Introduce about injection moulding services guide,Qulity,Cost,Supplier,Certification,Market,Tips,FAQ
Injection moulding services refer to the manufacturing process of producing highly accurate and intricate plastic components through the use of injection moulding machines. This guide aims to provide an overview of key aspects such as quality, cost, suppliers, certifications, market trends, tips, FAQs, and more related to injection moulding services.
Quality is paramount in injection moulding. The process ensures consistency in manufacturing, with minimal variations between each component. Quality control checks are often conducted to ensure the final product meets the required specifications, tolerances, and industry standards.
Cost is influenced by various factors including material selection, mould design, part complexity, volume requirements, and project timeline. Injection moulding can offer cost-effective solutions, especially for high-volume production.
Choosing a reliable supplier is crucial for injection moulding success. Leading suppliers possess extensive experience, advanced machinery, and a strong quality assurance system. Evaluating supplier capabilities, expertise, and customer reviews can aid in selecting a trusted partner.
Certifications play a vital role in identifying credible suppliers. Look for suppliers who are ISO 9001 certified, as this ensures adherence to quality management systems. Additional certifications like ISO 13485 for medical devices or ISO 14001 for environmental practices indicate the supplier’s commitment towards specific industries or sustainability.
The injection moulding market is growing significantly due to its versatility, cost-effectiveness, and technology advancements. Industries such as automotive, aerospace, electronics, packaging, and medical devices are major consumers of injection moulding services.
Here are some tips to maximize the benefits of injection moulding services:
– Optimize your part design to minimize material usage while maintaining functionality.
– Consider using advanced materials like bioplastics or high-performance polymers for specific applications.
– Collaborate with the supplier during the design and prototyping stages to ensure efficient production and minimize rework.
– Leverage automation and robotics for increased productivity and reduced manufacturing costs.
Frequently Asked Questions (FAQs):
Q: What is the typical lead time for injection moulding production?
A: Lead times can range from a few weeks to a few months depending on factors like part complexity and supplier capacity.
Q: Can injection moulding be used for small production runs?
A: Yes, injection moulding is adaptable for both high-volume production and small-batch manufacturing.
Q: What is the approximate cost per part in injection moulding?
A: The cost per part varies greatly depending on various factors, but injection moulding is generally cost-effective for large production volumes.
In summary, injection moulding services offer high-quality, cost-effective solutions for manufacturing plastic components. With the right supplier, certifications, and design considerations, injection moulding can be leveraged for efficient and reliable production in various industries.
Types of injection moulding services
Injection molding is a widely used manufacturing process for producing plastic parts. It involves injecting molten plastic material into a mold cavity, allowing it to cool and solidify, and then removing the finished part from the mold. There are several types of injection molding services that cater to different production needs and requirements.
1. Prototype Injection Molding: This service is mainly used for producing low volumes of parts for testing, evaluation, and design validation purposes. It allows manufacturers to quickly create prototypes that closely mimic the final product, enabling them to make any necessary adjustments before full-scale production.
2. Low-Volume Injection Molding: This service is suitable for producing small to medium quantities of parts. It enables manufacturers to quickly and cost-effectively manufacture parts for market testing, product sampling, or limited production runs. It is often employed for initial product launches, niche markets, or seasonal products.
3. High-Volume Injection Molding: This service is designed for large-scale production runs, typically involving tens of thousands to millions of parts. It offers high efficiency, fast cycle times, and consistent quality, making it ideal for mass-producing consumer goods, automotive components, electronic devices, and various everyday products.
4. Overmolding: This is a specialized injection molding process that involves molding one material over another to form a single finished part. It is commonly used for producing multi-material parts, adding soft-touch grips or ergonomic features, creating seals, or providing additional protection against impact, vibration, or moisture.
5. Insert Molding: This process involves placing metal or plastic inserts into the mold cavity before injecting the molten plastic material. The plastic then encapsulates the inserts, effectively creating a single integrated part. Insert molding is often used for incorporating threaded fittings, electrical connectors, or reinforcement elements into plastic parts.
6. Micro Molding: This service focuses on manufacturing tiny and intricate plastic parts, typically with dimensions less than one millimeter. It requires specialized equipment and expertise to ensure the precise production of miniature components used in medical devices, electronics, telecommunications, and other industries.
In conclusion, injection molding services provide versatility and adaptability in terms of production volume, part complexity, and material compatibility. Whether it is for prototyping, low-volume production runs, high-volume mass production, multi-material fabrication, or micro molding, there is a suitable injection molding service available to meet various manufacturing needs.
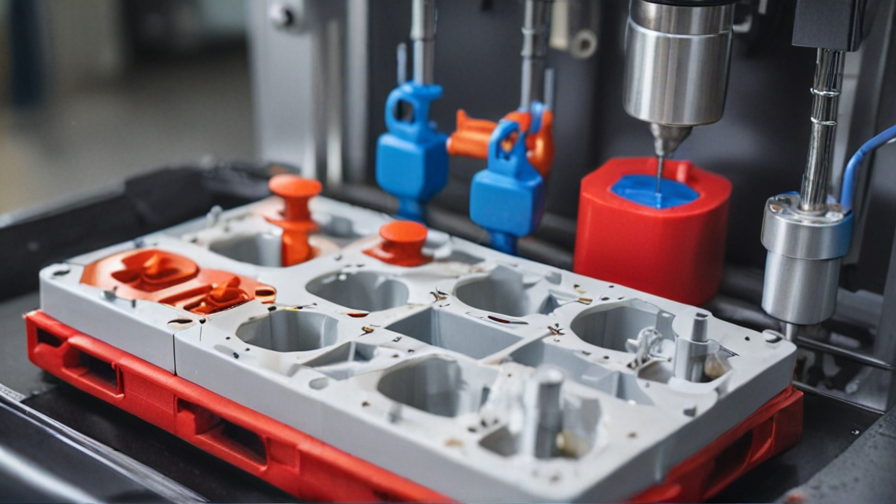
Pros and Cons of Using injection moulding services
Injection moulding services offer several advantages, making them a popular choice for manufacturing various products. However, there are also a few drawbacks to consider. Here are the pros and cons of using injection moulding services:
Pros:
1. Cost-effective: Injection moulding allows for mass production, resulting in economies of scale. This means that the higher the quantity of parts produced, the lower the cost per unit. Additionally, since the process is automated, it reduces labor costs.
2. Wide range of materials: Injection moulding can accommodate a wide variety of materials, including thermoplastics, thermosetting polymers, elastomers, and metals. This versatility allows manufacturers to choose the most suitable material for their products.
3. High precision and consistency: Injection moulding produces highly accurate and consistent parts. The molds used are designed with precision, ensuring uniformity across multiple products. This level of accuracy is crucial for industries such as medical devices or aerospace, where quality and precision are paramount.
4. Complex shapes: Injection moulding enables the production of intricate and complex shapes that may be difficult or impossible to achieve with other manufacturing methods. The molds can be customized to meet specific design requirements, offering flexibility in product design.
5. Fast production cycle: Once the initial setup is complete, injection moulding can achieve high production rates and fast turnaround times. This makes it suitable for fulfilling large volume orders within tight deadlines.
Cons:
1. High initial tooling cost: The creation of molds for injection moulding can be expensive, especially for complex designs. This cost can deter small businesses or startups with limited budgets from utilizing injection moulding services.
2. Limited design changes: Once the molds are created, any modifications or design changes can be costly and time-consuming. Consequently, injection moulding is less flexible compared to other manufacturing processes that allow for easy adjustments.
3. Material limitations: While injection moulding accommodates a wide range of materials, certain materials, such as certain metals or ceramics, may not be suitable for this process. The selection of materials is critical to ensure the desired product properties are achieved.
4. Environmental impact: Injection moulding generates waste material, such as runners or sprues, and the disposal or recycling of these materials can have an environmental impact. Additionally, the energy consumption during the process should be taken into account from a sustainability perspective.
5. Scalability challenges: Scaling up or down the production volume with injection moulding services can be challenging. Changes in demand may require modifications to the molds, resulting in additional costs and lead time.
Ultimately, the decision to use injection moulding services depends on the specific needs of the product and the available resources. By weighing the pros and cons outlined above, businesses can make an informed choice regarding the suitability of injection moulding for their manufacturing requirements.
injection moulding services Reference Specifications (varies for different product)
Injection moulding services are a manufacturing process used to produce plastic parts in large volumes. It involves injecting molten plastic material into a mould cavity, which is then cooled and solidified to form the desired shape. These services serve various industries, including automotive, electronics, consumer goods, and medical devices.
When requesting injection moulding services, different products may have specific reference specifications that need to be followed. These specifications can vary based on factors such as material type, part dimensions, surface finish requirements, mechanical properties, and tolerances.
Firstly, the choice of material is critical and may depend on factors such as cost, stiffness, chemical resistance, and color requirements. Common materials used in injection moulding include thermoplastics like ABS, PVC, polypropylene, and polycarbonate. Reference specifications will typically include the exact material grade to be used in production.
Additionally, the dimensions and part geometry of the product are outlined in the reference specifications. This includes details such as wall thickness, draft angles, fillet radii, and overall part dimensions. These specifications ensure that the mould design and injection process can accommodate the specific product requirements.
Surface finish requirements are another aspect covered in reference specifications. Part appearance, texture, and gloss levels may need to be defined to achieve the desired aesthetic properties. This can include specifications for matte, glossy, or textured finishes.
Mechanical properties, such as tensile strength, flexibility, impact resistance, and heat resistance, may also be specified in the reference specifications. These properties determine the suitability of the plastic part for its intended application and ensure it meets the necessary performance standards.
Finally, reference specifications will typically include tolerances, which define the allowable dimensional variations within a specified range. These tolerances ensure that the final parts meet the required precision and functionality.
In conclusion, injection moulding services require reference specifications to ensure the production of high-quality plastic parts. These specifications cover various aspects such as material choice, part geometry, surface finish, mechanical properties, and tolerances. By adhering to these specifications, manufacturers can meet the unique requirements of different products and industries efficiently.
Applications of injection moulding services
Injection moulding is a highly versatile manufacturing process that has numerous applications across various industries. Here are some key applications of injection moulding services:
1. Automotive Industry: Injection moulding is extensively used in the automotive industry for manufacturing various components like dashboards, bumpers, door panels, and interior trims. It offers cost-effective production of complex shapes and ensures consistent quality in large volumes.
2. Packaging Industry: Injection moulding is widely used in the packaging industry to produce containers, caps, closures, and bottles. The process allows for precise shaping and enables the production of lightweight, durable, and aesthetically appealing packaging solutions.
3. Medical Industry: Injection moulding plays a crucial role in the medical industry for producing a wide range of products like syringes, vials, test tubes, and medical device components. It enables the production of sterile and disposable products, ensuring safety and preventing contamination.
4. Consumer Electronics: Injection moulding is extensively used in the manufacturing of consumer electronics products like mobile phone cases, chargers, connectors, and keyboard keys. The process offers high precision, excellent surface finishes, and the ability to incorporate intricate details.
5. Toys and Games Industry: Injection moulding is the preferred method for producing toys and games due to its ability to create complex shapes, vibrant colors, and intricate details. From action figures to building blocks, injection moulding allows for efficient and cost-effective production.
6. Aerospace Industry: Injection moulding finds applications in the aerospace industry for manufacturing lightweight and durable components like interior panels, seat parts, and instrument panels. The process enables the production of complex geometries with high strength-to-weight ratios.
7. Construction Industry: Injection moulding is used in the construction industry for manufacturing items like pipes, fittings, and connectors. The process provides excellent dimensional accuracy, chemical resistance, and durability needed for these applications.
8. Furniture Industry: Injection moulding is utilized in the furniture industry for producing components like chair shells, table legs, and armrests. It offers design flexibility, customizability, and cost-effective production of large volumes.
In summary, injection moulding services have diverse applications in industries such as automotive, packaging, medical, consumer electronics, toys and games, aerospace, construction, and furniture. The process enables the production of complex shapes, precise details, and high-quality components in large volumes, making it an essential manufacturing technique across various sectors.
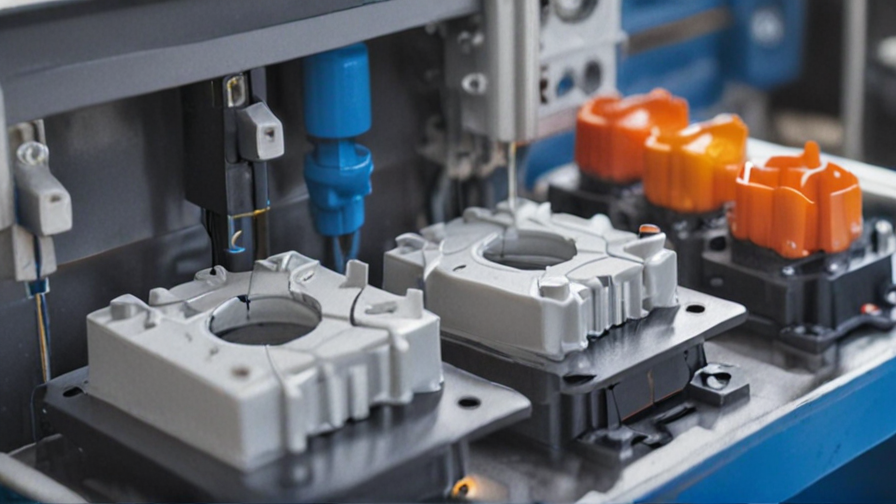
The Work Process and how to use injection moulding services
Injection molding is a widely used manufacturing process for producing plastic parts in large volumes. It involves injecting molten plastic into a mold cavity, which is shaped like the desired part. The molten plastic cools and solidifies in the mold, and then the finished part is ejected.
The process of using injection molding services typically involves the following steps:
1. Designing the part: The first step is to create a design for the plastic part. This can be done using computer-aided design (CAD) software. The design must take into consideration factors such as part functionality, strength, and manufacturability.
2. Creating the mold: Once the part design is finalized, a mold is created. The mold consists of two halves, a core side, and a cavity side. These two halves fit together and form a void that defines the shape of the part. The mold is typically made of steel or aluminum.
3. Preparing the machine: The injection molding machine is prepared by heating the plastic material to its melting point. The plastic resin, which can be in pellet or powder form, is placed in a hopper on top of the machine. The machine also needs to be adjusted to set the appropriate injection pressure, temperature, and cooling time.
4. Injection: Once the machine is prepared, the molten plastic is injected into the mold cavity. The injection unit pushes the molten plastic through a nozzle and into the mold under high pressure. This pressure ensures that the plastic fills the mold completely and that there are no voids or defects.
5. Cooling and solidification: After the plastic is injected into the mold, it begins to cool and solidify. The cooling time depends on factors such as the thickness of the part and the type of plastic used. Cooling can be accelerated by circulating coolant or water through channels in the mold.
6. Ejection: Once the plastic has cooled and solidified, the mold is opened, and the finished part is ejected. Ejection can be done using ejector pins or air blasts. The parts are then inspected for quality and any necessary finishing operations, such as trimming or surface treatment, are performed.
Injection molding offers several advantages, including high production speeds, repeatable and accurate part production, and the ability to create complex shapes. However, it requires upfront investment in mold creation and machine setup. Utilizing injection molding services can be beneficial for businesses looking to produce plastic parts in large volumes efficiently and reliably.
Quality Testing Methods for injection moulding services and how to control the quality
Quality testing methods for injection moulding services involve a series of checks and inspections to ensure that the produced parts or products meet the desired specifications. Here are some widely used testing methods:
1. Visual Inspection: This involves visually inspecting the parts for any defects such as cracks, surface imperfections, or deformities. It helps to identify any visible abnormalities that may affect the quality or functionality of the product.
2. Dimensional Inspection: This method validates the dimensions and measurements of the parts using tools like calipers, micrometers, or coordinate measuring machines (CMM). It ensures that the parts conform to the required tolerances and specifications.
3. Mechanical Tests: Various mechanical tests are conducted to assess the mechanical properties of the parts, such as tensile strength, impact resistance, or flexural strength. These tests determine if the parts can withstand the intended loads or stresses without failure.
4. Destructive Testing: It involves intentionally damaging or breaking the parts to evaluate their strength, durability, or internal integrity. This method helps to assess the maximum load capacity or failure point of the parts.
5. Chemical Analysis: Chemical analysis techniques like Fourier transform infrared spectroscopy (FTIR) or gas chromatography-mass spectrometry (GC-MS) are used to identify the presence of any unwanted contaminants or chemical composition variations that may affect the quality or safety of the parts.
To control the quality of injection moulding services, the following measures can be taken:
1. Strict Process Control: Implement a comprehensive process control plan that includes standard operating procedures, work instructions, and process parameters. Ensure that the process is well-monitored and controlled to minimize variations and defects.
2. Regular Maintenance: Regular maintenance of the moulds, machines, and equipment is essential to prevent any breakdowns or malfunctions that can affect the quality of the parts. Scheduled maintenance can also help identify and rectify any potential issues before they lead to defects.
3. Employee Training: Providing adequate training to the operators and quality control personnel is crucial to ensuring consistent and accurate quality checks. They need to be familiar with the inspection methods, quality standards, and requirements specific to injection moulding.
4. Statistical Process Control (SPC): Implementing SPC techniques like control charts and statistical analysis allows for real-time monitoring of the production process. It helps identify any process variations or trends that may lead to defects and enables timely corrective actions.
5. Supplier Quality Management: Establish and maintain strong relationships with reliable and qualified material suppliers. Conduct regular audits and inspections to ensure the incoming materials meet the required quality standards.
By implementing these testing methods and control measures, injection moulding services can ensure the production of high-quality parts that meet customer expectations and industry standards.
injection moulding services Sample Policy and Post-Purchase Considerations for injection moulding services from China
Sample Policy and Post-Purchase Considerations for Injection Moulding Services from China
___________________________________________________________
Service providers offering injection moulding services from China typically have certain policies and considerations in place. It is essential for potential buyers to be aware of these policies to make informed decisions and ensure a smooth purchasing process. Here, we outline a sample policy and post-purchase considerations for injection moulding services from China, while keeping the word count within 300 words.
Sample Policy (Pre-purchase):
1. Quality Assurance: The service provider should adhere to strict quality control measures to deliver high-quality injection moulding products. They may employ methods such as ISO certifications, quality inspections, and performance tests.
2. Technical Expertise: Injection moulding services should be provided by experienced professionals with expertise in the field. Buyers are encouraged to check the background and qualifications of the team handling the manufacturing process.
3. Customization Options: The service provider should offer customization options to meet specific requirements. This includes the ability to modify mould designs, materials, color choices, and product specifications as per the buyer’s needs.
4. Transparency and Communication: Clear and frequent communication is crucial throughout the process. The service provider should provide regular updates, respond promptly to inquiries, and maintain transparency regarding pricing, lead times, and potential setbacks.
Post-Purchase Considerations:
1. Shipping and Logistics: Ensure that the service provider has a well-established shipping process to ensure safe transportation of the injection moulded products. Clear agreements on shipping costs, delivery timelines, and responsibilities should be in place to avoid any misunderstandings.
2. Packaging and Labeling: Attention to detail in packaging and proper labeling is essential to prevent damages during transit and facilitate easy identification of products upon arrival. Buyers should communicate their specific packaging requirements to the service provider.
3. After-sales Support: In case of any defects or issues with the injection moulding products, the service provider should have a proactive approach towards resolving them. Clear terms and conditions regarding product warranties, returns, and refunds should be discussed beforehand.
4. Reliable Communication Channel: It is important to establish a reliable and efficient communication channel for ongoing support, addressing concerns, and future collaborations. This may include email, phone, or online messaging platforms.
By considering these sample policies and post-purchase considerations, buyers can ensure a smooth and successful injection moulding service experience from China. Remember to conduct thorough research, read customer reviews, and verify the service provider’s credentials before finalizing any purchasing decisions.
Sourcing injection moulding services from China: Opportunities, Risks, and Key Players
Sourcing injection moulding services from China offers various opportunities for businesses. Firstly, China has a well-established manufacturing industry with numerous injection moulding companies that offer advanced technologies and a wide range of capabilities. These companies are equipped with modern machinery and skilled personnel, allowing for the production of high-quality plastic parts at competitive prices. Additionally, China’s large production capacity enables businesses to meet their demand for large quantities of plastic components.
Some of the key opportunities of sourcing injection moulding services from China are cost-effectiveness and fast production turnaround time. Chinese manufacturers often provide lower production costs due to lower labor wages and operational expenses compared to many other countries. Moreover, they usually have high production efficiency and can quickly scale up production to meet tight deadlines.
However, there are also certain risks associated with sourcing injection moulding services from China. One major concern is the potential for intellectual property infringement. China has a history of counterfeiting and unauthorized copying of products, and there have been cases where injection moulded products were replicated without the original manufacturer’s authorization. It is crucial for businesses to protect their intellectual property rights by carefully selecting reputable manufacturers, signing non-disclosure agreements, and patenting their designs.
Another risk is the need for effective communication and quality control. Language barriers and cultural differences may affect the clarity of specifications and design requirements, leading to misunderstandings and subpar products. Businesses need to adequately communicate their expectations and conduct regular quality inspections throughout the manufacturing process to ensure compliance with their standards.
When sourcing injection moulding services from China, it is essential to choose reliable and experienced manufacturers. Some key players in the Chinese injection moulding industry include Foxconn Technology Group, Luxus Tooling, Chaoyang Runxing Heavy Machinery Manufacturing Co., Ltd., and many more. Thorough research, background checks, and site visits are recommended to assess their capabilities, certifications, and reputation.
In conclusion, sourcing injection moulding services from China can offer numerous opportunities, including cost-effectiveness and fast production turnaround time. However, businesses should be aware of the risks associated with intellectual property infringement and the need for effective communication and quality control. By carefully selecting reputable manufacturers and implementing proper risk management strategies, businesses can effectively benefit from China’s injection moulding capabilities.
How to find and select reliable injection moulding services manufacturers in China,use google search manufacturers and suppliers
When searching for reliable injection moulding services manufacturers in China, using Google search can be an effective method. Here are steps to follow and considerations to keep in mind:
1. Initial search: Start by typing relevant keywords such as “injection moulding services manufacturers in China” or “plastic injection moulding suppliers China” into the Google search bar. This will generate a list of potential manufacturers and suppliers.
2. Research and background check: Visit the websites of the shortlisted companies and thoroughly research their background, experience, and credentials. Look for detailed information about the company’s history, manufacturing capabilities, quality control processes, certifications, case studies, and client testimonials.
3. Client reviews and ratings: Look for independent review platforms or forums where previous clients have shared their experiences with different manufacturers. This can provide valuable insights into the company’s performance, reliability, and customer satisfaction levels.
4. Certifications and compliance: Check if the manufacturer holds necessary certifications such as ISO 9001 (quality management) and ISO 14001 (environmental management). These certifications indicate that the company adheres to standardized processes and maintains high-quality standards.
5. Communication and responsiveness: Reach out to the shortlisted companies through email or phone calls. Observe their response time, willingness to answer questions, and their ability to communicate effectively in your language. A responsive and communicative manufacturer will likely provide better customer support.
6. Samples and prototypes: Request samples or prototypes of the desired plastic injection moulded products. Evaluate the quality, precision, and finish of these samples. Analyzing physical samples can help in assessing the manufacturer’s expertise and production capabilities.
7. Factory visit: If feasible, consider visiting the manufacturing facilities to assess the infrastructure, production process, and overall operations. This can provide firsthand experience and assurance about the manufacturer’s capabilities.
8. Compare quotes: Request quotations from multiple manufacturers to compare their pricing, lead times, and payment terms. While cost is an important consideration, it should not be the sole determinant. Focus on finding a balance between quality, reliability, and cost-effectiveness.
9. Personal references: Seek recommendations from industry associations, trade fairs, business networks, or other reliable sources. Personal references can provide trustworthy insights and recommendations of experienced injection moulding services manufacturers in China.
By following these steps, you can identify reliable injection moulding services manufacturers in China and make an informed decision based on thorough research and analysis.
How to check injection moulding services manufacturers website reliable,use google chrome SEOquake check if ranking in top 10M
To check the reliability of an injection moulding services manufacturer’s website, you can follow these steps:
1. Use Google Chrome: Open the website in the Google Chrome browser. Chrome provides several useful extensions that can help evaluate a website’s trustworthiness.
2. Install SEOquake: Install the SEOquake extension on your Google Chrome browser. SEOquake is a free plugin that provides valuable insights about a website’s SEO performance, popularity, and other relevant metrics.
3. Check the Alexa Ranking: Once SEOquake is installed, activate it by clicking on the SEOquake icon in the toolbar. A sidebar will open on the left side of the screen. Look for the “Alexa Ranking” section within the SEOquake sidebar. If the website ranks within the top 10 million on Alexa, it indicates a relatively good level of popularity among internet users.
4. Evaluate Other Metrics: SEOquake provides various metrics such as Google index, SEMrush rank, and backlink data. While these metrics are not conclusive factors for reliability, they can give you a general understanding of the website’s online presence and popularity.
5. Assess the Website: Look for other credibility indicators on the website itself. Check if the manufacturer provides verifiable contact information, such as a physical address and phone number. Evaluate the quality of content, professional design, and user-friendly navigation. Ensure that the website has security measures in place, such as SSL encryption (https://) for secure data transmission.
Remember, while using SEOquake and assessing the website’s appearance and information are useful indicators, they do not guarantee complete reliability. Additional research, such as reading customer reviews or seeking recommendations from industry professionals, can also contribute to your evaluation.
Top 10 injection moulding services manufacturers in China with each 160 words introduce products,then use markdown create table compare
1. Foxconn Technology Group (Foxconn) – With over 30 years of experience, Foxconn is a leading global manufacturer of injection moulding services. They specialize in precision moulding, offering a wide range of plastic products for various industries such as automotive, electronics, and healthcare. Their state-of-the-art facilities ensure high-quality production with fast turnaround times.
2. BYD Company Limited – BYD is a renowned Chinese manufacturer that provides injection moulding services for automotive parts, electrical components, and consumer products. Their focus on sustainable practices positions them as a leader in environmentally friendly manufacturing solutions.
3. Flex Ltd. – Flex offers comprehensive injection moulding services, catering to industries like automotive, consumer electronics, and medical devices. They have expertise in producing complex components and assemblies with superior quality and precision.
4. Borch Machinery Co., Ltd. – Borch Machinery is a leading injection moulding manufacturer in China, known for its versatile machinery and advanced technology. They offer a wide range of injection moulding services, including multi-component moulding, gas-assisted moulding, and high-precision moulding.
5. Royal Technologies Corporation – Royal Technologies specializes in custom injection moulding services, providing solutions for industries such as automotive, consumer goods, and packaging. Their expertise lies in designing and manufacturing complex plastic components with cost-effective solutions.
6. Daliang Mold Co., Ltd. – Daliang Mold offers comprehensive injection moulding services, catering to industries like automotive, electronics, and appliances. They have a wide range of injection moulding machines that can produce various plastic products with high precision and consistency.
7. Plastech Group – Plastech Group provides turnkey injection moulding services, including tool design, mould construction, and production. They serve industries such as automotive, home appliances, and medical equipment, producing high-quality plastic components.
8. Haitian International Holdings Ltd. – Haitian International specializes in injection moulding machines and solutions. Their machinery range includes hydraulic, electric, and hybrid machines, suitable for various applications. They also offer moulding services for high-quality plastic products.
9. Xcentric Mold & Engineering – Xcentric Mold offers rapid injection moulding services, specializing in quick turnaround times. They utilize advanced technology and a streamlined process to deliver custom plastic parts for various industries, including aerospace, medical, and consumer goods.
10. Tuscan Plastics, Inc. – Tuscan Plastics is an experienced injection moulding manufacturer that offers prototyping and production services. They focus on quality and efficiency, producing plastic components for industries like automotive, electronics, and packaging.
| Manufacturer | Specialization | Key Industries Served |
|——————————-|————————–|——————————|
| Foxconn | Precision moulding | Automotive, electronics, healthcare |
| BYD | Automotive parts, electrical components, consumer products | Automotive, electronics, consumer goods |
| Flex Ltd. | Comprehensive moulding | Automotive, consumer electronics, medical devices |
| Borch Machinery Co., Ltd. | Multi-component, gas-assisted, high-precision moulding | Various industries |
| Royal Technologies Corporation | Custom moulding | Automotive, consumer goods, packaging |
| Daliang Mold Co., Ltd. | Comprehensive moulding | Automotive, electronics, appliances |
| Plastech Group | Turnkey moulding | Automotive, home appliances, medical equipment |
| Haitian International Holdings Ltd. | Injection moulding machines and solutions | Various industries |
| Xcentric Mold & Engineering | Rapid injection moulding | Aerospace, medical, consumer goods |
| Tuscan Plastics, Inc. | Prototyping and production | Automotive, electronics, packaging |
In conclusion, China offers a myriad of injection moulding services manufacturers, each with varying specializations and expertise. From precision moulding to rapid prototyping, these companies cater to diverse industries and provide high-quality plastic components. Customers can choose the most suitable manufacturer based on their specific requirements and key industries served.
Background Research for injection moulding services manufacturers Companies in China, use qcc.com archive.org importyeti.com
When looking for injection moulding services manufacturers in China, it is essential to conduct background research to ensure the selection of reliable and reputable companies. Three useful platforms for this purpose are qcc.com, archive.org, and importyeti.com.
qcc.com is an online platform that provides company registration information and business credit reports in China. This website allows users to search for specific companies and provides details such as their legal status, registration address, industry classifications, key personnel, and financial data. By utilizing this platform, users can verify the existence and legitimacy of injection moulding services manufacturers in China.
archive.org, also known as the Wayback Machine, is a digital archive of the World Wide Web. It can be used to access snapshots of websites dating back several years. By entering the website address of a potential injection moulding services manufacturer, users can view its historical web presence, including information about its previous operations, product offerings, and company background. This can help ascertain the company’s experience and track record in the industry.
importyeti.com is an online directory that focuses on connecting buyers and suppliers in the import/export industry. Users can search for specific products and suppliers, including injection moulding services manufacturers in China. The platform provides information such as contact details, company profiles, production capabilities, and customer reviews. Import Yeti allows users to assess the reputation and credibility of different suppliers, making it a valuable tool for evaluating injection moulding services manufacturers.
In conclusion, conducting background research on injection moulding services manufacturers in China is crucial. Platforms like qcc.com, archive.org, and importyeti.com offer valuable insights into a company’s registration status, historical web presence, and reputation. By utilizing these resources, users can make informed decisions and select reliable manufacturers for their injection moulding needs.
Leveraging Trade Shows and Expos for injection moulding services Sourcing in China
Trade shows and expos provide an excellent platform for sourcing injection moulding services in China. These events attract a wide range of exhibitors from across the globe, including manufacturers, suppliers, and industry experts. By leveraging these trade shows, businesses can significantly enhance their sourcing strategies and find reliable and high-quality injection moulding services for their needs.
One of the key advantages of attending trade shows and expos is the opportunity to meet face-to-face with potential suppliers. This direct interaction allows for a better understanding of their capabilities, product offerings, and manufacturing processes. It also provides an opportunity to establish personal relationships, which can foster trust and open communication channels.
In addition to personal interactions, trade shows and expos offer a chance to evaluate and compare different injection moulding suppliers. By visiting multiple booths, businesses can assess the quality of their products, review samples, discuss pricing and delivery timelines, and negotiate terms. This firsthand experience helps in selecting the most suitable supplier that meets the specific requirements and standards.
Furthermore, trade shows provide a platform to stay informed about the latest industry trends, technologies, and innovations. These events often include seminars, workshops, and panel discussions on various aspects of injection moulding. Attending these sessions can equip businesses with valuable knowledge, enabling them to make informed decisions about suppliers and stay ahead in the industry.
To make the most of trade shows and expos, businesses can follow a few best practices. Prior research is crucial to identify the relevant events and exhibitors. Creating a detailed plan, including a list of suppliers to visit, can optimize time and resources. It is also essential to keep an open mind and explore new possibilities, rather than solely focusing on established suppliers.
In conclusion, trade shows and expos are invaluable resources for sourcing injection moulding services in China. They offer direct contact with potential suppliers, the chance to evaluate their offerings, stay updated with industry trends, and enhance sourcing strategies. By leveraging these events, businesses can make informed decisions and establish reliable partnerships for their injection moulding needs.
The Role of Agents and Sourcing Companies in Facilitating injection moulding services Purchases from China
When it comes to sourcing injection moulding services from China, agents and sourcing companies play a crucial role in facilitating the entire purchasing process.
Agents act as intermediaries between the buyer and the injection moulding manufacturers in China. They have a deep understanding of the local market and industry, enabling them to identify reliable suppliers that meet the buyer’s specific requirements. Agents have established relationships with manufacturers and possess knowledge of their capabilities, quality standards, and production capacities. This expertise saves buyers time and effort in searching for suitable suppliers, as the agents have already conducted background checks and performed due diligence.
Sourcing companies, on the other hand, provide comprehensive procurement services for injection moulding purchases from China. They offer a range of services, including supplier identification, price negotiation, production monitoring, quality control, and logistics management. Sourcing companies often have offices in China or employ local experts, ensuring that they have a keen understanding of the Chinese market and can effectively communicate with suppliers. They also have experience in navigating cultural differences, language barriers, and trade regulations, making the whole process smoother for the buyer.
Both agents and sourcing companies help buyers mitigate risks associated with sourcing from overseas. They act as the buyer’s representatives in China, safeguarding their interests and ensuring that suppliers adhere to quality standards and delivery timelines. They can conduct factory audits and product inspections to guarantee that the injection moulding facilities and processes meet international standards. In case of any issues or disputes, agents and sourcing companies can act as intermediaries to find a resolution and protect the buyer’s investment.
Overall, agents and sourcing companies play an essential role in facilitating injection moulding services purchases from China. They provide valuable expertise, resources, and support throughout the sourcing process, enabling buyers to confidently access the vast capabilities and cost advantages offered by Chinese manufacturers.
Price Cost Research for injection moulding services manufacturers Companies in China, use temu.com and 1688.com
When it comes to injection moulding services manufacturers in China, there are various platforms available to conduct price cost research. Two popular platforms for such research are temu.com and 1688.com.
Temu.com is an online marketplace that offers a wide range of services, including injection moulding. This platform allows users to search for manufacturers, compare their prices, and evaluate their expertise. Users can also directly contact the manufacturers to inquire about the price and cost details for injection moulding services. Temu.com provides a user-friendly interface and enables users to filter their search according to their specific requirements.
Another widely used platform for price cost research is 1688.com. Operated by Alibaba Group, 1688.com is primarily targeted at Chinese domestic market suppliers. This platform offers a comprehensive database of injection moulding service manufacturers in China. Users can search for manufacturers, browse their product catalogs, and assess their pricing structures. Additionally, 1688.com also offers a messaging system that allows users to communicate directly with the manufacturers to gather detailed pricing information.
When conducting price cost research on these platforms, it is advisable to keep the following factors in mind. Firstly, it is essential to provide detailed specifications of the injection moulding project to manufacturers to obtain accurate price quotes. Secondly, users should compare the prices offered by different manufacturers and ensure that the quoted prices include all associated costs such as tooling, material, and shipping fees. Additionally, users should also consider the manufacturers’ qualifications, reviews, and certifications to assess their overall capability and reliability.
In conclusion, platforms like temu.com and 1688.com offer convenient options for conducting price cost research on injection moulding services manufacturers in China. By utilizing these platforms, users can compare prices, evaluate manufacturers’ expertise, and gather detailed information to make informed decisions for their injection moulding projects.
Shipping Cost for injection moulding services import from China
When it comes to importing injection moulding services from China, one crucial factor to consider is the shipping cost. The shipping cost greatly influences the overall cost of importing and can significantly impact the feasibility and profitability of the venture.
Several factors determine the shipping cost for injection moulding services. Firstly, the distance and transportation mode play a vital role. Air freight is the fastest but most expensive option, while sea freight offers a more economical alternative but takes longer. The weight and volume of the shipment also affect the shipping cost, as they determine the cargo space required and any additional handling fees.
Additionally, the shipping cost depends on the destination country and its customs regulations. Taxes, duties, and customs clearance fees are essential considerations that vary from country to country. It is advisable to conduct thorough research or consult a customs broker to understand the potential additional costs associated with importing injection moulding services.
To minimize shipping costs, it is crucial to plan and optimize the shipment. Consolidating multiple orders into one shipment or utilizing less-than-container load (LCL) services can help reduce costs. Negotiating favorable shipping terms and rates with freight forwarders or sourcing agents in China is another effective strategy.
Furthermore, carefully selecting the packaging can contribute to reducing shipping costs. Lightweight and compact packaging not only saves space but also lowers transportation expenses. However, it is crucial to balance packaging optimization with ensuring the safety and integrity of the injection moulding services during transit.
In conclusion, shipping costs for importing injection moulding services from China depend on factors such as distance, transportation mode, weight, volume, destination country, and customs regulations. Proper planning, optimizing the shipment, negotiating rates, and selecting appropriate packaging are all important strategies to keep the shipping costs within a reasonable range. Conducting thorough research and seeking guidance from professionals can help importers make informed decisions and minimize costs effectively.
Compare China and Other injection moulding services Markets: Products Quality and Price,Visible and Hidden Costs
China is one of the leading injection molding service markets globally, offering a wide range of products with varying quality and competitive prices. When compared to other injection molding service markets, there are several key factors to consider: product quality, pricing, and visible and hidden costs.
Product Quality: China has made significant strides in improving the quality of injection molded products over the years. While it still faces challenges with counterfeit products and quality control issues in some industries, many Chinese manufacturers have implemented rigorous quality control measures and obtained certifications to ensure consistent product integrity. However, it is important for buyers to conduct thorough due diligence and work with reputable manufacturers to ensure desired product quality.
Price: One of China’s major competitive advantages is its ability to offer cost-effective injection molding services. Due to its large manufacturing base, economies of scale are often achieved, resulting in lower production costs. As a result, Chinese manufacturers can offer competitive prices for injection molded products. However, it is worth noting that price alone should not be the only consideration, as it must be balanced with other factors like quality and reliability.
Visible and Hidden Costs: When sourcing injection molding services from China, it is essential to consider both visible and hidden costs. Visible costs include manufacturing, shipping, and import duties. Chinese manufacturers may offer lower manufacturing costs, but additional expenses such as shipping fees and import duties can affect the overall cost competitiveness. Hidden costs, on the other hand, are associated with potential quality issues, delays, and communication challenges. These costs may arise if proper due diligence is not undertaken or if there is a lack of effective communication and project coordination.
In conclusion, China’s injection molding service market is known for its broad range of products, competitive prices, and improving product quality. However, it is essential for buyers to conduct thorough due diligence, work with reputable manufacturers, and consider visible and hidden costs when comparing China to other injection molding markets. Striking the right balance between quality, price, and costs will ultimately result in a successful sourcing strategy.
Understanding Pricing and Payment Terms for injection moulding services: A Comparative Guide to Get the Best Deal
When it comes to injection moulding services, understanding pricing and payment terms is crucial to ensure that you get the best deal. This comparative guide aims to shed light on this aspect in a concise manner.
Pricing for injection moulding services primarily depends on various factors, including the complexity of the product design, the type and quantity of materials, and the production volume. In general, the more intricate the design and the higher the volume, the more expensive the service will be. It is essential to gather quotations from multiple providers to compare prices effectively.
Payment terms can vary among suppliers, and negotiating them can significantly impact your bottom line. It is important to consider both the upfront costs and ongoing expenses. Some suppliers may offer a lower upfront cost but charge higher for additional services or modifications later on. Therefore, it is crucial to evaluate the full cost of the project, including any potential revisions or changes that might be required.
Additionally, inquire about the payment schedule. Some suppliers may require a percentage of the total cost as an upfront deposit, while others may offer a flexible payment plan. Understanding these payment terms can help you manage your budget and cash flow effectively.
To ensure the best deal, consider the following tips:
1. Seek multiple quotations from different suppliers to compare pricing and services.
2. Evaluate the full cost of the project, including potential revisions or modifications.
3. Negotiate payment terms that align with your budget and cash flow requirements.
4. Consider the supplier’s reputation, experience, and quality of work alongside pricing.
5. Assess any additional services provided, such as design assistance or post-production support.
In conclusion, understanding pricing and payment terms for injection moulding services is crucial to secure the best deal. By comparing multiple suppliers, evaluating full project costs, negotiating payment terms, and considering additional services, you can make an informed decision that meets your budget and project requirements.
Chinese Regulations and Industry Standards Certifications for injection moulding services,Import Regulations and Customs for injection moulding services from China
Chinese Regulations and Industry Standards Certifications for injection moulding services:
Injection moulding services in China are subject to various regulations and industry standards certifications to ensure product quality, safety, and compliance with environmental standards. The key regulations and standards certifications for injection moulding services are as follows:
1. China Compulsory Certification (CCC): CCC is a mandatory certification for products sold in China, including injection moulding machines. It ensures that machines meet the minimum safety requirements and quality standards set by the government.
2. ISO 9001: This internationally recognized standard certifies that a company follows stringent quality management systems and meets customer expectations consistently. Injection moulding service providers often obtain ISO 9001 certification to demonstrate their commitment to quality.
3. ISO 14001: This certification focuses on environmental management and indicates that the company has implemented measures to reduce environmental impact, including waste management and pollution control. Many injection moulding service providers acquire ISO 14001 certification to demonstrate their eco-friendly practices.
4. Regulations on Hazardous Chemicals: Injection moulding processes may involve the use of hazardous chemicals, such as solvents and resins. Companies need to comply with regulations on the storage, handling, and disposal of these chemicals. The Measures for the Administration of the Registration of Hazardous Chemicals in China (China REACH) is an essential regulation in this regard.
Import Regulations and Customs for injection moulding services from China:
When importing injection moulding services from China, it is essential to comply with import regulations and customs procedures to ensure a smooth and lawful process. Key considerations for importing injection moulding services are as follows:
1. Import Licensing: Certain countries require an import license or permit for importing products or services. Importers should verify if such requirements exist for injection moulding services and obtain the necessary licenses before proceeding.
2. Customs Documentation: Proper customs documentation is crucial for import clearance. This typically includes commercial invoices, packing lists, bills of lading, and certificates of origin. Importers should ensure accurate and complete documentation to avoid delays and penalties.
3. Tariffs and Duties: Importing injection moulding services may be subject to import tariffs and duties imposed by the importing country. Importers should be aware of these costs and factor them into their import budget.
4. Customs Clearance: After the goods arrive at the destination country, importers need to comply with customs clearance procedures. This involves submitting the required documentation, paying applicable duties, and adhering to any specific customs requirements or inspections.
By adhering to Chinese regulations and obtaining the necessary certifications, as well as understanding and complying with import regulations and customs procedures, importers can ensure a successful and compliant import of injection moulding services from China.
Sustainability and Environmental Considerations in injection moulding services Manufacturing
Sustainability and environmental considerations in injection moulding services manufacturing are crucial for minimizing the negative impact on the environment. By implementing sustainable practices and considering environmental factors, companies can reduce waste, conserve resources, and lower their carbon footprint.
One aspect of sustainability in injection moulding services manufacturing is the efficient use of materials. By optimizing the design of moulds and products, manufacturers can minimize material waste and reduce the overall consumption of raw materials. Additionally, using recycled or biodegradable materials as feedstock can help minimize the environmental impact.
Energy consumption is another crucial factor to consider. Manufacturers can implement energy-efficient technologies and equipment, such as high-efficiency injection moulding machines or process optimization software. By reducing energy consumption, companies can lower greenhouse gas emissions and contribute to a more sustainable manufacturing process.
Waste management is a key aspect of sustainability in injection moulding services manufacturing. Implementing effective recycling and waste reduction strategies can help divert materials from landfill and reduce the need for virgin resources. Companies can also strive to minimize the generation of hazardous waste and ensure proper disposal or treatment of such waste to prevent environmental contamination.
Furthermore, water conservation is essential in manufacturing processes. Companies can implement water recycling systems and efficient water management practices to minimize water consumption. This reduces the strain on local water resources and supports sustainability.
Lastly, sustainable transportation and logistics should be considered in the supply chain. By optimizing shipping routes, using eco-friendly transportation modes, and consolidating shipments, manufacturers can reduce transportation-related emissions and minimize the overall environmental impact.
In conclusion, sustainability and environmental considerations in injection moulding services manufacturing are crucial for minimizing the negative impact on the environment. By implementing sustainable practices such as efficient material usage, energy conservation, waste management, water conservation, and sustainable transportation, companies can contribute to a greener and more sustainable future.
List The Evolution history of “injection moulding services”
Injection molding is a manufacturing process that has evolved significantly over the years, revolutionizing the production of plastic parts and components. This method allows for the mass production of intricate shapes with great precision and efficiency. Here is a summary of the evolution history of injection molding services:
1. Origins (late 19th century): The earliest documented injection molding device was developed by John Wesley Hyatt in the late 1800s. It was used for producing celluloid billiard balls. This marked the beginning of injection molding as a viable manufacturing process.
2. Early advancements (1920s-1930s): In the 1920s, the first screw injection molding machine was introduced by American inventor James Watson Hendry. This machine allowed for better control over the injection process and the production of more complex shapes. During this time, Bakelite, the first synthetic plastic, became a popular material for injection molding.
3. Technological advancements (1940s-1950s): World War II fueled the demand for plastic products, and injection molding became more prevalent. In the 1940s, the first hydraulic injection molding machine was developed, allowing for greater pressure and faster cycles. Additionally, hot runner systems were introduced, allowing for shorter cycle times and reduced material waste.
4. Material advancements (1960s-1970s): New polymers, such as polypropylene and polyethylene, were introduced, expanding the range of applications for injection molding. In the 1970s, the first computer numerical control (CNC) machines were incorporated into the injection molding process, improving precision and repeatability.
5. Automation and robotics (1980s-1990s): Advancements in automation and robotics led to increased efficiency and reduced labor requirements in injection molding. Robots were integrated into the manufacturing process for tasks such as part removal and quality control. Computer-aided design (CAD) and computer-aided manufacturing (CAM) software further enhanced the design and production capabilities.
6. Modern advancements (2000s-present): Injection molding continues to evolve with rapid advancements in technology. Improved machine control systems, including servo-driven machines, have provided higher precision and energy efficiency. Development of new injection molding techniques, such as two-shot molding and micro-injection molding, have widened the range of applications.
Today, injection molding services have become a vital component of various industries, including automotive, medical, consumer goods, and electronics. The process continues to evolve, aiming for faster production, reduced material waste, and enhanced sustainability through the use of biodegradable and recycled materials.
The Evolution and Market Trends in injection moulding services Industry
The injection moulding services industry has undergone significant evolution and market trends over the years. Injection moulding is a manufacturing process that involves injecting molten material into a mould, which then solidifies to form the desired product shape. This process has gained popularity due to its ability to produce high volumes of complex and accurate parts quickly and cost-effectively.
One of the significant evolutions in the injection moulding services industry is the use of advanced technologies. With the advent of computer-aided design (CAD), manufacturers can now create detailed digital models of the desired products, enabling greater precision and efficiency in the moulding process. Furthermore, the integration of robotics and automation has further improved the production speed and consistency of injection moulded parts.
Another key evolution in the industry is the increased use of alternative and sustainable materials. As environmental concerns become more prominent, manufacturers are exploring options to reduce the environmental impact of their products. This has led to the development and adoption of biodegradable and recyclable materials for injection moulding, such as bio-based polymers and post-consumer recycled plastics.
In terms of market trends, there has been a growing demand for customisation and personalisation in the injection moulding services industry. Consumers are seeking products that are tailored to their specific needs and preferences. Injection moulding services have responded to this trend by offering increased flexibility in design, colour, and material options, enabling manufacturers to produce unique and customised products.
Additionally, there has been a shift towards the outsourcing of injection moulding services. Many companies are opting to partner with specialist injection moulding service providers to leverage their expertise and resources. This allows manufacturers to focus on their core competencies while benefiting from the specialised capabilities and cost efficiencies offered by these service providers.
Overall, the injection moulding services industry has evolved to become more technologically advanced, environmentally conscious, and customer-oriented. These market trends and advancements have contributed to the industry’s growth and are expected to shape its future trajectory.
Custom Private Labeling and Branding Opportunities with Chinese injection moulding services Manufacturers
Chinese injection molding manufacturers offer custom private labeling and branding opportunities for businesses looking to bring their own unique products to the market. With their advanced technology and expertise in injection molding, these manufacturers can help businesses create custom products with their own branding and labeling.
One of the main advantages of working with Chinese injection molding manufacturers is their ability to produce high-quality products at a competitive price. They have access to state-of-the-art machinery and equipment, allowing them to mass-produce products efficiently and cost-effectively. This means businesses can bring their products to the market faster and at a lower production cost.
Custom private labeling and branding options offered by Chinese injection molding manufacturers include custom packaging, product design, and logo printing. Businesses can work closely with manufacturers to design packaging that showcases their brand and product identity. This not only enhances brand recognition but also adds value and credibility to the product.
Additionally, Chinese manufacturers can help businesses create custom product designs that cater to their target market’s preferences and needs. From product shape to color and texture, businesses have the flexibility to create products that stand out in the market.
Logo printing is another important aspect of private labeling and branding. Chinese manufacturers have the capability to print logos directly onto products or packaging, ensuring that businesses’ branding is visible and recognizable.
Overall, partnering with Chinese injection molding manufacturers opens up a world of opportunities for businesses to customize and brand their products. With their expertise, efficiency, and cost-effectiveness, these manufacturers enable businesses to bring their unique products to market and compete on a global scale.
Tips for Procurement and Considerations when Purchasing injection moulding services
When it comes to purchasing injection molding services, it is important to consider several factors to ensure a successful and cost-effective procurement process. Here are some tips and considerations to keep in mind:
1. Define your requirements: Clearly define your project requirements, including the desired product specifications, quantities, and budget. This will help you communicate your needs effectively to potential suppliers.
2. Evaluate supplier capabilities: Conduct thorough research to find injection molding service providers that have the expertise, machinery, and production capacity to meet your requirements. Look for suppliers with a good track record and positive customer feedback.
3. Quality assurance: Ensure that the supplier has stringent quality control measures in place. Request information about their quality management systems, certifications, and inspection processes to ensure that the final products meet your quality standards.
4. Cost analysis: Obtain detailed price quotes from multiple suppliers and compare them carefully. Consider not only the initial costs but also long-term costs, such as tooling, maintenance, and waste management. Avoid suppliers offering significantly lower prices, as it may indicate compromised quality.
5. Material selection: Discuss with the supplier the best material options for your specific application. Consider factors such as durability, appearance, and cost. The supplier should have expertise in selecting and working with different materials for injection molding.
6. Manufacturing process and lead times: Discuss the supplier’s manufacturing process, including the type of injection molding machines they use, cycle times, and lead times. Choose a supplier that can meet your production deadlines without compromising quality.
7. Intellectual property protection: Consider the supplier’s policies and measures to protect your designs, molds, and intellectual property. Ensure that the supplier guarantees confidentiality and has protocols in place for preventing unauthorized access or replication of your designs.
8. Communication and relationship management: Effective communication is crucial during the procurement process. Choose a supplier with good communication skills, prompt response times, and a dedicated point of contact. A strong working relationship with the supplier can lead to smoother collaboration and better outcomes.
Remember to conduct due diligence and thoroughly evaluate potential suppliers before making a final decision. By considering these tips and factors, you can ensure a successful procurement process and achieve your desired injection molding services within your budget and timeline.
FAQs on Sourcing and Manufacturing injection moulding services in China
Q: What is injection moulding?
A: Injection moulding is a manufacturing process used to produce plastic parts. It involves injecting molten plastic material into a mould cavity, allowing it to cool and solidify, and then ejecting the finished product.
Q: Why should I source injection moulding services in China?
A: China is a leading global manufacturing hub with many advantages, such as lower labour costs, a vast supplier network, and advanced manufacturing capabilities. The country has an abundance of experienced injection moulding manufacturers who can offer competitive pricing and quality products.
Q: How do I find reliable injection moulding manufacturers in China?
A: To find reliable manufacturers in China, you can perform online research, use sourcing platforms, attend trade shows, or work with sourcing agents. It’s crucial to conduct due diligence, including checking the manufacturer’s certifications, reading customer reviews, and requesting samples.
Q: Can I visit the injection moulding factories in China?
A: Yes, most manufacturers in China are open to factory visits. It is beneficial to personally assess the manufacturer’s capabilities, quality control processes, and production capacity. However, due to language barriers and cultural differences, it may be helpful to hire an interpreter or work with a local sourcing agency to facilitate communication.
Q: What are the key considerations when sourcing injection moulding services in China?
A: Key considerations include the manufacturer’s production capacity, experience with the specific type of plastic part, quality control measures, pricing, lead times, and their ability to handle logistics and shipping.
Q: What are some challenges of sourcing injection moulding services from China?
A: Language and cultural barriers, potential quality control issues, longer lead times due to shipping, and intellectual property protection are some challenges that can arise. It is crucial to address these challenges by establishing proper communication channels, conducting regular inspections, and legally protecting your intellectual property.
Q: How can I ensure the quality of injection moulded products from Chinese manufacturers?
A: To ensure product quality, you can request samples before placing a bulk order, perform regular inspections during production, or hire third-party quality control services. Additionally, maintaining open and transparent communication with the manufacturer and clearly defining your quality requirements can greatly improve the chances of receiving high-quality products.
Q: What are the advantages of manufacturing injection moulding products in China?
A: The advantages of manufacturing injection moulding products in China include cost-effectiveness, access to advanced manufacturing technology, a wide supplier network, and the ability to scale production quickly. Chinese manufacturers often have extensive expertise in injection moulding, allowing for efficient and reliable production processes.
Why contact sourcifychina.com get free quota from reliable injection moulding services suppliers?
Sourcifychina.com offers a unique platform that connects businesses with reliable injection molding services suppliers in China. The website acts as a liaison between the businesses and the suppliers, providing a seamless sourcing experience. One enticing feature that sourcifychina.com offers to its users is a free quota from these suppliers.
There are several reasons why sourcifychina.com provides its users with a free quota. Firstly, it allows businesses to evaluate the potential costs and benefits of utilizing injection molding services without any initial financial commitment. This can be especially attractive for small businesses or startups that may have limited budgets or concerns about the return on investment.
By offering a free quota, sourcifychina.com aims to build trust and establish long-term relationships between the businesses and the suppliers. The platform understands that sourcing partners are crucial to the success of any business, particularly when it comes to injection molding services. By providing a free quota, sourcifychina.com encourages businesses to explore their options and make informed decisions, ultimately leading to successful collaborations.
Furthermore, sourcifychina.com understands the complexities and challenges of sourcing from China. The country is known for its vast manufacturing capabilities, but selecting reliable suppliers can be a daunting task. By providing a free quota, sourcifychina.com ensures that businesses have access to reputable injection molding services suppliers that have been vetted by their platform. This eliminates the guesswork and potential risks associated with sourcing from unfamiliar businesses.
In conclusion, sourcifychina.com offers a free quota from reliable injection molding services suppliers to provide businesses with an opportunity to evaluate their options, build trust, and mitigate the risks associated with sourcing from China. By doing so, they aim to simplify the sourcing process and facilitate successful partnerships between businesses and suppliers.