Introduce about hydraulic plastic moulding machine guide,Qulity,Cost,Supplier,Certification,Market,Tips,FAQ
Hydraulic plastic molding machines are widely used in the manufacturing industry for producing plastic products through injection molding. This guide aims to provide an overview of these machines, covering aspects such as quality, cost, suppliers, certifications, markets, tips, FAQs, and more.
Quality is a vital consideration when choosing a hydraulic plastic molding machine. Look for a machine that is durable, reliable, and capable of producing high-quality, consistent results. It should have advanced features such as temperature control, pressure control, and programmable settings to ensure precise molding.
Cost is another crucial factor to consider. It varies depending on factors like machine size, injection capacity, features, and brand. Comparing prices and considering long-term operational costs can help make an informed decision.
Finding a reputable supplier is important to ensure the quality of the machine. Look for suppliers with a good track record, positive customer reviews, and a wide range of machine options. Additionally, consider suppliers who offer after-sales support, warranty, and spare parts availability.
Certification is essential to validate the machine’s compliance with industry standards. Look for machines that have obtained certifications like ISO 9001, CE, or FDA approval to ensure safety, reliability, and quality assurance.
The market for hydraulic plastic molding machines is extensive, catering to various industries such as automotive, consumer goods, packaging, and more. Analyzing market trends and understanding specific industry requirements can help identify potential opportunities.
Here are some tips for purchasing and operating hydraulic plastic molding machines:
1. Choose the right machine size and injection capacity for your production needs.
2. Regular maintenance and servicing are essential to ensure optimal performance and longevity.
3. Train operators properly to maximize productivity and minimize errors.
4. Optimize energy consumption by selecting machines with energy-saving features.
5. Regularly update your knowledge about new technologies and advancements in the industry.
Frequently Asked Questions (FAQ) about hydraulic plastic molding machines may include inquiries about machine specifications, troubleshooting, maintenance, and sourcing spare parts. To provide detailed answers, consider creating a comprehensive FAQ section addressing these common questions.
In conclusion, hydraulic plastic molding machines are vital for plastic manufacturing. Considering factors like quality, cost, suppliers, certifications, market trends, and following tips can help make an informed decision and successfully operate these machines.
Types of hydraulic plastic moulding machine
There are several types of hydraulic plastic moulding machines, each designed to cater to different manufacturing needs. Here is an overview of some common types:
1. Injection Moulding Machine: This is the most widely used type of hydraulic plastic moulding machine. It consists of a hopper where plastic granules are fed, a heating barrel where the granules are melted, and a mould cavity where the molten plastic is injected under pressure. Once cooled and solidified, the mould opens and releases the finished product.
2. Blow Moulding Machine: This machine is specifically used for creating hollow plastic products, such as bottles or containers. It uses a similar process to injection moulding but incorporates a cavity where compressed air is blown into the molten plastic, shaping it against the mould’s walls.
3. Extrusion Moulding Machine: This type of machine is used to produce long continuous shapes, such as pipes, tubes, or profiles. It works by feeding plastic material through a heated barrel with a rotating screw. This screw pushes the molten plastic out through a die, which forms it into the desired shape.
4. Compression Moulding Machine: This machine is used for producing large or complex parts, typically made of thermosetting plastics. The process involves placing a pre-measured amount of plastic material in a heated mould cavity. The mould is then closed, applying pressure and heat to cure the plastic and shape it as desired.
5. Transfer Moulding Machine: This type of machine is similar to compression moulding but utilizes a hydraulic plunger to transfer the molten plastic into the heated mould. It is commonly used for producing small precision parts or electronic components.
6. Rotational Moulding Machine: Also known as a rotomoulding machine, it is used to create large, hollow plastic products by rotating a mould that contains the plastic material. Heat is applied to melt the plastic and disperse it evenly throughout the mould, achieving uniform thickness and strength.
These are just a few examples of the various types of hydraulic plastic moulding machines. Each machine offers unique capabilities and advantages based on the specific requirements of the products being manufactured. Manufacturers must analyze their needs and product specifications to select the most suitable machine type for their operations.
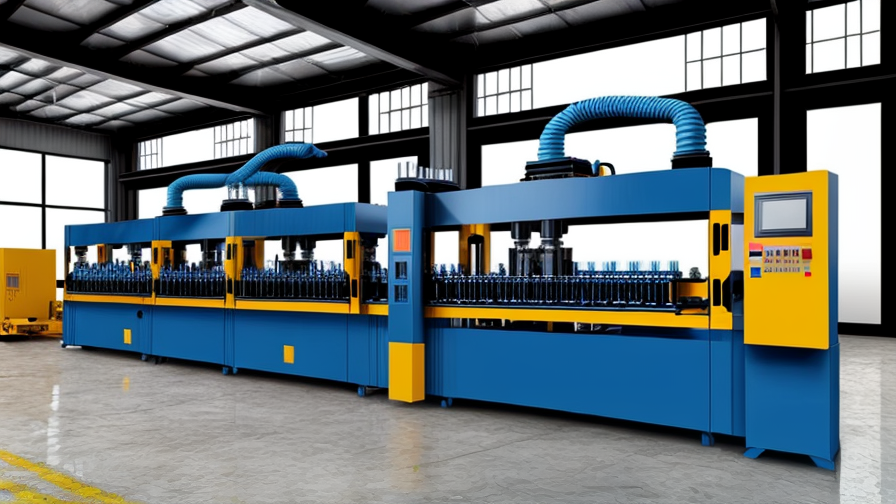
Pros and Cons of Using hydraulic plastic moulding machine
Hydraulic plastic molding machines have been widely used in the plastic industry for many decades due to their numerous advantages. However, they also have some limitations that need to be considered. Here are the pros and cons of using hydraulic plastic molding machines:
Pros:
1. High production capacity: Hydraulic machines are capable of producing high volumes of plastic components in a relatively short period. This makes them ideal for large-scale manufacturing.
2. Versatility: Hydraulic machines can handle a wide range of plastic materials and produce complex shapes with high precision. They provide excellent consistency and repeatability in molding processes.
3. Energy-efficient: Compared to other types of molding machines, hydraulic machines are relatively energy-efficient. They use less power during operation, leading to lower energy costs and a smaller carbon footprint.
4. Cost-effective: Hydraulic machines are generally more affordable than electric or hybrid machines, making them a preferred choice for small and medium-sized businesses. They have lower maintenance costs and are easier to repair.
5. Superior clamping force: Hydraulic machines can generate high clamping forces, allowing them to mold large and thick plastic components. This makes them suitable for applications that require robust and durable products, such as automotive parts.
Cons:
1. High energy consumption during idle time: One major drawback of hydraulic machines is their high energy consumption when not in use. The hydraulic system remains pressurized even when the machine is idle, resulting in unnecessary energy wastage.
2. Noisier operation: Hydraulic machines tend to produce more noise and vibrations compared to electric or hybrid machines. This can affect the working environment and may require additional noise reduction measures.
3. Slower response time: The hydraulic system in these machines has a slower response time compared to electric machines. This can limit the overall productivity and speed of the molding process.
4. High hydraulic oil consumption: Hydraulic machines require a continuous supply of hydraulic oil, which can lead to significant expenses. Regular maintenance and monitoring of oil levels are necessary to ensure the machine’s optimal performance.
5. Environmental concerns: Hydraulic machines rely on hydraulic oil, which can pose environmental risks if not properly handled or disposed of. Proper waste management and adherence to environmental regulations are essential when operating hydraulic plastic molding machines.
In conclusion, hydraulic plastic molding machines offer high production capacity, versatility, and cost-effectiveness in the manufacturing of plastic components. However, they have drawbacks such as high energy consumption during idle time, slower response time, and potential environmental concerns. Considering these pros and cons is crucial in deciding whether a hydraulic plastic molding machine is the right choice for a specific application.
hydraulic plastic moulding machine Reference Specifications (varies for different product)
A hydraulic plastic moulding machine is a type of machine used in the manufacturing industry for molding plastic products using hydraulic pressure. It consists of various components and operates based on specific reference specifications, which may vary depending on the product being manufactured.
The machine typically includes a hydraulic system, heating system, control system, and moulding system. The hydraulic system provides the necessary force and pressure required for the moulding process. It consists of a hydraulic power pack, hydraulic cylinders, valves, and hoses. The power pack generates hydraulic pressure which is transmitted to the cylinders for producing the force needed to push the molten plastic material into the mould cavity.
The heating system is responsible for melting the plastic material. It usually consists of electric heaters embedded in the barrel and nozzle of the machine. The control system manages the machine’s operation and ensures consistency in the moulding process. It may include various sensors, temperature controllers, timers, and programmable logic controllers (PLCs) to monitor and control the different parameters.
The moulding system comprises a mould cavity and a moulding unit. The mould cavity is the specialized cavity or mold in which the plastic material is injected and shaped to form the desired product. The moulding unit includes a plasticizing unit that feeds the plastic material into the barrel, where it is heated and compressed before being injected into the mould cavity.
The reference specifications of a hydraulic plastic moulding machine depend on the specific product being manufactured. These specifications may include parameters such as clamping force, injection capacity, injection pressure, molding temperature, and cycle time. Clamping force defines the maximum force applied by the machine to keep the mould closed during the injection process. Injection capacity refers to the maximum volume of plastic material that can be injected into the mould cavity. Injection pressure determines the force applied to inject the material into the mould, while molding temperature defines the temperature required for melting and shaping the plastic material. Cycle time refers to the time required for completing one full cycle of the moulding process.
In summary, a hydraulic plastic moulding machine is a versatile and efficient tool used in the manufacturing industry for producing various plastic products. Its components, such as the hydraulic system, heating system, control system, and moulding system, work together based on specific reference specifications to ensure accurate and precise molding of plastic materials.
Applications of hydraulic plastic moulding machine
Hydraulic plastic moulding machines are widely used in various industries for manufacturing a wide range of plastic products. These machines utilize hydraulic power to apply pressure and create the desired shape of the plastic material. The applications of hydraulic plastic moulding machines are vast and include:
1. Automotive Industry: Hydraulic plastic moulding machines are utilized in the production of various automotive parts such as bumpers, dashboards, interior trim, and engine components. With their ability to mold complex shapes and provide consistent quality, these machines are highly efficient for automotive manufacturers.
2. Packaging Industry: Hydraulic plastic moulding machines play a vital role in the packaging industry by producing plastic containers, bottles, caps, and other packaging materials. These machines ensure fast production rates and precision in the mold design, meeting the stringent requirements of the industry.
3. Consumer Goods Industry: Many consumer goods such as toys, household appliances, electronic devices, and furniture are manufactured using hydraulic plastic moulding machines. The versatility of these machines allows for the production of a wide range of designs and sizes, catering to the diverse needs of consumers.
4. Medical Industry: Hydraulic plastic moulding machines are used to manufacture a range of medical devices and equipment including syringes, IV components, vials, and medical consumables. These machines provide precise molding capabilities, maintaining the strict quality standards required for medical applications.
5. Electrical Industry: Electric components like connectors, switches, and electrical enclosures are manufactured using hydraulic plastic moulding machines. These machines offer high precision and tightly controlled molding parameters to ensure the reliability and safety of electrical products.
6. Construction Industry: Hydraulic plastic moulding machines are utilized in the construction industry to produce various plastic components, including pipes, fittings, and durable materials used for insulation, sealing, and reinforcement purposes.
7. Furniture Industry: From chair components to decorative elements, hydraulic plastic moulding machines are extensively used in the furniture manufacturing industry. These machines enable the production of intricate designs and facilitate the use of different materials, providing flexibility and quality in the furniture production process.
8. Agriculture Industry: Hydraulic plastic moulding machines are applied in the agriculture sector for the production of irrigation pipe fittings, greenhouse components, and other plastic parts used in farming equipment. The ability to create strong and durable plastic components is essential for the demanding agricultural environment.
In conclusion, hydraulic plastic moulding machines find applications in a wide range of industries, including automotive, packaging, consumer goods, medical, electrical, construction, furniture, and agriculture. These machines offer versatility, precision, efficiency, and cost-effectiveness in the production of various plastic products, contributing to the growth and development of these industries.
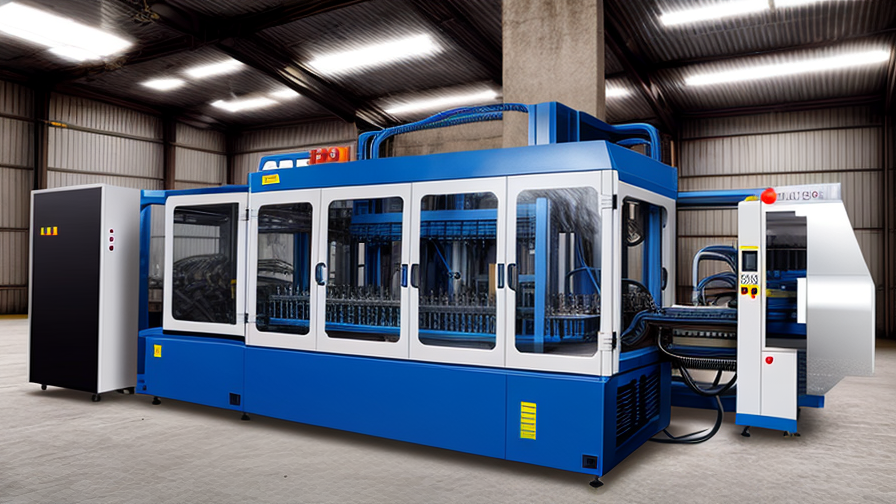
The Work Process and how to use hydraulic plastic moulding machine
Hydraulic plastic moulding machines are widely used in the manufacturing industry to produce plastic products. The work process of a hydraulic plastic moulding machine involves several steps.
1. Preparation: Before operating the moulding machine, the plastic material is prepared by melting it down to a liquid state. This can be done by heating the plastic resin in an extruder or by using preheated plastic pellets. The plastic material is then injected into the machine’s hopper.
2. Clamping: The next step is to close the moulding machine’s clamping unit. The moulding machine consists of two halves, the stationary platen and the moving platen. The mould cavity is created by the combination of these two halves. The clamping unit applies pressure to keep the mould tightly closed during the injection process.
3. Injection: Once the clamping unit is closed, the plastic material is injected into the mould cavity. This is done by the machine’s hydraulic system, which pushes the plastic material through a heated barrel and into the mould cavity. The injection process requires precise control of temperature and pressure to ensure that the plastic fills the mould completely and evenly.
4. Cooling: After the plastic material is injected into the mould cavity, it needs time to cool and solidify. Cooling is achieved by circulating chilled water or air through the mould. The cooling time depends on the thickness of the plastic part and the type of plastic material used. It is important to ensure proper cooling to avoid any deformation or shrinkage of the plastic part.
5. Ejection: Once the plastic part has cooled and solidified, it is time to eject it from the mould. The moulding machine’s hydraulic system applies a sufficient amount of force to push the ejector pins, which help remove the plastic part from the mould cavity. The mould halves are then opened, and the plastic part is released.
To use a hydraulic plastic moulding machine effectively, it is important to follow these steps:
1. Familiarize yourself with the machine’s operation manual and safety guidelines.
2. Preheat the plastic material to the recommended temperature range.
3. Adjust the machine’s settings, such as injection pressure and temperature, based on the type of plastic material and the desired product specifications.
4. Load the plastic material into the machine’s hopper and ensure a consistent flow of material.
5. Close the clamping unit and start the hydraulic system’s injection process.
6. Monitor the injection process to ensure proper filling of the mould cavity.
7. Allow sufficient cooling time for the plastic part to solidify.
8. Activate the ejector system to remove the plastic part from the mould cavity.
9. Inspect the plastic part for defects or imperfections.
10. Repeat the process for subsequent moulding cycles.
By understanding the work process and following the necessary steps, operators can efficiently use hydraulic plastic moulding machines to produce high-quality plastic products.
Quality Testing Methods for hydraulic plastic moulding machine and how to control the quality
When it comes to quality testing methods for hydraulic plastic moulding machines, there are several key techniques that can be used to control the quality. These methods focus on ensuring that the machines are functioning properly, producing high-quality plastic products, and meeting the required specifications.
1. Visual Inspection: One of the most basic and fundamental quality testing methods is visual inspection. This involves physically examining the plastic moulding machine to check for any issues such as leaks, wear and tear, or loose connections. It also includes inspecting the moulded plastic products for any defects or inconsistencies in shape, size, or color.
2. Pressure Testing: Another important quality testing method for hydraulic plastic moulding machines is pressure testing. This involves subjecting the machine to a specified amount of hydraulic pressure to ensure that it can handle the required pressure levels during the moulding process. Any leaks or weak points in the system can be identified through this method.
3. Material Testing: To ensure the quality of the plastic materials being used in the moulding machine, material testing methods can be employed. This involves analyzing the physical and chemical properties of the plastic materials, such as their strength, flexibility, and resistance to heat or chemicals. This testing can be done both on raw materials before moulding and on the final moulded products.
4. Dimensional Testing: It is essential to conduct dimensional testing on the moulded plastic products to ensure that they meet the required specifications. This involves measuring the dimensions of the products using precision instruments and comparing them with the desired measurements. Any deviations from the specified dimensions can be flagged as a quality issue.
To control the quality of a hydraulic plastic moulding machine, the following measures can be implemented:
1. Regular Maintenance: Regular maintenance and servicing of the machine can help identify and rectify any issues or potential problems before they become major quality concerns.
2. Calibration and adjustment: Regularly calibrating and adjusting the machine to ensure it is operating within the desired parameters is crucial for maintaining quality. This includes checking and adjusting temperature, pressure, and other important settings.
3. Training and Skill Development: Providing comprehensive training to the operators and ensuring they have the necessary skills and knowledge to operate the machine correctly is vital. Having well-trained operators can significantly reduce the chances of quality issues.
4. Documentation and Record-keeping: Maintaining detailed documentation of all quality testing procedures, inspection results, maintenance records, and any corrective actions taken is important for tracking and controlling the quality of the machine and the products it produces.
By implementing these quality testing methods and control measures, manufacturers can ensure that their hydraulic plastic moulding machines are functioning optimally, producing high-quality products, and meeting the required standards.
hydraulic plastic moulding machine Sample Policy and Post-Purchase Considerations for hydraulic plastic moulding machine from China
Sample Policy:
When purchasing a hydraulic plastic moulding machine from China, it is important to consider the following sample policy:
1. Minimum Order Quantity (MOQ): China’s suppliers generally require a minimum order quantity for hydraulic plastic moulding machines. Ensure that the MOQ aligns with your production needs and budget.
2. Sample Availability: Request samples of the machine to assess its quality, features, and capabilities. Check if the supplier provides free samples or charges a fee.
3. Customization Options: Inquire about customization possibilities, such as color, size, or additional features, and confirm if they are included in the price or charged separately.
4. Payment Terms: Discuss and finalize payment terms with the supplier. Opt for secure payment methods such as a letter of credit or use Alibaba’s trade assurance to protect your payment.
5. Quality Control: Ask the supplier about their quality control processes, certifications, and if they allow third-party inspection before shipment.
6. Shipping and Delivery: Clarify the shipping terms, including the shipping method, delivery time, and cost. Understand the responsibilities and obligations of both parties during shipping, including insurance coverage.
Post-Purchase Considerations:
After purchasing a hydraulic plastic moulding machine from China, it is essential to take the following post-purchase considerations into account:
1. Installation and Training: Coordinate with the supplier for technical installation and training details. Confirm if they provide on-site support or online assistance for machine setup and operation training.
2. After-Sales Service: Inquire about the supplier’s warranty terms, including its duration and coverage. Understand their after-sales service policy, availability of spare parts, and support channels.
3. Maintenance and Troubleshooting: Request maintenance guidelines and troubleshooting procedures from the supplier to ensure smooth machine operation. Consider partnering with a local technician familiar with hydraulic moulding machines for reliable support.
4. Documentation and Manuals: Obtain translated user manuals, technical documents, and electrical diagrams to assist in machine maintenance and troubleshooting.
5. Customer Reviews and Feedback: Participate in online forums, industry groups, or local associations to gather feedback from other buyers who have purchased hydraulic plastic moulding machines from China.
6. Maintain Communication: Maintain regular communication with the supplier regarding any concerns, questions, or post-purchase support required for the hydraulic plastic moulding machine.
With careful consideration of sample policy and post-purchase considerations, you can mitigate risks and ensure a smooth purchasing experience for a hydraulic plastic moulding machine from China.
Sourcing hydraulic plastic moulding machine from China: Opportunities, Risks, and Key Players
Sourcing hydraulic plastic moulding machines from China presents several opportunities and risks. China is known for its manufacturing capabilities and offers a wide range of hydraulic plastic moulding machines at competitive prices. The country has a well-established supply chain, making it easier to find various options and components for the machines. Additionally, Chinese manufacturers are often willing to provide customization options to suit specific requirements.
The main opportunity of sourcing from China is the cost advantage. Chinese hydraulic plastic moulding machines are generally cheaper compared to those from other countries, allowing businesses to save on investment costs. Moreover, the availability of a wide range of options ensures that businesses can find a machine that matches their specific production needs.
However, there are also certain risks associated with sourcing from China. Quality control can be a concern, as some manufacturers may produce lower-quality machines to reduce costs. Careful screening and due diligence are crucial to ensure the selected Chinese manufacturer meets international quality standards. Additionally, shipping and logistics can sometimes pose challenges, and timely delivery may be an issue if not properly managed.
When sourcing hydraulic plastic moulding machines from China, there are key players to consider. Some of the prominent Chinese manufacturers in this industry include Haitian International Holdings Limited, Chen Hsong Holdings Limited, and Yizumi Precision Machinery Co., Ltd. These companies have a strong presence in the market and are known for their expertise and quality machines. However, it is essential to conduct thorough research and seek recommendations from industry experts to choose the most reliable and suitable manufacturer.
In conclusion, sourcing hydraulic plastic moulding machines from China can offer cost advantages and a wide range of options, but it also carries risks related to quality control and logistics. Selecting reputable key players and conducting due diligence are vital to maximize the opportunities while minimizing potential risks.
How to find and select reliable hydraulic plastic moulding machine manufacturers in China,use google search manufacturers and suppliers
To find and select reliable hydraulic plastic moulding machine manufacturers in China, you can follow these steps:
1. Start with a Google search: Use specific keywords like “hydraulic plastic moulding machine manufacturers in China” or “reliable plastic moulding machine suppliers in China” in your search. This will provide you with a list of potential manufacturers.
2. Verify manufacturers’ websites: Visit the websites of the manufacturers that appear in the search results. Look for professional and well-designed websites that provide detailed information about their products, manufacturing capabilities, and company history. Reliable manufacturers usually have comprehensive and up-to-date websites.
3. Check for certifications and quality standards: Look for certifications like ISO 9001 which signifies adherence to quality management standards. Reliable manufacturers often display these certifications on their websites to demonstrate their commitment to quality production.
4. Evaluate production capabilities: Assess the manufacturer’s production capacity, technical expertise, and equipment capabilities. Look for advanced machinery, modern facilities, and a large production scale indicative of an experienced and reliable manufacturer.
5. Request product samples and specifications: Reach out to the shortlisted manufacturers to request samples or detailed product specifications. High-quality manufacturers will be willing to provide this information and may even offer tailored solutions based on your specific requirements.
6. Inquire about after-sales service and support: Reliable manufacturers prioritize customer satisfaction and offer prompt after-sales service and technical support. Contact the manufacturers and ask about their warranty policies, spare part availability, and maintenance services.
7. Check customer reviews and testimonials: Look for customer reviews and testimonials on the manufacturer’s website or other platforms. Positive feedback from previous clients is a good indicator of a manufacturer’s reliability and customer satisfaction.
8. Consider trade shows and exhibitions: Attend trade shows or exhibitions related to plastic moulding machines in China. These events provide an opportunity to meet manufacturers in person, see their products, and discuss your specific requirements.
9. Verify the manufacturer’s reputation: Conduct due diligence by researching the manufacturer’s reputation, years of experience in the industry, and business history. Check if they have faced any legal disputes, fraud allegations, or product-related safety issues.
10. Request quotations and compare: Finally, request quotations from multiple manufacturers, considering factors like price, delivery time, product quality, and after-sales support. Compare the offers and select the manufacturer that best meets your requirements and standards.
By following these steps, you can increase your chances of finding and selecting reliable hydraulic plastic moulding machine manufacturers in China.
How to check hydraulic plastic moulding machine manufacturers website reliable,use google chrome SEOquake check if ranking in top 10M
When looking to check the reliability of a hydraulic plastic moulding machine manufacturer’s website, follow these steps:
1. Use Google Chrome: Start by opening Google Chrome, a popular web browser that offers various tools and extensions for website analysis.
2. Install SEOquake: Access the Chrome web store and install the SEOquake extension. This tool provides valuable insights about a website’s ranking, traffic, and other metrics.
3. Search for the Manufacturer: Type the name of the hydraulic plastic moulding machine manufacturer in the Google search box. Ensure to enclose the name in quotes (“manufacturer name”) to get accurate search results.
4. Analyze Search Results: SEOquake will display a summary of the top search results on the right-hand side of the search page, including the website’s Alexa Rank, Google Index, and more.
5. Check Alexa Rank: The Alexa Rank is an estimate of a website’s popularity and traffic. If the manufacturer’s website has a low Alexa Rank, it indicates higher popularity and reliability.
6. Verify Google Index: SEOquake also provides information regarding the number of webpages indexed by Google for the manufacturer’s website. A higher indexed count implies a comprehensive and established website.
7. Assess Top 10M Ranking: Look for the ranking of the manufacturer’s website in the top 10M. If it falls within this range, it suggests a decent online presence and sufficient traffic flow.
8. Visit the Manufacturer’s Website: Open the manufacturer’s website from the search results to explore its content, layout, contact information, product details, and customer reviews. A professional website with complete information demonstrates reliability.
Remember to be cautious of websites with poor design, incomplete information, or lack of customer reviews, as these might indicate an unreliable or less established manufacturer.
By following these steps and using SEOquake in Google Chrome, you can quickly assess the reliability of a hydraulic plastic moulding machine manufacturer’s website.
Top 10 hydraulic plastic moulding machine manufacturers in China with each 160 words introduce products,then use markdown create table compare
1. Haitian International Holdings Limited: Established in 1966, Haitian is one of the leading manufacturers of hydraulic plastic injection molding machines in China. With a focus on innovation and technology, their products offer high precision, efficiency, and reliability. They offer a range of machines suitable for various industries, including automotive, packaging, medical, and consumer goods.
2. Ningbo Haida Plastic Machinery Co., Ltd: With over 15 years of experience, Haida Plastic Machinery specializes in manufacturing hydraulic plastic injection molding machines. Their products are known for their high production capacity, energy efficiency, and stable performance. They have a wide range of machines suitable for small to medium-sized plastic parts production.
3. Yizumi Group: Yizumi is a global leader in the manufacturing of hydraulic plastic injection molding machines. Their products are widely used in industries such as automotive, electronics, packaging, and medical. The machines offer fast cycle times, precise control, and energy efficiency. They also provide integrated solutions for automation and auxiliary equipment.
4. Zhejiang Sound Machinery Manufacture Co., Ltd: Sound Machinery is known for its high-quality hydraulic plastic injection molding machines. Their products are designed for precision molding and include features such as high-speed injection, low noise, and energy-saving capabilities. They offer a range of machine models suitable for different production needs.
5. Borche Machinery Co., Ltd: Borche Machinery has been manufacturing hydraulic plastic injection molding machines since 2003. Their products are known for their high performance, durability, and cost-effectiveness. They offer a wide range of machine models, including two-platen machines, hybrid machines, and electric machines.
6. Guangdong Yizumi Precision Machinery Co., Ltd: Yizumi Precision Machinery specializes in manufacturing hydraulic plastic injection molding machines for various industries. Their products are known for their high precision, stability, and energy efficiency. They offer a range of machines suitable for small to large-scale production.
7. Shenzhen Lingsheng Machinery Co., Ltd: Lingsheng Machinery specializes in manufacturing hydraulic plastic injection molding machines. They provide machines with advanced control systems, precise injection capability, and energy-saving features. Their products are widely used in industries such as automotive, medical, and packaging.
8. Ningbo SuRui Machinery Co., Ltd: SuRui Machinery offers a wide range of hydraulic plastic injection molding machines. Their products are known for their high performance, energy efficiency, and reliable operations. They have a strong focus on technological advancements and offer machines suitable for various industries.
9. Shenzhen Supermaster Technology Co., Ltd: Supermaster specializes in manufacturing high-quality hydraulic plastic injection molding machines. Their products are known for their precision, durability, and energy-saving features. They offer a range of machine models suitable for different applications, including multi-component molding and thin-wall molding.
10. Ningbo Well-Lih Robots Technology Co., Ltd: Well-Lih Robots Technology is a leading manufacturer of hydraulic plastic injection molding machines. Their products offer high precision, stability, and energy efficiency. They provide a range of machines suitable for different production requirements, including vertical machines, horizontal machines, and two-platen machines.
|Manufacturer|R&D Capability|Product Range|Energy Efficiency|Customer Satisfaction|
|—|—|—|—|—|
|Haitian International Holdings Limited|✓|Wide range of machines|Efficient energy consumption|High customer satisfaction|
|Ningbo Haida Plastic Machinery Co., Ltd|✓|Small to medium-sized machines|Energy-efficient|Positive customer reviews|
|Yizumi Group|✓|Global leader|Energy-efficient machines|Integrated automation solutions|
|Zhejiang Sound Machinery Manufacture Co., Ltd|✓|High-performance machines|Low noise|Positive customer feedback|
|Borche Machinery Co., Ltd|✓|Various machine models|Cost-effective|Durable machines|
|Guangdong Yizumi Precision Machinery Co., Ltd|✓|High precision machines|Energy-efficient|Positive customer testimonials|
|Shenzhen Lingsheng Machinery Co., Ltd|✓|Advanced control systems|Precise injection capability|Used in automotive, medical, and packaging industries|
|Ningbo SuRui Machinery Co., Ltd|✓|Technologically advanced machines|Energy-efficient operations|Strong focus on customer satisfaction|
|Shenzhen Supermaster Technology Co., Ltd|✓|High-quality machines|Energy-saving features|Used for multi-component and thin-wall molding|
|Ningbo Well-Lih Robots Technology Co., Ltd|✓|Vertical, horizontal, and two-platen machines|High precision|Positive customer feedback|
In this table, we have compared the top 10 hydraulic plastic molding machine manufacturers in China based on their research and development capability, product range, energy efficiency, and customer satisfaction. Each manufacturer has distinct strengths, such as Haitian International’s wide range of machines and Yizumi Group’s integrated automation solutions. Additionally, the table highlights other factors like energy efficiency and positive customer reviews, which are crucial for selecting the right manufacturer.
Background Research for hydraulic plastic moulding machine manufacturers Companies in China, use qcc.com archive.org importyeti.com
When it comes to hydraulic plastic moulding machine manufacturers in China, there are several reliable platforms that can be used for background research. Three such platforms are qcc.com, archive.org, and importyeti.com.
Qcc.com is a Chinese platform that provides information on companies registered in mainland China. It offers details about a company’s background, registration information, financial status, and key personnel. By using qcc.com, one can obtain valuable insights into the company’s credibility, market reputation, and business history.
Archive.org, also known as the Wayback Machine, is a digital archive of the World Wide Web. It captures snapshots of websites and allows users to access past versions of websites dating back to the late 1990s. This feature can be helpful in checking the longevity and consistency of a manufacturer’s online presence, observing any changes in its business strategy or product offerings over time.
Importyeti.com is a platform specializing in the import and export data of various products. It provides information on shipments, including the names of importers and exporters, shipment dates, quantity, and value. This data can help in identifying manufacturers actively involved in exporting hydraulic plastic moulding machines from China, providing an understanding of their market reach and potential customer base.
By utilizing these platforms, one can gather important information about manufacturers, such as their registration details, financial stability, overall reputation, export records, customer base, and more. This research will help in identifying reputable hydraulic plastic moulding machine manufacturers in China, enabling informed decision-making when selecting a suitable supplier for business needs.
Leveraging Trade Shows and Expos for hydraulic plastic moulding machine Sourcing in China
Trade shows and expos are excellent platforms for sourcing hydraulic plastic moulding machines from China. These events provide numerous benefits and opportunities for businesses looking to explore and connect with reliable suppliers.
Firstly, trade shows and expos bring together a wide range of exhibitors specializing in hydraulic plastic moulding machines. This concentrated gathering of suppliers allows buyers to efficiently evaluate multiple options and compare various products and services all under one roof. It also provides a unique chance to see the machines in action and speak directly with knowledgeable representatives.
Moreover, attending trade shows and expos in China offers the advantage of exploring the latest trends and innovations in the industry. It enables buyers to stay up-to-date with cutting-edge technologies, new materials, and advanced functionalities incorporated into hydraulic plastic moulding machines. This knowledge can be instrumental in making informed purchasing decisions and staying ahead of competitors.
Another significant benefit is the opportunity for face-to-face interaction with potential suppliers. Physical presence at trade shows and expos in China allows buyers to establish personal relationships, build trust, and negotiate favorable pricing and terms. Engaging directly with suppliers also facilitates better communication, ensuring that buyers can convey their specific requirements and receive accurate responses, ultimately leading to better sourcing decisions.
In addition, trade shows and expos often feature seminars, workshops, and product demonstrations. Participating in these sessions can enhance buyers’ understanding of the machinery, usage techniques, maintenance protocols, and troubleshooting methodologies. These insights can equip buyers with valuable knowledge when it comes to selecting the most suitable hydraulic plastic moulding machine for their specific needs.
Overall, leveraging trade shows and expos for hydraulic plastic moulding machine sourcing in China offers a multitude of advantages. It enables efficient evaluation, showcases the latest industry trends, supports face-to-face interactions with suppliers, and enhances buyers’ understanding of the products. By utilizing these platforms, businesses can optimize their sourcing processes and stay ahead in the dynamic market of hydraulic plastic moulding machines.
The Role of Agents and Sourcing Companies in Facilitating hydraulic plastic moulding machine Purchases from China
Agents and sourcing companies play a crucial role in facilitating hydraulic plastic molding machine purchases from China. These entities act as intermediaries between buyers and manufacturers, helping streamline the entire procurement process. Here’s how they contribute to this process:
1. Supplier Identification and Verification: Agents and sourcing companies have extensive networks and industry knowledge to identify reliable and reputable hydraulic plastic molding machine manufacturers in China. They conduct thorough due diligence to verify the supplier’s credibility, ensuring compliance with quality standards and certifications.
2. Negotiation and Price Evaluation: Negotiating favorable terms and prices is often a challenging task for foreign buyers. Agents and sourcing companies leverage their expertise in Chinese business practices to negotiate competitive prices for the hydraulic plastic molding machines on behalf of the buyer. They also evaluate the pricing to ensure it aligns with the market rates and product quality.
3. Quality Control and Inspection: Agents and sourcing companies play a crucial role in ensuring the quality of hydraulic plastic molding machines. They conduct pre-shipment inspections to ensure compliance with the buyer’s specifications and standards. Additionally, they can organize factory visits to assess the manufacturer’s production capability and quality control processes.
4. Logistics and Shipping Management: Handling the complex logistics and shipping processes involved in international trade is another significant responsibility of agents and sourcing companies. They coordinate the transportation, customs clearance, and documentation requirements, ensuring a smooth and timely delivery of the purchased hydraulic plastic molding machines.
5. After-sales Support and Communication: Agents and sourcing companies act as the buyer’s representative, facilitating effective communication between the buyer and the manufacturer. They assist in addressing any post-sales issues, warranty claims, or technical support required, bridging the language and cultural barriers that may exist.
By leveraging their expertise, industry connections, and local knowledge, agents and sourcing companies simplify the hydraulic plastic molding machine procurement process from China. They offer vital support in supplier selection, negotiation, quality control, logistics management, and after-sales services, ensuring a successful and hassle-free purchasing experience for buyers.
Price Cost Research for hydraulic plastic moulding machine manufacturers Companies in China, use temu.com and 1688.com
When conducting price cost research for hydraulic plastic moulding machine manufacturers in China, two popular online platforms to consider are temu.com and 1688.com. These platforms provide a wide range of products and suppliers, allowing buyers to compare prices and specifications.
To start the research process, the buyer can visit temu.com, a comprehensive sourcing platform that offers various industrial machinery and equipment. By using relevant keywords such as “hydraulic plastic moulding machine” or specific machine models, buyers can easily find multiple manufacturers, their product portfolios, and corresponding prices. The platform provides detailed product descriptions, images, and specifications, enabling buyers to make informed decisions.
Additionally, 1688.com, an online wholesale marketplace owned by Alibaba Group, is another valuable resource for prospective buyers. The platform specializes in connecting buyers with Chinese manufacturers and factories. By searching for “hydraulic plastic moulding machine manufacturers” or similar terms, buyers can find numerous suppliers offering competitive prices. Moreover, 1688.com allows buyers to communicate with manufacturers directly, negotiate prices, and inquire about customization options.
Buyers should consider comparing prices, product quality, certifications, and supplier reviews when conducting research on temu.com and 1688.com. It is essential to evaluate multiple manufacturers to ensure the best value for money. Additionally, buyers can leverage the platforms’ filtering tools to narrow down their search according to preferred specifications, production capacity, delivery options, or other relevant criteria.
By utilizing these online platforms, buyers can streamline their research process, compare prices, and gather necessary information to make informed decisions when seeking hydraulic plastic moulding machine manufacturers in China.
Shipping Cost for hydraulic plastic moulding machine import from China
The shipping cost for importing a hydraulic plastic moulding machine from China can vary depending on various factors. The most significant factors that influence the shipping cost include the weight and dimensions of the machine, the shipping method chosen, and the destination country.
In general, shipping heavy machinery like a hydraulic plastic moulding machine can be expensive due to its size and weight. It is important to work with a reliable freight forwarder or shipping agent who can provide accurate cost estimates and ensure smooth transportation.
The shipping methods commonly used for such machinery are sea freight and air freight. Sea freight is usually the most cost-effective option for transporting heavy machinery. However, it is a slower method compared to air freight. Air freight is typically more expensive but offers faster delivery, making it suitable for urgent shipments.
Additionally, the distance between the origin and destination countries affects the shipping cost. Shipping to countries further away will generally incur higher costs.
To estimate the shipping cost, it is necessary to provide the weight and dimensions of the hydraulic plastic moulding machine to the shipping agent or freight forwarder. They will consider these details and provide a quote based on the preferred shipping method and destination.
It is recommended to compare quotes from different shipping companies and negotiate the best deal to ensure cost-effectiveness. It is also essential to consider additional charges, such as customs duties, taxes, and insurance, which can impact the overall shipping cost.
In summary, the shipping cost for importing a hydraulic plastic moulding machine from China depends on the weight and dimensions of the machine, the chosen shipping method, and the destination. Working with a reliable shipping agent and comparing quotes will help in minimizing costs and ensuring a smooth import process.
Compare China and Other hydraulic plastic moulding machine Markets: Products Quality and Price,Visible and Hidden Costs
China has established itself as a dominant player in the hydraulic plastic moulding machine market, both in terms of production capacity and overall market share. Comparing China with other markets in terms of product quality and price reveals certain advantages and disadvantages.
In terms of product quality, China has made significant strides over the years. Many Chinese manufacturers have adopted advanced technologies and improved their processes to manufacture high-quality hydraulic plastic moulding machines. However, some concerns still persist regarding consistency and durability. In contrast, certain other markets like Germany and Japan have a longstanding reputation for producing top-notch, precision-engineered machines with excellent product quality and reliability. These markets often offer superior quality control measures and adhere to strict industry standards.
Price is a crucial factor when evaluating markets. China has an edge in terms of affordability due to lower labor and production costs. As a result, Chinese-made hydraulic plastic moulding machines are often priced more competitively compared to their counterparts from other countries. This affordability makes them accessible to a wider range of customers, particularly those from emerging economies. However, it’s worth mentioning that low prices sometimes correlate with compromises in product quality.
When considering visible and hidden costs, it is essential to evaluate factors beyond the initial machine price. For instance, transportation costs vary significantly depending on the origin and destination countries, and the overall distance involved. Shipping charges, import duties, and taxes can also significantly impact the total cost of procuring a hydraulic plastic moulding machine. Additionally, hidden costs associated with after-sales service, maintenance, and spare parts availability are important considerations that can vary across different markets.
In conclusion, China’s hydraulic plastic moulding machine market offers competitive pricing and has taken significant steps towards improving product quality. However, established markets like Germany and Japan often provide superior product quality and reliability. When evaluating different markets, buyers should consider visible and hidden costs associated with transportation, import duties, taxes, and after-sales support. Ultimately, the choice would depend on a buyer’s specific requirements, budget constraints, and the importance they place on product quality versus price.
Understanding Pricing and Payment Terms for hydraulic plastic moulding machine: A Comparative Guide to Get the Best Deal
When it comes to purchasing a hydraulic plastic moulding machine, understanding the pricing and payment terms is crucial to ensure you get the best deal. This comparative guide aims to provide you with relevant information in not more than 300 words.
1. Price range and factors affecting it: Hydraulic plastic moulding machines come in various sizes and capabilities, resulting in a wide price range. Entry-level models typically cost around $10,000, while high-end machines with advanced features can go up to $500,000 or more. Factors influencing the price include machine size, production capacity, speed, accuracy, durability, automation features, brand reputation, and after-sales services.
2. Additional costs: Besides the machine’s direct price, it’s essential to consider additional costs such as shipping, installation, training, and maintenance. Some suppliers may include these services in the initial price, while others require separate payments. Clarifying these details beforehand will prevent unexpected expenses.
3. Warranty and technical support: A reliable machine supplier should offer a warranty that covers manufacturing defects. The warranty period can range from one to several years, so inquire about the terms and conditions. Additionally, ensure that the supplier provides technical support, spare parts availability, and prompt repair services to minimize downtime.
4. Payment terms: Suppliers might offer various payment options, including upfront payment, installment plans, or leasing programs. Upfront payment often provides the best chances for negotiation and discounts, while installment plans allow you to spread the cost over a defined period. Leasing can be advantageous if you have budget constraints but require immediate access to the machine. However, it’s important to consider the total cost of ownership and compare the interest rates or leasing fees.
5. Comparative analysis: Research different suppliers and obtain multiple quotations to compare prices, machine specifications, warranty terms, and after-sales services. Engaging with trusted suppliers, attending industry trade shows, and seeking recommendations can help identify reputable brands and negotiate better deals.
In conclusion, understanding the pricing and payment terms when purchasing a hydraulic plastic moulding machine is essential to secure the best deal. Consider various factors influencing the price, such as machine specifications and additional costs. Evaluate warranty and technical support options and choose the payment plan that suits your requirements. Conduct thorough research and comparative analysis to make an informed decision and ultimately obtain the ideal machine for your needs.
Chinese Regulations and Industry Standards Certifications for hydraulic plastic moulding machine,Import Regulations and Customs for hydraulic plastic moulding machine from China
Chinese Regulations and Industry Standards Certifications for hydraulic plastic moulding machines are an important aspect to consider when importing from China. These regulations ensure that the machines meet safety standards and quality requirements. The main certification for hydraulic plastic moulding machines is the China Compulsory Certification (CCC) mark.
The CCC mark is a mandatory certification for a wide range of products, including machinery. It signifies that a product meets the requirements of China’s technical regulations and safety standards. To obtain the CCC mark, manufacturers must submit their products to a designated certification body for testing and evaluation.
In addition to the CCC mark, other industry standards and certifications may be relevant for hydraulic plastic moulding machines. These include the ISO 9001 certification, which ensures the quality management system of the manufacturer, and the CE mark, which indicates compliance with European safety standards.
When importing hydraulic plastic moulding machines from China, it is essential to comply with import regulations and customs procedures. Importers must provide necessary documentation, such as a commercial invoice, packing list, bill of lading or airway bill, and a certificate of origin. The certificate of origin is important for claiming preferential tariff treatment under free trade agreements.
Importers should also determine whether any import duties, taxes, or fees apply to their specific country and product. It is advisable to consult with customs authorities or a freight forwarder to ensure compliance with all import regulations.
To summarize, when importing hydraulic plastic moulding machines from China, it is crucial to ensure compliance with Chinese regulations and industry standards certifications, particularly the CCC mark. Importers must also be familiar with import regulations and customs procedures to avoid any potential complications during the importation process.
Sustainability and Environmental Considerations in hydraulic plastic moulding machine Manufacturing
Sustainability and environmental considerations are becoming increasingly important in the manufacturing industry, including the production of hydraulic plastic moulding machines. These machines play a crucial role in the manufacturing of plastic products, but their production and operation can have negative environmental impacts.
One key aspect of sustainability in hydraulic plastic moulding machine manufacturing is reducing energy consumption. Energy-efficient machines can be designed and manufactured to minimize power consumption during operation. This can be achieved by optimizing the machine’s hydraulic system, using energy-saving components, and implementing advanced control systems that minimize energy loss. By reducing energy consumption, manufacturers can not only save on operational costs but also reduce their carbon footprint.
Another important consideration is the reduction of waste and emissions during the manufacturing process. Traditional manufacturing methods often generate significant waste in the form of scrap materials, which can be harmful to the environment. Adopting lean manufacturing principles and implementing efficient production processes can help minimize waste generation and improve overall sustainability. Additionally, manufacturers can explore the use of recycled and sustainable materials in the construction of hydraulic plastic moulding machines, reducing the need for raw materials and minimizing the environmental impact.
Furthermore, manufacturers should also focus on extending the lifespan of hydraulic plastic moulding machines. By designing durable and reliable machines, manufacturers can reduce the frequency of replacements and extend the overall product life cycle. This approach not only reduces waste but also benefits the customers by lowering their long-term costs and minimizing disruptions in their production processes.
Lastly, manufacturers can adopt environmentally friendly practices in their production facilities. This includes efficient use of resources, such as water and electricity, implementing proper waste management systems, and promoting recycling and reuse of materials. Additionally, manufacturers can invest in renewable energy sources, such as solar or wind power, to reduce their dependence on fossil fuels and further lower their carbon footprint.
In conclusion, sustainability and environmental considerations in hydraulic plastic moulding machine manufacturing focus on reducing energy consumption, minimizing waste and emissions, extending product lifecycles, and adopting eco-friendly practices in production facilities. By incorporating these considerations into the manufacturing process, companies can contribute to a more sustainable and environmentally friendly future.
List The Evolution history of “hydraulic plastic moulding machine”
The evolution of hydraulic plastic molding machines has seen significant advancements throughout history, revolutionizing the manufacturing industry. The following is a brief overview of their evolution:
1. Early Years (Late 1800s): The first injection molding machines were developed in the late 19th century. These machines were mainly operated manually and used mechanical mechanisms to inject molten plastic into a mold cavity.
2. Introduction of Hydraulic Technology (Early to Mid-1900s): In the early 1900s, hydraulic-powered systems started to replace the mechanical mechanisms in molding machines. Hydraulic systems offered greater control and precision during the injection process, resulting in improved product quality.
3. Introduction of Electric Hydraulic Systems (Late 1900s): In the late 20th century, electric hydraulic systems were introduced, enhancing the efficiency and reliability of plastic molding machines. The combination of electric motors with hydraulic technology allowed for faster and more precise movements, reducing cycle times and increasing productivity.
4. Integration of Computer Numerical Control (CNC) (Late 1900s – Early 2000s): CNC technology gradually made its way into plastic molding machines, enabling automation and programmable control. This integration improved accuracy, repeatability, and overall manufacturing speed.
5. Adoption of Servo-Hydraulic Systems (2000s – Present): In recent years, the industry has seen a shift towards the use of servo-hydraulic technology. These systems combine the benefits of hydraulic and electric drives, providing energy efficiency, high precision, and reduced noise levels.
6. Introduction of All-Electric Machines (Present): All-electric plastic molding machines, which replaced hydraulic systems with electric drives, have gained popularity due to their energy efficiency and precise control. They offer faster cycle times, reduced maintenance, and decreased environmental impact.
Overall, the evolution of hydraulic plastic molding machines has been driven by the need for greater precision, efficiency, productivity, and sustainability. From their earliest days to the present, technological advancements have transformed these machines into highly capable tools used widely within the manufacturing industry.
The Evolution and Market Trends in hydraulic plastic moulding machine Industry
The hydraulic plastic moulding machine industry has witnessed significant evolution and market trends over the years. Initially, hydraulic machines were widely used in the plastic moulding industry due to their ability to provide high pressure and force for the moulding process. However, with the advancement in technology, new moulding machines have emerged that offer superior performance and energy efficiency.
One major evolution in the hydraulic plastic moulding machine industry is the introduction of electric and hybrid machines. Electric machines use servo motors instead of hydraulic systems, resulting in improved energy efficiency and higher precision control. Hybrid machines combine both hydraulic and electric systems, providing the advantages of both technologies. These advancements have gained popularity in the market, as they offer reduced energy consumption, quieter operation, and enhanced process control.
Another significant trend in the industry is the shift towards automation and Industry 4.0 principles. Manufacturers are increasingly incorporating robotics and automation technologies into plastic moulding processes to improve productivity and reduce labor costs. These automated systems can perform tasks such as material loading, mold changes, and quality inspection, resulting in faster production cycles and higher product quality.
Furthermore, there is a growing emphasis on sustainability and environmental concerns in the hydraulic plastic moulding machine industry. Manufacturers are developing machines that consume less energy and minimize waste generation. Additionally, the use of eco-friendly materials and recycling processes are being implemented in the production of plastic moulding machines.
In terms of market trends, the hydraulic plastic moulding machine industry is witnessing a shift towards emerging economies. Developing countries, particularly in Asia-Pacific, are experiencing rapid industrialization and urbanization, leading to increased demand for plastic products and packaging. As a result, the demand for plastic moulding machines is growing significantly in these regions.
Overall, the hydraulic plastic moulding machine industry has evolved to incorporate newer technologies such as electric and hybrid machines, automation, and sustainability. These trends are driven by the need for energy efficiency, process optimization, and environmental responsibility. Market expansion in emerging economies further fuels the growth of the industry.
Custom Private Labeling and Branding Opportunities with Chinese hydraulic plastic moulding machine Manufacturers
Chinese hydraulic plastic molding machine manufacturers offer a range of custom private labeling and branding opportunities to businesses looking to establish their own brand in the market. With their expertise in manufacturing high-quality hydraulic plastic molding machines, these manufacturers can help businesses in creating their own unique branding and packaging that reflects their identity.
One of the main advantages of partnering with Chinese manufacturers is the ability to customize various aspects of the machine to meet specific branding requirements. This includes incorporating a business’s logo, colors, and other branding elements on the machine’s exterior. This level of customization not only enhances brand recognition but also helps businesses differentiate themselves from competitors.
Furthermore, Chinese manufacturers can provide customized packaging solutions that align with a business’s brand image. This could include branded crates or boxes for transportation and storage of the machines. Companies can also request custom labels and user manuals to ensure a consistent brand experience for their customers.
Moreover, Chinese manufacturers are known for their flexibility and responsiveness. They can work closely with businesses to understand their branding goals and provide recommendations to optimize the branding elements of the machines. This collaborative approach ensures that the final product reflects the desired brand image accurately.
In addition to branding opportunities, partnering with Chinese hydraulic plastic molding machine manufacturers offers cost-effective solutions for businesses. China’s well-established manufacturing infrastructure and economies of scale allow for competitive pricing without compromising on quality or customization.
In conclusion, Chinese hydraulic plastic molding machine manufacturers offer businesses the opportunity to establish their own brand through private labeling and branding opportunities. With their customization capabilities, businesses can create a unique brand identity that helps them stand out in the market. Moreover, these manufacturers’ flexibility and cost-effectiveness make them an attractive choice for businesses looking to establish their presence in the industry.
Tips for Procurement and Considerations when Purchasing hydraulic plastic moulding machine
When purchasing a hydraulic plastic moulding machine, there are several essential considerations and tips that should be kept in mind.
Firstly, it is vital to assess the specific needs and requirements of your business. Consider the type and volume of plastic products you intend to produce, as well as the desired rate of production. This will help determine the appropriate size and capacity of the moulding machine.
Next, it is crucial to research and identify reputable suppliers and manufacturers of hydraulic plastic moulding machines. Look for companies with a proven track record of delivering high-quality machines and providing reliable after-sales support. It is advisable to obtain quotes from multiple suppliers to compare prices, features, and warranties.
Furthermore, consider the level of automation and customization options offered by the machine. The technology has evolved significantly in recent years, and many hydraulic plastic moulding machines come with advanced automation features that can enhance productivity and efficiency. Assess whether these additional features align with your production requirements and budget.
The durability and maintenance requirements of the machine are also crucial factors to consider. Look for machines constructed with high-quality materials to ensure long-term durability. Furthermore, inquire about the maintenance schedule and the availability of spare parts. A well-maintained machine will ensure uninterrupted production and minimize downtime.
It is advisable to assess the energy efficiency of the machine before making a purchase. Look for machines that incorporate energy-saving technologies to reduce operational costs and minimize environmental impact.
Lastly, consider the available training and technical support provided by the supplier. Adequate training for machine operators is essential to ensure safe and efficient operation. Additionally, it is vital to have access to reliable technical support in case of any issues or breakdowns.
In conclusion, when purchasing a hydraulic plastic moulding machine, it is crucial to assess your specific needs, research reputable suppliers, consider automation options, assess durability and maintenance requirements, evaluate energy efficiency, and inquire about training and technical support. Following these considerations will help ensure that you make an informed decision and acquire a machine that best suits your business requirements.
FAQs on Sourcing and Manufacturing hydraulic plastic moulding machine in China
Q: How can I source a hydraulic plastic moulding machine in China?
A: To source a hydraulic plastic moulding machine in China, you can start by researching and identifying reputable manufacturers or suppliers through online directories, trade shows, or referrals. Contact the shortlisted companies and request for detailed information about their machines, such as specifications, pricing, delivery time, and after-sales service. Evaluate their capabilities and certifications, and consider visiting their facilities to ensure they meet your requirements. Perform due diligence, negotiate pricing and terms, and finalize a contract before making a purchase.
Q: What are the advantages of sourcing a hydraulic plastic moulding machine from China?
A: Sourcing a hydraulic plastic moulding machine from China can offer various advantages. Firstly, China has a well-developed manufacturing industry with a wide range of suppliers, allowing you to choose from a large pool of options. Secondly, Chinese manufacturers often offer competitive pricing due to lower labor and production costs. Thirdly, many Chinese suppliers have extensive experience in producing hydraulic plastic moulding machines and can provide customization options or industry-specific expertise. Additionally, the production lead time in China can be relatively short, which is advantageous when needing urgent equipment.
Q: Are there any specific considerations when sourcing a hydraulic plastic moulding machine in China?
A: Yes, there are a few considerations when sourcing a hydraulic plastic moulding machine in China. Firstly, you should ensure that the supplier has sufficient experience and expertise in manufacturing such machines, preferably with a good track record and positive customer reviews. Secondly, thoroughly evaluate the machine specifications, quality, and manufacturing standards to ensure compliance with your requirements and industry regulations. Thirdly, verify the supplier’s certifications, such as ISO and CE, to ensure the equipment’s safety and quality standards. Lastly, consider the logistics and shipping arrangements, as well as potential import duties and customs regulations, to avoid any complications or delays.
In conclusion, sourcing a hydraulic plastic moulding machine in China involves researching suppliers, evaluating their capabilities, negotiating pricing and terms, and conducting proper due diligence before finalizing the purchase. Consider the advantages of a wide supplier base, competitive pricing, customization options, and shorter production lead times. Pay attention to supplier experience, specifications, quality standards, and certifications, as well as logistical arrangements and potential import duties.
Why contact sourcifychina.com get free quota from reliable hydraulic plastic moulding machine suppliers?
Sourcifychina.com, being a sourcing platform, aims to connect businesses with reliable suppliers in China. In order to attract potential clients and provide them with a valuable service, they offer a free quota for sourcing hydraulic plastic moulding machines from reliable suppliers.
The decision to focus on hydraulic plastic moulding machines can be attributed to several factors. Firstly, plastic moulding is a widely used technique in various industries such as automotive, electronics, and consumer goods. Therefore, the demand for plastic moulding machines, especially hydraulic ones, is high.
Secondly, sourcing reliable suppliers is crucial in ensuring the quality and efficiency of the machines. Sourcifychina.com understands the importance of working with trustworthy suppliers who can provide high-quality products and reliable after-sales support. By offering a free quota, they encourage businesses to utilize their platform and connect with verified and reliable hydraulic plastic moulding machine suppliers.
This free quota allows businesses to explore the platform and assess the potential of sourcing hydraulic plastic moulding machines from China. It provides an opportunity to connect with multiple suppliers, compare prices, production capabilities, delivery times, and negotiate favorable terms. By doing so, businesses can make informed decisions and choose the most suitable supplier for their specific requirements.
Moreover, by contacting reliable suppliers through Sourcifychina.com, businesses can minimize risks associated with sourcing from overseas, such as communication barriers, cultural differences, or quality control issues. Sourcifychina.com acts as a facilitator, ensuring smooth communication and assisting businesses throughout the sourcing process.
In summary, Sourcifychina.com offers a free quota for sourcing hydraulic plastic moulding machines from reliable suppliers due to the high demand for such machines and the importance of sourcing from trustworthy suppliers. This free quota enables businesses to explore the platform, connect with multiple suppliers, and make informed decisions while mitigating risks associated with sourcing from overseas.