Introduce about cnc milling turning guide,Qulity,Cost,Supplier,Certification,Market,Tips,FAQ
CNC milling and turning are two essential processes in the manufacturing industry that utilize computer numerical control (CNC) technology to shape and create complex parts. In this guide, we will provide an overview of CNC milling and turning, including their quality standards, cost factors, reliable suppliers, certifications, market trends, helpful tips, and frequently asked questions (FAQs).
Quality is a crucial aspect of CNC milling and turning processes. High precision, accuracy, and consistent output are essential for manufacturing parts with tight tolerances. The use of CNC technology ensures repeatable quality that surpasses traditional manual methods.
Cost factors for CNC milling and turning include machine setup, material costs, part complexity, and volume. While initial setup costs may be high, CNC machining offers cost advantages in terms of increased efficiency, reduced waste, and faster production times compared to conventional methods.
Finding a reliable supplier for CNC milling and turning services is crucial. Look for companies with a proven track record, advanced equipment, and skilled operators. Online directories, referrals, and trade shows are useful resources for identifying reputable suppliers.
Certifications such as ISO 9001 demonstrate a supplier’s commitment to quality management systems. Additionally, certifications specific to the industry, such as AS9100 for aerospace applications, ensure compliance with strict industry standards.
The market for CNC milling and turning is rapidly growing, driven by demand from various industries such as automotive, aerospace, electronics, and medical. Technological advancements, including multi-axis machining and automation, are further propelling the market.
Here are some helpful tips for optimizing CNC milling and turning processes:
1. Optimize tooling selection and speeds to improve efficiency and reduce costs.
2. Prioritize proper material selection for optimal performance and durability.
3. Regularly maintain and calibrate CNC machines to ensure accuracy and prolong their lifespan.
4. Collaborate closely with the supplier to address any design or manufacturing challenges.
FAQs:
1. What is the difference between CNC milling and turning?
CNC milling involves removing material using rotating cutting tools, while turning rotates the part against a cutting tool to create cylindrical shapes.
2. What are the advantages of CNC machining?
CNC machining offers increased precision, efficiency, and consistency compared to traditional methods, enabling faster production and reducing waste.
3. How long does it take to receive CNC-machined parts?
Production lead times vary depending on factors such as part complexity, volume, and supplier’s capacity. It is best to consult with the supplier for an accurate timeline.
In conclusion, CNC milling and turning provide efficient and precise manufacturing solutions. Partnering with a reliable supplier that meets stringent quality standards is crucial for successful outcomes. By understanding the market trends, cost factors, and following best practices, businesses can optimize CNC milling and turning processes for their specific needs.
Types of cnc milling turning
CNC milling and turning are two common types of machining processes used in the manufacturing industry. CNC stands for Computer Numerical Control, which means the machines are controlled by computer programs to precisely cut and shape materials.
CNC milling is a subtractive manufacturing process where a cutting tool rotates and removes material from a workpiece to create the desired shape or form. The milling machine moves in multiple axes (typically three or more) to achieve complex geometries. It can perform various operations, such as face milling, contouring, drilling, and pocketing. The ability to change and control the cutting tool’s direction and speed allows for high precision and efficiency in milling. CNC milling is commonly used in industries like aerospace, automotive, and electronics for producing parts with tight tolerances and intricate shapes.
On the other hand, CNC turning is a machining process that rotates a workpiece while a cutting tool moves linearly to remove material and create cylindrical parts. The workpiece is held in a chuck or collet, and the cutting tool moves along the length of the rotating workpiece to shape it. CNC turning is ideal for creating cylindrical components like shafts, pins, and studs. It is widely used in industries such as automotive, oil and gas, and medical devices.
There are different types of CNC milling and turning machines, each with their specific capabilities and applications. For example, vertical milling machines have a vertical spindle orientation and are commonly used for smaller parts, while horizontal milling machines have a horizontal spindle orientation and are suitable for larger workpieces.
Similarly, in CNC turning, there are various configurations available, such as standard lathes, Swiss-type lathes, and multi-axis lathes. Standard lathes work by rotating the workpiece on a single axis, while Swiss-type lathes use guide bushings to support long and slender workpieces during turning operations. Multi-axis lathes have the capability to move the cutting tool in multiple directions simultaneously, enabling more complex machining operations.
In summary, CNC milling and turning are essential processes in modern manufacturing. CNC milling is used for creating complex geometries, while CNC turning is primarily used for cylindrical parts. With various types of machines available, manufacturers can choose the most suitable option based on their specific requirements and the desired end product. The precise control provided by CNC technology ensures consistent and accurate machining, leading to high-quality finished parts.
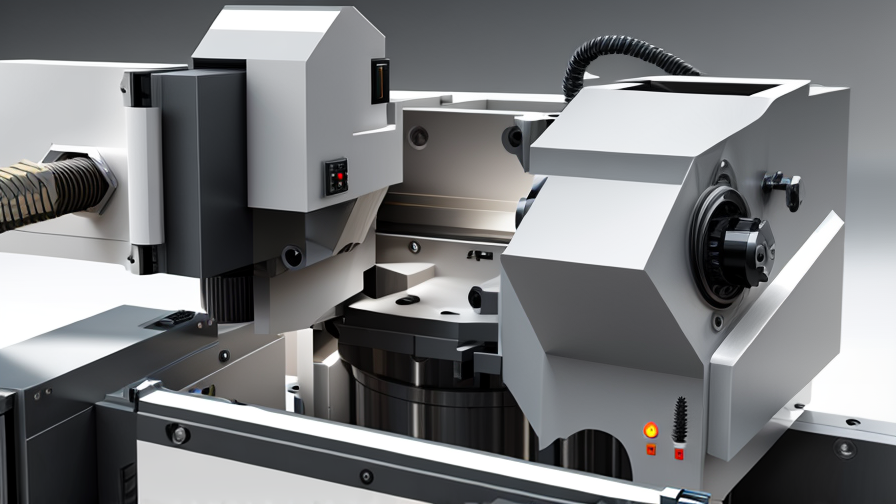
Pros and Cons of Using cnc milling turning
CNC milling and turning are widely used in the manufacturing industry to produce complex parts with high precision. Here are some of the pros and cons of using CNC milling and turning:
Pros:
1. Precision and accuracy: CNC milling and turning machines are known for their high accuracy and precision. They can produce parts with tight tolerances and consistent quality, ensuring that each product meets the required specifications.
2. Versatility: CNC milling and turning machines can work with a wide range of materials, including metals, plastics, and composites. This makes them suitable for a variety of applications in different industries, such as aerospace, automotive, and medical.
3. Efficiency and productivity: CNC milling and turning machines operate with high speed and efficiency. They can perform multiple operations in a single setup, reducing the need for manual intervention and increasing productivity.
4. Flexibility: CNC milling and turning machines can handle complex designs and geometries. They can create intricate shapes and features that would be difficult or impossible to achieve with manual methods.
5. Reproducibility: Once a CNC program is developed for a specific part, it can be easily replicated to produce identical pieces. This ensures consistency and saves time in the production process.
Cons:
1. Initial investment: CNC milling and turning machines are expensive to purchase and set up. This can be a significant barrier for small businesses or startups.
2. Skill requirements: Operating CNC machines requires specialized training and expertise. Skilled operators are needed to program and operate the machines, which can add to labor costs.
3. Maintenance and repair: CNC machines require regular maintenance and occasional repairs to ensure they operate at optimal levels. This can add to the overall cost of ownership.
4. Limited flexibility for small batch production: While CNC machines are highly efficient for mass production, they may not be as cost-effective for small batch sizes. The setup time and programming efforts involved may outweigh the benefits in such cases.
5. Complexity of programming: Developing CNC programs can be complex and time-consuming, particularly for intricate parts. This requires skilled programmers who have a deep understanding of CAD/CAM software and machining techniques.
In conclusion, CNC milling and turning offer numerous advantages in terms of precision, efficiency, versatility, and reproducibility. However, the initial investment, skill requirements, maintenance costs, limited flexibility for small batch production, and programming complexity should be considered as potential drawbacks.
cnc milling turning Reference Specifications (varies for different product)
CNC milling and turning reference specifications can vary depending on the specific product being manufactured. However, some common specifications apply to both processes.
In CNC milling, the reference specifications typically include dimensions such as length, width, and height, as well as tolerances for each dimension. These tolerances define the allowable variation in the dimensions of the milled product and ensure it meets the desired quality standards. Surface finish is another important specification that determines the texture of the milled product.
Additionally, the type of material being milled is essential to consider. Different materials have varying characteristics, such as hardness and strength, which influence the machining parameters, including the spindle speed and feed rate. The reference specifications may also include information regarding the specific tooling required to achieve the desired milling results.
In CNC turning, the reference specifications focus on the diameter and length of the turned product, as well as the tolerances associated with these dimensions. Similar to milling, the surface finish is an important specification in turning as well. Additionally, the desired shape of the turning operation, whether it is cylindrical, conical, or threaded, is specified in the reference specifications.
The material being turned is also a significant consideration. Factors such as the material’s hardness, ductility, and machinability influence the choice of cutting tools, cutting speeds, and feeds. The reference specifications for turning may also include details about the required workholding devices, such as chucks or collets, to securely hold the workpiece during the machining process.
It is important to note that these reference specifications may vary for different products as each product may have unique requirements. Manufacturers must carefully analyze and understand the specific needs of the product before establishing the reference specifications for CNC milling and turning operations.
In summary, CNC milling and turning reference specifications encompass dimensions, tolerances, surface finish requirements, material considerations, and other pertinent details. These specifications, although varying for different products, guide manufacturers in creating precise and quality machined parts.
Applications of cnc milling turning
CNC milling and turning are two widely used techniques in the manufacturing industry. They allow for precise and efficient production of complex parts and components. Here are a few applications of CNC milling and turning:
1. Aerospace Industry: CNC milling and turning are extensively used in the aerospace industry for manufacturing components such as turbine blades, engine parts, landing gears, and structural frames. The precise production capabilities of CNC machines ensure high-quality parts that are crucial for the safety and performance of aircraft.
2. Automotive Industry: CNC milling and turning are widely applied in the automotive industry to produce parts such as engine blocks, steering and suspension components, and brake system parts. These techniques enable the automotive industry to achieve high production rates and maintain the desired accuracy and quality of the parts.
3. Medical Industry: CNC milling and turning are essential in the production of medical devices and instruments. These techniques are used for manufacturing items like surgical tools, orthopedic implants, prosthetics, and dental components. The accuracy and precision offered by CNC machines are critical in ensuring the proper functioning and fit of these medical products.
4. Electronics Industry: CNC milling and turning play a significant role in the manufacturing of electronic components and devices. These techniques are used to fabricate precise circuit boards, connectors, and conductive parts. The ability to create intricate designs and meet tight tolerances makes CNC machining ideal for the electronics industry.
5. Defense Industry: CNC milling and turning are essential in the defense sector for producing weapons, military vehicles, and various components used in defense systems. The ability to manufacture complex and high-strength parts makes CNC machining crucial in this industry.
6. Energy Sector: CNC milling and turning are widely used in the energy sector for manufacturing parts for wind turbines, oil and gas equipment, solar panels, and power generation systems. The ability to produce intricate designs and maintain tight tolerances ensures the efficiency and reliability of these energy-related components.
In conclusion, CNC milling and turning are versatile manufacturing techniques with numerous applications across various industries. From aerospace and automotive to medical and defense sectors, these techniques consistently deliver precise, complex, and high-quality parts to meet the diverse needs of various industries.
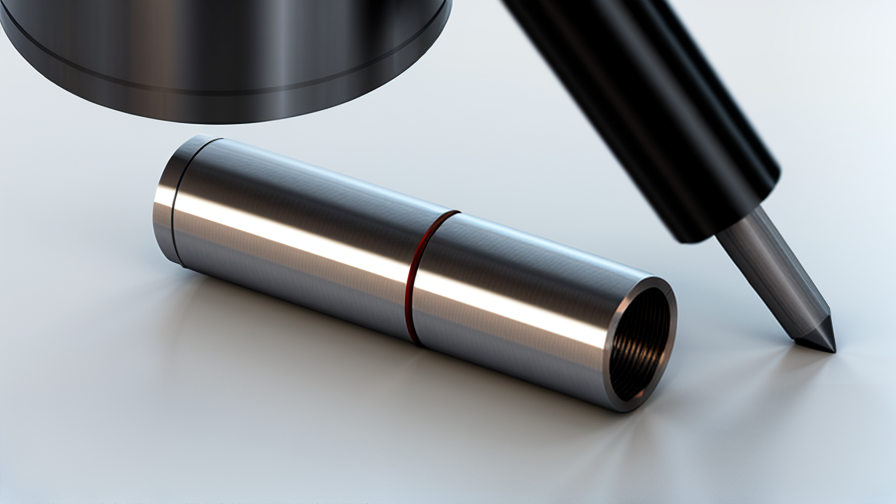
The Work Process and how to use cnc milling turning
CNC milling and turning are two essential processes used in the manufacturing industry to shape and fabricate parts and components. These processes involve using computer-controlled machines, known as CNC (Computer Numerical Control) machines, to remove materials from a workpiece and create the desired shape.
The work process of CNC milling starts with designing a 3D model of the part using computer-aided design (CAD) software. The CAD file is then uploaded to the CNC milling machine, which uses a variety of cutting tools to remove material from the workpiece and create the desired shape. The machine’s computer program coordinates the movement of the cutting tools in the X, Y, and Z axes, ensuring precise and accurate machining. CNC milling is ideal for creating complex shapes, holes, and slots in various materials such as metal, plastic, and wood.
CNC turning, on the other hand, is used to create cylindrical parts by rotating a workpiece while a cutting tool removes material to shape it. The work process of CNC turning involves mounting the workpiece on a CNC lathe, which spins it rapidly. The cutting tool is then brought into contact with the rotating workpiece, and material is removed to create the desired shape. Like CNC milling, CNC turning also relies on CAD software to design the part and a computer program to control the movements of the cutting tool.
To use CNC milling and turning effectively, one needs to have a good understanding of CAD software and programming. The CAD software is used to create precise 3D models of the part, which serve as a blueprint for the machining process. The CAD file is then converted into a CNC program using CAM (Computer-Aided Manufacturing) software. This program contains instructions for the CNC machine on how to move the cutting tools and remove material. The CNC program is then uploaded to the machine, and the machining process begins.
During the machining process, it is crucial to monitor the CNC machine, ensuring that it is operating correctly and producing the desired results. Factors such as tool wear, material properties, and machine settings need to be considered to achieve optimum machining outcomes. Regular maintenance and tool changes are also necessary to ensure the machine’s accuracy and precision.
In conclusion, CNC milling and turning are versatile manufacturing processes used to create various parts and components. By utilizing CAD software, CAM software, and CNC machines, manufacturers can achieve highly precise and complex shapes. Understanding the work process and effectively using these technologies can lead to efficient and accurate production.
Quality Testing Methods for cnc milling turning and how to control the quality
Quality testing methods for CNC milling and turning involve various techniques to ensure the products meet the required specifications and standards. Here are some commonly used methods:
1. Dimensional Inspection: The parts produced through CNC milling and turning need to be inspected for accurate measurements using tools such as calipers, micrometers, or coordinate measuring machines (CMM). This ensures that the dimensions of the finished product are within the specified tolerances.
2. Surface Finish Analysis: CNC milling and turning also require assessing the surface finish of the parts. Techniques like visual inspection, profilometry, or surface roughness measurement are employed to check for any defects, scratches, or inconsistencies on the surface.
3. Hardness Testing: Components produced through CNC milling and turning may need to undergo hardness testing to assess their mechanical properties. Hardness testers, such as Rockwell or Brinell machines, can measure the resistance of the material to indentation, providing information about its suitability for particular applications.
4. Material Analysis: CNC milling and turning may involve using different materials, including metals or plastics. Material analysis techniques, such as spectroscopy or chemical testing, ensure that the right materials are used and conform to the required specifications.
5. Performance Testing: CNC-machined components are often subjected to functional or performance testing. This could involve applying stress to the part to assess its strength or demonstrating its ability to meet specific performance criteria.
To ensure quality control during CNC milling and turning, several steps can be taken:
1. Proper Machine Setup: Adequate calibration of CNC machines, regular maintenance, and correct tooling selection are crucial to ensuring consistent quality output.
2. Process Monitoring: Real-time monitoring of machining parameters, such as cutting speed, feed rates, and tool wear, helps identify any deviations or issues during the production process. Implementing process control techniques like Statistical Process Control (SPC) can help maintain quality.
3. Inspection throughout the Process: Regular inspection and measurement during CNC milling and turning, at different stages of the production process, help identify defects or variations early on and prevent further wastage of time and resources.
4. Qualified Personnel: Skilled operators trained in CNC programming, machine operation, and quality inspection are essential for maintaining quality control. Regular training and qualifications are necessary to ensure that personnel can effectively handle the process.
5. Continuous Improvement: Implementing feedback mechanisms, conducting root cause analysis, and making necessary adjustments to the processes are essential for continuous improvement and effective quality control in CNC milling and turning.
By employing these testing methods and quality control measures, CNC milling and turning can deliver high-quality products that meet the required specifications and customer expectations.
cnc milling turning Sample Policy and Post-Purchase Considerations for cnc milling turning from China
Sample Policy and Post-Purchase Considerations for CNC Milling/Turning from China:
Sample Policy: When sourcing CNC milling/turning services from China, it is important to consider the following sample policy:
1. Sample Availability: Before placing a bulk order, request samples from the supplier to evaluate the quality, precision, and finish of their CNC milling/turning capabilities. Ensure that the supplier offers samples and is willing to accommodate customization requests if needed.
2. Sample Cost and Delivery: Understand the supplier’s sample cost and shipping charges. Clarify if the sample cost will be refunded if a bulk order is placed. Also, inquire about the estimated time for sample delivery.
3. Sample Revisions: Check with the supplier if they allow revisions to the samples based on your feedback and specific requirements. Clarify the revision process, cost implications, and turnaround time.
4. Documentation: Request complete documentation for the sample, including technical drawings, material specifications, and other relevant details. This will help evaluate the supplier’s attention to detail and adherence to specifications.
Post-Purchase Considerations: After placing a bulk order for CNC milling/turning from China, consider the following factors:
1. Quality Control: Insist on a quality control process to ensure that the final products meet the required standards. Discuss quality control procedures, such as inspections, certifications, and testing, that the supplier implements during the manufacturing process.
2. Communication and Collaboration: Establish clear lines of communication with the supplier to address any concerns, modifications, or delays during the production process promptly. Prompt communication is crucial to avoid any misunderstandings or errors.
3. Shipping and Logistics: Discuss shipping and logistics arrangements with the supplier, including packaging, transportation, and insurance. Ensure that the supplier has experience in handling international shipments and has a reliable shipping partner to minimize delays or damage.
4. Warranty and After-Sales Support: Inquire about the supplier’s warranty period and after-sales support. Check if they have provisions for repair, replacement, or refund in case of any manufacturing defects or non-compliance with the agreed specifications.
5. Compliance with Regulations: Verify if the supplier adheres to relevant industry standards, such as ISO certifications. Ensure that their manufacturing processes comply with safety and environmental regulations, as per your country’s requirements.
By considering these sample policy and post-purchase considerations, you can mitigate risks and ensure a smooth process while sourcing CNC milling/turning services from China.
Sourcing cnc milling turning from China: Opportunities, Risks, and Key Players
Sourcing CNC milling and turning services from China presents several opportunities and risks for businesses. China has a robust manufacturing sector and is known for its competitive pricing and quality capabilities. The country is home to numerous skilled workers and advanced machinery, making it a desirable destination for outsourcing production needs.
One of the main advantages of sourcing CNC milling and turning services from China is cost-effectiveness. Chinese manufacturers often offer lower labor costs compared to other countries, resulting in reduced production expenses. Additionally, China’s large-scale production capabilities allow for economies of scale, enabling businesses to enjoy significant cost savings.
Moreover, China’s manufacturing industry has witnessed rapid technological advancements in recent years. This has contributed to improved precision and efficiency in CNC milling and turning processes. The country’s manufacturers have invested in cutting-edge machinery and software, ensuring high-quality output.
However, there are risks associated with sourcing CNC milling and turning services from China. One key concern is intellectual property infringement. Instances of unauthorized copying and counterfeiting have been reported, potentially exposing businesses to legal disputes and brand reputation damage.
Quality control can also be a challenge when sourcing from China. While there are many reputable manufacturers in the country, there are also cases of substandard or counterfeit products being produced. Conducting thorough due diligence and quality checks on potential suppliers is crucial to mitigate this risk.
Despite the risks, China remains a dominant player in the CNC milling and turning market. Some key players in this sector include Foxconn Technology Group, Shenzhen Guanghongda Technology Co., Ltd., and Shenzhen Yi Xin Precision Metal and Plastic Ltd. These companies have extensive experience in providing CNC milling and turning services to global clients and have established a reputation for quality and reliability.
In conclusion, sourcing CNC milling and turning services from China provides opportunities for cost savings, advanced technology, and skilled labor. However, businesses must be cautious of potential risks such as intellectual property infringement and quality control issues. By partnering with reputable manufacturers, conducting thorough due diligence, and implementing proper quality control measures, businesses can leverage the benefits of Chinese manufacturing while minimizing potential risks.
How to find and select reliable cnc milling turning manufacturers in China,use google search manufacturers and suppliers
To find and select reliable CNC milling turning manufacturers in China, you can utilize the following steps using Google search:
1. Search relevant keywords: Begin your search by using keywords like “CNC milling turning manufacturers China” or “CNC milling turning suppliers China” in the Google search bar.
2. Refine search results: Analyze the top search results and visit the manufacturer’s websites to gather information about their services, expertise, and experience. Look for clear and comprehensive information, including the range of products offered, certifications, manufacturing capabilities, and customer reviews if available.
3. Check company background: Once you shortlist potential manufacturers, research about their background. Verify their company history, years of operation, and any notable achievements or partnerships. This helps in assessing their credibility and reliability.
4. Review manufacturing facilities: Look for information about their manufacturing facilities, machinery, and technologies used. Reliable manufacturers usually have well-equipped facilities with modern CNC machines and adhere to strict quality control measures. Evaluate whether they possess the necessary resources and capability to meet your specific requirements.
5. Certifications and quality standards: Check if the manufacturer has important certifications such as ISO 9001:2015, which validates their commitment to quality. Additionally, look for any industry-specific certifications or compliance with specific international standards that may be relevant to your project, such as ISO 13485 for medical devices.
6. Request for samples: Contact the shortlisted manufacturers and request samples of their CNC-machined products. This will allow you to assess the quality of their work firsthand. Evaluate the precision, surface finish, and overall quality of the samples to ensure they meet your expectations.
7. Price comparison and negotiation: Obtain detailed quotations from multiple manufacturers and compare their pricing. However, don’t solely focus on the lowest pricing as quality and reliability are equally important factors. Negotiate pricing based on the volume of your order or any other mutually beneficial terms.
8. Communication and responsiveness: Pay attention to manufacturers who promptly respond to your inquiries and provide clear communication throughout the process. Effective communication is crucial for ensuring that your requirements are understood and met.
9. Customer reviews and references: Look for reviews and testimonials from previous customers. Additionally, you can request the manufacturer to provide references of their existing or past clients. Reach out to these references to gain valuable insights into the manufacturer’s reliability, professionalism, and overall satisfaction.
By following these steps and conducting due diligence, you can find and select reliable CNC milling turning manufacturers in China for your specific requirements.
How to check cnc milling turning manufacturers website reliable,use google chrome SEOquake check if ranking in top 10M
To determine the reliability of a CNC milling turning manufacturer’s website, follow these steps:
1. Use Google Chrome and install the SEOquake extension:
– Open Chrome browser and search for “SEOquake extension.”
– Install the SEOquake extension to your browser.
2. Search for the manufacturer’s website:
– In the Chrome browser, type the name or keywords related to the CNC milling turning manufacturer in the search bar.
– Look for the manufacturer’s official website among the search results.
3. Check the website’s ranking with SEOquake:
– Once you have accessed the manufacturer’s website, click on the SEOquake extension icon.
– A toolbar will appear on the top of the website, displaying various metrics about the site’s SEO performance.
– Check the “Rank” value; if it is within the top 10 million, this indicates that the website receives a significant amount of traffic and is likely reliable.
4. Evaluate the website’s content:
– Analyze the manufacturer’s website content for quality and professionalism.
– Look for information about their expertise, experience, certifications, and customer reviews/testimonials.
– The presence of comprehensive information and positive customer feedback suggests reliability.
5. Verify contact information and policies:
– Make sure the manufacturer’s website provides accurate and detailed contact information, including physical address, phone number, and email.
– Check if they have a clear refund/return policy, terms of service, and privacy policy, indicating a transparent business operation.
6. Research the manufacturer:
– Conduct additional research on the company’s reputation and history.
– Look for reviews or feedback on trustworthy platforms or industry forums.
– Verify the manufacturer’s presence on social media channels, as active and engaged companies are often more reliable.
7. Trust your instincts:
– Consider your overall impression of the website and the manufacturer.
– If something feels too good to be true or if the site appears questionable or unprofessional, it may be wise to seek an alternative manufacturer.
Remember to use these steps as a guideline rather than a definitive method for determining reliability. It is always advisable to gather multiple sources of information and compare different manufacturers to make an informed decision.
Top 10 cnc milling turning manufacturers in China with each 160 words introduce products,then use markdown create table compare
1. Haas Automation Inc. specializes in CNC milling and turning machines for a wide range of applications. Their product line includes vertical machining centers, horizontal machining centers, turning centers, and rotary tables. Haas machines are known for their high accuracy, reliability, and affordability.
2. DMG Mori Co., Ltd. is a leading manufacturer of CNC milling and turning machines. Their product portfolio comprises of multi-axis machining centers, horizontal and vertical turning centers, and hybrid additive manufacturing machines. DMG Mori is known for its advanced technology, precision, and performance.
3. Makino, a renowned company, offers CNC milling and turning solutions that cater to various industries. Their product range includes vertical machining centers, horizontal machining centers, and high-speed milling machines. Makino machines are known for their advanced technology, durability, and high productivity.
4. DMG MORI Seiki Co., Ltd. is a global manufacturer of CNC milling and turning machines. Their product lineup features horizontal and vertical machining centers, turning centers, and automated production systems. DMG MORI Seiki machines are known for their superior performance, efficiency, and reliability.
5. Fanuc Corporation specializes in CNC milling and turning machines for diverse applications. Their product range includes vertical machining centers, horizontal machining centers, and turning centers. Fanuc machines are renowned for their precision, high-speed capabilities, and long-term reliability.
6. Mazak Corporation offers a wide range of CNC milling and turning machines for various industries. Their product portfolio includes both horizontal and vertical machining centers, as well as turnkey automation solutions. Mazak machines are known for their quality, high performance, and innovative features.
7. Okuma Corporation is a prominent manufacturer of CNC milling and turning machines. Their product lineup features vertical machining centers, double column machining centers, and multitasking machines. Okuma machines are renowned for their precision, versatility, and cutting-edge technology.
8. Doosan Machine Tools Co., Ltd. specializes in CNC milling and turning machines for different industries. Their product range includes vertical machining centers, horizontal machining centers, and turning centers. Doosan machines are known for their reliability, accuracy, and superior performance.
9. Haas Factory Outlet operates under Haas Automation Inc. and offers a wide range of CNC milling and turning machines. Their product lineup includes vertical machining centers, horizontal machining centers, turning centers, and rotary tables. Haas Factory Outlet provides high-quality machines, exceptional service, and technical support.
10. Chiron-Werke GmbH & Co. KG is a leading manufacturer of CNC milling and turning machines. Their product portfolio comprises vertical machining centers, horizontal machining centers, and turnkey solutions. Chiron machines are known for their precision, speed, and efficiency.
| Manufacturer | Product Range | Specialties |
| ———– | ————– | ———– |
| Haas Automation Inc. | Vertical machining centers, horizontal machining centers, turning centers, rotary tables | Accuracy, reliability, affordability |
| DMG Mori Co., Ltd. | Multi-axis machining centers, turning centers, hybrid additive manufacturing machines | Advanced technology, precision, performance |
| Makino | Vertical machining centers, horizontal machining centers, high-speed milling machines | Advanced technology, durability, productivity |
| DMG MORI Seiki Co., Ltd. | Horizontal machining centers, vertical machining centers, turning centers, automated production systems | Superior performance, efficiency, reliability |
| Fanuc Corporation | Vertical machining centers, horizontal machining centers, turning centers | Precision, high-speed capabilities, reliability |
| Mazak Corporation | Horizontal machining centers, vertical machining centers, turnkey automation solutions | Quality, high performance, innovation |
| Okuma Corporation | Vertical machining centers, double column machining centers, multitasking machines | Precision, versatility, cutting-edge technology |
| Doosan Machine Tools Co., Ltd. | Vertical machining centers, horizontal machining centers, turning centers | Reliability, accuracy, superior performance |
| Haas Factory Outlet | Vertical machining centers, horizontal machining centers, turning centers, rotary tables | High-quality machines, exceptional service, technical support |
| Chiron-Werke GmbH & Co. KG | Vertical machining centers, horizontal machining centers, turnkey solutions | Precision, speed, efficiency |
These top 10 CNC milling and turning manufacturers in China offer a comprehensive range of products that cater to various industries. Each manufacturer has its specialty, which makes them stand out in terms of technology, performance, and reliability. Customers can choose from a wide range of machining centers, turning centers, and other related solutions. By utilizing advanced technology and ensuring superior quality, these manufacturers strive to meet the needs of both domestic and international customers. With their expertise and experience, they play a significant role in the CNC machining industry in China and contribute to the growth of manufacturing across different sectors.
Background Research for cnc milling turning manufacturers Companies in China, use qcc.com archive.org importyeti.com
When it comes to finding CNC milling and turning manufacturers in China, several online platforms can provide valuable information. Three useful platforms for background research are QCC.com, Archive.org, and ImportYeti.com.
QCC.com is a comprehensive business information database that contains company profiles, financial information, industry analysis, and other relevant data. This platform can help researchers gather detailed information about CNC milling and turning manufacturers in China, including their business scope, legal status, registered capital, and key executives. Additionally, QCC.com provides insights into the company’s financial performance, such as payment records and credit ratings.
Archive.org is a platform that allows users to access snapshots of websites over time. By using Archive.org, researchers can explore the historical development and changes of CNC milling and turning manufacturers’ websites. This can provide insights into the company’s growth trajectory, product offerings, and technological advancements over time.
ImportYeti.com is a platform that provides data on import and export transactions. By using ImportYeti.com, researchers can obtain valuable information on the import activities of CNC milling and turning manufacturers in China. This includes details about the buyers, suppliers, product descriptions, shipment dates, and quantities imported. This data can help researchers determine the reputation and reliability of potential manufacturers, as well as their ability to fulfill international orders.
When conducting background research for CNC milling and turning manufacturers in China, utilizing these platforms can provide a wealth of information. By leveraging QCC.com, Archive.org, and ImportYeti.com, researchers can gain insights into the company’s history, financial performance, and import/export activities. This information can help assess the reliability, capabilities, and potential partnership opportunities with CNC milling and turning manufacturers in China.
Leveraging Trade Shows and Expos for cnc milling turning Sourcing in China
Trade shows and expos provide excellent opportunities for sourcing CNC milling and turning services in China. These events bring together manufacturers, suppliers, and industry experts under one roof, making it easier for businesses to connect with potential partners and explore a wide range of options.
When it comes to sourcing CNC milling and turning services from China, trade shows and expos offer several advantages. Firstly, these events allow businesses to see and examine the actual products and technologies offered by different suppliers. This firsthand experience helps in evaluating the quality, precision, and capabilities of the CNC milling and turning services.
Secondly, trade shows and expos provide a platform for direct communication with suppliers. Businesses can discuss their specific requirements, ask questions, and even negotiate pricing and terms on the spot. This face-to-face interaction fosters a better understanding of the supplier’s capabilities, manufacturing processes, and overall reliability.
Furthermore, trade shows and expos often feature seminars, workshops, and presentations by industry experts. Attending these sessions provides valuable insights into the latest trends, technologies, and advancements in CNC milling and turning services, helping businesses stay up-to-date and make informed decisions.
To make the most out of these events, it is crucial to prepare and plan in advance. Research and identify the trade shows and expos that align with your sourcing needs. Register and book your trip early to secure the best accommodations and access to important networking opportunities.
During the event, create a list of potential suppliers, noting down their contact details, product catalogs, and any other relevant information. Engage in conversations, ask for samples or demonstrations, and collect business cards for later reference.
After the trade show or expo, carefully evaluate the options and information gathered. Compare suppliers based on their quality, pricing, delivery capabilities, and past customer reviews. Narrow down your choices and initiate further discussions or negotiations with the selected suppliers.
In conclusion, trade shows and expos offer a convenient and efficient way to source CNC milling and turning services from China. These events provide an excellent platform for evaluating suppliers, connecting with potential partners, and staying updated on the latest industry developments. By leveraging these opportunities, businesses can find reliable and capable suppliers for their CNC milling and turning needs.
The Role of Agents and Sourcing Companies in Facilitating cnc milling turning Purchases from China
Agents and sourcing companies play a crucial role in facilitating CNC milling and turning purchases from China. These intermediaries act as a bridge between the buyers and the suppliers, ensuring a smooth and successful transaction.
One of the key advantages of using agents and sourcing companies is their knowledge and expertise in the Chinese market. They have a deep understanding of the local manufacturing industry, including the capabilities and specialties of different suppliers. This knowledge allows them to identify the most suitable suppliers for specific CNC milling and turning requirements. Additionally, they can provide valuable insights into the current market trends, pricing, and quality standards.
Agents and sourcing companies also streamline the sourcing process by handling supplier identification, negotiation, and communication. They conduct thorough supplier screenings, evaluating their qualifications, production capacity, and quality control measures. This saves buyers a significant amount of time and effort that would otherwise be spent researching and contacting potential suppliers.
Moreover, agents and sourcing companies play a crucial role in ensuring quality control and product inspection. They monitor the production process, conduct regular inspections, and thoroughly evaluate the finished products before they are shipped to the buyer. This minimizes the risk of receiving subpar or defective products and ensures that the CNC milling and turning requirements are met.
Another critical function of agents and sourcing companies is facilitating communication and overcoming language and cultural barriers. They serve as translators and interpreters, ensuring that there are no misunderstandings or miscommunications between the buyer and the supplier. This enhances clarity, efficiency, and trust in the business relationship.
In summary, agents and sourcing companies provide invaluable support in purchasing CNC milling and turning products from China. Their knowledge of the Chinese market, expertise in supplier identification and communication, and quality control measures streamline the sourcing process and help buyers ensure the successful procurement of high-quality products.
Price Cost Research for cnc milling turning manufacturers Companies in China, use temu.com and 1688.com
When it comes to finding CNC milling turning manufacturers in China, two popular platforms for sourcing price cost information are temu.com and 1688.com. These websites provide a wide range of suppliers and offer an extensive database for conducting research.
Temu.com is a well-known platform for connecting buyers and suppliers in the CNC machining industry. It offers a curated selection of manufacturers with a focus on quality and reliability. The website provides detailed company profiles, including information on their manufacturing capabilities, equipment, and certifications. Additionally, temu.com allows users to request quotes directly from suppliers, making it convenient to compare prices and negotiate terms.
1688.com, on the other hand, is a Chinese wholesale marketplace owned by Alibaba Group. It serves as a comprehensive platform for various products, including CNC milling and turning services. Although the website is primarily in Chinese, it offers a broad range of suppliers and competitive pricing. Users can explore different categories, filter search results, and contact suppliers for detailed pricing information.
To effectively utilize these platforms for price cost research, follow these steps:
1. Begin by creating an account on temu.com and 1688.com.
2. Specify your requirements, such as the quantity of parts, materials, and any specific manufacturing processes or tolerances.
3. Conduct a search on each platform, using relevant keywords like “CNC milling turning” or “CNC machining.”
4. Review multiple supplier profiles and shortlist those that meet your criteria.
5. Contact the shortlisted suppliers and provide them with detailed specifications, drawings, or designs to request accurate quotes.
6. Discuss pricing, lead times, payment terms, and any other necessary details with the suppliers.
7. Compare the quotes received, taking into consideration factors like quality, production capacity, and overall supplier reputation.
8. Negotiate with suppliers if necessary, aiming for the best possible price without compromising the quality of the CNC milling turning services.
9. Select the most suitable supplier based on their pricing, expertise, and capabilities.
10. Consider conducting a factory visit or requesting product samples before finalizing the agreement.
By utilizing temu.com and 1688.com, you can efficiently conduct price cost research for CNC milling turning manufacturers in China. Be sure to maintain clear communication with suppliers and thoroughly evaluate their capabilities and offerings to make an informed decision.
Shipping Cost for cnc milling turning import from China
The shipping cost for importing CNC milling turning machines from China depends on various factors such as the weight and dimensions of the machines, the shipping method, and the destination country. Generally, there are two main shipping methods for importing goods from China: air freight and sea freight.
Air freight is a faster but more expensive shipping option. It is suitable for small-sized or urgent shipments. The cost is calculated based on the weight of the goods and the volume they occupy in the aircraft. On average, air freight rates for CNC milling turning machines can range from $3 to $10 per kilogram. However, this cost can vary depending on the specific weight and dimensions of the machines.
Sea freight, on the other hand, is a more economical shipping option for large-sized shipments. It is suitable for bulk orders or non-urgent shipments. The cost is calculated based on the volume of the goods, measured in cubic meters (CBM), and the shipping route. On average, sea freight rates for CNC milling turning machines can range from $100 to $300 per cubic meter. However, additional charges such as customs fees, fuel surcharges, and documentation fees may apply.
It is important to note that these costs are estimates, and it is recommended to contact shipping companies or freight forwarders to get accurate quotes for the specific shipment requirements. Additionally, it is advisable to consider insurance coverage for the goods during transportation, which may incur additional costs but provides protection against any potential damages or losses.
In conclusion, the shipping cost for importing CNC milling turning machines from China can vary based on the weight, dimensions, shipping method, and destination country. Air freight is faster but more expensive, while sea freight is more economical for larger shipments. It is recommended to consult with shipping companies for accurate cost estimates and ensure appropriate insurance coverage for a successful and secure import process.
Compare China and Other cnc milling turning Markets: Products Quality and Price,Visible and Hidden Costs
China is undeniably one of the leading markets for CNC milling and turning. However, it is important to compare it with other markets in terms of product quality, price, visible and hidden costs.
In terms of product quality, China has gained a reputation for offering a wide range of products with varying quality levels. While some manufacturers in China offer high-quality CNC milling and turning products, others may provide inferior or substandard ones. Other markets, such as Germany, Japan, and the United States, often have a stronger reputation for consistently delivering high-quality precision components. These markets are renowned for their stringent quality control processes and adherence to international standards.
When it comes to price, China generally offers competitive pricing for CNC milling and turning services. The lower labor and production costs in China allow manufacturers to offer more affordable options compared to other markets. However, this can also be associated with compromises in terms of quality. Other markets, particularly countries with higher labor and production costs, tend to have higher price points. However, customers often find value in paying a premium for products that are known for their superior quality and reliability.
Visible costs include the direct expenses associated with CNC milling and turning, such as material and labor costs. China, benefiting from economies of scale, can provide cost advantages due to their large manufacturing capabilities. However, hidden costs, such as communication challenges, intellectual property concerns, and potential delays in shipping and customs clearance, exist in the Chinese market. In contrast, other markets may offer more streamlined processes, efficient communication, and stronger intellectual property protections, which can minimize such hidden costs.
In summary, while China excels in offering competitive pricing and a wide range of CNC milling and turning products, other markets such as Germany, Japan, and the United States often have a stronger reputation for producing consistent high-quality products. Additionally, hidden costs associated with doing business in China, such as communication challenges and intellectual property concerns, should also be taken into account when comparing markets. Ultimately, the choice between China and other markets depends on the specific requirements and priorities of the customers, weighing quality, price, and visible and hidden costs.
Understanding Pricing and Payment Terms for cnc milling turning: A Comparative Guide to Get the Best Deal
When it comes to CNC milling and turning services, understanding pricing and payment terms is crucial to ensure you get the best deal. Here is a comparative guide to help you navigate this process, all within a concise 300 words.
1. Pricing Structure:
CNC milling and turning services typically have two pricing structures: per hour or per part. The per hour pricing model charges based on the machine’s usage time, while the per-part model is based on the complexity and quantity of parts produced. Comparing quotes from multiple service providers will enable you to determine the most cost-effective option.
2. Material Costs:
The type and quality of materials used significantly impact the final price. Some CNC service providers may charge separate material costs, while others include these expenses in the overall price. Be sure to verify if the price quote includes materials or if they are billed separately.
3. Setup Fees:
Many CNC service providers charge a setup fee to cover the initial preparation work required for the job. This fee often varies based on factors such as machine setup time, tooling requirements, and programming needs. Understanding and comparing setup fees can help you identify the most affordable solution.
4. Volume Discounts:
If you require a large volume of parts, inquire about volume discounts from potential service providers. Many CNC milling and turning companies offer reduced prices for larger quantities, making it crucial to explore this possibility to save costs.
5. Payment Terms:
Payment terms can vary among CNC service providers. Some may require upfront payment, while others offer flexible payment options such as partial payments or net 30 terms. Assess your financial situation and choose a payment term that suits your budget and cash flow requirements.
6. Additional Services:
Evaluate whether additional services, like design assistance, material sourcing, or finishing, are included in the price or available at an extra cost. While these services may increase the final price, they might provide substantial added value and save you time and effort.
By understanding the aforementioned factors and comparing quotes from several CNC milling and turning service providers, you can secure the best deal for your requirements. Consider your budget, project complexity, delivery timeline, and quality expectations to make an informed decision that balances cost-efficiency and value.
Chinese Regulations and Industry Standards Certifications for cnc milling turning,Import Regulations and Customs for cnc milling turning from China
In China, the regulations and industry standards certifications for CNC milling turning include the following:
1. GB/T 6892: This is the national industry standard for aluminum alloy profiles used in CNC milling turning. It specifies the technical requirements, test methods, and inspection rules for these profiles.
2. GB/T 2970: This standard outlines the ultrasonic testing methods for steel plates used in CNC milling turning. It ensures the quality and integrity of the materials.
3. GB/T 3190: This standard lays down the chemical composition, mechanical properties, and allowable deviation of aluminum and aluminum alloys used in CNC milling turning. It ensures the desired characteristics and performance of the materials.
4. GB/T 1804: This standard provides the regulations for the tolerance calculations and fits used in CNC milling turning. It ensures the precision and accuracy of the machined parts.
Regarding import regulations and customs for CNC milling turning from China, several key points need to be considered:
1. Import Regulations: Importers need to comply with the regulations and requirements of their respective countries. This includes obtaining the necessary licenses and permits, as well as adhering to local customs and import duties.
2. Customs Declaration: A detailed customs declaration form, specifying the type, quantity, and value of the imported CNC milling turning products, needs to be filled out accurately.
3. Tariffs and Duties: Importers should be aware of the import tariffs and duties imposed by their countries. These charges are usually based on the product’s value and sometimes the country of origin.
4. Documentation: Proper documentation is crucial for customs clearance. This may include invoices, packing lists, certificates of origin, and compliance with safety standards.
5. Compliance with Standards: Imported CNC milling turning products should comply with the safety, quality, and performance standards set by the importing country.
It is important for importers to thoroughly research and comply with the specific regulations and customs requirements of their respective countries to ensure a smooth and hassle-free import process.
Sustainability and Environmental Considerations in cnc milling turning Manufacturing
Sustainability and environmental considerations play a vital role in CNC milling and turning manufacturing processes. These practices focus on minimizing the negative environmental impact of manufacturing activities, reducing waste generation, conserving energy, and implementing eco-friendly practices.
One significant aspect of sustainability in CNC milling and turning manufacturing is the efficient use of resources. By optimizing the design and material selection, manufacturers can minimize waste and reduce the consumption of raw materials. This not only reduces the environmental footprint but also lowers production costs. Additionally, the use of recyclable materials or implementing recycling programs allows for the reuse of materials, further reducing waste generation.
Energy conservation is another crucial aspect of sustainability in CNC milling and turning manufacturing. Manufacturers can employ advanced technologies such as energy-efficient equipment and machinery, LED lighting, and automated systems to minimize energy consumption. By reducing energy consumption, manufacturers can contribute to the reduction of greenhouse gas emissions and combat climate change.
Implementing proper waste management practices is also critical in sustainable CNC manufacturing. Companies can implement recycling programs to reduce waste sent to landfills. Waste materials such as metal chips, coolant, and other by-products can be effectively recycled or treated to prevent contamination of the environment.
Furthermore, the use of eco-friendly lubricants and coolants can also contribute to sustainable manufacturing practices. These substances reduce the release of harmful chemicals into the environment and minimize health risks for the workers.
To achieve sustainable manufacturing, companies should also consider the life cycle assessment (LCA) of their products. LCA involves assessing the environmental impact of a product throughout its entire life cycle, from raw material extraction to end-of-life disposal. By understanding the environmental impact, manufacturers can identify areas for improvement and implement sustainable practices.
In conclusion, sustainability and environmental considerations are integral to CNC milling and turning manufacturing processes. By optimizing resource use, conserving energy, implementing proper waste management, and considering LCA, manufacturers can minimize their environmental impact, reduce costs, and contribute to a greener future.
List The Evolution history of “cnc milling turning”
CNC milling and turning have revolutionized the manufacturing industry by enhancing precision, efficiency, and automation. Let’s explore the evolution history of these processes.
1. Early Machine Tools: The roots of CNC milling and turning can be traced back to the development of early machine tools in the 18th and 19th centuries. These tools, such as lathes and milling machines, were manually operated and required skilled craftsmen to control them.
2. Numerical Control (NC): The concept of numerical control emerged in the mid-20th century. The first numerical control machines were developed in the 1940s and 1950s. They used punched paper tape to control the movements of the machine tools, enabling automated and repeatable machining processes.
3. Computer Numerical Control (CNC): The introduction of computers in the 1960s marked a significant milestone in the evolution of milling and turning. CNC machines replaced the punched paper tape with computer programs to control the tool movements. This advancement allowed for more complex machining operations and improved accuracy.
4. Advancements in Controllers: Over time, CNC controllers became more advanced and powerful. They incorporated features like multiple-axis control, tool-path optimization, and real-time monitoring. These advancements increased the speed, precision, and versatility of CNC milling and turning machines.
5. Integration of CAD/CAM: CNC machines became even more powerful with the integration of computer-aided design (CAD) and computer-aided manufacturing (CAM) software. This integration enabled seamless digital communication between design and manufacturing, simplifying the programming and machining processes.
6. Automation and Robotics: The evolution of CNC milling and turning also saw the integration of automation and robotics. This allowed for unmanned, high-speed, and round-the-clock production capabilities. Robots now handle material handling, tool changing, and other repetitive tasks, further enhancing productivity.
7. Advanced Machining Techniques: CNC milling and turning have also evolved to incorporate advanced machining techniques such as high-speed machining, five-axis machining, and multitasking. These techniques have improved productivity, reduced cycle times, and expanded the range of materials and geometries that can be machined.
In conclusion, CNC milling and turning have come a long way since their early manual counterparts. From simple numerical control to powerful computer-controlled systems, these processes have constantly evolved to become indispensable tools in modern manufacturing, offering increased precision, automation, and efficiency.
The Evolution and Market Trends in cnc milling turning Industry
The CNC milling and turning industry has witnessed significant evolution and market trends over the years, transforming it into a vital component of modern manufacturing processes. CNC (Computer Numerical Control) technology has revolutionized the way milling and turning operations are carried out, offering greater precision, efficiency, and automation.
One of the key advancements in the industry is the integration of advanced software systems into CNC machines. These programs allow for greater control and optimization of the milling and turning processes, enabling manufacturers to achieve higher accuracy and improved productivity. Additionally, the use of CAD/CAM (Computer-Aided Design/Computer-Aided Manufacturing) software has further streamlined the design and production stages, reducing human errors and facilitating faster turnaround times.
Another significant trend has been the increasing popularity of multi-tasking machines that combine milling and turning capabilities in a single setup. Such equipment eliminates the need for transferring workpieces between different machines, resulting in reduced setup times and enhanced productivity. This trend is driven by the demand for versatility in manufacturing processes and the need to save space and costs.
In recent years, there has been a growing emphasis on sustainability and environmentally-friendly practices, leading to the adoption of greener technologies in the CNC milling and turning industry. Manufacturers are increasingly investing in energy-efficient machines, recycling systems, and implementing sustainable manufacturing practices to minimize waste and reduce their environmental impact. This trend is expected to continue as sustainability becomes a top priority for businesses across industries.
Additionally, the integration of IoT (Internet of Things) technology into CNC machines is another significant development in the industry. IoT-enabled machines provide real-time monitoring and analysis of production data, allowing manufacturers to optimize processes, enhance efficiency, and reduce downtime. This technology also facilitates remote monitoring and control, enabling manufacturers to manage multiple machines and operations from a centralized location.
Overall, the evolution and market trends in the CNC milling and turning industry have been characterized by greater automation, precision, sustainability, and connectivity. As technology continues to advance, we can expect further improvements in efficiency, quality, and customization capabilities, driving the growth and competitiveness of this industry.
Custom Private Labeling and Branding Opportunities with Chinese cnc milling turning Manufacturers
Chinese CNC milling turning manufacturers offer custom private labeling and branding opportunities for businesses looking to establish their unique identity in the market. With their advanced manufacturing capabilities, these manufacturers can produce high-quality products according to specific requirements and designs.
Private labeling allows businesses to create their own brand by placing their logo, name, and other design elements on the products. This helps in building brand recognition, loyalty, and differentiation in the market. Chinese manufacturers understand the value of private labeling and work closely with businesses to ensure their branding requirements are met.
In addition to private labeling, Chinese CNC milling turning manufacturers also offer branding opportunities. This involves designing and manufacturing products that align with a business’s brand image and values. Manufacturers can adapt their manufacturing processes to meet specific design requirements and incorporate unique features that reflect the desired brand identity.
By partnering with Chinese manufacturers, businesses can take advantage of their expertise in CNC milling and turning processes to create high-quality branded products. These manufacturers have skilled technicians, state-of-the-art machinery, and a strong quality control system to ensure the products meet the brand’s standards.
Moreover, Chinese manufacturers often provide flexible production volumes to accommodate the needs of different businesses. This enables businesses to start with small quantities and gradually increase production as their brand gains popularity.
In conclusion, Chinese CNC milling turning manufacturers offer custom private labeling and branding opportunities, providing businesses with the ability to create their own unique brand identity. By partnering with these manufacturers, businesses can manufacture high-quality branded products tailored to their specific requirements and design preferences.
Tips for Procurement and Considerations when Purchasing cnc milling turning
When it comes to purchasing CNC milling turning machines, it is important to consider several key factors in order to make a well-informed decision. Here are some tips and considerations to keep in mind:
1. Machine Size and Configuration: Determine the required size and configuration of the machine based on the size and complexity of the parts to be milled or turned. Consider the available workspace and the compatibility with existing equipment.
2. Accuracy and Precision: Look for machines that offer high accuracy and precision in their operations. Pay attention to features such as the spindle speed, axis drives, and control systems, as they greatly influence the machine’s performance.
3. Capacity and Workload: Assess the machine’s capacity to handle the required workload. Consider factors such as the maximum weight and size of the parts, as well as the required production rate.
4. Cutting Tools and Tool Holders: Ensure that the machine is compatible with a wide range of cutting tools and tool holders. This allows for versatility in machining operations and reduces the need for constant tool changes.
5. Software and Programming: Evaluate the machine’s software and programming capabilities. Look for machines that offer user-friendly interfaces and flexible programming options, such as CAD/CAM compatibility.
6. Maintenance and Support: Research the reputation of the manufacturer or supplier in terms of maintenance and support. Ensure that spare parts are readily available and that technical assistance is easily accessible.
7. Cost: Set a budget and evaluate the cost of the machine, including any optional extras and associated maintenance expenses. Consider the long-term value and return on investment that the machine can provide.
8. Training and Operator Skill: Assess the availability of training programs for the machine’s operation and programming. Evaluate the skill level of your operators and determine if additional training will be necessary.
9. Safety Features: Ensure that the machine has adequate safety features, such as guards, emergency stop buttons, and interlocks, to protect both operators and the machinery.
10. Future Expansion and Upgrades: Consider the possibility of future expansion or upgrades. Determine if the machine can be easily upgraded or modified to accommodate changing production needs.
In summary, when purchasing CNC milling turning machines, it is crucial to consider factors such as machine size, accuracy, capacity, cutting tools, software, maintenance, cost, training, safety, and future expansion. Taking these factors into account will help you make an informed decision and choose a machine that aligns with your specific requirements.
FAQs on Sourcing and Manufacturing cnc milling turning in China
1. Why should I consider sourcing and manufacturing CNC milling turning in China?
China is known for its competitive pricing, vast manufacturing capabilities, and strong supply chain infrastructure. By sourcing CNC milling turning services in China, businesses can benefit from cost savings without compromising on the quality of precision parts. Moreover, Chinese manufacturers have extensive experience in producing complex components and can offer a wide range of materials, finishes, and customization options.
2. How can I ensure the quality of CNC milling turning services in China?
To ensure quality, it is crucial to choose a reliable and reputable manufacturer. Conduct thorough research, check their certifications, visit their facilities if possible, and request samples or prototypes for evaluation. It is also recommended to establish a comprehensive quality control process, including inspections at different stages of production, to maintain consistent standards.
3. Can I manufacture small quantities of CNC milled and turned parts in China?
Yes, many Chinese manufacturers are capable of producing small to medium quantities of CNC milled and turned parts. However, it is important to communicate your specific requirements to the manufacturer to ensure they can accommodate your order size.
4. What is the typical lead time for CNC milling and turning in China?
Lead times may vary depending on the complexity of the parts, order quantity, and manufacturer’s capacity. Typically, Chinese manufacturers can provide relatively fast turnaround times, ranging from a few days to several weeks. Clear communication and setting realistic expectations with the manufacturer can help manage the lead time effectively.
5. How can I communicate effectively with Chinese manufacturers during the sourcing and manufacturing process?
Overcoming language barriers can be a challenge. It is recommended to work with manufacturers that have English-speaking staff or employ translators to facilitate communication. Utilizing detailed technical drawings, CAD models, and written specifications can help minimize misunderstandings. Prompt and regular communication, preferably via email, is also essential for maintaining a smooth collaboration.
6. What are the shipping options for CNC milled and turned parts from China?
Chinese manufacturers have good access to various shipping options, including air, sea, and express delivery services. The choice will depend on factors such as urgency, order size, and budget. Sea freight is generally more cost-effective for larger quantities, while air or express shipping may be preferable for urgent or smaller orders.
In conclusion, sourcing and manufacturing CNC milling and turning services in China can provide cost savings, diverse customization options, and efficient production capabilities. By conducting thorough research, ensuring quality control measures, effective communication, and choosing reliable manufacturers, businesses can benefit from the advantages offered by China’s manufacturing industry.
Why contact sourcifychina.com get free quota from reliable cnc milling turning suppliers?
Sourcifychina.com offers free quota from reliable CNC milling turning suppliers for several reasons. Firstly, it allows businesses to easily assess and compare the costs and services offered by different suppliers without any financial commitment. By obtaining multiple quotes, companies can make informed decisions and select the most suitable supplier based on their requirements, quality standards, and budget.
Secondly, offering a free quota helps build trust and credibility. Sourcifychina.com acts as a bridge between businesses and suppliers in China, a market known for its manufacturing capabilities. By providing free quotations, Sourcifychina.com demonstrates its commitment to assisting businesses in finding reliable and trustworthy suppliers, thereby alleviating concerns about potential scams or unreliable partners.
Furthermore, obtaining free quotes reduces the financial risk for businesses, particularly for smaller companies or startups with limited budgets. By offering this service at no cost, Sourcifychina.com ensures that even businesses with tight finances can access high-quality CNC milling turning suppliers in China, enabling them to compete on a global scale.
Additionally, by providing a free quota, Sourcifychina.com encourages businesses to explore outsourcing possibilities. Outsourcing production to China can often lead to significant cost savings, improved lead times, and access to advanced manufacturing technologies. By eliminating the financial barrier of obtaining quotes, Sourcifychina.com aims to promote and facilitate global trade and collaboration with Chinese suppliers.
In conclusion, Sourcifychina.com offers free quotas from reliable CNC milling turning suppliers to help businesses make informed decisions, build trust, reduce financial risks, and encourage outsourcing possibilities. This service enables companies to access the vast manufacturing capabilities of China and leverage its competitive advantages to enhance their own business operations.