Introduce about cnc lathe machining parts guide,Qulity,Cost,Supplier,Certification,Market,Tips,FAQ
CNC lathe machining parts refer to the components that are manufactured using computer numerical control (CNC) lathes. This process involves using a lathe machine that is controlled by a computer program to precisely shape and cut various materials such as metal, plastic, or wood. The use of CNC technology ensures accuracy, repeatability, and improved product quality.
When it comes to quality, CNC lathe machining parts are known for their high precision and excellent surface finish. The CNC machines can produce complex shapes and intricate designs that may not be easily achievable with traditional machining methods. This results in parts that have tight tolerances, ensuring a perfect fit and optimal functioning.
In terms of cost, CNC lathe machining parts can be relatively expensive due to the use of advanced technology and the need for skilled operators. However, the initial investment can be offset by the reduced labor costs, increased production efficiency, and minimized material waste. Additionally, the high-quality output reduces the chances of rework or defects, saving both time and money in the long run.
Finding a reliable supplier is crucial for obtaining high-quality CNC lathe machining parts. It is important to look for manufacturers that have a good track record, experience in the industry, and state-of-the-art equipment. The supplier should also be responsive, adaptable to customization requirements, and able to meet delivery deadlines consistently.
Certifications play a significant role in ensuring the quality and reliability of CNC lathe machining parts. ISO 9001 certification is a widely recognized standard for quality management systems, indicating that the manufacturer has implemented quality control processes and meets international quality standards.
The market for CNC lathe machining parts is extensive and diverse. These parts are widely used in industries such as automotive, aerospace, medical, electronics, and many others. With the increasing demand for precision components, the market is expected to continue to grow.
Here are a few tips for CNC lathe machining parts:
1. Provide accurate and detailed specifications to the supplier to ensure the desired outcome.
2. Choose the appropriate material for your specific application to optimize performance and durability.
3. Regularly maintain and calibrate the CNC machine to ensure accuracy and prolong its lifespan.
4. Communicate openly with the supplier to address any concerns or modifications timely.
Frequently Asked Questions (FAQ) about CNC lathe machining parts:
Q: What is the typical turnaround time for CNC lathe machining parts?
A: The turnaround time depends on factors such as complexity, quantity, and the supplier’s production capacity. It is best to consult with the supplier for an accurate estimate.
Q: Can CNC lathe machining parts be customized?
A: Yes, CNC machining allows for high flexibility in customization. You can provide design specifications to achieve the desired shape, size, and surface finish.
Q: Are CNC lathe machining parts suitable for high-volume production?
A: Yes, CNC machines are known for their high production efficiency, accuracy, and repeatability, making them ideal for high-volume production.
In summary, CNC lathe machining parts offer high quality, precision, and customization options. While the initial cost may be higher, they provide excellent value for money in terms of performance, durability, and reduced wastage. Finding a reliable supplier with quality certifications is essential for obtaining the desired outcome. The market for CNC lathe machining parts is vast, catering to various industries’ needs. Following some tips and understanding common FAQs can help optimize the CNC lathe machining process.
Types of cnc lathe machining parts
CNC lathe machining is a subtractive manufacturing process that involves cutting away material from a workpiece to create a desired shape or part. This process is commonly used in industries such as automotive, aerospace, and electronics to produce precision parts with high accuracy and consistency. There are various types of CNC lathe machining parts that can be produced. Some of them include:
1. Shafts: CNC lathes are often used to produce shafts, which are cylindrical components with varying lengths and diameters. These are commonly found in engines, pumps, and other rotating machinery.
2. Bushings: CNC lathe machining is ideal for creating bushings, which are cylindrical sleeves used as bearings, spacers, or reducers. They are commonly found in automotive applications and industrial equipment.
3. Flanges: Flanges are flat, disc-like components with holes that are used to connect pipes, valves, and other objects. CNC lathes can produce precise flanges with accurate dimensions and hole alignments.
4. Connectors: CNC lathe machining is often used to produce connectors, which are components that join two or more parts or systems together. Connectors can be found in a wide range of applications, such as electrical connectors, plumbing connectors, and hydraulic connectors.
5. Pins: CNC lathes are commonly used to produce pins, which are cylindrical components used for fastening, alignment, or support. Pins can come in different shapes and sizes, such as dowel pins, taper pins, and split pins.
6. Collars: CNC lathe machining is suitable for producing collars, which are cylindrical components used for positioning, guiding, or securing other parts. Collars can be found in applications such as shaft collars, split collars, and set collars.
7. Nuts and bolts: CNC lathes are often used to produce nuts and bolts, which are threaded fasteners used to join parts together. These are essential components in various industries, including automotive, construction, and machinery.
8. Bearings: CNC lathe machining is capable of producing precision bearings, which are crucial components for reducing friction and allowing smooth motion between parts. Bearings can come in different types, such as ball bearings, roller bearings, and plain bearings.
9. Pulleys: CNC lathes can produce pulleys, which are components used in power transmission systems to transfer motion and power between rotating shafts. Pulleys can have various designs, such as V-belt pulleys, timing pulleys, and flat belt pulleys.
These are just some examples of the types of parts that can be produced using CNC lathe machining. The process offers versatility, precision, and the ability to work with a wide range of materials, making it a popular choice for manufacturing various components in different industries.
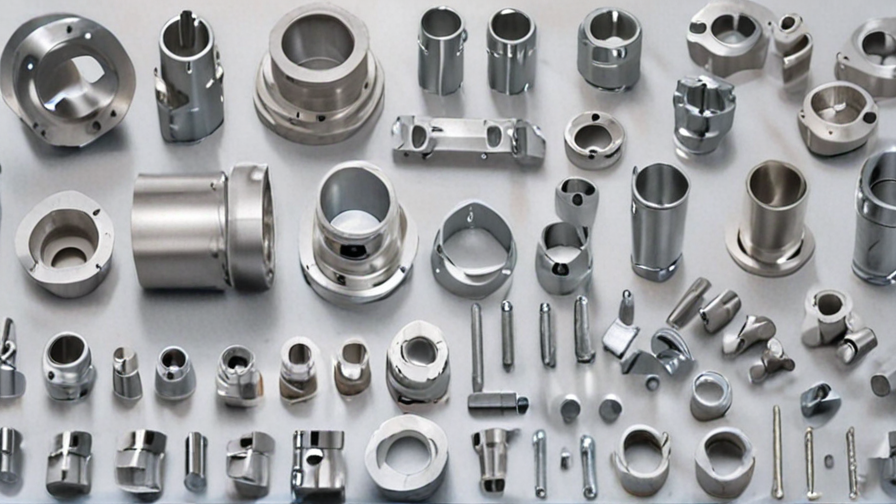
Pros and Cons of Using cnc lathe machining parts
CNC lathe machining parts have become increasingly popular in various industries for their precision, efficiency, and versatility. However, they also come with their own set of pros and cons. Let’s explore some of these advantages and disadvantages within a limited word count of 300 words.
Pros:
1. Precision: CNC lathe machining parts offer excellent accuracy and consistency, ensuring that each product adheres to exact specifications. This precision is especially important when dealing with complex and intricate designs.
2. Efficiency: These machines are highly automated, enabling them to work continuously without the need for human intervention. This significantly reduces production time and increases overall efficiency.
3. Versatility: CNC lathe machining parts can be utilized in a wide range of applications, from automotive and aerospace industries to medical equipment and consumer electronics. They can handle various materials like metal, plastic, and wood, making them ideal for diverse manufacturing needs.
4. Flexibility: CNC machines allow for quick and easy reprogramming, making it possible to produce different parts without major reconfigurations. This adaptability is beneficial for companies dealing with low volume, high mix production demands.
5. Consistency: Because CNC lathe machining parts are programmed and controlled digitally, they eliminate the possibility of human error and provide consistent results. This is especially significant when it comes to mass production, ensuring uniformity among all produced parts.
Cons:
1. High Initial Investment: CNC lathe machines are expensive, making them less accessible for small businesses or startups with limited budgets. The cost of purchasing and maintaining the equipment can be a significant drawback for companies on a tight financial plan.
2. Skilled Operators Required: Although CNC machines automate the manufacturing process, they require skilled operators who can program, monitor, and troubleshoot these complex systems. Training and employing qualified personnel can be both time-consuming and costly.
3. Limited Flexibility for Custom Designs: While CNC machines offer great flexibility for producing multiple parts, they may face limitations when it comes to intricate custom designs with complex shapes. The machinery may not be able to accomplish certain unconventional or unique specifications.
4. Maintenance and Downtime: Like any mechanical equipment, CNC lathe machining parts require regular maintenance to ensure proper functioning and prevent breakdowns. Downtime for repairs and maintenance can interrupt production schedules and affect overall productivity.
5. Steeper Learning Curve: Incorporating CNC lathe machining parts into a manufacturing process requires a learning curve for operators who may be accustomed to traditional manual equipment. Adapting to the new technology and mastering its programming and operation can take time and effort.
In conclusion, CNC lathe machining parts offer numerous advantages, such as precision, efficiency, versatility, and consistency. However, the high initial investment, the requirement for skilled operators, limited flexibility for custom designs, maintenance needs, and the learning curve involved must be considered as potential drawbacks.
cnc lathe machining parts Reference Specifications (varies for different product)
CNC lathe machining parts are manufactured with specific reference specifications, which can vary depending on the product being produced. These reference specifications serve as guidelines for the design, dimensions, and functionality of the parts, ensuring that they meet the desired requirements.
One of the key aspects of CNC lathe machining parts is their dimensional accuracy. The reference specifications provide detailed information about the dimensions and tolerances that need to be maintained during the manufacturing process. This ensures that the parts fit precisely into the designated spaces and work effectively within the intended system.
Additionally, reference specifications outline the desired surface finish for the CNC lathe machining parts. This includes parameters such as roughness, smoothness, and texture, which are crucial for achieving optimal performance and aesthetic appeal. These specifications help in ensuring that the surface finish is consistent across all parts and meets the desired quality standards.
The reference specifications also define the material requirements for CNC lathe machining parts. This includes the type of material, grade, and any additional treatments or coatings that may be needed. By following these specifications, manufacturers can ensure that the parts are made from the appropriate material, which can influence their durability, strength, and resistance to wear and tear.
Furthermore, the reference specifications provide information about any specific features or functionalities that the CNC lathe machining parts must possess. This includes details about the shape, angles, and other design elements that are required to achieve the desired performance. These specifications play a vital role in ensuring that the final parts meet customer expectations and function as intended.
In summary, reference specifications are essential for CNC lathe machining parts as they provide detailed guidelines for the design, dimensions, surface finish, material, and functionality of the parts. By adhering to these specifications, manufacturers can ensure that the parts meet the desired requirements and deliver optimal performance.
Applications of cnc lathe machining parts
CNC (Computer Numerical Control) lathe machining parts have various applications across multiple industries. These applications are characterized by their precision, versatility, and efficiency in producing complex geometries. Here are some notable applications of CNC lathe machining parts:
1. Automotive Industry: CNC lathe machining parts are extensively used in the automotive industry for manufacturing engine components such as crankshafts, pistons, cylinders, and camshafts. These machined parts need to be highly precise for optimal performance and durability.
2. Aerospace Industry: CNC lathe machining parts play a crucial role in the aerospace industry, where complex and high-precision components are required for aircraft engines, landing gears, and other critical parts. These parts need to meet stringent quality standards and must adhere to strict tolerances.
3. Medical Industry: CNC lathe machining parts are widely used in the medical field for manufacturing surgical instruments, orthopedic implants, dental devices, and prosthetics. The precise machining capabilities of CNC lathes ensure accuracy and compatibility with the human body, contributing to improved patient outcomes.
4. Electronics Industry: CNC lathe machining parts are utilized in the electronics industry for producing small, intricate components for electronic devices such as connectors, circuit boards, enclosures, and heat sinks. The precision of CNC machining is crucial to ensure proper functionality and performance of these parts.
5. Oil and Gas Industry: CNC lathe machining parts are employed in the oil and gas sector for manufacturing drill bits, valves, pumps, and other components used in exploration, extraction, refining, and distribution processes. These parts must possess high durability and resistance to extreme environments.
6. Furniture Industry: CNC lathe machining parts are utilized in the furniture industry for producing decorative components, legs, and fixtures. The ability to machine various materials like wood, plastic, and metal allows for intricate designs and customization options.
7. Defense Industry: CNC lathe machining parts are extensively used in the defense sector for producing firearms components, ammunition, military vehicle parts, and aircraft parts. The high precision and consistent quality provided by CNC lathes ensure reliable performance and safety.
8. Energy Industry: CNC lathe machining parts find applications in the energy sector for manufacturing turbine components, power generation equipment, and renewable energy system components. These machined parts must withstand high temperatures, pressures, and mechanical stresses.
In conclusion, CNC lathe machining parts find diverse applications in various industries, including automotive, aerospace, medical, electronics, oil and gas, furniture, defense, and energy sectors. The precision, versatility, and efficiency of CNC lathe machining make it a crucial manufacturing process for producing complex and high-quality components.
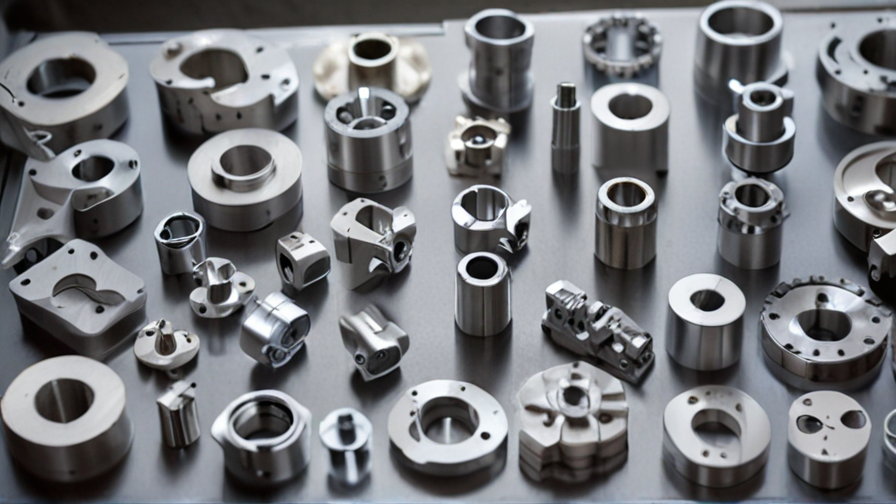
The Work Process and how to use cnc lathe machining parts
CNC lathe machining is a process used to create intricate parts and components using computer-controlled machine tools. It involves the use of a lathe machine, which rotates the workpiece while various cutting tools perform a range of operations.
The work process begins with the preparation of the CNC lathe machine. This includes loading the appropriate tools, setting up the workpiece, and inputting the necessary programming instructions into the computer system. The programming instructions specify various parameters such as tool paths, cutting speeds, and feed rates.
Once the machine is set up, the machining process begins. The CNC lathe rotates the workpiece at a controlled speed, while the cutting tools, guided by the programmed instructions, remove material from the workpiece. This can be done through various operations such as turning, drilling, threading, and boring. The precise movements of the cutting tools are controlled by the CNC system, ensuring accuracy and consistency.
Throughout the machining process, operators monitor the machine’s operation and make any necessary adjustments to ensure quality and efficiency. They may also perform routine maintenance tasks to keep the machine in optimal condition.
After the machining process is complete, the finished parts are inspected to ensure they meet the required specifications. This involves using measuring tools such as calipers, micrometers, and gauge blocks to check dimensions, tolerances, and surface finishes.
CNC lathe machining parts can be used in a wide range of industries, including automotive, aerospace, medical, and electronics. They are utilized to create complex components with high precision and repeatability.
To use CNC lathe machining parts effectively, it is important to have a clear understanding of the design requirements and specifications. This includes knowledge of the material properties, dimensional tolerances, and surface finish requirements. Additionally, operators must be proficient in programming and operating the CNC lathe machine, as well as performing quality control checks.
In conclusion, CNC lathe machining is a sophisticated process that utilizes computer-controlled machine tools to create intricate parts. It involves the setup of the machine, programming instructions, and the precise removal of material from the workpiece. By understanding the work process and having the necessary skills, CNC lathe machining parts can be used effectively to meet design requirements and produce high-quality components.
Quality Testing Methods for cnc lathe machining parts and how to control the quality
There are several quality testing methods that can be employed to ensure the precision and accuracy of CNC lathe machining parts. These methods include:
1. Dimensional Inspection: This involves using precise measuring tools such as calipers, micrometers, and coordinate measuring machines (CMM) to measure the dimensions of machined parts. This ensures that the parts meet the specified tolerance levels.
2. Surface Finish Analysis: Surface finish plays a crucial role in determining the functionality and aesthetics of the parts. Techniques such as profilometry or roughness measurement devices can be used to assess the texture and smoothness of the machined surfaces.
3. Visual Inspection: This method involves visually inspecting the parts for any visible defects such as cracks, dents, burrs, or other imperfections that may affect the quality or functionality of the parts.
4. Material Testing: It is important to confirm the material properties of the parts to ensure their mechanical strength and performance. This can be achieved through methods such as hardness testing, tensile testing, or spectroscopy analysis.
5. Functional Testing: Depending on the specific application, functional testing can be conducted to verify if the parts meet the desired functionality. This may involve testing the parts in simulated operational conditions or performing assembly tests to assess their compatibility with other components.
To effectively control the quality of CNC lathe machining parts, several practices can be implemented:
1. Implementing Standard Operating Procedures (SOPs): Developing SOPs for each stage of the manufacturing process helps maintain consistency and eliminates variability, ensuring that every part is produced with the same standards.
2. Regular Calibration: Calibrating the measuring and testing equipment at appropriate intervals is essential to guarantee accurate and reliable measurements.
3. Documentation and Traceability: Maintaining detailed records of production, inspection, and testing activities contributes to quality control. It provides traceability and facilitates identification of potential issues that may arise during the manufacturing process.
4. Employee Training: Properly trained employees are crucial for producing high-quality parts. Continuous training programs help enhance the skills and knowledge of the workforce, resulting in improved quality control practices.
5. Continuous Improvement: Regularly analyzing quality control data, identifying areas of improvement, and implementing corrective actions are key to enhancing the overall quality of CNC lathe machining parts.
By implementing these quality testing methods and quality control practices, CNC lathe machining part manufacturers can ensure that their products meet the specified requirements, resulting in customer satisfaction and increased competitiveness in the market.
cnc lathe machining parts Sample Policy and Post-Purchase Considerations for cnc lathe machining parts from China
Sample Policy:
When purchasing CNC lathe machining parts from China, it is important to establish a clear sample policy to ensure that the parts meet your requirements. Here are some considerations for your sample policy:
1. Sample Request: Clearly communicate your specifications and requirements to the supplier. Provide detailed drawings, technical specifications, and any other necessary documentation.
2. Sample Approval: Inspect and test the sample parts thoroughly to ensure they meet your quality standards. Evaluate their accuracy, precision, dimensions, material quality, and surface finish.
3. Sample Revisions: If the sample does not meet your requirements, provide clear feedback to the supplier. Request revisions or modifications until you are satisfied with the sample’s quality.
4. Sample Cost: Determine whether you will bear the sample cost or if it will be shared with the supplier. Negotiate this aspect beforehand to avoid misunderstandings later on.
5. Sample Timeframe: Establish a deadline for the supplier to deliver the sample. Consider the time required for production, shipping, and your own evaluation. Ensure that the supplier can meet this timeframe.
Post-Purchase Considerations:
After purchasing CNC lathe machining parts from China, it is crucial to consider post-purchase aspects to ensure smooth and successful business transactions. Here are some post-purchase considerations:
1. Quality Control: Implement a comprehensive quality control system to inspect the received parts. Perform random inspections or request third-party inspection services to ensure consistent quality.
2. Communication: Maintain regular communication with the supplier to address any concerns, resolve issues promptly, and build a long-term collaborative relationship.
3. Feedback and Reviews: Provide feedback to the supplier about the product quality, delivery time, and overall experience. Positive feedback can motivate the supplier to maintain or improve their performance, whereas negative feedback can serve as an opportunity for them to make necessary improvements.
4. Warranty and Support: Understand the supplier’s warranty policy and after-sales support. Inquire about their willingness to provide replacements or refunds in case of defects or non-compliance with specifications.
5. Continuous Improvement: Encourage the supplier to constantly improve their manufacturing processes and quality control measures to ensure ongoing reliability and effectiveness.
By setting clear sample policies and considering post-purchase aspects, you can enhance your experience of purchasing CNC lathe machining parts from China and establish a reliable and long-term partnership with your supplier.
Sourcing cnc lathe machining parts from China: Opportunities, Risks, and Key Players
Sourcing CNC lathe machining parts from China presents both opportunities and risks. China is known for its vast manufacturing capabilities, making it an attractive option for businesses looking to procure high-quality components at competitive prices.
One of the main opportunities of sourcing CNC lathe machining parts from China is cost savings. Chinese manufacturers generally offer lower labor and production costs compared to other countries, allowing businesses to save on expenses. This cost advantage can be significant, especially for companies seeking to reduce their manufacturing expenditure.
Furthermore, China’s manufacturing sector is highly developed, offering a wide range of CNC machining capabilities. This means that businesses can find various versatile and specialized CNC lathe machining parts to suit their specific requirements. The country’s vast supplier network ensures a high level of product availability, making it easier for companies to find the parts they need.
However, sourcing from China also presents risks that businesses should be aware of. Quality control can be a concern, as not all Chinese manufacturers adhere to the same rigorous standards. It is essential for companies to thoroughly vet potential suppliers, ensuring they have a track record of producing high-quality CNC machining parts. Additionally, quality inspection procedures should be established to ensure that the received components meet the required specifications.
Another risk is intellectual property infringement. China has been associated with the production of counterfeit products and unauthorized replication of patented designs. It is crucial for businesses to protect their intellectual property rights by working with reputable suppliers and implementing proper legal safeguards.
When it comes to key players in the Chinese CNC lathe machining parts industry, several prominent manufacturers stand out. Some of the notable companies include Foxconn Technology Group, BYD Co. Ltd, Huawei Technologies Co. Ltd, and the Luxshare Precision Industry Co. These players have established themselves as leaders in the industry, possessing advanced manufacturing facilities and a strong reputation for producing high-quality components.
In summary, sourcing CNC lathe machining parts from China offers cost savings and access to a diverse supplier network. However, businesses need to be cautious of quality control issues and potential intellectual property risks. By carefully selecting reputable suppliers and implementing robust quality control measures, companies can take advantage of the opportunities while mitigating the associated risks.
How to find and select reliable cnc lathe machining parts manufacturers in China,use google search manufacturers and suppliers
To find and select reliable CNC lathe machining parts manufacturers in China, you can follow these steps:
1. Conduct a Google search: Start by searching for “CNC lathe machining parts manufacturers in China” or similar keywords on Google. This will give you a list of potential manufacturers and suppliers.
2. Check their websites: Visit the websites of the shortlisted companies to gather information about their capabilities, production capacity, certifications, and experience. Look for details that indicate their expertise in CNC lathe machining parts production.
3. Evaluate their reputation: Look for customer reviews, testimonials, and ratings on their website or external review platforms. Pay attention to both positive and negative feedback to get a comprehensive understanding of their reliability.
4. Verify their certifications: Ensure that the manufacturers hold certifications such as ISO 9001:2015, which demonstrates their commitment to quality management systems. This certification guarantees that the company follows stringent manufacturing standards.
5. Assess their production capacity: Inquire about their production capabilities to ensure they can fulfill your requirements within the desired timeframe. Consider factors such as equipment, facility size, and workforce to determine if they can efficiently handle your CNC lathe machining parts orders.
6. Request samples: Requesting samples of their CNC lathe machining parts allows you to evaluate their quality firsthand. This will help you assess if their products meet your specifications and standards.
7. Communication and responsiveness: Contact the manufacturers directly and assess their communication skills and responsiveness. Prompt and clear communication is essential to ensure a smooth partnership.
8. Seek recommendations: Consult with industry experts, forums, or colleagues who have previously worked with CNC lathe machining parts manufacturers in China. Recommendations and personal experiences can offer valuable insights.
9. Assess shipping and logistics: Inquire about shipping options, lead times, and logistics support. It’s important to ensure the manufacturer can deliver the parts to your desired location efficiently and safely.
10. Compare prices: Obtain quotations from multiple manufacturers and conduct a price comparison. However, prioritize quality and reliability over choosing the cheapest option, as subpar parts can lead to quality issues and production delays.
By following these steps, you can identify and select reliable CNC lathe machining parts manufacturers in China, thus ensuring a successful and trusted partnership.
How to check cnc lathe machining parts manufacturers website reliable,use google chrome SEOquake check if ranking in top 10M
When trying to check the reliability of a CNC lathe machining parts manufacturer’s website, there are a few steps you can take. One effective method is to use Google Chrome’s SEOquake extension to check the website’s ranking in the top 10 million. Additionally, here are a few tips to keep in mind:
1. Install SEOquake: Start by installing the SEOquake extension on your Google Chrome browser. This tool allows you to assess various aspects of a website’s SEO and overall performance.
2. Conduct a search: Use relevant keywords related to CNC lathe machining parts and the manufacturer’s name to search for the website on Google. Look for the website within the first 10 million search results.
3. Analyze Google SERP: Click on the SEOquake icon in your Chrome browser, which opens a panel displaying numerous metrics related to the website’s SEO. Focus on the website’s Alexa Rank, Google Index, and SEMrush Rank, as these indicators can provide insights into its reliability.
4. Alexa Rank: The Alexa Rank signifies a website’s popularity. A lower rank indicates higher popularity and reliability. Aim for a rank below 10 million.
5. Google Index: This metric shows the number of pages indexed by Google. A higher number suggests more credibility and extensive website coverage. Ensure the website has multiple indexed pages.
6. SEMrush Rank: SEMrush Rank reflects a website’s visibility and reputation. A lower rank is indicative of higher reliability. Look for a rank below 10 million.
7. Analyze website content: Assess the website’s content for clarity, professionalism, and accuracy. Look for detailed product descriptions, specifications, and relevant information. A reliable manufacturer will provide comprehensive and well-presented content.
8. User reviews and testimonials: Explore the website for any customer reviews or testimonials. Genuine feedback from previous customers can help you gauge the manufacturer’s reliability and quality of their CNC lathe machining parts.
By following these steps and using SEOquake to analyze the website’s performance and ranking, you can gain a better understanding of the manufacturer’s reliability. Remember, it is important to use your judgment and conduct thorough research before finalizing any business dealings.
Top 10 cnc lathe machining parts manufacturers in China with each 160 words introduce products,then use markdown create table compare
1. Swissturn Precision Machining Co., Ltd.
Swissturn Precision Machining specializes in high-precision CNC lathe machining parts. With advanced equipment and a skilled team, they offer a wide range of products including shafts, connectors, fasteners, and complex components for industries such as automotive and aerospace.
2. Ningbo Haishu Sinster Machine Co., Ltd.
Sinster Machine focuses on the production of CNC lathe machining parts for various applications. They provide customized solutions for customers, manufacturing parts like valves, pumps, and gears. Their products are known for their accuracy, durability, and excellent performance.
3. Kunshan Hopeful Metal Products Co., Ltd.
Hopeful Metal Products manufactures CNC lathe machining parts using advanced technology and processes. Their product range includes precision screws, precision nuts, and other customized components. They adhere to strict quality control measures to ensure precision and reliability.
4. Dongguan Lemo Precision Metal Products Co., Ltd.
Lemo Precision Metal Products specializes in producing high-quality CNC lathe machining parts, including brass fittings, aluminum components, and stainless steel parts. They have a global clientele and are renowned for their expertise in precision engineering.
5. Wuxi Derf Precision Machinery Co., Ltd.
Derf Precision Machinery focuses on CNC lathe machining parts production for industrial machinery. Their products include motor shafts, couplings, and specialty fittings. With advanced manufacturing capabilities, they are able to meet the strict specifications of various industries.
6. Suzhou Rongwei Industry Co., Ltd.
Rongwei Industry specializes in CNC lathe machining parts for the automotive industry. They manufacture engine components, transmission parts, and braking system parts. Their products are known for their superior quality, performance, and longevity.
7. Shenzhen Xiangfu Precision Industry Co., Ltd.
Xiangfu Precision Industry is a leading manufacturer of CNC lathe machining parts in China. They cater to various industries and produce high-precision components such as connectors, shafts, and housings. Their products undergo rigorous quality control measures.
8. Shanghai Sourcing International Trade Co., Ltd.
Sourcing International Trade offers a wide range of CNC lathe machining parts, including fasteners, bushings, and gears. They have an extensive network of suppliers and can provide customized solutions at competitive prices.
9. Suzhou HaiTe Precision Machinery Co., Ltd.
HaiTe Precision Machinery specializes in CNC lathe machining parts for the electronics industry. They produce connectors, terminals, and housings with an emphasis on precision and quality. Their products are widely used in electronic devices.
10. Shenzhen Jiuzhou Precision Hardware Co., Ltd.
Jiuzhou Precision Hardware focuses on manufacturing CNC lathe machining parts for the telecommunications industry. Their product range includes antenna components, connectors, and brackets. They are committed to providing reliable and high-quality products.
Table for Comparison:
| Manufacturer | Specialization | Product Range | Industries Served | Reputation |
|————–|—————-|—————-|——————|————|
| Swissturn Precision Machining Co., Ltd. | High-precision CNC lathe machining parts | Shafts, connectors, fasteners | Automotive, aerospace | Excellent |
| Ningbo Haishu Sinster Machine Co., Ltd. | CNC lathe machining parts for various applications | Valves, pumps, gears | Various industries | Durable |
| Kunshan Hopeful Metal Products Co., Ltd. | Precision screws, nuts, and customized components | Industrial machinery | Precision, reliability | High-quality |
| Dongguan Lemo Precision Metal Products Co., Ltd. | High-quality brass fittings, aluminum components, stainless steel parts | Customized components | Global clientele | Expertise |
| Wuxi Derf Precision Machinery Co., Ltd. | CNC lathe machining parts for industrial machinery | Motor shafts, couplings, specialty fittings | Various industries | Strict specifications |
| Suzhou Rongwei Industry Co., Ltd. | CNC lathe machining parts for the automotive industry | Engine components, transmission parts, braking system parts | Automotive | Superior quality |
| Shenzhen Xiangfu Precision Industry Co., Ltd. | High-precision connectors, shafts, housings | Various industries | Precision, quality | Leading manufacturer |
| Shanghai Sourcing International Trade Co., Ltd. | Fasteners, bushings, gears | Various industries | Customized solutions | Competitive prices |
| Suzhou HaiTe Precision Machinery Co., Ltd. | CNC lathe machining parts for the electronics industry | Connectors, terminals, housings | Electronics | Precision, quality |
| Shenzhen Jiuzhou Precision Hardware Co., Ltd. | CNC lathe machining parts for the telecommunications industry | Antenna components, connectors, brackets | Telecommunications | Reliable, high-quality |
In this comparison table, the top 10 CNC lathe machining parts manufacturers in China are arranged based on their specialization, product range, industries served, and reputation. Each manufacturer offers unique products catered to specific industries while maintaining a solid reputation in terms of quality and precision.
Background Research for cnc lathe machining parts manufacturers Companies in China, use qcc.com archive.org importyeti.com
When searching for CNC lathe machining parts manufacturers in China, three reliable websites to gather background research are qcc.com, archive.org, and importyeti.com. These platforms provide valuable insights into the companies and their operations to make informed decisions.
Qcc.com is a popular Chinese business information and credit investigation platform that offers comprehensive company profiles. It includes details such as registered capital, main products, production scale, and ownership information. This database allows users to evaluate the credibility and reputation of CNC lathe machining parts manufacturers in China.
Archive.org is an internet archive platform that offers access to historical versions of websites. This tool can be utilized to retrieve previous iterations of the manufacturers’ websites, allowing for the analysis of their development over time. By reviewing past information and updates, users can assess the stability and growth of these companies.
Importyeti.com is an import-export data provider specifically focused on China. It contains detailed shipment records that enable users to identify the exporting activities of CNC lathe machining parts manufacturers. The data includes the names of the importer and exporter, product descriptions, date of shipment, quantity, and value. This platform can be particularly useful in understanding a manufacturer’s global presence and their relationships with international clients.
By utilizing these platforms, researchers can gather relevant information such as company profiles, historical records, and import-export data. These resources can assist in evaluating the capabilities, reliability, and reputation of CNC lathe machining parts manufacturers in China, aiding in the selection of a trustworthy and proficient supplier.
Leveraging Trade Shows and Expos for cnc lathe machining parts Sourcing in China
Trade shows and expos in China present excellent opportunities for sourcing CNC lathe machining parts. These events bring together numerous suppliers and manufacturers under one roof, providing a convenient platform for buyers to explore potential partnerships and source products.
By attending trade shows and expos, buyers can benefit from several advantages:
1. Access to a wide range of suppliers: Trade shows attract a large number of manufacturers and suppliers, offering buyers a diverse pool of options to choose from. This enables them to compare prices, quality, and capabilities to find the best fit for their requirements.
2. Direct communication and relationship building: Attending trade shows allows buyers to interact face-to-face with suppliers, facilitating direct communication and building strong relationships. This interaction helps establish trust and understanding, which is crucial for successful sourcing partnerships.
3. Product showcase and demonstrations: Exhibitors often display their products and conduct live demonstrations at trade shows. This allows buyers to inspect the quality, functionality, and performance of CNC lathe machining parts first-hand. It also gives them an opportunity to address any concerns or ask specific questions regarding the products.
4. Stay updated with industry trends: Trade shows act as information hubs, providing insights into the latest technologies, materials, and trends in CNC lathe machining parts. Staying updated with industry advancements helps buyers make informed decisions and stay ahead of the competition.
To maximize the effectiveness of trade show attendance, buyers should consider the following tips:
1. Plan in advance: Research and identify relevant trade shows and expos in China that focus on CNC lathe machining parts. Make a detailed plan including exhibitor lists, booth locations, and conference schedules to streamline the sourcing process.
2. Take notes and collect information: Bring a notebook or use a mobile app to jot down key information for each supplier. This will help in comparing and evaluating different options after the trade show.
3. Engage actively: Approach suppliers with specific questions to gather detailed information about their capabilities, quality control processes, pricing, and lead times. Seek clarification on any doubts or concerns to ensure a thorough understanding of their offerings.
4. Follow-up and nurture relationships: Make sure to exchange business cards, collect catalogs or brochures, and obtain contact information from potential suppliers. Follow up with them after the trade show to discuss further details and establish a long-term business relationship.
In conclusion, trade shows and expos in China offer valuable opportunities for sourcing CNC lathe machining parts. By attending these events, buyers can access a wide range of suppliers, establish direct communication, evaluate products firsthand, and stay updated with industry trends. Proper planning and active engagement can help leverage these opportunities to source high-quality parts at competitive prices.
The Role of Agents and Sourcing Companies in Facilitating cnc lathe machining parts Purchases from China
Agents and sourcing companies play a crucial role in facilitating CNC lathe machining parts purchases from China. These intermediaries serve as a bridge between buyers and suppliers, ensuring a smooth and efficient procurement process. Here is an overview of their key responsibilities:
1. Supplier identification and vetting: Agents and sourcing companies have extensive networks and expertise to identify reliable and qualified suppliers in China. They conduct thorough due diligence, visiting factories, and assessing their capabilities, quality control practices, and certifications. This ensures that buyers can confidently choose suppliers that meet their specific requirements.
2. Negotiations and contracts: Acting on behalf of the buyer, agents and sourcing companies negotiate prices, terms, and conditions with the suppliers. They leverage their knowledge of the market and industry standards to secure favorable contracts, including the protection of intellectual property rights and adherence to quality standards.
3. Quality control and inspection: To ensure the received CNC lathe machining parts meet the required standards, agents and sourcing companies conduct quality control inspections throughout the production process. They monitor quality control procedures, perform random checks, and provide feedback to the supplier. This minimizes the chance of receiving defective parts and reduces the risks associated with international trade.
4. Logistics and shipping management: Agents and sourcing companies handle the logistical aspects of the purchasing process, including shipping arrangements, customs documentation, and import/export regulations. They provide guidance on the most cost-effective and efficient shipping methods, ensuring timely delivery of the CNC lathe machining parts to the buyer’s location.
5. Language and cultural barrier mitigation: Dealing directly with suppliers in China can be challenging due to language and cultural differences. Agents and sourcing companies bridge this gap, acting as intermediaries in communication and facilitating effective collaboration between the buyer and supplier. This minimizes misunderstandings, enhances efficiency, and ensures smooth transactions.
In conclusion, agents and sourcing companies are indispensable in facilitating CNC lathe machining parts purchases from China. Their expertise in supplier identification, negotiation, quality control, logistics, and communication substantially simplify the procurement process for buyers, enabling them to acquire quality parts at competitive prices, while minimizing risks and ensuring a reliable supply chain.
Price Cost Research for cnc lathe machining parts manufacturers Companies in China, use temu.com and 1688.com
When researching the price and cost of CNC lathe machining parts manufacturers in China, two popular platforms that can be utilized are temu.com and 1688.com. These platforms provide a wide range of options and enable users to find reliable suppliers at competitive prices.
To conduct the research, start by visiting temu.com. This website serves as a global manufacturing and sourcing platform and features numerous CNC lathe machining parts manufacturers in China. Utilize the search bar to input relevant keywords such as “CNC lathe machining parts” or “CNC lathe manufacturers.” Browse through the search results and review the profiles and product catalogs of different suppliers.
Next, explore 1688.com, which is a leading B2B wholesale marketplace owned by Alibaba. It primarily caters to the Chinese market and offers an extensive range of products, including CNC machining parts. Use the search function on the website and enter keywords to find relevant suppliers. Again, assess the profiles and product listings to gather information on pricing and cost.
During the research process, aim to consider the following factors:
1. Pricing: Compare the prices provided by different manufacturers and evaluate whether they are competitive. Keep in mind that the cheapest option may not always guarantee the best quality, so it’s important to balance cost and quality.
2. Minimum Order Quantity (MOQ): Determine if the manufacturers have any minimum order requirements. This information is crucial for planning production and managing costs.
3. Quality Assurance: Look for suppliers that emphasize quality control and offer certifications or guarantees for their products. This ensures the reliability and durability of the CNC lathe machining parts.
4. Communication and Support: Assess the responsiveness and willingness of the manufacturers to provide support and address any concerns or inquiries you may have. Good communication is vital for a smooth and successful collaboration.
Remember to take notes throughout the research process and compile a list of potential manufacturers that meet your requirements. Reach out to them directly for further inquiries and negotiation of prices and terms.
Shipping Cost for cnc lathe machining parts import from China
The shipping cost for CNC lathe machining parts imported from China can vary depending on several factors. These include the size and weight of the package, the shipping method chosen, the final destination, and any additional services required.
In general, there are two main shipping methods: air freight and sea freight. Air freight is usually faster but more expensive compared to sea freight. The cost of air freight is calculated based on the weight and volume of the package. Sea freight, on the other hand, is generally cheaper but takes longer to reach its destination. It is commonly used for bulk shipments.
Apart from the shipping method, additional services such as insurance, customs clearance fees, and import duties may also affect the overall shipping cost. Insurance is crucial to protect the goods from damage or loss during transportation. The customs clearance process involves paperwork and fees that need to be considered. Import duties are taxes imposed by the destination country and can significantly impact the final cost.
To get an estimate, it is advisable to contact shipping companies or freight forwarders for quotes. They will consider the dimensions and weight of the package, the desired shipping method, and any additional services required to provide an accurate cost estimate. Additionally, it is worth comparing multiple quotes from different shipping providers to ensure competitive pricing.
In summary, the shipping cost for CNC lathe machining parts import from China is determined by factors such as the shipping method chosen, package size and weight, destination, and additional services required. It is essential to obtain quotes from multiple shipping providers to ensure the best pricing option.
Compare China and Other cnc lathe machining parts Markets: Products Quality and Price,Visible and Hidden Costs
China is known as one of the largest manufacturers and exporters of CNC lathe machining parts in the world. When comparing China with other CNC lathe machining parts markets, several factors need to be considered, including products quality and price, visible and hidden costs.
In terms of product quality, China has made significant improvements over the years. Many Chinese manufacturers have adopted advanced technologies and quality control systems to ensure the production of high-quality parts. The overall quality of CNC lathe machining parts in China has become comparable to that of other markets. However, it is worth noting that there may still be variations in quality among different manufacturers. Therefore, it is essential to choose reputable manufacturers when sourcing CNC lathe machining parts from China or any other market.
When it comes to price, China often offers competitive pricing for CNC lathe machining parts. The lower labor and production costs in China allow manufacturers to offer more affordable prices compared to other markets. However, it is crucial to consider the direct and indirect costs associated with sourcing from China. Direct costs include shipping fees and import taxes, which need to be factored into the purchase decision. Indirect costs can include longer lead times, potential language barriers, and cultural differences that may affect communication and collaboration.
Visible costs, such as the actual price of the product and shipping fees, can be relatively straightforward to evaluate. However, hidden costs may arise when sourcing CNC lathe machining parts from China or any other market. These hidden costs can include quality issues that result in defective or non-conforming parts, delays in production or shipping, and additional expenses for rework or replacements. It is crucial to consider these potential hidden costs and factor them into the decision-making process.
In conclusion, China’s CNC lathe machining parts market offers competitive prices and improved product quality. However, it is essential to carefully evaluate visible and hidden costs when comparing China with other markets. By considering all these factors, companies can make informed decisions and find the right balance between quality, price, and overall value.
Understanding Pricing and Payment Terms for cnc lathe machining parts: A Comparative Guide to Get the Best Deal
When it comes to purchasing CNC lathe machining parts, understanding the pricing and payment terms is essential in order to get the best deal. This comparative guide aims to provide a concise overview to help buyers navigate this process efficiently.
Pricing for CNC lathe machining parts can vary significantly depending on various factors. These include the complexity and intricacy of the part, material requirements, quantity needed, and desired delivery time. To ensure accurate pricing, it is crucial to provide detailed specifications to the supplier. This will enable them to assess the cost of materials, labor, and machining processes involved.
When requesting quotes, it is wise to compare multiple suppliers to find the most competitive offer. However, be cautious of significantly low prices, as they may indicate compromised quality or hidden charges. Look for a balance between competitive pricing and reputable service.
Payment terms can also vary among suppliers. Common options include full upfront payment, partial upfront payment with the remaining balance upon delivery, or even installment plans. It’s important to clarify payment terms before placing an order to avoid any surprises or disputes later on. Additionally, some suppliers may require payment in the currency of their country, so it is essential to confirm this to avoid currency conversion fees.
Another factor to consider is shipping and logistics costs, which can significantly impact the overall price. These costs depend on the weight, size, and destination of the parts. It is advisable to ask for shipping quotes from different carriers, as this can help identify the most cost-effective option.
To ensure quality and minimize risks, it is vital to establish clear communication with the supplier. Requesting samples or visiting their facility can provide valuable insights into their capabilities and quality control processes.
In conclusion, understanding the pricing and payment terms for CNC lathe machining parts is crucial for obtaining the best deal. By comparing quotes from multiple suppliers, clarifying payment terms, and considering shipping costs, buyers can make informed decisions. Remember, it is not solely about finding the cheapest price, but also ensuring quality and reliability from the chosen supplier.
Chinese Regulations and Industry Standards Certifications for cnc lathe machining parts,Import Regulations and Customs for cnc lathe machining parts from China
Chinese Regulations and Industry Standards Certifications for CNC Lathe Machining Parts
In China, the regulations and industry standards certifications for CNC lathe machining parts primarily focus on quality control, safety, and environmental protection. The main regulations that govern the manufacturing and exporting of CNC lathe machining parts include:
1. ISO 9001: This international standard ensures that the manufacturer has implemented a quality management system to consistently produce high-quality products.
2. ISO 14001: This certification focuses on environmental management systems, ensuring that the manufacturer minimizes their environmental impact and complies with relevant environmental laws and regulations.
3. GB/T 2828.1-2012: This standard specifies sampling procedures and tables for inspection by attributes. It ensures that the final products meet the defined quality requirements through proper sampling and inspection procedures.
4. GB/T 1804-2000: This standard specifies the thread tolerance for machine screws, bolts, and nuts, ensuring the interchangeability and compatibility of CNC lathe machining parts with other components.
Additionally, specific industry certifications may be required depending on the application of the CNC lathe machining parts. For example:
1. CE Certification: This certification is required for CNC lathe machining parts that are intended for use in the European market, ensuring that the products meet the health, safety, and environmental protection standards set by the European Union.
2. RoHS Compliance: For CNC lathe machining parts exported to countries with RoHS regulations (Restriction of Hazardous Substances), such as the European Union and the United States, manufacturers must ensure that their products are free from specific hazardous substances like lead, mercury, and cadmium.
Import Regulations and Customs for CNC Lathe Machining Parts from China
When importing CNC lathe machining parts from China, it is essential to comply with the import regulations and customs procedures of the destination country. Key considerations include:
1. Customs Duties and Taxes: Importers must be aware of the customs duties, tariffs, and taxes applicable to CNC lathe machining parts in their respective countries. These fees can vary significantly and must be factored into the overall import cost.
2. Customs Documentation: Proper documentation, including commercial invoices, packing lists, and bills of lading or airway bills, is required for customs clearance. Importers should ensure that the documents accurately describe the imported CNC lathe machining parts and meet the specific requirements of the destination country.
3. Import Restrictions: Some countries may have specific restrictions on the importation of certain CNC lathe machining parts, such as those related to national security or public safety concerns. Importers should familiarize themselves with any import restrictions or requirements imposed by their country’s governing authorities.
4. Product Inspection and Compliance: Depending on the destination country, CNC lathe machining parts may undergo product inspections to ensure compliance with safety, quality, and labeling standards. Importers should be prepared to provide any necessary documentation or conduct additional testing, if required.
It is crucial for importers to stay up-to-date with any changes in regulations and customs procedures to facilitate a smooth import process and avoid any potential disruptions or delays.
Sustainability and Environmental Considerations in cnc lathe machining parts Manufacturing
In recent years, there has been increasing focus on sustainability and environmental considerations in various industries, including CNC lathe machining parts manufacturing. This shift is driven by the growing awareness of the environmental impacts associated with manufacturing processes and the need to reduce our carbon footprint.
One significant way that manufacturers can promote sustainability is by adopting eco-friendly materials. CNC lathe machining parts manufacturers can opt for recyclable or biodegradable materials, such as aluminum or bio-plastics, which have a lower environmental impact compared to traditional materials. Additionally, using recycled materials to produce parts can further reduce waste and conserve resources.
Furthermore, energy efficiency is another crucial aspect of sustainability in CNC lathe machining parts manufacturing. Companies can invest in energy-efficient machinery and tools, such as CNC lathes with advanced controller systems and high-efficiency motors. Implementing energy-efficient lighting and heating/cooling systems in the manufacturing facility can also contribute to reduced energy consumption.
Reducing waste generation is another important consideration. Implementing lean manufacturing principles can optimize production processes, minimize scrap, and reduce material waste. Recycling programs for waste materials, such as metal shavings or coolant, can further enhance sustainability efforts.
Manufacturers can also explore alternative technologies that have a lower environmental impact. For instance, additive manufacturing (3D printing) can minimize material waste and offer greater design flexibility compared to traditional subtractive manufacturing methods like CNC lathe machining. While not suitable for all applications, it can be used in certain instances to reduce waste and improve sustainability.
Finally, manufacturers should also prioritize the responsible disposal and management of hazardous materials. Adhering to regulations and industry standards for the handling and disposal of chemicals and other hazardous waste is essential to minimize environmental harm.
In conclusion, sustainability and environmental considerations are becoming increasingly important in CNC lathe machining parts manufacturing. By adopting eco-friendly materials, promoting energy efficiency, reducing waste generation, exploring alternative technologies, and practicing responsible waste management, manufacturers can contribute to a more sustainable and environmentally friendly industry.
List The Evolution history of “cnc lathe machining parts”
The evolution history of CNC lathe machining parts spans several decades, witnessing significant advancements and improvements in technology and processes.
In the early days of machining, traditional lathes were manually operated by skilled operators who would move the cutting tool along the workpiece. This process was time-consuming and required high levels of expertise.
The introduction of computer numerical control (CNC) technology revolutionized the machining industry. The use of computer control allowed for automation and greater precision in turning operations. The first CNC lathes were developed in the 1950s and relied on punched tape as the means of programming the machine.
As technology advanced, the use of punched tape gave way to computer-aided design (CAD) and computer-aided manufacturing (CAM) systems. This allowed for more complex parts to be programmed and produced with ease. CNC lathes became more versatile, capable of producing intricate shapes and higher tolerances.
With the advent of improved sensors and measurement systems, CNC lathes began to incorporate real-time feedback mechanisms. This enabled the machine to make dynamic adjustments during the machining process, leading to enhanced accuracy and reduced errors.
The integration of advanced materials and coatings also contributed to the evolution of CNC lathe machining parts. High-speed steel and carbide tooling offered improved cutting performance and longevity. Coatings such as titanium nitride and aluminum oxide further enhanced the durability and wear resistance of cutting tools.
More recently, the development of multi-axis CNC lathes has expanded the capabilities of lathe machining. These machines can perform simultaneous cutting operations on multiple surfaces, reducing the need for multiple setups. This has resulted in increased efficiency and reduced production time.
Furthermore, advancements in software and simulation technology have allowed for virtual testing and optimization of machining operations. This enables manufacturers to identify potential issues and optimize tool paths before physical machining takes place, reducing scrap and improving overall productivity.
In conclusion, the evolution of CNC lathe machining parts has been driven by advancements in computer control, materials, coatings, and simulation technology. These advancements have led to increased automation, precision, versatility, and efficiency in turning operations, making CNC lathes an indispensable tool in modern manufacturing.
The Evolution and Market Trends in cnc lathe machining parts Industry
The CNC lathe machining parts industry has experienced significant evolution and market trends over the years. With the advent of Computer Numerical Control (CNC) technology, machining processes have become more efficient, accurate, and streamlined.
One of the key developments in this industry is the integration of advanced software and automation. CNC lathes now come equipped with software that allows for computerized programming, optimizing machine performance, and reducing errors. This has led to increased productivity and reduced operating costs for manufacturers.
Another trend in the CNC lathe machining parts industry is the growing demand for customization and complex parts. With CNC technology, manufacturers can easily produce intricate parts with high precision and repeatability. This has resulted in the industry catering to a wider range of customer needs, from small-scale to mass production.
Moreover, the industry has witnessed a shift towards sustainable manufacturing practices. As environmental concerns continue to grow, manufacturers are adopting eco-friendly processes, such as using recyclable materials, reducing waste, and implementing energy-saving measures. This trend aligns with the global focus on sustainability and offers a competitive advantage to those who embrace it.
Additionally, the market for CNC lathe machining parts has expanded due to globalization and the rise of e-commerce. Manufacturers now have access to a larger customer base worldwide, boosted by online platforms that connect them directly with buyers. This has increased market competition and encouraged innovation in terms of product quality, delivery times, and customer service.
In conclusion, the CNC lathe machining parts industry has evolved significantly, driven by advancements in technology and changing market demands. The integration of software and automation, the emphasis on customization, sustainable manufacturing practices, and the global market expansion via e-commerce have all shaped the industry’s evolution. To stay competitive, manufacturers in this industry must adapt to these trends and continually innovate to meet customer expectations.
Custom Private Labeling and Branding Opportunities with Chinese cnc lathe machining parts Manufacturers
Chinese CNC lathe machining parts manufacturers offer custom private labeling and branding opportunities to businesses looking to differentiate and promote their products. Private labeling involves placing a company’s logo and branding on products manufactured by the Chinese manufacturer. This allows businesses to sell products under their own brand name, creating brand recognition and loyalty.
With Chinese manufacturers, businesses can easily customize their products’ design, packaging, and labeling according to their specific requirements. CNC lathe machining parts can be customized in terms of material, dimensions, finish, and functionality, allowing businesses to tailor them to their target market.
Chinese manufacturers excel in producing high-quality CNC lathe machining parts at competitive prices due to lower labor costs and efficient production processes. This makes private labeling and branding opportunities economically viable for businesses, as they can obtain customized products at affordable prices.
Private labeling and branding also enable businesses to build their brand reputation and stand out from competitors. The ability to create a unique value proposition and establish a strong brand image can lead to increased customer loyalty, market share, and profitability.
Communication with Chinese manufacturers is typically facilitated through emails, phone calls, or instant messaging apps. Manufacturers provide design consultations, product samples, and production timelines to ensure that the final products meet the client’s requirements.
It is important for businesses to choose reliable and reputable Chinese CNC lathe machining parts manufacturers to ensure quality products and smooth collaboration. Verification of the manufacturer’s certifications, quality control processes, and client reviews can aid in making an informed decision.
Collaborating with Chinese manufacturers for custom private labeling and branding of CNC lathe machining parts allows businesses to enhance their product offerings, strengthen their brand identity, and gain a competitive edge in the market.
Tips for Procurement and Considerations when Purchasing cnc lathe machining parts
When it comes to procuring CNC lathe machining parts, there are several tips and considerations that can help you make the right purchasing decisions. Here are some key points to keep in mind:
1. Understand your requirements: Before starting the procurement process, thoroughly analyze your needs. Consider factors like the type of parts you need, the required specifications, tolerances, and quantity.
2. Research supplier capabilities: Look for reliable suppliers with a proven track record in CNC lathe machining. Check their experience, reputation, certifications, and customer reviews to ensure they can meet your requirements.
3. Quality assurance: Quality is crucial in CNC machining. Ensure that the supplier has stringent quality control measures in place, such as inspection procedures, certifications like ISO 9001, and compliance with industry standards.
4. Material selection: Choose the appropriate materials for your CNC lathe machining parts based on their mechanical properties, compatibility with the intended application, and overall cost-effectiveness.
5. Cost considerations: While cost is important, don’t compromise on quality to save money. Compare prices from multiple suppliers, and consider the total cost of ownership, including factors like production time, post-machining processes, and potential rework.
6. Customization capabilities: Confirm if the supplier can accommodate any customization requirements for your CNC lathe machining parts, such as specific geometries, surface finishes, or special coatings.
7. Delivery time: Evaluate the supplier’s ability to meet your required delivery timeline. Late deliveries can disrupt your production schedule, leading to increased costs and customer dissatisfaction.
8. Communication and support: Ensure the supplier has effective communication channels and responsive customer support. Prompt and reliable communication can help address any concerns or queries during the procurement process.
9. Scalability: If your future requirements might increase, consider the supplier’s capacity to handle larger orders or accommodate changes in volume.
10. Confidentiality and data security: Protecting your design and intellectual property is critical. Verify the supplier’s commitment to confidentiality and data security measures to avoid any potential risks of information leakage.
By considering these tips and taking the time to research and evaluate potential suppliers, you can ensure the procurement of CNC lathe machining parts that meet your specific needs and specifications.
FAQs on Sourcing and Manufacturing cnc lathe machining parts in China
1. Why should I consider sourcing and manufacturing CNC lathe machining parts in China?
China has become a global manufacturing hub for various industries, including CNC machining. The country offers competitive pricing due to low labor costs and abundant raw materials. Moreover, China boasts a wide range of manufacturing capabilities, including CNC lathe machining, and has a vast network of suppliers and manufacturers with state-of-the-art facilities. This allows for efficient production and quick turnaround times.
2. What are the advantages of CNC lathe machining in China?
Chinese manufacturers have years of experience in CNC lathe machining and have developed advanced techniques and expertise in the field. They can provide high precision and complex machining capabilities, ensuring the production of accurate and reliable parts. Additionally, Chinese manufacturers often invest in modern equipment and technologies, enabling them to produce parts with tight tolerances and intricate designs.
3. How can I find a reliable CNC lathe machining supplier in China?
Finding a reliable supplier in China can be achieved through various channels. One popular method is to leverage online sourcing platforms, such as Alibaba or Made-in-China, which provide access to thousands of suppliers and allow you to compare their capabilities, ratings, and customer reviews. It is essential to conduct detailed research on potential suppliers, verify their certifications, request samples, and even visit their facilities to ensure they meet your quality standards.
4. What are the quality control measures in place when sourcing CNC lathe machining parts from China?
Reputable Chinese manufacturers have robust quality control procedures in place to ensure the production of high-quality CNC lathe machining parts. This includes conducting in-process quality checks, final inspections, and implementing comprehensive quality management systems, such as ISO 9001 certification. Many manufacturers also use advanced inspection tools, such as coordinate measuring machines (CMMs), to verify the dimensions and specifications of the parts.
5. Can Chinese manufacturers handle large-volume production?
Yes, Chinese manufacturers are capable of handling large-volume production. With their extensive production facilities and capacity, they are equipped to handle high volumes of CNC lathe machining parts efficiently. They have experience in scaling up production while ensuring quality control and adherence to lead times. However, communication and supply chain management are crucial when dealing with larger orders to ensure smooth production and timely delivery.
In conclusion, sourcing and manufacturing CNC lathe machining parts in China present numerous advantages, including cost-effectiveness, advanced machining capabilities, and a wide supplier network. However, thorough supplier evaluation, quality control measures, and effective communication are essential to ensure a successful manufacturing partnership.
Why contact sourcifychina.com get free quota from reliable cnc lathe machining parts suppliers?
Sourcifychina.com may offer a free quota from reliable CNC lathe machining parts suppliers for several reasons. Firstly, by collaborating with these suppliers, Sourcifychina.com can build a trustworthy reputation as a sourcing platform. By providing a free quota, they aim to attract potential customers and showcase their ability to connect businesses with reliable suppliers.
Additionally, offering a free quota allows Sourcifychina.com to collect valuable data about the sourcing needs of their customers. By understanding these needs, they can better tailor their services and improve their supplier network. This data can also be used to negotiate better deals with suppliers, resulting in more competitive pricing for their customers.
Furthermore, providing a free quota can be beneficial for CNC lathe machining parts suppliers as well. It allows them to showcase their capabilities and attract new customers. By collaborating with Sourcifychina.com, they gain access to a broader customer base and increase their chances of securing future business deals.
By limiting the quota to a specific number of free requests, Sourcifychina.com ensures a manageable workload for their team while still providing an opportunity for potential customers to try their services. It indicates that the platform values customer satisfaction and wants to establish long-term partnerships.
In conclusion, by offering a free quota from reliable CNC lathe machining parts suppliers, Sourcifychina.com aims to attract potential customers, gather valuable sourcing data, and provide a platform for suppliers to expand their customer base. This approach helps build a trustworthy reputation and allows for the customization of services to better meet the needs of customers.