Introduce about insert molding guide,Qulity,Cost,Supplier,Certification,Market,Tips,FAQ
Insert molding is a popular manufacturing technique that combines plastic injection molding and insert placement. This process allows for the incorporation of pre-formed inserts, such as metal or plastic components, into a plastic part during the molding cycle. Here is a comprehensive guide to help you understand all aspects of insert molding.
Quality is a crucial consideration in insert molding. It ensures that the inserts are accurately placed and firmly bonded to the plastic, resulting in a strong and durable final product. High-quality insert molding also reduces the risk of part failure or defects.
Cost is another important aspect to consider. The cost of insert molding varies depending on factors such as the complexity of the part design, the selected materials, and the volume of production. However, insert molding often offers cost advantages over traditional post-molding assembly methods by eliminating the need for additional assembly steps and reducing labor costs.
Choosing a reliable supplier is essential for successful insert molding projects. Look for suppliers with extensive experience in insert molding and a track record of producing high-quality parts. Make sure they have the necessary equipment, expertise, and capacity to meet your specific requirements.
Certification is an important consideration, particularly if you operate in highly regulated industries such as medical or automotive. Ensure that your supplier adheres to relevant industry certifications, such as ISO 9001 or ISO 13485, to guarantee compliance with quality and safety standards.
The market for insert molding is extensive and diverse. It covers various industries, including automotive, electronics, medical devices, consumer goods, and more. The versatility and efficiency of insert molding make it a preferred manufacturing method in many sectors.
Here are a few tips for successful insert molding projects:
1. Properly design the part and insert for easy insertion and optimal performance.
2. Choose the right materials to ensure compatibility between the insert and plastic.
3. Optimize the molding process by adjusting parameters like temperature, pressure, and cooling time.
Frequently Asked Questions (FAQ):
1. What types of inserts can be used in insert molding?
Ans: Inserts can be made of metal, plastic, or even ceramics.
2. What are the benefits of insert molding?
Ans: It reduces assembly costs, improves product quality, and enhances design flexibility.
3. How long does the insert molding process take?
Ans: The duration depends on the complexity of the part and the production volume but generally ranges from seconds to minutes.
In conclusion, insert molding is a versatile manufacturing technique that offers numerous benefits in terms of quality, cost, and design flexibility. Choosing a reputable supplier, considering certification requirements, and optimizing the molding process are key factors to ensure successful insert molding projects.
Types of insert molding
Insert molding is a process that involves injecting a molten material around an insert or substrate to create a finished product that combines the insert and the molded material into one integrated unit. It is commonly used to enhance the functionality, durability, and aesthetics of products in various industries such as automotive, electronics, medical, and telecommunications. There are several types of insert molding, each offering unique advantages and suitable for specific applications.
1. Overmolding: This type of insert molding involves encapsulating a substrate with a second material to create a soft-grip surface, improve shock absorption, or add color contrast. It is frequently used in the production of handle grips, tool grips, and other applications that require improved ergonomics.
2. Threaded insert molding: In this type of insert molding, metal or plastic inserts with internal threads are placed into the mold before the injection process. The molten material surrounds and bonds with the insert, forming a strong threaded connection. Threaded insert molding is commonly used in manufacturing electronic enclosures, appliance components, and automotive parts.
3. Electrical insert molding: This method is utilized to integrate electrical components such as connectors, sensors, and terminals into a molded part. It provides a sealed and reliable connection between the electrical component and the molded structure, protecting against moisture, dust, and other environmental factors. Electrical insert molding is widely used in the production of connectors, switches, and electronic housing.
4. Heat insert molding: Heat insert molding involves inserting metallic heat sinks or thermally conductive materials into the mold before injecting the molten material. It ensures efficient heat dissipation in applications such as LED lighting, power electronics, and automotive components that generate heat during operation.
5. Metal insert molding: This technique combines metal inserts with plastic molding to create strong and durable components. Metal inserts can improve strength, reinforce critical areas, or add weight to specific parts where needed. Metal insert molding is commonly employed in automotive engines, bearings, and other heavy-duty applications.
6. Component insert molding: This type of insert molding involves the integration of various components, such as fasteners, bearings, magnets, or springs, into a molded part. It simplifies assembly processes, reduces manufacturing time, and increases overall product reliability.
7. Screw insert molding: Screw insert molding is used to create parts with threaded holes or spaces to accommodate screws or bolts for assembly purposes. It is commonly employed in the manufacturing of plastic enclosures, housings, and components that require secure fastening.
Each type of insert molding offers specific benefits, including improved functionality, enhanced aesthetics, increased strength, reduced assembly time, and cost-effective production. Manufacturers can choose the most appropriate type of insert molding based on their specific requirements and desired outcomes.
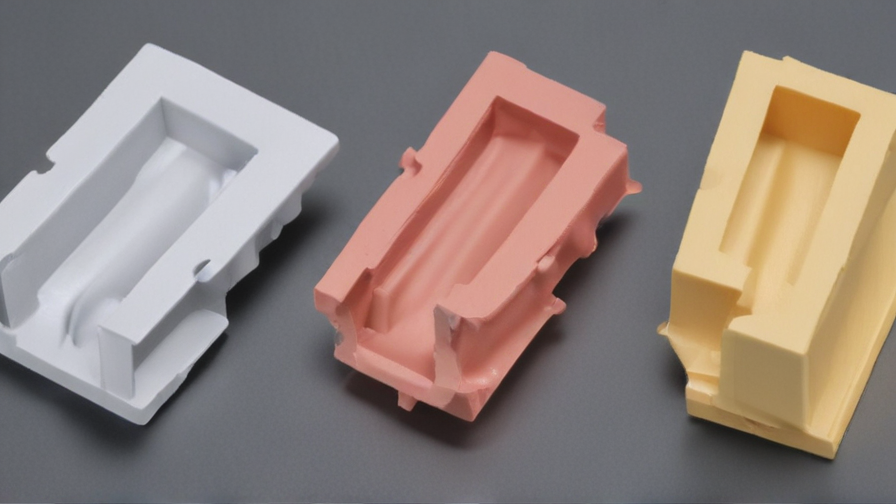
Pros and Cons of Using insert molding
Insert molding is a process that involves inserting a separate component or part during the injection molding process, resulting in a single, integrated part. This technique offers certain advantages and disadvantages, which are summarized below:
Pros:
1. Cost-effective: By combining multiple manufacturing steps into one process, insert molding can help reduce production costs. It eliminates the need for additional assembly steps, reduces labor costs, and minimizes the risk of component misalignment or damage.
2. Enhanced part functionality: Insert molding allows for the integration of different materials, such as metal or electronic components, into a plastic part. This integration enhances the functionality of the final product and provides additional strength, conductivity, or insulation properties.
3. Improved part durability: The bond between the insert and the plastic material in insert molding results in a more sturdy and durable part. This is particularly beneficial for components that may experience high-stress conditions or require extra strength.
4. Design flexibility: Compared to other manufacturing methods, insert molding offers greater design flexibility. Manufacturers can incorporate various insert types, shapes, and sizes into complex geometries, allowing for innovative and customized product designs.
Cons:
1. Limited choice of materials: The choice of insert materials may be restricted due to the requirements of the injection molding process. For example, the high temperatures involved might limit the range of compatible metals or components that can be used.
2. Increased upfront investment: The initial costs for insert molding can be higher compared to traditional molding techniques. Tooling costs and the need for specialized equipment may require a higher upfront investment, especially for small production runs.
3. Longer production cycles: The process of insert molding typically takes longer due to the additional steps involved, such as placing the inserts and ensuring proper adhesion. This may result in longer lead times for production.
4. Design limitations: Insert molding may pose certain design limitations, such as restrictions on the location or orientation of inserts. The geometry and accessibility of the part may impact the feasibility of insert molding, requiring careful consideration during the design phase.
In conclusion, insert molding offers advantages like cost-effectiveness, improved functionality, durability, and design flexibility. However, it also comes with limitations such as material restrictions, increased upfront costs, longer production cycles, and design limitations. These factors should be carefully considered and evaluated to determine if insert molding is the right manufacturing process for a specific application.
insert molding Reference Specifications (varies for different product)
When it comes to insert molding, the reference specifications can vary depending on the specific product being manufactured. Insert molding is a process that combines metal or plastic inserts with the mold during the injection molding process, resulting in a final product that harmoniously integrates different components.
In terms of dimensions, the reference specifications might include the size and shape of the inserts, as well as the overall dimensions of the finished product. These specifications ensure that the inserts fit precisely into the mold and that the final product meets the required size requirements.
The choice of materials is another crucial aspect of insert molding. The reference specifications will typically outline the type of insert material, such as metal or plastic, and the appropriate molding material. This ensures compatibility between the two materials and facilitates efficient bonding during the molding process.
Surface finish requirements are also commonly included in the reference specifications. This relates to the appearance and texture of the final product. Certain industries may have specific surface finish requirements for aesthetic or functional purposes, and these specifications must be followed accurately during the manufacturing process.
The reference specifications may also cover specific mechanical or electrical requirements, depending on the intended application of the final product. These requirements might include factors such as strength, conductivity, resistance, or any other performance-related specifications necessary for the product to function as intended.
Additionally, the reference specifications might address any specific quality or testing standards that the product needs to adhere to. This ensures that the insert molded product meets the necessary quality and reliability standards before it reaches the market.
It is important to note that the reference specifications for insert molding can vary significantly from one product to another. Manufacturers and designers should refer to the specific requirements provided by the customer, industry standards, or any relevant regulations to define the most suitable specifications for their insert molding project.
In conclusion, insert molding reference specifications encompass various aspects such as dimensions, material choices, surface finish requirements, mechanical/electrical specifications, and quality/testing standards. Adhering to these specifications ensures the successful manufacturing of insert molded products that meet the desired performance, appearance, and reliability requirements.
Applications of insert molding
Insert molding is a widely used manufacturing process that combines multiple components into a single finished product. It offers numerous advantages in terms of efficiency, cost savings, and product performance. Here are some prominent applications of insert molding:
1. Electrical Connectors: Insert molding is extensively applied in the production of electrical connectors. It allows for the integration of metal pins or sockets with insulating materials, providing excellent electrical conductivity, mechanical strength, and resistance to moisture and temperature variations.
2. Automotive Parts: Insert molding is used in automotive manufacturing to create various parts like handles, buttons, switches, and panels. By incorporating metal components such as fasteners or connectors with plastic materials, insert molding enables efficient production, improved part strength, and reduced assembly steps.
3. Medical Devices: In the medical industry, insert molding is commonly utilized to manufacture items like syringe pistons, surgical instruments, connectors for catheters, and hearing aids. Integration of multiple materials and components ensures reliable function, better hygiene, and enhanced patient safety.
4. Consumer Electronics: Insert molding plays a crucial role in the production of consumer electronic devices. From power switches and USB connectors to small components like buttons and keypads, insert molding ensures reliable functionality, improved aesthetics, and ease of assembly.
5. Aerospace Components: Many aerospace applications require lightweight components with high strength and reliability. Insert molding enables the production of intricate parts such as connectors, knobs, and monitors, where metal inserts can be incorporated with composite materials, resulting in lightweight yet durable components.
6. Plumbing and Sanitary Fittings: Insert molding is commonly used in plumbing and sanitary applications. By overmolding metal inserts like valves, fittings, or connectors with plastic materials, manufacturers can ensure leak-proof connections, improved performance, and easy installation.
7. Industrial Tools and Equipment: Insert molding is extensively applied in the production of industrial tools and equipment. It allows for the integration of metal blade edges, gripping surfaces, or threaded inserts with plastic bodies, resulting in durable, ergonomic, and high-performance products.
In conclusion, insert molding finds broad applications across various industries, providing significant advantages such as reduced assembly, improved part strength, enhanced functionality, and cost savings. Its versatility and ability to combine different materials make it an integral part of many manufacturing processes.
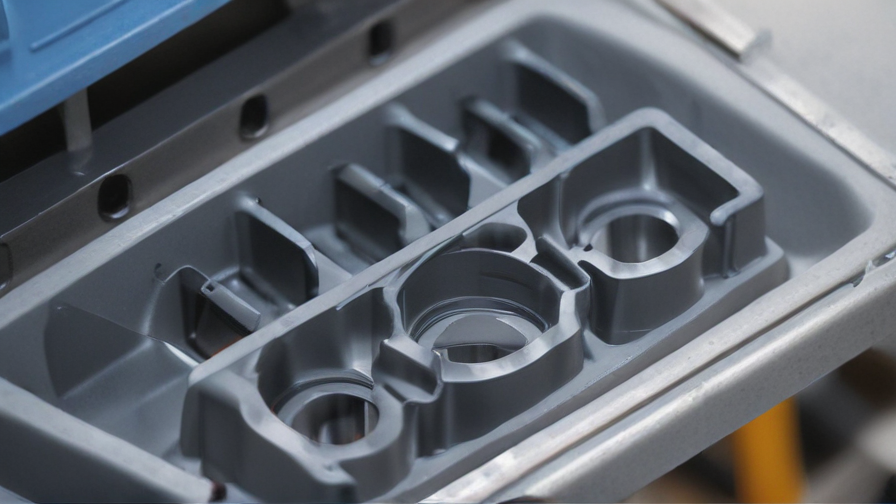
The Work Process and how to use insert molding
The work process of insert molding involves combining multiple materials or components into a single finished product. This technique is commonly used in industries such as automotive, electronics, and medical devices. Here is a brief overview of the steps involved in insert molding:
1. Design and preparation: The first step is to design the mold and prepare the insert. The insert is typically a metal or plastic component that will be placed into the mold.
2. Injection molding: The mold is then clamped and plastic material is injected into the mold cavity. The plastic material is usually in the form of pellets or granules, which are melted and injected under high pressure into the mold.
3. Insert placement: Once the plastic material is injected, the insert is placed into the mold cavity before the plastic cools and solidifies. The insert is positioned in such a way that it becomes integrated into the final molded product.
4. Molding process: The mold is held closed while the plastic cools and solidifies. This process can take a few seconds to minutes, depending on the specific material and product requirements.
5. Ejection: After the plastic has solidified, the mold is opened and the finished product is ejected. The insert is now encapsulated within the plastic and forms an integral part of the final product.
The technique of insert molding offers several advantages, including improved part strength, reduced assembly time and cost, and enhanced design flexibility. It allows for the creation of complex and multi-material parts without the need for additional assembly processes.
To use insert molding effectively, it is important to consider factors such as material compatibility, insert design, and mold construction. The selection of the right plastic material, the proper integration of the insert, and designing a mold that accommodates both the insert and plastic flow are crucial for a successful insert molding process.
In conclusion, insert molding is a versatile manufacturing process that enables the combination of multiple materials or components into a cohesive finished product. Understanding the work process and considering the various aspects of insert molding can lead to efficient and cost-effective production of complex and integrated parts.
Quality Testing Methods for insert molding and how to control the quality
Insert molding is a manufacturing process that combines injection molding with the placement of additional components, such as metal inserts or electronic parts, into the mold cavity before injection. This allows the creation of parts with enhanced functionality, reduced assembly costs, and improved product integrity. To ensure the quality of insert molded parts, several testing methods and quality control measures can be implemented.
One commonly used quality testing method is dimensional inspection. It involves measuring critical dimensions of the insert molded part using precision equipment, such as calipers or coordinate measuring machines, to ensure they meet the specified tolerances. This ensures that the part will fit and function correctly.
Another important testing method is visual inspection. This involves examining the part visually to identify any defects, such as cracks, voids, or warping. It is crucial to ensure these defects are absent or within acceptable limits to maintain the intended functionality and aesthetic appeal of the part.
Mechanical testing can also be used to assess the strength and durability of the insert molded part. Tensile tests, for example, can measure the maximum force the part can withstand without breaking. This helps verify that the part can handle the expected stresses during its intended use.
In addition to these specific testing methods, implementing a robust quality control system throughout the manufacturing process is essential. This involves monitoring and controlling various factors that can impact the quality of insert molded parts. For example, process parameters, such as injection pressure, temperature, and cooling time, should be carefully monitored and adjusted to ensure consistent part quality.
Regular maintenance and calibration of molding machines and tools are also necessary to minimize variations and defects. Training and skill development programs for operators and quality control personnel can further enhance the overall quality control system.
By employing these testing methods and quality control measures, manufacturers can ensure the production of high-quality insert molded parts. This, in turn, leads to improved product reliability, customer satisfaction, and ultimately, the success of the manufacturing process.
insert molding Sample Policy and Post-Purchase Considerations for insert molding from China
Sample Policy:
When it comes to insert molding from China, it is important to have a clear understanding of the sample policy in order to ensure satisfaction with the final product. In general, most manufacturers offer a sample policy that allows customers to receive and evaluate a prototype or sample of the insert molding before proceeding with mass production.
The sample policy typically includes the following considerations:
1. Sample Cost: Customers are usually responsible for covering the cost of the sample, including manufacturing and shipping fees. The exact cost may vary depending on the complexity and size of the insert molding.
2. Lead Time: The sample policy will specify the expected lead time for the production of the sample. This duration can range from a few days to weeks, depending on the manufacturer’s capacity and workload.
3. Customization: If any specific customization is required for the insert molding, such as color, texture, or sizing, it should be clearly communicated to the manufacturer beforehand. The sample policy may outline the limitations and options for customizations.
4. Revisions: In case the customer requests changes or modifications to the sample, the manufacturer may offer a limited number of revisions or iterations. However, it is important to clarify if there are any additional costs associated with revisions.
Post-Purchase Considerations:
After purchasing insert molding from China, certain post-purchase considerations can contribute to a successful experience. These considerations include:
1. Quality Inspection: Upon receiving the ordered insert molding, it is crucial to thoroughly inspect the products for any defects, damages, or deviations from the approved sample. Address any concerns promptly with the manufacturer to rectify any issues.
2. Communication and Feedback: Maintain open lines of communication with the manufacturer for continuous feedback and support. This allows for addressing any future concerns, modifications, or future orders effectively.
3. Documentation and Warranty: Keep relevant documentation, including invoices, contracts, and warranty details, for future reference. Ensure that the warranty terms and conditions are clear and understood.
4. Long-Term Partnership: If insert molding is required regularly or on an ongoing basis, consider establishing a long-term partnership with a reliable manufacturer in China. Building a strong relationship can lead to better pricing, improved product quality, and smoother transactions.
By understanding and following the sample policy and post-purchase considerations, customers can have a more seamless and satisfactory experience when purchasing insert molding from China.
Sourcing insert molding from China: Opportunities, Risks, and Key Players
Sourcing insert molding from China presents both opportunities and risks for businesses. China is known for its advanced manufacturing capabilities, cost-effective production, and vast supplier network, making it an attractive option for businesses looking to source insert molding. Key players in the Chinese insert molding market include manufacturers such as Foxconn, Flextronics, and BYD Company Limited.
One of the main opportunities of sourcing insert molding from China is the cost advantage. Labor costs in China are significantly lower compared to many other countries, allowing businesses to save on production expenses. Moreover, the country’s robust supply chain infrastructure enables efficient production and faster time to market. Chinese manufacturers also offer a wide range of materials and production capabilities, providing businesses with flexibility in customizing their insert molding products.
However, sourcing from China also comes with certain risks. Quality control can be a concern, as some manufacturers may prioritize lower costs over strict quality standards. To mitigate this risk, businesses should carefully vet potential suppliers based on their certifications, experience, and previous customer feedback. Conducting on-site visits and utilizing third-party inspection services can also help ensure product quality.
Another risk is intellectual property (IP) protection. China has had a reputation for IP infringement, and businesses sourcing insert molding should take precautions to protect their proprietary designs and technologies. Signing non-disclosure agreements (NDAs) and working with reliable suppliers with a strong commitment to IP protection can help safeguard against potential risks.
Additionally, businesses should consider geopolitical factors, such as trade tensions or regulatory changes that could impact the sourcing landscape. Monitoring these factors and diversifying sourcing strategies can help mitigate the risks associated with relying too heavily on one country for manufacturing.
In summary, sourcing insert molding from China offers opportunities in terms of cost advantages, production capabilities, and supply chain efficiency. However, businesses must also be aware of risks related to quality control and IP protection. By thoroughly evaluating potential suppliers and taking necessary precautions, businesses can successfully navigate the Chinese insert molding market and benefit from its advantages.
How to find and select reliable insert molding manufacturers in China,use google search manufacturers and suppliers
When looking for reliable insert molding manufacturers in China, using Google search is a great starting point for your research. Here’s a step-by-step guide to help you find and select the right manufacturers in China:
1. Initial search: Begin by searching for “insert molding manufacturers in China” or a similar phrase on Google. This will give you a broad list of potential manufacturers and suppliers.
2. Refine your search: Narrow down the search results by adding specific keywords related to your requirements. For example, include the type of insert material, production volume, or any specific certifications needed. This will help you find manufacturers that specifically meet your criteria.
3. Evaluate the websites: Open the websites of potential manufacturers and suppliers to gather information on their company background, manufacturing capabilities, product range, quality certifications, and any notable clients they may have worked with. This will allow you to gauge their experience and credibility.
4. Check online directories: Utilize online directories such as Alibaba, Made-in-China, and Global Sources. These directories provide detailed supplier profiles, customer reviews, ratings, and sometimes even product samples. This can help you narrow down your options further.
5. Verify legitimacy: Verify the legitimacy of a manufacturer by checking their business license, registration, certifications, and physical address. This can be done through trade directories, government websites, or by directly contacting the manufacturer.
6. Request quotations: Contact a few shortlisted manufacturers and request quotations based on your specific insert molding requirements. This will help you compare pricing, lead time, packaging, and other relevant factors.
7. Evaluate responsiveness and communication: Assess the responsiveness and communication skills of each manufacturer during the quotation process. Reliable manufacturers tend to be prompt, professional, and respond to your queries in a clear manner.
8. Quality control and testing: Inquire about the manufacturers’ quality control procedures, testing equipment, and certifications like ISO or RoHS. This will ensure that the chosen manufacturer follows proper quality guidelines.
9. Samples and factory visits: Request product samples to evaluate the manufacturer’s output quality. If feasible, consider visiting the shortlisted factories to personally assess their facilities, equipment, and production processes.
10. Client references: Ask the manufacturers for references of their previous or existing clients. Contact these references to gain insights into their experience working with the manufacturer and their overall satisfaction.
By following these steps, you can identify and select reliable insert molding manufacturers in China that match your specific requirements. Remember to conduct thorough due diligence before finalizing your choice to ensure a successful partnership.
How to check insert molding manufacturers website reliable,use google chrome SEOquake check if ranking in top 10M
To determine the reliability of an insert molding manufacturer’s website, you can follow these steps:
1. Use Google Chrome: Open the manufacturer’s website using Google Chrome browser. Chrome offers various tools and extensions that can help in evaluating the website’s reliability.
2. Install SEOquake: SEOquake is a free browser extension that provides valuable statistics and parameters for website analysis. Install this extension from the Chrome Web Store.
3. Check website ranking: Once installed, activate SEOquake. Look for the SEOquake icon at the top right corner of Chrome and click on it. A dropdown menu will appear with multiple options. Select “Show SERP overlay.” SERP stands for Search Engine Results Page.
4. Analyze top 10 million ranking: After enabling the SERP overlay, conduct a simple Google search by typing the manufacturer’s name or relevant keywords. SEOquake will display the website’s ranking among the top 10 million websites worldwide.
5. Evaluate ranking position: If the insert molding manufacturer’s website appears within the top 10 million, it indicates decent traffic and popularity. However, note that lower rankings might not necessarily indicate an unreliable website, as it is also influenced by other factors like competition and niche market.
6. Assess website quality: While it’s important to consider the ranking, it is equally crucial to evaluate the website’s overall quality. Look for professional design, user-friendly navigation, relevant and accurate information, contact details, certifications, customer reviews, and testimonials.
7. Consider additional factors: Reputation, industry experience, and the presence of social media accounts can further contribute to the website’s reliability. Check if they have an active presence on platforms like LinkedIn, Facebook, or Instagram, as it can provide insights into their credibility and engagement with customers.
Remember, these are just preliminary steps to assess the reliability of an insert molding manufacturer’s website. Extensive research, contacting the manufacturer directly, and seeking recommendations from other industry professionals are recommended for a comprehensive evaluation.
Top 10 insert molding manufacturers in China with each 160 words introduce products,then use markdown create table compare
**Top 10 Insert Molding Manufacturers in China**
1. **First-Rate Molding** – First-Rate Molding specializes in insert molding, providing a wide range of products such as automotive components, electronic connectors, and medical device parts. They utilize advanced technology and have a strong focus on quality control.
2. **Moldex Plastics** – Moldex Plastics offers insert molding solutions for various industries like consumer electronics, automotive, and healthcare. Their products include connectors, switches, and small precision components.
3. **Crystal Plastic Products** – Crystal Plastic Products is a leading manufacturer of insert molded and over-molded products. They cater to industries such as aerospace, automotive, and electrical appliances, producing high-quality components and assemblies.
4. **ABIS Mold Technology** – ABIS Mold Technology specializes in custom insert molding, providing services for industries like medical, automotive, and consumer electronics. They offer comprehensive solutions ranging from product design to manufacturing.
5. **HTMOLD Technology** – HTMOLD Technology is a supplier of precision insert molded parts for industries such as electronics, automotive, and telecommunications. They focus on delivering high-quality products and have a strong commitment to customer satisfaction.
6. **Wisconsin Plastics** – Wisconsin Plastics specializes in insert molding, offering a wide range of products including connectors, switches, and medical device components. They have extensive experience in high-volume production.
7. **Eagle Mold** – Eagle Mold is a leading insert molding manufacturer with expertise in industries like automotive, electrical, and medical. Their products include connectors, terminals, and custom components.
8. **Plastic Mold Manufacturer** – Plastic Mold Manufacturer provides custom insert molding solutions for various industries. They have a strong focus on quality and offer integrated services from design to production.
9. **Sositar Mould** – Sositar Mould specializes in insert molding, producing components for industries such as automotive, electrical, and healthcare. They offer a comprehensive range of services including product design, prototyping, and mass production.
10. **Universal Plastic Mold** – Universal Plastic Mold offers insert molding solutions for industries like automotive, electronics, and household appliances. They have a strong emphasis on quality control and utilize advanced manufacturing techniques.
| Manufacturer Name | Industries Served | Product Range |
|————————–|——————————–|———————————————————|
| First-Rate Molding | Automotive, Electronics, Medical | Components, Connectors, Device Parts |
| Moldex Plastics | Consumer Electronics, Automotive, Healthcare | Connectors, Switches, Precision Components |
| Crystal Plastic Products | Aerospace, Automotive, Electrical Appliances | Insert Molded Products, Assemblies |
| ABIS Mold Technology | Medical, Automotive, Consumer Electronics | Custom Insert Molded Products, Comprehensive Solutions |
| HTMOLD Technology | Electronics, Automotive, Telecommunications | Precision Insert Molded Parts |
| Wisconsin Plastics | Connectors, Switches, Medical Device Components | Insert Molded Products, High-Volume Production |
| Eagle Mold | Automotive, Electrical, Medical | Connectors, Terminals, Custom Components |
| Plastic Mold Manufacturer | Custom Insert Molding for Various Industries | Integrated Services, Design to Production |
| Sositar Mould | Automotive, Electrical, Healthcare | Insert Molded Components, Design, Prototyping, Mass Production |
| Universal Plastic Mold | Automotive, Electronics, Household Appliances | Insert Molded Solutions, Advanced Manufacturing Techniques |
These top 10 insert molding manufacturers in China provide a wide range of products and services across various industries. Their expertise in insert molding enables them to produce high-quality components, connectors, switches, and other precision parts for automotive, electronics, medical, and consumer sectors. From comprehensive solutions and integrated services to a strong focus on quality control and customer satisfaction, these manufacturers offer a variety of options to meet the diverse needs of their clients.
Background Research for insert molding manufacturers Companies in China, use qcc.com archive.org importyeti.com
When it comes to insert molding manufacturers in China, there are a few reputable companies that can be explored for background research. Qcc.com, Archive.org, and Importyeti.com are reliable platforms to gather relevant information on these manufacturers. Here is a brief overview of each platform:
1. Qcc.com: Qcc.com is a Chinese company database that provides detailed information about businesses operating in China. It offers data on a variety of industries, including insert molding manufacturers. This platform can be used to gather information about the company’s registration, financial status, contact details, and more.
2. Archive.org: Archive.org is an online archive that takes snapshots of websites, allowing users to access and review past versions of different websites. This can be useful to understand the historical development and evolution of the insert molding manufacturing companies in China. By reviewing archived versions of company websites, one can analyze changes in product offerings, company strategies, and milestones achieved.
3. Importyeti.com: Importyeti.com is a platform for tracking import and export activities of companies. It provides shipment data, including details about the products imported or exported and the companies involved. By searching for specific insert molding manufacturers on Importyeti.com, one can gather information about their overseas trade activities, potential clients, and distribution network.
By utilizing these platforms, researchers can access comprehensive information about insert molding manufacturers in China. This includes company profiles, historical data, financial information, import-export activities, and more. These insights can help in making informed decisions when choosing the right manufacturer for insert molding requirements.
Leveraging Trade Shows and Expos for insert molding Sourcing in China
Trade shows and expos provide excellent opportunities for businesses to source insert molding services in China. These events act as platforms for industry professionals to come together, exchange knowledge, showcase products, and develop business relationships.
By attending trade shows and expos focused on manufacturing, injection molding, or plastics, businesses can connect with a wide range of suppliers and manufacturers specializing in insert molding in China. These events often attract a diverse pool of exhibitors, from large manufacturing companies to small-scale specialized insert molding providers.
Engaging with suppliers at trade shows and expos allows businesses to directly interact with potential vendors, gaining insights into their capabilities, quality control processes, and production capacities. This face-to-face interaction also enables businesses to gauge the supplier’s responsiveness, communication skills, and ability to meet specific project requirements.
In addition to meeting potential suppliers, trade shows and expos offer opportunities to explore the latest technological advancements and innovations in insert molding. Exhibitors often showcase their capabilities, demonstrating their expertise and showcasing successful project examples. This can be particularly valuable for businesses seeking to stay competitive and incorporate cutting-edge technology into their insert molding projects.
Furthermore, trade shows and expos provide businesses with a platform to network and forge partnerships with industry peers and experts. Collaborating with other businesses within the industry can lead to valuable insights, knowledge sharing, and potential opportunities for joint ventures or collaborations.
To make the most of trade shows and expos, businesses should prepare by conducting thorough research on the exhibitors and event agenda beforehand. This will help identify potential suppliers that align with specific insert molding needs. It is also important to clearly communicate project requirements, expectations, and quality standards to potential suppliers during the event.
In summary, trade shows and expos present businesses with a unique opportunity to source insert molding services in China. By leveraging these events, businesses can connect with a wide range of suppliers, explore the latest innovations, and establish valuable industry connections, ultimately enhancing their insert molding sourcing strategies.
The Role of Agents and Sourcing Companies in Facilitating insert molding Purchases from China
Agents and sourcing companies play a significant role in facilitating insert molding purchases from China. These intermediaries act as a bridge between buyers and manufacturers, helping to streamline the procurement process and ensure a successful transaction.
One of the key advantages of using agents and sourcing companies is their local knowledge and expertise. They are well-versed in the Chinese manufacturing landscape, understanding the capabilities and strengths of different suppliers. This knowledge allows them to identify and connect buyers with the most suitable manufacturers for their insert molding requirements.
Agents and sourcing companies also help buyers navigate the language and cultural barriers that can often arise when dealing with Chinese suppliers. They act as interpreters and facilitators, ensuring effective communication and understanding between both parties. This helps to prevent misunderstandings, minimize risks, and build strong relationships.
Additionally, agents and sourcing companies provide valuable assistance in quality control and assurance. They conduct factory audits, inspect production processes, and check product samples to ensure that the manufacturers comply with international standards and buyer specifications. This is crucial in maintaining the desired quality and reliability of insert molded products.
Furthermore, these intermediaries assist in negotiating favorable terms and prices. Given their familiarity with the market, they have the bargaining power to secure cost-effective deals on behalf of the buyers. This helps to maximize cost savings and improve the overall profitability of insert molding purchases from China.
Overall, agents and sourcing companies play a pivotal role in facilitating insert molding purchases from China by leveraging their local expertise, bridging communication gaps, ensuring quality control, and negotiating favorable terms. Their involvement streamlines the procurement process, mitigates risks, and enhances the overall buying experience for customers.
Price Cost Research for insert molding manufacturers Companies in China, use temu.com and 1688.com
When it comes to insert molding manufacturers in China, two popular platforms for price cost research are temu.com and 1688.com. These platforms provide a plethora of options for finding the right manufacturer at competitive prices.
Temu.com is an online platform that specializes in connecting global buyers with reliable Chinese suppliers. It offers a wide range of insert molding manufacturers from all over China. The platform provides detailed information on each manufacturer, including their location, production capacity, certifications, and contact details. Additionally, temu.com allows users to compare prices, request quotations, and negotiate directly with the suppliers.
1688.com, on the other hand, is another prominent online marketplace in China. It is operated by Alibaba Group, one of the world’s largest e-commerce companies. Similar to Alibaba.com, 1688.com primarily caters to the domestic market in China. However, it is possible to navigate the platform using online translation tools to search and communicate with manufacturers.
Both platforms offer a vast selection of insert molding manufacturers, allowing users to find suitable suppliers based on their specific requirements. Users can filter their searches by location, production capacity, certifications, and more. Furthermore, these platforms provide an opportunity to review and compare the prices offered by different manufacturers, helping users make informed decisions about their sourcing needs.
Conducting price cost research on temu.com and 1688.com can streamline the process of identifying insert molding manufacturers in China. These platforms enable users to access a comprehensive database of suppliers, compare prices, and communicate directly, all in one convenient location. By utilizing these resources, global buyers can save time and effort while ensuring they find the right insert molding manufacturer at the most competitive price.
Shipping Cost for insert molding import from China
When importing products from China, the shipping cost for insert molding can vary depending on various factors such as the size and weight of the shipment, the distance between the origin and destination, and the mode of transportation chosen.
For smaller orders, air freight is often the preferred mode of transportation due to its speed and convenience. However, air freight can be relatively expensive compared to other options. The cost is typically calculated based on the dimensional weight or actual weight of the shipment, whichever is higher.
For larger orders, sea freight is a more cost-effective option. The cost of sea freight is typically calculated based on the volume of the shipment, measured in cubic meters (CBM). The rates can vary depending on the shipping company, the shipping route, and any additional services required such as customs clearance.
To give a rough estimate, the shipping cost for insert molding imported from China can range from a few hundred dollars for smaller air freight shipments to several thousand dollars for sea freight shipments. It is essential to consider additional costs such as customs duties, taxes, and any other charges associated with shipping.
To optimize the shipping cost, it is advisable to consider consolidating your order and shipping in larger quantities. This reduces the shipping cost per unit and allows for better negotiation with shipping companies. It is also essential to work closely with a reliable freight forwarder or shipping agent who can help navigate the complexities of international shipping and ensure a smooth delivery process.
In conclusion, the shipping cost for insert molding imported from China can vary based on factors such as size, weight, distance, and mode of transportation. By carefully considering these factors and working with experienced professionals, you can minimize the shipping cost and ensure a cost-effective import process.
Compare China and Other insert molding Markets: Products Quality and Price,Visible and Hidden Costs
China is a major player in the insert molding market, but it is essential to compare it with other markets in terms of product quality, price, visible and hidden costs.
In terms of product quality, China has made significant strides in improving its manufacturing capabilities. Many Chinese manufacturers have adopted advanced technologies and modern equipment to enhance their production processes. However, quality inconsistencies may still exist due to the large number of manufacturers in the country. On the other hand, some other markets such as Germany and Japan have a reputation for producing high-quality products consistently. These markets often prioritize precision engineering and rigorous quality control measures, resulting in superior product quality.
When it comes to pricing, China has long been known for its competitive pricing strategy. The country has a vast manufacturing infrastructure that allows for economies of scale, enabling Chinese manufacturers to offer lower prices compared to many other markets. However, this low pricing often raises concerns about the quality of the products, as some manufacturers may compromise on quality to maintain low costs. Other markets, especially those with higher labor and operational costs, typically have higher price points but often offer products with better quality assurance.
Visible costs, such as the initial purchase price, shipping, and import duties, are relatively transparent and can be easily compared between markets. In terms of visible costs, China often has a competitive advantage due to its large manufacturing capabilities and efficient logistics networks. However, hidden costs, such as intellectual property risks, quality control issues, and supply chain disruptions, are also important to consider. China’s intellectual property laws and enforcement have been a concern for many foreign companies, leading to potential risks and financial losses. Additionally, language and cultural barriers can sometimes hinder effective communication and collaboration with Chinese manufacturers, resulting in potential quality control issues. Other markets often offer more transparent and reliable business environments, minimizing the potential hidden costs.
In conclusion, while China has made significant advancements in the insert molding market, it is important to consider product quality, pricing, visible and hidden costs when comparing it with other markets. Other markets may excel in terms of product quality, albeit potentially at a higher price. Visible costs can favor China due to its economies of scale, but hidden costs such as intellectual property risks and quality control issues should also be taken into account. Ultimately, the choice of market would depend on the specific requirements and priorities of the customer.
Understanding Pricing and Payment Terms for insert molding: A Comparative Guide to Get the Best Deal
When it comes to insert molding, understanding pricing and payment terms is crucial to get the best deal possible. This comparative guide aims to provide insight into the factors that affect pricing and the various payment terms offered by manufacturers.
Pricing for insert molding typically depends on several factors, including the complexity of the part design, the materials used, the quantity needed, and production lead time. The more complex the part, the higher the cost. Additionally, the choice of materials, such as thermoplastics or thermosetting plastics, can impact pricing. Quantity also plays a role, as larger orders often come with volume discounts. Lastly, the production lead time affects the overall cost, as rush orders may incur additional fees.
Payment terms vary among manufacturers, and understanding these options can help negotiate the best deal. Common payment terms include:
1. Net 30: This term allows the buyer to pay the invoice within 30 days of receiving the parts. It is a common option for established businesses with good credit.
2. Net 60: Similar to Net 30, but with a 60-day payment window. This option provides more flexibility for the buyer’s cash flow but may come with a higher cost due to delayed payment.
3. Partial payment: Some manufacturers offer the option to split the payment into several installments, allowing buyers to pay a portion upfront and the rest upon completion or in predefined milestones.
4. Down payment: In some cases, manufacturers require a percentage of the total cost upfront as a down payment to secure the production slot. The remaining balance is then paid upon completion.
5. Payment upon delivery: Although less common, this payment option involves paying in full upon the delivery of the parts. It offers a higher level of security for the buyer but may not be available for large orders or custom-made parts.
By understanding these pricing factors and payment terms, buyers can compare quotes from different manufacturers and negotiate the best deal for their insert molding needs. It is essential to consider both the cost and terms offered to ensure a mutually beneficial arrangement that meets quality standards and delivery schedules.
Chinese Regulations and Industry Standards Certifications for insert molding,Import Regulations and Customs for insert molding from China
China, being a major global manufacturing hub, has implemented several regulations and industry standards certifications related to insert molding. These measures ensure product quality, safety, and compliance with international norms.
One crucial certification for insert molding in China is the ISO 9001:2015. This certification guarantees that the manufacturer follows a standardized quality management system, including design, development, production, and customer satisfaction.
Another significant certification is the RoHS (Restriction of Hazardous Substances) compliance, which ensures that the materials used in insert molding do not contain harmful substances such as lead, mercury, cadmium, or various flame retardants. This certification is crucial for industries that prioritize sustainability and environmental-friendly practices.
For product safety and performance validation, China has the CCC (China Compulsory Certification). This certification is mandatory for products like electrical and electronic appliances, including those incorporating insert molded components. It ensures that products meet the required safety, electromagnetic compatibility, and energy efficiency standards.
Regarding import regulations and customs procedures for insert molding from China, it is essential to comply with the individual country’s import laws and regulations. This includes adhering to customs documentation and procedures, such as providing invoices, packing lists, and product descriptions. It is also crucial to understand any specific import restrictions or tariffs imposed by the destination country.
To ensure a smooth import process, it is advisable to work with a reliable freight forwarder who can assist in navigating customs requirements and handling logistics efficiently.
In conclusion, complying with Chinese regulations and industry standards certifications, such as ISO 9001:2015 and RoHS, is vital for manufacturers involved in insert molding. Additionally, understanding the import regulations and customs procedures of the destination country helps ensure a successful import process.
Sustainability and Environmental Considerations in insert molding Manufacturing
Insert molding is a manufacturing process that combines multiple components into a single, integrated product. It offers numerous benefits such as improved product durability, reduced manufacturing time, and increased design flexibility. However, it is important to consider sustainability and environmental factors when implementing insert molding in manufacturing.
One of the primary environmental considerations in insert molding manufacturing is the choice of materials. Selecting materials that are recyclable, biodegradable, or made from renewable resources can significantly reduce the environmental footprint of the manufacturing process. Materials such as bio-based plastics, recycled metals, and natural fibers can be used as inserts to enhance sustainability.
Additionally, energy consumption is a crucial factor to consider. Implementing energy-efficient machinery, optimizing processing parameters, and reducing idle times can help minimize energy usage. This not only reduces greenhouse gas emissions but also lowers operational costs.
Waste management is another critical aspect of sustainability in insert molding manufacturing. Implementing waste reduction strategies, such as reusing or recycling waste materials, can minimize the amount of waste sent to landfills. Furthermore, proper disposal of hazardous materials, such as solvents or adhesives, is essential to prevent environmental contamination and comply with regulations.
To prioritize sustainability, manufacturers can also consider the overall lifecycle of the product. This involves the assessment of the product’s environmental impact throughout its entire lifecycle, from raw material extraction to disposal. By striving to reduce the environmental impact at every stage, manufacturers can enhance the sustainability of the insert molding process.
In conclusion, sustainability and environmental considerations play a crucial role in insert molding manufacturing. Selecting eco-friendly materials, minimizing energy consumption, implementing waste management strategies, and considering the product lifecycle are essential for reducing the environmental footprint of the manufacturing process. By integrating these considerations into the manufacturing practice, companies can contribute to a more sustainable and environmentally-friendly future.
List The Evolution history of “insert molding”
Insert molding is a versatile manufacturing process that combines the advantages of both injection molding and insert placement techniques. It involves inserting pre-formed components, such as metal or plastic parts, into the injection mold before the molding process begins. The molten material then encapsulates the insert, forming a single, integrated part.
The evolution of insert molding can be traced back to the early 20th century when early forms of insert molding were utilized, predominantly in metalworking industries. This technique involved manually placing inserts in molds and pouring molten metal into the cavity. It was primarily used for fabricating metal parts with embedded hardware, such as screws or handles. However, this method was time-consuming, labor-intensive, and limited in its applications.
Significant advancements in insert molding occurred in the mid-20th century with the introduction of thermoplastic materials and injection molding machines. The use of thermoplastics expanded the possibilities of insert molding by allowing for the overmolding of various types of inserts, including plastics, metals, and electronics. Injection molding machines enabled more efficient and automated production.
In the 1970s, technical advancements in injection molding machinery and mold design further revolutionized insert molding. The widespread adoption of computer numerical control (CNC) systems improved precision, repeatability, and accuracy in manufacturing processes, including insert molding. This led to higher-quality parts with tighter tolerances and greater complexity.
Over the years, insert molding continued to evolve with the development of new materials, advanced molding techniques, and enhanced automation. The availability of engineered thermoplastics and thermosetting resins expanded the range of applications for insert molding. Additionally, innovations such as automated insert loading systems, robotics, and in-mold sensing technologies improved production efficiency, reduced cycle times, and enhanced product consistency.
Today, insert molding finds applications in various industries, including automotive, electronics, medical, and consumer goods. It offers advantages like simplified assembly, improved part integrity, reduced production costs, and enhanced product functionality. With the advent of additive manufacturing and 3D printing, the boundaries of insert molding continue to be pushed, allowing for more complex geometries and lightweight design possibilities.
In conclusion, insert molding has come a long way from its manual insertion origins to being a highly automated and efficient manufacturing process. Its evolution has been driven by advancements in materials, machinery, automation, and design techniques, enabling the production of intricate and functional parts across a wide range of industries.
The Evolution and Market Trends in insert molding Industry
The insert molding industry has experienced significant growth and evolution over the years, driven by various factors such as advancements in technology, changing consumer needs, and shifting market trends.
One of the key developments in the insert molding industry is the increasing use of automation and robotics. Automation has revolutionized the manufacturing process, enabling faster and more efficient production. With the help of robotics, manufacturers can achieve higher precision, consistency, and productivity, leading to reduced costs and improved overall quality.
Another important trend in the insert molding industry is the growing demand for lightweight and durable materials. This trend is driven by factors such as the need for fuel-efficient vehicles, the rising popularity of wearable devices, and the increasing demand for compact and portable consumer electronics. As a result, manufacturers are utilizing materials like thermoplastics and composites, which offer a perfect balance between strength and weight. Additionally, these materials allow for more complex and intricate designs, leading to enhanced product functionality and aesthetics.
Furthermore, sustainability has become a significant consideration in the insert molding industry. Environmental concerns and regulations have prompted manufacturers to adopt more eco-friendly practices and materials. Incorporating recycled or bio-based materials into the insert molding process helps to reduce the carbon footprint and minimize waste. Additionally, manufacturers are focusing on optimizing the product lifecycle, including end-of-life recycling and disposal management.
Moreover, the market trends in the insert molding industry are being driven by changing consumer preferences. Customers today demand products that are not only functional but also aesthetically pleasing and customizable. This trend has led to increased demand for insert molded products with intricate designs, color variations, and personalized features.
Furthermore, the insert molding industry is witnessing growth in various sectors such as automotive, electronics, healthcare, and consumer goods. The automotive sector, in particular, is a major driver of the market, with the increasing demand for lightweight and safety-enhancing components. The electronics and healthcare sectors are also experiencing growth due to the rising adoption of wearable devices and medical equipment.
In summary, the insert molding industry has evolved significantly, with advancements in technology, changing consumer preferences, and increasing focus on sustainability. Automation and robotics have improved manufacturing processes, while lightweight and sustainable materials have enabled enhanced product designs. Customization and personalization are also becoming essential factors in the market. Overall, the insert molding industry is poised for further growth and innovation in the coming years.
Custom Private Labeling and Branding Opportunities with Chinese insert molding Manufacturers
Chinese insert molding manufacturers offer custom private labeling and branding opportunities to businesses. With a vast array of capabilities and expertise, these manufacturers can help businesses create unique and exclusive products.
Private labeling allows businesses to have their own branding and logo on the products they sell. This helps them establish a distinct identity and build customer loyalty. Chinese insert molding manufacturers offer the option to customize product appearance, packaging, and labels according to the business’s specifications. This ensures that the final product reflects the brand’s image and aligns with its marketing strategy.
Moreover, Chinese manufacturers can also provide branding opportunities through product design and development. They have experienced engineers and designers who can collaborate with businesses to create innovative and differentiated products. By leveraging the manufacturer’s expertise, businesses can develop unique molds and designs that set their products apart from competitors.
Additionally, Chinese insert molding manufacturers offer competitive pricing and high-quality manufacturing processes. This ensures that businesses can maintain their desired profit margins while delivering superior products to the market. The manufacturers utilize advanced technologies and strict quality control measures to ensure that the finished products meet the highest standards.
Collaborating with Chinese insert molding manufacturers for private labeling and branding opportunities can be a strategic move for businesses looking to expand their product offerings and establish themselves in the market. With their cost-effective manufacturing capabilities and expertise, these manufacturers can help businesses create custom branded products that resonate with their target audience.
Overall, Chinese insert molding manufacturers offer businesses the possibility to create unique products through custom private labeling and branding opportunities. By leveraging their capabilities, businesses can enhance their brand image, increase customer loyalty, and ultimately drive sales and revenue.
Tips for Procurement and Considerations when Purchasing insert molding
When purchasing insert molding, there are several important considerations that must be taken into account to ensure a successful procurement process. Here are some tips and considerations to keep in mind:
1. Material Selection: Determine the specific material requirements for your insert molding project. Consider the application, end-use, strength, durability, and any chemical or temperature resistance needed.
2. Manufacturer Expertise: Choose a reputable manufacturer with experience in insert molding. Look for companies that specialize in this process and have a proven track record of delivering high-quality products.
3. Design Support: Work closely with the manufacturer to ensure that your design is suitable for insert molding. They can provide valuable input on design considerations, part consolidation, and manufacturability.
4. Mold Design: Collaborate with the manufacturer to design an efficient and cost-effective mold. Consider factors such as complexity, number of cavities, gate placement, and ease of maintenance.
5. Compatibility Testing: Conduct thorough compatibility testing of the insert material and the molding material to ensure proper bonding and adhesion. This step is crucial to prevent issues such as delamination or part failure.
6. Quality Control: Establish clear quality control standards and requirements with the manufacturer. Insist on regular inspections, statistical process control, and testing protocols to ensure consistent quality throughout production.
7. Cost and Lead Time: Obtain detailed cost estimates and lead times from multiple suppliers to ensure competitive pricing and realistic delivery schedules. Consider factors such as tooling costs, material costs, and any secondary operations required.
8. Supplier Selection: Evaluate potential suppliers based on their technical expertise, production capabilities, financial stability, and customer support. Request references and visit their facilities if possible.
9. Intellectual Property Protection: Discuss and establish confidentiality and intellectual property protection agreements with the manufacturer, particularly if your insert molding design is proprietary or has patentable features.
10. Responsiveness and Communication: Choose a supplier who is responsive, communicates effectively, and is willing to collaborate throughout the procurement process. Good communication ensures that any issues or concerns are addressed promptly.
Remember, proper planning and communication are key to a successful procurement process when purchasing insert molding. By considering these tips and engaging in thorough research, you can select a reliable supplier that meets your specific needs and requirements.
FAQs on Sourcing and Manufacturing insert molding in China
1. What is insert molding?
Insert molding is a manufacturing process where a pre-formed object, called an insert, is inserted into a mold cavity. The molten material, typically plastic, is then injected into the mold, surrounding and encapsulating the insert. This process results in a single, integrated part with the insert securely embedded within it.
2. Why should I consider sourcing insert molding from China?
China is a leading destination for sourcing manufacturing services, including insert molding. The country offers competitive pricing due to its lower labor costs and well-established supply chain networks. Chinese manufacturers specialize in various industries and can provide a wide range of insert molding capabilities, from simple to complex designs.
3. What are the advantages of insert molding?
The advantages of insert molding include increased part strength and durability due to the direct bonding of the insert with the surrounding material. This process also eliminates the need for additional assembly steps, reducing production time and costs. Insert molding allows for the integration of multiple components into a single part, reducing overall product complexity and improving functionality.
4. What types of inserts can be used in insert molding?
Various inserts can be used in insert molding, including metal components, such as screws, bolts, connectors, or electrical contacts. Plastic parts, such as threaded inserts, clips, or bushings, can also be used. Other materials like ceramics or glass can be incorporated as inserts, depending on the specific application requirements.
5. How does the sourcing process for insert molding in China work?
The sourcing process starts with identifying reputable manufacturers in China specializing in insert molding. This can be done through online platforms, industry trade shows, or referrals. Once potential suppliers are identified, RFQs (Request for Quotations) are sent to them, specifying the required design, material, quantity, and other specifications. Samples and prototypes are then produced for evaluation and verification before moving into mass production.
6. What quality control measures should be considered for insert molding in China?
To ensure consistent manufacturing and product quality, it is essential to work with manufacturers who have robust quality management systems in place. This may include comprehensive inspection and testing procedures, certification adherence (such as ISO 9001), and strict adherence to product specifications. Regular quality checks and on-site visits are also recommended to maintain production standards.
In conclusion, insert molding is a cost-effective and efficient manufacturing process for producing integrated parts. China provides a favorable environment for sourcing insert molding, offering competitive pricing and a wide range of manufacturing capabilities. However, it is crucial to engage in thorough supplier selection, quality control, and communication to ensure successful sourcing and manufacturing of insert molded products in China.
Why contact sourcifychina.com get free quota from reliable insert molding suppliers?
SourcifyChina.com, as a sourcing platform, aims to connect businesses with reliable suppliers in China. The platform offers a range of services, including facilitating communication, quality control, and supplier verification. In order to attract potential customers and entice them to use their services, SourcifyChina.com has partnered with reputable insert molding suppliers to provide a free quota.
There are several reasons why these suppliers are willing to offer a free quota through SourcifyChina.com. Firstly, by offering a free quota, the suppliers can showcase their capabilities and expertise in insert molding. This allows them to establish a reputation and potentially attract new customers who may require their services in the future.
Secondly, by partnering with SourcifyChina.com, the suppliers can tap into a larger pool of potential customers. SourcifyChina.com acts as a bridge between businesses looking for reliable suppliers and the suppliers themselves. By participating in this partnership, the suppliers can extend their reach and increase their chances of connecting with new customers.
Additionally, the suppliers may benefit from the marketing and promotion efforts of SourcifyChina.com. As a sourcing platform, SourcifyChina.com actively promotes its services and suppliers to businesses in need of manufacturing solutions. By offering a free quota, the suppliers gain exposure to a wider audience who may not have been aware of their services otherwise.
Furthermore, the suppliers may view the free quota as a way to build long-term relationships with potential customers. By providing a sample or initial quota without charge, the suppliers can demonstrate the quality of their products and services. This can help establish trust and encourage businesses to continue working with them on larger-scale projects in the future.
In conclusion, SourcifyChina.com offers a free quota from reliable insert molding suppliers to attract potential customers and facilitate connections between businesses and suppliers. This benefits the suppliers by showcasing their capabilities, expanding their customer base, and building long-term relationships.