Introduce about cnc milling components guide,Qulity,Cost,Supplier,Certification,Market,Tips,FAQ
CNC milling is a precise machining process commonly used in the manufacturing industry. It involves the use of computer numerical control (CNC) machines that cut and shape materials into desired forms. This guide aims to introduce the key components, quality standards, costs, suppliers, certifications, market trends, and provide some tips and frequently asked questions (FAQs) related to CNC milling.
1. Components: CNC milling machines consist of various components, including the machine base, spindle, motor, tooling, worktable, and controls. These components work together to carry out the milling process.
2. Quality: The quality of CNC milling components depends on several factors, such as the material used, precision of machining, surface finish, and dimensional accuracy. High-quality components ensure consistent performance and durability.
3. Cost: The cost of CNC milling components may vary based on factors like material selection, complexity of design, volume of production, and supplier pricing. It is crucial to find a balance between cost and quality to achieve the desired outcome.
4. Supplier: Choosing the right supplier for CNC milling components is essential. Consider factors like their experience, reputation, manufacturing capabilities, quality control processes, and customer reviews before making a decision.
5. Certification: Look for suppliers that hold relevant certifications such as ISO 9001, ensuring they meet international standards for quality management systems. Certification provides assurance of consistent quality and reliable manufacturing processes.
6. Market: The CNC milling market is growing rapidly due to increasing demand for precision machining in various industries, including aerospace, automotive, medical, and electronics. Stay updated with market trends and innovations to make informed decisions.
7. Tips: When working with CNC milling components, consider aspects like material selection, part design optimization for manufacturability, tool path optimization, and fixture design. These factors can impact the efficiency and quality of the milling process.
8. FAQ: Some common questions regarding CNC milling components include queries related to material compatibility, tolerance requirements, surface finish options, turnaround time, and pricing. Addressing these FAQs can help in making informed decisions.
In summary, CNC milling components are vital for precise machining processes. Ensure quality, cost-effectiveness, and certification when choosing a supplier. Stay informed about market trends and follow tips and FAQs for improved outcomes in CNC milling projects.
Types of cnc milling components
CNC milling machines are widely used in various industries, such as manufacturing, automotive, aerospace, and medical, to produce complex parts with high precision and accuracy. These machines consist of several components that work together to facilitate the milling process. Here are some of the key components of a CNC milling machine:
1. Machine Bed: The machine bed provides a rigid and stable platform for supporting the components and workpiece during the milling process. It is typically made of cast iron or steel for strength and stability.
2. Spindle: The spindle is the main rotating component of the machine, responsible for holding and rotating the cutting tool. It is driven by a motor and can rotate at high speeds, allowing for precise cutting and shaping of the workpiece.
3. Tooling: CNC milling machines utilize various types of cutting tools, including end mills, ball mills, and drills, to perform different operations. These tools are typically made of high-speed steel (HSS) or carbide and can be easily replaced or changed using a tool changer.
4. Worktable: The worktable is a movable platform that holds the workpiece in place during the milling process. It can move in multiple axes (X, Y, and Z) to position the workpiece accurately for cutting and shaping.
5. Control Panel: The control panel houses the computer numerical control (CNC) system, which is the brain of the machine. The CNC system receives instructions from the operator or pre-programmed software and controls the movements and functions of the machine components.
6. Linear Guides: Linear guides, also known as linear bearings or slides, provide smooth and precise linear motion to the cutting tool, worktable, and other moving components. These guides are usually made of hardened steel or aluminum and are equipped with ball bearings or rollers for reduced friction.
7. Coolant System: To dissipate heat and lubricate the cutting tool, CNC milling machines often have a coolant system. This system supplies coolant (usually a liquid coolant or oil) to the cutting area, which helps in cooling the tool and removing chips and swarf.
In summary, CNC milling machines consist of several essential components, including the machine bed, spindle, tooling, worktable, control panel, linear guides, and coolant system. Each component plays a crucial role in facilitating precise and efficient milling operations.
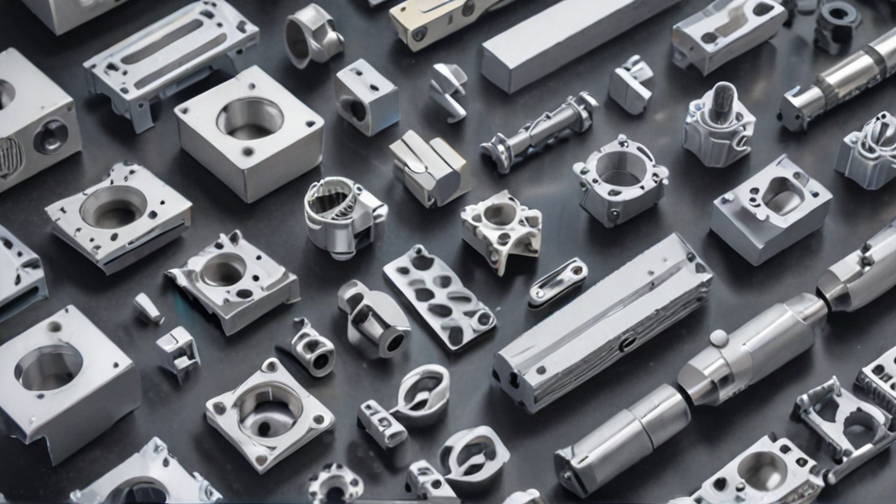
Pros and Cons of Using cnc milling components
CNC milling components offer several advantages and disadvantages that should be considered before deciding to use them in a manufacturing process.
Pros:
1. Precision: CNC milling components provide exceptional accuracy and precision, ensuring the production of high-quality and consistent parts. This level of precision is especially beneficial for complex or intricate designs.
2. Versatility: CNC milling can work with a wide range of materials, including metals, plastics, and composites. This versatility allows for the production of diverse parts and components.
3. Automation: CNC milling machines are automated, reducing the need for manual labor and human intervention. This automation leads to increased efficiency, improved productivity, and reduced labor costs.
4. Complex geometries: Using CNC milling, it is possible to produce parts with complex geometries that would be difficult or impossible to achieve with traditional machining methods. This is particularly advantageous for industries such as aerospace and automotive.
5. Faster production: CNC milling can produce parts at a faster rate compared to conventional machining methods. This speed can help meet production deadlines and reduce time-to-market.
Cons:
1. High initial cost: CNC milling machines can be expensive to purchase and set up, making them less accessible to small businesses or startups with limited capital.
2. Skilled operators: Operating CNC milling machines requires skilled personnel with specialized knowledge. Training and hiring qualified operators can be costly and time-consuming.
3. Maintenance and upkeep: CNC milling machines require regular maintenance and upkeep to ensure optimal performance and prevent breakdowns. This maintenance incurs additional costs and may result in production downtime.
4. Limited flexibility: CNC milling is best suited for producing large quantities of identical or similar parts. If there is a need for frequent design changes or customization, CNC milling may not be the most efficient solution.
5. Size limitations: CNC milling is generally limited in terms of the maximum size of the parts that can be produced. Oversized or large-scale components may require alternative manufacturing processes.
In conclusion, CNC milling components offer numerous benefits such as precision, versatility, automation, complex geometries, and faster production. However, their high initial cost, the need for skilled operators, maintenance requirements, limited flexibility, and size limitations should also be considered when deciding to implement them in a manufacturing process.
cnc milling components Reference Specifications (varies for different product)
CNC milling is a subtractive manufacturing process that utilizes computer numerical control (CNC) machine tools to remove material from a workpiece to create final components. The process involves using rotating cutting tools to precisely shape and cut the workpiece according to the desired specifications. The reference specifications for CNC milling components can vary depending on the specific product being manufactured.
In general, CNC milling components need to meet certain criteria to ensure optimal performance. These specifications include dimensional accuracy, surface finish, material properties, and tolerances. Dimensional accuracy refers to the ability of the component to meet the required size and shape specifications. Surface finish refers to the quality and smoothness of the surface texture of the milled component, while material properties define the physical and chemical characteristics of the material used for the component.
Tolerances are crucial in CNC milling components as they determine the allowable deviations from the desired specifications. Tight tolerances ensure that the milled components fit together accurately and function properly. The level of precision required in tolerances can vary depending on the application and the complexity of the component.
Additionally, the reference specifications for CNC milling components may also encompass specific requirements for features such as holes, grooves, threads, and chamfers. These features are critical for the assembly and functionality of the final product.
It is important to note that the reference specifications for CNC milling components can differ significantly depending on the industry, application, and customer requirements. For example, components for aerospace applications may have more stringent specifications compared to those used in general industrial applications.
Overall, CNC milling components reference specifications are essential guidelines that ensure the final product meets the necessary quality standards, functionality, and performance criteria. By adhering to these specifications, manufacturers can produce high-quality components that meet the unique needs of various industries and applications.
Applications of cnc milling components
CNC milling components find extensive applications in various industries due to their precision and versatility. Here are some key applications:
1. Aerospace Industry: CNC milling components are widely used in aerospace engineering for manufacturing complex parts like engine components, turbine blades, and aircraft structures. The ability to achieve high accuracy and repeatability is crucial in this industry.
2. Automotive Industry: CNC milling is utilized in the automotive sector for manufacturing engine blocks, cylinder heads, gearboxes, and suspension components. The consistent precision of CNC milling machines ensures the quality and interchangeability of parts.
3. Medical Industry: CNC milling is employed in the medical field for intricate manufacturing of prosthetics, implants, surgical instruments, and orthopedic devices. The reliability and precision of CNC milling contribute to the success of medical procedures.
4. Electronics Industry: CNC milling components are used for creating complex circuit boards and housings for electronic devices. The milling machines produce precise shapes and drill holes with accuracy, ensuring the quality and functionality of electronic products.
5. Mold-making Industry: CNC milling is crucial in the production of molds used in plastic injection molding or die casting processes. CNC milling machines are capable of accurately replicating intricate mold designs to produce high-quality components.
6. Defense Industry: CNC milling components are extensively utilized in the defense sector for manufacturing weapons, munitions, and military vehicle parts. CNC milling ensures the production of durable and reliable defense equipment.
7. Energy Industry: CNC milling finds application in the energy sector for manufacturing turbine components, electrical connectors, and renewable energy equipment. CNC milling allows for efficient production of parts with high levels of accuracy and performance.
8. Furniture and Design Industry: CNC milling components are used to create intricate and customized designs in the furniture and design field. CNC milling machines can sculpt and carve different materials, enabling the production of unique and precise designs.
In conclusion, CNC milling components have diverse applications in industries such as aerospace, automotive, medical, electronics, mold-making, defense, energy, and furniture and design. The accuracy, precision, and versatility of CNC milling machines make them indispensable in modern manufacturing processes.
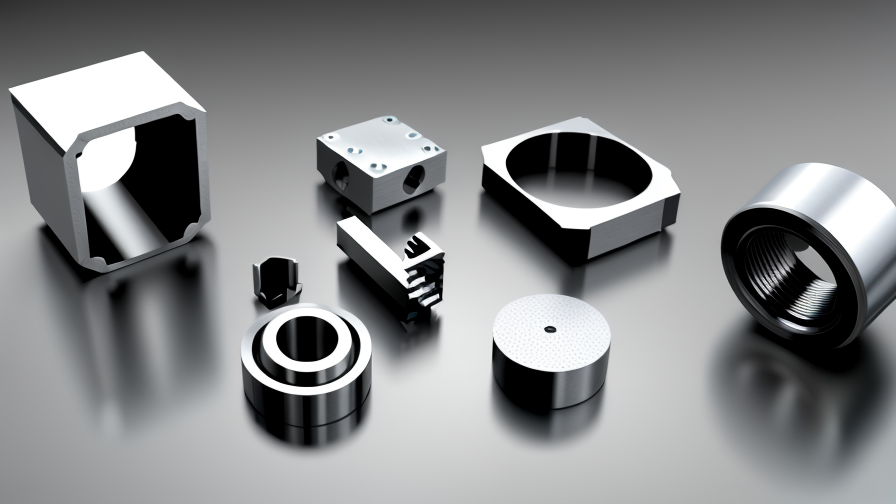
The Work Process and how to use cnc milling components
CNC milling is a manufacturing process that involves the use of computer numerical control (CNC) machines to remove material from a workpiece to create a desired shape or design. CNC milling components refer to the various parts and tools used in this process.
The work process of CNC milling typically involves several steps. Firstly, a CAD (Computer-Aided Design) model of the desired part or component is created. This digital model is then translated into a CNC program using CAM (Computer-Aided Manufacturing) software. The program contains instructions for the CNC machine on how to move and position the cutting tools to achieve the desired outcome.
Once the program is ready, the workpiece is securely clamped onto the CNC machine’s worktable or vice. The cutting tools, typically end mills or drills, are loaded into the machine’s spindle. The CNC program is then executed, and the machine begins to remove material from the workpiece according to the programmed instructions. The cutting tools move along multiple axes, guided by the CNC machine’s controls, to accurately shape the workpiece.
During the milling process, coolant or lubricant can be applied to the workpiece and cutting tools to reduce friction and heat. This helps to prolong tool life and improve surface finish. The milling process can produce complex shapes, including holes, slots, and intricate profiles, with high precision and repeatability.
To effectively use CNC milling components, it is important to understand the capabilities and limitations of the CNC machine being used. This includes knowledge of the machine’s axis movement, cutting speeds, and feed rates. Proper selection and setup of cutting tools are necessary for achieving desired results. Additionally, regularly monitoring and maintaining the machine and its components, such as replacing worn-out tools or checking for any mechanical issues, are essential for efficient and safe operation.
In conclusion, CNC milling is a versatile manufacturing process that can efficiently produce precise and complex components. By following the proper work process, including design, programming, setup, and tool selection, CNC milling components can be effectively utilized to create high-quality products.
Quality Testing Methods for cnc milling components and how to control the quality
Quality testing methods for CNC milling components involve a series of processes and techniques to ensure the precision, accuracy, and reliability of the final product. These methods can be categorized into two main types: dimensional testing and functional testing. By implementing these methods, companies can effectively control the quality of CNC milling components.
Dimensional testing focuses on evaluating the physical dimensions and tolerances of the components. This includes employing measurement tools such as micrometers, calipers, height gauges, and coordinate measuring machines (CMMs) to verify the component’s conformity to the specified dimensions. By conducting these tests, manufacturers can identify any variations or deviations from the desired measurements and take corrective actions accordingly.
Functional testing, on the other hand, ensures that the CNC milling components perform as intended under various operating conditions. This type of testing involves subjecting the components to different loads, stresses, or environmental conditions to assess their performance, durability, and functionality. For example, fatigue testing can be conducted to determine the component’s ability to withstand repeated cycles of stress. Similarly, hardness testing can be performed to evaluate the material’s resistance to indentation or deformation.
To control the quality of CNC milling components, manufacturers need to implement several measures. Firstly, they should establish stringent quality control procedures and standards that align with industry regulations and customer requirements. This includes defining the acceptable tolerances, conducting regular inspections throughout the production process, and implementing documentation and traceability systems to ensure accountability and transparency.
Furthermore, effective training programs for operators and quality assurance personnel should be implemented to ensure a clear understanding of testing procedures and product requirements. This will enable these personnel to detect anomalies, anomalies, and address them promptly. Also, continuous improvement initiatives, such as Six Sigma or Lean manufacturing techniques, can be employed to identify and eliminate defects, reduce variability, and enhance overall production efficiency and quality.
By utilizing these quality testing methods and implementing robust quality control measures, manufacturers can ensure that CNC milling components meet the highest standards and specifications. This guarantees customer satisfaction, reduces the risk of product failures or recalls, and enhances the reputation and competitiveness of the company in the market.
cnc milling components Sample Policy and Post-Purchase Considerations for cnc milling components from China
Sample Policy:
When purchasing CNC milling components from China, it is important to have a clear understanding of the supplier’s sample policy. This policy should outline the terms, conditions, and costs associated with obtaining samples of the CNC milling components before making a bulk purchase.
Ideally, the supplier should offer a reasonable sample policy that allows the buyer to evaluate the quality, performance, and compatibility of the CNC milling components. This may include providing free or discounted samples, or allowing for a refund or exchange if the samples do not meet the buyer’s expectations.
Post-Purchase Considerations:
After purchasing CNC milling components from China, there are several key post-purchase considerations to keep in mind:
1. Quality Control: Carefully inspect the received components for any defects or discrepancies in design, dimensions, or functionality. Conducting thorough quality control measures can help identify any issues before integrating the components into production machinery.
2. Compatibility: Ensure that the purchased CNC milling components are compatible with the intended machinery and the existing setup. This may require conducting compatibility tests and consulting the supplier for any necessary technical information.
3. Supplier Communication: Maintaining open and effective communication with the supplier is crucial. It allows for addressing any concerns, resolving issues, and clarifying any questions that may arise after the purchase. Additionally, maintaining a strong relationship with the supplier can facilitate future purchases and collaborations.
4. Warranty and after-sales service: Review the supplier’s warranty policy and available after-sales service options for the CNC milling components. A reliable supplier should provide a warranty period and clear terms for repairs, replacements, or refunds if any issues arise.
5. Feedback and reviews: Provide feedback to the supplier and consider leaving a review regarding the purchased CNC milling components. This can help other buyers make informed decisions and encourage the supplier to maintain or improve the quality of their products and services.
By understanding and implementing these post-purchase considerations, buyers can ensure a smooth integration of CNC milling components into their production process, minimize potential risks, and maintain a productive and satisfactory supplier relationship.
Sourcing cnc milling components from China: Opportunities, Risks, and Key Players
Sourcing CNC milling components from China presents numerous opportunities for businesses looking for cost-effective solutions and a wide range of options. China is known for its strong manufacturing capabilities, offering competitive pricing and high-quality products. The country has a thriving CNC milling industry with a large number of suppliers and manufacturers, making it an ideal destination for sourcing components.
One of the primary advantages of sourcing CNC milling components from China is the cost savings. Chinese manufacturers often offer lower prices due to the lower labor and production costs compared to other countries. This can result in significant savings for businesses, especially when sourcing large quantities of components.
Additionally, China has a vast network of suppliers and manufacturers specializing in CNC milling. This provides businesses with a wide selection of options, allowing them to find the right components to meet their specific requirements. Whether it is simple or complex machined parts, businesses can find reliable suppliers capable of producing high-quality components.
Despite the benefits, there are some risks involved in sourcing CNC milling components from China. One of the key challenges is ensuring product quality and adherence to specifications. Communication barriers and distance can sometimes lead to misunderstandings, leading to subpar components being produced. It is crucial to conduct thorough due diligence and quality checks to minimize these risks.
Moreover, businesses must also consider the potential for longer lead times and shipping delays when sourcing from China. It is vital to establish clear timelines and maintain regular communication with suppliers to ensure on-time delivery of components.
Some of the key players in the Chinese CNC milling components market include Jinan Paiwo Engineering Machinery Co., Ltd., Ningbo OEM Industry Manufacturer Ltd., Dongguan Longwang Hardware Co., Ltd., and Shenzhen HuaYueXin Precision Technology Co., Ltd. These companies have established themselves as reliable suppliers, known for their quality products and reasonable pricing.
In conclusion, sourcing CNC milling components from China offers opportunities for cost savings and a wide range of options. However, businesses should be aware of the risks associated with product quality and lead times. Conducting thorough due diligence and maintaining clear communication with suppliers are essential for successful sourcing from China.
How to find and select reliable cnc milling components manufacturers in China,use google search manufacturers and suppliers
When searching for reliable CNC milling components manufacturers in China, Google can be a useful tool. Follow these steps to find and select reliable manufacturers:
1. Use relevant keywords: Start by using specific keywords such as “CNC milling components manufacturers in China” or “reliable CNC milling suppliers in China.”
2. Refine the search: Go through the search results and scan for reliable websites and manufacturers. Consider factors such as the website’s design, professionalism, and the range of products they offer.
3. Verify authenticity: Once you shortlist a few manufacturers, conduct thorough research on each of them. Look for information about their experience, certifications, product quality, and customer reviews. Check if they have any partnerships or associations with trusted organizations in the industry.
4. Contact manufacturers: Reach out to the manufacturers directly to gather more information about their products, manufacturing processes, and quality control measures. Inquire about their customization options, lead times, and pricing. Quality manufacturers will typically respond promptly and provide detailed information.
5. Ask for samples: Request samples of CNC milling components from the manufacturers you are interested in. This will allow you to evaluate the quality of their products firsthand and ensure they meet your specific requirements.
6. Perform due diligence: Before making a final decision, perform due diligence by comparing prices, product quality, delivery times, and customer service among the shortlisted manufacturers. Consider factors such as the manufacturer’s reputation, reliability, and ability to meet your milling component requirements consistently.
7. Consider MOQ and customization options: Check if the manufacturers have minimum order quantity (MOQ) requirements that align with your needs. Additionally, inquire about their customization capabilities to ensure they can fulfill any specific requirements you may have.
8. Request references: Ask the shortlisted manufacturers for references from their existing clients. Contact these references to gather feedback on the manufacturer’s product quality, service, and reliability.
By following these steps, you can find and select reliable CNC milling components manufacturers in China that meet your specific requirements while ensuring high-quality products and services.
How to check cnc milling components manufacturers website reliable,use google chrome SEOquake check if ranking in top 10M
One way to check the reliability of a CNC milling components manufacturer’s website is to use Google Chrome with the SEOquake extension. This tool can help you assess the website’s ranking and popularity.
First, make sure you have Google Chrome installed on your device. Then, go to the Chrome Web Store and search for the SEOquake extension. Install the extension and activate it.
Once you have SEOquake set up, open Google Chrome and search for the manufacturer’s website by typing its name in the search bar. Look for the official website in the search results and click on it to visit the site.
With the website open, activate the SEOquake extension by clicking on its icon in your browser’s toolbar. A sidebar will appear displaying various metrics and information about the website.
One important metric to consider is the Alexa Rank, which indicates the website’s popularity and traffic. A rank below 10 million generally suggests the website has significant traffic and is more likely to be reliable. You can find the Alexa Rank in the SEOquake sidebar, under the “Alexa” tab.
Additionally, you can explore other SEOquake metrics like the number of indexed pages, the website’s age, social media presence, and more, to assess the manufacturer’s online credibility and visibility.
It’s important to note that while SEOquake can provide valuable insights into a website’s ranking and popularity, it shouldn’t be the only factor determining reliability. It’s also a good idea to consider the manufacturer’s reputation, customer reviews, certifications, and other relevant information.
In summary, using Google Chrome with the SEOquake extension can help you quickly assess a CNC milling components manufacturer’s website reliability by checking its ranking in the top 10 million websites.
Top 10 cnc milling components manufacturers in China with each 160 words introduce products,then use markdown create table compare
1. Haas Automation Inc.:
Haas Automation Inc. is a leading manufacturer of CNC milling components in China. They specialize in producing high-quality CNC mills, lathes, and machining centers. Their products are widely used in various industries and are known for their precision, reliability, and durability. Some of their popular products include the Haas Super Mini Mill, Haas VM Series Vertical Mills, and the Haas DS-30Y Dual-Spindle Turning Center.
2. Brother Industries Ltd.:
Brother Industries Ltd. is another prominent manufacturer of CNC milling components in China. They offer a wide range of CNC milling machines, including vertical machining centers and tapping centers. Their machines are known for their advanced features, high-speed operation, and excellent accuracy. Brother’s products are widely used in industries such as automotive, aerospace, and electronics.
3. Makino Milling Machine Co. Ltd.:
Makino Milling Machine Co. Ltd. is a globally recognized manufacturer of CNC milling components. They offer a diverse range of milling machines that cater to various industrial needs. Their products include vertical and horizontal machining centers, graphite machining centers, and 5-axis machining centers. Makino machines are renowned for their superior precision, rigidity, and cutting-edge technology.
4. DMG Mori Co. Ltd.:
DMG Mori Co. Ltd. is one of the largest manufacturers of CNC milling components in China. They specialize in producing high-performance milling machines, such as vertical and horizontal machining centers, hybrid additive manufacturing machines, and 5-axis milling machines. DMG Mori’s products are known for their exceptional quality, innovative design, and advanced control systems.
| Manufacturer | Popular Products | Features |
|—————————–|———————————————–|———————————————-|
| Haas Automation Inc. | Haas Super Mini Mill, VM Series Vertical Mills | Precision, reliability, durability |
| Brother Industries Ltd. | Vertical Machining Centers, Tapping Centers | Advanced features, high-speed operation |
| Makino Milling Machine Co. | Vertical Machining Centers, 5-Axis Machining | Superior precision, high rigidity, technology |
| DMG Mori Co. Ltd. | Vertical & Horizontal Machining Centers | High performance, advanced control systems |
5. Mazak Corporation:
Mazak Corporation is a globally renowned manufacturer of CNC milling components. They offer a wide range of advanced machining centers, including vertical and horizontal mills, multi-tasking machines, and 5-axis machining centers. Mazak machines are known for their exceptional productivity, versatility, and cutting-edge technology.
6. Okuma Corporation:
Okuma Corporation is a leading manufacturer of CNC milling components in China. They provide a comprehensive range of milling machines, including vertical and horizontal machining centers, double column machining centers, and 5-axis machining centers. Okuma machines are renowned for their high precision, stability, and advanced functionality.
7. SMTCL Intelligent Equipment Manufacturing Co. Ltd.:
SMTCL is a prominent manufacturer of CNC milling components known for their superior technology, reliability, and cost-effectiveness. They offer a wide range of milling machines that cater to various industrial applications. SMTCL machines are popular in industries such as automotive, aerospace, and energy.
8. Doosan Machine Tools:
Doosan Machine Tools is a globally recognized manufacturer of CNC milling components. They provide a diverse range of milling machines, including vertical and horizontal machining centers, 5-axis machining centers, and multitasking machines. Doosan machines are known for their excellent stability, high-speed operation, and advanced technology.
9. Kent Industrial (USA) Inc.:
Kent Industrial is a renowned manufacturer of CNC milling components known for their precision, durability, and performance. They offer a wide range of milling machines, including vertical and horizontal machining centers, double column machining centers, and 5-axis machines. Kent Industrial machines are widely used in industries such as automotive, mold making, and aerospace.
10. Shenyang Machine Tool Co. Ltd.:
Shenyang Machine Tool Co. Ltd. is a leading manufacturer of CNC milling components in China. They specialize in producing high-performance milling machines, including vertical and horizontal machining centers, gantry type machining centers, and 5-axis machining centers. Shenyang Machine Tool machines are known for their reliability, precision, and technological advancements.
Background Research for cnc milling components manufacturers Companies in China, use qcc.com archive.org importyeti.com
When it comes to CNC milling components manufacturers in China, there are several websites that provide valuable information and data. Two such websites include qcc.com and importyeti.com. Additionally, the archived version of these websites on archive.org can be used to access historical data.
qcc.com is a Chinese business database that provides information on millions of companies in China. It offers a comprehensive directory of manufacturers, including those involved in CNC milling components. The website includes details such as contact information, company profiles, product descriptions, and customer reviews. Users can search for specific companies or browse through industry categories to find potential CNC milling components manufacturers.
importyeti.com is another platform that provides insights into Chinese manufacturers. It focuses on import and export data, helping users identify which companies are involved in the CNC milling components trade. The website offers information on the export history, shipment details, and buyer information of specific companies. This data can be useful in assessing the reliability and capability of potential manufacturers.
Both qcc.com and importyeti.com can also be accessed through their archived versions on archive.org. This allows users to access historical data and compare the performance and track record of different manufacturers over time. It can help in evaluating the stability and consistency of a company’s business operations.
By utilizing these websites and their archived versions, researchers can gather relevant information about CNC milling components manufacturers in China. They can find companies with good track records and verified customer reviews, which can serve as a basis for further evaluation and potential business partnerships.
Leveraging Trade Shows and Expos for cnc milling components Sourcing in China
Trade shows and expos are valuable platforms for sourcing CNC milling components in China. These events offer the opportunity to directly engage with manufacturers, suppliers, and industry experts, ultimately streamlining the sourcing process.
Attending trade shows and expos specific to CNC milling components in China enables buyers to access a wide range of exhibitors in one location. These events gather numerous manufacturers, giving buyers the chance to compare products, negotiate prices, and evaluate the quality of the components. This face-to-face interaction fosters trust and creates lasting business relationships.
In addition to meeting suppliers, trade shows and expos provide insights into the latest trends and technologies in the CNC milling component industry. Exhibitors often showcase cutting-edge prototypes, innovative solutions, and upgraded machinery. By being present at these events, buyers can gain knowledge about emerging market developments, leading to informed procurement decisions.
Moreover, trade shows and expos facilitate networking with industry peers and experts. Attending seminars, workshops, and panel discussions allows buyers to stay updated about market trends, regulations, and best practices. Engaging in such events also provides an opportunity to gain insights from experienced professionals, who can offer advice on sourcing strategies, supplier assessment, and quality control measures.
To make the most out of trade shows and expos, it is essential to plan ahead. Researching the event schedule and exhibitor list in advance helps identify the most relevant events and suppliers. Buyers should also define their sourcing objectives and prepare a list of questions to ask potential suppliers. Bringing samples or technical drawings of the required CNC milling components can facilitate discussions and enable suppliers to provide accurate quotations.
In conclusion, leveraging trade shows and expos for CNC milling components sourcing in China offers numerous advantages. These events allow buyers to meet a variety of manufacturers, access the latest industry trends, and network with industry professionals. With careful planning and preparation, attending trade shows and expos can prove instrumental in finding reliable suppliers and securing high-quality CNC milling components.
The Role of Agents and Sourcing Companies in Facilitating cnc milling components Purchases from China
Agents and sourcing companies play a crucial role in facilitating CNC milling components purchases from China. These entities act as intermediaries between the buyer and the supplier, providing support, guidance, and expertise throughout the sourcing process.
One of the primary functions of agents and sourcing companies is to conduct supplier research and due diligence. They have access to vast networks and databases of reliable suppliers, helping buyers identify the most suitable ones for their specific requirements. This saves time and effort for the buyer, as they can avoid the tedious task of individually screening potential suppliers.
Agents and sourcing companies also assist in negotiation and contract management. They have experience in dealing with Chinese suppliers and are equipped with knowledge of industry standards and pricing. By leveraging their bargaining power and expertise, agents can negotiate favorable terms and conditions, including price, quality, delivery time, and payment terms. They ensure that all parties agree to a mutually beneficial agreement and oversee contract compliance.
Quality control is another critical aspect facilitated by agents and sourcing companies. They have in-depth knowledge of the CNC milling industry, know the required quality standards, and have experience with quality control processes. Agents conduct inspections and audits at various stages of production, ensuring that the components meet the specified requirements. This minimizes the risk of receiving defective or non-compliant parts.
Logistics coordination is also part of their responsibility. Agents and sourcing companies handle the transportation and shipping logistics, ensuring smooth and timely delivery of the purchased components. They are familiar with the export/import regulations, and they can minimize potential delays or complications.
Lastly, agents and sourcing companies act as a bridge between cultures and language barriers. They facilitate effective communication and understanding between buyers and suppliers, preventing misunderstandings and disputes that may arise due to language or cultural differences.
In summary, agents and sourcing companies simplify the process of purchasing CNC milling components from China. By conducting supplier research, negotiating contracts, ensuring quality control, coordinating logistics, and facilitating communication, these entities provide invaluable support to buyers, enabling them to make efficient and successful purchases.
Price Cost Research for cnc milling components manufacturers Companies in China, use temu.com and 1688.com
When conducting price cost research for CNC milling components manufacturers in China, two popular websites to explore are temu.com and 1688.com. These platforms offer a wide range of suppliers and products, making them ideal for comparing prices and finding the best deals.
Temu.com is a comprehensive platform that connects global buyers with Chinese suppliers. It provides an extensive database of CNC milling components manufacturers, allowing users to filter results based on their specific requirements. The platform also features a convenient inquiry system, where users can directly communicate with suppliers to negotiate prices and gather additional information.
1688.com, operated by Alibaba Group, is a leading wholesale marketplace in China. It offers a vast selection of CNC milling component manufacturers, catering to a wide range of industries. The website is available in Chinese, so it is recommended to use translation tools or seek assistance for non-Chinese speakers. Despite the language barrier, the platform’s extensive product listings and competitive prices make it worth exploring.
To maximize the efficiency of price cost research on these platforms, it is advisable to follow these steps:
1. Thoroughly define and document the specific CNC milling components required, including material specifications, tolerances, and quantities.
2. Utilize the search functions on both temu.com and 1688.com to find relevant suppliers. Pay attention to ratings, reviews, and transaction histories to gauge the reliability and credibility of the manufacturers.
3. Compare prices offered by different suppliers for the desired CNC milling components. Consider not only the unit price but also shipping costs and potential discounts for bulk orders.
4. Reach out to selected suppliers through the inquiry or messaging systems provided by the platforms. Seek clarifications, ask for more detailed quotations, and negotiate prices to achieve the best possible deals.
Overall, by utilizing temu.com and 1688.com, companies can efficiently conduct price cost research for CNC milling components manufacturers in China. With their comprehensive databases, user-friendly interfaces, and direct communication channels, these platforms facilitate the procurement process while ensuring competitive pricing.
Shipping Cost for cnc milling components import from China
The shipping cost for importing CNC milling components from China can vary depending on various factors such as the size, weight, quantity, and destination of the shipment, as well as the preferred mode of transportation.
If the components are small and lightweight, air freight may be the most suitable option. Air freight rates are typically calculated either by the actual weight or the volumetric weight of the shipment, whichever is higher. The volumetric weight is calculated based on the dimensions of the package. It is important to consider that air freight rates can be expensive, especially for large or heavy shipments.
Alternatively, sea freight may be a more cost-effective option for larger and heavier shipments. Sea freight rates are usually calculated based on the volume or weight of the cargo, as well as the distance between the origin and destination ports. Additional costs such as custom duties, taxes, and handling charges should also be taken into account.
To get an accurate estimate for the shipping cost, it is recommended to contact freight forwarders or shipping companies that specialize in international trade. They can provide specific rates based on the details of the shipment, such as the dimensions, weight, and destination.
In order to reduce shipping costs, it is advisable to consolidate multiple orders into one shipment whenever possible. This can help in achieving economies of scale and reduce handling charges. Furthermore, negotiating with the shipping company or freight forwarder for better rates or exploring different shipping options can also help in minimizing costs.
In summary, the shipping cost for importing CNC milling components from China can vary depending on factors such as size, weight, quantity, and destination. It is crucial to research and compare rates from different shipping companies or freight forwarders to find the most cost-effective option. Regularly reviewing and optimizing shipping methods can also help in reducing overall shipping costs.
Compare China and Other cnc milling components Markets: Products Quality and Price,Visible and Hidden Costs
China and other CNC milling component markets can be compared based on products quality and price, as well as visible and hidden costs.
In terms of product quality, China’s CNC milling components market has seen significant improvements in recent years. Chinese manufacturers have invested heavily in technology and machinery, enabling them to produce high-quality components that meet international standards. However, there is still a perception that products from China may not always meet the same level of quality as those from other markets, such as Europe or North America. This perception is slowly changing as China’s manufacturing capabilities continue to evolve.
Price is another aspect of comparison between China and other CNC milling component markets. China is often known for its competitive pricing, offering more affordable options compared to other markets. This lower cost is primarily due to China’s low labor and production costs, as well as economies of scale. As a result, many companies choose to source their CNC milling components from China to reduce costs and remain competitive in the global market.
Visible costs, such as the initial purchase price of CNC milling components from China, tend to be lower compared to other markets. However, hidden costs can also be a factor to consider. These hidden costs may include shipping expenses, import duties, and potential delays in delivery. Additionally, communication and language barriers may pose challenges when dealing with Chinese manufacturers. These hidden costs should be carefully evaluated to ensure a comprehensive understanding of the total cost of procurement.
Other markets, on the other hand, may have higher initial purchase prices for CNC milling components. However, their hidden costs might be lower due to proximity or better communication channels, resulting in faster delivery times and fewer language barriers. It is important to carefully consider these visible and hidden costs when comparing China and other markets.
In conclusion, China’s CNC milling components market has made significant strides in product quality, offering competitive pricing. However, careful consideration should be given to both visible and hidden costs, including shipping expenses, import duties, potential delivery delays, and communication barriers. Comparisons with other markets should be made based on individual business needs and requirements to make an informed decision.
Understanding Pricing and Payment Terms for cnc milling components: A Comparative Guide to Get the Best Deal
When it comes to pricing and payment terms for CNC milling components, it is crucial to understand the factors that influence the costs and negotiate for the best deal. By comparing various suppliers, you can ensure that you get the most competitive price for your required components. Here is a comparative guide to help you navigate pricing and payment terms effectively:
1. Request for Quotes (RFQs): Begin by requesting quotes from multiple suppliers, providing detailed specifications of the CNC milling components you need. This allows you to compare the prices offered by different suppliers for the same components, facilitating a more informed decision-making process.
2. Volume and Frequency: Consider the volume and frequency of your order. Typically, suppliers offer discounted prices for larger orders or for customers who place regular orders. You can negotiate pricing based on your order volume to secure a better deal.
3. Quality Assurance: While price is important, never compromise on the quality of CNC milling components. Ensure that the suppliers can provide the desired level of quality and reliability, as subpar components may result in production delays or malfunctioning final products. Compare suppliers based on their track record and customer reviews.
4. Payment Terms: Discuss payment terms with potential suppliers. Some may require full payment upfront, while others may be open to partial payments or payment upon delivery. Negotiate terms that align with your budget and cash flow requirements. Additionally, inquire about any available discounts for early or bulk payments.
5. Delivery Time: Evaluate suppliers based on their estimated delivery time for the CNC milling components. Consider lead times and production capacities to ensure that the components will be delivered within your required timeframe. Price negotiations can also be influenced by the urgency of your order.
6. Additional Costs: Inquire about any additional costs that may affect the overall pricing, such as packaging, shipping, or import fees. These costs can vary significantly between suppliers and should be factored into your comparative analysis.
7. Payment Methods: Lastly, discuss the available payment methods with potential suppliers. Determine if they accept credit cards, bank transfers, or other payment options that align with your preferences and capabilities.
By following this comparative guide, you can ensure that you secure the best deal for your CNC milling components without compromising on quality. Remember to thoroughly review the terms and conditions before finalizing any agreement, and maintain open communication with the supplier throughout the process to address any concerns or negotiate further if needed.
Chinese Regulations and Industry Standards Certifications for cnc milling components,Import Regulations and Customs for cnc milling components from China
In China, the regulations and industry standards certifications for CNC milling components are important to ensure product quality, safety, and compliance with both national and international standards. The following certifications are commonly required for CNC milling components:
1. ISO 9001: This certification demonstrates that a company has implemented a quality management system to consistently provide products that meet customer and regulatory requirements.
2. ISO 14001: It indicates that a company has established an environmental management system to minimize the negative impact of its operations on the environment.
3. CE Marking: As a mandatory conformity mark for certain products sold within the European Economic Area, it demonstrates compliance with the relevant European Union legislation.
4. RoHS: This certification ensures that the components are compliant with the Restriction of Hazardous Substances directive, restricting the use of certain hazardous substances in electrical and electronic equipment.
5. UL Mark: UL certification ensures that the components have been tested and meet specific safety standards issued by Underwriters Laboratories.
When importing CNC milling components from China, it is crucial to comply with import regulations and customs procedures. Some key aspects to consider include:
1. Customs Declarations: Accurate and complete documentation, including invoices, packing lists, and shipping documents, must be provided to customs authorities.
2. Import Duties and Taxes: Depending on the country of import, applicable import duties and taxes must be paid. It is advisable to consult with local customs authorities or import/export professionals to determine the specific charges.
3. Import Restrictions: Certain countries may have import restrictions or require additional certifications/permits, especially for sensitive industries or products. It is important to consult relevant government agencies for any restrictions or requirements.
4. Customs Clearance: Goods may need to undergo customs inspections, including physical checks, to ensure compliance with regulations and document accuracy.
5. Transportation and Logistics: Choosing a reliable and experienced freight forwarder or shipping agent can help navigate complex import procedures and ensure timely delivery.
It is essential to stay updated with the latest regulations, standards, and customs procedures to ensure a smooth and compliant import process for CNC milling components from China.
Sustainability and Environmental Considerations in cnc milling components Manufacturing
Sustainability and environmental considerations in CNC milling components manufacturing are essential to minimize the industry’s ecological footprint and promote a more eco-friendly approach to production. Implementing these considerations involves various practices that can significantly reduce waste, energy consumption, and environmental impact.
One significant aspect is material selection. Choosing sustainable materials, such as recycled or responsibly sourced metals, can lower the environmental impact of CNC milling. Additionally, selecting materials that are more lightweight can reduce energy consumption during machining and transportation.
The efficient use of resources is another crucial factor. Implementing processes to optimize material usage, such as minimizing scrap and utilizing all parts of the raw material, can help reduce waste. This can be achieved through improved cutting strategies, more precise tool paths, and enhanced machining technologies.
Proper waste management and recycling practices should also be implemented to handle any waste generated during CNC milling. This can involve segregating different waste streams, such as metal scraps or spent cutting fluids, and ensuring they are appropriately recycled or disposed of to prevent environmental pollution.
Energy efficiency is another critical consideration. Implementing energy-saving practices like using high-efficiency CNC machines, optimizing machining parameters, and employing energy management systems can help reduce energy consumption during manufacturing processes.
Furthermore, the use of environmentally friendly cutting fluids should be considered. These fluids, such as vegetable-based or water-based alternatives, can minimize the use of hazardous chemicals and reduce the overall environmental impact.
Promoting a circular economy approach is also beneficial. Designing parts and components for easy repair, maintenance, and recycling can extend their lifespan, reduce the need for new production, and minimize waste generation.
Lastly, implementing proper environmental certifications and standards, such as ISO 14001, can ensure that the CNC milling components manufacturing process complies with environmental regulations and continuously improves its sustainability performance.
By integrating these sustainability and environmental considerations into CNC milling components manufacturing, companies can contribute to a more sustainable and responsible industry, minimize their ecological footprint, and meet the increasing demand for environmentally friendly products.
List The Evolution history of “cnc milling components”
CNC milling components have come a long way since their inception. The evolution of these components can be traced back to the mid-20th century when the first computer numerical control (CNC) machines were developed. These machines revolutionized the manufacturing industry by allowing for automated and precise machining processes.
In the early days, the primary component of CNC milling machines was the machine tool itself. These machines were large, bulky, and operated using punched paper tapes containing the instructions for the machining process. Over time, the machine tools became more advanced and were equipped with electric motors, allowing for greater precision and speed.
As computers became more accessible and powerful, the evolution of CNC milling components took a significant leap forward. The introduction of computer-aided design (CAD) and computer-aided manufacturing (CAM) software enabled engineers to create complex 3D models and generate tool paths for CNC machines. This advancement streamlined the manufacturing process, reducing errors and increasing productivity.
In the late 1980s and early 1990s, the development of faster and more powerful microprocessors led to the emergence of what is known as the second generation of CNC milling components. These components featured improved control systems, enhanced user interfaces, and expanded capabilities. Additionally, the introduction of servo-controlled axes and linear encoders resulted in higher accuracy and precision in milling operations.
The third generation of CNC milling components emerged in the late 1990s and early 2000s. This period witnessed significant advancements in communication technology and network integration. CNC machines could now be connected to local area networks (LANs) and communicate with other machines for data sharing and coordinated manufacturing processes.
Recent years have seen the rise of fourth-generation CNC milling components, characterized by the integration of Internet of Things (IoT) technology. CNC machines now have sensors that collect real-time data, allowing for predictive maintenance, optimization of machining parameters, and remote monitoring. These advancements have contributed to increased efficiency, reduced downtime, and improved overall productivity.
In conclusion, the evolution of CNC milling components has been driven by advancements in computer technology, software development, precision engineering, and network integration. From the early days of punched paper tapes to today’s IoT-enabled machines, CNC milling components have transformed the manufacturing industry, enabling faster, more precise, and automated machining processes.
The Evolution and Market Trends in cnc milling components Industry
The CNC milling components industry has experienced significant evolution and market trends over the years. CNC milling, also known as computer numerical control milling, is a machining process in which computerized controls and programming are used to automate the milling process.
One of the major evolutions in the CNC milling components industry is the advancement in technology. With the advent of computerized designs and programming, the precision and accuracy of milling components have improved significantly. CNC machines now have the capability to produce complex and intricate components with higher efficiency and speed. This evolution has led to increased productivity and reduced manufacturing costs.
Another evolution in the industry is the integration of automation and robotics. CNC milling machines can now be seamlessly integrated with robots and automated systems for loading and unloading components, reducing human intervention and increasing process efficiency. This automation also improves workplace safety by reducing the risk of human errors or accidents.
In terms of market trends, there is a growing demand for CNC milling components in various sectors, including aerospace, automotive, electronics, and medical industries. As these industries evolve and require more complex and precise components, the demand for CNC milling solutions continues to grow.
Additionally, there is a shift towards miniaturization in the industry, with the need for smaller and lighter components. CNC milling machines are now capable of producing micro-components with high precision. This trend is driven by the increasing demand for compact and lightweight products in industries such as electronics and medical devices.
Furthermore, sustainability and eco-friendly manufacturing practices are becoming more important in the CNC milling components industry. Manufacturers are adopting energy-efficient machines, recycling and waste reduction practices, and using environmentally friendly materials. This trend is driven by both regulatory requirements and consumer demand for sustainable products.
In conclusion, the CNC milling components industry has evolved significantly with advancements in technology, automation, and robotics. The market trends reflect the growing demand for precision, miniaturization, and sustainability in various industries. As technology continues to advance, we can expect further improvements in CNC milling processes and products.
Custom Private Labeling and Branding Opportunities with Chinese cnc milling components Manufacturers
Chinese CNC milling components manufacturers offer custom private labeling and branding opportunities to businesses. With their advanced manufacturing capabilities and cost-effective production processes, these manufacturers can produce high-quality components according to specific requirements.
Custom private labeling allows businesses to have their brand name, logo, and other identifying details printed or engraved on the components. This offers a great advantage as it helps in creating brand recognition and enhancing brand image. It also provides a professional and customized look to the products, which can attract more customers and increase sales.
Branding opportunities with Chinese CNC milling components manufacturers provide businesses with the advantage of customization. They can work closely with the manufacturers to design components that align with their brand identity. This includes selecting materials, finishes, and dimensions that reflect the business’s values and aesthetic preferences.
Chinese CNC milling components manufacturers have a vast range of capabilities, including precision machining, surface treatment, and assembly services. This ensures that businesses can customize their components to meet specific functional requirements. Whether it is a complex design or a unique shape, these manufacturers have the expertise to produce components that match the desired specifications.
Furthermore, working with Chinese manufacturers for private labeling and branding opportunities offers cost advantages. China is known for its competitive pricing and efficient manufacturing processes. By leveraging these advantages, businesses can obtain high-quality components at a lower cost, resulting in increased profitability.
In conclusion, Chinese CNC milling components manufacturers provide custom private labeling and branding opportunities for businesses. This allows businesses to enhance brand recognition, customize their products, and take advantage of cost-effective manufacturing processes. By partnering with these manufacturers, businesses can establish a strong brand presence in the market and cater to the unique needs of their customers.
Tips for Procurement and Considerations when Purchasing cnc milling components
When purchasing CNC milling components, there are several important considerations that should be taken into account to ensure a successful procurement process. Here are some valuable tips and considerations:
1. Define your requirements: Clearly identify your specific needs and requirements before starting the procurement process. Consider factors such as the size and specifications of the components needed, as well as any special features or capabilities required.
2. Quality assurance: Ensure that the supplier can provide high-quality components that meet your standards. Look for certifications or quality management systems in place to guarantee consistent quality.
3. Supplier reliability: Evaluate the supplier’s reputation and reliability. Check for customer feedback and reviews to ensure that they have a track record of delivering on time and providing excellent customer service.
4. Price competitiveness: Compare prices from multiple suppliers to ensure you are getting the best value for your money. However, be cautious of significantly lower prices, as they may indicate a compromise in quality.
5. Compatibility and integration: Ensure that the CNC milling components you purchase are compatible with your existing machinery or systems. Consider factors such as the software, power requirements, and mounting compatibility to avoid any compatibility issues.
6. Delivery time: Inquire about the lead time for delivery. This is crucial to ensure that the components arrive within your required timeframe and do not cause any delays in your production process.
7. After-sales support: Assess the level of after-sales support provided by the supplier. This includes warranty coverage, technical assistance, and spare parts availability.
8. Environmental considerations: Look for suppliers who prioritize sustainability and environmental responsibility. This includes using eco-friendly materials, adhering to environmental regulations, and having proper waste management practices in place.
9. Customization options: If you require specific modifications or customization for your CNC milling components, ensure that the supplier can accommodate your needs and has the necessary expertise.
10. Long-term relationship: Consider the potential for a long-term relationship with the supplier. A trusted and reliable supplier can provide ongoing support and be a valuable partner in your future procurement needs.
By considering these tips and factors, you can ensure a successful procurement process when purchasing CNC milling components.
FAQs on Sourcing and Manufacturing cnc milling components in China
1. Why should I consider sourcing and manufacturing CNC milling components in China?
China has become a prominent manufacturing hub due to its competitive pricing, vast production capabilities, and skilled labor force. The country’s CNC milling industry offers high-quality components at relatively lower costs, making it an attractive option for businesses worldwide.
2. How can I find reliable suppliers for CNC milling components in China?
To find reliable suppliers, you can consider various avenues. Online platforms like Alibaba, Global Sources, and Made-in-China provide access to a wide range of suppliers. Conduct thorough research by checking their certifications, customer reviews, and visiting their factories if possible. It is also beneficial to engage a sourcing agent or company with expertise in China’s manufacturing industry to help identify trustworthy suppliers.
3. Can I trust the quality of CNC milling components produced in China?
While there are both good and bad suppliers, China possesses a considerable number of reputable manufacturers that produce high-quality CNC milling components. To ensure quality, conduct thorough due diligence, request manufacturing samples, and perform quality inspections before finalizing any manufacturing agreement.
4. How long does it take to manufacture CNC milling components in China?
The manufacturing timeline depends on factors like component complexity, order quantity, production capacity, and supplier responsiveness. On average, it may take anywhere from a few weeks to several months. Communication and clear production timelines with suppliers are crucial to achieving timely delivery.
5. Are there any language or cultural barriers when sourcing and manufacturing in China?
Language barriers exist, primarily if you have limited proficiency in Mandarin or if suppliers have limited English skills. However, many Chinese manufacturers and sourcing agents have English-speaking staff to assist in overcoming language obstacles. Cultural differences, such as business etiquette and negotiation styles, also exist but can be managed effectively through open communication and mutual understanding.
6. How can I ensure the protection of intellectual property rights (IPR) when sourcing from China?
Protecting intellectual property rights is crucial when sourcing from China. To ensure IPR safety, consider applying for patents, trademarks, or copyrights in China and your home country. Have clear contracts and agreements in place that include confidentiality clauses. Working with reputable manufacturers and maintaining a good business relationship with them can also help strengthen IP protection.
In summary, sourcing and manufacturing CNC milling components in China offer cost advantages and access to skilled labor. By conducting proper due diligence, partnering with reliable suppliers, and understanding cultural differences, businesses can successfully leverage China’s manufacturing capabilities while ensuring product quality and protecting their intellectual property rights.
Why contact sourcifychina.com get free quota from reliable cnc milling components suppliers?
Sourcifychina.com, a platform that connects global buyers with suppliers in China, offers a free quota from reliable CNC milling components suppliers for a few reasons.
Firstly, by providing a free quota, sourcifychina.com aims to attract more customers and establish itself as a preferred platform for sourcing CNC milling components. Offering a free quota demonstrates their commitment to providing value to potential buyers.
Secondly, sourcifychina.com understands the importance of reliable suppliers in the manufacturing industry. By partnering with reliable CNC milling components suppliers, they can assure their customers of the quality and credibility of the products they source. This increases buyer confidence, leading to more business transactions.
Moreover, sourcifychina.com benefits from this collaboration with suppliers as it helps them expand their supplier network and enhance their reputation as a trusted platform for sourcing high-quality components. Building strong relationships with reliable suppliers is crucial for their long-term success in the industry.
Additionally, offering a free quota allows sourcifychina.com to showcase their sourcing capabilities and expertise. By providing this service, they can demonstrate their proficiency in identifying suitable suppliers for specific requirements. This enhances customer satisfaction and encourages buyers to use their services for future sourcing needs.
In summary, sourcifychina.com offers a free quota from reliable CNC milling components suppliers to attract customers, enhance their reputation, expand their supplier network, and demonstrate their sourcing expertise. This initiative serves as a value-added service that benefits both buyers and suppliers, fostering mutual growth and success.