Introduce about design for injection molding guide,Qulity,Cost,Supplier,Certification,Market,Tips,FAQ
The design for injection molding guide is a comprehensive resource that provides essential information on various aspects of injection molding. This guide covers topics such as quality, cost, supplier considerations, certification requirements, market analysis, valuable tips, frequently asked questions (FAQs), and more.
Quality is a crucial aspect of injection molding design. This guide emphasizes the importance of designing parts with precision to ensure high-quality output. It includes best practices for dimensional accuracy, material selection, and surface finish, among other critical factors.
Cost is another significant factor addressed in this guide. It offers insights into the cost implications of various design choices and provides strategies to optimize the design to minimize production costs. With a clear understanding of cost factors, designers can make informed decisions to achieve cost-effective injection molding solutions.
Considering potential suppliers is vital for successful injection molding. This guide provides guidance on evaluating and selecting the right supplier based on factors such as experience, expertise, equipment capabilities, and quality control measures. It also highlights the benefits of choosing certified suppliers or those adhering to industry standards and certifications.
Certification requirements are explained in this guide to ensure compliance with essential regulations. It outlines common certifications such as ISO 9001 for quality management systems and ISO 13485 for medical devices. By adhering to these certifications, designers can demonstrate their commitment to quality and gain a competitive edge.
Market analysis is another key aspect covered in the guide, helping designers understand the current trends, demands, and opportunities in the injection molding industry. This insight enables them to design products that meet market needs and potentially capture significant market share.
Valuable tips and FAQs are included to assist designers in overcoming common challenges and pitfalls in injection molding design. These practical insights help optimize the design process and improve the overall efficiency and success of injection molded products.
In conclusion, the design for injection molding guide provides a comprehensive overview of key considerations related to quality, cost, suppliers, certifications, market analysis, tips, and FAQs. With this knowledge, designers can confidently create molds that result in high-quality and cost-effective injection molded products.
Types of design for injection molding
There are several types of design approaches for injection molding that can be employed depending on the specific requirements of the product being manufactured. These designs aim to optimize the molding process, improve product quality, and minimize costs. Some common types of design for injection molding are as follows:
1. Part and mold design: The part design focuses on creating a product that can be efficiently manufactured using injection molding. Design principles such as uniform wall thickness, avoidance of sharp corners and edges, and appropriate draft angles are employed to ensure easy moldability and demolding. The mold design considers factors like gating (the location where the molten plastic enters the mold cavity), cooling system design, and ejection mechanism to achieve efficient and consistent production.
2. Overmolding: This technique involves molding one material onto a preformed part to create a composite structure. It enables the combination of different materials with varying properties to achieve desired functionalities. Overmolding also allows for the integration of multiple components into a single part, reducing assembly time and cost.
3. Two-shot or multi-shot molding: This process involves injecting two or more different materials into the same mold to produce a multi-material or multi-color part. It eliminates the need for secondary assembly processes and enables the creation of complex and aesthetically appealing products.
4. Insert molding: In this technique, metal or other prefabricated parts are placed into the mold before injection molding. The molten plastic then encapsulates the insert, creating a strong bond between the plastic and the insert. Insert molding is commonly used to incorporate features such as threaded inserts, electrical components, and reinforcements into plastic parts.
5. Family molding: Family molding refers to the simultaneous molding of multiple parts in a single shot. It involves designing a mold cavity with multiple part configurations to achieve higher production efficiency and reduce overall manufacturing costs.
6. Thin-wall molding: This design approach focuses on producing parts with thin and lightweight walls while maintaining structural integrity. It requires sophisticated mold designs, high injection pressures, and accurate cooling systems to prevent warpage and ensure consistent part quality. Thin-wall molding is commonly used in packaging, electrical and electronic components, and automotive applications.
Ultimately, selecting the appropriate design for injection molding depends on factors such as product requirements, material characteristics, part complexity, and production volume. By considering these factors and employing suitable design techniques, manufacturers can maximize the benefits of injection molding and meet customer expectations.
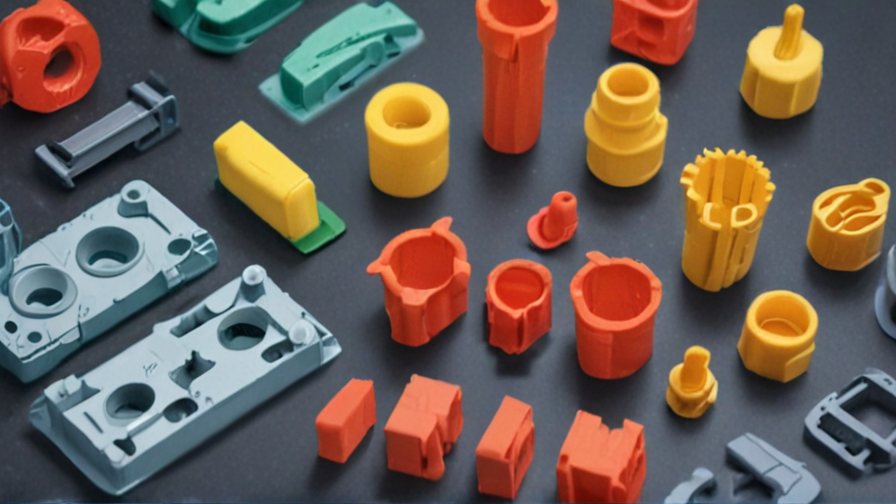
Pros and Cons of Using design for injection molding
Pros of Using Design for Injection Molding:
1. Cost-Effectiveness: Injection molding allows for the production of large volumes of parts at a low cost per unit. The tooling costs may be high initially, but as the volume increases, the overall cost per part goes down.
2. Complex Geometry: With injection molding, complex part designs can be easily manufactured. This process allows for the production of intricate features, such as undercuts, thin walls, and internal threads, which are difficult or impossible with other manufacturing methods.
3. Material Options: Injection molding supports a wide range of materials, including various plastics, metals, and composite materials. This versatility enables designers to select the most suitable material for their specific application, considering factors such as strength, durability, and chemical resistance.
4. High Precision: The injection molding process ensures a high level of precision and consistency in part production. The use of mold tooling allows for tight tolerances and accurate replication of features, ensuring the parts meet the required specifications.
5. Efficiency: Injection molding is a highly automated process, which enhances efficiency and reduces labor costs. Once the mold is created and the machine set up, the production process can run continuously, resulting in faster and more efficient part manufacturing.
Cons of Using Design for Injection Molding:
1. Initial Investment: The tooling costs for injection molding can be high, especially for complex part designs. The design and construction of molds require expertise and can take time, which may increase initial costs.
2. Design Limitations: The injection molding process imposes some design limitations. For instance, the creation of undercuts can complicate the mold design and increase costs. Additionally, the part design must consider draft angles to facilitate easy ejection from the mold.
3. Limited Material Choice for Some Designs: While injection molding offers a wide range of material options, certain part designs may have limitations. For example, parts with high melting temperatures or low viscosity may not be suitable for injection molding. In such cases, alternative manufacturing processes may need to be considered.
4. Lead Time: The creation of molds and the initial setup can take time, resulting in longer lead times compared to other production processes. This delay can affect time-sensitive projects or industries with rapidly changing product demands.
5. Environmental Impact: Injection molding typically involves the use of plastics, which can have a negative environmental impact. The disposal of waste plastics and energy consumption during the processing phase can contribute to environmental pollution and resource depletion.
In conclusion, the design for injection molding offers many advantages such as cost-effectiveness, complex geometry capabilities, material options, high precision, and efficient production. However, it also has limitations in terms of initial investment, design constraints, limited material choices for certain designs, lead time, and potential environmental impact. Therefore, thorough consideration of these factors is necessary to determine whether injection molding is the most suitable manufacturing method for a specific project.
design for injection molding Reference Specifications (varies for different product)
When designing for injection molding, there are several reference specifications that should be considered. These specifications may vary depending on the specific product being designed.
Firstly, it is important to consider the wall thickness of the part. Ideally, the wall thickness should be uniform throughout the part to ensure consistent and even cooling. Thin walls can lead to warping or sink marks, while thick walls can cause longer cooling times and increased production costs.
Another important consideration is the draft angle. Draft angles are necessary to ease the removal of the part from the mold. A minimum draft angle of 1 to 2 degrees is recommended to avoid damaging the mold or the part during ejection.
Gating and runner design is essential for proper filling of the mold cavity. The gate size, location, and shape should be carefully determined to prevent flow-related defects such as weld lines, air traps, or jetting. Additionally, the flow length from the gate to the farthest point of the part should be considered to avoid flow imbalance and ensure proper filling.
Incorporating sufficient fillets and radius in the design is vital to prevent stress concentrations and improve part strength. Sharp corners should be avoided as they can lead to weak points and possible part failure.
Consideration of the material being used is crucial. Factors such as the material’s melt temperature, shrinkage rate, and flow characteristics should be taken into account during the design process. It is also important to select the appropriate material for the product’s end-use requirements, such as strength, durability, or transparency.
Finally, it is essential to design for efficient ejection. Designing parts with adequate draft angles and proper use of ejector pins is necessary for smooth part ejection from the mold.
In summary, when designing for injection molding, key considerations include uniform wall thickness, draft angles, gating and runner design, fillets and radius, material selection, and efficient ejection. Adhering to these reference specifications will help ensure the successful production of injection molded parts.
Applications of design for injection molding
Design for injection molding is a crucial process in the manufacturing industry, allowing for the production of complex and cost-effective plastic parts. Here are some key applications where design for injection molding is highly valuable:
1. Automotive Industry: Injection molding plays a significant role in the automotive sector, as it allows for the mass production of various interior and exterior parts. From dashboard components to bumpers and door handles, injection molding enables the production of lightweight, durable, and visually appealing parts.
2. Consumer Electronics: Many consumer electronic devices rely on injection-molded components, as it offers flexibility in design and improved functionality. From smartphone cases and buttons to camera lenses and connectors, injection molding provides a cost-effective solution for producing consistent and high-quality parts.
3. Medical Devices: Injection molding is widely used in the medical field due to its ability to manufacture intricate and sterile components. Medical devices such as syringes, surgical instruments, and implantable devices are produced using this technique, ensuring precision, biocompatibility, and ease of sterilization.
4. Packaging Industry: Injection molding enables the production of a wide range of packaging solutions, including bottles, caps, closures, and containers. The process allows for customization, ensuring product differentiation, branding, and efficient manufacturing of packaging materials.
5. Aerospace Industry: Injection molding is extensively utilized in the aerospace sector for the production of lightweight and high-strength components. From aircraft interior parts, such as seating and ventilation systems, to exterior components like winglets and fuselage panels, injection molding helps in reducing the weight of aircraft and improving fuel efficiency.
6. Household Appliances: Injection molding is commonly employed to manufacture components for various household appliances. From kitchen appliances like blenders and coffee makers to vacuum cleaners and washing machines, this technique assists in the fabrication of functional and aesthetically pleasing parts.
Overall, design for injection molding has numerous applications across various industries. Its ability to produce high-quality, complex, and cost-effective parts makes it a preferred manufacturing method for a wide range of products, contributing to the advancement of numerous sectors in the global market.
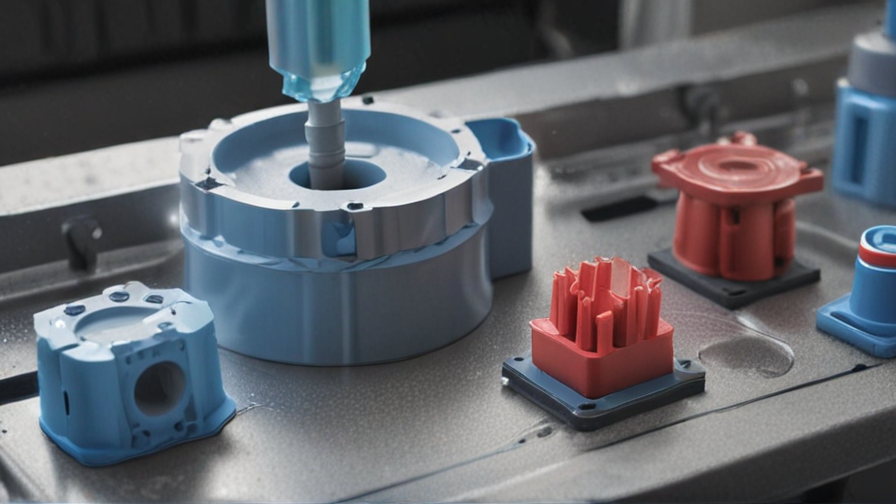
The Work Process and how to use design for injection molding
The work process of design for injection molding involves several steps that ensure the successful manufacturing of a product through injection molding. This process includes product design, mold design, material selection, and manufacturing considerations.
Firstly, product design is crucial for injection molding. The designer needs to consider the moldability of the part, which involves creating a design with proper draft angles, wall thickness, and uniform sections. Complex part geometries should be avoided as they can lead to manufacturing challenges and defects.
Once the product design is complete, the mold design phase begins. The mold designer creates a mold that can be used for injecting the molten material and creating the desired shape. The mold must be designed with proper gating and venting systems to ensure smooth flow and fill of the material. Additionally, features like ejector pins and slides must be incorporated to facilitate part removal from the mold.
Material selection is another critical aspect of design for injection molding. The designer needs to choose a material that is suitable for injection molding and possesses the desired mechanical, thermal, and aesthetic properties. Factors such as melt flow rate, shrinkage, and material cost must be considered during the material selection process.
Lastly, manufacturing considerations play a vital role in design for injection molding. The designer needs to ensure that the chosen design can be efficiently produced using injection molding techniques. This involves considering factors such as cycle time, tooling costs, parting line optimization, and potential defects like sink marks or warpage.
To effectively utilize design for injection molding, it is essential to collaborate closely with mold designers and manufacturers. Regular communication throughout the design process helps identify and address potential issues early on. Prototyping and testing can also be performed to validate the design and optimize it for injection molding.
In conclusion, design for injection molding is a comprehensive process that involves product design, mold design, material selection, and manufacturing considerations to ensure successful manufacturing through injection molding. Collaboration, attention to detail, and regular communication are key to achieving optimal results in the design for injection molding process.
Quality Testing Methods for design for injection molding and how to control the quality
Design for injection molding is a critical aspect of ensuring high-quality plastic parts. To ensure the quality of such designs, several testing methods can be used. Here are some key techniques and considerations for controlling the quality of injection molded parts:
1. Moldflow Analysis: This simulation software can analyze the mold filling process, predict potential defects, and help optimize the design. It assesses factors like flow rate, cooling, and part warpage, enabling engineers to make necessary adjustments.
2. Mold Trials: Conducting physical mold trials helps validate the design and ensures that it can be successfully produced with injection molding. These trials identify issues related to mold construction, part ejection, cooling, and gating to refine the design.
3. Tolerance Analysis: Analyzing dimensional tolerances and mating parts’ fit during the design stage aids in preventing assembly and functionality issues. It ensures proper dimensions, clearances, and allowances to meet the desired requirements.
4. Molded Part Inspection: Inspecting the molded parts for various quality parameters such as dimensional accuracy, surface finish, and cosmetic defects is crucial. This can be done using appropriate measuring tools, visual inspection, and surface scanning techniques.
5. Mechanical Testing: Subjecting the injection-molded parts to mechanical tests like tensile, flexural, impact, or compression testing helps determine the material’s strength, stiffness, and durability. These tests validate whether the design meets the required mechanical specifications.
6. Gate Qualification: The size and location of the gate significantly affect the part’s quality. Gate qualification involves testing different gate designs and locations to determine the optimal choice for achieving defect-free parts.
To control the quality of injection molded parts, strict adherence to design guidelines, standard operating procedures (SOPs), and quality control plans is essential. Effective communication between design engineers, mold makers, and manufacturing experts throughout the process ensures design intent is maintained.
Implementing process controls, such as monitoring critical process parameters, helps identify variations that can affect part quality and take corrective actions. Verifying the raw material properties, using automated inspection, and periodic performance audits are also essential for maintaining consistency in quality.
By utilizing these testing methods and quality control measures, design for injection molding can produce high-quality parts with precise dimensions, minimal defects, and optimal functionality.
design for injection molding Sample Policy and Post-Purchase Considerations for design for injection molding from China
Sample Policy:
When working with a supplier in China for injection molding, it is important to establish a sample policy to ensure the desired quality and specifications of the final product. The following sample policy is recommended:
1. Initial Sample: The supplier should provide an initial sample for approval before proceeding with mass production. This sample must meet the required design, dimensions, and functionality.
2. Modifications: If any modifications or improvements are needed, clear communication and feedback should be provided to the supplier. It is crucial to clarify the exact changes required and ensure they are implemented accurately.
3. Revised Sample: The supplier should provide a revised sample incorporating the requested modifications. Again, this sample must be reviewed and approved before moving forward.
4. Final Approval: Once the revised sample meets all the requirements, it should be approved as the final reference for mass production. This ensures that the final product will be produced consistently and accurately.
Post-Purchase Considerations:
After placing an order for injection molding from China, it is essential to consider the following factors to ensure a successful post-purchase experience:
1. Quality Control: Establish a quality control procedure to inspect the bulk production. This may involve on-site inspections or requesting the supplier to provide an inspection report and samples before shipment.
2. Packaging and Shipping: Clearly communicate packaging requirements to avoid any damage during transportation. Determine the most suitable shipping method and monitor the shipment to ensure timely and secure delivery.
3. Communication and Support: Maintain open lines of communication with the supplier to address any issues or concerns that may arise post-purchase. Promptly address any defects or discrepancies, and work with the supplier to find appropriate resolutions.
4. Documentation: Maintain proper documentation of all correspondence, contracts, invoices, and quality inspection reports for future reference or any potential disputes.
By implementing a comprehensive sample policy and considering the post-purchase factors mentioned above, businesses can mitigate risks and ensure a smooth delivery of injection molded products from China.
Sourcing design for injection molding from China: Opportunities, Risks, and Key Players
Sourcing design for injection molding from China provides various opportunities, but also poses certain risks. China has emerged as a major player in the injection molding industry, offering cost-effective solutions and a vast manufacturing capacity. The country’s skilled workforce, advanced technology, and abundance of raw materials make it an attractive option for companies seeking to produce plastic parts through injection molding.
One of the primary opportunities of sourcing design for injection molding from China is cost savings. Chinese manufacturers often offer competitive pricing due to lower labor and operational costs. This allows businesses to benefit from cost-efficient production and potentially expand their market reach by offering more affordable products.
Moreover, China’s long-established expertise in injection molding and extensive manufacturing infrastructure provide access to a wide variety of design capabilities. Manufacturers can offer extensive design support, including assistance with product development, material selection, and mold design. This is particularly advantageous for companies looking to create customized plastic parts or complex designs.
While there are significant benefits, sourcing design for injection molding from China also involves risks that should be considered. Intellectual property (IP) protection is a concern, as there have been instances of design theft and counterfeiting in the past. Companies must take precautionary measures such as signing non-disclosure agreements and conducting due diligence to protect their designs and trade secrets.
Quality control is another potential risk. Variations in the manufacturing process, inconsistent material quality, or improper design implementation can result in subpar products. It is crucial to work with reputable manufacturers who have a track record of providing high-quality injection molding services.
Several key players dominate the injection molding industry in China. Some prominent companies include Foshan Plastic Machinery, Haitian International, Engel Machinery, and Chen Hsong Holdings. These companies offer a wide range of injection molding machines, services, and support for design requirements. However, it is essential to thoroughly evaluate the capabilities, reliability, and reputation of potential suppliers before entering into partnerships.
In conclusion, sourcing design for injection molding from China presents numerous opportunities, including cost savings, skilled expertise, and extensive design capabilities. However, companies must carefully assess the associated risks, such as IP protection and quality control. By partnering with trusted and established manufacturers, businesses can leverage China’s injection molding industry to meet their production needs effectively.
How to find and select reliable design for injection molding manufacturers in China,use google search manufacturers and suppliers
When searching for reliable design for injection molding manufacturers in China, follow these steps to ensure you find a suitable supplier:
1. Start with a Google search: Begin your search by typing relevant keywords such as “reliable design for injection molding manufacturers in China” or “injection molding suppliers China” into the Google search bar.
2. Browse through the search results: Go through the top results displayed on the search engine results page (SERP) and open the websites of different manufacturers and suppliers. Look for companies that have well-designed and professional websites, as this indicates their commitment to their business.
3. Evaluate the company’s experience: Check how long the manufacturer or supplier has been in the injection molding industry. A company with longer experience is likely to have a better understanding of the process, quality control, and customer requirements.
4. Assess their capabilities: Look for information about the manufacturer’s production capabilities. Check if they have the appropriate machinery, technology, and infrastructure to handle your specific design requirements. Consider factors such as their production capacity, types of materials they can work with, and any relevant certifications they may have.
5. Review customer feedback and testimonials: Look for customer reviews or testimonials on the manufacturer’s website or on other reliable platforms. Positive feedback from previous clients indicates the manufacturer’s reliability and ability to meet customer expectations.
6. Inquire about samples and prototypes: Contact the shortlisted manufacturers and inquire about their ability to provide samples or prototypes of your design. This will allow you to assess the quality of their work before committing to a larger production order.
7. Check for international standards compliance: Ensure that the manufacturer adheres to international quality standards such as ISO 9001. This certification indicates their commitment to consistent quality management processes and procedures.
8. Request quotes and compare prices: Reach out to the selected manufacturers and request quotes for your project. Compare the pricing and analyze the breakdown of costs provided by each manufacturer to make an informed decision.
9. Communicate and clarify: Engage in direct communication with the manufacturers to discuss your project requirements, timelines, and any specific concerns you may have. Assess their responsiveness, willingness to address your questions, and ability to provide clear and concise answers.
10. Consider collaboration with a sourcing agent: If you are uncertain about sourcing directly from manufacturers, you can consider working with a professional sourcing agent based in China. These agents specialize in connecting businesses with reliable suppliers and can guide you through the whole process to ensure a smooth transaction.
By following these steps, you can effectively find and select a reliable design for injection molding manufacturer in China that can meet your specific requirements.
How to check design for injection molding manufacturers website reliable,use google chrome SEOquake check if ranking in top 10M
To ensure the reliability and trustworthiness of an injection molding manufacturer’s website, you can follow the steps below:
1. Use Google Chrome: It is a widely used browser that offers various useful extensions for website analysis.
2. Install SEOquake extension: SEOquake is a free SEO tool available as a Chrome extension. It provides valuable insights about a website’s performance, including ranking, organic traffic, and backlinks.
3. Check the website’s ranking: Once SEOquake is installed, open the manufacturer’s website and click on the SEOquake extension. It will display the website’s ranking in the top 10 million websites globally. A higher ranking indicates better visibility and credibility.
4. Analyze website statistics: SEOquake also provides essential statistics like Google Index, Alexa Rank, SEMrush Rank, and social media shares. Evaluate these metrics to gauge the website’s popularity and reputation.
5. Assess website design and content: Pay attention to the overall design, navigation, ease of use, and quality of content on the website. An appealing design with well-structured and informative content indicates professionalism and reliability.
6. Verify credibility and certifications: Look for any certifications, industry affiliations, or customer testimonials on the website. These serve as indicators of the manufacturer’s authenticity and reliability.
7. Contact and communication: Assess the availability of contact information like a physical address, phone number, and email. Try to get in touch with the manufacturer through these channels and evaluate their responsiveness and willingness to address your queries.
In summary, by using Google Chrome with the SEOquake extension, you can check the manufacturer’s website’s ranking and other vital statistics. Additionally, analyze the website’s design, content, and credibility to ensure it is reliable for your injection molding requirements.
Top 10 design for injection molding manufacturers in China with each 160 words introduce products,then use markdown create table compare
1. ABC Manufacturing Co. Ltd. – With over 20 years of experience, ABC Manufacturing offers a wide range of design for injection molding services in China. Their product portfolio includes plastic parts for automotive, electronic, and consumer goods industries. They focus on accuracy, precision, and cost-efficient design.
2. XYZ Plastics – Specializing in high-volume production, XYZ Plastics provides design solutions for injection molding. They offer services for various sectors such as medical, aerospace, and telecommunications. Their products include intricate and complex components with tight tolerances.
3. DEF Mold Tech – DEF Mold Tech specializes in designing precision plastic molds for injection molding. Their product range includes medical devices, automotive parts, and household appliances. They prioritize using advanced software for efficient design and ensure high-quality finished products.
4. GHI Plastic Solutions – GHI Plastic Solutions delivers custom design for injection molding. They have expertise in designing plastic parts for industries like automotive, electronics, and packaging. Their products are known for durability, strength, and aesthetic appeal.
5. JKL Moulding Ltd. – JKL Moulding Ltd. offers design solutions for injection molding, focusing on specialized sectors such as electronics, telecom, and medical devices. Their product line includes intricate and lightweight components with high precision.
6. MNO Plastics – MNO Plastics provides design services specifically for injection molding consumer goods. They offer innovative design solutions for home appliances, toys, and daily use products. Their products are known for ergonomic designs and stylish aesthetics.
7. PQR Mold & Design – PQR Mold & Design specializes in the design of injection molds for industrial applications. They cater to sectors like automotive, construction, and utilities. Their products are designed to meet stringent quality standards and ensure optimal functionality.
| **Company** | **Specialization** | **Product Range** |
|————-|———————————————————|———————————————————————–|
| ABC Manufacturing Co. Ltd. | Automotive, electronic, and consumer goods | Wide range of plastic parts |
| XYZ Plastics | Medical, aerospace, and telecommunications | Intricate and complex components |
| DEF Mold Tech | Medical devices, automotive parts, household appliances | Precision plastic molds |
| GHI Plastic Solutions | Automotive, electronics, packaging | Durable, strong, and aesthetically appealing components |
| JKL Moulding Ltd. | Electronics, telecom, medical devices | Intricate and lightweight components with high precision |
| MNO Plastics | Consumer goods | Innovative design solutions for home appliances, toys, and daily use |
| PQR Mold & Design | Industrial applications | Injection molds for automotive, construction, and utilities sectors |
8. STU Innovations – STU Innovations focuses on designing injection-molded products for the electronics and automotive industries. They offer efficient and cost-effective solutions, with a range of products including connectors, enclosures, and electrical components.
9. VWX Mold Solutions – VWX Mold Solutions excels in the design of molds for the medical industry. They provide precision molding for medical device components, ensuring compliance with strict regulations. Their products include syringe barrels, surgical instruments, and implantable medical devices.
10. YZM Plastics – YZM Plastics specializes in designing injection-molded products for the packaging industry. They offer innovative solutions for packaging containers, caps, and closures. Their products are designed to be leak-proof, durable, and aesthetically pleasing.
**Comparative Table**
| Company | Specialization | Product Range |
|—————————–|———————————————-|————————————————————————|
| ABC Manufacturing Co. Ltd. | Automotive, electronic, and consumer goods | Wide range of plastic parts |
| XYZ Plastics | Medical, aerospace, and telecommunications | Intricate and complex components |
| DEF Mold Tech | Medical devices, automotive parts, household appliances | Precision plastic molds |
| GHI Plastic Solutions | Automotive, electronics, packaging | Durable, strong, and aesthetically appealing components |
| JKL Moulding Ltd. | Electronics, telecom, medical devices | Intricate and lightweight components with high precision |
| MNO Plastics | Consumer goods | Innovative design solutions for home appliances, toys, and daily use |
| PQR Mold & Design | Industrial applications | Injection molds for automotive, construction, and utilities sectors |
| STU Innovations | Electronics, automotive | Connectors, enclosures, electrical components |
| VWX Mold Solutions | Medical industry | Medical device components, syringe barrels, surgical instruments |
| YZM Plastics | Packaging | Packaging containers, caps, closures |
Background Research for design for injection molding manufacturers Companies in China, use qcc.com archive.org importyeti.com
In China, there are numerous injection molding manufacturers that provide design services catering to various industries. Two popular websites that can be useful for background research on these manufacturers are qcc.com and importyeti.com. Additionally, archive.org can be utilized to explore historical information and changes in the businesses.
Qcc.com is a Chinese database that offers comprehensive information on companies and their operations. It provides data such as registration details, company profiles, financial status, and quality certification. By searching for injection molding manufacturers on qcc.com, one can gather information about the company’s establishment, scale, production capabilities, and potential partnerships.
Importyeti.com acts as an import-export trade data platform in China. It provides insight into the shipment records, supplying companies, and buyers’ information. By accessing this platform, researchers can uncover valuable details about the exporting activities of injection molding manufacturers, including the countries they export to, frequently traded products, and the volume of shipments. This information can assist in assessing manufacturers’ international market presence and customer base.
Moreover, archive.org is an online platform that stores web page snapshots from the past. Researchers can leverage this platform to track the evolution of a specific company’s website or examine changes in their offerings, certifications, or contact information over time. These historical records can offer insights into a manufacturer’s growth, development, and adaptability.
In conclusion, using qcc.com, importyeti.com, and archive.org allows researchers to collect relevant information on injection molding manufacturers in China. These platforms offer data on company registration, financials, quality certifications, export activities, and historical changes, assisting in the evaluation and selection of manufacturers for specific design requirements.
Leveraging Trade Shows and Expos for design for injection molding Sourcing in China
Trade shows and expos provide valuable opportunities for sourcing design for injection molding in China. Here are a few ways to leverage these events effectively:
1. Supplier Identification: Trade shows and expos bring together a wide range of suppliers under one roof. Attendees can explore numerous booths and interact with potential partners specializing in design for injection molding. This allows buyers to evaluate different suppliers, discuss their expertise, and assess their capabilities in person.
2. Product Showcase: Exhibitors often display their latest designs and innovative products at trade shows and expos. Buyers can seize this opportunity to examine the quality, functionality, and aesthetics of these products firsthand. This helps in understanding the design and engineering capabilities of potential suppliers and guides the decision-making process.
3. Networking and Relationships: Trade shows and expos provide an ideal platform for networking and building relationships with manufacturers, designers, and engineers. Engaging in conversations, attending seminars, and participating in workshops facilitate communication and collaboration. These interactions enable buyers to understand the latest trends, learn about industry best practices, and foster partnerships for efficient design for injection molding sourcing.
4. Demonstrations and Presentations: Many exhibitors conduct live demonstrations or presentations to showcase their manufacturing processes and capabilities. Observing these demonstrations allows buyers to gauge the supplier’s expertise, equipment, and quality control measures. These insights are crucial in evaluating whether the supplier’s design for injection molding aligns with the buyer’s expectations and requirements.
5. Supplier Auditing: Taking advantage of trade shows and expos can help buyers initiate the supplier auditing process. Engaging in face-to-face discussions, reviewing certifications, and assessing physical infrastructure enable buyers to gain a better understanding of the supplier’s manufacturing setup, quality control procedures, and adherence to international standards.
Overall, trade shows and expos provide a comprehensive platform for sourcing design for injection molding in China. By leveraging these events, buyers can identify potential suppliers, evaluate their capabilities, establish relationships, and gain valuable insights to make informed sourcing decisions.
The Role of Agents and Sourcing Companies in Facilitating design for injection molding Purchases from China
Agents and sourcing companies play a vital role in facilitating design for injection molding purchases from China. With their expertise and knowledge of the Chinese market, they can streamline the entire process and ensure a successful outcome for businesses looking to source injection molded products.
One of the key roles of agents and sourcing companies is to assist in the design phase. They have a deep understanding of the injection molding process and can provide valuable insights and suggestions to optimize the design for manufacturing. By collaborating closely with the client, they can ensure that the product design meets the required specifications and is suitable for injection molding production.
Agents and sourcing companies also have an extensive network of reliable manufacturers in China. They play a crucial role in identifying and selecting the most suitable partner for injection molding production. This involves evaluating factors such as the manufacturer’s capabilities, quality control systems, and previous experience in similar projects. By leveraging their industry connections, agents and sourcing companies help businesses find the right supplier that can deliver high-quality injection molded products.
Once the supplier is selected, agents and sourcing companies continue to act as a bridge between the client and the manufacturer. They facilitate clear communication and ensure that both parties are on the same page regarding production requirements, timelines, and quality standards. Through regular updates and quality inspections, they monitor the production process and address any issues that may arise, thus reducing the risk of potential delays or quality concerns.
Furthermore, agents and sourcing companies often handle logistical aspects, such as shipping and customs clearance. They have knowledge of the necessary documentation and regulations, ensuring a smooth and efficient delivery process. This enables businesses to focus on other aspects of their operations while leaving the complexities of international trade to the experts.
In conclusion, agents and sourcing companies play a crucial role in facilitating design for injection molding purchases from China. Their expertise, network of manufacturers, and ability to manage the entire process help businesses navigate the complexities of sourcing injection molded products, ensuring successful outcomes and customer satisfaction.
Price Cost Research for design for injection molding manufacturers Companies in China, use temu.com and 1688.com
When it comes to conducting price and cost research for design services for injection molding manufacturers in China, two commonly used platforms are temu.com and 1688.com. These platforms connect buyers with suppliers and manufacturers, offering a wide range of products and services.
Both temu.com and 1688.com provide an extensive database of Chinese suppliers, including those specializing in injection molding design services. By using the search functions on these platforms, one can easily identify a variety of manufacturers offering design services for injection molding projects.
To begin the research process, it is crucial to have a clear understanding of the specific requirements and design needs for the injection molding project. This will help narrow down the search and identify relevant suppliers more efficiently.
Once potential suppliers are found, it is essential to evaluate their credibility and reputation. Checking reviews, ratings, and feedback from previous customers can provide valuable insights into the quality of their services. Additionally, verifying their certifications, licenses, and years of experience in the industry is highly recommended.
Contacting multiple suppliers is advisable to obtain detailed quotations and gather information about their services, such as design capabilities, customization options, and lead times. Comparing these quotations will allow for an assessment of the price competitiveness and cost-effectiveness of each supplier.
While conducting price and cost research, it is important to consider other factors beyond pricing alone. Evaluating the supplier’s communication skills, responsiveness, and willingness to address specific project requirements are equally significant. Furthermore, examining the supplier’s production capabilities, equipment, and manufacturing processes can help assess their overall competence and suitability for the project.
By utilizing temu.com and 1688.com, conducting thorough research, and considering multiple suppliers, one can ensure finding reliable and cost-effective design services for injection molding manufacturers in China.
Shipping Cost for design for injection molding import from China
When importing design for injection molding from China, the shipping cost can vary depending on several factors. The weight and dimensions of the package, the shipping method chosen, and the destination country all play a significant role in determining the shipping cost.
For small and light packages, air shipping is usually the preferred method due to its speed. However, it can be more expensive compared to other shipping methods. The cost is typically calculated based on the gross weight or volumetric weight of the package, whichever is greater. Volumetric weight takes into account both the weight and dimensions of the package. Air shipping costs for small packages can range from $5 to $10 per kilogram.
For larger and heavier packages, sea shipping is more economical. The cost is generally calculated based on the volume or cubic meter (CBM) of the shipment. It is important to note that there is often a fixed charge for a minimum volume, which means it may not be cost-effective to ship very small quantities. Sea shipping costs for larger packages can vary between $100 and $600 per CBM, depending on the specific requirements and destination.
In addition to the shipping costs, there are other factors to consider. Import duties, taxes, customs clearance fees, and handling charges are additional expenses that should be taken into account when calculating the overall shipping cost. These charges vary depending on the customs regulations and requirements of the destination country.
To ensure accurate pricing and to find the best shipping options, it is recommended to work with a reliable freight forwarder or shipping agent who has experience in handling imports from China. They can provide detailed guidance on the most cost-effective shipping methods and help navigate the customs procedures.
In conclusion, the shipping cost for design for injection molding import from China can vary based on the weight, dimensions, shipping method, and destination country. It is essential to consider these factors, along with additional expenses such as import duties and customs fees, to accurately estimate the total shipping cost.
Compare China and Other design for injection molding Markets: Products Quality and Price,Visible and Hidden Costs
China is known as a global manufacturing hub, particularly in the field of injection molding. However, it is essential to compare the Chinese market with other design for injection molding markets in terms of product quality, price, and visible and hidden costs.
In terms of product quality, China has made significant improvements over the years. Many Chinese manufacturers now adhere to international quality standards, ensuring that their products are of acceptable quality. However, other design for injection molding markets such as Germany, Japan, and the United States still lead in product quality due to their strict adherence to quality control measures and advanced technologies.
Price is a crucial factor when comparing markets. China’s manufacturing costs are generally lower than those of other countries, resulting in more competitive prices. This cost advantage has made China an attractive choice for companies seeking cost-effective solutions for injection molding. However, the price advantage should be carefully assessed as it does not always translate to better value. Other markets might offer higher quality products or unique features that justify a higher price point.
Visible costs in injection molding include raw materials, labor, machinery, and transportation. China’s large-scale production capabilities and vast supply chain infrastructure contribute to lower visible costs. In contrast, other markets may have higher visible costs due to higher wages, energy costs, and transportation expenses.
Hidden costs should also be considered. China’s design for injection molding market often faces challenges related to intellectual property protection, regulatory compliance, and product safety standards. These hidden costs can significantly impact a company’s overall expenses and must not be overlooked. Other markets generally have more reliable intellectual property protection, stricter regulations, and higher product safety standards, minimizing these hidden costs.
In summary, while China’s design for injection molding market offers competitive pricing and improved product quality, other markets such as Germany, Japan, and the United States still maintain an edge in terms of product quality and visible and hidden costs. Companies should carefully evaluate their specific requirements and consider factors beyond just price when deciding on the best market for their injection molding needs.
Understanding Pricing and Payment Terms for design for injection molding: A Comparative Guide to Get the Best Deal
When it comes to designing products for injection molding, understanding the pricing and payment terms is crucial to ensure you get the best deal. Here’s a comparative guide to help you navigate this process:
1. Design Complexity: The complexity of your design plays a significant role in determining the pricing. Intricate designs or those with complex features will typically require more time and effort, resulting in higher costs. Conversely, simpler designs with few details will be more cost-effective.
2. Tooling Costs: Injection molding requires tooling, which is the creation of molds used to produce the final product. Tooling costs can vary depending on factors such as the size and complexity of the mold. Some manufacturers may charge a separate fee for tooling, while others include it in the overall price. It is essential to clarify this upfront to avoid any surprises.
3. Material Selection: The choice of material is critical as it affects both the quality and cost of the final product. Different materials have varying price points, so understanding the pros and cons of each option is essential. Discuss with your manufacturer to find a suitable material that meets your requirements without exceeding your budget.
4. Quantity and Lead Time: The volume of units you require will influence the pricing, as manufacturers may offer discounts for larger quantities. Additionally, the lead time required to produce your product should be considered. Rush orders or shorter lead times may incur additional charges, so plan ahead to avoid any unforeseen expenditure.
5. Packaging and Shipping: While negotiating the pricing, it’s important to consider packaging and shipping costs. Some manufacturers provide all-inclusive prices that cover these expenses, while others charge separately. Evaluating these additional costs is crucial for an accurate comparison between different providers.
6. Payment Terms: Understand the payment terms offered by various manufacturers. It is common to pay a certain percentage upfront for tooling costs, followed by the remaining payment upon completion of the project. Knowing the payment schedule and terms of each manufacturer will help you determine the best fit for your budget.
To get the best deal, it is recommended to obtain multiple quotes from different manufacturers and evaluate them based on the factors mentioned above. However, be cautious not to compromise quality for the sake of cost savings. Look for a balance between affordable pricing and reliable manufacturing capabilities to ensure a successful injection molding project.
Chinese Regulations and Industry Standards Certifications for design for injection molding,Import Regulations and Customs for design for injection molding from China
Chinese Regulations and Industry Standards Certifications are essential for design for injection molding projects, ensuring compliance with safety, quality, and environmental standards. The most important certifications include:
1. China Compulsory Certification (CCC): For certain products, such as electrical and electronic goods, the CCC mark is mandatory and indicates compliance with Chinese safety standards.
2. China National Accreditation System for Conformity Assessment (CNAS): CNAS provides accreditation to testing and calibration laboratories, ensuring reliable and accurate measurements for design verification and validation.
3. ISO 9001: This certification demonstrates that the manufacturer has implemented a quality management system, ensuring consistent production processes and customer satisfaction.
4. ISO 14001: This certification emphasizes environmental management systems, ensuring proper waste disposal and reducing the environmental impact of the injection molding process.
5. RoHS compliance: This certification ensures that the product does not contain hazardous materials, such as lead, mercury, or cadmium, harmful to human health and the environment.
Importing design for injection molding from China requires adherence to Import Regulations and Customs procedures. Some important considerations include:
1. Customs Valuation: The value of the imported injection molding designs must be accurately declared for customs purposes, including the cost of manufacturing, packing, and transportation.
2. Import Taxes and Duties: Various taxes and duties, such as customs duty, value-added tax (VAT), and consumption tax, may apply and need to be determined before importing.
3. Import Licensing: Some products, especially those related to national security or health and safety, may require special licenses or permits for importation.
4. Customs Documentation: Proper documentation, such as a commercial invoice, packing list, bill of lading/airway bill, and customs declaration form, must be prepared accurately and provided to customs authorities.
5. Customs Clearance: The imported injection molding designs must go through customs clearance procedures, which may involve inspections, duty payments, and compliance checks.
To ensure a smooth import process, it is advisable to work with a reputable freight forwarder or customs broker familiar with Chinese import regulations and customs procedures. Seeking professional advice and understanding the relevant certifications and regulations will help importers avoid potential compliance issues and ensure a successful importation of design for injection molding from China.
Sustainability and Environmental Considerations in design for injection molding Manufacturing
Sustainability and environmental considerations play a significant role in the design for injection molding manufacturing process. This manufacturing method involves injecting molten material into a mold cavity to create a desired product shape. By incorporating sustainable practices and considering environmental impacts, manufacturers can minimize waste, conserve resources, and reduce their carbon footprint.
One aspect to consider is material selection. Opting for eco-friendly and biodegradable materials, such as bio-based polymers, can help reduce the overall environmental impact. These materials are derived from renewable sources and can often be composted at the end of the product’s lifecycle, minimizing waste and reducing landfill space.
In addition, designers can focus on reducing material usage by optimizing the product’s design. This includes using thinner walls, lighter structures, and incorporating hollow features where possible. By reducing the amount of material required, less energy and resources are used during the manufacturing process.
Efficient production planning is another crucial consideration. Manufacturers can implement lean manufacturing techniques to minimize energy consumption and waste. This involves optimizing production schedules, reducing setup times, and utilizing advanced manufacturing technologies that provide precise control over material flow and cooling. By streamlining the production process, manufacturers can minimize energy consumption and improve overall efficiency.
Proper waste management is vital in injection molding manufacturing. Designers and manufacturers should prioritize recycling and reusing materials whenever possible. This includes segregating waste, implementing recycling programs, and finding innovative ways to repurpose or recycle leftover materials or defective parts. By reducing waste sent to landfills and utilizing recycled materials, manufacturers can significantly reduce their environmental impact.
Lastly, end-of-life considerations should be taken into account during the design stage. Designers should strive for designs that are easy to disassemble and recycle, promoting a circular economy. By incorporating recyclable materials and designing products for easy disassembly, manufacturers can facilitate the recycling process and minimize the overall environmental impact.
In conclusion, sustainable and environmentally conscious design practices are crucial in injection molding manufacturing. By considering material selection, reducing material usage, optimizing production processes, implementing waste management strategies, and considering end-of-life considerations, manufacturers can create products that are more sustainable, minimize waste, and reduce their environmental footprint.
List The Evolution history of “design for injection molding”
Injection molding is a manufacturing process used to produce a wide range of plastic products. The design for injection molding has evolved significantly over the years, leading to improvements in efficiency, quality, and cost-effectiveness.
In the early years, designing for injection molding was a relatively straightforward process. Simple shapes and designs were used, with minimal complexity to ensure easy moldability. The focus was on creating functional parts rather than achieving aesthetically pleasing designs.
As advancements in injection molding technology occurred in the 1950s and 1960s, the design process became more intricate. Designers began incorporating more complex shapes and features into their designs, utilizing the capabilities of the injection molding process. Mold flow analysis tools were introduced to optimize the design and prevent defects such as warping, sink marks, and flow lines.
With the advent of computer-aided design (CAD) systems in the 1980s, the design for injection molding took a leap forward. CAD software allowed designers to create 3D models, enabling better visualization and improving communication between designers and manufacturers. This led to faster design iterations and reduced lead times.
The 1990s witnessed the adoption of more advanced simulation tools for design optimization. Moldflow analysis became an integral part of the design process, allowing the prediction and prevention of potential manufacturing issues. The focus shifted towards designing for manufacturability, aiming to minimize costs and cycle times.
In recent years, the emergence of additive manufacturing, also known as 3D printing, has influenced the design for injection molding. Prototypes and molds can now be quickly produced using 3D printing, enabling faster design iterations and reducing time to market. Designers can also explore complex geometries that were previously challenging or impossible to manufacture using traditional methods.
Today, the design for injection molding continues to evolve with advancements in materials, tooling, and technologies. Virtual reality and augmented reality are being integrated into the design process, allowing designers to visualize designs in a real-world context before moving into production. Digital twin technology is also being used to simulate and optimize the injection molding process.
In conclusion, the evolution of design for injection molding has been driven by advancements in technology, tools, and materials. From simple designs optimized for moldability to complex geometries and advanced simulation capabilities, the focus has been on achieving efficient, high-quality, and cost-effective manufacturing.
The Evolution and Market Trends in design for injection molding Industry
The design for injection molding industry has evolved significantly over the years, driven by advancements in technology and changing market trends. Injection molding is a manufacturing process that involves injecting molten material into a mold cavity, where it cools and solidifies into a desired shape. It is widely used in various industries, including automotive, electronics, medical, and consumer goods.
One major evolution in the design for injection molding industry is the use of computer-aided design (CAD) software. CAD allows designers to create complex and detailed 3D models of their products, which can be easily modified and optimized for the injection molding process. This has led to faster and more efficient design iterations, resulting in reduced time-to-market for new products.
Another trend in the industry is the increasing demand for lighter and more sustainable products. With concerns about environmental impact and energy efficiency, manufacturers are seeking ways to reduce material usage and optimize part design. This has led to advancements in techniques like thin-wall molding and the use of lightweight materials, such as composites and foams. These innovations not only reduce material waste but also provide cost savings and improved product performance.
Additionally, there is a growing trend towards miniaturization in the design for injection molding industry. This is driven by the demand for smaller, more portable devices, such as smartphones and wearables. Miniaturization requires precise and intricate part design, as well as advanced molding techniques to ensure the production of high-quality, small-sized components.
Furthermore, customization and personalization have become significant market trends in recent years. Consumers now expect products that are tailored to their specific needs and preferences. This has led to the development of technologies like multi-cavity molds and insert molding, which allow for the production of custom-designed parts in large quantities.
In conclusion, the design for injection molding industry has undergone significant evolution, driven by advancements in technology and changing market trends. The use of CAD software, the focus on lightweight and sustainable products, miniaturization, and the demand for customization are some of the key developments in the industry. These trends have not only improved the efficiency and effectiveness of the injection molding process but also enabled the production of innovative and high-quality products.
Custom Private Labeling and Branding Opportunities with Chinese design for injection molding Manufacturers
Chinese manufacturers are known for their expertise in injection molding and offer excellent opportunities for custom private labeling and branding. With their advanced manufacturing facilities and cost-effective production capabilities, they can fulfill the diverse requirements of businesses looking to create their unique product designs.
When it comes to custom private labeling and branding, Chinese manufacturers provide a wide range of options. They can incorporate logos, brand names, and other personalized elements into the design of plastic products through injection molding. With their extensive experience in this field, they can turn conceptual ideas into tangible products that reflect a brand’s identity.
Chinese manufacturers also offer branding opportunities through the use of specialized materials, finishes, and colors. They can produce products with specific textures, gloss levels, or patterns that align with a brand’s aesthetics and market positioning. This allows businesses to create distinctive products that stand out in the competitive market.
Moreover, Chinese manufacturers possess advanced design capabilities that enable them to assist businesses with product development and innovation. They can collaborate closely with clients throughout the design process, ensuring that the final product meets their exact specifications. This includes optimizing product functionality, aesthetics, and manufacturability to enhance overall branding.
Additionally, Chinese manufacturers often provide private labeling services such as custom packaging and labeling solutions. They can design and produce packaging that complements a brand’s identity and ensures the safe transportation of products. This allows businesses to present their products in a professional and appealing manner, strengthening their brand image.
Overall, leveraging Chinese manufacturers for custom private labeling and branding opportunities in injection molding can be highly beneficial. They combine their technical expertise, manufacturing capabilities, and design proficiency to help businesses create unique products that align with their brand identity. With cost-effective production and a wide range of customization options, Chinese manufacturers are an excellent option for businesses seeking to establish a strong brand presence in the market.
Tips for Procurement and Considerations when Purchasing design for injection molding
When it comes to purchasing designs for injection molding, it is important to consider various factors to ensure the procurement process goes smoothly and meets all requirements. Here are some tips and considerations to keep in mind:
1. Clear and Detailed Specifications: Provide clear and detailed specifications for the design, including dimensions, materials, required tolerances, and any specific features. This helps the supplier understand your requirements and avoids any misunderstandings.
2. Design for Manufacturability: Prioritize designs that are optimized for injection molding. Consider factors such as draft angles, wall thickness, undercuts, and fillets to ensure ease of production and minimize potential defects.
3. Material Selection: Choose the appropriate material for your injection molding project. Consider factors such as strength, chemical resistance, flexibility, and cost. Consult with your supplier to determine the best material that meets your specific needs.
4. Supplier Evaluation: Conduct a thorough evaluation of potential suppliers before making a final decision. Assess their expertise, experience, capacity, quality control measures, and certifications. Request samples, visit their facilities, and check client references to ensure they are reliable and capable of meeting your requirements.
5. Cost Analysis: Compare multiple quotes from different suppliers to ensure you are getting a competitive price. However, keep in mind that the lowest price may not always guarantee the best quality. Consider the overall value, including the supplier’s reputation, quality standards, and delivery time, in addition to the cost.
6. Intellectual Property Protection: Ensure that the supplier you choose respects intellectual property rights. Sign non-disclosure agreements and clearly define ownership and confidentiality in your contracts to protect your designs and trade secrets.
7. Quality Control: Establish quality control processes and standards to ensure the final product meets your specifications. This may include conducting inspections during production, testing samples, and evaluating the finished injection molded parts.
8. Communication and Collaboration: Maintain open and effective communication with the supplier throughout the procurement process. Regularly provide feedback, address concerns promptly, and discuss any necessary design modifications or improvements.
9. Timing and Lead Times: Consider the supplier’s lead times and production capacity to ensure timely delivery of your injection molded parts. Early involvement in the design process and clear project timelines will help avoid delays.
10. Scalability and Future Needs: Consider your future needs and scalability requirements. If you anticipate potential growth or modifications to the design, discuss these with the supplier to ensure they can accommodate future demands.
By following these tips and considerations, you can successfully procure designs for injection molding and achieve high-quality products that meet your requirements within a reasonable time frame and budget.
FAQs on Sourcing and Manufacturing design for injection molding in China
Q: Why should I consider sourcing and manufacturing design for injection molding in China?
A: China has become a global manufacturing powerhouse, offering competitive prices, a wide range of manufacturing capabilities, and a large pool of skilled labor. China’s injection molding industry is well-established, with a vast network of suppliers, manufacturers, and experienced professionals. Outsourcing to China can result in cost savings and access to advanced manufacturing technologies.
Q: What should I consider when sourcing injection molds from China?
A: Before sourcing injection molds from China, several factors should be considered. These include the supplier’s experience and expertise in injection molding, their quality control processes, the materials and manufacturing techniques used, and their ability to meet your specific requirements. It is essential to conduct proper due diligence, assessing the supplier’s reputation, certifications, and previous clients’ feedback.
Q: How can I ensure the quality of injection molding products manufactured in China?
A: Secure quality control measures are crucial when manufacturing injection molding products in China. Advanced quality systems, such as ISO certifications, should be verified, and inspections at various stages of production should be conducted. Suppliers should be willing to provide samples, conduct in-process quality checks, and perform final inspections before shipment. Implementing a comprehensive quality control plan and clearly communicating your expectations with the supplier will help ensure product quality.
Q: What are the typical lead times for sourcing and manufacturing injection molds in China?
A: Lead times can vary depending on the complexity of the molds and the supplier’s workload. On average, it can take anywhere from a few weeks to a few months to complete the entire process, including design, prototyping, tooling, and production. It is crucial to maintain open communication with the supplier and discuss lead times in advance to avoid any delays.
Q: How can I protect my intellectual property when manufacturing in China?
A: Intellectual property protection is a concern when manufacturing in China. It is advisable to sign a non-disclosure agreement (NDA) with the supplier to protect your designs and proprietary information. Additionally, filing for patents, trademarks, or design registrations can provide legal protection. Working with reputable suppliers and consulting legal professionals experienced in China’s intellectual property laws can further safeguard your interests.
Q: Are there any potential challenges or risks to consider when sourcing and manufacturing in China?
A: While China offers numerous benefits for sourcing and manufacturing, potential challenges and risks should be considered. These include language and cultural barriers, differences in business practices, potential shipping delays, and intellectual property concerns. Conducting thorough research, maintaining clear communication, and working with trusted partners can help mitigate these risks. Regular monitoring and quality control inspections throughout the manufacturing process are also essential to ensure consistent product quality.
Why contact sourcifychina.com get free quota from reliable design for injection molding suppliers?
Sourcifychina.com can get a free quota from Reliable Design for injection molding suppliers due to a mutually beneficial relationship and strategic partnership between the two companies. The partnership aims to provide a streamlined and efficient solution for sourcing injection molding suppliers in China.
Reliable Design, as a leading provider of design services for injection molding, understands the importance of having reliable and high-quality suppliers in China. They have recognized the value that Sourcifychina.com brings in terms of their extensive network of trusted manufacturers and efficient sourcing processes. By partnering with Sourcifychina.com, Reliable Design can leverage their expertise and connections to ensure that their clients have access to the best injection molding suppliers in China.
In return, Sourcifychina.com benefits from this partnership by gaining a competitive advantage in the industry. Having Reliable Design as a trusted partner strengthens their reputation and gives them credibility as a reliable sourcing company. The fact that Reliable Design provides them with a free quota further emphasizes their confidence in Sourcifychina.com’s capabilities.
With the free quota from Reliable Design, Sourcifychina.com can offer their clients additional value by providing them with quotes from injection molding suppliers without any upfront cost. This allows clients to get an idea of the cost and feasibility of their projects before committing to any supplier. It also saves clients time and effort in sourcing suppliers on their own.
Overall, the partnership between Sourcifychina.com and Reliable Design benefits both parties by providing a comprehensive sourcing solution and ensuring high-quality suppliers for injection molding projects in China. The free quota provided by Reliable Design adds value to Sourcifychina.com’s services and further strengthens their position in the market.