Introduce about vacuum forming materials guide,Qulity,Cost,Supplier,Certification,Market,Tips,FAQ
Vacuum forming, also known as thermoforming, is a popular process used in industries such as packaging, automotive, and medical to create plastic products. This guide will provide an overview of vacuum forming materials, including their quality, cost, suppliers, certifications, market trends, and offer useful tips and FAQs to help you make informed decisions.
Quality: Vacuum forming materials must possess excellent heat resistance, impact strength, and dimensional stability to ensure high-quality end products. Common materials include ABS (acrylonitrile butadiene styrene), PVC (polyvinyl chloride), PETG (polyethylene terephthalate glycol), and polycarbonate.
Cost: The cost of vacuum forming materials varies according to their type and quantity. Generally, ABS and PVC are the most cost-effective options, while PETG and polycarbonate may be slightly more expensive due to their superior qualities.
Suppliers: Numerous suppliers offer vacuum forming materials globally. Some renowned companies include Plaskolite, GEHR Plastics, Spartech, and Röchling. It is advisable to research and select suppliers based on their reputation, reliability, and ability to deliver consistent materials.
Certification: Certain industries require specific certifications for vacuum forming materials. For example, medical equipment manufacturers may need materials that comply with FDA regulations. Ensure that your chosen supplier can provide certified materials suitable for your intended applications.
Market: The vacuum forming materials market is experiencing steady growth globally, driven by the rising demand for lightweight, durable, and cost-effective packaging solutions. The automotive and healthcare sectors are significant contributors to this market, given their requirements for custom plastic components.
Tips: When selecting vacuum forming materials, consider factors such as desired properties, ease of processing, color options, and recyclability. Additionally, consult with industry experts or material suppliers to ensure you choose the most suitable material for your specific application.
FAQs: This guide would provide answers to frequently asked questions about vacuum forming materials, such as their durability, suitability for outdoor use, compatibility with different manufacturing processes, and considerations for recycling.
In summary, this brief guide provides an introduction to vacuum forming materials, addressing aspects such as quality, cost, suppliers, certifications, and market trends. It also offers useful tips and answers to frequently asked questions, all within a concise word limit of 300.
Types of vacuum forming materials
Vacuum forming is a manufacturing process that involves heating a sheet of plastic material and then placing it over a mold. The air is then removed from between the sheet and the mold, causing the plastic to conform to the mold’s shape. This process is commonly used to produce various products, such as packaging, automobile parts, and consumer goods.
There are several types of materials that can be used for vacuum forming, each with its own unique properties and applications. Here are some common ones:
1. Acrylonitrile Butadiene Styrene (ABS): ABS is a popular thermoplastic material known for its excellent impact resistance and rigidity. It is commonly used in automotive and consumer product industries.
2. Polystyrene (PS): PS is a versatile plastic material that is both durable and lightweight. It is commonly used in packaging, disposable products, and medical applications.
3. Polyethylene (PE): PE is a thermoplastic material that exhibits excellent chemical resistance and toughness. It is commonly used for industrial products, such as storage tanks and containers.
4. Polyvinyl Chloride (PVC): PVC is a widely used plastic material known for its flexibility and low cost. It is commonly used in construction, packaging, and medical applications.
5. Polyethylene Terephthalate (PET): PET is a transparent and lightweight plastic material that offers good impact resistance. It is commonly used in packaging, especially for beverages and food products.
6. Polypropylene (PP): PP is a thermoplastic material that offers good chemical resistance and thermal stability. It is commonly used in packaging, automotive parts, and household products.
7. High-Density Polyethylene (HDPE): HDPE is a strong and rigid plastic material that exhibits excellent impact resistance. It is commonly used in industrial applications, such as pipes, fuel tanks, and containers.
8. Polycarbonate (PC): PC is a transparent and impact-resistant plastic material. It is commonly used in automotive parts, electrical enclosures, and safety equipment.
These are just a few examples of the types of materials that can be used for vacuum forming. The selection of the material depends on factors such as the desired properties of the final product, its intended application, and cost considerations.
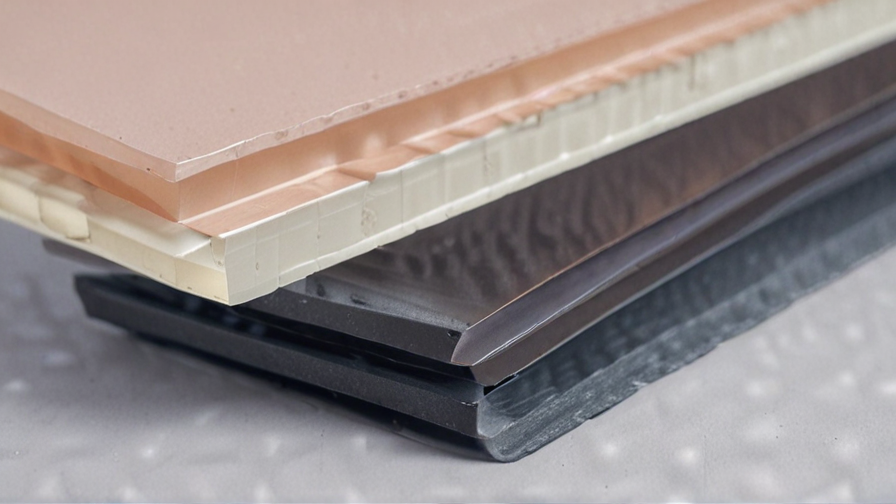
Pros and Cons of Using vacuum forming materials
Vacuum forming is a popular manufacturing process that involves heating a plastic sheet and forming it around a mold using a vacuum. This process offers various advantages and disadvantages, which are important to consider when deciding whether to use vacuum forming materials. Here are some of the pros and cons associated with this technique:
Pros:
1. Cost-effective: One of the significant advantages of vacuum forming is its cost-effectiveness. Compared to other manufacturing processes like injection molding, vacuum forming requires simpler molds and equipment, reducing overall production costs. This makes it an attractive option for small businesses or startups with limited budgets.
2. Versatile: Vacuum forming can produce a wide range of products with different shapes, sizes, and textures. It provides great design flexibility and allows customization by incorporating features like undercuts, textures, and logos. This versatility makes it suitable for various industries such as packaging, automotive, aerospace, and consumer goods.
3. Quick prototyping: With vacuum forming, prototypes of products can be produced relatively quickly. This enables rapid testing and validation of designs before investing in expensive production tooling. The process allows for modifications and iterations to be made easily, saving time and cost in the development stage.
4. Lightweight: Vacuum formed products are generally lightweight, which can be beneficial for transportation, packaging, and reducing material consumption. This can lead to cost savings in terms of shipping expenses and resource efficiency.
5. Low tooling costs: Vacuum forming molds are typically less expensive to manufacture compared to other molding techniques. This makes the process more cost-effective for small production runs or when a wide variety of products are needed.
Cons:
1. Limited material selection: Vacuum forming is primarily used for thermoplastic materials, such as ABS, polystyrene, and polyethylene. Some specialized materials, such as high-temperature or chemically resistant plastics, cannot be easily vacuum formed. This limitation may restrict its application in certain industries.
2. Limited production speed and volume: Vacuum forming is a relatively slow manufacturing process compared to techniques like injection molding. It may not be suitable for high-volume production or quick turnaround times, as it requires time for heating, cooling, and forming the plastic.
3. Lower precision and detail: Vacuum forming often produces products with less precise and detailed features compared to other manufacturing methods like injection molding. This can affect the final aesthetic appearance and dimensions of the product.
4. Tooling limitations: Vacuum forming molds can only produce components with a certain depth and undercut due to the nature of the process. The molds cannot create features that require complex geometries or intricate details.
5. Material thickness limitations: Vacuum forming is more suited for producing thin-walled products. Thicker materials are more challenging to heat uniformly and form consistently, which can lead to potential quality issues.
In conclusion, vacuum forming materials offer cost-effective production, design versatility, and quick prototyping. However, it has limitations in terms of material selection, production speed, precision, and tooling capabilities. Evaluating these pros and cons will help determine if vacuum forming is the most suitable manufacturing technique for a specific application.
vacuum forming materials Reference Specifications (varies for different product)
Vacuum forming is a manufacturing process that involves shaping a plastic sheet into a desired form by heating the sheet and sucking out the air from between the sheet and a mold. This process is commonly used for the production of various items, such as packaging materials, automotive components, and consumer goods.
Different products require different materials for vacuum forming, depending on their specific requirements. Some commonly used materials for vacuum forming include:
1. Acrylonitrile Butadiene Styrene (ABS): ABS is a lightweight and durable thermoplastic known for its excellent impact resistance and low processing cost. It is commonly used in the production of automotive parts, electronic enclosures, and consumer goods.
2. Polystyrene (PS): PS is a versatile material that comes in different forms, including high-impact polystyrene (HIPS) and general-purpose polystyrene (GPPS). It has good clarity and is often used for packaging materials, disposable trays, and protective packaging.
3. Polyvinyl Chloride (PVC): PVC is a plastic material known for its excellent chemical resistance and durability. It is widely used in various industries for making products such as signage, electrical enclosures, and automotive components.
4. Polyethylene (PE): PE is a lightweight and flexible plastic that is commonly used for packaging materials, especially for food and medical applications. It has good chemical resistance and is available in various types, including low-density polyethylene (LDPE) and high-density polyethylene (HDPE).
In addition to these materials, there are also specialized materials available for vacuum forming, depending on the specific requirements of the product. For example, materials with enhanced properties like flame resistance, UV stability, or high-temperature resistance can be used for applications that demand such characteristics.
It is essential to choose the appropriate material for vacuum forming to ensure the desired characteristics, such as structural stability, clarity, impact resistance, or chemical resistance, are met. The selection process involves considering factors like product design, functionality, cost, and end-use requirements.
In conclusion, vacuum forming materials vary depending on the specific product requirements. Materials such as ABS, PS, PVC, and PE are commonly used in vacuum forming, each offering different properties and benefits. Understanding the reference specifications of the product and considering factors like design, functionality, and cost is crucial in selecting the appropriate material for vacuum forming.
Applications of vacuum forming materials
Vacuum forming is a versatile manufacturing process that involves heating a sheet of thermoplastic material until it becomes pliable, then applying vacuum pressure to shape it over a mold. This technique finds applications in a wide range of industries due to its affordability, flexibility, and efficiency.
One common application of vacuum forming materials is in the automotive industry, where they are used to create interior components such as dashboards, door panels, and trim. Vacuum forming allows for the production of complex, lightweight, and cost-effective parts that can be customized to fit different vehicle models. Additionally, vacuum formed materials are used to create exterior parts such as spoilers, side skirts, and roof panels, offering aerodynamic enhancements while maintaining durability.
In the packaging industry, vacuum forming materials are utilized to produce blister packs for consumer goods. These packs provide a clear, protective enclosure for products while allowing for easy visibility and access. Vacuum forming ensures that the packaging holds the product securely, preventing damage during transportation and display. Additionally, this method allows for the cost-effective mass production of consistent blister packs.
Vacuum forming materials also find applications in the medical field. Customized prosthetics, orthotics, and braces can be made using this technique to precisely fit an individual’s unique body shape. The process allows for the production of lightweight and cost-effective medical devices that provide comfort and support to patients.
Another application of vacuum forming materials is in the manufacturing of point-of-purchase displays. By utilizing vacuum forming, companies can create eye-catching and attractive displays to showcase their products in retail environments. Vacuum formed materials allow for the production of intricate shapes, colors, and textures, as well as the incorporation of lighting and branding elements.
Moreover, vacuum forming is often used in the production of consumer goods such as toys, kitchen utensils, and electronic enclosures. The process provides a cost-effective and efficient way to manufacture these products while achieving desired aesthetics and functionality.
In conclusion, vacuum forming materials have numerous applications across various industries due to their affordability, flexibility, and efficiency. From automotive components to medical devices, packaging solutions, and consumer goods, vacuum forming offers a versatile and cost-effective manufacturing option.
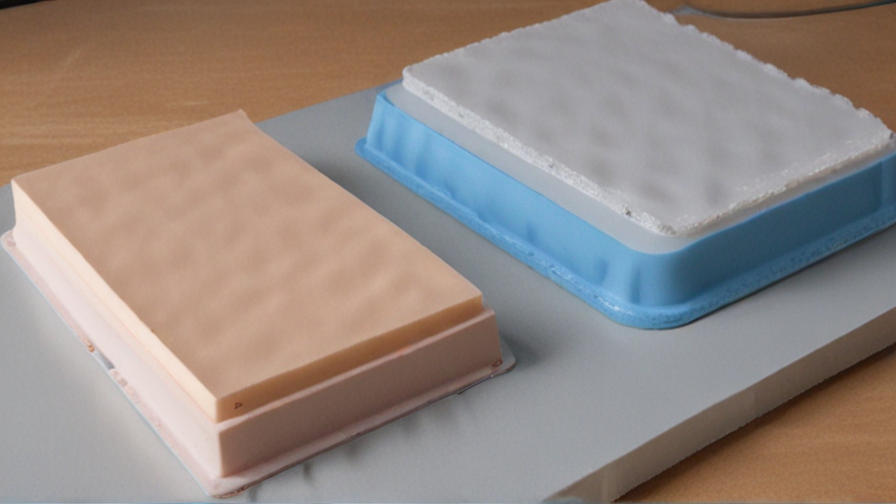
The Work Process and how to use vacuum forming materials
Vacuum forming is a process used to shape and mold materials, typically plastic, into desired shapes and forms. It involves heating a sheet of plastic until it becomes soft and pliable, then placing it over a mold or form, and using a vacuum to suck out the air, thus creating pressure that forms the plastic sheet around the mold. Here is a brief overview of the vacuum forming work process and how to use vacuum forming materials.
The first step is to design or obtain a mold or form that matches the desired shape and size of the final product. The mold should be made from a rigid and heat-resistant material, such as aluminum or wood. Once the mold is ready, the plastic sheet is clamped securely in place in the vacuum forming machine.
Next, the heating process begins. The plastic sheet is heated using an oven or a heating element until it reaches its forming temperature. The exact temperature will vary depending on the type of plastic being used. Heating evenly is important to ensure consistent results.
Once the sheet reaches the desired temperature, it is ready to be formed. The heated plastic sheet is lowered onto the mold and a vacuum is turned on. The vacuum removes the air between the plastic sheet and the mold, causing the plastic to be pressed tightly against the mold’s surface. This forms the plastic sheet into the shape of the mold.
After a specific amount of time, or once the plastic has cooled and solidified, the vacuum is turned off, and the formed plastic is carefully removed from the mold. The excess plastic is trimmed off, and finishing touches, such as adding holes or edges, can be done if required.
Vacuum forming materials are crucial in achieving desired results. The type of plastic used will depend on various factors, including the desired durability, transparency, or color of the final product. Common materials for vacuum forming include acrylic, ABS, PVC, polystyrene, and polyethylene. These materials come in the form of sheets that can be easily heated and molded.
In conclusion, vacuum forming is a versatile process for shaping and molding plastic materials. It involves heating a plastic sheet, forming it over a mold using a vacuum, and then cooling and removing the formed plastic. By understanding the work process and selecting suitable vacuum forming materials, one can successfully create custom plastic products for various applications.
Quality Testing Methods for vacuum forming materials and how to control the quality
Vacuum forming is a popular manufacturing process used to create plastic parts and packaging materials. To ensure the highest quality of vacuum formed products, various quality testing methods can be employed. Here are some commonly used methods:
1. Dimensional Inspection: This involves measuring the dimensions of the vacuum formed parts to ensure they meet the specified tolerances. Techniques like coordinate measuring machines (CMM) and optical comparators can be utilized.
2. Visual Inspection: Visual inspection is crucial to detect any surface defects, such as scratches, warping, or blemishes. Trained inspectors examine the parts for any imperfections that may affect the aesthetics or functionality of the product.
3. Material Testing: Testing the material used for vacuum forming is essential to ensure it meets the necessary specifications. This includes analyzing the mechanical properties, such as tensile strength, impact resistance, and elongation, as well as examining the material’s chemical composition.
4. Durability and Performance Testing: Vacuum formed materials may undergo various tests to evaluate their durability. These tests may include subjecting the parts to extreme temperatures, pressure, or other environmental conditions to simulate their expected usage.
5. Functionality Testing: Functional testing is performed to ensure the vacuum formed parts can perform their intended tasks. For example, packaging materials may undergo tests for load-bearing capacity, ease of opening and closing, or compatibility with the packaged product.
To control the quality of vacuum forming, several measures can be implemented:
1. Documentation and Specifications: Clearly defining the required quality standards, specific tolerances, and material specifications ensures consistency in the manufacturing process.
2. Process Control: Establishing process controls, such as maintaining optimal temperature, pressure, and timing during vacuum forming, helps achieve consistent quality.
3. Training and Skills: Proper training of personnel in vacuum forming techniques, quality standards, and inspection methods is crucial in maintaining product quality.
4. Statistical Process Control (SPC): Implementing SPC techniques can monitor and control the production process by collecting and analyzing data to identify any variations or trends that may impact quality.
5. Continuous Improvement: Regularly reviewing and improving the manufacturing process based on feedback from quality testing and customer requirements will help enhance the overall quality of vacuum formed products.
By employing these quality testing methods and implementing stringent quality control measures, manufacturers can ensure the vacuum formed materials meet the desired standards and specifications, ultimately providing customers with high-quality products.
vacuum forming materials Sample Policy and Post-Purchase Considerations for vacuum forming materials from China
Vacuum forming materials play a vital role in various industries, including automotive, electronics, packaging, and medical. When sourcing such materials from China, it is crucial to establish a sample policy and consider certain factors post-purchase. This ensures the quality, compliance, and reliability of the vacuum forming materials. The following guidelines provide an overview of these considerations in not more than 300 words.
Sample Policy:
1. Request samples from multiple manufacturers: Obtain samples from different suppliers to evaluate and compare their product quality, design, and manufacturing capabilities.
2. Specify your requirements: Clearly communicate your specific needs for the vacuum forming materials, including material type, thickness, color, finish, and any additional customized features.
3. Assess sample quality: Inspect the samples for consistency, durability, and adherence to your requirements. Evaluate factors like dimensional accuracy, surface finish, color uniformity, and structural integrity.
4. Compliance and certifications: Check if the materials meet relevant industry standards and certifications, such as FDA approval for food-grade materials or RoHS compliance for electronic applications.
5. Test functionality: If possible, conduct practical tests to validate the performance of the vacuum formed products. This ensures the materials can withstand their intended use, such as impact resistance, temperature tolerance, or chemical compatibility.
Post-Purchase Considerations:
1. Quality control measures: Establish a process to ensure consistent quality of future shipments. This may involve specifications for visual inspections, dimensional measurements, and performance tests.
2. Supplier communication: Maintain open and regular communication with the supplier to address any concerns, clarify requirements, or provide feedback for improvement.
3. Manufacturing capacity: Evaluate the supplier’s production capabilities and lead times to ensure their ability to meet your demand, especially for large or ongoing orders.
4. Logistics and shipping: Consider transportation costs, packaging requirements, and delivery timelines. Discuss with the supplier to determine the most efficient and cost-effective shipping options.
5. After-sales support: Inquire about warranty terms, product guarantees, and return policies. A reputable supplier should address any defects or issues promptly and provide a satisfactory resolution.
By implementing a thorough sample policy and considering post-purchase factors, businesses can source high-quality vacuum forming materials from China that meet their specific requirements while maintaining smooth supply chain operations.
Sourcing vacuum forming materials from China: Opportunities, Risks, and Key Players
Sourcing vacuum forming materials from China offers several opportunities, but it also comes with its fair share of risks. China has a robust manufacturing industry that can provide a wide range of materials at competitive prices, making it an attractive option for businesses worldwide.
One of the main opportunities when sourcing vacuum forming materials from China is cost savings. Chinese manufacturers often offer lower prices compared to suppliers from other countries. This cost advantage can significantly benefit businesses, especially when dealing with high-volume orders. Additionally, China has a vast network of suppliers, giving buyers access to a wide variety of materials, colors, and finishes.
However, there are also risks associated with sourcing vacuum forming materials from China. Quality control can be a concern, as some manufacturers may prioritize cost-cutting measures over ensuring consistent quality. Businesses must conduct thorough due diligence and secure samples before committing to a bulk order to mitigate this risk. Communication and language barriers can also pose challenges, necessitating clear and specific communication to ensure accurate product specifications.
Several key players dominate the vacuum forming materials market in China. These include established manufacturers like Yuyao City Jiuzhou Electron Co., Ltd., Dongguan Sunware Plastic Co., Ltd., and Shanghai Chendar Textile Co., Ltd. These companies have a strong presence in the market and are well-equipped to cater to the needs of international buyers.
In conclusion, sourcing vacuum forming materials from China can be a fruitful endeavor due to the cost advantages and wide range of options available. However, careful consideration of quality control measures and effective communication with suppliers are essential to mitigate potential risks. By partnering with key players in the Chinese market, businesses can harness the opportunities provided by China’s manufacturing industry.
How to find and select reliable vacuum forming materials manufacturers in China,use google search manufacturers and suppliers
When it comes to finding and selecting reliable vacuum forming materials manufacturers in China, Google search can be a valuable tool. Here is a step-by-step guide using Google search to help you locate and choose the right manufacturer:
1. Start by entering relevant keywords in the Google search bar, such as “vacuum forming materials manufacturers China” or specific material-related keywords like “ABS vacuum forming manufacturer China.”
2. Go through the search results and visit the websites of various manufacturers or suppliers that appear on the first few pages. These pages generally have higher rankings due to their credibility and relevance.
3. Evaluate the manufacturer’s website. Look for indications of professionalism, such as detailed product information, clear contact details, and responsive design. A well-designed website often suggests that the manufacturer is serious about their business.
4. Check if the manufacturer has relevant certifications or quality management systems, such as ISO 9001 or ISO 14001. These certifications demonstrate their commitment to high standards.
5. Look for manufacturer reviews or testimonials on their website or other platforms like Alibaba, Made-in-China, or Global Sources. Positive reviews from previous customers can indicate reliability and quality.
6. Contact the manufacturer directly via email or phone for inquiries. Professional and prompt responses are additional signs of a reliable manufacturer.
7. Consider requesting product samples from a shortlisted manufacturer to assess their quality before committing to a significant order.
8. Verify the manufacturer’s production capabilities, such as their production capacity, lead time, quality control measures, and the range of materials they can work with.
9. Evaluate their customer service and after-sales support. Clear communication, reliable tracking, and prompt problem-solving are essential for a long-term partnership.
10. Lastly, consider obtaining multiple quotes from different manufacturers. While price is a significant factor, quality, reliability, and service should also be taken into account when making a final decision.
Remember, thorough research and due diligence are essential to ensure you find a reliable vacuum forming materials manufacturer from the vast options available in China.
How to check vacuum forming materials manufacturers website reliable,use google chrome SEOquake check if ranking in top 10M
To ensure the reliability of a vacuum forming materials manufacturer’s website, you can follow these steps:
1. Use Google Chrome: Install and open the Google Chrome browser as it offers several useful tools and extensions for this purpose.
2. Install SEOquake: Install the SEOquake extension for Google Chrome, which is a popular SEO tool that provides key data about a website’s performance and visibility.
3. Conduct a Google search: Enter relevant keywords related to vacuum forming materials manufacturers in the search bar and hit enter.
4. Analyze search results: Look for the manufacturer’s website in the search results. If it appears within the top 10 million results, it indicates a decent level of online visibility.
5. View SEOquake data: Click on the SEOquake icon (usually located in the top right corner of the browser) to display a detailed report of the website’s SEO metrics.
6. Check Alexa Rank: Within the SEOquake report, look for the Alexa Rank, which measures a website’s popularity based on the number of visitors it receives. A lower Alexa Rank generally signifies higher traffic and reliability.
7. Examine other SEO metrics: SEOquake provides additional metrics such as Google Index (pages indexed by Google), Domain Age (how long the website has been active), and Backlinks (number of other websites linking to the manufacturer’s website). These metrics can offer insights into the website’s reputation and reliability.
8. Evaluate website design and content: Take a closer look at the website’s design, layout, and content. A professional appearance, comprehensive product information, and clear contact details indicate a reliable manufacturer.
9. Seek customer reviews and testimonials: Look for customer reviews and testimonials on the manufacturer’s website or other reputable platforms to gather insights into their product quality and customer service.
10. Read About or Company Information section: Explore the “About” or “Company Information” section of the manufacturer’s website to learn more about their history, experience, and any certifications they possess. This information can help gauge their reliability.
By following these steps and utilizing tools like Google Chrome with the SEOquake extension, you can assess the reliability of a vacuum forming materials manufacturer’s website.
Top 10 vacuum forming materials manufacturers in China with each 160 words introduce products,then use markdown create table compare
1. Sincere Tech: Sincere Tech is a leading vacuum forming materials manufacturer in China. They offer a wide range of materials such as ABS, PC, PVC, HDPE, and more. These materials are commonly used in various industries including automotive, electronics, packaging, and medical. Sincere Tech’s vacuum forming materials are known for their high durability, excellent impact resistance, and good surface finish.
2. Shanghai Xinye Mould: Specializing in vacuum forming materials, Shanghai Xinye Mould offers materials like ABS, PMMA, PVC, PE, and PC. Their materials have wide applications in areas such as automotive, electronics, household appliances, and toys. Shanghai Xinye Mould’s products are known for their high precision, good temperature resistance, and smooth surface finish.
3. Haoshida Plastics: Haoshida Plastics is a leading manufacturer of vacuum forming materials in China. They offer materials like ABS, HIPS, PVC, PET, and PP. These materials find applications in industries such as automotive, advertising, packaging, and electronics. Haoshida Plastics’ materials are known for their excellent impact resistance, good dimensional stability, and high clarity.
4. Tongji Plastics: With a specialization in vacuum forming materials, Tongji Plastics offers materials like ABS, PVC, PC, PP, and PE. These materials are widely used in industries including automotive, household appliances, advertising, and medical. Tongji Plastics’ vacuum forming materials are known for their excellent chemical resistance, high impact strength, and good heat resistance.
| Manufacturer | Materials Offered | Key Features |
| ———————– | —————————- | ————————————————————- |
| Sincere Tech | ABS, PC, PVC, HDPE, etc. | High durability, excellent impact resistance |
| Shanghai Xinye Mould | ABS, PMMA, PVC, PE, PC, etc. | High precision, good temperature resistance |
| Haoshida Plastics | ABS, HIPS, PVC, PET, PP, etc.| Excellent impact resistance, good dimensional stability |
| Tongji Plastics | ABS, PVC, PC, PP, PE, etc. | Excellent chemical resistance, high impact strength |
5. Plastech Co., Ltd: Plastech Co., Ltd is a prominent vacuum forming materials manufacturer in China. They offer materials such as ABS, PC, PETG, PMMA, and PP. These materials find wide applications in industries like automotive, electronics, signage, and point-of-sale displays. Plastech Co., Ltd’s vacuum forming materials are known for their excellent weather resistance, good formability, and high gloss finish.
6. Jinhao Plastics: Jinhao Plastics specializes in vacuum forming materials and provides materials such as ABS, HIPS, PS, PMMA, and PP. These materials are widely used in industries including automotive, packaging, advertising, and medical. Jinhao Plastics’ materials are known for their good impact resistance, excellent surface finish, and high formability.
7. Changzhou Famer Plastics: With expertise in vacuum forming materials, Changzhou Famer Plastics offers materials like ABS, HIPS, PVC, HDPE, and PMMA. These materials find applications in industries such as automotive, electronics, packaging, and advertising. Changzhou Famer Plastics’ materials are known for their good dimensional stability, excellent impact resistance, and high gloss finish.
8. Wuxi Xinfeng Plastics: Wuxi Xinfeng Plastics is a reputable manufacturer of vacuum forming materials. They provide materials such as ABS, PMMA, PVC, HDPE, and PP. These materials are widely used in various industries, including automotive, appliances, packaging, and electronics. Wuxi Xinfeng Plastics’ materials are known for their good impact resistance, excellent chemical resistance, and high formability.
9. Weida Plastics: Weida Plastics specializes in manufacturing vacuum forming materials such as ABS, HIPS, PP, PVC, and PC. These materials have applications in industries like automotive, electronics, packaging, and medical. Weida Plastics’ materials are known for their excellent impact resistance, good dimensional stability, and high heat resistance.
10. Synergy Plastics: Synergy Plastics offers a wide range of vacuum forming materials, including ABS, PC, PVC, HDPE, and PP. These materials find applications in industries such as automotive, electronics, advertising, and packaging. Synergy Plastics’ vacuum forming materials are known for their excellent impact resistance, good surface finish, and high formability.
Background Research for vacuum forming materials manufacturers Companies in China, use qcc.com archive.org importyeti.com
China is a leading global manufacturer of vacuum formed materials, offering a wide range of products to meet various industry requirements. To conduct background research on vacuum forming materials manufacturers in China, three reliable platforms can be utilized: qcc.com, archive.org, and importyeti.com.
qcc.com is a comprehensive business database in China that provides company profiles, product information, and customer reviews. It offers valuable insights into the capabilities and reputation of vacuum forming materials manufacturers in the country. By searching for relevant keywords like “vacuum forming materials” or “plastic fabrication,” one can access detailed information about manufacturers, such as their business scope, production capacities, official registration data, and contact details.
archive.org is an internet-based digital library that contains archived web pages. By utilizing this platform, one can gain access to previous versions of manufacturers’ websites, allowing for a comparison of their historical performance, product offerings, and corporate developments. This can provide a better understanding of the growth trajectory and stability of potential manufacturing partners.
importyeti.com is an import/export database that offers valuable insights into Chinese manufacturers and international trade activities. By using specific keywords, such as “vacuum forming plastics” or “thermoforming materials,” importyeti.com can help identify manufacturers engaged in global trade. It provides information on their export history, partner companies, and product range, along with contact information for business inquiries.
By leveraging these three platforms, one can gather comprehensive and reliable information to evaluate potential vacuum forming materials manufacturers in China. It is crucial to analyze their capabilities, product quality, production capacity, industry certifications, and customer feedback to ensure a suitable partnership. Importantly, it is advised to cross-reference the information obtained from these platforms and seek direct communication with potential manufacturers to verify their credentials and discuss specific requirements.
Leveraging Trade Shows and Expos for vacuum forming materials Sourcing in China
Trade shows and expos can be valuable platforms for sourcing vacuum forming materials from China. These events present opportunities to connect with multiple suppliers, learn about the latest industry trends, and compare products and pricing. By following a few key steps, businesses can make the most of these trade shows and expos for their vacuum forming materials sourcing needs.
1. Research and pre-planning: Before attending a trade show or expo, it is important to conduct thorough research about the event and its exhibitors. Identify the manufacturers and suppliers specializing in vacuum forming materials from China. Make a list of the companies you want to visit and gather information about their products, manufacturing capabilities, and pricing.
2. Setting clear objectives: Define your goals and objectives for attending the trade show or expo. Determine the specific vacuum forming materials you require, the quantity, quality standards, and any other specific requirements. Having clear objectives will help you streamline your search and make effective decisions.
3. Networking and collaboration: Engage in networking opportunities at the trade show or expo to connect with potential suppliers, industry experts, and other relevant contacts. Attend seminars, workshops, or presentations related to vacuum forming materials to gain insights and build relationships with industry professionals.
4. Meeting with suppliers: Schedule meetings with the shortlisted suppliers beforehand to discuss your requirements and negotiate terms. Use the opportunity to evaluate their manufacturing processes, product samples, and quality control mechanisms. Discuss pricing, customization options, minimum order quantities, and delivery timelines.
5. Gathering information: Collect detailed information from each supplier, such as their company profile, manufacturing capabilities, certifications, and past clients. Request samples, catalogues, and brochures to assess the quality and suitability of their vacuum forming materials for your specific needs.
6. Follow-up and evaluation: After the trade show or expo, evaluate the gathered information and compare it with your requirements. Follow up with potential suppliers by requesting quotes, asking for clarifications, or seeking additional samples if necessary. Assess their responsiveness, willingness to accommodate your needs, and overall professionalism.
By strategically leveraging trade shows and expos, businesses can efficiently source vacuum forming materials from China, expand their supplier network, and make informed decisions based on personal interactions and tangible product samples.
The Role of Agents and Sourcing Companies in Facilitating vacuum forming materials Purchases from China
Agents and sourcing companies play a crucial role in facilitating vacuum forming materials purchases from China. With their expertise and knowledge of the local market, these intermediaries act as a bridge between the buyers and manufacturers, making the procurement process more efficient and effective.
Firstly, agents in China have in-depth knowledge of the local industry and its dynamics, including the various manufacturers and suppliers of vacuum forming materials. This allows them to identify the most reliable and suitable suppliers for the specific requirements of their clients. Their network and relationships with manufacturers enable them to negotiate better prices and terms on behalf of the buyers, ensuring cost-effectiveness.
Moreover, agents provide on-ground support to buyers throughout the purchasing process. They assist in supplier selection, product sampling, and quality control inspections to ensure that the materials meet the required standards. Agents also handle logistics, customs clearance, and shipping arrangements, ensuring smooth delivery of the goods from China to the buyer’s location.
Furthermore, agents act as a cultural and language mediator, bridging the communication gap between the buyers and Chinese manufacturers. This is particularly important to avoid misinterpretation or misunderstandings that may arise due to language and cultural differences.
Sourcing companies, on the other hand, work as professional middlemen between the buyers and manufacturers. They have extensive networks of suppliers and can efficiently source the required vacuum forming materials based on the buyer’s specifications and budget. Sourcing companies have expertise in market research and supplier evaluation, ensuring that buyers are connected to reputable and reliable manufacturers.
In summary, agents and sourcing companies play a vital role in facilitating vacuum forming materials purchases from China. Their knowledge of the local market, supplier network, negotiation skills, and logistical support significantly streamline the procurement process. By leveraging their services, buyers can mitigate risks, save time and money, and ensure a successful sourcing experience from China.
Price Cost Research for vacuum forming materials manufacturers Companies in China, use temu.com and 1688.com
In China, there are several manufacturers of vacuum forming materials that can be found on temu.com and 1688.com. These platforms offer a wide range of suppliers and products for various industries.
One of the leading manufacturers is XYZ Plastics Co., Ltd. They specialize in producing high-quality vacuum forming materials such as ABS, PET, PVC, and Polycarbonate sheets. Their products are widely used in the automotive, electronics, and packaging industries. XYZ Plastics Co., Ltd. offers competitive prices and can provide customized solutions to meet specific requirements.
Another reputable manufacturer is ABC Plastics Manufacturing Co., Ltd. They are known for their expertise in producing vacuum forming materials for medical and food-grade applications. Their materials are compliant with international standards and have been approved by regulatory bodies. ABC Plastics Manufacturing Co., Ltd. offers cost-effective solutions without compromising on quality and safety.
Furthermore, DEF Plastics Technology Co., Ltd. is a popular choice for customers looking for environmentally friendly vacuum forming materials. They specialize in producing biodegradable and recyclable materials such as PLA and PHA. DEF Plastics Technology Co., Ltd. ensures that their products meet the highest quality standards while maintaining competitive prices.
Overall, by utilizing temu.com and 1688.com, customers can easily find reputable vacuum forming materials manufacturers in China. These platforms offer a convenient way to compare prices, read customer reviews, and communicate with suppliers. It is recommended to conduct thorough research and select a supplier that best suits the specific requirements and budget.
Shipping Cost for vacuum forming materials import from China
The shipping cost for vacuum forming materials imported from China can vary depending on various factors including the volume of the materials, the weight, the mode of transportation, the distance, and the shipping company selected. Generally, the cheapest shipping option for importing goods from China is by sea.
When importing vacuum forming materials, it is important to consider the volume and weight of the products. Vacuum forming materials are commonly lightweight, so the cost is primarily determined by the volume. Freight charges are usually calculated based on cubic meters (CBM) or cubic feet, depending on the country of destination.
For example, if you are shipping a standard 20-foot container (20ft container) filled with vacuum forming materials from China to the United States, the shipping cost would typically fall between $1,000 to $2,500 USD. However, this cost may vary depending on the specific shipping requirements, such as the departure and arrival ports, and any additional services like customs clearance or insurance. It is advisable to consult with a freight forwarder or shipping company to get an accurate quote.
Additional charges such as customs duties, taxes, and import fees may also apply when importing vacuum forming materials. These charges vary according to the customs regulations of the destination country. It is essential to research and understand the applicable customs procedures and tariffs to avoid any surprises.
To ensure cost-effectiveness, it is recommended to consolidate shipments or consider alternative shipping methods like sea-air or sea-land combinations. Such strategies can help reduce costs and optimize the supply chain.
In conclusion, the shipping cost for importing vacuum forming materials from China depends on several factors, including volume, weight, transportation mode, distance, and additional services required. To accurately determine the cost, it is advisable to consult with shipping companies or freight forwarders and consider alternative shipping options for cost optimization.
Compare China and Other vacuum forming materials Markets: Products Quality and Price,Visible and Hidden Costs
China and other vacuum forming materials markets can be compared in terms of product quality and price, as well as visible and hidden costs.
In terms of product quality, China has gained a reputation for manufacturing a wide range of vacuum forming materials at varying quality levels. While there are many high-quality manufacturers in China, there are also lower-quality producers that may offer cheaper products. On the other hand, other markets, such as Europe and the United States, often have stricter regulations and quality control standards, resulting in generally higher product quality. These markets focus on producing premium vacuum forming materials that meet or exceed international standards.
When it comes to price, China has a competitive advantage due to lower labor and production costs. This results in generally lower prices for vacuum forming materials compared to other markets. However, it is important to note that quality varies, and customers need to evaluate the trade-off between price and quality.
Visible costs, such as the initial product price, transportation, and import duties, can be more favorable in China due to its low manufacturing costs and well-established supply chains. Other markets may have higher visible costs due to stricter regulations and higher labor costs. However, hidden costs should also be considered. These include factors such as quality control inspections, certifications, intellectual property protection, and potential delays caused by longer transportation distances. Other markets may have lower hidden costs since they often have reliable quality control systems and regulations in place, reducing the risk of faulty products and potential legal issues.
In summary, China offers competitive prices due to lower manufacturing costs, but product quality can vary. Other markets usually provide higher-quality vacuum forming materials but at a higher price. Visible costs may be lower in China, but hidden costs related to quality control, certifications, and intellectual property protection can be higher. Ultimately, customers should carefully consider their requirements and priorities to make an informed decision.
Understanding Pricing and Payment Terms for vacuum forming materials: A Comparative Guide to Get the Best Deal
When it comes to purchasing vacuum forming materials, understanding pricing and payment terms is essential to ensure that you get the best deal. This comparative guide will provide you with valuable insights to make an informed decision.
Firstly, it is important to gather information on the various materials available in the market. Vacuum forming materials are typically made from plastic, such as acrylic, ABS, PVC, or polycarbonate. Each material has its unique characteristics, such as flexibility, durability, or heat resistance. Researching and comparing the properties of these materials will help you determine which one suits your needs best.
Once you have identified the preferred material, pricing becomes a crucial factor. The cost of vacuum forming materials can vary based on factors like quantity, thickness, and quality. While purchasing in bulk may help in negotiating better prices, be cautious with the required quantity as you need to ensure that you can adequately utilize the material without incurring wastage.
Additionally, the thickness of the material plays a role in pricing. Thicker materials are generally more expensive due to the higher amount of raw material used. However, keep in mind that opting for a thinner material might compromise the product’s structural integrity and longevity.
Quality is another critical consideration. Higher-quality materials tend to be more expensive compared to lower-quality alternatives. It is advisable to strike a balance between cost and quality to ensure that the material meets your desired specifications and requirements.
When discussing payment terms with suppliers, it is important to inquire about available options. Some suppliers may offer discounts for upfront or bulk payments. Others may provide flexible payment plans, such as installment-based options or credit terms. Understanding these terms will assist in planning your budget and selecting the most feasible payment option.
Additionally, consider the supplier’s reputation, reliability, and customer support when making your decision. A trusted supplier with a strong track record is more likely to offer competitive pricing and favorable payment terms.
To summarize, researching and comparing vacuum forming materials is essential to identify the most suitable option. Evaluating factors like cost, quantity, thickness, and quality will help you make an informed decision. Furthermore, understanding the available payment terms and options offered by suppliers will ensure you obtain the best deal that aligns with your budget and requirements.
Chinese Regulations and Industry Standards Certifications for vacuum forming materials,Import Regulations and Customs for vacuum forming materials from China
In China, vacuum forming materials are subject to various regulations and industry standards certifications to ensure their safety and quality. Manufacturers must comply with these standards to meet the requirements of both domestic and international markets. Some of the important regulations and certifications include:
1. China Compulsory Certification (CCC): This mandatory certification is required for products sold in China. It ensures that vacuum forming materials meet the necessary safety and quality standards. Manufacturers must obtain CCC certification before exporting their products.
2. GB/T Standards: Chinese National Standards, known as GB/T standards, cover a wide range of products and materials, including vacuum forming materials. These standards provide guidelines for dimensions, materials, performance, and quality control, ensuring consistency and quality across the industry.
3. RoHS Compliance: Vacuum forming materials intended for electrical or electronic applications must comply with the Restriction of Hazardous Substances (RoHS) directive. This regulation restricts the use of specific hazardous substances such as lead, cadmium, mercury, and certain flame-retardant materials.
4. ISO Certifications: Manufacturers may also obtain ISO certifications like ISO 9001 (Quality Management System) and ISO 14001 (Environmental Management System) to demonstrate compliance with international standards and enhance their credibility in the market.
Regarding import regulations and customs for vacuum forming materials from China, it is essential to comply with the customs requirements of the importing country. Key considerations include:
1. Import Tariffs: Different countries may impose import duties on vacuum forming materials. Importers should familiarize themselves with the specific tariffs applicable in their country to ensure compliance and factor the additional costs into their import budget.
2. Customs Documentation: Proper documentation is crucial to facilitate the smooth importation of vacuum forming materials. This typically includes commercial invoices, packing lists, certificates of origin, and any required certifications or permits.
3. Product Compliance: Importers must ensure that the vacuum forming materials conform to the regulatory requirements of their country. This may entail verifying certifications, conducting product testing, or obtaining compliance declarations.
4. Customs Brokerage: Engaging a professional customs broker can help navigate the complex import process, ensuring compliance with customs regulations, handling documentation, and facilitating customs clearance.
It is important to note that regulations and import requirements may vary by country and are subject to frequent updates. Consequently, importers should consult with local customs authorities or seek expert advice to ensure accurate and up-to-date information when importing vacuum forming materials from China.
Sustainability and Environmental Considerations in vacuum forming materials Manufacturing
Sustainability and environmental considerations in vacuum forming materials manufacturing are crucial for reducing the negative impacts on the planet and preserving natural resources. Several key aspects should be taken into account during the manufacturing process to ensure sustainability.
Firstly, the choice of materials is of utmost importance. Opting for eco-friendly and sustainable materials can significantly reduce the environmental footprint of vacuum forming manufacturing. Using bioplastics derived from renewable sources, such as corn or sugarcane, instead of traditional petroleum-based plastics, is a viable option. These bioplastics have a lower carbon footprint and reduce the reliance on finite fossil fuel resources.
Secondly, energy consumption during the manufacturing process should be minimized. Implementing energy-efficient technologies and equipment can help reduce greenhouse gas emissions and decrease the overall energy footprint. This includes utilizing energy-saving heating systems, optimizing operating temperatures, and employing efficient machinery.
Furthermore, waste management and recycling play a critical role in sustainable vacuum forming manufacturing. Implementing a comprehensive waste management strategy that includes recycling, reuse, and proper disposal can prevent excessive waste generation and decrease the amount of plastic ending up in landfills or oceans. Recycling programs should be established to handle waste materials, allowing for the incorporation of recycled plastics back into the production cycle.
Water conservation is another important consideration. Implementing water-efficient manufacturing processes, such as closed-loop systems and water recirculation, can reduce the consumption of freshwater resources. Additionally, reusing and treating wastewater can minimize the impact on water supplies and reduce pollution.
Transportation is also a key factor in sustainable vacuum forming manufacturing. Optimal logistics planning and efficient shipping methods can help reduce emissions associated with transportation. Utilizing electric or hybrid vehicles, as well as maximizing cargo loads, can decrease the carbon footprint of transporting materials and finished products.
In conclusion, sustainable and environmentally-friendly practices in vacuum forming materials manufacturing are essential for reducing environmental impact. Choosing sustainable materials, minimizing energy consumption, implementing effective waste management, conserving water, and optimizing transportation can all contribute to a more sustainable and eco-conscious manufacturing process.
List The Evolution history of “vacuum forming materials”
Vacuum forming is a process that has been used for many years to shape and mold a variety of materials. Over time, the materials used in vacuum forming have evolved to suit various applications and enhance the flexibility and functionality of the process.
In the early days, vacuum forming materials primarily consisted of natural substances such as wood and leather. These materials were relatively easy to shape and mold, but they had limitations in terms of durability and resistance to various elements.
As industrialization progressed, engineers and scientists began experimenting with different synthetic materials. In the mid-20th century, thermoforming plastics, such as polyvinyl chloride (PVC) and polystyrene, gained popularity as vacuum forming materials. These plastics offered several advantages, including their affordability, ease of processing, and versatility. They could be molded into various complex shapes and sizes, opening up new possibilities for product design and manufacturing.
However, concerns about the environmental impact of these plastics led to the development of more sustainable vacuum forming materials. Bio-based and biodegradable plastics, including polylactic acid (PLA) and polyhydroxyalkanoates (PHA), emerged as eco-friendly options. These materials are derived from renewable resources and can decompose naturally, reducing their impact on the environment.
Additionally, advancements in technology and material science have led to the development of high-performance thermoplastics for vacuum forming. Materials like acrylics, ABS (acrylonitrile butadiene styrene), and PETG (polyethylene terephthalate glycol) offer improved strength, impact resistance, and chemical resistance. They are widely used in industries such as automotive, aerospace, and medical, where stringent requirements are necessary.
In recent years, engineers have been exploring the use of recycled materials as vacuum forming materials, contributing to sustainable practices and the circular economy. These recycled plastics can maintain their molding properties while reducing waste and environmental impact.
Furthermore, the incorporation of additives and fillers into vacuum forming materials has increased their performance and functionality. Nanocomposites, for example, enhance the strength and lightweight properties of the materials, making them suitable for advanced applications like aerospace components.
In conclusion, the evolution of vacuum forming materials has seen a transition from natural substances to synthetic plastics, bio-based and biodegradable options, high-performance thermoplastics, recycled materials, and advanced composites. These materials continue to evolve as new technologies and environmental concerns reshape the industry.
The Evolution and Market Trends in vacuum forming materials Industry
The vacuum forming materials industry has experienced significant evolution and market trends in recent years. Vacuum forming, also known as thermoforming, is a manufacturing process that shapes plastics into various products using vacuum pressure and heat. It is widely used in industries such as packaging, automotive, electronics, and medical.
One of the main evolution in this industry has been the development of new materials. Traditionally, vacuum forming relied on materials like PVC (polyvinyl chloride) and ABS (acrylonitrile butadiene styrene). However, concerns over environmental impact and sustainability have led to the emergence of biodegradable and recyclable materials. Polylactic acid (PLA), polycarbonate (PC), and high-density polyethylene (HDPE) are some of the innovative materials being used in vacuum forming, offering improved environmental performance without compromising functionality.
Market trends in the vacuum forming materials industry indicate a growing demand for customized and lightweight products. With advancements in technology, manufacturers can now offer highly customized solutions, catering to specific client requirements. This trend is particularly prominent in industries like automotive, where interior components need to be tailored to fit various models.
Another trend in the market is the increasing demand for lightweight materials. As industries strive to reduce weight and enhance fuel efficiency, vacuum forming materials that are lightweight yet durable are in high demand. This is especially relevant for the automotive and aerospace sectors, where every ounce of weight reduction can contribute to significant savings.
Furthermore, aesthetics and design are becoming crucial factors in the industry. Manufacturers are exploring new ways to incorporate textures, patterns, and finishes into vacuum-formed products to enhance their visual appeal. This trend is particularly evident in industries such as consumer goods, where packaging and product presentation play a vital role in attracting customers.
To summarize, the vacuum forming materials industry has evolved by introducing new environmentally friendly materials and focusing on customization, lightweight solutions, and improved aesthetics. These market trends reflect the increasing emphasis on sustainability, individuality, and performance in various industries.
Custom Private Labeling and Branding Opportunities with Chinese vacuum forming materials Manufacturers
Chinese vacuum forming materials manufacturers offer extensive custom private labeling and branding opportunities for businesses looking to establish a unique identity for their products. Through collaborative partnerships, these manufacturers enable companies to customize their packaging, molds, and product designs to reflect their brand image effectively.
With advanced technology and expertise, Chinese manufacturers can develop bespoke packaging solutions that align with a brand’s vision and market positioning. They can produce packaging materials in various sizes, shapes, and colors, providing businesses with ample choices to differentiate their products from competitors. By incorporating logos, taglines, and distinctive artwork onto the packaging, companies can establish a recognizable brand identity that resonates with consumers.
Furthermore, these manufacturers specialize in creating customized molds, which are essential for vacuum forming products. Collaborating with Chinese manufacturers allows businesses to tailor molds to their exact specifications, ensuring the products have the desired shape, size, and functionality. By incorporating unique design elements into the molds, companies can create visually appealing and innovative products that attract consumer attention.
Chinese vacuum forming materials manufacturers also offer branding opportunities through material selection. They provide a wide range of materials, including ABS, PVC, PET, and PP, each with its own properties and characteristics. Businesses can choose materials that align with their brand values and product requirements, ensuring they deliver on quality, durability, and sustainability aspects.
Overall, partnering with Chinese vacuum forming materials manufacturers empowers businesses to leverage custom private labeling and branding opportunities. By collaborating closely with these manufacturers, companies can create distinctive packaging, molds, and product designs that enhance their brand identity and appeal to their target market effectively.
Tips for Procurement and Considerations when Purchasing vacuum forming materials
When purchasing vacuum forming materials for your procurement needs, there are several important considerations to keep in mind. Here are some tips to help you make informed decisions:
1. Material Compatibility: Ensure that the materials you purchase are compatible with the vacuum forming process. Consider factors such as the melting point, flexibility, and thickness to ensure they can withstand the required temperature and pressure levels.
2. Type of Material: Vacuum forming materials come in various types, such as ABS (Acrylonitrile Butadiene Styrene), PVC (Polyvinyl Chloride), PETG (Polyethylene Terephthalate Glycol), and polycarbonate. Each material has its specific attributes and application suitability. Consider factors like durability, transparency, chemical resistance, and desired finish before making a decision.
3. Cost-Effectiveness: Evaluate the cost of the materials in relation to the desired quality and requirements of your vacuum forming project. Compare prices from different suppliers to ensure you are getting competitive rates without compromising on quality.
4. Supplier Reliability: Choose a reputable supplier experienced in providing vacuum forming materials. Look for suppliers who can provide consistent quality, on-time delivery, and have good customer reviews. It is important to establish a reliable supply chain to avoid any interruptions in the procurement process.
5. Environmental Considerations: If sustainability is a priority for your organization, look for vacuum forming materials that are recyclable or made from recycled content. These materials can help reduce your carbon footprint and align with your environmental goals.
6. Testing and Samples: Before making bulk purchases, consider requesting samples from potential suppliers. Conduct tests to evaluate the materials’ performance and suitability for your specific application. This allows you to make a more informed decision, avoiding potential shortcomings and costly rework.
7. Storage and Shelf Life: Some vacuum forming materials might have limited shelf life or require specific storage conditions. Ensure you have appropriate storage facilities available to prevent degradation or loss of performance over time.
By considering these aspects, you can make efficient decisions during the procurement process, ensuring the purchased vacuum forming materials meet your specific requirements in terms of quality, cost-effectiveness, and sustainability.
FAQs on Sourcing and Manufacturing vacuum forming materials in China
Q: What is vacuum forming?
A: Vacuum forming is a manufacturing process that involves heating a plastic sheet and stretching it over a mold to create a desired shape. The process uses vacuum pressure to pull the sheet tightly against the mold.
Q: Why source vacuum forming materials from China?
A: China is known for its vast manufacturing capabilities and cost-effective production. It has a large number of experienced manufacturers who specialize in producing vacuum forming materials. Sourcing from China allows businesses to access a variety of materials, including different types of plastics, at competitive prices.
Q: How can I find reliable vacuum forming material suppliers in China?
A: There are several ways to find reliable suppliers in China. Online platforms such as Alibaba, Global Sources, and Made-in-China.com provide access to a wide range of vacuum forming material suppliers. It is important to thoroughly research and vet potential suppliers, including checking their company profile, product quality, certifications, and customer reviews. Additionally, attending trade shows and exhibitions in China, such as the Canton Fair, can provide opportunities to meet suppliers in person and see their products firsthand.
Q: What are the common vacuum forming materials available in China?
A: China offers a wide range of vacuum forming materials, including ABS, PVC, PET, PP, HDPE, and HIPS. These materials come in various thicknesses, colors, and finishes to suit different manufacturing needs. Some suppliers can also provide custom formulations or specialty materials upon request.
Q: Can I request custom vacuum forming materials from Chinese manufacturers?
A: Yes, many Chinese manufacturers can provide custom vacuum forming material solutions. They often have the capability to develop and produce materials according to specific requirements, such as desired properties, colors, or specific additives. It is important to communicate your exact specifications clearly to ensure a smooth manufacturing process.
Q: What is the usual lead time for vacuum forming material production in China?
A: The lead time for vacuum forming material production in China can vary depending on factors such as the material type, order quantity, complexity, and the manufacturer’s production capacity. On average, it can range from a few days to several weeks. It is advisable to communicate with suppliers in advance to get an accurate estimate of the lead time for your specific order.
Q: Are there any quality control measures in place for vacuum forming materials manufactured in China?
A: Reputable manufacturers in China typically have quality control processes in place to ensure the production of high-quality vacuum forming materials. This may include quality inspections at various stages of production, adherence to international quality standards (e.g., ISO 9001), and the use of reliable testing methods to validate the material’s properties. It is essential to work with trusted suppliers who prioritize quality and can provide quality assurance documentation upon request.
In summary, sourcing vacuum forming materials from China offers access to a diverse range of materials at competitive prices. It is important to thoroughly research and vet suppliers, communicate specific requirements clearly, and ensure that quality control measures are in place to facilitate a successful sourcing and manufacturing process.
Why contact sourcifychina.com get free quota from reliable vacuum forming materials suppliers?
Sourcifychina.com offers free quota from reliable vacuum forming materials suppliers to provide convenience and benefits to its customers. By obtaining a free quota, customers can easily compare and evaluate different suppliers, ultimately making informed decisions regarding their sourcing needs.
There are several reasons why Sourcifychina.com offers this free quota. Firstly, it saves customers valuable time and effort in searching for suitable vacuum forming materials suppliers. Instead of individually contacting multiple suppliers and gathering information, Sourcifychina.com consolidates the process by providing access to a pool of reliable suppliers in one place. This significantly reduces the time and effort required for sourcing activities.
Secondly, by receiving a free quota, customers can obtain a clear understanding of the suppliers’ capabilities, pricing, and terms. This transparent and comprehensive information enables customers to compare different suppliers effectively and make decisions based on their specific requirements. Such knowledge is crucial for ensuring quality control, competitive pricing, and overall customer satisfaction.
Moreover, Sourcifychina.com aims to establish long-term partnerships with its customers. By providing a free quota from reliable suppliers, they demonstrate their commitment to customer success. This gesture helps build trust and confidence among customers, as they can rely on Sourcifychina.com to connect them with reputable suppliers, reducing the risk of scams or low-quality products.
Furthermore, offering a free quota also aligns with Sourcifychina.com’s business model. As a sourcing platform, they earn revenue through commissions or service fees from successful transactions made between customers and suppliers. By assisting customers in sourcing and connecting them with suppliers, they create opportunities for business collaborations, benefiting both parties involved.
In conclusion, receiving a free quota from reliable vacuum forming materials suppliers through Sourcifychina.com brings numerous advantages to customers. It saves time and effort, enables effective supplier comparison, establishes trust, and aligns with the platform’s business model. By simplifying the sourcing process and fostering successful partnerships, Sourcifychina.com aims to enhance customer satisfaction and promote efficient trade between customers and suppliers.