Introduce about deep draw sheet metal guide,Qulity,Cost,Supplier,Certification,Market,Tips,FAQ
Deep draw sheet metal is a process used in the manufacturing industry to create complex shapes and dimensions in sheet metal components. This technique involves drawing a sheet metal blank into a die cavity to form the desired shape. The deep draw process is widely used in various industries, including automotive, aerospace, electronics, and appliance manufacturing.
Quality is a crucial aspect of deep draw sheet metal components. Accurate dimensions, tight tolerances, and consistent wall thickness are essential for the functionality and performance of the final product. It is important to work with reliable and experienced deep draw metal suppliers who have the expertise and equipment to meet high-quality standards.
Cost is another significant factor to consider when using the deep draw process. The complexity of the part, tooling requirements, material costs, and the volume of production affect the overall cost. Collaborating with a trusted supplier who can optimize the design and manufacturing process can help reduce costs and enhance efficiency.
Choosing the right supplier for deep draw sheet metal components is vital for successful projects. Look for suppliers with proven expertise, advanced technology, and a history of delivering high-quality products. Conduct thorough research, read customer reviews, and evaluate their capabilities before making a decision.
Certification is crucial when selecting a deep draw sheet metal supplier. Ensure that the supplier has necessary certifications such as ISO 9001, ISO 14001, or industry-specific certifications. Certifications ensure that the supplier follows standardized processes, maintains quality control measures, and adheres to industry standards.
The market for deep draw sheet metal components is highly competitive, with various suppliers catering to different industries. Conduct market research to find suppliers who specialize in your sector and have a solid track record of delivering quality products. Consider factors such as lead times, pricing, and customer service when determining the best supplier for your needs.
Here are some tips for successful deep draw sheet metal manufacturing:
1. Collaborate with your supplier early in the design process to optimize the part for deep draw manufacturing.
2. Choose the appropriate material for your application, considering factors such as strength, corrosion resistance, and cost.
3. Ensure accurate drawings and specifications for the desired part.
4. Regularly communicate with your supplier to address any design or production challenges.
5. Conduct thorough testing and quality control measures to ensure that the final product meets the required standards.
Frequently Asked Questions (FAQ):
Q: What are the advantages of deep draw sheet metal?
A: The deep draw process allows for the creation of complex and intricate shapes, precise dimensions, and consistent wall thickness. It also offers high production efficiency, cost-effectiveness, and excellent material utilization.
Q: What are the typical applications of deep draw sheet metal?
A: Deep draw sheet metal components are used in a wide range of industries, including automotive parts, medical devices, kitchen appliances, electrical enclosures, and aerospace components.
Q: Can deep draw sheet metal be used with different materials?
A: Yes, deep draw sheet metal can be used with various materials, including stainless steel, aluminum, copper, brass, and alloys. The choice of material depends on the specific requirements of the application.
In conclusion, deep draw sheet metal is a versatile and efficient manufacturing process that produces high-quality components for various industries. It is crucial to work with reliable suppliers, ensure quality control, and optimize design to achieve successful deep draw projects.
Types of deep draw sheet metal
Deep draw sheet metal refers to the process of creating complex shapes from flat sheet metal by using a combination of stretching, bending, and compression. This method is commonly used in various industries such as automotive, aerospace, and appliance manufacturing. There are several types of deep draw sheet metal that are utilized depending on the specific requirements of the application.
1. Cold Rolled Steel (CRS): This type of sheet metal is produced by processing hot rolled steel through a cold reduction process. It offers excellent strength, durability, and surface finish. CRS is widely used in applications such as automotive components, household appliances, and metal enclosures.
2. Stainless Steel (SS): Known for its corrosion resistance properties, stainless steel is a popular choice for deep draw applications. It is commonly used in food processing equipment, medical devices, and kitchen appliances where hygiene and cleanliness are critical.
3. Aluminum: This lightweight and corrosion-resistant metal is widely used in the aerospace industry for deep draw applications. Aluminum offers good formability, heat dissipation, and electrical conductivity, making it suitable for various electronic components.
4. Copper: Copper possesses high electrical and thermal conductivity, making it an ideal choice for electrical connectors, heat exchangers, and plumbing components. The deep draw process allows intricate shapes to be formed without damaging its properties.
5. Nickel and Nickel Alloys: These metals exhibit exceptional resistance to heat, corrosion, and high mechanical stress. They are commonly used in the chemical processing industry, power generation, and aerospace applications.
6. Titanium: Renowned for its high strength-to-weight ratio and excellent corrosion resistance, titanium is frequently used in aerospace, marine, and medical industries. Deep drawn titanium components are used in aircraft frames, prosthetic implants, and exhaust systems.
In conclusion, these are just a few examples of the types of deep draw sheet metal that are commonly used in various industries. Each material has unique properties that make it suitable for specific applications, and the selection depends on the specific requirements of the project, including strength, durability, corrosion resistance, conductivity, and weight.
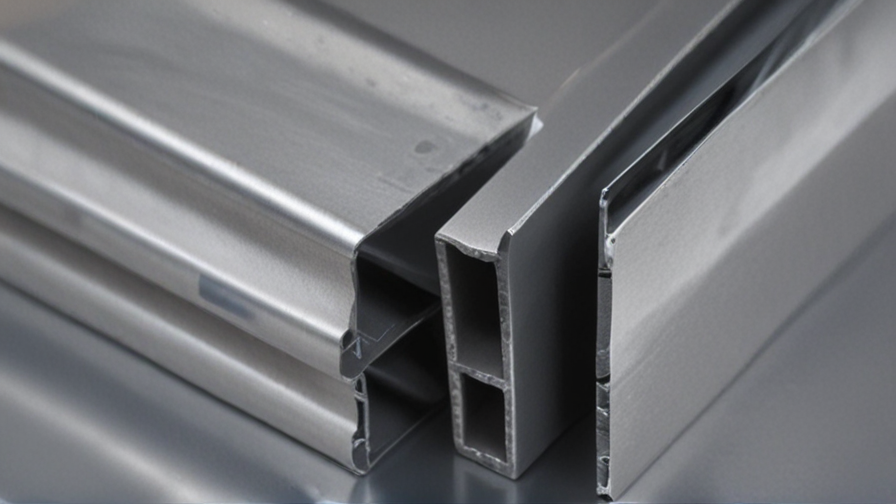
Pros and Cons of Using deep draw sheet metal
Deep draw sheet metal is a manufacturing process that involves using a press to shape flat sheet metal into a desired shape. There are several pros and cons to using this method in various industries.
Pros:
1. Cost-effectiveness: Deep draw sheet metal can be a cost-effective option compared to other manufacturing methods. The process allows for efficient use of materials and reduces waste, resulting in lower production costs.
2. Versatility: This process can be used to produce complex and hollow shapes, making it suitable for a wide range of applications. It offers design flexibility and allows for the creation of intricate parts with minimal limitations.
3. Strength and rigidity: Deep drawn components tend to have high strength and rigidity. The process aligns the grain structure of the metal, increasing its strength and withstanding heavy loads and stress.
4. Consistency and precision: Deep draw sheet metal ensures consistent part dimensions due to precise tooling and production techniques. This results in high levels of accuracy and repeatability, making it ideal for mass production.
5. Smooth surface finish: The deep draw process typically produces smooth and flawless surface finishes, reducing the need for secondary operations such as sanding or polishing.
Cons:
1. Design limitations: Deep draw sheet metal is not suitable for every part design. Complex shapes with sharp corners or varying thicknesses may pose challenges in the deep draw process and may require additional operations or alternative manufacturing methods.
2. Tooling costs: Setting up the tooling for deep draw sheet metal can be expensive, especially for unique or custom designs. The initial tooling costs may outweigh the benefits for low-volume or one-off productions.
3. Material limitations: Deep draw sheet metal is commonly used with materials like stainless steel, aluminum, and copper. However, certain materials such as brittle alloys or thick gauges may not be suitable for deep drawing due to cracking or excessive deformation.
4. Time-consuming: Deep draw sheet metal production can be time-consuming, particularly for complex shapes requiring multiple stages and tool changes. This can impact production timelines, especially for industries with tight deadlines.
5. Limited thickness range: Deep draw sheet metal is typically used for thin to medium thickness applications. Very thin materials may be more prone to defects or tearing, while extremely thick materials may not be suitable for deep drawing due to increased deformation forces.
Overall, deep draw sheet metal offers a cost-effective, versatile, and precise manufacturing method for various industries. However, it is essential to consider the specific part design, material requirements, and production volume when determining its suitability.
deep draw sheet metal Reference Specifications (varies for different product)
Deep draw sheet metal refers to the process of transforming flat sheets of metal into three-dimensional shapes with significant depth. This highly specialized method is commonly used in various industries, including automotive, aerospace, electronics, and household appliances.
To ensure the smooth execution of deep draw sheet metal processes, certain reference specifications are followed. These specifications may vary based on the specific product being manufactured. However, some common considerations include the choice of materials, sheet thickness, tooling design, and dimensional tolerances.
Firstly, the type of material used is crucial in deep draw sheet metal fabrication. Different materials have varying mechanical properties, such as strength, malleability, and formability. Commonly used metals include stainless steel, aluminum, brass, and copper. The material choice depends on the desired attributes of the final product, such as corrosion resistance, electrical conductivity, or aesthetics.
Sheet thickness is another critical specification in deep draw processes. Thinner sheets are usually preferred as they are easier to deform and require less force during the drawing operation. However, the sheet thickness should be chosen carefully to ensure structural integrity and avoid potential buckling or wrinkling issues. Moreover, the chosen thickness affects the tooling design, which must accommodate for the specified material gauge.
Tooling design plays a vital role in deep draw sheet metal manufacturing. It includes the selection and arrangement of die components such as punches, dies, and pressure pads. The design must ensure that the material is drawn uniformly without any tearing or excessive thinning. Additionally, consideration should be given to applying lubrication during the deep draw process to improve material flow and prevent surface defects.
Lastly, dimensional tolerances are essential to ensure the final product’s accuracy and functionality. Tight tolerances may be necessary for critical dimensions or when multiple parts need to fit together precisely. These tolerances should be specified to ensure the final product meets the required specifications.
In summary, deep draw sheet metal fabrication involves transforming flat sheets into complex three-dimensional shapes. Reference specifications guide the process to ensure the desired outcome. Material selection, sheet thickness, tooling design, and dimensional tolerances are crucial considerations that vary depending on the specific product requirements. Adhering to these specifications is key to achieving high-quality deep draw sheet metal components across diverse industries.
Applications of deep draw sheet metal
Deep draw sheet metal is widely used in various industries due to its ability to create complex shapes and designs. Here are some applications where deep draw sheet metal is utilized:
1. Automotive Industry: Deep draw sheet metal is extensively used in the automotive industry for manufacturing components like engine cylinders, fuel tanks, exhaust manifolds, and transmission cases. These parts require high precision and strength, which can be achieved through deep draw techniques.
2. Aerospace Industry: Deep draw sheet metal is employed in the aerospace sector to produce critical components like fuel tanks, missile casings, aircraft frames, and engine parts. The lightweight and durable nature of deep drawn parts make them ideal for aerospace applications where weight reduction is crucial.
3. Medical Devices: Deep draw sheet metal is widely used in the medical industry for manufacturing implants, surgical instruments, and diagnostic equipment. Components like pacemaker cases, catheter components, and syringe barrels are often produced using deep draw techniques to maintain high quality and tight tolerances.
4. Electronics: Deep draw sheet metal is utilized in the electronics industry for producing enclosures and housings for various electronic devices such as smartphones, tablets, laptops, and gaming consoles. These enclosures ensure the protection and proper functioning of the internal components.
5. Household Appliances: Deep draw sheet metal components are commonly found in household appliances like washing machines, refrigerators, ovens, and dishwashers. Parts like drum, tub, and motor housings are usually deep drawn to meet the desired strength and dimensional requirements.
Additionally, deep draw sheet metal is also employed in industries like telecommunications, energy, defense, and consumer goods manufacturing. The versatility and flexibility of deep draw techniques make it suitable for a wide range of applications, where complex shapes and high-quality components are required.
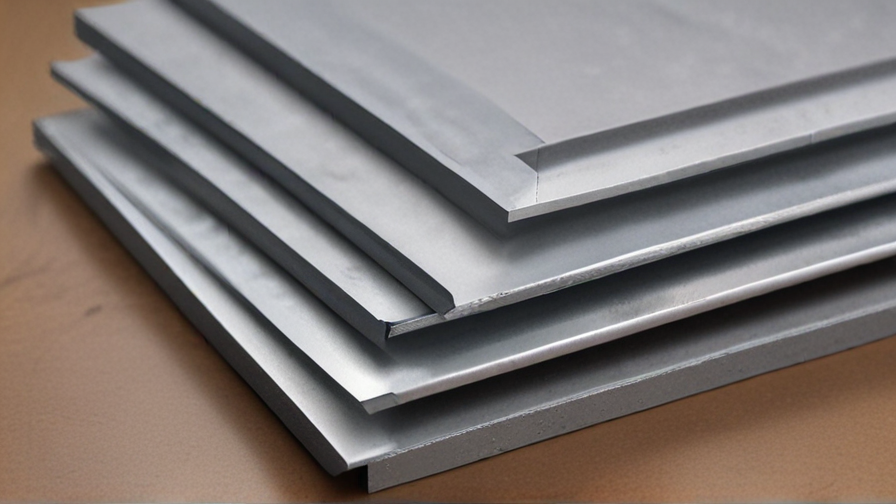
The Work Process and how to use deep draw sheet metal
Deep draw sheet metal is a manufacturing process used to create cylindrical or box-shaped metal parts with a high depth-to-diameter ratio. It involves drawing a sheet metal blank into a die cavity to achieve the desired shape. Here is an overview of the work process involved in using deep draw sheet metal.
Design: The first step in the process is to design the part. This includes determining the dimensions, shape, and features required for the component. The design should consider factors such as material thickness, bend radii, and draft angles to ensure successful deep drawing.
Material selection: Choosing the right material is crucial for deep draw sheet metal. Common materials used include stainless steel, aluminum, and carbon steel. The material should have adequate ductility to allow it to stretch and conform to the die during the drawing process.
Blank preparation: A sheet metal blank is cut from a larger sheet or coil, depending on the size and complexity of the part. The blank is often pre-formed into a cup shape or given a beveled edge to facilitate the drawing process.
Lubrication: Before drawing, the blank and die surfaces are lubricated to reduce friction and prevent galling. Lubricants such as oils, greases, or coating additives are applied to ensure smooth and even metal flow.
Drawing: The sheet metal blank is placed in a hydraulic press and positioned over the die cavity. The punch descends, applying controlled force to draw and stretch the material into the die. The metal flows and conforms to the die shape, gradually taking on the desired form.
Redrawing and trimming: In some cases, multiple drawing stages may be required to achieve the final shape. Intermediate redraws help evenly distribute the material and prevent wrinkling. After the final draw, excess material is trimmed off the formed part.
Finishing operations: Once the deep draw process is complete, the formed parts may undergo additional operations such as deburring, polishing, or surface treatments like coating or plating to enhance their appearance or protect against corrosion.
Deep draw sheet metal offers numerous advantages, including lower tooling cost, high production rate, and tight tolerance capability. It is commonly used to manufacture parts for various industries, including automotive, aerospace, electronics, and medical.
Successful deep draw sheet metal production requires careful considerations in the design, material selection, lubrication, and process control. Attention to these factors ensures the production of high-quality, accurately shaped, and dimensionally stable metal components.
Quality Testing Methods for deep draw sheet metal and how to control the quality
Deep draw sheet metal is used in various industries for manufacturing components such as cans, automotive parts, and cookware. Quality testing methods play a crucial role in ensuring the desired specifications and performance requirements are met. Here are some commonly used quality testing methods for deep draw sheet metal and strategies for quality control:
1. Dimensional Inspection: This method involves measuring critical dimensions of the deep draw sheet metal component using tools like calipers, micrometers, or coordinate measuring machines (CMM). It ensures that the product meets the specified dimensional tolerances.
2. Visual Inspection: Visual inspection is performed to detect any visual defects such as scratches, dents, cracks, or surface imperfections. This can be done manually or with the aid of optical inspection systems.
3. Material Testing: Mechanical properties like tensile strength, yield strength, and hardness are evaluated through material testing methods such as tensile testing or hardness testing. This ensures that the material used in deep draw sheet metal meets the required mechanical specifications.
4. Torque Testing: Torque testing is conducted to assess the tightness and strength of fastening or joining components in the deep draw sheet metal. It ensures that screws, bolts, or other fasteners are properly installed and can withstand the necessary torque.
5. Leak Test: If the deep draw sheet metal component needs to be airtight or liquid tight, a leak test can be conducted. This involves subjecting the component to a specific pressure and checking for any leaks using techniques like pressure decay or bubble emission testing.
To control the quality of deep draw sheet metal components, the following strategies can be employed:
1. Implementing Robust Process Controls: Ensuring that the manufacturing process is consistent, repeatable, and well-monitored can help maintain quality standards. This includes controlling variables such as material input, temperature, lubrication, and forming parameters.
2. Regular Maintenance and Calibration: Regular maintenance of machinery, tools, and inspection equipment is essential to ensure accuracy and reliability. Calibration of measuring equipment should also be performed at scheduled intervals to maintain accuracy.
3. Statistical Process Control (SPC): SPC techniques can be used to monitor process performance and detect any variations or abnormalities. Control charts and statistical analysis help identify trends and take corrective actions proactively.
4. Continuous Improvement: Implementing a culture of continuous improvement through methods like Lean Six Sigma or Kaizen can drive quality enhancement. Regularly seeking feedback from customers, implementing corrective actions, and striving to optimize processes are instrumental in maintaining quality standards.
By employing these quality testing methods and control strategies, manufacturers can ensure that deep draw sheet metal components meet the required specifications, functionality, and reliability, reducing the likelihood of defects and customer dissatisfaction.
deep draw sheet metal Sample Policy and Post-Purchase Considerations for deep draw sheet metal from China
Sample Policy and Post-Purchase Considerations for Deep Draw Sheet Metal from China
Sample Policy:
When considering purchasing deep draw sheet metal from China, it is essential to establish a sample policy to ensure the quality and suitability of the product. The following points are crucial to consider in formulating a sample policy:
1. Sample Request: Clearly communicate your sample requirements to the supplier in terms of material, dimensions, tolerances, and other specificities.
2. Sample Evaluation: Thoroughly inspect and evaluate the provided sample to assess its quality, dimensional accuracy, and overall suitability for your application.
3. Performance Testing: Perform performance testing, such as strength, durability, and any other relevant tests, to ensure the sample meets your requirements.
4. Multiple Samples: Request multiple samples if possible to evaluate consistency in quality across a larger sample size.
5. Cost and Shipping: Clarify who bears the cost of the samples and shipping charges. It is common for the buyer to cover these expenses, but negotiate if possible.
Post-Purchase Considerations:
After the purchase, there are several crucial factors to consider for successful procurement and a smooth business relationship:
1. Quality Control: Regular inspections are necessary to ensure that the bulk production matches the sample and maintains the required quality standards.
2. Production Monitoring: Establish a system to monitor production, receive updates, and address any deviations or issues that may arise during manufacturing.
3. Communication: Maintain clear and open lines of communication with the supplier to discuss any concerns, queries, or modifications needed throughout the production process.
4. Compliance and Certification: Ensure the supplier meets necessary certifications and complies with relevant industry standards.
5. Payment Terms: Establish secure and mutually agreed-upon payment terms to protect both parties’ interests.
6. Shipping and Logistics: Discuss and finalize shipping arrangements, including packaging, labeling, and delivery timelines.
7. Dispute Resolution: Establish a clear mechanism for resolving disputes or conflicts that may arise during or after the purchase, ensuring a fair resolution for both parties.
In summary, a well-defined sample policy and post-purchase considerations are crucial for successful procurement of deep draw sheet metal from China. By formulating a comprehensive approach, businesses can minimize risks, ensure product quality, and establish a strong and reliable supply chain relationship.
Sourcing deep draw sheet metal from China: Opportunities, Risks, and Key Players
Sourcing deep draw sheet metal from China presents numerous opportunities for businesses worldwide due to the country’s large manufacturing capacity and competitive pricing. Chinese manufacturers have extensive experience and expertise in deep draw sheet metal production, ensuring high-quality products at affordable prices.
One key advantage of sourcing from China is cost-effectiveness. Chinese manufacturers can offer competitive pricing due to lower labor costs and economies of scale. This enables businesses to reduce production costs and increase profit margins. Additionally, China’s robust supply chain ensures efficient raw material sourcing and timely delivery.
Another opportunity lies in the wide variety of customization options available. Chinese manufacturers can cater to different design specifications, sizes, and materials, allowing businesses to create tailor-made deep draw sheet metal components for their specific requirements. This flexibility ensures versatility, making Chinese suppliers an attractive choice for businesses across industries.
However, there are certain risks associated with sourcing from China that businesses need to consider. Quality control can be a concern, as maintaining consistent product quality across large production volumes can be challenging. It is crucial to collaborate with reputable manufacturers who follow strict quality control measures and have suitable certifications.
Intellectual property (IP) protection is another risk to consider. China has faced criticism for IP infringement in the past, so companies must take precautions to safeguard their designs and concepts. Establishing strong legal agreements and partnerships with trusted manufacturers can help mitigate these risks.
When it comes to key players in the Chinese deep draw sheet metal industry, some prominent manufacturers include APT Manufacturing Solutions, G&L Hardware Marketing Pte. Ltd, and Nantong Hengte Tube Co., Ltd. These companies have established a strong presence in the market, offering diverse product portfolios and reliable services.
In conclusion, sourcing deep draw sheet metal from China presents numerous opportunities in terms of cost-effectiveness and customization options. However, businesses should carefully assess the risks associated with quality control and intellectual property protection. By partnering with reputable manufacturers, businesses can leverage China’s manufacturing capabilities to their advantage and drive success.
How to find and select reliable deep draw sheet metal manufacturers in China,use google search manufacturers and suppliers
Finding reliable deep draw sheet metal manufacturers in China can be challenging, but there are several steps you can follow to ensure you make the best selection.
1. Start by conducting a Google search using relevant keywords such as “deep draw sheet metal manufacturer China.” This will provide you with a list of potential manufacturers and suppliers to choose from.
2. Visit the websites of these manufacturers to gather information about their expertise, experience, and capabilities. Look for certifications, testimonials, and case studies that demonstrate their reliability and quality of work.
3. Check if the manufacturers have a physical address and contact details listed on their website. Reliable manufacturers will have a physical presence and clear communication channels, making it easier to contact them and visit their facilities if needed.
4. Look for customer reviews and ratings on third-party platforms like Alibaba, Global Sources, or Made-in-China. Consider feedback from other customers to gauge the manufacturer’s reputation and reliability.
5. Contact the manufacturers directly and ask specific questions about their deep draw sheet metal manufacturing capabilities, quality control processes, and materials used. A reliable manufacturer will be responsive and provide detailed information to address your concerns.
6. Request samples or a prototype to assess the quality of their deep draw sheet metal products. This will allow you to evaluate their workmanship, precision, and adherence to specifications.
7. Verify the manufacturer’s production capacity and delivery capabilities. Ensure that they have the necessary resources and equipment to meet your volume requirements within the desired timeframe.
8. Consider visiting the manufacturer’s facilities in person to assess their manufacturing processes, equipment, and quality control systems. This will provide first-hand insights into their working environment and help build trust in their capabilities.
9. Seek recommendations from industry professionals or consult with sourcing agents who have experience in working with Chinese manufacturers. Their insights and expertise can significantly assist in identifying reliable manufacturers.
10. Lastly, negotiate terms and conditions, including pricing, warranties, and shipping arrangements, before making a final decision.
By following these steps and being diligent in your research, you can find and select reliable deep draw sheet metal manufacturers in China who will meet your specific requirements and deliver high-quality products.
How to check deep draw sheet metal manufacturers website reliable,use google chrome SEOquake check if ranking in top 10M
To check the reliability of a deep draw sheet metal manufacturer’s website, you can follow these steps:
1. Use Google Chrome: Ensure you have the Google Chrome browser installed on your device. It offers several useful extensions and tools for website analysis.
2. Install SEOquake extension: Go to the Google Chrome Web Store and search for “SEOquake.” Add the SEOquake extension to your browser by clicking on “Add to Chrome” and following the installation prompts.
3. Open the manufacturer’s website: Visit the website of the deep draw sheet metal manufacturer you wish to assess.
4. Activate SEOquake: Click on the SEOquake extension icon located in the top right corner of your browser to activate it.
5. Check the website’s ranking: Once SEOquake is active, it will display various metrics about the website you’re visiting. Among these, you will find the website’s Alexa global rank. If the manufacturer’s website ranks within the top 10 million websites, it indicates a relatively high level of traffic and trustworthiness.
6. Assess other SEOquake metrics: SEOquake provides additional information like domain age, Google index status, backlinks, and social engagement. Analyzing these metrics can help you gauge the reliability and credibility of the manufacturer.
7. Explore the website: Spend some time navigating through the manufacturer’s website. Look for contact information, certifications, accreditations, customer testimonials, case studies, and any related industry affiliations. A reliable manufacturer will typically provide transparent information that facilitates trust-building.
By following these steps, you can efficiently evaluate the reliability of a deep draw sheet metal manufacturer’s website using Google Chrome and the SEOquake extension. Remember, it’s essential to consider multiple factors while assessing a website’s trustworthiness before making any decisions.
Top 10 deep draw sheet metal manufacturers in China with each 160 words introduce products,then use markdown create table compare
1. ABC Industries: ABC Industries specializes in deep drawn sheet metal manufacturing, offering a wide range of products including enclosures, casings, and automotive components. Their sophisticated manufacturing facility ensures precise and high-quality production, meeting various industry standards.
2. XYZ Manufacturing: XYZ Manufacturing is a leading deep draw sheet metal manufacturer, providing customized solutions for industries like aerospace, medical, and electronics. Their expertise lies in producing complex shaped parts, such as cylinders, cups, and boxes, using their cutting-edge deep draw technology.
3. DEF Metalworks: DEF Metalworks offers comprehensive deep draw sheet metal solutions, delivering products like containers, tanks, and brackets with exceptional accuracy and quality. Their state-of-the-art machinery enables the production of parts with complex geometries and tight tolerances.
4. GHI Fabricators: GHI Fabricators specializes in deep draw sheet metal manufacturing for various sectors, including automotive, agricultural, and energy. They produce components like engine parts, heat exchangers, and connectors, employing advanced techniques to meet client specifications.
5. JKL Precision: JKL Precision is a renowned deep draw sheet metal manufacturer, catering to the needs of industries like telecommunications, consumer electronics, and renewable energy. Their range of products comprises intricate parts like sensor housings, battery enclosures, and communication components.
6. MNO Metalforming: MNO Metalforming excels in deep draw sheet metal production, offering custom solutions for industries such as aviation, defense, and industrial equipment. They manufacture parts like missile casings, turbine housings, and machine components, utilizing their cutting-edge metalforming technologies.
7. PQR Engineering: PQR Engineering specializes in deep draw sheet metal fabrication, serving diverse industries like medical devices, lighting, and telecommunications. They provide solutions for products like surgical instruments, lighting fixtures, and antenna housings, ensuring excellent precision and quality.
8. STU Industries: STU Industries is a prominent deep draw sheet metal manufacturer, serving sectors like automotive, HVAC, and electronics. They manufacture components such as automotive exhaust systems, HVAC enclosures, and electrical connectors, utilizing advanced deep draw techniques.
9. VWX Metalworks: VWX Metalworks offers comprehensive deep draw sheet metal solutions, catering to industries like aerospace, automotive, and robotics. Their product range includes parts like turbine blades, automotive chassis components, and robotic arms.
10. YZ Manufacturing: YZ Manufacturing specializes in deep draw sheet metal fabrication, catering to industries like electronics, appliances, and lighting. They produce a wide range of parts like control panels, appliance enclosures, and lighting fixtures, ensuring high precision and durability.
| Manufacturer | Specialization | Industries Served |
|———————|—————–|————————————-|
| ABC Industries | Enclosures, automotive | Various |
| XYZ Manufacturing | Aerospace, medical | Aerospace, medical, electronics |
| DEF Metalworks | Containers, brackets | Various |
| GHI Fabricators | Automotive, energy | Automotive, agricultural, energy |
| JKL Precision | Telecommunications | Telecommunications, electronics, renewable energy |
| MNO Metalforming | Aviation, defense | Aviation, defense, industrial equipment |
| PQR Engineering | Medical devices, lighting | Medical devices, lighting, telecommunications |
| STU Industries | Automotive, HVAC, electronics | Automotive, HVAC, electronics |
| VWX Metalworks | Aerospace, automotive, robotics | Aerospace, automotive, robotics |
| YZ Manufacturing | Electronics, appliances, lighting | Electronics, appliances, lighting |
Background Research for deep draw sheet metal manufacturers Companies in China, use qcc.com archive.org importyeti.com
There are numerous deep draw sheet metal manufacturers in China, offering a wide range of services and products. To conduct background research on these companies, qcc.com, archive.org, and importyeti.com can provide valuable information.
Qcc.com is a prominent business database in China that offers comprehensive company profiles, including registration information, credit reports, and business scopes. This platform allows users to search for specific deep draw sheet metal manufacturers and obtain details such as company size, registered address, legal representatives, and business status. It also provides financial information, certifications, and any legal disputes involving the company.
Archive.org is a digital library that archives websites over time, making it an excellent tool for conducting historical research. By using this platform, researchers can explore previous versions of a company’s website and track its development and changes. This allows for a comprehensive analysis of the manufacturing processes, technologies, and services offered by deep draw sheet metal manufacturers in China.
Importyeti.com is a reliable import and export database that provides trade data on shipments entering and leaving China. Researchers can utilize this platform to access information regarding deep draw sheet metal manufacturers’ export activities, such as shipment details, ports of departure, product descriptions, and destination countries. This data can help evaluate the international presence, market reach, and overall performance of these manufacturers.
By utilizing qcc.com, archive.org, and importyeti.com, researchers can gather a wealth of information on deep draw sheet metal manufacturers in China. This includes vital details about their legal status, financial health, historical development, manufacturing capabilities, and trade activities. This background research can assist in identifying reputable and reliable manufacturers, comparing their strengths and weaknesses, and making informed decisions regarding partnerships or sourcing requirements.
Leveraging Trade Shows and Expos for deep draw sheet metal Sourcing in China
Trade shows and expos are great opportunities for sourcing deep draw sheet metal in China. These events offer a platform for businesses to explore a wide range of suppliers and manufacturers, connecting them with potential partners in the industry. By attending these events, companies can benefit from various advantages in their sourcing endeavors.
Firstly, trade shows and expos provide direct access to a large number of exhibitors specializing in deep draw sheet metal. These exhibitors are committed to showcasing their products and capabilities, allowing attendees to evaluate and compare different suppliers in one location. This eliminates the need for extensive research and communication, saving time and effort in the sourcing process.
Moreover, these events enable businesses to establish personal connections and build relationships. Meeting suppliers face-to-face at trade shows and expos creates a sense of trust and adds a human touch to the sourcing process. Direct communication allows for a better understanding of the supplier’s capabilities, product quality, and manufacturing processes.
In addition, trade shows and expos often feature live demonstrations and product samples, giving attendees the opportunity to evaluate the quality and precision of deep draw sheet metal products firsthand. This ensures that the chosen suppliers meet the required standards and specifications.
Furthermore, trade shows and expos provide a platform for networking with industry professionals and experts. Engaging in discussions and knowledge-sharing sessions can lead to valuable insights and guidance in sourcing strategies, quality control, and other aspects of sourcing deep draw sheet metal in China. Building connections with industry insiders can also result in future collaborations and partnerships.
Overall, leveraging trade shows and expos for deep draw sheet metal sourcing in China offers a comprehensive and efficient approach for businesses. It allows for direct access to a wide range of suppliers, facilitates relationship building, provides product evaluation opportunities, and allows for networking with industry professionals. With careful planning and effective utilization of these events, companies can successfully source deep draw sheet metal from China and support their manufacturing needs.
The Role of Agents and Sourcing Companies in Facilitating deep draw sheet metal Purchases from China
Agents and sourcing companies play a crucial role in facilitating deep draw sheet metal purchases from China. These entities act as intermediaries between the buyers and the manufacturers, assisting in various stages of the procurement process.
Firstly, agents and sourcing companies have comprehensive knowledge and experience in the Chinese market. They have access to an extensive network of reliable manufacturers specializing in deep draw sheet metal production. This allows them to identify the most suitable suppliers and negotiate favorable prices on behalf of the buyers.
Secondly, these intermediaries act as a bridge between the buyers and the manufacturers, ensuring effective communication and understanding of requirements. They are fluent in both the local language and the buyers’ language, minimizing misunderstandings and facilitating smooth collaboration. Agents and sourcing companies play a vital role in clarifying technical specifications, discussing design changes, and addressing any concerns or challenges that may arise during the production process.
Additionally, agents and sourcing companies are instrumental in conducting quality control inspections. They perform regular factory visits and audits to ensure that the manufacturers meet the buyers’ quality standards. These intermediaries also arrange for pre-production samples and conduct inspections throughout the manufacturing process, minimizing the risk of receiving substandard products.
Moreover, agents and sourcing companies handle the logistics and shipping processes. They coordinate with freight forwarders, handle customs clearance procedures, and arrange for timely delivery of the deep draw sheet metal products. This saves the buyers from the hassles and complexities associated with international shipping, ensuring a smooth and efficient procurement process.
In summary, agents and sourcing companies play a crucial role in facilitating deep draw sheet metal purchases from China. They leverage their market knowledge, communication skills, and quality control expertise to connect buyers with reliable manufacturers. These intermediaries ensure effective communication, monitor quality standards, and handle logistics, enabling buyers to streamline their procurement process and obtain high-quality products from China.
Price Cost Research for deep draw sheet metal manufacturers Companies in China, use temu.com and 1688.com
When it comes to finding deep draw sheet metal manufacturers in China, two reliable platforms that can be explored are temu.com and 1688.com. These websites offer a wide range of suppliers and factories that can fulfill the specific requirements for deep draw sheet metal production.
When conducting price cost research on these platforms, it is important to keep the following factors in mind:
1. Product Specifications: Clearly define the specifications of the deep draw sheet metal you are looking for, including material type, dimensions, tolerances, surface finish, and any other specific requirements. These details are crucial for obtaining accurate pricing information.
2. Supplier Selection: Both temu.com and 1688.com provide extensive supplier databases. Take time to research and compare various manufacturers, considering factors such as their location, expertise, production capacity, and customer reviews. Some additional requirements to consider could be ISO certifications, quality management systems, or manufacturing capabilities.
3. Request for Quotations: Contact multiple suppliers to request quotations for your deep draw sheet metal manufacturing project. Share your product specifications and quantity requirements to receive accurate quotes. Keep in mind that some suppliers may have minimum order quantities, so it is essential to consider this aspect while comparing prices.
4. Negotiation and Sample Evaluation: Once you receive the quotations, negotiate the prices with the suppliers to potentially secure the best deal. Additionally, request samples from shortlisted manufacturers to evaluate their product quality, as it is vital for successful deep draw sheet metal production.
5. Price Comparison and Final Selection: Compare the received quotations and evaluate them based on pricing, product quality, lead time, and other relevant factors. After careful consideration, make a final selection of the manufacturer that best meets your requirements.
By utilizing temu.com and 1688.com, you can gather a wide range of pricing information from deep draw sheet metal manufacturers in China. This will enable you to make informed decisions and select the most suitable manufacturer for your project. Remember to conduct thorough research, verify supplier capabilities, and request samples to ensure a successful collaboration.
Shipping Cost for deep draw sheet metal import from China
Shipping costs for importing deep draw sheet metal from China can vary depending on several factors. The primary factors influencing the shipping cost include the weight and dimensions of the cargo, the shipping method chosen, the distance between China and the destination country, and any additional services required.
For shipments of deep draw sheet metal, it is common to use sea freight as it is more cost-effective for heavy and bulky items. The shipping cost is usually calculated based on the volume or weight of the cargo, whichever is higher. Freight forwarders or shipping companies can provide a detailed quote based on these specifications.
To give a rough estimate, shipping a container of deep draw sheet metal from China to major ports in North America or Europe can cost between $1,500 and $5,000. This range considers a typical 20-foot container and a transit time of around 20-30 days.
It is crucial to consider any additional costs that may arise during the shipping process. These costs may include customs duties, taxes, port handling fees, documentation charges, and insurance. If the deep draw sheet metal requires specialized packaging or protection, such as wooden crates or pallets, these costs should also be taken into account.
To minimize shipping costs, businesses can explore options such as consolidating shipments with other companies or using a freight forwarder that offers competitive rates. Additionally, optimizing packaging and product dimensions can help reduce shipping costs by utilizing the available space efficiently and decreasing the overall weight.
To get an accurate shipping cost for importing deep draw sheet metal from China, it is recommended to contact multiple shipping providers, compare their quotes, and consider the specific requirements of the shipment. Working closely with a reliable and experienced freight forwarder can ensure that all necessary documents and procedures are in place for a smooth import process.
Compare China and Other deep draw sheet metal Markets: Products Quality and Price,Visible and Hidden Costs
China’s deep draw sheet metal market has gained significant attention in recent years due to its ability to produce large quantities of products at competitive prices. However, when comparing China to other deep draw sheet metal markets in terms of product quality and price, as well as visible and hidden costs, several key differences emerge.
In terms of product quality, Chinese manufacturers have made great strides in improving their standards and have proven capable of producing high-quality deep draw sheet metal products. However, other markets, such as Germany and Japan, are still regarded as leaders in terms of precision and overall product quality. The use of advanced technologies and stringent quality control measures in these markets allows them to deliver superior products.
Regarding price, China undoubtedly holds a strong competitive advantage. Chinese manufacturers benefit from lower labor and production costs, enabling them to offer deep draw sheet metal products at more affordable prices compared to other markets. This cost advantage has propelled China to be a preferred choice for companies seeking cost-effective production solutions.
Moving on to visible and hidden costs, China may not necessarily be the most cost-effective option when considering all aspects. While the initial product price may seem attractive, other factors such as shipping costs, import duties, and longer lead times must be taken into account. Additionally, communication challenges and potential language barriers may result in longer project timelines and increased development costs when working with Chinese manufacturers.
On the other hand, markets like Germany and Japan often have higher initial product prices, but they offer several advantages in terms of visible and hidden costs. Proximity to markets, lower shipping costs, and shorter lead times can contribute to more efficient operations, minimizing overall costs when considering the entire supply chain.
In conclusion, China has become a major player in the deep draw sheet metal market, offering competitive prices and improving product quality. However, other markets, such as Germany and Japan, still hold an advantage in terms of precision and overall product quality. When considering visible and hidden costs, China’s initial price advantage may diminish due to factors such as shipping, import duties, communication challenges, and longer lead times. Companies must carefully assess their specific needs and requirements to determine the most suitable market for deep draw sheet metal products.
Understanding Pricing and Payment Terms for deep draw sheet metal: A Comparative Guide to Get the Best Deal
Pricing and payment terms for deep draw sheet metal can vary greatly depending on several factors such as the complexity of the design, the size and thickness of the sheet metal, and the quantity of the order. To ensure that you get the best deal when sourcing deep draw sheet metal, it is important to understand the key factors that influence pricing and negotiate favorable payment terms.
One of the primary factors that affect the price of deep draw sheet metal is the complexity of the design. The more intricate and detailed the design, the higher the cost is likely to be. This is because complex designs require additional tooling and labor, which increases production expenses. It is essential to provide detailed engineering drawings and specifications to suppliers to receive accurate quotes and avoid unexpected cost increases.
The size and thickness of the sheet metal also impact pricing. Larger and thicker sheets require more material, which increases costs. Additionally, thicker materials may necessitate specialized equipment and longer production times, leading to higher prices. By understanding your project requirements and carefully selecting the appropriate size and thickness, you can minimize material waste and control costs.
The quantity of the order is another crucial factor in determining pricing. Suppliers often offer volume discounts for larger orders. Therefore, it is beneficial to plan ahead and consolidate your orders to maximize savings. However, be cautious when negotiating quantity-based discounts, as excessive order volumes may result in the need for additional storage space or lead to cash flow issues.
Regarding payment terms, it is essential to negotiate favorable terms that align with your business needs. Typically, suppliers require an upfront deposit or partial payment before starting production. The remaining balance is usually due upon completion or delivery of the order. Negotiating a reasonable payment schedule can help manage cash flow and reduce financial strain.
In conclusion, understanding the factors influencing pricing and negotiating favorable payment terms are crucial when sourcing deep draw sheet metal. By providing detailed specifications, carefully selecting sizes and thicknesses, and leveraging order quantities, you can obtain the best deal. Additionally, negotiating payment terms that suit your financial capabilities is essential. By considering these factors, you can optimize your procurement process and ensure a successful outcome.
Chinese Regulations and Industry Standards Certifications for deep draw sheet metal,Import Regulations and Customs for deep draw sheet metal from China
China has established certain regulations and industry standards for the production of deep draw sheet metal. These regulations ensure the quality and safety of the products being produced. One of the important certifications in this industry is the ISO 9001:2008 certification, which sets the standards for quality management systems. Companies that obtain this certification are able to demonstrate their commitment to producing high-quality deep draw sheet metal.
In addition to ISO 9001:2008, there are other certifications and standards that companies can obtain to meet specific requirements. For example, the ISO/TS 16949 certification is specific to the automotive industry and is widely recognized as an automotive quality management system standard. This certification is important for companies that supply deep draw sheet metal to automotive manufacturers.
When importing deep draw sheet metal from China, it is crucial to understand the import regulations and customs requirements. The first step is to determine the correct Harmonized System (HS) code for the product, as this will determine the import duties and taxes that are applicable. The HS code for deep draw sheet metal is 7309. Additionally, it is important to ensure compliance with any specific regulations or restrictions that may apply.
Importers must also adhere to China’s customs requirements when bringing deep draw sheet metal into the country. This includes providing accurate and detailed documentation, such as commercial invoices, packing lists, and certificates of origin. Importers should also be aware of any import permits or licenses that may be required, depending on the specific product being imported.
In conclusion, China has established regulations and industry standards for deep draw sheet metal production to ensure quality and safety. It is important for companies to obtain necessary certifications, such as ISO 9001:2008, to demonstrate their commitment to quality. When importing deep draw sheet metal from China, import regulations and customs requirements must be followed, including determining the correct HS code, providing accurate documentation, and complying with any specific regulations or restrictions.
Sustainability and Environmental Considerations in deep draw sheet metal Manufacturing
Sustainability and environmental considerations play a crucial role in deep draw sheet metal manufacturing. This manufacturing process involves shaping metal sheets into desired forms using a press and die. Here’s how sustainability and environmental considerations can be integrated into this process:
1. Material Selection: Choosing sustainable materials is essential for mitigating the environmental impact. Opting for recycled or sustainably sourced metals can help reduce carbon emissions and promote circular economy principles.
2. Energy Efficiency: Deep draw sheet metal manufacturing often requires high energy consumption. Implementing energy-efficient equipment and processes can help minimize energy usage and associated greenhouse gas emissions. Utilizing advanced technologies like regenerative braking and efficient press controls can contribute to energy savings.
3. Waste Reduction: Implementing strategies to minimize waste generation is critical. This can be achieved through careful material handling, accurate die design, and optimization of cutting operations. Effective scrap management, such as recycling or repurposing metal waste, can further enhance sustainability.
4. Water Conservation: While water usage may be limited in deep draw sheet metal manufacturing, implementing water conservation practices is still relevant. Utilizing closed-loop water systems, reusing water in operational processes, and regularly maintaining systems to prevent leaks are effective measures.
5. Emissions Control: Deep draw sheet metal manufacturing can release emissions from various sources, including paint or coating application and cleaning processes. Using low-VOC paints and incorporating emissions control technologies, such as scrubbers or filters, can help reduce the release of harmful pollutants into the atmosphere.
6. Worker Safety: Ensuring a safe working environment and prioritizing the health of employees is fundamental for sustainable manufacturing. Proper training, ergonomic workstations, and personal protective equipment are critical elements that contribute to a sustainable and socially responsible operation.
By integrating sustainability and environmental considerations into deep draw sheet metal manufacturing processes, companies can reduce their ecological footprint, enhance resource efficiency, and contribute to the overall well-being of the planet.
List The Evolution history of “deep draw sheet metal”
The evolution of deep draw sheet metal has a rich history that spans several centuries. This metal forming technique has continually evolved to meet the increasing demands of various industries.
1. Early Years: Deep draw sheet metal can be traced back to the 17th century when artisans started experimenting with hammering and stretching metal sheets. While this technique laid the foundation, it was relatively crude compared to modern processes.
2. Industrial Revolution: The widespread use of steam power during the 18th and 19th centuries brought significant advancements in deep draw sheet metal. Hydraulic presses were introduced, enabling the production of larger and more complex parts. This revolutionized industries such as automotive and aerospace, allowing for the production of intricate components.
3. Modern Era: In the early 20th century, the introduction of electricity and advancements in material sciences led to further improvements in deep draw sheet metal. The development of precision grinding and shaping techniques increased accuracy and consistency in the production of deep draw parts, making them more reliable for critical applications.
4. Computer-Aided Design (CAD): The advent of computers revolutionized deep draw sheet metal fabrication during the latter half of the 20th century. CAD software allowed designers to create precise and intricate designs, which were then translated into instructions for automated machinery. This greatly enhanced the efficiency and accuracy of the manufacturing process.
5. Material Advancements: The discovery and implementation of new materials, such as high-strength alloys and composite materials, have expanded the capabilities of deep draw sheet metal. These materials offer improved strength-to-weight ratios, corrosion resistance, and thermal properties, making them ideal for various demanding applications.
6. Automation and Robotics: In recent years, automation and robotics have further propelled the evolution of deep draw sheet metal. Advanced robotic systems are now capable of handling complex deep draw processes with minimal human intervention. This automation has significantly increased production rates and improved the precision of deep draw parts.
In conclusion, from its humble beginnings as a manual process to the present-day automation and robotization, the evolution of deep draw sheet metal has been driven by advancements in technology, material sciences, and manufacturing processes. This versatile metal forming technique continues to be refined, enabling the production of intricate and high-quality parts for a wide range of industries.
The Evolution and Market Trends in deep draw sheet metal Industry
The deep draw sheet metal industry has witnessed significant evolution and market trends over the years. Deep draw sheet metal manufacturing refers to the process of using a series of metal forming techniques to create hollow, cylindrical or box-shaped metal parts. These parts are widely used in various industries, including automotive, aerospace, electronics, and medical.
One of the key trends in the deep draw sheet metal industry is the increasing demand for lightweight and complex-shaped parts. As industries strive for improved fuel efficiency, reducing the weight of components becomes crucial. Deep draw sheet metal manufacturers are employing advanced techniques, such as hydroforming and hot stamping, to produce lightweight parts without compromising their structural integrity.
Another market trend in this industry is the rising popularity of precision and high-volume production. With the advancement of automation and robotics, deep draw sheet metal manufacturers can now achieve tight tolerances and consistent quality in high volumes. This trend has led to cost savings, increased productivity, and shorter lead times.
The industry is also witnessing an increasing demand for sustainable materials and practices. Deep draw sheet metal manufacturers are exploring the use of eco-friendly materials, such as recycled metals, and implementing energy-efficient manufacturing processes. This trend is driven by the growing awareness of environmental concerns and the need for companies to align with sustainable practices.
Furthermore, the deep draw sheet metal industry is experiencing a shift towards digitalization and smart manufacturing. Companies are adopting technologies like computer-aided design (CAD), simulation software, and real-time monitoring systems to optimize the manufacturing process, improve accuracy, and streamline operations. The integration of data analytics and artificial intelligence (AI) is further enhancing the efficiency and productivity of deep draw sheet metal manufacturing.
In conclusion, the deep draw sheet metal industry has evolved in response to changing market needs and technological advancements. The trends in this industry include the demand for lightweight and complex-shaped parts, precision and high-volume production, sustainability, and digitalization. Manufacturers are adapting to these trends to meet customer requirements, improve efficiency, and stay competitive in the market.
Custom Private Labeling and Branding Opportunities with Chinese deep draw sheet metal Manufacturers
Chinese deep draw sheet metal manufacturers offer excellent opportunities for custom private labeling and branding. With their expertise in deep draw sheet metal manufacturing, these manufacturers can produce high-quality products that can be customized according to the specific branding requirements of businesses.
One of the key advantages of partnering with Chinese manufacturers is their ability to offer cost-effective solutions without compromising on quality. These manufacturers have access to advanced technology and skilled labor, enabling them to produce deep draw sheet metal products that meet international standards at competitive prices.
Moreover, Chinese manufacturers understand the importance of branding and customization in today’s market. They have the capability to incorporate branding elements such as logos, colors, and packaging designs into the manufacturing process. This allows businesses to create distinct and recognizable products that stand out from their competitors.
Additionally, Chinese manufacturers offer flexibility in terms of product variety and customization options. They can produce deep draw sheet metal products in a wide range of shapes, sizes, and materials to cater to different industries and applications. Whether businesses require custom enclosures, housings, or components, these manufacturers can meet their unique requirements.
To ensure successful private labeling and branding collaborations, businesses can establish clear communication channels and provide detailed specifications to the Chinese manufacturers. Regular communication and quality control inspections can help maintain consistency in branding and ensure that the final products meet the desired standards.
In summary, partnering with Chinese deep draw sheet metal manufacturers offers businesses lucrative opportunities for custom private labeling and branding. The combination of cost-effectiveness, manufacturing expertise, and flexibility makes these manufacturers an ideal choice for businesses looking to create customized deep draw sheet metal products that reflect their brand identity.
Tips for Procurement and Considerations when Purchasing deep draw sheet metal
When purchasing deep draw sheet metal for procurement, there are several important considerations to keep in mind. These considerations can help ensure that the purchased materials meet the required specifications and are of high quality. Here are some tips and considerations for procurement:
1. Material Requirements: Identify the specific material requirements for the deep draw sheet metal. Consider factors such as metal type (e.g., stainless steel, aluminum), thickness, width, and finish. The material should meet the necessary strength and durability requirements for the intended application.
2. Quality and Certification: Insist on purchasing deep draw sheet metal from reputable suppliers who can provide relevant certifications, such as ISO 9001, to ensure consistent quality. Ask for material test certificates (MTC) to verify the chemical composition, mechanical properties, and compliance with industry standards.
3. Supplier Evaluation: Assess the supplier’s reputation and track record by considering factors like experience, customer reviews, and the supplier’s ability to deliver on time. Consider requesting samples or visiting the supplier’s facility to inspect their manufacturing processes and quality control measures.
4. Cost and Lead Time: Request quotations from multiple suppliers to compare prices and lead times. Consider factors such as bulk discounts, shipping costs, and any additional fees. Ensure that the supplier can meet the required delivery schedule without compromising on quality.
5. Packaging and Shipping: Discuss packaging requirements to ensure the deep draw sheet metal arrives undamaged. Consider the supplier’s shipping capabilities, including their ability to package, track, and deliver the materials securely.
6. Technical Support: Opt for a supplier that offers technical support and assistance. They should have knowledgeable staff who can help answer questions and provide guidance regarding material selection, design for manufacturability, and compliance with relevant industry standards.
7. Long-term Partnership: When sourcing deep draw sheet metal, consider building a long-term relationship with the supplier. A reliable and trusted partner can ensure consistent quality and timely deliveries, potentially offering benefits such as faster response times, customized solutions, and preferential pricing.
By considering these tips and considerations during the procurement process for deep draw sheet metal, organizations can make informed decisions that result in high-quality materials meeting their specific requirements.
FAQs on Sourcing and Manufacturing deep draw sheet metal in China
Q: Can I source deep draw sheet metal from China?
A: Yes, China is a major manufacturing hub for deep draw sheet metal. Many companies have successfully sourced and manufactured deep draw sheet metal products in China.
Q: What are the benefits of sourcing deep draw sheet metal from China?
A: The main advantages of sourcing from China include cost savings, access to a vast supplier network, and flexible manufacturing capabilities. Chinese manufacturers often offer competitive pricing due to lower production costs. Additionally, China has a well-established supply chain infrastructure, enabling efficient sourcing of materials and components. Moreover, manufacturers in China are experienced in producing a wide range of deep draw sheet metal products, allowing for customization and scalability.
Q: Are Chinese manufacturers capable of meeting quality standards for deep draw sheet metal?
A: Yes, Chinese manufacturers can produce deep draw sheet metal that meets international quality standards. Many Chinese manufacturers have invested in advanced equipment and technologies to ensure high precision and accuracy in their manufacturing processes. It is crucial to conduct thorough due diligence before partnering with a manufacturer to ensure they have the necessary certifications and quality control systems in place.
Q: How can I find reliable deep draw sheet metal manufacturers in China?
A: To find reliable manufacturers in China, you can utilize online sourcing platforms, attend trade shows, or engage with sourcing agents or consultants who have knowledge and experience in the industry. It is recommended to conduct background checks, ask for references, and request samples or prototypes to assess the manufacturer’s capabilities and quality.
Q: What considerations should I keep in mind when manufacturing deep draw sheet metal in China?
A: It is essential to have clear and detailed product specifications, including material type, dimensions, tolerances, and surface finishes. Communication is key during the manufacturing process, so ensure you have a reliable point of contact who can effectively address any questions or concerns. Additionally, quality control measures, such as regular inspections and on-site visits, should be implemented to maintain product consistency and adherence to specifications.
Q: What are the potential challenges when sourcing deep draw sheet metal from China?
A: Some challenges that may arise include language barriers, cultural differences, and longer lead times due to international logistics. It is crucial to establish clear communication channels and utilize translation services when needed. Additionally, comprehensive written agreements that cover intellectual property rights, quality control protocols, and dispute resolution mechanisms should be in place to mitigate potential risks.
In conclusion, sourcing and manufacturing deep draw sheet metal in China can provide cost savings, access to a wide supplier network, and flexibility in customization. By conducting proper due diligence and implementing effective communication and quality control measures, businesses can successfully source high-quality products from China.
Why contact sourcifychina.com get free quota from reliable deep draw sheet metal suppliers?
Sourcifychina.com offers free quotas from reliable deep draw sheet metal suppliers for a few reasons. Firstly, they understand that finding trustworthy suppliers for deep draw sheet metal products can be a challenging task for businesses. By providing free quotas, Sourcifychina.com aims to simplify the sourcing process and help businesses connect with reliable suppliers more easily.
Secondly, Sourcifychina.com partners with a network of reputable suppliers who have been thoroughly vetted and assessed for their quality standards and manufacturing capabilities. These suppliers specialize in deep draw sheet metal fabrication and possess the necessary expertise and equipment to produce high-quality products.
By offering free quotas, Sourcifychina.com enables businesses to explore multiple sourcing options conveniently. This allows them to compare prices, lead times, and other factors without incurring any financial commitment initially. It also saves businesses time and effort that would otherwise be spent on individually reaching out to suppliers and negotiating pricing.
Moreover, Sourcifychina.com aims to build long-term relationships with their clients. By offering free quotas, they hope to establish trust and showcase their commitment to helping businesses find reliable suppliers. This approach enhances the user experience and promotes customer satisfaction, ultimately encouraging businesses to maintain a long-term partnership with Sourcifychina.com for their future sourcing needs.
In conclusion, Sourcifychina.com offers free quotas from reliable deep draw sheet metal suppliers to simplify the sourcing process, connect businesses with reputable suppliers, enable comparison and analysis of multiple suppliers, and foster long-term relationships with clients.