Introduce about extrusion blow molding machines guide,Qulity,Cost,Supplier,Certification,Market,Tips,FAQ
Extrusion blow molding machines are widely used in the manufacturing industry to produce hollow plastic products. This technology utilizes melted plastic resin that is extruded and shaped into a parison, which is then blown into a mold to create the desired product shape. This guide provides an overview of extrusion blow molding machines, including quality, cost, suppliers, certifications, market trends, tips, FAQs, and more.
Quality is a crucial factor when considering extrusion blow molding machines. High-quality machines ensure consistent product dimensions, strength, and durability. Look for machines manufactured with precision engineering and robust materials to minimize downtime and improve productivity.
Cost is another important aspect to consider. The price of extrusion blow molding machines can vary based on factors such as machine size, capabilities, and technology features. It is essential to assess the return on investment and long-term maintenance costs before making a purchase decision.
When selecting a supplier, it is vital to work with reputable manufacturers who have a proven track record in the industry. Consider suppliers that offer comprehensive after-sales support, including training, spare parts availability, and technical assistance.
Certifications ensure that the extrusion blow molding machines meet industry standards and comply with safety regulations. Look for machines that hold certifications such as ISO 9001, CE, or UL, as they reflect the manufacturer’s commitment to quality and compliance.
The market for extrusion blow molding machines is rapidly expanding due to the increasing demand for lightweight and cost-efficient plastic products. Industries such as automotive, packaging, consumer goods, and healthcare heavily rely on this technology for their production needs.
Here are some tips to maximize the performance of extrusion blow molding machines: regularly maintain and clean the machines, invest in quality molds, optimize process parameters, and train operators to operate the machines efficiently.
Frequently Asked Questions (FAQ) related to extrusion blow molding machines include queries about machine operation, material compatibility, customization options, energy consumption, and noise levels. It is advisable to consult with manufacturers or industry experts to get detailed answers to specific queries.
In conclusion, extrusion blow molding machines offer an efficient and cost-effective solution for the production of hollow plastic products. By considering factors like quality, cost, suppliers, certifications, market trends, and following the provided tips, companies can make informed decisions while procuring these machines for their manufacturing operations.
Types of extrusion blow molding machines
Extrusion blow molding machines are widely used in the manufacturing industry to produce various plastic products, such as bottles, containers, and packaging materials. These machines utilize the extrusion process to create hollow plastic shapes by blowing air into a molten plastic parison (a tube-like structure). There are several types of extrusion blow molding machines available, each catering to different production needs and requirements.
1. Continuous Extrusion Blow Molding Machines: Continuous extrusion blow molding machines are widely used for high-volume production. They consist of a continuous extruder, which continuously creates a molten plastic parison. The parison is then clamped in a mold, and air is blown into it to expand and shape it. These machines have high productivity and can produce a large number of parts in a short time.
2. Accumulator Head Extrusion Blow Molding Machines: Accumulator head extrusion blow molding machines are suitable for large and complex parts. They feature an accumulator, where molten plastic is accumulated and stored before it is pushed into the mold. This allows for the production of larger parts with different wall thicknesses. These machines offer versatility and are commonly used in the automotive and industrial sectors.
3. Injection Blow Molding Machines: Injection blow molding machines combine the principles of injection molding and blow molding. They utilize an injection molding unit to create a preform, which is then transferred to a blow mold to be inflated and shaped. These machines are ideal for producing small and intricate plastic bottles and containers.
4. Reheat Blow Molding Machines: Reheat blow molding machines are used for the production of PET (polyethylene terephthalate) bottles. They employ a two-step process, where preforms are first produced using injection molding and then reheated to soften the material. The softened preforms are subsequently blown into the desired shape using compressed air. These machines are widely used in the beverage industry.
5. Multi-layer Blow Molding Machines: Multi-layer blow molding machines are designed to produce plastic containers with multiple layers. These machines have several extruders, each feeding a different plastic material. By incorporating various plastic layers, these machines can enhance the barrier properties of the products, making them suitable for food and beverage packaging.
In conclusion, extrusion blow molding machines come in various types suited to different production requirements. Continuous extrusion, accumulator head, injection blow, reheat blow, and multi-layer blow molding machines offer a range of capabilities and applications in the plastic manufacturing industry.
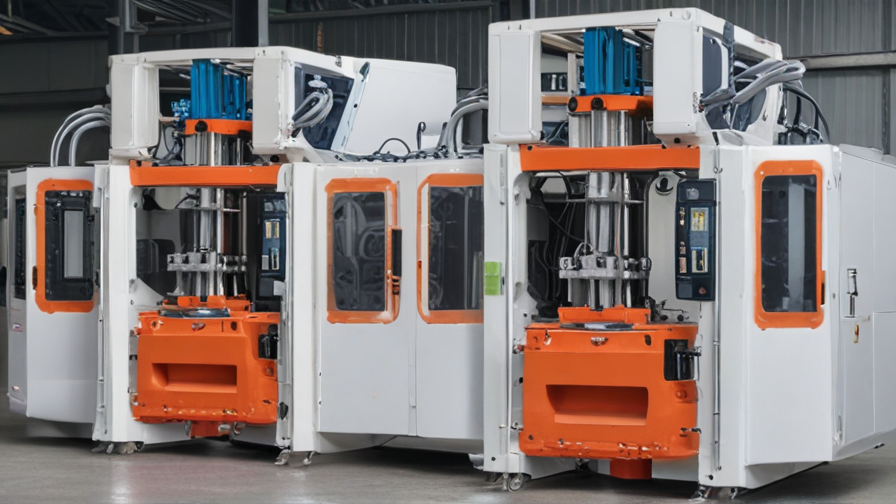
Pros and Cons of Using extrusion blow molding machines
Extrusion blow molding machines are widely used in the manufacturing industry for producing hollow plastic products such as bottles, containers, and tanks. Like any manufacturing process, there are pros and cons associated with using these machines. Here is an overview of some of the advantages and disadvantages:
Pros:
1. Cost-effective: Extrusion blow molding machines are considered to be a cost-effective manufacturing option, especially in high volume production. This is because they can produce a large number of products in a relatively short period, minimizing labor costs and maximizing productivity.
2. Versatility: These machines offer versatility in terms of the range of products that can be produced. They can be adjusted to create products of various sizes, shapes, and designs, allowing manufacturers to cater to different market demands.
3. Rapid production: Extrusion blow molding machines are capable of producing products at a high production rate. They can manufacture products continuously, leading to shorter cycle times and faster turnaround times. This is particularly beneficial for manufacturers requiring large quantities of products in a timely manner.
4. Quality control: These machines offer excellent consistency and precision in the production process. Manufacturers can achieve uniform thickness and wall strength of the produced products, ensuring consistent quality across the entire batch.
Cons:
1. Limited material selection: Extrusion blow molding machines are primarily designed for processing thermoplastics such as polyethylene and polypropylene. This limits the choice of materials available for manufacturing. Certain materials may not be suitable for this process, restricting the potential range of products that can be produced.
2. Initial setup and maintenance: Setting up an extrusion blow molding machine requires specialized knowledge and skills. It may involve complex adjustments and calibrations to ensure an optimal production process. Additionally, regular maintenance is necessary to keep the machine in good working condition, which can be time-consuming and costly.
3. Mold changeover: Changing the mold of an extrusion blow molding machine often requires halting production and manually adjusting various components. This can result in downtime and decreased productivity, especially when producing different products with distinct specifications.
4. Energy consumption: The extrusion blow molding process relies on heating, melting, and cooling of the plastic material, which consumes substantial amounts of energy. This can lead to higher energy costs for manufacturers, impacting the overall production expenses.
In conclusion, extrusion blow molding machines offer several advantages such as cost-effectiveness, versatility, and rapid production. However, there are also limitations in terms of material selection, setup and maintenance requirements, mold changeover, and energy consumption. Manufacturers need to carefully consider these pros and cons before deciding to incorporate these machines into their production processes.
extrusion blow molding machines Reference Specifications (varies for different product)
Extrusion blow molding machines are widely used in the manufacturing industry to produce various plastic products, such as bottles, containers, and tanks. These machines utilize a specific process that involves heating a thermoplastic material and then extruding it as a hollow tube or parison. The parison is then placed in a mold where it is inflated with compressed air until it takes the shape of the mold cavity.
The reference specifications of extrusion blow molding machines may vary depending on the specific product being manufactured. However, some common specifications include the machine’s capacity, clamping force, and extrusion capacity. The capacity of the machine refers to its ability to produce a certain number of units per hour or day. This can range from a few hundred to thousands of units, depending on the machine’s size and design.
Clamping force is another important specification that determines the machine’s ability to securely hold the mold during the blow molding process. It ensures that the mold remains in place and that the final product is accurately formed. The clamping force can range from a few tons to several dozen tons, depending on the size and complexity of the mold.
Extrusion capacity refers to the machine’s ability to extrude the plastic material into a parison. It is typically measured in kilograms per hour or pounds per hour and determines the speed at which the machine can produce the parisons.
Other specifications that may vary include the maximum mold size, the number of cavities in the mold, and the control system used to operate the machine. These specifications are tailored to meet the specific requirements of each product and ensure efficient and precise manufacturing.
In conclusion, extrusion blow molding machines have reference specifications that are determined based on the specific product being manufactured. These specifications include capacity, clamping force, and extrusion capacity, and may vary to accommodate different sizes and complexities of molds. By understanding these specifications, manufacturers can choose the appropriate machine to meet their production needs.
Applications of extrusion blow molding machines
Extrusion blow molding machines are versatile and widely used in the manufacturing industry for various applications. Here are some common applications of these machines:
1. Packaging Industry: Extrusion blow molding machines are extensively used in the packaging industry to produce containers, bottles, and jars made of plastic materials such as high-density polyethylene (HDPE), polyethylene terephthalate (PET), and polypropylene (PP).
2. Consumer Goods: These machines are utilized to manufacture a wide range of consumer goods such as shampoo bottles, detergent containers, food storage containers, and cosmetic packaging. The ability to produce lightweight and durable products makes extrusion blow molding machines ideal for consumer applications.
3. Automotive Industry: Extrusion blow molding machines play a crucial role in the automotive industry. They are used to produce various parts like fuel tanks, air ducts, automotive fluid containers, and even car bumpers. The high strength and impact resistance of blow-molded plastic parts make them suitable for automotive applications.
4. Medical Sector: These machines are employed to produce medical equipment and devices such as squeeze bottles for liquid medication, anesthesia masks, drip chambers, and other healthcare-related products. Blow-molded medical products are preferred due to their ability to maintain a sterile environment and ease of disposal.
5. Industrial Containers: Extrusion blow molding machines are widely used to manufacture large industrial containers for storing and transporting fluids and chemicals. These containers can range in size from a few liters to several hundred liters and are commonly used in industries like agriculture, chemicals, and industrial cleaning.
6. Toys and Recreation: Extrusion blow molding machines are also used to produce various toys and recreational items such as balls, water guns, frisbees, and outdoor play equipment. The flexibility in design and the ability to create hollow shapes make blow molding an ideal choice for these applications.
Overall, extrusion blow molding machines have a significant impact on various industries by providing a cost-effective, efficient, and customizable solution for manufacturing plastic products. The use of blow molding technology continues to expand as new advancements enable the production of more complex and innovative products.
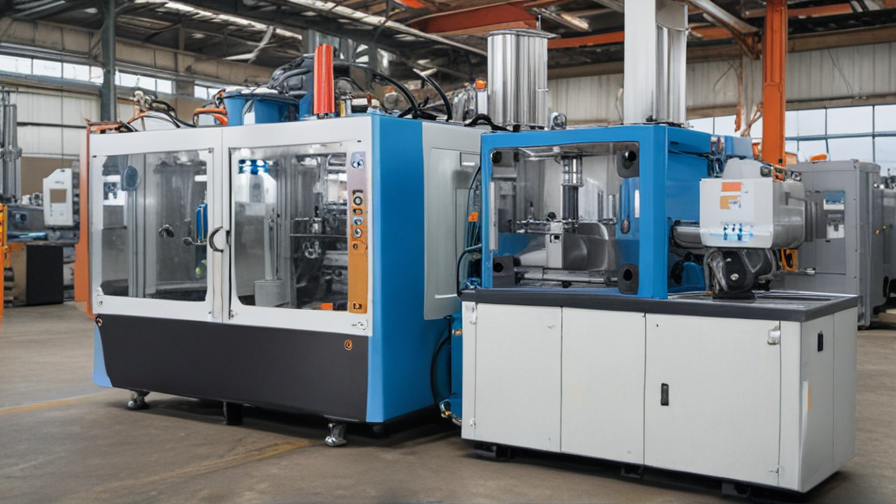
The Work Process and how to use extrusion blow molding machines
Extrusion blow molding is a popular manufacturing process used to produce hollow plastic products such as bottles, containers, and tanks. This process involves melting plastic resin and then extruding it into a hollow tube, which is then stretched and formed into the desired shape using compressed air. The following is an overview of the work process and how to use extrusion blow molding machines.
Firstly, the plastic resin pellets are loaded into a hopper, which feeds them into an extruder. The extruder consists of a rotating screw within a heated barrel. The resin pellets are gradually melted and mixed as they are pushed forward by the rotating screw.
Once the molten plastic reaches the end of the extruder, it is forced through a die head. The die head shapes the molten plastic into a parison, which is a hollow tube. The die head can be customized to create different parison shapes and sizes.
The parison is then transferred to the mold cavity. The mold consists of two halves, which close around the parison to form a sealed cavity. The mold halves are typically made of metal and are cooled to help solidify the plastic.
After the mold is closed, compressed air is blown into the parison through a blow pin. The air pressure stretches and expands the plastic, shaping it against the mold walls. The mold remains closed until the plastic has hardened and is ready to be ejected.
Once the plastic has cooled and solidified, the mold halves open, and the finished product is ejected from the machine. The excess plastic, known as flash, may be trimmed off to achieve the desired aesthetic and functional properties of the product. The extrusion blow molding machine then repeats the process to produce additional parts.
To use an extrusion blow molding machine, operators must have a thorough understanding of the machine controls, heating and cooling systems, and mold design. They must carefully monitor and adjust parameters such as temperature, pressure, and blow rate to ensure consistent production and high-quality products.
In conclusion, extrusion blow molding is a versatile and efficient manufacturing process for producing hollow plastic products. By following the work process and properly operating the machine, manufacturers can create a wide range of products with consistent quality.
Quality Testing Methods for extrusion blow molding machines and how to control the quality
Extrusion blow molding machines are commonly used in the production of plastic bottles, containers, and other hollow objects. To ensure the quality of the products, several testing methods can be implemented at different stages of the manufacturing process.
1. Visual Inspection: This is a basic method that involves visually inspecting the products for any defects, such as surface imperfections, deformations, or color variations. Trained personnel can identify and remove any defective items.
2. Dimensional Measurement: Precise measurements of key parameters like wall thickness, length, diameter, or weight can be conducted using specialized instruments. These measurements are compared to the desired specifications, and any out-of-tolerance dimensions are flagged for further investigation.
3. Leak Testing: Leak detection is crucial to ensure the integrity of the products. Various techniques such as pressure decay testing, vacuum testing, or immersion testing can be employed to check for leakage. These tests assess the tightness of the container by measuring pressure changes or the presence of bubbles.
4. Drop Testing: This method assesses the impact resistance of the products. Containers are dropped from specified heights onto different surfaces, simulating real-life scenarios. The products are evaluated visually and structurally for any damages, cracks, or breakages.
5. Material Testing: Testing the properties of the raw materials used in the extrusion blow molding process is essential. Mechanical tests, such as tensile or flexural tests, can assess the strength and flexibility of the material. Other tests, like melt flow index or density measurement, ensure the material meets the required specifications.
To control the quality of the extrusion blow molding process, several measures can be taken:
1. Regular Maintenance: Routine maintenance of the machines, including cleaning, lubrication, and calibration, helps in ensuring optimal performance and accurate outputs.
2. Process Monitoring: Constant monitoring of key process variables, such as temperature, pressure, and cycle times, helps in identifying any deviations from the set parameters, allowing for immediate corrective actions.
3. Personnel Training: Proper training of operators and quality control personnel is essential to maintain consistent quality standards. Educating them about potential defects, appropriate inspection techniques, and relevant testing methods enhances their ability to identify and control quality issues effectively.
4. Statistical Process Control (SPC): Implementing SPC techniques can help in analyzing process data, identifying trends, and detecting any potential quality problems proactively. This allows for timely adjustments and interventions to prevent defective production.
By implementing these testing methods and quality control measures, manufacturers can ensure the quality and reliability of extrusion blow molded products, meeting customer expectations and regulatory standards.
extrusion blow molding machines Sample Policy and Post-Purchase Considerations for extrusion blow molding machines from China
Sample Policy:
Before purchasing extrusion blow molding machines from China, it is important to understand the sample policy of the manufacturer. Most manufacturers offer the option to provide samples of their machines. This allows potential buyers to assess the quality, efficiency, and overall performance of the machine before making a purchase. Some manufacturers may charge a fee for providing samples, while others may offer free samples or deduct the sample cost from the final purchase price. It is advisable to clarify the sample policy with the manufacturer to avoid any misunderstandings.
Post-Purchase Considerations:
After purchasing extrusion blow molding machines from China, there are several post-purchase considerations that should be taken into account:
1. Logistics and shipping: Assessing the logistics and shipping options is crucial to ensure that the machines are delivered safely and in a timely manner. Communication with the manufacturer regarding the shipping process, costs, and any necessary import/export documentation should be established.
2. Installation and training: Understanding how the machines will be installed and operated is essential. Some manufacturers may provide installation services and training, while others may rely on the buyer’s expertise or provide detailed manuals. Clarifying the installation process and training requirements is important to ensure a smooth setup.
3. Warranty and after-sales service: Inquire about the warranty coverage and after-sales service provided by the manufacturer. A reliable warranty ensures that any potential defects or malfunctions are addressed promptly without incurring additional costs. Knowing the availability and responsiveness of the manufacturer’s customer service support is essential.
4. Spare parts availability: Check with the manufacturer regarding the availability of spare parts for the machines. Availability of spare parts is crucial in case of any repairs or replacements needed in the future. It is recommended to discuss the accessibility and procurement process of spare parts with the manufacturer.
5. Maintenance and servicing: Understand the maintenance requirements and recommended servicing intervals for the machines. Regular maintenance and servicing ensure the longevity and efficient performance of the blow molding machines. Obtaining detailed maintenance guidelines from the manufacturer is advisable.
In conclusion, understanding the sample policy and considering the post-purchase factors for extrusion blow molding machines from China helps to ensure a successful procurement process and satisfactory performance of the machines.
Sourcing extrusion blow molding machines from China: Opportunities, Risks, and Key Players
Sourcing extrusion blow molding machines from China can offer various opportunities for businesses in terms of cost-effectiveness and market expansion. Chinese manufacturers are known for their competitive pricing, which can help companies save on production costs. Additionally, China boasts a large and skilled labor force that is experienced in manufacturing extrusion blow molding machines, ensuring quality products.
One of the main risks associated with sourcing from China is the lack of intellectual property protection. Chinese manufacturers have been notorious for copying and reproducing patented designs without proper licensing, which can potentially lead to legal disputes. However, companies can mitigate this risk by conducting thorough due diligence, including background checks and extensive research on potential Chinese suppliers.
China hosts several key players in the extrusion blow molding machine industry. One prominent player is Yankang Plastic Machinery, which specializes in the production of blow molding machines for various applications, such as packaging, automotive, and household products. Another noteworthy player is Fong Kee International Machinery, which has a significant market presence and offers a diverse range of blow molding machines to meet different customer requirements.
It is recommended for businesses to establish clear communication channels and ensure effective quality control measures when sourcing extrusion blow molding machines from China. Regular visits to factories or engaging third-party inspection agencies can help in maintaining product standards and ensuring timely deliveries.
In conclusion, sourcing extrusion blow molding machines from China presents opportunities for cost savings and market expansion. However, companies should be aware of the risks associated with intellectual property protection. Conducting thorough due diligence and selecting reliable and reputable Chinese manufacturers are crucial steps to mitigate potential risks and ensure successful sourcing.
How to find and select reliable extrusion blow molding machines manufacturers in China,use google search manufacturers and suppliers
When looking for reliable extrusion blow molding machine manufacturers in China, utilizing Google search can be an effective method. Here’s a guide to help you find and select the right manufacturers within a limited word count:
1. Start by searching relevant keywords on Google, such as “extrusion blow molding machine manufacturers in China” or “reliable blow molding machine suppliers.” This will provide you with a list of potential manufacturers.
2. Assess the manufacturers’ websites: Visit the websites of the shortlisted manufacturers to gather more information about their products, technology, experience, and certifications. Look for established companies with a good reputation in the industry.
3. Check for certifications: Reliable manufacturers often have certifications such as ISO 9001, CE, or other industry-specific certifications. These certifications ensure that the manufacturer follows standardized processes and maintains product quality.
4. Evaluate product range and customization options: Examine the different types and models of extrusion blow molding machines offered by each manufacturer. Choose a manufacturer that offers a wide range of products to suit your specific requirements. Additionally, check if they provide customization options to tailor the machines to your unique needs.
5. Read customer reviews and testimonials: Look for reviews or testimonials from existing customers on the manufacturer’s website or other platforms. This will give you insights into their reputation, reliability, and customer satisfaction.
6. Direct communication: Reach out to the shortlisted manufacturers and request more detailed information about their products, including technical specifications, pricing, delivery time, and after-sales services. Prompt and helpful responses indicate their professionalism and commitment.
7. Ask for references: Request the manufacturers to provide references of their existing customers. Contact these customers to get direct feedback on their experiences with the manufacturer’s products and services.
8. Consider supplier capacity and support: Evaluate the manufacturer’s production capacity, infrastructure, and ability to handle large orders. Also, check if they provide comprehensive technical support, warranty, and after-sales services.
By following these steps, utilizing Google search, and effectively assessing the manufacturers’ online presence, you can narrow down your choices and identify reliable extrusion blow molding machine manufacturers in China.
How to check extrusion blow molding machines manufacturers website reliable,use google chrome SEOquake check if ranking in top 10M
To check the reliability of extrusion blow molding machine manufacturers’ websites, you can follow the steps below:
1. Use Google Chrome: Begin by using the Google Chrome browser as it has various tools and extensions that can help in analyzing websites.
2. Install SEOquake: Install the SEOquake extension on your Google Chrome browser. SEOquake is a powerful tool that provides a wealth of information about websites, including their rankings, traffic, and other useful metrics.
3. Check the Ranking: Once the SEOquake extension is installed, perform a Google search for the specific manufacturer you want to evaluate. Look for their website in the search results and check if it ranks within the top 10 million websites globally. A higher ranking indicates more credibility and popularity.
4. Analyze Traffic: With SEOquake, you can view the estimated monthly traffic of a website. Check if the manufacturer’s website has a significant amount of traffic, implying that it is visited by many users and therefore more reliable.
5. Assess Website Quality: Pay attention to the design, layout, and overall user experience of the manufacturer’s website. A professional and well-maintained website suggests that the manufacturer is serious about their business and likely to be trustworthy.
6. Explore Additional Information: Beyond SEOquake, explore the website to find information such as company background, years of experience, product details, certifications, testimonials, and customer reviews. All these factors can help you determine the reliability and reputation of the manufacturer.
Remember, using SEOquake and checking ranking within the top 10 million are just initial indicators of reliability. It is essential to conduct thorough research and consider multiple aspects before making a final judgment.
Top 10 extrusion blow molding machines manufacturers in China with each 160 words introduce products,then use markdown create table compare
1. Kautex Maschinenbau GmbH: Kautex is a renowned manufacturer of extrusion blow molding machines in China, famous for its advanced technology and innovative solutions. Their product range includes machines for different capacities, from small containers to large industrial packaging. They offer high-quality machines that are efficient, reliable, and provide consistent production output.
2. Sidel: Sidel is another major player in the Chinese extrusion blow molding machine industry. Their machines are designed for various applications, such as bottles, containers, and jars. Sidel focuses on delivering sustainable solutions, integrating energy-saving features and reducing material waste. Their machines are equipped with cutting-edge technology and ensure high productivity.
3. Techne: Techne offers a wide range of blow molding machines suitable for different industries like food and beverage, pharmaceutical, and cosmetics. Their machines are known for their versatility, allowing the production of various bottle shapes and sizes. Techne’s machines are designed for easy operation and maintenance, ensuring a seamless production process.
4. Full Shine Plastic Machinery Co., Ltd: Full Shine specializes in the production of extrusion blow molding machines for the packaging industry. Their machines are known for their reliability, accuracy, and high production capacity. Full Shine also offers customization options, allowing customers to tailor the machines as per their specific requirements.
5. Powerjet Plastic Machinery Co., Ltd: Powerjet Plastic Machinery is a leading manufacturer of extrusion blow molding machines in China. They offer a comprehensive range of machines suitable for different applications, such as bottles, cans, and containers. Their machines are designed to provide high production efficiency, energy-saving features, and precise control systems.
6. Meccanoplastica: Meccanoplastica has a long-standing presence in the Chinese blow molding machine market. Their machines are designed to provide excellent production performance, durability, and reliability. Meccanoplastica offers a wide range of models for different packaging needs, and their machines are known for their user-friendly interface and efficient automation.
7. Jomar Corporation: Jomar Corporation specializes in manufacturing extrusion blow molding machines for the plastic packaging industry. Their machines are designed to produce high-quality containers and bottles with precision. Jomar’s machines feature advanced control systems, ensuring maximum productivity and ease of operation.
8. Kebeln Plastic Machinery Co., Ltd: Kebeln Plastic Machinery is a well-established manufacturer of extrusion blow molding machines in China. They offer a diverse range of machines suitable for various packaging applications. Kebeln’s machines are known for their durability, stability, and excellent performance, making them an ideal choice for high-volume production.
9. Akei Blow Molding Machine & Mold Engineering Ltd: Akei is a renowned manufacturer of extrusion blow molding machines with a focus on producing innovative solutions for the packaging industry. Their machines are known for their high-speed production capabilities, energy efficiency, and low maintenance requirements. Akei offers a wide range of models to meet different production needs.
10. Magic MP: Magic MP specializes in the production of extrusion blow molding machines for the packaging industry. Their machines are designed for high-speed production, ensuring maximum efficiency and productivity. Magic MP also offers customization options to meet specific customer requirements, ensuring a seamless production process.
Markdown Table:
| Manufacturer | Key Features |
| ——————————————–| ——————————————————–|
| Kautex Maschinenbau GmbH | Advanced technology, reliable, high-quality outputs |
| Sidel | Sustainable solutions, energy-saving, high productivity |
| Techne | Versatile, easy operation and maintenance |
| Full Shine Plastic Machinery Co., Ltd | Reliable, accurate, high capacity, customization |
| Powerjet Plastic Machinery Co., Ltd | Comprehensive range, energy-saving, precise control |
| Meccanoplastica | Excellent performance, durability, user-friendly |
| Jomar Corporation | High-quality, advanced control systems |
| Kebeln Plastic Machinery Co., Ltd | Durable, stable, excellent performance |
| Akei Blow Molding Machine & Mold Engineering | Innovative solutions, high-speed, energy-efficient |
| Magic MP | High-speed production, customizable |
In conclusion, these top 10 extrusion blow molding machine manufacturers in China offer a wide range of machines that cater to the diverse needs of the packaging industry. Whether it is high-quality outputs, energy efficiency, ease of operation, or customization options, these manufacturers are committed to providing advanced technology and innovative solutions to their customers.
Background Research for extrusion blow molding machines manufacturers Companies in China, use qcc.com archive.org importyeti.com
There are several extrusion blow molding machine manufacturers in China that can be researched through various online platforms. Two of the popular platforms are qcc.com and importyeti.com. Archive.org can also be used to access historical information on these manufacturers.
Qcc.com is a Chinese website that provides business information and credit reports of companies in China. It can be used to find details about the extrusion blow molding machine manufacturers, such as company profiles, contact information, and credit ratings. By searching for relevant keywords such as “extrusion blow molding machine manufacturers,” users can retrieve information on several companies in this industry.
Importyeti.com is a B2B platform that allows users to search for import and export data of various products and companies. By searching for “extrusion blow molding machine manufacturers” on this platform, users can find information about import and export transactions, including company names, product descriptions, shipment records, and more.
In addition to these platforms, researchers can also utilize Archive.org, which is a digital library that provides access to archived web pages. By searching for the websites of specific extrusion blow molding machine manufacturers in China, researchers can access previous versions of their websites and obtain historical information about their products, certifications, company news, and other relevant details.
It is important to note that researchers should closely analyze the information obtained from these platforms to ensure its accuracy and reliability. The gathered information can be used to create a comprehensive background research on extrusion blow molding machine manufacturers in China, and can assist in making informed decisions regarding potential collaborations or business partnerships.
Leveraging Trade Shows and Expos for extrusion blow molding machines Sourcing in China
Trade shows and expos provide valuable opportunities for sourcing extrusion blow molding machines in China. These events bring together manufacturers, suppliers, and industry professionals, offering a comprehensive platform to explore the latest technologies, trends, and product offerings.
Participating in trade shows and expos allows businesses to connect with a wide range of suppliers and compare their offerings in person. This face-to-face interaction gives buyers the chance to assess the quality of the machines, discuss specifications, negotiate prices, and establish relationships with potential suppliers.
China, being a global manufacturing hub, hosts numerous trade shows and expos dedicated to the plastics and packaging industry. One of the prominent events is the Chinaplas exhibition, which showcases a vast array of extrusion blow molding machines and related equipment. This event attracts both local and international exhibitors, providing ample opportunities for buyers to source machines directly from Chinese manufacturers.
By attending these trade shows and expos, buyers can gain valuable insights into the latest technological developments, process improvements, and new product launches in the extrusion blow molding industry. They can also attend seminars, workshops, and conferences to enhance their knowledge and stay updated with industry trends.
Additionally, trade shows and expos provide a platform for networking and forging partnerships with industry experts, suppliers, and other relevant stakeholders. This networking aspect enables buyers to tap into a broad network of contacts, exchange information, and explore potential collaborations.
To make the most out of these events, buyers should thoroughly research the trade shows and expos, their exhibitor profiles, and the products on display. Preparing a list of key suppliers to visit and establishing appointments beforehand can save time and ensure productive discussions during the event.
In conclusion, trade shows and expos present excellent opportunities for sourcing extrusion blow molding machines in China. These events offer unparalleled access to suppliers, enable direct assessment of product quality, foster networking, and facilitate knowledge-sharing. By leveraging these platforms, businesses can find the right suppliers, make informed decisions, and establish long-term partnerships in the Chinese market.
The Role of Agents and Sourcing Companies in Facilitating extrusion blow molding machines Purchases from China
Agents and sourcing companies play a significant role in facilitating the purchase of extrusion blow molding machines from China. These intermediaries act as a bridge between buyers and Chinese manufacturers, helping them navigate the complexities of the procurement process.
One crucial role of agents and sourcing companies is to identify reputable Chinese manufacturers that produce high-quality extrusion blow molding machines. They have extensive knowledge of the market and can provide valuable insights and recommendations based on their experience. By thoroughly assessing manufacturers’ capabilities, certifications, and product quality, they can shortlist reliable suppliers for buyers.
Agents and sourcing companies also assist with negotiation and pricing. They have a deep understanding of the local business environment and can effectively communicate with Chinese manufacturers to negotiate favorable terms on behalf of the buyers. This includes securing competitive prices, discussing payment options, and defining the terms of the purchase agreement.
Additionally, they play a vital role in overcoming language and cultural barriers. Communication is critical during the purchasing process, and agents and sourcing companies act as translators, ensuring clear and effective communication between buyers and manufacturers. They help with clarifying technical specifications, addressing concerns, and resolving any misunderstandings that may arise during the transaction.
Furthermore, agents and sourcing companies facilitate the logistics and shipping of the purchased machines. They handle the coordination between buyers, manufacturers, and shipping companies, ensuring smooth transportation and timely delivery of the equipment. This includes managing customs procedures, documentation, and resolving any potential issues that may arise during shipping.
In summary, agents and sourcing companies simplify and streamline the process of purchasing extrusion blow molding machines from China. They provide expertise in supplier selection, negotiation, communication, and logistics, ensuring that buyers can confidently and efficiently source high-quality equipment from Chinese manufacturers.
Price Cost Research for extrusion blow molding machines manufacturers Companies in China, use temu.com and 1688.com
When it comes to extrusion blow molding machines, China is known for its wide range of manufacturers offering competitive prices. Two popular platforms to search for these manufacturers are temu.com and 1688.com. By using these platforms, you can conduct price-cost research to find the most suitable options for your needs.
Temu.com is a comprehensive B2B platform that connects buyers and suppliers. It offers a variety of search filters to narrow down your options, such as machine types, production capacity, and location. You can directly contact manufacturers, obtain quotes, and negotiate prices. It is essential to compare multiple quotes to ensure you are getting competitive prices.
1688.com, on the other hand, is a popular business-to-business wholesale marketplace in China. It is highly recommended for price-cost research as you can find numerous manufacturers and suppliers for extrusion blow molding machines. The website is primarily in Chinese, so using a translation tool or seeking assistance may be helpful if you are not fluent in the language.
When researching prices on both platforms, it is essential to consider factors that may affect the cost. These can include machine specifications, technology used, material compatibility, and after-sales support. Additionally, you should verify the manufacturer’s reputation, production capacity, and quality certifications before making a purchase decision.
By utilizing temu.com and 1688.com, you can easily compare prices, review product specifications and details, and ultimately find the best manufacturers for extrusion blow molding machines in China. Keep in mind that conducting thorough research and communicating with potential suppliers will help you secure competitive prices while ensuring product quality.
Shipping Cost for extrusion blow molding machines import from China
The shipping cost for importing extrusion blow molding machines from China can vary depending on several factors. These factors include the size and weight of the machines, the shipping method chosen, and the destination country.
For smaller machines, air freight is a popular shipping option. The cost of air freight is usually calculated based on either the weight or the volume of the shipment, whichever is greater. It is important to note that air freight charges tend to be higher compared to other shipping methods.
For larger machines, sea freight is often the preferred shipping method. The cost of sea freight is usually based on the volume of the shipment, measured in cubic meters. Additional charges, such as customs duties and port fees, should also be taken into account.
When calculating the shipping cost, it is essential to consider other factors such as packaging, insurance, and transportation to the port of origin. Packaging must be done properly to ensure the safety of the machines during transit. Insurance is also recommended to protect against any potential damages or losses during shipping.
Shipping cost can vary widely depending on the destination country. Factors that may affect the cost include distance, import duties, taxes, and any additional fees or paperwork required by the destination country’s customs authorities.
To get an accurate estimate of the shipping cost, it is advisable to work with a reputable shipping company or freight forwarder. They can provide detailed information on the different shipping options available and help with any necessary documentation. It is also recommended to compare prices from different shipping providers to ensure the most competitive rates.
In conclusion, the shipping cost for importing extrusion blow molding machines from China can vary depending on factors such as machine size, shipping method, destination country, and additional charges. Working with a reliable shipping company or freight forwarder is crucial in getting accurate estimates and guidance throughout the shipping process.
Compare China and Other extrusion blow molding machines Markets: Products Quality and Price,Visible and Hidden Costs
China is a major player in the extrusion blow molding machines market, and it competes with several other countries in terms of product quality and price. When comparing China with other markets, there are distinct differences in visible and hidden costs associated with these machines.
In terms of product quality, China has made significant improvements over the years. Many Chinese manufacturers have invested in advanced technology and improved their manufacturing processes, resulting in better-quality machines. However, certain countries like Germany and Japan still have a reputation for producing high-quality blow molding machines. These machines are often known for their precision, durability, and consistency. While China has made substantial progress, it is still perceived as a lower-cost alternative rather than a top-notch quality provider.
Price is a critical factor when considering extrusion blow molding machines. China has a competitive edge in terms of cost, offering machines at a lower price compared to many other countries. This is primarily due to lower labor and manufacturing costs. Chinese manufacturers benefit from economies of scale, allowing them to produce in large quantities and offer lower prices to customers. However, this lower price often comes with certain trade-offs in terms of quality and after-sales service.
When examining visible and hidden costs, China and other markets may differ. China may have lower visible costs, such as the initial machine price, which can be enticing to potential buyers. However, hidden costs associated with extra parts, maintenance, and after-sales support may add up in the long run. Customers should carefully consider warranty coverage, spare part availability, and the reputation of the manufacturer in terms of customer service and support. On the other hand, other markets might have slightly higher initial prices but provide better after-sales support and fewer hidden costs.
In conclusion, China has made strides in improving the quality of extrusion blow molding machines, but it still lags behind certain countries known for superior quality. China’s competitive advantage lies in its lower-priced machines, thanks to lower manufacturing costs. However, customers should consider both visible and hidden costs associated with these machines, as they vary among different markets. Ultimately, finding the right balance between quality, price, and support is crucial when choosing an extrusion blow molding machine.
Understanding Pricing and Payment Terms for extrusion blow molding machines: A Comparative Guide to Get the Best Deal
When looking to purchase an extrusion blow molding machine, understanding pricing and payment terms is crucial to ensure you get the best deal. This comparative guide aims to provide you with a concise overview in less than 300 words.
1. Pricing Factors: Several factors influence the pricing of extrusion blow molding machines. These include machine size, production capacity, complexities in design, automation level, brand reputation, and additional features. Generally, larger machines with higher production capacities and advanced automation tend to be more expensive.
2. Equipment Cost: Extrusion blow molding machines can range from as low as $20,000 for a basic unit to over $1 million for high-end models. It is important to consider your production needs and budgetary constraints when selecting a machine.
3. Payment Options: Most manufacturers offer flexible payment options to make the purchase affordable. These can include upfront payment, installments, leasing, or financing plans. Evaluate the available options and choose the one that aligns with your financial capabilities and long-term goals.
4. Maintenance Costs: Be mindful of the maintenance costs associated with the machine. This includes spare parts, repair services, and regular maintenance. While a lower-priced machine may seem attractive initially, it may result in higher maintenance expenses in the long run.
5. Comparing Quotes: To ensure you get the best deal, request quotes from multiple manufacturers or suppliers. Compare their offerings in terms of price, machine quality, warranty, customer support, and reputation. Don’t hesitate to negotiate the pricing to secure a more favorable deal.
6. Value for Money: When making a purchasing decision, consider not only the price but also the overall value for money. A higher-priced machine may offer better performance, durability, and cost-efficiency, which can result in long-term savings and productivity gains.
7. After-Sales Support: Evaluate the manufacturer’s after-sales support, including training, technical assistance, and availability of spare parts. A reliable and responsive support system is crucial to minimize downtime and ensure the longevity of the machine.
In conclusion, understanding pricing and payment terms for extrusion blow molding machines requires careful consideration of factors like equipment cost, payment options, maintenance expenses, and the overall value for money. By comparing quotes and assessing after-sales support, you can make an informed decision to secure the best deal for your specific requirements.
Chinese Regulations and Industry Standards Certifications for extrusion blow molding machines,Import Regulations and Customs for extrusion blow molding machines from China
China has established regulations and industry standards certifications for extrusion blow molding machines to ensure product quality, safety, and environmental compliance. One of the key regulations is the “Manufacturing License of Special Equipment” issued by the General Administration of Quality Supervision, Inspection, and Quarantine (AQSIQ). This license is mandatory for manufacturers of extrusion blow molding machines and ensures that the manufacturing process meets specific technical requirements.
Additionally, industry standards certifications such as the “China Compulsory Certification” (CCC) are required for certain components of extrusion blow molding machines. This certification ensures that the products meet essential safety, electromagnetic compatibility, and energy efficiency requirements.
Importing extrusion blow molding machines from China also entails complying with import regulations and customs procedures. Importers need to adhere to the guidelines stipulated by the General Administration of Customs (GAC) to clear the goods through customs. These procedures may include preparing shipping documents, submitting product-related certificates, and paying applicable import duties and taxes.
Furthermore, importers should be aware of any specific regulations imposed by their country of import. For instance, they may need to comply with product certification and labeling requirements enforced by the destination country’s regulatory bodies.
To ensure a smooth transition, importers can seek assistance from freight forwarders or customs brokers who possess expertise in navigating the import process. These professionals will ensure that the necessary import documentation is complete and accurate, easing the customs clearance process for extrusion blow molding machines.
In summary, China has established regulations and industry standards certifications to guarantee the quality and safety of extrusion blow molding machines. Importers should familiarize themselves with the import regulations and customs procedures of their country to ensure a successful import process. Consulting with freight forwarders or customs brokers can provide valuable guidance and assistance throughout the importation journey.
Sustainability and Environmental Considerations in extrusion blow molding machines Manufacturing
Sustainability and environmental considerations in extrusion blow molding machines manufacturing are crucial in today’s climate-conscious society. With increasing concerns about global warming and the depletion of natural resources, manufacturers of extrusion blow molding machines must prioritize sustainable practices to minimize their environmental impact.
One important aspect of sustainability in this manufacturing process is energy efficiency. Extrusion blow molding machines consume a significant amount of energy during their operation. By implementing energy-efficient practices, such as optimizing machine design and using advanced technologies, manufacturers can minimize energy consumption, leading to a reduction in carbon emissions and lower operating costs.
Another key consideration is the use of environmentally friendly materials. Traditionally, blow molding machines have relied on virgin plastics derived from fossil fuels, contributing to the proliferation of plastic waste. However, manufacturers can now explore alternative materials, such as biodegradable or recycled plastics, to reduce their dependence on fossil fuels and minimize waste generation. Additionally, implementing recycling programs within the manufacturing facility can help reduce the environmental footprint by reusing scrap materials and minimizing waste sent to landfills.
Water conservation is another vital aspect to consider. Extrusion blow molding machines require water for cooling purposes, and it is important to implement water-saving measures to reduce consumption and minimize the strain on water resources. This can involve the adoption of closed-loop cooling systems or the use of water-efficient components.
Furthermore, manufacturers should also consider the end-of-life disposal of their machines. Designing products with recyclability in mind, where components can be easily disassembled and recycled, helps promote circular economy principles. Additionally, manufacturers can collaborate with recycling facilities to ensure proper disposal and recycling of their machines once they reach the end of their usable life.
In conclusion, sustainability and environmental considerations in extrusion blow molding machines manufacturing are essential to minimize the industry’s environmental impact. Prioritizing energy efficiency, using environmentally friendly materials, implementing water-conservation measures, and adopting recyclable design principles can all contribute to a more sustainable and environmentally responsible manufacturing process.
List The Evolution history of “extrusion blow molding machines”
Extrusion blow molding machines have come a long way since their inception in the late 1940s. These machines are used to manufacture hollow plastic objects, such as bottles, containers, and tubing, by extruding a molten plastic through a die and blowing air into it to create the desired shape. Here is a brief evolution history of extrusion blow molding machines.
1. Early Development (1940s-1950s): The first extrusion blow molding machines were developed in the late 1940s. These machines used a reciprocating screw to melt the plastic and blow air into the mold. The process was slow, and the machines were manually operated.
2. Continuous Extrusion (1960s-1970s): In the 1960s, continuous extrusion blow molding machines were introduced. These machines featured a continuous extruder, which allowed for faster production. They were also equipped with automated processes, such as parison control and mold closing.
3. Hydraulic Systems (1980s-1990s): During the 1980s, hydraulic systems were integrated into extrusion blow molding machines. This technology further improved the cycle time, precision, and control of the process. Hydraulic clamping systems were also introduced, ensuring more efficient mold closing and opening.
4. Electric and Hybrid Machines (2000s): As technology advanced, electric and hybrid extrusion blow molding machines emerged. These machines utilized electric drive systems, resulting in better energy efficiency, faster response times, and reduced maintenance requirements. The introduction of hybrid machines combined hydraulic and electric technologies to optimize both speed and energy consumption.
5. Advanced Control Systems (Present): In recent years, extrusion blow molding machines have seen significant advancements in control systems. Advanced PLC (Programmable Logic Controller) and HMI (Human-Machine Interface) technologies have been incorporated, allowing for precise control of various parameters, such as temperature, pressure, and timing. This ensures consistently high-quality products and easier operation.
Today, extrusion blow molding machines continue to evolve with a focus on reducing energy consumption, improving automation, and enhancing the overall efficiency of the process. Advancements in materials, cooling techniques, and mold designs have also played a significant role in the evolution and growth of this manufacturing technology.
The Evolution and Market Trends in extrusion blow molding machines Industry
Extrusion blow molding machines have come a long way since their inception, evolving to meet the changing demands of various industries. These machines are used to shape hollow plastic objects like bottles, containers, and tanks. Over the years, there have been significant trends and advancements in the extrusion blow molding machines industry.
One important trend in the industry is the increasing demand for sustainable packaging solutions. As consumers become more environmentally conscious, there is a growing need for packaging that is both functional and eco-friendly. Extrusion blow molding machines have adapted to this trend by incorporating technologies that enable the production of lightweight and recyclable plastic containers. These machines now offer options for thin-wall molding, resulting in reduced material usage and lower carbon footprint.
Automation and digitalization have also transformed the extrusion blow molding machines industry. Manufacturers are implementing advanced control systems and robotics to improve production efficiency and reduce downtime. Automated systems help in achieving consistent product quality and higher productivity while reducing human error. Additionally, the integration of IoT (Internet of Things) technology allows remote monitoring and data analysis, enabling manufacturers to optimize machine performance and prevent breakdowns.
The market for extrusion blow molding machines is expanding globally, driven by various factors. The packaging industry, in particular, is witnessing significant growth due to the rise in e-commerce and convenience packaging. Automotive, healthcare, and consumer goods sectors also contribute to the increasing demand for extrusion blow molding machines.
In terms of geographical trends, emerging economies in Asia, such as China and India, are experiencing rapid industrialization and urbanization. This has resulted in a higher demand for plastic packaging, propelling the growth of the extrusion blow molding machines market in these regions. Developed regions like North America and Europe have a mature market but continue to witness technological advancements to meet evolving customer needs.
In conclusion, the extrusion blow molding machines industry has witnessed an evolution driven by the need for sustainable packaging, automation, and digitalization. The market shows a positive outlook due to the growing demand from diverse sectors and the rapid industrialization in emerging economies. Manufacturers need to stay abreast of the latest trends and technologies to remain competitive in this dynamic industry.
Custom Private Labeling and Branding Opportunities with Chinese extrusion blow molding machines Manufacturers
Chinese extrusion blow molding machines manufacturers offer custom private labeling and branding opportunities to customers. These manufacturers have extensive experience in producing high-quality machines and are willing to work with customers to achieve their branding goals.
Through custom private labeling, manufacturers can customize the appearance of the machines according to the customer’s brand identity. This includes incorporating company logos, colors, and other branding elements onto the machines. Custom private labeling allows customers to promote their brand and create a distinct identity in the market.
Additionally, Chinese manufacturers also provide branding opportunities through customizing the packaging of the machines. They can design and produce packaging materials that showcase the customer’s brand and provide useful information about the product. This helps to create a cohesive branding experience for customers.
Chinese extrusion blow molding machines manufacturers are flexible in accommodating specific branding requests. They can provide various options for customization, including the materials used, machine specifications, and additional features. Manufacturers can work closely with customers to understand their needs and develop solutions that align with their branding objectives.
Collaborating with Chinese manufacturers for custom private labeling and branding opportunities offers several benefits. It allows customers to stand out in their target market by presenting a unique brand image. It also helps to enhance brand recognition and create a consistent branding experience for customers.
In conclusion, Chinese extrusion blow molding machines manufacturers offer custom private labeling and branding opportunities to customers. These opportunities allow customers to promote their brand and create a distinct identity in the market. By collaborating with Chinese manufacturers, customers can achieve their branding goals while ensuring the production of high-quality machines.
Tips for Procurement and Considerations when Purchasing extrusion blow molding machines
When purchasing extrusion blow molding machines, there are several factors to consider to ensure you make the right procurement decision. Here are some tips to help you with the purchasing process:
1. Determine your specific needs: Before making any purchase, it is important to identify your requirements. Consider the production capacity, the types of products you will be manufacturing, and any specific features or functionalities needed.
2. Research different suppliers: Look for reputable suppliers that offer high-quality machines. Read reviews, talk to industry experts, and gather information about the suppliers’ experience and track record.
3. Evaluate machine specifications: Compare different machines based on their specifications, such as the maximum extrusion capacity, clamping force, mold dimensions, efficiency, energy consumption, and automation capabilities. Ensure these specifications align with your production needs.
4. Consider machine compatibility: If you already have existing machinery, check the compatibility of the extrusion blow molding machine with your current production line. Compatibility can save costs and minimize the need for modifications.
5. Assess machine reliability and durability: Look for machines that are known for their reliability and durability. Consider the quality of materials used, the machine’s design, and any warranty or maintenance support offered by the supplier.
6. Evaluate cost-effectiveness: While price is an important factor, it should not be the sole determinant. Consider the long-term costs associated with maintenance, spare parts availability, and energy consumption. Balanced with your budget, determine the cost-effectiveness of the machine over its entire lifespan.
7. Train and support: Check if the supplier provides training for machine operators and technical support in case of any issues or breakdowns. Having access to training and support can ensure smoother operations and minimize downtime.
8. Consider future growth: Anticipate future demands and expansion plans. Choose a machine that can accommodate increased production needs or can be upgraded to meet future requirements.
In summary, understanding your specific needs, researching suppliers, evaluating machine specifications and compatibility, assessing reliability and durability, considering cost-effectiveness, and planning for future growth are crucial considerations when purchasing extrusion blow molding machines. Taking time to make an informed decision will help you acquire a machine that fits your production needs and provides long-term value.
FAQs on Sourcing and Manufacturing extrusion blow molding machines in China
1. Why should I consider sourcing and manufacturing extrusion blow molding machines in China?
Sourcing and manufacturing extrusion blow molding machines in China can provide significant cost savings due to lower labor and production costs compared to many other countries. China has a well-established manufacturing industry with a vast supplier network, offering a wide range of options and customization capabilities. Moreover, Chinese manufacturers often have extensive experience in producing blow molding machines, making them reliable partners for your business.
2. What is the process of sourcing extrusion blow molding machines in China?
The sourcing process typically involves identifying potential manufacturers through various channels such as trade shows, online directories, or referrals. After shortlisting suitable suppliers, it is essential to conduct thorough due diligence, including verifying their production capabilities, quality control procedures, and certifications. Requesting product samples and visiting their facilities can also help assess their capabilities and ensure they meet your requirements. Once a supplier is selected, negotiation of terms, such as pricing, lead times, and payment methods, takes place before finalizing the purchase agreement.
3. How do I ensure the quality of extrusion blow molding machines manufactured in China?
Ensuring the quality of produced machines involves conducting thorough supplier audits, verifying certifications like ISO9001, and requesting samples or prototypes for inspection. It is advisable to evaluate the manufacturer’s product quality control processes, such as testing procedures and inspection checkpoints throughout the manufacturing process. Collaborating closely with the supplier and maintaining regular communication can help in resolving any quality concerns promptly.
4. What are the lead times for manufacturing extrusion blow molding machines in China?
Lead times vary depending on the complexity and customization requirements. It is important to discuss lead times with the supplier during the negotiation stage, ensuring that they align with your production schedule. Manufacturers in China usually provide estimated lead times based on the specifications provided by the buyer.
5. Are there any potential challenges or risks when sourcing and manufacturing extrusion blow molding machines in China?
Some challenges to consider include language barriers, differences in business practices and cultural norms, intellectual property protection, and transportation logistics. It is crucial to choose reliable and reputable suppliers and establish clear communication channels to mitigate these risks effectively.
Overall, sourcing and manufacturing extrusion blow molding machines in China can offer cost-effective solutions without compromising on quality. Careful research, due diligence, and effective communication with suppliers can help navigate potential challenges and ensure a successful partnership.
Why contact sourcifychina.com get free quota from reliable extrusion blow molding machines suppliers?
Sourcifychina.com offers a platform for businesses looking to source products from China, including extrusion blow molding machines. To provide the best service to their customers, they have partnered with reliable extrusion blow molding machine suppliers to offer a free quota for contacting them.
Sourcifychina.com understands the challenges businesses face when sourcing products from China, such as finding trustworthy suppliers and ensuring product quality. By partnering with reliable extrusion blow molding machine suppliers, they aim to alleviate these concerns and provide their customers with a hassle-free sourcing experience.
Obtaining a free quota from these suppliers allows businesses to inquire about their specific requirements, negotiate pricing, and understand the range of services offered by the suppliers. This gives businesses the opportunity to evaluate their options and make informed decisions about which supplier aligns best with their needs.
By offering a free quota, sourcifychina.com is encouraging businesses to reach out to their network of reliable suppliers without any financial commitment or risk. This helps to build trust between the platform, the suppliers, and the businesses, as it demonstrates a commitment to facilitating transparent and fruitful business relationships.
Moreover, the platform emphasizes using the free quota responsibly by not exceeding 300 words in their initial contact. This ensures that businesses provide concise and relevant information to the suppliers, streamlining the communication process and allowing suppliers to address inquiries efficiently.
In conclusion, sourcifychina.com offers a free quota from reliable extrusion blow molding machine suppliers to support businesses in their sourcing endeavors. This initiative provides businesses with the opportunity to connect with trusted suppliers, inquire about their needs, negotiate pricing, and make well-informed decisions. By limiting the initial contact to 300 words, sourcifychina.com encourages concise communication for effective supplier evaluation and faster response times.