Introduce about cnc lathe tooling guide,Qulity,Cost,Supplier,Certification,Market,Tips,FAQ
CNC lathe tooling guide is a comprehensive information resource that offers guidance on different types of tools used in CNC lathe machining operations. It provides detailed information on tool specifications, selection criteria, and usage techniques.
Quality is a crucial aspect of CNC lathe tooling as it directly impacts the machining process and final product. High-quality tools ensure precision, accuracy, and increased productivity. It is important to source tools from reputed suppliers known for their commitment to quality.
Cost is another important consideration while selecting CNC lathe tooling. While high-quality tools may come at a higher price, they often offer better performance, longer tool life, and reduced downtime. It is advisable to assess the overall value and cost-effectiveness of the tools rather than solely focusing on the initial price.
Choosing a reliable supplier for CNC lathe tooling is essential to ensure consistent supply, timely delivery, and access to technical support. Reputable suppliers often provide certifications and warranties for their products.
Certification is an essential factor to consider when choosing CNC lathe tooling. Look for tools that have been tested and certified by relevant authorities, ensuring that they meet industry standards and are safe to use.
The CNC lathe tooling market is highly competitive, with numerous suppliers offering a wide range of tools. It is advisable to conduct thorough market research and compare offerings from different suppliers to make an informed decision.
Here are some tips to consider:
1. Assess your specific machining requirements before selecting the tooling.
2. Seek recommendations and advice from experts in the field.
3. Regularly maintain and inspect your tooling to ensure optimum performance.
Frequently Asked Questions (FAQs) about CNC lathe tooling may include queries about tool compatibility, tool life, speed, feed rates, and troubleshooting common issues. Referencing the manufacturer’s guidelines and seeking technical support when needed can help address these queries effectively.
In conclusion, a CNC lathe tooling guide provides valuable information about tool specifications, selection, and usage. Considering factors such as quality, cost, supplier reputation, certification, and market offerings can help in making an informed decision. Additionally, following tips and referring to FAQs can enhance the overall CNC lathe machining experience.
Types of cnc lathe tooling
CNC lathe tooling is used in a variety of applications to create precision parts and components. There are numerous types of CNC lathe tooling available, each designed for specific tasks and machining operations. Here are some common types:
1. Turning Tools: These tools are used for the primary machining operation in CNC lathe machines. They include single-point turning tools, which are used to remove material and shape the workpiece accurately.
2. Boring Bars: These tools are used for enlarging existing holes and creating internal features like cavities or channels. They are available in various sizes and shapes to accommodate different machining requirements.
3. Threading Tools: Threading tools are used to create screw threads on the workpiece. They come in different types, such as internal threading tools (for creating threads inside a hole) and external threading tools (for creating threads on the outside diameter of a cylindrical workpiece).
4. Parting Tools: Parting tools are used to cut through a workpiece to create separate parts. They have a thin blade that separates the workpiece and provides a clean cut.
5. Grooving Tools: Grooving tools are used to create grooves or slots on the workpiece. They can be used to create internal or external grooves of different shapes and sizes.
6. Knurling Tools: Knurling tools are used to create a pattern of ridges or teeth on the surface of the workpiece, improving grip or aesthetics.
7. Drill Bits: Drill bits are used to create holes in the workpiece. They can vary in size and shape, depending on the desired hole diameter and depth.
8. Milling Tools: Some CNC lathe machines come with milling capabilities. In such cases, milling tools can be used to remove material and create complex shapes and features on the workpiece.
These are just a few examples of the types of CNC lathe tooling available. The specific tooling required for a particular machining operation depends on factors such as the material being machined, the desired outcome, and the capabilities of the CNC lathe machine being used.
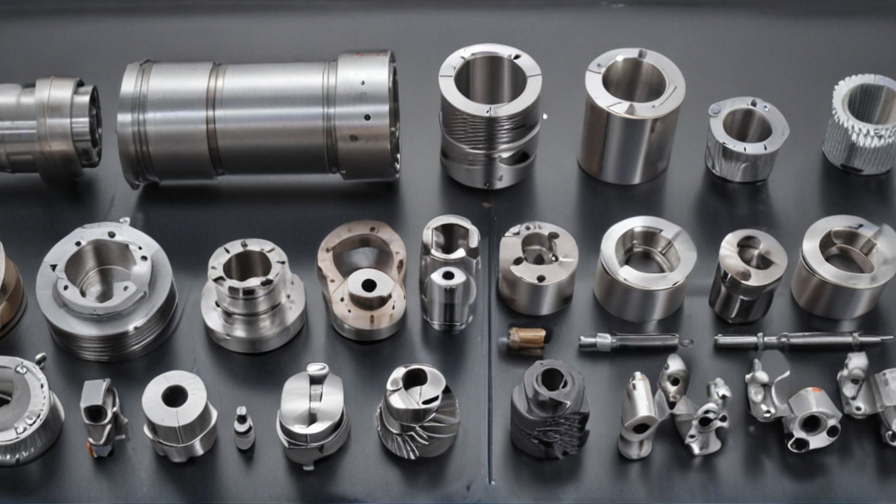
Pros and Cons of Using cnc lathe tooling
CNC lathe tooling refers to the tools and equipment used in computer numerical control (CNC) lathe machines. These tools are essential for cutting, shaping, and forming materials such as metal and plastic. Like any technology, CNC lathe tooling has its own set of pros and cons.
Pros:
1. Precision: CNC lathe tooling offers unmatched precision and accuracy. Computer-controlled machines ensure consistent, repeatable results, reducing human error and minimizing variations in the finished product.
2. Efficiency: CNC lathe tooling enables high-speed production, reducing cycle times and increasing productivity. The automatic tool changing feature allows for uninterrupted machining, reducing downtime and optimizing resource utilization.
3. Flexibility: CNC lathe tooling can handle a wide range of materials, from soft metals to hard alloys. The ability to switch tools and cutting parameters allows for versatile machining operations, accommodating various shapes, sizes, and complexities.
4. Cost-effectiveness: Although CNC lathe tooling requires significant upfront investment, it can save costs in the long run. The automation and precision reduce material wastage, rework, and scrap, resulting in higher efficiency and cost savings.
5. Integration: CNC lathe machines can be integrated with computer-aided design (CAD) and computer-aided manufacturing (CAM) software, allowing for seamless part programming and design modifications. This integration enhances overall coordination and reduces errors.
Cons:
1. High initial costs: CNC lathe machines and tooling have high upfront costs, including the machine itself, software, and training. Small businesses and startups may find it challenging to invest in this technology.
2. Skills requirement: Operating CNC lathe machines and tooling requires specialized skills and training. Skilled operators and programmers are essential for efficient and safe operation, and their expertise often comes at a higher cost.
3. Limited flexibility for small batch production: CNC lathe machines are highly efficient for large-scale production runs, but they may not be as flexible for small batch or custom orders. Setting up the machine for each unique job can be time-consuming and costly.
4. Maintenance and downtime: CNC lathe machines require regular maintenance and occasional repairs, which can result in machine downtime. Machine breakdowns can disrupt production schedules and lead to delays.
5. Technology dependency: Dependence on technology can be a double-edged sword. Power outages, software glitches, or compatibility issues with new software versions can affect machine performance and result in production delays.
In conclusion, CNC lathe tooling offers several advantages such as precision, efficiency, flexibility, cost-effectiveness, and integration with software. However, the high initial costs, skills requirement, limited flexibility for small batches, maintenance and downtime, and technology dependency are some of the potential drawbacks. Overall, the decision to use CNC lathe tooling should consider the specific needs, budget, and capabilities of the business.
cnc lathe tooling Reference Specifications (varies for different product)
CNC lathe tooling reference specifications vary depending on the specific product being manufactured. These specifications include factors such as dimensions, material composition, and tool design. By adhering to these specifications, manufacturers can ensure optimal performance and produce high-quality products.
Dimensional specifications are crucial for CNC lathe tooling as they determine the size and shape of the cutting tool. This includes parameters such as length, diameter, and tool tip radius. The dimensions may vary depending on the intended application and the specific machine being used.
Material composition is another important aspect of CNC lathe tooling. Different materials possess varying properties, such as hardness, toughness, and heat resistance. Common materials used for lathe tooling include high-speed steel (HSS), carbide, and ceramic. The choice of material depends on factors such as the workpiece material, cutting speed, and desired tool life.
Tool design specifications play a significant role in determining the efficiency and accuracy of the machining process. These specifications include the shape and geometry of the cutting edge, the number and type of inserts or blades, and the tool’s overall rigidity. Proper tool design ensures efficient chip removal, reduced vibration, and improved surface finish.
In addition to the above specifications, specific products may require additional features or modifications. These could include specialized coatings, chip breakers, or coolant channels, which enhance performance for specific applications.
Manufacturers must carefully evaluate and select the appropriate tooling specifications for each product they produce. This involves considering factors such as material properties, expected tool life, cutting forces, and desired surface finish. Failure to adhere to these reference specifications can result in poor product quality, increased tool wear, and inefficient machining processes.
Therefore, it is essential for manufacturers to thoroughly understand the reference specifications for CNC lathe tooling and ensure compliance to achieve consistent and reliable results in their manufacturing processes.
Applications of cnc lathe tooling
CNC lathe tooling is a critical component in the manufacturing industry as it enables the efficient and precise machining of various materials. Here are some key applications of CNC lathe tooling:
1. Turning operations: CNC lathe tooling is primarily used for turning operations, where the material is rotated and a cutting tool is applied to remove material and create the desired shape. This process is commonly used in the production of cylindrical parts, such as shafts, rods, and pipes.
2. Threading: CNC lathe tooling can be used to create threads on cylindrical surfaces, allowing for the production of components like screws, bolts, and nuts. This ensures accurate and consistent threading, which is crucial for proper fittings and assembly.
3. Facing operations: CNC lathe tooling is also used for facing operations, where the tool moves across the workpiece to create a flat surface. This is often necessary to achieve proper alignment and fit of components in assemblies.
4. Grooving and parting: CNC lathe tooling allows for the creation of grooves and parting off sections of the workpiece. This is commonly used in the production of rings, bearings, and other components where a specific gap or separation is necessary.
5. Taper turning: CNC lathe tooling can be used to create tapered surfaces, such as conical shapes or chamfers. This is essential in industries like automotive and aerospace, where tapered components are prevalent.
6. Knurling: CNC lathe tooling can be equipped with special knurling tools to create decorative or functional patterns on the surface of the workpiece. This is commonly seen on components like handles, knobs, and hand tools for improved grip.
7. Boring: CNC lathe tooling can also be used for boring operations, where existing holes are enlarged or precision holes are produced. This is particularly important in the production of precise and smooth bores for bearings, gears, and other rotating components.
8. Bar feeding automation: CNC lathe tooling often incorporates bar feeding systems that automatically load long bars of material into the lathe for continuous machining. This is highly efficient for high-volume production and reduces manual labor requirements.
In conclusion, CNC lathe tooling is essential for a wide range of machining operations, enabling the production of precise and high-quality components in various industries including automotive, aerospace, and machinery manufacturing.
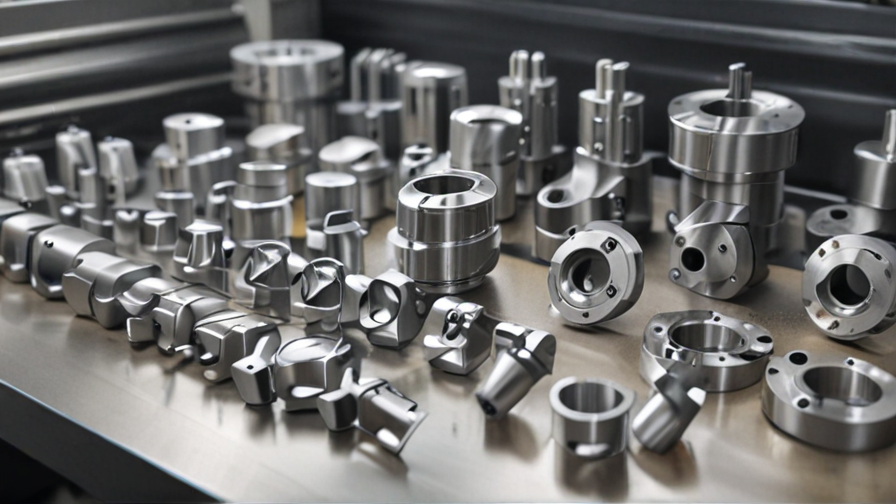
The Work Process and how to use cnc lathe tooling
CNC lathe tooling is a process used in the machining industry to shape and cut metal or other materials using a computer numerical control (CNC) lathe machine. The process involves the use of various tools and techniques to achieve the desired result.
The work process begins with the design of the part to be machined. This can be done using computer-aided design (CAD) software, which allows for precise and detailed specifications. Once the design is complete, it is converted to a format that can be read by the CNC lathe machine.
Next, the material to be machined is chosen. The CNC lathe machine can handle a wide variety of materials, including metals like aluminum, steel, and titanium, as well as plastics and composites. The material is cut into a shape that is close to the final desired form.
The CNC lathe machine is then set up with the appropriate tooling. This includes the cutting tools, which are inserted into tool holders and secured in place. The machine is programmed with the specific instructions for the machining process, such as the cutting speed, feed rate, and depth of cut.
Once the machine is set up and programmed, the machining process can begin. The CNC lathe machine rotates the material at high speeds while the cutting tool removes material to shape it according to the design specifications. The machine continuously monitors and adjusts the cutting parameters to ensure accuracy and consistency.
During the machining process, it is essential to periodically check and adjust the tooling. This can involve changing worn-out cutting inserts or sharpening the cutting edges. Proper maintenance of the tooling is crucial to ensure optimal cutting performance and extended tool life.
Once the machining is complete, the finished part is carefully inspected for any defects or imperfections. If necessary, additional finishing operations such as polishing or deburring may be performed.
In summary, the use of CNC lathe tooling involves a series of steps from design to inspection. It requires careful planning, programming, and maintenance of the machine and tooling to achieve precise and high-quality machined parts.
Quality Testing Methods for cnc lathe tooling and how to control the quality
When it comes to CNC lathe tooling, ensuring quality is essential for producing accurate and precise machined parts. There are several methods for quality testing and controlling the tooling process to ensure optimal performance and minimize defects.
Firstly, regular inspection of tooling is crucial to identify any signs of wear, damage, or improper alignment. Visual examinations can help detect issues such as chipped or broken inserts, deformed tool holders, or loose screws. Using magnifying tools like microscopes or borescopes can provide a more detailed inspection.
Measurement and inspection tools like calipers, micrometers, and coordinate measuring machines (CMMs) can be utilized to check dimensional accuracy and tolerances. These tools help ensure that the tooling components meet the required specifications and maintain consistent quality.
Additionally, functionality tests can be performed to assess the performance of the tooling. This involves running machining operations with the tooling to analyze the results. Evaluating factors such as surface finish, chip formation, cutting forces, and tool life can help determine the quality and effectiveness of the tooling.
To control the quality of CNC lathe tooling, implementing a comprehensive quality management system is necessary. This includes establishing standard operating procedures (SOPs) for tooling setup, maintenance, and inspection. Adhering to these SOPs ensures consistent and reliable tooling performance.
Regular maintenance and replacement schedules should be established based on tooling usage and wear rates. This helps to prevent premature tool failures and ensures that the tooling is always in optimal condition.
Furthermore, feedback from operators and machinists should be encouraged to identify any recurring issues or areas for improvement in the tooling process. Conducting periodic performance reviews and addressing any concerns promptly will help maintain quality and productivity.
In conclusion, quality testing methods for CNC lathe tooling include visual inspections, measurement and inspection tools, and functionality tests. Implementing a robust quality management system and regular maintenance schedules is essential for controlling the quality of tooling. By following these practices, manufacturing companies can ensure consistent and reliable performance of their CNC lathe tooling.
cnc lathe tooling Sample Policy and Post-Purchase Considerations for cnc lathe tooling from China
Sample Policy:
When purchasing CNC lathe tooling from China, it is important to establish a sample policy to ensure the quality and suitability of the tools. The supplier should be able to provide samples of the tooling before making a large order. This allows the buyer to test the tools and assess their performance, accuracy, and durability. The sample policy should include the following considerations:
1. Sample requirements: Clearly outline the specifications and requirements for the samples, including dimensions, material, coating, and any other relevant factors.
2. Quantity and cost: Specify the number of samples required and whether they will be provided free of charge or at a discounted price.
3. Delivery time: Set a reasonable timeframe for the supplier to deliver the samples, ensuring that there is enough time for testing and evaluation.
4. Testing and evaluation: Establish a process for testing the samples, including the necessary equipment and procedures, to determine the performance and quality of the tools.
Post-Purchase Considerations:
Once the CNC lathe tooling has been purchased from China, there are several post-purchase considerations that should be taken into account:
1. Quality control: Implement a comprehensive quality control process to ensure that the tools meet the required standards and specifications. Regular inspections and testing should be conducted to identify any defects or issues.
2. Warranty and support: Check if the supplier offers a warranty on the tooling and inquire about the level of technical support and assistance that will be provided in case of any problems or inquiries.
3. Maintenance and servicing: Establish a maintenance schedule to ensure that the tools are properly cleaned and serviced, maximizing their lifespan and performance.
4. Continuous improvement: Provide constructive feedback to the supplier based on the performance and experience with the CNC lathe tooling. This encourages them to make necessary improvements and rectify any identified issues.
By implementing a sample policy and considering crucial post-purchase factors, buyers can enhance their purchasing experience and ensure the efficiency and effectiveness of CNC lathe tooling from China.
Sourcing cnc lathe tooling from China: Opportunities, Risks, and Key Players
Sourcing CNC lathe tooling from China can provide both opportunities and risks for businesses. China is known for its low-cost manufacturing capabilities, making it an attractive option for companies looking to reduce costs. However, it is essential to carefully evaluate potential risks before engaging in business with Chinese suppliers.
Opportunities:
1. Cost-effectiveness: Chinese manufacturers can offer competitive prices due to lower labor and production costs.
2. Wide range of options: China has a vast network of suppliers offering various CNC lathe tooling options, providing businesses with a wide range of choices.
3. Customization: Chinese suppliers often provide customization options, allowing businesses to tailor the tooling to their specific needs.
4. Growth potential: By sourcing from China, businesses can tap into the country’s rapidly growing market and benefit from its booming manufacturing industry.
Risks:
1. Quality control: Ensuring consistent quality can be a challenge when sourcing from China. It is crucial to conduct due diligence and work only with reliable and certified suppliers.
2. Intellectual property concerns: China has had a reputation for intellectual property infringement. Companies should take steps to protect their patents, designs, and trade secrets.
3. Communication and language barriers: Effective communication can sometimes be a challenge due to language differences, which may lead to misunderstandings or delays in production.
4. Supply chain disruption: Dependence on a single source of supply can increase the risk of disruption, such as delays, transportation issues, or political instability.
Key Players:
1. Tungaloy Corporation: Provides a wide range of CNC lathe tooling, including carbide inserts and toolholders.
2. Sandvik AB: Offers high-performance tooling solutions for CNC lathes, focusing on efficiency and productivity.
3. Iscar Ltd: Specializes in carbide cutting tools, including CNC lathe tooling, with a strong presence in the Chinese market.
4. Seco Tools AB: Known for its advanced cutting tools and solutions, Seco Tools also offers CNC lathe tooling.
In conclusion, while sourcing CNC lathe tooling from China can present significant opportunities in terms of cost-effectiveness and customization, businesses must carefully evaluate and manage the associated risks. Thorough due diligence, effective quality control, and ensuring protection of intellectual property can help mitigate potential challenges and establish successful partnerships with Chinese suppliers.
How to find and select reliable cnc lathe tooling manufacturers in China,use google search manufacturers and suppliers
When looking for reliable CNC lathe tooling manufacturers in China, utilizing Google search can be a helpful tool. Here is a step-by-step guide to finding and selecting the right manufacturer:
1. Start by opening Google search and entering relevant keywords. For example, search for “CNC lathe tooling manufacturers in China” or “reliable CNC lathe tooling suppliers in China.”
2. Review the search results carefully. Pay attention to the first few pages as they usually include the most relevant and trusted sources.
3. Visit the websites of the potential manufacturers. Gather information about their company profile, product catalog, specialization, production capabilities, and certifications. Look for any indication that suggests they are reliable and reputable.
4. Check out their product quality and manufacturing processes. Look for images, videos, or descriptions that demonstrate the quality of their CNC lathe tooling products. It is also essential to explore whether they follow international quality standards like ISO certifications.
5. Verify their experience and market reputation. Check how long they have been in the business and if they have positive client reviews or testimonials. Additionally, search for any news or online forums discussing their products and services to gain insights into their reputation.
6. Look for their OEM/ODM ability. If customization or private labeling is important to you, ensure that the manufacturer has the capability to fulfill your specific requirements.
7. Get in touch. Contact the shortlisted manufacturers through their website’s contact forms, email, or phone, and ask any questions or concerns you may have. Prompt and professional responses are indicative of a reliable manufacturer.
8. Request samples or a product catalog. If possible, ask for samples to assess the quality and compatibility of their CNC lathe tooling. Alternatively, request a product catalog detailing their range of tooling options.
9. Evaluate pricing and terms. Compare the pricing, delivery times, and payment terms offered by different manufacturers. Keep in mind that the cheapest option may not always indicate the best quality, so prioritize high-quality and reliable suppliers.
10. Choose a reliable manufacturer. Based on their responsiveness, reputation, product quality, experience, and pricing, make an informed decision to select a CNC lathe tooling manufacturer that meets your requirements.
By following these steps and utilizing Google search effectively, you can find reputable CNC lathe tooling manufacturers in China that deliver reliable products to meet your needs.
How to check cnc lathe tooling manufacturers website reliable,use google chrome SEOquake check if ranking in top 10M
When it comes to checking the reliability of a CNC lathe tooling manufacturer’s website, using Google Chrome and the SEOquake extension can be an effective approach.
Firstly, open Google Chrome and install the SEOquake extension. Once installed, navigate to the website of the CNC lathe tooling manufacturer you want to evaluate.
Now, click on the SEOquake icon in your browser’s toolbar, which will open a drop-down menu of SEOquake options. From this menu, select the “Diagnosis” tab.
Within the Diagnosis tab, check the “SEMrush” feature. This feature will provide you with valuable information about the website’s organic search traffic, ranking, and keywords.
Look for the website’s ranking in the top 10 million. If the website ranks within the top 10 million, it indicates that it receives a decent amount of traffic and has a relatively high presence on search engines.
Additionally, you can explore other features within SEOquake to obtain more insights about the website, such as its PageRank, Alexa rank, and social media activity. These metrics can help you gauge the overall credibility and popularity of the manufacturer.
By conducting this analysis using SEOquake, you can make an informed decision about the reliability and credibility of the CNC lathe tooling manufacturer’s website.
Top 10 cnc lathe tooling manufacturers in China with each 160 words introduce products,then use markdown create table compare
1. Sandvik Coromant: Sandvik Coromant is a renowned CNC lathe tooling manufacturer in China. They offer a wide range of cutting tools, inserts, and tool holders for various machining operations. Their products are known for their exceptional performance in terms of speed, precision, and durability. Sandvik Coromant’s tools are designed using advanced technologies and materials, ensuring high productivity and efficiency in CNC lathe machining.
2. Mitsubishi Materials: Mitsubishi Materials is another leading CNC lathe tooling manufacturer in China. They provide a comprehensive range of cutting tools, including inserts, drills, end mills, and indexable cutting inserts. Their tools are designed to deliver optimal cutting performance, accuracy, and reliability. Mitsubishi Materials’ CNC lathe tooling is widely used in industries such as automotive, aerospace, and general machining.
3. Kyocera Industrial Ceramics: Kyocera Industrial Ceramics specializes in developing and manufacturing high-quality ceramic cutting tools for CNC lathe applications. Their products are known for their excellent heat resistance, wear resistance, and dimensional stability. Kyocera’s ceramic inserts and toolholders offer exceptional machining performance, allowing for higher cutting speeds and extended tool life.
4. Taegutec: Taegutec is a leading manufacturer of cutting tools, carbide inserts, and toolholders for CNC lathe applications in China. They provide a wide range of turning, milling, and drilling tools that deliver superior performance and long tool life. Taegutec’s CNC lathe tooling is widely used in industries such as automotive, mold and die, and general machining.
5. Sumitomo Electric Hardmetal: Sumitomo Electric Hardmetal offers a diverse range of cutting tools, including carbide inserts, toolholders, and drills, for CNC lathe machining. Their products are known for their high cutting speeds, exceptional chip control, and long tool life. Sumitomo Electric Hardmetal continuously innovates cutting edge technologies to meet the evolving demands of the CNC lathe industry.
| Brand | Specialization | Product Range | Notable Features |
|————————-|———————————————-|——————————————|—————————————————————————————–|
| Sandvik Coromant | Cutting tools, inserts, tool holders | Extensive range of options | Advanced technologies, high productivity, and durability |
| Mitsubishi Materials | Cutting tools, inserts, drills, end mills | Comprehensive product range | Optimal cutting performance, accuracy, and reliability |
| Kyocera Industrial Ceramics | Ceramic cutting tools, inserts, toolholders | Heat resistance, wear resistance | Excellent heat resistance, wear resistance, and dimensional stability |
| Taegutec | Cutting tools, carbide inserts, toolholders | Wide range of options | Superior performance and long tool life |
| Sumitomo Electric Hardmetal | Carbide inserts, toolholders, drills | High cutting speeds, exceptional chip control | High cutting speeds, exceptional chip control, and long tool life |
6. Iscar: Iscar is a well-known CNC lathe tooling manufacturer in China, offering a wide range of products like carbide inserts, solid carbide end mills, and indexable toolholders. Iscar’s cutting tools are known for their advanced geometries and coatings, ensuring excellent chip evacuation, increased productivity, and improved performance.
7. WIDIA: WIDIA is a global leader in metalworking solutions, providing top-quality CNC lathe tooling products in China. Their extensive range of cutting tools, including inserts, drills, and end mills, offer exceptional performance, precision, and long tool life. WIDIA’s tools are designed to handle various machining applications under different conditions, enabling efficient material removal and high accuracy.
8. Kennametal: Kennametal is a renowned manufacturer of cutting tools, inserts, and tooling systems for CNC lathe machining in China. Their range of products includes rotary tooling, indexable inserts, and solid carbide end mills. Kennametal’s CNC lathe tooling is known for its reliability, versatility, and superior cutting performance, ensuring improved productivity and reduced downtime.
9. Zhuzhou Cemented Carbide: Zhuzhou Cemented Carbide is a leading manufacturer specializing in carbide inserts and toolholders for CNC lathe applications in China. Their products are highly regarded for their excellent cutting performance, wear resistance, and long tool life. Zhuzhou Cemented Carbide’s CNC lathe tooling is widely used in various industries such as automotive, aerospace, and machinery manufacturing.
10. KennaFlow: KennaFlow offers a wide range of CNC lathe tooling, including cutting tools, toolholders, and inserts. Their products are designed to provide exceptional precision, stability, and high-performance cutting. KennaFlow’s CNC lathe tooling is recognized for its excellent chip evacuation, optimized cutting force, and enhanced machining efficiency.
Please note that the above information is a brief introduction to each manufacturer’s products, and there may be additional factors to consider when choosing the most suitable CNC lathe tooling for specific machining requirements.
Background Research for cnc lathe tooling manufacturers Companies in China, use qcc.com archive.org importyeti.com
China is known for its thriving manufacturing industry, and this holds true for CNC lathe tooling manufacturers as well. When conducting background research on these companies, three useful platforms to consider are qcc.com, archive.org, and importyeti.com.
Qcc.com is a Chinese business database that provides comprehensive information on various companies, including CNC lathe tooling manufacturers. It offers details such as company profiles, business scope, contact information, and financial data. This platform can be used to gain insights into the size, capabilities, and reputation of different manufacturers.
Archive.org is a digital library that allows users to access archived versions of websites. It can be particularly helpful in researching historical information about CNC lathe tooling manufacturers in China, such as their past performance, product range, and any notable achievements or awards.
Importyeti.com is an import-export data platform that provides information on shipments and customs data. This platform can be used to track the import and export activities of CNC lathe tooling manufacturers in China, including the countries they trade with, the volume of their exports, and the types of tools being exported.
By leveraging these three platforms, researchers can gather essential information about CNC lathe tooling manufacturers in China. This includes details about their company profile, historical performance, capabilities, export activities, and other relevant data. Taking advantage of these resources can aid in identifying reliable and suitable manufacturers in China for CNC lathe tooling needs, while also staying within a concise word limit of 300 words.
Leveraging Trade Shows and Expos for cnc lathe tooling Sourcing in China
Trade shows and expos are an excellent platform for sourcing CNC lathe tooling in China. These events provide a unique opportunity to connect with numerous suppliers, compare products and prices, and establish valuable business relationships. By strategically leveraging trade shows and expos, businesses can effectively source CNC lathe tooling in China.
Firstly, trade shows and expos gather a large number of industry professionals and suppliers under one roof, providing a convenient and efficient way to explore various options. Visitors can interact directly with suppliers, inspect samples, and gain insights into the latest trends and developments in the CNC lathe tooling industry. This face-to-face communication allows for better understanding of products and builds trust between the buyer and supplier.
Secondly, trade shows and expos offer an environment conducive to comparison shopping. Businesses can examine different CNC lathe tools, compare quality, prices, and features, and evaluate suppliers side by side. This helps in making informed decisions and choosing the most suitable supplier based on specific requirements.
Furthermore, trade shows and expos often attract established and reputable suppliers from China. Such events provide a platform for businesses to engage with these suppliers, discuss their needs, and negotiate favorable terms. By directly engaging with potential suppliers, companies can establish long-term partnerships and ensure a reliable source of CNC lathe tooling.
To maximize the benefits of attending trade shows and expos, companies should prepare beforehand. This involves researching and identifying the most relevant events in the CNC lathe tooling industry, understanding the market, and setting clear objectives for attending the event. It is also essential to allocate sufficient time and resources to visit booths, collect information, and establish contacts with potential suppliers.
In conclusion, trade shows and expos are a valuable resource for sourcing CNC lathe tooling in China. They offer a platform to connect with suppliers, compare products and prices, and establish long-term business relationships. By strategically leveraging these events, businesses can successfully source high-quality CNC lathe tooling and gain a competitive edge.
The Role of Agents and Sourcing Companies in Facilitating cnc lathe tooling Purchases from China
Agents and sourcing companies play a crucial role in facilitating CNC lathe tooling purchases from China. These intermediaries act as a bridge between buyers and manufacturers, streamlining the procurement process and ensuring a smooth transaction.
One key role of agents and sourcing companies is to identify reliable and competent manufacturers in China. They have a deep understanding of the local market and can leverage their network to find top-quality suppliers who specialize in CNC lathe tooling. By thoroughly vetting manufacturers, agents can help buyers mitigate the risk of dealing with untrustworthy or low-quality suppliers.
Moreover, agents and sourcing companies provide comprehensive support throughout the purchasing process. They assist buyers in negotiating prices, terms, and conditions with manufacturers, thereby ensuring a fair deal. By acting as a mediator, they help bridge any communication gaps arising from language barriers or cultural differences, facilitating effective communication between both parties.
Agents also play a crucial role in quality assurance. They conduct thorough factory audits, ensuring that the manufacturer meets the necessary quality standards and has the required certifications. By performing inspections during production and before shipment, agents help buyers verify the quality of the CNC lathe tooling, thus reducing the risk of receiving substandard products.
Additionally, agents and sourcing companies can provide logistical support. They organize and coordinate shipping arrangements, handle customs clearance procedures, and ensure prompt delivery of the purchased goods. This relieves buyers of the logistical complexities involved in international transactions, allowing them to focus on their core business operations.
In summary, agents and sourcing companies serve as valuable intermediaries in facilitating CNC lathe tooling purchases from China. Their expertise in identifying reliable manufacturers, negotiating fair deals, ensuring quality assurance, and managing logistics significantly simplifies the procurement process and minimizes risks for buyers.
Price Cost Research for cnc lathe tooling manufacturers Companies in China, use temu.com and 1688.com
When conducting price cost research for CNC lathe tooling manufacturers in China, two popular platforms to explore are temu.com and 1688.com. These platforms provide a comprehensive range of suppliers and products, allowing buyers to compare prices and choose the most suitable option for their needs.
Temu.com is a renowned online sourcing platform that connects global buyers with suppliers from China. It offers an extensive database of CNC lathe tooling manufacturers, making it easier for buyers to find reliable suppliers. The platform allows users to compare prices, product specifications, and seller ratings. Additionally, temu.com provides the option to request quotations from multiple suppliers, helping buyers negotiate better prices.
Another prominent website to explore is 1688.com. This platform, run by Alibaba, is primarily in Chinese. However, with translation tools and Chrome extensions, it can be navigated by non-Chinese speakers. 1688.com offers a vast selection of CNC lathe tooling manufacturers, allowing buyers to browse through various product options and suppliers. Many manufacturers on this platform offer competitive prices, as they cater primarily to the domestic market.
When conducting research on these platforms, buyers should consider several factors to make an informed decision. Firstly, it is important to review the product specifications and quality assurance measures provided by the manufacturers. Additionally, buyers should consider supplier ratings and customer reviews to gauge the reliability and trustworthiness of the manufacturer.
Moreover, contacting multiple suppliers and requesting quotations would help in understanding the overall pricing range in the market. It is crucial to communicate the specifications, required quantity, and any specific customization needs to receive accurate quotations.
While comparing costs and pricing, buyers should not solely focus on the cheapest option. Instead, they should consider the overall value, including factors such as quality, customer service, and delivery times.
In conclusion, temu.com and 1688.com are two leading platforms for conducting price cost research on CNC lathe tooling manufacturers in China. Buyers can benefit from the vast supplier database, compare prices, and assess the overall value proposition when looking to procure CNC lathe tooling from China.
Shipping Cost for cnc lathe tooling import from China
The shipping cost for importing CNC lathe tooling from China can vary depending on several factors such as the weight and dimensions of the package, the shipping method chosen, and the destination country.
One of the most common shipping methods for international trade is sea freight, which is typically more cost-effective for heavier and bulkier shipments. The cost can be calculated based on the volume or weight of the shipment, and it is advisable to obtain quotes from different freight forwarders or shipping companies. On average, the shipping cost for a CNC lathe tooling package weighing around 100 kilograms can range from $500 to $2000, excluding any additional charges such as customs fees or insurance.
For smaller and lighter packages, air freight can be a faster option but usually comes at a higher cost. The shipping cost for a CNC lathe tooling package weighing around 20 kilograms by air can vary from approximately $300 to $800, depending on the airline and service level chosen. It is crucial to consider transit times, as air freight is usually faster than sea freight.
Additionally, it is important to note that the shipping cost may increase if there are any special requirements or restrictions associated with the CNC lathe tooling, such as hazardous materials or oversized dimensions. It is advisable to consult with the supplier in China and a trusted freight forwarder to ensure compliance with all regulations and avoid any unexpected fees.
Furthermore, it is recommended to consider the Incoterms (International Commercial Terms) agreed upon with the supplier, as it determines which party is responsible for arranging and paying for the shipping. The most common Incoterms used for international trade are FOB (Free on Board) and CIF (Cost, Insurance, and Freight).
In conclusion, the shipping cost for importing CNC lathe tooling from China can vary greatly depending on factors such as weight, dimensions, shipping method, and destination. It is crucial to gather multiple quotes, consider different shipping options, and consult with experienced professionals to ensure a smooth and cost-effective import process.
Compare China and Other cnc lathe tooling Markets: Products Quality and Price,Visible and Hidden Costs
China is one of the major players in the global CNC lathe tooling market, offering a wide range of products at competitive prices. However, when comparing China with other markets, such as Europe or the United States, there are certain differences in terms of products quality and price, as well as visible and hidden costs.
In terms of product quality, China has made significant progress over the years. Chinese manufacturers have invested in improving their production processes and implementing strict quality control measures. As a result, many Chinese CNC lathe tooling products now meet international standards and offer reliable performance. However, there may still be some variations in quality among different Chinese manufacturers, so it is important for buyers to conduct thorough research and choose reliable suppliers.
When it comes to price, China has a competitive advantage due to lower manufacturing and labor costs. Chinese manufacturers can produce CNC lathe tooling products at a lower price compared to their European or American counterparts. This cost advantage makes Chinese products more affordable and attractive to many buyers. However, it is important to consider the trade-off between price and quality. While Chinese products may be cheaper, it is essential to ensure that they meet the required standards and specifications.
Visible costs include the purchase price of the CNC lathe tooling products. Chinese manufacturers generally offer competitive prices that are lower compared to other markets. However, hidden costs should also be considered. These include factors such as shipping costs, import taxes, and potential product defects or delays. Buyers should account for these hidden costs when comparing prices and making purchasing decisions.
In terms of visible costs, China often offers a significant cost advantage. However, hidden costs such as longer lead times, language barriers, and potential quality issues may arise. Buyers should carefully evaluate these factors and work closely with Chinese suppliers to mitigate any potential risks.
In conclusion, China offers a wide range of CNC lathe tooling products with improved quality and competitive prices. However, buyers should conduct due diligence and consider both visible and hidden costs when comparing China with other markets. By carefully assessing product quality, price, and associated costs, buyers can make informed decisions and choose the most suitable option for their CNC lathe tooling needs.
Understanding Pricing and Payment Terms for cnc lathe tooling: A Comparative Guide to Get the Best Deal
When it comes to purchasing CNC lathe tooling, understanding pricing and payment terms is crucial to ensure the best deal. This comparative guide aims to shed light on the factors to consider while making a purchase, all within 300 words.
Price plays a fundamental role in any purchasing decision. However, it is essential to focus on the value provided by the tooling rather than solely considering the price tag. High-quality tooling may come at a higher cost initially, but it can lead to increased productivity, reduced downtime, and longer tool life, resulting in cost savings in the long run.
Some key factors that influence pricing include the material used, tool geometry, brand reputation, and complexity of manufacturing. Different suppliers may offer various pricing models, such as bulk discounts, package deals, or volume-based pricing. It is crucial to assess the overall cost and weigh it against the performance and longevity of the tooling.
Payment terms also vary among suppliers, and negotiation is often possible. Common payment options include upfront payment, payment upon delivery, or partial payments with milestones. Evaluating your cash flow needs and aligning them with the offered payment terms can help determine the most suitable option.
When comparing pricing and payment terms, it is recommended to reach out to multiple suppliers for quotes. This allows for a competitive analysis and ensures that you get the best deal. Additionally, understanding the supplier’s reputation, customer reviews, and certifications can provide insights into their reliability and product quality.
Furthermore, considering the supplier’s warranty or return policy is crucial. Knowing whether you have recourse in case of tool failure or dissatisfaction can provide peace of mind while finalizing the purchase.
To get the best deal, it is helpful to establish a relationship with the supplier. Long-term partnerships often lead to preferential pricing, special promotions, or access to new product lines.
In conclusion, when purchasing CNC lathe tooling, understanding pricing factors and payment terms is vital. Considering the value provided by the tooling, assessing various pricing models, negotiating payment terms, and evaluating supplier reputation are all essential steps to secure the best deal. Building a long-term relationship with suppliers enhances the likelihood of obtaining advantageous pricing and promotions.
Chinese Regulations and Industry Standards Certifications for cnc lathe tooling,Import Regulations and Customs for cnc lathe tooling from China
In China, the regulations and industry standards certifications for CNC lathe tooling are stringent to ensure product quality and safety. The most prominent certification in this industry is the ISO 9001:2015 standard, which specifies the requirements for a quality management system. This certification ensures that the manufacturer adheres to internationally recognized quality standards in the design, development, production, installation, and servicing of their CNC lathe tooling.
Other important industry standards that Chinese manufacturers often comply with include the GB/T (Guo Biao/Tui Jian) standards, which provide technical specifications and guidelines for different aspects of CNC lathe tooling manufacturing. These standards cover areas like materials selection, dimensions, performance, safety requirements, and testing methods.
When importing CNC lathe tooling from China, it is crucial to comply with import regulations and customs procedures. The first step is to classify the CNC lathe tooling based on the Harmonized System (HS) codes, which determine the applicable tariffs, import restrictions, and regulations. It is advisable to seek guidance from customs agents or trade specialists to ensure correct classification.
Importers should also familiarize themselves with the specific import regulations of their country. This may include obtaining permits or certifications, adhering to safety standards, or fulfilling labeling and packaging requirements. Documentation such as commercial invoices, packing lists, and bills of lading should be prepared accurately to facilitate customs clearance.
To smooth the import process, importers may also choose to work with an established freight forwarder or customs broker who can handle all the necessary documentation, communicate with Chinese suppliers, and navigate customs procedures efficiently.
In conclusion, Chinese regulations and industry standards certifications for CNC lathe tooling ensure product quality and safety. When importing from China, it is crucial to comply with import regulations and customs procedures, including proper classification of the products and fulfilling the necessary documentation and requirements. Seeking professional assistance can help streamline the import process.
Sustainability and Environmental Considerations in cnc lathe tooling Manufacturing
Sustainability and environmental considerations play a significant role in CNC lathe tooling manufacturing. This industry involves the production of tools used in computerized numerical control (CNC) lathes, which are widely used in various manufacturing processes. Here are some key aspects to consider in terms of sustainability and the environment:
1. Material Selection: Choosing sustainable materials is crucial in CNC lathe tooling manufacturing. Opting for materials with lower environmental impacts, such as recycled or biodegradable materials, can significantly reduce the industry’s carbon footprint. Additionally, using materials that are durable and require less maintenance can lead to longer tool lifecycles and reduced waste generation.
2. Energy Efficiency: CNC lathe tooling manufacturing requires energy-intensive processes, including machining, grinding, and heat treatment. Reducing energy consumption through the use of efficient machinery, optimizing tool paths, and implementing energy management systems can help minimize greenhouse gas emissions and lower manufacturing costs.
3. Waste Reduction: Implementing waste reduction strategies is paramount in promoting sustainability. This can include recycling and reusing materials, implementing lean manufacturing practices to eliminate waste in production processes, and properly disposing of hazardous waste. Reducing waste generation not only benefits the environment but also improves the overall efficiency and profitability of CNC lathe tooling manufacturing.
4. Packaging and Transportation: Sustainable packaging solutions and optimizing transportation logistics are essential considerations in achieving a greener supply chain. Using eco-friendly packaging materials and reducing packaging waste can help minimize the industry’s environmental impact. Additionally, implementing efficient transportation routes and modes can reduce fuel consumption and associated emissions.
5. Compliance with Regulations: Adhering to local, regional, and international environmental regulations is vital in CNC lathe tooling manufacturing. Companies must ensure they comply with regulations related to emissions, hazardous waste management, and workplace health and safety. Continued monitoring and improvement of manufacturing processes can help ensure compliance and minimize negative environmental impacts.
In conclusion, sustainability and environmental considerations are of utmost importance in CNC lathe tooling manufacturing. Implementing sustainable practices such as material selection, energy efficiency, waste reduction, responsible packaging, and compliance with regulations can help reduce the industry’s environmental footprint and create a greener manufacturing sector.
List The Evolution history of “cnc lathe tooling”
CNC (Computer Numerical Control) lathe tooling has come a long way since its inception. The evolution of CNC lathe tooling can be traced through several key milestones.
1. Early Developments: The concept of using numerical control in machine tools emerged in the mid-20th century. In the 1940s, the first experimental CNC machine was built, using punched paper tape as a means of program input. However, it was not until the 1950s that true CNC technology started to take shape.
2. Transition to Digital Control: In the 1960s, CNC lathe tooling began to shift from analog to digital control systems. The introduction of minicomputers and microprocessors enabled faster and more accurate control over machine movements. This transition marked a significant leap forward in the capabilities of CNC lathe tools.
3. CAD/CAM Integration: In the 1970s and 1980s, Computer-Aided Design (CAD) and Computer-Aided Manufacturing (CAM) technologies started to be integrated with CNC lathe tooling. This integration allowed for the easy creation and modification of part designs, which could then be directly translated into machine instructions. This not only increased efficiency but also enhanced the precision and complexity of the parts that could be manufactured.
4. Advancements in Control Systems: Throughout the 1990s and 2000s, CNC lathe tooling saw significant improvements in control systems. The introduction of more powerful processors and advanced software algorithms resulted in faster and more accurate machining operations. Additionally, advancements in servo and feedback systems improved the control over spindle speeds and tool movements.
5. Automation and Robotics: In recent years, automation and robotics have revolutionized CNC lathe tooling. The incorporation of robotic arms and automatic tool changers has enabled unmanned machining operations, reducing the need for human intervention and further increasing productivity.
6. Industry 4.0 and IoT: The current trend in CNC lathe tooling is towards Industry 4.0 and the Internet of Things (IoT). Machine learning algorithms, real-time data monitoring, and predictive analytics allow for more efficient production planning, optimization, and preventive maintenance. This integration of technology is enhancing the overall performance and reliability of CNC lathe tooling.
In conclusion, CNC lathe tooling has witnessed a remarkable evolution over the years. From the early experimental stages to the incorporation of advanced technologies like CAD/CAM integration and automation, CNC lathe tooling has continuously improved in precision, efficiency, and versatility. As we move into the era of Industry 4.0, we can expect further advancements and innovations in CNC lathe tooling technology.
The Evolution and Market Trends in cnc lathe tooling Industry
The CNC lathe tooling industry has witnessed significant evolution and market trends in recent years. The utilization of computer numerical control (CNC) technology has revolutionized the way lathe machines are operated, leading to increased efficiency, accuracy, and productivity.
One evolution in the CNC lathe tooling industry is the development of advanced cutting tools. Manufacturers are continuously seeking ways to enhance tooling performance to meet the demands of modern machining. This has resulted in the introduction of high-speed steel (HSS), carbide, and diamond-coated tools that offer superior cutting capabilities and longer tool life.
Another evolution is the integration of automation and robotics into CNC lathe tooling. Automation has enabled lights-out manufacturing, where machines can run uninterrupted for extended periods without human intervention. Robotics have further enhanced this aspect by facilitating the loading and unloading of parts, increasing production rates, and reducing labor costs.
Market trends in the CNC lathe tooling industry are largely influenced by technological advancements and market demands. One trend is the increasing demand for multi-axis machining. With the ability to simultaneously perform multiple operations, multi-axis lathes are becoming more popular, especially in industries such as aerospace, automotive, and medical.
Another trend is the growing focus on sustainability and eco-friendly practices. Manufacturers are increasingly adopting coolant-through tooling systems to reduce waste and improve cutting performance. Additionally, there is a rising demand for more energy-efficient CNC lathe machines that consume less power and have reduced carbon footprints.
Furthermore, market trends also include the shift towards digitalization and connectivity. CNC lathe tooling systems are being designed to integrate with Industry 4.0 principles, enabling real-time monitoring, data analysis, and remote control. This connectivity allows for predictive maintenance, minimizing machine downtime and optimizing production schedules.
In conclusion, the evolution and market trends in the CNC lathe tooling industry are driven by advancements in cutting tools, automation, multi-axis machining, sustainability, and digitalization. With continuous development and innovation, the industry is anticipated to grow further, meeting the increasing demands of various manufacturing sectors.
Custom Private Labeling and Branding Opportunities with Chinese cnc lathe tooling Manufacturers
There are numerous custom private labeling and branding opportunities available with Chinese CNC lathe tooling manufacturers. With their expertise and advanced technology, they can provide high-quality products tailored to meet specific branding requirements.
Chinese CNC lathe tooling manufacturers offer a range of customization options, allowing businesses to personalize their products according to their brand image and customer preferences. This includes logo engraving or printing, customized packaging, color variations, and more.
Private labeling enables businesses to establish their own brand identity and market themselves as unique entities in the industry. By partnering with Chinese manufacturers, companies can showcase their brand name and logo on the CNC lathe tooling, creating a professional and personalized touch to their products.
Branding opportunities also extend to promotional materials and marketing collateral. Chinese CNC lathe tooling manufacturers often offer additional services such as designing and producing marketing materials like brochures, catalogues, and user manuals. This helps businesses maintain a consistent brand image throughout their marketing campaigns.
Moreover, working with Chinese manufacturers allows businesses to take advantage of cost-efficient production processes and competitive pricing. This means businesses can maintain a competitive edge without compromising on quality.
In conclusion, Chinese CNC lathe tooling manufacturers offer extensive custom private labeling and branding opportunities for businesses. By partnering with these manufacturers, companies can personalize their products, establish a unique brand identity, and benefit from cost-effective production. With their advanced technology and expertise, they can help businesses leave a lasting impression in the market.
Tips for Procurement and Considerations when Purchasing cnc lathe tooling
When it comes to purchasing CNC lathe tooling, there are several factors to consider and tips to keep in mind to ensure the best procurement process. Here are some key considerations:
1. Assess your specific needs: Before starting the procurement process, thoroughly assess your requirements. Consider factors such as the type of materials you’ll be working with, the intended applications, and the production volume. Identifying your needs will help you make more informed decisions while purchasing.
2. Research and gather information: Take the time to research and gather information about different CNC lathe tooling options available in the market. Look for trusted suppliers who offer high-quality products and have a good reputation in the industry. Check online reviews, supplier websites, and industry forums to gain insights.
3. Quality and durability: CNC lathe tooling should be durable and of good quality to ensure optimal performance and longevity. Look for tools made from high-quality materials such as carbide, as they offer excellent wear resistance and longer tool life. Review customer feedback and ensure the products meet industry standards.
4. Compatibility: Ensure that the CNC lathe tooling you purchase is compatible with your specific lathe machine. Consider factors like the tool holder size, shank type, and any unique requirements of your machine. Mismatched tools can lead to poor performance, tool breakage, or incorrect machining results.
5. Price and value for money: While cost is an important consideration, prioritize value for money over the cheapest option. Look for suppliers who offer competitive prices without compromising on quality. Consider the long-term benefits and potential cost savings associated with higher-quality tools that last longer and perform better.
6. Supplier support: Choose a supplier who provides excellent customer support and after-sales service. This includes technical assistance, troubleshooting, and any necessary replacements or repairs. A reliable supplier will have knowledgeable staff who can offer guidance and support when needed.
7. Trial/testing phase: If feasible, request a trial or testing phase where you can assess the performance of the CNC lathe tooling in your specific production environment. This will help you gather real-time data and make more informed decisions based on observed performance.
Remember, effective procurement involves careful consideration, research, and collaboration with trusted suppliers. By understanding your needs, ensuring compatibility, prioritizing quality, and considering long-term value, you can make informed decisions when purchasing CNC lathe tooling.
FAQs on Sourcing and Manufacturing cnc lathe tooling in China
1. What are the advantages of sourcing and manufacturing CNC lathe tooling in China?
Sourcing and manufacturing CNC lathe tooling in China offers several advantages. Firstly, China has a well-developed manufacturing industry with a large number of skilled laborers and advanced machinery. This ensures high-quality precision tools at competitive prices.
2. How can I find reliable suppliers for CNC lathe tooling in China?
Finding reliable suppliers in China can be accomplished through various methods. Online platforms like Alibaba and Global Sources provide access to a wide range of manufacturers and suppliers. Conducting thorough background checks, reading reviews, and requesting samples are crucial steps to ensure credibility and product quality.
3. What should I consider when selecting a supplier for CNC lathe tooling in China?
When selecting a supplier, factors such as quality control processes, manufacturing capabilities, delivery time, and after-sales service should be considered. It is also essential to understand their experience and expertise in CNC lathe tooling production.
4. Can I customize the CNC lathe tooling according to my requirements?
Yes, many manufacturers in China offer customization services. They can design and produce CNC lathe tooling based on your specific requirements and specifications.
5. Are there any potential challenges or risks associated with sourcing and manufacturing CNC lathe tooling in China?
Some potential challenges include communication barriers, intellectual property protection, and quality control. Ensuring clear and constant communication with the supplier, protecting intellectual property through legal measures, and performing rigorous quality inspections can mitigate these risks.
6. What is the typical lead time for manufacturing CNC lathe tooling in China?
Lead times vary depending on the complexity of the tooling and the supplier’s production capacity. On average, it can range from a few weeks to a couple of months. It is crucial to discuss lead times with potential suppliers to align expectations.
7. How do I ensure product quality when sourcing CNC lathe tooling in China?
To ensure product quality, it is advisable to conduct factory visits, inspect manufacturing processes, and request samples. Performing third-party quality inspections and establishing clear quality control standards with the supplier are also effective measures.
In summary, sourcing and manufacturing CNC lathe tooling in China offer advantages such as competitive prices, skilled labor, and advanced manufacturing capabilities. To find reliable suppliers, thorough research, sample requests, and background checks are crucial. It is essential to consider factors like customization capability, quality control, and after-sales service when selecting a supplier. Challenges like communication barriers and intellectual property protection exist, but can be managed through clear communication, legal measures, and quality inspections. The lead time for manufacturing CNC lathe tooling varies, and ensuring product quality can be achieved through factory visits, inspections, and third-party inspections.
Why contact sourcifychina.com get free quota from reliable cnc lathe tooling suppliers?
Sourcifychina.com offers free quota from reliable CNC lathe tooling suppliers to provide convenience and benefits to its customers. Below are some reasons why they offer this service:
1. Trustworthy Suppliers: Sourcifychina.com has established strong relationships with reliable CNC lathe tooling suppliers in China. These suppliers have been thoroughly vetted and verified for their reputation, quality of products, and reliability in meeting customer requirements. By offering free quotas from these trusted suppliers, Sourcifychina.com ensures that their customers will be connected with reputable and credible sources.
2. Quality Assurance: The primary concern for Sourcifychina.com is to ensure that customers receive high-quality CNC lathe tooling products. By partnering with reliable suppliers, they can guarantee that the products offered are manufactured using top-notch materials and production processes. This helps customers avoid any potential issues with the quality of the tools they purchase, giving them peace of mind and confidence in their sourcing decisions.
3. Cost Savings: Accessing free quotas from reliable suppliers allows customers to save costs associated with sourcing CNC lathe tooling. These suppliers may offer competitive pricing or even exclusive discounts to Sourcifychina.com customers, enabling them to secure the best possible deals. Additionally, customers can avoid the expenses involved in conducting their own supplier research, negotiations, and quality checks.
4. Time Efficiency: Sourcing CNC lathe tooling can be a time-consuming process. Sourcifychina.com streamlines this process by connecting customers directly with pre-vetted suppliers who can provide free quotes. This saves customers valuable time that would otherwise be spent searching and communicating with potential suppliers.
In conclusion, Sourcifychina.com offers free quota access to reliable CNC lathe tooling suppliers to ensure customers receive quality products, cost savings, and time efficiency. By partnering with trusted suppliers, they provide a reliable platform for sourcing CNC lathe tooling needs in a convenient and efficient manner.