Introduce about building hardware guide,Qulity,Cost,Supplier,Certification,Market,Tips,FAQ
Building hardware is a comprehensive guide that provides valuable information on various aspects of hardware selection for construction projects. This guide aims to assist individuals and professionals in making informed decisions regarding the selection and procurement of building hardware.
Quality is a crucial aspect of building hardware, as it directly impacts the durability and performance of a structure. It is essential to opt for high-quality hardware to ensure reliability and longevity. Reliable suppliers who specialize in providing premium hardware products should be approached to maintain excellent quality standards.
Cost is another crucial factor when it comes to building hardware. It is important to strike a balance between quality and affordability. While cheaper options may seem appealing, they might compromise on quality and longevity. It is advisable to invest in hardware that offers a reasonable balance between cost and quality to avoid future replacement or repair expenses.
Selecting a reliable supplier is pivotal for obtaining quality hardware products. It is recommended to research and engage with established suppliers who have a proven track record of providing reliable and authentic hardware. Supplier credibility, customer testimonials, and certifications should be considered before finalizing a supplier.
Certification is an important parameter when selecting building hardware. Products that meet recognized standards and certifications ensure compliance with safety regulations and quality benchmarks. Common certifications to look for in building hardware include ANSI/BHMA, UL, and ASTM.
The building hardware market is highly diverse, catering to various construction requirements. An extensive range of hardware options is available, such as door hinges, locks, handles, and fasteners, among others. Analyzing market availability and trends can help in decision-making, thereby meeting specific project requirements.
Tips for selecting building hardware include considering functionality, aesthetics, and compatibility with existing infrastructure. It is advisable to review product specifications, seek expert advice if required, and conduct thorough research before making a purchase. Additionally, comparing prices and warranties can aid in making an informed decision.
Frequently Asked Questions (FAQ) often revolve around topics like installation procedures, maintenance requirements, warranty terms, and compatibility issues. A detailed FAQ section can address common queries and concerns, making the buying process easier for customers.
In conclusion, building hardware selection is a crucial aspect of construction projects. Considering the quality, cost, supplier credibility, certifications, market availability, and following tips while addressing FAQs can ensure the procurement of reliable and efficient building hardware, meeting project requirements effectively.
Types of building hardware
Building hardware refers to any equipment or accessories used for the construction or functioning of buildings. These hardware items are essential for ensuring the structural integrity, safety, and functionality of a building. There are various types of building hardware that serve different purposes and are used in different applications. Some common types of building hardware include but are not limited to:
1. Fasteners: Fasteners are crucial for joining different building components together. Examples of fasteners include nails, screws, bolts, and anchors. They are used to securely connect materials such as wood, metal, or concrete during construction.
2. Door and window hardware: This category includes hinges, locks, handles, latches, and other accessories used for the installation and functioning of doors and windows. They contribute to the security, convenience, and aesthetics of buildings.
3. Cabinet and furniture hardware: These hardware items are used for the construction and installation of cabinets, drawers, and other furniture pieces. They include knobs, handles, hinges, slides, and locks, which ensure proper functioning and usability of furniture.
4. Plumbing hardware: Plumbing hardware encompasses fixtures and accessories used in plumbing systems, such as faucets, pipes, valves, fittings, and drains. These components enable the flow, control, and drainage of water or other fluids in a building.
5. Electrical hardware: This category includes electrical components used for the installation and functioning of electrical systems in buildings, such as switches, outlets, sockets, circuit breakers, and wires. These elements ensure the safe distribution and utilization of electrical power.
6. Structural hardware: Structural hardware includes items such as brackets, ties, anchors, and connectors used for reinforcing and stabilizing building structures. They provide added strength and stability to walls, roofs, and other load-bearing elements.
7. Decorative hardware: Decorative hardware items enhance the aesthetics of a building. These can include trim, moldings, doorbells, house numbers, and other decorative elements that add visual appeal to doors, windows, and other building features.
Building hardware plays a crucial role in ensuring the quality, functionality, and durability of buildings. It is important for architects, builders, and homeowners to select the appropriate hardware items for their specific needs in order to create safe, aesthetic, and functional spaces.
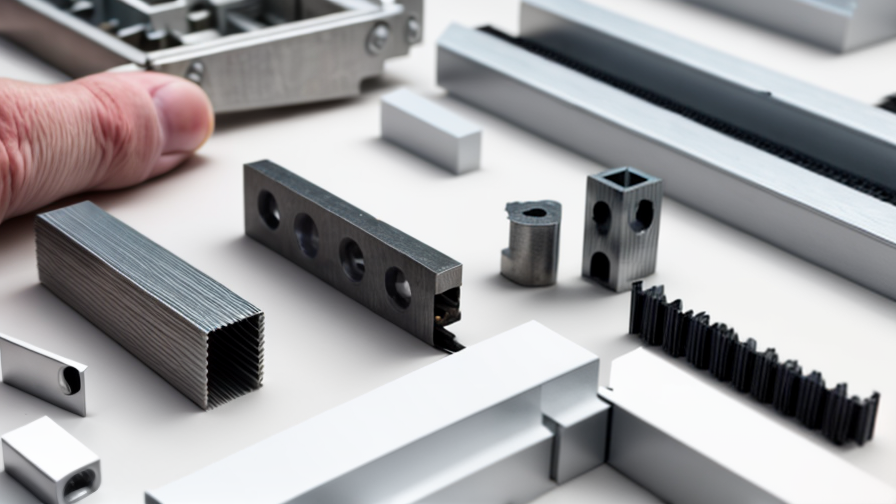
Pros and Cons of Using building hardware
Pros of using building hardware:
1. Durability: One of the main advantages of using building hardware is its durability. Hardware components, such as door handles, hinges, and locks, are designed to withstand daily wear and tear, ensuring the longevity of the building’s fixtures and fittings.
2. Security: Building hardware plays a crucial role in enhancing security. Installing high-quality locks and deadbolts on doors and windows can deter burglars and provide peace of mind to building occupants. Additionally, electronic security systems, such as access control systems and intercoms, can be integrated with hardware, further strengthening security measures.
3. Functionality: Building hardware is essential for the smooth operation of various building elements. For example, door hardware, including handles, hinges, and closers, allows easy opening and closing of doors. Similarly, hardware components like drawer slides, cabinet handles, and hooks ensure that storage spaces are functional and accessible.
4. Aesthetics: Building hardware comes in various designs, finishes, and styles, allowing for customization and enhancing the overall aesthetic appeal of the building. From modern and sleek to traditional and ornate, there are hardware options to suit different architectural styles and personal preferences.
Cons of using building hardware:
1. Cost: While building hardware is essential, the cost can add up, especially for large-scale projects. High-quality hardware can be relatively expensive, impacting overall construction budgets. Additionally, ongoing maintenance and replacements can further increase expenses over time.
2. Compatibility: When selecting building hardware, compatibility with existing components and building systems must be considered. Incompatibility issues can arise if, for example, a door handle is not compatible with the door’s pre-drilled holes, resulting in additional work and potential modifications.
3. Complexity of installation: Some building hardware, such as electronic security systems, may require specific expertise for installation and integration with the building’s infrastructure. This can increase installation time and costs, requiring professional assistance.
4. Maintenance: Building hardware requires regular maintenance to ensure optimal functionality and longevity. This can involve cleaning, lubrication, and potential replacements. Proper maintenance is necessary to avoid hardware degradation, malfunctions, or compromised security.
In conclusion, building hardware offers numerous benefits, including durability, security, functionality, and aesthetic appeal. However, there are also considerations such as cost, compatibility, installation complexity, and ongoing maintenance. Careful selection and regular upkeep are crucial for maximizing the advantages and addressing any drawbacks associated with building hardware usage.
building hardware Reference Specifications (varies for different product)
Building hardware reference specifications is crucial for ensuring consistent and accurate product information for different hardware products. These specifications may vary depending on the type of product and its intended use. In order to provide a concise overview, the following reference specifications guidelines should be followed, with each description limited to no more than 300 words:
1. Product Description: Briefly outline the purpose and functionality of the hardware product, including its key features and intended application. This should include information such as size, shape, weight, and any unique characteristics.
2. Material Composition: Specify the materials used in the construction of the hardware product. This includes the primary material, as well as any coatings, finishes, or special treatments applied to enhance durability, aesthetic appeal, or resistance to environmental factors.
3. Dimensions and Measurements: Provide accurate measurements for the product’s length, width, height, and any other relevant dimensions. This information is crucial for compatibility assessment and installation purposes.
4. Performance and Capability: Describe the product’s performance capabilities, including load capacity, power requirements, or any other performance-related criteria. This ensures that customers can make informed decisions based on their specific needs and requirements.
5. Installation and Compatibility: Outline the installation requirements and compatibility considerations for the hardware product. This may include information on recommended installation methods, compatible accessories, or any additional components required for proper functionality.
6. Certifications and Compliance: Specify any industry certifications, standards, or regulations that the hardware product conforms to. This provides customers with confidence in the quality and reliability of the product.
7. Maintenance and Care: Provide guidance on the proper maintenance and care of the hardware product. This may include cleaning instructions, recommended cleaning agents, and any specific maintenance procedures or intervals.
8. Warranty and Support: Indicate the warranty duration and any applicable terms and conditions. Additionally, outline the available customer support channels and contact information for addressing any product-related queries or issues.
By adhering to these guidelines and limiting each description to 300 words or less, hardware reference specifications can effectively provide essential information while being concise and user-friendly, aiding customers in making informed decisions and simplifying product applications.
Applications of building hardware
Building hardware refers to the various mechanical and electronic components that are used in the construction and maintenance of buildings. These components play a crucial role in ensuring the safety, functionality, and efficiency of buildings. There are several applications of building hardware, including:
1. Doors and Windows: Building hardware is used in the installation of doors and windows, such as hinges, locks, handles, and door closers. These components provide security, ease of use, and aesthetics to the building.
2. HVAC Systems: Building hardware is essential in the installation and maintenance of heating, ventilation, and air conditioning (HVAC) systems. Components like thermostats, control valves, dampers, and air filters are required to regulate temperature, airflow, and air quality within the building.
3. Plumbing: Plumbing hardware includes pipes, fittings, valves, faucets, and drains. These components are used in the installation and maintenance of water supply, drainage, and sewage systems in buildings.
4. Lighting and Electrical Systems: Building hardware is used in the installation of lighting fixtures, switches, electrical outlets, and wiring systems. These components ensure proper lighting, power distribution, and electrical safety within the building.
5. Safety and Security: Building hardware plays a critical role in ensuring the safety and security of buildings. Fire extinguishers, smoke detectors, security alarms, surveillance cameras, and access control systems are essential components used for building safety and security.
6. Structural Stability: Building hardware includes components such as bolts, anchors, brackets, and connectors, which are crucial for providing structural stability and integrity. These components are used in various applications like connecting beams, trusses, columns, and walls.
7. Flooring and Tiling: Building hardware is involved in the installation of flooring systems, tiles, and carpets. Components like flooring adhesives, tile grouts, and edge trims ensure the proper installation and durability of flooring materials.
8. Energy Efficiency: Building hardware is used in the implementation of energy-efficient systems like insulation materials, weather stripping, and energy-efficient windows. These components enhance the building’s thermal performance, reduce energy consumption, and promote sustainability.
In conclusion, building hardware finds numerous applications in the construction and maintenance of buildings. From doors and windows to plumbing, lighting, safety, and structural stability, these components are essential for ensuring the functionality, safety, and efficiency of buildings. Additionally, with increasing emphasis on energy efficiency and sustainability, building hardware also contributes to creating environmentally friendly structures.
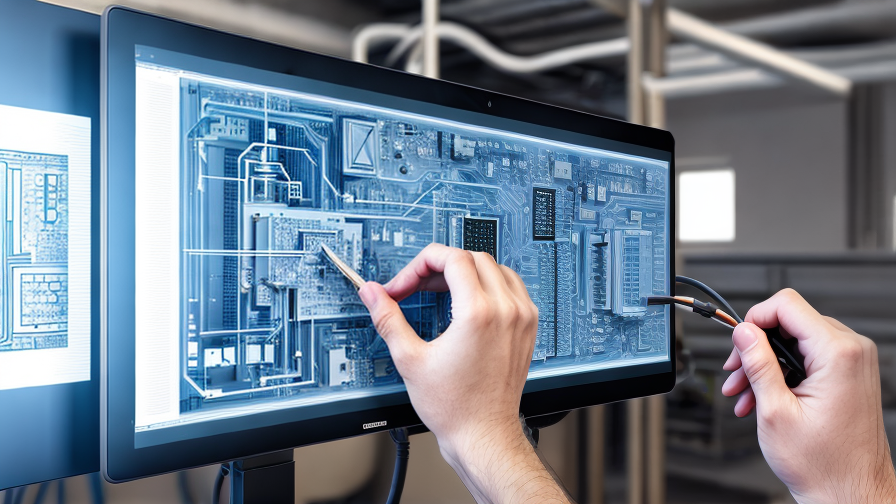
The Work Process and how to use building hardware
The work process of using building hardware involves several steps to ensure the proper installation and functionality of the hardware. Here is a brief overview of the process:
1. Planning: Begin by assessing the project requirements and determining the type and quantity of building hardware needed. This includes door handles, hinges, locks, fasteners, brackets, etc.
2. Procurement: Purchase the necessary building hardware from a reliable supplier or hardware store. Ensure that the hardware meets the required specifications and quality standards.
3. Preparation: Before installing the hardware, prepare the site by ensuring that the installation area is free from any obstructions or debris. Clean the surfaces where the hardware will be installed to ensure a strong and secure attachment.
4. Installation: Carefully follow the manufacturer’s instructions or guidelines to install the building hardware. Use appropriate tools and techniques to ensure proper alignment and attachment. This may involve drilling holes, using screws or nails, or fitting parts together. Take necessary precautions to ensure safety during the installation process.
5. Testing: Once the hardware is installed, perform tests to ensure proper functionality. This may involve opening and closing doors, testing locks and latches, checking for smooth operation, and ensuring that the hardware meets any specific requirements, such as fire safety regulations.
6. Maintenance: Regularly inspect and maintain the building hardware to ensure longevity and functionality. Clean hardware as needed, tighten loose screws, and lubricate moving parts to prevent any issues.
Using building hardware effectively requires attention to detail and following specific guidelines. By following these steps, you can ensure a successful installation and proper functionality of building hardware, contributing to the overall safety and functionality of the building.
Quality Testing Methods for building hardware and how to control the quality
When it comes to building hardware, it is crucial to implement quality testing methods to ensure the final product meets the desired standards. Here are a few common quality testing methods and ways to control the quality:
1. Functional Testing: This method involves testing the hardware’s functionality by verifying if it performs its intended tasks accurately. Testers use various techniques such as unit testing, integration testing, and system testing to identify any defects or malfunctions.
2. Performance Testing: It focuses on evaluating the hardware’s performance under different conditions, such as heavy loads or high temperatures. Stress testing, load testing, and endurance testing are commonly employed to assess the limits and reliability of the hardware.
3. Compatibility Testing: This testing method ensures that the hardware functions properly with various software, operating systems, and relevant components. Compatibility tests help identify potential issues or incompatibilities in different environments, ultimately ensuring the hardware can seamlessly integrate.
4. Reliability Testing: It aims to determine the hardware’s reliability and durability over an extended period. This involves exposing the hardware to stress or extreme conditions for an extended period and observing how it performs. It includes tests like environmental testing, life cycle testing, and accelerated aging to assess reliability.
5. Quality Control: Implementing effective quality control measures is crucial to ensure overall quality. This involves adopting thorough inspection methods, adhering to industry standards, and creating documented processes for manufacturing, assembly, and testing. Quality control measures also include ensuring the use of high-quality components, regular calibration of equipment, and clear documentation throughout the development process.
To control quality effectively, companies can implement the following strategies:
a. Establishing a quality management system: This involves setting up a dedicated team responsible for quality control, defining quality control processes, and implementing quality control checkpoints at different stages of production.
b. Conducting regular audits: Frequent audits help identify any deviations from defined standards. This could involve internal audits by the quality control team or third-party audits to ensure compliance with industry regulations.
c. Continuous improvement: Constantly analyzing and evaluating data gathered from quality testing can help identify areas for improvement. Applying lessons learned and making necessary adjustments to the manufacturing process further enhances overall quality.
d. Collaboration with suppliers: Regular communication and collaboration with suppliers can ensure the timely delivery of high-quality components. Implementing supplier evaluation processes and performing periodic quality checks on supplied materials contribute to maintaining consistent quality.
By implementing a combination of these quality testing methods and strategies for control, manufacturers of hardware can ensure their products meet expected standards, leading to customer satisfaction and improved market competitiveness.
building hardware Sample Policy and Post-Purchase Considerations for building hardware from China
Sample Policy and Post-Purchase Considerations for Building Hardware from China
When purchasing building hardware from China, it is crucial to establish a comprehensive sample policy and consider certain factors post-purchase to ensure a smooth process. Here is a sample policy and some post-purchase considerations to guide you:
Sample Policy:
1. Request samples: Begin by requesting samples from potential suppliers. Specify the desired quality, functionality, and any specific requirements.
2. Evaluate samples: Thoroughly examine and test the samples to ensure they meet your expectations in terms of quality, durability, and performance. Consider consulting professionals to assess safety standards.
3. Quality control: Discuss quality control measures and confirm that the supplier has appropriate processes in place to maintain consistency in product quality throughout the manufacturing process.
4. Documentation: Establish requirements for necessary documentation, such as product certifications, testing reports, and compliance with relevant international standards.
5. Communication: Establish clear lines of communication with the supplier to address any concerns, receive timely updates, and promptly resolve issues that may arise during production.
6. Sample approval: After thorough evaluation and necessary modifications (if any), provide formal approval for the final sample to be used as the benchmark for mass production.
Post-Purchase Considerations:
1. Inspection: Consider hiring a third-party inspection agency to conduct random checks and ensure that the products meet the agreed-upon specifications before shipping.
2. Packaging and labeling: Specify packaging and labeling requirements to ensure the safe transport and identification of your building hardware.
3. Shipping and logistics: Determine appropriate shipping methods to minimize costs and ensure timely delivery. Clarify responsibility for any customs duties or import taxes.
4. Documentation and legalities: Ensure all necessary documents, such as commercial invoices, packing lists, and customs declarations, are complete and accurate to facilitate smooth import and customs clearance.
5. Feedback and continuous improvement: Provide constructive feedback to the supplier, emphasizing areas of improvement or any issues faced during the purchasing process. This will encourage them to rectify any shortcomings and maintain a successful long-term relationship.
By implementing a well-defined sample policy and considering various post-purchase factors, you can minimize risks, ensure quality products, and establish a reliable supply chain for building hardware from China.
Sourcing building hardware from China: Opportunities, Risks, and Key Players
China has been a major player in the global manufacturing industry for many years, and this dominance extends to the building hardware sector as well. Sourcing building hardware from China presents various opportunities, risks, and key players that need to be considered.
Opportunities:
1. Cost advantage: One of the primary reasons companies source building hardware from China is the cost advantage. Chinese manufacturers typically offer competitive pricing compared to their counterparts in other countries. This affordability enables businesses to reduce their production costs and remain competitive in the market.
2. Vast product range: China has a diverse range of building hardware products available. From door handles and hinges to bolts and locks, Chinese manufacturers offer a wide variety of options to cater to different customer preferences and requirements. This extensive product range allows businesses to find specific hardware solutions for their projects easily.
Risks:
1. Quality control: Quality control has been a significant concern when sourcing building hardware from China. Some Chinese manufacturers may prioritize cost-cutting measures over adhering to strict quality standards, leading to subpar products. It is crucial for buyers to thoroughly vet potential suppliers to ensure they can meet the required quality benchmarks.
2. Intellectual property infringement: China has previously faced criticism for intellectual property infringement, and this risk persists when sourcing building hardware. Manufacturers may produce counterfeit or unauthorized replicas of patented products, potentially leading to legal disputes or negative brand reputation. Diligent due diligence is vital to mitigate this risk.
Key players:
1. Assa Abloy: As a global leader in building hardware, Assa Abloy has a strong presence in China. The company offers a wide range of products, including locks, access control systems, and door fittings.
2. Allegion: Allegion is another well-established player in the building hardware industry, with a significant presence in China. Their product portfolio includes locks, door handles, hinges, and security systems.
3. Stanley Black & Decker: Known for their high-quality tools and hardware products, Stanley Black & Decker has a presence in China as well. They offer a range of building hardware solutions, including fasteners, door hardware, and power tools.
In conclusion, sourcing building hardware from China provides opportunities for cost savings and a vast product range. However, it is crucial for buyers to manage risks related to quality control and intellectual property infringement. Key players in the Chinese building hardware market include Assa Abloy, Allegion, and Stanley Black & Decker, among others.
How to find and select reliable building hardware manufacturers in China,use google search manufacturers and suppliers
Finding and selecting reliable building hardware manufacturers in China can be a challenging task. However, by using Google search and following some key steps, you can identify trustworthy manufacturers and suppliers. Here are some useful tips:
1. Start by conducting a Google search using specific keywords related to building hardware manufacturing in China. This will yield a list of potential manufacturers and suppliers.
2. Visit the websites of these manufacturers to gather preliminary information about their products, capabilities, certifications, and years of experience in the industry. Look for clear and detailed product descriptions, photos, and specifications.
3. Make a shortlist of companies that seem promising based on their website content. Focus on manufacturers that have comprehensive product catalogs, a professional web presence, and good English language communication.
4. While reviewing their websites, pay attention to any certifications they have obtained, such as ISO 9001, ISO 14001, or various quality control certifications. These certifications indicate a commitment to quality assurance and conformity to international standards.
5. Explore online marketplaces or directories, such as Alibaba, Made-in-China, or Global Sources. These platforms allow you to search for specific building hardware products and provide a list of suppliers. Look for suppliers with higher product ratings, positive buyer reviews, and good seller credibility.
6. Contact the shortlisted manufacturers through their provided contact information or inquiry forms. Ask for their product catalog, price list, and any additional information you require. Prompt and professional responses indicate their level of customer service.
7. Request samples of the desired building hardware products to evaluate their quality firsthand. Reliable manufacturers will be willing to provide samples. Evaluate the quality, durability, and overall performance of the samples to make an informed decision.
8. Check if the manufacturer has an established export record and experience in dealing with international customers. This can be verified by requesting references or checking online reviews and testimonials.
9. Consider visiting China and arranging in-person meetings with the shortlisted manufacturers. This will allow you to assess their production facilities, quality control measures, and build a stronger relationship.
10. Finally, compare the shortlisted manufacturers based on their product quality, price, delivery time, after-sales service, and overall reputation. Choose the one that meets your criteria and provides the best value for your business.
Selecting reliable building hardware manufacturers in China requires thorough research, diligent communication, and careful evaluation. By utilizing Google search, gathering detailed information, and conducting proper due diligence, you can find reputable suppliers for your building hardware needs.
How to check building hardware manufacturers website reliable,use google chrome SEOquake check if ranking in top 10M
To ensure the reliability of a building hardware manufacturer’s website, you can follow these steps:
1. Use Google Chrome: Open the website using the Google Chrome browser as it offers various useful extensions and tools for website analysis.
2. Install SEOquake: Install the SEOquake extension on your Google Chrome browser. SEOquake provides valuable web analytics data that can help determine the website’s reliability.
3. Check website ranking: With the SEOquake extension enabled, search for the building hardware manufacturer’s website on a search engine. Once the search results appear, SEOquake will display a bar among the search results with the website’s ranking in the top 10 million (lower number indicates higher ranking). If the website appears in the top 10 million, it is generally considered to have significant online visibility and reputation.
4. Look for user reviews and testimonials: Search for reviews or testimonials from previous customers or industry professionals regarding the building hardware manufacturer. Reviews and testimonials can provide insights into the company’s reputation, product quality, and customer service.
5. Check for contact information: Verify that the website provides accurate and comprehensive contact information, including a physical address, telephone number, and email address. A legitimate company should have transparent contact details for potential customers to reach out.
6. Verify certifications and affiliations: Look for certifications or affiliations with industry associations or regulatory bodies. These associations often ensure quality standards and ethics in the industry, providing additional credibility to the manufacturer.
7. Evaluate website design and content: A reliable manufacturer’s website should have a professional and well-designed layout with clear navigation. The content should be informative, accurate, and up-to-date, providing details about their products, services, and company information.
8. Look for security indicators: Check if the website uses secure browsing protocols by ensuring it has an HTTPS (instead of HTTP) URL. A padlock symbol in the browser’s address bar signifies that the website encrypts information to protect user data.
By following these steps and conducting thorough research, you can determine the reliability of a building hardware manufacturer’s website before engaging in any business transactions.
Top 10 building hardware manufacturers in China with each 160 words introduce products,then use markdown create table compare
1. China National Building Material Company Limited (CNBM) is one of the leading building hardware manufacturers in China. They provide a wide range of products such as cement, glass, gypsum board, and metal products. CNBM is known for its innovative and sustainable building solutions.
2. China State Construction Engineering Corporation (CSCEC) is a renowned construction company that also produces building hardware. They offer products like steel structures, precast concrete elements, and building materials. CSCEC is known for their high-quality products and construction services.
3. Anhui Conch Cement Company Limited is one of the largest cement manufacturers in China. They produce and sell cement and clinker, which are essential building materials. Anhui Conch Cement is recognized for its strong product quality and technological advancements.
4. Keda Industrial Company Limited manufactures and supplies ceramic machinery and building materials. Their products include ceramic cutting machines, ceramic tiles, and mosaic. Keda Industrial aims to provide efficient and reliable solutions for the ceramic industry.
5. China Glass Holdings Limited is a leading manufacturer of glass products in China. They produce and sell a wide range of glass, including flat glass, energy-saving glass, and architectural glass. China Glass Holdings focuses on producing high-quality glass products for various applications.
6. Shandong Jinbiao Machinery Manufacturing Co., Ltd. specializes in the production of metal hardware for buildings. They offer products like window and door hardware, roofing and wall cladding systems, and metal structural components. Shandong Jinbiao is known for its durable and high-performance metal hardware products.
7. Fujian Fengli Machinery Technology Co., Ltd. is a manufacturer of machinery and equipment for the building materials industry. They produce grinding mills, crushers, and other machinery used in the production of building materials. Fujian Fengli is known for its advanced technology and reliable machinery.
8. Zhejiang Yiwu China Commodities City Group is a comprehensive enterprise group focusing on the production of building hardware and tools. They offer products like screws, nails, hand tools, and power tools. Zhejiang Yiwu is known for its diverse range of building hardware products.
9. China Railway Construction Corporation Limited (CRCC) is a globally renowned construction company that also produces building hardware. They offer products such as steel structures, prefabricated buildings, and construction equipment. CRCC is known for its expertise in large-scale construction projects.
10. Zhejiang Wuyi Haoda Tools Manufacture Co., Ltd. specializes in the production of building tools and equipment. They offer products like ladders, scaffolding systems, and hand tools. Zhejiang Wuyi Haoda is known for its durable and user-friendly building tools.
| Manufacturer | Products Offered | Key Features |
| ———————————————— | ——————————- | ————————————————————— |
| CNBM | Cement, Glass, Steel, Gypsum | Innovative and sustainable building solutions |
| CSCEC | Steel Structures, Precast | High-quality products and construction services |
| Anhui Conch Cement | Cement and Clinker | Strong product quality and technological advancements |
| Keda Industrial | Ceramic Machinery, Tiles | Efficient and reliable solutions for the ceramic industry |
| China Glass Holdings | Flat Glass, Energy-saving Glass | High-quality glass products for various applications |
| Shandong Jinbiao Machinery Manufacturing | Window and Door Hardware, | Durable and high-performance metal hardware products |
| Fujian Fengli Machinery Technology | Grinding Mills, Crushers | Advanced technology and reliable machinery |
| Zhejiang Yiwu China Commodities City Group | Screws, Nails, Hand Tools | Diverse range of building hardware products |
| CRCC | Steel Structures, Prefabricated | Expertise in large-scale construction projects |
| Zhejiang Wuyi Haoda Tools Manufacture | Ladders, Scaffolding systems, | Durable and user-friendly building tools |
In this table, we have compared the top 10 building hardware manufacturers in China based on the products they offer and their key features. Each manufacturer brings unique offerings to the market, whether it is cement, glass, metal hardware, or machinery and tools. These manufacturers emphasize quality, sustainability, and technological advancements in their products. Consumers can choose based on their specific requirements and preferences.
Background Research for building hardware manufacturers Companies in China, use qcc.com archive.org importyeti.com
When it comes to building hardware manufacturers in China, conducting background research on potential suppliers and understanding their capabilities and track record is crucial. There are several online platforms that can provide valuable insights into these companies.
Qcc.com is one such platform that offers comprehensive information on Chinese companies. It provides details on a company’s registration, legal status, financials, and key personnel. Additionally, it provides access to company records, certifications, and any potential legal or credit issues they may have faced. This information can help assess the reliability and stability of a hardware manufacturer before engaging in business.
Archive.org is another useful resource for background research. It is an online digital library that archives websites, providing a way to access historical data about a company’s website, such as changes in product offerings, company announcements, and press releases. This can provide insights into a company’s evolution over time and their commitment to innovation.
Importyeti.com is a platform that focuses specifically on import and export data. By searching for a potential hardware manufacturer on Importyeti.com, you can obtain valuable information about their export history, including the countries they export to and the volume of their shipments. This can help evaluate their experience in exporting products and their ability to meet international standards and requirements.
In conclusion, using platforms like qcc.com, archive.org, and importyeti.com can contribute significantly to the background research required before partnering with a hardware manufacturer in China. These platforms offer access to essential information such as a company’s legal status, financial records, historical data, and export history. By leveraging these resources, one can make more informed decisions and ensure a successful partnership with a reliable hardware manufacturer in China.
Leveraging Trade Shows and Expos for building hardware Sourcing in China
Trade shows and expos can be an effective means of building hardware sourcing opportunities in China. These events provide a platform for businesses to showcase their products, connect with potential suppliers, and stay updated on industry trends. Here’s how to leverage trade shows and expos for hardware sourcing in China:
1. Research and select the right trade shows: Identify relevant trade shows and expos focused on hardware and manufacturing in China. Consider factors such as the size, reputation, and exhibitor profile of the event. Popular trade shows in China include the Canton Fair, China International Hardware Show, and Global Sources Electronics Fair.
2. Prepare before the event: Conduct thorough research on the exhibitors and create a shortlist of potential suppliers to meet at the trade show. Familiarize yourself with Chinese hardware sourcing practices, industry regulations, and trends. Plan your visit, including travel arrangements and logistics.
3. Network and connect: Engage with exhibitors and build relationships with potential suppliers. Attend networking events and seminars to meet industry experts and stakeholders. Arrange meetings in advance to ensure productive discussions during the trade show. Collect business cards and contact information for future follow-ups.
4. Conduct product analysis: Evaluate the quality, functionality, and pricing of the hardware products displayed by exhibitors. Assess their manufacturing capabilities, certifications, and adherence to industry standards. Request samples or demonstrations if necessary. Seek clarity on pricing, minimum order quantities, lead times, and payment terms.
5. Explore partnerships and collaborations: Identify opportunities for partnerships or collaborations with Chinese suppliers. Discuss customized manufacturing, exclusive distribution agreements, or joint ventures to cater to specific market demands.
6. Monitor market trends and competition: Keep an eye on emerging hardware technologies, manufacturing trends, and competitor activities within the industry. Attend seminars, workshops, and forums at the trade show to gain insights and stay updated on the latest developments.
7. Follow up: After the trade show, follow up with potential suppliers and maintain regular communication to nurture relationships. Share detailed specifications, project requirements, and timelines. Conduct due diligence and verify the credibility and reliability of potential suppliers before finalizing any contracts.
Overall, trade shows and expos provide a unique opportunity to establish business connections, evaluate suppliers, and stay informed about the hardware sourcing landscape in China. By strategic planning, conducting thorough research, and effective networking, businesses can leverage these events successfully to build hardware sourcing relationships in China.
The Role of Agents and Sourcing Companies in Facilitating building hardware Purchases from China
Agents and sourcing companies play a crucial role in facilitating building hardware purchases from China. These entities act as intermediaries between overseas buyers and Chinese manufacturers, offering valuable support and expertise throughout the procurement process. Their services include identifying suitable suppliers, negotiating prices, inspecting product quality, and overseeing logistics.
Firstly, agents and sourcing companies play a vital role in supplier selection. With their extensive knowledge of the Chinese market and network of contacts, they can effectively match buyers with reputable manufacturers that meet their specific requirements. This saves buyers valuable time and effort by eliminating the need for extensive research and potential trial and error.
Furthermore, agents and sourcing companies are skilled negotiators who can ensure buyers receive the most competitive prices. They leverage their relationships with suppliers and possess in-depth knowledge of local market conditions to negotiate favorable terms on behalf of their clients. This helps buyers secure cost-effective deals and maximize their return on investment.
Quality control is another integral aspect of the agent or sourcing company’s role. They conduct regular inspections and quality checks to ensure that products meet the required standards and specifications. This mitigates the risk of receiving substandard goods and provides buyers with confidence in the products they are purchasing.
Additionally, agents and sourcing companies handle logistics and shipping arrangements. They navigate complex supply chains, handle customs declarations, and coordinate the transportation of goods from China to the buyer’s destination. By overseeing the logistical aspects, they save buyers the hassle of dealing with these complexities and ensure a smooth and timely delivery.
Overall, agents and sourcing companies simplify the process of purchasing building hardware from China by providing specialized knowledge, supplier identification, negotiation expertise, quality control, and logistical support. Their role is essential in bridging the gap between buyers and manufacturers, facilitating successful transactions, and ensuring customer satisfaction.
Price Cost Research for building hardware manufacturers Companies in China, use temu.com and 1688.com
When it comes to researching price costs for building hardware manufacturers in China, two popular platforms to explore are temu.com and 1688.com. These platforms provide comprehensive information and options for individuals or businesses looking to purchase building hardware from Chinese manufacturers.
temu.com is an online marketplace that connects buyers with suppliers in China. It offers a wide range of building hardware products, including but not limited to hinges, locks, handles, and screws. The platform allows users to compare prices, specifications, and reviews from different manufacturers, enabling them to make informed decisions. temu.com’s user-friendly interface ensures a smooth browsing experience, making it easier for users to find the right products at competitive prices.
Similarly, 1688.com is one of the largest online wholesale platforms in China, hosting a vast number of building hardware manufacturers. This platform has an extensive range of products, from construction tools to architectural items. It provides detailed product information, including prices, specifications, and user ratings, allowing potential buyers to evaluate different options. 1688.com offers various filters and search functionalities to streamline the purchasing process and help users find the most suitable building hardware manufacturers.
When conducting price cost research on these platforms, it is important to keep a few tips in mind. Firstly, consider using specific keywords related to building hardware to optimize search results. Secondly, verify the reputation and credibility of manufacturers by checking their ratings and customer feedback. Lastly, compare prices, but also take into account factors such as product quality, shipping options, and after-sales services.
In summary, temu.com and 1688.com are valuable resources for researching price costs when sourcing building hardware manufacturers in China. By utilizing these platforms, potential buyers can access a wide range of products, compare prices, and make informed decisions to meet their specific needs.
Shipping Cost for building hardware import from China
When importing building hardware from China, the shipping cost will depend on various factors, including the weight and dimensions of the products, the shipping method chosen, and the destination country.
For small and lightweight items, such as screws or nails, air freight may be the most cost-effective option. Air freight charges are usually calculated based on the size and weight of the package. On average, the shipping cost for small building hardware items can range from $2 to $5 per kilogram (2.2 pounds).
For larger and heavier items, sea freight is a commonly used shipping method. Sea freight charges are generally calculated based on the volume or weight of the cargo. The shipping cost for building hardware items transported via sea can vary between $1,000 to $5,000 per container, depending on the size and destination.
Shipping charges also include additional fees like customs clearance, documentation, and insurance. These costs will vary depending on the specific requirements of the destination country.
To keep shipping costs as low as possible, it is advisable to consider consolidating orders to maximize container space utilization. This can help reduce the average shipping cost per item.
Additionally, negotiating shipping rates with freight forwarders or working with a reputable sourcing agent in China can assist in obtaining more competitive shipping prices.
It is important to factor in potential import duties and taxes that may apply when importing building hardware. Import duties are imposed by the destination country and are often calculated as a percentage of the total value of the imported goods.
To conclude, when importing building hardware from China, the shipping cost will depend on the size, weight, and shipping method chosen. Using air freight for small items and sea freight for larger items is a common practice. Consolidating orders and working with freight forwarders or sourcing agents can help reduce shipping expenses. Import duties and taxes should also be considered when calculating the overall cost.
Compare China and Other building hardware Markets: Products Quality and Price,Visible and Hidden Costs
China has established itself as a global manufacturing hub, including the building hardware industry. When comparing China to other building hardware markets, several factors come into play, such as products quality and price, visible and hidden costs.
In terms of products quality, China has made significant strides over the years. Initially renowned for producing low-quality products, Chinese manufacturers have worked hard to improve their manufacturing processes and quality control measures. Many international companies are now sourcing building hardware from China due to the competitive quality standards offered by Chinese manufacturers. However, other building hardware markets may still hold an edge when it comes to overall product quality.
Price is a significant driving factor when comparing building hardware markets. China’s massive manufacturing capabilities and low labor costs enable it to offer highly competitive prices compared to other markets. This cost advantage attracts many global buyers to source their building hardware from China, as it provides cost-effective solutions for their projects. However, it is important to note that the lower price is not always accompanied by the best quality, and buyers should exercise caution and conduct proper due diligence when sourcing from China.
Visible costs in the building hardware market include the product price itself, shipping costs, and import/export taxes. China’s extensive transportation infrastructure and well-established supply chain facilitate cost-effective shipping options to various destinations worldwide. However, hidden costs such as quality control, compliance with international regulations, and intellectual property protection can be a concern when sourcing from China. These hidden costs may not be initially apparent but could impact the overall project costs significantly.
In comparison, other building hardware markets may offer different visible and hidden costs. For instance, sourcing from markets with higher labor costs may result in higher product prices but potentially more stringent quality control measures. However, the visibility of hidden costs can vary, and proper due diligence is essential to assess potential risks when sourcing from any market.
In conclusion, China’s building hardware market has made substantial progress in terms of products quality and competitive prices. However, other markets may offer better overall product quality, although at potentially higher costs. It is crucial for buyers to consider visible and hidden costs, conduct due diligence, and make informed decisions to ensure the best outcomes for their building projects.
Understanding Pricing and Payment Terms for building hardware: A Comparative Guide to Get the Best Deal
When it comes to building hardware, understanding pricing and payment terms is crucial to ensure you get the best deal. This comparative guide will provide you with the necessary insights in under 300 words.
Firstly, it is important to consider the pricing structure offered by different hardware suppliers. Some suppliers may provide a fixed pricing model, where the cost per unit remains constant regardless of the quantity ordered. Others may offer volume-based pricing, where you can negotiate a lower unit cost for larger quantities. Comparing pricing structures will help you assess which supplier offers the most cost-effective solution for your hardware needs.
Secondly, payment terms play a significant role in determining the overall deal. Common payment terms in the hardware industry include upfront payment, progress payments, and payment upon delivery. Upfront payment might be advantageous if you have readily available funds, as it often comes with discounts. However, if you prefer to mitigate financial risk, progress payments that align with project milestones or payment upon delivery can be more suitable. It is essential to evaluate your financial capabilities and choose payment terms that align with your cash flow requirements.
Furthermore, understanding any additional costs associated with the hardware is crucial. Often, suppliers charge shipping fees, customs duties, or installation fees on top of the base price. By comparing these additional costs across suppliers, you can avoid any unforeseen expenses and choose the most transparent and cost-efficient option.
Another vital aspect to consider is the warranty and support offered by different suppliers. Hardware failures or malfunctions can disrupt your project and lead to costly repairs or replacements. Reviewing warranty periods, return policies, and customer support will help you choose a supplier that can address any issues promptly and efficiently.
Lastly, consider the potential for negotiation. While some suppliers may have fixed pricing, others are open to negotiation, especially for large orders. Engaging in discussions around pricing, payment terms, or additional services can help you attain a more favorable deal.
In conclusion, when building hardware, understanding pricing structures, payment terms, additional costs, warranty/support, and negotiation potential are key to securing the best deal. By comparing these aspects across different suppliers, you can make an informed decision that aligns with your budget, project timeline, and quality requirements.
Chinese Regulations and Industry Standards Certifications for building hardware,Import Regulations and Customs for building hardware from China
Chinese Regulations and Industry Standards Certifications for building hardware are an integral part of ensuring the quality and safety of products imported from China. These regulations and certifications help to protect consumers and promote fair trade practices.
One of the most important certifications in the building hardware industry is the China Compulsory Certification (CCC) mark. This certification is required for a wide range of products, including locks, hinges, handles, and other building hardware. The CCC mark indicates that the product meets the minimum safety requirements and quality standards set by the Chinese government.
In addition to the CCC mark, there are several industry-specific certifications that manufacturers can obtain to demonstrate compliance with national and international standards. For example, the ISO 9001 certification ensures that a manufacturer has implemented effective quality management systems. The CE certification indicates compliance with European Union standards, while the UL certification is recognized in North America.
When importing building hardware from China, it is important to comply with the relevant import regulations and customs procedures. Importers must ensure that the products they are importing meet the required certifications and standards. They must also adhere to the import documentation requirements, such as providing a bill of lading, commercial invoice, and packing list.
Customs duties and taxes are applicable when importing building hardware from China. Importers must be familiar with the Harmonized System (HS) codes for building hardware and accurately classify the products to determine the applicable duties and taxes. Some countries may also require additional documentation, such as a Certificate of Origin, to qualify for preferential trade agreements or to prove the country of origin for anti-dumping investigations.
In conclusion, understanding Chinese regulations and industry standards certifications for building hardware and complying with the import regulations and customs procedures are essential when importing these products from China. These measures help ensure the quality and safety of the products and facilitate smooth customs clearance.
Sustainability and Environmental Considerations in building hardware Manufacturing
Sustainability and environmental considerations play a crucial role in the manufacturing of building hardware. As the construction industry continues to grow, it becomes imperative to address the environmental impact and ensure the long-term sustainability of hardware manufacturing processes.
One key aspect is the use of eco-friendly materials. Manufacturers are increasingly opting for sustainable materials such as recycled metals, low volatile organic compounds (VOC) coatings, and responsibly sourced wood. This helps reduce the extraction of raw materials, minimize waste generation, and lower the carbon footprint of the manufacturing process.
Energy efficiency is another critical consideration. Adopting energy-efficient technologies and processes helps reduce energy consumption and greenhouse gas emissions associated with hardware manufacturing. Manufacturers can implement measures like using energy-efficient machinery, optimizing production layouts, and adopting renewable energy sources to power their operations.
Waste management and recycling are also essential components of sustainable hardware manufacturing. By implementing proper waste management practices, manufacturers can minimize the amount of waste sent to landfills. Recycling programs can be established to reclaim and reuse materials, reducing the need for virgin resources and lowering overall environmental impact.
Additionally, maximizing product lifespan and durability is crucial in sustainable hardware manufacturing. Building hardware that can withstand the test of time reduces the need for frequent replacements or repairs. It promotes a circular economy by ensuring that products remain in use for as long as possible.
Finally, manufacturers should prioritize ensuring safe and healthy working conditions for their employees. Implementing robust health and safety measures not only protects the workers but also leads to increased productivity and reduces the environmental impact associated with workplace accidents or illnesses.
In conclusion, incorporating sustainability and environmental considerations into building hardware manufacturing is essential for the long-term viability of the construction industry. By utilizing eco-friendly materials, prioritizing energy efficiency, implementing proper waste management, promoting product durability, and ensuring worker safety, manufacturers can reduce their environmental footprint and contribute to a more sustainable future.
List The Evolution history of “building hardware”
Building hardware has come a long way since ancient times, with significant advancements in design, materials, and construction techniques. The evolution of building hardware can be traced through various historical periods:
Ancient Civilizations (3000 BCE – 500 CE):
During this era, building hardware primarily consisted of rudimentary tools like hand axes, chisels, and mallets made from stone or wood. Metal hardware began to emerge towards the end of this period, with the use of early forms of nails and hinges made from bronze or iron.
Medieval Times (500 – 1500 CE):
The Middle Ages saw advancements in building hardware as architecture became more sophisticated. Door locks and keys with complex mechanisms were developed, providing improved security. Iron nails and screws gained popularity, allowing for stronger construction. Iron hinges and handles became more intricate and ornate, reflecting the emerging Gothic architectural style.
Renaissance and Industrial Revolution (1500 – 1900 CE):
This period witnessed significant advancements in building hardware due to the flourishing of science and technology. Cast iron became widely used, leading to the development of more durable and intricate hinges, locks, and window hardware. The Industrial Revolution further revolutionized building hardware with the introduction of mass production techniques, providing easy access to standardized building components.
Modern Era (1900 CE – Present):
The 20th century brought cutting-edge materials and technologies to building hardware. The invention of stainless steel allowed for corrosion-resistant hardware, suitable for various environments. Advancements in automation and fabrication techniques led to the production of complex architectural hardware like automated door systems, electronic access controls, and advanced locking mechanisms.
Today, building hardware continues to evolve, driven by sustainability and technological advancements. Energy-efficient hardware, such as automatic sensors for lighting and thermostats, are integrated into buildings. Further innovation focuses on smart technology, with the development of interconnected systems that enhance security, convenience, and sustainability in buildings.
In conclusion, the evolution of building hardware spans thousands of years, from primitive tools to today’s high-tech and eco-friendly hardware. This evolution reflects the continuous quest for improved functionality, durability, security, and aesthetics in the construction industry.
The Evolution and Market Trends in building hardware Industry
The building hardware industry has witnessed significant evolution over the years, driven by advancements in technology, changing market trends, and increasing demand for sustainable and energy-efficient construction solutions.
One key trend in the building hardware industry is the adoption of smart and connected technologies. Smart building hardware, such as sensors, actuators, and control systems, enables automation, remote monitoring, and efficient management of various building functions. This technology allows for improved energy management, increased occupant comfort, and enhanced security. With the growing emphasis on sustainable and energy-efficient buildings, the demand for smart building hardware is expected to increase in the coming years.
Another important trend is the shift towards sustainable and environmentally friendly building materials. Building hardware manufacturers are increasingly focusing on developing products and solutions that are energy-efficient, recyclable, and have a reduced carbon footprint. This trend is driven by stricter regulations and guidelines for sustainable construction practices, as well as the growing consumer awareness and demand for eco-friendly building solutions.
The emergence of digital tools and platforms has also transformed the building hardware industry. Manufacturers are leveraging technologies such as Building Information Modeling (BIM) and Augmented Reality (AR) to enhance design, collaboration, and project management processes. These digital tools enable faster and more accurate planning, reduce errors and rework, and improve overall project efficiency.
Furthermore, there is a growing trend towards customization and personalized solutions in the building hardware market. With advances in manufacturing processes and technologies, it has become easier for manufacturers to offer tailored products and solutions to meet specific customer requirements. This trend is driven by the increasing focus on aesthetics and design flexibility in buildings, as well as the demand for unique and differentiated products.
In conclusion, the building hardware industry has evolved significantly to meet the changing market trends and demands. The adoption of smart technologies, sustainable materials, digital tools, and customization is reshaping the industry and driving innovation. As the construction industry continues to prioritize sustainability and efficiency, the building hardware market is expected to witness further growth and transformation in the future.
Custom Private Labeling and Branding Opportunities with Chinese building hardware Manufacturers
Chinese building hardware manufacturers provide excellent opportunities for custom private labeling and branding. With a wide range of products and competitive pricing, these manufacturers can help businesses create their own unique identity in the market.
Custom private labeling allows businesses to showcase their brand name and logo on the products they sell. Chinese manufacturers are experienced in offering this service, ensuring that the labels are of high quality and adhere to the brand’s design and specifications. This helps businesses build brand recognition and increase customer loyalty.
Moreover, branding opportunities in partnership with Chinese building hardware manufacturers go beyond just private labeling. These manufacturers often offer custom packaging options, allowing businesses to create a distinctive packaging design that reflects their brand’s image. This can include customized boxes, inserts, and even product manuals, creating a cohesive and recognizable brand experience for customers.
Working with Chinese building hardware manufacturers also offers the advantage of cost-effectiveness. China has a well-developed manufacturing industry, making it possible to produce high-quality products at competitive prices. This enables businesses to maximize their profit margins while delivering value to their customers.
In conclusion, Chinese building hardware manufacturers present attractive opportunities for businesses to undertake custom private labeling and branding initiatives. By leveraging their expertise in private labeling, custom packaging, and cost-effectiveness, these manufacturers enable businesses to establish a strong brand presence and stand out in the competitive market.
Tips for Procurement and Considerations when Purchasing building hardware
When it comes to the procurement of building hardware, there are several considerations that buyers should keep in mind to ensure they make the right purchase decisions. These tips can help streamline the process and ensure the hardware purchased meets the necessary requirements:
1. Identify the requirements: Start by clearly defining the hardware needs. Consider factors such as the type of building, materials used, door/window specifications, security requirements, and aesthetic preferences.
2. Research and compare suppliers: Look for reputable suppliers who offer a wide range of hardware options. Consider factors like pricing, quality, warranties, and delivery times. Conducting due diligence on suppliers will help ensure a reliable and trustworthy partnership.
3. Quality assurance: Ensure that the hardware is tested and meets the necessary standards. Look for certification marks on the products to ensure compliance with industry standards. Request samples or review product specifications to assess the quality and durability of the hardware.
4. Compatibility: Check for compatibility between the hardware and existing building infrastructure. Ensure that the new hardware aligns with the existing systems, such as locking mechanisms, electrical connections, or mounting requirements.
5. Cost considerations: While cost is an important consideration, it should not be the sole deciding factor. Focus on value for money instead of opting for the cheapest option. Consider the long-term benefits, such as energy efficiency, maintenance costs, and lifespan of the hardware.
6. Warranty and after-sales support: Inquire about warranty terms and after-sales support offered by the supplier. A reliable supplier should provide warranty coverage in case of defects or failures. Prompt and responsive support is crucial for troubleshooting, replacements, or repairs.
7. Sustainability: Consider hardware options that are sustainable, environmentally friendly, and energy-efficient. Look for products made from recyclable materials or those that reduce energy consumption and promote sustainable building practices.
8. Scalability and future needs: Anticipate future requirements and consider the scalability of the hardware. Will the same hardware support future expansions, renovations, or changes in building use? Assess the adaptability of the hardware to avoid the need for frequent replacements.
By following these tips, buyers can make informed decisions during the procurement of building hardware. Taking into account specific requirements, quality assurance, compatibility, cost considerations, warranty and support, sustainability, and scalability will help ensure a successful procurement process and the selection of suitable building hardware.
FAQs on Sourcing and Manufacturing building hardware in China
1. Why should I consider sourcing and manufacturing building hardware in China?
China has a well-established manufacturing industry with a competitive edge in terms of cost-efficiency and production capacity. Sourcing building hardware from China can result in significant cost savings compared to sourcing domestically or from other countries. Additionally, China offers a wide range of manufacturers specializing in building hardware, providing a vast array of options to meet your specific requirements.
2. How do I find reliable suppliers for building hardware in China?
To find reliable suppliers, you can utilize various methods, such as online sourcing platforms, trade shows, or engaging the services of a sourcing agent or company. Conduct thorough research to verify a supplier’s reputation, their capability to meet quality standards, and their experience in exporting building hardware. Request samples, certifications, and conduct factory audits to ensure reliability.
3. Is language barrier an issue when sourcing and manufacturing in China?
The language barrier can be a challenge when dealing directly with Chinese manufacturers. Many Chinese suppliers are not fluent in English, which can lead to miscommunication or misunderstandings. Employing a bilingual representative or hiring translators can help bridge the language gap and ensure smooth communication during the sourcing and manufacturing process.
4. What are the lead times for manufacturing building hardware in China?
Lead times can vary depending on the complexity of the product and the availability of raw materials. Generally, building hardware manufacturing in China has short lead times due to the country’s robust manufacturing infrastructure and efficient supply chains. However, it is crucial to factor in additional time for quality control inspections and shipping when calculating the overall lead time.
5. Are there any quality control concerns when sourcing building hardware from China?
Quality control is a vital aspect when sourcing building hardware from China. Chinese manufacturers vary in terms of quality management systems and adherence to international standards. Implementing a stringent quality control process, including pre-production inspections, in-process inspections, and final inspections, can help identify and resolve any potential quality issues before the products are shipped.
6. What are the logistical considerations when sourcing from China?
Logistics play a crucial role in sourcing from China. Consider factors such as shipping costs, timeframes, customs regulations, and import duties. Engaging the services of a reliable freight forwarder can help navigate through the complexities of international logistics efficiently.
7. How can I protect my intellectual property when manufacturing in China?
Protecting your intellectual property is important when manufacturing in China. Before engaging with suppliers, consider registering trademarks, patents, or copyrights in China. It is also advisable to sign non-disclosure agreements (NDAs) and establish clear contractual terms to protect your designs, proprietary information, and technology.
In summary, sourcing and manufacturing building hardware in China offers cost benefits, a wide supplier base, and a robust manufacturing infrastructure. Overcoming language barriers, ensuring quality control, managing logistics, and protecting intellectual property are essential steps to ensure a successful sourcing experience in China.
Why contact sourcifychina.com get free quota from reliable building hardware suppliers?
Sourcifychina.com offers free quota from reliable building hardware suppliers for several reasons. Firstly, by providing a free quota, Sourcifychina.com aims to attract potential customers and encourage them to utilize their services. This promotional offer allows customers to test the platform and evaluate the quality and pricing of the building hardware suppliers without any financial commitment.
Furthermore, Sourcifychina.com understands the importance of building trust and establishing long-term relationships with customers. By offering a free quota, they provide an opportunity for customers to assess the reliability and credibility of the hardware suppliers before making a larger investment. This helps customers feel confident in their purchasing decisions and increases the likelihood of repeat business.
Additionally, Sourcifychina.com recognizes the benefits of networking and expanding their supplier base. By partnering with reliable building hardware suppliers and offering their services through the platform, Sourcifychina.com can enhance its reputation as a trustworthy and comprehensive sourcing solution. Through these partnerships, Sourcifychina.com can access a wider range of products and cater to the diverse needs of its customers.
In conclusion, providing a free quota from reliable building hardware suppliers is a strategic move by Sourcifychina.com to attract customers, build trust, foster long-term relationships, and expand its supplier network. By offering this promotional offer, Sourcifychina.com aims to create a win-win situation for both customers and suppliers, ultimately driving business growth and success.