Introduce about coating equipments guide,Qulity,Cost,Supplier,Certification,Market,Tips,FAQ
Coating equipment plays a crucial role in various industries, including automotive, aerospace, and architecture, by providing a protective layer to enhance the durability, aesthetics, and performance of the coated products. This guide aims to provide an overview of coating equipment, including quality considerations, cost factors, reliable suppliers, certifications, market trends, helpful tips, and frequently asked questions.
When selecting coating equipment, quality is paramount. Look for equipment that uses advanced technologies, offers precise control over coating parameters, and ensures uniform and consistent coating application. High-quality equipment minimizes the risk of defects and ultimately leads to superior coating results.
Cost is another crucial factor to consider. Coating equipment prices vary based on several elements, such as the type of coating technology used (e.g., spray, dip, or powder coating), the size and capacity of the equipment, and additional features like automation and customization options. It is essential to balance your budget with the features and capabilities required for your specific coating application.
Finding a reputable supplier is vital to ensure the quality and reliability of the coating equipment. Look for suppliers with a solid track record, positive customer reviews, and excellent after-sales service. Additionally, suppliers that offer comprehensive support, such as training, technical assistance, and spare parts availability, are preferable.
Certifications ensure that the coating equipment meets industry standards and regulatory requirements. Look for equipment that has been certified by recognized organizations, such as ISO (International Organization for Standardization) or relevant industry associations. Certification provides assurance of the equipment’s performance, safety, and environmental compliance.
The coating equipment market is dynamic, driven by innovation and evolving industry needs. Stay informed about emerging trends, such as robotic coating systems, environmentally friendly coatings, and advanced digital control systems. These trends can offer improved efficiency, sustainability, and cost-effectiveness.
To maximize the coating process and equipment performance, consider the following tips: ensure proper maintenance of equipment, conduct regular inspections, follow manufacturer guidelines, and provide adequate operator training. These practices contribute to prolonged equipment lifespan and optimal coating results.
Frequently asked questions about coating equipment may include topics such as equipment compatibility with different coating materials, safety considerations during operation, troubleshooting common coating defects, or recommendations for specific applications. Ensure to consult the supplier’s FAQ section or seek expert advice when encountering any queries or concerns.
In summary, coating equipment guides users through the selection process, considering quality, cost, suppliers, certifications, and market trends. Follow helpful tips to optimize equipment performance, while seeking advice and reviewing frequently asked questions when needed.
Types of coating equipments
Coating equipment is used across various industries for applying a protective or decorative coating to a surface. These coatings can serve different purposes, including enhancing the durability, appearance, and functionality of the substrate. There are several types of coating equipment available, each designed for specific applications. Here are some commonly used coating equipment types:
1. Spray Coating Equipment: This type of equipment uses a spray gun to atomize the coating material and propel it onto the surface. It can be used with different types of coatings such as liquid paint, powder coatings, and adhesives. Spray coating equipment offers versatility and can be used for a wide range of applications, including automotive, aerospace, furniture, and construction.
2. Dip Coating Equipment: In this method, the substrate is dipped into a tank or vat filled with the coating material. The coating adheres to the surface as it is withdrawn from the tank. Dip coating equipment is commonly used for smaller objects or parts that require a thin, even coating, such as small metal or plastic components.
3. Roll Coating Equipment: This equipment involves passing the substrate through a series of rollers that apply the coating material uniformly. It is commonly used in industries such as paper and printing, where large sheets or webs need to be coated.
4. Electrostatic Coating Equipment: This technique involves applying a high voltage charge to the coating material and grounding the substrate. The charged particles are attracted to the grounded surface, resulting in an even coating. Electrostatic coating equipment is efficient and can reduce overspray and material wastage. It is often used for powder coatings or liquid paints in applications such as automotive, appliances, and electronics.
5. Curtain Coating Equipment: This method involves forming a falling curtain of coating material that the substrate passes through. The excess coating is collected and recirculated for reuse. Curtain coating equipment is commonly used for high-speed applications, such as coating paper, films, and certain types of wood products.
6. Vacuum Coating Equipment: This type of equipment is used for applying thin films or coatings to substrates under vacuum conditions. It includes techniques such as physical vapor deposition (PVD) and chemical vapor deposition (CVD). Vacuum coating equipment is commonly used in industries such as optics, electronics, and solar panels.
These are just a few examples of the types of coating equipment available. The choice of equipment depends on the specific coating requirements, substrate material, desired results, and production volume. Advanced technologies and coatings continue to drive innovation in the field of coating equipment, introducing new and specialized equipment for specific applications.
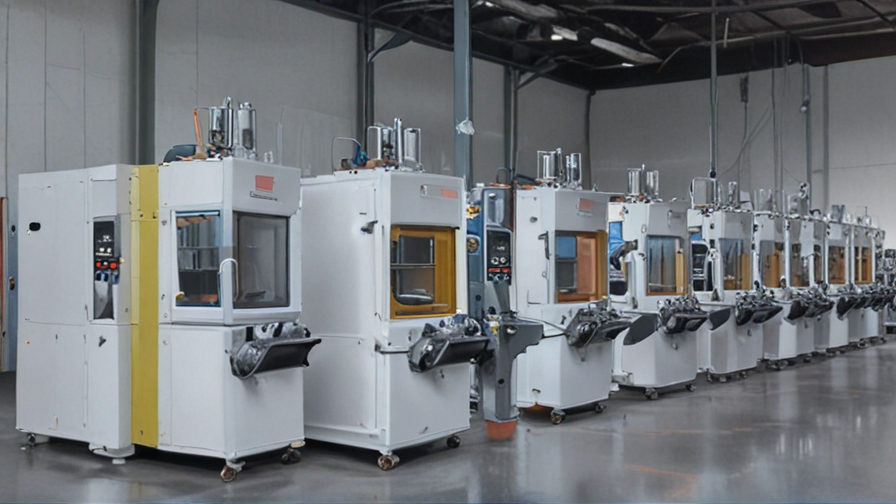
Pros and Cons of Using coating equipments
Coating equipment refers to a variety of machinery and tools used in the process of applying coatings to surfaces. This can include paint, varnish, powder coating, and other protective or decorative finishes. While there are several advantages to using these types of equipment, there are also some drawbacks to consider.
One of the main advantages of using coating equipment is the efficiency and accuracy it provides. These machines can ensure a uniform and consistent application of the coating, leaving no room for human error. This can result in a higher quality finish with minimal wasted material. Additionally, coating equipment can often apply coatings at a much faster rate than manual methods, improving overall productivity and reducing labor costs.
Another benefit of using coating equipment is the increased level of control it offers. Many of these machines have advanced settings and features that allow operators to adjust factors such as spray pattern, coating thickness, and drying time. This level of precision can be particularly useful when working on complex or delicate surfaces that require specific coating requirements.
In terms of drawbacks, one of the main considerations is the initial cost of purchasing coating equipment. These machines can be quite expensive, which may not be feasible for smaller businesses or those with limited budgets. Additionally, it is necessary to train operators on how to properly use and maintain the equipment, which can require additional time and resources.
Maintenance and cleaning of coating equipment can also be a challenge. Depending on the type of equipment being used, there may be specific cleaning processes or chemicals that are required to ensure optimal performance. This can add to production downtime and increase operational costs.
Furthermore, some types of coating equipment may have limited versatility or may not be suitable for all types of coatings. For example, certain machines may be designed for liquid coatings, whereas others are better suited for powder coatings. It is important to carefully consider the specific requirements of the project and choose the appropriate equipment accordingly.
In conclusion, the use of coating equipment offers numerous advantages, including improved efficiency, accuracy, and control over the coating process. However, these benefits must be weighed against the initial investment cost, maintenance requirements, and potential limitations of the equipment. By carefully evaluating these factors and considering the specific needs of the project, businesses can determine whether investing in coating equipment is the right choice for them.
coating equipments Reference Specifications (varies for different product)
Coating equipment is essential in various industries to apply a protective or decorative layer on different products. The specific reference specifications for coating equipment vary depending on the product being coated. However, there are some common characteristics and requirements that are generally considered while designing coating equipment.
Firstly, the size and type of the product being coated play a crucial role in determining the specifications. For small products, such as bolts or screws, a compact and automated coating system is preferred. On the other hand, larger products like automotive parts or industrial machinery require a more robust and heavy-duty coating setup.
Secondly, the nature of the coating material also affects the specifications. Different coatings such as liquid paints, powder coatings, electroplating, or thermal spraying require specific equipment features. For instance, liquid paint coating equipment may include atomizers, air or airless spraying systems, and drying ovens. Powder coating equipment, on the other hand, includes booths, electrostatic spray guns, and curing ovens.
Thirdly, the desired coating thickness and uniformity influence the specifications. Achieving consistent and precise coating thickness is crucial for optimal product performance. Coating equipment may include features like adjustable spray nozzles, rotating fixtures, or automated robotic arms to ensure even coverage.
Furthermore, the production volume and speed also impact the specifications. For high-volume manufacturing, automatic or continuous coating systems are preferred. These systems involve conveyors, dip tanks, or electrostatic coating setups to achieve efficient and rapid coating application.
Considering the safety and environmental aspects, coating equipment must meet certain standards. These may include proper ventilation systems, chemical containment facilities, and waste disposal mechanisms.
Additionally, the control and monitoring system for coating equipment are important features. Advanced systems may include PLC (programmable logic controller), HMI (human-machine interface), or SCADA (supervisory control and data acquisition) for precise control, data collection, and process optimization.
It is critical to note that coating equipment specifications vary significantly based on the product, industry, and specific coating requirements. Hence, it is crucial to consult with industry experts, manufacturers, and supplier guidelines while designing and selecting coating equipment for specific applications.
Applications of coating equipments
Coating equipment plays a vital role in various industries by providing protective and functional coatings to enhance the performance, durability, and aesthetics of a wide range of products. Below are some key applications of coating equipment:
1. Automotive industry: Coating equipment is used to apply protective coatings on cars, trucks, and motorcycles. These coatings protect against corrosion, UV radiation, and chemicals, while also enhancing the appearance of the vehicle.
2. Aerospace industry: Coating equipment is utilized in the aerospace sector to apply protective coatings on aircraft components, such as engine parts, wings, and landing gear. These coatings enhance resistance against high temperatures, corrosion, and wear, ensuring the safety and longevity of the aircraft.
3. Metal industry: Coating equipment is extensively used in the metal industry to apply protective coatings on various metal products, including pipes, valves, tools, and machinery. These coatings protect against rust, oxidation, abrasion, and chemical exposure, extending the lifespan and performance of the metal products.
4. Electronic industry: Coating equipment is employed in the electronic industry for encapsulating and protecting delicate electronic components, such as circuit boards, microchips, and connectors. The coatings provide insulation from moisture, dust, and contaminants, while also offering electrical insulation properties.
5. Pharmaceutical industry: Coating equipment is utilized in the pharmaceutical sector for tablet coating. The coatings applied to tablets can improve taste, control release, and protect the active ingredients from degradation. Coating equipment ensures precise and uniform coating thickness, resulting in consistent quality and effectiveness of the medication.
6. Food industry: Coating equipment is used in the food industry for various purposes. It can be employed to apply a protective coating to food packaging materials, enhancing their barrier properties and extending the product’s shelf life. Additionally, coating equipment can also be utilized to apply coatings on confectionery, bakery products, and snacks, providing a glossy appearance, improving taste, and preserving freshness.
In conclusion, coating equipment finds widespread applications across industries, including automotive, aerospace, metal, electronics, pharmaceutical, and food. The versatility of coating equipment allows for the application of protective coatings that enhance performance, durability, and aesthetics of various products, ensuring their longevity and satisfying customer needs.
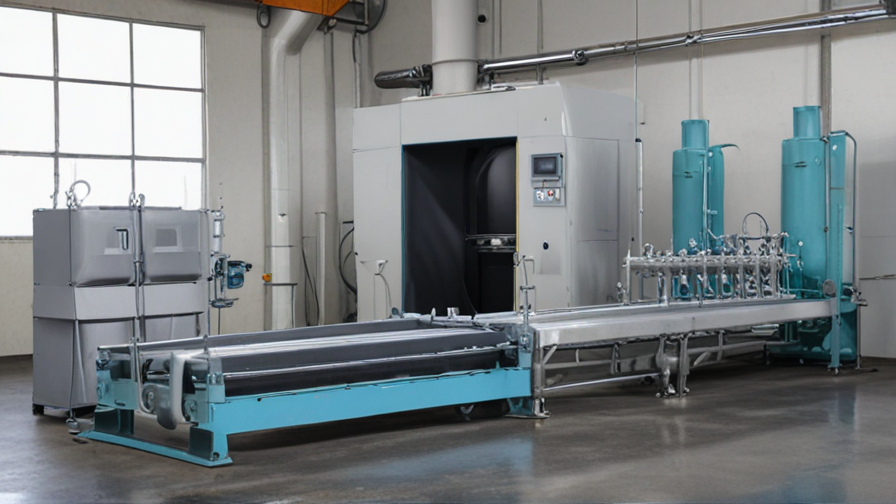
The Work Process and how to use coating equipments
The work process involving coating equipment is generally composed of several steps, starting with surface preparation, followed by the application of the coating material, and ending with the curing or drying of the coated surface.
Surface preparation is crucial for ensuring proper adhesion of the coating material. It involves cleaning the surface to remove any dirt, dust, grease, or old coatings. This can be done by abrasive blasting, chemical cleaning, or mechanical cleaning methods.
Once the surface is clean and dry, the coating material is applied using various coating equipment. Examples of coating equipment include spray guns, brushes, rollers, and dip tanks. The choice of equipment depends on the type of coating material, desired finish, and application method.
Using coating equipment effectively requires proper technique and understanding of the coating material. Spray guns, for instance, require adjusting the spray pattern, air pressure, and material flow rate to achieve the desired coating thickness and coverage. Brushes and rollers need to be used with proper pressure and even strokes to ensure uniform application.
After applying the coating material, the coated surface needs to be cured or dried. This can be done through various methods such as air drying, oven drying, or curing under UV light, depending on the coating material. It is important to follow the manufacturer’s instructions for curing to ensure optimum performance and longevity of the coating.
Regular maintenance and cleaning of coating equipment are essential for their longevity and consistent performance. This includes cleaning the equipment after each use and properly storing them to prevent clogging or drying of the coating material.
In conclusion, the work process involving coating equipment consists of surface preparation, coating application using various equipment, and the curing or drying of the coated surface. Proper technique, understanding of the coating material, and regular equipment maintenance are vital for achieving high-quality and durable coatings.
Quality Testing Methods for coating equipments and how to control the quality
Quality testing methods for coating equipment play a crucial role in ensuring that the coating process is efficient, effective, and meets the desired quality standards. Here are some commonly used quality testing methods for coating equipment:
1. Visual Inspection: Visual inspection allows operators to visually assess the coating equipment for any defects, damage, or abnormal conditions. It involves inspecting the equipment’s surface, moving parts, connections, and any other relevant components.
2. Thickness Measurement: Coating thickness is a critical quality parameter. Non-destructive techniques such as eddy current, magnetic induction, or ultrasonic testing are often used to measure the coating’s thickness accurately.
3. Adhesion Testing: Adhesion testing measures the coating’s ability to adhere to the substrate. Different methods, such as pull-off tests, cross-hatch adhesion tests, or tape tests, are employed to evaluate the coating’s adhesion strength.
4. Hardness Testing: Coating hardness is vital for various applications. Techniques like pencil hardness testing or indentation hardness measurement assess the hardness of the coating surface.
5. Gloss Measurement: Gloss is an essential aesthetic property of coatings. Gloss meters can measure the amount of light reflected from the coated surface, indicating the coating’s glossiness.
6. Salt Spray Testing: Salt spray tests simulate harsh environmental conditions to assess the coating’s resistance to corrosion. The equipment is subjected to a saltwater mist to observe any signs of corrosion or degradation.
To ensure control over the quality of coatings, a few measures can be adopted:
1. Establishing Standard Operating Procedures (SOPs): Clearly defined procedures help ensure consistent coating quality. SOPs should cover equipment setup, maintenance, cleaning, calibration, and testing procedures.
2. Regular Equipment Maintenance: Following a robust maintenance schedule, including regular cleaning, lubrication, and calibration of coating equipment, can prevent malfunctions and maintain optimal performance.
3. Operator Training: Thoroughly trained operators have a better understanding of the coating process, quality standards, and equipment operation. This reduces the chances of errors and improves overall quality control.
4. Statistical Process Control (SPC): Implementing SPC methods involves regularly monitoring process variables such as thickness, adhesion, or hardness, and analyzing the data to identify any deviations from the desired quality standards.
5. Continuous Improvement: Encouraging a culture of continuous improvement can help identify and address quality issues promptly. This involves conducting root cause analysis, implementing corrective actions, and regularly reviewing and updating quality control measures.
Implementing comprehensive quality testing methods and adopting appropriate quality control measures can help ensure that coating equipment consistently delivers high-quality coatings, meets customer expectations, and minimizes defects or failures.
coating equipments Sample Policy and Post-Purchase Considerations for coating equipments from China
Sample Policy for Coating Equipment from China:
1. Quality Assurance: We guarantee that all coating equipment purchased from China will be of high quality and meet international standards. In the unlikely event of any defects or malfunctions, we offer a warranty period of [X] months from the date of purchase. During this period, we will provide free repairs or replacement for any faulty components or parts.
2. Shipment and Delivery: All orders will be processed and shipped within [X] days of receiving the payment. We work in partnership with reliable and experienced shipping companies to ensure prompt and secure delivery. Customers will be provided with a tracking number to monitor the progress of their shipment.
3. Customization and Technical Support: We understand that each customer may have unique requirements for their coating equipment. We offer customization options to tailor the equipment to your specific needs. Our team of experienced technicians is also available to provide technical support and assistance regarding installation, operation, and maintenance of the coating equipment.
4. Returns and Refunds: If for any reason the customer is dissatisfied with their purchase, they can initiate a return within [X] days of receiving the equipment. The equipment must be in its original condition and packaging for a full refund to be processed. Return shipping costs will be the responsibility of the customer, unless the return is due to a defect or error on our part.
Post-Purchase Considerations for Coating Equipment from China:
1. Installation and Training: It is recommended to engage the services of a professional installer to ensure proper installation and setup of the coating equipment. Additionally, our technical support team can provide training sessions to familiarize your staff with the equipment’s operation and maintenance.
2. Spare Parts and Maintenance: To ensure long-term efficiency and minimize downtime, we advise customers to keep a stock of commonly used spare parts for the coating equipment. We can provide a list of recommended spare parts and offer maintenance packages to keep the equipment in optimal condition.
3. Quality Control and Testing: Upon receiving the equipment, it is advisable to conduct thorough quality control checks and testing to ensure that all components are functioning correctly. Any discrepancies or issues should be immediately reported to our customer service team for prompt resolution.
4. Feedback and Review: We value our customers’ feedback and encourage them to provide reviews or testimonials about their experience with our coating equipment from China. This will help us improve our products and services to better meet the needs of our customers.
In conclusion, our sample policy and post-purchase considerations aim to ensure customer satisfaction and provide a seamless experience when purchasing coating equipment from China. We strive to provide high-quality products, reliable delivery, customization options, and ongoing support to meet your coating equipment needs.
Sourcing coating equipments from China: Opportunities, Risks, and Key Players
Sourcing coating equipment from China presents both opportunities and risks. China is one of the largest manufacturers of coating equipment globally and offers a wide range of options at competitive prices. The country’s advanced manufacturing capabilities, skilled workforce, and efficient supply chain make it an attractive sourcing destination.
Opportunities:
1. Cost-competitive: China’s low labor and production costs allow for cost-effective sourcing of coating equipment. This translates into lower purchase prices and reduced overall production costs for businesses.
2. Wide variety: China offers a wide range of coating equipment options, from small-scale machinery to large-scale industrial equipment, catering to diverse needs and specifications.
3. Advanced technology: Chinese manufacturers have made significant strides in developing advanced coating technologies that can match international standards.
4. Scalability: China’s manufacturing sector has the capacity to fulfill both small and large orders, making it suitable for businesses with different production requirements.
Risks:
1. Quality control: Ensuring product quality can be a challenge when sourcing from China. It is critical to assess suppliers’ quality control processes, certifications, and track records to mitigate any potential risks.
2. Intellectual property protection: China has faced criticism for intellectual property infringement. Businesses must take precautions and consider legal protections to safeguard their proprietary coating technologies.
3. Communication and language barriers: Effective communication with Chinese suppliers may be challenging due to language barriers. This can lead to misunderstandings in specifications, production requirements, and quality standards.
4. Supply chain disruptions: Events such as natural disasters, labor strikes, or disruptions in shipping can impact the timely delivery of goods. Businesses should have contingency plans in place to mitigate these risks.
Key Players:
1. Wagner Group: Specializes in various types of coating equipment, including spray guns, paint spraying systems, and fluid management solutions.
2. Gema Switzerland: A leading manufacturer of powder coating equipment, offering a comprehensive range of solutions for industrial applications.
3. Nordson Corporation: Offers advanced coating and dispensing equipment, including powder coating systems, liquid painting equipment, and adhesives dispensing systems.
4. Sames Kremlin: Provides innovative coating solutions, including airspray, airless, and electrostatic spray guns, as well as robotic systems for various industries.
In conclusion, sourcing coating equipment from China offers opportunities in terms of cost, variety, advanced technology, and scalability. However, businesses must be aware of the risks associated with quality control, intellectual property protection, communication barriers, and supply chain disruptions. By carefully selecting reliable suppliers and taking necessary precautions, businesses can leverage the benefits of sourcing from China in the coating equipment industry.
How to find and select reliable coating equipments manufacturers in China,use google search manufacturers and suppliers
When searching for reliable coating equipment manufacturers in China, utilizing Google search can be a helpful tool. Here are some steps to follow:
1. Begin with a specific search query: Enter relevant keywords like “coating equipment manufacturers in China” or “reliable coating equipment suppliers in China” to narrow down the search results.
2. Review the search results: Go through the list of manufacturers and suppliers that appear on the search engine results page (SERP). Pay attention to the top-ranking websites as they are likely to be more established and reputable.
3. Check the website and company information: Visit the websites of shortlisted manufacturers. Look for information about their company, history, product range, manufacturing facilities, certifications, and any other relevant details. A well-designed and informative website often indicates a professional and reliable manufacturer.
4. Evaluate product quality and diversity: Explore the range of coating equipment offered by the manufacturers. Assess their product quality, technological capabilities, and innovation. Look for variations in designs, specifications, and customization options.
5. Verify experience and reputation: Look for indications of the manufacturer’s experience and reputation in the industry. Look for testimonials, reviews, or case studies on their website or from other reliable sources. Additionally, consider reaching out to industry experts, forums, or business directories to see if they have any recommendations or feedback on the manufacturers under consideration.
6. Assess production capacity and capabilities: Determine if the manufacturer has adequate production capacity to meet your requirements. Consider factors such as production facilities, workforce, machinery, and lead times. Ensure that the manufacturer can handle the volume of orders you require within the desired time frame.
7. Inquire about certifications and quality control: Check if the manufacturer has relevant certifications such as ISO, CE, or others specific to the coating equipment industry. Inquire about their quality control processes and whether they adhere to international standards.
8. Communication and customer support: Evaluate the manufacturer’s responsiveness and willingness to address your inquiries promptly. Establish clear channels of communication to ensure effective collaboration during the manufacturing process. Good customer support is essential for long-term business relationships.
9. Request for samples or visit the factory: If possible, request samples of their coating equipment or visit their factory in person. This will allow you to assess the quality, craftsmanship, and production conditions yourself.
10. Compare quotes and terms: Request quotes from multiple manufacturers and compare pricing, lead times, payment terms, and after-sales support. However, keep in mind that the cheapest option may not always be the best in terms of quality and reliability.
It is crucial to thoroughly research and evaluate different coating equipment manufacturers in China to ensure you select a reliable and trustworthy partner.
How to check coating equipments manufacturers website reliable,use google chrome SEOquake check if ranking in top 10M
When it comes to checking the reliability of a coating equipment manufacturer’s website, using Google Chrome with the SEOquake extension can help in determining their ranking and credibility. Here’s how to do it in three easy steps.
1. Install SEOquake Extension: Start by installing the SEOquake extension in your Google Chrome browser. You can find it in the Chrome Web Store. Once installed, the SEOquake toolbar will appear at the top of your browser window.
2. Search Engine Results: Go to your preferred search engine and enter relevant keywords related to coating equipment manufacturers. Look for options that appear on the first few pages of the search results. This indicates that the website is well-optimized and has good visibility.
3. Check SEOquake Data: Click on the SEOquake toolbar and make sure the drop-down menu is set to display data from Google. Scan through the websites you found in the search results, looking for their Alexa Rank. If the website’s ranking falls within the top 10 million, it can be considered reliable. Additionally, you can check the number of indexed pages, domain age, and other relevant statistics provided by SEOquake to get a better idea of the website’s performance and credibility.
By following these steps, you can quickly and effectively determine if a coating equipment manufacturer’s website is reliable based on its ranking and visibility in search engine results. Remember to consider other factors such as customer reviews, certifications, and industry reputation to make a well-informed decision.
Top 10 coating equipments manufacturers in China with each 160 words introduce products,then use markdown create table compare
1. Wuxi Lima Chemical Machinery Co., Ltd.: Wuxi Lima is a renowned manufacturer of coating equipment in China. Their product range includes coating machines, mixers, and filtration systems. These machines offer efficient and precise coating solutions for various industries such as pharmaceutical, chemical, and food processing.
2. Shanghai Rucca Mechanical and Electrical Technology Co., Ltd.: Rucca specializes in manufacturing coating equipment like automatic spray machines and powder coating systems. They provide innovative, reliable, and cost-effective solutions for surface coating requirements across different fields like automotive, electronics, and furniture industries.
3. Guangdong Chuangzhi Intelligent Equipment Co., Ltd.: Chuangzhi is a leading manufacturer of coating equipment in China. Their product portfolio includes spray coating machines, UV curing systems, and drying ovens. These advanced and energy-efficient machines are widely used in industries such as automobile, aerospace, and electronics.
4. Foshan Juyue Automation Equipment Co., Ltd.: Juyue Automation offers a wide range of coating equipment, including spray coating machines, electrostatic coating systems, and paint booths. These high-quality machines are designed to ensure excellent coating performance and enhance productivity in industries like furniture, metal fabrication, and plastic molding.
5. Zhejiang Meibao Industrial Technology Co., Ltd.: Meibao specializes in manufacturing coating equipment for the chemical industry. Their product lineup comprises coating machines, drying and cooling systems, and fluidized bed reactors. These robust and efficient machines enable precise and uniform coating applications in sectors like pharmaceuticals, cosmetics, and agrochemicals.
| Company Name | Products |
| —————————————————– | ——————————————————— |
| Wuxi Lima Chemical Machinery Co., Ltd. | Coating machines, mixers, filtration systems |
| Shanghai Rucca Mechanical and Electrical Technology Co. | Automatic spray machines, powder coating systems |
| Guangdong Chuangzhi Intelligent Equipment Co., Ltd. | Spray coating machines, UV curing systems, drying ovens |
| Foshan Juyue Automation Equipment Co., Ltd. | Spray coating machines, electrostatic systems, paint booths|
| Zhejiang Meibao Industrial Technology Co., Ltd. | Coating machines, drying/cooling systems, fluidized beds |
6. Guangdong Jingzhongjing Industrial Painting Equipment Co., Ltd.: Jingzhongjing manufactures a comprehensive range of industrial painting equipment including automatic spray systems, reciprocators, and paint booths. Their high-performance machines are widely utilized in automotive, aerospace, and machinery manufacturing industries for quality surface finishing.
7. Yangzhou Meida Filling Machinery Co., Ltd.: Meida specializes in the production of coating equipment, including liquid filling machines and automatic capping machines. These versatile machines are widely used in industries such as pharmaceuticals, cosmetics, and food processing for accurate and efficient coating applications.
8. Hangzhou Color Powder Coating Equipment Co., Ltd.: Color Powder Coating Equipment is a leading manufacturer of powder coating systems, spray guns, and powder coating booths. Their state-of-the-art equipment ensures superior surface finishing and excellent adhesion for applications in industries like architecture, furniture, and automotive.
9. Shenzhen Anfengtai Coating Equipment Co., Ltd.: Anfengtai is known for its expertise in manufacturing coating equipment such as electrostatic spray guns, powder coating machines, and sandblasting equipment. Their reliable and user-friendly machines are widely employed in industries like metal fabrication, electronics, and automotive for high-quality and durable coatings.
10. Jiangmen Pinnxun Metal Coating Equipment Co., Ltd.: Pinnxun Metal Coating Equipment specializes in the production of powder coating systems, curing ovens, and spray booths. These cutting-edge machines offer efficient and precise coating solutions for numerous industries, including automotive, furniture, and electronics.
Table:
| Company Name | Products |
| ————————————————– | —————————————————————————————- |
| Guangdong Jingzhongjing Industrial Painting… | Automatic spray systems, reciprocators, paint booths |
| Yangzhou Meida Filling Machinery Co., Ltd. | Liquid filling machines, automatic capping machines |
| Hangzhou Color Powder Coating Equipment Co., Ltd. | Powder coating systems, spray guns, powder coating booths |
| Shenzhen Anfengtai Coating Equipment Co., Ltd. | Electrostatic spray guns, powder coating machines, sandblasting equipment |
| Jiangmen Pinnxun Metal Coating Equipment Co., Ltd. | Powder coating systems, curing ovens, spray booths |
In summary, China has a wide range of top-quality coating equipment manufacturers catering to various industries such as pharmaceuticals, automotive, electronics, and furniture. These companies offer advanced and reliable machines that ensure precise and efficient coating applications. Whether it’s spray coating machines, powder coating systems, or complete coating lines, these manufacturers strive to provide innovative solutions to meet diverse industry requirements.
Background Research for coating equipments manufacturers Companies in China, use qcc.com archive.org importyeti.com
Coating equipment manufacturers are companies that specialize in the production and supply of machinery and equipment used for coating various surfaces. In China, there are several well-established manufacturers in this industry. In order to gather information about these manufacturers, the following sources can be utilized: qcc.com, archive.org, and importyeti.com.
Qcc.com is a comprehensive business directory that provides information about companies registered in China. Through this platform, one can access details such as company profiles, contact information, and product listings of coating equipment manufacturers. This resource can be helpful in understanding the background, capabilities, and product offerings of different manufacturers in China.
Archive.org is a digital library that provides access to archived websites. It can be used to explore past versions of manufacturer websites. By reviewing these archived websites, one can gain insight into the historical development of coating equipment manufacturers in China, their previous products, and any significant changes or advancements over time.
Importyeti.com is a platform specifically focused on import-export data. This resource can provide information about the export activities of coating equipment manufacturers in China. By utilizing this platform, one can gain an understanding of the markets these manufacturers serve, the frequency and volume of their exports, and the countries they primarily export to. This information can be useful in evaluating the reputation and popularity of different manufacturers in the international market.
It is important to note that while these sources can provide valuable information, it is advisable to cross-reference the data collected from multiple sources to ensure accuracy and validity. Additionally, reaching out to industry associations, trade shows, and conducting direct communication with manufacturers can provide further insights into the background and capabilities of coating equipment manufacturers in China.
Leveraging Trade Shows and Expos for coating equipments Sourcing in China
Trade shows and expos provide a unique opportunity for businesses to source coating equipment from China. These events bring together a large number of manufacturers, suppliers, and industry professionals under one roof, making it convenient for companies looking to identify and connect with potential suppliers.
When it comes to coating equipment sourcing in China, trade shows and expos offer several advantages. Firstly, they allow businesses to explore a wide range of products, enabling them to compare features, specifications, and prices in person. This hands-on experience helps to assess the quality and functionality of different coating equipment options.
Secondly, trade shows and expos offer an excellent platform for networking and establishing business relationships. Companies can have direct interaction with manufacturers and suppliers, enabling them to ask questions, gather detailed information, and negotiate contracts. This face-to-face communication helps build trust and confidence in the chosen supplier.
Additionally, attending trade shows and expos also provides opportunities to stay updated with the latest trends, innovations, and advancements in the coating equipment industry. Companies can observe live demonstrations, participate in workshops, and attend seminars to enhance their understanding of the market and gain valuable insights.
To make the most out of trade shows and expos for coating equipment sourcing in China, businesses should plan and prepare in advance. This includes researching and identifying relevant trade shows and expos that specifically cater to coating equipment and related industries. Prioritizing these events based on their credibility, reputation, and the number of exhibitors is essential.
Moreover, businesses should allocate sufficient time to visit the trade shows and expos, ensuring they have enough time to explore and interact with potential suppliers. Bringing along a team of professionals specializing in coating equipment or relevant technical expertise can also be beneficial in making informed decisions.
In conclusion, trade shows and expos serve as effective platforms for sourcing coating equipment in China. They offer the advantages of product comparison, direct communication with suppliers, relationship-building, and market insights. By strategically utilizing these events, businesses can optimize their sourcing efforts and find reliable suppliers for their coating equipment needs.
The Role of Agents and Sourcing Companies in Facilitating coating equipments Purchases from China
Agents and sourcing companies play a crucial role in facilitating coating equipment purchases from China. These intermediaries act as a bridge between buyers and manufacturers, ensuring a smooth and efficient procurement process. Here are some key ways in which agents and sourcing companies contribute to the purchasing process:
1. Supplier identification and vetting: Agents and sourcing companies have extensive networks and knowledge of the Chinese market. They help buyers identify reliable and high-quality coating equipment manufacturers that suit their specific requirements. These intermediaries conduct thorough due diligence to vet suppliers, ensuring they meet industry standards and have a track record of producing reliable products.
2. Negotiation and communication: Agents and sourcing companies serve as the main point of contact with the manufacturers. They have experience in negotiating price, terms, and delivery options. These intermediaries bridge any language or cultural gaps, ensuring effective communication and understanding between the buyer and the supplier.
3. Quality control and inspection: Agents and sourcing companies carry out rigorous quality control measures to ensure that the coating equipment meets the buyer’s specifications and quality standards. They conduct factory inspections, product testing, and quality checks throughout the production process, reducing the risk of receiving substandard or defective products.
4. Logistics and shipping: Agents and sourcing companies handle the logistics and shipping process, coordinating the transportation of the purchased coating equipment from the manufacturer’s facility to the buyer’s location. They arrange for packaging, customs clearance, and documentation, ensuring smooth and timely delivery.
5. After-sales support: Agents and sourcing companies provide valuable after-sales support, acting as a liaison between the buyer and the manufacturer for any warranty claims, repairs, or technical assistance required. They ensure prompt resolution of any issues and help maintain a positive buyer-supplier relationship.
In summary, agents and sourcing companies streamline the purchasing process for coating equipment from China by identifying reliable suppliers, facilitating communication and negotiation, ensuring quality control, managing logistics, and providing after-sales support. Their expertise and network in the Chinese market bring efficiency and trust to the procurement process for buyers worldwide.
Price Cost Research for coating equipments manufacturers Companies in China, use temu.com and 1688.com
When it comes to coating equipment manufacturers in China, two popular online platforms that can be utilized for price cost research are temu.com and 1688.com. These platforms provide a wide range of options, allowing users to find the best deals and compare prices from various manufacturers.
At temu.com, users can explore a large database of coating equipment manufacturers and get detailed information about their products and prices. The platform offers a user-friendly interface, making it easy to navigate and search for specific types of coating equipment. From spray booths and powder coating systems to paint mixers and curing ovens, users can find a diverse range of options to meet their needs.
Similarly, 1688.com is another popular online marketplace in China that connects buyers with coating equipment manufacturers. The website offers a vast selection of products, including coating machines, spray guns, coating materials, and more. Users can browse through different suppliers, compare prices, and read customer reviews to make informed decisions.
To conduct price cost research on these platforms, it is recommended to follow these steps:
1. Begin by visiting temu.com and 1688.com.
2. Use the search bar to enter relevant keywords such as “coating equipment manufacturers” or specify the type of equipment you need, such as “powder coating system” or “spray booth.”
3. Refine your search results by filtering based on product specifications, price range, and other requirements.
4. Review the product listings from different manufacturers and compare prices, specifications, and customer reviews.
5. Take note of the prices, additional costs such as shipping fees, minimum order quantities, and payment terms.
6. Reach out to the manufacturers directly through the platform’s messaging system or obtain their contact information for further inquiries.
By utilizing temu.com and 1688.com, researchers can access a wide range of coating equipment options from manufacturers in China. These platforms provide an efficient way to analyze prices, compare offerings, and connect with suppliers, ensuring that users can make informed decisions based on their specific needs and budget.
Shipping Cost for coating equipments import from China
Importing coating equipment from China can incur various shipping costs depending on several factors. The size and weight of the equipment, the shipping method chosen, and additional services required all contribute to the final cost.
When importing coating equipment, air freight and sea freight are the most common shipping methods. Air freight is generally more expensive but faster, while sea freight is more cost-effective but has a longer transit time.
For air freight, the cost is primarily based on the weight and dimensions of the equipment. The heavier and larger the shipment, the higher the shipping cost. Additional charges may apply for fuel surcharges and handling fees. It is essential to consider the packaging of the equipment to minimize its size and weight, potentially reducing the shipping cost.
Sea freight is calculated based on the volume of the shipment, measured in cubic meters (CBM), rather than just weight. The cost varies depending on the departure and destination ports. It is advisable to book a full container load (FCL) if the equipment quantity is sufficient to fill an entire container. Less than container load (LCL) is also available for smaller shipments, but the cost per CBM is typically higher than that of FCL.
Furthermore, there are additional costs involved, such as customs duties, import taxes, and destination fees. These charges vary depending on the country of importation and the type of equipment being imported. It is recommended to consult with a customs broker or freight forwarder to understand the applicable fees and ensure compliance with import regulations.
To minimize shipping costs, it is advisable to compare quotes from multiple freight forwarders and negotiate for the best rates. Consolidating multiple shipments, optimizing packaging, and selecting the most suitable shipping method can also help reduce costs.
In conclusion, the shipping cost for importing coating equipment from China depends on various factors, including the size and weight, shipping method, and additional charges. Careful planning, optimization, and obtaining multiple quotes can help ensure cost-effective shipping.
Compare China and Other coating equipments Markets: Products Quality and Price,Visible and Hidden Costs
China’s coating equipment market is known for its wide range of products, competitive pricing, and both visible and hidden costs. When compared to other markets, several key differences and similarities can be identified in terms of product quality, price, and associated costs.
In terms of product quality, China’s coating equipment market offers a diverse range of options. While some manufacturers may provide high-quality products comparable to those offered in other markets, there can be variations in the overall quality. This variance arises from the presence of numerous manufacturers, ranging from large, established companies to small-scale enterprises with varying levels of expertise and quality control measures. On the other hand, markets in countries like Germany, the United States, or Japan are known for their stringent quality standards and advanced technologies, resulting in consistently high-quality coating equipment options.
Price is another important factor to consider. China’s coating equipment market generally offers competitive pricing due to several factors, such as lower manufacturing costs, economies of scale, and intense market competition. This affordability makes China an attractive option for both domestic and international buyers. In comparison, other markets might have higher price tags due to factors like higher labor costs or research and development investments.
Visible costs, such as the purchase price and maintenance fees, can be relatively similar across markets. However, hidden costs can vary significantly. For instance, import duties, shipping charges, and customs fees can increase the overall cost when purchasing from China for international customers. Additionally, dealing with language barriers, cultural differences, or potential delays in customs clearance can also introduce hidden costs. Conversely, other markets may have their own set of hidden costs, such as higher service charges or stricter regulatory compliance, which may influence the overall purchasing decision.
Overall, China’s coating equipment market offers a wide array of products at competitive prices. However, buyers should carefully consider the varying levels of product quality, as well as additional visible and hidden costs associated with purchasing from China. Other markets, known for their stringent quality standards, might offer higher-priced options with fewer hidden costs. Consequently, potential buyers should evaluate their specific requirements and consider these aspects to make an informed decision concerning product quality, price, and overall costs.
Understanding Pricing and Payment Terms for coating equipments: A Comparative Guide to Get the Best Deal
When it comes to purchasing coating equipment, understanding pricing and payment terms is essential to ensure you get the best deal. This comparative guide aims to provide you with a comprehensive overview of the factors you should consider.
1. Equipment Price: The first and most obvious factor to consider is the price of the coating equipment itself. It is important to compare prices from different vendors to ensure you are getting the best value for your money. However, don’t solely focus on the price, as quality and durability are equally crucial.
2. Additional Costs: Apart from the equipment price, there may be additional costs associated with purchasing and maintaining the coating equipment. Consider factors such as installation, shipping, spare parts, maintenance, and any potential training fees. Understanding these costs beforehand will help you make an accurate cost assessment.
3. Payment Terms: Different vendors may offer varying payment terms, so it is crucial to assess the options available. Some common payment terms include upfront payment, installment plans, or leasing options. Consider your budget and the long-term cost implications before selecting the most suitable payment term.
4. Financing Options: If the upfront cost of the coating equipment seems unaffordable, enquire about financing options available. Some vendors offer financing plans with favorable interest rates. Consider the financing terms, including the down payment, interest rate, and repayment period, to evaluate its feasibility for your business.
5. Warranty and After-Sales Support: Coating equipment is a significant investment, so it is vital to understand the warranty provided by the vendor. Analyze the duration of the warranty, what it covers, and the reputation of the vendor for after-sales support. A reliable warranty can save you from unexpected repair costs.
6. Return on Investment (ROI): Lastly, estimate the ROI by considering factors such as the lifespan of the equipment, maintenance costs, efficiency gains, and potential revenue increase. This analysis will help you determine the long-term benefits and determine if the purchase is financially viable.
In conclusion, to get the best deal on coating equipment, compare prices from multiple vendors, consider additional costs, evaluate payment terms, explore financing options, assess warranty and after-sales support, and calculate the ROI. Armed with this knowledge, you can confidently select the most cost-effective and reliable coating equipment for your business.
Chinese Regulations and Industry Standards Certifications for coating equipments,Import Regulations and Customs for coating equipments from China
China, being one of the leading manufacturers and exporters of coating equipment, has stringent regulations and industry standards certifications required for such products. These regulations ensure the quality, safety, and environmental compliance of coating equipment. One of the key certifications is the China Compulsory Certification (CCC), which is mandatory for a wide range of products, including coating equipment.
To obtain the CCC certification, manufacturers need to meet specific technical requirements and undergo testing and evaluation by authorized certification bodies. The certification covers product safety, electromagnetic compatibility, as well as other technical parameters. It is essential for manufacturers to comply with CCC regulations before exporting coating equipment from China.
In addition to CCC, there are various industry standards that coating equipment manufacturers need to meet. These standards include the China National Standard (GB), which sets benchmarks for product quality, performance, and safety. Compliance with these standards is crucial for manufacturers to ensure their products are in line with industry requirements.
When it comes to importing coating equipment from China, importers must also abide by certain regulations and customs procedures. Firstly, they need to ensure that the selected suppliers have obtained the necessary certifications, such as CCC or other relevant industry certifications. This helps confirm that the products meet the required standards and comply with Chinese regulations.
Importers should also be aware of customs regulations to avoid any potential delays or issues. They need to provide accurate and detailed product information to customs authorities, including descriptions, values, and relevant certifications. Moreover, import duties and taxes may be applicable based on the category and value of the coating equipment being imported. Understanding these customs procedures and regulations is crucial to streamline the import process and avoid any unforeseen complications.
In conclusion, Chinese regulations and industry standards certifications play a vital role in ensuring the quality and safety of coating equipment. Compliance with CCC and other relevant certifications is essential for manufacturers, while importers need to be aware of customs regulations and procedures to successfully import coating equipment from China.
Sustainability and Environmental Considerations in coating equipments Manufacturing
In recent years, sustainability and environmental considerations have become increasingly important in the manufacturing industry, including the coating equipment sector. Manufacturers of coating equipment have recognized the need to minimize their environmental impact, conserve resources, and support sustainable practices throughout the entire product lifecycle.
One key aspect of sustainability in coating equipment manufacturing is the efficient use of energy. Companies are investing in research and development to develop energy-efficient designs and technologies, aiming to reduce the carbon footprint associated with manufacturing operations. This includes incorporating energy-saving features in the equipment itself, optimizing production processes, and utilizing renewable energy sources wherever possible.
Another crucial consideration is the reduction of waste and the promotion of recycling. Manufacturing processes often generate waste materials such as scrap metal, packaging materials, and solvent residues. To address this, coating equipment manufacturers are implementing waste reduction strategies, including recycling programs, to minimize the amount of waste sent to landfills. Additionally, companies are exploring ways to reuse materials and employ sustainable packaging solutions.
Water usage is another significant concern in coating equipment manufacturing. Manufacturers are improving water management practices by implementing water recycling systems and reducing water consumption during production. Moreover, they are investing in research and development to develop water-based coating technologies that are less harmful to the environment compared to solvent-based alternatives.
Furthermore, sustainable sourcing and supply chain management are critical components of sustainability in coating equipment manufacturing. Manufacturers are partnering with suppliers who adhere to environmentally responsible practices, such as using sustainable raw materials and reducing their own carbon footprint. This ensures that the entire manufacturing process aligns with sustainable principles and reduces environmental impacts at all stages.
Lastly, education and awareness play a vital role in promoting sustainability in the coating equipment manufacturing sector. Manufacturers are focusing on training their employees about sustainable practices, promoting environmental awareness among customers, and providing resources for sustainable product use and maintenance.
In conclusion, coating equipment manufacturers are increasingly prioritizing sustainability and environmental considerations. By focusing on energy efficiency, waste reduction, water management, sustainable sourcing, and education, these manufacturers are striving to minimize their environmental impact and support a more sustainable future for the industry.
List The Evolution history of “coating equipments”
Coating equipment has undergone a significant evolution throughout history, with advancements in technology and industry demands driving its development. From simple handheld brushes to automated machines, the evolution of coating equipment has revolutionized various industries.
The earliest forms of coating can be traced back to the ancient Egyptians and their use of natural materials like beeswax and oils to protect and decorate surfaces. Over time, simple brushes and rollers emerged, improving the efficiency and ease of coating application.
In the late 19th century, the introduction of spray painting marked a major breakthrough in coating technology. Initially, spray guns were manually operated, but soon, compressed air was used to atomize the paint, providing more uniform and precise application. This advancement transformed various industries, including automotive and manufacturing, enabling faster and more efficient coating processes.
The 20th century witnessed further developments in coating equipment, particularly with the emergence of electrostatic spraying in the 1940s. Electrostatic guns charged paint particles with electricity, resulting in a more controlled and targeted coating application, minimizing waste and improving efficiency.
In the 1980s, advancements in robotic technology led to the incorporation of automation in coating equipment. Robotic coating systems offered precise control and consistent application, reducing human error and increasing productivity. This innovation proved particularly beneficial in industries that required repetitive and labor-intensive coating processes.
As industry demands continued to evolve, so did coating equipment. Developments in powder coating technology gained momentum in the late 20th century. Powder coating involves spraying charged particles onto the surface to be coated, which are then cured through heat, resulting in a durable finish. This method provided superior protection, aesthetics, and environmental benefits compared to traditional liquid coatings.
In recent years, coating equipment has integrated advanced technologies like nanotechnology. Nanocoatings, consisting of nanoparticles, offer enhanced durability, corrosion resistance, and other specific properties depending on the application requirements.
Overall, the evolution of coating equipment has been driven by the need for increased efficiency, precision, and sustainability in various industries. From manual brushes to automated robotic systems and innovative nanocoatings, coating equipment continues to evolve to meet the evolving demands of the modern world.
The Evolution and Market Trends in coating equipments Industry
The coating equipments industry has witnessed significant evolution and market trends in recent years. With advancements in technology and increasing demand for efficient and high-quality coating processes, the industry has transformed to meet these requirements.
One of the key developments in coating equipments is the adoption of automation and robotics. This trend has revolutionized the industry by enabling faster and more precise coating processes. Robotic systems are capable of handling complex tasks and provide uniform coating application, thereby improving product quality and reducing labor costs. Automation also ensures worker safety by minimizing exposure to hazardous substances used in coatings.
Another important trend in the coating equipments industry is the shift towards eco-friendly and sustainable solutions. With growing concerns about environmental impact, manufacturers are now focusing on developing coating equipments that use water-based or powder coatings instead of harmful solvent-based options. These eco-friendly coatings not only reduce greenhouse gas emissions but also comply with stringent regulations.
In addition, there is a growing demand for customization and flexibility in coating equipments. Manufacturers are increasingly offering modular systems that can be easily modified or upgraded to meet specific customer requirements. This allows companies to adapt to changing coating needs without the need for complete equipment replacement, resulting in cost savings.
Furthermore, the adoption of digitalization and data analytics has become essential in the coating equipments industry. By integrating smart sensors and software, manufacturers can monitor and optimize coating processes in real-time. This real-time monitoring enables early identification of defects or variations, reducing waste and improving overall efficiency.
Going forward, the coating equipments industry is expected to see further advancements in areas such as nano-coatings, 3D printing, and application-specific coating solutions. Additionally, the industry will continue to focus on sustainable and environmentally-friendly coatings to meet the growing demand for greener practices.
In conclusion, the coating equipments industry has evolved significantly to meet the demands of the market. The adoption of automation, eco-friendly coatings, customization, and digitalization has transformed the industry and will continue to drive its growth in the future.
Custom Private Labeling and Branding Opportunities with Chinese coating equipments Manufacturers
Chinese coating equipment manufacturers offer a multitude of custom private labeling and branding opportunities. These manufacturers are experienced in producing high-quality coating equipment and can help businesses establish their own unique brand in the industry. The process of private labeling involves incorporating a company’s logo, design, and other branding elements onto the equipment.
Through private labeling, businesses can differentiate their products from competitors, enhance brand recognition, and establish a distinct identity in the market. Chinese manufacturers provide extensive customization options, allowing businesses to tailor the coating equipment to their specific requirements. This includes selecting the desired color, design, materials, and other features to align with the brand’s identity.
Moreover, Chinese coating equipment manufacturers offer branding opportunities by providing customized packaging options. Businesses can have their brand name, logo, and relevant information printed on the packaging, creating a cohesive and professional look. This not only enhances brand visibility but also ensures that the product stands out on store shelves or in the online marketplace.
Partnering with Chinese manufacturers for private labeling and branding opportunities offers numerous benefits. These manufacturers have the expertise, technology, and production capabilities to meet high-quality standards while delivering cost-effective solutions. Their vast experience in producing coating equipment for international clients ensures that they understand the importance of maintaining consistent branding across different markets.
In conclusion, Chinese coating equipment manufacturers provide businesses with custom private labeling and branding opportunities. By leveraging these services, businesses can establish their own unique brand identity, differentiate their products, enhance brand recognition, and gain a competitive edge in the global market. These manufacturers offer extensive customization options, including branding elements on the equipment and personalized packaging options, ensuring a cohesive and professional look.
Tips for Procurement and Considerations when Purchasing coating equipments
When purchasing coating equipment for your business or project, there are several important considerations to keep in mind. These tips can help ensure that you make an informed decision and select the right equipment for your specific needs.
1. Define your requirements: Before starting your search, clearly define the coating requirements for your application. Consider factors such as the type of coating material, desired coating thickness, production volume, and any specific features or capabilities you need.
2. Research reliable suppliers: Look for suppliers with a proven track record in manufacturing and supplying coating equipment. Research their reputation, customer reviews, and certifications to ensure you are dealing with a reliable and reputable company.
3. Quality and durability: Check the quality of the equipment to ensure it is durable and will stand up to the demands of your application. Look for equipment made with high-quality materials that can withstand the coating process and any external factors that may impact its performance.
4. Consider ease of use: Choose equipment that is user-friendly and easy to operate and maintain. Complex equipment may require extensive training or specialized knowledge, adding to your costs and operational complexity.
5. Compatibility and customization: Ensure that the equipment you choose is compatible with the coating materials you plan to use. Additionally, consider if any customization or modifications are required to meet your specific needs.
6. Energy efficiency: Look for equipment that is energy-efficient to help reduce operating costs and minimize environmental impact. Consider features such as automatic shut-off, energy-saving modes, or systems that reduce waste.
7. Warranty and after-sales support: Inquire about the warranty provided with the equipment and the level of after-sales support offered by the supplier. A comprehensive warranty and responsive customer service can provide peace of mind and assistance if any issues arise.
8. Total cost of ownership: Consider not only the initial purchase price but also the long-term cost of ownership. Evaluate factors such as maintenance requirements, consumables, and energy consumption to get a clear understanding of the ongoing costs associated with the equipment.
9. Safety features: Ensure the equipment has adequate safety features to protect operators and meet industry standards. Look for features like emergency stop buttons, safety interlocks, and proper ventilation systems.
10. Training and support: Inquire about the availability of training programs or resources for operators to ensure they can effectively and safely use the equipment. Adequate training and ongoing support can help optimize performance and enhance operational efficiency.
By considering these tips and conducting thorough research, you can confidently select the most suitable coating equipment that meets your requirements and maximizes your return on investment.
FAQs on Sourcing and Manufacturing coating equipments in China
Q: What are the benefits of sourcing and manufacturing coating equipments in China?
A: Sourcing and manufacturing coating equipments in China offer several benefits. Firstly, China has a well-established manufacturing infrastructure and is known for its low production costs, which can lead to significant cost savings for businesses. Additionally, China has a large number of experienced and skilled manufacturers and suppliers in the coating equipment industry, offering a wide range of options and customization possibilities. The country also has access to abundant raw materials, facilitating the production process. Lastly, China’s strong logistical network and efficient supply chain management make it easier to ship and distribute coating equipment globally.
Q: How to find reliable suppliers and manufacturers for coating equipments in China?
A: Finding reliable suppliers and manufacturers in China requires thorough research and due diligence. One effective way is to attend industry trade shows and exhibitions in China, where you can directly meet and evaluate potential suppliers. Online platforms such as Alibaba, Made-in-China, and Global Sources also provide a vast directory of suppliers and user reviews to help in the selection process. It is important to verify the supplier’s legitimacy, such as checking their business license and certifications. Requesting samples, conducting factory visits, and having direct communication with suppliers can also help assess their reliability and quality standards. Lastly, working with a sourcing agent or a reputable third-party inspection company can provide an added layer of assurance.
Q: What factors should be considered when sourcing and manufacturing coating equipments in China?
A: Several factors must be considered when sourcing and manufacturing coating equipments in China. Quality control is of utmost importance, so it is crucial to have a clear understanding of the desired specifications and requirements for the equipment. Intellectual property protection should also be taken into account, as China has been known for intellectual property infringement issues. Therefore, ensuring proper contracts and agreements are in place is necessary. Furthermore, considering the manufacturing capabilities and capacity of suppliers, their production lead time, and after-sales services are vital for a successful sourcing process. It is also important to stay updated with any regulatory changes and compliance requirements, which may affect importing and using specific coating equipment.
Q: Are there any risks or challenges involved in sourcing and manufacturing coating equipments in China?
A: While sourcing and manufacturing coating equipments in China offer numerous advantages, there are certain risks and challenges to be mindful of. The language and cultural barriers can sometimes lead to miscommunication or misunderstandings in the production process. Intellectual property protection can be a concern, so taking appropriate legal measures and working with reputable manufacturers is advised. Quality control can also be a challenge; therefore, careful selection of suppliers and implementing effective quality control measures is necessary. Additionally, the distance and time zone differences may present logistical challenges when it comes to communication and coordination. It is important to have a robust supply chain management system in place to mitigate any potential risks.
Why contact sourcifychina.com get free quota from reliable coating equipments suppliers?
Sourcifychina.com may receive a free quota from reliable coating equipment suppliers for several reasons. Firstly, offering a free quota allows coating equipment suppliers to showcase their products and services to a broader audience. By partnering with Sourcifychina.com, they can increase their visibility and attract potential customers who are in need of coating equipment.
Secondly, providing a free quota allows coating equipment suppliers to establish themselves as trusted and reliable sources within the industry. By showcasing their expertise and professionalism, suppliers can build credibility and gain the trust of potential customers. This can subsequently lead to long-term relationships and increased business opportunities.
Moreover, offering a free quota through Sourcifychina.com enables coating equipment suppliers to access a larger customer base. Sourcifychina.com is a platform that connects buyers and suppliers, making it an effective channel for reaching out to a wide range of potential customers. By utilizing this platform, suppliers can expand their market reach and increase their chances of finding potential buyers.
Additionally, offering a free quota can be seen as a marketing strategy for coating equipment suppliers. It allows them to differentiate themselves from competitors and attract potential customers by offering value-added services. By providing a free quota, suppliers demonstrate their commitment to customer satisfaction and their willingness to go the extra mile to meet their needs.
In conclusion, coating equipment suppliers may provide a free quota to Sourcifychina.com to increase visibility, establish credibility, access a larger customer base, and differentiate themselves from competitors. It is a marketing strategy aimed at attracting potential customers and building long-term business relationships.