Introduce about injection mold design guide,Qulity,Cost,Supplier,Certification,Market,Tips,FAQ
Injection Mold Design Guide: This comprehensive guide aims to provide valuable insights into the process of injection mold design. It covers essential aspects such as design considerations, material selection, cooling system design, gating and venting, ejection system design, and machining requirements. By following this guide, manufacturers can enhance their overall design efficiency and productivity.
Quality: Injection mold design plays a crucial role in ensuring high-quality finished products. By incorporating appropriate design elements, manufacturers can minimize defects, improve part uniformity, enhance dimensional accuracy, and achieve excellent surface finish. Adhering to quality standards throughout the design process is essential for optimal results.
Cost: Efficient injection mold design can significantly impact production costs. By optimizing the mold design and considering factors like materials, manufacturing techniques, and product complexity, manufacturers can minimize costs while maintaining product quality. Skillful analysis and iteration during the design phase can lead to cost-effective solutions without compromising on performance.
Supplier: Choosing the right injection mold design supplier is vital for successful production. Supplier selection criteria should include expertise, experience, reputation, and ability to deliver high-quality molds within specified timelines. Collaborating with a reliable supplier ensures access to skilled professionals and state-of-the-art technology, resulting in superior mold designs.
Certification: Certification ensures that mold designs meet industry standards and regulatory requirements. Suppliers and manufacturers should collaborate with certified partners who possess relevant certifications such as ISO 9001 to ensure adherence to stringent quality standards. Certification instills trust in customers and enhances market competitiveness.
Market: Injection mold designs cater to a vast array of industries, including automotive, consumer goods, electronics, medical devices, and more. Understanding market trends, application requirements, and industry-specific regulations is essential for creating successful mold designs that meet market demands effectively.
Tips: Incorporating tips and best practices can greatly improve injection mold designs. Tips may include optimizing gate location, designing adequate cooling channels, creating robust ejection systems, and utilizing simulation tools to identify potential design flaws. Implementing these tips can enhance design efficiency, reduce production downtime, and maximize overall productivity.
FAQ: Frequently Asked Questions section can address common queries related to injection mold design. This section can cover topics like materials selection, design iterations, cost considerations, mold maintenance, and troubleshooting common issues. Providing comprehensive answers to these frequently asked questions helps manufacturers gain clarity and make informed decisions during the mold design process.
In conclusion, efficient injection mold design is crucial for achieving high-quality products while controlling costs. Collaborating with certified suppliers, staying updated on market trends, and implementing best practices can greatly optimize mold designs. By following this guide, manufacturers can enhance their design capabilities, ensure customer satisfaction, and drive success in the injection molding industry.
Types of injection mold design
There are several types of injection mold designs that are used in various industries. Each design has its own advantages and considerations, depending on the requirements of the specific product being manufactured. Here are some commonly used types of injection mold designs:
1. Two-Plate Mold: This is the simplest and most commonly used mold design. It consists of two plates, the cavity plate and the core plate, which are separated to eject the molded part. The two-plate mold is cost-effective and easy to maintain, making it suitable for a wide range of applications.
2. Three-Plate Mold: In this design, an additional plate called the stripper plate is added between the cavity and the core plates. The stripper plate helps in ejecting the part from the core, eliminating the need for manual removal. Three-plate molds are suitable for parts with complex geometries and multiple sliders or lifters.
3. Hot Runner Mold: This type of mold design includes a heated manifold system that delivers molten plastic directly to the mold cavities without the need for a sprue or runner system. Hot runner molds eliminate the need for post-molding operations, such as trimming and regrinding, resulting in shorter cycle times and reduced material waste.
4. Multi-Cavity Mold: As the name suggests, this mold design enables the production of multiple identical parts simultaneously. It consists of multiple cavities within the mold, allowing for higher productivity and lower production costs. Multi-cavity molds are commonly used for high-volume production of small to medium-sized parts.
5. Overmolding Mold: Overmolding involves molding a second material onto the first molded part, usually to enhance its appearance, functionality, or grip. This mold design requires precise alignment and coordination between the two materials, ensuring a strong bond between them. Overmolding molds are commonly used in the production of electrical connectors, handles, and soft-touch applications.
6. Insert Mold: Insert molding involves inserting pre-formed components, such as metal inserts or other plastic parts, into the mold cavity before the injection process. The molten plastic then encapsulates the insert, forming a single molded part with integrated features. Insert molding is used to improve part strength, functionality, and assembly efficiency.
These are just a few examples of the various types of injection mold designs used in manufacturing industries. Each design offers unique advantages and considerations, and the selection depends on factors such as part complexity, production volume, material characteristics, and cost constraints.
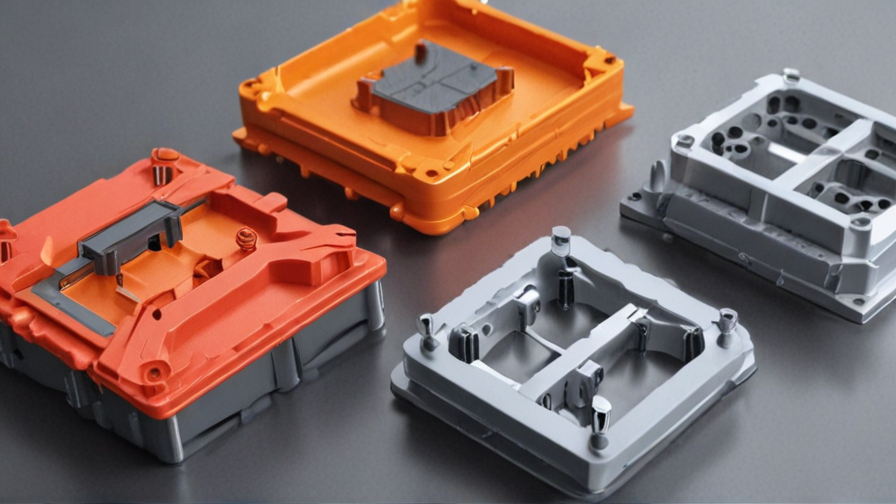
Pros and Cons of Using injection mold design
Injection mold design is a commonly used manufacturing process in which molten material is injected into a mold cavity to form the desired shape. This technique offers several advantages, but it also comes with certain drawbacks. Here are the key pros and cons of using injection mold design.
Pros:
1. Cost-effective: Injection molding is a cost-effective manufacturing method for producing large quantities of identical parts. Once the mold is designed and manufactured, the cost per part decreases significantly.
2. High accuracy and precision: Injection molding allows for the production of complex and intricate designs with high accuracy and precision. The molds can be designed with intricate details, tight tolerances, and uniform wall thicknesses.
3. Wide range of materials: Injection molding can work with a wide variety of materials, including plastics, metals, glasses, and elastomers, offering flexibility in material selection to meet specific product requirements.
4. High efficiency and productivity: Injection molding is a highly automated process, allowing for fast production cycles and high productivity. It enables the production of large volumes of products in a short time frame.
5. Design flexibility: Injection molding allows for design flexibility, as the molds can be easily modified to accommodate design changes or product enhancements. This flexibility makes it suitable for rapid prototyping and iterative design processes.
Cons:
1. High initial costs: The upfront costs of designing and manufacturing injection molds can be significant. This makes it less cost-effective for low volume production or for products with short life cycles.
2. Long lead time: The design and manufacturing of injection molds can take a considerable amount of time, especially for complex designs. The lead time required for mold production can delay the overall manufacturing process.
3. Limited design considerations: Certain design elements, such as undercuts or complex internal geometries, may be challenging to replicate using injection molding. This can limit the design possibilities for certain products.
4. Material limitations: Although injection molding offers a wide range of material options, the choice of materials is still limited compared to other manufacturing techniques. Certain materials may not be suitable for injection molding due to their properties or requirements.
5. Environmental impact: Injection molding generally requires the use of large quantities of raw materials, which can have an environmental impact. Additionally, the disposal of excess materials or scrap generated during the process can be a challenge.
In summary, injection mold design offers cost-effective production, high precision, a wide range of materials, efficiency, and design flexibility. However, it also entails high initial costs, long lead times, limited design considerations, material limitations, and potential environmental impact.
injection mold design Reference Specifications (varies for different product)
Injection mold design reference specifications may vary for different products and industries. However, there are certain common factors that need to be taken into consideration while designing an injection mold.
1. Material: The choice of material for the mold depends on the product requirements. Common materials used include steel alloys, aluminum, and other specialized metals. The material should have excellent thermal conductivity, resistance to wear, and high hardness to withstand the injection molding process.
2. Mold Type: Different products require different mold types such as two-plate molds, three-plate molds, hot runner molds, or insert molds. The mold type selection should be based on factors like product complexity, material flow requirements, and production volume.
3. Mold Cavity: The number of mold cavities determines the number of parts that can be produced in each cycle. The cavity layout should be optimized to achieve maximum productivity while ensuring balanced filling and cooling.
4. Parting Line: The parting line is the line where the mold splits into two halves. It should be strategically placed to avoid critical part features like logos or text and ensure easy ejection of the molded part.
5. Cooling System: Proper cooling is essential to ensure uniform part quality and minimize cycle time. Cooling channels should be designed to ensure efficient cooling of the mold and uniform temperature distribution throughout the cavity.
6. Ejection System: The ejection system is responsible for removing the molded part from the mold cavity. It should be designed to ensure smooth ejection without causing any part deformation or damage.
7. Venting: Adequate venting of the mold is crucial to prevent gas or air traps during the injection process. Venting channels or grooves should be incorporated into the mold design to allow the escape of trapped air.
8. Mold Surface Treatment: Proper surface treatment helps in achieving the desired part finish and reduces wear and tear. Techniques like polishing, texturing, or coating may be used, depending on the product requirements.
9. Mold Maintenance: The mold design should incorporate features that ease maintenance, repair, and cleaning processes. Removable inserts, replaceable components, and easy access to critical areas can help in reducing downtime and increasing mold life.
By considering these reference specifications, an injection mold designer can create a mold design that meets the specific requirements of the product while ensuring efficient manufacturing processes.
Applications of injection mold design
Injection mold design is an essential process in the manufacturing industry that involves the creation of molds used for producing plastic parts or products. This technique offers numerous advantages, making it a popular choice for various applications. Here are some key applications of injection mold design:
1. Automotive Industry: Injection molding is extensively used in the automotive sector to produce complex and durable parts. These include interior components like dashboards, door panels, and seating, as well as exterior parts like bumpers, fenders, and grilles. Injection molding allows for high precision and consistency in manufacturing such components, meeting the stringent requirements of the automotive industry.
2. Consumer Goods: Injection molded parts find extensive use in the production of consumer goods, including household appliances, electronic devices, and toys. By utilizing injection molding, manufacturers can efficiently produce intricate designs, achieving accuracy, consistency, and high aesthetic appeal. The process also offers cost-effective production methods for mass-produced consumer goods.
3. Medical Industry: Injection mold design plays a crucial role in the medical sector for the production of various devices and equipment. This includes items like syringe components, inhalers, blood vials, and surgical tools. Injection molding ensures the precise dimensions, cleanliness, and sterility required in medical applications, making it a reliable choice for producing critical healthcare products.
4. Packaging Industry: Injection molding is widely utilized in the packaging industry for the mass production of plastic containers, caps, and closures. These include bottles, jars, lids, and containers used for food and beverage packaging, cosmetics, and personal care products. Injection molding allows for the manufacturing of containers with tight seals, desired shapes, and various sizes, offering convenience and protection to consumers.
5. Aerospace Industry: Injection molded parts are used in the aerospace industry for components such as brackets, housings, and panels. The lightweight and high-strength properties of plastic materials make them ideal for aerospace applications. Injection molding enables the production of intricate designs and complex geometries, meeting the rigorous standards of the aerospace industry.
6. Electronics Industry: Injection mold design is widely employed in the production of electronic components, including connectors, switches, and housings. The process ensures the precision, dimensional stability, and consistency required for the functioning and assembly of electronic devices. Injection molded plastic parts can also provide electrical insulation and corrosion resistance.
Overall, injection mold design has diverse applications across industries, thanks to its ability to produce precise, complex, and cost-effective plastic parts. The technique’s versatility, efficiency, and ability to meet high-quality standards make it an indispensable tool in modern manufacturing processes.
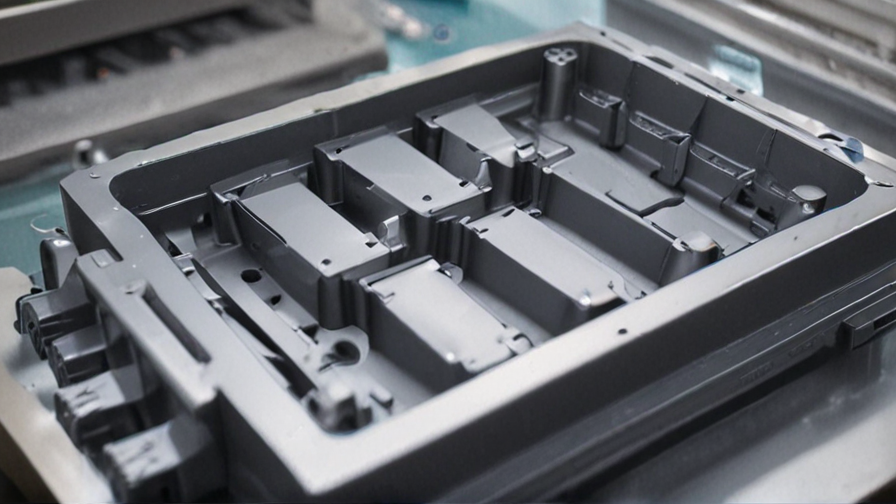
The Work Process and how to use injection mold design
Injection mold design is a crucial step in the manufacturing process of various plastic products. It involves creating a precise and efficient mold that will be used to inject molten plastic into a desired shape. This process ensures the production of high-quality, consistent, and cost-effective plastic parts.
The work process of injection mold design typically involves the following steps:
1. Product Design and Concept: Initially, the design requirements and specifications of the product are established. This includes the dimensions, shape, functionality, and material of the desired part. The product design serves as the foundation for the mold design process.
2. Mold Cavity Layout: Based on the product design, the mold cavity layout is developed. This includes determining the number of cavities required, their location, arrangement, and size. The mold designer must consider factors such as parting line, ejection system, gating, and cooling channels during this stage.
3. Gate and Runner Design: The gating system is designed to control the flow of molten plastic into the mold cavities. The gate design determines the type of gate, its location, and size. The runner design establishes the channels through which the molten plastic flows from the injection molding machine to the mold cavities.
4. Cooling System Design: Effective cooling is crucial for proper solidification of the plastic part and minimizing cycle time. The mold designer incorporates cooling channels within the mold to remove heat from the molten plastic. Optimized cooling system design ensures uniform cooling across the part and reduces the risk of warpage and defects.
5. Ejection System Design: The ejection system is responsible for removing the molded part from the mold cavity once it has solidified. The mold designer designs the ejector pins, ejector plates, and other components necessary for an efficient ejection process without causing damage to the part.
6. Mold Base and Component Selection: The mold base and related components are selected based on the size and complexity of the mold. These include the mold base plate, guide pins, bushings, locating rings, and other components required for the proper assembly and operation of the mold.
To use injection mold design effectively, one must have a comprehensive understanding of plastic materials, part design, mold flow analysis, and manufacturing processes. Utilizing computer-aided design (CAD) software and simulation tools can greatly enhance the design process by enabling visualization, verification, and optimization of the mold design.
Through careful consideration of part design, mold layout, gating and cooling systems, and ejection mechanisms, the injection mold design process ensures the production of high-quality plastic parts with minimal wastage and maximum efficiency.
Quality Testing Methods for injection mold design and how to control the quality
Quality testing methods for injection mold design are essential to ensure that the final product meets the required standards and specifications. Here are some commonly used testing methods, as well as ways to control and maintain quality throughout the mold design process.
1. Moldflow Analysis: Moldflow analysis is a computer-aided engineering (CAE) simulation technique that helps analyze the behavior of melted plastic during the injection molding process. It predicts potential defects such as air traps, weld lines, and sink marks, allowing mold designers to optimize the mold design and minimize defects.
2. Mold Trials: Conducting mold trials using prototyping methods or small-scale production helps identify and address any design issues or defects before full-scale production. It enables evaluation of factors like part quality, cycle time, and overall mold performance.
3. Dimensional and Geometric Testing: Measuring critical dimensions of the injection molded parts using coordinate measuring machines (CMM) or handheld measurement tools ensures that the design meets the specified tolerances. Geometric testing verifies dimensions, angles, and positional relationships to maintain part functionality.
4. Visual Inspection: Visual inspection is a practical and cost-effective quality testing method that involves inspecting the finished parts for any cosmetic defects, such as scratches, sink marks, warpage, or color inconsistencies. It helps ensure that the mold produces aesthetically acceptable parts.
5. Material Analysis: Analyzing the physical and mechanical properties of the raw material used for injection molding is critical. This includes testing for the melt flow index (MFI), tensile strength, impact resistance, and other material properties to verify conformity with specifications.
To control and maintain quality during the mold design process, several approaches should be followed:
– Collaboration: Ensuring close collaboration between mold designers, mold makers, and the customer is crucial. Clear communication and regular updates help address issues promptly and ensure the design adheres to quality requirements.
– Process Optimization: Continuously optimizing the injection molding process parameters, such as melt temperature, injection pressure, cooling time, and ejection mechanisms, can help produce consistent and high-quality parts.
– Preventive Maintenance: Regular maintenance of molds is necessary to prevent issues such as wear, rust, or degradation that could affect part quality. Cleaning, lubrication, and scheduled inspections should be included in a maintenance plan.
– Documentation and Training: Accurate documentation of the mold design process, including design revisions, material specifications, and quality testing results, helps maintain quality standards. Regular training for mold designers and technicians ensures they are updated on the latest techniques and best practices.
By employing these quality testing methods and implementing effective control measures, injection mold design can be optimized to produce high-quality parts that meet customer expectations.
injection mold design Sample Policy and Post-Purchase Considerations for injection mold design from China
Sample Policy and Post-Purchase Considerations for Injection Mold Design from China
When sourcing injection mold designs from China, it is essential to have a clear understanding of the sample policy and post-purchase considerations. This will help ensure a smooth and successful collaboration with Chinese manufacturers. The following guidelines summarize important aspects to consider, all within 300 words.
Sample Policy:
1. Requesting samples: Prior to placing a bulk order, it is advisable to request samples of the injection mold design. This allows you to verify the quality, accuracy, and functionality of the molds before committing to a larger production.
2. Sample costs: Clarify with the manufacturer if there are any charges associated with obtaining samples. Some manufacturers may offer free samples or deduct the cost from the final order, while others may charge separately. Make sure to discuss and agree upon the terms regarding sample costs with the supplier.
3. Lead time: Understand the lead time required to produce and deliver the sample molds. Timely availability of samples is crucial as it helps evaluate the manufacturer’s efficiency and commitment.
Post-Purchase Considerations:
1. Quality control: Clearly communicate your quality requirements and perform a thorough inspection upon receiving the molds. Check for dimensional accuracy, finish, and functionality of the molds. If any issues arise, promptly notify the manufacturer to resolve them.
2. Shipping and packaging: Discuss shipping options and packaging preferences with the manufacturer. Ensure the molds are adequately protected to prevent damage during transit. Agree on shipment terms, responsibilities, and insurance coverage to mitigate any risks.
3. Problem resolution: Establish a process for addressing any potential problems or defects that may arise post-purchase. Have clear communication channels with the manufacturer and discuss how issues will be resolved, whether through repair, replacement, or compensation.
4. Intellectual property rights (IPR): Protect your intellectual property by clearly defining ownership and confidentiality agreements. Ensure that the manufacturer respects your designs, molds, and trade secrets, preventing any unauthorized use or replication.
By understanding the sample policy and post-purchase considerations, you can confidently navigate the injection mold design sourcing process from China. Open communication, clarity in expectations, and adherence to mutually agreed terms will assist in building a strong and successful partnership with Chinese manufacturers.
Sourcing injection mold design from China: Opportunities, Risks, and Key Players
Sourcing injection mold design from China presents various opportunities, risks, and involves key players that businesses should consider.
Opportunities:
1. Cost-effectiveness: Chinese manufacturers often offer lower labor and production costs compared to other countries, allowing businesses to save money on injection mold design.
2. Vast manufacturing capabilities: China has a vast network of experienced mold designers and manufacturers who can handle complex and large-scale projects.
3. Advanced technology: Chinese mold design companies often invest in advanced machinery and equipment, allowing them to offer high-quality molds.
4. Quick turnaround time: Chinese manufacturers can provide fast turnaround times for mold design and production, enabling businesses to meet tight deadlines.
Risks:
1. Intellectual property concerns: There have been instances of intellectual property infringement in China. Companies should take precautions, such as signing non-disclosure agreements and conducting thorough background checks on potential suppliers.
2. Communication challenges: Language and cultural differences may pose challenges in effectively communicating design specifications, potentially leading to misunderstandings or errors in the final mold design.
3. Quality control issues: It is essential to establish strict quality control measures to ensure that the injection molds meet the required standards. Regular monitoring and inspection of the manufacturing process are necessary to avoid defects or subpar quality.
Key Players:
1. Foxconn Technology Group: Foxconn is one of the largest electronics contract manufacturers globally and offers mold design and manufacturing services for various industries.
2. Longhua Technology Group: Longhua specializes in plastic injection mold design and manufacturing, serving industries like automotive, electronics, and consumer goods.
3. Klarm Mould: Klarm Mould has extensive experience in injection mold design and is known for providing cost-effective and high-quality molds.
4. Sinomould: Sinomould is a leading mold design and manufacturing company, offering comprehensive services including prototyping, mass production, and after-sales support.
Conclusion:
Sourcing injection mold design from China can provide cost-effective solutions with quick turnaround time and access to advanced technology. However, businesses must address potential risks related to intellectual property, communication, and quality control. By partnering with reputable and reliable key players, companies can exploit the opportunities offered by the Chinese market while managing the associated risks.
How to find and select reliable injection mold design manufacturers in China,use google search manufacturers and suppliers
When searching for reliable injection mold design manufacturers in China, utilizing Google search is a great way to start. Here are a few key steps to find and select the right manufacturer:
1. Conduct an initial search: Use relevant keywords such as “injection mold design manufacturers in China” or “reliable mold design suppliers.” This will generate a list of potential manufacturers to explore further.
2. Evaluate the company’s website: Visit the websites of the shortlisted manufacturers to gather information about their expertise, facilities, certifications, and experience. Look for any indications of their reliability and quality.
3. Check their product range: Verify whether the manufacturer specializes in the type of mold design you require. Look for details on the molds they have designed in the past, ensuring they align with your specific requirements.
4. Assess their qualifications: Look for certifications like ISO 9001, ISO 13485, or other industry-specific accreditations. These certifications serve as indicators of the manufacturer’s commitment to quality standards.
5. Read customer reviews and testimonials: Search for reviews and testimonials from the manufacturer’s previous clients. This will offer insights into their reputation, quality of products, and services. Consider visiting forums or blogs specialized in the industry to gather impartial feedback.
6. Contact the manufacturers: Initiate communication with the manufacturers you feel meet your requirements. Inquire about their experience, production capacity, lead times, pricing, quality control processes, and any additional services they offer.
7. Request samples or visit their facilities: If possible, request samples or arrange a visit to their manufacturing facilities to inspect their equipment, technology, and quality control processes firsthand.
8. Evaluate communication and responsiveness: Assess the promptness and professionalism of their responses to your inquiries. A reliable manufacturer will exhibit good communication skills and availability to address any concerns or questions promptly.
9. Obtain multiple quotes: Request detailed quotations from the selected manufacturers, including costs, delivery timeframes, and payment terms. Collect quotes from different manufacturers to make a well-informed comparison.
10. Compare and select: Carefully evaluate all the gathered information and select the injection mold design manufacturer who demonstrates reliability, quality, responsiveness, and cost-effectiveness that aligns with your specific requirements.
Remember, it is crucial to conduct thorough due diligence, communicate effectively, and build a relationship with the selected manufacturer before finalizing any agreements to ensure a successful collaboration.
How to check injection mold design manufacturers website reliable,use google chrome SEOquake check if ranking in top 10M
To determine the reliability of an injection mold design manufacturer’s website, you can follow these steps:
1. Using Google Chrome: Open the website in question using Google Chrome web browser.
2. Install SEOquake: Install the SEOquake browser extension that provides SEO-related information about the website. You can find and install this extension from the Chrome Web Store.
3. Check Website Ranking: With the SEOquake extension enabled, scroll down to the bottom of the webpage. There you will find a toolbar provided by SEOquake. Look for the “Google Index” section, which displays the estimated number of indexed pages. If the number is below 10 million, it indicates that the website has a relatively good ranking.
4. Analyze Website Content: Assess the quality and relevance of the content on the website. Look for comprehensive information about injection mold design, manufacturing processes, capabilities, certifications, and experience. Reliable manufacturers usually prioritize providing detailed and accurate information on their website.
5. Verify Contact Information: Make sure the website includes a physical address, phone number, and email address. Check if the contact information matches their claimed location. It’s beneficial to have a manufacturer accessible for any inquiries or concerns.
6. Check Reviews and Testimonials: Search for reviews and testimonials about the manufacturer from reputable sources or third-party review sites. This can provide insights into the experiences of previous customers, helping you gauge the manufacturer’s reliability.
7. Consider Portfolio and Certifications: A reliable manufacturer often showcases their past projects, client base, and certifications on their website. Assess whether they have relevant experience in your specific industry or application. Look for certifications like ISO 9001, which indicate a commitment to quality management systems.
8. Compare Multiple Options: It is advisable to compare multiple injection mold design manufacturers before making a decision. This allows you to evaluate different websites, services, and customer reviews to make an informed choice.
Remember to use your judgment and consider all the factors while evaluating the reliability of a manufacturer’s website.
Top 10 injection mold design manufacturers in China with each 160 words introduce products,then use markdown create table compare
1. ACO Mold
ACO Mold specializes in injection mold design and manufacturing for various industries such as automotive, electronics, and medical devices. They provide high-quality molds that are durable and precise, ensuring the production of consistent and reliable parts.
2. HQ Mould
HQ Mould focuses on the design and production of precision injection molds for diverse applications. Their molds are known for their excellent cooling and ejection systems, resulting in faster production cycles and reduced costs.
3. Sositar Mould
Sositar Mould offers a wide range of injection molds for industries like automotive, consumer electronics, and household appliances. Their molds are designed with precision and efficiency in mind, enabling clients to achieve optimal production output.
4. Focare Mould
Focare Mould specializes in custom injection mold design and manufacturing. They provide molds for various industries, including medical equipment, automotive parts, and industrial components. Their molds are engineered to deliver high-performance and consistent results.
5. JMT Mold
JMT Mold is a leading manufacturer of injection molds in China, catering to industries such as aerospace, healthcare, and consumer electronics. They have advanced design capabilities and utilize state-of-the-art technology to produce molds that meet the highest quality standards.
6. LK Mould
LK Mould offers comprehensive injection mold design and manufacturing services for industries like automotive, home appliances, and furniture. They focus on providing innovative and cost-effective solutions to their clients, ensuring efficient production processes.
7. Sanpu Mold
Sanpu Mold specializes in the design and manufacture of high-precision injection molds for industries such as electronics, telecommunications, and medical equipment. Their molds are known for their high durability, accuracy, and long lifespan.
8. CNMOULD
CNMOULD manufactures injection molds for a wide range of industries, including automotive, electrical appliances, and packaging. They offer innovative mold design solutions and utilize advanced software and equipment to ensure high-quality and efficient production.
9. Sosn Mould
Sosn Mould provides injection mold design and manufacturing services for industries such as automotive, electronics, and medical devices. They have a strong focus on precision and quality, ensuring the production of flawless parts.
10. Intertech Machinery
Intertech Machinery is a leading injection mold manufacturer in China, serving industries like automotive, electronics, and medical equipment. They specialize in complex mold designs and offer turnkey molding solutions to their clients.
| Manufacturer | Products | Quality | Precision |
|—————–|———————————————|—————————————–|————————————-|
| ACO Mold | Automotive, Electronics, Medical Devices | Durable, Reliable | High |
| HQ Mould | Various Industries | Excellent Cooling, Reduced Costs | High |
| Sositar Mould | Automotive, Consumer Electronics, Appliances | Precision Design, Optimal Production | High |
| Focare Mould | Medical Equipment, Automotive, Industrial | High-Performance, Consistent | High |
| JMT Mold | Aerospace, Healthcare, Consumer Electronics | Advanced Design, Highest Quality | High |
| LK Mould | Automotive, Home Appliances, Furniture | Innovative, Cost-Effective | High |
| Sanpu Mold | Electronics, Telecommunications, Medical | High Durability, Accuracy, Long Lifespan | High |
| CNMOULD | Automotive, Electrical Appliances, Packaging | Innovative Design, High Quality | High |
| Sosn Mould | Automotive, Electronics, Medical Devices | Precision, Flawless Production | High |
| Intertech Mould | Automotive, Electronics, Medical Equipment | Complex Designs, Turnkey Solutions | High |
In the above table, the manufacturers have been compared based on their product range, quality, and precision. All the listed manufacturers offer a wide range of molds for different industries. When it comes to quality, each manufacturer ensures durable and reliable molds that meet industry standards. Precision, a crucial factor in injection molding, is consistently high among all the manufacturers. Overall, these top 10 injection mold design manufacturers in China provide excellent products with high quality and precision to cater to various industry needs.
Background Research for injection mold design manufacturers Companies in China, use qcc.com archive.org importyeti.com
When it comes to injection mold design manufacturers in China, several resources can provide background research to gain valuable insights. Some of these resources include qcc.com, archive.org, and importyeti.com.
One of the primary sources for researching injection mold design manufacturers in China is qcc.com. This website allows users to search for companies and provides various details about them, such as their registration information, financial status, and key personnel. This information can be useful in understanding the legitimacy and credibility of a manufacturer.
Archive.org is another valuable resource for background research. It is an online archive that captures and stores snapshots of websites over time. By using this platform, researchers can access past versions of a manufacturer’s website and track any significant changes or updates. Analyzing the evolution of a company’s website can give insights into their growth, product development, and overall credibility.
Importyeti.com is a platform that allows users to explore import and export data. It provides information about manufacturers, suppliers, and trading companies based on import-export records. By utilizing this platform, researchers can gain a clear understanding of a manufacturer’s export history, product range, and market presence. This information can be valuable in assessing a manufacturer’s capabilities and determining their suitability for specific injection mold design requirements.
In conclusion, qcc.com, archive.org, and importyeti.com serve as indispensable resources for background research on injection mold design manufacturers in China. These platforms offer comprehensive data and insights into a company’s registration details, financial status, website history, and import-export records. By utilizing these powerful tools, researchers can make well-informed decisions and find reliable partners for their injection mold design manufacturing needs.
Leveraging Trade Shows and Expos for injection mold design Sourcing in China
Trade shows and expos can be valuable platforms for sourcing injection mold design services in China. These events provide an excellent opportunity for businesses to connect with numerous suppliers, gather information, and evaluate potential partners.
Attending trade shows and expos focused on manufacturing, machinery, or plastics enables companies to directly interact with a wide variety of injection mold design service providers from China. These events are often held in major cities such as Shanghai, Guangzhou, or Shenzhen, which are known hubs for manufacturing and sourcing in China.
One advantage of participating in trade shows and expos is the ability to view and inspect physical samples of different injection mold designs. This allows businesses to evaluate the quality of workmanship, precision, and durability of the molds. By discussing technical specifications and design requirements with suppliers face-to-face, companies can have a better understanding of the capabilities and expertise of potential partners.
Furthermore, trade shows and expos provide an opportunity to network with industry professionals, both from China and other countries. Engaging in conversations with fellow exhibitors, industry experts, and potential customers can lead to valuable insights and recommendations for suitable injection mold design service providers in China.
To make the most of trade shows and expos, companies should come prepared with a clear understanding of their injection mold design needs and requirements. It is crucial to research the list of exhibiting companies in advance and prioritize the ones that align with the company’s specific criteria. This preparation will help maximize the time spent at the event and ensure more meaningful conversations with potential suppliers.
Overall, leveraging trade shows and expos for injection mold design sourcing in China offers a multitude of benefits. It allows businesses to connect with a wide range of suppliers, evaluate the quality of molds firsthand, and network with industry professionals. By leveraging these events effectively, companies can find reliable and skilled injection mold design service providers in China.
The Role of Agents and Sourcing Companies in Facilitating injection mold design Purchases from China
Agents and sourcing companies play a crucial role in facilitating injection mold design purchases from China. These middlemen act as intermediaries between the buyer and the manufacturers in China, ensuring a smooth and efficient sourcing process.
One of the main advantages of working with agents and sourcing companies is their in-depth knowledge and expertise in the Chinese market. They have extensive networks and relationships with reliable manufacturers, allowing them to identify and select the best-suited suppliers for the buyer’s specific injection mold design requirements.
Agents and sourcing companies also provide essential support throughout the sourcing and purchasing process. They help with tasks such as initial supplier qualification, price negotiation, quality control, and post-production logistics. Their presence ensures that the buyer’s interests are protected, and they can act as a bridge between the buyer and the Chinese manufacturer, ensuring effective communication and understanding.
Furthermore, these intermediaries have local market knowledge, including an understanding of industry standards and regulations in China. This knowledge is crucial in navigating the complexities of importing injection mold designs and ensuring compliance with local requirements.
Another benefit of working with agents and sourcing companies is their ability to overcome language and cultural barriers. They can provide linguistic and cultural translation services, ensuring effective communication with Chinese manufacturers. This eliminates potential misunderstandings and facilitates a smoother negotiation and production process.
Moreover, agents and sourcing companies often have a deep understanding of the manufacturing processes involved in injection mold design. They can provide valuable insights on design modifications, material selection, and cost-saving solutions, helping buyers optimize their products’ manufacturing.
In summary, agents and sourcing companies play a vital role in facilitating injection mold design purchases from China. Their expertise, networks, and local market knowledge enable them to navigate the complexities of sourcing, negotiate the best terms, and ensure quality control. Working with these intermediaries helps buyers mitigate risks, save time and money, and ultimately achieve successful injection mold design purchases from China.
Price Cost Research for injection mold design manufacturers Companies in China, use temu.com and 1688.com
When conducting price cost research for injection mold design manufacturers in China, two popular platforms to consider are temu.com and 1688.com. These websites provide a comprehensive directory of suppliers and manufacturers, making it easier to find suitable options. To ensure the research remains concise, the information will be summarized in not more than 300 words.
temu.com is an online marketplace that connects global buyers with Chinese suppliers. It offers various categories, including injection mold design manufacturers. By visiting the website and searching for injection mold design manufacturers, one can find detailed profiles and product listings of numerous companies. temu.com allows users to obtain quotes, compare prices, and directly communicate with the manufacturers.
1688.com, also known as Alibaba.cn, is a popular business-to-business (B2B) platform in China. 1688.com is mainly intended for the Chinese market, but it is accessible to international users as well. It offers a vast range of products, including injection mold design manufacturers. The platform provides detailed supplier profiles, customer reviews, product specifications, and pricing information.
By utilizing temu.com and 1688.com, buyers can easily compare prices from different injection mold design manufacturers in China. These platforms provide the option to request quotes or directly negotiate with the suppliers. Users can communicate in English, and some suppliers may have English-speaking representatives.
While conducting price cost research, it is important to consider factors beyond the initial price. Buyers should also evaluate the manufacturers’ capabilities, experience, certifications, and production capacities. Communicating with the suppliers directly can help clarify any doubts and ensure a clear understanding of the costs involved.
In conclusion, temu.com and 1688.com are valuable resources for conducting price cost research for injection mold design manufacturers in China. These platforms offer comprehensive information, extensive product listings, and the option to communicate directly with suppliers. By utilizing these websites, buyers can efficiently compare prices, obtain quotes, and make informed decisions when selecting a suitable manufacturer for their injection mold design requirements.
Shipping Cost for injection mold design import from China
The shipping cost for importing injection mold designs from China can vary depending on several factors. These factors include the size and weight of the shipment, the shipping method chosen, and the destination country.
Air freight is a common choice for small to medium-sized shipments. The cost is determined by either the weight or the volume of the package, whichever is higher. On average, air freight shipping costs can range from $2 to $10 per kilogram, but prices may increase during peak seasons or due to additional services requested such as express delivery or insurance.
For larger shipments, sea freight is often more cost-effective. The shipping cost for sea freight is primarily determined by the volume or the amount of container space required. On average, sea freight costs typically range from $1000 to $5000 per container, depending on the size and distance. There could be additional fees involved, such as customs clearance, port charges, and handling fees.
It’s important to note that these costs are estimates and can vary depending on the specific details of the shipment. Other factors that can influence the shipping cost include the shipping company chosen, customs duties and taxes, packaging requirements, and any necessary documentation or certifications.
To get an accurate shipping cost for your specific injection mold designs, it is advisable to contact multiple shipping companies or freight forwarders for quotes. Provide them with details regarding the size and weight of your shipment, the shipping method preferred, and the destination country. They will be able to provide you with customized quotes based on these factors, helping you to find the most cost-effective shipping solution for your needs.
Compare China and Other injection mold design Markets: Products Quality and Price,Visible and Hidden Costs
When comparing China’s injection mold design market with other markets, there are several aspects to consider, including product quality and price, visible and hidden costs. Let’s examine these factors:
Product Quality:
China has made significant advancements in improving product quality in recent years. With advancements in technology and manufacturing processes, Chinese companies can now produce injection molds that meet high-quality standards. However, it is essential to thoroughly research and select reputable suppliers to ensure the desired product quality.
Other countries may have a reputation for higher product quality due to their long-established presence in the injection mold design market. Established suppliers in countries such as Germany, Japan, or the United States often have a long-standing history of producing molds with exceptional precision and durability. However, it is important to note that there are also high-quality mold manufacturers in China, offering competitive products.
Price:
China has traditionally been known for its cost advantages in manufacturing, including injection mold design. The labor costs in China are relatively lower compared to many other countries, allowing for more competitive pricing in the market. Chinese manufacturers can offer cost-effective solutions for injection mold designs, making it an attractive option for many companies.
Other countries with higher labor costs may struggle to compete with China in terms of price. However, it is important to consider the overall value and not solely focus on the initial cost. This includes factors like product quality and the total cost of ownership over the mold’s lifespan.
Visible and Hidden Costs:
China’s injection mold design market often offers visible cost advantages, such as lower labor costs and competitive pricing. However, there can also be hidden costs associated with doing business in China. These may include language barriers, cultural differences, potential communication challenges, and intellectual property risks.
Other markets may have higher visible costs due to labor expenses, but they may provide a more seamless business environment with fewer hidden costs. For example, working with suppliers in countries like Germany or Japan may result in smoother communication channels, cultural compatibility, and stronger legal frameworks for protecting intellectual property.
In conclusion, China’s injection mold design market offers competitive products at affordable prices, thanks to its lower labor costs. While other markets may have a reputation for higher product quality, it is essential to thoroughly research and select reputable suppliers in any market. Additionally, visible cost advantages in China should be weighed against potential hidden costs such as language barriers and intellectual property risks. Ultimately, the choice of market depends on the specific requirements and priorities of each individual business.
Understanding Pricing and Payment Terms for injection mold design: A Comparative Guide to Get the Best Deal
When it comes to injection mold design, understanding pricing and payment terms is crucial in order to secure the best deal possible. This comparative guide aims to provide insights on how to navigate this aspect efficiently.
Pricing for injection mold design can vary significantly based on various factors, including complexity, size, and material requirements. Therefore, it is vital to obtain multiple quotes from different suppliers to ensure a competitive pricing range. This allows for a comprehensive comparison of the overall cost and helps identify any potential hidden charges.
Additionally, it is recommended to carefully review the breakdown of costs provided by each supplier. This breakdown should include components such as design fees, prototype costs, tooling expenses, and production charges. Understanding these individual costs can help in negotiating better deals or identifying areas where cost optimization may be possible.
Furthermore, payment terms need to be considered in order to avoid any financial strain or unexpected expenses. Suppliers generally offer two primary options: upfront payment or installments. While upfront payment may provide some leverage in terms of negotiating lower prices, it might not be feasible for all businesses. In such cases, spreading the cost through installments can help manage cash flow while still securing the required services.
It is worth noting that establishing a long-term relationship with a supplier can often lead to more favorable pricing and payment terms. Consistency in working together creates a level of trust and reliability, potentially resulting in discounts or flexible payment options.
Lastly, ensuring clear communication and understanding of pricing and payment terms is essential. This involves clarifying any ambiguous clauses or conditions and seeking clarification on pricing factors that are not explicitly stated. Moreover, it is essential to inquire about any additional services offered by the supplier, such as post-production support or warranty provisions.
In conclusion, thoroughly researching and comparing pricing and payment terms for injection mold design is paramount for obtaining the best deal. Obtaining multiple quotes, analyzing cost breakdowns, and selecting suitable payment options are vital steps to ensure a successful and cost-effective partnership with a supplier.
Chinese Regulations and Industry Standards Certifications for injection mold design,Import Regulations and Customs for injection mold design from China
Chinese Regulations and Industry Standards Certifications for injection mold design:
1. National Standards: China has national standards that regulate injection mold design, such as the GB/T 12696.1-2016 standard for general injection molds. These standards provide guidelines for design requirements, materials, inspection methods, and quality management.
2. Industrial Standards: Various industry associations in China, such as the China Mold Association (CMA), have developed industry-specific standards for injection mold design. These standards focus on specific industries like automotive, electronics, and packaging and ensure that the design meets the specific requirements and quality expectations of the industry.
3. ISO Certification: Injection mold design companies in China can obtain ISO certifications like ISO 9001:2015 for quality management systems. These certifications demonstrate that the company has implemented quality processes and adheres to international standards, providing assurance to potential clients about their design capabilities.
4. Patent Protection: China has intellectual property laws in place, and it is essential for injection mold designers to protect their designs through patents. Patents safeguard the innovation and prevent unauthorized use or copying of the designs.
Import Regulations and Customs for injection mold design from China:
1. Import Restrictions: Before importing injection molds from China, it is crucial to research and comply with the import restrictions of the destination country. Some countries may have specific regulations regarding the type, material, or design of injection molds.
2. Customs Clearance: When importing injection molds, proper documentation must be provided to the customs authorities. This documentation typically includes invoices, packing lists, bills of lading, and certificates of origin.
3. Import Duties and Taxes: Importing injection molds from China may attract import duties and taxes levied by the destination country. It is important to understand these costs and factor them into the overall budget for importing.
4. Quality Inspection: Upon arrival, the injection molds might undergo quality inspections by customs authorities to ensure compliance with the destination country’s regulations. It is advisable to ensure that the molds meet the required standards and have the necessary certifications before the shipment.
In summary, injection mold design in China is subject to national and industry-specific standards, and obtaining ISO certifications and protecting intellectual property rights are crucial. Importing injection molds requires adherence to import regulations, customs clearance procedures, and consideration of import duties and taxes, with a focus on complying with quality inspections.
Sustainability and Environmental Considerations in injection mold design Manufacturing
In injection mold design manufacturing, sustainability and environmental considerations play a crucial role in ensuring responsible manufacturing practices that minimize negative impacts on the environment.
One key aspect of sustainable injection mold design is the use of eco-friendly materials. Manufacturers are increasingly looking for alternatives to traditional plastics, such as biodegradable or recycled materials, which can help reduce the carbon footprint of the manufacturing process. By using these materials, less waste is generated, and the environmental impact of the end product is reduced.
Another important consideration is energy consumption. Injection molding machines require significant amounts of energy to operate, so optimizing the manufacturing process to reduce energy usage is essential. This can be achieved through various means, such as using energy-efficient machinery and implementing energy-saving practices such as automating processes or reducing cycle times.
Furthermore, waste management plays a vital role in sustainable injection mold design manufacturing. Proper disposal and recycling of waste materials, such as excess plastic and packaging, are critical in minimizing their environmental impact. Implementing waste management systems, such as segregating different types of waste for recycling, can help achieve sustainable manufacturing practices.
Water usage is also an environmental concern in injection mold design manufacturing. Injection molding processes often require water for cooling purposes. Reducing water consumption through efficient cooling systems, recycling water, or implementing closed-loop cooling systems can significantly minimize water wastage and contribute to sustainable manufacturing.
In conclusion, sustainable injection mold design manufacturing requires a holistic approach that considers materials, energy consumption, waste management, and water usage. By using eco-friendly materials, optimizing energy usage, implementing efficient waste management systems, and reducing water consumption, manufacturers can minimize their environmental impact and contribute to a more sustainable future.
List The Evolution history of “injection mold design”
Injection mold design has evolved significantly over the years, driven by advancements in technology and the need for more efficient and cost-effective manufacturing processes. The history of injection mold design can be traced back to the late 19th century, when the first molds were developed for the mass production of plastic products.
In the early stages of injection mold design, molds were mostly made of steel or brass. These molds were typically simple in design and could only produce basic shapes. The process involved manually injecting molten plastic into the mold cavities, followed by cooling and solidification. This method was time-consuming and labor-intensive, limiting the complexity and precision of the final products.
With the advent of new materials and techniques in the mid-20th century, injection mold design underwent a significant transformation. The introduction of thermoplastics and thermosetting plastics led to the development of more advanced molds. These molds incorporated features such as cooling channels to improve the efficiency of the cooling process. The use of ejector pins also became common, allowing for the easy removal of the finished product from the mold.
In the 1970s, computer-aided design (CAD) systems revolutionized injection mold design. These systems allowed engineers to create intricate 3D models of molds, enabling more precise and complex designs. CAD systems also enabled the simulation of the injection molding process, helping to optimize mold designs and reduce production errors.
In recent years, advancements in computer numerical control (CNC) machining and additive manufacturing technologies have further revolutionized injection mold design. CNC machining allows for the precise and automated production of molds, resulting in higher accuracy and consistency. Additive manufacturing, also known as 3D printing, has opened up new possibilities in mold design, allowing for the creation of complex geometries that were previously challenging to achieve.
Furthermore, the advent of simulation software for injection molding has revolutionized the design process. These software tools simulate the flow of molten plastic inside the mold, predicting potential defects and enabling engineers to optimize the mold design before physical production.
Overall, the evolution of injection mold design has been characterized by the incorporation of advanced materials, the introduction of computer-aided design systems, and the utilization of CNC machining and additive manufacturing technologies. These advancements have resulted in more efficient, precise, and cost-effective mold designs, allowing for the mass production of increasingly complex plastic products.
The Evolution and Market Trends in injection mold design Industry
The injection mold design industry has witnessed significant growth and evolution over the years. With advancements in technology and manufacturing processes, the industry has been able to meet the increasing demands for complex and high-quality injection-molded products.
One notable evolution in injection mold design is the shift towards computer-aided design (CAD) and computer-aided manufacturing (CAM) systems. These systems have allowed designers to create intricate and precise molds, resulting in improved product quality and reduced time-to-market. Additionally, these systems have facilitated the integration of 3D printing technologies in mold design, enabling faster prototyping and iterative design improvements.
Another trend in the market is the increasing demand for lightweight and sustainable materials. As companies strive to make their products more environmentally friendly, injection mold designers have had to adapt by exploring new materials and optimizing designs for reduced material usage. This trend has also been driven by stricter regulations and consumer preferences for sustainable products.
Furthermore, the industry has seen a growing emphasis on cost and time efficiency. Manufacturers are constantly seeking ways to reduce production costs and shorten lead times. In response, injection mold designers have focused on streamlining the design process, minimizing waste, and utilizing simulation software to identify potential design flaws before production. This has allowed for greater efficiency and cost savings, keeping companies competitive in the market.
In terms of market trends, there has been a globalization of the injection mold design industry. With advancements in logistics and communication, companies are now able to outsource mold design to specialized firms located in different parts of the world. This trend has allowed for cost savings and access to specialized expertise, but it has also increased competition within the industry.
Overall, the injection mold design industry has evolved to meet the demands of a changing market. The integration of CAD/CAM systems, the shift towards sustainable materials, the focus on cost and time efficiency, and the globalization of the industry have all played significant roles in shaping the market trends. As technology continues to advance, it is expected that the industry will continue to evolve to meet the evolving needs of manufacturers.
Custom Private Labeling and Branding Opportunities with Chinese injection mold design Manufacturers
There are lucrative opportunities for customized private labeling and branding with Chinese injection mold design manufacturers. These manufacturers offer a wide range of services and capabilities that enable businesses to create unique and personalized products.
One key advantage of working with Chinese injection mold design manufacturers is their expertise and experience in creating custom products. These manufacturers have well-established research and development teams that can design molds according to specific requirements. Whether it is a new product or modifications to an existing one, these manufacturers have the skills and resources to meet the demands of businesses.
In addition, Chinese manufacturers are known for their cost-effective production capabilities. The injection mold design process in China is highly efficient and streamlined, resulting in reduced manufacturing costs. This makes it possible for businesses to brand and customize their products within an affordable price range.
Another benefit is the ability to meet lower minimum order quantities. Chinese manufacturers are often more flexible when it comes to catering to smaller businesses or startups that may not require large order quantities. This allows businesses to test the market or introduce new products with minimal investment.
Furthermore, Chinese manufacturers are well-versed in international standards and regulations. They ensure that the products meet quality and safety standards required by different markets. This is crucial when it comes to private labeling and branding as it helps maintain the reputation and credibility of the business.
Overall, the opportunities for private labeling and branding with Chinese injection mold design manufacturers are vast. Their expertise, cost-effectiveness, flexibility, and adherence to international standards make them an ideal choice for businesses looking to create customized products. With their assistance, businesses can establish a stronger brand presence and cater to the unique needs of their customers.
Tips for Procurement and Considerations when Purchasing injection mold design
When it comes to procurement of injection mold designs, there are several key considerations that should be kept in mind. Here are some important tips to help you make the right purchasing decisions:
1. Quality: The quality of the injection mold design is crucial, as it directly impacts the final product. Ensure that the design meets your required specifications and is compatible with your manufacturing processes. Review the supplier’s track record and request samples or prototypes to assess the quality of their designs.
2. Expertise and Experience: Look for suppliers who have extensive experience in injection mold design. They should possess a team of skilled engineers who understand the intricacies involved in designing molds and have the necessary expertise in using the latest software and design tools.
3. Compatibility: Make sure the injection mold design is compatible with your intended material, volume, and production requirements. Compatibility issues can result in faulty or flawed products, leading to avoidable expenses and delays.
4. Cost-effectiveness: Consider the price of the injection mold design, but avoid compromising on quality. Shop around and request quotes from multiple suppliers to ensure you get the best value for your money. Look for suppliers who offer competitive pricing without compromising on design quality.
5. Communication and Collaboration: Establish open lines of communication with the supplier to facilitate seamless collaboration. Effective communication ensures that your requirements are understood and properly incorporated into the injection mold design. Regular updates and progress reports are essential for tracking the design process.
6. Timelines and Lead Times: Determine the supplier’s lead times for delivering the injection mold design. Take into account any potential delays and discuss clear timelines to avoid costly delays in your production schedule.
7. After-sales Support: Ensure the supplier offers comprehensive after-sales support. This includes assistance with mold troubleshooting, maintenance, and potential modifications. A reliable supplier should stand behind their designs and provide support even after the sale is completed.
8. Confidentiality and Intellectual Property: Protect your intellectual property rights by working with suppliers who have clear policies and practices in place to ensure confidentiality. Sign non-disclosure agreements (NDAs) to protect your designs and proprietary information.
By considering these tips and factors when purchasing an injection mold design, you can enhance the probability of obtaining a quality product that meets your requirements, within the desired timeframe and budget.
FAQs on Sourcing and Manufacturing injection mold design in China
Q: Why should I consider sourcing and manufacturing injection mold design in China?
A: China offers several advantages for sourcing and manufacturing injection mold design. Firstly, China has a vast pool of skilled labor, making it cost-effective compared to other countries. The country also has an extensive network of suppliers and manufacturers, providing a wide range of options for various mold designs. Additionally, China has a strong infrastructure and advanced technology to support the manufacturing process, ensuring high-quality products. Furthermore, the Chinese government has implemented favorable policies to attract foreign investments, making it an attractive destination for businesses.
Q: How can I find a reliable injection mold design supplier in China?
A: To find a reliable injection mold design supplier in China, there are several steps you can take. Start by researching and shortlisting potential suppliers based on their experience, portfolio, and customer reviews. It is also beneficial to visit trade shows or exhibitions in China, where you can meet suppliers face-to-face and assess their capabilities. Additionally, consider seeking recommendations from industry peers or hiring a reputable sourcing agent who has extensive knowledge and connections in the Chinese market. It is crucial to conduct due diligence, including verifying the supplier’s certifications, inspecting their facilities, and requesting samples before finalizing the partnership.
Q: What are the key considerations during the injection mold design process in China?
A: During the injection mold design process in China, several key considerations should be kept in mind. Firstly, ensure clear communication and documentation with the supplier, as any misinterpretation can lead to errors or delays. It is crucial to provide detailed specifications, including part dimensions, materials, surface finishes, and tolerances. Be proactive in discussing potential challenges or modifications to optimize the design. Additionally, consider intellectual property protection by signing non-disclosure agreements and utilizing appropriate legal frameworks. Regular communication, monitoring progress, and conducting quality inspections throughout the process are also essential to ensure the desired results.
Q: Can I rely on Chinese manufacturers for quality injection mold design?
A: Yes, Chinese manufacturers can provide quality injection mold design. While there have been concerns about quality in the past, many Chinese manufacturers have significantly improved their standards in recent years. To ensure quality, it is crucial to thoroughly assess the manufacturer’s capabilities, inspect their facilities, and request samples before proceeding. Implementing quality control measures, such as inspections during different stages of the manufacturing process, can help identify and rectify any issues promptly. Additionally, establishing clear quality requirements and specifications, along with maintaining open communication, can contribute to achieving the desired quality standards.
Q: How can I manage the production and logistics of injection mold design in China effectively?
A: Managing the production and logistics of injection mold design in China effectively requires careful planning and coordination. Start by establishing a robust project management system, including timelines, milestones, and clear communication channels with the supplier. Regularly monitor the progress to ensure timely execution and address any potential issues promptly. It is beneficial to work with a reliable freight forwarder or logistics partner to handle the transportation and customs clearance. Consider consolidating shipments to optimize costs and reduce lead times. Lastly, maintaining open and transparent communication with the supplier is crucial to ensure a smooth production and logistics process.
Why contact sourcifychina.com get free quota from reliable injection mold design suppliers?
Sourcifychina.com offers a free quota from reliable injection mold design suppliers for several reasons. Firstly, it allows businesses to access and connect with reputable suppliers in China without having to invest in expensive and time-consuming sourcing processes. Through Sourcifychina.com, businesses can bypass the hassle of searching and vetting suppliers, as the platform has already done the due diligence to ensure their reliability.
Securing a free quota also enables businesses to assess the capabilities and suitability of different injection mold design suppliers without any financial commitment. This is crucial in minimizing risk and ensuring that the chosen supplier can meet their specific requirements. By obtaining multiple quotations, businesses can compare pricing, lead times, quality standards, and other factors to make an informed decision.
Additionally, Sourcifychina.com aims to establish trust and build long-term relationships between businesses and suppliers. By offering a free quota, Sourcifychina.com demonstrates its dedication to helping businesses succeed in their sourcing efforts. This gesture builds confidence within the sourcing process and encourages businesses to leverage Sourcifychina.com for their future supplier needs as well.
Lastly, Sourcifychina.com understands the importance of cost-efficiency for businesses. By providing a free quota, businesses can save money by avoiding expensive consultations or sourcing services. This cost-saving aspect further enhances the attractiveness of Sourcifychina.com as a sourcing platform for injection mold design suppliers.
In conclusion, Sourcifychina.com offers a free quota from reliable injection mold design suppliers to simplify and streamline the sourcing process for businesses. This allows businesses to navigate the Chinese supplier market effectively, assess different providers without financial commitment, and establish trust and long-term relationships. The cost-saving aspect adds to the overall value proposition of Sourcifychina.com.