Introduce about injection molding silicone guide,Qulity,Cost,Supplier,Certification,Market,Tips,FAQ
Injection molding silicone is a highly versatile and efficient manufacturing process used to produce a wide range of silicone-based products. This guide provides an overview of the key aspects related to injection molding silicone, including quality, cost, suppliers, certifications, market trends, tips, and frequently asked questions.
Quality plays a crucial role in injection molding silicone products. High-quality silicone materials ensure durability, flexibility, and resistance to heat, chemicals, and abrasion. Additionally, precise injection molding techniques, such as controlling temperature and pressure, result in products with excellent dimensional accuracy and consistency.
In terms of cost, injection molding silicone can be a cost-effective option for large-scale production due to its high production rate and repeatability. Efficient utilization of raw materials and reduced labor costs also contribute to cost savings. However, small-scale production runs may incur higher initial costs.
Choosing a reliable silicone injection molding supplier is vital to ensure the quality of the final products. Supplier selection should be based on their expertise, track record, production capabilities, and the ability to meet specific requirements. Assessing their equipment, quality control processes, and adherence to industry standards is essential.
Certifications, such as ISO 9001, are crucial for ensuring compliance with quality management systems. Additionally, suppliers with ISO 13485 certification demonstrate adherence to standards specifically designed for medical devices. Customers should prioritize partnering with certified suppliers to guarantee the highest quality standards.
The market for injection molding silicone is witnessing significant growth due to increasing demand in various industries, including automotive, consumer goods, healthcare, and electronics. Silicone’s unique properties, such as high temperature resistance and biocompatibility, make it a popular choice for manufacturing diverse products.
Here are some useful tips when dealing with injection molding silicone:
1. Carefully choose the right silicone material for your specific application.
2. Optimize design features to maximize the efficiency of the injection molding process.
3. Ensure proper maintenance and inspection of molds to avoid defects and prolong their lifespan.
4. Conduct thorough quality control testing to ensure the desired product characteristics.
Frequently Asked Questions:
1. What are the advantages of injection molding silicone over other molding processes?
2. How can I estimate the cost of injection molding silicone products?
3. What are the typical lead times for injection molding silicone production?
4. Can injection molding silicone be used for food-contact applications?
5. What are the limitations of silicone injection molding?
In conclusion, injection molding silicone offers versatility, cost-effectiveness, and high-quality end products. Choosing experienced suppliers and ensuring certifications are essential steps in utilizing this manufacturing process successfully. By considering these factors, businesses can capitalize on the growing market demand for silicone products.
Types of injection molding silicone
Injection molding is a popular manufacturing process used to produce a wide range of products, including silicone parts. Silicone, a versatile material known for its durability and flexibility, can be injected into molds to create various shapes and forms. Different types of silicone can be used in injection molding, each offering unique properties and advantages.
1. High Consistency Rubber (HCR): HCR silicone, also known as solid silicone, is a commonly used material in injection molding. It is a high-viscosity rubber that can be processed at room temperature, making it suitable for complex and intricate designs. HCR silicone offers excellent tear resistance, heat resistance, and electrical insulation properties, making it ideal for applications in automotive, electronics, and medical industries.
2. Liquid Silicone Rubber (LSR): LSR silicone is a two-part material that cures at room temperature through a platinum catalyzation process. It has a low viscosity, allowing it to flow easily into intricate molds. LSR silicone offers several advantages, including excellent tolerance for temperature extremes, chemical resistance, and biocompatibility. Its ability to produce parts with precision and tight tolerances make it widely used in medical devices, consumer electronics, and automotive applications.
3. Fluorosilicone Rubber (FSR): FSR silicone is a specialty silicone that contains both organic and inorganic components. It exhibits exceptional resistance to fuel, oil, and solvents, making it well-suited for applications in the aerospace, automotive, and oil and gas industries. FSR silicone offers high-temperature stability, good electrical insulation properties, and resistance to extreme environments.
4. Room Temperature Vulcanization (RTV) Silicone: RTV silicone is a two-part material commonly used for prototype development and short-run production. It cures at room temperature through a condensation or addition reaction, producing flexible and durable parts. RTV silicone offers good dimensional stability, low shrinkage, and can be easily pigmented or modified. It is often used in various industries for rapid prototyping, molding of complex shapes, and creating silicone molds.
These are just a few types of silicone that can be used in injection molding. Each type offers distinct characteristics and advantages, making it important to choose the right silicone for specific applications. Injection molding allows for efficient production of silicone parts, ensuring consistent quality and precision in the final products.
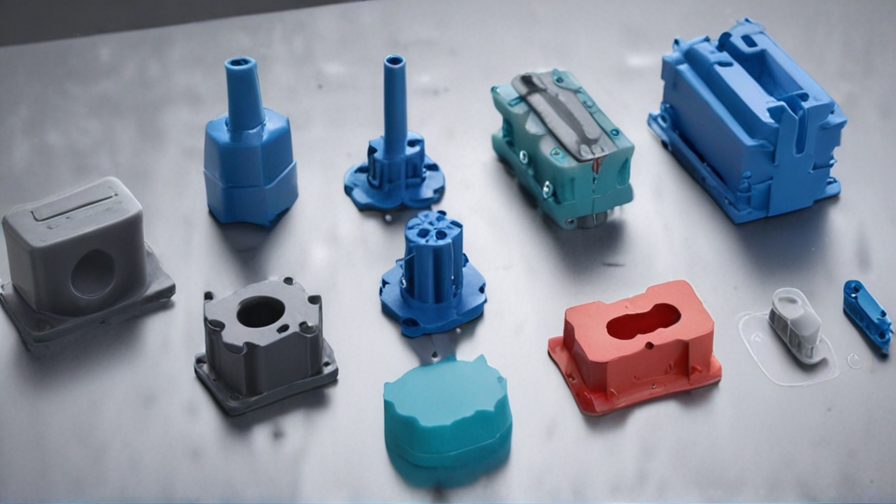
Pros and Cons of Using injection molding silicone
Pros of using injection molding silicone:
1. Versatility: Silicone injection molding offers a wide range of options for creating complex shapes and intricate details. It allows for the production of parts with various degrees of hardness and softness, making it suitable for a wide range of applications.
2. High precision and accuracy: Injection molding silicone enables the creation of highly precise and accurate products, even in small dimensions. This is particularly useful for manufacturing components with tight tolerances or intricate designs.
3. Durability: Silicone is known for its durability and resilience. It can withstand extreme temperatures, UV radiation, moisture, and chemical exposure, making it suitable for demanding applications that require long-lasting performance.
4. Production efficiency: Injection molding silicone can be a cost-effective solution for high-volume production. The process allows for the rapid production of identical parts, reducing labor costs and increasing efficiency.
5. Cosmetic appeal: Silicone injection molding can produce parts with smooth surfaces and excellent surface finish, resulting in visually appealing products. This is particularly important for applications where the appearance of the final product is crucial, such as consumer electronics or medical devices.
Cons of using injection molding silicone:
1. Cost: Compared to other molding processes, injection molding silicone can be more expensive initially. The cost of the silicone material, equipment, and mold design can be higher, especially for small production runs.
2. Longer lead times: Setting up a silicone injection molding process can take longer compared to other molding techniques. This is due to the complexity of mold design and fabrication, testing, and optimization of process parameters.
3. Limited material options: While silicone offers many advantages, it may not be suitable for all applications. Some specific material properties may not be achievable with silicone, such as extreme hardness or chemical resistance to certain substances.
4. Design limitations: Silicone injection molding may have some design restrictions due to the mold structure and process limitations. Complex designs or undercut features might require additional steps or modifications to the mold.
5. Waste and environmental impact: Injection molding silicone generates waste material during production, which needs to be properly managed. Additionally, silicone production can have an environmental impact due to the use of certain chemicals and energy-intensive processes.
In conclusion, while injection molding silicone offers numerous benefits such as versatility, high precision, durability, production efficiency, and cosmetic appeal, it also comes with some drawbacks including cost, longer lead times, limited material options, design limitations, and waste/environmental impact. Assessing these pros and cons is crucial to determine the suitability of silicone injection molding for specific applications.
injection molding silicone Reference Specifications (varies for different product)
Injection molding is a popular manufacturing process used to produce a wide range of silicone products. This process involves injecting molten silicone material into a mold cavity, which is then cooled and hardened to form the final product. The specifications for injection molding silicone can vary depending on the specific product being manufactured. Here are some common reference specifications:
1. Material: Silicone used for injection molding is typically a high-quality, heat-resistant polymer with excellent flexibility and durability. It can have varying hardness levels, ranging from very soft and flexible (10 Shore A) to relatively hard and rigid (70 Shore A).
2. Mold design: The mold used for silicone injection molding should be designed to handle the required part geometry and material flow. It should have proper channels for the silicone to flow into the cavity, as well as vents to allow for air or excess material to escape. The mold should be made from durable, heat-resistant materials, such as steel or aluminum, to withstand the injection process and maintain dimensional stability.
3. Injection parameters: Silicone injection molding typically requires precise control over several parameters, including injection pressure, temperature, and time. The injection pressure is usually high (ranging from 1000 to 5000 psi) to fill the mold cavity completely and achieve high-quality surface finish. The temperature of the silicone material is controlled to ensure proper flow and curing, typically ranging from 150 to 200 degrees Celsius. The injection time is determined by the part size and complexity, and it varies accordingly.
4. Post-processing: After the silicone has been injected into the mold cavity and cooled, the mold is opened to release the finished part. Any excess material or flash is trimmed or removed to achieve the desired final shape. Some silicone products may require additional post-processing steps, such as surface finishing, painting, or assembly.
It is important to note that these specifications can vary for different silicone products. Factors such as part design, complexity, material properties, and application requirements influence the specific reference specifications for each product. Manufacturers carefully consider these factors to ensure the production of high-quality silicone products through injection molding.
Applications of injection molding silicone
Injection molding silicone is a versatile material that finds application in various industries. This article will discuss some of the common applications of injection molding silicone within the 300-word limit.
1. Medical Industry: Injection molding silicone is widely used in the medical field due to its biocompatible properties. It is used to manufacture medical devices such as tubing, catheters, gaskets, seals, and surgical tools. The material’s high flexibility, durability, and resistance to chemical sterilization ensure safe and reliable performance in medical applications.
2. Automotive Industry: Silicone injection molding is utilized in the automotive sector for manufacturing various components. It is used to produce gaskets, seals, O-rings, connectors, and wiring harnesses. Silicone’s resistance to heat, oil, and chemicals make it an ideal choice for automotive applications that require durability and reliability.
3. Consumer Electronics: Injection molding silicone is commonly used in the production of consumer electronic devices. It is used to manufacture protective cases, buttons, keypads, and seals for electronic devices such as smartphones, tablets, and remote controls. Silicone’s flexibility, water resistance, and electrical insulation properties make it suitable for these applications.
4. Aerospace Industry: Silicone injection molding is also employed in the aerospace sector for manufacturing various components. It is used to produce gaskets, seals, connectors, and electrical insulation materials. Silicone’s ability to withstand extreme temperatures, pressure differentials, and environmental conditions makes it an ideal choice for aerospace applications.
5. Food and Beverage Industry: Silicone injection molding is widely used in the food and beverage industry for manufacturing food-grade components. It is used to produce seals, gaskets, valves, and tubing for food processing, packaging, and dispensing equipment. Silicone’s non-toxic and odorless properties, as well as its ability to withstand high temperatures and resist chemicals, make it suitable for these applications.
6. Industrial Applications: Injection molding silicone is utilized in various industrial applications where a combination of flexibility, durability, and chemical resistance is required. It is used to manufacture seals, gaskets, O-rings, and vibration damping components for industrial machinery and equipment. Silicone also finds applications in the construction industry for producing seals, gaskets, and weatherproofing materials.
In conclusion, injection molding silicone finds application in a wide range of industries due to its versatility and advantageous properties. Its use in medical, automotive, consumer electronics, aerospace, food and beverage, and various industrial applications highlights its importance and adaptability in modern manufacturing processes.
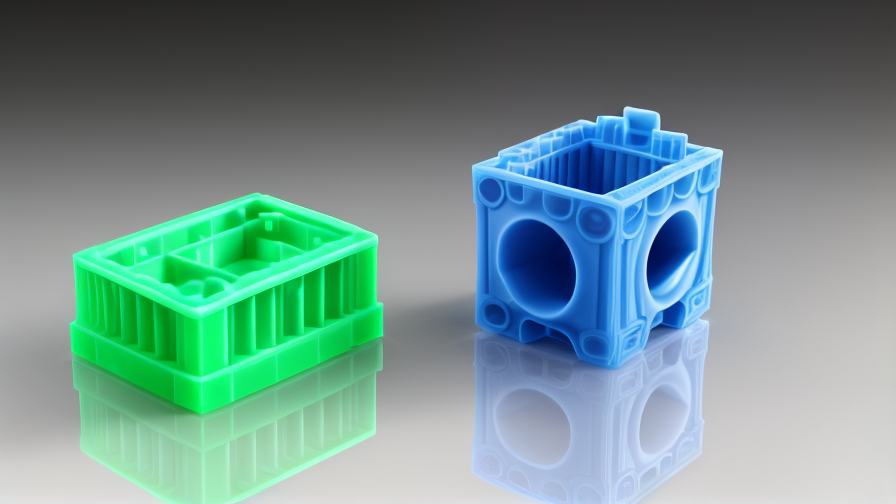
The Work Process and how to use injection molding silicone
The work process of injection molding silicone involves several steps. First, a mold is created, typically made of metal or aluminum, with the desired shape or pattern. The mold is then prepped by applying a release agent to ensure that the silicone does not stick to the mold.
Next, the silicone material is mixed and prepared. This usually involves combining two components, a base material and a catalyst. The exact mixing ratio and process may vary depending on the specific silicone being used.
Once the silicone is mixed, it is poured into a separate container called the pot. From the pot, the silicone is injected into the mold using an injection molding machine. The machine applies pressure to fill the mold cavity, ensuring the silicone material forms to the desired shape.
After injection, the silicone is allowed to cure or harden. The curing time may vary depending on the silicone type and manufacturer’s instructions. Once cured, the mold can be opened, and the finished silicone product can be removed.
To effectively use injection molding silicone, it is recommended to follow the manufacturer’s guidelines and instructions. This includes accurately measuring and mixing the silicone components, using the proper injection molding machine settings, and ensuring the mold is properly prepped with a release agent.
It is essential to consider factors such as temperature, curing time, and pressure during the injection molding process. These variables may affect the quality and characteristics of the final silicone product.
Regular maintenance of the injection molding machine and molds is also crucial to ensure consistent and reliable results. This may involve cleaning, inspection, and repairs as needed.
By understanding and following the recommended work process and guidelines, injection molding silicone can be used effectively to create a wide range of silicone products with precise shapes and dimensions.
Quality Testing Methods for injection molding silicone and how to control the quality
Injection molding silicone is a widely used manufacturing process in various industries, including medical, automotive, and consumer goods. To ensure the quality of silicone products, several testing methods are employed, along with effective quality control measures.
One common testing method for injection molding silicone is visual inspection. This involves visual examination of the finished products for any visible defects or imperfections such as surface irregularities, air bubbles, or flash. Any defective product is rejected to prevent it from reaching the market.
Another important testing method is dimensional inspection. This involves measuring the silicone parts using precise tools like calipers or coordinate measuring machines. Dimensional inspection ensures that the parts meet the specified dimensions and tolerances as per the design requirements.
Additionally, mechanical properties testing is crucial for quality control. This typically involves conducting tests like tensile strength, tear resistance, compression modulus, and elongation at break. These tests assess the mechanical characteristics of the silicone parts and ensure they meet the required standards.
Furthermore, hardness testing is commonly performed on silicone products. Durometer hardness testers are used to measure the hardness of the material, ensuring it falls within the desired range. This test helps ensure that the silicone parts possess the optimal hardness required for their intended applications.
To effectively control the quality of injection molded silicone parts, a comprehensive quality control plan is essential. This plan includes establishing stringent process parameters to ensure consistency in the molding process. Regular monitoring of these parameters, such as temperature, pressure, and injection speed, helps identify any deviations that may impact product quality.
Implementing a robust quality management system, such as ISO 9001, can also help control the quality of silicone products. This involves documenting procedures, conducting regular audits, and implementing corrective and preventive actions based on identified non-conformities.
Finally, conducting a thorough final inspection of each batch of injection molded silicone parts before packaging and shipping is crucial. This inspection should include visual inspection, dimensional checks, mechanical testing, and any other relevant quality tests specific to the product requirements.
By employing these testing methods and implementing effective quality control measures, manufacturers can ensure the production of high-quality injection molded silicone products that meet customer expectations and regulatory requirements.
injection molding silicone Sample Policy and Post-Purchase Considerations for injection molding silicone from China
Sample Policy:
When it comes to injection molding silicone from China, it is important to establish a sample policy before placing an order. This helps in ensuring the quality and functionality of the product. Here are some considerations for the sample policy:
1. Request a sample: It is recommended to request a sample from the manufacturer before finalizing the order. This allows you to test the material, assess its quality, and verify if it meets your specific requirements.
2. Review the sample thoroughly: Examine the sample for any defects, inconsistencies, or deviations from your specifications. Check the material’s color, texture, flexibility, and other physical properties. Ensure that it meets your desired standards.
3. Testing and verification: Conduct various tests to validate the performance of the injected silicone. This could include durability tests, temperature resistance tests, and any other specific tests relevant to your application. Make sure the sample meets your desired specifications and requirements.
4. Seek feedback: Share the sample with relevant stakeholders within your organization for their input and feedback. This provides a broader perspective on the suitability of the product and helps in making an informed decision.
Post-Purchase Considerations:
Once you have placed an order for injection molding silicone from China, there are a few post-purchase considerations you should keep in mind:
1. Quality control: Establish a system for quality control during the production process. Discuss the quality standards with the manufacturer and set clear expectations. Regularly communicate with the supplier to ensure all requirements are being met.
2. Communication and feedback loop: Maintain open and transparent communication with the manufacturer. Regularly update them regarding your expectations, changes, or concerns. Encourage the supplier to provide updates on the production progress and any potential challenges.
3. Third-party inspection: Consider engaging a third-party inspection agency to verify the quality and conformity of the silicone products. An independent inspection reduces the risk of receiving substandard or defective goods.
4. Dispute resolution: In case of any disagreements or disputes, establish a clear mechanism for dispute resolution. Clearly define the steps to be taken in case of any issues and approach the resolution process in a professional and systematic manner.
By following the above sample policy and post-purchase considerations, you can ensure a smooth and successful procurement experience for injection molding silicone from China.
Sourcing injection molding silicone from China: Opportunities, Risks, and Key Players
Chinese injection molding silicone manufacturers offer various opportunities for businesses looking to source their products from China. The country has a strong manufacturing base and a well-developed supply chain, which allows for cost-effective production and timely delivery. Additionally, China’s injection molding silicone industry has experienced significant growth in recent years, making it a competitive market with a wide range of products and options available.
One of the main opportunities of sourcing injection molding silicone from China is the potential cost savings. Chinese manufacturers often offer lower prices compared to their counterparts in other countries. This cost advantage can be attributed to several factors, including lower labor costs, economies of scale, and government support for the manufacturing sector. By sourcing from China, businesses can effectively reduce their production costs, which can lead to increased profitability.
Another opportunity lies in the wide range of products and options available in the Chinese market. Chinese injection molding silicone manufacturers produce a diverse array of products, including different grades and types of silicone materials, various sizes and shapes, and customized solutions. This allows businesses to find the right product that meets their specific requirements and market demands.
However, there are also risks associated with sourcing injection molding silicone from China. Quality control can be a challenge, as some manufacturers may prioritize lower costs over product quality. It is crucial for businesses to conduct thorough due diligence and select reliable suppliers with a proven track record of producing high-quality silicone products. This can be achieved through supplier audits, quality inspections, and obtaining samples for testing.
Intellectual property protection is another concern when sourcing from China. It is essential to have robust contracts and non-disclosure agreements in place to safeguard proprietary information. Businesses should also consider the enforcement of intellectual property rights in China, which can vary in effectiveness.
When sourcing injection molding silicone from China, key players in the industry should be identified. Some prominent Chinese manufacturers include Dow Corning, Wacker Chemie AG, Shin-Etsu Chemical Co., Ltd., Momentive Performance Materials Inc., and Bluestar Silicones. These companies have established themselves as leaders in the injection molding silicone industry and have a strong reputation for producing high-quality materials.
In conclusion, sourcing injection molding silicone from China presents opportunities for businesses, such as cost savings and a wide range of products. However, it is important to carefully manage the associated risks, including quality control and intellectual property protection. Identifying reliable suppliers, conducting thorough due diligence, and implementing appropriate safeguards can help businesses successfully navigate the Chinese market and benefit from its advantages.
How to find and select reliable injection molding silicone manufacturers in China,use google search manufacturers and suppliers
Finding and selecting reliable injection molding silicone manufacturers in China can be a daunting task, but using Google search for manufacturers and suppliers is a good starting point. Here are a few steps to follow:
1. Start by conducting a basic Google search using relevant keywords such as “injection molding silicone manufacturers China” or “reliable silicone molding suppliers in China.” This will help you find a list of potential manufacturers and suppliers.
2. Visit the websites of the manufacturers and suppliers that appear in your search results. Look for information about their company, manufacturing capabilities, certifications, and experience in the industry. Reliable manufacturers often have detailed and professional websites.
3. Check if the manufacturer has relevant certification such as ISO 9001, which indicates that they follow stringent quality control processes. Look for other certifications specific to the silicone molding industry as well.
4. Look for customer reviews or testimonials on the manufacturer’s website or other online platforms. Positive reviews from previous clients can indicate the manufacturer’s reliability and quality of their products.
5. Contact the shortlisted manufacturers directly and request additional information such as product samples, manufacturing processes, pricing, lead times, and minimum order quantities. Prompt and detailed responses demonstrate the manufacturer’s professionalism and commitment to customer service.
6. Consider visiting the manufacturer’s facility in person if feasible. This allows you to assess their production capabilities, quality control measures, and overall infrastructure.
7. Ask for references from the manufacturer and contact their previous or existing clients to inquire about their experiences. This can provide valuable insights into the manufacturer’s reliability, communication, and ability to deliver on time.
8. Compare the quotes, lead times, and product quality of multiple manufacturers to make an informed decision. However, it is important to remember that the lowest price may not always guarantee the best quality.
Ultimately, finding and selecting a reliable injection molding silicone manufacturer in China requires thorough research, communication, and evaluation. By using Google search, exploring websites, checking certifications, reading reviews, contacting manufacturers directly, and seeking references, you can increase your chances of finding a trustworthy and suitable partner for your silicone molding needs.
How to check injection molding silicone manufacturers website reliable,use google chrome SEOquake check if ranking in top 10M
To check the credibility and reliability of an injection molding silicone manufacturer’s website, you can follow these steps:
1. Use Google Chrome: Start by opening the manufacturer’s website using the Google Chrome web browser, as it offers several helpful tools and extensions for evaluating website reliability.
2. Install SEOquake Extension: Add the SEOquake extension to your Google Chrome browser. This extension provides valuable insights into a website’s SEO performance and popularity.
3. Check Website Ranking: After installing SEOquake, a toolbar will appear at the top of your browser window. Within this toolbar, click on the SEOquake logo and select “Show SERP overlay.” This will display the current website’s ranking in the Google search results.
4. Evaluate Ranking Position: If the manufacturer’s website appears within the top 10 million search results on Google, it indicates reasonable popularity and online presence.
5. Examine Meta Description: Analyze the meta description, which is a brief summary of the webpage’s content displayed below the link in search results. A well-written and relevant meta description suggests professionalism and reliability.
6. Verify Website Content: Assess the quality and relevance of the website’s content by exploring various sections, including the home page, product descriptions, about us page, and contact information. Look for accurate and detailed information, clear product imagery, and any certifications or affiliations that can validate the manufacturer’s credibility.
7. Check Website Design: A professionally designed website with a clean layout, easy navigation, and visually appealing elements generally indicates a reliable manufacturer. Poorly designed websites with broken links, outdated content, or excessive advertisements may be warning signs of an unreliable source.
8. Read Customer Reviews and Testimonials: Look for customer reviews and testimonials either on the manufacturer’s website itself or on third-party platforms. Genuine, positive feedback from satisfied customers can reinforce the credibility of the manufacturer.
By using Google Chrome’s SEOquake extension and following these steps, you can evaluate the reliability of an injection molding silicone manufacturer’s website and make a more informed decision regarding their products and services.
Top 10 injection molding silicone manufacturers in China with each 160 words introduce products,then use markdown create table compare
Injection molding silicone is a versatile material widely used in various industries, including automotive, electronics, medical, and consumer goods. China, being one of the leading manufacturing hubs, has numerous manufacturers specialized in producing high-quality injection molding silicone. Here are the top 10 injection molding silicone manufacturers in China, along with a brief introduction to their products:
1. Wacker Chemicals China: Wacker Chemicals is a renowned global leader in the production of high-quality silicone products. Their injection molding silicones offer excellent flexibility, heat resistance, and low compression set for various applications.
2. Dow Chemical China: Dow Chemical is known for its advanced silicone solutions. Their injection molding silicones exhibit high tear strength, good flowability, and excellent heat resistance, making them suitable for intricate and complex designs.
3. Shin-Etsu Chemical China: Shin-Etsu Chemical specializes in producing silicone materials for injection molding. Their elastomers provide outstanding bounce, exceptional heat resistance, and low compression set, making them ideal for automotive gaskets and seals.
4. Momentive Performance Materials China: Momentive prides itself on manufacturing high-performance silicones for injection molding. Their products possess excellent tensile strength, good tear resistance, and superior moldability, catering to diverse industries.
5. Elkem Silicone China: Elkem Silicone offers a wide range of injection molding silicones with excellent mechanical properties, including good tear strength, elongation, and elasticity. Their products are widely used in the automotive and industrial sectors.
6. Reiss Manufacturing China: Reiss specializes in precision injection molding silicone, providing customizable solutions for intricate designs. Their silicones offer high dimensional stability, low shrinkage, and excellent compression properties.
7. Guangdong Polysil Technology China: Guangdong Polysil Technology is a leading manufacturer of liquid silicone rubber (LSR) for injection molding. Their LSR products offer excellent transparency, low viscosity, and good tear strength, suitable for a variety of applications.
8. TCL Chemical China: TCL Chemical produces silicone elastomers with exceptional mechanical properties, including high tear strength and elongation. Their injection molding silicones exhibit excellent weatherability and UV resistance.
9. NuSil Technology China: NuSil Technology specializes in high-purity silicone materials for injection molding. Their silicones offer superior biocompatibility, good mechanical properties, and excellent clarity, making them suitable for medical and pharmaceutical applications.
10. Guangzhou OTT New Materials China: Guangzhou OTT New Materials is a prominent manufacturer of liquid silicone rubber for injection molding. Their LSR products provide high transparency, low viscosity, and outstanding stability, meeting the stringent quality demands of various industries.
| Manufacturer | Products |
| ——————————- | —————————- |
| Wacker Chemicals China | High-quality silicone products |
| Dow Chemical China | Advanced silicone solutions |
| Shin-Etsu Chemical China | Silicone elastomers for automotive applications |
| Momentive Performance Materials | High-performance silicones |
| Elkem Silicone China | Silicones for automotive and industrial sectors |
| Reiss Manufacturing China | Precision injection molding silicones |
| Guangdong Polysil Technology | Liquid silicone rubber (LSR) |
| TCL Chemical China | Silicone elastomers with UV resistance |
| NuSil Technology China | High-purity silicone materials for medical applications |
| Guangzhou OTT New Materials China | Liquid silicone rubber (LSR) products |
In this table, the top 10 injection molding silicone manufacturers in China are compared based on their primary products. The table provides a concise overview of their focus areas and enables easy comparison for potential buyers or industry professionals.
Background Research for injection molding silicone manufacturers Companies in China, use qcc.com archive.org importyeti.com
When looking for injection molding silicone manufacturers in China, there are several websites that can be utilized to conduct background research and gather information. These websites include qcc.com, archive.org, and importyeti.com. Here is a brief overview of each platform:
1. qcc.com:
Qcc.com is a Chinese business information database that provides comprehensive company information, including registration details, business scope, financial reports, and legal representatives. Users can search for specific companies, browse through industry categories, or conduct background checks on potential partners. This platform can be especially useful to verify the legitimacy and reliability of silicone manufacturers in China.
2. archive.org:
Archive.org is a digitized library that contains snapshots of websites from different points in time. This platform allows users to access historical versions of websites, enabling them to review past information, product catalogs, or business profiles of silicone manufacturers. It can help in assessing the company’s stability, growth, and the consistency of their offerings over time. This information can be valuable for evaluating a company’s track record and reputation.
3. importyeti.com:
Importyeti.com is a B2B marketplace that focuses on importing and exporting data. It provides information on companies that engage in international trade, including manufacturers, suppliers, and exporters. By using importyeti.com, users can quickly access shipping records, trade data, and import-export trends of silicone manufacturers in China. This platform can be beneficial in determining a manufacturer’s capabilities, their global reach, and their experience in delivering products internationally.
In summary, qcc.com, archive.org, and importyeti.com are three useful web resources to conduct background research on injection molding silicone manufacturers in China. The combination of these platforms offers access to vital data such as company registration information, business history, past website review, and shipping records. It is recommended to utilize these platforms to gather a comprehensive understanding of potential manufacturers before making business decisions.
Leveraging Trade Shows and Expos for injection molding silicone Sourcing in China
Trade shows and expos are excellent platforms for sourcing injection molding silicone in China. As the global hub for manufacturing and sourcing, China offers a wide range of opportunities for businesses in various industries.
Attending trade shows and expos related to injection molding and silicone production provides a unique opportunity to connect with manufacturers, suppliers, and industry professionals. These events showcase the latest products, technologies, and innovations in the field, allowing businesses to stay up-to-date with the latest trends and developments.
One of the key advantages of attending these events is the ability to meet potential suppliers face-to-face. This allows for direct communication and a better understanding of their capabilities, product range, and manufacturing processes. It also provides an opportunity to establish personal relationships, which are crucial in building trust and a strong business partnership.
Trade shows and expos also offer the chance to compare and evaluate different suppliers in one place. By visiting multiple booths and engaging in conversations, businesses can gather essential information about pricing, quality control measures, lead times, and other critical factors. This firsthand experience enables better-informed decision-making and increases the chances of finding the most suitable supplier for injection molding silicone needs.
Moreover, trade shows and expos often feature seminars, workshops, and presentations by industry experts. These educational sessions provide valuable insights into the best practices, new techniques, and emerging trends in silicone molding. By participating in these activities, businesses can enhance their knowledge and stay competitive in the market.
In conclusion, leveraging trade shows and expos for sourcing injection molding silicone in China offers numerous benefits. It allows businesses to connect with potential suppliers, compare different options, and stay updated with the latest industry trends. With careful planning and effective networking, these events can be a valuable resource for businesses looking to source silicone products from China, ultimately contributing to their success in the market.
The Role of Agents and Sourcing Companies in Facilitating injection molding silicone Purchases from China
When it comes to purchasing injection molding silicone from China, agents and sourcing companies play a crucial role in facilitating the process and ensuring a smooth experience for buyers. Their involvement can greatly simplify the complexities of dealing with overseas suppliers, language barriers, quality control, and logistics. Below are some key roles they play:
1. Supplier Identification: Agents and sourcing companies have intricate knowledge of the Chinese market and can help identify reliable and reputable silicone injection molding manufacturers. They have established networks and partnerships, saving valuable time in the search for suitable suppliers.
2. Quality Assurance: Ensuring product quality is critical, especially when dealing with manufacturers in a distant country. Agents and sourcing companies can perform factory assessments, complete audits, and conduct quality control inspections to guarantee that the products meet the buyer’s requirements and standards.
3. Negotiation: Agents and sourcing companies have experience in negotiating prices, contracts, and production terms on behalf of the buyer. They possess knowledge of local market conditions and can leverage their relationships to secure competitive pricing and favorable terms.
4. Communication and Language Barrier: Effective communication is vital when dealing with overseas suppliers. Agents and sourcing companies act as intermediaries, bridging the language barrier and facilitating communication between buyers and Chinese manufacturers. They ensure that all requirements, specifications, and concerns are accurately conveyed and understood.
5. Logistics and Shipping: Navigating the complexities of shipping products from China can be challenging. Agents and sourcing companies handle logistics, including coordinating transportation, customs documentation, and navigating export regulations. They ensure that the products are shipped safely and on time.
6. Risk Mitigation: Agents and sourcing companies help mitigate risks associated with international transactions. They provide advice on legal and regulatory issues, assist in drafting contracts, and offer support in resolving disputes or issues that may arise during the purchasing process.
By employing agents and sourcing companies, buyers can benefit from their expertise, local knowledge, and established networks in China. They ensure a streamlined purchasing process, reduce risks, and facilitate successful injection molding silicone purchases from China.
Price Cost Research for injection molding silicone manufacturers Companies in China, use temu.com and 1688.com
When conducting price cost research for injection molding silicone manufacturers in China, two reliable platforms for sourcing information are temu.com and 1688.com. These platforms provide comprehensive listings of suppliers and enable easy comparison of prices and products.
To begin the research process, start by visiting temu.com, a leading B2B platform in China. Utilize the search function to find silicone injection molding manufacturers. Narrow down the options by selecting the preferred location, such as Guangdong or Zhejiang, which are major manufacturing hubs in China.
Review the profiles, product catalogs, and ratings of the listed manufacturers. It is essential to consider their production capacity, certifications, and customer reviews as indicators of their reliability and quality. After shortlisting a few potential manufacturers, collect quotes from them, specifying your requirements, quantity, and desired delivery timeline. This will help in comparing the prices and obtaining a better understanding of the cost structure.
Additionally, visit 1688.com, a popular domestic sourcing platform in China. This platform offers an extensive range of suppliers, including manufacturers of injection molding silicone. Similar to temu.com, conduct a search using relevant keywords and filters to narrow down the options.
While on 1688.com, delve into each manufacturer’s profile, product details, and customer reviews, if available. Collect quotes from multiple suppliers to ensure a comprehensive price comparison.
In both platforms, try to directly communicate with the manufacturers through their provided contact information or in-built messaging systems. Engage in discussions regarding your specific requirements and inquire about any additional costs not included in the quotes, such as tooling expenses, packaging, or shipping fees.
Remember to keep track of all the gathered information, including prices, delivery terms, and other pertinent details. This will help in making an informed decision based on cost-effectiveness and the manufacturers’ suitability for your project needs.
By utilizing temu.com and 1688.com, alongside diligent communication and meticulous price comparison, you can conduct effective price cost research for injection molding silicone manufacturers in China.
Shipping Cost for injection molding silicone import from China
The shipping cost for importing injection molding silicone from China depends on several factors such as the quantity, weight, shipping method, and destination location. There are generally two main shipping methods available: sea freight and air freight.
Sea freight is typically the more cost-effective option for large quantities or heavy shipments. The cost is usually calculated based on the volume of the goods (in cubic meters) and the shipping distance. Additionally, there may be fees such as customs clearance charges, documentation fees, and handling charges, which vary depending on the shipping company and destination. The shipping time can range from a few weeks to a month or more, depending on the ocean freight routing.
On the other hand, air freight is faster but generally more expensive compared to sea freight. The cost is usually calculated based on the weight of the goods (in kilograms) and the shipping distance. Like sea freight, there may be additional fees such as customs clearance charges and documentation fees. Air freight is recommended for urgent shipments or small quantities, and shipping time is typically around 3-7 business days.
To get an accurate shipping cost estimate, it is best to contact shipping companies or freight forwarders that specialize in importing goods from China. They can provide detailed information and quotes based on your specific requirements. Additionally, it’s important to consider other related costs such as import duties, taxes, customs fees, and insurance, which can vary depending on the destination country and the type of product being imported.
In conclusion, the shipping cost for importing injection molding silicone from China can vary depending on factors such as quantity, weight, shipping method, and destination location. It is recommended to consult with shipping companies or freight forwarders for accurate cost estimates and to consider other related costs involved in the import process.
Compare China and Other injection molding silicone Markets: Products Quality and Price,Visible and Hidden Costs
China is one of the leading markets for injection molding silicone products, but it is important to compare it with other markets in terms of product quality and price. While China has a reputation for offering lower-priced products, the quality may vary compared to other markets.
Product quality in China’s injection molding silicone market can be a mixed bag. While there are many reputable manufacturers that produce high-quality products, there are also lower-tier manufacturers that may compromise on quality to offer competitive prices. It is crucial for buyers to thoroughly research and vet potential suppliers to ensure they meet the required quality standards.
Price is often a major factor when considering sourcing from China. Chinese manufacturers generally offer lower prices due to factors such as lower labor and production costs. This can be advantageous for buyers looking for cost-effective solutions. However, it is important to consider the trade-offs between price and quality. Buyers should carefully review samples, certifications, and supplier track records before making a purchasing decision.
Visible costs in the Chinese market may include the product price, shipping fees, and any additional charges for customization, packaging, or labeling. However, hidden costs should also be taken into account. These may include potential quality issues leading to product defects or failures, resulting in additional expenses for replacements or repairs. Moreover, communication barriers, cultural differences, and longer lead times can also contribute to hidden costs.
Comparing China’s injection molding silicone market with other markets is crucial to ensure the best balance between quality and price. Markets such as the United States, Germany, and Japan are known for their stringent quality standards and high-end products. While these markets may come with higher price tags, buyers can expect superior quality control and product consistency.
In conclusion, while China offers competitive prices in the injection molding silicone market, product quality can vary. Buyers must carefully assess suppliers and consider both visible and hidden costs. Comparing China with other markets can help determine the optimal balance between product quality and price.
Understanding Pricing and Payment Terms for injection molding silicone: A Comparative Guide to Get the Best Deal
When it comes to injection molding silicone, understanding the pricing and payment terms is crucial to secure the best deal. This comparative guide aims to shed light on the key factors involved and provide valuable insights in 300 words or less.
The pricing of injection molding silicone depends on various factors that can significantly impact the final cost. These factors include the complexity and size of the mold, the volume of parts needed, the type and grade of silicone used, and any additional requirements such as color or special finishes. Each supplier may have different pricing structures, so it is vital to compare multiple quotes to get the best price for your specific project.
Considering payment terms is equally essential. Typically, injection molding suppliers require an upfront payment, which can range from 30% to 50% of the total cost. This initial payment covers the expenses associated with mold design and fabrication. The remaining amount is usually paid upon completion, before the molded parts are shipped. It’s important to clarify these payment terms upfront to avoid any misunderstandings or financial issues.
To get the best deal, it is advisable to obtain quotes from multiple silicone injection molding suppliers. An extensive evaluation of the quotes should be undertaken to compare prices and identify any hidden costs. It’s also crucial to consider the supplier’s reputation, experience, and quality of service.
In addition, requesting samples of the silicone molded parts can help evaluate the supplier’s capabilities and ensure that the product meets your requirements before making a final decision. This step can prevent potential quality issues and save both time and money in the long run.
Furthermore, consider the production volume required. Some suppliers may offer lower prices for higher production quantities, while others may have more competitive rates for smaller orders. Understanding your production needs and discussing them with potential suppliers will help determine the most cost-effective option.
Lastly, be aware of any additional costs that may arise, such as shipping fees, packaging, or mold maintenance fees. These expenses may vary depending on the supplier, so considering all potential costs will help determine the overall affordability of the injection molding project.
In conclusion, understanding the pricing and payment terms for injection molding silicone is essential for obtaining the best deal. Comparing multiple quotes, evaluating the supplier’s reputation, obtaining samples, considering production volume, and accounting for all associated costs are all crucial steps to secure a cost-effective and high-quality injection molding solution.
Chinese Regulations and Industry Standards Certifications for injection molding silicone,Import Regulations and Customs for injection molding silicone from China
Chinese Regulations and Industry Standards Certifications for injection molding silicone play a vital role in ensuring the quality, safety, and compliance of these products. The most notable certifications and regulations in China for injection molding silicone are as follows:
1. China Compulsory Certification (CCC): This certification is mandatory for certain products, ensuring their compliance with national safety, quality, and environmental protection standards. Injection molding silicone products need to obtain CCC before they can be marketed in China.
2. ISO 9001: This international standard certification ensures that the manufacturer has implemented effective quality management systems, ensuring consistent product quality and customer satisfaction.
3. ISO 14001: This certification focuses on environmental management systems, indicating that the manufacturer is committed to minimizing harmful environmental impacts caused by their production processes.
4. GB/T Standards: Injection molding silicone products must meet relevant national and industry-specific standards, such as GB/T 1236-2020 for silicone rubber compounds and GB/T 22048-2012 for silicone rubber seals.
5. Import and Export Regulations: When importing injection molding silicone from China, several regulations and customs requirements must be followed. These include providing accurate product descriptions, obtaining necessary licenses, documenting proper customs value, complying with labeling and packaging regulations, and ensuring conformity with regional product regulations (e.g., European CE marking).
6. Quality Inspection: Importers may also conduct quality inspections of injection molding silicone products before shipping to ensure compliance with specifications, safety standards, and buyer requirements.
To summarize, obtaining certifications such as CCC, ISO 9001, and ISO 14001 assures the quality and compliance of injection molding silicone products in China. Importers must adhere to Chinese import regulations and customs requirements, ensuring accurate documentation, compliance with regional regulations, and optional quality inspections. Compliance with these regulations and certifications ensures the integrity and safety of injection molding silicone products and facilitates successful import and export transactions.
Sustainability and Environmental Considerations in injection molding silicone Manufacturing
Injection molding silicone manufacturing is a widely used process for creating a variety of products in various industries. However, it is important to consider sustainability and environmental factors during this manufacturing process.
One key aspect to consider is the energy consumption during injection molding silicone manufacturing. Energy-intensive processes, such as heating, cooling, and operating injection molding machinery, can contribute to a significant carbon footprint. Employing energy-saving measures, such as optimizing machine operating parameters, implementing efficient heating and cooling systems, and utilizing renewable energy sources, can help reduce energy consumption and minimize environmental impact.
Another critical consideration is the use of raw materials and waste generation. Silicone is derived from finite resources and its production can lead to waste generation and environmental pollution. Reducing material waste can be achieved through careful production planning, precise machine calibration, and implementing recycling initiatives. Additionally, exploring alternative sustainable materials, such as bio-based or recycled silicone, can help minimize the environmental impact associated with traditional silicone production.
Furthermore, the disposal of silicone products at the end of their lifecycle is a significant environmental concern. Silicone is not readily biodegradable and can persist in the environment for a long time. To mitigate this issue, implementing recycling programs or providing customers with information on proper disposal methods for silicone products can help reduce their environmental impact.
Ongoing research and development efforts in the field of injection molding silicone manufacturing aim to improve sustainability and environmental considerations further. This includes the development of environmentally friendly additives, such as bio-based plasticizers or recycling aids, to enhance the eco-friendliness of silicone products.
In conclusion, sustainability and environmental considerations in injection molding silicone manufacturing play a vital role in minimizing the industry’s impact on the environment. Through energy-saving measures, waste reduction, exploration of alternative materials, and proper disposal methods, the manufacturing process can become more sustainable, ensuring a greener future for silicone products.
List The Evolution history of “injection molding silicone”
Injection molding silicone is a versatile material used in various industries for its exceptional properties. Its evolution has been characterized by advancements in materials, manufacturing processes, and application techniques over the years.
The history of injection molding silicone can be traced back to the mid-20th century when the first synthetic elastomers were developed. These initial rubber-like materials, such as silicone rubber, were created by polymerizing silicon and oxygen atoms, resulting in a flexible and heat-resistant substance. However, the early production methods were tedious and expensive, limiting widespread adoption.
In the 1950s, with the advent of plastic injection molding, the concept of injecting liquid silicone into molds arose. This introduced a more efficient and cost-effective production technique compared to traditional methods like compression molding. However, silicone compression molding continued to be the preferred technique due to its lower costs and well-established processes.
It was not until the 1970s that significant breakthroughs occurred in the development of injection molding processes for silicone. Researchers started experimenting with different feed systems, mold designs, and curing techniques to overcome the challenges of injecting and solidifying the highly viscous liquid silicone. This led to the introduction of cold runner systems, which minimized waste and reduced cycle times.
Throughout the 1980s and 1990s, advancements continued in silicone chemistry, allowing for the creation of materials with enhanced properties such as high tear strength, improved transparency, and increased heat resistance. These developments broadened the range of applications for silicone injection molding, including automotive parts, medical devices, consumer products, and more.
Furthermore, the introduction of computer-aided design (CAD) and computer-aided manufacturing (CAM) technologies in the late 20th century revolutionized the production of silicone injection molded parts. These digital tools enhanced precision, reduced production time, and enabled the creation of complex and intricate designs.
In recent years, advancements in automation, robotics, and 3D printing technologies have further accelerated the evolution of silicone injection molding. These innovations have improved process control, increased production efficiency, and expanded the possibilities for customization and rapid prototyping.
Overall, the evolution of injection molding silicone has been driven by the need for cost-effective production methods, advancements in material properties, and continuous improvement in manufacturing techniques. Today, silicone injection molding stands as a reliable and versatile solution for a wide range of industries, with ongoing research and development promising further advancements in the future.
The Evolution and Market Trends in injection molding silicone Industry
In recent years, the injection molding silicone industry has witnessed significant evolution and market trends. Silicone is a versatile material with excellent thermal stability, flexibility, and durability, making it ideal for various applications such as automotive, healthcare, electronics, and consumer goods.
One of the key trends in the industry is the shift towards the use of liquid silicone rubber (LSR) materials for injection molding. LSR offers several advantages over traditional solid silicone rubber, including faster curing times, improved processability, and higher production efficiency. This has led to increased adoption of LSR in industries such as medical devices, where precise and intricate components are required.
Another emerging trend is the utilization of additive manufacturing technologies, such as 3D printing, in silicone injection molding. This enables the production of complex geometries and prototypes, reducing the overall lead time and cost of product development. Additionally, 3D printing allows for customization and personalization, which aligns with the growing demand for unique and bespoke silicone products.
The industry has also witnessed a growing emphasis on sustainability and environmental considerations. Manufacturers are increasingly opting for greener alternatives, such as bio-based or recycled silicone materials, to reduce their carbon footprint. Additionally, the development of more efficient injection molding processes, such as micro-injection molding and gas-assisted molding, has contributed to increased material savings and reduced waste generation.
Furthermore, the market for injection molding silicone has expanded with the rising demand in emerging economies, particularly in Asia-Pacific. The automotive industry’s growth in the region, coupled with the increasing penetration of silicone in electrical and electronic applications, has driven the demand for injection molded silicone products. As a result, manufacturers are investing in developing their production capacities and establishing strategic partnerships to cater to this growing market.
In conclusion, the injection molding silicone industry has undergone significant evolution and witnessed several market trends. The shift towards liquid silicone rubber, the utilization of additive manufacturing technologies, the focus on sustainability, and the growing market in emerging economies are shaping the industry’s trajectory. Manufacturers must adapt to these trends to remain competitive and capitalize on the expanding opportunities in this dynamic market.
Custom Private Labeling and Branding Opportunities with Chinese injection molding silicone Manufacturers
Chinese injection molding silicone manufacturers offer custom private labeling and branding opportunities for businesses looking to market their products with a distinctive identity. These manufacturers have the capabilities to produce high-quality silicone products that can be customized with a brand’s logo, design, or any other unique element.
Private labeling allows businesses to build their brand image by having their logo or branding information prominently displayed on the silicone products. This helps create brand recognition and establishes a strong visual identity, enhancing the product’s marketability.
With Chinese injection molding silicone manufacturers, businesses have the advantage of accessing a wide range of customization options. This includes the ability to choose from various colors, finishes, and textures to align with the brand’s aesthetics and target audience preferences.
Moreover, these manufacturers often provide comprehensive branding services, such as custom packaging design and printing options. This further enhances the brand’s visibility and professionalism in the market.
Chinese injection molding silicone manufacturers are known for their cost-effective production capabilities and efficient turnaround times. Businesses can benefit from competitive pricing without compromising on the quality of the final product. This advantage enables businesses to allocate their resources more effectively and invest in other aspects of their branding and marketing initiatives.
Collaborating with these manufacturers also allows businesses to tap into the vast experience and expertise they possess. By leveraging their knowledge, businesses can receive valuable guidance on product design, material selection, and manufacturing processes, leading to a superior end result.
In conclusion, partnering with Chinese injection molding silicone manufacturers for custom private labeling and branding provides businesses with an excellent opportunity to market their products with a distinct identity. Acting as a one-stop solution for customization, these manufacturers offer cost-effective production, comprehensive branding services, and valuable expertise, ensuring the success of any branding initiative.
Tips for Procurement and Considerations when Purchasing injection molding silicone
When purchasing injection molding silicone, there are several considerations and tips that can help ensure a successful procurement process. Here are some key points to keep in mind:
1. Determine your requirements: Before purchasing silicone, identify your specific needs and requirements. Consider factors such as the type of product to be manufactured, the production volume, and desired quality standards. This will allow you to select the right silicone that meets your needs.
2. Quality assurance: Check the supplier’s quality control system and certifications. Ensure that the silicone material complies with relevant industry standards and regulations. Request samples or previous client references to assess the quality of the silicone.
3. Supplier reputation: Research and select reliable suppliers with a good reputation in the industry. Look for suppliers with a track record of delivering high-quality silicone products consistently and within specified timelines.
4. Material properties: Understand the properties of the silicone material, such as hardness, color, and stability. Ensure that the material is compatible with your manufacturing process.
5. Cost considerations: Compare prices from different suppliers while keeping in mind the quality of the silicone. Avoid compromising quality for a lower price, as it might result in substandard products or production issues.
6. Lead time: Ensure that the supplier can meet your required delivery schedules. Timeliness is crucial in maintaining an efficient production process.
7. After-sales support: Inquire about the level of support the supplier provides after purchase. Confirm if they offer technical assistance, troubleshooting guidance, or any warranties for their silicone products.
8. Environmental compatibility: Consider choosing silicone that is environmentally friendly and complies with environmental regulations. This includes selecting materials that can be recycled or reused to minimize waste.
9. Compatibility with equipment: Check whether the silicone is suitable for your injection molding equipment. Consider factors such as the material’s viscosity and the machine’s specifications to ensure compatibility.
10. Flexibility in ordering quantities: Some suppliers may have minimum order quantity requirements. Choose a supplier that offers flexibility in this aspect to avoid unnecessary overhead costs and inventory management challenges.
By considering these tips and factors, you can make an informed decision while purchasing injection molding silicone. Remember to thoroughly research suppliers, assess material quality, and ensure compatibility with your production requirements to achieve successful outcomes.
FAQs on Sourcing and Manufacturing injection molding silicone in China
Q: What is injection molding silicone?
A: Injection molding silicone refers to the process of using a silicone material to create complex and precise components through injection molding. This method involves injecting molten silicone into a mold cavity, allowing it to cool and solidify into the desired shape.
Q: Why source and manufacture injection molding silicone in China?
A: China has emerged as a leading global manufacturing hub, offering cost-effective solutions for various industries. Sourcing and manufacturing injection molding silicone in China can significantly reduce production costs without compromising on quality. Chinese manufacturers specialize in producing a wide range of silicone products and have extensive experience in injection molding technology.
Q: What are the advantages of sourcing injection molding silicone from China?
A: Sourcing injection molding silicone from China offers several advantages. Firstly, the cost of production can be significantly lower due to lower labor and material costs. China also has a vast network of reliable suppliers, ensuring a steady supply of raw materials. Additionally, Chinese manufacturers have the expertise in producing large quantities of silicone components, offering efficient and streamlined production processes.
Q: How to find reliable injection molding silicone manufacturers in China?
A: It is essential to conduct thorough research to find reliable injection molding silicone manufacturers in China. One should consider factors such as experience, reputation, and certifications when selecting a manufacturer. Online platforms and trade shows provide opportunities to connect with potential suppliers. It is recommended to request samples, visit the factories, and seek references to assess the manufacturer’s ability to meet specific requirements.
Q: Are there any potential challenges or risks when sourcing injection molding silicone from China?
A: While there are several benefits, sourcing injection molding silicone from China does come with certain challenges. Communication can be a potential hurdle due to language barriers. Quality control and intellectual property protection must also be addressed to ensure the products meet international standards and avoid unauthorized replication. Additionally, it is crucial to have a clear understanding of customs regulations and logistics to minimize any potential delays or issues during shipping.
In summary, sourcing and manufacturing injection molding silicone in China offer numerous advantages such as cost-effectiveness and expertise. However, thorough research, supplier evaluation, and addressing potential challenges are vital to ensure a successful sourcing experience.
Why contact sourcifychina.com get free quota from reliable injection molding silicone suppliers?
Sourcifychina.com, a sourcing platform connecting businesses with manufacturers in China, offers free quota from reliable injection molding silicone suppliers for several reasons. Firstly, by providing a free quota, Sourcifychina.com aims to attract potential customers and promote their platform as a reliable sourcing solution for injection molding silicone products.
Secondly, collaborating with reliable injection molding silicone suppliers allows Sourcifychina.com to ensure the quality of the products being sourced. By carefully selecting trusted suppliers, they establish credibility and build trust with their clients. This increases customer satisfaction and encourages businesses to continue using their services.
Additionally, receiving a free quota from these suppliers enables businesses to compare prices and negotiate better deals. The availability of multiple quotes helps them make informed decisions and choose the most suitable supplier based on their requirements.
By offering a free quota, Sourcifychina.com also simplifies the sourcing process for businesses. Instead of individually contacting multiple suppliers, customers can conveniently receive quotes and make comparisons through the platform. This streamlines the process, saving time and effort for businesses in finding the best injection molding silicone supplier.
Furthermore, Sourcifychina.com benefits from this collaboration as well. They gain valuable insights and feedback about the suppliers they work with, allowing them to continuously improve their selection criteria and further enhance the quality of their supplier network.
In summary, Sourcifychina.com offers a free quota from reliable injection molding silicone suppliers to attract customers, ensure product quality, allow price comparisons, simplify the sourcing process, and gain valuable insights. This approach benefits both the customers and Sourcifychina.com, fostering long-term relationships between businesses and suppliers while promoting their platform as a trusted sourcing solution.