows buyers to compare and evaluate the quality, features, and pricing of various machines, helping them make informed decisions.
Attending trade shows and expos also provides the chance to interact face-to-face with suppliers and manufacturers. This direct communication allows for better understanding of the product specifications, customization options, and production capabilities. Moreover, it helps build relationships and establish trust with potential suppliers, which is essential for successful sourcing in China.
In addition, trade shows and expos often feature seminars, workshops, and demonstrations by experts in the welding technology industry. These educational sessions can enhance the buyer’s knowledge about the latest advancements, techniques, and trends in welding machines. Such insights empower buyers to make more informed decisions and stay updated with the cutting-edge technologies in the market.
To maximize the benefits of trade shows and expos for sourcing welding machines in China, it is essential to come prepared. Extensive research about the event, including the list of exhibitors, detailed floor plans, and seminar schedules, helps buyers prioritize their time and target specific suppliers. Additionally, having a clear understanding of the requirements and specifications of the desired welding machines enables efficient communication with potential suppliers.
In conclusion, trade shows and expos offer a unique opportunity for sourcing types of welding machines in China. By attending these events, buyers can compare, evaluate, and connect with a wide range of suppliers, gain insights from industry experts, and build long-term relationships. Utilizing these platforms effectively can greatly contribute to successful sourcing endeavors and help businesses find the right welding machines for their needs.
The Role of Agents and Sourcing Companies in Facilitating types of welding machines Purchases from China
Agents and sourcing companies play a crucial role in facilitating the purchase of welding machines from China. Their expertise and knowledge of the Chinese market enable them to effectively manage the entire sourcing process, making it easier and more efficient for buyers.
Firstly, agents and sourcing companies have extensive networks and connections with manufacturers and suppliers in China. They can identify and shortlist the most suitable welding machine manufacturers based on the buyer’s requirements. This saves the buyer considerable time and effort in finding and vetting potential suppliers.
Moreover, agents and sourcing companies are well-versed in negotiating with Chinese manufacturers to obtain the best prices and terms for buyers. They have an in-depth understanding of Chinese business practices and cultural norms, allowing them to navigate negotiations successfully and ensure that buyers get the most value for their money.
Agents and sourcing companies also provide quality control services throughout the production process. They conduct factory inspections, monitor production, and perform quality checks to ensure that the welding machines meet the buyer’s specifications and adhere to international standards. This helps buyers to avoid potential quality issues and guarantees the reliability of the purchased machines.
Furthermore, agents and sourcing companies handle logistical aspects such as transportation, shipping, and customs clearance. They leverage their expertise to optimize the supply chain and ensure smooth delivery of the welding machines to the buyer’s location. This eliminates the complexities and administrative burden associated with international shipping, allowing buyers to focus on their core business.
In summary, agents and sourcing companies streamline the sourcing process by leveraging their networks, negotiating skills, quality control expertise, and logistical knowledge. They play a vital role in facilitating the purchase of welding machines from China, providing buyers with a hassle-free and efficient sourcing experience.
Price Cost Research for types of welding machines manufacturers Companies in China, use temu.com and 1688.com
When it comes to price and cost research for types of welding machines from manufacturers in China, two reliable online platforms to consider are temu.com and 1688.com. These websites provide access to a wide range of manufacturers and suppliers, offering competitive prices and quality products.
Temu.com is a comprehensive B2B platform that connects buyers with verified suppliers in China. It offers a user-friendly interface, making it easy to browse through various categories and find welding machine manufacturers. The platform provides detailed product descriptions, specifications, and often includes pricing information. It also allows users to directly negotiate with suppliers, ensuring transparency and flexibility in discussing price and cost details.
1688.com, operated by Alibaba Group, is a leading wholesale marketplace in China. It offers a vast array of products, including welding machines, at wholesale prices. The platform is primarily in Chinese, but using translation tools can help overcome language barriers. 1688.com provides detailed product listings, supplier profiles, and customer reviews, enabling buyers to assess both the quality and pricing of welding machines offered by different manufacturers.
When conducting price and cost research on these platforms, it is important to keep certain factors in mind. Firstly, compare prices from multiple manufacturers to get a better sense of the average market price for the desired welding machine. Secondly, consider the quality and durability of the product offered by different manufacturers to ensure value for money. Lastly, factor in shipping costs and delivery times to accurately assess the overall cost.
In summary, temu.com and 1688.com are reliable online platforms for conducting price and cost research for welding machine manufacturers in China. These platforms provide a wide variety of options, detailed product descriptions, and often include pricing information. Taking into account factors such as product quality and shipping costs can help buyers make informed decisions while ensuring competitive prices for welding machines.
Shipping Cost for types of welding machines import from China
When importing welding machines from China, it’s essential to consider the shipping costs involved. The shipping cost primarily depends on various factors such as the weight and dimensions of the machines, the shipping method chosen, and the location of the buyer.
For smaller welding machines, air freight is often the preferred shipping method due to its speed. The cost of air freight is calculated based on the weight or volumetric weight (whichever is higher) of the package. Volumetric weight is calculated by multiplying the length, width, and height of the package (in centimeters) and dividing it by a volumetric factor. The rate per kilogram for air freight varies depending on the carrier and the destination country. On average, the air freight cost for smaller welding machines can range from $3 to $6 per kilogram.
For larger and heavier welding machines, sea freight is the most economical shipping option. The cost of sea freight is determined by several factors, including the volume (cubic meters) and weight (in kilograms) of the cargo, the destination port, and the chosen shipping method (FCL or LCL). If the buyer is importing a significant number of machines, opting for a full container load (FCL) is often more cost-effective compared to less than container load (LCL). The average sea freight cost for welding machines ranges from $400 to $1500 per cubic meter, depending on the factors mentioned above.
In addition to the shipping costs, it’s essential to consider other expenses such as customs clearance fees, documentation charges, import duties, and local transportation costs from the port to the buyer’s location. These costs can vary widely depending on the specific destination country and its import regulations.
To accurately determine the shipping cost for importing welding machines from China, it is advisable to consult with freight forwarders or shipping agents who specialize in international trade. They can provide more accurate quotations based on the specific requirements and circumstances of the buyer.
Compare China and Other types of welding machines Markets: Products Quality and Price,Visible and Hidden Costs
In terms of product quality and price, the Chinese welding machine market has made significant advancements in recent years. Chinese manufacturers have made substantial investments in research and development to enhance the quality of their products. This has led to the production of welding machines that meet international standards and rival the quality of machines from other countries.
In terms of price, Chinese welding machines are often more affordable compared to those from other countries. This is primarily because of the lower labor and production costs in China. As a result, Chinese manufacturers are able to offer competitively priced welding machines without compromising on quality.
However, it is important to consider both the visible and hidden costs associated with purchasing Chinese welding machines. While the initial purchase price may be lower, buyers need to be cautious about potential issues such as after-sales service and support. Communication barriers and time zone differences can sometimes make it difficult to resolve any technical problems that may arise.
Additionally, buyers should also be aware of potential hidden costs such as import duties, taxes, and shipping charges when importing welding machines from China. These costs can significantly impact the overall price and should be factored into the decision-making process.
In comparison, other types of welding machine markets, such as those in Europe or the United States, may offer higher quality products but at a higher price. These markets have well-established manufacturers with a long history of producing reliable and durable welding machines. However, buyers should be prepared to pay a premium for these machines.
When considering product quality and price, it is important for buyers to assess their specific needs and budget. For those seeking cost-effective welding machines with acceptable quality, Chinese manufacturers can be a viable option. However, buyers should carefully evaluate all visible and hidden costs associated with purchasing from China to make an informed decision.
Understanding Pricing and Payment Terms for types of welding machines: A Comparative Guide to Get the Best Deal
When purchasing a welding machine, it is important to understand pricing and payment terms to ensure that you get the best deal. This comparative guide will help you navigate through the different options available and make an informed decision.
One of the first factors to consider is the type of welding machine you require. There are various types such as MIG, TIG, stick, and plasma cutters, each with its own pricing range. MIG welding machines are generally considered more economical, whereas TIG welding machines tend to be higher in price due to their precise welding capabilities.
The pricing of welding machines also depends on their power output and features. Machines with higher power outputs are usually priced higher than those with lower outputs. Similarly, machines with advanced features like digital controls, multiple welding processes, and automated settings often come with a higher price tag.
It is essential to compare prices from different suppliers to ensure you get the best deal. Online retailers, local distributors, and manufacturers can offer varying prices, so shopping around is crucial. Additionally, consider if the supplier offers any discounts or promotions that could further reduce the price.
Payment terms can also play a significant role in securing the best deal. Some suppliers offer financing options, allowing you to pay in installments over a designated period. This can be beneficial if you are on a tight budget or prefer to spread out the cost. It is important to understand the interest rates and any additional fees associated with these financing options.
Another payment term to consider is the warranty provided by the supplier. Welding machines are a significant investment, and having a warranty can give you peace of mind. Compare the duration and coverage of warranties offered by different suppliers to ensure you are protected against any potential defects or malfunctions.
Lastly, factor in any additional costs such as shipping, taxes, and accessories when comparing prices. Some suppliers may offer free shipping or include essential accessories like welding helmets or gloves, which can add value to your purchase.
By understanding pricing and payment terms, comparing options, and considering additional costs, you can navigate the market to find the best deal on a welding machine that suits your needs and budget.
Chinese Regulations and Industry Standards Certifications for types of welding machines,Import Regulations and Customs for types of welding machines from China
Chinese Regulations and Industry Standards Certifications for types of welding machines:
In China, the regulations and industry standards for welding machines aim to ensure quality, safety, and compliance with environmental standards. The primary regulatory body responsible for overseeing the welding machine industry is the State Administration for Market Regulation (SAMR). It issues industry standards, certifications, and monitors compliance with relevant regulations. The most relevant standards for welding machines include the GB 15579-2008 and the GB/T 15579-2018.
The GB 15579-2008 standard specifies the general technical requirements for welding and cutting equipment, including welding machines. It covers aspects such as electrical safety, performance parameters, and testing methods. The more recent GB/T 15579-2018 standard further emphasizes safety aspects and introduces additional requirements related to emissions, noise, and environmental protection.
For certification, welding machine manufacturers in China typically obtain the China Compulsory Certification (CCC). This certification is required for specific product categories and ensures compliance with Chinese safety standards. Manufacturers must apply for the CCC and undergo a series of tests and inspections to obtain the certificate. The CCC mark is affixed to certified products before they can be legally sold in the Chinese market.
Import Regulations and Customs for types of welding machines from China:
Importing welding machines from China to other countries requires compliance with local import regulations and customs procedures. Importers should be aware of the following key points:
1. Import Duties and Taxes: Importers need to be aware of the applicable import duties and taxes, which vary based on the destination country. These charges are usually based on the customs value of the imported welding machines.
2. Product Compliance: Importers must ensure that the imported welding machines meet the safety and quality standards of their respective countries. This may involve obtaining relevant certifications, test reports, or conformity assessment documents to demonstrate compliance.
3. Customs Documentation: Importers are required to provide certain customs documents, including a properly filled-out commercial invoice, packing list, bill of lading or airway bill, and any additional documents specific to the destination country. These documents facilitate smooth customs clearance.
4. Customs Entry Process: Importers need to submit the necessary customs declarations and pay any duties or taxes owed. It is essential to have accurate and complete documentation to avoid unnecessary delays or issues during customs clearance.
5. Local Regulations and Certification: Depending on the destination country, imported welding machines may need to comply with specific local regulations and certifications. Importers should familiarize themselves with these requirements to ensure compliance.
It is advisable for importers to work with freight forwarders or customs brokers experienced in importing welding machines to navigate the complexities of customs regulations and ensure a smooth import process.
Sustainability and Environmental Considerations in types of welding machines Manufacturing
When considering sustainability and environmental considerations in the manufacturing of welding machines, it is important to evaluate various aspects of the production process. These include the use of raw materials, energy consumption, waste generation, emissions, and end-of-life disposal.
One significant factor to consider is the use of raw materials. Manufacturers should aim to use sustainable materials, such as recycled metals, in the construction of welding machines. This helps to reduce the demand for virgin resources and decreases the environmental impact associated with mining and extraction processes.
Energy consumption is another crucial aspect to address. Welding machine manufacturers can incorporate energy-efficient technologies in their production processes. This includes using energy-saving components, such as efficient motors and power electronics, as well as optimizing the design to minimize energy losses. Additionally, implementing procedures for equipment shutdown or standby modes when not in use can also aid in reducing energy consumption.
Reducing waste generation is important in promoting sustainability. Manufacturers can minimize waste by implementing effective material handling and storage practices, as well as by optimizing production processes to minimize scrap and rework. Additionally, recycling initiatives should be established to handle waste materials, such as metal scraps and packaging materials, ensuring they are properly treated and reused instead of being disposed of in landfills.
Emissions during the manufacturing process should also be minimized. This can be achieved by utilizing cleaner manufacturing techniques, such as implementing advanced air filtration systems and exhaust controls. Adoption of greener alternatives, such as water-based coatings instead of harmful solvents, can also help reduce emissions and the environmental impact associated with manufacturing operations.
Lastly, considering the end-of-life disposal of welding machines is crucial. Manufacturers should focus on designing products with parts that can be easily disassembled and recycled. Implementing take-back programs or collaborating with recycling facilities can ensure proper disposal and recycling of welding machines at the end of their life cycle, avoiding unnecessary waste and environmental pollution.
In conclusion, sustainability and environmental considerations in the manufacturing of welding machines involve using sustainable materials, minimizing energy consumption, reducing waste generation, controlling emissions, and promoting proper end-of-life disposal. By addressing these aspects, manufacturers can contribute to a more sustainable and environmentally friendly industry.
List The Evolution history of “types of welding machines”
Welding is the process of permanently joining two or more materials together by applying heat and pressure. Over time, various types of welding machines have been developed to meet the needs of different industries and applications. Here is a brief evolution history of welding machines:
1. Forge Welding: The earliest form of welding can be traced back to ancient times when metal pieces were heated in a forge and hammered together to create a bond. This technique involved skilled blacksmiths using manual tools.
2. Arc Welding: In the late 19th century, electric arc welding was introduced. It utilized a power source to create an electric arc between an electrode and the workpiece, melting the metals and allowing them to fuse. Initially, carbon electrodes were used, but advancements led to the development of coated electrodes for better control.
3. Resistance Welding: In the early 20th century, resistance welding machines emerged. This process utilized electric current flowing through the materials being joined to create heat and generate a welded joint. Resistance welding was widely employed in industries such as automotive and aerospace.
4. Gas Welding: Also known as oxy-fuel welding, this technique emerged around the same time as arc welding. It involves combining a fuel gas, such as acetylene, and oxygen to produce a flame with a high temperature that can melt the metals. Gas welding machines allowed for portability and versatility.
5. TIG Welding: Tungsten Inert Gas (TIG) welding was developed during World War II. It involved a non-consumable tungsten electrode that created an arc and was shielded by an inert gas like argon. TIG welding machines provided precise control over the welding process and allowed for welding various metals.
6. MIG Welding: Metal Inert Gas (MIG) welding or Gas Metal Arc Welding (GMAW) was introduced in the 1940s. This technique used a continuously fed wire electrode and a shielding gas to protect the weld pool. MIG welding machines became popular due to their high productivity and ease of use.
7. Laser Welding: In the late 20th century, laser technology revolutionized the welding industry. Laser welding machines utilize a highly concentrated beam of light to generate heat, allowing for precise welding on small and delicate components. This process found applications in electronics, medical devices, and automotive industries.
8. Robotic Welding: As automation advanced, robotic welding systems were developed. These machines use robotic arms to perform welding operations with high accuracy and speed. Robotic welding has enhanced productivity and efficiency in industries like automotive manufacturing.
In conclusion, welding machines have evolved significantly over the years, from manual forge welding to advanced robotic systems. These advancements have improved welding capabilities, efficiency, and opened up new possibilities in various industries.
The Evolution and Market Trends in types of welding machines Industry
The welding machines industry has drastically evolved over the years, with advancements in technology and increasing demand for more efficient and versatile welding equipment. Various factors have influenced the market trends in the industry, such as the growth of industrialization, infrastructure development, and the increasing adoption of automation.
One significant evolution is the shift towards more portable and compact welding machines. Traditional large and bulky machines are being replaced by portable and lightweight models, allowing for greater mobility and convenience. This trend has been driven by the increasing need for on-site welding in industries such as construction, automotive, and oil and gas. Portable welding machines have become a preferred choice for professionals who require flexibility and efficiency.
Another notable trend is the integration of advanced technologies in welding machines. The industry has seen the adoption of automated welding systems, robotic welding machines, and computer numerical control (CNC) systems. These technologies offer improved precision, speed, and productivity in welding processes. Robotic welding machines, in particular, have gained popularity due to their ability to perform complex welds with minimal human intervention. This trend is driven by industries seeking to enhance productivity, reduce labor costs, and improve the quality of welds.
Market trends also indicate a growing demand for energy-efficient and eco-friendly welding machines. The industry is witnessing a shift towards greener technologies, driven by environmental concerns and government regulations. Manufacturers are increasingly focusing on developing energy-efficient machines that reduce carbon emissions and save energy. This trend reflects the industry’s commitment to sustainability and reducing the overall ecological impact.
Lastly, there is a rising trend towards digitalization and connectivity in welding machines. Internet of Things (IoT) technology is being integrated into welding machines, allowing for real-time data monitoring, analysis, and remote control. This enables operators to optimize the welding process, improve quality control, and enhance overall efficiency. Digitalization also facilitates predictive maintenance, reducing downtime and ensuring continuous operation.
Overall, the welding machines industry is evolving to meet the changing needs of various sectors. The market trends indicate a shift towards portable and advanced welding machines, energy-efficient technology, and digital connectivity. These advancements are driven by the need for flexibility, productivity, sustainability, and optimization of welding processes.
Custom Private Labeling and Branding Opportunities with Chinese types of welding machines Manufacturers
Having a private label allows businesses to showcase their own brand identity and offer unique products to their customers. When it comes to welding machines, Chinese manufacturers offer a plethora of opportunities for custom private labeling and branding.
Chinese manufacturers are renowned for their expertise in producing high-quality welding machines at competitive prices. By leveraging their manufacturing capabilities, businesses can collaborate with these manufacturers to create custom welding machines under their own brand name.
Private labeling and branding opportunities enable businesses to have full control over the product features, design, and packaging. Whether it’s a specific type of welding machine or any innovative features, Chinese manufacturers can cater to the specific requirements of businesses, ensuring the final product aligns with their brand identity.
Additionally, Chinese manufacturers provide flexibility in terms of branding options. From prominent branding on the machine itself to customized packaging and user manuals, businesses have the freedom to tailor every aspect of the product to suit their marketing strategies.
Moreover, by availing private labeling and branding services, businesses can strengthen their brand image and gain a competitive advantage in the welding machine market. With their extensive experience in manufacturing, Chinese manufacturers can ensure that the custom products meet international quality standards and certifications, further enhancing the brand’s credibility.
It is important to note that while exploring private labeling and branding opportunities with Chinese manufacturers, businesses should establish clear communication channels and provide comprehensive specifications to ensure the desired outcome.
In conclusion, partnering with Chinese manufacturers for private label and branding opportunities in welding machines can unlock a range of customization options, allowing businesses to establish their unique presence in the market. With their manufacturing expertise and competitive pricing, Chinese manufacturers offer a valuable opportunity to create high-quality custom products under a brand’s name.
Tips for Procurement and Considerations when Purchasing types of welding machines
When it comes to purchasing welding machines for your procurement needs, there are several considerations that you need to keep in mind to ensure that you make a well-informed decision. Here are some tips and considerations to bear in mind:
1. Determine your welding requirements: Identify the types of welding processes you are looking to perform. This will help you in selecting the appropriate machine that suits your specific needs. Common types of welding machines include MIG, TIG, stick, and plasma cutters.
2. Power requirements: Consider the power source available at your location. Some machines operate on single-phase power, while others require three-phase power. Make sure to match the power requirements with your available power supply.
3. Duty Cycle: Duty cycle refers to the amount of time a welding machine can operate continuously before it requires a period of rest to prevent overheating. Ensure that the duty cycle of the machine aligns with your expected usage.
4. Portability: If you require a welding machine for on-site jobs or frequent movement, portability becomes a key factor. Opt for lightweight and compact machines that are easy to transport.
5. Brand reputation and reliability: Choose a reputable brand known for its quality and reliability. Check customer reviews and ratings to ensure that the machine you are considering has a good track record.
6. Price and budget: Set a budget for your procurement and compare different options within your budget range. However, remember that cheaper machines may often lack durability and quality.
7. Warranty and after-sales support: Ensure that the machine comes with a warranty to cover any potential defects or malfunctions. Additionally, consider the availability of after-sales support such as spare parts and technical assistance.
8. Safety features: Look for machines that have essential safety features like thermal overload protection, voltage protection, and arc force control to ensure the safety of the operator.
9. Noise considerations: If noise levels are a concern in your workspace or environment, consider machines with noise-reduction features or models known for their quiet operation.
10. Future expansion: If you anticipate expanding your welding capabilities in the future, consider investing in machines that allow for upgrades or have versatile functionalities to accommodate your future needs.
By considering these factors, you can make an informed decision and select a welding machine that meets your specific procurement requirements.
FAQs on Sourcing and Manufacturing types of welding machines in China
Q1: Can I source welding machines from China?
A1: Yes, China is a leading manufacturer of welding machines and is known for producing a wide range of high-quality products. Many global companies source welding machines from China due to their competitive pricing and advanced manufacturing capabilities.
Q2: What types of welding machines can be sourced from China?
A2: China offers a vast array of welding machines, including MIG welders, TIG welders, arc welders, spot welders, plasma cutters, and more. These machines are available in various power outputs, sizes, and functionalities to meet different welding requirements.
Q3: Can I get custom-made welding machines from China?
A3: Yes, many Chinese manufacturers offer customization services to tailor welding machines to specific customer needs. This includes modifications in power output, welding processes, controls, and other features. Manufacturers have the ability to design and produce machines according to customer specifications.
Q4: Are Chinese welding machines of good quality?
A4: While the quality of welding machines can vary, China has a mix of manufacturers that produce both high-quality and lower-quality machines. To ensure good quality, it is crucial to conduct thorough research, evaluate manufacturers’ reputation and certifications, and ask for samples or references before making a purchase decision.
Q5: How does sourcing welding machines from China work?
A5: Sourcing welding machines from China typically involves identifying and contacting manufacturers or suppliers, discussing requirements, obtaining samples or prototypes, negotiating pricing and terms, conducting quality inspections, and finalizing the order. It is advisable to work with reputable sourcing agents or brokers who can assist in finding reliable manufacturers and ensuring a smooth sourcing process.
Q6: What are the advantages of sourcing welding machines from China?
A6: The advantages include access to a wide variety of products, competitive pricing, advanced manufacturing capabilities, customization options, flexible order quantity, and experienced logistics infrastructure for international shipments. China’s robust industrial ecosystem allows for cost-effective production and quick turnaround times.
Q7: Are there any challenges in sourcing welding machines from China?
A7: Some potential challenges include language barriers, cultural differences, intellectual property protection, and the need for thorough due diligence to ensure product quality and compliance with international standards. Proper communication, clear specifications, and professional legal support can help mitigate these challenges.
In conclusion, China is a reliable destination for sourcing welding machines due to its vast manufacturing capabilities. However, prospective buyers should undertake diligent research, choose reputable manufacturers, and conduct quality inspections to ensure the desired standards are met. Working with experienced sourcing professionals can enhance the efficiency and success of the sourcing process.
Why contact sourcifychina.com get free quota from reliable types of welding machines suppliers?
SourcifyChina.com is able to offer free quota from reliable types of welding machines suppliers because of several reasons.
Firstly, SourcifyChina.com has established long-term relationships with a network of trustworthy welding machine suppliers in China. These suppliers have been thoroughly vetted and are known for their quality products and reliable services. By partnering with these suppliers, SourcifyChina.com can confidently offer free quota to its customers.
Secondly, SourcifyChina.com has a strong presence and reputation in the sourcing industry. Over the years, it has built a solid reputation for providing customers with high-quality products, competitive prices, and exceptional customer service. This reputation has allowed SourcifyChina.com to negotiate favorable deals with its suppliers, including the provision of free quota.
Furthermore, SourcifyChina.com understands the value of building long-term relationships with its customers. By offering free quota from reliable suppliers, it aims to build trust and loyalty with its customers. The company believes that by providing value-added services such as free quota, it can attract more customers and retain existing ones.
Additionally, SourcifyChina.com has a deep understanding of the welding machine market in China. It keeps a close eye on industry trends, product innovations, and supplier capabilities. This knowledge enables SourcifyChina.com to identify the most reliable types of welding machines suppliers and negotiate favorable terms.
In conclusion, SourcifyChina.com is able to offer free quota from reliable types of welding machines suppliers due to its strong relationships with trustworthy suppliers, its reputation in the sourcing industry, its focus on building long-term customer relationships, and its deep knowledge of the welding machine market in China.