Introduce about cnc machine metal guide,Qulity,Cost,Supplier,Certification,Market,Tips,FAQ
CNC machine metal guide is a highly advanced and precision tool that is used in metal fabrication processes. It is designed to provide accurate and intricate shaping, cutting, and drilling of metal components. The quality of CNC machine metal guide is ensured by using high-quality materials and advanced technology in its construction. This ensures high precision and consistency in its performance.
The cost of CNC machine metal guide depends on factors such as the size, complexity, and features of the machine. It can range from a few thousand dollars to several hundred thousand dollars. It is important to choose a reputable supplier that offers quality products and reliable customer support. Certification from regulatory bodies ensures the quality and safety of the CNC machine metal guide.
The market for CNC machine metal guide is highly competitive with several manufacturers and suppliers offering a wide range of products. It is important to research and compare different options to find the best fit for your specific needs. Some tips for purchasing a CNC machine metal guide include considering the size and capacity of the machine, the compatibility with your existing equipment, and the level of customer support provided by the supplier.
Frequently asked questions about CNC machine metal guide include inquiries about the warranty, maintenance requirements, training and support options, and the compatibility with different metal types. It is important to carefully consider these factors when selecting a CNC machine metal guide to ensure optimal performance and longevity.
Types of cnc machine metal
There are several types of CNC machines that are specifically designed for cutting and shaping metal. Some common types include:
1. CNC Milling Machine: This type of machine uses rotating cutting tools to remove material from a workpiece. It is commonly used for creating complex parts and prototypes from a variety of metals including steel, aluminum, and titanium.
2. CNC Lathe Machine: A CNC lathe machine is used to create cylindrical parts by rotating a workpiece while a cutting tool moves along it. This machine is ideal for turning and shaping metal rods, tubes, and other cylindrical pieces.
3. CNC Plasma Cutter: This machine uses a high-velocity jet of ionized gas to cut through metal sheets. It is commonly used for cutting thick metal plates, creating intricate designs, and producing parts for industries such as automotive and aerospace.
4. CNC Laser Cutter: This machine uses a high-powered laser beam to cut through metal sheets with precision and speed. It is particularly effective for cutting thin metals like stainless steel, aluminum, and brass.
5. CNC Waterjet Cutter: A CNC waterjet cutter uses a stream of high-pressure water mixed with abrasive particles to cut through metal materials. It is suitable for cutting a wide range of metals including steel, copper, and titanium, as well as other materials like glass and stone.
Overall, these CNC machines provide high accuracy, repeatability, and efficiency in metal cutting processes, making them indispensable tools for the manufacturing industry. By utilizing these machines, manufacturers can produce intricate metal parts with tight tolerances and high quality finishes.
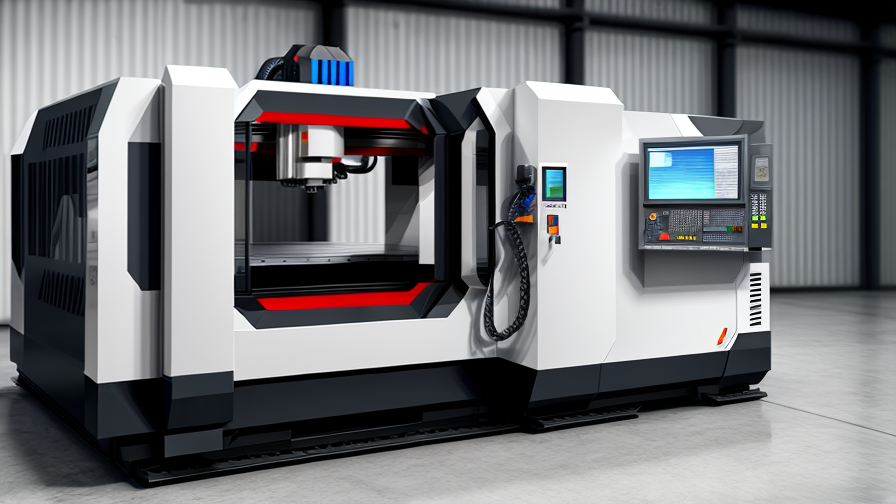
Pros and Cons of Using cnc machine metal
Pros of Using CNC Machine for Metal:
1. Precision: CNC machines offer a high level of precision, allowing for accurate and consistent results. This is crucial in metalworking, where precision is often essential for proper fit, functionality, and safety of the final product.
2. Efficiency: CNC machines can work at a much faster rate compared to manual methods. They have the ability to perform complex machining tasks in a fraction of the time it would take for a human operator, thereby increasing productivity.
3. Automation: CNC machines can be programmed to perform repetitive tasks automatically, reducing the need for manual labor and minimizing the chance of errors. This frees up human operators to focus on other important aspects of production.
4. Versatility: CNC machines can be used to manufacture a wide range of metal components, from simple to highly complex designs. They are capable of machining various materials, such as aluminum, steel, brass, and titanium, to name a few.
5. Cost-effectiveness: While the initial investment in CNC machines may be high, they can provide long-term cost savings. The reduction in labor costs, increased productivity, and minimized material waste contribute to overall cost-effectiveness.
Cons of Using CNC Machine for Metal:
1. Initial Investment: Purchasing CNC machines, especially those with advanced features, can be expensive for small businesses or individuals. Additionally, maintenance and repair costs can add to the overall expenses.
2. Skill Requirement: Operating CNC machines requires skilled personnel who can properly program and set up the machines. The training and expertise needed may limit the availability of qualified operators, potentially leading to higher labor costs.
3. Programming Complexity: Programming CNC machines can be complex, requiring knowledge of specialized software and coding languages. This can be time-consuming and potentially challenging for those without prior experience.
4. Limited Flexibility: CNC machines are designed to perform specific operations based on their programming. Altering the design or modifying the production process may require reprogramming, which can be time-consuming and disruptive.
5. Maintenance and Downtime: Like any machinery, CNC machines require regular maintenance to ensure optimal performance. Unscheduled downtime for repairs can disrupt production schedules and lead to delays in delivering finished products.
In summary, the pros of using CNC machines for metal include precision, efficiency, automation, versatility, and cost-effectiveness. However, the cons involve the initial investment, skill requirement, programming complexity, limited flexibility, and maintenance and downtime considerations.
cnc machine metal Reference Specifications (varies for different product)
CNC (Computer Numerical Control) machines are widely used in the metalworking industry to automate the manufacturing process. The specifications of CNC machines can vary depending on the specific metal product being manufactured. However, several common reference specifications exist for CNC machines used in metalworking.
One key specification is the machine’s maximum table size or working envelope, which determines the size of metal parts that can be processed. This specification varies depending on the CNC machine model and can range from small tabletop machines to large industrial-sized machines capable of handling large metal sheets.
Another important specification is the spindle speed, which refers to the rotational speed of the cutting tool. Spindle speeds can vary widely depending on the material being machined and the desired cutting action. Higher spindle speeds are generally used for softer metals, while lower speeds are utilized for harder materials like stainless steel.
The cutting tool used in CNC machines is another critical specification. Different tools are designed for specific tasks, such as drilling, milling, or turning, and come in various sizes and shapes. Tool compatibility and interchangeability are crucial considerations when selecting a CNC machine for metalworking.
CNC machines also have specific power requirements, including electrical voltage and phase, which can vary depending on the machine’s size and capabilities. Adequate power supply and grounding are essential to ensure proper machine operations and avoid electrical issues during metal production.
Furthermore, the control system is a significant specification of CNC machines. Modern CNC systems typically use computer-based controllers that provide programming flexibility and precise control over machining operations. The control system should be user-friendly, offering a range of programming options and compatibility with common CAD/CAM software.
In summary, CNC machines used for metalworking have varying specifications depending on the specific product being manufactured. Key specifications include the machine’s table size, spindle speed, cutting tool compatibility, power requirements, and the control system. Understanding and considering these specifications are crucial for selecting the appropriate CNC machine for metal manufacturing processes.
Applications of cnc machine metal
CNC machines are widely used in the metalworking industry for a variety of applications due to their precision and efficiency. Some common applications of CNC machines in metalworking include:
1. Metal cutting: CNC machines are used for cutting metal sheets, bars, pipes, and other metal components with high precision and accuracy. The machines can be programmed to cut complex shapes and designs, allowing for intricate metal fabrication.
2. Drilling and tapping: CNC machines are also used for drilling and tapping operations on metal components. The machines can be programmed to drill precise holes of varying sizes and depths, as well as tap threads into metal parts.
3. Turning and milling: CNC machines are commonly used for turning and milling operations on metal components. Turning involves rotating a metal workpiece on a spindle while a cutting tool shapes the material, while milling involves removing material from a workpiece using a rotary cutting tool.
4. Welding and fabrication: CNC machines can be used for welding and fabrication of metal components, such as welding together metal parts or fabricating metal structures with high precision and accuracy.
5. Engraving and etching: CNC machines are also used for engraving and etching metal components, allowing for intricate designs and markings to be added to metal surfaces.
Overall, CNC machines play a crucial role in the metalworking industry by providing precision, efficiency, and versatility in a wide range of applications.
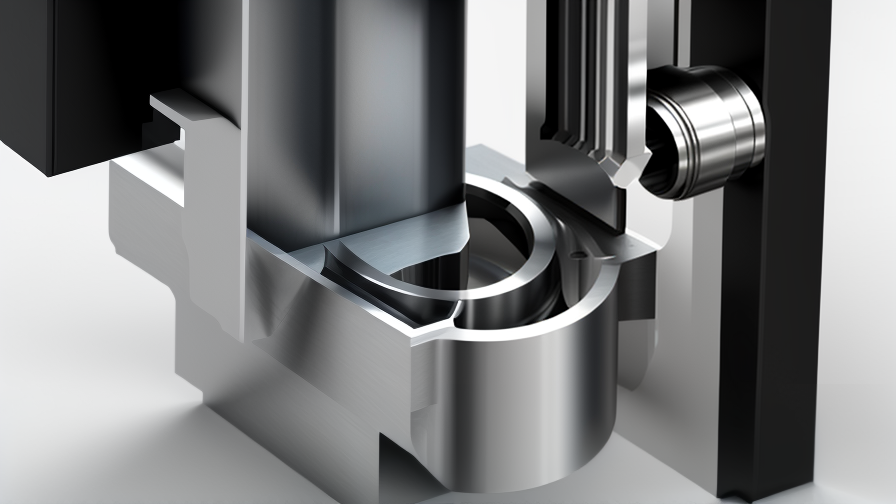
The Work Process and how to use cnc machine metal
The work process of using a CNC machine for metal involves several steps. First, a computer-aided design (CAD) file is created that contains the design and dimensions of the metal part to be produced. This file is then inputted into the CNC machine’s control software.
Next, the raw metal material is loaded onto the machine’s worktable and secured in place. The machine’s cutting tools are then programmed to follow the instructions from the CAD file, cutting and shaping the metal according to the design.
During the cutting process, the CNC machine moves the cutting tool along different axes (X, Y, and Z) to remove material and create the desired shape. The machine’s precision and accuracy allow for complex shapes and tight tolerances to be achieved.
After the cutting is completed, the metal part may undergo additional processes such as deburring, polishing, or surface treatment to improve its finish and quality.
To use a CNC machine for metal, the operator must have a good understanding of the machine’s operation and programming. This includes setting up the machine, loading the CAD file, and running the cutting program. The operator must also regularly monitor the machine to ensure it is functioning correctly and make any necessary adjustments.
Overall, using a CNC machine for metal involves precise planning, programming, and execution to produce high-quality metal parts efficiently and accurately.
Quality Testing Methods for cnc machine metal and how to control the quality
Quality testing methods for CNC machine metal involve various techniques to ensure that the final product meets the desired specifications and standards. Some of the common methods used are:
1. Dimensional accuracy: This involves measuring the dimensions of the machined metal components using precision tools such as calipers, micrometers, and coordinate measuring machines (CMMs). The measurements are compared to the specified tolerances to ensure the parts are within the required limits.
2. Surface roughness evaluation: The surface roughness of machined metal parts is examined using techniques like profilometers or roughness testers. This helps assess the quality of the surface finish and verifies if it meets the required standards.
3. Visual inspection: This involves visually examining the machined parts for any visible defects or inconsistencies such as cracks, dents, burrs, or deformities. It ensures that the parts have been manufactured without any apparent flaws.
4. Hardness testing: This method determines the hardness of the metal using techniques like Rockwell hardness testing, Brinell hardness testing, or Vickers hardness testing. It helps verify if the material’s hardness is within the desired range and confirms the quality of the metal.
To control the quality of CNC machine metal, several measures can be implemented:
1. Documented specifications: Clearly define and document the required specifications, including tolerances, surface finish, hardness, and other relevant parameters. This provides a reference for quality control during production.
2. Statistical process control (SPC): Implement SPC techniques such as control charts and process capability studies to monitor and control the machining process. This helps identify any deviations from the target values, enabling timely corrective measures.
3. Regular maintenance: Ensure that the CNC machine is properly maintained, calibrated, and serviced regularly. This prevents any issues in the machining process that could compromise the quality of the final products.
4. Operator training: Train the machine operators on proper machining techniques, quality standards, and inspection methods. Well-trained operators improve the chances of producing quality components and detecting potential issues.
5. Quality assurance checks: Regularly perform quality checks at various stages of the production process, including raw material inspection, in-process inspection, and final inspection. This ensures that any quality issues are identified early and corrected before reaching the final product.
By implementing these quality testing methods and control measures, manufacturers can ensure that CNC machine metal products meet the required standards and specifications, resulting in high-quality, reliable components.
cnc machine metal Sample Policy and Post-Purchase Considerations for cnc machine metal from China
Sample Policy:
When considering purchasing a CNC machine metal from China, it is recommended to request samples from potential suppliers. This allows buyers to evaluate the quality, precision, and performance of the machine before making a bulk purchase. The sample policy should be discussed with the supplier to ensure mutual understanding and agreement. Factors to consider in a sample policy may include the cost of samples, sample lead time, and any requirements for returning or keeping the samples.
Post-Purchase Considerations:
After purchasing a CNC machine metal from China, there are several important considerations for the buyer. Firstly, it is crucial to carefully inspect the machine upon arrival to ensure it is in good condition and functions properly. Any defects or damage should be reported to the supplier immediately.
Secondly, it is important to establish a regular maintenance schedule for the CNC machine metal. This includes routine cleaning, lubrication, and calibration to ensure optimal performance and longevity. The supplier may provide guidelines or recommendations for maintenance, which should be followed accordingly.
Furthermore, it is advisable for the buyer to maintain open communication with the supplier, especially in case of any concerns or issues that may arise with the machine. Promptly addressing such matters can help resolve any problems efficiently and prevent any negative impacts on production or operations.
Lastly, the buyer should consider any additional costs or requirements that may arise after purchasing the CNC machine metal. This may include installation, training, and technical support. Discussing these factors with the supplier beforehand can help the buyer prepare and budget accordingly.
In summary, requesting samples and having a clear sample policy is recommended when purchasing a CNC machine metal from China. Post-purchase considerations include inspecting the machine upon arrival, establishing a maintenance schedule, maintaining communication with the supplier, and considering any additional costs or requirements.
Sourcing cnc machine metal from China: Opportunities, Risks, and Key Players
China is a major hub for sourcing CNC machine metal due to its extensive manufacturing capabilities and cost-effective solutions. The country offers numerous opportunities for businesses looking to procure CNC machine metal, including a wide range of suppliers, competitive pricing, and advanced technological capabilities.
However, there are also risks associated with sourcing CNC machine metal from China, including quality control issues, intellectual property concerns, and language barriers. It is important for businesses to conduct thorough due diligence and work with reputable suppliers to mitigate these risks.
Key players in the CNC machine metal market in China include companies such as Haas Automation, DMG Mori, Amada, and Trumpf. These companies have established a strong presence in the market and offer a wide range of CNC machine metal products to cater to various needs and requirements.
Overall, sourcing CNC machine metal from China can be a lucrative opportunity for businesses looking to access cost-effective solutions and advanced technological capabilities. However, it is essential for businesses to carefully consider the risks and challenges associated with sourcing from China and work with reputable suppliers to ensure a successful procurement process.
How to find and select reliable cnc machine metal manufacturers in China,use google search manufacturers and suppliers
When looking for reliable CNC machine metal manufacturers in China, the first step is to conduct a Google search for manufacturers and suppliers. This will provide a list of potential companies that specialize in CNC machining services.
Next, carefully review the websites of these manufacturers to gather information about their capabilities, expertise, and experience. Look for testimonials, case studies, and customer reviews to assess their reputation and reliability.
Additionally, look for manufacturers that have certifications or memberships in industry organizations, as this can indicate a high level of professionalism and quality.
It is also important to reach out to potential manufacturers directly to ask about their processes, equipment, quality control measures, and pricing. Request quotes from multiple manufacturers to compare costs and services.
Lastly, ask for samples of their work or visit their facilities if possible to see their operations firsthand. By taking these steps, you can find and select a reliable CNC machine metal manufacturer in China that meets your specific requirements and standards.
How to check cnc machine metal manufacturers website reliable,use google chrome SEOquake check if ranking in top 10M
To verify the reliability of a CNC machine metal manufacturer’s website, one can use Google Chrome SEOquake to check if the website is ranking in the top 10 search results for relevant keywords. This can give an indication of the website’s credibility and authority in the industry.
Additionally, one can look for customer reviews, testimonials, and case studies on the website to see what others have to say about their experiences with the manufacturer. This can provide valuable insights into the quality of their products and services.
It is also important to check if the website has clear contact information, including a physical address, phone number, and email address. This can help ensure that the manufacturer is legitimate and can be contacted if needed.
Furthermore, looking for certification badges and industry affiliations on the website can also be a good indicator of the manufacturer’s credibility and commitment to quality.
Overall, by using a combination of these methods, one can determine if a CNC machine metal manufacturer’s website is reliable and trustworthy.
Top 10 cnc machine metal manufacturers in China with each 160 words introduce products,then use markdown create table compare
1. Haas Automation – Haas Automation is a renowned manufacturer of CNC machines for metal manufacturing in China. Their product line includes CNC vertical machining centers, CNC horizontal machining centers, CNC lathes, and rotary tables. Haas machines are known for their robust construction, high-performance capabilities, and user-friendly interface.
2. DMG Mori – DMG Mori offers a wide range of CNC metal machine tools, including CNC milling machines, turning centers, grinding machines, and additive manufacturing machines. Their products are recognized for their precision, durability, and advanced technological features.
3. Mazak – Mazak specializes in advanced CNC machinery for metal cutting, including vertical machining centers, horizontal machining centers, multi-tasking machines, and laser processing machines. Mazak machines are known for their high-speed capabilities, exceptional accuracy, and reliability.
4. Fanuc – Fanuc is a leading supplier of CNC systems, machines, and robots for metal manufacturing. Their product range includes CNC milling machines, turning machines, electric discharge machines, and wire-cut electric discharge machines. Fanuc machines are acclaimed for their precision, efficiency, and innovative automation features.
5. Doosan Machine Tools – Doosan Machine Tools offers a wide variety of CNC metal machines, including vertical machining centers, horizontal machining centers, multi-axis turning centers, and double column machining centers. Doosan machines are known for their high rigidity, rapid feed rates, and cutting-edge technology.
6. Okuma – Okuma provides an extensive range of CNC metal machine tools, including CNC lathes, machining centers, multitasking machines, and grinders. Okuma machines are recognized for their high accuracy, thermal stability, and excellent machining performance.
7. Tongtai Machine & Tool Co., Ltd. – Tongtai is a leading manufacturer of CNC metal machines, including vertical machining centers, horizontal machining centers, and turn-mill centers. Their machines feature high rigidity, precision, and advanced control systems.
8. Shenyang Machine Tool Co., Ltd. – Shenyang Machine Tool specializes in producing CNC metal machine tools, including vertical machining centers, horizontal machining centers, CNC lathes, and grinding machines. Their products are known for their stability, precision, and efficient performance.
9. SMTCL – SMTCL offers a wide range of CNC metal manufacturing machines, including vertical machining centers, horizontal machining centers, CNC lathes, and boring mills. SMTCL machines are celebrated for their high productivity, accuracy, and cost-effectiveness.
10. Chiron – Chiron manufactures high-performance CNC metal machine tools, including vertical machining centers, twin-spindle machining centers, and multi-axis turn-mill centers. Chiron machines are renowned for their speed, accuracy, and flexibility in metal manufacturing applications.
| Manufacturer | Specializations | Key Features |
|—————————-|———————————-|———————————————–|
| Haas Automation | CNC vertical machining centers, CNC horizontal machining centers, CNC lathes, rotary tables | Robust construction, high-performance, user-friendly interface |
| DMG Mori | CNC milling machines, turning centers, grinding machines, additive manufacturing | Precision, durability, advanced technology |
| Mazak | Vertical machining centers, horizontal machining centers, multi-tasking machines, laser processing | High-speed capabilities, exceptional accuracy, reliability |
| Fanuc | CNC milling machines, turning machines, electric discharge machines, wire-cut electric discharge machines | Precision, efficiency, innovative automation features |
| Doosan Machine Tools | Vertical machining centers, horizontal machining centers, multi-axis turning centers, double column machining centers | High rigidity, rapid feed rates, cutting-edge technology |
| Okuma | CNC lathes, machining centers, multitasking machines, grinders | High accuracy, thermal stability, excellent machining performance |
| Tongtai Machine & Tool | Vertical machining centers, horizontal machining centers, turn-mill centers | High rigidity, precision, advanced control systems |
| Shenyang Machine Tool | Vertical machining centers, horizontal machining centers, CNC lathes, grinding machines | Stability, precision, efficient performance |
| SMTCL | Vertical machining centers, horizontal machining centers, CNC lathes, boring mills | High productivity, accuracy, cost-effectiveness |
| Chiron | Vertical machining centers, twin-spindle machining centers, multi-axis turn-mill centers | Speed, accuracy, flexibility in metal manufacturing applications |
Background Research for cnc machine metal manufacturers Companies in China, use qcc.com archive.org importyeti.com
When looking for CNC machine metal manufacturers in China, qcc.com, archive.org, and importyeti.com are great resources to check for background research. These websites provide valuable information about companies and their reputation in the industry.
Qcc.com offers business information on companies in China, including their registration details, shareholders, and financial performance. This can give you an insight into the stability and credibility of a CNC machine metal manufacturer.
Archive.org is a useful tool for checking the history of a company’s website. By looking at past versions of their website, you can see how long they have been in business and how their online presence has evolved over time. This can be an indicator of the company’s experience and expertise in the industry.
Importyeti.com is a platform that provides data on import and export activities of companies. By checking the import records of a CNC machine metal manufacturer, you can get an idea of their production capacity and their experience in supplying products to international markets.
Overall, these websites can help you gather important information about CNC machine metal manufacturers in China before making a decision on which company to partner with. It is important to thoroughly research and evaluate potential manufacturers to ensure a successful partnership and high-quality products.
Leveraging Trade Shows and Expos for cnc machine metal Sourcing in China
Trade shows and expos are excellent platforms for sourcing CNC machine metal in China. These events provide an opportunity to meet with a large number of suppliers, compare products and prices, and establish relationships with potential partners. Here are some tips for leveraging trade shows and expos for sourcing CNC machine metal in China:
1. Research and plan ahead: Before attending a trade show or expo, research the exhibitor list and identify potential suppliers of CNC machine metal. Make a list of companies you want to visit and products you are interested in sourcing.
2. Network and establish contacts: Trade shows and expos are great opportunities to meet with suppliers face-to-face, discuss your needs, and establish relationships. Take the time to network with exhibitors, ask questions, and exchange contact information.
3. Compare products and prices: Visit booths of multiple suppliers to compare products, prices, and quality. Take notes and collect product samples or brochures for future reference.
4. Negotiate and finalize deals: If you find a supplier that meets your requirements, negotiate terms and finalize the deal at the trade show or expo. Be prepared to negotiate on price, quantity, delivery terms, and payment terms.
5. Follow up and maintain relationships: After the trade show or expo, follow up with suppliers to confirm orders, arrange shipment, and provide feedback. Maintain relationships with your suppliers to ensure smooth and successful transactions in the future.
Overall, trade shows and expos are valuable tools for sourcing CNC machine metal in China. By researching, networking, comparing products, negotiating deals, and maintaining relationships, you can find reliable suppliers and high-quality products for your business.
The Role of Agents and Sourcing Companies in Facilitating cnc machine metal Purchases from China
Agents and sourcing companies play a crucial role in facilitating CNC machine metal purchases from China. These entities act as intermediaries between buyers and suppliers, using their expertise and experience to ensure smooth transactions and successful outcomes.
One of the key roles of agents and sourcing companies is to identify suitable suppliers for CNC machine metal in China. With an extensive network and knowledge of the local market, they can connect buyers with trusted manufacturers and suppliers who meet their specific requirements. This saves buyers the time and effort of searching for potential suppliers themselves and mitigates the risks associated with dealing with unknown sources.
Agents and sourcing companies also aid in negotiating favorable prices and terms with Chinese suppliers. They have a deep understanding of market dynamics, including pricing trends, production costs, and the competitive landscape. Leveraging this knowledge, they can negotiate better deals on behalf of buyers, helping them secure competitive prices and favorable payment terms.
Furthermore, agents and sourcing companies oversee the production and quality control processes. They ensure that suppliers comply with the specified quality standards and delivery schedules. These entities conduct regular factory visits, perform inspections, and coordinate with suppliers to resolve any issues that may arise during production. Their involvement minimizes the risk of substandard products or delays, providing buyers with peace of mind and confidence in their purchase.
Additionally, agents and sourcing companies handle logistics and shipping arrangements. They coordinate with freight forwarders, arrange transportation, and handle all necessary documentation, including customs clearance. By managing these complex logistics processes, agents and sourcing companies ensure that CNC machine metal purchases from China are seamlessly delivered to buyers’ locations.
In conclusion, agents and sourcing companies serve as essential facilitators in the procurement of CNC machine metal from China. Their roles include identifying suitable suppliers, negotiating competitive prices, overseeing production and quality control, and managing logistics. Harnessing their expertise and local knowledge, buyers can streamline their purchasing processes and achieve successful outcomes in their CNC machine metal purchases from China.
Price Cost Research for cnc machine metal manufacturers Companies in China, use temu.com and 1688.com
When researching prices for CNC machine metal manufacturers in China, two popular websites to use are temu.com and 1688.com. These websites are known for their wide range of suppliers and competitive pricing for various products, including CNC machines for metal manufacturing.
On temu.com, you can find a variety of CNC machine metal manufacturers offering different types of machines at various price points. You can filter your search based on your specific requirements such as machine type, features, and price range to find the best match for your needs. Additionally, you can compare prices from different suppliers to ensure you are getting the best deal possible.
1688.com is another great resource for finding CNC machine metal manufacturers in China. The website is known for its extensive supplier network, making it easy to find a variety of options for CNC machines at competitive prices. You can also contact suppliers directly through the website to negotiate prices and terms for your purchase.
Overall, by using temu.com and 1688.com, you can efficiently research and compare prices for CNC machine metal manufacturers in China. This will help you find the best deal and supplier for your specific needs while ensuring quality and reliability in your purchase.
Shipping Cost for cnc machine metal import from China
Shipping costs for importing a CNC machine from China can vary depending on several factors such as the size and weight of the machine, the shipping method chosen, and the destination country. However, there are some general estimates to consider.
For smaller CNC machines that can be packed in wooden crates or pallets, air freight is a viable option. Air shipping is typically faster but can be more expensive. The approximate cost for air shipping a small CNC machine from China to various destinations can range from $500 to $2,500, depending on the size and weight of the machine.
For larger CNC machines, sea freight is usually the preferred option. Sea shipping is more cost-effective but takes longer. The cost of sea shipping a CNC machine from China can range from $1,000 to $10,000 or more, depending on factors like the size of the machine and the distance it needs to travel.
It’s important to note that these estimates are rough figures and can vary significantly. Additional charges may also apply, such as customs duties, taxes, and import fees. It’s advisable to consult with a freight forwarder or shipping agent who can provide more accurate and specific cost information based on your requirements and destination.
Lastly, it’s crucial to consider the importance of proper packaging to ensure the safety of the CNC machine during transit. Properly securing and protecting the machine can help minimize the risk of damage during shipping and reduce potential costs associated with repairs or replacements.
Compare China and Other cnc machine metal Markets: Products Quality and Price,Visible and Hidden Costs
China has emerged as a global leader in the manufacturing industry, including the market for CNC machine metal products. When comparing China to other CNC machine metal markets, several factors can be taken into consideration including product quality and price as well as visible and hidden costs.
Product quality is an important aspect to consider when comparing China to other markets. China has made significant advancements in its manufacturing capabilities and is capable of producing high-quality CNC machine metal products. However, it is worth noting that the quality of products can vary depending on the manufacturer. Other markets may also offer products of comparable quality, especially in countries with established manufacturing industries such as Germany, Japan, and the United States.
Price is another crucial factor when comparing China to other markets. China has long been known for its competitive pricing, offering CNC machine metal products at relatively lower costs compared to many other countries. This advantage can be attributed to China’s large workforce, lower labor costs, and the presence of a well-developed supply chain. However, as labor costs rise in China, this price advantage may diminish over time. Other markets may have higher manufacturing costs but can compete based on other factors such as quality, innovation, or specialized expertise.
Visible costs refer to the costs that are apparent during the purchasing process, such as the product price and shipping fees. China generally offers competitive visible costs due to its efficient supply chain and economies of scale. Other markets may also provide transparent pricing structures, particularly when it comes to high-value precision CNC machine metal products.
Hidden costs, on the other hand, refer to additional expenses that may arise during the manufacturing and delivery process. China’s hidden costs can include language barriers, intellectual property concerns, longer lead times for production, and potential quality control issues. These costs may vary across different manufacturers and can be minimized through proper due diligence and effective communication. In other markets, hidden costs may differ based on specific factors such as import/export regulations, logistics, or customization requirements.
In summary, China offers competitive product quality and pricing for CNC machine metal products, thanks to its advanced manufacturing capabilities and cost advantages. However, other markets with established manufacturing industries can also compete in terms of product quality and innovation. Visible costs in China are generally competitive, but hidden costs can arise due to factors like language barriers and intellectual property concerns. Other markets may have their own set of hidden costs based on specific circumstances. Overall, a thorough analysis of product quality, pricing, and visible and hidden costs is necessary when comparing China to other CNC machine metal markets.
Understanding Pricing and Payment Terms for cnc machine metal: A Comparative Guide to Get the Best Deal
When it comes to pricing and payment terms for CNC machine metal, there are several factors to consider to ensure that you are getting the best deal possible.
First and foremost, it is important to understand the pricing structure of the CNC machine metal supplier. Some suppliers may offer a fixed price per unit of metal, while others may have a variable pricing structure based on factors such as volume, complexity of the design, and material cost.
It is also important to consider the payment terms offered by the supplier. Some suppliers may require full payment upfront, while others may offer payment plans or financing options. It is important to assess your own financial situation and determine which payment terms are most feasible for your business.
Additionally, it is important to compare pricing and payment terms among multiple suppliers to ensure that you are getting the best deal. Request quotes from several suppliers and carefully review the pricing structure and payment terms offered by each. This will allow you to make an informed decision and choose the supplier that offers the best value for your money.
By understanding pricing and payment terms for CNC machine metal and comparing options among multiple suppliers, you can ensure that you are getting the best deal possible for your business.
Chinese Regulations and Industry Standards Certifications for cnc machine metal,Import Regulations and Customs for cnc machine metal from China
China has a comprehensive set of regulations and industry standards certifications for CNC machine metal. These regulations and certifications ensure that the CNC machine metal produced in China meets specific quality, safety, and environmental standards.
One of the key regulations is the Certification and Accreditation Administration of the People’s Republic of China (CNCA). The CNCA oversees the mandatory certification system for products, including CNC machine metal. This certification ensures that the product complies with Chinese national standards and technical regulations.
In addition to CNCA certification, there are several important industry standards certifications for CNC machine metal in China. The most commonly used certifications include the China Compulsory Certification (CCC), ISO 9001:2015 (Quality Management System), ISO 14001:2015 (Environmental Management System), and ISO 45001:2018 (Occupational Health and Safety Management System).
Importing CNC machine metal from China also requires compliance with import regulations and customs procedures. Importers should ensure that the product meets the specific regulations and standards of their destination country. They may need to provide documentation such as product specifications, test reports, and certificates of compliance.
Customs procedures for importing CNC machine metal from China involve several key steps. First, importers need to verify the classification and tariff codes for their product. They should then complete the necessary customs declaration forms and pay any applicable import duties or taxes. Additionally, some countries may require additional documentation, such as a bill of lading, packing list, or commercial invoice.
To ensure a smooth import process, it is advisable for importers to work with a reputable customs broker or freight forwarder who is familiar with the import regulations and customs procedures of both China and the destination country.
In conclusion, China has strict regulations and certifications for CNC machine metal, and importers need to adhere to import regulations and customs procedures when importing CNC machine metal from China. Compliance with these regulations and certifications ensures product quality, safety, and environmental standards are met.
Sustainability and Environmental Considerations in cnc machine metal Manufacturing
Sustainability is an increasingly important factor in the manufacturing industry, including CNC machine metal manufacturing. One key aspect of sustainability in this type of manufacturing is the reduction of waste. CNC machines are capable of producing highly precise parts, which can minimize material waste compared to traditional manufacturing methods. Additionally, strategies such as nesting parts together and optimizing tool paths can further reduce material waste.
Environmental considerations in CNC machine metal manufacturing also include the reduction of energy consumption. CNC machines can be programmed to operate more efficiently, reducing the amount of energy required to produce parts. Using energy-efficient equipment and technologies can also help minimize the environmental impact of manufacturing operations.
Another important aspect of sustainability in CNC machine metal manufacturing is the use of eco-friendly materials and processes. This can include using recycled metals, choosing suppliers that prioritize sustainability, and implementing recycling programs for metal scraps and waste materials.
Overall, sustainability and environmental considerations are essential in CNC machine metal manufacturing to minimize waste, reduce energy consumption, and promote the use of eco-friendly materials and processes. By incorporating these practices into manufacturing operations, companies can not only reduce their environmental impact but also improve their long-term sustainability and competitiveness in the market.
List The Evolution history of “cnc machine metal”
The evolution of CNC machine metal began in the late 1940s with the development of Numerical Control (NC) machines. These early machines were controlled by punch cards that dictated the movement of cutting tools.
In the 1970s, Computer Numerical Control (CNC) machines were introduced, which revolutionized the industry by using computer programs to control the movement of cutting tools. These machines were more precise and efficient than their NC counterparts.
Throughout the 1980s and 1990s, CNC technology continued to advance with the introduction of multi-axis machines, allowing for more complex and intricate metal cutting. The integration of CAD/CAM software further enhanced the capabilities of CNC machines, allowing for more intricate designs and faster production times.
In the early 2000s, advancements in robotics and automation led to the development of CNC machining centers, which further improved accuracy and productivity. These machines were capable of performing multiple operations in a single setup, reducing the need for manual labor and increasing efficiency.
Today, CNC machine metal technology continues to evolve with the introduction of 5-axis machines, which can move along five different axes simultaneously, allowing for even greater precision and complexity in metal cutting. Additionally, the integration of Internet of Things (IoT) technology has enabled real-time monitoring and data analysis, further enhancing the capabilities of CNC machines.
The Evolution and Market Trends in cnc machine metal Industry
The CNC machine metal industry has seen significant evolution over the years with advancements in technology and automation. The use of Computer Numerical Control (CNC) machines has revolutionized the manufacturing process by providing precise and efficient metal cutting and shaping capabilities.
One of the key trends in the CNC machine metal industry is the adoption of Industry 4.0 principles, which includes the integration of digital technologies such as Internet of Things (IoT), data analytics, and artificial intelligence. This has led to the development of smart CNC machines that can communicate and optimize their operations, leading to increased productivity and reduced downtime.
Another trend in the CNC machine metal industry is the shift towards additive manufacturing or 3D printing. This technology allows for the production of complex metal parts with minimal waste and faster turnaround times, making it ideal for prototyping and small-batch production.
Moreover, there is a growing demand for customized and personalized metal parts, driving the need for CNC machines that can handle a variety of materials and complex designs. This has led to the development of multi-axis CNC machines that offer greater flexibility and precision in machining operations.
Overall, the CNC machine metal industry is experiencing rapid technological advancements and market growth, driven by the need for efficient and cost-effective metal manufacturing solutions. Companies that can adapt to these trends and invest in the latest technologies will likely see success in this evolving industry.
Custom Private Labeling and Branding Opportunities with Chinese cnc machine metal Manufacturers
Chinese manufacturers of CNC machine metal offer a range of custom private labeling and branding opportunities for businesses looking to establish their own identity in the market. With expertise in CNC machining, these manufacturers can create high-quality metal parts or components, customizing them according to specific requirements and preferences.
Private labeling allows businesses to add their own branding elements, such as logos, colors, and designs, to the products. This ensures that the manufactured goods reflect the business’s unique identity and helps in building brand recognition and loyalty among customers. Chinese CNC machine metal manufacturers offer flexible customization options, allowing businesses to choose from various finishes, materials, and sizes.
By partnering with a Chinese manufacturer, businesses can take advantage of cost-effective production solutions while maintaining control over their brand. Chinese manufacturers offer competitive pricing due to their advanced production capabilities and cost-efficient operations. This allows businesses to stay competitive in today’s global market while ensuring quality and reliability.
Furthermore, Chinese manufacturers often have extensive experience in international trade, including exporting products worldwide. This makes them well-equipped to handle the logistics and shipping requirements of private-labeled products to different countries and markets.
In conclusion, collaborating with Chinese CNC machine metal manufacturers offers businesses exciting opportunities to create their own private-labeled products. These manufacturers provide custom branding options, cost-effective production solutions, and comprehensive export services. By leveraging their expertise, businesses can establish a distinct brand identity and gain a competitive edge in the market.
Tips for Procurement and Considerations when Purchasing cnc machine metal
1. Consider the type of material you will be working with: Make sure the CNC machine you are purchasing is suitable for the specific type of metal you will be machining. Some machines may be better suited for softer materials, while others are designed for harder metals.
2. Look for machines with a solid construction: Stability and durability are key factors when selecting a CNC machine for metal. Look for machines with a heavy-duty frame and sturdy components to ensure precision and longevity.
3. Evaluate the machine’s accuracy and precision: Accuracy is crucial when working with metal, so look for machines with high precision levels and powerful spindle motors. Features like linear guides and ball screws can also improve the overall accuracy of the machine.
4. Consider the machine’s speed and efficiency: Look for CNC machines that offer fast spindle speeds and rapid travel rates to optimize productivity. These features can help reduce cycle times and increase overall efficiency.
5. Check for compatibility with CAD/CAM software: Make sure the CNC machine you choose is compatible with the CAD/CAM software you plan to use. This will streamline the programming process and ensure seamless communication between the software and the machine.
6. Consider the size of the work envelope: The size of the work envelope will determine the maximum size of parts you can machine. Make sure the CNC machine you choose has a work envelope that can accommodate the size of the parts you typically work with.
7. Look for additional features and accessories: Consider additional features like automatic tool changers, coolant systems, and chip conveyors to improve efficiency and productivity. These optional accessories can make a significant difference in the overall performance of the machine.
8. Evaluate the reputation of the manufacturer: Choose a reputable manufacturer with a track record of producing high-quality CNC machines for metal. Read reviews, ask for references, and compare different brands to ensure you are getting a reliable and well-built machine.
FAQs on Sourcing and Manufacturing cnc machine metal in China
1. What are the benefits of sourcing cnc machine metal in China?
Sourcing cnc machine metal in China offers a cost-effective solution with competitive pricing, high-quality products, advanced technology, and a wide range of suppliers to choose from.
2. How can I find reliable manufacturers for cnc machine metal in China?
It is recommended to conduct thorough research, check supplier qualifications, visit manufacturing facilities, request samples, and ask for references from other customers to ensure the reliability of the manufacturer.
3. What are the common challenges when sourcing cnc machine metal in China?
Some common challenges include language barriers, cultural differences, quality control issues, intellectual property protection, and long lead times for production and shipping.
4. How can I ensure the quality of cnc machine metal manufactured in China?
To ensure quality, it is essential to have clear communication with the manufacturer, establish quality control processes, conduct inspections during production, and request third-party testing or certification when necessary.
5. What are the factors to consider when selecting a manufacturer for cnc machine metal in China?
Factors to consider include production capacity, expertise in cnc machining, reliability, cost-effectiveness, location, communication capabilities, and compliance with industry standards and regulations.
Why contact sourcifychina.com get free quota from reliable cnc machine metal suppliers?
Sourcifychina.com offers a convenient platform for businesses looking to source high-quality CNC machine metal suppliers in China. By contacting Sourcifychina.com, you can receive a free quota from reliable suppliers who have been pre-vetted for quality and reliability. This can save you valuable time and effort in finding the right supplier for your specific needs.
Working with reliable CNC machine metal suppliers is crucial for ensuring the quality and consistency of your products. By partnering with reputable suppliers through Sourcifychina.com, you can access a wide range of options and find the best fit for your business.
Additionally, receiving a free quota from these suppliers allows you to compare prices and services before making a decision. This can help you negotiate better terms and potentially save costs on your manufacturing process.
Overall, contacting Sourcifychina.com for a free quota from reliable CNC machine metal suppliers can streamline your sourcing process and help you find the best possible partner for your business needs. Don’t hesitate to reach out and take advantage of this valuable resource.