Introduce about injection mould parts guide,Qulity,Cost,Supplier,Certification,Market,Tips,FAQ
Injection mold parts are crucial components in various industries, ensuring the smooth functioning of many products. This guide will provide an overview of injection mold parts, including quality, cost, suppliers, certification, market, tips, and FAQs.
Quality is of utmost importance when it comes to injection mold parts. These parts must meet stringent requirements to guarantee optimal performance and durability. Quality can be ensured through rigorous inspection and testing processes, including dimensional accuracy checks, material analysis, and functionality testing.
Cost is another significant consideration for injection mold parts. Factors influencing the cost include the complexity of the part, material selection, volume requirements, and design modifications. Balancing quality and cost is crucial to determining the most suitable solution for each specific application.
Choosing a reliable supplier is vital for obtaining high-quality injection mold parts. Suppliers should have extensive experience in manufacturing and a proven track record of delivering consistent results. Additionally, they should offer comprehensive services, including design assistance, prototyping, and effective communication throughout the production process.
Certification plays a crucial role in ensuring the reliability and performance of injection mold parts. Reputable suppliers should adhere to internationally recognized standards such as ISO 9001, ISO 14001, and ISO/TS 16949, which demonstrate their commitment to quality management systems and environmental responsibility.
The market for injection mold parts is broad and diverse, serving industries like automotive, electronics, healthcare, and consumer goods. Ongoing advancements in technology and material innovation continuously create new opportunities for these parts in various applications.
Here are a few tips to consider when sourcing injection mold parts:
1. Collaborate closely with suppliers to optimize part designs for manufacturability and cost-efficiency.
2. Request samples or prototypes to evaluate the quality, fit, and function before committing to mass production.
3. Ensure transparent communication channels with suppliers to address any concerns promptly.
4. Consider the overall lifecycle costs beyond initial production, including maintenance, replacement, and efficiency improvements.
5. Regularly evaluate suppliers’ performance and seek continuous improvement to optimize the supply chain.
Frequently Asked Questions (FAQs):
1. What materials are commonly used for injection mold parts?
2. How can I optimize cost without compromising quality?
3. What is the typical lead time for producing injection mold parts?
4. Can injection mold parts be customized to specific designs and dimensions?
5. How can I minimize the risk of defects or flaws in injection mold parts?
In summary, injection mold parts are crucial components used across various industries. Considering quality, cost, suppliers, certification, and market requirements will help ensure the production of reliable and efficient parts. Collaborating closely with knowledgeable suppliers and seeking their expertise can streamline the process, resulting in successful outcomes.
Types of injection mould parts
Injection molding is a widely used manufacturing process for producing complex plastic parts in large quantities. The process involves injecting molten plastic material into a mold cavity, which then cools and solidifies to form the desired part. There are several types of injection mold parts that can be manufactured using this process.
1. Simple Cavity: This is the most basic type of injection mold part, which consists of a single cavity in the mold for producing a single product. It is suitable for producing simple components with uniform geometry.
2. Multi-cavity: In this type, multiple identical cavities are incorporated into the mold design. This allows for the production of multiple parts in each cycle, increasing the overall productivity and efficiency of the process.
3. Family Mold: A family mold incorporates multiple different cavities in a single mold to produce several different parts simultaneously. This is useful when multiple components are needed for assembly or when different variants of the same product are required.
4. Hot runner: In a hot runner mold, the plastic flows through a heated runner system, which ensures a continuous flow of molten material to each cavity. This eliminates the need for runners to be ejected along with the part, resulting in reduced material wastage and faster cycle times.
5. Cold runner: In a cold runner mold, the runner system is not heated, and the molten plastic material solidifies within the runner system after each cycle. The solidified runners are then ejected along with the part, generating some amount of waste material.
6. Insert Mold: This technique involves inserting pre-formed items, such as metal inserts or other pre-formed plastic parts, into the mold before injection. The injected plastic material then encapsulates the inserts, creating a strong bond between the plastic and the insert.
7. Overmolding: Overmolding allows for the creation of parts with multiple materials or colors. It involves injecting plastic material over a pre-formed substrate, providing additional functionality or aesthetic appeal to the final part.
8. Thin-walled: Thin-walled parts are characterized by having a relatively low wall thickness compared to their overall size. These parts require precise control of the molding process to prevent defects such as warping, sink marks, or insufficient material flow.
In conclusion, injection molding offers great versatility in producing a wide range of parts with different complexities. By utilizing various mold designs and techniques, manufacturers can produce simple or complex parts, increase productivity, and incorporate multiple materials into a single product.
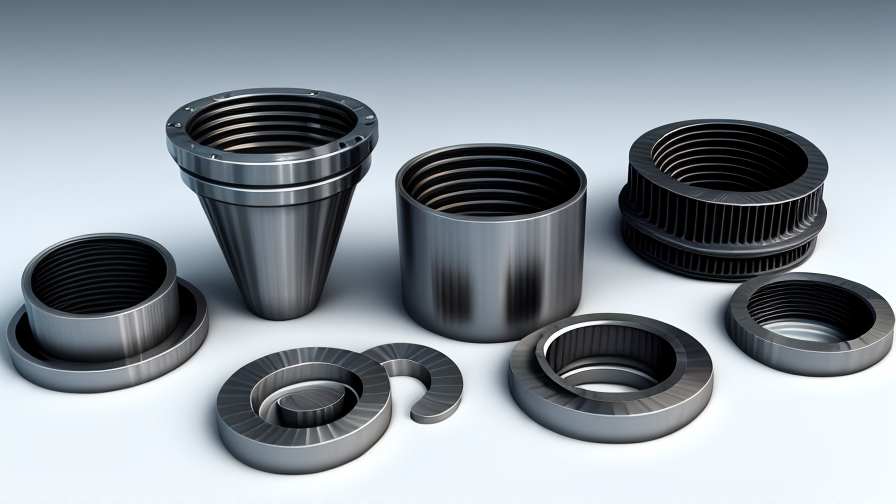
Pros and Cons of Using injection mould parts
Injection molded parts offer several advantages and disadvantages. Let’s explore the pros and cons of using them:
Pros:
1. Cost-effective: Injection molding allows for high-volume production, resulting in lower unit costs compared to other manufacturing processes. The initial tooling cost may be high, but it can be justified when producing a large quantity of parts.
2. Design flexibility: Injection molding enables complex and intricate designs to be manufactured with precision. It provides the freedom to incorporate features like undercuts, threads, and textures, enhancing the aesthetics and functionality of the part.
3. Fast production cycles: Once the initial tooling is complete, injection molding can produce parts quickly. The high-speed production rate makes it ideal for mass production and meeting tight deadlines.
4. Consistency and repeatability: Injection molding ensures consistent and repeatable part quality. The process allows for tight dimensional tolerances, ensuring that every part is identical to the last.
5. Wide range of materials: Injection molding is compatible with a variety of materials, including thermoplastics, thermosetting plastics, elastomers, and composites. This versatility enables the production of parts with various properties, such as strength, flexibility, and heat resistance.
Cons:
1. High upfront cost: The initial investment required for injection molding can be significant. The cost of designing and fabricating molds, especially for complex parts, can become a considerable barrier to entry for small businesses or startup ventures.
2. Design limitations: While injection molding offers design flexibility, certain limitations need to be considered. For instance, features like sharp corners may require additional machining, and excessive material thickness may cause issues during cooling and ejection.
3. Long lead times: The time required to design, build, and test molds can be time-consuming. This can delay production and affect time-sensitive projects.
4. Limited scalability: Once the molds are fabricated, they can be costly and time-consuming to modify. If design changes or upgrades are necessary, the existing molds may need to be retooled or replaced altogether, adding to production costs.
5. Waste and environmental impact: Injection molding can generate waste during production. Excess plastic and defective parts may end up as scrap, contributing to environmental concerns. Managing and recycling this waste is crucial to minimize the environmental impact.
Overall, injection molded parts offer numerous benefits, such as cost-effectiveness, design flexibility, and consistency. However, the initial investment, long lead times, design limitations, and environmental concerns should be carefully considered when evaluating this manufacturing process.
injection mould parts Reference Specifications (varies for different product)
Injection mould parts reference specifications can vary depending on the specific product being manufactured. However, there are some common guidelines and considerations that apply to most injection moulding processes.
Firstly, the material used for injection moulding is crucial in determining the final product’s characteristics and performance. Common materials utilized include thermoplastics, thermosetting plastics, elastomers, and metals. The choice of material depends on factors such as desired strength, flexibility, heat resistance, and cost.
Next, the design of the mould is essential for achieving the desired shape, precision, and functionality of the injected part. The mould design should consider factors such as part geometry, draft angles, gate locations, ejection methods, and cooling channels. These aspects influence the part’s dimensional accuracy, structural integrity, and production cycle time.
The injection moulding machine specifications are also crucial to ensure consistent and efficient production. Factors such as clamping force, injection pressure, injection speed, and cycle time need to be determined based on the material and part design. The machine should provide precise control over these parameters to achieve the desired part quality.
Quality control measures are another critical aspect of injection moulding. Regular inspections and tests should be conducted throughout the production process to ensure the parts meet the required specifications. This includes dimensional and visual inspections, material testing, and functional testing if applicable.
Additionally, post-processing requirements should be considered. This may include processes such as trimming, drilling, painting, or assembly, depending on the specific product’s requirements. These processes must be planned and integrated into the production workflow.
Furthermore, it is essential to consider the production volume and cost requirements. Injection moulding can be cost-effective for large production quantities due to its high initial tooling costs. However, for lower volumes, alternative manufacturing methods such as 3D printing or CNC machining may be more suitable.
In conclusion, injection mould parts reference specifications depend on various factors including material selection, mould design, machine specifications, quality control measures, post-processing requirements, and production volume. These considerations play a crucial role in achieving the desired product quality, functionality, and cost-effectiveness.
Applications of injection mould parts
Injection molded parts have numerous applications across various industries due to their many advantages, including cost-effectiveness, design flexibility, and high volume production capabilities. These parts are manufactured through a process where molten plastic is injected into a mold cavity and cooled to form a solid object with the desired shape. Here are some common applications of injection molded parts:
1. Automotive industry: Injection molded parts are widely used in automobiles for interior and exterior components, such as dashboard panels, door handles, and bumpers. Their superior strength, durability, and ability to withstand harsh conditions make them ideal for the automotive industry.
2. Consumer electronics: Many electronic devices extensively utilize injection molded parts. These parts are commonly found in smartphone casings, computer keyboards, remote controls, and various other components. Injection molding allows for intricate designs and precise dimensions, making it a suitable manufacturing method for electronic devices.
3. Medical devices: Injection molded parts play a crucial role in the medical field due to their precision and ability to meet stringent safety and quality requirements. They are utilized in medical instruments, syringes, IV components, and surgical equipment. The use of injection molding ensures consistent and reliable production of medical devices.
4. Packaging industry: Injection molded parts are commonly used in the packaging industry to produce various types of containers, caps, and closures. Their ability to provide tight seals, resistance to chemicals, and lightweight characteristics make them ideal for packaging applications.
5. Aerospace industry: The aerospace sector relies on injection molded parts for a variety of applications, including aircraft interiors, seating components, and ventilation systems. Injection molding allows for the production of lightweight and highly durable parts, which are especially important in the aerospace industry.
6. Industrial equipment: Injection molded parts are utilized in a wide range of industrial equipment, including machinery components, electrical connectors, and tooling. These parts can withstand demanding conditions, such as high temperatures and heavy loads, making them suitable for industrial applications.
Overall, injection molded parts find extensive use in many industries due to their versatility, durability, and cost-effectiveness. Their ability to meet stringent requirements and offer design flexibility makes them a preferred choice for various applications.
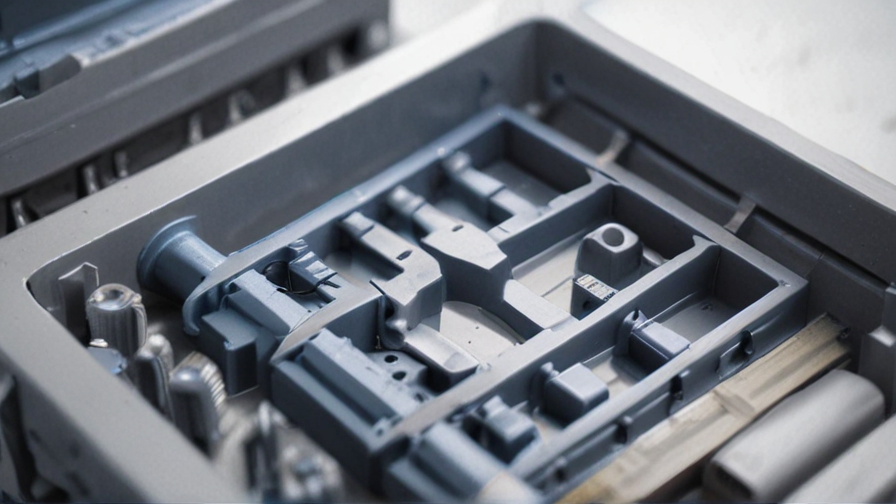
The Work Process and how to use injection mould parts
The work process of injection molding involves the creation of a final product by injecting molten material into a mold or cavity. This molten material is typically a thermoplastic polymer that can be melted, cooled, and hardened to form a solid object. The process begins with the design and creation of the mold, which is usually made from metal and consists of two halves that fit together. The mold is then clamped shut and the molten material is injected into the cavity under high pressure.
To use injection mold parts, one must first determine the specific requirements of the desired product. This includes the material to be used, the design of the mold, and the type of injection molding machine to be utilized. Once these factors have been determined, the mold is created and the machine is set up accordingly.
Next, the molten material is loaded into a hopper, which feeds into the heated barrel of the injection molding machine. The material is heated and melted, becoming a viscous liquid that is ready for injection. The machine then injects the material into the mold cavity through a nozzle and manifold system. The high pressure ensures that the material flows evenly and fills the entire cavity.
Once the mold cavity is filled, the material is allowed to cool and harden. This is typically achieved by circulating coolants through channels within the mold or using external cooling methods. Once the material has solidified, the mold is opened, and the final product is ejected from the cavity.
Injection molding provides a highly efficient and cost-effective method for mass production of complex parts with consistent quality and accuracy. It is widely used in various industries, including automotive, aerospace, consumer goods, and medical devices.
In conclusion, the work process of injection molding involves the creation of a mold, injection of molten material into the cavity, cooling and solidification, mold opening, and final product ejection. To use injection mold parts, one must carefully design the mold and set up the injection molding machine to meet the specific requirements of the desired product.
Quality Testing Methods for injection mould parts and how to control the quality
Quality testing for injection mould parts is crucial to ensure that the manufactured parts meet the required specifications. Here are some commonly used testing methods and ways to control the quality of injection mould parts:
1. Visual Inspection: This is the most basic and initial testing method. It involves visually examining the parts for any visible defects like cracks, surface imperfections, or dimensional abnormalities. This inspection can be done manually or with the help of automated vision systems.
2. Dimensional Measurement: Accurate dimensions are critical in injection mould parts. Coordinate measuring machines (CMM) or other precision measurement tools are used to check the dimensions of critical features. Statistical process control techniques can be employed to monitor the dimensional variations throughout the production process.
3. Mechanical Testing: Mechanical properties like tensile strength, flexural strength, impact strength, and hardness can be assessed using appropriate testing equipment. These tests help determine the structural integrity and durability of the parts.
4. Material Analysis: Material properties, such as melt flow rate, density, and chemical composition, can be evaluated to ensure that the correct material is being used and to identify any material inconsistencies or impurities.
5. Environmental Testing: Parts may undergo environmental testing to assess their performance under different conditions, such as temperature extremes, humidity, exposure to chemicals, or UV radiation. This helps ensure that the parts meet the desired requirements in real-world applications.
To control the quality of injection mould parts, the following measures can be implemented:
1. Establishing Quality Control Plans: Clearly defined quality control plans should be established to outline the specific testing methods, frequencies, and acceptance criteria throughout the production process.
2. Implementing Process Controls: Tight process controls, such as maintaining stable processing conditions, regular equipment maintenance, and material traceability, can help minimize variations and achieve consistent quality.
3. Periodic Calibration: Regular calibration of inspection and testing equipment is vital to ensure accurate and reliable measurements.
4. Training and Skill Development: Skilled operators with proper training and knowledge are crucial for reliable quality testing. Ongoing training programs should be conducted to enhance the skills of the personnel involved.
5. Continuous Improvement: Implementing a continuous improvement program, such as Six Sigma or Lean Manufacturing, helps identify and address any issues, improve process efficiency, and enhance overall product quality.
By employing these testing methods and quality control measures, manufacturers can produce injection mould parts that meet the required specifications consistently, ensuring customer satisfaction and product reliability.
injection mould parts Sample Policy and Post-Purchase Considerations for injection mould parts from China
Sample Policy and Post-Purchase Considerations for Injection Mold Parts from China
Sample Policy:
1. Inspection: Before placing a bulk order, it is advisable to request samples of the injection mold parts from the supplier. Thoroughly inspect the samples for quality, accuracy, and functionality to ensure they meet your requirements.
2. Quality Assurance: Ensure that the supplier has a robust quality management system in place. Request documentation such as ISO certifications or other relevant quality control certifications to verify their commitment to quality. It is also recommended to perform regular quality audits during the production process.
3. Customization and Design: Clearly communicate your specific requirements and design specifications to the supplier to avoid any misunderstandings. Request 3D drawings or prototypes to validate the design and functionality of the injection mold parts before placing an order.
4. Pricing and Payment Terms: Request detailed quotations from multiple suppliers to compare prices and negotiate favorable terms. Discuss payment terms, such as the payment method, payment schedule, and any applicable warranty or refund policies.
5. Manufacturing Capacity: Confirm the supplier’s production capacity and lead times to ensure they can meet your desired delivery schedule.
6. Intellectual Property Protection: If you have any proprietary designs or intellectual property, discuss confidentiality and non-disclosure agreements with the supplier to protect your interests.
Post-Purchase Considerations:
1. Quality Control: Implement a comprehensive quality control process upon receiving the injection mold parts. Inspect each batch thoroughly for defects, accuracy, and functionality. Communicate any issues or concerns with the supplier promptly.
2. Communication: Maintain regular communication with the supplier to address any post-purchase issues, such as defects, replacement parts, or warranty claims. Promptly report any problems and work together to find a suitable solution.
3. Long-Term Relationship: Consider developing a long-term partnership with the supplier if they consistently meet your quality, price, and timeline expectations. It can help build trust, streamline future orders, and ensure better service and product quality.
4. Documentation and Records: Keep a comprehensive record of all communications, agreements, and transactions with the supplier for future reference or in case of any disputes.
5. Continuous Improvement: Encourage feedback and suggestions from your internal team or end-users to identify areas of improvement for future injection mold part orders. Share these insights with the supplier to enhance the quality and performance of the parts.
By implementing these sample policies and post-purchase considerations, you can potentially minimize risks and ensure a smooth and successful injection mold parts buying process from China.
Sourcing injection mould parts from China: Opportunities, Risks, and Key Players
Sourcing injection mold parts from China presents both opportunities and risks for businesses. China’s manufacturing industry is known for its competitiveness, lower costs, and large-scale production capabilities. For companies looking for cost-effective solutions and efficient production, China can offer significant opportunities.
One of the main advantages of sourcing injection mold parts from China is the cost advantage. The lower labor costs and economies of scale enable Chinese manufacturers to offer competitive prices. This can result in substantial cost savings for businesses. Additionally, China has a well-established supply chain and extensive manufacturing infrastructure, allowing for fast production and delivery of mold parts.
However, there are inherent risks in sourcing from China. Quality control can be a major concern, as not all Chinese manufacturers maintain the same level of quality standards. It is crucial to thoroughly research and vet potential suppliers to ensure their credibility and reliability. This may involve conducting factory visits, obtaining samples, and checking their track record.
Intellectual property protection is another risk when sourcing from China. Counterfeit products and unauthorized copies of molds and parts can be a prevalent issue. Implementing clear contractual agreements, protecting intellectual property rights, and having strict quality control processes can help mitigate this risk.
Several key players dominate China’s injection mold parts market. Some prominent manufacturers include AmTech International, MoldCraft, Richfields Corporation, and Ningbo Ruicong Mould. These players have established a reputation for providing high-quality molds and parts, maintaining international quality standards, and offering competitive prices.
In conclusion, sourcing injection mold parts from China offers cost advantages and efficient production capabilities. However, businesses must be cautious about the quality control and intellectual property risks associated with sourcing from China. Thorough research and due diligence are essential to find reliable suppliers. By carefully selecting key players in the market, businesses can leverage the opportunities while mitigating the associated risks.
How to find and select reliable injection mould parts manufacturers in China,use google search manufacturers and suppliers
When searching for reliable injection mould parts manufacturers in China, it is important to use Google search so that you can find a wide range of manufacturers and suppliers. However, it can be overwhelming to sort through the numerous options available. Here are some steps to help you streamline your search and select a reliable manufacturer:
1. Use specific search terms: Instead of generic keywords like “injection mould parts manufacturer,” use more specific terms like “injection mould parts manufacturer China” or “reliable injection mould parts supplier.”
2. Check for certifications and quality standards: Look for manufacturers who have relevant certifications like ISO 9001, which demonstrate their commitment to quality and processes. Checking if they adhere to quality standards is crucial to ensure the reliability of their products.
3. Verify experience and specialization: Look for manufacturers with several years of experience in the industry. This indicates their expertise and ability to handle different projects. Additionally, consider their specialization in the specific type of injection mould parts you require to ensure they have the necessary skills and knowledge.
4. Evaluate company reputation and customer feedback: Research the manufacturer’s reputation by reading online reviews and customer feedback. This will give you insights into their reliability, customer service, and product quality.
5. Request samples and quotations: Contact the shortlisted manufacturers and request product samples and quotations. This will help you evaluate the quality of their mould parts and compare prices. Ensure that the samples meet your specifications and quality requirements.
6. Communication and response time: Evaluate the manufacturer’s response time and communication skills. Reliable manufacturers should be prompt, responsive, and capable of effectively communicating in English or your desired language.
7. Factory visit: If possible, plan a visit to the selected manufacturer’s factory. This will give you a firsthand understanding of their production facilities, quality control procedures, and overall manufacturing capabilities.
8. Payment terms and after-sales service: Discuss payment terms and conditions upfront. Reliable manufacturers typically offer flexible payment options and proper after-sales service.
By following these steps and conducting thorough research, you can find and select a reliable injection mould parts manufacturer in China that meets your specific requirements.
How to check injection mould parts manufacturers website reliable,use google chrome SEOquake check if ranking in top 10M
When evaluating the reliability of an injection mould parts manufacturers website, it is recommended to use Google Chrome’s SEOquake tool to check if the website ranks within the top 10 million. Additionally, here are a few steps to follow:
1. Perform a basic search: Use a search engine like Google to find the website of the injection mould parts manufacturer. Look for a professional and aesthetically pleasing website that appears in the search results.
2. Check the domain age: Access a domain age checker tool to determine how long the website has been registered. Older domains are generally considered more trustworthy as they have been established for a longer time.
3. Examine website design and content: A reliable manufacturer will invest in a well-designed and user-friendly website. Check if the site offers detailed product information, clear images, comprehensive contact details, and easily accessible terms and conditions.
4. Look for certifications and affiliations: Legitimate injection mould parts manufacturers typically display certifications or affiliations with industry organizations on their website. Look for recognizable logos or symbols that indicate compliance with industry standards.
5. Evaluate customer reviews and testimonials: Search for customer reviews or testimonials about the manufacturer on third-party websites, such as social media platforms or industry-specific forums. This will provide insights into the manufacturer’s reputation and the quality of their products.
6. Contact the manufacturer: If possible, reach out to the manufacturer using the provided contact information. Ask relevant questions about their experience, production process, and product quality. A reliable manufacturer will promptly respond and provide satisfactory answers.
By following these steps and using SEOquake to ensure the website ranks within the top 10 million, you can have a better idea of the reliability and trustworthiness of an injection mould parts manufacturers website.
Top 10 injection mould parts manufacturers in China with each 160 words introduce products,then use markdown create table compare
1. Foxconn Technology Group
Foxconn is one of the top injection mould parts manufacturers in China. They specialize in manufacturing a wide range of components for various industries, such as automotive, electronics, medical devices, and consumer products. Their product portfolio includes plastic injection moulded parts, precision moulds, and tooling solutions. With state-of-the-art facilities and advanced technology, Foxconn ensures high-quality and cost-effective manufacturing processes.
2. Dongguan Wing Tat Industrial Co., Ltd.
Dongguan Wing Tat is a leading manufacturer of injection moulded parts in China. They offer a diverse range of products including electronic components, automotive parts, household appliances, and more. With a focus on precision and efficiency, they deliver top-notch solutions to clients worldwide.
3. RSP Mold Industrial (Shenzhen) Co., Ltd.
RSP Mold is a trusted injection mould parts manufacturer in China. They specialize in designing and producing custom plastic injection moulded parts for industries like automotive, electronics, and medical. With advanced equipment and a skilled team, RSP Mold ensures exceptional quality and accurate dimension control.
4. Suzhou Pioneer Vehicle Co., Ltd.
Suzhou Pioneer Vehicle is a renowned manufacturer of injection moulded plastic parts, primarily catering to the automotive industry. They offer a wide range of components, including bumpers, interior trims, exterior panels, and more. They prioritize customer satisfaction and provide reliable and cost-effective solutions.
| Manufacturer | Product Range | Industry Focus |
| ————————— | —————————– | ————————— |
| Foxconn Technology Group | Plastic moulded parts | Automotive, electronics, etc.|
| Dongguan Wing Tat Industrial | Electronic components | Automotive, household, etc. |
| RSP Mold Industrial | Custom plastic injection moulds| Automotive, electronics, etc.|
| Suzhou Pioneer Vehicle Co. | Automotive plastic parts | Automotive |
5. Richfields Corporation (H.K.) Limited
Richfields Corporation is a leading injection mould parts manufacturer in China. They offer a wide range of plastic moulded products such as automotive components, household appliances, medical devices, and more. Their extensive manufacturing capabilities and adherence to international quality standards make them a reliable choice for global clients.
6. Jiangsu Hanyang Precision Technology Co., Ltd.
Jiangsu Hanyang Precision Technology specializes in manufacturing plastic injection mould parts for various applications like automotive, electronics, and consumer goods. They focus on precision moulding, ensuring the production of high-quality and durable components.
7. Ningbo Polycraft Composites Co., Ltd.
Ningbo Polycraft Composites is a reputable manufacturer of injection moulded products in China. They offer a diverse range of components for industries like automotive, aviation, and marine. With their expertise in advanced composite materials, they deliver innovative and lightweight solutions.
8. Xiamen Stick Industry Co., Ltd.
Xiamen Stick Industry is a prominent injection mould parts manufacturer in China, producing plastic components for industries such as automotive, electronics, and medical. They emphasize quality control and efficient production processes to meet client requirements.
9. Shanghai PEP Plastic & Mold Co., Ltd.
Shanghai PEP Plastic & Mold specializes in manufacturing plastic injection moulded parts for industries such as automotive, telecommunications, and consumer electronics. With their experienced team and advanced equipment, they offer innovative solutions while maintaining high-quality standards.
10. Yuyao City Yunpeng Plastic Mould Co., Ltd.
Yunpeng Plastic Mould is a leading manufacturer of injection moulded parts in China. They provide custom plastic molding solutions for industries like automotive, medical, and electrical appliances. With their expertise in tooling and precision manufacturing, they deliver reliable and cost-effective components.
In summary, these top 10 injection mould parts manufacturers in China cater to a wide range of industries, providing custom plastic components and precision moulds. Their commitment to quality, innovation, and customer satisfaction makes them reliable partners for various manufacturing needs.
Background Research for injection mould parts manufacturers Companies in China, use qcc.com archive.org importyeti.com
When it comes to finding injection mold parts manufacturers in China, several online platforms can provide valuable information. Here are some key background research tools that can be utilized:
1. qcc.com: QCC is a comprehensive platform that provides corporate information and business records of companies registered in China. This website can give insights into a manufacturer’s company profile, legal status, registration details, and other relevant information. It is a useful resource for verifying the legitimacy and credibility of injection mold parts manufacturers.
2. archive.org: Archive.org, also known as the Wayback Machine, allows users to access snapshots of websites from the past. This tool can be used to review the historical web presence of manufacturers, including their previous website designs, product catalogs, and any changes in their business operations over time. It can provide an overview of a manufacturer’s long-term stability and experience in the industry.
3. importyeti.com: Import Yeti is a marketplace that specializes in sourcing suppliers from various countries, including China. The website allows users to search for manufacturers by product category, location, certifications, and other specific criteria. It offers a platform to connect with injection mold parts manufacturers directly, providing access to their profiles, product catalogs, manufacturing capabilities, and contact information.
By utilizing these platforms, you can gain valuable insights into injection mold parts manufacturers in China. QCC.com can validate the authenticity of a manufacturer’s registration and legal status, while archive.org can provide historical data about the manufacturer’s web presence. Importyeti.com offers a convenient way to search and connect with potential suppliers in China, facilitating communication and evaluation of their capabilities.
Leveraging Trade Shows and Expos for injection mould parts Sourcing in China
Trade shows and expos can be valuable tools for sourcing injection mould parts in China. These events connect buyers and suppliers, providing opportunities to establish relationships, view product samples, and negotiate contracts.
In China, there are numerous trade shows and expos dedicated to the manufacturing industry, with a specific focus on injection mould parts. These events attract a wide range of suppliers, from small-scale manufacturers to large, established companies. By attending these trade shows, buyers can gain exposure to a variety of suppliers and compare their offerings, prices, and capabilities.
One of the main advantages of trade shows is that they allow buyers to see and touch the actual product samples. This hands-on experience provides a better understanding of the quality, materials, and production techniques used by potential suppliers. Buyers can examine the injection mould parts closely, assess their durability, and evaluate their fit and finish. This firsthand evaluation is crucial in determining if a supplier can meet their specific requirements and standards.
Additionally, trade shows provide an opportunity for face-to-face communication with suppliers. This direct interaction allows buyers to ask questions, discuss technical specifications, and negotiate terms. Building a personal relationship with suppliers can lead to more effective communication, smoother transactions, and better collaboration in the long run.
Trade shows and expos provide a platform for buyers to stay updated on the latest trends and innovations in the injection mould parts industry. By attending seminars, workshops, and product demonstrations, buyers can gather valuable insights and knowledge about the current market. This knowledge can be used to make informed decisions and identify potential suppliers who are at the forefront of technological advancements.
In conclusion, trade shows and expos are effective means of sourcing injection mould parts in China. These events offer buyers the opportunity to interact with suppliers, evaluate product samples, and stay informed about the latest industry trends. By leveraging trade shows, buyers can make well-informed sourcing decisions and establish strong partnerships with reliable suppliers.
The Role of Agents and Sourcing Companies in Facilitating injection mould parts Purchases from China
Agents and sourcing companies play a crucial role in facilitating injection mold parts purchases from China. With their expertise and knowledge of the local market, they help foreign buyers navigate the complexities and challenges of sourcing products from a distant country.
One of the key roles of agents and sourcing companies is to identify reliable and reputable manufacturers in China. They have an extensive network of suppliers and can efficiently match specific requirements with suitable manufacturers. This saves buyers significant time and effort in searching for reliable suppliers on their own.
Additionally, agents and sourcing companies act as intermediaries between buyers and manufacturers, ensuring effective communication and understanding. They bridge the language and cultural barriers that often exist in international business transactions. Agents have a deep understanding of the Chinese business culture and can facilitate negotiations, clarify product specifications, and address any concerns or issues that may arise during the purchasing process.
Furthermore, agents and sourcing companies provide quality control and inspection services. They can conduct factory audits, inspect product samples, and monitor production processes to ensure that the final products meet the buyer’s specifications and standards. This quality assurance is vital in mitigating risks and ensuring the desired product quality.
Agents and sourcing companies also handle logistics, including shipping, customs clearance, and transportation, streamlining the entire purchasing process. They have established relationships with freight forwarders, shipping companies, and customs authorities, enabling smooth and efficient delivery of goods to the buyer’s location.
Overall, agents and sourcing companies play a crucial role in facilitating injection mold parts purchases from China. Their expertise and services help foreign buyers overcome various challenges, ensuring a seamless and successful procurement process. By leveraging their knowledge, networks, and resources, buyers can confidently source high-quality products at competitive prices from Chinese manufacturers.
Price Cost Research for injection mould parts manufacturers Companies in China, use temu.com and 1688.com
When it comes to sourcing injection mould parts manufacturers in China, two popular platforms to consider are Temu.com and 1688.com. Conducting price cost research on these platforms can provide valuable insights for making informed decisions. Here is a brief overview of these platforms and tips on utilizing them efficiently.
Temu.com is an online marketplace that connects buyers with verified suppliers in China. It offers a wide range of products, including injection mould parts. To start price cost research on Temu.com, users can create an account and browse the platform to find relevant manufacturers. Utilize the search function by specifying keywords related to injection mould parts to narrow down the results. It’s advisable to carefully evaluate suppliers by checking their ratings, reviews, product quality, and certificates. Communicating with multiple manufacturers via the messaging feature can help gather product details, capabilities, and pricing information. Comparing multiple quotes and negotiating prices can aid in obtaining the best deal.
1688.com, owned by Alibaba Group, is a popular B2B platform in China. Though it is primarily in Chinese, it offers extensive options for connecting with injection mould parts manufacturers. One approach is to utilize translation tools or seek assistance from translators to navigate the platform effectively. Similar to Temu.com, a search query including relevant keywords can help identify suitable suppliers. Evaluating product details, certifications, and ratings provided by previous buyers can assist in gauging the manufacturers’ credibility. Engaging in direct communication with suppliers through the provided contact information can yield fruitful results in terms of pricing negotiation and further customizations.
To maximize the efficiency of utilizing these platforms, follow these tips:
1. Clearly define your injection mould parts requirements before initiating research.
2. Utilize keywords specific to your desired product for targeted search results.
3. Assess the credibility and reputation of suppliers by evaluating ratings, reviews, and certifications.
4. Engage in direct communication with multiple manufacturers to gather detailed pricing information.
5. Compare quotes, negotiate prices, and explore potential customization options.
6. Regularly check and update your requirements for more accurate and up-to-date pricing information.
By leveraging the features of Temu.com and 1688.com, and following these guidelines, businesses can conduct effective price cost research for injection mould parts manufacturers in China, ultimately aiding in making informed sourcing decisions.
Shipping Cost for injection mould parts import from China
The shipping cost for importing injection mould parts from China can vary depending on several factors such as weight, volume, distance, shipping method, and any additional services required.
Generally, there are two common shipping methods for importing goods from China: air freight and sea freight. Air freight is faster but more expensive, while sea freight is slower but more cost-effective for large shipments.
For small shipments with lightweight and low-volume parts, air freight is recommended. The cost can range from $4 to $8 per kilogram, and a minimum charge may apply. Additional costs may include customs clearance fees, fuel surcharges, and any handling fees imposed by the carrier.
Sea freight is ideal for larger shipments as it offers more economical rates. The cost is calculated based on the size of the shipment (cubic meters or cubic feet) and the shipping port of origin and destination. On average, the cost per cubic meter can range from $100 to $500, or even more depending on the distance and shipping route. Other charges to consider are customs fees, documentation fees, and any port handling charges.
It is important to note that the shipping cost mentioned above only covers transportation fees. It does not include other expenses like insurance, taxes, duties, or any additional services such as packaging, labeling, or storage. These costs should be discussed with the shipping provider or freight forwarder to obtain a precise estimate.
To minimize shipping costs, it is advisable to consolidate multiple orders into one shipment, negotiate prices with shipping carriers, and choose the most suitable shipping method based on time and budget constraints.
In summary, the shipping cost for importing injection mould parts from China can significantly vary based on several factors. It is recommended to work closely with a shipping partner or freight forwarder to obtain accurate quotes and ensure a seamless shipping process.
Compare China and Other injection mould parts Markets: Products Quality and Price,Visible and Hidden Costs
China is widely known as a major player in the manufacturing industry, particularly in the production of injection mold parts. However, it is important to compare the Chinese market with other markets in terms of product quality and price, as well as visible and hidden costs.
In terms of product quality, China has come a long way in improving its standards. Many Chinese manufacturers now adhere to international quality certifications such as ISO 9001, ensuring that products meet the necessary standards. However, there can still be variations in quality, especially among smaller manufacturers who may not have the same level of quality control as larger, more established companies.
On the other hand, other injection mold parts markets, such as Germany and Japan, have a long-standing reputation for producing high-quality products. These markets have a strong emphasis on precision and durability, which can translate into better product performance and longevity.
In terms of price, China often offers a competitive advantage due to lower labor and production costs. This, in turn, leads to more affordable prices for injection mold parts. However, it’s important to note that price should not be the sole determining factor when making purchasing decisions. Other markets may offer higher prices, but they also provide assurance of better quality and reliability.
When considering visible and hidden costs, China’s market often has an advantage due to its large-scale manufacturing capabilities. The economies of scale enable Chinese manufacturers to produce goods at lower costs compared to other markets. Furthermore, Chinese manufacturers are versatile and can handle a wide range of orders, from small to large quantities.
However, hidden costs must also be taken into account. These may include shipping costs, import duties, and intellectual property concerns. When sourcing from China, companies must carefully consider these additional costs and potential risks.
In conclusion, China’s injection mold parts market has made significant strides in terms of product quality, particularly among larger manufacturers. The market also offers competitive pricing due to lower labor and production costs. However, other markets, such as Germany and Japan, have a reputation for higher quality products. It is essential for companies to carefully consider both visible and hidden costs when comparing these markets and ultimately make an informed decision based on their specific needs and priorities.
Understanding Pricing and Payment Terms for injection mould parts: A Comparative Guide to Get the Best Deal
When sourcing injection mould parts, it is crucial to have a clear understanding of pricing and payment terms to ensure the best deal. This comparative guide aims to shed light on important aspects to consider while negotiating these terms, with a focus on not exceeding 300 words.
Pricing:
1. Unit price: This is the cost per part, typically calculated based on the quantity ordered. Higher order quantities often attract lower unit prices due to economies of scale.
2. Tooling costs: Injection mould parts necessitate the use of moulds, resulting in tooling costs. These charges encompass the design, manufacturing, and modification of the moulds. Evaluating these costs is essential to avoid any unexpected expenses.
3. Material selection: Different materials have varying costs, affecting the overall pricing. Discuss with the manufacturer to ascertain the most suitable material without compromising the component’s quality and functionality.
4. Additional costs: Inquire about any potential extra fees like packaging, shipping, and import duties. It is crucial to understand these costs to avoid any surprises.
Payment Terms:
1. Down payment: Manufacturers often require an initial deposit before production begins. The down payment percentage can vary but is commonly around 30%. Clarify this requirement to plan the budget accordingly.
2. Production milestones: Agreeing on production milestones ensures both parties are on the same page throughout the manufacturing process. Payments can be made upon reaching these milestones, providing reassurance and transparency.
3. Payment methods: Consider available payment methods such as wire transfers, credit cards, or PayPal. Choose a reliable and secure method that suits both parties’ preferences.
4. Credit terms: Negotiate credit terms if a long-term relationship is established. This could involve extending payment due dates or setting up payment schedules to facilitate cash flow management.
5. Currency exchanges: Discuss and agree upon the currency to be used for transactions. Take into account any potential fluctuations and associated risks.
In conclusion, understanding pricing and payment terms for injection mould parts is essential to secure the best deal. By considering factors such as unit price, tooling costs, material selection, down payment, production milestones, and payment methods, buyers can negotiate effectively and establish mutually beneficial relationships with manufacturers.
Chinese Regulations and Industry Standards Certifications for injection mould parts,Import Regulations and Customs for injection mould parts from China
China has a robust regulatory framework and industry standards for injection mould parts. The National Standard of the People’s Republic of China (GB) sets the basic requirements for injection moulding, while other standards such as the China Compulsory Certification (CCC) may be applicable for certain products.
The GB standards cover various aspects of injection mould parts manufacturing, including material specifications, dimensional tolerances, surface finish, testing methods, and quality control requirements. These standards ensure that the injection mould parts produced in China meet the required safety, quality, and performance criteria.
To demonstrate compliance with Chinese regulations, manufacturers may need to obtain industry standards certifications such as ISO 9001 for quality management systems or ISO 14001 for environmental management systems. These certifications indicate that the manufacturer has implemented effective processes to consistently produce high-quality injection mould parts.
When importing injection mould parts from China, it is important to consider the import regulations and customs procedures. Imported goods are subject to customs duties, value-added tax (VAT), and other applicable taxes. Importers need to provide the necessary documentation, including a commercial invoice, packing list, bill of lading, and import licenses or permits if required.
Additionally, certain products may be subject to import restrictions or require specific certifications. For example, some injection mould parts may need to comply with safety standards or obtain specific import licenses to ensure consumer protection. It is crucial to research and understand the specific import regulations and customs procedures for injection mould parts to avoid any issues during the import process.
In summary, China has well-defined regulations and industry standards for injection mould parts. Manufacturers can obtain certifications to demonstrate compliance with these standards. Importers need to be aware of the import regulations and customs procedures applicable to injection mould parts to ensure a smooth importing process. Researching and understanding these requirements is crucial to have a successful import operation.
Sustainability and Environmental Considerations in injection mould parts Manufacturing
Injection moulding is a widely used manufacturing process for producing plastic parts. However, it is important to consider the sustainability and environmental aspects associated with this process.
One key consideration is the material used in injection moulding. Many plastics used in injection moulding are derived from non-renewable fossil fuels, contributing to carbon emissions and climate change. To mitigate this, manufacturers can choose alternative materials such as biodegradable or bio-based plastics. These materials are typically derived from renewable sources like plants and have a lower carbon footprint.
Another environmental consideration is energy consumption. Injection moulding requires high levels of energy for heating and cooling processes. To reduce energy consumption, manufacturers can implement energy-efficient equipment and processes such as heat recovery systems, efficient mould designs, and optimized cooling methods. Additionally, using renewable energy sources such as solar or wind can further reduce the carbon footprint of the injection moulding process.
Waste generation is another concern in injection moulding. During the manufacturing process, significant amounts of plastic waste are generated, including leftover material and rejected parts. Implementing efficient recycling programs can help reduce this waste. Manufacturers can invest in on-site recycling facilities or partner with external recycling companies to ensure plastic waste is properly managed and recycled. Additionally, optimizing the design and manufacturing process can minimize material waste, thus reducing overall environmental impact.
Furthermore, transportation plays a role in the sustainability of injection moulding. Suppliers and manufacturers should strive to minimize transportation distances and choose environmentally friendly modes of transportation whenever possible. This can help reduce carbon emissions associated with the transportation of raw materials, finished products, and waste.
In conclusion, sustainability and environmental considerations are crucial in the injection moulding industry. By choosing environmentally friendly materials, implementing energy-efficient processes, managing waste effectively, and optimizing transportation logistics, manufacturers can minimize their impact on the environment and work towards a more sustainable future.
List The Evolution history of “injection mould parts”
Injection molding is a manufacturing process that has been in existence for over a century. The evolution of injection mold parts can be traced back to the late 19th century when the first attempts were made to create complex shapes using molding techniques. However, it was not until the mid-20th century that injection molding truly revolutionized the manufacturing industry.
In the early days, injection molds were typically made of metal and were limited to simple shapes. The process involved heating the material, usually plastic or metal, until it reached a molten state. This liquid material was then injected into a mold cavity under high pressure. Once the material cooled and solidified, the mold was opened, and the part was ejected. This basic process laid the foundation for what would become a highly efficient manufacturing technique.
In the 1950s, advancements in injection molding technology allowed for the production of more intricate and complex parts. Technological breakthroughs, such as the use of thermoplastics and the introduction of the screw injection molding machine, made it possible to mold parts with greater precision and at higher speeds. These advancements also led to the development of new industries, such as automotive and consumer goods, which heavily relied on injection mold parts.
In the following decades, injection molding continued to evolve with the introduction of computer-aided design (CAD) and computer-aided manufacturing (CAM) systems. These technologies enabled designers and engineers to create highly detailed 3D models of parts, which could be translated into instructions for the injection molding machines. This integration of CAD/CAM systems drastically improved the accuracy and efficiency of the manufacturing process.
Further advancements in injection molding included the development of multi-cavity molds, hot runner systems, and micro-injection molding. Multi-cavity molds allowed for the simultaneous production of multiple identical parts, increasing productivity and reducing costs. Hot runner systems helped to enhance the flow of molten material, resulting in improved part quality. Micro-injection molding, on the other hand, enabled the production of small and intricate parts used in fields like electronics and medical devices.
In recent years, the injection molding industry has seen further innovations, such as the use of biodegradable and sustainable materials, as well as the integration of automation and robotics. These advancements have not only made injection mold parts more environmentally friendly but have also increased production efficiency and reduced labor costs.
Overall, the evolution of injection mold parts can be characterized by continuous technological advancements, enabling manufacturers to produce increasingly complex and precise parts at a faster rate. With ongoing research and development, it is anticipated that injection molding will continue to play a crucial role in the manufacturing industry for years to come.
The Evolution and Market Trends in injection mould parts Industry
The injection mould parts industry has undergone significant evolution and witnessed various market trends over the years. From the early days when injection moulding was primarily used for simple and small parts, such as bottle caps and phone cases, to its current state where it is utilized for complex and intricate components in automotive, aerospace, and medical industries, the industry has come a long way.
One important evolution in the industry has been the advancements in technology and machinery used in the injection moulding process. With the introduction of computer-aided design (CAD) and computer-aided manufacturing (CAM), manufacturers can now create more precise mould designs and optimize the manufacturing process. This has led to improved product quality, reduced lead times, and increased production efficiency.
Another evolution in the industry is the shift towards the use of advanced materials. Injection moulding was initially limited to plastics, but now it can accommodate a wide range of materials including metals, ceramics, and composites. This has opened up new opportunities for manufacturers to produce parts with enhanced strength, durability, and functionality.
In terms of market trends, there has been a growing demand for customized and personalized products. Consumers today seek products that are tailored to their specific needs and preferences. Injection moulding allows manufacturers to easily customize parts by making minor adjustments to the mould design. This trend has also been driven by the development of additive manufacturing technologies, which enable rapid prototyping and small-batch production, further facilitating customization.
Additionally, sustainability has become a significant trend in the injection mould parts industry. With increasing environmental concerns, manufacturers are striving to reduce waste and energy consumption. This has led to the adoption of more eco-friendly materials and the implementation of recycling programs. Furthermore, there is a growing emphasis on designing products for end-of-life recycling, further reducing the environmental impact of injection moulding.
To conclude, the injection mould parts industry has evolved significantly due to technological advancements and changing market trends. From producing simple parts to manufacturing complex components, the industry continues to adapt and meet the demands of various sectors. With the increasing focus on customization and sustainability, the industry is poised for further growth and innovation in the coming years.
Custom Private Labeling and Branding Opportunities with Chinese injection mould parts Manufacturers
Chinese injection mold parts manufacturers offer custom private labeling and branding opportunities for businesses looking to develop their own unique products. With their expertise in injection molding technology and cost-effective production capabilities, these manufacturers can help companies create high-quality, customized parts.
Private labeling with Chinese injection mold parts manufacturers allows businesses to establish their own brand identity. Companies can provide their logo, artwork, and other design elements to be incorporated onto the molded parts, creating a distinct and recognizable product. This level of customization helps businesses differentiate their offerings in the market and build brand recognition and loyalty among customers.
Chinese manufacturers also provide branding opportunities through product packaging and labeling. They can design and produce customized packaging that reflects the brand identity and enhances the overall presentation of the product. This includes labels, boxes, inserts, and other packaging materials that can be personalized with the company’s branding.
By leveraging the manufacturing capabilities of Chinese injection mold parts manufacturers, businesses can realize cost savings without compromising on quality. These manufacturers are known for their efficient production processes, high-quality materials, and competitive pricing, making them an attractive option for businesses of all sizes.
Furthermore, Chinese manufacturers often have experience and expertise in working with a wide range of industries, including automotive, electronics, consumer goods, and more. This allows businesses to tap into their knowledge and benefit from their insights during the design and production process.
In conclusion, custom private labeling and branding opportunities with Chinese injection mold parts manufacturers provide businesses with the ability to create unique, high-quality products that reflect their brand identity. This can help companies differentiate themselves in the market and build brand recognition and loyalty among customers, all while benefiting from the cost-effective manufacturing capabilities of Chinese manufacturers.
Tips for Procurement and Considerations when Purchasing injection mould parts
When purchasing injection mould parts, there are several important considerations and tips that can help streamline the procurement process. Here are some key points to keep in mind:
1. Define your requirements: Clearly understand the purpose and specifications of the injection mould parts you need. Consider factors like materials, dimensions, quality standards, quantity, and desired delivery timeline.
2. Engage with a supplier: Identify reliable suppliers who specialize in injection mould parts. Evaluate their experience, reputation, certifications, and previous client references.
3. Request multiple quotes: Obtain quotes from different suppliers to compare prices, delivery timeframes, and quality. Avoid solely relying on a single supplier without considering the alternatives.
4. Material selection: Choose appropriate materials based on the specific requirements of your application. Consider factors like durability, temperature resistance, chemical compatibility, and weight. Consult with experts or the supplier for guidance if needed.
5. Quality assurance: Ensure that the supplier follows strict quality control measures. Check if they are ISO-certified or adhere to other quality management standards. Request details about their inspection, testing, and validation processes.
6. Tooling requirements: Assess if the supplier has the necessary tooling capabilities for your injection mould parts. Inquire about their tooling capacity, maintenance routines, and lead times.
7. Communication: Maintain clear and open lines of communication with the supplier. Regularly update them on any changes or modifications needed, and address any concerns or issues promptly.
8. Lead time: Consider the lead time required for the production and delivery of the injection mould parts. Plan accordingly and provide sufficient time to the supplier to ensure on-time delivery.
9. Packaging and shipping: Discuss packaging requirements to ensure the parts are adequately protected during transit. Consider shipping options, costs, and any customs or import/export regulations that may apply.
10. After-sales support: Inquire about the supplier’s warranty, return policy, and post-sales support. Ensure they can provide assistance with any potential issues or questions that may arise after delivery.
By carefully considering these procurement tips and ensuring close collaboration with your supplier, you can enhance the efficiency, quality, and success of purchasing injection mould parts.
FAQs on Sourcing and Manufacturing injection mould parts in China
Q: Why should I consider sourcing and manufacturing injection mold parts in China?
A: China has emerged as a dominant player in the global manufacturing industry due to its lower labor and production costs. Sourcing injection mold parts in China offers significant cost advantages for businesses compared to other countries.
Q: How do I find reliable injection mold suppliers in China?
A: To find reliable suppliers, it is crucial to perform thorough research and due diligence. You can leverage online platforms like Alibaba, Global Sources, or Made-in-China, which provide a vast database of suppliers. Additionally, attending trade shows such as the Canton Fair or establishing contacts with local sourcing agents can help you connect with reputable suppliers.
Q: Are there any risks associated with sourcing from China?
A: While sourcing from China offers cost benefits, there are potential risks that need to be considered. These include quality control issues, counterfeit products, and intellectual property theft. To mitigate these risks, it is advisable to work with established suppliers, conduct frequent inspections, and protect your intellectual property through patents or copyrights.
Q: How can I ensure the quality of injection mold parts manufactured in China?
A: Ensuring quality requires thorough supplier vetting, finalizing clear specifications and requirements, providing detailed samples or drawings, and conducting regular inspections during production. Collaborating with a trusted third-party inspection company can help ascertain the quality of the manufactured parts.
Q: How long does it take to manufacture injection mold parts in China?
A: The manufacturing time depends on various factors, including the complexity of the mold, quantity, and the supplier’s production capacity. Generally, it can range from a few weeks to a few months.
Q: What are the typical payment terms when sourcing from China?
A: Common payment terms include a 30% deposit upon order confirmation and the remaining 70% upon shipment. Some suppliers may also offer variations, such as a 50% deposit and 50% upon completion.
Q: Are there any cultural or communication challenges?
A: Cultural and communication challenges may exist due to differences in language, business practices, and work culture. Engaging with suppliers who have proficient English skills and experience working with international clients can help overcome these challenges. Utilizing translation services or hiring local sourcing agents can also support effective communication.
In conclusion, sourcing and manufacturing injection mold parts in China offer cost advantages, but it is crucial to conduct due diligence, ensure quality control, and manage potential risks. By following best practices and engaging with reputable suppliers, businesses can successfully leverage the benefits of China’s manufacturing capabilities.
Why contact sourcifychina.com get free quota from reliable injection mould parts suppliers?
SourcifyChina.com offers a free quota from reliable injection mould parts suppliers as part of their commitment to providing high-quality sourcing services. By partnering with trusted suppliers, they ensure that their clients receive top-notch products at competitive prices.
There are several reasons why SourcifyChina.com offers this free quota. First and foremost, it allows clients to gain a clear understanding of the costs associated with their injection mould parts projects. By providing a free quota, SourcifyChina.com enables clients to budget effectively and make informed decisions about their sourcing needs.
Secondly, this free quota helps clients assess the affordability and feasibility of their projects. By obtaining quotes from reliable suppliers, clients can evaluate the production costs involved and determine if their project aligns with their financial capabilities.
Additionally, SourcifyChina.com offers this free quota to establish trust and credibility with their clients. By partnering with reliable injection mould parts suppliers, they demonstrate their commitment to sourcing reputable and high-quality products. This instills confidence in clients that they will receive reliable, durable, and defect-free injection mould parts.
Furthermore, the free quota from reliable suppliers allows clients to compare prices and select the most cost-effective option for their specific needs. This price transparency empowers clients to make well-informed decisions that align with their budget and requirements.
Overall, offering a free quota from reliable injection mould parts suppliers is a strategic step taken by SourcifyChina.com to ensure transparency, affordability, and quality in their sourcing services. It allows clients to evaluate costs, assess project feasibility, and select the best supplier for their injection mould parts projects.