Introduce about hdpe extrusion guide,Qulity,Cost,Supplier,Certification,Market,Tips,FAQ
HDPE Extrusion Guide:
HDPE (High-Density Polyethylene) is a versatile plastic material widely used in various industries due to its excellent properties. HDPE extrusion refers to the process of forming HDPE pellets into a continuous profile or shape by applying heat and pressure.
Quality: HDPE extrusion offers high-quality products with excellent durability, chemical resistance, and UV stability. It provides a smooth surface finish and dimensional accuracy, ensuring the final product meets strict quality standards.
Cost: HDPE extrusion is cost-effective compared to other materials. Its low production and maintenance costs make it an economical choice for various applications. Additionally, HDPE is recyclable, contributing to sustainability and cost savings.
Supplier: Numerous suppliers specialize in HDPE extrusion. It is crucial to choose a reliable supplier with extensive experience, advanced equipment, and a commitment to quality control. Trusted suppliers offer customized solutions, on-time delivery, and technical support.
Certification: It is important to source HDPE extrusion products from certified suppliers. Look for suppliers with ISO 9001 certification, ensuring adherence to strict quality management systems. Additionally, consider checking for certifications like ISO 14001 for environmental management and OHSAS 18001 for occupational health and safety.
Market: HDPE extrusion finds applications across various industries such as packaging, construction, agriculture, automotive, and more. It is commonly used to manufacture pipes, profiles, sheets, containers, and fittings. The growing demand for sustainable and durable materials continues to drive the market for HDPE extrusion.
Tips: When working with HDPE extrusion, ensure proper machine setup, including temperature control and screw design. Utilize appropriate cooling methods, such as air or water, to achieve desired product properties. Regularly inspect and maintain equipment to ensure smooth operation and prevent downtime.
FAQ:
1. What is the maximum temperature HDPE can withstand during extrusion?
HDPE can typically withstand temperatures up to 250°C during extrusion.
2. Can HDPE be recycled?
Yes, HDPE is highly recyclable and can be used to create new products.
3. What are the advantages of HDPE extrusion over other methods?
HDPE extrusion offers cost-effectiveness, excellent quality, and design flexibility compared to other manufacturing methods.
In summary, HDPE extrusion provides high-quality products at a competitive cost. Choosing a reliable supplier with certifications and considering proper machine setup are essential for successful extrusion. HDPE’s versatility and recyclability contribute to its growing market demand in various industries.
Types of hdpe extrusion
High-density polyethylene (HDPE) is a versatile thermoplastic polymer that is widely used in the extrusion industry for various applications. HDPE extrusion refers to the process of shaping and forming HDPE into a specific profile or shape using an extruder.
There are several types of HDPE extrusion techniques commonly used, including:
1. Sheet Extrusion: This is the most common type of HDPE extrusion, where a continuous sheet or film is produced by melting the HDPE resin and forcing it through a flat die. The sheet can have different thicknesses and is used in a wide range of applications, such as packaging materials, geomembranes, and industrial liners.
2. Profile Extrusion: In this technique, HDPE is extruded into a desired cross-sectional shape continuously. A specialized die is used to impart the desired shape, such as pipes, tubes, rods, or custom profiles. Profile extrusion is used in applications like conduit pipes, window profiles, and automotive trims.
3. Blow Molding: HDPE can also be extruded using the blow molding process to produce hollow plastic products, such as bottles, containers, and tanks. In this process, molten HDPE is extruded into a hollow tube shape (parison) and then clamped into a mold. Compressed air is then blown into the parison, expanding it to match the shape of the mold.
4. Welding Rod Extrusion: HDPE welding rods are produced through extrusion for use in joining or repairing HDPE pipes and liners. The HDPE resin is melted, extruded through a die to form a continuous rod, and then cooled before being cut into smaller lengths.
5. Co-Extrusion: This technique involves extruding multiple layers of HDPE simultaneously to create a composite structure with different properties. Co-extrusion is used to produce multi-layer films or sheets with specific characteristics like barrier properties, UV resistance, or enhanced strength.
HDPE extrusion offers numerous advantages, including excellent chemical resistance, durability, and versatility. Its wide range of applications across industries makes it a popular choice for extrusion processes. Whether it is for sheet production, profile extrusion, blow molding, welding rods, or co-extruded products, HDPE extrusion techniques offer tailor-made solutions to meet different requirements.
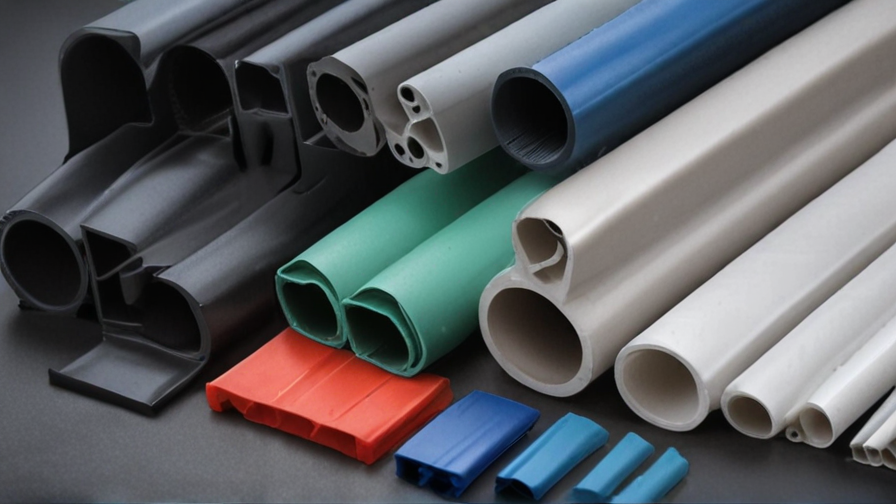
Pros and Cons of Using hdpe extrusion
High-Density Polyethylene (HDPE) extrusion is a manufacturing process used to produce plastic products by melting and shaping HDPE resin into a continuous profile. This process offers several advantages and disadvantages, which are discussed below.
Pros:
1. Strength and durability: HDPE is a tough and strong thermoplastic material, making it suitable for producing products that require strength and durability. HDPE extrusion provides excellent resistance to impact, chemicals, and environmental stress cracking, ensuring the longevity of the finished products.
2. Chemical resistance: HDPE has high resistance to a wide range of chemicals, including acids, bases, and solvents. This makes it a popular choice for manufacturing containers, pipes, and fittings used in various industries, such as chemical processing, water treatment, and agriculture.
3. Flexibility: HDPE extrusion allows manufacturers to produce products with various shapes, sizes, and thicknesses. The versatility of HDPE makes it suitable for a wide range of applications, including packaging materials, drainage systems, and geomembranes for environmental protection.
4. Lightweight: HDPE is a lightweight material, which can reduce transportation costs and make installation easier. It is about one-eighth the density of steel and significantly lighter than other traditional materials like concrete or metal.
5. Recyclability: HDPE is highly recyclable, making it an environmentally friendly choice. It can be melted and reprocessed into new products, reducing the demand for virgin materials and decreasing waste sent to landfills.
Cons:
1. Temperature limitations: HDPE has relatively low-temperature resistance compared to other engineering plastics. It has a melting point around 120 to 130 degrees Celsius, limiting its use in applications that involve high-temperature environments.
2. UV degradation: HDPE is susceptible to ultraviolet (UV) degradation when exposed to direct sunlight over a prolonged period. To overcome this limitation, manufacturers often add UV stabilizers or pigments to improve the UV resistance of the finished products.
3. Limited stiffness: HDPE has a low modulus of elasticity, which means it has limited stiffness compared to materials like steel or aluminum. In applications where high rigidity is required, additional reinforcements or modifications may be needed.
4. Welding requirements: If HDPE products need to be joined together, specialized welding techniques are often required. This can add complexity and cost to the manufacturing process.
5. Cost: While HDPE is generally considered an affordable material, the cost can vary depending on factors such as product complexity, size, and volume. In some cases, other materials may be more cost-effective, depending on the specific application.
In summary, HDPE extrusion offers numerous advantages, including strength, chemical resistance, flexibility, and recyclability. However, it has limitations in terms of temperature resistance, UV degradation, stiffness, welding requirements, and cost considerations.
hdpe extrusion Reference Specifications (varies for different product)
HDPE (High-Density Polyethylene) extrusion is a versatile process used to manufacture a wide range of products. The reference specifications for HDPE extrusion vary depending on the desired product, as different applications require specific properties and performance characteristics.
In general, HDPE extrusion involves heating the polymer resin and pushing it through a die to form a continuous profile or shape. The extruded material then goes through a cooling process to solidify and maintain its desired properties. Some common products of HDPE extrusion include pipes, tubes, sheets, rods, profiles, and wire insulations.
The reference specifications for HDPE extrusion take into consideration various factors such as melt flow rate, melt temperature, cooling temperature, extrusion speed, and die design. The melt flow rate determines the viscosity and flowability of the resin, which affects the final product’s strength and surface finish. The melt and cooling temperatures ensure proper melting and solidification of the polymer, influencing the product’s mechanical properties.
Extrusion speed plays a crucial role in determining the output rate and quality. Higher extrusion speeds may lead to insufficient cooling and result in poor dimensional accuracy. On the other hand, lower speeds may increase the cooling time and hamper productivity.
Die design is another crucial aspect as it determines the shape and dimensions of the final product. It should facilitate uniform flow of the molten resin, ensuring even distribution and avoiding defects like warping or uneven wall thickness.
Moreover, different products have specific requirements. For example, HDPE pipes need to meet certain standards for pressure rating, resistance to environmental stress cracking, and long-term durability. Sheet extrusion for industrial applications may require specific tensile strength, impact resistance, or chemical resistance.
To sum up, HDPE extrusion reference specifications encompass factors like melt flow rate, melt and cooling temperatures, extrusion speed, and die design. These parameters vary according to the desired product and its specific performance requirements. Understanding and adhering to these specifications are crucial for achieving high-quality HDPE extrusion products across different industries.
Applications of hdpe extrusion
High-density polyethylene (HDPE) extrusion is a versatile process used in various industries for a wide range of applications. Here are some key applications of HDPE extrusion:
1. Packaging: HDPE extrusion is used to manufacture rigid packaging materials such as bottles, containers, caps, and closures. HDPE’s excellent strength-to-weight ratio, chemical resistance, and durability make it suitable for packaging of food, beverages, household chemicals, and personal care products.
2. Pipes and fittings: HDPE extrusion is widely used in the construction industry for manufacturing pipes and fittings due to its high strength, corrosion resistance, and flexibility. HDPE pipes are used for water supply, drainage, gas distribution systems, and even as conduits for electrical cables.
3. Geomembranes: HDPE geomembranes are impermeable liners used in civil engineering applications. These liners are used in landfills, mining, oil and gas containment, water storage, and agricultural applications to prevent the seepage or contamination of chemicals and liquids.
4. Agricultural films: HDPE extrusion is used to manufacture agricultural films such as mulch films, greenhouse films, and silage covers. These films provide protection against weather elements, control weed growth, conserve moisture, and enhance crop yields.
5. Automotive components: HDPE extrusion is employed in the automotive industry for manufacturing various components such as fuel tanks, fluid tanks, coolant pipes, and bumpers. HDPE’s lightweight, impact resistance, and chemical compatibility make it suitable for these applications.
6. Toys and sporting goods: HDPE extrusion is used to manufacture toys, playground equipment, and sporting goods such as kayaks, foam boards, hockey boards, and ski boots. HDPE’s durability, impact resistance, and weather resistance make it ideal for such applications.
7. Stationery and office products: HDPE extrusion is utilized in the production of stationery items like folders, document pockets, binders, and pen holders. The lightweight, flexibility, and durability of HDPE make it ideal for such products.
8. Medical and pharmaceutical applications: HDPE extrusion is used in the medical field for manufacturing items like catheters, medical tubing, pill bottles, and medication packaging. HDPE’s chemical resistance, non-toxic nature, and ease of sterilization make it suitable for use in medical and pharmaceutical applications.
In conclusion, HDPE extrusion finds extensive application in various industries including packaging, construction, agriculture, automotive, toys, stationery, and medical. Its superior properties such as high strength, chemical resistance, durability, and flexibility make it a popular choice for a wide range of products and applications.
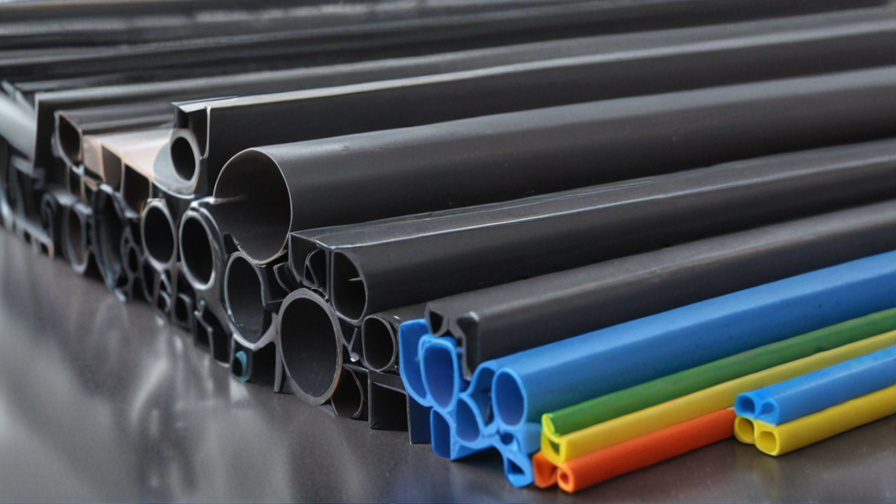
The Work Process and how to use hdpe extrusion
HDPE extrusion is a process used to create products made from high-density polyethylene (HDPE). This material is known for its durability, flexibility, and resistance to chemicals and weather conditions, making it popular in a wide range of industries.
The work process of HDPE extrusion involves several steps. Firstly, HDPE resin pellets are fed into the extruder, which is a machine consisting of a rotating screw in a heated barrel. The resin is melted and compressed by the screw as it moves through the barrel. The heat and pressure help to break down the resin into a molten state.
Once the HDPE resin is molten, it is forced through a die, which is a specialized tool that shapes the material into the desired form. The die can be customized to create various profiles, such as pipes, tubing, sheets, or profiles. The molten HDPE is pushed through the die, and as it passes through, it takes on the shape of the die.
After passing through the die, the HDPE product is cooled and solidified. This can be done using water, air, or a combination of both, depending on the specific requirements of the product. The cooling process is important to ensure that the product retains its shape and structural integrity.
After cooling, the HDPE product is cut or trimmed to the desired length. It can then undergo further processing, such as printing, coating, or assembling, depending on its intended use. Finally, the finished HDPE product is inspected for quality assurance and packaged for shipping or distribution.
To effectively use HDPE extrusion, it is important to understand the properties and capabilities of the material. HDPE extrusions can be produced in various sizes, shapes, and colors to meet specific project requirements. It is essential to determine the appropriate HDPE grade, thickness, and dimensions based on the intended application and environmental conditions.
During the extrusion process, proper control of temperature, pressure, and speed is crucial to ensure consistent and high-quality output. Regular maintenance and cleaning of the extrusion equipment are also essential to maximize productivity and prevent any interruptions or defects.
In conclusion, HDPE extrusion is a versatile and efficient process used to manufacture products made from high-density polyethylene. By understanding the work process and optimizing the use of HDPE extrusion, manufacturers can produce reliable, durable, and cost-effective products for various industries.
Quality Testing Methods for hdpe extrusion and how to control the quality
When it comes to quality testing methods for HDPE extrusion, there are several approaches that can be employed to ensure the desired quality standards are met. Here are some commonly used methods:
1. Dimensional Analysis: This involves measuring the dimensions of the extruded HDPE product using calipers, micrometers, or other similar measuring tools. It helps identify any deviations from the specified dimensions and ensures the product meets the required tolerances.
2. Visual Inspection: Visual inspection is crucial to identify any surface defects such as scratches, dents, or discoloration. Skilled operators visually examine the extruded HDPE product for any abnormalities that may affect its quality and intended use.
3. Tensile Strength Testing: Tensile strength testing assesses the strength and integrity of the extruded HDPE product. Tensile testing machines apply a controlled force to a test sample, measuring the maximum load it can withstand before breaking. This helps determine if the product meets the required tensile strength specification.
4. Impact Resistance Testing: Impact resistance testing measures the product’s ability to withstand sudden impacts or shock loads. It involves subjecting the HDPE extrusion to predetermined impact forces using pendulum-type impact testers. This test checks whether the product can withstand impact without fracturing or cracking.
5. Environmental Stress Cracking Resistance (ESCR) Test: ESCR tests quantify the HDPE extrusion’s resistance to cracking when exposed to specific environmental conditions, such as chemicals or stress. Samples are typically immersed in a chemical solution while simultaneously being subjected to stress. The results help evaluate the product’s durability and resistance to deterioration over time.
To control the quality of HDPE extrusion, manufacturers can implement the following measures:
1. Routine Equipment Maintenance: Regular maintenance and calibration of extrusion equipment ensure precise process control and consistent product quality.
2. Raw Material Selection: Using high-quality HDPE resins from reputable suppliers minimizes variability in material characteristics, resulting in more consistent extrusion outcomes.
3. Process Control Parameters: Strictly monitoring and adjusting critical process parameters like temperature, pressure, and extrusion speed helps maintain consistent product quality.
4. Statistical Process Control (SPC): Implementing SPC techniques enables real-time monitoring and control of process variables, detecting any potential deviations from the desired quality standards to take corrective actions promptly.
5. Employee Training: Properly trained operators and quality control personnel help maintain consistent quality by following established standard operating procedures and promptly identifying and addressing any quality issues.
By incorporating these quality testing methods and control measures, manufacturers can ensure that HDPE extrusions meet the required specifications, minimizing defects and enhancing customer satisfaction.
hdpe extrusion Sample Policy and Post-Purchase Considerations for hdpe extrusion from China
Sample Policy:
When it comes to hdpe extrusion from China, it is important to establish a clear sample policy before making a purchase. This policy ensures that you receive product samples to evaluate its quality, specifications, and performance before placing a bulk order. Here are some key considerations for a sample policy:
1. Requesting Samples: Contact the supplier to request hdpe extrusion samples. Clearly mention your requirements, such as size, color, and any specific features. Suppliers may provide samples for free or charge a nominal fee, which can later be deducted from your order if you choose to proceed.
2. Sample Evaluation: Evaluate the hdpe extrusion samples thoroughly to ensure they meet your expectations. Check for characteristics like strength, flexibility, durability, and overall product quality. Verify that the samples adhere to the required specifications and standards.
3. Communication: Share your feedback with the supplier regarding the sample’s quality and suitability. This is crucial for the supplier to understand your expectations and make any necessary modifications or adjustments.
4. Negotiations: If the samples are satisfactory, initiate negotiations with the supplier on terms of the bulk order. Discuss any customization requirements, pricing, lead times, and payment methods to finalize the deal.
Post-Purchase Considerations:
After purchasing hdpe extrusion from China, it is recommended to consider the following factors to ensure a smooth transaction and maximize satisfaction:
1. Quality Assurance: Confirm that the supplier guarantees consistent quality throughout the production process. This includes meeting specified specifications, maintaining product integrity, and complying with relevant industry standards.
2. Production Schedule: Establish a clear timeline for manufacturing and delivery to avoid delays. Regularly communicate with the supplier to stay updated on the progress of your order.
3. Packaging and Shipping: Discuss packaging requirements, labeling, and shipping methods with the supplier. Ensure that the products are securely packaged to endure transportation and arrive in optimal condition.
4. Payment and Documentation: Agree upon a secure and convenient payment method, such as bank transfer or letter of credit. Verify that the supplier provides proper documentation, including invoices, packing lists, and certificates of origin, for customs clearance.
5. After-Sales Support: Clarify the supplier’s policy on warranty, returns, and replacements. A reliable supplier should provide satisfactory after-sales support to address any issues or concerns that may arise.
By implementing a clear sample policy and considering post-purchase factors, you can mitigate potential risks and establish a strong, mutually beneficial relationship with your hdpe extrusion supplier from China.
Sourcing hdpe extrusion from China: Opportunities, Risks, and Key Players
China is one of the major players in the global HDPE extrusion market, offering numerous opportunities for businesses looking to source this material. HDPE (High-Density Polyethylene) is a versatile thermoplastic used in various applications, including packaging, automotive, construction, and more.
One of the key opportunities of sourcing HDPE extrusion from China is its cost-effectiveness. China is known for its competitive prices due to low labor and manufacturing costs. This makes it an attractive option for businesses looking to minimize production expenses and increase profit margins.
Additionally, China has a well-established infrastructure for manufacturing and exporting HDPE extrusion. It is home to several reputable manufacturers with advanced production facilities and the ability to meet large-scale demands. This ensures a steady supply of high-quality HDPE extrusion for businesses worldwide.
However, sourcing HDPE extrusion from China also comes with certain risks that need to be considered. One such risk is the distance involved in shipping the products. The longer shipping time can cause delays in the supply chain and increases the risk of damage or loss during transit. It is essential to work with reliable logistics partners to mitigate these risks.
Another risk is the potential for quality issues. While China has reputable manufacturers, there are also some companies that may produce substandard or counterfeit HDPE extrusion. Thorough due diligence, such as conducting factory audits, obtaining samples, and checking certifications, is crucial to ensure the quality and authenticity of the products.
When sourcing HDPE extrusion from China, it is important to consider key players in the market. Some notable Chinese manufacturers and exporters in this industry include Sinopec, PetroChina, China National Chemical Corporation (ChemChina), and China Lesso Group. They have a strong presence in both domestic and international markets, offering a wide range of HDPE extrusion products.
In conclusion, sourcing HDPE extrusion from China presents significant opportunities for businesses due to cost-effectiveness and a well-established manufacturing infrastructure. However, it is essential to carefully assess the associated risks, such as longer shipping distances and potential quality issues. Identifying and partnering with reliable key players in the market can help mitigate these risks and ensure a successful sourcing experience.
How to find and select reliable hdpe extrusion manufacturers in China,use google search manufacturers and suppliers
Finding and selecting reliable HDPE extrusion manufacturers in China requires some research and careful evaluation. One effective method is to use Google search to identify manufacturers and suppliers. Here are a few steps to follow:
1. Begin by entering relevant keywords in the search bar, such as “HDPE extrusion manufacturers in China” or “reliable HDPE extrusion suppliers.”
2. The search results will display a list of websites and directories. Visit the websites that appear to be relevant and reliable.
3. Evaluate the manufacturer’s website for essential information. Look for details on their experience, production capacity, certifications, and product specifications. A professional and informative website is often an indicator of a reliable manufacturer.
4. Check for customer reviews and testimonials on the manufacturer’s website or other trusted platforms. Positive feedback from previous customers can help determine their reliability and product quality.
5. Verify the manufacturer’s certifications and compliance with industry standards. Reliable HDPE extrusion manufacturers in China are likely to have certifications such as ISO 9001:2015, ISO 14001:2015, and OHSAS 18001:2007.
6. Contact potential manufacturers to inquire about their product range, customization options, lead times, and pricing. Engage in direct communication to assess their responsiveness and professionalism.
7. Request samples or visit their factory if possible. This allows you to evaluate the quality of their HDPE extrusion products and their overall production capabilities firsthand.
8. Besides Google search, explore other sourcing platforms like Alibaba, Global Sources, or Made-in-China. These platforms usually provide information on the manufacturer’s credibility, certifications, and customer ratings.
9. Consider partnering with a sourcing agent or a reputable trading company in China. They have extensive networks and knowledge to help you find reliable HDPE extrusion manufacturers according to your specific requirements.
10. Finally, compare multiple manufacturers based on their product quality, reliability, pricing, certifications, and customer reviews before making a decision.
By following these steps and conducting thorough research, you can increase your chances of finding and selecting a reliable HDPE extrusion manufacturer in China.
How to check hdpe extrusion manufacturers website reliable,use google chrome SEOquake check if ranking in top 10M
To check the reliability of an HDPE extrusion manufacturer’s website, you can follow these steps:
1. Use Google Chrome: Open your web browser and make sure you are using Google Chrome for this process.
2. Install SEOquake: Add the SEOquake extension to your Google Chrome browser. This extension provides various SEO-related information about websites, including their ranking.
3. Search for the manufacturer: Go to the Google search bar and enter the name of the HDPE extrusion manufacturer you want to check. Press enter to get the search results.
4. Analyze the rankings: Look for the manufacturer’s website link in the search results. Check if it appears on the first page, which typically consists of the top 10 results. If it does, this indicates that the website is well-ranked and likely more reliable.
5. Use SEOquake for more insights: Click on the SEOquake extension in your browser to view more detailed information about the manufacturer’s website. The extension will provide a ton of data, including the PageRank, Alexa rank, number of indexed pages, and more. This information can further help you evaluate the website’s reliability.
6. Confirm ranking in top 10M: If the manufacturer’s website is not listed on the first page of the search results, you can use SEOquake to confirm if it ranks within the top 10 million websites globally. This information is useful to determine if the website is widely recognized or visited.
7. Consider additional information: Apart from SEOquake, you can also look for other factors such as customer reviews, certifications, industry associations, and any other relevant information that can help verify the reliability of the HDPE extrusion manufacturer.
Remember to exercise your judgment and consider multiple sources of information before concluding on the reliability of a manufacturer’s website.
Top 10 hdpe extrusion manufacturers in China with each 160 words introduce products,then use markdown create table compare
1. BOSTON PLASTICS: Boston Plastics is one of the leading HDPE extrusion manufacturers in China, providing a wide range of high-quality products. Their HDPE extruded products include sheets, rods, tubes, and profiles. These products offer excellent chemical resistance, impact strength, and UV resistance, making them ideal for applications in industries like construction, agriculture, and automotive.
2. QINGDAO DAERXIN PLASTICS: Qingdao Daerxin Plastics specializes in the extrusion of HDPE pipes and fittings. Their HDPE pipes are widely used in water supply, gas distribution, and industrial applications due to their high flexibility, corrosion resistance, and easy installation. They also manufacture HDPE pipe fittings, such as elbows, tees, and couplings, ensuring a complete solution for piping systems.
3. ZHEJIANG CHENGMEI INDUSTRIAL: Zhejiang Chengmei Industrial is renowned for its HDPE geomembranes, used for waterproofing and lining applications. Their HDPE geomembranes provide exceptional resistance to chemicals, puncture, and UV radiation, ensuring long-lasting protection for environmental projects, landfills, and reservoirs.
| **Manufacturer** | **Products** |
| ————————– | ———————————————– |
| Boston Plastics | Sheets, rods, tubes, and profiles |
| Qingdao Daerxin Plastics | HDPE pipes and fittings |
| Zhejiang Chengmei Industrial | HDPE geomembranes |
4. POLYWIN PLASTICS: Polywin Plastics specializes in the extrusion of HDPE packaging products. Their HDPE extruded packaging solutions include bottles, caps, containers, and film rolls. These products offer excellent impact resistance and barrier properties, making them suitable for various industries such as food, pharmaceuticals, and chemicals.
5. SHANDONG JINRUI PLASTICS: Shandong Jinrui Plastics focuses on manufacturing HDPE sheets and films. Their HDPE sheets are available in different thicknesses and sizes to cater to diverse applications such as construction, agriculture, and packaging. Additionally, they offer HDPE films for use in greenhouse coverings, pond liners, and geomembranes.
6. THUNDER PLASTICS: Thunder Plastics specializes in the extrusion of HDPE plastic profiles used in industries like automotive, construction, and furniture. Their HDPE profiles are customized to meet specific requirements, ensuring excellent dimensional stability, weather resistance, and durability. Examples of their profiles include channels, trims, and seals.
7. FUJIAN HAOMAI PLASTICS: Fujian Haomai Plastics is a leading manufacturer of HDPE pipes for water supply and gas distribution applications. Their HDPE pipes offer high strength, resistance to corrosion and scaling, and long service life. With strict quality control measures, they ensure that their products comply with international standards.
8. ZHEJIANG SHIFANG PIPELINE: Zhejiang Shifang Pipeline specializes in the extrusion of HDPE pipes for various applications, including irrigation, drainage, and industrial fluid transportation. Their HDPE pipes are known for their high toughness, good flexibility, and resistance to chemicals and abrasion.
9. JOY PLASTICS: Joy Plastics is a prominent manufacturer of HDPE bottles and containers used in the packaging industry. Their HDPE bottles are available in different shapes, sizes, and colors to cater to diverse product requirements. With a focus on quality, their products meet industry standards.
10. WEIFANG HUAWEI PLASTICS: Weifang Huawei Plastics specializes in the extrusion of HDPE nets and meshes for agricultural and industrial applications. Their HDPE nets are used for shade structures, protection against birds and insects, and fencing. With a wide range of options, they provide customized solutions to meet specific requirements.
Overall, China offers a wide range of HDPE extrusion manufacturers catering to various industries. Whether you are looking for pipes, sheets, bottles, or specialized products like geomembranes and nets, these manufacturers provide quality solutions meeting international standards.
Background Research for hdpe extrusion manufacturers Companies in China, use qcc.com archive.org importyeti.com
HDPE (High-Density Polyethylene) is a thermoplastic polymer widely used in various applications due to its excellent strength, durability, and chemical resistance. China is known to be a major player in the manufacturing of HDPE extrusion products, offering a wide range of options to global buyers. To conduct background research on HDPE extrusion manufacturers in China, three useful online platforms can be utilized: qcc.com, archive.org, and importyeti.com.
Qcc.com is a Chinese business information platform that provides comprehensive company profiles, including registration information, legal status, financial data, and key personnel. It allows users to search for HDPE extrusion manufacturers in China, providing essential details about the companies’ backgrounds, capabilities, and product offerings.
Archive.org, also known as the Wayback Machine, allows users to access historical snapshots of websites and internet content. By using this platform, researchers can trace the past activities and changes of HDPE extrusion manufacturers’ websites to gain insights into their development, product lines, and customer base over time.
ImportYeti.com is an import-export data portal that helps researchers identify suppliers and buyers of particular products. By searching for HDPE extrusion suppliers on this platform, users can access records of past shipments, including the names of the manufacturers, the customers, and the products exported. This information can provide an idea of the manufacturers’ export activities and customer relationships.
By combining data from qcc.com, archive.org, and importyeti.com, researchers can gain a holistic understanding of HDPE extrusion manufacturers in China. This information can aid in evaluating their capabilities, reputation, market history, and export activities. It is important to note that these platforms offer both paid and free access, and the available data may vary in depth and accuracy.
Leveraging Trade Shows and Expos for hdpe extrusion Sourcing in China
Trade shows and expos are valuable opportunities for businesses seeking to source HDPE extrusion from China. These events bring together numerous suppliers, manufacturers, and industry professionals in one location, offering a convenient platform for networking, exploring new products and technologies, and building relationships with potential suppliers.
In China, trade shows dedicated to plastic extrusion and related industries are abundant, such as the China International Exhibition for Plastics and Rubber Industries (Chinaplas) and the China Plas exhibition. These shows attract a wide range of exhibitors, including HDPE extrusion manufacturers, machinery suppliers, and raw material providers.
By participating in these trade shows and expos, businesses can benefit in several ways. Firstly, they gain access to a large pool of suppliers, allowing them to compare the quality, pricing, and capabilities of different manufacturers. This proactive approach can help businesses identify reliable and reputable HDPE extrusion suppliers in China.
Additionally, trade shows provide opportunities for face-to-face communication and establishing personal connections with potential suppliers. This enables businesses to establish trust, discuss specific requirements, and negotiate terms directly. Meeting suppliers in person also allows businesses to assess their production facilities, equipment, and overall capabilities.
Furthermore, trade shows often feature live demonstrations, showcasing the latest technologies and machinery used in HDPE extrusion. This allows businesses to stay updated on industry advancements and select suppliers who incorporate the most efficient and innovative processes. Attending seminars and conferences held during these events also provides valuable industry insights and knowledge-sharing opportunities.
To leverage trade shows and expos effectively, businesses should arrive well-prepared. This involves conducting prior research on potential suppliers, developing a clear list of requirements, and setting up meetings in advance. Maximizing the time spent at the event by visiting relevant booths, attending relevant seminars, and engaging in meaningful conversations is crucial for making the most of these opportunities.
Overall, trade shows and expos in China are invaluable resources for businesses sourcing HDPE extrusion. They provide a centralized platform for connecting with numerous suppliers, exploring the latest technologies, and building business relationships. By leveraging these events, businesses can identify reliable suppliers, negotiate better deals, and stay updated on advancements in the HDPE extrusion industry.
The Role of Agents and Sourcing Companies in Facilitating hdpe extrusion Purchases from China
Agents and sourcing companies play a crucial role in facilitating HDPE extrusion purchases from China. They act as intermediaries between buyers and manufacturers, streamlining the sourcing process and ensuring a smooth transaction. Here are some key functions they perform:
1. Supplier Identification: Agents and sourcing companies have an extensive network and knowledge of the market, allowing them to identify reliable and reputable HDPE extrusion manufacturers in China. They conduct research, evaluate suppliers, and verify their credentials to ensure they meet the buyer’s requirements.
2. Quality Assurance: Ensuring product quality is paramount when purchasing from China. Agents and sourcing companies perform thorough quality checks on behalf of the buyers, assessing the manufacturing facilities, inspecting product samples, and conducting on-site visits. They help buyers assess the quality control systems of potential suppliers, reducing the risk of substandard products.
3. Negotiation and Contractual Agreements: Agents and sourcing companies are skilled negotiators, representing the buyer’s interests in price negotiations and contractual agreements. They help buyers secure the best possible terms, including pricing, volume discounts, delivery schedules, and payment terms. By leveraging their market knowledge, they can ensure a fair deal for both parties.
4. Order Monitoring and Production Supervision: Once the order is placed, agents and sourcing companies closely monitor the production process, ensuring that manufacturers meet the agreed specifications, timelines, and quality standards. They coordinate with suppliers, providing regular updates to buyers and addressing any issues that may arise during production.
5. Logistics and Shipping: Managing logistics and shipping can be complex, especially when dealing with international transactions. Agents and sourcing companies handle the transportation and shipping arrangements, ensuring that the HDPE extrusion products are delivered safely and on time. They coordinate with freight forwarders, handle customs documentation, and oversee the entire shipping process.
In summary, agents and sourcing companies simplify the process of purchasing HDPE extrusion from China by facilitating supplier identification, ensuring product quality, negotiating contracts, monitoring production, and managing logistics. Their expertise and experience in the Chinese market help buyers navigate potential challenges and establish a reliable supply chain.
Price Cost Research for hdpe extrusion manufacturers Companies in China, use temu.com and 1688.com
When it comes to finding HDPE extrusion manufacturers in China, two popular online platforms can be utilized for price and cost research: temu.com and 1688.com.
Temu.com is an e-commerce platform that connects buyers and sellers globally. It specializes in various industrial products and services, making it a suitable platform for sourcing HDPE extrusion manufacturers. By searching for HDPE extrusion manufacturers on temu.com, you can explore different suppliers and compare their prices, product specifications, and customer reviews. This will help you understand the market prices and estimated costs for HDPE extrusion manufacturing in China.
Another widely used platform for sourcing suppliers in China is 1688.com. 1688.com is a Chinese-language B2B platform, primarily used by local manufacturers and suppliers. It offers a vast range of products, including HDPE extrusion machinery. Although the platform is in Chinese, using translation services can help navigate and find relevant information. Similar to temu.com, you can search for HDPE extrusion manufacturers on 1688.com, compare prices, and evaluate customer reviews to determine the average market cost.
Performing price and cost research on both platforms will provide a more comprehensive understanding of the HDPE extrusion manufacturing market in China. Ensure you thoroughly communicate with the suppliers to clarify pricing details, additional costs (such as packaging and shipping), and any customization requirements that might impact the final pricing structure.
In conclusion, temu.com and 1688.com are valuable resources for researching HDPE extrusion manufacturers in China and determining price and cost information. By leveraging these platforms, you can gain insights into the market prices and estimate the overall cost associated with HDPE extrusion manufacturing.
Shipping Cost for hdpe extrusion import from China
The shipping cost for HDPE (High-Density Polyethylene) extrusion imports from China can vary depending on several factors. These factors include the weight and dimensions of the shipment, the shipping method chosen, and the destination country.
There are generally two main shipping methods: air freight and sea freight. Air freight is usually faster but more expensive, while sea freight is slower but more cost-effective for large and heavy shipments.
For a small shipment of HDPE extrusion products weighing less than 100kg, air freight might be a preferable option. The cost can range from $4 to $10 per kilogram, including shipping and handling fees. However, this method is not cost-effective for larger shipments.
For larger shipments exceeding 100kg, sea freight is a more suitable option. The cost will depend on the cubic meter (CBM) or cubic foot (CBF) volume of the shipment. The shipping cost can range from $100 to $300 per CBM, excluding additional charges such as customs clearance fees, insurance, and local delivery charges.
It’s important to note that these costs are estimates and can vary depending on the shipping company, specific routes, and any additional services required.
To get an accurate shipping cost, it is recommended to contact multiple freight forwarders or shipping companies to compare prices and services. They will require specific details of the shipment, including the weight, dimensions, and destination address.
It’s also advisable to consider additional costs such as customs duties, taxes, and import fees imposed by the destination country. These fees are not included in the shipping cost and can vary greatly depending on the country’s import regulations and the value of the products.
Overall, it is crucial to research and plan ahead to ensure a smooth import process and to get the most cost-effective shipping option for HDPE extrusion imports from China.
Compare China and Other hdpe extrusion Markets: Products Quality and Price,Visible and Hidden Costs
China is a major player in the HDPE extrusion market, but how does it compare to other markets in terms of product quality, price, and visible and hidden costs?
In terms of product quality, China has made significant progress in recent years. Chinese manufacturers have invested heavily in technology and equipment, allowing them to produce high-quality HDPE extrusion products that meet international standards. However, it is important to note that the overall quality of Chinese products can vary greatly, as there are both excellent and lower-quality manufacturers in the country.
In comparison, other markets, such as the United States and Europe, also have well-established HDPE extrusion industries. These markets generally have a reputation for producing high-quality products, backed by strict quality control measures and regulations. The standards in these markets are generally higher, resulting in consistent and reliable product quality.
When it comes to price, China has a clear advantage. Chinese manufacturers can offer competitive prices due to low labor and production costs. This has made China a popular choice for many international buyers, particularly those looking for cost-effective solutions.
On the other hand, HDPE extrusion products from other markets tend to be more expensive. This can be attributed to higher labor and production costs, as well as stricter environmental and safety regulations. However, the higher price often reflects the superior quality and reliability of products from these markets.
In terms of visible costs, China excels in providing cost-effective solutions. The lower labor and production costs translate into lower prices for customers. However, customers should also consider hidden costs, such as shipping, import duties, and quality control inspections, when importing from China. These additional expenses can sometimes outweigh the initial cost advantage.
In comparison, other markets may have higher visible costs due to higher labor and production costs. However, they often have more streamlined logistics and supply chain processes, resulting in lower hidden costs. Customers in these markets can benefit from improved efficiency and reduced shipping and inspection costs.
In conclusion, China’s HDPE extrusion market offers competitive pricing and improving product quality. However, customers should carefully consider visible and hidden costs before making a purchasing decision. Other markets, such as the United States and Europe, have a reputation for higher product quality but may come with higher visible costs.
Understanding Pricing and Payment Terms for hdpe extrusion: A Comparative Guide to Get the Best Deal
When it comes to sourcing HDPE (high-density polyethylene) extrusion for your business needs, understanding pricing and payment terms is crucial to ensure you get the best deal. This comparative guide aims to provide insights and tips to help you navigate this process effectively.
Pricing for HDPE extrusion can vary based on several factors. Firstly, the quantity you require will impact pricing, as bulk orders often yield lower unit costs. Secondly, the complexity and specifications of the extruded products will influence the price, as intricate designs or customizations may require additional resources or setup costs. Additionally, market demand and supply can also affect pricing, so keeping an eye on industry trends is beneficial.
When comparing prices, it is essential to consider the overall value rather than solely focusing on the lowest cost. Evaluate the reputation and reliability of different suppliers, as subpar quality or delayed deliveries could result in additional costs or business disruptions. Requesting samples or visiting the supplier’s facility can help determine the quality and consistency of their HDPE extrusion.
Payment terms are another critical aspect to consider. Common types of payment arrangements include upfront payments, partial payments, and net terms. Upfront payments often offer discounts but can be risky due to the lack of buyer protection. Partial payments can be a compromise, where an initial deposit is made, and the remaining balance is settled upon delivery or after a grace period. Net terms allow businesses to receive goods first and pay within a specified period, usually 30, 60, or 90 days. However, net terms may come with higher prices due to increased risk for the supplier.
Negotiating favorable payment terms is possible by leveraging your purchasing power. If you plan to make regular or significant orders, suppliers may be open to adjusting their terms to accommodate your needs. Building a long-term relationship with a trusted supplier can also enhance your bargaining power and allow for more favorable terms.
Lastly, it is essential to balance pricing and payment terms with the quality and reliability of the supplier. Opting for the cheapest option may result in subpar products, inconsistent deliveries, or poor customer service. Therefore, conducting thorough research, seeking referrals, and exploring customer reviews are essential to find a supplier that offers competitive pricing, favorable payment terms, and a track record of delivering high-quality HDPE extrusion.
In conclusion, understanding pricing and payment terms for HDPE extrusion is vital to ensure you secure the best deal. By considering factors such as quantity, complexity, and quality, along with negotiating suitable payment arrangements, you can strike a balance between price and reliability, ultimately benefiting your business in the long run.
Chinese Regulations and Industry Standards Certifications for hdpe extrusion,Import Regulations and Customs for hdpe extrusion from China
In China, the extrusion of high-density polyethylene (HDPE) is subject to various regulations and industry standards certifications to ensure product quality and safety. The most important certifications include the Quality Management System Certification (ISO 9001), Environmental Management System Certification (ISO 14001), Occupational Health and Safety Management System Certification (ISO 45001), and the Product Certification of the China National Accreditation Service for Conformity Assessment (CNAS).
The ISO 9001 certification ensures that the HDPE extrusion manufacturers have a well-established quality management system in place, including quality control processes, documentation, and continuous improvement practices. ISO 14001 certification signifies that the manufacturers adhere to environmental management standards, minimizing their impact on the environment during the extrusion process. ISO 45001 certification emphasizes the manufacturers’ commitment to ensuring a safe and healthy working environment for their employees.
Moreover, the CNAS product certification provides independent third-party verification of the HDPE products’ compliance with applicable standards and regulations. This certification assures buyers that the HDPE extrusion products from China meet the required quality and safety standards.
When it comes to import regulations and customs procedures for HDPE extrusion products from China, importers need to comply with the regulations of their respective countries. This typically includes providing relevant documentation, such as commercial invoices, packing lists, bill of lading or airway bills, and certificates of origin.
Importers also need to ensure compliance with the customs regulations of their country, which may include tariff classification, valuation, and the payment of applicable duties and taxes. It is important to consult with customs authorities or seek the assistance of a customs broker to ensure smooth importation of HDPE extrusion products from China.
In conclusion, HDPE extrusion manufacturers in China must meet various industry standards certifications to ensure product quality and safety. Importers need to comply with import regulations and customs procedures specific to their countries when importing HDPE extrusion products from China.
Sustainability and Environmental Considerations in hdpe extrusion Manufacturing
In HDPE extrusion manufacturing, sustainability and environmental considerations play a crucial role in ensuring a responsible and eco-friendly production process. HDPE (High-Density Polyethylene) is a commonly used plastic material known for its durability, strength, and versatility. However, the manufacturing of HDPE involves several aspects that can impact the environment.
One key environmental consideration is the sourcing of raw materials. HDPE is derived from fossil fuels, such as natural gas and petroleum. To promote sustainability, manufacturers should prioritize sourcing these feedstocks from environmentally responsible suppliers, ensuring compliance with regulations and standards.
Energy consumption is another significant aspect to address. Extrusion processes require substantial energy inputs for heating, melting, and shaping the plastic. Implementing energy-efficient technologies and optimizing production processes can help reduce energy consumption and minimize greenhouse gas emissions.
Waste management is critical to mitigate the environmental impact of HDPE extrusion manufacturing. Proper handling and disposal of waste materials, such as scraps and offcuts, are necessary to prevent pollution and maximize resource utilization. Implementing recycling programs can also significantly reduce the consumption of virgin HDPE, conserve energy, and minimize waste generation.
Water usage is an important consideration as well. Extrusion processes typically require water for cooling and lubrication. Reducing water consumption through efficient system designs, water recycling, and treatment processes can minimize the strain on local water resources and reduce the overall environmental footprint.
Furthermore, manufacturers should consider the use of additives and chemicals in the extrusion process. Selecting environmentally friendly additives and avoiding toxic substances not only reduces harm to the environment but also ensures the safety of workers and end-users.
To promote sustainability, HDPE extrusion manufacturers should strive to implement a lifecycle approach. This involves considering the environmental impact of the entire product lifecycle, from raw material extraction to production, distribution, use, and end-of-life disposal or recycling.
In conclusion, HDPE extrusion manufacturing can embrace sustainability and environmental considerations by sourcing responsibly, reducing energy consumption, implementing proper waste management and recycling practices, minimizing water usage, and choosing environmentally friendly additives. By incorporating these measures, manufacturers can produce HDPE products in a more environmentally conscious manner, reducing their ecological footprint and contributing to a greener future.
List The Evolution history of “hdpe extrusion”
HDPE extrusion, also known as high-density polyethylene extrusion, has undergone significant evolution in its history. This process involves the production of objects or components by forcing molten HDPE material through a die to obtain the desired shape. Below is a brief overview of the evolution history of HDPE extrusion:
1. Early Developments: HDPE, a thermoplastic polymer, was first developed in the 1930s by German scientists Karl Ziegler and Erhard Holzkamp. However, it wasn’t until the late 1940s and early 1950s that HDPE gained commercial popularity due to its excellent chemical resistance, high tensile strength, and toughness.
2. Extrusion Machinery: In the 1950s, advancements in extrusion machinery and technology began to revolutionize the HDPE extrusion process. Initially, conventional single-screw extruders were used, followed by the introduction of twin-screw extruders in the 1960s. Twin-screw extruders offered better control over the extrusion process, improved mixing capabilities, and increased efficiency.
3. Pipe Extrusion: The 1970s witnessed significant developments in HDPE pipe extrusion. Large-scale production of HDPE pipes began, initially for applications in the gas distribution industry. Innovations in pipe extrusion technology, such as co-extrusion processes, allowed the production of multi-layer pipes with enhanced properties. These advancements expanded the use of HDPE pipes in various industries, including water supply, sewer systems, and irrigation.
4. Profile Extrusion: By the 1980s, HDPE extrusion expanded beyond pipe production to include the extrusion of profiles. Profile extrusion involves shaping the HDPE material into specific geometries, such as rods, tubes, channels, or complex cross-sections. The versatility of HDPE extrusion made it suitable for various industries, including construction, automotive, and consumer goods.
5. Blown Film Extrusion: In the 1990s, HDPE extrusion further evolved with the development of blown film extrusion. This process involves blowing a tubular HDPE film bubble, which is then collapsed and wound to produce flat film sheets. Blown film extrusion enabled the production of packaging materials, such as bags and wraps, with excellent strength, durability, and flexibility.
6. Continuous Enhancements: Over the years, HDPE extrusion has benefited from continuous technological advancements. These developments include improvements in extruder design, screw geometry, die head technology, automation, and process control systems. These advancements have enhanced the efficiency, quality, and flexibility of the HDPE extrusion process while reducing waste.
Today, HDPE extrusion remains a crucial manufacturing process used in various industries worldwide. Its evolution has allowed for the production of a wide range of HDPE products, addressing diverse application needs and contributing to sustainable development.
The Evolution and Market Trends in hdpe extrusion Industry
The HDPE (High-Density Polyethylene) extrusion industry has witnessed significant evolution and market trends over the years. HDPE is a versatile thermoplastic polymer that is widely used in various industries such as packaging, construction, automotive, and agriculture due to its desirable properties like high strength, chemical resistance, and durability.
One of the key technological advancements in HDPE extrusion is the development of advanced extrusion machinery. Manufacturers have been focusing on enhancing the efficiency and output of extruders, improving extrusion die designs, and incorporating advanced control systems. These advancements have led to higher production rates, improved quality control, and reduced downtime in the extrusion process.
Another notable evolution in the HDPE extrusion industry is the shift towards sustainable practices. Environmental concerns and regulations have pushed manufacturers to develop eco-friendly HDPE products. This has resulted in the development of bio-based and recycled HDPE materials. Additionally, initiatives have been taken to optimize energy consumption during the extrusion process, reducing the carbon footprint of the industry.
Market trends in the HDPE extrusion industry indicate a growing demand for HDPE products in various end-use sectors. The packaging industry is a significant consumer of HDPE extruded products, driven by the increasing need for lightweight and sustainable packaging solutions. The construction industry also presents a lucrative market for HDPE extrusions, with the demand for pipes, profiles, and sheets for applications in infrastructure and building construction.
Moreover, the emerging trend of 3D printing has also impacted the HDPE extrusion industry. The ability to print with HDPE materials has expanded the range of applications in industries such as engineering, prototyping, and product development. This trend has created new opportunities for HDPE extrusion manufacturers to cater to the growing demand for 3D printable materials.
In conclusion, the HDPE extrusion industry has experienced significant evolution and market trends. Technological advancements, sustainability initiatives, and increasing demand from various sectors have shaped the industry’s direction. The future of the HDPE extrusion industry looks promising as manufacturers continue to innovate and meet changing market needs.
Custom Private Labeling and Branding Opportunities with Chinese hdpe extrusion Manufacturers
Chinese HDPE extrusion manufacturers offer a wide range of opportunities for custom private labeling and branding. With their expertise and advanced technology, these manufacturers can help companies create unique and high-quality HDPE extrusion products that will effectively represent their brand.
One major advantage of working with Chinese HDPE extrusion manufacturers is their ability to provide custom private labeling. They can print logos, brand names, and other unique designs directly onto the HDPE products, ensuring that they are easily recognizable and associated with a specific brand. This allows companies to create a strong brand identity and differentiate themselves from competitors.
In addition to private labeling, these manufacturers also offer branding opportunities. They can work closely with companies to design and develop HDPE extrusion products that align with their brand image and values. Manufacturers can incorporate specific colors, shapes, and textures to create a product that is not only functional but also visually appealing and consistent with the brand’s aesthetics.
Moreover, Chinese HDPE extrusion manufacturers are highly flexible and capable of producing various types of products. Whether it is pipes, sheets, or profiles, they can create custom solutions that meet the specific requirements and preferences of companies. This versatility allows companies to expand their product offerings and cater to a wider range of customers.
Furthermore, working with Chinese manufacturers can also be cost-effective. China has a rich manufacturing infrastructure and economies of scale, allowing for competitive pricing without compromising on quality. With lower production costs, companies can invest more in marketing, sales, and other areas to grow their brand presence and reach.
Overall, Chinese HDPE extrusion manufacturers offer excellent opportunities for custom private labeling and branding. Their expertise, flexibility, and cost-effectiveness enable companies to create unique and high-quality products that effectively represent their brand identity in the market.
Tips for Procurement and Considerations when Purchasing hdpe extrusion
When it comes to procurement of HDPE extrusion, there are several key tips and considerations that should be kept in mind. HDPE (High-Density Polyethylene) extrusion is commonly used in various industries for its durability, flexibility, and corrosion resistance. Here are some tips for a successful procurement process:
1. Identify your specific requirements: Before purchasing HDPE extrusion, clearly define your project requirements such as dimensions, thickness, color, and desired properties. This will help you select the most suitable product.
2. Quality assurance: Ensure that the supplier follows stringent quality control measures during the manufacturing process. Look for suppliers who have necessary certifications, such as ISO 9001, to ensure consistent quality.
3. Supplier reputation: Research and choose a reputable supplier with a track record of delivering high-quality HDPE extrusion. Read customer reviews, testimonials, and evaluate the supplier’s experience in the industry.
4. Pricing and cost-effectiveness: Compare prices from multiple suppliers to ensure you are getting the best value for your money. However, be cautious of extremely low prices, as it may indicate compromised quality.
5. Minimum order requirements: Check with the supplier if they have minimum order requirements. This information is crucial, especially if you require a small quantity or want to test the product before making bulk purchases.
6. Customization options: Inquire about the supplier’s ability to customize HDPE extrusion according to your specific requirements. This may include custom colors, sizes, or unique profiles.
7. Shipping and lead times: Consider the supplier’s delivery capabilities and lead times to ensure your project timeline is met. Some suppliers may offer expedited shipping options if you have urgent requirements.
8. Warranty and customer support: Inquire about the warranty provided by the supplier and their after-sales customer support. A reliable supplier should stand behind their product and assist you with any issues that may arise.
9. Environmental responsibility: Consider suppliers who prioritize sustainability and environmental responsibility. Look for certifications such as ISO 14001, which ensures environmentally friendly manufacturing practices.
10. Ongoing relationship: Building a long-term relationship with a trusted supplier can bring benefits such as better pricing, priority on orders, and improved collaboration.
By keeping these tips and considerations in mind, you can ensure a successful procurement of HDPE extrusion that meets your specific project requirements and delivers optimal performance.
FAQs on Sourcing and Manufacturing hdpe extrusion in China
1. What is HDPE extrusion and why is it popular in manufacturing?
HDPE extrusion is a manufacturing process that involves melting a high-density polyethylene (HDPE) plastic resin and passing it through a die to create a continuous profile. This process allows manufacturers to produce customized plastic products of various shapes and sizes, making it highly versatile and cost-effective.
2. Why should I consider sourcing and manufacturing HDPE extrusion in China?
China has established itself as a global manufacturing hub offering competitive pricing, advanced technology, and skilled labor. The country has a vast network of suppliers and manufacturers specializing in HDPE extrusion, ensuring a wide range of options for sourcing and manufacturing requirements.
3. How can I find reliable suppliers in China for HDPE extrusion?
To find reliable suppliers, you can begin by conducting thorough research online and using industry-specific directories. It is recommended to reach out to multiple suppliers, request samples, and evaluate their pricing, certifications, production capabilities, and past client experiences. Additionally, attending specialized trade shows and exhibitions can help establish direct connections with potential suppliers.
4. How can I ensure the quality of HDPE extrusion products from China?
Quality control is crucial when sourcing and manufacturing HDPE extrusion in China. It is advisable to work closely with suppliers, clearly communicate your requirements, and conduct regular inspections throughout the manufacturing process. Engaging a third-party quality inspection company can provide an additional layer of assurance.
5. What are the production lead times for HDPE extrusion in China?
Production lead times can vary depending on the complexity of the product, quantity, and supplier’s capacity. Generally, it is recommended to allocate sufficient time for production, including sample approval, tooling development, manufacturing, and shipping. Discussing timelines with suppliers and establishing clear delivery expectations can help avoid delays.
6. Are there any specific certifications or regulatory compliances that need to be considered for HDPE extrusion in China?
The most common certifications for HDPE extrusion products include ISO 9001 (quality management system) and ISO 14001 (environmental management system). Additionally, specific industry certifications and regulatory compliances may be required depending on the intended use of the product. Suppliers in China should be able to provide information on the certifications they hold and ensure compliance with relevant regulations.
In conclusion, sourcing and manufacturing HDPE extrusion in China provides various benefits such as cost-efficiency, a wide range of suppliers, and advanced manufacturing capabilities. Conducting thorough research, maintaining clear communication, and implementing quality control measures are essential in ensuring successful sourcing and manufacturing processes.
Why contact sourcifychina.com get free quota from reliable hdpe extrusion suppliers?
Sourcifychina.com offers a free quota from reliable HDPE extrusion suppliers for several reasons. Firstly, Sourcifychina.com aims to provide customers with a hassle-free sourcing experience. By offering a free quota, customers can quickly and easily access information about multiple suppliers without any financial commitment upfront. This allows customers to compare different options and make an informed decision based on their specific requirements.
Moreover, Sourcifychina.com collaborates with reliable HDPE extrusion suppliers who have been vetted and verified for their product quality, manufacturing capabilities, and business integrity. By partnering with such suppliers, Sourcifychina.com ensures that customers receive high-quality products that meet their standards and specifications.
Additionally, offering a free quota helps Sourcifychina.com build trust and credibility in the market. By providing customers with the opportunity to receive quotations from reliable suppliers, Sourcifychina.com showcases their commitment to transparency and delivering value to customers. This helps establish a positive brand reputation and encourages more customers to use their services.
Furthermore, by limiting the quota to free quotations, Sourcifychina.com can manage the influx of inquiries and ensure a smooth process for both customers and suppliers. This prevents overwhelming the suppliers and allows them to provide accurate and timely quotations to interested customers.
In conclusion, Sourcifychina.com offers a free quota from reliable HDPE extrusion suppliers to simplify the sourcing process for customers, ensure product quality and integrity, build trust and credibility, and manage the influx of inquiries. This approach helps customers make informed decisions and eliminates any financial risk associated with sourcing from new suppliers.