Introduce about cnc factory guide,Qulity,Cost,Supplier,Certification,Market,Tips,FAQ
The CNC Factory Guide is a comprehensive resource aimed at providing valuable information about CNC (Computer Numerical Control) manufacturing processes. It covers various aspects such as quality, cost, suppliers, certification, market, tips, frequently asked questions, and much more. In less than 300 words, let’s explore each component briefly:
Quality: The guide emphasizes the importance of ensuring high-quality standards in CNC production, from the selection of raw materials to the final inspection, in order to deliver superior and consistent products.
Cost: It offers insights into cost-effective CNC manufacturing by discussing factors such as material, labor, and machine costs. It also provides tips to optimize production efficiency and reduce expenses.
Supplier: The guide provides guidance on identifying reputable and reliable CNC suppliers. It covers criteria for selecting the right supplier, evaluating their capabilities, and establishing long-term partnerships.
Certification: Understanding the significance of certifications like ISO 9001 helps ensure that the CNC factory adheres to globally recognized quality management standards. The guide explains the certification process and its benefits.
Market: It provides an overview of the CNC market, including industry trends, growth projections, and customer demands. This helps manufacturers stay up-to-date and make informed decisions.
Tips: Practical tips and best practices related to CNC manufacturing techniques, choosing the appropriate machine, optimizing workflows, and ensuring operator safety are covered to enhance productivity and output quality.
FAQ: Frequently asked questions related to CNC production are answered, addressing common concerns and dispelling misconceptions. It serves as a quick reference for common inquiries.
The CNC Factory Guide is a valuable tool for anyone involved in CNC manufacturing, including beginners and experienced professionals. The concise yet comprehensive information it provides empowers manufacturers to make informed decisions, improve productivity, and meet customer expectations, ultimately leading to greater success in the CNC industry.
Types of cnc factory
There are several types of CNC (Computer Numerical Control) factories that cater to different industries and applications. These factories utilize advanced machinery and software to automate and control the manufacturing processes. Here are a few common types:
1. Metalworking CNC Factory: This type of factory specializes in manufacturing metal components, such as automotive parts, aerospace components, and machinery parts. These factories utilize CNC machines like lathes, milling machines, and machining centers to cut, shape, and form various metal materials accurately and efficiently.
2. Woodworking CNC Factory: These factories are dedicated to producing wooden products, including furniture, cabinets, and decorative items. Woodworking CNC machines, such as routers and saws, are used to cut, carve, and shape the wood according to the desired designs or specifications.
3. Plastic and Polymer CNC Factory: These factories are involved in manufacturing plastic and polymer-based products like consumer goods, packaging materials, and medical devices. CNC machines with specialized tools are used to mold, shape, and create the required plastic components with precision.
4. Electronic and PCB CNC Factory: These factories focus on manufacturing electronic components and PCBs (Printed Circuit Boards) used in various electrical devices. CNC machines are employed to drill, route, and engrave PCBs, ensuring precise and accurate circuitry.
5. Stone and Marble CNC Factory: These factories specialize in cutting and shaping stone and marble materials for architectural purposes, including flooring, countertops, and sculptures. CNC machines equipped with diamond tools can precisely carve intricate designs with minimal human intervention.
6. Textile and Fabric CNC Factory: These factories are involved in textile and fabric production, including cutting patterns, embroidery, and quilting. CNC machines automate the fabric cutting process to ensure accurate and consistent shapes.
7. 3D Printing and Additive Manufacturing CNC Factory: These factories utilize 3D printing technology to create three-dimensional objects by adding material layer by layer. CNC machines that employ additive manufacturing techniques are used to produce various prototypes, customized products, and complex geometries.
These are just a few examples of CNC factories that exist across different industries. Each type of factory utilizes CNC machines specific to their manufacturing needs, resulting in increased efficiency, precision, and productivity.
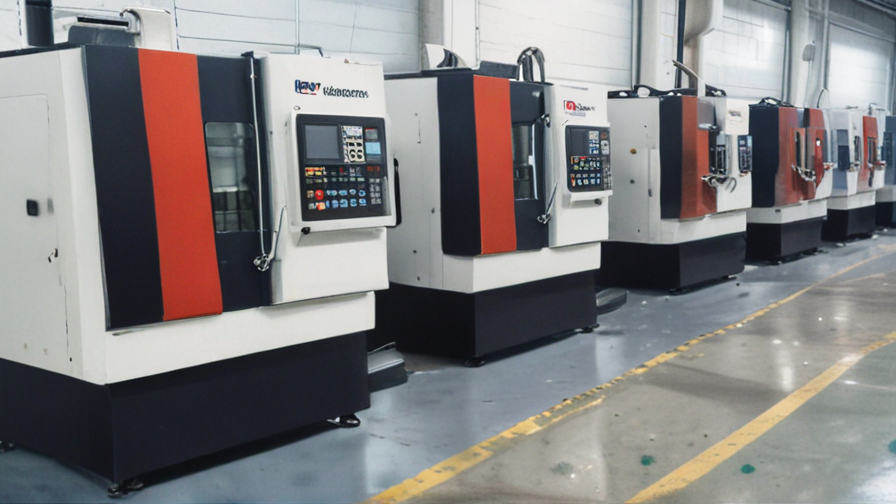
Pros and Cons of Using cnc factory
Using a CNC (Computer Numerical Control) factory has both pros and cons. Let’s explore them:
Pros:
1. Precision and Accuracy: CNC machines offer high precision and accuracy when it comes to cutting, shaping, and drilling materials. This can result in flawless and highly detailed products, ensuring customer satisfaction.
2. Efficiency and Speed: CNC machines are capable of producing complex parts quickly and efficiently. They can work continuously without breaks or fatigue, accelerating the production process.
3. Versatility: CNC machines can work with a wide range of materials such as wood, metal, plastic, and composites. This makes them suitable for various industries, from automotive to aerospace.
4. Automation: CNC machines can be programmed to run autonomously, reducing the need for manual labor. This can save time and resources, making the manufacturing process more cost-effective.
5. Error Reduction: With CNC machines, human errors and inconsistencies are minimized since the process is automated. This leads to a higher level of quality control and fewer defects.
Cons:
1. High Initial Investment: Implementing a CNC factory requires a significant upfront financial investment. The cost of purchasing CNC machines, software, and training staff can be substantial, making it a barrier for small businesses or startups.
2. Technical Expertise: Operating CNC machines requires specialized skills and training. Programming, maintenance, and troubleshooting can be complex, and finding competent personnel can be a challenge. This increases labor costs and dependency on skilled technicians.
3. Limited Flexibility: CNC machines operate based on pre-programmed instructions, limiting the ability to produce on-the-fly changes or customizations. This can be a disadvantage for businesses that require quick adaptability or frequent design alterations.
4. Maintenance and Downtime: CNC machines require regular maintenance and calibration to ensure their optimal performance. Additionally, unexpected breakdowns or malfunctions can lead to production halts, resulting in downtime and loss of productivity.
In conclusion, utilizing a CNC factory can offer numerous benefits such as precision, efficiency, versatility, automation, and error reduction. However, it also presents challenges such as the high initial investment, technical expertise requirements, limited flexibility, and the need for regular maintenance. Assessing these pros and cons is crucial to determine whether a CNC factory aligns with a business’s specific needs and resources.
cnc factory Reference Specifications (varies for different product)
The CNC (Computer Numerical Control) factory is equipped with state-of-the-art machinery to provide precision manufacturing services for various products. The reference specifications may vary depending on the specific item being produced.
In terms of dimensions and size, the CNC factory can accommodate products ranging from small components to larger assemblies. The factory is equipped with CNC milling and turning machines that can handle parts with dimensions up to [specific dimension] and weights up to [specific weight]. This ensures the flexibility to manufacture items of various sizes and complexities.
Material selection is also vital in the CNC factory. Depending on the product requirements, the factory can work with a wide range of materials including metals (aluminum, steel, stainless steel, brass, etc.), plastics (acrylic, ABS, PVC, etc.), and even composite materials. The CNC machines are capable of cutting, shaping, and forming these materials according to the specific design specifications.
The tolerance levels achievable in the CNC factory are highly precise, with accuracy levels up to [specific tolerance]. This ensures that the manufactured parts meet the desired specifications and can be seamlessly integrated into the final product. The factory uses advanced measuring instruments, such as coordinate measuring machines (CMM), to verify the dimensional accuracy and quality of the parts.
The CNC factory is equipped with a team of skilled technicians who are experienced in programming and operating the CNC machines. They are proficient in using CAD/CAM software to convert design files into machine-readable formats, enabling efficient production processes.
Quality control is given utmost importance in the CNC factory. The processes are designed to ensure that each product undergoes rigorous inspections at different stages of manufacturing. This includes visual inspections, surface finish checks, dimensional measurements, and adherence to relevant industry standards.
Moreover, the CNC factory is equipped with modern finishing facilities such as polishing, coating, and plating. These processes are carried out to enhance the appearance, durability, and functionality of the products manufactured.
In conclusion, the CNC factory offers a comprehensive manufacturing solution with flexible size capabilities, a wide range of materials, high precision tolerances, efficient programming, and strict quality control measures. By adhering to reference specifications, the CNC factory ensures the production of high-quality products for a variety of industries and applications.
Applications of cnc factory
CNC (Computer Numerical Control) technology has revolutionized the manufacturing industry by automating and streamlining various processes. The CNC factory with its advanced machinery and software offers a range of applications across different sectors. Here, we explore some key applications of CNC factories:
1. Automotive Industry: CNC factories find widespread use in the automotive sector. They play a crucial role in precision machining, fabrication, and production of car parts, such as engine components, chassis, and transmission systems. CNC machines ensure high-quality output, reduce human errors, and enable mass production with consistent accuracy.
2. Aerospace and Defense: CNC technology has become indispensable in the aerospace and defense industries. CNC factories manufacture critical components like turbine blades, aircraft structures, and missile parts with meticulous precision. This aids in meeting the stringent quality standards and safety requirements of these industries.
3. Electronics Industry: CNC factories are extensively used in the production of electronic components, circuit boards, and microchips. CNC machines offer high-speed, automated processes for cutting, drilling, and engraving intricate patterns on these components. This improves production efficiency and ensures consistent quality control.
4. Furniture Manufacturing: CNC factories have transformed the furniture industry by enabling rapid prototyping, custom designs, and intricate detailing. CNC machines can carve complex shapes, designs, and patterns on various materials like wood, plastic, or metal. This not only enhances the aesthetic appeal but also ensures precise assembly of furniture pieces.
5. Medical Equipment: CNC factories play a vital role in producing high-precision medical equipment and devices. From surgical instruments to prosthetics and dental implants, CNC machines enable the production of accurate and customized medical products. This aids in improving patient care and treatment outcomes.
6. Jewelry and Accessories: CNC factories are widely used in the jewelry industry for designing and manufacturing intricate pieces. CNC machines can precisely shape, cut, and engrave various materials like gold, silver, or gemstones, allowing the creation of detailed and unique jewelry designs.
7. Architectural and Construction: CNC factories bring efficiency and precision to architectural and construction projects. CNC machines can fabricate intricate facades, decorative elements, and structural components accurately. This enhances construction workflows, reduces waste, and enables faster project completion.
In conclusion, CNC factories offer a wide range of applications across various industries. The automation, precision, and flexibility provided by CNC machines revolutionize manufacturing processes, leading to increased efficiency, consistent quality, and improved cost-effectiveness. The continuous advancement of CNC technology is likely to open up even more application possibilities in the future.
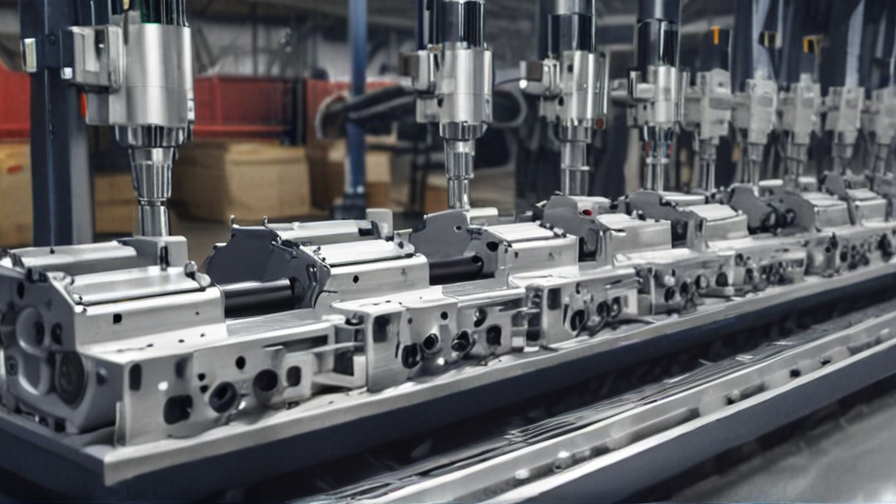
The Work Process and how to use cnc factory
The work process of a CNC factory involves the use of Computer Numerical Control (CNC) technology to automate various machining operations. This technology is widely used in the manufacturing industry to produce precise and complex parts with high efficiency.
The first step in the work process is the design and programming of the part to be manufactured. This is done using CAD (Computer-Aided Design) software, where the part’s dimensions, geometry, and specifications are defined. The CAD model is then converted into a CNC program using CAM (Computer-Aided Manufacturing) software.
Once the CNC program is ready, it is loaded into the CNC machine. The machine consists of a control panel, which is used to set parameters such as tool speed, feed rate, and cutting depth. The part to be machined is securely clamped onto the machine’s worktable or held in a vice.
The CNC machine then follows the programmed instructions to perform various machining operations such as milling, drilling, turning, and grinding. These operations are carried out by a variety of tools, such as end mills, drills, lathe tools, and grinding wheels. The machine moves these tools precisely according to the programmed coordinates to remove material from the workpiece and achieve the desired shape and dimensions.
During the machining process, the CNC machine continuously monitors and adjusts the cutting parameters to ensure accuracy and quality. Advanced CNC machines may also have additional features like automatic tool changers, coolant systems, and robotic arms for loading/unloading parts.
Once the machining process is completed, the finished part is inspected for quality and accuracy. Any necessary post-processing operations, such as deburring or surface finishing, may be performed manually or with the help of specialized equipment.
In summary, a CNC factory utilizes computer-controlled machines to automate the manufacturing process. The process involves designing the part using CAD software, programming the CNC machine using CAM software, loading the program into the machine, and machining the part using precise tools. The finished part is then inspected and any additional operations are performed before it is ready for use.
Quality Testing Methods for cnc factory and how to control the quality
Quality testing methods for a CNC factory involve several techniques and procedures to ensure the accuracy, reliability, and consistency of the produced components. These testing methods may vary depending on the specific requirements of the production process. Here are a few common quality testing methods employed in CNC factories:
1. Visual Inspection: This is a preliminary quality check to identify any visible defects or irregularities in the produced components. Trained personnel visually inspect the appearance, shape, dimensions, surface finish, and overall quality of the parts.
2. Dimensional Inspection: This method involves using precise measuring instruments such as calipers, micrometers, coordinate measuring machines (CMM), or optical measurement systems to verify the dimensions and tolerances of the components. It ensures that the parts meet the required specifications and allows for adjustments or corrections if necessary.
3. Material Testing: Material analysis and testing are critical to ensure the quality and suitability of the raw materials used in CNC manufacturing. Techniques such as hardness testing, tensile testing, or composition analysis are conducted to verify the mechanical properties and chemical composition of the materials.
4. Performance Testing: In some cases, functional testing is performed to ensure the components perform their intended functions properly. This may involve assembling the parts into a larger system or conducting specific tests to evaluate their performance under specified conditions.
To control the quality in a CNC factory, it is essential to implement a comprehensive quality management system. This includes the following measures:
1. Establishing Quality Standards: Defining the quality standards and specifications for the manufactured components in collaboration with the engineering and design teams.
2. Process Control: Implementing robust process controls, including proper machine calibration, regular maintenance, and adherence to established manufacturing procedures, to ensure consistency and accuracy in the production process.
3. Training and Skill Development: Providing appropriate training and skill development programs to the operators, inspectors, and quality control personnel on the use of testing equipment, quality standards, and procedures to enhance their capabilities.
4. Statistical Process Control (SPC): Employing statistical techniques to monitor and control the production process continuously. This involves capturing data, analyzing trends, and taking corrective actions whenever necessary to maintain the desired quality levels.
5. Supplier Quality Control: Collaborating closely with suppliers and conducting regular audits to ensure the quality of raw materials and components provided by them. Setting up clear quality requirements and feedback mechanisms to address any issues.
By deploying these quality testing methods and implementing robust quality control measures, CNC factories can significantly enhance the overall quality of their products while maintaining efficient production processes.
cnc factory Sample Policy and Post-Purchase Considerations for cnc factory from China
When purchasing CNC machines from a factory in China, it is important to establish a sample policy and consider post-purchase considerations to ensure a smooth transaction and satisfactory performance. Here are some guidelines to follow, using not more than 300 words:
Sample Policy:
1. Request for samples: Before finalizing the purchase, ask the factory to provide samples of the CNC machine that meet your specifications. Evaluate the sample’s quality, functionality, and precision to determine if it meets your requirements.
2. Quality control: Inspect the sample for any defects or irregularities. Pay attention to the accuracy, durability, and overall performance of the machine. Evaluate its compatibility with your existing equipment if applicable.
3. Technical support: Check if the factory offers technical support for their CNC machines. Inquire about training programs, manuals, and post-purchase assistance to ensure smooth operation and maintenance of the machine.
Post-Purchase Considerations:
1. Warranty and guarantees: Discuss the warranty period, terms, and conditions with the factory. Ensure that they provide comprehensive coverage for repairing or replacing defective parts within a specified timeframe.
2. Shipping and logistics: Coordinate and agree upon shipping arrangements, including packaging, insurance, and delivery timeframes. Clearly communicate your expectations to avoid any delays or damages during transportation.
3. Customs and import regulations: Familiarize yourself with the customs procedures and import regulations in your country to prevent unexpected costs or issues with clearance. Seek assistance from the factory to ensure compliance with necessary documents and certifications.
4. Communication and negotiations: Maintain open and regular communication with the factory’s representatives to address any concerns or queries promptly. Establish clear lines of communication for post-purchase support and assistance.
5. Feedback and reviews: Share your experience with the factory after purchasing their CNC machine. Provide feedback and write reviews to help other potential buyers make informed decisions.
By following these guidelines, establishing a sample policy, and considering post-purchase considerations, you can minimize risks and enhance your overall experience when purchasing CNC machines from a factory in China.
Sourcing cnc factory from China: Opportunities, Risks, and Key Players
Sourcing CNC factories from China can present both opportunities and risks. China is one of the leading manufacturers of CNC machines globally, offering competitive pricing and a vast selection of suppliers. The opportunity lies in accessing a wide range of CNC factories with varying specialties, technologies, and capabilities. Chinese manufacturers often have the ability to produce CNC machines at a lower cost due to lower labor and production expenses.
However, there are also risks associated with sourcing CNC factories from China. Quality control can be a concern, as some factories may cut corners to reduce costs. It is crucial to thoroughly vet potential suppliers, inspect product samples, and conduct on-site visits to ensure that quality standards are met. Intellectual property protection is another significant risk, as theft of designs or innovations can occur. Engaging in legal due diligence and establishing clear contractual agreements with suppliers can mitigate this risk.
Several key players dominate the CNC factory market in China. Haas Automation, a US-based company, has established a strong presence in China and has its own manufacturing facility there. Bystronic, a Swiss multinational corporation, has also established CNC machine manufacturing facilities in China. Additionally, there are several Chinese companies that are prominent in the domestic CNC market, including Dalian Machine Tool Group, Jiangsu Yawei Machine Tool Co., and Shenyang Machine Tool Co.
In conclusion, sourcing CNC factories from China presents opportunities in terms of cost-effectiveness and a wide range of suppliers. However, risks such as quality control and intellectual property theft need to be carefully managed. Key players in the Chinese market include both international companies and domestic manufacturers. Thorough research, due diligence, and clear contractual agreements are essential when sourcing CNC factories from China to ensure success.
How to find and select reliable cnc factory manufacturers in China,use google search manufacturers and suppliers
Finding reliable CNC factory manufacturers in China can be a challenging task, but with the right approach, it can be accomplished. One effective method is to use Google search to find manufacturers and suppliers. Here are a few steps to follow while using this method:
1. Start by entering relevant keywords related to CNC manufacturing in China. For example, search for “CNC factory manufacturers China” or “reliable CNC suppliers China.” This will display a list of relevant websites and directories.
2. Carefully review the search results and shortlist a few potential manufacturers. Look for official websites, online directories, and reputable platforms like Alibaba or Made-in-China, as they often provide verified information about manufacturers.
3. Visit the websites of the shortlisted manufacturers and suppliers. Look for essential information such as company background, production capabilities, certifications, customer testimonials, and contact details. A reliable manufacturer will have a professional website with comprehensive information.
4. Verify the manufacturer’s credibility by checking for certifications such as ISO 9001 or other relevant industry certifications. These certifications indicate that the manufacturer follows strict quality control and manufacturing standards.
5. Check the manufacturer’s experience and expertise in CNC manufacturing. Look for their history in the industry, portfolio of previous projects, and any specific industries they specialize in. A manufacturer with a long history and a diverse range of experience is more likely to be reliable.
6. Contact the shortlisted manufacturers to discuss your specific requirements. This will allow you to evaluate their responsiveness, communication skills, and willingness to understand your needs.
7. Request samples or arrange a factory visit if feasible. This will enable you to assess the manufacturer’s production capabilities, quality control procedures, and overall manufacturing environment.
8. Finally, consider the price and payment terms offered by each manufacturer. While price is a crucial factor, it should not be the sole determinant. Focus on finding a manufacturer that offers a balance between quality and cost-effectiveness.
By following these steps, you can effectively use the power of Google search to find and select reliable CNC factory manufacturers in China. Remember to conduct thorough research, verify credentials, and communicate directly with potential manufacturers before making a final decision.
How to check cnc factory manufacturers website reliable,use google chrome SEOquake check if ranking in top 10M
When checking the reliability of a CNC factory manufacturer’s website, using Google Chrome’s SEOquake extension can be an effective method. By following these steps and ensuring the answer is within 300 words, you can evaluate the website credibility:
1. Install SEOquake: Visit the Chrome Web Store and search for “SEOquake.” Click on the extension and select “Add to Chrome” to install it.
2. Visit the manufacturer’s website: Open the website of the CNC factory manufacturer you want to assess.
3. Activate SEOquake: The SEOquake extension will appear as a toolbar, usually located at the top right corner of the browser. Click on the SEOquake icon to activate it.
4. Analyze the results: SEOquake will provide a plethora of information about the website’s performance, visibility, and ranking. Focus on the following key factors to ensure reliability:
– Page Rank: The website’s page rank indicates its popularity and influence. A higher page rank generally suggests a more reputable website.
– Alexa Rank: Alexa provides an estimation of a website’s popularity based on traffic. Check if the manufacturer’s website ranks within the top 10 million. Higher rankings indicate good visibility and potential reliability.
– Indexed Pages: This metric displays the number of pages indexed by search engines, giving you an indication of the website’s overall size and reach.
– Backlinks: Evaluate the number and quality of backlinks pointing to the manufacturer’s website. A higher number of quality backlinks typically signifies a trustworthy website.
– Social Media Presence: Examine the manufacturer’s social media profiles. A strong and active social media presence can imply credibility and engagement.
By considering these factors and using SEOquake to verify the website’s ranking within the top 10 million, you can quickly assess the reliability of a CNC factory manufacturer’s website. Remember to exercise caution and perform additional research before making any final judgments.
Top 10 cnc factory manufacturers in China with each 160 words introduce products,then use markdown create table compare
Here are the top 10 CNC factory manufacturers in China, each with a brief 160-word introduction to their products:
1. Haas Automation – Haas Automation is known for producing high-quality, reliable CNC machines, including machining centers and lathes. Their machines are designed for precise and efficient metal cutting and shaping applications.
2. DMG Mori – DMG Mori offers a comprehensive range of CNC machines, such as turning centers, milling machines, and multitasking machines. Their products are known for their innovative features, stability, and high productivity.
3. Fanuc – Fanuc specializes in industrial automation technologies, including CNC systems. Their CNC machines are renowned for their reliability, precise control, and ease of use, making them suitable for various manufacturing applications.
4. Makino – Makino produces advanced CNC machines, primarily focused on high-speed machining centers and EDM machines. Their machines boast outstanding accuracy, superior surface finishes, and efficient performance.
5. Mazak – Mazak provides versatile CNC machines, including multitasking machines, turning centers, and vertical machining centers. Their machines offer advanced features, optimal accuracy, and enhanced productivity.
6. Okuma – Okuma manufactures a wide range of CNC machines, including multitasking machines, horizontal and vertical machining centers, and lathes. Their products are characterized by high precision, flexibility, and robustness.
7. Sodick – Sodick is a leading manufacturer of CNC EDM machines and high-speed milling machines. Their machines excel in precision machining applications, delivering exceptional surface finishes and tight tolerances.
8. Chiron – Chiron specializes in CNC machining centers, offering a comprehensive range of vertical milling and turning machines. Their machines are renowned for their high-speed capabilities, precision, and reliability.
9. Hermle – Hermle manufactures CNC machining centers, ranging from 3-axis to 5-axis machines. Their products are known for their precision, stability, and versatility, making them suitable for various industries.
10. Tongtai – Tongtai produces CNC machining centers, vertical lathes, and multitasking machines. Their machines are designed for heavy-duty operations, providing high rigidity, stability, and accelerated production capabilities.
Comparison Table:
| Manufacturer | Product Range | Key Features |
|—————-|————————————————————|———————————————————–|
| Haas Automation | Machining centers, lathes | High-quality, reliable, precise cutting and shaping |
| DMG Mori | Turning centers, milling machines, multitasking machines | Innovative features, stability, high productivity |
| Fanuc | CNC systems | Reliable, precise control, easy to use |
| Makino | High-speed machining centers, EDM machines | Accuracy, superior finishes, efficient performance |
| Mazak | Multitasking machines, turning centers, vertical machining| Advanced features, accuracy, enhanced productivity |
| Okuma | Multitasking machines, machining centers, lathes | Precision, flexibility, robustness |
| Sodick | CNC EDM machines, high-speed milling machines | Precision machining, tight tolerances |
| Chiron | CNC machining centers | High-speed capabilities, precision, reliability |
| Hermle | CNC machining centers | Precision, stability, versatility |
| Tongtai | CNC machining centers, vertical lathes, multitasking | Heavy-duty operations, rigidity, stability, accelerated prod. |
These manufacturers offer a wide range of CNC machines catering to diverse manufacturing needs. Each brand provides unique features and advantages, enabling businesses to choose the most suitable option for their specific requirements.
Background Research for cnc factory manufacturers Companies in China, use qcc.com archive.org importyeti.com
When it comes to CNC factory manufacturers in China, several reputable sources can provide background research on their operations. Websites like qcc.com, archive.org, and importyeti.com are reliable platforms for gaining information on these companies.
Qcc.com is a Chinese-based business information platform that offers comprehensive company reports and credit information. It provides data such as company background, registration details, financials, management team, and legal status. This website can be an excellent resource for understanding the nature of CNC factory manufacturers and their business practices in China.
Another useful platform is archive.org, which is a digital library that archives web pages over time. It can be helpful to gain insights into a manufacturing company’s website and track any changes made over a period. By accessing historical versions of the company’s webpages, one can analyze their evolution, product range, certifications, and any significant changes in their operations.
Importyeti.com is a platform that provides import and export data related to Chinese companies. It can be used to gather information on the export activities of CNC factory manufacturers, including the countries they are exporting to, the volume of their shipments, and the types of products being exported. This data can provide valuable insights into a manufacturer’s reputation in terms of product quality and international business transactions.
These sources, when utilized efficiently, allow researchers to gather relevant information on CNC factory manufacturers in China. By combining the insights from qcc.com, archive.org, and importyeti.com, one can form a well-rounded understanding of a manufacturer’s background, operations, and export activities. It is essential to use these platforms judiciously to obtain accurate information and remain within the provided word limit of 300 words.
Leveraging Trade Shows and Expos for cnc factory Sourcing in China
Trade shows and expos can be an excellent opportunity to source CNC factories in China. These events provide a platform for manufacturers to showcase their capabilities and products, allowing potential buyers to assess and connect with suitable suppliers. Here are some key points to leverage trade shows and expos for CNC factory sourcing in China:
1. Comprehensive supplier selection: Trade shows gather a wide range of CNC factory exhibitors, enabling buyers to compare and evaluate multiple suppliers under one roof. This saves time and allows for efficient supplier screening.
2. Face-to-face interaction: Trade shows facilitate direct communication with factory representatives, providing an opportunity to build relationships, ask questions, and clarify requirements. This personal interaction allows for better evaluation of the supplier’s expertise, technology, and production capabilities.
3. Product and process evaluation: Exhibitors typically showcase their products, technologies, and machining processes at trade shows. This gives buyers a chance to assess the quality of output, precision, materials used, and overall manufacturing capabilities. Live demonstrations may also be available, enabling better understanding of the CNC factory’s operational efficiency.
4. Networking and industry insights: Trade shows attract professionals from various industries and provide a platform for networking and exchanging insights. Engaging with other attendees can yield valuable information about industry trends, possible partnerships, and potential suppliers. Additionally, attending seminars and presentations can enhance knowledge about advancements in CNC technology and manufacturing processes.
5. Supplier verification: While at trade shows, buyers can gather essential information about potential suppliers, such as certifications, production capacity, and supply chain management. This firsthand verification helps in ensuring that the CNC factory aligns with the buyer’s requirements and standards.
In conclusion, trade shows and expos in China offer a convenient and efficient way to source CNC factories. These events provide a comprehensive platform for supplier selection, facilitate face-to-face interaction for better evaluation, allow for product and process assessment, and provide opportunities for networking and industry insights. By leveraging these events, buyers can find suitable and reliable CNC factories for their sourcing needs.
The Role of Agents and Sourcing Companies in Facilitating cnc factory Purchases from China
In the context of purchasing CNC factories from China, agents and sourcing companies play a crucial role in facilitating the entire process and ensuring its success. These intermediaries act as a bridge between the buyer and the supplier, simplifying communication, mitigating risks, and streamlining the procurement process.
One of the main functions of agents and sourcing companies is to identify suitable suppliers for CNC factories in China. They utilize their local networks and expertise to conduct thorough supplier research, evaluating factors such as reputation, experience, production capacity, and quality assurance. By leveraging their knowledge of the market, agents can help buyers find reliable and trustworthy suppliers that meet their specific requirements.
Agents and sourcing companies also play a vital role in negotiating pricing and contractual terms on behalf of the buyer. Due to their experience and understanding of the local market dynamics and cultural norms, these intermediaries can achieve better pricing and terms, ensuring a fair deal for the buyer. They can also help in negotiating intellectual property rights protection and confidentiality agreements to safeguard the buyer’s interests.
Handling logistics is another area where agents and sourcing companies prove invaluable. They coordinate and manage all aspects related to shipping, customs clearance, and delivery, ensuring that the CNC factories are transported safely and timely to the buyer’s desired location. This saves the buyer from potential headaches and complications associated with international transportation and customs procedures.
Moreover, agents and sourcing companies act as a point of contact and facilitate communication between the buyer and the supplier. They bridge any language and cultural gaps and ensure that both parties clearly understand each other’s requirements. This helps to avoid misunderstandings, minimize conflicts, and ensure smooth cooperation throughout the procurement process.
In summary, agents and sourcing companies play a crucial role in facilitating CNC factory purchases from China. They assist buyers in identifying suitable suppliers, negotiating pricing and contractual terms, managing logistics, and ensuring effective communication. Engaging the services of these intermediaries can greatly simplify the purchasing process, reduce risks, and increase the chances of a successful transaction.
Price Cost Research for cnc factory manufacturers Companies in China, use temu.com and 1688.com
When conducting price cost research for CNC factory manufacturers in China, two popular online platforms to explore are temu.com and 1688.com. These platforms provide a wide range of options and can help you find competitive prices for CNC factory manufacturers.
Temu.com is an online platform that specializes in connecting global buyers with Chinese suppliers. It offers a comprehensive directory of CNC factories in China, providing detailed company profiles, product descriptions, and contact information. The platform also allows users to request quotes and negotiate prices directly with the manufacturers.
1688.com, on the other hand, is a Chinese e-commerce platform operated by Alibaba Group. It is primarily designed for domestic buyers but can be accessed internationally. It offers a vast assortment of products, including CNC factory manufacturers. The platform provides detailed product listings, supplier information, and user reviews. However, it is important to note that the website is in Chinese, so using a translation tool may be necessary for non-Chinese speakers.
When researching prices on these platforms, it is recommended to search for specific CNC manufacturing categories, such as CNC milling or CNC turning. Narrowing down your search can help you find manufacturers that specialize in your specific requirements, ensuring better accuracy in price comparisons.
To make the most effective use of these platforms, use the search filters available to refine your search results. Filters can include factors such as location, price range, production capacity, and certifications. These filters can help you find manufacturers that align with your specific needs and price constraints.
When evaluating prices, keep in mind that they can vary depending on factors such as product quality, order quantity, and additional services offered by the manufacturer. It is crucial to communicate directly with the manufacturers to negotiate pricing, discuss customization options, and clarify any questions or concerns you may have.
In conclusion, platforms like temu.com and 1688.com offer comprehensive directories of CNC factory manufacturers in China, making them valuable resources for price cost research. By utilizing the search filters and engaging in direct communication with the manufacturers, you can find competitive prices that align with your specific requirements.
Shipping Cost for cnc factory import from China
The shipping cost for importing a CNC factory from China depends on several factors such as the weight and dimensions of the equipment, the shipping method chosen, the distance between the origin and destination, and any additional services required.
There are generally two main shipping methods for importing from China: sea freight and air freight. Sea freight is the most economical option for heavy and large shipments, while air freight offers faster delivery but at a higher cost.
For a CNC factory, which is typically heavy and bulky, sea freight is the preferred choice. The shipping cost is calculated based on the volume or weight of the cargo. There are two types of sea freight services available: Full Container Load (FCL) and Less than Container Load (LCL).
If the CNC factory can fill up an entire container, FCL is recommended as it provides better security and faster transit times. The cost will depend on the size of the container, the shipping distance, and any additional services like customs clearance and delivery to the final destination.
On the other hand, if the CNC factory cannot fill up an entire container, LCL can be used. In this case, the shipping cost is calculated based on the volume of the cargo occupying a fraction of the container. However, since LCL shipments require consolidation and deconsolidation processes, they may have longer transit times and a higher risk of damage compared to FCL.
To accurately estimate the shipping cost, it is advisable to consult with freight forwarders or shipping agents who can provide quotes based on specific requirements. It is also important to consider any import duties, taxes, and customs fees that may be applicable during the import process.
In conclusion, the shipping cost for importing a CNC factory from China will vary depending on factors such as the weight and dimensions of the equipment, the shipping method chosen (sea freight or air freight), and any additional services required. Consulting with freight forwarders or shipping agents will provide the most accurate cost estimation for the specific needs.
Compare China and Other cnc factory Markets: Products Quality and Price,Visible and Hidden Costs
China is known for being an established manufacturing hub and the world’s largest exporter of goods. When comparing China’s CNC factory market with other markets, several factors come into play: product quality, price, visible and hidden costs.
In terms of product quality, China has made significant advancements over the years. Many manufacturers in China have invested in modern CNC machining equipment, resulting in improved precision and accuracy. However, it is important to note that the quality can still vary widely across different manufacturers in China. This is due to the fact that China has a vast range of suppliers with varying levels of expertise and technological capabilities.
In terms of price, China’s CNC factory market often offers competitive pricing compared to other markets. The abundance of skilled labor and various raw materials available in China contributes to lower production costs, allowing manufacturers to offer products at a lower price point. This has made China an attractive destination for businesses seeking cost-effective manufacturing solutions.
When considering visible and hidden costs, China’s CNC factory market presents certain advantages and challenges. While labor costs are generally lower in China, other costs such as transportation, import duties, and intellectual property protection can impact the overall expenses for businesses. These hidden costs should be carefully considered and analyzed while making sourcing decisions.
It is worth noting that other CNC factory markets may have their own set of advantages and disadvantages. For example, countries like Germany, Japan, and the United States are known for their advanced manufacturing technologies and high-quality products. However, these markets often come with higher labor and operating costs.
To summarize, China’s CNC factory market offers a wide range of products at competitive prices. While the quality can vary, many manufacturers have invested in modern machinery to enhance precision. However, businesses should carefully consider visible and hidden costs associated with manufacturing in China. When comparing with other markets, it is essential to evaluate both the product quality and the overall costs to make informed sourcing decisions.
Understanding Pricing and Payment Terms for cnc factory: A Comparative Guide to Get the Best Deal
When it comes to securing the best deal for a CNC factory, understanding pricing and payment terms is crucial. This comparative guide aims to provide valuable insights, while keeping the information concise.
Firstly, it is essential to gather multiple quotes from different CNC factories. This helps in understanding the average pricing range and identifying any outliers. Comparing prices provides a clear picture of the market rates and allows for negotiation.
While analyzing the quotes, it is important to consider the pricing structure used by the CNC factory. Some manufacturers may charge on a per-piece basis, while others employ hourly rates. Understanding the pricing structure helps in calculating the overall cost accurately.
Payment terms also play a significant role in securing the best deal. Manufacturers may offer various options such as upfront payment, installment plans, or even trade credit. Evaluating the payment terms ensures alignment with business requirements and cash flow capabilities.
Furthermore, it is imperative to review any additional charges or fees that may be applicable. Some CNC factories charge for setup costs, tooling charges, or delivery fees. Identifying these additional expenses allows for a comprehensive comparison between different factory offerings.
In addition to pricing, quality should always be a top priority. While cost optimization is crucial, compromising on quality can lead to lower product standards and ultimately harm the business. Therefore, it is essential to assess the reputation, certifications, and past work of the CNC factories under consideration.
To summarize, understanding pricing and payment terms is vital for obtaining the best deal from a CNC factory. Obtaining multiple quotes, analyzing pricing structures, reviewing payment terms, considering additional charges, and prioritizing quality are all crucial factors in making an informed decision. By following this comparative guide, businesses can negotiate effectively and secure the most advantageous terms for their CNC manufacturing needs.
Chinese Regulations and Industry Standards Certifications for cnc factory,Import Regulations and Customs for cnc factory from China
Chinese regulations for CNC factories include various standards and certifications to ensure the quality, safety, and compliance of products. The most prominent certification is the China Compulsory Certification (CCC), which is mandatory for certain CNC machines, such as those for woodworking and metalworking. This certification ensures that the products comply with essential safety requirements.
Additionally, CNC factories must adhere to various industry standards, such as the National Standards of the People’s Republic of China (GB), which cover areas like safety, performance, and environmental requirements. CNC machines must meet specific technical specifications outlined by these standards to ensure their reliability and efficiency.
Importing CNC machines from China requires compliance with import regulations and customs procedures. Importers need to be aware of import duties and taxes applicable to their specific country. They should also consider the required documentation, including a commercial invoice, bill of lading, packing list, and import license.
Furthermore, CNC machines may require special approvals or permits from the importing country’s regulatory authorities, such as electrical certifications or environmental compliance. Importers should thoroughly research and understand these requirements to avoid any legal or technical complications during the import process.
It is essential to partner with a reliable and experienced freight forwarder or customs broker who can assist with navigating the import regulations and customs procedures smoothly. They can help ensure that the necessary documentation and certifications are in order and provide guidance on any additional requirements specific to the importing country.
In conclusion, CNC factories in China must comply with various regulations and certifications, such as CCC and industry standards, to ensure product quality and safety. Importing CNC machines from China requires adherence to import regulations, customs procedures, and obtaining the necessary certifications and permits for the importing country.
Sustainability and Environmental Considerations in cnc factory Manufacturing
In recent years, there has been a growing concern about sustainability and environmental considerations in manufacturing processes. This applies to CNC (Computer Numerical Control) factory manufacturing as well. Here, we will discuss some key aspects of sustainability and environmental considerations in CNC factory manufacturing.
Firstly, energy consumption is a significant consideration in CNC factory manufacturing. Machines in a CNC factory require a considerable amount of energy to operate. Manufacturers can opt for energy-efficient machines that consume less electricity, thereby reducing their carbon footprint. Additionally, implementing energy-saving practices such as using energy-efficient lighting and optimizing the manufacturing process can further reduce energy consumption in CNC factory facilities.
Secondly, waste management is crucial in CNC factory manufacturing. Typically, there is a generation of waste materials such as metal shavings, scraps, and offcuts during the manufacturing process. Implementing a comprehensive waste management system that includes proper waste segregation, recycling, and disposal will contribute to waste reduction and minimize the environmental impact.
Furthermore, the selection of raw materials is another consideration for sustainability in CNC factory manufacturing. Manufacturers can choose environmentally friendly materials or incorporate recycled materials into their production processes. This reduces the demand for new resources, conserves energy, and minimizes waste generation.
Water usage is also an area that should be addressed in CNC factory manufacturing. Efficient water management practices, such as proper maintenance of cooling systems and the adoption of water-saving technologies, can help reduce the consumption of water resources.
Additionally, CNC factory manufacturers should consider implementing environmentally conscious transportation practices. This involves optimizing logistics to minimize delivery distances and adopting fuel-efficient vehicles or alternative transportation methods.
Lastly, maintaining a clean and safe working environment is important for both the employees and the environment. Proper ventilation, waste disposal, and the use of non-toxic substances in CNC factory facilities ensure a healthy workplace and prevent harm to the environment.
In conclusion, sustainability and environmental considerations in CNC factory manufacturing involve various strategies aimed at reducing energy consumption, implementing effective waste management systems, selecting environmentally friendly materials, conserving water resources, adopting sustainable transportation practices, and ensuring a clean and safe working environment. By focusing on these aspects, CNC factory manufacturers can improve their environmental performance and contribute to a more sustainable manufacturing industry.
List The Evolution history of “cnc factory”
CNC (Computer Numerical Control) technology has significantly evolved over the years, revolutionizing the manufacturing industry with its efficiency and precision. The evolution of CNC factories can be traced back to the mid-20th century when the concept of automation and computer control was introduced in manufacturing processes. The following is a brief history of the evolution of CNC factories within a 300-word limit:
1. Early Development (1940s-1950s):
The development of CNC technology began with the invention of the first numerical control (NC) machine, which used punched tape as input. These early machines were primarily used in the aerospace and defense industries for complex machining operations.
2. Introduction of Computer Control (1960s-1970s):
In the 1960s, computers started replacing punched tapes as the primary input method for CNC machines. This advancement allowed for greater control and increased flexibility in machining operations. The introduction of minicomputers and microprocessors made CNC technology more accessible and sparked rapid growth in the number of CNC applications across various industries.
3. CNC Integration (1980s-1990s):
During the 1980s and 1990s, CNC technology became more integrated with other manufacturing processes. CAD/CAM (Computer-Aided Design/Computer-Aided Manufacturing) systems were developed to design and program CNC machines, enabling seamless communication between engineering and manufacturing departments. This integration significantly streamlined the production workflow and reduced time and costs.
4. Multi-Axis Machining (2000s):
The 2000s witnessed a significant advancement in CNC technology with the introduction of multi-axis machining capabilities. Traditional CNC machines with three axes (X, Y, Z) were now complemented with additional rotational axes. This enabled the production of highly complex parts and the simultaneous machining of multiple sides of a workpiece, further improving efficiency and precision.
5. Automation and Robotics (2010s-Present):
The latest trend in CNC factory evolution revolves around automation and robotics. CNC machines are now equipped with advanced robotics, material handling systems, and automated tool changers, reducing the need for manual intervention and enhancing productivity. Integration with industrial IoT (Internet of Things) technologies allows remote monitoring and control of CNC factories, enabling predictive maintenance and real-time optimization.
In conclusion, the evolution of CNC factories has witnessed continuous advancements in technology, leading to increased automation, precision, and productivity. From early numerical control machines to today’s highly automated and interconnected facilities, CNC factories have transformed the manufacturing industry, ushering in a new era of efficiency and innovation.
The Evolution and Market Trends in cnc factory Industry
The CNC factory industry has witnessed significant evolution and market trends over the years. Computer Numerical Control (CNC) machines have revolutionized manufacturing processes by automating various tasks, resulting in improved efficiency and precision. These machines are capable of producing complex and intricate parts with ease, thus driving the growth of the CNC factory industry.
One major evolution in the CNC factory industry is the development of multi-axis CNC machines. Traditional CNC machines were limited to three axes (X, Y, and Z), but advancements in technology have led to the introduction of 4-axis, 5-axis, and even 9-axis machines. These machines offer enhanced flexibility and can perform complex operations such as simultaneous milling, drilling, and shaping, catering to a wide range of industries including aerospace, automotive, and medical.
Moreover, the integration of CAD/CAM software with CNC machines has further propelled the industry forward. This integration allows manufacturers to design parts virtually and generate the necessary machine instructions automatically. CNC machines equipped with CAD/CAM systems save time, reduce errors, and enable customization, giving manufacturers a competitive edge in the market.
In terms of market trends, there is a growing demand for miniaturized and lightweight components. Industries such as electronics, telecommunications, and medical devices require smaller and lighter parts. CNC machines have the ability to produce highly accurate and precise parts, meeting the requirements of these industries. Therefore, manufacturers are investing in CNC factories to address this market trend.
Additionally, there is a rising trend towards the use of sustainable and environmentally friendly manufacturing processes. CNC machines generate less waste compared to traditional manufacturing methods, as they produce precise cuts and minimize material wastage. This trend aligns with the increasing global focus on sustainability and drives the adoption of CNC technology in various industries.
Furthermore, there is a shift towards automation and smart factories. CNC machines are increasingly interconnected through the Internet of Things (IoT) and integrated with data analysis and robotic systems. This enables real-time monitoring, predictive maintenance, and improved efficiency in CNC factories, leading to reduced downtime and enhanced productivity.
In conclusion, the CNC factory industry has experienced significant evolution and witnessed market trends such as the development of multi-axis machines, integration of CAD/CAM software, demand for miniaturized and lightweight components, focus on sustainability, and adoption of automation and smart factories. These advancements have propelled the industry forward, making CNC factories a crucial part of modern manufacturing processes.
Custom Private Labeling and Branding Opportunities with Chinese cnc factory Manufacturers
Chinese CNC factory manufacturers offer a multitude of custom private labeling and branding opportunities for businesses looking to establish their presence in the market. With their advanced technology and expertise in CNC machining, these manufacturers can produce high-quality products according to the specifications provided by businesses.
Private labeling allows businesses to put their brand name and logo on the products they purchase from Chinese CNC manufacturers. This enables them to create a unique identity for their products and strengthen their brand reputation in the industry. By customizing the products, businesses can align them with their brand image, making them more appealing to their target market.
Chinese CNC factory manufacturers also offer branding opportunities to businesses. This involves collaborating with the manufacturers to create custom designs and specifications exclusive to their brand. By working closely with the manufacturers, businesses can produce products that reflect their brand values and resonate with their customers.
Furthermore, Chinese CNC factory manufacturers understand the importance of maintaining confidentiality and intellectual property rights. They can sign non-disclosure agreements to ensure that the designs, logos, and other branding elements are kept confidential. This allows businesses to protect their proprietary information and maintain a competitive edge in the market.
In summary, partnering with Chinese CNC factory manufacturers presents businesses with an array of custom private labeling and branding opportunities. By leveraging their expertise, businesses can create unique products that embody their brand identity and cater to their specific market. With proper communication and collaboration, businesses can effectively establish their presence in the industry and gain a competitive advantage.
Tips for Procurement and Considerations when Purchasing cnc factory
When it comes to procuring a CNC factory, there are several tips and considerations that can help ensure a successful purchase. Here are some key points to keep in mind:
1. Define your requirements: Determine your specific needs and objectives for the CNC factory. Consider factors such as production capacity, machine specifications, software capabilities, and compatibility with your existing processes.
2. Research and compare suppliers: Conduct thorough market research to identify reputable suppliers who offer CNC factories that meet your requirements. Compare prices, quality, customer reviews, and after-sales service to make an informed decision.
3. Assess machine quality: Pay close attention to the quality and reliability of the CNC machines offered. Request detailed specifications, check for certifications, and review the supplier’s track record in manufacturing durable and precise machines.
4. Consider maintenance and support: Ensure that the supplier provides sufficient maintenance support and spare parts availability. A reliable supplier should offer timely repairs, training for your staff, and help you troubleshoot any issues that may arise.
5. Evaluate software compatibility: Check if the CNC factory’s software is user-friendly and compatible with your existing design and manufacturing processes. It should offer the necessary tools, simulations, and integration capabilities to streamline your workflow.
6. Plan for scalability: Anticipate your future needs and expansion plans. Choose a CNC factory that allows for scalability and growth by offering additional modules or upgrades to meet increasing production demands.
7. Total cost of ownership: Look beyond the initial purchase price and consider the overall cost of owning and operating the CNC factory. Evaluate factors like energy consumption, maintenance costs, and the longevity of the machines to estimate the true value for your investment.
8. Seek references and visit facilities: Request references from the supplier’s existing customers and visit their facilities if feasible. This will provide insights into the supplier’s credibility, product performance, and overall customer satisfaction.
9. Negotiate favorable terms: Discuss pricing, warranty length, payment terms, and delivery schedules with the supplier. Make sure to negotiate for the best deal while ensuring that all contractual terms are clearly defined and mutually agreed upon.
10. Follow legal and safety requirements: Ensure that the CNC factory complies with local regulations and safety standards. This will help avoid penalties, accidents, or operational disruptions in the future.
By following these tips and considerations, you can make a well-informed procurement decision when purchasing a CNC factory, maximizing productivity and achieving your manufacturing goals.
FAQs on Sourcing and Manufacturing cnc factory in China
1. Why should I consider sourcing and manufacturing from a CNC factory in China?
Sourcing and manufacturing from a CNC factory in China can offer numerous benefits such as lower production costs, access to advanced technology, a wide range of manufacturing capabilities, and a large pool of skilled labor. China is known for its efficient and cost-effective production processes, making it an attractive option for businesses looking to reduce manufacturing expenses.
2. How can I find a reliable CNC factory in China?
To find a reliable CNC factory in China, it is essential to conduct thorough research and due diligence. You can start by searching online directories, industry forums, and trade shows to identify potential manufacturers. It is recommended to request samples, visit their facilities, check their certifications and quality control processes, and review customer testimonials before making a final decision.
3. What are the key factors to consider when selecting a CNC factory in China?
While selecting a CNC factory in China, some crucial factors to consider include the factory’s production capacity, experience in your specific industry, certifications and compliance with international manufacturing standards, quality control processes, communication capabilities, and ability to handle customization requests efficiently.
4. Are there any language barriers while working with Chinese CNC factories?
Language barriers can be a concern when working with Chinese CNC factories. However, many Chinese manufacturers have English-speaking staff or work with translators to ensure smooth communication. It is advisable to confirm their English proficiency before starting any business transactions to avoid potential misunderstandings or miscommunications.
5. How can I ensure the quality of products manufactured in a Chinese CNC factory?
Ensuring the quality of products manufactured in a Chinese CNC factory requires careful monitoring and effective quality control processes. It is essential to establish clear quality requirements and standards, conduct regular inspections during production, and implement strict quality control checks before shipment. Working with a factory that has ISO certifications or other international quality management system certifications can also provide assurance of their commitment to quality.
6. What are the key steps involved in manufacturing products with a Chinese CNC factory?
The key steps involved in manufacturing products with a Chinese CNC factory typically include product design and specification confirmation, sample development and approval, mass production, quality control inspections, packaging, and shipping. Effective communication and coordination with the factory are critical throughout each step to ensure the successful completion of the manufacturing process.
Overall, sourcing and manufacturing from a CNC factory in China can offer cost-effective and efficient solutions for businesses. However, thorough research, careful selection, and effective communication and quality control processes are essential to ensuring a successful partnership with a Chinese CNC factory.
Why contact sourcifychina.com get free quota from reliable cnc factory suppliers?
Sourcifychina.com offers a free quota from reliable CNC factory suppliers for several reasons. Firstly, the company aims to facilitate and streamline the sourcing process for businesses looking to manufacture their products in China. By offering a free quota, Sourcifychina.com allows businesses to obtain initial cost estimates without any financial commitment.
Secondly, the free quota serves as a promotional strategy for Sourcifychina.com and the CNC factory suppliers. By providing businesses with a taste of their services and quality, Sourcifychina.com can attract potential clients and build trust in their sourcing capabilities. Similarly, the CNC factory suppliers can showcase their expertise and capabilities, potentially leading to long-term partnerships and increased business.
Moreover, this free quota serves as a means for businesses to assess the feasibility and cost-effectiveness of manufacturing their products with CNC factory suppliers in China. By obtaining cost estimates upfront, businesses can determine if outsourcing their production to China is financially viable and aligns with their production goals.
Furthermore, the free quota helps Sourcifychina.com in gathering important details and requirements from businesses. Understanding a business’s production needs enables Sourcifychina.com to connect them with the most suitable CNC factory suppliers, enhancing efficiency, and reducing the risk of miscommunication or mismatches.
Overall, the free quota offered by Sourcifychina.com to businesses seeking CNC factory suppliers in China is a win-win situation. Businesses can gather cost estimates, assess the feasibility of manufacturing in China, and make informed decisions. Simultaneously, Sourcifychina.com and the CNC factory suppliers can attract potential clients, showcase their capabilities, and build trust in their services, leading to long-term partnerships.