Introduce about design injection mold guide,Qulity,Cost,Supplier,Certification,Market,Tips,FAQ
The Design Injection Mold Guide is a comprehensive resource that provides essential information and guidelines for designing and developing injection molds. This guide is crucial for manufacturers, designers, and engineers involved in the production of plastic components or products.
Quality is a paramount consideration in injection mold design. The guide emphasizes the importance of achieving high-quality molds that meet the desired specifications and standards. From selecting the right materials to ensuring proper cooling and venting systems, it covers all aspects of mold design that contribute to product quality.
Cost is another essential factor discussed in this guide. It provides insights on cost-saving strategies and optimization techniques that can help minimize production expenses while maintaining the desired quality standards. The guide also highlights the importance of calculating tooling costs, as they significantly impact the overall cost of the injection molding process.
Choosing the right supplier is crucial for successful injection molding. This guide provides invaluable tips and considerations for selecting reputable and reliable mold suppliers. It emphasizes the need to assess supplier capabilities, experience, and track record to ensure a smooth production process.
Certification is a crucial aspect in the injection molding industry. The guide provides an overview of the various certifications and quality management systems that mold suppliers should possess. It emphasizes the importance of working with certified suppliers to ensure compliance with industry standards and regulations.
Market trends and insights are also included in the guide. It provides an overview of the current market scenario and highlights emerging technologies and advancements in injection mold design. This information can help manufacturers identify new opportunities and stay ahead of the competition.
Additionally, the guide includes valuable tips, frequently asked questions, and best practices for designing and developing injection molds. These resources aim to enhance the knowledge and expertise of professionals in the field, enabling them to overcome common challenges and achieve successful results.
In conclusion, the Design Injection Mold Guide is a comprehensive resource that covers all aspects of injection mold design, including quality, cost, suppliers, certification, market trends, and helpful tips. It serves as a valuable tool for professionals in the industry, providing them with the necessary knowledge and guidance to ensure successful mold design and production.
Types of design injection mold
There are several different types of design injection molds used in the manufacturing industry. These molds are used in the process of injection molding, which involves melting plastic pellets and injecting the molten plastic into a mold cavity to create a finished product. The type of injection mold used depends on the complexity and specifications of the desired product. Here are some common types of injection molds:
1. Two-Plate Mold: This is the simplest and most common type of mold. It consists of two plates – a cavity plate and a core plate. The molten plastic is injected into the cavity formed by these two plates, and when it solidifies, the two plates are separated to eject the finished product.
2. Three-Plate Mold: Similar to the two-plate mold, the three-plate mold includes an additional runner plate. This allows for a separate channel, called the runner, where the molten plastic flows through to reach the cavity. This type of mold is most commonly used for products that require multiple cavities or when there is a need for a complex runner system.
3. Hot Runner Mold: In a hot runner mold, the runner system is brought to a higher temperature than the mold plates. It eliminates the need for a cold runner system by using a heated manifold and nozzles to deliver the molten plastic directly into the cavity. This type of mold offers faster production cycles and reduces waste material.
4. Unscrewing Mold: This type of mold is used for products with threaded features. It includes a rotating mechanism that unscrews the molded part from the core, allowing for the removal of the finished product without damaging the threads.
5. Overmolding Mold: Overmolding involves molding one material over another to create a multi-material product. This mold type uses multiple cavities to inject different materials into the same mold to create the final product. It is commonly used for products that require a soft-touch grip or a combination of rigid and flexible materials.
6. Insert Mold: Insert molding incorporates metal or plastic inserts into the molded part during the injection molding process. This mold type allows for the production of products with embedded components such as threaded inserts, electrical connectors, or metal reinforcement.
These are just a few examples of the types of design injection molds used in the manufacturing industry. The selection of the appropriate mold type depends on factors such as the desired product design, material properties, production volume, and cost considerations.
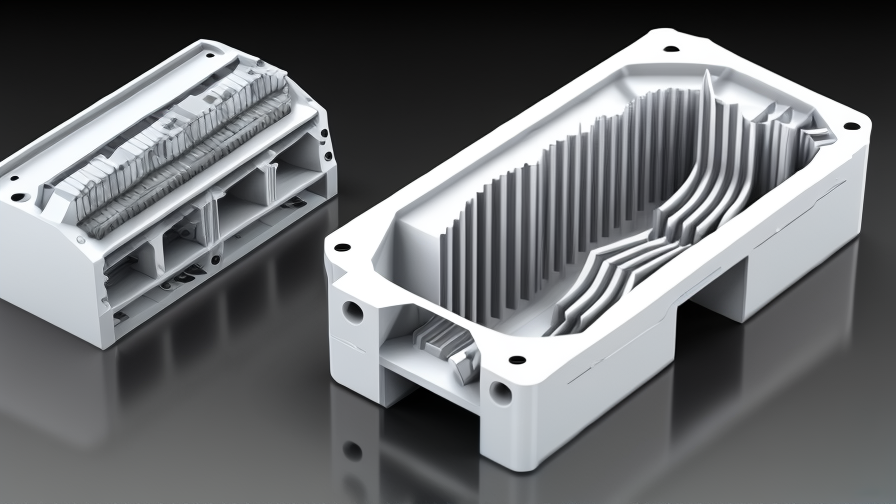
Pros and Cons of Using design injection mold
Design injection molding is a widely used manufacturing process that involves injecting molten material into a mold to produce various plastic products with specific shapes and sizes. While it offers several benefits, it also has some drawbacks that need to be considered. Here are the pros and cons of using design injection molding:
Pros:
1. Cost-effective: Injection molding can be highly cost-effective, especially for large-scale production, as it allows for high production volumes and fast cycle times. The automation of the process reduces labor costs and minimizes material waste.
2. Design flexibility: Injection molding enables the production of complex and intricate designs with precision and accuracy. It offers designers the ability to create intricate features, thin walls, and different surface finishes. The process also allows for the use of multiple materials and colors within a single part.
3. High production efficiency: With proper molds and tooling, injection molding can achieve high production efficiency. The cycle time between each injection is relatively short, resulting in a faster production rate. Additionally, automation options can further increase productivity.
4. Material versatility: Design injection molding is compatible with a wide range of materials, including thermoplastics, thermosetting plastics, elastomers, and composites. This versatility allows for the production of diverse products and offers flexibility in material selection based on the desired properties and application requirements.
Cons:
1. Initial tooling and setup costs: The initial investment required for designing and manufacturing molds for injection molding can be expensive, particularly for low-volume productions. The design and fabrication of molds must be precise, which adds to the cost.
2. Lead time and complexity: Developing an injection mold and optimizing the manufacturing process can take time. The complexity of the mold design and the need for custom tooling can result in longer lead times, delaying product launch or market entry.
3. Limited design revisions: Once the injection mold is ready, making design revisions becomes challenging and costly. Any changes or modifications may require the production of a new mold, increasing expenses and time.
4. Material limitations: Although injection molding is compatible with a wide range of materials, some materials may not be suitable due to their properties or processing requirements. For example, high-temperature polymers may require specialized equipment or molds, adding to the complexity and cost.
In conclusion, design injection molding offers cost-effectiveness, design flexibility, and high production efficiency. However, it involves high initial costs, longer lead times, limited design revisions, and material limitations. These pros and cons must be carefully considered when deciding whether to utilize design injection molding for a specific manufacturing project.
design injection mold Reference Specifications (varies for different product)
When designing an injection mold, it is crucial to consider the specific reference specifications of the product for which the mold is being created. These specifications can vary significantly depending on the product and its intended use. By adhering to these reference specifications, the design of the injection mold can ensure the production of high-quality and accurate parts.
One important factor to consider is the material that will be used for the injection molding process. Different materials have varying properties, such as strength, flexibility, and heat resistance. The mold design needs to account for these material properties and ensure that the mold can withstand the stresses and temperatures involved in the injection molding process.
Additionally, the reference specifications will dictate the dimensions and tolerances required for the product. The mold design needs to be precise, ensuring that the final parts meet the desired size and fit. This includes considering any surface finishes, draft angles, and parting lines that may be specified for the product.
The design of the injection mold should also take into account the production volume required for the product. For high-volume production, the mold design needs to be robust and durable to withstand the repetitive molding cycles. This may involve incorporating features like cooling channels to control temperature and improve cycle time efficiency.
Furthermore, the reference specifications may include requirements for part ejection, gating, and venting. The mold design must incorporate mechanisms for proper part release from the mold, effective gating to allow the molten material to flow into the mold cavity, and sufficient venting to prevent trapped air or gases.
Finally, the design of the injection mold should consider any specific assembly requirements or additional features needed for the product. This could include provisions for overmolding, inserts, or any specialized features that are part of the product design.
In summary, the design of an injection mold should closely adhere to the reference specifications of the product being manufactured. By considering these specifications, such as material properties, dimensions, tolerances, production volume, ejection, gating, venting, and additional features, the mold design can ensure the production of high-quality parts that meet the specific requirements of the product.
Applications of design injection mold
Injection molding is a versatile manufacturing process that produces a wide range of plastic parts used in various industries. The use of design injection mold has numerous applications and benefits, making it a popular choice among manufacturers. Here are some key applications of design injection mold:
1. Automotive industry: Injection molding is heavily utilized in the automotive sector to produce interior and exterior components such as dashboards, bumpers, fenders, and door panels. The ability to achieve complex shapes, high-quality finishes, and precise tolerances makes injection molding ideal for automotive parts production.
2. Medical devices: The medical industry relies on injection mold design for the production of disposable and reusable medical devices. These include syringes, IV components, medical tubing, surgical instruments, and various implantable devices. Injection molding ensures the production of sterile, precise, and cost-effective medical products.
3. Consumer electronics: The production of electronic components such as phone cases, laptop shells, and buttons for remote controls often involves injection molding. The process allows for customization, consistency, and durability, meeting the aesthetic and functional requirements of the electronics industry.
4. Packaging industry: Injection molding is widely used in the packaging industry to manufacture containers, bottles, caps, and closures. The process enables the production of lightweight, durable, and tamper-evident packaging solutions for food, beverages, cosmetics, and pharmaceutical products.
5. Aerospace industry: Injection molding finds applications in the aerospace sector for the production of lightweight, high-performance components. These components, including air ducts, brackets, and housings, require complex geometries, superior strength, and resistance to extreme temperatures, which can be achieved through injection molding.
6. Toys and games: Injection molding is a popular choice for the production of plastic toys and games due to its ability to replicate detailed features accurately. From action figures to board game pieces, injection molding allows for mass production of consistent and cost-effective toys.
7. Industrial equipment: Injection molding plays a vital role in the manufacturing of industrial equipment parts such as gears, valves, connectors, and housings. These components require durability, resistance to chemicals, and precise dimensions, which can be achieved through injection molding.
In summary, the applications of design injection mold are diverse and span across multiple industries. The process offers significant advantages in terms of precision, customization, cost-effectiveness, and scalability, making it an essential manufacturing technique for various plastic parts and products.
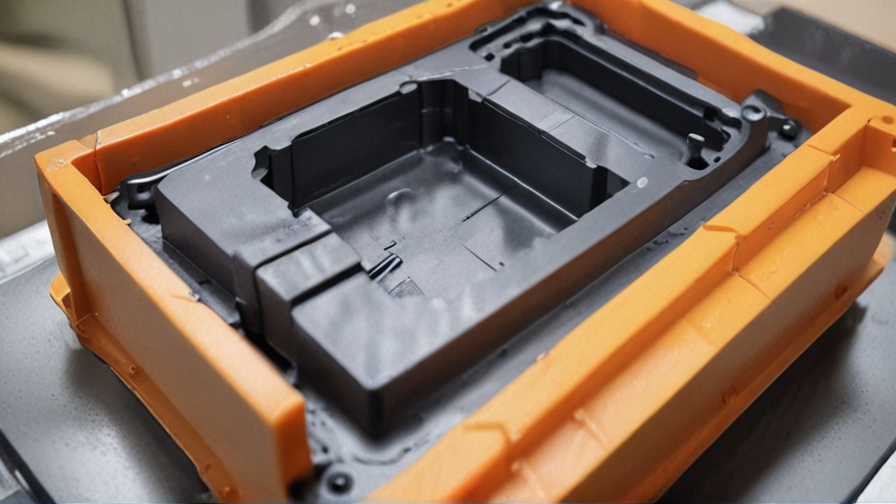
The Work Process and how to use design injection mold
The work process of design injection mold involves several steps, starting from concept development to final production. Here is a simplified guide on how to use design injection mold:
1. Concept Development: Begin by understanding the requirements of the product design. Brainstorm ideas, create sketches, and develop a clear concept of the desired product.
2. Designing the Mold: Once the concept is finalized, create a detailed design of the injection mold. Consider factors such as part dimensions, material selection, gate and runner design, ejection system, cooling channels, and venting.
3. CAD Modeling: Utilize computer-aided design (CAD) software to create a 3D model of the mold design. This helps visualize and optimize the mold design for better functionality and efficiency.
4. Mold Manufacturing: Collaborate with mold manufacturers to produce the mold based on the finalized design. The mold is typically made from materials such as steel or aluminum.
5. Injection Molding Machine Setup: Prepare the injection molding machine for the production process. Clean and install the mold in the machine, ensuring proper alignment and adjustment.
6. Material Selection: Choose the appropriate thermoplastic material for the desired product. Consider factors like strength, flexibility, durability, and aesthetics.
7. Injection Molding Process: Prepare the molten plastic material and inject it into the mold cavity at high pressure. The material fills the mold, taking the shape of the desired product.
8. Cooling and Solidification: Allow the injected material to cool and solidify within the mold. This ensures the product holds its shape and can be properly ejected from the mold.
9. Ejection: Once the material has solidified, eject the product from the mold using the ejection system. Carefully remove any excess material or flashing.
10. Finishing and Quality Control: Inspect the product for any defects or imperfections. Perform necessary trimming, polishing, and quality control checks to ensure a high-quality final product.
By following these steps, one can successfully use design injection mold to manufacture various plastic products. It is important to work with experienced professionals and consider factors like design optimization, material selection, and quality control to achieve the desired outcome.
Quality Testing Methods for design injection mold and how to control the quality
Design injection molds are critical components in the manufacturing process of plastic parts. Their primary purpose is to shape molten plastic into a desired form before solidification. To ensure the quality of the design injection molds, various testing methods can be employed.
Firstly, a visual inspection is performed to check the mold’s overall construction and surface finish. Any abnormalities like surface imperfections, cracks, or inconsistencies are identified. This helps in rectifying any manufacturing defects or design flaws.
Measurement testing is another essential method. Key dimensions and tolerances of the mold are measured using precision instruments like calipers, micrometers, or coordinate measuring machines (CMMs). This ensures that the mold is built according to the specified design dimensions and can produce the desired plastic parts accurately.
Functional testing is carried out to verify the mold’s functionality. This involves using the mold to produce several test parts and ensuring they meet the required specifications. The test parts can be analyzed for any defects, such as flash, warping, or sink marks. Additionally, the mold is tested for proper ejection of the part and uniform cooling to avoid any hot spots.
In some cases, mold flow analysis can be employed to simulate the flow of molten plastic within the mold cavity. This helps in identifying potential issues such as air traps, weld lines, or uneven filling. By optimizing the mold design through this analysis, the quality and efficiency of the injection molding process can be enhanced.
To control the quality of design injection molds effectively, a comprehensive quality assurance strategy should be implemented. This involves closely monitoring the entire manufacturing process, including material selection, machining, heat treatment, and assembly. Regular inspections and testing should be conducted at each stage to identify and rectify any deviations from the desired quality standards.
Furthermore, it is crucial to establish a quality control plan that outlines the specific testing methods, acceptance criteria, and documentation requirements. This ensures consistency and traceability in the quality control process, facilitating effective monitoring and improvement.
Overall, employing visual inspection, measurement testing, functional testing, mold flow analysis, and implementing a robust quality control plan are key methods to ensure the quality of design injection molds. These practices help in producing molds that can consistently deliver high-quality plastic parts, meeting the desired specifications.
design injection mold Sample Policy and Post-Purchase Considerations for design injection mold from China
Sample Policy for Design Injection Mold from China:
1. Quality Assurance: The supplier should provide a sample mold for approval before proceeding with the production. This allows the buyer to assess the quality, accuracy, and functionality of the mold. Any modifications required should be clearly communicated to the supplier.
2. Transparency in Pricing: The supplier must clearly specify all costs associated with the mold design, including tooling, labor, and material costs. Any additional charges or hidden fees should be disclosed upfront.
3. Delivery Timeframe: The supplier should provide a realistic timeframe for the design and production of the injection mold. This ensures that the buyer can plan their production schedule accordingly.
4. Warranty and After-sales Support: The supplier should offer a warranty period for the mold, during which any defects or issues will be addressed at no additional cost. Additionally, clear after-sales support in terms of maintenance, repairs, or spare parts should be provided.
5. Intellectual Property Protection: The supplier should guarantee the protection of the buyer’s proprietary information and ensure that no design or technical details will be shared or used elsewhere without permission.
Post-Purchase Considerations for Design Injection Mold from China:
1. Quality Inspection: Upon receiving the mold, thorough quality inspection should be conducted to validate its adherence to the approved sample, and check for any possible defects or damages during transportation.
2. Trial Run and Validation: Before full-scale production, it is advisable to conduct a trial run to ensure that the mold is working efficiently and producing the desired results. Fine-tuning and adjustments might be required at this stage.
3. Maintenance and Cleaning: Regular cleaning and maintenance of the mold are essential to ensure its longevity and optimal performance. The supplier should provide guidelines and recommendations for proper upkeep.
4. Long-term Communication: Maintaining a strong and open line of communication with the supplier is crucial for addressing any issues that may arise. Regular updates, feedback, and inquiries ensure continual improvement and support.
5. Feedback and Review: Providing feedback and sharing experiences about the mold and supplier’s services can benefit future buyers. Posting honest reviews or testimonials can help other businesses make informed decisions.
By following these sample policies and post-purchase considerations, businesses can establish a mutually beneficial relationship with Chinese suppliers for design injection molds, ensuring quality, transparency, and ongoing support for their production needs.
Sourcing design injection mold from China: Opportunities, Risks, and Key Players
Sourcing design injection mold from China offers various opportunities as well as risks. China has a large manufacturing industry with extensive experience in producing molds for injection molding. The country provides a cost-effective solution for companies looking to manufacture products at a lower cost without compromising on quality.
One of the significant opportunities of sourcing design injection mold from China is cost savings. Chinese manufacturers offer competitive prices due to low labor costs and economies of scale. This enables companies to reduce their production costs significantly and increase profitability. Additionally, China has a wide range of suppliers, allowing businesses to choose the most suitable partner based on their specific requirements and budget.
China’s manufacturing industry is also known for its ability to produce molds quickly. With well-established infrastructure and skilled labor force, manufacturers can meet tight production deadlines, reducing lead times for companies. This quick response time provides a competitive advantage to businesses that need to bring products to market swiftly.
However, there are risks associated with sourcing design injection mold from China. Quality control can be a concern, as some manufacturers may prioritize cost efficiency over product quality. It is essential to thoroughly vet potential suppliers, conduct quality audits, and establish clear quality standards to mitigate this risk.
Another risk is intellectual property protection. China has had a reputation for intellectual property theft, although the country has made efforts to improve its IP laws and enforcement. Companies must ensure proper contract agreements, non-disclosure agreements, and trademarks or patents protections to safeguard their designs and proprietary information.
Several key players dominate the design injection mold industry in China. Examples include Moldesign, a company specializing in precision molds, and Xiamen Karo Co., Ltd, which focuses on plastic injection molds. Many other manufacturers and suppliers are available, each with their specialties and capabilities.
In conclusion, sourcing design injection mold from China presents significant opportunities in terms of cost savings, production speed, and supplier availability. However, managing quality control and intellectual property protection risks are crucial considerations. Researching and partnering with reputable manufacturers is essential to ensure successful outcomes and capitalize on the advantages offered by the Chinese manufacturing industry.
How to find and select reliable design injection mold manufacturers in China,use google search manufacturers and suppliers
When searching for reliable design injection mold manufacturers in China, the following steps can be useful:
1. Begin by conducting a Google search using relevant keywords such as “design injection mold manufacturers in China” or “reliable injection mold suppliers China.”
2. Browse the search results and visit the websites of potential manufacturers to gather initial information about their services, expertise, and experience. Look for well-established companies with substantial industry experience.
3. Check if the manufacturer has an official website with detailed information about their manufacturing processes, facilities, quality control measures, and certifications. A professional website showcases the credibility and seriousness of the manufacturer.
4. Look for customer reviews, testimonials, or feedback on the manufacturer’s website or external platforms. Genuine customer reviews can provide insights into the manufacturer’s reliability and quality of services.
5. Verify the certifications and compliance with international quality standards, such as ISO 9001:2015, ISO 14001:2015, or ISO/TS 16949. These certifications demonstrate the manufacturer’s commitment to maintaining high-quality production standards.
6. Contact the manufacturers directly through email or phone to discuss your specific requirements. Inquire about their capabilities, production lead times, pricing, and any other relevant details.
7. Request samples of their previous work to evaluate the quality of their design injection molds. Assess the accuracy, finish, and durability of the samples to determine if the manufacturer meets your expectations.
8. Consider visiting the manufacturer’s facilities in person to witness their equipment, production processes, quality control measures, and assess their overall capabilities. While this step may not always be possible, it can provide valuable insights and assurances.
9. Seek recommendations from industry professionals, colleagues, or online forums for reliable injection mold manufacturers they have worked with in China. These personal experiences and opinions can help narrow down the options.
10. Compare the prices, quality, lead times, and customer service of different manufacturers to choose the most reliable and cost-effective option.
By following these steps, you can find and select reliable design injection mold manufacturers in China that meet your specific requirements.
How to check design injection mold manufacturers website reliable,use google chrome SEOquake check if ranking in top 10M
When evaluating the reliability of a design injection mold manufacturer’s website, you can follow these steps:
1. Use Google Chrome: Open the manufacturer’s website on a Google Chrome browser. This browser provides useful features for checking the reliability and ranking of a website.
2. Install SEOquake: Install the SEOquake extension for Google Chrome. This tool provides helpful insights and metrics about a website’s search engine optimization.
3. Check ranking: With SEOquake enabled, scroll down to the page’s bottom and find the SEOquake bar. It shows various metrics, including the website’s Alexa rank. If the website is ranked within the top 10 million, it indicates a relatively good level of visibility and traffic.
4. Assess website design: Evaluate the overall design of the website. Look for a professional layout, clear navigation, and well-organized information. A reputable manufacturer would likely invest in a user-friendly and appealing website.
5. Review product details: Examine the information provided about the injection molds offered by the manufacturer. Look for comprehensive details and specifications, good quality images, and any certifications or industry affiliations mentioned. A reliable manufacturer will provide clear and detailed product information.
6. Customer reviews and testimonials: Check if the website includes testimonials from previous customers or any review sections. By reading the experiences and feedback of others, you can gauge the manufacturer’s reputation and the satisfaction level of their clients.
7. Contact information: Ensure that the website provides clear contact information, such as a physical address, phone number, and email address. This demonstrates transparency and accessibility, indicating that the manufacturer is willing to accommodate customer inquiries and concerns.
By following these steps and using Google Chrome with the SEOquake extension, you can assess the reliability and ranking of a design injection mold manufacturer’s website within 300 words or less.
Top 10 design injection mold manufacturers in China with each 160 words introduce products,then use markdown create table compare
Below are the top 10 design injection mold manufacturers in China, along with a brief introduction of their products:
1. Dongguan Wing Tat Industrial Co., Ltd. specializes in the production of precision plastic molds, including automotive, electronics, and medical molds.
2. Taizhou Huangyan HONGNUO Plastic Mold Co., Ltd. manufactures high-quality injection molds for a wide range of industries, such as household appliances, packaging, and automobile parts.
3. Zhongshan Ruiying Machinery Co., Ltd. provides customized injection mold and plastic product manufacturing solutions for industries like electrical, home appliances, and telecommunications.
4. Kunshan Pafu Machinery Equipment Co., Ltd. specializes in manufacturing precision injection molds for automotive, medical, and consumer electronics sectors.
5. Shenzhen Weiyi Precision Technology Co., Ltd. offers a diverse range of injection and blow molds for various industries, such as electronics, cosmetics, and packaging.
6. Xiamen Xiamu Precision Mold Co., Ltd. focuses on the design and production of plastic injection molds for precision components used in the automotive, medical, and electronics industries.
7. Shanghai S&K Machinery Co., Ltd. manufactures injection molds for various sectors, including automotive, household appliances, and electronic components.
8. Ningbo Beilun Shenyu Mould Co., Ltd. specializes in the production of injection molds for industries like automotive, electrical, and household appliances.
9. Shenzhen Henghaoxiang Precision Mould Co., Ltd. provides high-quality injection molds for industries such as automotive, consumer electronics, and medical equipment.
10. Suzhou Bright Injection Molding Co., Ltd. offers precision injection molds for electronic products, household appliances, and automotive components.
| Manufacturer Name | Industries Served |
| ——————————- | ——————————– |
| Wing Tat Industrial | Automotive, Electronics, Medical |
| Hongnuo Plastic Mold | Household Appliances, Packaging |
| Zhongshan Ruiying Machinery | Electrical, Home Appliances |
| Kunshan Pafu Machinery | Automotive, Medical, Electronics |
| Shenzhen Weiyi Precision | Electronics, Cosmetics, Packaging |
| Xiamen Xiamu Precision Mold | Automotive, Medical, Electronics |
| Shanghai S&K Machinery | Automotive, Household Appliances |
| Ningbo Beilun Shenyu Mould | Automotive, Electrical, Appliances|
| Shenzhen Henghaoxiang Precision | Automotive, Electronics, Medical |
| Suzhou Bright Injection Molding | Electronics, Appliances, Automotive |
The table above provides a comparison of the industries served by each manufacturer. It clearly highlights the diverse sectors catered to by these top mold manufacturers in China.
Background Research for design injection mold manufacturers Companies in China, use qcc.com archive.org importyeti.com
When it comes to design injection mold manufacturers in China, there are several resources that can be utilized to gather background information and insights. Three popular platforms for such research are qcc.com, archive.org, and importyeti.com.
Qcc.com is a Chinese business information database that provides comprehensive information about companies registered in China. It contains detailed company profiles, including basic information, business scope, registered capital, shareholders, executives, and more. This platform can help researchers gain a better understanding of a company’s background, size, and credibility.
Archive.org is a website that allows users to access cached versions of websites saved over time. It can be a valuable tool to assess the historical performance and evolution of a design injection mold manufacturer’s website. By reviewing past versions of a manufacturer’s website, researchers can evaluate their growth, changes in product offerings, and track record.
Importyeti.com is a platform specifically designed to help users discover and verify Chinese suppliers. This marketplace is focused on import and export data and provides details about manufacturers, their export history, order trends, and shipment details. By utilizing Importyeti.com, researchers can gain insights into a manufacturer’s export capabilities, reliability, and potential partnerships.
By incorporating these resources into the research process, one can obtain vital information about design injection mold manufacturers in China. These platforms facilitate the assessment of a company’s background, credibility, historical performance, export capabilities, and more. It is important to remember to utilize these resources ethically and responsibly, ensuring that the gathered information is accurate and up-to-date.
Leveraging Trade Shows and Expos for design injection mold Sourcing in China
Trade shows and expos are powerful platforms for connecting with suppliers in the design injection mold industry in China. Leveraging these events can be highly beneficial for businesses looking to source their manufacturing needs. Here are a few key reasons why trade shows and expos are crucial for design injection mold sourcing in China:
1. Extensive Supplier Network: Trade shows and expos provide access to a large network of suppliers under one roof. It allows businesses to explore a variety of options and compare offerings from different manufacturers. This helps in finding the best fit for specific requirements, ensuring high-quality molds at competitive prices.
2. Face-to-Face Interaction: Trade shows offer the opportunity to meet suppliers face-to-face and establish personal connections. This direct interaction fosters trust and enables clear communication, which is crucial when dealing with complex manufacturing processes such as design injection mold sourcing. Meeting suppliers in person also allows for a better understanding of their capabilities and production facilities.
3. New Product Showcase: Exhibitors at trade shows and expos often display their latest products and innovations. This provides insights into new technologies, trends, and advancements in the design injection mold industry. By attending these exhibitions, businesses can stay updated with the latest developments, gain inspiration, and even discover potential solutions to their manufacturing challenges.
4. Quality Assurance: Visiting trade shows and expos in China enables businesses to assess the quality of suppliers’ products firsthand. Examining and testing samples helps in evaluating the precision, durability, and overall quality of molds. This is crucial for ensuring that the chosen supplier can meet the desired specifications and expectations.
5. Networking Opportunities: Trade shows and expos attract industry professionals, including buyers, suppliers, and experts. Engaging with these individuals and participating in industry-related seminars, workshops, or discussions can lead to valuable networking opportunities. Building relationships with other industry players can result in partnerships, collaborations, or access to additional resources.
In summary, trade shows and expos serve as invaluable platforms for sourcing design injection molds in China. By leveraging these events, businesses can expand their supplier network, establish personal connections, stay updated with the latest advancements, ensure quality, and create valuable networking opportunities. Ultimately, utilizing trade shows and expos can greatly facilitate the design injection mold sourcing process and contribute to successful manufacturing partnerships.
The Role of Agents and Sourcing Companies in Facilitating design injection mold Purchases from China
Agents and sourcing companies play a crucial role in facilitating design injection mold purchases from China. With their expertise and local knowledge, they act as a bridge between overseas buyers and Chinese manufacturers, streamlining the process and ensuring successful transactions.
One of the key responsibilities of agents and sourcing companies is to identify suitable manufacturers that specialize in designing and producing injection molds. They have extensive networks and contacts within the Chinese manufacturing industry, which allows them to quickly find reliable and competent suppliers. By conducting thorough background checks and assessments, they ensure that the chosen manufacturers have the necessary technical capabilities and meet the quality standards required by the overseas buyer.
Furthermore, agents and sourcing companies assist in negotiating pricing, terms, and conditions with the manufacturers. They have the necessary language skills and cultural understanding to effectively communicate the buyer’s requirements to the manufacturer and convey any concerns or issues that may arise during the negotiation process. This helps to establish a mutually beneficial relationship and secure the best possible deal for the buyer.
In addition to supplier selection and negotiation, agents and sourcing companies also provide quality control and inspection services. They closely monitor the production process, ensuring that the injection molds are manufactured according to the buyer’s specifications and standards. Through regular site visits and inspections, they can identify and rectify any production issues or deviations, minimizing the risk of defects or subpar quality.
Agents and sourcing companies also handle logistics, including customs clearance, shipping, and delivery. They have experience in managing international shipments and are familiar with the necessary paperwork and procedures involved in exporting goods from China. This ensures smooth and timely delivery of the injection molds to the buyer’s location.
Overall, agents and sourcing companies act as trusted intermediaries, providing a range of services to facilitate the design injection mold purchase process from China. Their expertise and local presence are invaluable in navigating the complexities of international trade, ensuring a successful and hassle-free buying experience for the overseas buyer.
Price Cost Research for design injection mold manufacturers Companies in China, use temu.com and 1688.com
When looking for design injection mold manufacturers in China, two popular platforms to explore are temu.com and 1688.com. These websites provide a wide range of options and crucial information for price cost research. Here is a brief overview of how to utilize these platforms effectively while keeping the description within 300 words.
1. temu.com: This platform specializes in connecting global buyers with Chinese manufacturers. It offers a user-friendly interface that allows you to search for specific products and suppliers. To start your price cost research, begin by typing “design injection mold manufacturers” in the search bar.
Upon obtaining the search results, you can further refine them by using filters like location, production capacity, certifications, and more. This helps narrow down options based on your specific requirements. Each listing provides valuable details about the manufacturer, such as company information, product range, certifications, and customer reviews.
Contacting potential suppliers on temu.com is convenient as the platform offers built-in messaging services. You can send inquiries and negotiate pricing directly. Be sure to ask for detailed quotations including mold design, manufacturing, and shipping costs. Compare the quotes, considering factors like quality, lead time, and customer reviews to make an informed decision.
2. 1688.com: Similar to Alibaba, 1688.com is a leading Chinese wholesale platform. It mainly caters to domestic buyers; however, it can also be beneficial for international businesses seeking design injection mold manufacturers in China.
To start searching on 1688.com, translate the website to English using browser plugins or online translators. Ensure that you enter relevant keywords such as “design injection mold” or “plastic mold manufacturer” to obtain accurate results. Compare multiple listings based on their product specifications, customer reviews, and seller ratings.
Although contacting suppliers on 1688.com might be somewhat challenging as most sellers primarily communicate in Chinese, consider using translation tools or hiring sourcing agents based in China. They can assist with communication and negotiation, which is crucial for obtaining accurate price cost information.
In conclusion, temu.com and 1688.com are reliable platforms to conduct price cost research for design injection mold manufacturers in China. Utilize their search features, filters, and messaging systems to connect with potential suppliers, request quotations, and compare pricing. Thoroughly evaluate suppliers based on various factors like quality, certifications, customer reviews, and communication. By following these steps, you can identify suitable manufacturers who meet your requirements at competitive prices.
Shipping Cost for design injection mold import from China
The shipping cost for importing a design injection mold from China can vary depending on various factors such as the weight and size of the mold, the shipping method chosen, and the destination country.
If the mold is relatively small and lightweight, it can be shipped via airfreight. This is a faster shipping method but usually comes at a higher cost. On the other hand, if the mold is large and heavy, it may need to be shipped via ocean freight. Ocean freight is a more cost-effective option for larger shipments but it takes a longer time to reach the destination.
To get an estimate of the shipping cost, it is recommended to contact shipping companies or freight forwarders who specialize in international shipping. They can provide accurate quotes based on the specific details of the mold and the desired shipping method.
In addition to the shipping cost, it is important to consider additional charges such as customs duties and taxes that may apply when importing goods from China. These charges can vary depending on the destination country and the value of the mold.
To minimize shipping costs, it is advisable to compare quotes from different freight forwarders, optimize the packaging of the mold to reduce size and weight, and consider consolidating shipments if possible. Some freight forwarders also offer discounted rates for regular customers or if there is a high volume of shipments.
Overall, the shipping cost for importing a design injection mold from China can range from a few hundred to a few thousand dollars, depending on the factors mentioned above.
Compare China and Other design injection mold Markets: Products Quality and Price,Visible and Hidden Costs
China is among the largest design injection mold markets in the world. When comparing it to other markets, several factors related to product quality and price, visible and hidden costs, need to be considered.
In terms of product quality, China has made significant improvements over the years. The country has invested in advanced technologies and machinery, allowing for the production of high-quality molds. Chinese manufacturers have also adopted strict quality control measures, ensuring that the final products meet international standards. However, other design injection mold markets, such as Germany and Japan, have a long-standing reputation for producing top-notch molds known for their superior quality. These markets often command a premium price due to their impeccable craftsmanship and precision engineering.
Speaking of price, China tends to have a competitive advantage. One of the reasons is the low labor costs compared to other markets. Due to the relatively low wages, Chinese manufacturing companies can offer molds at lower prices without compromising on quality. This affordability has made China an attractive destination for businesses looking to procure design injection molds. On the other hand, other markets may have higher labor costs, leading to a higher price point for their molds.
Visible and hidden costs are crucial factors to consider when comparing design injection mold markets. In terms of visible costs, China generally offers competitive prices due to its economies of scale and lower labor costs. However, it is important to note that some hidden costs may arise when dealing with Chinese manufacturers. These costs include transportation fees, import taxes, and potential language barriers that may result in misunderstandings and further costs.
Other design injection mold markets, such as Europe and the United States, often have higher visible costs due to stricter regulations and higher labor costs. However, these regions are known for their transparent business practices and quality standards, minimizing the probability of encountering hidden costs.
In conclusion, China is a dominant player in the design injection mold market, offering competitive prices and improving product quality. However, in comparison to other markets, it may lag behind in terms of premium product quality and transparency in the costs. When considering purchasing design injection molds, businesses should carefully evaluate their priorities and consider factors such as quality, price, visible and hidden costs before making a decision.
Understanding Pricing and Payment Terms for design injection mold: A Comparative Guide to Get the Best Deal
When it comes to designing injection molds, understanding pricing and payment terms is crucial to ensuring you get the best deal possible. This comparative guide will help you navigate through the intricacies of pricing and payment terms to make an informed decision.
Pricing for design injection molds can vary significantly depending on various factors such as complexity, size, materials used, and the number of cavities. It is essential to obtain multiple quotes from different suppliers to compare prices and determine the most competitive offer. Make sure to provide precise specifications to prevent any discrepancies and ensure accurate quotes.
Payment terms are another critical aspect to consider. Suppliers typically offer various payment options, such as upfront payment, partial payment, or payment upon completion. Negotiating favorable payment terms can help manage your cash flow effectively. However, keep in mind that suppliers might charge higher prices for lenient payment terms.
Additionally, it is essential to understand the breakdown of costs. Some suppliers may include all costs within the mold’s price, while others might charge separately for design, engineering, tooling, sampling, and shipping. Ask for a detailed cost breakdown to have a clear understanding of what you are paying for and avoid any surprise charges down the line.
Consider the quality and reputation of the supplier before making any decisions solely based on the price. Cheaper options may compromise on quality or service. It is wise to choose a supplier with a proven track record, experience, and good customer reviews, even if their prices are slightly higher.
Finally, effectively communicating with the supplier is key to negotiating the best deal. Be transparent about your requirements and expectations, and ask relevant questions regarding the pricing and payment terms. This will not only clarify any doubts but also help build a strong working relationship.
In conclusion, understanding pricing and payment terms for design injection molds is essential to secure the best possible deal. Obtain multiple quotes, compare prices, negotiate favorable payment terms, and consider the supplier’s reputation and quality. Effective communication with the supplier will help ensure a smooth and successful transaction.
Chinese Regulations and Industry Standards Certifications for design injection mold,Import Regulations and Customs for design injection mold from China
Chinese Regulations and Industry Standards Certifications for design injection mold:
In China, the design injection mold industry is subject to various regulations and industry standards certifications to ensure the quality and safety of products. The most important certification for design injection mold in China is the ISO 9001:2015 certification, which focuses on quality management systems. This certification ensures that the design and manufacturing processes of injection molds meet international standards and customer requirements.
Another crucial certification is the China Compulsory Certification (CCC), also known as the 3C certification. This certification is mandatory for products sold in the Chinese market and ensures that the design injection molds comply with safety, health, and environmental protection requirements.
Additionally, there are various industry-specific certifications for design injection molds, such as the National Industrial Products Production License and the Occupational Health and Safety Management System certification. These certifications provide additional assurance of quality and compliance with industry-specific standards.
Import Regulations and Customs for design injection mold from China:
When importing design injection molds from China, it is important to comply with the import regulations and customs procedures of the destination country. The specific requirements may vary depending on the country, but some common aspects include:
1. Documentation: Importers need to provide necessary documents such as commercial invoices, packing lists, bills of lading or airway bills, and certificates of origin.
2. Customs Duties and Tariffs: Importers must determine the appropriate customs duties and tariffs applicable to the imported design injection molds and comply with the customs regulations of the destination country.
3. Product Compliance: Imported design injection molds should meet the safety and quality standards of the destination country. Some countries may require additional certifications or testing to ensure product compliance.
4. Intellectual Property Rights (IPR) Protection: Importers should ensure that the design injection molds they import do not infringe on any intellectual property rights, such as patents or trademarks, of the destination country.
It is essential for importers to work with a reputable freight forwarder or customs broker who is familiar with the import regulations and customs procedures of the destination country to avoid any potential issues or delays during the import process from China.
Sustainability and Environmental Considerations in design injection mold Manufacturing
Sustainability and environmental considerations are increasingly important in the manufacturing industry, including the design and production of injection molds. The injection molding process involves the use of a mold to produce plastic parts, and it is essential to minimize the negative impact on the environment throughout this process.
One key area of concern is the material used for the injection molds. Traditional molds are typically made from metals such as steel or aluminum, which are energy-intensive to produce and often involve mining operations that can have significant environmental consequences. To address this, manufacturers are exploring alternative materials like composites or biodegradable polymers that are more sustainable and have a lower carbon footprint.
In addition to the material choice, optimizing the design of the injection mold can also contribute to sustainability. Designing molds with minimized material waste is crucial to reduce environmental impact. This can be achieved by adopting efficient manufacturing techniques, such as using computer-aided design (CAD) software to optimize the mold design and improve material utilization. Furthermore, incorporating modular designs allows for easier maintenance and repair, reducing the need for replacement and ultimately reducing waste.
Energy consumption is another aspect to consider in sustainable injection mold manufacturing. By using energy-efficient machinery and technologies, manufacturers can reduce the energy requirements during production. Embracing technologies like electric injection molding machines can significantly decrease energy consumption compared to traditional hydraulic machines.
Lastly, the recycling and disposal of injection molds should be carefully managed to minimize environmental impact. Implementing recycling programs for mold components and excess material can help recover valuable resources and reduce waste. Additionally, responsible disposal methods should be implemented to prevent pollutants from entering the environment.
Overall, sustainability and environmental considerations in the design and manufacturing of injection molds are essential for minimizing the impact on the environment. By adopting alternative materials, optimizing mold designs, reducing energy consumption, and implementing recycling and proper disposal methods, manufacturers can contribute to a more sustainable and environmentally friendly manufacturing industry.
List The Evolution history of “design injection mold”
The evolution history of design injection molds dates back to the 19th century when the first injection molding machine was patented by John Wesley Hyatt in 1872. This machine utilized a plunger system to inject heated celluloid into a mold cavity, creating various products.
In the early 20th century, advancements in plastics and machinery led to the development of more sophisticated injection molding techniques. In the 1930s, the first screw injection molding machines were introduced, offering better control over the injection process and allowing for more complex molds.
During World War II, injection molding gained significant importance as it was used to produce large volumes of military products such as buttons, combs, and helmet liners. This period marked a major shift towards mass production and the widespread adoption of injection molding technology.
In the 1950s, the introduction of thermoplastics transformed the industry. These versatile polymers reduced production costs and expanded the range of available materials. Additionally, hot runner systems were developed, enabling faster cycle times and more efficient production.
The 1970s witnessed the emergence of computer-aided design (CAD) and computer-aided manufacturing (CAM) systems. This integration of technology allowed for precise and accurate mold designs, reducing errors and improving overall efficiency in the manufacturing process.
With the advent of 3D printing in the 1980s, rapid prototyping became more accessible. Manufacturers could now create physical models of injection molds quickly and cost-effectively, facilitating design iterations and reducing lead times.
In recent years, technological advancements have continued to shape the evolution of design injection molds. High-speed machining and advanced CNC (Computer Numerical Control) systems have improved the precision and quality of mold components. Furthermore, the integration of sensors and automation has enabled real-time monitoring, troubleshooting, and optimization of the injection molding process.
Today, with the increasing demand for customized and sustainable products, designers are focusing on designing injection molds that reduce material wastage, energy consumption, and carbon footprint. Innovative approaches such as overmolding and micro-injection molding are also gaining popularity, enabling the creation of complex and intricate parts.
In summary, the history of design injection molds has seen significant advancements in materials, machinery, software, and manufacturing techniques. From the basic plunger system to integrated CAD/CAM systems and 3D printing, the evolution has revolutionized the industry, leading to greater efficiency, precision, and flexibility in producing a wide range of plastic products.
The Evolution and Market Trends in design injection mold Industry
The design injection mold industry has witnessed significant evolution over the years, driven by advancements in technology, changing consumer demands, and market trends. This industry plays a crucial role in the manufacturing process of various products, including automobiles, appliances, electronics, and packaging.
One notable evolution is the integration of computer-aided design (CAD) and computer-aided manufacturing (CAM) software. This has revolutionized the design process, allowing for more precise and complex mold designs. CAD software enables designers to create 3D models, test different variations, and simulate the molding process before physical production. CAM software, on the other hand, facilitates the translation of these 3D designs into instructions for CNC machines, enhancing accuracy and efficiency.
Another key trend in the design injection mold industry is the increasing use of additive manufacturing or 3D printing. This technology has proven to be highly advantageous, particularly in creating prototypes and low-volume production runs. It offers the flexibility to quickly iterate designs, reducing the lead time and cost associated with traditional mold production methods. Additionally, 3D printing enables the production of complex geometries with ease, expanding the design possibilities.
Market trends in the design injection mold industry are influenced by various factors. Growing consumer demand for lightweight and eco-friendly products has fueled the use of materials like carbon fiber-reinforced polymers and biodegradable plastics. This shift in material preference has led to the development of molds capable of accommodating these materials, including multi-shot and overmolding techniques.
Additionally, the increasing emphasis on customization and personalization has prompted the industry to adapt accordingly. Manufacturers are investing in molds that can produce products with unique features, colors, and textures to cater to individual consumer preferences. Rapid tooling technologies, such as aluminum molds and soft molds, have gained popularity due to their ability to provide faster turnaround times and cost-effectiveness for small batch production.
Overall, the design injection mold industry continues to evolve in response to technological advancements and changing market demands. The integration of CAD/CAM software, the rise of additive manufacturing, the use of advanced materials, and the trend towards customization are significant factors shaping the industry’s current landscape. As technology continues to advance, it is likely that the industry will continue to innovate and adapt to meet the evolving needs of manufacturers and consumers alike.
Custom Private Labeling and Branding Opportunities with Chinese design injection mold Manufacturers
Chinese design injection mold manufacturers offer custom private labeling and branding opportunities for businesses looking to create their own unique products. By collaborating with these manufacturers, companies can have their logo, brand name, or any other custom design printed or embossed on their products. This provides a cost-effective way to build brand recognition and establish a strong market presence.
One key advantage of working with Chinese design injection mold manufacturers is their ability to produce high-quality products at competitive prices. With advanced technology and expertise in injection molding, these manufacturers are capable of creating intricate designs and achieving precision in their products. This ensures that the custom labeling and branding will be of excellent quality.
Another benefit is the wide range of materials and finishes available. Chinese design injection mold manufacturers offer various options such as plastic, metal, or a combination of both. They can also provide different surface treatments, including glossy, matte, or textured finishes. This flexibility allows businesses to choose the material and finish that best represents their brand identity.
Moreover, Chinese manufacturers typically have a fast production turnaround time, helping businesses meet tight deadlines and quickly bring their custom-branded products to market. Their efficient production processes and large-scale manufacturing capabilities enable them to accommodate both small and large order quantities.
In summary, collaborating with Chinese design injection mold manufacturers allows businesses to leverage their expertise and capabilities to create custom-branded products. This not only helps enhance brand recognition but also provides a cost-effective and efficient solution for businesses looking to establish a strong market presence. With a wide range of materials, finishes, and fast production turnaround times, businesses can confidently explore custom private labeling and branding opportunities in partnership with Chinese design injection mold manufacturers.
Tips for Procurement and Considerations when Purchasing design injection mold
When purchasing a design injection mold, there are several factors to consider to ensure a successful procurement process. Here are some tips and considerations to keep in mind:
1. Define your project requirements: Clearly articulate your specific needs, including the product specifications, quantity, budget, and timelines. This will help you communicate effectively with potential suppliers and ensure that they understand your expectations.
2. Conduct market research: Look for reputable suppliers with a proven track record in mold manufacturing. Consider factors such as their experience, expertise, customer reviews, and certifications. Obtain multiple quotes to compare prices and services offered.
3. Quality control: Ensure that the supplier follows quality control processes to minimize the risk of defects or inefficiencies in the injection mold. Ask about their quality control measures, inspection protocols, and the use of advanced technologies for precision and consistency.
4. Material selection: Discuss the material requirements for the mold with the supplier. Consider factors such as durability, resistance to temperature variations, and compatibility with the injection molding process.
5. Design and engineering support: Choose a supplier that provides design and engineering assistance. This will help optimize the mold design, minimize manufacturing challenges, and improve the overall production process.
6. Communication and project management: Effective communication is essential throughout the procurement process. Ensure that the supplier is responsive and has clear lines of communication. Establish project management protocols and determine how progress updates will be shared.
7. Cost considerations: While cost is an important factor, it should not be the sole determining factor. Consider the value for money, the supplier’s reputation, their experience, and any additional services they provide. Balance cost savings with the desired quality and expected outcomes.
8. After-sales support: Inquire about post-purchase support, maintenance, repair, and warranty options. A reliable supplier should be willing to assist you even after the sale is complete.
By considering these tips and considerations, you can increase the chances of a successful procurement process when purchasing a design injection mold. Remember to conduct thorough research, communicate effectively, and choose a supplier that meets your specific needs.
FAQs on Sourcing and Manufacturing design injection mold in China
Q: What are the key factors to consider when sourcing and manufacturing injection molds in China?
A: When sourcing and manufacturing injection molds in China, it is essential to consider several factors. Firstly, selecting a reliable and experienced manufacturer is crucial. Thoroughly researching potential suppliers, evaluating their track record, and requesting samples or references can help determine their credibility.
Secondly, communication is essential. Overcoming language barriers and ensuring effective communication with the manufacturer is vital to avoid misunderstandings and achieve the desired results. Explore reliable communication channels like email, phone, or video conferences to maintain regular contact throughout the manufacturing process.
Another factor to consider is quality control. Implementing a rigorous quality control system that includes regular inspections, testing, and quality standards is vital to ensure the molds meet the required specifications. Conducting onsite inspections or appointing a third-party inspection company can help verify the quality of the molds before shipment.
Additionally, logistics and shipping must be carefully considered. Determine the transportation method and plan the shipment process ahead to avoid any delays or complications. Understanding the packaging requirements, customs regulations, and potential import taxes is necessary to ensure smooth delivery.
Lastly, it is crucial to establish clear milestones and deadlines for the manufacturing process. Regularly monitoring the progress of the mold production and addressing any issues promptly is essential to avoid extended lead times and production delays.
Q: How can one ensure the quality of injection molds manufactured in China?
A: To ensure the quality of injection molds manufactured in China, several steps can be taken. Firstly, conducting thorough research and due diligence on potential manufacturers is vital. This includes checking their certifications, past projects, and client testimonials to ensure their capability to produce high-quality molds.
Secondly, implementing a comprehensive quality control system is necessary. This can involve on-site inspections during different stages of production, verifying materials and measurements, and conducting functional testing to ensure the molds meet the specified requirements.
Collaborating closely with the manufacturer and providing detailed specifications, CAD drawings, and samples can help in clarifying expectations and minimizing errors. Regular communication and progress updates can enable addressing any quality concerns early on.
Moreover, appointing a third-party inspection agency can provide an unbiased assessment of the molds’ quality. These agencies can conduct inspections throughout the production process and verify that the finished molds meet the required standards.
Lastly, establishing clear documentation and contracts that outline quality expectations, warranties, and remedies for non-compliance is essential. This can help protect the buyer’s interests and provide recourse if any quality issues arise.
Overall, a combination of rigorous research, effective communication, quality control measures, and appropriate contractual arrangements can help ensure the quality of injection molds manufactured in China.
Why contact sourcifychina.com get free quota from reliable design injection mold suppliers?
Sourcifychina.com is able to offer free quota from reliable design injection mold suppliers because of several reasons. Firstly, Sourcifychina.com has built strong and long-standing relationships with these suppliers. Over the years, they have established a level of trust and credibility with each other, making it possible for the suppliers to provide their services at no cost.
Secondly, Sourcifychina.com serves as a platform that connects buyers and suppliers. By offering free quota, they attract more potential buyers to their platform, increasing the customer base and generating more business for the suppliers. This mutually beneficial arrangement helps to strengthen the partnership between Sourcifychina.com and the suppliers.
Additionally, the suppliers may see providing a free quota as a marketing strategy. By showcasing their services and expertise through Sourcifychina.com, they can attract more customers and compete with other suppliers in the market. This can be seen as an investment in their business growth, as they may receive future orders from the buyers who initially obtained a free quota.
Furthermore, providing a free quota allows the suppliers to demonstrate their commitment to customer satisfaction. It gives them an opportunity to showcase their capabilities and offer a sample of their work, which can potentially lead to long-term collaborations with the buyers.
Lastly, Sourcifychina.com may have negotiated discounted rates or volume-based agreements with the suppliers, enabling them to offer free quota as part of their value-added services to buyers.
In conclusion, Sourcifychina.com obtains free quota from reliable design injection mold suppliers through the trust and credibility built over time, the value they bring as a platform connecting buyers and suppliers, marketing strategies, and potential long-term collaborations. This arrangement benefits both Sourcifychina.com and the suppliers, and allows buyers to access quality services without any upfront costs.