Introduce about injection molding service guide,Qulity,Cost,Supplier,Certification,Market,Tips,FAQ
Injection molding is a widely used manufacturing process for producing plastic parts. This guide provides insights into various aspects of injection molding service, including quality, cost, suppliers, certifications, market trends, tips, FAQs, and more.
Quality is crucial in injection molding, as it determines the durability and functionality of the final product. Many factors influence quality, such as the design, material selection, mold construction, and molding process. High-quality injection molding involves employing precise manufacturing techniques and adhering to stringent quality control measures.
Cost is a critical consideration in injection molding. It depends on several factors, including the complexity of the part, material selection, tooling costs, and production volume. Injection molding offers cost advantages for large production runs due to its ability to efficiently produce a high volume of parts.
Selecting a reliable and experienced injection molding supplier is vital for successful production. Factors to consider include the supplier’s expertise, capabilities, equipment, quality control measures, and turnaround time. It is recommended to work with suppliers who offer integrated services, from design assistance to the production of finished parts.
Certifications play a crucial role in ensuring the quality and reliability of injection molding suppliers. Look for suppliers with certifications such as ISO 9001, which demonstrate their commitment to quality management systems. Other certifications, like ISO 13485 (medical devices) or ISO/TS 16949 (automotive), may be necessary for specific industries.
The injection molding market is continually evolving, driven by advancements in materials, machinery, and manufacturing techniques. With increasing demand for lightweight and sustainable solutions, injection molding is gaining popularity in industries such as automotive, electronics, consumer goods, healthcare, and packaging.
Consider the following tips for successful injection molding projects: invest in proper mold design and maintenance, optimize production parameters, choose suitable materials, and collaborate closely with the chosen supplier.
Frequently asked questions regarding injection molding service cover topics such as the maximum part size, material options, production lead times, mold lifespan, secondary operations, and cost estimation. It is advisable to consult with the supplier to get precise answers tailored to your specific project requirements.
In conclusion, injection molding is a versatile and cost-effective manufacturing process for producing plastic parts. By understanding the key aspects of quality, cost, supplier selection, certifications, market trends, tips, and FAQs, you can make informed decisions and ensure successful injection molding projects.
Types of injection molding service
Injection molding is a widely used manufacturing process that involves injecting molten material into a mold cavity to create products of various shapes and sizes. The process offers several advantages, including high production efficiency, accuracy, and repeatability. There are different types of injection molding services available, each catering to specific needs and requirements.
1. Plastic Injection Molding: This is the most common type of injection molding service and involves the use of thermoplastic materials. Plastic pellets are melted, injected into a mold cavity, and cooled to solidify into the desired shape. It is suitable for producing a wide range of products, including bottles, lids, automotive parts, and consumer goods.
2. Rubber Injection Molding: This type of molding service is specifically designed for producing rubber-based products. It involves injecting liquid silicone rubber or solid rubber compounds into a mold cavity. Rubber injection molding is ideal for producing rubber seals, gaskets, O-rings, and other similar items.
3. Metal Injection Molding: Also known as MIM, this process combines the advantages of plastic injection molding and traditional powdered metallurgy. Fine metal powders are mixed with a binder to form a feedstock, which is then injected into a mold cavity. After the part is formed, it undergoes a debinding and sintering process to remove the binder and achieve the final metal density. Metal injection molding is commonly used for producing complex metal parts with high precision.
4. Ceramic Injection Molding: This type of injection molding service is used to manufacture ceramic components. Ceramic powders are mixed with a binder and injected into a mold cavity. After shaping, the part is subject to a debinding and sintering process to remove the binder and achieve the desired ceramic properties. Ceramic injection molding is widely used in the production of electronic components, medical devices, and aerospace parts.
In conclusion, injection molding services offer a versatile and efficient means of manufacturing products from various materials. Plastic injection molding is the most common, but rubber, metal, and ceramic injection molding services are also available to cater to specific requirements. These processes enable the production of high-quality, complex, and repeatable parts, making injection molding a preferred choice for many industries.
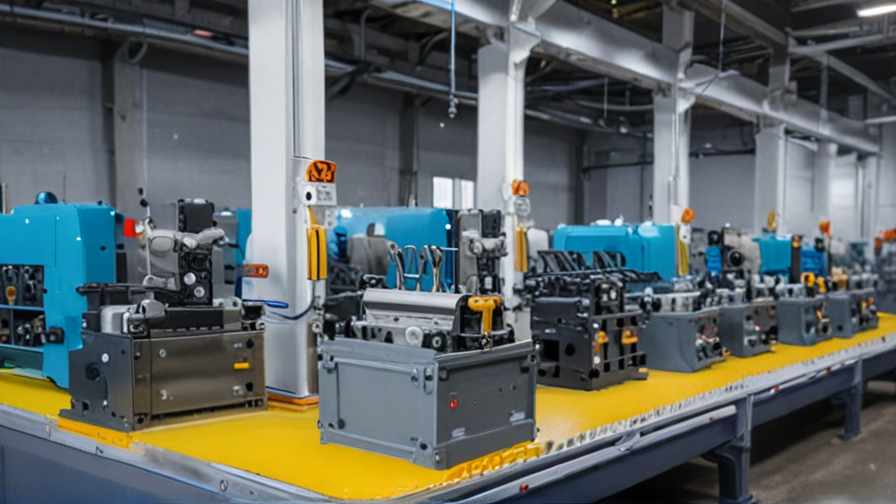
Pros and Cons of Using injection molding service
Pros of Using Injection Molding Service:
1. Cost-effective: Injection molding is a cost-effective manufacturing method for producing large quantities of identical plastic parts. The initial tooling costs can be high, but the per-unit cost decreases significantly with higher production volumes.
2. Efficiency: Injection molding allows for high-speed production, enabling manufacturers to produce thousands of parts in a short time. The process is highly automated, reducing labor costs and increasing overall efficiency.
3. Design flexibility: Injection molding offers great design flexibility, allowing for intricate and complex shapes to be produced. It also enables the incorporation of various features like undercuts, threads, and textures, which would be difficult or impossible to achieve with other manufacturing methods.
4. Material variety: Injection molding works with a wide range of thermoplastic materials, including ABS, polypropylene, polystyrene, nylon, and more. This versatility allows for the production of parts with different characteristics, such as strength, flexibility, transparency, or heat resistance.
5. Consistency and accuracy: Injection molding offers high repeatability and precision, ensuring consistent quality and accuracy in each molded part. The use of computer-controlled machines and precise molds minimizes variations and defects.
Cons of Using Injection Molding Service:
1. High initial costs: Injection molding requires the creation of molds, which can be expensive, especially for complex designs or low-volume production. The tooling costs must be considered before starting production.
2. Lead time: The design and fabrication of molds can take several weeks or even months, increasing the lead time for manufacturing. This may not be suitable for urgent or time-sensitive production needs.
3. Design limitations: While injection molding offers design flexibility, there are certain limitations to consider. For example, thin walls may require additional support, and some complex geometries may be challenging to mold. Design revisions may be necessary to accommodate the manufacturing process.
4. Environmental impact: Injection molding produces waste in the form of scrap plastic material. However, many of these materials can be recycled or reused to minimize environmental impact. Additionally, the energy consumption of the injection molding process should be taken into account.
5. Limited to plastic parts: Injection molding is primarily suited for plastic parts. If other materials like metals or ceramics are required, alternative manufacturing methods may be necessary.
Overall, injection molding offers significant advantages in terms of cost-efficiency, design flexibility, and high-quality production for large quantities of plastic parts. However, the initial costs, lead time, design limitations, and environmental considerations should be carefully evaluated before opting for this manufacturing service.
injection molding service Reference Specifications (varies for different product)
Injection molding is a manufacturing process that involves melting and injecting a molten material into a mold cavity, allowing it to cool and solidify into the desired shape. This manufacturing method is suitable for mass production of complex and intricate parts with high precision and repeatability. Here are some reference specifications that may vary depending on the product being molded.
Material: The choice of material is crucial in injection molding as it affects the performance, durability, and appearance of the final product. Common materials used include thermoplastics, thermosetting polymers, and elastomers.
Mold Design: The design of the mold is critical in achieving the desired product. It should incorporate features like runners, gates, cooling lines, and ejector pins to facilitate the molding process. The mold should also take into account factors such as shrinkage, warpage, and draft angles to ensure the quality and functionality of the final part.
Part Dimensions: The size and shape of the part are defined by the specifications provided. Tight tolerances may be required for certain applications. The design should consider factors like wall thickness, surface finish requirements, and dimensional stability.
Injection Pressure and Temperature: The injection pressure and temperature are significant parameters to achieve optimal mold filling and part quality. The ideal values depend on the material being used and the complexity of the part. A careful balance of pressure and temperature is essential to avoid defects like sink marks, voids, or flash.
Cycle Time: The cycle time is the duration taken to complete one injection molding cycle, including mold filling, cooling, and ejection. Efficient cycle times contribute to higher productivity and cost-effectiveness. Factors such as material characteristics, part complexity, and cooling system design influence the cycle time.
Quality Control: Quality control measures ensure that the molded parts meet the specified requirements. This may include dimensional inspections, visual inspections for defects, mechanical testing, and other quality checks to ensure consistent and reliable part production.
Post-processing: Depending on the product’s requirements, additional operations such as trimming, painting, assembly, or packaging may be necessary. These post-processing steps are determined by the specific product and its intended use.
By considering these reference specifications, injection molding service providers can tailor their processes to suit the unique requirements of each product. The careful selection of materials, design of molds, control of process parameters, and adherence to quality control measures are critical in delivering high-quality molded parts efficiently and economically.
Applications of injection molding service
Injection molding is an essential manufacturing process that involves injecting molten materials into a mold cavity to create various types of products. It is widely used in various industries due to its numerous advantages, including high production efficiency, cost-effectiveness, and the ability to produce complex designs. Here are some applications of injection molding services:
1. Automotive Industry: Injection molding is extensively utilized in the automotive industry to manufacture various components such as interior and exterior trim, dashboards, knobs, buttons, and even entire car body parts. It enables the production of lightweight yet durable components that meet industry standards and regulatory requirements.
2. Packaging Industry: Injection molding is commonly employed for the production of packaging materials, including bottles, caps, lids, trays, and containers. It offers excellent material flow control, allowing the creation of intricate designs with precise dimensions and consistent quality. Furthermore, injection molding facilitates the manufacturing of packaging products with different colors and finishes.
3. Consumer Goods: Injection molding is widely employed in the consumer goods industry for the production of a broad range of items such as toys, electronic casings, appliances, kitchenware, and beauty product containers. The process allows for customization and can accommodate the use of various materials, including plastics, elastomers, and metals, to create products with distinct features and textures.
4. Medical Industry: Injection molding plays a vital role in the medical field by producing medical devices and equipment with high precision and quality. It enables the manufacturing of items like syringes, containers, connectors, and surgical instruments with specific dimensions, sterilization compatibility, and biocompatibility.
5. Electronics Industry: Injection molding is utilized extensively in the electronics industry for the production of casings, enclosures, connectors, and other components of electronic devices. The process can incorporate features such as snap fits, threads, and fine details required for electrical connectors and housings.
6. Aerospace Industry: Injection molding is employed in the aerospace industry to manufacture lightweight, high-strength components for aircraft and spacecraft. These components include interior panels, air ducts, brackets, and electrical connectors.
Overall, injection molding services offer tremendous versatility and reliability, making it an integral manufacturing process for a wide range of industries. Its ability to produce high-quality, consistent, and complex parts quickly and cost-effectively has made it a preferred choice for various applications.
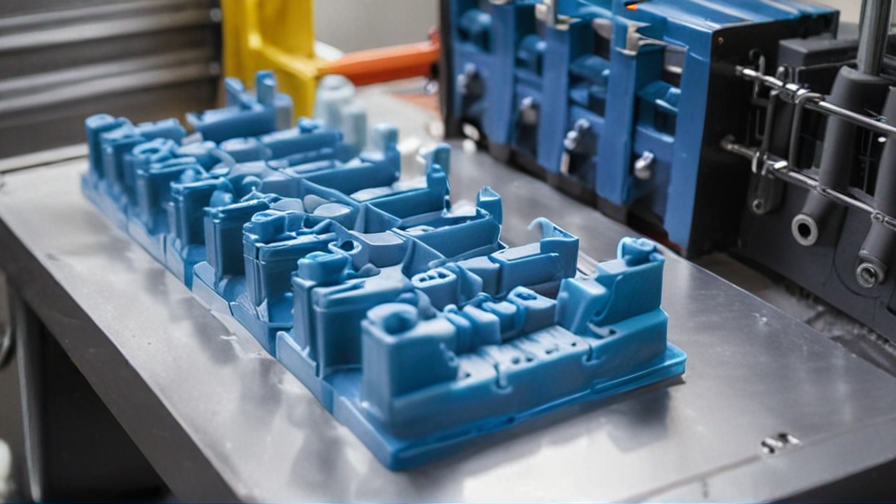
The Work Process and how to use injection molding service
Injection molding is a widely used manufacturing process that involves the creation of plastic parts and products. It is a highly efficient method for mass production and offers a range of benefits such as cost-effectiveness, design flexibility, and production speed.
The work process of injection molding involves several steps. Firstly, a mold or a tool is designed according to the specifications of the desired product. This mold is generally made of steel or aluminum and consists of two halves, which are then clamped together tightly during the production process. The mold is designed to have cavities and channels that will form the shape of the final product and allow the molten plastic to flow efficiently.
The next step is the injection of the plastic material into the mold. The plastic, in the form of pellets or granules, is heated to a molten state and then injected into the mold under high pressure. This pressure ensures that the plastic fills all the cavities and channels of the mold, resulting in a precise and detailed part.
Once the plastic is injected into the mold, it is cooled rapidly. Cooling is a crucial step as it solidifies the plastic and allows it to take the shape of the mold. After cooling, the mold is opened, and the newly formed part is ejected. Depending on the complexity of the mold and part, multiple parts can be produced in a single cycle.
To use injection molding service effectively, it is important to follow certain guidelines. Firstly, proper mold design is crucial for achieving accurate and high-quality parts. It is essential to work closely with the injection molding service provider to ensure that the mold design meets the desired specifications.
Secondly, selecting the right plastic material is key. The choice of material depends on factors such as the desired properties of the final part, its application, and cost considerations. It is necessary to consult with the injection molding service provider to determine the most suitable material for the project.
Lastly, regular communication and collaboration with the injection molding service provider throughout the entire process is essential. This helps in addressing any issues or design changes that may arise and ensures that the final product meets the required standards.
In conclusion, injection molding is a highly efficient manufacturing process for mass production of plastic parts. Understanding the work process and effectively utilizing injection molding service involves proper mold design, material selection, and effective communication with the service provider. By following these guidelines, companies can leverage the benefits of injection molding and achieve high-quality, cost-effective products.
Quality Testing Methods for injection molding service and how to control the quality
Injection molding is a highly popular manufacturing process used to produce high volumes of identical parts. However, to ensure the quality of injection molding services, several testing methods and quality control measures are essential.
One of the most common quality testing methods for injection molding is dimensional inspection. This involves precise measurements of the dimensions of the molded parts using tools such as calipers, micrometers, and laser scanners. By comparing the measurements against the specifications provided by the customer, any deviations or discrepancies can be identified and corrected, ensuring accurate and consistent dimensions.
Another important quality testing method is visual inspection. Trained operators carefully examine each molded part to detect any defects such as surface imperfections, color variations, or visible damages. This inspection ensures that the parts meet the aesthetic requirements specified, ensuring a high-quality product appearance.
In addition to dimensional and visual inspections, functional testing is also performed. This involves testing the molded parts for their intended functionality. For example, if the parts are meant to interlock or fit together, assembly tests can confirm whether they meet the desired standards. This ensures the parts will function properly once they are integrated into the final product.
To control the quality of injection molding, various techniques can be adopted. Firstly, process monitoring and control are crucial. Thermal imaging cameras, pressure sensors, and other monitoring tools are employed to continuously assess and adjust the injection molding process parameters. This ongoing monitoring helps maintain consistent quality and prevent defects.
Secondly, the use of statistical process control (SPC) methods can improve quality control. SPC involves collecting and analyzing data throughout the production process to identify any variations or trends. By identifying deviations from the desired standards, corrective actions can be taken proactively, ensuring consistent quality production.
Furthermore, quality control can be enhanced by implementing a comprehensive quality management system (QMS). A QMS includes procedures, checklists, and documentation to ensure that quality standards are met at each step of the injection molding process. This system helps identify potential issues, initiate preventive measures, and document quality-related information for traceability and continuous improvement.
To summarize, quality testing methods for injection molding encompass dimensional inspections, visual inspections, and functional testing. Quality control is achieved through process monitoring, statistical process control, and the implementation of a comprehensive quality management system. By employing these methods, injection molding services can consistently produce high-quality parts that meet customer specifications.
injection molding service Sample Policy and Post-Purchase Considerations for injection molding service from China
Sample Policy and Post-Purchase Considerations for Injection Molding Service from China:
1. Sample Policy:
Before placing a bulk order for injection molding services from China, it is important to request and evaluate samples. Most manufacturers offer a sample policy, which may include the following considerations:
a) Free or paid samples: Clarify if the manufacturer charges for samples or provides them free of cost. In some cases, manufacturers may offer free samples but charge for shipping.
b) Sample customization: Discuss the possibility of customizing the samples to meet your specific requirements. This will help you evaluate the manufacturer’s ability to fulfill your desired specifications.
c) Delivery time: Inquire about the time it takes for the manufacturer to produce and ship the samples. This will give you an idea of their production capacity and efficiency.
d) Quality assurance: Check if the samples are representative of the manufacturer’s overall product quality. Evaluate the samples for dimensional accuracy, material quality, and finish.
2. Post-Purchase Considerations:
After receiving the samples and deciding to proceed with the injection molding service, the following aspects should be considered:
a) Production timeline: Communicate your desired delivery date and negotiate a clear production timeline with the manufacturer. Ensure they can meet your required deadlines without compromising quality.
b) Quality control: Establish a mechanism to monitor production quality throughout the manufacturing process. This can include onsite inspections, video conferences, or having a representative from your company stationed at the manufacturer’s facility.
c) Packaging and shipping: Discuss packaging requirements to ensure products are protected during transportation. Also, agree on the shipping method, carrier, and any necessary documentation for hassle-free customs clearance.
d) Payment terms and contracts: Clearly define payment terms, such as down payment, milestone payments, and final payment. Consider using an escrow service or a performance bond to secure the transaction. Additionally, draft a comprehensive contract that covers all aspects of the agreement, including intellectual property rights and product warranty.
e) After-sales support: Inquire about the manufacturer’s after-sales support services, such as product maintenance, repair, or replacement policies. Having a reliable support system in place can mitigate potential issues that may arise after the purchase.
By following these sample policies and post-purchase considerations, you can ensure a smooth and successful experience when procuring injection molding services from China.
Sourcing injection molding service from China: Opportunities, Risks, and Key Players
China is a major player in the global injection molding industry and offers numerous opportunities for sourcing this service. With its vast manufacturing capabilities, cost advantages, and skilled labor force, China has become a preferred destination for businesses seeking injection molding services. However, sourcing from China also comes with certain risks that need to be carefully considered.
One of the main opportunities of sourcing injection molding services from China is the cost advantage. Chinese manufacturers often offer competitive pricing due to lower labor and production costs. This allows businesses to save on their manufacturing expenses and remain cost-effective in a highly competitive market.
Additionally, China has a large number of injection molding companies with advanced technology and equipment. They possess the necessary expertise and experience to handle complex projects, large production volumes, and a wide range of materials. This ensures that businesses can find suitable suppliers in China for their specific requirements.
However, there are also risks associated with sourcing injection molding services from China. One major concern is the potential for quality issues. While many Chinese manufacturers adhere to high-quality standards, there is a risk of encountering suppliers who may compromise on quality to reduce costs. To mitigate this risk, businesses should conduct thorough due diligence on potential suppliers, including checking their certifications and inspecting their facilities.
Another risk is the distance and language barriers. Communication with Chinese suppliers can sometimes be challenging due to the language barrier and time zone differences. This can lead to misunderstandings, delays, and difficulties in resolving issues. Utilizing qualified translators and project managers, as well as establishing effective communication channels, can help mitigate these risks.
When it comes to key players in the injection molding industry in China, some prominent companies include Longhua Die-Casting Machine Co. Ltd., Haitian International Holdings Limited, and Bohong Precision Machinery. These companies are known for their high-quality products, technological innovation, and strong market presence. Other notable players include Yizumi Precision Machinery Co. Ltd. and Chen Hsong Holdings Limited.
In conclusion, sourcing injection molding services from China offers significant opportunities in terms of cost advantage and access to skilled manufacturers. However, it is crucial for businesses to carefully evaluate potential risks and take appropriate measures to ensure product quality, effective communication, and successful outcomes.
How to find and select reliable injection molding service manufacturers in China,use google search manufacturers and suppliers
When looking to find and select reliable injection molding service manufacturers in China, using Google search is undoubtedly a helpful tool. By following a few steps, you can narrow down your options and find a trustworthy supplier. Here’s a guide to help you:
1. Begin by searching for relevant keywords on Google, such as “injection molding service China” or “plastic injection molding manufacturers China.” This will provide you with a list of potential suppliers.
2. Visit the websites of different manufacturers and carefully evaluate their information. Look for evident signs of reliability, such as a professional layout, detailed product descriptions, and comprehensive contact information.
3. Check if the manufacturer has certifications, such as ISO 9001 or ISO 13485, which demonstrate their adherence to international quality standards.
4. Look for testimonials or case studies on the manufacturer’s website. Positive feedback and successful projects indicate their capability to fulfill your requirements.
5. Examine their production capabilities and capacity. Ensure that the manufacturer has the necessary equipment, facilities, and expertise to handle your project and desired order quantity.
6. Verify the manufacturer’s experience in your specific industry or product category. Established manufacturers with relevant expertise are more likely to deliver satisfactory results.
7. Search for online reviews or ratings from independent sources. Websites like Alibaba, Made-in-China, or global sourcing platforms often have user reviews that can help gauge the manufacturer’s reputation.
8. Contact the manufacturer directly and ask for references or past customer testimonials. Speak to their existing clients to gain insights into their performance, quality, and responsiveness.
9. Request samples of their previous work to assess the quality standards they maintain.
10. Obtain detailed quotes from multiple manufacturers and compare their prices, lead times, and services offered. Select the one that provides the best value for your specific requirements.
Remember that communication is crucial throughout the process. Consider language proficiency, responsiveness, and clear communication when selecting a manufacturer, as these factors greatly impact project success.
In summary, by utilizing Google search, meticulously evaluating websites, verifying certifications, considering reviews, and engaging in direct communication, you can effectively find and select reliable injection molding service manufacturers in China.
How to check injection molding service manufacturers website reliable,use google chrome SEOquake check if ranking in top 10M
When checking the reliability of an injection molding service manufacturer’s website, here’s a simple process using Google Chrome and SEOquake:
1. Install SEOquake: Add the SEOquake extension to your Google Chrome browser. This tool provides comprehensive SEO-related information about websites.
2. Search for the manufacturer: Enter the name of the injection molding service manufacturer in the Google search bar.
3. Check the organic ranking: Once the search results are displayed, look for the manufacturer’s website and check its organic ranking. SEOquake will display the website’s position in the search results. If the website ranks within the top 10 million, it indicates that it has a reasonable level of online visibility.
4. Evaluate the website’s appearance: Open the manufacturer’s website and evaluate its design, structure, and overall appearance. A reliable website will generally have a professional and user-friendly layout, with clear navigation and high-quality images.
5. Check for relevant information: Pay attention to the information provided on the website. Identify if they have detailed descriptions of their injection molding services, their capabilities, certifications, and any other relevant details. Reliable manufacturers will often have comprehensive and transparent information available.
6. Look for a physical address and contact information: A trustworthy manufacturer will have a physical address, phone number, and email address listed on their website. Make sure these details are easily visible and functional.
7. Check for certifications and quality assurance: Reliable manufacturers often showcase their certifications, quality control measures, and industry affiliations on their website. Look for these indicators to ensure they adhere to high standards.
8. Consider customer reviews and testimonials: Look for customer reviews or testimonials on the manufacturer’s website or through external sources. Positive reviews can indicate the company’s reliability and customer satisfaction.
9. Assess responsiveness: Contact the manufacturer through the provided contact information or inquiry form and assess their responsiveness. A reliable manufacturer will typically respond promptly and professionally to customer inquiries.
Remember to use your judgment and consider other sources of information when evaluating the reliability of an injection molding service manufacturer. The steps outlined above can provide a starting point in determining the credibility of their website.
Top 10 injection molding service manufacturers in China with each 160 words introduce products,then use markdown create table compare
1. Foxconn Technology Group is a leading injection molding service manufacturer in China. They specialize in providing high-quality plastic injection molding solutions for a wide range of industries, including electronics, automotive, medical devices, and consumer goods. Foxconn is known for their advanced manufacturing capabilities and cutting-edge technologies, ensuring precise product specifications and efficient production processes.
2. Flex Ltd. is another prominent injection molding service manufacturer in China. They offer integrated design and manufacturing services, including plastic injection molding, to industries like automotive, medical, and consumer electronics. Flex focuses on delivering high-quality products, adhering to strict quality control measures and utilizing innovative technologies for efficient production.
3. Jabil Inc. is a global manufacturing solutions provider operating in China. Their injection molding services cater to various industries such as healthcare, automotive, and consumer electronics. Jabil’s expertise lies in precision injection molding, enabling them to produce complex components with tight tolerances and superior quality standards.
Below is a comparison of the top 3 injection molding service manufacturers in China:
|Molding Manufacturer|Specializations|Core Competencies|Quality Assurance|
|—|—|—|—|
|Foxconn Technology Group|Electronics, automotive, medical devices, consumer goods|Advanced manufacturing technologies, precision molding, efficient production processes|Strategic quality control measures, ensuring product specifications are met|
|Flex Ltd.|Automotive, medical, consumer electronics|Integrated design and manufacturing services, high-quality products|Strict adherence to quality control measures, utilization of innovative technologies|
|Jabil Inc.|Healthcare, automotive, consumer electronics|Precision injection molding, complex component production|Stringent quality standards and testing procedures|
It is important to note that there are several other reputable injection molding service manufacturers in China, each with their own unique specializations and core competencies. The selection of a suitable manufacturer depends on specific project requirements, budget constraints, and quality expectations.
Background Research for injection molding service manufacturers Companies in China, use qcc.com archive.org importyeti.com
When it comes to injection molding service manufacturers in China, several platforms can be utilized for background research. Qcc.com, archive.org, and importyeti.com are three useful tools to gather relevant information about these companies.
Qcc.com is a prominent platform that provides comprehensive company data in China. It offers detailed business profiles, financial information, and contact details of various companies. By using Qcc.com, researchers can gather information about injection molding service manufacturers, such as company registration details, legal status, and key personnel. This platform helps to establish the credibility and legitimacy of the manufacturers under consideration.
Archive.org is an invaluable resource for accessing historical data and website archives. Researchers can find past versions of a manufacturer’s website, allowing them to track changes in the company’s offerings, capabilities, and expertise over the years. Analyzing this data can provide insights into the manufacturer’s growth and development, as well as assess their consistency and reliability.
Importyeti.com provides additional information on manufacturers in China by examining import records and shipment data. This platform enables researchers to determine the export activities of injection molding service manufacturers, the countries they ship to, and the quantity and frequency of their shipments. Such data can help evaluate the manufacturer’s international reputation and customer base.
In conclusion, conducting background research on injection molding service manufacturers in China using platforms like qcc.com, archive.org, and importyeti.com can provide valuable insights into a company’s profile, history, and export activities. The combination of these platforms allows researchers to assess a manufacturer’s credibility, track their growth, and analyze their international presence.
Leveraging Trade Shows and Expos for injection molding service Sourcing in China
Trade shows and expos provide excellent opportunities for sourcing injection molding services in China. These events bring together industry professionals, suppliers, and manufacturers in one place, making it easier to connect with potential suppliers and explore new business opportunities.
When attending trade shows and expos, it is important to have a clear sourcing strategy in mind. Here are some tips to leverage these events for injection molding service sourcing in China:
1. Research and select relevant trade shows: Identify trade shows and expos that specifically focus on plastic products, molding, or manufacturing industry. These events attract a wide range of injection molding service providers, giving you ample choices to explore.
2. Plan and prepare: Before attending the event, set clear objectives and create a checklist of specific criteria you seek in an injection molding service provider. Do some background research on potential suppliers you want to meet and have a list of questions ready to assess their expertise and capabilities.
3. Networking and building relationships: Trade shows provide an opportunity to meet suppliers face-to-face and build relationships. Engage in conversations with suppliers, ask for their portfolio, discuss production capabilities, quality control measures, and lead time. Networking also helps in establishing rapport and gaining an understanding of each supplier’s commitment to customer satisfaction.
4. Attend seminars and conferences: Trade shows often offer seminars and conferences addressing industry trends, technological advancements, and market insights. Attending these sessions can provide valuable knowledge and help in identifying potential injection molding service providers with a competitive edge.
5. Evaluate samples and prototypes: Many suppliers showcase their products and prototypes at trade shows. Take the opportunity to evaluate the quality of their work by inspecting samples. This allows you to assess their manufacturing capabilities, precision, and the suitability of their products to meet your requirements.
6. Follow-up and due diligence: After the event, follow up with the potential suppliers you connected with. Request comprehensive quotations, share detailed specifications, and discuss terms and conditions. Conduct due diligence by verifying their credentials, checking references, and visiting manufacturing facilities if possible.
Overall, trade shows and expos provide a concentrated platform for injection molding service sourcing in China. By following a strategic approach, networking, and evaluating options, you can find reliable suppliers and establish strong partnerships for your injection molding needs.
The Role of Agents and Sourcing Companies in Facilitating injection molding service Purchases from China
Agents and sourcing companies play a crucial role in facilitating injection molding service purchases from China. These intermediaries act as a bridge between foreign buyers and Chinese manufacturers, aiding in the smooth and efficient purchase process. Here is an overview of their role in this context.
Firstly, agents and sourcing companies have extensive knowledge and experience in the Chinese market. They have established relationships and networks with numerous injection molding manufacturers, allowing them to identify the most suitable suppliers based on the buyer’s requirements. These intermediaries are aware of the capabilities, expertise, and quality of the manufacturers, ensuring that the buyer receives the best possible service.
Additionally, agents and sourcing companies provide valuable assistance in supplier selection and negotiation. They thoroughly evaluate and verify potential manufacturers, taking into account factors such as production capacity, equipment, certifications, and previous client feedback. With their expertise, they can effectively negotiate favorable terms with the chosen supplier, including pricing, quality standards, timelines, and intellectual property protection.
Furthermore, these intermediaries offer essential support in language and cultural barriers. They act as translators and interpreters, ensuring effective communication between the buyer and the Chinese manufacturer. As they understand the local customs and business practices, agents and sourcing companies can bridge cultural gaps and establish trusting relationships.
Moreover, agents and sourcing companies take responsibility for quality control and inspection. They conduct regular visits to the manufacturer’s facilities to monitor the production process, ensure compliance with specifications, and rectify any issues promptly. This minimizes the risk of substandard products and helps maintain the desired quality standards.
Lastly, agents and sourcing companies handle logistics and shipping arrangements. They coordinate transportation, customs clearance, and documentation, making the buyer’s purchase process hassle-free. By leveraging their expertise in international trade, these intermediaries accelerate delivery times and reduce potential delays or complications.
In conclusion, agents and sourcing companies play a vital role in facilitating injection molding service purchases from China. Their market knowledge, supplier selection expertise, negotiation skills, language and cultural proficiency, quality control oversight, and logistics assistance are instrumental in ensuring a smooth and successful purchase process from start to finish.
Price Cost Research for injection molding service manufacturers Companies in China, use temu.com and 1688.com
In China, there are several online platforms that can be used for price cost research on injection molding service manufacturers. Two popular platforms to consider are temu.com and 1688.com.
Temu.com is a comprehensive sourcing platform that provides access to a wide range of suppliers across various industries. It allows users to search for injection molding service manufacturers in China, ensuring access to a large pool of potential suppliers. The platform offers detailed company profiles, product catalogs, and pricing information to assist in the decision-making process. It also provides communication tools to facilitate direct interactions with suppliers and negotiate pricing.
1688.com, on the other hand, is a leading online business-to-business platform owned by Alibaba Group. It functions similarly to its international counterpart, Alibaba.com, but primarily caters to the Chinese market. 1688.com offers extensive listings of injection molding service manufacturers in China, allowing users to efficiently compare prices and services. The platform includes various features such as product filters, supplier ratings, and inquiry systems to simplify the sourcing process. Additionally, it provides comprehensive transaction services, including secure payment systems and buyer protection policies.
When using these platforms for price cost research, it is important to leverage their search functions and filters to narrow down the options based on specific requirements. Evaluating supplier profiles, reviews, and certifications can help ensure the reliability and quality of services. Communicating with the shortlisted manufacturers through the provided tools will enable further discussions on pricing, customization options, and delivery terms. It is also advisable to compare prices across multiple manufacturers and consider factors like production capacity, lead time, and their ability to accommodate different order sizes.
In conclusion, temu.com and 1688.com are valuable resources when conducting price cost research for injection molding service manufacturers in China. These platforms offer extensive supplier databases, convenient search features, and tools for direct communication and negotiation. By utilizing these platforms effectively, businesses can make informed decisions and find the most suitable manufacturers to meet their injection molding needs.
Shipping Cost for injection molding service import from China
When importing injection molding services from China, the shipping cost can be influenced by several factors. These include the weight and dimensions of the products, the shipping method chosen, and the destination.
For lighter and smaller injection molded parts, air freight can be a viable option. This shipping method is generally faster but can be more expensive, especially for larger quantities. On the other hand, for larger and heavier shipments, sea freight might be a more cost-effective choice. While it takes longer, it can handle bulk orders at a lower rate.
To determine the precise shipping cost, it is essential to consider the Incoterms agreed upon with the supplier. The most commonly used terms are FOB (Free on Board) and CIF (Cost, Insurance, and Freight). With FOB, the buyer takes responsibility for shipping costs and arrangements, while with CIF, the supplier handles the shipping and includes the cost in the product’s price.
Additionally, extra expenses might occur, such as customs duties, import taxes, and handling fees. These costs vary depending on the destination country and the specific product being imported. It is crucial to research and account for these fees to accurately calculate the total shipping cost.
To mitigate shipping expenses, it is advisable to consolidate orders, as larger shipments typically have lower shipping costs per unit. Moreover, working with an experienced freight forwarder or shipping agent can ensure smooth transportation and assist in optimizing shipping costs.
Although providing an exact shipping cost is not possible without specific details, estimating the freight expense for importing injection molding services from China can help in planning and budgeting. Considering factors like product size, weight, shipping method, Incoterms, and additional charges, importers can get an approximate idea of the shipping cost and make informed decisions while staying within their budget.
Compare China and Other injection molding service Markets: Products Quality and Price,Visible and Hidden Costs
China is known for being one of the leading injection molding service markets in the world. When comparing the Chinese market to other injection molding service markets, several factors should be considered, including product quality, price, visible and hidden costs.
In terms of product quality, China has made significant progress in recent years. Many Chinese injection molding companies now possess advanced machinery and technologies, allowing for the production of high-quality products that meet international standards. However, it is still essential for buyers to verify the reputation and certifications of the specific Chinese manufacturer they are interested in, as product quality can vary. Other injection molding service markets, primarily in developed countries such as the United States, Germany, and Japan, are known for their stringent quality control measures, resulting in consistently high-quality products.
Price is a significant factor in injection molding service markets. China is often the preferred choice for buyers due to its competitive pricing. The lower labor costs and higher production efficiencies in China allow for cost-effective manufacturing. However, other injection molding service markets may have higher production costs due to factors such as higher labor wages, stricter regulations, and more expensive raw materials. As a result, products from these markets tend to have higher price tags.
Visible costs, such as manufacturing and material costs, can easily be compared among different injection molding service markets. However, hidden costs must also be considered, specifically transportation, customs, and logistics costs. These costs can impact the overall price of products, and each market may have different advantages or disadvantages. Chinese injection molding service markets have an advantage due to their extensive transportation and logistics networks, allowing for relatively low shipping costs. Still, other markets may offer quicker delivery times or more straightforward customs procedures, reducing hidden costs.
In conclusion, China’s injection molding service market has made significant strides in terms of product quality and remains competitive in terms of pricing. However, other injection molding service markets in developed countries may have an advantage in terms of product quality due to their stringent quality control measures. Price-wise, China’s lower labor costs and higher production efficiencies make it an attractive option, but hidden costs such as transportation and customs should also be considered. Ultimately, the choice of market will depend on the specific requirements and priorities of the buyer.
Understanding Pricing and Payment Terms for injection molding service: A Comparative Guide to Get the Best Deal
When it comes to injection molding services, understanding pricing and payment terms is crucial to ensure you get the best deal possible. This comparative guide aims to provide insightful information within 300 words to assist you in navigating this process effectively.
Pricing for injection molding services can vary significantly, depending on several factors. These factors include the complexity of the part design, the type and quantity of material, the expected production volume, and any additional services or features required. It is essential to communicate your specific requirements to the molding service provider to obtain accurate pricing estimates.
Payment terms typically involve a combination of upfront costs, tooling fees, and production payments. Upfront costs cover the initial setup, including mold design and fabrication. Tooling fees cover the cost of creating the mold, which is a one-time expense. Production payments are based on the volume of parts produced and are typically billed either per part or per production run.
To get the best deal on injection molding services, consider obtaining quotes from multiple providers. This allows you to compare pricing and payment terms to find the most cost-effective option for your project. However, it is important to balance price with quality and reliability. Choosing the lowest-priced service without considering the provider’s expertise, equipment capabilities, and customer reviews may result in subpar products and delayed timelines.
Additionally, be wary of hidden costs that may arise during the process. Ask potential providers about additional fees, such as post-molding finishing, quality control inspections, and shipping expenses. Understanding these potential expenses upfront can help you accurately evaluate different offers and avoid unexpected surprises later on.
To summarize, understanding pricing and payment terms for injection molding services involves considering factors such as part complexity, material type, production volume, and additional services required. Obtaining quotes from multiple providers and comparing them based on price, quality, and reliability is key. It is essential to clarify hidden costs and ask about additional fees to accurately evaluate offers. With this knowledge, you can confidently negotiate pricing and payment terms to secure the best deal for your injection molding project.
Chinese Regulations and Industry Standards Certifications for injection molding service,Import Regulations and Customs for injection molding service from China
Chinese Regulations and Industry Standards Certifications for injection molding service are essential factors to consider when outsourcing injection molding services from China. These regulations and certifications ensure the quality and safety of the products and the compliance of manufacturing processes with international standards.
One of the main certifications for injection molding services in China is the ISO 9001 certification. This certification guarantees that the manufacturer follows a set of quality management principles, including a strong customer focus, involvement of top management, a process approach, and continuous improvement.
Additionally, the Chinese government has implemented strict regulations for the injection molding industry to ensure environmental protection. The Environmental Impact Assessment (EIA) is a mandatory certification that assesses the potential impact of injection molding operations on the environment. This certification verifies that the manufacturer complies with environmental regulations and properly manages waste disposal and emissions.
Import Regulations and Customs for injection molding services from China should also be considered to avoid any potential problems. It is important to ensure compliance with the regulations of the importing country. Some common import regulations include product safety standards, labeling requirements, and customs duties.
When importing injection molding services from China, it is crucial to understand the customs procedures and requirements. These may include completing customs declarations, providing necessary documentation such as commercial invoices and bills of lading, and paying import duties and taxes. Importers should also be aware of any specific regulations related to the injection molding industry and consult with customs authorities or import experts if needed.
In conclusion, Chinese Regulations and Industry Standards Certifications are crucial when considering injection molding services from China. Compliance with these regulations ensures quality, safety, and environmental sustainability. Additionally, understanding import regulations and customs procedures is essential for a smooth and successful importation process. Careful consideration of these factors will help in selecting reliable and compliant injection molding service providers from China.
Sustainability and Environmental Considerations in injection molding service Manufacturing
Injection molding is a widely used manufacturing process for the production of plastic parts. However, the process of injection molding also has a significant impact on the environment. Therefore, it is crucial for injection molding service providers to consider sustainability and environmental factors in their operations.
One important aspect of sustainability in injection molding is the choice of materials. As plastic parts are produced using injection molding, it is essential to select materials that are eco-friendly and have a lower environmental footprint. Biodegradable and recyclable plastic materials should be preferred over conventional plastics to reduce waste and promote a circular economy.
Another consideration is energy consumption. Injection molding requires the use of energy, mainly in the form of electricity, to melt the plastic and operate the machinery. Manufacturers can adopt energy-efficient technologies, such as high-performance heaters and advanced control systems, to minimize energy consumption during the injection molding process. Additionally, utilizing renewable energy sources, like solar or wind power, can further reduce the environmental impact of the manufacturing process.
Waste management is also crucial in injection molding. Inefficient production processes can lead to excessive scrap and waste. By implementing lean manufacturing principles and optimizing production layouts, manufacturers can minimize waste generation and improve material efficiency. Additionally, implementing recycling programs and reusing scrap materials are effective ways to reduce waste disposal and promote a more sustainable approach.
Furthermore, injection molding service providers should prioritize proper disposal and treatment of hazardous substances. Chemicals used during the manufacturing process, such as cleaning agents and mold release agents, should be handled and disposed of according to strict environmental regulations to prevent pollution and protect the ecosystem.
Lastly, injection molding companies should consider the overall life cycle of their products. This includes assessing the environmental impact not only during manufacturing but also during product use and end-of-life disposal. Designing products for easy disassembly and recycling can facilitate the recovery of valuable materials, reduce waste generation, and improve the overall sustainability of injection molding operations.
In summary, sustainability and environmental considerations in injection molding service manufacturing involve selecting eco-friendly materials, optimizing energy consumption, managing waste effectively, handling hazardous substances properly, and considering the entire life cycle of products. By incorporating these practices, injection molding service providers can minimize their environmental footprint and contribute to a more sustainable future.
List The Evolution history of “injection molding service”
Injection molding, a widely used manufacturing process, has evolved significantly since its inception in the late 19th century. The history of injection molding service can be traced through several key milestones that have shaped the industry over time.
1. 1872: The first injection molding machine was patented by John Wesley Hyatt and his brother Isaiah. It used a plunger to inject a synthetic material known as celluloid into a mold. Although this early machine had limited capabilities and produced simple products, it laid the foundation for future advancements.
2. 1926: The first fully automatic injection molding machine was developed by German engineer Heinrich Kühn. This machine incorporated a screw mechanism, which greatly improved the efficiency and accuracy of the injection molding process. It enabled the production of more complex parts on a larger scale.
3. 1946: American inventor James Watson Hendry built the first screw injection molding machine that used a reciprocating screw. This innovation allowed for better control of the injection speed and pressure, resulting in higher quality products. Hendry’s machine formed the basis for modern-day injection molding technology.
4. 1950s: Plastics became increasingly popular in various industries, leading to advancements in injection molding techniques. Hot runner systems were introduced, eliminating the need for runners and allowing for more efficient use of material. Additionally, new materials such as polyethylene and polypropylene opened up new possibilities for injection molding applications.
5. 1970s: Computerized numerical control (CNC) technology revolutionized the injection molding process. With CNC systems, operators could program precise control over the machine’s parameters, resulting in improved part quality and consistency. This era also saw the introduction of robots in injection molding, automating various tasks such as part removal and assembly.
6. 1980s and beyond: Injection molding continued to evolve with the advent of computer-aided design (CAD) and computer-aided manufacturing (CAM) software. These tools allowed for more intricate part designs and enhanced process simulations, reducing the need for costly trial and error. Additionally, advancements in mold materials, cooling systems, and mold flow analysis further improved the quality and efficiency of injection molding services.
Today, injection molding services have evolved into highly sophisticated, precise, and efficient processes. From its humble beginnings as a manual plunger-based technique, injection molding has embraced automation, computer control, and advanced materials to become a fundamental manufacturing method across various industries, including automotive, electronics, medical, and consumer goods.
The Evolution and Market Trends in injection molding service Industry
The injection molding service industry has witnessed significant evolution and market trends over the years. Injection molding is a manufacturing process that involves injecting molten material into a mold to create a wide range of plastic products. Here, we will discuss the evolution and market trends that have shaped this industry.
Evolution:
1. Technological advancements: The injection molding industry has seen major advancements in technology, including the development of computer-aided design (CAD) software, 3D printing, and robotic automation. These technologies have improved the efficiency and precision of the injection molding process, leading to faster production and higher-quality products.
2. Material innovation: The introduction of new materials, such as bioplastics and composite materials, has expanded the possibilities in injection molding. These materials offer improved strength, sustainability, and aesthetics, allowing manufacturers to create innovative and eco-friendly products.
Market Trends:
1. Growing demand in automotive and packaging industries: The automotive industry extensively utilizes injection molding for the production of components like dashboards, bumpers, and interior trims. Similarly, the packaging industry relies on injection molding for manufacturing bottles, caps, and containers. As these sectors continue to grow, the demand for injection molding services is expected to rise.
2. Customization and personalization: With consumer preferences shifting towards unique and personalized products, injection molding companies are adapting to meet this demand. Manufacturers now offer customization options, enabling customers to design their own products or tailor existing designs to suit their specific needs. This trend has led to increased customer satisfaction and market competitiveness.
3. Sustainability and recycling: As the focus on sustainable practices and circular economy principles increases, the injection molding industry is embracing environmentally friendly solutions. There is a growing demand for recycled plastics and biodegradable materials in injection molding. Manufacturers are adopting recycling technologies and incorporating sustainable materials into their processes to meet these demands.
4. Shift towards localized production: In recent years, there has been a growing trend towards localized production and shorter supply chains. Injection molding services are being sought closer to consumer markets to reduce transportation costs, time, and environmental impact. This trend is expected to continue, leading to the establishment of more localized injection molding facilities worldwide.
In summary, the injection molding service industry has evolved through technological advancements and material innovation. Market trends include increased demand in automotive and packaging sectors, a focus on customization and personalization, sustainability and recycling initiatives, and a shift towards localized production. By adapting to these trends, injection molding companies can stay competitive and meet the evolving needs of their customers.
Custom Private Labeling and Branding Opportunities with Chinese injection molding service Manufacturers
Chinese injection molding service manufacturers offer a wide range of custom private labeling and branding opportunities for businesses. With their expertise in injection molding technology, these manufacturers can help businesses create custom products that are unique and tailored to their brand identity.
One of the main advantages of working with Chinese injection molding service manufacturers is their ability to offer cost-effective solutions. They have access to advanced machinery and technology, allowing them to produce high-quality products at competitive prices. This makes it easier for businesses to incorporate private labeling and branding into their products without exceeding their budgets.
Chinese manufacturers also provide a wide range of customization options. They can help businesses design molds and create products in different shapes, sizes, colors, and materials to meet their specific branding requirements. This level of customization ensures that the final products align with the brand’s aesthetic and messaging.
Moreover, Chinese injection molding service manufacturers have experience working with various materials, such as plastics and metals. This versatility enables businesses to explore different options for their branded products, ensuring that they can select the most suitable material for their specific branding needs.
Furthermore, Chinese manufacturers are well-equipped to handle large production volumes. They have the capacity to meet high-volume orders, making them an ideal partner for businesses looking to scale up their operations. This scalability allows businesses to maintain brand consistency across their product range, even as they expand.
In summary, Chinese injection molding service manufacturers offer businesses valuable opportunities for custom private labeling and branding. Their cost-effective solutions, customization options, expertise in different materials, and ability to handle large production volumes make them an ideal partner for businesses looking to create unique and branded products.
Tips for Procurement and Considerations when Purchasing injection molding service
When considering purchasing injection molding services, there are several important factors to keep in mind to ensure a successful procurement process:
1. Quality Assurance: Consider the supplier’s track record for quality control, their certifications, and experience with the materials and processes you require. Look for suppliers who have a robust quality management system in place.
2. Cost: Obtain multiple quotes from different suppliers to ensure competitive pricing. However, while cost is important, it should not be the sole determining factor. Balancing cost with quality is key.
3. Capacity and Lead Time: Evaluate the supplier’s production capacity and lead times to ensure they can meet your requirements within your desired time frame. This is particularly crucial for time-sensitive projects.
4. Communication and Collaboration: Look for suppliers who prioritize open and clear communication. Regular updates, responsiveness, and willingness to work collaboratively are vital to maintaining a strong relationship throughout the procurement process.
5. Materials and Processes: Check if the supplier has experience and expertise in working with the specific materials and processes required for your project. Ask for samples or visit their facility to assess the quality of their work.
6. Tooling and Equipment: Inquire about the supplier’s tooling capabilities, machinery, and equipment. Modern and well-maintained equipment is likely to yield better results and minimize production delays.
7. Sustainability: Consider the supplier’s commitment to sustainability. Look for partnerships with suppliers that prioritize environmentally-friendly practices, recycling, and waste reduction initiatives.
8. Intellectual Property Protection: Evaluate the supplier’s protocols for safeguarding intellectual property rights and confidential information to ensure your project’s confidentiality is protected.
9. Supplier Stability and Longevity: Assess the supplier’s financial stability and longevity in the industry. A stable supplier is more likely to have the resources and expertise to meet your long-term needs.
10. References and Feedback: Request references and check reviews or testimonials from previous customers. This will provide insights into their customer service, reliability, and overall satisfaction with the supplier.
By considering these factors, businesses can make informed decisions when selecting an injection molding service provider, setting the stage for a successful partnership in procuring high-quality products.
FAQs on Sourcing and Manufacturing injection molding service in China
Q: What is injection molding?
A: Injection molding is a manufacturing process used to produce parts by injecting molten material into a mold. The molten material is typically a thermoplastic or thermosetting polymer that is melted and then cooled to form the desired shape.
Q: Why source injection molding services in China?
A: China has become a leading destination for sourcing injection molding services due to several factors. Firstly, Chinese manufacturers have advanced equipment and technology, allowing for high-quality production. Secondly, labor costs in China are relatively lower compared to other countries, resulting in cost-effective manufacturing. Additionally, China has a well-established supply chain and a vast network of suppliers, making it easier to source raw materials. Lastly, many Chinese manufacturers have experience in working with international clients and can provide efficient communication and logistical support.
Q: How to find a reliable injection molding manufacturer in China?
A: When sourcing injection molding services in China, it is essential to conduct thorough research and due diligence. Start by searching for manufacturers that specialize in injection molding and have a good reputation. Review their website, check their certifications, and read customer reviews. It is advisable to request samples or visit the manufacturer’s facility if feasible. Communication is key; ensure the manufacturer can effectively understand your requirements and provide timely updates. It is also important to clarify pricing, lead times, and quality control measures before proceeding with the manufacturing process.
Q: How to ensure quality control in injection molding manufacturing?
A: Quality control in injection molding manufacturing can be ensured by working with manufacturers who have strict quality control procedures in place. This may include the use of advanced inspection equipment, such as coordinate measuring machines (CMMs), ensuring dimensional accuracy. Manufacturers should also conduct regular inspections during the production process, checking for any defects or inconsistencies. Additionally, they should be willing to provide quality control reports and certifications upon request.
Q: What are the advantages and challenges of sourcing injection molding services in China?
A: The advantages of sourcing injection molding services in China include lower labor costs, advanced technology, a vast supplier network, and efficient communication. However, challenges may arise due to potential language barriers, cultural differences, longer lead times for international shipping, and the need to ensure intellectual property protection. Overcoming these challenges can be achieved through effective communication, thorough due diligence, and legal agreements to protect intellectual property rights.
Overall, by carefully selecting a reliable injection molding manufacturer in China, businesses can benefit from cost-effective manufacturing and high-quality production.
Why contact sourcifychina.com get free quota from reliable injection molding service suppliers?
Sourcifychina.com is a platform that connects businesses with reliable injection molding service suppliers in China. They offer a unique benefit of providing a free quota to businesses looking to source injection molding services. This is advantageous for several reasons.
Firstly, obtaining a free quota allows businesses to evaluate the cost and feasibility of their injection molding projects without any financial commitment. This helps in making informed decisions regarding budgeting and sourcing strategies. By receiving multiple quotes from different suppliers, companies can compare prices, production capabilities, and lead times, allowing them to choose the most suitable supplier for their specific needs.
Secondly, the reliability of the injection molding service suppliers on Sourcifychina.com ensures high-quality end products. The platform has a rigorous vetting process for suppliers, carefully screening them for their manufacturing capabilities, quality control measures, and industry certifications. This ensures that only reputable suppliers are listed on the platform, offering businesses peace of mind when choosing a supplier for their injection molding projects.
Moreover, Sourcifychina.com offers a comprehensive platform that streamlines the entire sourcing process, saving time and effort for businesses. From request submission to receiving and comparing quotes, the platform provides a user-friendly interface that simplifies project management. This not only enhances the efficiency of the sourcing process but also allows businesses to focus on other critical aspects of their operations.
Lastly, by offering a free quota, Sourcifychina.com encourages businesses to explore the possibilities of sourcing injection molding services from China. China is known for its competitive manufacturing capabilities and cost advantages. By experiencing the cost-effective and high-quality services offered by Chinese suppliers, businesses can unlock potential savings and gain a competitive edge in their respective industries.
In conclusion, the free quota offered by Sourcifychina.com allows businesses to access multiple quotes from reliable injection molding service suppliers in China. This helps in evaluating project feasibility, choosing the right supplier, and exploring cost advantages. The platform’s commitment to reliability, convenience, and cost-effectiveness makes it a valuable resource for businesses seeking injection molding services.