Introduce about liquid silicone molding guide,Qulity,Cost,Supplier,Certification,Market,Tips,FAQ
Liquid silicone molding is a versatile manufacturing process that involves injecting liquid silicone rubber into a mold to produce high-quality and intricate parts and products. This molding guide aims to provide a brief overview of the process, its advantages, cost factors, reliable suppliers, certifications, current market trends, and relevant tips.
Liquid silicone molding ensures a consistent level of quality due to its precision and low variability. The process allows for the production of complex shapes, tight tolerances, and smooth finish, making it suitable for various industries like healthcare, automotive, electronics, and consumer goods.
Cost factors for liquid silicone molding comprise material costs, mold design, production volume, and complexity, as well as post-processing requirements. A detailed quotation from suppliers can give a more accurate estimation.
Reliable suppliers in the liquid silicone molding field offer comprehensive services, including mold design and fabrication, material selection, prototyping, and production. Conduct thorough research to ensure a supplier’s experience, reputation, and capability to meet specific project requirements.
Certifications such as ISO 9001 and ISO 13485 are crucial when choosing a liquid silicone molding supplier. These certifications guarantee adherence to stringent quality management systems, ensuring consistency and reliability in production processes.
The market for liquid silicone molding is expanding rapidly, driven by the demand for medical devices, electrical components, and consumer products. The automotive industry also employs liquid silicone rubber for applications like seals and gaskets due to its durability and flexibility.
Some tips for successful liquid silicone molding include proper mold design, careful material selection, and effective process control. Collaborating closely with the supplier during the design and prototyping phases can enhance product quality and reduce costs.
Frequently asked questions regarding liquid silicone molding typically address topics like material properties, mold lifespan, prototype production, and lead times. Communicating with experienced suppliers can provide answers to these queries and ensure a better understanding of the process.
In conclusion, liquid silicone molding offers a reliable, precise, and versatile manufacturing process for the production of high-quality parts. Considering the cost factors, reliable suppliers, relevant certifications, market trends, and following the provided tips can ensure a successful project outcome.
Types of liquid silicone molding
Liquid silicone molding is a versatile process that allows the production of a wide range of silicone-based products. There are several types of liquid silicone molding methods, each offering unique benefits and applications. Here are five common types:
1. Compression molding: This traditional molding technique involves placing a pre-measured amount of liquid silicone material into a mold cavity, which is then closed and compressed. The applied pressure forces the liquid silicone to flow and fill the desired shape. Compression molding is suitable for low to medium production volumes and is commonly used for manufacturing gaskets, O-rings, and seals.
2. Transfer molding: In transfer molding, the liquid silicone material is first placed in a separate chamber or pot. A plunger forces the material through a channel and into the mold cavity. Once it fills the cavity, the plunger is retracted, and the cured product is removed. Transfer molding is often preferred for complex designs, delicate parts, or when precise positioning of inserts is required.
3. Injection molding: This widely used technique involves injecting liquid silicone into a mold cavity under high pressure. The liquid silicone is forced into the cavity through a sprue, runner, and gate system. Injection molding allows for high production volumes and is suitable for intricate shapes and overmolding, where two materials are combined in one molded part.
4. LSR (Liquid Silicone Rubber) overmolding: This technique combines liquid silicone rubber and another material, typically a rigid plastic substrate. The process involves injecting liquid silicone rubber onto or around the substrate, creating a bond that results in a single component. LSR overmolding is commonly used in the production of medical devices, consumer electronics, and automotive components.
5. Micro molding: Micro molding utilizes liquid silicone to produce small, precise, and intricate parts. This specialized technique allows for the production of micro-components with tight tolerances and intricate geometries. Micro molding finds applications in medical devices, electronics, and telecommunications industries.
Liquid silicone molding offers numerous advantages, including excellent dimensional stability, resistance to extreme temperatures, chemical inertness, and biocompatibility. The choice of molding method depends on the specific product design, required volume, complexity, and material properties. Ultimately, liquid silicone molding enables the production of high-quality silicone-based products across various industries.
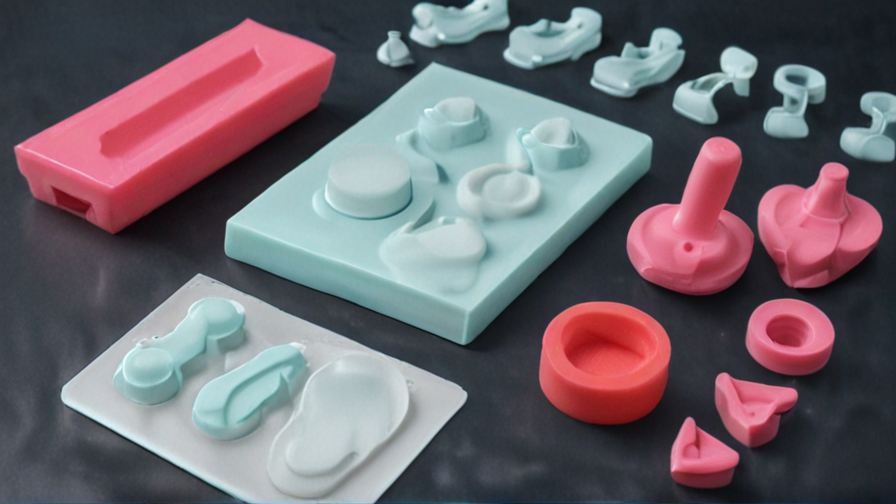
Pros and Cons of Using liquid silicone molding
Liquid silicone molding is a popular manufacturing process used to create a variety of products. This technique involves injecting liquid silicone into a mold cavity, allowing it to cure and form the desired shape. Like any manufacturing method, liquid silicone molding has its advantages and disadvantages.
Pros:
1. High precision: Liquid silicone molding offers a high level of precision and accuracy, allowing for the production of intricate and complex designs. The liquid silicone easily fills the mold cavity, ensuring that every detail is captured with excellent reproducibility.
2. Wide range of material properties: Liquid silicone is available in various grades and can be customized to meet specific requirements. It exhibits a broad range of material properties such as high flexibility, heat resistance, biocompatibility, and electrical insulation, making it suitable for a wide range of applications.
3. Excellent part quality: The use of liquid silicone molding ensures that finished parts have a smooth and flawless surface finish. This eliminates the need for additional post-processing steps, such as sanding or polishing, saving time and cost in the production process.
4. Cost-effective for high-volume production: Once the mold is manufactured, liquid silicone molding becomes a cost-effective method for mass production. The process allows for quick and efficient production cycles, reducing labor costs and improving overall productivity.
Cons:
1. Tooling cost: The initial investment in creating the mold can be quite expensive, especially for intricate designs with complex geometries. This can be a deterrent for small-scale production or businesses with limited budgets.
2. Longer lead time: Designing and manufacturing the mold typically takes longer compared to other manufacturing processes. The mold needs to be carefully designed, machined, and tested for quality assurance before production can begin, which can result in longer lead times.
3. Limited material options: Although liquid silicone comes in a variety of grades, the material options for liquid silicone molding are more limited compared to other molding techniques. This may restrict the choice of material properties available for specific applications.
4. Limited part size: Liquid silicone molding is generally suitable for small to medium-sized parts. The maximum part size and thickness are limited by the mold design and the properties of the liquid silicone material itself. Large or thick parts may require alternative manufacturing methods.
In conclusion, using liquid silicone molding offers high precision, excellent part quality, and a wide range of material properties. However, the initial tooling cost, longer lead time, limited material options, and size restrictions are some factors to consider when deciding on this manufacturing method.
liquid silicone molding Reference Specifications (varies for different product)
Liquid silicone molding, also known as liquid injection molding (LIM), is a highly efficient and versatile manufacturing process used for producing various types of silicone rubber products. It involves injecting liquid silicone into a mold cavity, allowing it to cure and solidify into the desired shape.
The liquid silicone used in this process is a two-part platinum-cured elastomer, which offers exceptional advantages over traditional solid silicone materials. It has excellent flexibility, high tear strength, biocompatibility, and resistance to heat, chemicals, and UV radiation. This makes it suitable for a wide range of applications, including medical devices, automotive components, consumer products, and electrical connectors.
The reference specifications for liquid silicone molding can vary depending on the specific product requirements. These specifications determine the key parameters for the molding process, such as the mold design, injection speed, curing time, and temperature. They are influenced by factors like product dimensions, complexity, desired mechanical properties, and surface finish.
For example, in medical device manufacturing, the reference specifications might include strict adherence to ISO 13485 quality standards, FDA compliances, and specific requirements related to biocompatibility and sterilization. Automotive components may have specifications related to resistance to automotive fluids, such as oil and coolant, as well as stringent durability and safety requirements.
The liquid silicone molding process typically involves precision-engineered molds, made from steel or aluminum, that are designed to form the desired shape of the product. These molds have multiple cavities to allow for high-volume production. Injection of the liquid silicone is conducted using an automated LIM machine, which precisely controls the injection pressure, temperature, and speed to deliver consistent and reliable results.
Once injected, the silicone cures in the mold under heat to achieve the desired shape and properties. The curing time can range from minutes to several hours, depending on the material formulation and product thickness. After curing, the finished products are removed from the molds, and additional post-processing, such as trimming or surface treatment, may be performed to meet the required specifications.
In summary, liquid silicone molding is a highly efficient and versatile manufacturing process for producing silicone rubber products. With its ability to meet varying reference specifications, it offers significant advantages in terms of flexibility, durability, and resistance to various environmental factors, making it widely favored across diverse industries.
Applications of liquid silicone molding
Liquid silicone molding, also known as LSR molding, is a versatile manufacturing process that utilizes liquid silicone rubber to create various types of products. This molding technique offers several advantages, making it valuable in a wide range of applications.
Medical Industry: LSR molding is extensively used in the medical field due to its biocompatibility, transparency, and sterilization resistance. It is employed to produce medical-grade components such as surgical instruments, implants, valves, and seals. LSR’s hypoallergenic properties make it suitable for devices that come into contact with the human body, and its ability to withstand high temperatures ensures proper sterilization.
Electronics Industry: Liquid silicone molding is valuable in the production of electronic components and devices. LSR’s exceptional electrical insulation properties make it ideal for manufacturing insulators, connectors, and transfer pads. Its ability to effectively protect against moisture and other environmental factors enhances the reliability and durability of electronic products.
Automotive Industry: Liquid silicone molding is widely used to manufacture automotive parts, including seals, gaskets, connectors, and spark plug boots. LSR’s resistance to extreme temperatures and its ability to maintain flexibility and integrity over time make it particularly suitable for demanding automotive environments.
Consumer Goods: Liquid silicone molding is employed in the production of numerous consumer goods due to its ability to produce high-quality, precise, and durable parts. It is used to create products such as phone cases, kitchen utensils, baby products like pacifiers and bottle nipples, and various household items, including seals and gaskets.
Aerospace Industry: The aerospace field requires parts that can withstand harsh environmental conditions, vibration, and extreme temperatures. Liquid silicone molding is utilized in the manufacturing of aerospace components like seals, gaskets, insulators, and connectors. Its high-performance properties, including resistance to UV radiation, ozone, and high altitude conditions, make it a valuable material for this industry.
Industrial Equipment: Liquid silicone molding is employed to create components for various industrial equipment. It offers excellent resistance to chemicals, UV radiation, and extreme temperatures, making it suitable for applications such as gaskets, seals, o-rings, and encapsulation of electronic parts.
Overall, liquid silicone molding finds applications in a diverse range of industries due to its outstanding properties and versatility. From medical devices to consumer goods, automotive parts to aerospace components, this molding technique allows the production of high-quality, precise, and durable products.
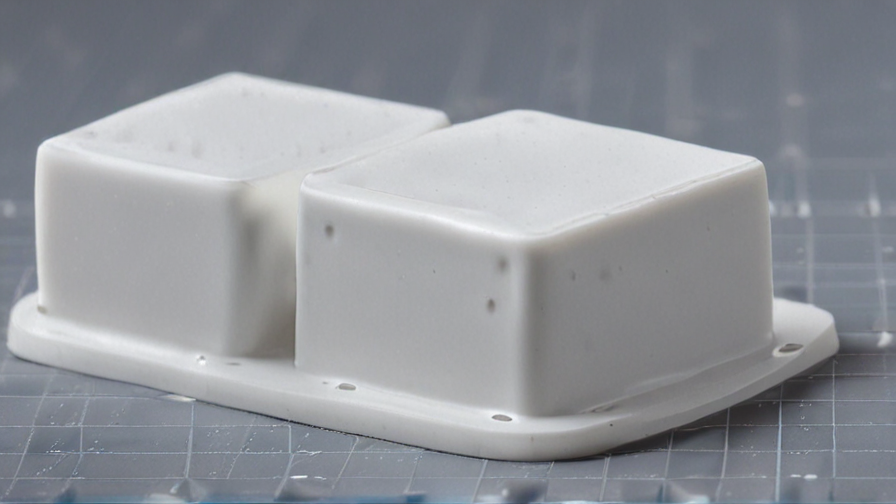
The Work Process and how to use liquid silicone molding
Liquid silicone molding is a highly efficient and versatile process used for manufacturing high-quality silicone products. The work process involves several key steps.
Firstly, a master prototype or 3D model of the desired silicone product is created. This can be achieved using CAD software or by 3D printing. The prototype serves as a mold for producing multiple replicas.
Next, the prototype mold is prepared by applying a release agent, ensuring easy removal of the silicone product once it solidifies. The mold is then clamped shut using a specialized mold-pressing machine.
Liquid silicone rubber, composed of two liquid components, is carefully mixed and degassed to remove any air bubbles. The liquid silicone is then poured or injected into the mold cavity. The mold is closed, creating a tight seal, and the silicone is allowed to cure.
Curing typically involves heating the mold to a specified temperature for a designated period. This process can also be accelerated by using heat and pressure. Once cured, the mold is cooled to allow the silicone to solidify fully.
After cooling, the mold is opened, and the solidified silicone product is removed. The product is inspected for any defects or imperfections on the surface. If necessary, excess material is trimmed off, and any corrective measures are taken.
Liquid silicone molding offers many advantages. It enables the production of complex shapes and intricate details, ensuring high dimensional accuracy. The process also allows for the creation of products with varying durometer and colors.
Moreover, liquid silicone molding is well-suited for producing parts on a large scale. The molds can be fabricated from various materials, such as aluminum or steel, depending on the required lifespan and complexity of the product.
In conclusion, liquid silicone molding is a precise and efficient method used for manufacturing high-quality silicone products. By following the steps outlined above, manufacturers can create a wide range of silicone parts with excellent detail and durability.
Quality Testing Methods for liquid silicone molding and how to control the quality
Liquid silicone molding is a versatile and widely used manufacturing process for producing silicone products. To ensure the quality of products obtained through this method, several testing methods and quality control measures are implemented.
One common quality testing method for liquid silicone molding is visual inspection. Inspectors examine the molded parts for any visual defects such as surface imperfections, air bubbles, or incomplete filling of the mold. They also check for dimensional accuracy, ensuring that the parts meet the required specifications.
Another testing method involves carrying out hardness testing. A durometer is used to measure the hardness of the silicone parts. This test helps to determine if the material has been properly cured and if it possesses the desired hardness level.
Another critical quality control measure is performing compression set testing. This test assesses the material’s ability to recover to its original shape after being compressed for a specific duration at a designated temperature. It aids in evaluating the silicone’s resilience, compression resistance, and long-term performance.
Moreover, performing tensile testing is crucial to check the strength and elongation properties of the silicone molded parts. This test helps in determining if the material meets the required tensile strength and elongation at break specifications, ensuring its suitability for the intended applications.
To enhance quality control, statistically based sampling plans are implemented. These sampling plans ensure that a representative number of parts are inspected and tested throughout the production process to detect any potential issues early on.
Furthermore, closely monitoring and controlling the process parameters during liquid silicone molding is vital. Factors such as material mixing ratios, injection pressure, curing time, and temperature must be carefully monitored to maintain consistent quality. Process validation techniques, including design of experiments (DOE), can be employed to optimize the process and identify the optimal parameter settings for achieving the desired quality outcomes.
In conclusion, quality testing methods for liquid silicone molding include visual inspection, hardness testing, compression set testing, and tensile testing. Implementing statistically based sampling plans and closely monitoring process parameters are additional measures to ensure quality control. By employing these methods and measures, manufacturers can produce high-quality silicone molded parts that meet the required specifications.
liquid silicone molding Sample Policy and Post-Purchase Considerations for liquid silicone molding from China
Sample Policy:
When purchasing liquid silicone molding products from China, it is essential to establish clear sample policies to ensure that both parties are satisfied with the final products. The following aspects should be considered:
1. Sample Availability: The supplier should provide samples of the liquid silicone molding products for evaluation before placing a bulk order. The samples should accurately represent the desired specifications and quality of the final product.
2. Sample Cost: It is customary for the buyer to bear the sample cost, including the product cost and shipping fees. However, for bulk orders, this cost can be later deducted from the total order value.
3. Customization: If the liquid silicone molding products require customization, it is important to clearly communicate the specific requirements, including dimensions, colors, and any additional features. The supplier should provide a detailed sample that meets all of the customization requests.
4. Lead Time: The supplier should provide a realistic lead time for sample production and delivery. This ensures that the buyer can evaluate the product and make an informed decision within a reasonable timeframe.
5. Acceptance Criteria: Clearly establish the acceptance criteria for the samples. This may include the quality of the product, accuracy of dimensions, color matching, and any other specific requirements. All parties should agree upon the acceptance criteria beforehand.
Post-Purchase Considerations:
After the purchase of liquid silicone molding products from China, the following considerations should be taken into account:
1. Quality Inspection: Upon receiving the bulk order, conduct a comprehensive quality inspection to ensure that the products meet the agreed-upon sample standards. This may involve checking dimensions, functionality, and overall quality.
2. Communication with the Supplier: Maintain open and frequent communication with the supplier throughout the process. Address any concerns or issues promptly to find suitable solutions.
3. Feedback and Reviews: Provide feedback to the supplier regarding the overall experience, product quality, and any areas for improvement. This can help build a long-term relationship and enhance future collaborations.
4. Reordering and Maintenance: If satisfied with the liquid silicone molding products, consider reordering from the same supplier for future requirements. Additionally, discuss maintenance and care instructions for the products to ensure their longevity.
In conclusion, establishing a clear sample policy and considering post-purchase aspects are crucial when engaging in liquid silicone molding purchasing from China. By doing so, one can ensure customer satisfaction and successful long-term business partnerships.
Sourcing liquid silicone molding from China: Opportunities, Risks, and Key Players
Sourcing liquid silicone molding from China offers both opportunities and risks for businesses. With its vast manufacturing capabilities and lower production costs, China has become a popular destination for companies looking to source liquid silicone molding. The opportunities include access to a wide range of suppliers, competitive pricing, and efficient production processes. China’s well-established supply chain and advanced manufacturing technologies also contribute to its attractiveness as a sourcing destination.
One of the key advantages of sourcing from China is the availability of a large pool of experienced manufacturers and suppliers specializing in liquid silicone molding. These suppliers often have the necessary expertise, equipment, and facilities to meet the diverse requirements of buyers in terms of volume, quality, and customization. Additionally, China’s competitive labor costs can help reduce manufacturing expenses, leading to cost savings for businesses.
However, there are also risks associated with sourcing liquid silicone molding from China. Quality control can be a major concern, as some suppliers may not adhere to the same rigorous manufacturing standards and regulations followed in other countries. It is crucial for businesses to conduct thorough due diligence on potential suppliers, including factory audits, quality inspections, and certifications, to ensure product quality and reliability. Another risk is intellectual property (IP) protection, as China has often faced criticism for IP infringements. Businesses must take appropriate measures to protect their designs, patents, and trademarks when sourcing from China.
Several key players dominate the liquid silicone molding market in China. Some prominent manufacturers include GW Plastics, Xiamen Better Silicone Rubber Co., Ltd., SIMTEC Silicone Parts, and Star Prototype. These companies have established themselves as reliable suppliers with a strong track record in producing high-quality liquid silicone molded parts. However, it is essential for businesses to thoroughly evaluate these players based on their capabilities, certifications, quality control measures, and past customer reviews before making a sourcing decision.
In conclusion, sourcing liquid silicone molding from China presents both opportunities and risks. While the country offers access to a vast supplier network and cost advantages, concerns such as quality control and IP protection must be carefully addressed. By conducting proper due diligence and selecting reputable key players in the market, companies can effectively navigate these risks and seize the opportunities presented by sourcing from China.
How to find and select reliable liquid silicone molding manufacturers in China,use google search manufacturers and suppliers
Finding and selecting reliable liquid silicone molding manufacturers in China can be done using a combination of online research, supplier directories, and personal recommendations. Here is a brief guide on how to accomplish this:
1. Use Google Search: Begin by searching for liquid silicone molding manufacturers in China on Google. Use relevant keywords like “liquid silicone molding manufacturers China” or “silicone molding suppliers China.” This will generate a list of potential manufacturers.
2. Supplier Directories: Explore popular supplier directories like Alibaba, Made-in-China, or Global Sources. These platforms allow you to filter your search based on product type, location, and other criteria. Look for manufacturers or suppliers with positive ratings, reviews, and a substantial number of transactions.
3. Verify Company Information: Visit the manufacturers’ websites identified during your search. Look for detailed company information, such as years of experience, production capacity, certifications, and product range. A reliable manufacturer will have a professional and informative website.
4. Assess Certifications and Quality Control: Check if the liquid silicone molding manufacturers have relevant certifications, such as ISO 9001 or ISO 13485. These certifications indicate that the manufacturer follows standardized quality control processes and meets industry standards.
5. Request Samples or Catalogs: Contact the shortlisted manufacturers and request samples or product catalogs. Assess the quality of their products, paying attention to material consistency, finishing, and if they meet your specific requirements.
6. Communication and Responsiveness: Gauge the manufacturers’ communication skills and responsiveness. A reliable manufacturer will promptly answer your inquiries and maintain clear and effective communication throughout the process.
7. Ask for References or Customer Feedback: Seek references from the manufacturer’s previous or current clients. This will help you assess their reliability, product quality, and overall customer satisfaction.
8. Factory Audit: If feasible, consider conducting a factory audit or arranging for a third-party inspection to evaluate the manufacturing facilities, equipment, and operational processes. This will provide additional assurance of the manufacturer’s reliability.
By following these steps and conducting thorough research, you can find and select reliable liquid silicone molding manufacturers in China for your specific needs. Remember to consider factors such as quality, certifications, communication, and customer feedback to make an informed decision.
How to check liquid silicone molding manufacturers website reliable,use google chrome SEOquake check if ranking in top 10M
To check the reliability of a liquid silicone molding manufacturer’s website, you can follow these steps:
1. Use Google Chrome: Start by opening the website in the Google Chrome browser. Chrome has a wide range of built-in tools and extensions that can help you evaluate a website.
2. Install SEOquake Extension: Add the SEOquake extension to your Chrome browser. SEOquake is a popular tool that provides valuable SEO-related information about websites, such as their ranking, traffic, and other key metrics.
3. Check Website Ranking: Once the SEOquake extension is installed, navigate to the liquid silicone molding manufacturer’s website and activate SEOquake by clicking on its icon at the top right corner of your Chrome browser. It will generate a summary of SEO-related data.
4. Top 10M Ranking: Look for the website’s Alexa Rank, which is a measure of its popularity and traffic compared to other websites. If the website falls within the top 10 million, it indicates a significant level of traffic and potentially higher reliability.
5. Evaluate Website Design and Content: While rankings are helpful, it’s also essential to assess the website’s overall design, functionality, and content. A reliable manufacturer will invest in a professional, user-friendly website that highlights their expertise, services, and contact details.
6. Trustworthiness: Look for trust signals such as testimonials, customer reviews, certifications, and affiliations. Genuine customer feedback and endorsements provide an indication of the manufacturer’s reliability and quality.
Remember not to solely rely on rankings. A website’s position in search engine results can be influenced by various factors, and a high ranking does not guarantee reliability. Utilize SEOquake as a supplementary tool and consider other factors mentioned above to make an informed judgment about the liquid silicone molding manufacturer’s website.
Top 10 liquid silicone molding manufacturers in China with each 160 words introduce products,then use markdown create table compare
1. Xiamen Better Silicone Rubber Co., Ltd.:
Specializing in liquid silicone molding, Xiamen Better Silicone Rubber Co., Ltd. offers a wide range of products such as silicone rubber keypads, silicone kitchenware, silicone baby products, and silicone medical accessories. Their liquid silicone molding process ensures high precision and consistency in the manufacturing of these products.
2. Guangzhou JMT Mold Co., Ltd.:
Guangzhou JMT Mold Co., Ltd. is a trusted liquid silicone molding manufacturer known for producing high-quality silicone products for various industries including automotive, electronic, and medical. Their liquid silicone molding capabilities enable them to manufacture intricate designs and complex shapes.
3. Dongguan City Betterly New Materials Co., Ltd.:
Dongguan City Betterly New Materials Co., Ltd. specializes in liquid silicone molding and offers a diverse range of products such as silicone seals, gaskets, and silicone parts for electronic devices. With a state-of-the-art production facility, they ensure that their products are of the highest quality.
4. Shenzhen HuaChengXin Silicone Rubber Co., Ltd.:
Shenzhen HuaChengXin Silicone Rubber Co., Ltd. is a leading liquid silicone molding manufacturer in China. They have a wide range of products including silicone medical accessories, silicone baby products, and silicone kitchenware that are all produced using their advanced liquid silicone molding techniques.
5. Xiamen Fuke Car Accessories Co., Ltd.:
Xiamen Fuke Car Accessories Co., Ltd. specializes in liquid silicone molding for automotive applications. They produce silicone gaskets, seals, and other automotive parts that are highly durable and resistant to extreme temperatures and chemicals.
6. Shenzhen XinHaiWang Technology Co., Ltd.:
Shenzhen XinHaiWang Technology Co., Ltd. offers liquid silicone molding services to produce high-quality silicone medical products. Their range includes silicone medical tubes, silicone valves, and silicone implants, all manufactured to meet strict medical standards.
7. Yuyao Hongrui Plastic Products Co., Ltd.:
Yuyao Hongrui Plastic Products Co., Ltd. is a liquid silicone molding manufacturer that specializes in producing silicone baby products. Their range includes silicone baby pacifiers, bottle nipples, and teething toys, all made from safe and non-toxic materials.
8. Hangzhou Bright Rubber Plastic Product Co., Ltd.:
Hangzhou Bright Rubber Plastic Product Co., Ltd. uses liquid silicone molding to manufacture a wide range of silicone rubber products such as kitchenware, seals, gaskets, and O-rings. Their products exhibit excellent resistance to heat, chemicals, and weathering.
9. Dongguan Tianwar Silicone Technology Co., Ltd.:
Dongguan Tianwar Silicone Technology Co., Ltd. is a liquid silicone molding manufacturer known for producing high-quality silicone products for the electronic industry. They offer silicone buttons, keypads, and conductive pads that are widely used in electronics manufacturing.
10. Shenzhen Jiuding Silicone Material Co., Ltd.:
Shenzhen Jiuding Silicone Material Co., Ltd. specializes in liquid silicone molding for medical applications. They produce silicone catheters, tubing, and surgical instruments, ensuring strict adherence to medical standards and regulations.
| Manufacturer | Description | Products |
|————–|————-|———-|
| Xiamen Better Silicone Rubber Co., Ltd. | Offers liquid silicone molding services for silicone keypads, kitchenware, baby products, and medical accessories. | Key pads, kitchenware, baby products, medical accessories |
| Guangzhou JMT Mold Co., Ltd. | Specializes in liquid silicone molding and produces high-quality silicone products for industries like automotive, electronic, and medical. | Automotive products, electronic products, medical products |
| Dongguan City Betterly New Materials Co., Ltd. | Offers liquid silicone molding for seals, gaskets, and electronic parts. | Seals, gaskets, electronic parts |
| Shenzhen HuaChengXin Silicone Rubber Co., Ltd. | Leading manufacturer producing silicone medical accessories, baby products, and kitchenware using liquid silicone molding. | Medical accessories, baby products, kitchenware |
| Xiamen Fuke Car Accessories Co., Ltd. | Specializes in liquid silicone molding for automotive applications, producing seals, gaskets, and other automotive parts. | Seals, gaskets, automotive parts |
| Shenzhen XinHaiWang Technology Co., Ltd. | Manufacturing medical silicone products such as tubes, valves, and implants using liquid silicone molding. | Medical tubes, valves, implants |
| Yuyao Hongrui Plastic Products Co., Ltd. | Produces liquid silicone molding products specifically for babies, including pacifiers, bottle nipples, and teething toys. | Pacifiers, bottle nipples, teething toys |
| Hangzhou Bright Rubber Plastic Product Co., Ltd. | Specializes in liquid silicone molding of kitchenware, seals, gaskets, and O-rings. | Kitchenware, seals, gaskets, O-rings |
| Dongguan Tianwar Silicone Technology Co., Ltd. | Manufactures silicone buttons, keypads, and conductive pads for the electronics industry using liquid silicone molding. | Buttons, keypads, conductive pads |
| Shenzhen Jiuding Silicone Material Co., Ltd. | Produces liquid silicone molded medical products such as catheters, tubing, and surgical instruments. | Catheters, tubing, surgical instruments |
Background Research for liquid silicone molding manufacturers Companies in China, use qcc.com archive.org importyeti.com
When looking for liquid silicone molding manufacturers in China, several websites can provide valuable information. These include qcc.com, archive.org, and importyeti.com.
Qcc.com is a Chinese business directory where users can find information about numerous companies operating in different industries. By searching for “liquid silicone molding manufacturers” on qcc.com, one can access detailed profiles of companies involved in this field. These profiles typically contain information such as company name, contact details, business scope, product description, and certification status. Users can also find ratings and reviews from previous customers, which can help evaluate the reliability and quality of the manufacturers.
Archive.org is a platform that captures and stores web page snapshots from the past. While it may not directly provide information on liquid silicone molding manufacturers in China, it can be helpful to explore historical versions of manufacturer websites. This can give insights into the company’s evolution, past projects, certifications, and other pertinent details. Additionally, it may provide access to images, product catalogs, and other relevant information that may no longer be available on the live website.
Importyeti.com is a global trade data platform that provides import and export information. Users can search for specific products, including liquid silicone molding, to find companies that have engaged in international trade in this sector. This platform offers details such as company name and contact information, shipment records, and trade histories. This information can assist in identifying reputable and experienced liquid silicone molding manufacturers in China.
In conclusion, qcc.com, archive.org, and importyeti.com are valuable resources for conducting background research on liquid silicone molding manufacturers in China. By utilizing these platforms, users can access comprehensive company profiles, historical website data, and trade information to make informed decisions in their search for manufacturers.
Leveraging Trade Shows and Expos for liquid silicone molding Sourcing in China
Trade shows and expos offer a wealth of opportunities for businesses seeking to source liquid silicone molding in China. These events bring together industry professionals, suppliers, and manufacturers in one location, providing a platform for networking, knowledge sharing, and sourcing.
Attending trade shows and expos related to silicone molding in China allows businesses to connect with a wide range of suppliers and manufacturers specialized in liquid silicone molding. It offers a unique chance to meet face-to-face with potential partners, discuss requirements, and establish relationships.
One key advantage of trade shows and expos is the ability to see and touch physical samples or prototypes. This hands-on experience helps in assessing the quality, material, finish, and design capabilities of different suppliers. It also enables businesses to gain a better understanding of the manufacturing process and ask specific questions related to their requirements.
Trade shows and expos also provide a platform for businesses to stay up-to-date with the latest industry trends, advancements, and innovations in liquid silicone molding. Companies can attend seminars, workshops, or presentations by industry experts, gaining valuable insights into new technologies, materials, or techniques. This knowledge can inform decision-making and enhance product development processes.
Furthermore, trade shows and expos offer a competitive environment where businesses can compare and evaluate multiple suppliers in one location. This streamlines the sourcing process, saving time and effort. Companies can gather information, collect brochures, and even negotiate deals at the event itself.
To make the most of trade shows and expos, businesses should prepare beforehand. This includes identifying relevant events, conducting thorough research on participating exhibitors, and setting specific sourcing goals. It is essential to have a clear understanding of the required product specifications, quality standards, and expected delivery timelines.
In conclusion, trade shows and expos present significant opportunities for sourcing liquid silicone molding in China. By leveraging these events, businesses can connect with suppliers and manufacturers, evaluate their capabilities, gain industry insights, and streamline the sourcing process. Attending trade shows and expos offers a cost-effective and efficient way to source liquid silicone molding while building valuable relationships with potential partners.
The Role of Agents and Sourcing Companies in Facilitating liquid silicone molding Purchases from China
Agents and sourcing companies play a crucial role in facilitating liquid silicone molding purchases from China. They act as intermediaries between buyers and manufacturers, helping to bridge the gap in language, culture, and logistics. By utilizing their expertise and networks, agents and sourcing companies can simplify the procurement process and ensure a successful purchase.
One of the main functions of agents and sourcing companies is to identify suitable suppliers in China. They have extensive knowledge of the local market and can evaluate potential manufacturers based on quality, price, production capabilities, and other factors. This saves buyers significant time and effort in finding reliable suppliers on their own.
Furthermore, agents and sourcing companies can handle negotiations on behalf of buyers. They have experience in dealing with Chinese manufacturers and are familiar with local business practices and customs. This expertise allows them to secure favorable terms and conditions, such as competitive pricing, favorable payment methods, and production lead times.
Agents and sourcing companies also assist in quality control. They can conduct factory inspections, monitor production processes, and perform pre-shipment inspections to ensure that the final products meet the required standards and specifications. This helps buyers mitigate the risks of receiving substandard or defective products.
Additionally, agents and sourcing companies help navigate the complexities of shipping and logistics. They coordinate with freight forwarders, handle documentation, and arrange for efficient transportation from China to the buyer’s destination. This ensures a timely and seamless delivery of the liquid silicone moldings.
Overall, agents and sourcing companies play a vital role in facilitating liquid silicone molding purchases from China. By leveraging their knowledge, networks, and expertise, they streamline the procurement process, enhance quality control, and ensure reliable delivery. This allows buyers to tap into China’s manufacturing capabilities while mitigating risks and maximizing their sourcing efficiency.
Price Cost Research for liquid silicone molding manufacturers Companies in China, use temu.com and 1688.com
When researching liquid silicone molding manufacturers in China, two popular websites to use are temu.com and 1688.com.
temu.com is an online platform that connects global buyers with Chinese suppliers. This website allows you to search for liquid silicone molding manufacturers in China and provides detailed information about each company. You can find information such as the company’s location, certification, capacity, and product range. temu.com also provides a chat feature that allows you to communicate directly with manufacturers for further inquiries and negotiations.
1688.com is a Chinese e-commerce platform owned by Alibaba Group. It is widely used by domestic buyers in China and offers a variety of products and manufacturers. On 1688.com, you can search for liquid silicone molding manufacturers and view their product listings, prices, and company information. This platform also provides a chat feature for communication.
When researching the price and cost of liquid silicone molding manufacturers in China, it is essential to consider various factors. The cost will depend on the complexity of the mold, the material used, the production volume, and other specifications. It is recommended to request quotes from multiple manufacturers to compare prices.
In conclusion, when conducting price and cost research for liquid silicone molding manufacturers in China, temu.com and 1688.com are valuable resources. They provide comprehensive information about companies and their products. By utilizing these platforms, buyers can connect with manufacturers, request quotes, and negotiate pricing.
Shipping Cost for liquid silicone molding import from China
The shipping cost for liquid silicone molding imports from China can vary depending on various factors such as weight, dimensions, distance, shipping method, and additional services required. Generally, there are two common shipping methods: sea freight and air freight.
Sea freight is often the most cost-effective option for large and heavy shipments. It is suitable for bulk orders as it offers lower prices per kilogram or cubic meter. The shipping cost for liquid silicone molding imports via sea freight can range from $800 to $4000 or even more, depending on the distance and volume of the shipment.
Air freight is a faster but more expensive option. It is ideal for smaller orders or time-sensitive shipments. The shipping cost for liquid silicone molding imports via air freight can range from $5 to $15 per kilogram. Additional charges may apply for fuel surcharges, handling fees, customs clearance, and delivery to final destination.
It’s important to note that these costs are approximate and can vary depending on various factors, including the shipping company chosen, current market rates, and any additional services required. It’s recommended to consult with shipping companies or freight forwarders to obtain accurate quotes based on your specific requirements.
Furthermore, it’s advisable to consider additional costs such as customs duties, import taxes, and customs brokerage fees, which will be incurred upon arrival in the destination country. These charges vary depending on the country’s regulations and the declared value of the goods.
To ensure a smooth shipping process and avoid unexpected costs, it is crucial to properly calculate and budget for shipping expenses. Working with a reliable shipping agent or freight forwarder who specializes in China imports can help you navigate the complexities of shipping and provide accurate cost estimates.
Compare China and Other liquid silicone molding Markets: Products Quality and Price,Visible and Hidden Costs
China is known for its dominance in the liquid silicone molding market due to its vast manufacturing capabilities and competitive pricing. However, it is essential to compare China with other liquid silicone molding markets in terms of product quality and price, as well as visible and hidden costs.
Product quality is a crucial factor while choosing a liquid silicone molding market. China has made significant progress in improving product quality over the years. Many Chinese manufacturers have obtained certifications such as ISO 9001, ISO 14001, and FDA, indicating adherence to international quality standards. However, other markets, such as Germany and the United States, have long-established reputations for producing high-quality liquid silicone molded products. These markets often adhere to stricter quality control procedures and regulations, ensuring superior product quality compared to China.
Pricing is another factor that needs to be considered. China has a reputation for offering competitive pricing due to its low labor costs and economies of scale. This advantage has made it attractive to many businesses worldwide. However, other liquid silicone molding markets, particularly Western countries, may have higher labor costs, resulting in relatively higher prices. However, it is important to note that these markets often offer superior product quality, which can justify the higher cost.
Visible costs, such as the cost of raw materials, manufacturing, and transportation, are relatively comparable across different liquid silicone molding markets. These costs are typically transparent and can be easily compared to make an informed decision. However, hidden costs, such as intellectual property protection, delivery delays, or quality issues, may vary significantly across markets. China, in particular, has faced criticism for intellectual property theft and may entail greater risks for companies concerned about protecting their proprietary technology.
In conclusion, while China’s liquid silicone molding market offers competitive pricing and improving product quality, other markets, such as Germany and the United States, have established themselves as leaders in terms of superior product quality. Additionally, hidden costs and risks associated with intellectual property protection in China may be a significant consideration for some businesses. Therefore, companies must thoroughly evaluate their specific requirements and weigh the trade-offs between product quality, pricing, and potential risks when choosing a liquid silicone molding market.
Understanding Pricing and Payment Terms for liquid silicone molding: A Comparative Guide to Get the Best Deal
Liquid silicone molding is a popular manufacturing process for producing high-quality, precision silicone parts. When considering this technique for your project, it is essential to understand the pricing and payment terms to secure the best deal.
Determining the cost of liquid silicone molding requires assessing various factors. These include the complexity and size of the part, the required volume, tooling requirements, and material selection. Complex designs or intricate details may increase the price due to more extensive tooling and longer production times. Similarly, larger parts or higher production volumes often result in higher costs. Material selection also plays a role, as specialized or custom compounds may incur additional expenses.
To get the best deal, it is crucial to compare quotes from multiple manufacturers. Request detailed breakdowns of costs, including tooling charges, material costs, labor expenses, and any additional fees. It is advisable to avoid selecting the lowest-priced quote without understanding what is included. Ensure that all quotes are based on the same specifications, as variations can significantly impact the final cost.
Besides pricing, payment terms are another crucial aspect to consider. Common payment structures include:
1. Upfront payment: Some manufacturers may require a percentage of the total cost upfront before starting production. This option provides assurance for the supplier but may present risks for the client.
2. Progressive payments: In this approach, payments are made at predetermined stages throughout the manufacturing process. It helps distribute the financial burden and provides reassurance for both parties.
3. Net payment terms: Net payment terms allow the client to pay the full amount after the completed production and delivery of parts. This option minimizes upfront costs but requires trust and confidence in the supplier’s ability to meet expectations.
It is important to discuss and negotiate payment terms with potential manufacturers to find the most suitable arrangement for your project’s financial circumstances.
In conclusion, understanding pricing and payment terms when considering liquid silicone molding is crucial to secure the best deal. Assessing the factors affecting costs, comparing quotes from multiple manufacturers, and negotiating payment terms can help optimize the outcome. By investing time and effort into the procurement process, you can obtain the desired parts at competitive prices while safeguarding your financial interests.
Chinese Regulations and Industry Standards Certifications for liquid silicone molding,Import Regulations and Customs for liquid silicone molding from China
China has established a comprehensive set of regulations and industry standards certifications for liquid silicone molding. These regulations ensure that the manufacturing process and product quality meet specific criteria. Some of the key regulations and certifications in China for liquid silicone molding include:
1. National Compliance Standards: China has national standards and regulations for liquid silicone molding, such as GB/T 24674-2009, which specifies the technical requirements for liquid silicone rubber products.
2. ISO Certification: Manufacturers can obtain ISO certifications such as ISO 9001 (Quality Management System Certification) and ISO 13485 (Medical Devices Quality Management System Certification) to demonstrate compliance with international quality standards.
3. RoHS Compliance: The Restriction of Hazardous Substances (RoHS) directive restricts the use of certain hazardous substances in electrical and electronic equipment. Manufacturers are required to comply with RoHS regulations, ensuring that their liquid silicone molding products are free from harmful substances.
4. FDA Approval: For liquid silicone molding products intended for medical or food contact applications, manufacturers need to obtain Food and Drug Administration (FDA) approval. This ensures that the products meet the safety and performance requirements mandated by the FDA.
Import regulations and customs procedures for liquid silicone molding products from China vary depending on the importing country. However, some general considerations include:
1. Customs Tariffs: Importers need to comply with customs regulations and pay relevant import duties and tariffs when bringing liquid silicone molding products into their country.
2. Product Documentation: Importers must prepare and submit necessary product documentation, such as commercial invoices, packing lists, and certificates of origin, as required by the importing country’s customs authorities.
3. Product Inspections: In some cases, liquid silicone molding products may be subject to inspections by the importing country’s customs authorities to ensure compliance with quality standards and regulations.
4. Import Licenses and Permits: Depending on the nature and intended use of the products, importers may need to obtain specific licenses or permits from their country’s regulatory authorities.
To ensure a smooth import process, it is advisable for importers to work with experienced freight forwarders or customs brokers who can provide guidance and assistance in navigating the complex import requirements for liquid silicone molding products from China.
Sustainability and Environmental Considerations in liquid silicone molding Manufacturing
In recent years, there has been a growing trend towards sustainability and environmental considerations in manufacturing processes. This holds true for liquid silicone molding, a versatile manufacturing technique used in a wide range of industries. To ensure sustainability in liquid silicone molding manufacturing, several aspects need to be addressed.
Firstly, the choice of raw materials plays a crucial role. Silicone, the primary material used in this process, should be responsibly sourced and free from harmful substances. Manufacturers can opt for eco-friendly silicone that meets sustainability standards, thereby minimizing the environmental impact.
Energy efficiency is another important aspect. Manufacturers should employ energy-efficient machinery and optimize process parameters to reduce energy consumption during liquid silicone molding. By employing advanced technologies and adopting energy-saving practices, manufacturers can significantly minimize their carbon footprint and contribute to sustainability.
Waste reduction and recycling are essential to sustainable manufacturing. Waste generated during the silicone molding process, such as excess material or defective products, should be minimized through careful process control. Additionally, recycling programs can be implemented to recycle silicone waste and reduce the need for virgin material.
Water is a valuable resource, and its conservation is crucial. In liquid silicone molding, water is used for cooling and curing processes. Manufacturers must implement water-saving measures, such as closed-loop cooling systems and water recycling, to minimize water consumption and ensure efficient use.
To enhance sustainability, manufacturers can also explore alternatives to traditional silicone molding techniques. For example, using 3D printing technologies to create silicone molds can significantly reduce material waste and energy consumption.
Lastly, manufacturers should prioritize the life cycle assessment (LCA) of liquid silicone molding products. LCA evaluates the environmental impact of a product from raw material extraction to disposal. By considering LCA in the design phase, manufacturers can identify opportunities for improvement and develop more sustainable products.
In conclusion, sustainability and environmental considerations are increasingly important in liquid silicone molding manufacturing. By focusing on responsible sourcing, energy efficiency, waste reduction, water conservation, exploring alternative techniques, and considering the product life cycle, manufacturers can minimize their environmental impact and contribute to a sustainable future.
List The Evolution history of “liquid silicone molding”
Liquid silicone molding, also known as liquid silicone rubber (LSR) molding, has a rich history of evolution that spans several decades. The technique emerged as a result of advancements made in both silicone materials and injection molding technology.
In the late 1950s and early 1960s, the first attempts to develop LSR molding were made. At this time, silicone materials were already being used in various applications due to their unique properties, such as high thermal stability and chemical inertness. However, they were primarily processed using compression molding techniques, which limited their potential.
In the 1970s, significant progress was made when silicone raw materials suitable for injection molding became available. Injection molding allowed for more efficient and precise production, making it an ideal manufacturing method for complex parts. This breakthrough paved the way for the commercialization of liquid silicone molding.
Throughout the 1980s and 1990s, LSR molding technologies continued to advance. Improvements in injection molding machines, including the development of cold runner systems and valve gating techniques, enabled manufacturers to produce more detailed and intricate silicone parts. These advancements expanded the application possibilities of liquid silicone molding, allowing it to be used in industries such as automotive, medical, and consumer electronics.
In recent years, the evolution of liquid silicone molding has been driven by the demand for more sustainable and eco-friendly manufacturing processes. Manufacturers have focused on optimizing energy efficiency, reducing waste, and minimizing the use of hazardous materials. Additionally, advancements in tooling technologies, such as the utilization of 3D printing for mold making, have further enhanced the capabilities of LSR molding.
Moreover, the incorporation of automation and robotics in liquid silicone molding has improved production speed and consistency while reducing labor costs. These technological advancements have made the process more reliable, efficient, and cost-effective.
Looking ahead, liquid silicone molding is expected to continue evolving as new materials, technologies, and manufacturing approaches emerge. The industry will likely focus on further improving the performance and properties of silicone materials, exploring new application areas, and finding innovative solutions to meet the evolving needs of various industries.
The Evolution and Market Trends in liquid silicone molding Industry
The liquid silicone molding industry has evolved significantly over the years, adapting to changing market trends and technological advancements. Liquid silicone molding, also known as LSR molding, is a manufacturing process that involves injecting liquid silicone into a mold to produce various products and components.
One of the key trends in the liquid silicone molding industry is the increasing demand for precision and complex parts. Liquid silicone molding offers high precision and dimensional stability, making it suitable for applications in industries such as automotive, medical, and electronics. As companies seek to improve the performance and quality of their products, the demand for liquid silicone molding has been steadily growing.
Another trend in the industry is the focus on sustainability and environmentally friendly manufacturing. Liquid silicone is a biocompatible material that can be recycled, reducing waste and minimizing the environmental impact of production processes. This shift towards sustainability is driven by both consumer demands for greener products and regulatory requirements in various regions.
Furthermore, advancements in technology have facilitated the growth of the liquid silicone molding industry. Automation and robotics have improved production efficiency and reduced costs, making liquid silicone molding more accessible to a wider range of companies. Additionally, the development of innovative mold designs and simulation software has enabled manufacturers to optimize the molding process and achieve faster turnaround times.
In terms of market growth, the liquid silicone molding industry is expected to expand significantly in the coming years. The medical and healthcare sector, in particular, presents a lucrative opportunity for liquid silicone molding companies, as the demand for medical devices and equipment continues to rise. The automotive industry is also a major market for liquid silicone molding, with applications in gaskets, seals, and electrical components.
In conclusion, the liquid silicone molding industry has witnessed significant evolution and is driven by market trends such as the demand for precision parts, sustainability, and advancements in technology. With the increasing demand in sectors such as medical and automotive, the industry is expected to experience significant growth in the foreseeable future.
Custom Private Labeling and Branding Opportunities with Chinese liquid silicone molding Manufacturers
Chinese liquid silicone molding manufacturers offer custom private labeling and branding opportunities for businesses looking to create their own unique products. With their expertise in liquid silicone molding, these manufacturers can produce high-quality products that align with a company’s branding and specifications.
Private labeling allows businesses to have their own brand name, logo, and packaging on the products they sell. This gives companies the ability to establish their brand identity and build customer loyalty. Chinese manufacturers can help businesses with the entire private labeling process, from designing the packaging to printing the brand name and logo on the product.
In addition to private labeling, Chinese liquid silicone molding manufacturers also offer branding opportunities. This means that businesses can customize the product itself to match their branding. Manufacturers can create products in various colors, sizes, and designs, ensuring that they reflect a company’s image and appeal to its target market.
Chinese manufacturers are known for their cost-effective production capabilities, making private labeling and branding opportunities more affordable for businesses. With their advanced equipment and skilled workforce, these manufacturers can produce high-quality products at competitive prices.
Collaborating with Chinese liquid silicone molding manufacturers for private labeling and branding opportunities offers businesses numerous advantages. It allows them to have unique products that stand out in the market and differentiate themselves from competitors. It also gives them control over the entire product development process, ensuring that the final result meets their expectations.
In conclusion, Chinese liquid silicone molding manufacturers provide custom private labeling and branding opportunities for businesses seeking to create their own products. These manufacturers offer comprehensive solutions from packaging design to product customization, enabling businesses to have a distinct brand identity and appeal to their target market. Moreover, their cost-effective production capabilities make private labeling and branding opportunities more accessible to businesses of all sizes.
Tips for Procurement and Considerations when Purchasing liquid silicone molding
When purchasing liquid silicone molding (LSM), it is essential to consider certain factors to ensure a successful procurement process. Here are some key tips and considerations:
1. Material Requirements: Determine the specific requirements of the liquid silicone molding material based on your intended use. Consider factors such as temperature resistance, flexibility, hardness, chemical resistance, and biocompatibility if applicable.
2. Supplier Selection: Choose a reliable and experienced supplier who specializes in liquid silicone molding. Consider factors such as their reputation, track record, certification, quality control processes, and customer service.
3. Material Quality: Ensure that the liquid silicone molding material meets the required quality standards, such as ISO certifications. Request samples and conduct thorough testing to determine its suitability for your desired application.
4. Compatibility: Ensure that the liquid silicone molding material is compatible with other materials or substrates that will be used in the final product or component. Compatibility issues may lead to adhesion problems or reduced performance.
5. Cost-Effectiveness: Evaluate the overall cost-effectiveness of the liquid silicone molding material, considering factors such as the price per unit, wastage during the molding process, and long-term durability. Seek competitive pricing by comparing multiple suppliers.
6. Lead Time: Consider the lead time required for manufacturing and delivering the liquid silicone molding material. Ensure that the supplier can meet your production timeline and the material is readily available when needed.
7. Customization Options: Discuss with the supplier about any customization options available for the liquid silicone molding material. This includes color, appearance, texture, and other specific requirements that may be needed for your product.
8. Regulatory Compliance: Ensure that the liquid silicone molding material meets any necessary regulatory requirements, such as FDA approval for medical or food-grade applications. Compliance to regulations is vital for product safety and legality.
9. Technical Support: Inquire about the technical support and expertise offered by the supplier. They should be able to provide guidance on material selection, design optimization, and troubleshooting during the manufacturing process.
10. Warranty and Return Policy: Seek clarity on the supplier’s warranty or return policy for the liquid silicone molding material. This is crucial in case of any material defects or performance issues that may arise after procurement.
By considering these tips and factors during the procurement process, you can ensure the successful purchase of liquid silicone molding material that meets your specific requirements and expectations.
FAQs on Sourcing and Manufacturing liquid silicone molding in China
1. What is liquid silicone molding and why is it popular in China?
Liquid silicone molding is a manufacturing process used to produce silicone rubber parts and products. It involves injecting liquid silicone rubber into a mold cavity, where it solidifies and takes the shape of the mold. This process is highly preferred in China due to its versatility, cost-effectiveness, and the ability to produce complex and intricate designs with high precision.
2. What are the advantages of sourcing liquid silicone molding in China?
China offers several advantages for sourcing liquid silicone molding, including lower labor costs, a vast pool of skilled workers, and an established infrastructure for manufacturing. Additionally, Chinese manufacturers have extensive experience in liquid silicone molding and are equipped with advanced technology, enabling them to deliver high-quality products at competitive prices. Moreover, China’s manufacturing industry has a strong supply chain network, ensuring efficient sourcing of raw materials.
3. What are the key considerations when sourcing liquid silicone molding in China?
When sourcing liquid silicone molding in China, there are a few key considerations to keep in mind. Firstly, it is essential to conduct thorough research and due diligence to identify reliable and reputable manufacturers who have a proven track record in liquid silicone molding. Verifying certifications, quality control measures, and production capabilities is crucial to ensure consistent and compliant manufacturing.
Another important consideration is communication and language barriers. It is advisable to work with a manufacturing partner that can effectively communicate in English and provide prompt responses to queries and concerns. Clear and detailed communication is vital to avoid misunderstandings and ensure that the final product meets all requirements.
Additionally, it is essential to discuss and negotiate terms and contracts, including pricing, production timelines, quality control procedures, and intellectual property protection. Visiting the manufacturer’s facility in person or conducting video inspections can also help assess their capabilities and establish a strong working relationship.
4. Are there any challenges that might arise when sourcing liquid silicone molding in China?
While sourcing liquid silicone molding in China offers substantial benefits, there can be challenges to consider. These include intellectual property protection, potential quality issues, and language barriers. It is crucial to have proper legal agreements and non-disclosure agreements in place to protect intellectual property and product designs. Regular quality inspections and establishing a robust quality control process are also essential to mitigate any potential issues. Working with a trusted sourcing agent or conducting thorough due diligence can help overcome these challenges.
In conclusion, China is an ideal destination for sourcing liquid silicone molding due to its cost-effectiveness, manufacturing expertise, and robust supply chain. However, conducting proper research, effective communication, and establishing strong partnerships are vital to ensure a successful sourcing experience.
Why contact sourcifychina.com get free quota from reliable liquid silicone molding suppliers?
Contacting Sourcify China to get a free quota is beneficial for several reasons. Firstly, Sourcify China is a trusted platform known for connecting businesses with reliable suppliers in China. By accessing their network, businesses can be assured of finding reputable liquid silicone molding suppliers.
Liquid silicone molding is a specialized manufacturing process, and finding reliable suppliers can be challenging. Sourcify China has already vetted and verified their suppliers, ensuring that businesses can find high-quality products at competitive prices. This saves businesses time and effort in searching for suitable suppliers independently.
Additionally, Sourcify China also offers a free quota for contacting suppliers. This allows businesses to explore different options and obtain customized quotations specific to their requirements. By getting multiple quotations, businesses can compare prices, negotiate terms, and choose the most cost-effective solution.
Furthermore, Sourcify China’s network of suppliers also provides various value-added services. This includes design support, prototyping, and post-production services, which can further enhance the manufacturing process. These added services can contribute to the overall efficiency and success of a project.
In conclusion, contacting Sourcify China for obtaining a free quota from reliable liquid silicone molding suppliers is advantageous for businesses. It provides access to pre-vetted suppliers, the ability to compare quotations, and access to value-added services. This simplifies the sourcing process and enables businesses to find the best supplier that meets their specific requirements.