Introduce about cnc mills and lathes guide,Qulity,Cost,Supplier,Certification,Market,Tips,FAQ
CNC mills and lathes are advanced machining tools used in manufacturing processes to shape and create precise components. These machines combine computer numerical control (CNC) technology with the functions of conventional mills and lathes, allowing for efficient and accurate production.
When it comes to quality, CNC mills and lathes offer exceptional precision and repeatability. The automated nature of these machines ensures consistent performance, reducing errors and enhancing productivity. These tools are capable of producing intricate designs and complex shapes with minimal human intervention, resulting in high-quality finished products.
In terms of cost, CNC mills and lathes tend to be higher-priced compared to conventional machining tools. However, their long-term cost benefits outweigh their initial investment. The efficiency and accuracy of CNC machines translate into reduced material waste, shorter production times, and lower labor costs, making them cost-effective in the long run.
Finding reliable suppliers for CNC mills and lathes is crucial to ensure the quality and effectiveness of these machines. It is advisable to select suppliers with a strong reputation in the industry, preferably those with extensive experience and positive customer reviews. Additionally, considering suppliers who offer comprehensive after-sales support and warranty options can be beneficial.
Certification is an essential factor to consider when purchasing CNC mills and lathes. Look for suppliers that adhere to international quality standards, such as ISO certification. This certification ensures that the supplier follows strict quality control measures in manufacturing their machines, guaranteeing their reliability and performance.
The market for CNC mills and lathes is growing steadily, driven by the increasing demand for precision machining in various industries, including aerospace, automotive, and medical. As technology advances, the market is expected to witness further growth, with constant improvements and innovations in CNC machine capabilities.
Tips for optimizing CNC mills and lathes’ performance include proper machine maintenance, regular calibration, and effective programming techniques. Routine maintenance prevents breakdowns and extends the machine’s lifespan. Calibration ensures accurate measurements and precise machining. Additionally, learning and implementing efficient programming techniques can enhance productivity and reduce production time.
Frequently Asked Questions (FAQ) about CNC mills and lathes may include queries regarding machine capabilities, software compatibility, training requirements, and pricing. By addressing these questions upfront, potential buyers can make informed decisions when selecting the most suitable CNC mill or lathe for their specific needs.
In conclusion, CNC mills and lathes are cost-effective, high-quality machining tools that incorporate advanced automation and precision. Buyers should consider suppliers with appropriate certifications and positive market reputation. With proper maintenance and programming techniques, these machines can significantly enhance manufacturing efficiency and productivity.
Types of cnc mills and lathes
CNC mills and lathes are machines used in the manufacturing industry to shape and cut various materials, such as metal, plastic, and wood, with precision and accuracy. They are essential for producing a wide range of products, from small components to large-scale structures. There are several types of CNC mills and lathes, each with its own unique capabilities and advantages.
One of the most common types of CNC mill is the vertical machining center (VMC). VMCs have a vertical spindle that moves along the Z-axis, while the workpiece remains stationary. This type of mill is suitable for applications that require drilling, tapping, and milling operations on flat or box-shaped workpieces. VMCs offer high-speed cutting capabilities, making them ideal for producing intricate parts with complex geometries.
Another type of CNC mill is the horizontal machining center (HMC), which has a horizontally oriented spindle and a rotating table for holding the workpiece. HMCs are typically used for heavy-duty machining tasks, such as milling large and heavy parts. They are known for their exceptional cutting power and stability, making them popular in industries like aerospace and automotive.
CNC lathes, on the other hand, are designed for cylindrical workpieces and perform turning operations. One common type of CNC lathe is the 2-axis lathe, which can perform simple operations like facing, drilling, and turning. These lathes are commonly used for small to medium-sized cylindrical parts, such as shafts and bolts.
More advanced CNC lathes include the multi-axis lathe and the Swiss-style lathe. Multi-axis lathes have additional axes of movement, enabling them to perform complex operations like milling, drilling, and tapping on the workpiece. They are ideal for producing highly intricate parts with tight tolerances. Swiss-style lathes, on the other hand, have a sliding headstock and a guide bushing that ensures high precision and stability during the cutting process. These lathes are commonly used in the production of small, high-precision parts like medical devices and electronics.
In summary, the different types of CNC mills and lathes offer a range of capabilities suited to specific machining needs. Whether it’s a VMC or HMC for milling operations, or a 2-axis lathe, multi-axis lathe, or Swiss-style lathe for turning operations, CNC machines play a crucial role in modern manufacturing processes, providing increased efficiency, accuracy, and versatility.
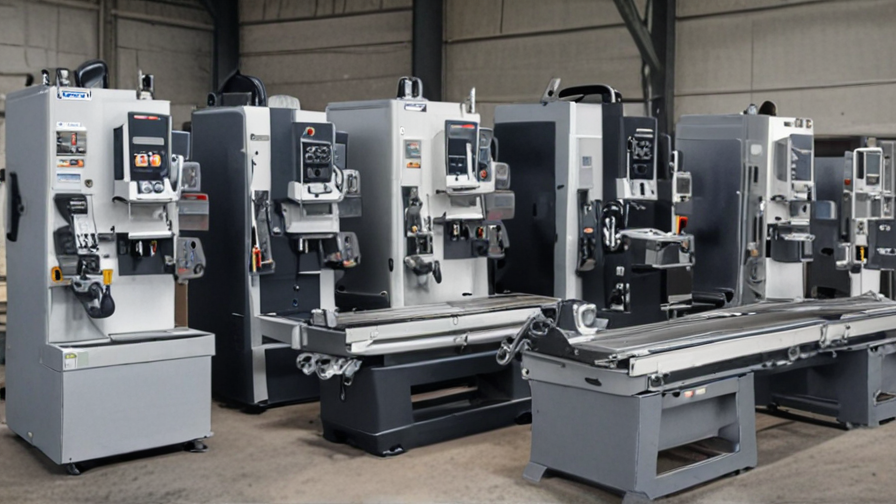
Pros and Cons of Using cnc mills and lathes
CNC mills and lathes are widely used in the manufacturing industry due to their ability to automate and streamline the production process. However, like any technology, they have their pros and cons.
Pros of using CNC mills and lathes:
1. Accuracy and precision: CNC machines are programmed with precise instructions, resulting in highly accurate and repeatable output. This eliminates human error and ensures consistent quality in the manufactured parts.
2. Increased productivity: CNC machines are capable of running continuously, 24/7, without the need for breaks or rest. They can operate at high speeds, reducing production time and increasing overall productivity.
3. Versatility: CNC machines can perform a wide range of tasks, such as milling, drilling, cutting, and turning. They can work with various materials, including metal, plastic, wood, and even composites. This versatility allows for greater flexibility in manufacturing different components.
4. Complex shapes and designs: CNC mills and lathes enable the production of intricate and complex parts that would be challenging or impossible to achieve manually. They offer the ability to create curves, angles, and contours with precise dimensions.
5. Cost-effective for batch production: Once the design and programming are set up, CNC machines can produce large batches of parts with minimal supervision. This reduces labor costs and increases efficiency.
Cons of using CNC mills and lathes:
1. High initial investment: CNC machines are costly to purchase and set up, requiring a significant upfront investment. The cost of maintenance, repairs, and operator training should also be considered.
2. Complexity: Operating CNC machines requires skilled personnel with knowledge of programming, machine operation, and troubleshooting. The learning curve can be steep, and mistakes can lead to costly errors.
3. Limited flexibility: While CNC machines offer versatility, they may not be suitable for every manufacturing task. Certain intricate designs or highly specialized components may still require manual machining.
4. Maintenance and repairs: CNC mills and lathes require regular maintenance to ensure optimal performance. Any breakdown or malfunction can halt production and incur additional costs for repairs.
5. Lack of adaptability: CNC machines are programmed to perform specific instructions, making them less adaptable to sudden design changes or modifications. Alterations in the production process may necessitate reprogramming or tooling adjustments.
In conclusion, CNC mills and lathes offer numerous advantages such as accuracy, productivity, versatility, and the ability to produce complex parts. However, they also pose challenges in terms of investment, complexity, limited flexibility, maintenance, and adaptability. Ultimately, the decision to use CNC machines should be based on the specific needs and requirements of the manufacturing process.
cnc mills and lathes Reference Specifications (varies for different product)
CNC mills and lathes are highly versatile and precise machines used in manufacturing processes. These machines are capable of producing complex geometries with high levels of accuracy and repeatability. While the specific specifications can vary depending on the manufacturer and the desired application, there are some common reference specifications for CNC mills and lathes.
One key specification is the maximum spindle speed. This refers to the rotational speed of the cutting tool, usually measured in revolutions per minute (RPM). Higher spindle speeds allow for faster cutting rates and can result in increased productivity. Another important specification is the maximum feed rate, which determines how quickly the cutting tool can move along the workpiece. This is typically measured in inches per minute (IPM) or millimeters per minute (mm/min). Higher feed rates can achieve faster machining times.
Another critical specification is the maximum travel distance or working envelope. This refers to the range of motion that the machine can achieve in the X, Y, and Z axes. The X-axis represents the horizontal movement, the Y-axis represents the vertical movement, and the Z-axis represents the depth or axial movement. The maximum travel distance determines the size of the workpiece that can be accommodated by the machine.
Precision is a crucial aspect of CNC mills and lathes. The accuracy specification refers to how closely the machine can achieve a desired position or dimension. It is typically measured in thousandths of an inch (in) or micrometers (µm). The repeatability specification, on the other hand, indicates how consistently the machine can return to a given position. Both accuracy and repeatability contribute to achieving high-quality parts and consistent results.
Furthermore, tool capacity is an important consideration. The number of tools that the machine can accommodate directly affects the versatility and complexity of the parts that can be manufactured. This can range from a few tools to dozens, depending on the machine size and type.
Lastly, it is crucial to consider the controller type and software capabilities. The controller serves as the machine’s brain, converting the CAD/CAM designs into machine instructions. Various control systems may have different features, programming languages, and compatibility with different software tools.
In conclusion, CNC mills and lathes have varying specifications depending on the specific product and manufacturer. Some key considerations include spindle speed, feed rate, maximum travel distance, accuracy, repeatability, tool capacity, and controller type. These specifications play crucial roles in determining the capabilities and performance of the machines.
Applications of cnc mills and lathes
CNC mills and lathes are versatile machines used in various industries for precision machining. These computer-controlled tools can fabricate complex and intricate parts with high accuracy and repeatable results. Some applications of CNC mills and lathes include:
1. Automotive industry: CNC mills and lathes are extensively used for manufacturing parts such as engine components, transmission parts, and brake systems. These machines offer precise cutting, shaping, and drilling capabilities, resulting in superior quality and functionality.
2. Aerospace industry: CNC mills and lathes play a critical role in the production of aircraft parts, including turbine blades, engine mounts, landing gear, and control surfaces. The ability to create intricate geometries and maintain tight tolerances ensures optimal performance and safety.
3. Medical devices: CNC machining is widely utilized for manufacturing medical implants, surgical instruments, and prosthetics. The high precision and customization capabilities of CNC mills and lathes enable the creation of patient-specific designs, ensuring better fit and improving patient outcomes.
4. Renewable energy: CNC mills and lathes are utilized in the production of wind turbine components, solar panels, and hydroelectric systems. These machines enable the creation of complex shapes and precise tolerances, resulting in efficient and reliable renewable energy solutions.
5. Electronics and telecommunications: CNC machining is instrumental in manufacturing electronic components, such as printed circuit boards (PCBs), connectors, and housings. The ability to create intricate patterns and precise drilling ensures the quality and functionality of electronic devices.
6. Defense and firearms: CNC mills and lathes are employed in the production of firearm components, weapon systems, and defense equipment. The high accuracy and repeatability of these machines contribute to consistent performance and reliability.
7. Tool and die industry: CNC machining is used to create molds, dies, and custom tooling. The ability to precisely cut, shape, and carve various materials facilitates the production of complex and customized tooling solutions.
8. Jewelry making: CNC mills and lathes are adopted in the jewelry industry for designing and producing intricate and delicate pieces. These machines provide precise control over cutting and carving, enhancing the craftsmanship and quality of jewelry items.
In summary, CNC mills and lathes find vital applications in industries such as automotive, aerospace, medical, renewable energy, electronics, defense, tool and die, and jewelry making. These machines allow for precise and efficient production of complex components, ensuring superior quality and functionality in the final products.
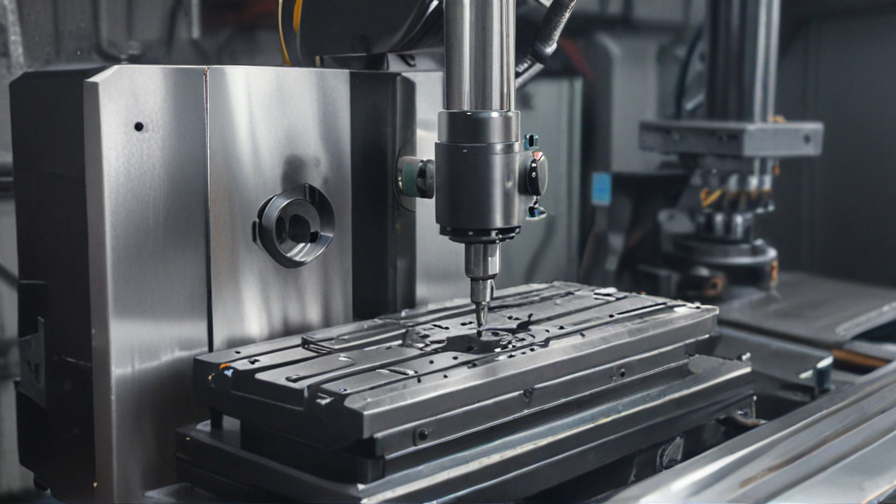
The Work Process and how to use cnc mills and lathes
CNC mills and lathes are sophisticated machines used in the manufacturing industry to fabricate complex parts and components with high precision. The work process involves several steps, which can be summarized as follows:
1. Designing the part: The first step is to create a detailed design of the part using computer-aided design (CAD) software. This involves specifying the part’s dimensions, features, and tolerances.
2. Programming: The CAD design is then converted into instructions that the CNC machine can understand. This is done through computer-aided manufacturing (CAM) software, which generates the machining code or G-code required by the CNC machine.
3. Machine setup: The next step is to set up the CNC mill or lathe. This includes installing the appropriate cutting tools, securing the workpiece in the machine, and configuring the machine’s operating parameters, such as cutting speed and feed rate.
4. Loading the program: The machinist loads the G-code program onto the CNC machine’s control unit. This program contains all the instructions necessary to carry out the machining operations.
5. Machine operation: Once the program is loaded, the machine is ready to start running. The CNC mill or lathe automatically moves the cutting tool according to the instructions in the program, removing material from the workpiece to shape it as per the design.
6. Monitoring and adjusting: During operation, the machinist monitors the machine to ensure that everything is running smoothly. They may make adjustments to the cutting parameters or tooling if necessary.
7. Finishing process: After the required machining operations are completed, the machined part may require additional finishing processes, such as deburring, polishing, or coating, to achieve the desired surface quality and appearance.
8. Quality control: The final step is to inspect the machined part to verify its dimensional accuracy and quality. This may involve using measuring equipment such as calipers, micrometers, or coordinate measuring machines (CMMs).
To effectively use CNC mills and lathes, operators must have a strong understanding of programming, machine setup, and tooling. Additionally, they need to possess knowledge of machining principles, material properties, and cutting parameters to optimize the machining process for each specific task. Continuous learning and experience are crucial in mastering the operation of CNC mills and lathes to produce high-quality parts efficiently.
Quality Testing Methods for cnc mills and lathes and how to control the quality
Quality testing methods for CNC mills and lathes involve a combination of manual measurements and automated inspections. Here are three commonly used methods:
1. First Article Inspection (FAI): A comprehensive inspection is performed on the first manufactured part. Key dimensions and tolerances are measured manually using calibrated equipment. This helps ensure that the manufacturing process is able to produce parts within the required specifications.
2. Statistical Process Control (SPC): SPC involves monitoring and controlling the manufacturing process using statistical techniques. Key parameters, such as dimensions, tolerances, and machining speeds, are continuously measured and analyzed. Control charts are used to detect variations and prevent non-conforming parts from being produced.
3. Non-Destructive Testing (NDT): NDT methods are used to identify defects or flaws in finished parts without causing damage. Techniques like ultrasonic testing, magnetic particle inspection, or X-ray inspection are utilized to check the integrity of the parts. NDT can detect cracks, porosity, or other material defects that could affect the quality of the final product.
To control quality, several practices can be implemented:
1. Calibration and maintenance: Regular calibration and maintenance of measuring devices, cutting tools, and machine components are essential to ensure accurate and precise measurements and overall equipment performance.
2. Process optimization: Continuous process improvement techniques like Lean or Six Sigma can be applied. This involves reducing waste, optimizing cutting parameters, and eliminating sources of variation to enhance process efficiency and quality.
3. Employee training: Operators should be trained on machine operation, quality requirements, and measurement techniques. Regular training sessions can help improve their skills and understanding of quality control processes.
4. Documented procedures: Standard operating procedures, work instructions, and quality control plans should be well-documented and followed consistently to ensure that quality standards are met. This includes defining inspection frequencies and acceptance criteria.
By combining these testing methods and control measures, CNC mills and lathes can achieve higher levels of quality assurance. Effectively controlling the quality helps ensure that the manufactured parts meet customer specifications and minimizes the risk of defects or non-conformance.
cnc mills and lathes Sample Policy and Post-Purchase Considerations for cnc mills and lathes from China
When considering purchasing CNC mills and lathes from China, it is important to establish a comprehensive sample policy and take certain considerations into account before making a final decision.
Sample Policy:
1. Request samples: Begin by requesting samples of the CNC mills and lathes you are interested in purchasing. This will allow you to assess the quality, precision, and functionality of the machines. Ensure that the vendor can provide samples that are representative of the final product.
2. Evaluate sample performance: Test the samples rigorously in terms of accuracy, speed, and reliability. Look for any potential design flaws or issues that may affect the overall performance of the machines. Compare the samples with the specifications provided by the vendor.
3. Third-party testing: Consider engaging a third-party testing agency to verify the quality and performance of the samples. This will ensure an unbiased evaluation of the machines and provide confidence in their capabilities.
4. Assess documentation: Review the provided documentation, including user manuals, maintenance guidelines, and safety instructions. Ensure that the documentation is comprehensive, easy to understand, and available in a language that is suitable for your operators.
5. Customer references: Request references from other customers who have purchased CNC mills and lathes from the Chinese vendor. Contact these customers to inquire about their experience regarding product quality, after-sales support, and overall satisfaction.
Post-Purchase Considerations:
6. Warranty and after-sales support: Confirm the warranty period offered by the vendor and understand the after-sales support provided. Ensure that the vendor has a reliable and responsive support team to address any issues that may arise after the purchase.
7. Spare parts availability: Inquire about the availability of spare parts for the CNC mills and lathes. It is crucial to have a supply of readily available spare parts to minimize downtime and prevent disruptions in production.
8. Compliance with safety standards: Verify that the machines conform to safety standards and regulations applicable within your country. Ensure that all necessary certifications are in place.
9. Shipping and logistics: Discuss shipping options and establish a clear understanding of shipping costs, delivery times, and potential customs duties or taxes. Plan for any necessary infrastructure or manpower adjustments required upon delivery.
By implementing a thorough sample policy and considering key post-purchase factors, you can make an informed decision when purchasing CNC mills and lathes from China. This approach will help mitigate risks and ensure a successful investment in high-quality manufacturing equipment.
Sourcing cnc mills and lathes from China: Opportunities, Risks, and Key Players
China has emerged as a leading global player in the manufacturing industry, particularly in machinery and equipment. When it comes to CNC mills and lathes, Chinese manufacturers offer numerous opportunities, but also pose certain risks. Understanding these factors and identifying key players is essential for businesses considering sourcing from China.
Opportunities:
1. Cost-Effective: Chinese manufacturers generally offer CNC mills and lathes at significantly lower prices compared to other countries. The cost advantage allows businesses to access advanced technology at a fraction of the price.
2. Wide Variety: China boasts a diverse range of CNC mill and lathe manufacturers, providing buyers with numerous options in terms of machine capabilities, sizes, and customizations. Whether businesses require high precision or large-scale production, they can find suitable solutions.
3. Advanced Technology: Chinese machinery manufacturers have significantly improved their technological expertise in recent years. Many companies now offer state-of-the-art CNC mills and lathes with advanced features, ensuring high accuracy and efficiency.
Risks:
1. Quality Concerns: While many Chinese manufacturers offer high-quality machines, there can be varying levels of quality control. It is crucial for businesses to thoroughly research and assess potential suppliers to ensure they meet required standards.
2. Intellectual Property (IP) Protection: Intellectual property rights might not be as strictly enforced in China as in other countries. There is a risk of counterfeit products being sold or IP infringement. Careful due diligence and proper legal protection are essential.
3. Communication and Logistics: Language barriers and cultural differences can pose challenges when communicating with Chinese suppliers. Similarly, managing logistics and transportation can be complex, affecting lead times and overall supply chain efficiency.
Key Players:
1. Haas Automation: Haas Automation, an American company, manufactures CNC milling machines and lathes in China, making them a well-established player in the market.
2. DMG Mori: As an internationally renowned company, DMG Mori has a strong presence in China. They offer a wide range of CNC milling and lathe machines, combining German engineering with Chinese manufacturing.
3. Shenyang Machine Tool Co., Ltd: This Chinese company is one of the leading CNC machine tool manufacturers globally, offering a broad range of CNC mills and lathes.
In conclusion, sourcing CNC mills and lathes from China presents both opportunities and risks. With cost-effectiveness, technological advancements, and a diverse market, businesses can benefit from Chinese manufacturers. However, it is crucial to carefully evaluate suppliers, address quality concerns, protect intellectual property, and mitigate communication and logistics challenges. By doing so, businesses can leverage the advantages and successfully tap into the Chinese market. (288 words)
How to find and select reliable cnc mills and lathes manufacturers in China,use google search manufacturers and suppliers
Finding and selecting reliable CNC mills and lathes manufacturers in China can be achieved by following a systematic approach. One effective method is to utilize Google search for manufacturers and suppliers. Here are the steps to do so:
1. Start by conducting a broad search using relevant keywords such as “CNC mills and lathes manufacturers in China” or “reliable CNC machine suppliers in China.” This will give you a list of potential manufacturers and suppliers in the industry.
2. Refine your search by adding specific criteria or preferences. For example, you can include “high-quality,” “reliable,” or “certified” in your search queries. This will help filter out unreliable or low-quality manufacturers.
3. Visit the websites or online platforms of the shortlisted manufacturers. Look for detailed information about the company, including their history, production capabilities, certifications, and quality control processes. Assess their experience and expertise in manufacturing CNC mills and lathes.
4. Check if the manufacturer has any testimonials, client lists, or case studies on their website. This can provide insights into their reputation and customer satisfaction levels.
5. Look for reviews and ratings of the manufacturers on industry-specific websites, discussion forums, or social media platforms. Genuine customer feedback can give you a better understanding of the manufacturer’s reliability and product quality.
6. Contact the potential manufacturers directly via email or phone. Inquire about their production capabilities, customization options, quality control measures, and after-sales services. Prompt and helpful responses indicate a manufacturer’s professionalism and reliability.
7. Request samples or arrange factory visits if possible. This will allow you to evaluate the quality of their CNC mills and lathes firsthand and assess the manufacturer’s manufacturing facilities and processes.
8. Consider working with manufacturers that have relevant certifications such as ISO 9001 or CE. These certifications ensure adherence to quality standards and can be an indicator of reliability.
9. Obtain multiple quotations from different manufacturers to compare prices, lead times, and customer service. While price is an important consideration, it should not be the sole determining factor for selecting a manufacturer.
10. Before finalizing the decision, conduct due diligence by researching the manufacturer’s reputation, trying to obtain references from their existing clients, or seeking feedback from import-export platforms.
By following these steps and using Google search effectively, you can find and select reliable CNC mills and lathes manufacturers in China that meet your requirements.
How to check cnc mills and lathes manufacturers website reliable,use google chrome SEOquake check if ranking in top 10M
When evaluating the reliability of CNC mills and lathes manufacturers’ websites, one effective method is using Google Chrome’s SEOquake extension to check their ranking in the top 10 million websites. Here’s how you can do it in a few simple steps:
1. Install SEOquake: Visit the Chrome Web Store and search for “SEOquake.” Click “Add to Chrome” and wait for the extension to install.
2. Open Google: Launch Google Chrome and open the search engine.
3. Enter the Manufacturer’s Name: Type the name of the CNC mills and lathes manufacturer you want to assess into the search bar and hit Enter.
4. Check Top 10M Ranking: Once the search results appear, look for the SEOquake icon displayed on the right side of the browser’s address bar. Click on it to open the SEOquake tool.
5. Assess Top 10M Ranking: In the SEOquake window, locate the “Google Index” section and check the “Rank in Top” value. Ensure it is within the top 10,000,000 websites for higher reliability.
While using SEOquake is an essential step, it’s also crucial to keep the following points in mind:
1. Evaluate Website Quality: Look for a professionally designed website that is easy to navigate, provides detailed product descriptions, specifications, and has clear contact information.
2. User Reviews: Check if the manufacturer’s website includes customer testimonials or feedback. Reading about others’ experiences with their products can provide insights into customer satisfaction.
3. Certifications and Associations: Reliable manufacturers often display industry certifications and affiliations on their websites. Verify if they are associated with relevant trade organizations or have any quality certifications.
4. Customer Support: Reliable manufacturers will have dedicated customer support channels, such as phone, email, or live chat, available to assist with any inquiries or issues.
By combining the use of SEOquake to check the ranking and considering factors like website quality, user reviews, certifications, and customer support, you can make a more informed assessment of a CNC mills and lathes manufacturer’s website reliability.
Top 10 cnc mills and lathes manufacturers in China with each 160 words introduce products,then use markdown create table compare
China is known for being a global manufacturing hub, and when it comes to CNC mills and lathes, it is no different. Here are the top 10 CNC mills and lathes manufacturers in China and a brief introduction to their products:
1. Haas Automation: Haas offers a wide range of CNC milling machines and lathes that are known for their accuracy, reliability, and cost-effectiveness.
2. DMG Mori: DMG Mori produces high-performance CNC milling machines and lathes that cater to a variety of industries including automotive, aerospace, and medical.
3. Mazak: Mazak is renowned for its innovative CNC mills and lathes, delivering precision, productivity, and flexibility to its customers.
4. Doosan Machine Tools: Doosan offers a diverse range of CNC mills and lathes, equipped with advanced technologies and designed to meet the needs of various industries.
5. Okuma: Okuma’s CNC mills and lathes are known for their exceptional precision, efficiency, and cutting-edge technology, making them popular among manufacturers worldwide.
6. Yangzhou Euro Brother Machine & Tools Co., Ltd.: Yangzhou Euro Brother specializes in manufacturing CNC mills and lathes that are cost-effective while ensuring high-quality and reliability.
7. Shenyang Machine Tool Co., Ltd.: Shenyang produces CNC milling machines and lathes suitable for heavy-duty machining while maintaining precision and stability.
8. Jiangsu Dongqing CNC Machine Tool Co., Ltd.: Jiangsu Dongqing offers a wide range of CNC mills and lathes, known for their high accuracy, rigidity, and durability.
9. SYIL Machine Corp: SYIL manufactures compact CNC mills and lathes that are designed for small workshops and hobbyists, providing high precision and affordability.
10. SMTCL: SMTCL produces a comprehensive range of CNC mills and lathes, catering to various industries, with a focus on quality, performance, and cost-effectiveness.
| Manufacturer | Product Range |
| ———————————- | ————————————————————————————————- |
| Haas Automation | CNC milling machines and lathes |
| DMG Mori | High-performance CNC milling machines and lathes |
| Mazak | Innovative CNC mills and lathes |
| Doosan Machine Tools | Diverse range of CNC mills and lathes |
| Okuma | Precision CNC mills and lathes with cutting-edge technology |
| Yangzhou Euro Brother Machine | Cost-effective CNC mills and lathes |
| Shenyang Machine Tool | CNC milling machines and lathes for heavy-duty machining |
| Jiangsu Dongqing CNC Machine Tool | High-accuracy, rigid, and durable CNC mills and lathes |
| SYIL Machine Corp | Compact and precise CNC mills and lathes |
| SMTCL | Comprehensive range of CNC mills and lathes with a focus on quality, performance, and cost-effectiveness |
In summary, these top 10 CNC mills and lathes manufacturers in China offer a diverse range of products, known for their precision, performance, and cost-effectiveness. Whether it is for heavy-duty industrial applications or compact machines for small workshops, these manufacturers cater to various needs in the machining industry.
Background Research for cnc mills and lathes manufacturers Companies in China, use qcc.com archive.org importyeti.com
China is known to be a major player in the manufacturing industry, including the production of CNC mills and lathes. To conduct background research on CNC mills and lathes manufacturers in China, several online platforms can be utilized, such as qcc.com, archive.org, and importyeti.com. These platforms provide valuable insights into the companies operating in this sector.
Qcc.com is a comprehensive business database that offers information on Chinese companies. It allows users to search for specific company profiles, including their background, industry, products, and key executives. To obtain information on CNC mills and lathes manufacturers, a search on qcc.com can be conducted using relevant keywords or specific company names.
Archive.org is a digital archive that captures and preserves web pages, allowing users to access historical website data. This platform can be useful to investigate the past websites of CNC mills and lathes manufacturers, providing insights into their previous products, technologies, and company history. By entering the URLs of specific company websites, users can explore archived versions and track changes over time.
Importyeti.com is an online platform that provides import and export data, giving access to shipment records and details about Chinese CNC mills and lathes manufacturers. This platform allows users to search for specific manufacturers, analyze their export activities, identify their trading partners, and gather information about the products being exported.
It is important to note that conducting research on these platforms may require a subscription or payment for accessing certain detailed information. Therefore, it is advisable to utilize the available search functions effectively and efficiently, focusing on keywords and establishing specific criteria to obtain the most relevant and useful information.
In conclusion, using qcc.com, archive.org, and importyeti.com can provide valuable insights into CNC mills and lathes manufacturers in China. These platforms offer information on company profiles, historical website data, and import/export records, allowing researchers to gain a comprehensive understanding of the industry in a concise manner.
Leveraging Trade Shows and Expos for cnc mills and lathes Sourcing in China
Trade shows and expos provide excellent opportunities for sourcing CNC mills and lathes in China. These events serve as a platform for manufacturers, suppliers, and potential buyers to interact and explore new business opportunities. Leveraging such events can be extremely beneficial in several ways.
Firstly, trade shows and expos focused on machinery and manufacturing industries attract a wide range of exhibitors and visitors from all over the world. This creates a conducive environment for buyers to find potential suppliers and compare different options in one place, saving time and effort.
Secondly, attending these events allows buyers to physically inspect and evaluate the quality of CNC mills and lathes showcased by Chinese manufacturers. This firsthand assessment reduces the risk of receiving substandard or counterfeit products when sourcing remotely.
Moreover, trade shows and expos provide a platform for buyers to engage in face-to-face discussions with suppliers. This direct interaction helps in building relationships, understanding manufacturing processes, and negotiating deals. Meeting suppliers in person also allows buyers to gain insights into their production capabilities, quality control measures, and technological advancements.
Additionally, attending trade shows and expos provides opportunities to attend seminars, presentations, and workshops that can enhance one’s knowledge about the latest trends and developments in the CNC machinery industry. This knowledge can be crucial while selecting the most suitable suppliers and making informed decisions.
To make the most out of these events, buyers should come prepared with a clear understanding of their requirements, budget constraints, and desired specifications for CNC mills and lathes. Conducting thorough research about potential exhibitors and pre-scheduling meetings with them can further optimize the sourcing process.
In conclusion, leveraging trade shows and expos for sourcing CNC mills and lathes in China offers numerous advantages. It facilitates direct interaction with suppliers, physical evaluation of products, and access to industry knowledge. By embracing these opportunities, buyers can streamline their sourcing process, ensure product quality, and establish valuable business relationships.
The Role of Agents and Sourcing Companies in Facilitating cnc mills and lathes Purchases from China
Agents and sourcing companies play a crucial role in facilitating the purchase of CNC mills and lathes from China. These entities act as intermediaries between buyers and suppliers, assisting in various stages of the procurement process to ensure smooth transactions and satisfactory outcomes.
Firstly, agents and sourcing companies possess a deep understanding of the Chinese manufacturing industry, including the market trends, supplier capabilities, and regulatory requirements. They leverage this knowledge to identify suitable suppliers that meet the specific requirements of the buyers, whether it is a CNC mill or lathe with particular specifications or a desired price range.
Moreover, these intermediaries assist buyers in performing due diligence on potential suppliers by conducting factory audits and quality checks. This ensures that the chosen supplier adheres to international standards, possesses the necessary certifications, and has a solid reputation for delivering high-quality products. By undertaking these assessments, agents and sourcing companies help buyers minimize the risk of receiving substandard or non-compliant machinery.
Additionally, agents and sourcing companies play a pivotal role in negotiation and communication with Chinese manufacturers. They handle price negotiations, contract terms, and customization requests on behalf of the buyers. With their local language proficiency and cultural familiarity, they bridge the communication gap between buyers and suppliers, reducing the chance of misunderstandings and ensuring clear expectations on both sides.
Furthermore, agents and sourcing companies assist in logistics coordination, including arranging shipment, managing customs procedures, and ensuring timely delivery. They possess knowledge of shipping regulations and can navigate the complexities of international trade, facilitating the smooth movement of goods from China to the buyer’s location.
In summary, agents and sourcing companies act as indispensable facilitators in the procurement process of CNC mills and lathes from China. Their expertise in the Chinese manufacturing landscape, ability to identify reliable suppliers, and skills in negotiation, quality control, and logistics coordination make them valuable partners for buyers seeking to source machinery from China.
Price Cost Research for cnc mills and lathes manufacturers Companies in China, use temu.com and 1688.com
When it comes to sourcing CNC mills and lathes manufacturers in China, two popular online platforms that can be utilized are temu.com and 1688.com. These platforms provide extensive listings of manufacturers and suppliers, making it easier for businesses to find suitable options for their needs.
Temu.com is a global B2B e-commerce platform that connects international buyers with Chinese suppliers. It offers a wide range of industrial products, including CNC mills and lathes. The website allows users to browse through different suppliers, compare prices, and even communicate directly with manufacturers. This can help businesses gather quotes and negotiate deals efficiently.
1688.com, on the other hand, is a Chinese domestic wholesale platform owned by Alibaba Group. It primarily caters to domestic buyers within China, but international buyers can also access the platform with the help of translation tools or by working with local agents. 1688.com provides a vast database of Chinese manufacturing companies, including those specializing in CNC mills and lathes. The platform’s large scale and competitive nature often lead to more competitive pricing from manufacturers.
When researching prices and costs on these platforms, it is essential to consider various factors such as specifications, quality, brand reputation, and after-sales services offered by the manufacturers. To narrow down choices, businesses can filter results based on their specific requirements, such as machine size, accuracy, functionality, and materials to be milled or turned.
It is important to note that while these platforms offer a wide range of choices, it is always advisable to conduct thorough due diligence on the manufacturers before making any final decisions. This can include checking their certifications, customer reviews, and conducting sample tests if possible. Additionally, it is recommended to communicate directly with the manufacturers to negotiate prices and discuss any customizations or additional requirements.
By utilizing temu.com and 1688.com, businesses can efficiently research and compare prices, ensuring that they find reliable CNC mills and lathes manufacturers in China while staying within their budget.
Shipping Cost for cnc mills and lathes import from China
The shipping cost for importing CNC mills and lathes from China can vary depending on several factors. These factors include the weight and dimensions of the machinery, the shipping method chosen, the distance between China and the destination country, and any additional services required.
Generally, there are two main shipping methods for importing heavy machinery like CNC mills and lathes from China: sea freight and airfreight. Sea freight is typically more cost-effective for larger and heavier machinery, while airfreight is faster but more expensive.
When shipping by sea, the cost is calculated based on the volume or weight of the cargo. The shipment will need to be packaged securely and transported to the nearest seaport in China. The cost will also include additional charges such as customs duties, documentation fees, and local handling charges at the destination port. Additionally, if you require any extra services like insurance or customs clearance assistance, these will also add to the total cost.
Alternatively, if you choose to ship by air, the cost will be determined by the weight of the machinery. Airfreight rates are generally higher compared to sea freight, but the transit time is significantly shorter. The machinery will need to be securely packaged and transported to the nearest airport in China. Like sea freight, additional charges such as customs duties, documentation fees, and local handling charges at the destination airport will apply. Insurance and customs clearance assistance can also be arranged at an additional cost.
It is important to note that shipping costs can vary significantly based on the size, weight, and specific requirements of the machinery being imported. It is advisable to request quotes from multiple freight forwarders to compare prices and services. Working with an experienced freight forwarder who specializes in shipping heavy machinery can help ensure a smooth and cost-effective shipping process.
Compare China and Other cnc mills and lathes Markets: Products Quality and Price,Visible and Hidden Costs
China is often seen as the primary player in the CNC mills and lathes market, due to its vast manufacturing capabilities and cost advantages. However, when comparing China to other markets, several factors need to be considered, including product quality, price, and visible and hidden costs.
In terms of product quality, China has made significant progress over the years. Chinese manufacturers have increasingly focused on improving their production processes and adopting international quality standards. While the quality may not always be on par with Western counterparts, they offer competitive options at lower prices. Other markets, such as those in Europe and North America, generally have a reputation for higher quality products, but these often come at a premium price.
Price is where China has a distinct advantage. The country’s cost advantages, including low labor costs and economies of scale, allow Chinese manufacturers to offer CNC mills and lathes at significantly lower prices compared to other markets. This affordability has made China a preferred choice for many buyers, especially those who prioritize cost-effectiveness over other factors.
However, when considering the overall costs, both visible and hidden, other markets may have an edge. Visible costs refer to the upfront expenses, such as the purchase price, transportation, and import taxes. China’s cost advantage in terms of visible costs is well-known. On the other hand, hidden costs, which include factors like after-sales service, maintenance, and support, can often be overlooked. Other markets, particularly well-established ones, may offer better customer service, warranties, and spare parts availability, ensuring long-term satisfaction and reliability.
In conclusion, when comparing China to other CNC mills and lathes markets, the key considerations are product quality and price, as well as visible and hidden costs. While China has improved its product quality, other markets are often associated with higher quality options. However, China’s significant cost advantages make it an attractive choice for buyers who prioritize affordability. Additionally, the hidden costs of after-sales service and maintenance should be taken into account, as other markets may offer better support and reliability. Ultimately, the decision depends on the buyer’s specific requirements and priorities.
Understanding Pricing and Payment Terms for cnc mills and lathes: A Comparative Guide to Get the Best Deal
When it comes to purchasing CNC mills and lathes, understanding pricing and payment terms is crucial to ensure that you get the best deal. This comparative guide aims to provide insights into these aspects, helping you make an informed decision within a limited word count of 300.
Pricing for CNC mills and lathes varies based on several factors such as machine specifications, brand reputation, and technological advancements. It is essential to research the market to gain an understanding of the price range for the equipment you require. Comparing prices from multiple suppliers or manufacturers can help you identify competitive pricing and avoid overpaying.
Payment terms are equally important to consider. Many suppliers offer various payment options that can help you manage your budget. Common payment terms include upfront payment, installment payments, or leasing options. Analyzing your financial capabilities and requirements will determine the most suitable payment option for your specific situation.
Another crucial aspect is evaluating the total cost of ownership (TCO) for CNC mills and lathes. TCO encompasses not only the initial purchase price but also maintenance, repair, and operating expenses over the machine’s lifetime. It is recommended to assess the TCO of different models or brands to determine the most cost-effective option in the long run.
Additionally, negotiating with suppliers can help you secure a better deal. Remember to consider factors beyond the price, such as warranty, support, and training. Sometimes, paying a slightly higher price can be advantageous if it comes with better after-sales service or training opportunities.
To get the best deal, it is crucial to explore both local and international suppliers. While local suppliers may offer convenience and faster support, international manufacturers can provide competitive pricing due to economies of scale. Balancing quality, price, and service is the key to making an optimal decision.
In conclusion, understanding pricing and payment terms for CNC mills and lathes is vital to get the best deal. Researching the market, evaluating TCO, and negotiating with suppliers are all essential steps in this process. Carefully considering these factors within the limited word count of 300 words will help you make an informed decision and find the ideal equipment for your needs.
Chinese Regulations and Industry Standards Certifications for cnc mills and lathes,Import Regulations and Customs for cnc mills and lathes from China
China has established specific regulations and industry standards certifications for CNC mills and lathes to ensure the quality and safety of these products. The two main regulations are the “Technical Requirements for Safety of Metal Cutting Machine Tools” and the “Standards for the Classification of Technical Requirements for Metal Cutting Machine Tools.”
The “Technical Requirements for Safety of Metal Cutting Machine Tools” outlines the safety standards that CNC mills and lathes must meet. These include requirements for electrical safety, mechanical safety, radiation safety, and noise control. The regulation also specifies that manufacturers must conduct performance tests to ensure compliance with the safety requirements.
The “Standards for the Classification of Technical Requirements for Metal Cutting Machine Tools” categorizes CNC mills and lathes based on their technical characteristics and performance. It defines different classes and types of machine tools and provides specific requirements for each. These requirements cover aspects such as precision, stability, control systems, and cutting capabilities.
In terms of import regulations and customs procedures, importing CNC mills and lathes from China requires adherence to specific procedures and documentation. Importers need to provide the necessary documentation, including a purchase contract, commercial invoice, packing list, and bill of lading or airway bill. They must also comply with customs regulations, such as tariff classifications and valuation.
In addition, importers may be required to meet certain standards and obtain certifications for the imported CNC mills and lathes. These certifications may include product compliance with safety standards, quality control systems, and industry-specific certifications.
It is important for importers to have a clear understanding of Chinese regulations and industry standards certifications for CNC mills and lathes. They should also be aware of the import regulations and customs procedures to ensure a smooth import process and compliance with the applicable requirements.
Sustainability and Environmental Considerations in cnc mills and lathes Manufacturing
Sustainability and environmental considerations are essential in the manufacturing process of CNC mills and lathes. These machines play a significant role in the production of various components for multiple industries. However, their operation can have adverse impacts on the environment if not properly managed.
One aspect of sustainability in CNC mill and lathe manufacturing is energy efficiency. CNC machines consume a significant amount of electricity during their operation. Implementing energy-saving measures such as using more efficient motors, optimizing cutting parameters, and employing power management systems can reduce their environmental footprint. Additionally, the use of renewable energy sources for powering these machines can further enhance their sustainability.
Another key consideration is waste management. CNC mills and lathes generate various types of waste, including metal shavings, coolant, and cutting oils. Proper disposal and recycling of these waste materials are crucial to minimize adverse effects on the environment. Implementing recycling programs, using eco-friendly cutting fluids, and adopting filtration systems for coolant can significantly reduce waste generation and contribute to the overall sustainability.
The selection of materials used in CNC mill and lathe manufacturing is also important. Opting for sustainable and recyclable materials, such as aluminum or composite materials, can reduce the environmental impact of these machines. Additionally, designing for disassembly and using modular components can enable easier repair and end-of-life recycling, further enhancing sustainability.
Effective maintenance practices are vital for sustainable CNC mill and lathe manufacturing. Properly maintained machines operate more efficiently, reducing energy consumption and prolonging their lifespan. Regular maintenance procedures, such as lubrication, calibration, and cleaning, are essential to ensure optimal performance and minimize environmental impacts.
Lastly, the transportation of CNC mills and lathes should be considered in terms of sustainability. Optimizing logistics and reducing transportation distances can minimize carbon emissions associated with their delivery.
In conclusion, sustainability and environmental considerations in CNC mill and lathe manufacturing involve various aspects, including energy efficiency, waste management, material selection, maintenance practices, and transportation. By incorporating these considerations into the manufacturing process, the environmental footprint of CNC mills and lathes can be reduced, contributing to a more sustainable future.
List The Evolution history of “cnc mills and lathes”
CNC (Computer Numerical Control) mills and lathes have significantly evolved over the years, transforming the manufacturing industry with their precision and efficiency. The following is a summary of their evolution history:
1. Early Development: The concept of CNC machines began in the late 1940s. At this time, numerical control systems were introduced, enabling operators to control machine tools using punched tape or magnetic cards.
2. Introduction of CNC Mills: In the 1960s, CNC mills were first developed. These machines used punched tapes for programming instructions. They offered increased accuracy, repeatability, and automation compared to conventional mills.
3. Transition to Microcomputers: The 1970s witnessed the introduction of microcomputers, which revolutionized CNC machines. These microcomputers could store and process larger programs, leading to enhanced capabilities and improved performance.
4. Adoption of CAD/CAM: In the 1980s, Computer-Aided Design (CAD) and Computer-Aided Manufacturing (CAM) systems started to be integrated with CNC machines. This allowed engineers and designers to create intricate 3D models and convert them into machine-compatible programs, further enhancing precision and complexity.
5. Evolution of Control Systems: CNC mills and lathes began utilizing more advanced control systems in the 1990s. Integrated circuits and microprocessors improved machine performance, such as faster processing speeds and better servo control.
6. Development of Multi-Axis Machines: In the late 1990s, multi-axis CNC mills and lathes were introduced. These machines moved beyond traditional three-axis movements, offering increased flexibility to handle complex geometries and reduce setup time.
7. Automation and Connectivity: In recent years, CNC machines have become more automated and connected to network systems. This enables real-time monitoring, remote operation, and data analysis, enhancing efficiency and productivity on the factory floor.
8. Advancements in Software and Simulation: Modern CNC mills and lathes benefit from advanced software that simplifies programming, optimizes tool paths, and performs simulations to identify potential errors before actual machining. This saves time, reduces waste, and minimizes costly mistakes.
9. Integration of Robotics and Artificial Intelligence: The latest trend in CNC machining involves the integration of robots and artificial intelligence. These machines can now load and unload workpieces, perform quality inspection, and even make autonomous decisions to optimize machining operations.
In conclusion, CNC mills and lathes have undergone a remarkable evolution, from basic numerical control systems to highly advanced, connected, and automated machines. Their continuous development has played a vital role in increasing productivity, improving accuracy, and expanding the capabilities of modern manufacturing processes.
The Evolution and Market Trends in cnc mills and lathes Industry
The CNC mills and lathes industry has experienced significant evolution and market trends over the years. These machines have played a crucial role in the manufacturing sector by automating the production process, improving precision and efficiency, and reducing labor requirements. This has resulted in increased productivity and cost-effectiveness for businesses.
One of the key advancements in this industry has been the development of computer numerical control (CNC) technology. This technology allows for the automation of machining operations by using pre-programmed instructions to control the movement of the machine tools. CNC mills and lathes have become faster, more accurate, and more versatile, enabling manufacturers to produce complex components with ease.
Another major trend in the CNC mills and lathes industry is the integration of additive manufacturing techniques. Additive manufacturing, also known as 3D printing, has gained popularity in recent years for its ability to create intricate parts and prototypes directly from a digital model. The combination of CNC machining and 3D printing allows manufacturers to optimize both speed and accuracy, resulting in more efficient and cost-effective production processes.
Additionally, the market has witnessed a rise in demand for smaller, desktop-sized CNC mills and lathes. These compact machines are often preferred by small businesses, hobbyists, and educational institutions due to their affordability, ease of use, and versatility. This trend has opened up new opportunities for individuals and small enterprises to engage in CNC manufacturing, previously accessible only to larger organizations.
Furthermore, there has been a growing focus on sustainability and eco-friendly manufacturing practices in the CNC mills and lathes industry. Manufacturers are increasingly adopting energy-efficient technologies, optimizing material usage, and implementing waste management strategies to minimize their environmental impact. As sustainability becomes more important to consumers and regulatory bodies, the demand for CNC mills and lathes that support eco-friendly manufacturing practices is expected to rise.
In conclusion, the evolution of CNC mills and lathes has been characterized by advancements in technology, the integration of additive manufacturing, the availability of compact machines, and a growing emphasis on sustainability. These trends have not only improved the performance and capabilities of these machines but have also widened the market scope by making CNC manufacturing more accessible to a broader range of users.
Custom Private Labeling and Branding Opportunities with Chinese cnc mills and lathes Manufacturers
Chinese CNC mills and lathes manufacturers offer lucrative opportunities for custom private labeling and branding. With their advanced technology, cost-effectiveness, and expertise in the manufacturing sector, these companies provide a wide range of services to cater to the specific needs of businesses around the world.
Private labeling allows businesses to have their own branding and logo on the products they purchase. Chinese CNC mills and lathes manufacturers understand the importance of branding and offer customization options to meet the unique requirements of their clients. They have the expertise to integrate branding elements seamlessly into the manufacturing process, ensuring that the final products reflect the desired image of the brand.
Additionally, Chinese manufacturers have extensive experience in working with international clients, making communication and collaboration efficient and effective. They have dedicated teams to provide comprehensive support throughout the entire production process, from initial design to final delivery.
Furthermore, these manufacturers offer competitive pricing without compromising on quality. Thanks to their strong supply chains and economies of scale, they can deliver high-quality CNC mills and lathes at affordable prices. This cost-effectiveness allows businesses to maximize their profit margins or invest in other areas of their operations.
Businesses can take advantage of custom private labeling and branding opportunities with Chinese CNC mills and lathes manufacturers to expand their market presence. They can establish a unique identity and differentiate themselves from competitors by offering customized products under their own brand. This helps in increasing brand recognition, customer loyalty, and overall market share.
In conclusion, Chinese CNC mills and lathes manufacturers provide exciting opportunities for businesses to custom private-label and brand their products. With their technological expertise, cost-effective solutions, and excellent customer support, these manufacturers enable businesses to create their own identity in the market and maximize their competitive advantage.
Tips for Procurement and Considerations when Purchasing cnc mills and lathes
When it comes to purchasing CNC mills and lathes, there are several considerations that can help streamline the procurement process. Here are some tips and factors to keep in mind:
1. Define needs and requirements: Begin by clearly defining your needs and requirements for the CNC mills and lathes. Consider factors such as the type of materials you’ll be working with, the size and complexity of the parts, production volume, and any specific features or capabilities required.
2. Budget: Determine a realistic budget for your procurement. CNC mills and lathes can vary significantly in price based on factors like size, brand, and functionality. Set a budget that aligns with your business goals and accounting constraints.
3. Research and comparison: Conduct thorough research to identify reputable manufacturers and suppliers who offer CNC mills and lathes that meet your requirements. Compare various models, features, and prices to ensure you make an informed decision.
4. Quality and reliability: Assess the quality and reliability of the machines you are considering. Read customer reviews and testimonials, and check for any certifications or awards that highlight their performance and durability. A reliable CNC machine will result in fewer breakdowns and disruptions to your operations.
5. After-sales service and support: Evaluate the after-sales service and support provided by the manufacturer or supplier. Ensure they offer prompt technical assistance, spare parts availability, and training options for your machine operators.
6. Training and expertise: Consider your team’s existing skills and knowledge in CNC machining. Will additional training be required for operating the specific models you are considering? Ensure the manufacturer or supplier offers training programs to help your operators maximize the capabilities of the machines.
7. Maintenance and downtime: Inquire about the maintenance requirements and downtime associated with each CNC mill and lathe model. Opt for machines that require minimal maintenance and have proven uptime records to minimize production disruptions.
8. Scalability and future needs: Anticipate any potential growth or changes in your manufacturing requirements, and choose CNC machines that have the flexibility and scalability to adapt to your evolving needs.
9. Support network: Consider the availability of local service technicians or distributors in your area. Having a support network nearby can reduce response times and minimize downtime in case of any issues.
10. Warranty: Review the warranty terms and conditions provided by the manufacturer. Understand what is covered and for how long, as well as any limitations or exclusions.
By carefully considering these factors during the procurement process, you can choose CNC mills and lathes that align with your needs, budget, and overall business objectives.
FAQs on Sourcing and Manufacturing cnc mills and lathes in China
Q1: Why should I consider sourcing and manufacturing CNC mills and lathes in China?
A: China is known for its cost-effective manufacturing processes, allowing you to obtain CNC mills and lathes at competitive prices. The country has a wide range of suppliers and manufacturers with expertise in CNC machining, ensuring a variety of options to choose from. Additionally, China has a robust supply chain network, making it easier to source parts and components required for CNC mills and lathes.
Q2: How do I find reliable suppliers and manufacturers in China?
A: Several online platforms and directories provide access to a comprehensive database of suppliers and manufacturers, enabling you to search for CNC mill and lathe providers in China. It is essential to conduct thorough research and due diligence to authenticate the credibility and reliability of potential suppliers. Reading customer reviews, asking for samples, and visiting the manufacturer’s facilities are recommended steps to ensure quality and professionalism.
Q3: Can I customize CNC mills and lathes according to my specific requirements?
A: Yes, many Chinese manufacturers offer customization services to meet individual specifications. This may include modifications to the machine’s dimensions, power requirements, tooling systems, and control software. It is essential to communicate your requirements clearly to the manufacturer to ensure they can accommodate your customization needs.
Q4: How can I handle quality control while manufacturing in China?
A: To maintain quality control, it is advisable to establish clear quality requirements and expectations early in the manufacturing process. Building a strong relationship with the manufacturer and conducting regular inspections during various stages of production can help identify and address any quality issues promptly. Requesting product samples and conducting third-party quality inspections before shipment are additional measures to ensure that the final products meet your standards.
Q5: What are the shipping and import costs associated with sourcing from China?
A: Shipping and import costs depend on factors such as the size and weight of the machinery, shipping method, and destination. It is recommended to obtain quotes from different freight forwarders and consider additional expenses like customs duties, taxes, and handling fees. Working with a knowledgeable freight forwarding agent can help navigate the shipping and import processes while minimizing costs.
Q6: Are there any challenges or risks associated with sourcing from China?
A: While sourcing from China offers various advantages, challenges can include language barriers, differences in business practices, and potential intellectual property risks. It is crucial to engage in proper due diligence, including signing legal contracts, protecting intellectual property rights, and maintaining open communication with the supplier. Working with an experienced sourcing agent or consultant can provide valuable support in navigating these challenges.
In summary, sourcing and manufacturing CNC mills and lathes in China can offer cost-effective solutions with a wide range of customization options. However, thorough research, due diligence, and effective quality control measures are essential to ensure a successful partnership with reliable suppliers in China.
Why contact sourcifychina.com get free quota from reliable cnc mills and lathes suppliers?
SourcifyChina.com offers free quota from reliable CNC mills and lathes suppliers for several reasons.
1. Building Trust: By offering free quota from reliable suppliers, SourcifyChina.com aims to build trust with potential customers. Providing a free quota allows customers to experience the quality and professionalism of the suppliers without committing financially. This helps customers gain confidence in the supplier’s capabilities and build a long-term relationship.
2. Quality Assurance: SourcifyChina.com wants to ensure that customers receive high-quality CNC mills and lathes. By partnering with reliable suppliers, they can guarantee the quality of the machines. Offering a free quota enables customers to assess the supplier’s products and manufacturing processes before making a purchase. This reduces the risk of receiving substandard equipment.
3. Cost Savings: CNC mills and lathes are significant investments for businesses. SourcifyChina.com understands that customers want to save costs without compromising on quality. By securing quotations from reliable suppliers, customers can compare prices and negotiate better deals. This allows businesses to obtain the best possible pricing for their required CNC machines, ultimately saving them money.
4. Streamlined Sourcing Process: SourcifyChina.com aims to simplify the sourcing process for businesses. By providing free quotas, they eliminate the need for customers to spend time searching for reliable suppliers independently. This saves customers valuable time and effort, allowing them to focus on other aspects of their business operations.
5. Expert Guidance: SourcifyChina.com offers expert guidance throughout the sourcing process. By securing free quotas from reliable suppliers, they can provide customers with valuable advice and recommendations based on their specific requirements. This ensures that customers make informed decisions and select the most suitable CNC mills and lathes for their business needs.
In summary, SourcifyChina.com offers free quota from reliable CNC mills and lathes suppliers to build trust, ensure quality, save costs, streamline the sourcing process, and provide expert guidance to customers. This helps businesses make informed decisions and obtain high-quality equipment at the best possible price.